甲醇生产工艺介绍
甲醇的生产工艺流程设计

甲醇的生产工艺流程设计引言甲醇是一种重要的化工原料,广泛应用于合成气体、燃料、溶剂等领域。
甲醇的生产工艺流程设计是确保甲醇生产过程高效、稳定和环保的关键。
本文将介绍甲醇的生产工艺流程设计及其关键环节。
原料准备甲醇的主要原料是天然气和煤炭。
在原料准备阶段,首先对原料进行预处理,去除杂质和不纯物质,以保证后续反应过程的顺利进行。
天然气和煤炭分别经过脱硫、脱氮等处理,以提高甲醇的产率和质量。
合成气制备合成气是甲醇生产过程中的重要中间产物。
合成气由一定比例的氢气和一氧化碳组成。
合成气的制备一般采用蒸汽重整、催化重整和气化等方法。
其中,蒸汽重整是最常用的方法之一。
在蒸汽重整过程中,烃类化合物和蒸汽在高温下进行催化反应,生成合成气。
甲醇合成甲醇合成是甲醇生产的核心环节。
合成气与催化剂接触,在一定的温度和压力下进行甲醇合成反应。
常用的甲醇合成方法有低温法和高温法两种。
低温法低温法是一种在相对较低的温度下进行甲醇合成的方法。
该方法的特点是反应速率较慢,但选择性较高。
常用的催化剂有氧化钡、氧化铜等。
低温法主要包括气相法、液相法和气液两相法。
高温法高温法是一种在相对较高的温度下进行甲醇合成的方法。
该方法的特点是反应速率较快,但选择性较低。
常用的催化剂有氧化锌、氧化铝等。
高温法主要包括固定床法、悬浮床法和流化床法。
甲醇分离与纯化甲醇合成反应产物中通常含有杂质和其他副产物。
为了提高甲醇的纯度,需要进行甲醇的分离与纯化。
甲醇的分离与纯化一般采用精馏、萃取、吸附等方法。
其中,精馏是最常用的方法之一。
通过精馏,可以将甲醇和其他有机物、水分等分离开来,得到高纯度的甲醇。
甲醇的储存与运输甲醇生产后需要进行适当的储存和运输,以满足市场需求。
甲醇的储存和运输一般采用特殊的容器,如储罐和运输车辆。
在储存和运输过程中,需要采取相应的安全措施,以避免甲醇泄漏和爆燃等事故。
环保措施甲醇生产工艺流程设计中,环保问题尤为重要。
在甲醇生产过程中,会产生一定量的废水、废气和固体废物。
甲醇制造工艺

甲醇制造工艺
甲醇是一种重要的有机化工原料,其制造工艺主要有以下几种:
1. 低温合成工艺:在高温高压条件下,通过合成气(一氧化碳和氢气)经过甲醇合成反应生成甲醇。
该工艺使用催化剂催化反应,反应温度一般在200-300摄氏度,反应压力在10-100
兆帕之间。
这种工艺具有反应速度快、产量高的特点,广泛应用于大规模工业生产。
2. 二氧化碳催化还原工艺:利用二氧化碳与氢气催化还原反应生成甲醇。
该工艺有利于减少温室气体排放,可以利用二氧化碳资源,具有环保和可持续发展的特点。
3. 生物质气化工艺:利用生物质原料,通过气化反应产生合成气,再通过合成气转化反应生成甲醇。
该工艺可以利用农林废弃物等生物质资源,具有可再生性和环保性。
4. 其他工艺:包括通过煤炭气化、太阳能光电化学反应等制造甲醇的工艺。
这些工艺相对较新,仍处于研发和实验阶段。
甲醇工艺流程介绍

甲醇工艺流程介绍甲醇是一种重要的有机化工产品,广泛应用于化工、医药、农药、塑料、合成纤维等领域。
甲醇的生产工艺主要有四种,包括合成气法、天然气重整法、甲烷水蒸气重整法和木质素液化法。
本文将详细介绍甲醇的生产工艺流程。
一、合成气法合成气法是最常用的甲醇生产工艺,其主要原料是天然气或煤炭。
该工艺流程包括气化、合成气净化、气体转化、甲醇合成和甲醇精制等环节。
首先,将天然气或煤炭进行气化,生成合成气。
气化反应需要高温高压环境下进行,主要反应为C+H2O=CO+H2、气化产物中含有一定量的一氧化碳和氢气。
接下来,对合成气进行净化。
合成气中的杂质如硫化物、氨、氯化物等需要被去除,以保证后续反应的顺利进行。
净化工艺主要包括酸性气体的吸收、氢气和一氧化碳的选择性吸附等。
然后,将净化后的合成气进行转化。
转化主要是通过催化剂的作用,将一氧化碳和二氧化碳转化为甲醇。
转化反应的主要反应为CO+2H2=CH3OH。
该反应需要适宜的温度和压力条件,并且需要选择合适的催化剂。
最后,将合成气中生成的甲醇进行精制。
精制工艺主要包括蒸馏、吸附和冷凝等过程,以去除甲醇中的杂质,得到高纯度的甲醇产品。
二、天然气重整法天然气重整法是一种以天然气为原料生产甲醇的工艺。
该工艺流程包括重整、甲醇合成和甲醇精制等环节。
首先,将天然气进行重整反应,生成合成气。
重整反应主要是将天然气中的甲烷和水蒸气在催化剂的作用下进行反应,生成氢气和一氧化碳。
重整反应的主要反应为CH4+H2O=CO+3H2接下来,将重整反应生成的合成气进行甲醇合成。
甲醇合成反应的条件和催化剂与合成气法相似。
最后,对甲醇进行精制,得到高纯度的甲醇产品。
三、甲烷水蒸气重整法甲烷水蒸气重整法是一种以天然气为原料生产甲醇的工艺。
该工艺流程包括甲烷水蒸气重整、甲醇合成和甲醇精制等环节。
首先,将甲烷进行水蒸气重整反应,生成合成气。
重整反应的主要反应为CH4+H2O=CO+3H2接下来,将重整反应生成的合成气进行甲醇合成。
甲醇生产工艺与操作

