压铸模设计程序及图例
压铸工艺流程图示资料

一、压铸(BODY)工艺流程图示1,压铸机调试2,压铸模安装4,模具预热、涂料7,合型(合模)10浇注压射11,保压12,开模、抽芯取件14,清理(整修)17,终检验3,压铸模设计与制造5,涂料配制6,模具清理8,合金熔炼保温9,嵌件准备13,表面质量检查15,时效处理16,铸件浸渗、喷丸处理二、压射压力P3 P4压力P2P1 P2P1T1 t2 t3 t4 保压时间升压充填增压注:t1 金属液在压室中未承受压力的时间;P1为一级(慢速)t2 金属液于压室中在压射冲头的作用下,通过内浇口充填型腔的时间;P2为二级(快速)t3 充填刚刚结束时的舜间;P3为三级(增压)t4 最终静压力;P4为补充压实铸件4P yP b=Лd2式中:P b 比压(Mpa); Py 机器的压射力(N);(压射力=压射缸直径×蓄压器压射时间最小压力)d 压室(冲头)直径(MM)选择比压考虑的的主要因素上海旭东压铸技术咨询培训资料压铸工艺参数比压因素选择条件高低壁厚薄壁厚壁压铸件结构形状复杂简单工艺性差些好些结晶温度范围大小压铸合金特性流动性差好密度大小比强度大小阻力大小浇注系统散热速度快慢公布合理不太合理排溢系统截面积大小内浇口速度快慢温度合金与压铸模具温度大小压铸各种合金常用比压表(Mpa)铸件壁厚≤3(mm) 铸件壁厚>3(mm)合金结构简单结构复杂结构简单结构复杂锌合金20-30 30-40 40-50 50-60 铝硅、铝铜合金25-35 35-45 45-60 60-70铝、镁合金30-40 40-50 50-65 65-75 镁合金30-40 40-50 50-65 65-80铜合金40-50 50-60 60-70 70-80 压力损失折算系数K直浇道导入口截面F1,K值与内浇铸口截面F2之比>1 =1 <1立式冷室压铸机0.66-0.70 0.72-0.74 0.76-0.78卧式冷室压铸机0.88压射速度浇注金属液量占压室容积百分数(%) 压射速度(cm/s)≤30 30-4030-60 20-30>60 10-20高压速度计算公式:VVh= ×[1+(n-1)×0.1]1/4Лd2T式中:Vh 高速压射速度(CM/S);V 型腔容积(CM3);N 型腔数;D 冲头直径(CM);T 适当的充填时间。
第12章压铸模设计实例与结构图例.
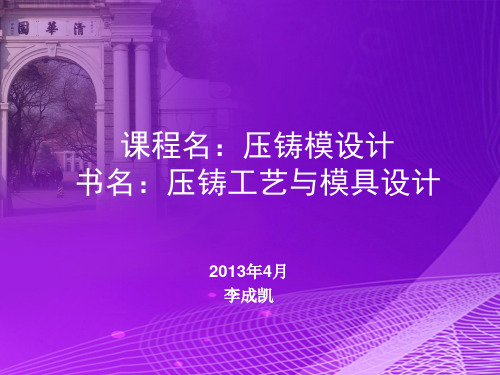
a)
b)
图3-1分型面
(2) 第二种方案如图b,分型面作在硅钢片铁芯的左边,大部分 型腔处于定模,开模时,压铸件不能理解随动一起移动,而要延时 ,由动模拉出定模,人工取出。 综上所述,结合电机转子的特殊性,选择第二种分型面的设计
方案较为合理。
(四)浇注系统设计 查表可知铝合金密度为2.7g/cm³ ,铝合金液态时密度为 2.4g/cm³ ;一般铝合金的充型速度在20~60m/s,壁厚为
(五)压铸机的预选 压铸机是压铸生产的专用设备,设计压铸模时必须熟悉压铸机的特性 和技术规范,通过必要的计算,选用合理压铸机,以发挥其最大的效益。 1.压射比压的确定 吊扇转子压铸件,压铸合金为纯铝,铸件平均厚度为6mm,且压铸件的 结构简单。依据有关资料铝合金的压射比压应该在40~60MPa,我们初步选 用50 Mpa。 2.压铸机锁模力的确定 锁模力的作用主要是为了克服充型时,型腔内产生的压力(涨型力) ,以锁紧模具的分型面,防止金属液飞溅,保证铸件的尺寸精度,涨型力 计算过程如下:
F涨=∑K·F主 =K(F铸+F浇+F余+F溢) F铸=πR² P=3.14×〔(0.175/2)2-(0.131/2) ² )×50Mpa =7.93×105N =793KN F浇=1×8×3×50Mpa =1.2KN F余=πR² p=3.14×(0.04/2)2×50 Mpa =62.8KN F涨=(F铸+F浇+F余+F溢)×P=857KN F涨—涨型力 F铸—铸件产生的涨型力 F浇—浇注系统产生的涨型力 F余—余料产生的涨型力 F溢—溢流槽产生的涨型力 锁模力计算如下:F≥K F涨=943KN;K—安全系数,取1.1 故锁模力大于或等于943KN的压铸机均可选用,因此,决定选用 国产J116D系列卧式冷压室压铸机
123536压铸模的设计之四-84页PPT资料
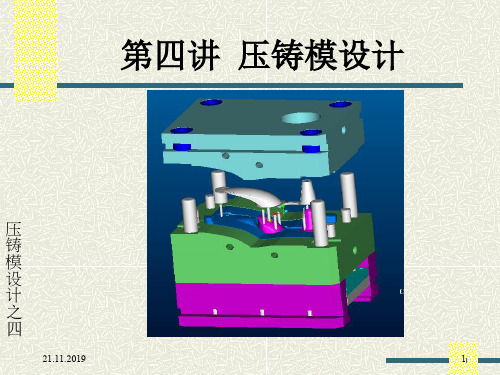
(2)平键
c)压块式
d)螺塞固定
(3)平面式
21.11.2019
e)螺柱联接
29
三.压铸模零部件设计
(三)成型零部件工作尺寸计算
1. 定义:成型零部件中直接决定压铸件几何形状的尺寸称为工作尺寸.
分为:型腔尺寸,型芯尺寸,中心距尺寸. 径向尺寸
型腔尺寸
包容尺寸,磨损变大
深度尺寸
压 铸 模
径向尺寸 型芯尺寸
F≥K(F1+F2)
压 铸 模 设 计
式中,F为压铸机应有的锁模力(kN);K为安全系数 (一般K-1.25);F1为主胀型力,即作用在分型面上的 投影面积(包括浇注系统、溢流排气系统的面积)的力 (kN),F2为分胀型力,作用在滑块楔紧块上的法向分力 所引起的胀型力之和(kN)
之
四
21.11.2019
第四讲 压铸模设计
压 铸 模 设 计 之 四
21.11.2019
1
一、压铸模的设计过程 一)设计前的基础性准备
研究产品对象
熟悉压铸机
压 铸
模具制造知识
模 设
现场压铸工艺知识
计
之
四
21.11.2019
2
二)压铸模设计的工艺准备
对零件图进行工艺性分析
对模具结构的初步分析
压
选定压铸机
铸 模
设 高度尺寸
计
之
四
被包容尺寸,磨损变小
21.11.2019
30
三.压铸模零部件设计
2.尺寸标注规定:
压铸件上的外形尺寸采用单向负偏差,基本尺寸为最 大值,与压铸件外形尺寸相应的模具上型腔类尺寸采 用单向正偏差,基本尺寸为最小值.
压铸模设计实例
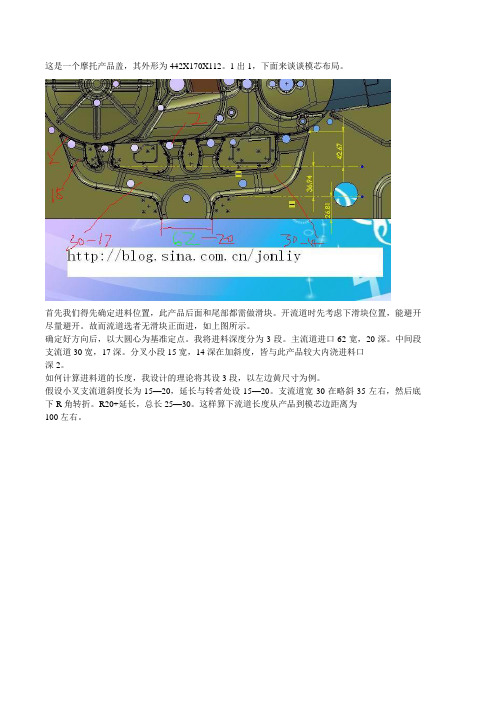
这是一个摩托产品盖,其外形为442X170X112。
1出1,下面来谈谈模芯布局。
首先我们得先确定进料位置,此产品后面和尾部都需做滑块。
开流道时先考虑下滑块位置,能避开尽量避开。
故而流道选者无滑块正面进,如上图所示。
确定好方向后,以大圆心为基准定点。
我将进料深度分为3段。
主流道进口62宽,20深。
中间段支流道30宽,17深。
分叉小段15宽,14深在加斜度,皆与此产品较大内浇进料口深2。
如何计算进料道的长度,我设计的理论将其设3段,以左边黄尺寸为例。
假设小叉支流道斜度长为15—20,延长与转者处设15—20。
支流道宽30在略斜35左右,然后底下R角转折。
R20+延长,总长25—30。
这样算下流道长度从产品到模芯边距离为100左右。
渣包尺寸为30宽以上,长40以上,距离足够的话。
深度13—15,出模度数8—10度,底下R3—5过度。
假设渣包宽35,进料边口为5,预设渣包后留25。
那么产品到模芯边为60余量。
如有滑块得根据抽出距离另行计算或者加宽余量边,祥见以下图所示。
对于有滑块面的余量放置,假设模内抽芯距离为70,那么后面的距离为70+余量,使之滑块滑出绝对距离后始终在模芯内,余量15—20最起码。
另外边也同样的道理,这样我们可以计算出模芯的大小,然后去小归整。
设计好大小后,然后来设计模芯的厚度。
厚度的设计准则以模芯最低出开始算余量50以上。
因为底下通10水管,水管位置离产品模芯底面下来20—25距离,底下留余量为25—30,然后以分型面为定点基准,凑整数。
绿色为水管,红色,蓝色为点冷却。
一般模芯不是很厚的,如果中间没有孔位,可以直通,或环绕试。
如果无法通水管,那就采取点冷却。
一般在型腔的镶快出,凸起出,热聚处。
其深度离腔体最深出低20—30左右。
滑块的设计,皆如此产品的滑芯不是很大。
宽度方面一般滑座比滑芯大5一边,然后凑整数。
滑块高度的设计,首先确定此滑块是用油泵。
如油泵接头最大处为32,那我设置尾座面比接头高4,底下留9,这样尾座高度为45。
压铸工艺流程图示

压铸(BODY)工艺流程图示i,压铸机调试2,压铸模安装呻3,压铸模设计与制造斗8,合金熔炼保温6,模具清理—7,合型(合模)9,嵌件准备12,开模、抽芯取件13,表面质量检查> 16,铸件浸渗、喷丸处理d压室(冲头)直径(MM )1、压射压力注:t1 ------ 金属液在压室中未承受压力的时间;P1为一级(慢速) t2 ----- 金属液于压室中在压射冲头的作用下, 通过内浇口充填型腔的时间;P2为二级(快速)t3 ------ 充填刚刚结束时的舜间; P3为三级(增压) t4 ------ 最终静压力;P4为补充压实铸件4P yP b =刃d 2式中:Pb ------ 比压(Mpa ) ; Py --------- 机器的压射力(N ); (压射力=压射缸直径x蓄压器压射时间最小压力)选择比压考虑的的主要因素艺参数压铸各种合金常用比压表( Mpa)压力损失折算系数K压射速度浇注金属液量占压室容积百分数 (%)压射速度(cm/s)< 30 30-40 30-60 20-30 >6010-20高压速度计算公式VVh= -----------2__1/4 刃 dTx [1+(n-1) x 0.1]压铸合金 铸件壁厚v 2.5MM铸件壁厚〉2,5〜6MM 锌合金 1〜2 3〜7 铝合金 1〜2 3〜8 镁合金 1〜2 3〜8 铜合金2〜35〜10式中:oCM/S);留模时间浇注温度②含铝的锌合金温度不宜超过不去450C,否则结晶粗大。