甲醇生产工艺与操作甲醇(CH3OH)是一种无色、难燃的液体,是重要的工业原料和溶剂。
甲醇的生产工艺主要有合成气法、天然气法和余热法等。
下面简要介绍甲醇的生产工艺和操作。
1. 合成气法合成气法是目前甲醇生产中最常用的方法。
该方法是通过将天然气或煤转化为合成气(一氧化碳和氢气的混合物),再通过催化剂的作用,将合成气转化为甲醇。
合成气法的主要步骤包括气化、净化、合成、分离和净化等。
2. 天然气法天然气法是利用天然气作为原料生产甲醇的方法。
该方法在气化步骤中,直接利用天然气进行气化,生成合成气,然后经过合成、分离和净化等步骤得到甲醇。
天然气法相对于合成气法,减少了气化步骤,简化了工艺流程。
3. 余热法余热法是利用工业生产中产生的余热来生产甲醇的方法。
该方法在循环床和余热再利用等工艺条件下,通过将废气进行循环利用,使得废气中的有机物充分利用,生成合成气,再经过催化剂的作用转化为甲醇。
甲醇的生产操作包括原料准备、反应、分离、回收和净化等步骤。
1. 原料准备在甲醇生产过程中,对于不同的工艺,相应的原料也不同。
合成气法中,主要原料包括天然气和煤。
天然气法中,主要原料为天然气。
余热法则是利用工业生产中的余热进行甲醇生产。
2. 反应甲醇的合成反应主要通过催化剂的作用进行。
合成气与催化剂在适当的温度和压力条件下进行反应,生成甲醇。
3. 分离在反应后,需要对产物进行分离。
主要的分离操作包括冷凝分离和蒸馏分离。
通过降温,将甲醇从反应气体中分离出来。
4. 回收回收操作主要是对分离得到的甲醇进行回收利用。
通过蒸馏、过滤和再结晶等操作,将甲醇进行纯化。
5. 净化甲醇的净化操作主要是去除杂质。
通过吸附剂或催化剂的作用,去除甲醇中的杂质,提高甲醇的纯度。
总的来说,甲醇的生产工艺主要有合成气法、天然气法和余热法等方法,生产操作包括原料准备、反应、分离、回收和净化等步骤。
这些工艺和操作对于甲醇的生产具有重要意义,能够确保甲醇的质量和产量。
甲醇合成工艺
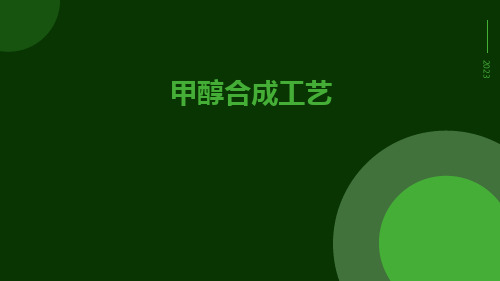
甲醇合成的催化剂与反应条件
甲醇合成的催化剂主要有铜基催化剂、锌基催化剂和铬基催化剂等。
在甲醇合成过程中,反应温度、压力、空速等是影响甲醇合成的重要因素。
铜基催化剂具有活性高、选择性好、稳定可靠等优点,因此应用最广泛。
在适当的温度和压力条件下,催化剂的活性可以得到充分发挥,有利于提高甲醇的产率和纯度。
河南煤业化工集团
该企业采用新型甲醇合成工艺,生产出高质量甲醇产品,并实现年产值数十亿元。
中国石化集团
该企业在燕山石化、上海石化等大型企业应用甲醇合成工艺,提高产品质量和降低能源消耗。
甲醇合成工艺在大型化工企业中的应用案例
风能甲醇合成气项目
*某公司利用风能发电,将风能转化为电能,再利用该电能生产甲醇合成气,实现新能源的综合利用。
2023
甲醇合成工艺
甲醇合成工艺简介甲醇合成工艺原理甲醇合成工艺流程甲醇合成工艺的环境影响与安全措施甲醇合成工艺的发展趋势与前景甲醇合成工艺的实际应用案例
contents
目录
01
甲醇合成工艺简介
1
甲醇的定义与性质
2
3
甲醇是一种有机化合物,其分子式为CH4O,结构简式为CH3OH。
甲醇是一种无色、透明、易燃的液体,具有刺激性气味,熔点为-97.8℃,沸点为64.5℃。
甲醇合成工艺的环保与可持续发展
资源高效利用
利用副产物和废弃物,实现循环经济。
循环经济发展
减少对环境的污染,实现绿色生产。
环境保护
05
甲醇合成工艺的发展趋势与前景
国内发展现状
我国甲醇合成工艺研究起步较晚,但发展迅速,目前已经成为全球最大的甲醇生产国和消费国,年产量超过全球总量的三分之一。
甲醇合成工艺流程

甲醇合成工艺流程
《甲醇合成工艺流程》
甲醇是一种重要的化工原料,广泛用于化工、医药、塑料等领域。
甲醇的合成工艺流程是一项复杂的化工过程,需要经过多道工序才能完成。
下面我们来简单介绍一下甲醇合成的工艺流程。
首先,甲醇的合成主要采用的是气相催化法。
该方法以一氧化碳和氢气为原料,经过催化剂的作用,进行一系列化学反应,最终产生甲醇。
整个工艺主要包括气体净化、气体混合、催化反应、产品分离等几个关键步骤。
气体净化是甲醇合成的第一步,主要是通过一系列的吸附、洗涤等操作,将原料气体中的杂质去除,确保进入催化反应器的气体是纯净的。
然后将经过净化的一氧化碳和氢气进行合并混合,按照一定的配比进入催化反应器中。
催化反应是甲醇合成的关键步骤,这一步需要催化剂的作用,将一氧化碳和氢气进行催化转化成甲醇。
催化反应器的设计和操作对反应效率和产物纯度有着重要的影响,需要进行精密控制。
最后,经过催化反应生成的混合气体中含有未反应的气体、甲醇和水等产物,需要进行产品分离。
通过冷凝、蒸馏、吸附等工艺,将甲醇从混合气体中分离出来,得到高纯度的甲醇产品。
以上就是甲醇合成的简要工艺流程,整个过程需要综合考虑原料质量、反应条件、催化剂选择等因素,才能获得高效、可靠的甲醇生产工艺。
随着化工技术的进步,甲醇合成工艺也在不断改进和完善,为甲醇产业的发展提供了更好的支持。
甲醇生产工艺 生产甲醇的工艺

甲醇生产工艺生产甲醇的工艺甲醇是一种重要的有机化学品,是一种无色、透明、易挥发的液体,具有较高的化学稳定性和燃烧性能。
甲醇是一种重要的化工原料,广泛应用于制造甲醛、甲酸、乙酸、氯化甲烷、甲基丙烯酸甲酯等化工产品。
此外,甲醇还是一种重要的能源原料,可以被用作汽油和柴油的替代品,可以被用作燃料电池的燃料等。
甲醇生产工艺是指甲醇从原料气体中分离出来的过程。
甲醇的生产工艺主要包括合成气制甲醇法、天然气制甲醇法、木质素制甲醇法等。
合成气制甲醇法是目前甲醇生产的主要工艺,其原理是将天然气、煤炭、石油等碳源通过气化反应,生成合成气,然后将合成气在催化剂的作用下转化为甲醇。
合成气制甲醇法的主要优点是原料来源广泛、成本低廉、生产效率高。
但是,该方法需要大量的能源和水资源,同时还会产生大量的二氧化碳和其他有害气体,对环境造成一定的污染。
天然气制甲醇法是一种比较新的甲醇生产工艺,其原理是将天然气直接转化为甲醇。
天然气制甲醇法的主要优点是原料来源广泛、成本低廉、生产效率高、环保性好。
但是,该方法需要特殊的催化剂和反应器,生产成本较高。
木质素制甲醇法是一种以木质素为原料制备甲醇的方法。
木质素是一种天然有机物,主要存在于木材、草木等植物的细胞壁中。
木质素制甲醇法的主要优点是可以利用废弃的木材和农作物秸秆等资源,减少环境污染和资源浪费。
但是,该方法的生产效率较低,需要特殊的催化剂和反应器,生产成本较高。
甲醇生产工艺的发展趋势是提高生产效率、降低成本、减少环境污染。
随着科技的不断进步和环保意识的不断增强,新型的甲醇生产工艺将逐渐取代传统生产工艺,成为未来甲醇生产的主流方法。
例如,光催化甲醇生产技术、生物甲醇生产技术等,都具有较高的生产效率和环保性。
总之,甲醇生产工艺是一个复杂的过程,需要综合考虑原料成本、生产效率、环保性等因素。
未来的甲醇生产工艺将更加环保、高效、经济。
甲醇合成的工艺流程和设备

甲醇合成的工艺流程和设备甲醇是一种重要的化工原料,广泛应用于化工、医药、食品等领域。
甲醇的合成工艺流程主要包括天然气制甲醇和煤制甲醇两种。
以下将以天然气制甲醇为例,介绍甲醇的合成工艺流程和设备。
1. 甲醇合成工艺流程甲醇的合成主要通过气相合成法进行,该方法通过一系列复杂的催化反应将一氧化碳和氢气合成甲醇。
具体的工艺流程如下:- 天然气→天然气净化→变化转换反应→合成气→合成气净化→合成气改质→甲醇合成→甲醇回收2. 甲醇合成设备甲醇合成设备主要包括催化反应器、冷凝器、分离塔等:- 催化反应器:将一氧化碳和氢气催化反应生成甲醇,需要具有较高的反应活性和选择性。
- 冷凝器:用于冷却和凝结合成气中的甲醇,使其形成液体甲醇。
- 分离塔:用于将液体甲醇从残余的气相中分离出来,保证甲醇的纯度和回收率。
3. 甲醇生产过程甲醇生产过程主要包括天然气的催化转变、合成气的制备、甲醇的合成和甲醇的回收等环节。
整个过程需要耗费大量的热能和电能,因此需要具备较为完备的能源设施和配套设备。
总的来说,甲醇的合成工艺流程较为复杂,需要涉及多个催化反应和分离过程,所需要的设备也比较繁杂。
企业在进行甲醇合成生产时,需要充分考虑到工艺流程和设备配置,确保生产过程的高效稳定。
甲醇是一种重要的化学品,其合成工艺的复杂性和对能源的依赖性使得甲醇工业在全球范围内备受关注。
天然气制甲醇是目前全球最为主流的甲醇生产工艺。
下面将详细介绍甲醇的合成工艺流程和设备,以及在甲醇生产过程中可能出现的关键技术和挑战。
4. 甲醇合成过程甲醇的合成工艺主要涉及以下几个过程:4.1 天然气制备合成气首先,天然气需要在天然气净化设备中进行净化处理,去除其中的硫化氢、二氧化碳和水等杂质。
通过石灰石和干燥剂的吸附、脱硫等处理,可使天然气达到合成气制备的要求。
然后,经催化转化反应,天然气中的甲烷和水蒸气进行高温反应,生成一氧化碳和氢气,形成合成气。
4.2 合成气的制备合成气是由一氧化碳和氢气所组成的气体混合物,它是甲醇合成的重要中间产物。
甲醇生产工艺技术

甲醇生产工艺技术甲醇生产工艺是提取甲醇的工序和流程,主要有合成法和干储法,合成法是甲醇生产的主要方法,合成的化学反应式为2H2+C0fCH3OH,干偶法最早是用木材干镭法生产甲醇,故甲醇也叫木醇。
一、国内外生产情况分析国外甲醇工艺技术,国外以天然气为原料生产的甲醇占92%,以煤为原料生产的甲醇2.3%,因此国外公司的甲醇技术均集中于天然气制甲醇。
国际上广泛采用的先进的甲醇生产工艺技术主要有:DAVY(原LC.I)、OPSOE、Uhde、LUrgi公司甲醇技术等,不同甲醇技术的消耗及能耗差异不大,其主要的差异在于所采用的主要设备甲醇合成塔的类型不同。
1.1DAVY甲醇技术特点DAVY低压甲醇合成技术的优势在于其性能优良的低压甲醇合成催化齐!L合成压力:5.0~IOMPa,大规模甲醇生产装置的合成压力为8~10MPa o合成塔型式有:第一种,激冷式合成塔,单塔生产能力大,出口甲醇浓度约为4~6%voI0第二种,内换热冷管式甲醇合成塔。
又开发了水管式合成塔。
精储多数采用二塔,有时也用三塔精僧,与蒸汽系统设置统一考虑。
蒸汽系统:分为高压10.5MPa、中压2.8MPa、低压0.45MPa 三级。
转化产生的废热与转化炉烟气废热,用于产生10.5MPa、510C高压过热蒸汽。
高压过热蒸汽用于驱动合成压缩机蒸汽透平,抽出中压蒸汽用作装置内使用。
1.2Lurgi甲醇技术Lurgi公司的合成有自己的特色,即有自己的合成塔专利。
其特点是合成塔为列管式,副产蒸汽,管内是Lurgi合成催化剂,管间是锅炉水,副产3.5〜4.OMPa的饱和中压蒸汽。
由于大规模装置如2000MTPD的合成塔直径太大,常采用两个合成塔并联。
若规模更大,则采用列管式合成塔后再串一个冷管式或热管式合成塔,同时还可采用两个系列的合成塔并联。
Lurgi工艺的精储采用三塔精储或三塔精储后再串一个回收塔。
有时也采用两塔精储。
三塔精储流程的预精镭塔和加压精谯塔的再沸器热源来自转化气的余热。
煤制甲醇的四个工艺过程