压铸模温度T m=3式中:Tm -------------------- 压铸模所需的工作温度(C);Th ------- 合金浇注温度(C);△ t ----- 温度控制公差(一般为25C)压铸涂料润滑剂,咼温粘附剂、咼温成膜剂、乳化剂、极压添加1,改善环境污染2,除润滑、脱膜作用外水基涂膜剂齐9、防腐杀菌剂、分散剂、可冷却压铸模,提高生产型腔和冲头润滑剂、抗氧剂率3,用喷枪喷涂4,便于自动化生产自配涂料。
123536压铸模的设计之四
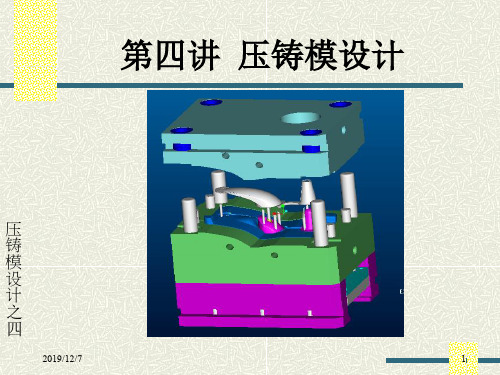
F≥K(F1+F2)
压 铸 模 设 计
式中,F为压铸机应有的锁模力(kN);K为安全系数 (一般K-1.25);F1为主胀型力,即作用在分型面上的 投影面积(包括浇注系统、溢流排气系统的面积)的力 (kN),F2为分胀型力,作用在滑块楔紧块上的法向分力 所引起的胀型力之和(kN)
之
四
2019/12/7
压 LM ------模具型腔的径向尺寸
铸 LZ ------压铸件的径向尺寸
模 X-------修正数,0.5~0.7
设 计
LM=[(1+K’)LZ-X△]
一般X=0.5+δZ
之
四
2019/12/7
34
三.压铸模零部件设计
b 型芯的径向尺寸:
LM= (1+K’) LZ+X△
0
LM=[(1+K’) LZ+X△]
2). 磨损后减小的成型中心边距
压 铸
(C’M
)±δZ/2=[(1+K’)C’Z+△/24]±δZ/2
模
设
计
之
四
2019/12/7
38
压铸机选用
压铸机分类:
1)卧式冷室压铸机
2)热室压铸机
压 3)特种压铸机
铸
模
设
计
之 四
撰稿: 杨军
2019/12/7
39
压 铸 模 设 计 之 四
2019/12/7
腔;开模时,动模与定模分开,借助于设在动模上的推出机构将铸件
设 推出.
计
之
四
2019/12/7
14
二. 压铸模的结构组成
二)压铸模结构根据作用分类
第三章 压铸模设计

4.导向零件的设计
(1)导柱和导套的设计要点 导柱应有足够刚度,在开合模时运动灵活,没有卡死现象。
(2)导柱、导套的尺寸和结构形式 在压铸模中,一般均设四根导柱。导向部分的直径可按下式经验公
式计算:
dK A
导柱和导套已经标准化,有A型和B型两种。
第三节 浇注系统和溢排系统的设 计
一.浇注系统的组成
(1)镶块的主要尺寸 1)镶块壁厚尺寸见教材表3-1; 2)整体镶块的台阶尺寸见表3-2; 3)组合形式成型镶块固定部分长度见表3-3。
(2)圆型芯的主要尺寸 见表3-4。
(3)影响铸件尺寸精度的因素 1)成型零件的制造误差; 2)压铸件的收缩率;
L模 L铸 100%
L模 3)成型零件的磨损; 4)模具结构及压铸工艺的影响。
(4)成型零件工作尺寸的计算
1)型腔尺寸计算
DM
2
D
2
D
2
% c
2
标注制造公差后得:DM D D% 0.70
同理型腔深度尺寸:HM H H% 0.70
2)型芯尺寸计算
dM
2
d
2
d
2
%
c
2
标注制造公差后得: dM d d% 0.70 同理型芯深度尺寸: hM h h% 0.70
F pb A
(2)动模支承板厚度推荐尺寸 见表3-7。
(3)动模支承板的加强结构
3.动、定模座板的设计
(1)定模座板的设计 定模座板与定模套板构成压铸模定模部分基体,安装在压铸机的固
定模板上。
(2)动模座板的设计
动模座板与垫块构成压铸模动模部分基体,安装在压铸机的活动模 板上,因此动模座板上也必须留出安装压板或紧固螺钉的位置。
压铸模设计
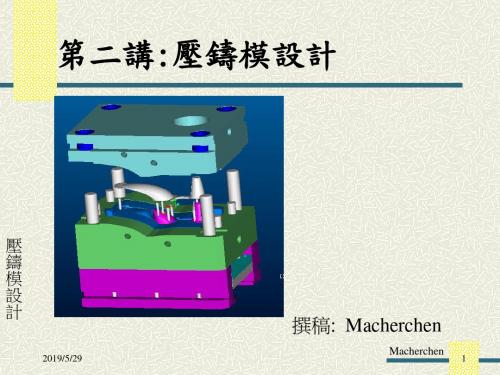
鑄 模 設
為基準,減去斜度值及加工余量,另一端按脫模斜度 相應增大.