煤制甲醇的四个工艺过程煤制甲醇是指利用煤作为原料,通过化学反应将其转化为甲醇的过程。
煤是一种丰富的化石燃料资源,其主要成分是碳、氢、氧、氮和硫等元素。
煤制甲醇的工艺过程主要包括煤气化、气体净化、甲醇合成和甲醇精制四个步骤。
下面将详细介绍这四个工艺过程。
1. 煤气化煤气化是将煤在高温下进行化学反应,将其转化为气体燃料和化工原料的过程。
该过程主要通过两种方法进行:一种是氧气气化,即利用氧气在高温下与煤发生反应,产生合成气和焦炭;另一种是空气气化,即利用空气氧化煤,产生气化气和灰渣。
气化产物中的合成气是煤制甲醇的重要原料,它主要由一氧化碳、二氧化碳、氢气和甲烷等组成。
2. 气体净化气体净化是将煤气化产生的合成气进行净化处理,去除其中的杂质和有害物质的过程。
合成气中的杂质主要包括硫化物、氨、焦油、灰尘等。
这些杂质会对催化剂产生毒性影响,降低甲醇合成的效果。
因此,在甲醇合成之前,需要对合成气进行精细处理和净化。
这一过程主要通过吸附、洗涤、除尘和脱硫等方法进行。
3. 甲醇合成甲醇合成是将净化后的合成气进行化学反应,将一氧化碳和氢气转化为甲醇的过程。
该过程主要通过催化剂催化进行,常用的催化剂包括铜锌基和锌铬基等。
在反应过程中,一氧化碳和氢气在催化剂的作用下发生反应,生成甲醇。
甲醇是一种无色、可燃液体,可以作为燃料、溶剂和化学原料等。
甲醇合成反应具有一定的热力学和动力学特征,需要在适宜的温度、压力和催化剂条件下进行。
4. 甲醇精制甲醇精制是将合成甲醇进行分离和提纯的过程。
在甲醇合成反应中,会生成一些副反应产物和杂质,如二甲醚、水、硫化物等。
这些物质会对甲醇的质量和纯度产生影响,因此需要进行精制处理。
通常采用蒸馏、萃取、吸附、冷却等技术进行甲醇的分离和提纯。
通过这些工艺,可以使甲醇的纯度达到工业要求,并满足不同行业的使用需求。
总结起来,煤制甲醇的四个工艺过程包括煤气化、气体净化、甲醇合成和甲醇精制。
这些过程对于制备高质量的甲醇至关重要,可以充分利用煤资源,实现清洁能源的生产和利用。
甲醇的生产工艺

甲醇的生产工艺甲醇(化学式CH3OH),也称为木醇,是一种重要的化工原料。
甲醇广泛应用于合成其他有机化合物、制造溶剂、制备钾甲醇和其他甲醇盐,并且还可以作为清洗剂和燃料使用。
甲醇的生产工艺主要有两种,即天然气法和煤制甲醇法。
天然气法是指利用天然气为原料制造甲醇的工艺。
首先,将天然气经过清洗和脱硫处理,去除其中的杂质和硫化物。
然后,通过蒸汽重整反应将天然气转化为一氧化碳和氢气。
接下来,将一氧化碳和氢气经过水煤气化反应转化为合成气。
最后,利用合成气和催化剂进行甲醇合成反应,生成甲醇。
这种方法具有高转化率和产品纯度高的优点,但需要大量的能源和催化剂,加工过程复杂。
煤制甲醇法是指利用煤炭为原料制造甲醇的工艺。
煤炭经过气化和水煤气转化得到合成气,然后将合成气进行氨合成反应,生成尿素和一氧化碳。
接着,将一氧化碳和水进行加热反应,生成甲醛。
最后,将甲醛脱水反应得到甲醇。
这种方法可以直接利用煤炭资源,减少对天然气的依赖,是一种较为经济的方式。
但是,由于煤炭气化过程中产生的废气和废水对环境造成污染,因此需要采取相应的污染物净化措施。
除了以上两种主要的甲醇生产工艺,还有其他次要的生产工艺。
例如,生物质制甲醇法利用生物质作为原料,经过厌氧发酵、产甲烷反应和甲醛合成反应制备甲醇。
这种方法可以有效利用农作物秸秆和木材废料等资源,具有绿色环保的特点。
另外,二氧化碳电化学还原法和引燃碳酸盐法也可以用来制备甲醇,但需要较高的能源消耗。
总的来说,甲醇的生产工艺主要有天然气法和煤制甲醇法,分别利用天然气和煤炭作为原料,经过一系列化学反应合成甲醇。
此外,生物质制甲醇法、二氧化碳电化学还原法和引燃碳酸盐法也可以用于甲醇的生产。
随着科学技术的进步和环保意识的提高,未来甲醇的生产工艺可能会有更多革新和改进,以实现更高效、低耗和环保的生产方式。
甲醇合成工艺介绍

降低能耗的措施
能耗分析
对甲醇合成过程中的能耗进行详细分析,找出能耗高的环节。
节能设备与技术
采用高效换热器、回收余热等节能设备和技术,降低能耗。
能耗管理
建立能耗管理制度,加强能源利用监测与优化,提高能源利用效率。
环保与安全问题
废气、废水处理
对甲醇合成过程中产生的废气、废水进行妥善处理,防止 环境污染。
产物检测与纯化
合成得到的甲醇需要进行纯度检测和 提纯,以满足实验需求。
实验条件控制
实验室条件下,需严格控制反应温度、 压力、原料配比等参数,确保实验结 果的准确性。
生物质来源的甲醇合成工艺流程
生物质预处理
气化与合成
将生物质原料进行破碎、干燥、脱灰等预 处理,以去除杂质和提高原料的利用率。
生物质在高温条件下进行气化反应,生成合 成气(CO、H2),随后在催化剂的作用下 合成甲醇。
反应器优化设计
改进反应器设计,实现高效传热、传质和混合,降低能耗和物耗。
反应过程强化
采用微波、超声波等物理场强化技术,促进反应速率和产物分离效率。
绿色合成工艺的开发
低碳排放技术
开发低碳排放的合成工 艺,降低温室气体排放, 实现绿色可持续发展。
副产物回收利用
对合成过程中产生的副 产物进行回收利用,提 高资源利用率和经济效 益。
意识和环保措施的落实。
THANKS FOR WATCHING
感谢您的观看
精制后的甲醇可以作为产品进行储存和运输,以满足 市场需求。
03 甲醇合成工艺的优化与改 进
提高反应效率的方法
催化剂选择与优化
选用高效、稳定的催化剂,提高甲醇合成反应速率和选择性。
反应温度和压力控制
甲醇的化工生产技术概述

甲醇的化工生产技术概述引言甲醇,又称为“木醇”,是一种无色、易挥发液体。
它是一种重要的有机基础化工产品,广泛应用于能源、化工、制药和食品等领域。
本文将对甲醇的化工生产技术进行概述。
甲醇的制备方法甲醇的制备方法有多种,主要包括煤制甲醇、天然气制甲醇和生物质制甲醇等。
1. 煤制甲醇煤制甲醇是利用煤作为原料进行甲醇生产的技术。
该方法的主要步骤包括煤气化、气体净化、合成气的制备、甲醇合成等。
煤制甲醇具有资源广泛、化学品多样、产业链较长等优势。
2. 天然气制甲醇天然气制甲醇是利用天然气作为原料进行甲醇生产的技术。
该方法的主要步骤包括天然气蒸汽重整、合成气的制备、甲醇合成等。
天然气制甲醇具有资源丰富、生产成本低等优势。
3. 生物质制甲醇生物质制甲醇是利用生物质作为原料进行甲醇生产的技术。
该方法的主要步骤包括生物质预处理、糖化、发酵、甲醇合成等。
生物质制甲醇具有可再生性、减少温室气体排放等优势。
甲醇的生产工艺甲醇的生产工艺主要包括合成气的制备和甲醇的合成两个环节。
1. 合成气的制备合成气是甲醇合成的关键中间体,通常由一定比例的氢气和一氧化碳组成。
合成气的制备方法包括煤气化、重整、发酵等。
2. 甲醇的合成甲醇的合成主要通过合成气中的一氧化碳和氢气进行催化反应得到。
常用的甲醇合成催化剂有铜-锌基催化剂、改性催化剂等。
甲醇合成的工艺包括高温和低温两种,其中高温工艺常用于煤制甲醇,低温工艺常用于天然气制甲醇和生物质制甲醇。
甲醇的应用领域甲醇作为一种重要的有机化工产品,被广泛应用于能源、化工、制药和食品等领域。
1. 能源领域甲醇作为清洁燃料或替代燃料,被广泛应用于汽车燃料、燃料电池等能源领域。
2. 化工领域甲醇作为一种重要的化工原料,被用于合成甲醛、甲酸、甲丙腈、乙二醇等多种有机化工产品。
3. 制药领域甲醇作为溶剂或反应介质,被广泛应用于制药领域,用于制备抗生素、维生素、激素等药物。
4. 食品领域甲醇作为一种安全无毒的溶剂,被广泛应用于食品加工、食品保存等领域。
甲醇生产工艺流程

甲醇生产工艺流程
甲醇是一种重要的有机化工产品,在化工、医药、塑料、溶剂等领域有广泛应用。
本文将介绍甲醇的生产工艺流程。
甲醇的生产主要通过合成气(含一氧化碳和氢气)进行催化反应得到。
甲醇生产工艺可以分为四个主要步骤:原料准备、合成气制备、甲醇合成和甲醇提纯。
首先,原料准备阶段需要将天然气、煤或其他含有碳氢化合物的燃料转化为合成气的原料。
一般采用蒸汽重整或部分氧化等方法进行煤气化,得到一氧化碳和氢气的混合气体。
接下来,合成气制备阶段是将原料经过一系列净化、变压、变温等处理,以及催化剂的加入和调整,得到适合甲醇合成反应的合成气。
这个过程主要包括气体净化、合成气变压变温和催化剂的选择。
然后,甲醇合成阶段是将合成气通过催化剂床层进行催化反应,生成甲醇。
通常采用低温、高压下,气体通过催化剂床层,反应生成液相的甲醇。
这个过程是一个复杂的反应过程,需要考虑反应温度、压力、催化剂选择和反应时间等因素。
最后,甲醇提纯阶段是将反应产物中的甲醇从杂质中分离出来,提纯得到高纯度的甲醇产品。
这个过程主要包括脱水、脱碳等步骤,通过蒸馏、吸附等方法进行分离纯化。
提纯后的甲醇可以得到各种不同纯度的甲醇产品,用于不同领域的应用。
总的来说,甲醇的生产工艺流程包括原料准备、合成气制备、甲醇合成和甲醇提纯四个主要步骤。
其中的每个步骤都有具体的条件和操作要求,工艺设计需要充分考虑各种因素,以保证甲醇的高产、高纯度和高品质。
随着科技的不断进步,新的工艺流程和技术不断涌现,将进一步提高甲醇的生产效率和产品质量。
甲醇合成工艺介绍
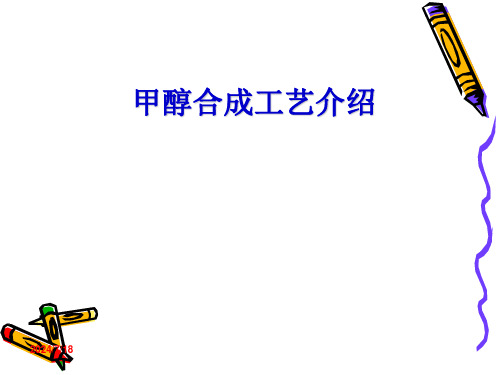
2024/7/18
第二章 液体燃料及其添加剂
11
➢中压法:
中压法是在低压法研究基础上进一步发展起来 的,由于低压法操作压力低,导致设备体积相当庞 大,不利于甲醇生产的大型化。因此发展了压力为 10MPa左右的甲醇中压合成法。它能更有效的降低 建厂费用和甲醇生产成本。中压法的操作压力范围 为一般为10~27MPa,温度为235~315℃。该法的关 键在于使用了一种新型铜基催化剂(Cu-Zn-Al), 综合利用指标要比低压法更好。
(2)气相合成甲醇法
气相合成甲醇的主要反应式为:
✓ CO+2H2=CH3OH(g)
△H= -90.8kJ/mol ①
✓ 当有CO2存在时,CO2按下列反应生成甲醇:
✓ CO2+H2=CO+H2O(g) △H= +41.3kJ/mol ②
✓ CO+2H2=CH3OH(g) △H= -90.8kJ/mol ③
➢ Lurgi管壳型甲醇合成反应器
– 结构特点:
• 形似列管式换热器,在塔内,列管中装填催 化剂,管间为沸腾水 ;
• 原料气与出塔气换热至230℃左右进入合成塔, 反应放出的热经管壁传给管间的沸腾水,产 生4MPa左右的饱和蒸汽,用来驱动透平压缩 机。合成塔全系统的温度条件用蒸汽压来控 制,从而保证催化剂床层大致为等温。
➢中压法合成甲醇工艺流程ห้องสมุดไป่ตู้
以上三种方法的流程基本相同。但 所使用的催化剂不同,因而操作压力和 操作温度等级不同,反应器的结构也就 有所不同。从合成反应理论上讲,提高 压力对合成反应有利,但在高活性铜基 催化剂研制成功后,降低合成压力就有 了可能。在较低压力和较低温度下合成 甲醇,可以降低对设备的要求,简化压 缩系统,节省动力消耗,可以节省投资 和降低生产成本。
甲醇合成的原理及工艺