計
2019/5/29
Macherchen
25
三.壓鑄模零部件設計
d 中心距尺寸:
CM=(1+K’) CZ (CM )±δZ/2 =[(1+K’) CZ] ±δZ/2
中心距尺寸在加工製造和磨損過程中不受影響及上下
壓
偏差對稱分布.
鑄
模
設
計
2019/5/29
Macherchen
26
三.壓鑄模零部件設計
e 成型中心邊距尺寸: 1). 磨損後增大的成型中心邊距
(C’M )±δZ/2 =[(1+K’) C’Z -△/24 ] ±δZ/2
2). 磨損後減小的成型中心邊距
壓
(C’M )±δZ/2 =[(1+K’) C’Z +△/24 ] ±δZ/2
壓 鑄 模 設 計
2019/5/29
Macherchen
13
三.壓鑄模零部件設計
(3)避免銳角的鑲拼
壓 鑄 模 設 計
2019/5/29
Macherchen
14
三.壓鑄模零部件設計
(4)防止熱處理變形的鑲拼
壓 鑄 (5)便於更換維修的鑲拼 模 設 計
2019/5/29
Macherchen
15
三.壓鑄模零部件設計
3)壓鑄件上和模具上的中心距尺寸均采用雙向等值正負偏差,它
壓
們的基本尺寸為平均值.
鑄
模
設
計
2019/5/29
Macherchen
20
三.壓鑄模零部件設計
3. 影響壓鑄件尺寸精度的因素:
压铸工艺及模具设计 压铸5-p82-2
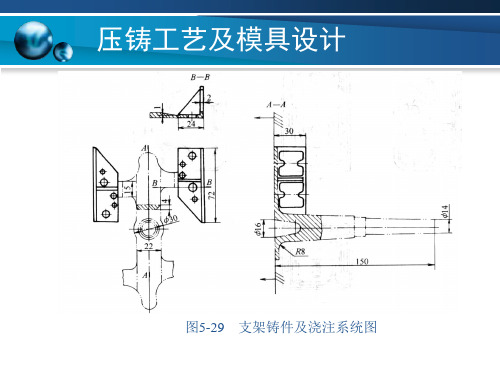
压铸工艺及模具设计
5.4.1 溢流槽设计
设置溢流槽除了作为接纳型腔中的气体、气体夹杂物 及冷污金属外,还可用作调节型腔局部温度、改善充填条 件以及必要时作为工艺搭子顶出铸件。
1. 溢流槽的设计要点 一般溢流槽设置在分型面上、 型腔内、防止金属倒流的位置。溢流槽的设计要点如图539所示。
(1) 设在金属流最初冲击的地方,以排除端部进入型 腔的冷凝金属流。容积比该冷凝金属流稍大一些(见图539a)。
图5-35 门锁铸件及浇注系统图
压铸工艺及模具设计
5.3.4 浇注系统设计举例分析 图5-36为凸缘外套的铸件图。该铸件为带有方法兰圆
筒,有铸出的外螺纹,壁厚为2~4mm。要求有较高的同轴 度和圆柱度,材料为ZL401铝锌合金。
图5-36 凸缘外套铸件图
根据凸缘外套的工艺特点,有五种浇注系统设计方案 (见图5-37)。
压铸工艺及模具设计
5.4.2 排气槽设计 排气槽是充型过程中型腔内受到排挤的气体得以逸出
的通道。设置排气槽的目的是为了能排除浇道、型腔及溢 流槽内的混合气体,以利于充填、减少和防止压铸件中气 孔缺陷的产生。
排气槽一般与溢流槽配合,布置在溢流槽后端以加强 溢流和排气效果。在某些情况下也可在型腔的必要部位单 独布置排气槽。排气槽不能被金属流堵塞,排气槽相互间 不应连通。排气槽的设计要点如下:
(1) 采用曲折的排气槽时,为了减少排气阻力,在转折处 宽度可取正常排气槽宽度的两倍。正常排气槽的长度不小于 15~25mm,见图5-42a。
压铸工艺及模具设计
(2) 直通的排气槽可做成阶梯状,加深到1.5δ,如
图5-42b所示,或制成带0°15′的斜度,如图5-42c所示, 或在分型面上的投影形状制成扩大的喇叭形状,如图542d所示。
UG压铸模具设计2

2.8 UG典型压铸件建模过程本节以如图2-104所示的滚轮、基座和衬套压铸件为例,详细讲解综合运用UG NX4.0建模功能创建压铸件的过程。
(1)滚轮压铸件(2)基座压铸件(3)衬套压铸件图2-104 典型压铸件2.8.1 滚轮压铸件建模过程(1)小直径圆柱体的创建按2.1.3操作,进入UG建模环境后,单击工具栏的圆柱体图标,在出现的【圆柱体】对话框中选【高度,直径】,在出现的【矢量构成】对话框中选择ZC为正方向,如图2-105所示。
单击确定,在出现的【圆柱】对话框中输入直径12.5、高20,如图2-106所示,单击确定完成圆柱体的创建。
此时,系统将构建如图2-107所示的圆柱体,其底面圆心位于坐标原点。
图2-105 矢量构成器图2-106 圆柱对话框图2-107 创建圆柱体素(2)大直径圆柱体的创建单击工具栏的圆柱体图标,在出现的【圆柱体】对话框中选【高度,直径】,在出现的【矢量构成】对话框中选择ZC为正方向,并单击确定。
在【圆柱】对话框中输入直径27.5、高15,并单击确定,如图2-108所示。