一、甲醇合成原理1、化学反应合成甲醇的主要化学反应为CO和H2在多相铜基催化剂上的反应:CO+2H2⇋CH3OH(g)-90.8kJ/mol反应气体中含有CO2时,发生以下反应:CO2+3H2⇋CH3OH(g)+H2O-49.5kJ/mol同时CO2和H2发生CO的逆变换反应:CO2+H2⇋CO+H2O(g)+41.3kJ/mol反应过程中除生成甲醇外,还伴随一些副反应的发生,生成少量的烃、醇、醛、醚、酸和酯等化合物。
这些副反应的产物还可以进一步发生脱水、缩合、酰化或酮化等反应,生成烯烃、酯类、酮类等副产物。
当催化剂中含有碱类化合物时,这些化合物的生成更快。
副产物不仅消耗原料,而且影响甲醇的质量和催化剂的寿命。
尤其是生成甲烷的反应为一个强放热反应,不利于反应温度的操作控制,且甲烷不能随着产品冷凝,在循环系统中循环,更不利于主反应的化学平衡和反应速率。
2、甲醇合成反应的特点(1)放热反应甲醇合成是一个可逆放热反应,为了使反应过程能够向着有利于生成甲醇的方向进行,适应最佳温度曲线的要求,达到较好的产量,需及时移走热量。
(2)体积缩小反应从化学反应可以看出,无论是CO还是CO2分别与H2合成CH3OH,都是体积缩小的反应,因此压力增高,有利于反应向着生成CH3OH的方向进行。
(3)可逆反应即在CO、CO2和H2合成生成CH3OH的同时,甲醇也分解为CO2、CO和H2,合成反应的转化率与压力、温度和氢碳比ƒ=(H2-CO2)/(CO+CO2)有关。
(4)催化反应在有催化剂时,合成反应才能较快进行。
二、甲醇合成催化剂随着英国ICI公司铜‐锌‐铝催化剂的研制成功,甲醇生产进入了低温(220~280℃)、中低压(5~10MPa)时代。
近年来,低压铜基催化剂的使用逐渐普遍,各种新型甲醇催化剂层出不穷,无论活性、选择性、寿命等各方面均大大超过前代产品,从而推动甲醇生产实现了长周期、低能耗、低成本运行。
1、铜基催化剂(1)CuO‐ZnO‐Al2O3催化剂英国ICI公司开发的CuO‐ZnO‐Al2O3催化剂是比较有代表性的铜基催化剂。
甲醇合成工艺简析
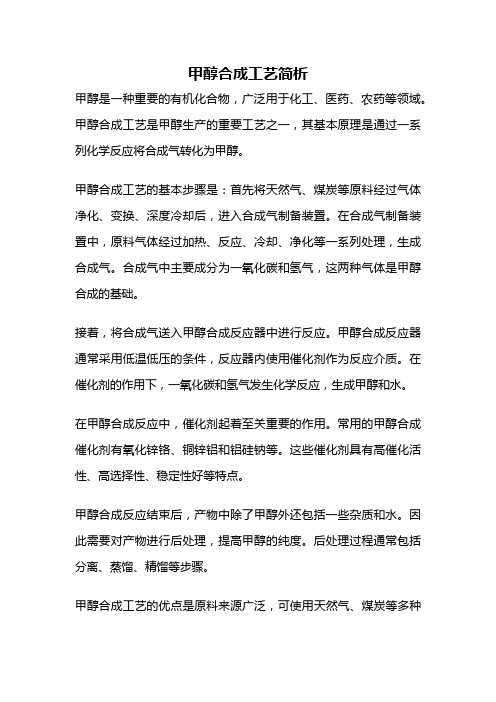
甲醇合成工艺简析
甲醇是一种重要的有机化合物,广泛用于化工、医药、农药等领域。
甲醇合成工艺是甲醇生产的重要工艺之一,其基本原理是通过一系列化学反应将合成气转化为甲醇。
甲醇合成工艺的基本步骤是:首先将天然气、煤炭等原料经过气体净化、变换、深度冷却后,进入合成气制备装置。
在合成气制备装置中,原料气体经过加热、反应、冷却、净化等一系列处理,生成合成气。
合成气中主要成分为一氧化碳和氢气,这两种气体是甲醇合成的基础。
接着,将合成气送入甲醇合成反应器中进行反应。
甲醇合成反应器通常采用低温低压的条件,反应器内使用催化剂作为反应介质。
在催化剂的作用下,一氧化碳和氢气发生化学反应,生成甲醇和水。
在甲醇合成反应中,催化剂起着至关重要的作用。
常用的甲醇合成催化剂有氧化锌铬、铜锌铝和铝硅钠等。
这些催化剂具有高催化活性、高选择性、稳定性好等特点。
甲醇合成反应结束后,产物中除了甲醇外还包括一些杂质和水。
因此需要对产物进行后处理,提高甲醇的纯度。
后处理过程通常包括分离、蒸馏、精馏等步骤。
甲醇合成工艺的优点是原料来源广泛,可使用天然气、煤炭等多种
资源进行生产,同时甲醇可以作为清洁能源的替代品,具有广泛的应用前景。
但是该工艺也存在一些问题,如催化剂的活性和稳定性需要进一步提高,后处理过程对能源消耗较大等。
甲醇合成工艺是一项重要的化工工艺,其合成原理和工艺流程相对简单,但对催化剂的选择和后处理过程要求较高。
未来,应该进一步加强研究,提高甲醇合成工艺的效率和环保性,促进其在清洁能源领域的应用。
甲醇生产工艺流程图

合成气为原料生产甲醇主要分为三种方式: 1 高压法
2 中压法
3 低压法
甲醇的生产方法介绍
1、高压法 用一氧化碳与氢在高温(340~420℃)
高压(30.0~50.0MPa)下用锌-铬氧化物作催化剂 合成甲醇。
2、低压法
一氧化碳与氢气为原料在低压(5.0MPa)和 275℃左右的温度下,采用铜基催化剂合成甲醇。低 压法成功的关键是采用了铜基催化剂,铜基催化剂 比锌-铬催化剂活性好得多,是甲醇合成反应能在较 低的压力和温度下进行。
甲醇合成反应器是甲醇生产的核心设备,从操作、结构
材料、及维修等方面考虑,甲醇反应器的基本要求如下:
1
、在操作上,要求催化剂床层的温度易控制,调
节灵活,合成反应的转化率高,催化剂的生产强度大,能以
较高能位回收反应热,床层中气体分布均匀,压降低。
2
、在结构上,要求简单紧凑,高压空间利用率高,
触媒装卸方便。
1 、温度高会影响催化剂的使用寿命。在温度高 的情况下,铜基催化剂晶格发生变化,催化剂 活性表面逐渐减少。如果温度超过280℃,催化 剂活性很快丧失。
2 、温度高会影响产品质量。反应温度高,在CO 加H2的反应中,副反应生产量增加,使 粗甲 醇中杂质增加,不但影响产品质量,而且增加 了H2的单耗。
选用合成压力一般为
4~6Mp。操作压力还受
400
350℃
催化剂活性、负荷高低、
空速大小、冷3 4 5 6 7 8 9 10 11 12
P/MPa
3、催化剂
在低压法甲醇合成工业中,催化剂的使用是至关重 要的。
铜基催化剂改进了甲醇合成塔结构,使得反应温度 能够严格控制,从而延长了铜基催化剂的使用寿命。 铜基催化剂的活性与铜含量有关
甲醇生产工艺

甲醇生产工艺
甲醇,也称为甲醇、甲醇、甲醇、甲醇,是常见的有机化工物质,具有特殊的化学性质、一定的工业应用价值,被广泛用于精细化工、农药、汽油、润滑油、染料、塑料以及食品等领域。
甲醇是一种天然的清洁能源,其是汽油的替代品,可以有效改善城市空气质量。
甲醇的生产工艺有多种方式,但是重点介绍的是高温法的生产工艺,它是利用空气中的氧分子作为氢氧形成水,由氢氧与烃类化合,温度高达1000℃,利用烯烃作为热源的反应气体,由反应气体再经过冷却、凝固成混合物,进而得到甲醇。
采用高温法生产甲醇,技术过程十分复杂,首先要精确控制反应温度,维持在900-1000℃;其次,需要在反应过程控制催化剂的添加,以增加转化率;第三,反应室中催化剂在使用后,应及时维护与更换,以保证反应质量。
甲醇的提纯工艺主要有蒸馏法和洗涤法,蒸馏法是利用甲醇的沸点比其他有机物低的特点来进行的,把原料中的其他物质蒸出,最后达到99.9%以上的纯度;洗涤法是通过用存在牢固结合的洗涤剂对甲醇进行洗涤,即可有效地去除甲醇中的杂质。
甲醇提纯后可以再通过液化、压缩等方式得到更高质量的甲醇,并封装成钢桶、液气罐等容器,以物流的方式运输到各个地方使用。
甲醇的生产工艺具有一定的复杂性,要进行多种技术试验,确保甲醇生产的质量,安全性和经济效益。
因此,甲醇生产是一项具有挑战的工作,只有在安全的基础上,以及在实施一定技术和方案的前提
下,才能够获得更好的甲醇生产效果。
总结而言,甲醇生产工艺是一个复杂的过程,从原料处理、反应到提纯和液化等步骤,都要求严格遵守技术要求,才能保证最终甲醇的质量,以及在经济上获得更多的效益。
- 1、下载文档前请自行甄别文档内容的完整性,平台不提供额外的编辑、内容补充、找答案等附加服务。
- 2、"仅部分预览"的文档,不可在线预览部分如存在完整性等问题,可反馈申请退款(可完整预览的文档不适用该条件!)。
- 3、如文档侵犯您的权益,请联系客服反馈,我们会尽快为您处理(人工客服工作时间:9:00-18:30)。
甲醇生产工艺介绍我自己的文献综述截下的一部分甲醇生产工艺介绍3.1联醇法产甲醇工艺介绍[4,15-21]合成氨的联醇工艺, 始于20 世纪60 年代并实现了工业化, 这是化肥工业史上的一次创举,它使化肥企业的产品结构突破了单一的局面, 节能降耗有了新发展, 还增强了企业的市场应变能力。
到20 世纪80~90 年代更是有了突飞猛进的发展, 联醇在全国遍地开花。
我国是一个“多煤少油”的国家, 甲醇开始向燃料市场倾斜, 这已经是个无法阻挡的趋势, 这就使合成氨工艺有了联醇后亦又有甲醇合成的联氨工艺的发展趋势。
随着甲醇市场的红火, 化肥行业不仅原有的联醇工艺不断完善, 增加产量, 还有不少企业在建设中。
在此新形势下, 现就联醇装置的设计、建设、施工、投产、运行、催化剂的使用等进行简单的介绍3.1.1联醇规模的确定联醇规模的确定, 也就是醇氨比( 实际上是醇与总氨的比例) 。
最经济的联醇规模, 在不增加脱碳能力或降低尿素产量, 把变换剩余的CO使之合成甲醇, 作为副产品, 这时醇氨比在10%~20%, 合成氨的经济效益最好。
但这样的比例形不成生产规模, 经不起市场变化。
当甲醇利润高, 而化肥利润率低迷时, 却无法提高甲醇产量。
因此考虑联醇规模时, 还应考虑甲醇的市场前景。
可过高的醇氨比又使造气煤耗增加, 增加脱碳的消耗和甲醇合成循环机的电耗等, 而成本上升, 影响合成氨的综合效益。
合成氨企业总体规模不大时, 一般醇氨比在40%~50%, 总体规模较大时醇氨比不超过40%。
对新建厂而言还考虑投资回报率, 醇氨比过高,不如搞联氨工艺了,即单醇联产合成氨。
3.1.2联醇合成工艺流程的选择合成氨的联醇之甲醇合成工艺, 老企业绝大部分是把甲醇合成设置在铜洗之前, 即压缩机五段或六段出口处。
新建厂用双甲工艺的, 也有把联醇放在与合成氨同一压力等级上, 即所谓等高压联醇。
其甲醇合成工艺流程是随该工艺的不断完善而目前有下列三种。
普遍的是合成塔内自设换热器, 无热量回收, 见图1压缩来的气体与循环气混合进入油分,分二路,主线进合成塔筒体与内件夹套后入下部换热器,副线直接入塔底进入中心管与换热后的气体混合后入内件的催化剂筐内。
而出塔的含有甲醇的气体直接进入水冷器,冷却后在醇分分离甲醇后一路去铜洗,另一路进循环机加压后再回到油分。
醇分分离的粗醇再进一步经精馏后作产品销售。
合成塔内自设换热器占据了高压空间, 使催化剂装填量减少, 另外由于主副线气量调节有限而使该流程进塔CO的高限值受制约, 而调节幅度降低, 为此出现了第二种流程, 设置塔外换热器。
见图2。
压缩来的气体与循环气混合进入油分, 主线经换热器提温后进合成塔筒体与内件夹套, 后进入内件中心管到催化剂筐, 副线可直接进内件中心管与主线气混合入催化剂筐, 出塔气进换热器后去水冷器、醇分。
此流程与前不同的是把内件里的换热器移到塔外, 使合成塔高压空间得到充分利用, 调节幅度比以前更大了。
但该流程中要注意的是塔出口温度超过200℃以上, 也就是合成塔出口到换热器进口及合成塔底部和换热器底部要接触超过200℃以上的气体, 其材质必需是耐热合金钢。
为此该流程大部分都是在合成塔内保留部分换热器, 使出塔温度不超过200℃而解决。
这样的流程与前流程无大的区别, 热量均未利用, 仅改变和增加了调节手段, 增加了甲醇产量。
现在为不少厂家所接受的流程是带有热量回收的流程。
见图3。
主线气进夹套后一出气到换热器, 提温度后作为二进气入塔, 进催化剂筐; 副线气可直接进塔或加到二进气上。
而合成出塔气进入废热锅炉或水加热器) , 回收热量产生蒸汽( 或加热全厂的锅炉用水) 后进换热器、后到水冷器、醇分。
在这个流程中当需提高甲醇产量时其反应热可得到回收, 还降低水冷器的负荷。
并能使调节更灵活, 得到的甲醇产量也最高。
但必须考虑气体温度200℃以上设备、管道材质问题。
但其废热锅炉和换热器外筒都可充分利用合成氨淘汰下来的设备。
3.1.3联醇中决定甲醇产量的因素在联醇中决定甲醇产量的是参加CO+2H2→CH3OH 化学反应CO 量, 从此反应式可看出,生产一吨甲醇需转化的CO 量为: 1 000÷32×322.4=700Nm/t也就是说合成塔确定后, 其催化剂装填量也是定值, 那么单位时间通过单位体积催化剂上的气体量即空速是第一因素。