在【点构造器】输入ZC为2.5,如图2-109所示:图2-108 圆柱对话框图2-109 点构造器图2-110 创建圆柱体(3)实体求和运算选择菜单命令【插入】【联合体】【求和】或单击工具栏在的按钮,选择两个实体后,单击确定,完成的圆柱体创建,如图2-110所示;(4)草绘选择菜单对话框中的【草图】,系统将弹出如图2-111所示的【草图】对话框,选择xc-yc为绘图平面,单击确定进入草图界面。
图2-111 草图对话框绘制如图2-112所示的二维轮廓图,并单击【完成草图】按钮,返回实体编辑状态。
图2-112 绘制的草绘轮廓图图2-113 实体拉伸(5)拉伸移动光标选择上步所绘制的轮廓呈高亮显示,然后在【成型特征】工具条中单击【拉伸】,通过拉伸特征构建高为20的实体,如图2-113所示;(6)实体求差运算绕一点旋转变换复制的八个特征体后,选择菜单命令【插入】【联合体】【求差】或单击工具栏的按钮,选择旋转体为目标体,选择八个特征体为工具体,单击确定,完成零件创建,如图2-114所示:图2-114 实体模型(7)内孔圆柱体创建单击工具栏的圆柱体图标,在出现的【圆柱体】对话框中输入直径6,高25,如图2-115所示,单击确定;在出现的【矢量构成】对话框中选择ZC为正方向,单击确定;在【点构造器】中单击重置,如图2-116所示:图2-115 圆柱对话框图2-116 点构造器(8)实体求差运算选择菜单命令【插入】【联合体】【求差】或单击工具栏的按钮,选择已完成的圆柱体,单击确定,完成实体的创建,如图2-117所示:图2-117 实体模型 图2-118 倒圆角 (9)倒圆角 单击边倒圆图标,选择所要倒的圆角,输入圆角半径为1,确定完成倒圆角,如图2-118所示。
压铸模具设计标准-PPT

压铸模排位设计
压铸模具设计
压铸模胚中,夹模槽的标 准位25*25(mm),距离装
夹面为25mm。
压铸模排位设计
以模板背面为基准
压铸模具设计
压铸机的选择
根据模具大小合理选择压铸机
1. 模具不能与所选择压铸机格林 柱干涉
2. 模具在压铸机可夹持范围 3. 模具水路、油路接口规格数量
8. 镶件材料应与模仁的材质相同,有特殊要求的除外。圆形的镶件均用 SKD61真空热处理,其它零件材质也要明确。
9. 模具中的结构如滑块、斜梢,脱模行程应为产品的实际行程+2-5MM, 大滑块背面增加耐磨板,有多支斜梢时应保证能同时脱模。
10.有双托顶针或扁顶时应增加限位柱来控制行程,以防止顶出行程过大而 造成损坏,同时订购时尽量使用标准。
油槽
自润滑导套
压铸模具设计
13.压铸模具公、母模板之间的间 隙的设计。原则为0.4,但如 果产品的分型面有高低差比较 大的情况,可以视情况加大。
A板
0.40mm B板
压铸模模架的设计
压铸模具设计
压铸模胚中,吊环标准,吊 环大小依据模具重量来选择
压铸模模架的设计
锁模块标准
压铸模具设计
压铸模胚中锁模块的设计。每套模 具必须设计锁模快,大小按标准使 用
1. A取值一般为50---80MM,如有滑 块为100MM左右;
2. 成品尺寸〈150X150;C〈20MM, 则B取值一般为35---40MM,D取值 一般为40-50MM。
3. D取值一般为C+30---40MM。E取值 公模部分一般大于2D;母 模部 分一般略小于2D。
123536压铸模的设计之四-PPT文档资料

压 铸 模 设 计 之 四
動模
定模
動模
動模 定模 定模
2019/2/24
19
三.压铸模零部件设计
(二)按分型面的形状分类 1平直分型 2倾斜分型
3 阶梯分型 4曲面分型
压 铸 模 设 计 之 四
2019/2/24 20
三.压铸模零部件设计
注意事项(分型面选择的原则)﹕ 分型后压铸件能从模具型腔内取出来 开模后压铸件应留在动模上 分型面选择应保证压铸件的尺寸精度和表 面质量(产品的要求) 有利于浇注系统和排气系统的布置 应便于模具加工,模具加工工艺的可行性, 可靠性及方便性
利於加工
27
三.压铸模零部件设计
(2)小型芯的结构形式 a.小型芯要有起导流作用的圆角弧或倒角过渡,如图a)所示。通常 台阶c的大小为1-2mm,最小0.3mm。如果制成直通式﹐如图B) 所示﹐则金属易进入配合间隙﹐常期使用会侵蚀该处(图 中A处)﹐严重时影响脱模。 b. 如果型芯虽有台阶但制成清角而不是圆弧过渡﹐过小的型芯在热 处理时会产生应力集中而折断。
合模时,闭合构成型腔与浇铸系统,液体金属在高压下充满型 腔;开模时,动模与定模分开,借助于设在动模上的推出机构将铸件 推出.