对联醇而言, 此空速不能取得过高, 一般在8 000~10 000h 。
由于各种调节手段决定了入塔的气体中CO最高含量和催化剂活性而决定了出塔气体中CO含量。
一般出塔CO 在该空速下能达到0.5%以下, 而入塔气体中的CO由内件结构及工艺流程所决定,因此通气量一定后, 决定甲醇产量的是进塔CO含量及CO转化率。
也就是要提高产量就要设法提高进塔CO含量, 要提高催化剂活性, 提高CO转化率即降低出塔CO含量。
3.1.4进合成塔的CO含量的决定从前述看出, 合成塔内CO转化率不变, 则提高进塔CO含量就能增加产量。
以工艺流程和内件结构确定后, 空速一定, 在有限的调节手段内, 进塔最高CO含量也就到一极限值。
在联醇中通过计算热量平衡得出, 每转化1%的CO, 使反应气体的绝热温升29~30℃。
若出塔温度控制在270℃, 进入催化剂筐的气体温度是30℃的话, 则绝热温升可达240℃, 也就是此时反应的CO可达8%, 这种状态实际是不可能的。
出塔温度达270℃, 意味着在床层内的反应热点温度有可能超过300℃, 这是催化剂操作温度不允许的, 另外催化剂的活性温度的波幅较小( 220~290℃) , 进口不预热直接进筐, 使床层内能很快达到均温。
这样的内件目前还没有一家能做到。
还以均温型内件为例, 在流程1 中, 若以出床层温度240℃, 反应的CO百分比为3.5%, 其温度升为: 3.5%×30=105℃则进入催化剂筐的温度: 240- 105=135℃, 而流程2、3 中反应CO的百分比为5.5%, 温升为: 5.5×30=165℃则进催化剂筐温度要降到240- 165=75℃这使内件设计制作上增加了难度, 同时在操作中, 可能使床层的温差增大。
在生产中进塔的CO含量高低由循环量大小及进系统原料气中的CO含量高低来决定( 也即由原料气中的CO含量决定) 。
3.1.5联醇中循环机大小的选择工艺流程确定后应考虑选择循环机, 要考虑在正常生产中达到最高甲醇产量时所需要的循环量,对循环机选用时不仅考虑正常生产时所需,还考虑备机, 若在最大负荷时循环量是满负荷时该机故障, 若无备机将来不及处理而使催化剂烧毁失活。
另外还需考虑催化剂升温还原时所需。
3.1.6进入系统的气体的精制和除去有害物质硫及硫化物、氯及氯化物、羰基金属化合物、微量氨、油污等都是对Cu、Zn、AI 催化剂极其敏感, 容易中毒失活, 因此入系统前必需对原料气进行净化精制处理。
硫及硫化物对催化剂的毒害, 己为大家所共识, 现在联醇工艺中没有精脱硫装置的可能很少了, 但是不经过事先检测, 随意上一套精脱硫装置的还不少, 因此效果差达不到精脱要求, 短时间内穿透而使催化剂很快中毒的情况还是存在着。
一定要事先检测, 确定硫化物的形态和含量而设置对应的精脱装置, 才能保证投产进入系统的气体中总硫< 0.1×10 。
氯及氯化物的毒害是近几年才提到日程上的, 对Cu、Zn、AI 催化剂而言, 氯比硫的毒害更大, 含有0.1×10 的氯就会发生明显的中毒, 催化剂中0.01%~0.03%的吸氯量其活性就会大幅下降, 这是不可忽视的。
我认为在设置常温精脱硫装置时应留出按装脱氯剂的位置, 以彻底解决氯的毒害。
羰基金属化合物问题, 早几年就有人提出这问题, 也有了脱除方法。
但靠牺牲催化剂的容积,在其上部加装一点脱羰剂, 显然是不解决问题,在文献上有记载,“加压条件下即使在25~100℃下, 只要有CO, 就有羰基化合物生成的可能性。
CO 分压越高越有利于羰基金属化合物的生成。
150~200℃羰基腐蚀的速度最大, 若气体中有氯、硫时又会加速腐蚀。
”因此提出在催化剂床层上部加些脱羰剂或精脱硫装置上加脱氯剂同时加脱羰剂是不够的, 常温精脱硫装置一般设置在压缩机三段入口或脱碳以后, 而在甲醇合成塔前羰基金属化合物生成条件比三段入口生成几率要大得多, 为此建议在合成甲醇工艺中的油分后, 另增设一脱羰器, 根除这个毒物。
另外应在操作中减少CO在系统内生成羰基化合物的几率。
微量氨对催化剂的毒害, 有时在还原时已发生, 氨的带入将生成铜氨络合物, 还原时出水呈蓝色, 这已为很多实例所证实。
在生产过程中当原料气有微量氨时, 合成过程发生胺化反应,生成甲胺进入粗甲醇中, 使碱值高, 增加了精馏困难, 精甲醇中游离碱超标, 而增加了消耗, 且这类甲醇有特殊的鱼腥臭味, 降低其品级。
在甲醇合成过程中还会与催化剂中的铜生成铜氨络离子,造成铜的流失而失活。
原料气中的氨来源于合成氨的碳化工序, 丙碳脱碳串中压氨洗, 尿素联产碳铵工艺等。
使三段入口到甲醇合成系统进口带氨, 为此我们在合成工序的油分前加设除氨洗涤分离器装置, 目前有二种方法: 一是用洗涤塔加水喷淋, 连续加水、连续排放, 但由于水量很小, 而效果较差; 或保持一定液位气体鼓泡吸收, 间断加水、间断排放, 效果是时好时坏。
二是专用的高压**吸收装置,设在进口管线上, 高压水成雾状与气体充分混合接触而除氨, 到氨洗分离器里分离液体, 这样效果较好。
现在有个别厂就在油分前管道上用高压**装置, 把油分当成分离器, 液位控制不好时,气体夹带雾滴而造成催化剂中毒。
还有的取消高压机平衡段, 当活塞环损坏, 或缸套拉毛等情况而串气时, 也会使甲醇进口气中带氨。
油污的除净, 从实践看, 在工艺流程中有氨洗分离装置的油污影响不大, 因为进系统的气体实际经一次洗涤, 二次分离效果较好, 但若对循环机的维护保养不好, 造成循环机出口气体带油那这就成问题了, 但目前不少企业沿用的油分都是简单的分离内件, 分离效果很差。
油污对催化剂的污染早为大家所认识, 不仅润滑油本身有机硫含量较高, 而且油受热分解成炭黑, 堵塞催化剂的内孔隙, 使催化剂双重中毒。
应对油分效果差的分离器进行结构改造。
高效机械分离加超滤分离值得借鉴应用。
现在湖北化学研究院提出了新的ET—10 吸油剂和ET—6 脱氨剂, 可考虑应用。
但必须在塔前使用才有效。
3.1.7出系统甲醇的水洗回收由于水冷后在气体中还有一定的未冷凝的甲醇平衡蒸气分压, 如40℃时有0.28%甲醇蒸气, 30℃时0.17%甲醇蒸气, 再加上醇分分离效果差, 醇后气中夹带甲醇雾沫, 则损失相当可观。