2019/2/24
14
二. 压铸模的结构组成
二)压铸模结构根据作用分类
型腔:外表面 (一)成型零件 型芯:内表面 直浇道(浇口套)
压 铸 模 设 计 之 四
(二)浇注系统
模浇道(镶块) 内浇口 余料
压 铸 模 设 计 之 四
2019/2/24 9
压 铸 模 设 计 之 四
2019/2/24 10
压 铸 模 设 计 之 四
2019/2/24 11
2020年《金属压铸工艺与模具设计》第14章压铸模设计程序及图例参照模板

14.2 压铸模设计举例
图14.6 动模镶块
14.2 压铸模设计举例
技术条件:1. 材料:3Cr2W8V
2. 成型部分表面粗糙度Ra 0.8 µ m,其余未注明表面 粗糙度Ra1.6 µ m
3. 45~50HRC,试模后氮化,氮化深度0.08~0.15
mm,硬度Hv>600
4. 浇道处脱模斜度为3°,其余地方都为1°
14.2 压铸模设计举例
技术条件:1. 材料:45钢28~32HRC 2. 4~30 孔位置与定模套板一致
14.2 压铸模设计举例
图14.7 侧型芯(一)
14.2 压铸模设计举例
14.2 压铸模设计举例
14.2 压铸模设计举例
14.2 压铸模设计举例
14.2 压铸模设计举例
技术条件:1. 材料:45钢40~45HRC
2. 其余表面粗糙度Ra3.2 µ m
14.2 压铸模设计举例
图14.12 动模套板
14.1 压铸模设计程序
4.选择压铸机型号 根据压铸件的质量、压铸件在分型面上的投影面积计算所需的锁模力并结合压铸件生产单
位实际拥有的压铸机情况,初步选择压铸机(对压铸模与压铸机有关参数校核后,最后确 定压铸机型号)。 5.确定模具结构组成 在分型面与浇注系统、排溢系统确定后,需考虑以下几方面: (1) 确定成型零件的结构形式。如果是镶拼式,确定镶块、型芯的组合形式、固定形式。 (2) 根据侧孔、侧凹的形状特点,确定抽芯机构的结构形式、结构组成。 (3) 确定导向机构的形式、布置。 (4) 根据压铸件结构特点选择推出机构的类型;确定压铸件的推出部位及推出机构的复 位和导向形式。 (5) 决定温度调节系统的形式,初步考虑冷却通道的布置(有待于模具总装图中各机构 组成的位置、大小确定之后才能最后决定冷却通道的位置和大小尺寸)。 (6) 在考虑模具各机构组成时,要兼顾零件的加工性能。
压铸模设计第11章压铸模设计步骤及图例[补充new]
![压铸模设计第11章压铸模设计步骤及图例[补充new]](https://img.taocdn.com/s3/m/f3fededf7c1cfad6195fa745.png)
(2)校核压室容量
查手册,可知J116型压铸机,其压室直径为40mm时, 压室内铝合金浇入量为0.7kg。经计算(计算从略),压 铸件、浇注系统及排溢系统总重量小于0.7kg,故J116型 压铸机能满足要求。
据此,初步确定选用J116型卧式冷式压铸机.
第十一章 压铸模设计步骤及图例
• 由于压铸件的品种繁多,模具的结构特征和要求各不 相同,而且不同的设计者和加工单位也有各自的特点 和习惯,因此压铸模设计程序也会有些差异。不过,
基本的设计程序应该是相同的。
• §1 压铸模设计步骤 • §2 压铸模设计举例 • §3 压铸模结构图例
§1 压铸模设计步骤
• 压铸模设计步骤一般包括以下几个方面: 1.取得必要的资料和数据
设计前,设计者必须向模具用户取得如下资料和数据: (1) 压铸件的零件图。图中零件的尺寸、尺寸公差、形位
公差、表面粗糙度、材质、热处理要求以及其他技术要求 等应该齐全。 (2) 压铸件的生产数量及交货期限。 (3) 压铸件生产单位的设备情况(即压铸机的型号)。 (4) 模具加工单位的加工能力和设备条件。 (5) 用户的其他要求。
5.参数的计算与校核
模具结构形式确定后应对有关参数进行计算或校核。
1)成型零件成型尺寸计算。
成型零件尺寸分为:型腔径向尺寸、型芯径向尺寸、型
腔深度尺寸、型芯高度尺寸及中心距尺寸或位置尺寸。
按第7章的规定和图纸要求,零件尺寸公差为IT12级,这
些尺寸可用式7-5、6、7等计算。
零件最大外形尺寸为80mm,标上公差后为800-0.30mm,
§1 压铸模设计步骤
2.分析压铸件的结构、合金材料的性能及技术要求 (1) 分析压铸件的结构能否保证铸件质量及有利成型。如压铸件的壁厚是
- 1、下载文档前请自行甄别文档内容的完整性,平台不提供额外的编辑、内容补充、找答案等附加服务。
- 2、"仅部分预览"的文档,不可在线预览部分如存在完整性等问题,可反馈申请退款(可完整预览的文档不适用该条件!)。
- 3、如文档侵犯您的权益,请联系客服反馈,我们会尽快为您处理(人工客服工作时间:9:00-18:30)。
/webnew/
14.1 压铸模设计程序
6.选择模具零件材料及热处理工艺 7.绘制模具结构草图 绘制模具结构草图可以检查所考虑的结构相互间的协调关系。对经验不足的设计人员来说, 绘制模具结构草图可以检查所考虑的结构相互间的协调关系。对经验不足的设计人员来说, 以此草图征求模具制造和模具操作人员的意见,以便将他们丰富实践经验引入设计中。 以此草图征求模具制造和模具操作人员的意见,以便将他们丰富实践经验引入设计中。 8.参数的计算与校核 (1) 计算成型零件成型尺寸。 计算成型零件成型尺寸。 (2) 计算校核成型零件型腔侧壁与底板厚度,以决定模板的尺寸 亦可由图、表查得 。 计算校核成型零件型腔侧壁与底板厚度,以决定模板的尺寸(亦可由图 表查得)。 亦可由图、 (3) 计算抽芯力、抽芯距离、抽芯所需开模行程及斜导柱尺寸。 计算抽芯力、抽芯距离、抽芯所需开模行程及斜导柱尺寸。 (4) 推杆抗压失稳校核。 推杆抗压失稳校核。 (5) 压铸机有关参数的校核,如:锁模力、压室容量、开模行程及模具安装尺寸。 压铸机有关参数的校核, 锁模力、压室容量、开模行程及模具安装尺寸。 (6) 计算温度调节系统参数 亦可选用经验数据 。 计算温度调节系统参数(亦可选用经验数据 亦可选用经验数据)。
/webnew/
14.3 压铸模结构图例
前面各章介绍了压铸模的组成、各组成部分的作用及设计要点。 前面各章介绍了压铸模的组成、各组成部分的作用及设计要点。本节介绍几种压铸件的模 具结构,以供参考。 具结构,以供参考。 1.外壳压铸模(图14.13) 外壳是一壳体零件,材料为铝合金,最大外形尺寸170 mm×110 mm×70 mm,壁厚 外壳是一壳体零件,材料为铝合金,最大外形尺寸 × × , 大部分为2 大部分为 mm,六个圆柱体较粗大,与壳顶连接处易产生缩松。 ,六个圆柱体较粗大,与壳顶连接处易产生缩松。 选用立式冷压室压铸机,一模一件。平直分型面取在壳底,铸件全部在定模。采用顶浇口, 选用立式冷压室压铸机,一模一件。平直分型面取在壳底,铸件全部在定模。采用顶浇口, 铸件对型芯8包紧力大 故开模后铸件能跟随动模移动。溢流槽在四周共十个。 包紧力大, 铸件对型芯 包紧力大,故开模后铸件能跟随动模移动。溢流槽在四周共十个。 壳顶四角的四个盲孔由安装在定模上的型芯13成型 壳体内腔由动模上的型芯8成型 成型。 成型。 壳顶四角的四个盲孔由安装在定模上的型芯 成型。壳体内腔由动模上的型芯 成型。 该零件由推件板4及推杆 联合推出。限位螺杆18控制推件板推出距离 及推杆6联合推出 控制推件板推出距离。 该零件由推件板 及推杆 联合推出。限位螺杆 控制推件板推出距离。壳顶有一环状凹 使直浇口在开模时因该凹槽的作用而可靠地脱出定模。同时, 槽a,使直浇口在开模时因该凹槽的作用而可靠地脱出定模。同时,亦避免铸件薄壁顶面 产生变形。 产生变形。 2.支架压铸模(见图14.14) 此零件是一块曲折板状铝合金件,壁厚均匀为4~ 此零件是一块曲折板状铝合金件,壁厚均匀为 ~5 mm。 。 选用卧式冷压室压铸机,一模一件,侧浇口。分型面按铸件外形轮廓为阶梯分型, 选用卧式冷压室压铸机,一模一件,侧浇口。分型面按铸件外形轮廓为阶梯分型,以便金 属液充填的最后部位开设的溢流槽在分型面上。 属液充填的最后部位开设的溢流槽在分型面上。 采用推杆推出,推杆2、 设在溢流槽处 推杆26在浇口处 用复位杆3复位 设在溢流槽处, 在浇口处。 复位。 采用推杆推出,推杆 、10设在溢流槽处,推杆 在浇口处。用复位杆 复位。
14.2 压铸模设计举例
图14.6 动模镶块
/webnew/
Байду номын сангаас
14.2 压铸模设计举例
技术条件: 材料: 技术条件:1. 材料:3Cr2W8V 2. 成型部分表面粗糙度Ra 0.8 m,其余未注明表面 , 粗糙度Ra1.6 m 3. 45~50HRC,试模后氮化,氮化深度0.08~0.15 ~ ,试模后氮化,氮化深度 ~ mm,硬度Hv>600 , > 4. 浇道处脱模斜度为 °,其余地方都为 ° 浇道处脱模斜度为3° 其余地方都为1°
/webnew/
14.1 压铸模设计程序
4.选择压铸机型号 根据压铸件的质量、 根据压铸件的质量、压铸件在分型面上的投影面积计算所需的锁模力并结合压铸件生产单 位实际拥有的压铸机情况,初步选择压铸机(对压铸模与压铸机有关参数校核后 对压铸模与压铸机有关参数校核后, 位实际拥有的压铸机情况,初步选择压铸机 对压铸模与压铸机有关参数校核后,最后确 定压铸机型号)。 定压铸机型号 。 5.确定模具结构组成 在分型面与浇注系统、排溢系统确定后,需考虑以下几方面: 在分型面与浇注系统、排溢系统确定后,需考虑以下几方面: (1) 确定成型零件的结构形式。如果是镶拼式,确定镶块、型芯的组合形式、固定形式。 确定成型零件的结构形式。如果是镶拼式,确定镶块、型芯的组合形式、固定形式。 (2) 根据侧孔、侧凹的形状特点,确定抽芯机构的结构形式、结构组成。 根据侧孔、侧凹的形状特点,确定抽芯机构的结构形式、结构组成。 (3) 确定导向机构的形式、布置。 确定导向机构的形式、布置。 (4) 根据压铸件结构特点选择推出机构的类型;确定压铸件的推出部位及推出机构的复 根据压铸件结构特点选择推出机构的类型; 位和导向形式。 位和导向形式。 (5) 决定温度调节系统的形式,初步考虑冷却通道的布置 有待于模具总装图中各机构 决定温度调节系统的形式,初步考虑冷却通道的布置(有待于模具总装图中各机构 组成的位置、大小确定之后才能最后决定冷却通道的位置和大小尺寸)。 组成的位置、大小确定之后才能最后决定冷却通道的位置和大小尺寸 。 (6) 在考虑模具各机构组成时,要兼顾零件的加工性能。 在考虑模具各机构组成时,要兼顾零件的加工性能。
/webnew/
14.2 压铸模设计举例
/webnew/
14.2 压铸模设计举例
/webnew/
14.2 压铸模设计举例
/webnew/
第14章 压铸模设计程序及图例 14章
(时间:2次课,4学时)
/webnew/
第14章 压铸模设计程序及图例 14章
由于压铸件的品种繁多, 由于压铸件的品种繁多,模具的结构特征和要求各 不相同,而且不同的设计者和加工单位也有各自的 不相同, 特点和习惯,因此压铸模设计程序也会有些差异。 特点和习惯,因此压铸模设计程序也会有些差异。 不过,基本的设计程序应该是相同的。 不过,基本的设计程序应该是相同的。
/webnew/
14.1 压铸模设计程序
9.绘制压铸模装配图 压铸模装配图除需表明各零件之间的装配关系之外,还应注明: 压铸模装配图除需表明各零件之间的装配关系之外,还应注明: (1) 模具最大外形尺寸、安装尺寸; 模具最大外形尺寸、安装尺寸; (2) 选用的压铸机型号; 选用的压铸机型号; (3) 最小开模行程及推出机构推出行程; 最小开模行程及推出机构推出行程; (4) 铸件浇注系统及其主要尺寸; 铸件浇注系统及其主要尺寸; (5) 特殊机构动作过程; 特殊机构动作过程; (6) 模具零件的名称、数量、材料、规格; 模具零件的名称、数量、材料、规格; (7) 压铸模装配技术要求 参考 压铸模装配技术要求(参考 参考13.2节)。 节 。 10.绘制压铸模零件图 绘制压铸模零件图应从成型零件开始,再设计动定模套板、滑块、斜导柱等结构零件。 绘制压铸模零件图应从成型零件开始,再设计动定模套板、滑块、斜导柱等结构零件。模 具零件图应正确反映零件形状、标明零件尺寸、尺寸公差、形位公差、表面粗糙度、技术 具零件图应正确反映零件形状、 标明零件尺寸、尺寸公差、形位公差、表面粗糙度、 要求和材料热处理要求。 要求和材料热处理要求。
14.2 压铸模设计举例
/webnew/
14.2 压铸模设计举例
/webnew/
14.2 压铸模设计举例
/webnew/
14.2 压铸模设计举例
技术条件:1. 材料:3Cr2W8V 技术条件: 材料: 2. 成型部分表面粗糙度Ra 0.8 m,其余未注表面粗糙度Ra1.6 m , 3. 45~50HRC,试模后氮化,氮化深度 ~ ,试模后氮化,氮化深度0.08~0.15 mm,硬度Hv> ~ , > 600
/webnew/
/webnew/
14.1 压铸模设计程序
2.分析压铸件的结构、合金材料的性能及技术要求 (1) 分析压铸件的结构能否保证铸件质量及有利成型。如压铸件的壁厚是否均匀合理; 分析压铸件的结构能否保证铸件质量及有利成型。如压铸件的壁厚是否均匀合理; 壁的转角处是否有圆角;孔的直径和深度比例是否合适; 壁的转角处是否有圆角;孔的直径和深度比例是否合适;要求的尺寸精度和表面粗糙度是 否恰当;是否要另加脱模斜度;有没有嵌件等。 否恰当;是否要另加脱模斜度;有没有嵌件等。 (2) 分析压铸件合金材料对模具材料的要求及适用的压铸机。 分析压铸件合金材料对模具材料的要求及适用的压铸机。 对有不合理或不恰当的结构和要求,提出修改意见与用户商榷。产品设计、模具设计、 对有不合理或不恰当的结构和要求,提出修改意见与用户商榷。产品设计、模具设计、模 具制造与产品生产几方面很好的结合,才能得到质量完美的压铸件。 具制造与产品生产几方面很好的结合,才能得到质量完美的压铸件。 3.确定型腔数目,选择分型面及浇注系统、排溢系统 (1) 根据压铸机及压铸件生产批量初步确定压铸模的型腔数目。 根据压铸机及压铸件生产批量初步确定压铸模的型腔数目。 (2) 根据 根据7.4.2节所述分型面选择基本原则合理选择分型面的位置。 节所述分型面选择基本原则合理选择分型面的位置。 节所述分型面选择基本原则合理选择分型面的位置 (3) 根据铸件的结构特点,合理选择浇注系统类型及浇口位置,使铸件有最佳的成型条 根据铸件的结构特点,合理选择浇注系统类型及浇口位置, 件。 (4) 决定排溢系统的形式、位置。 决定排溢系统的形式、位置。
/webnew/
14.2 压铸模设计举例
/webnew/
14.2 压铸模设计举例