薄板坯连铸连轧(3)—邯钢CSP
CSP连铸辊套毛坯成型与热处理工艺研究
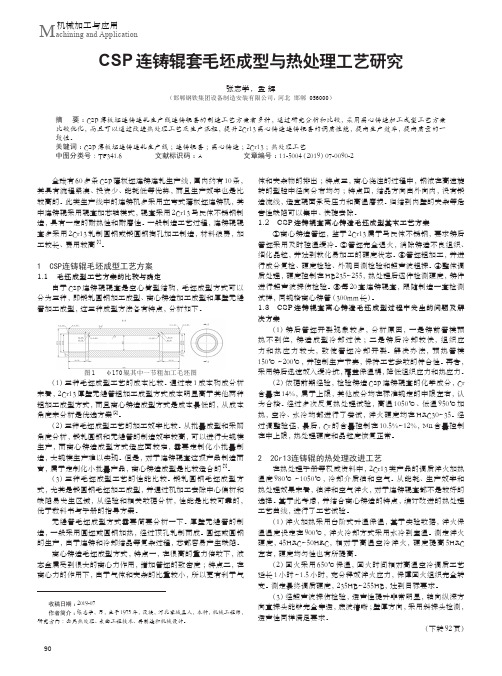
离心铸造毛坯成型方式,特点一,在很高的重力倍数下,液 态金属受到很大的离心力作用,增加管坯的致密度 ;特点二,在 离心力的作用下,由于气体和夹杂的比重较小,所以更有利于气
收稿日期 :2019-07 作者简介 :张志学,男,生于 1975 年,汉族,河北容城县人,本科,机械工程师, 研究方向 :金属热处理、表面工程技术、再制造和机械设计。
体和夹杂物的排出 ;特点三,离心浇注的过程中,钢液在高速旋 转的型腔中径向分布均匀 ;特点四,结晶方向由外向内,没有锻 造流线,适宜辊面承受压力和高温磨损。归结到内壁的夹杂等危 害性缺陷可以集中、快捷去除。 1.2 CSP 连铸辊套离心铸造毛坯成型基本工艺方案
(2)依据前期经验,检验铸造 CSP 连铸辊套的化学成分,Cr 含量在 14%,属于上限,其他成分均在标准规定的中限左右,认 为合格。经过多次反复热处理试验,高温 1050℃、低温 950℃加 热,空冷、水冷均都进行了尝试,淬火硬度均在 HRC30~35。经 过调整验证,最后,Cr 的含量控制在 10.5%~12%,Mn 含量控制 在中上限,热处理硬度和晶粒度恢复正常。
(1)淬火加热采用台阶式升温保温,基于实验数据,淬火保 温温度设定在 900℃,淬火冷却方式采用水冷到室温。测定淬火 硬度,45HRC~50HRC,相对于高温空冷淬火,硬度提高 5HRC 左右,硬度均匀性也有所提高。
(2)回火采用 650℃保温,回火时间相对高温空冷调质工艺 延长 1 小时 ~1.5 小时,充分释放淬火应力,保障回火组织完全转 变。测定最终调质硬度,235HB~255HB,达到目标要求。
邯钢薄板坯连铸连轧建设及工艺流程

邯钢薄板坯连铸连轧建设及工艺流程赵海峰1,陈维平2(1 邯郸钢铁集团公司设备制造分公司,河北邯郸056015;2 《河北冶金》杂志社,河北石家庄 050031)摘要:介绍了薄板坯连铸连轧生产工艺的特点及邯钢薄板坯连铸连轧生产工艺技术状况。
该生产线建设工期短、投资省、试产和达产速度快,月产已突破10万t,连铸漏钢率低,最小轧制规格为1.2mm,已生产15个钢种,取得了理想的经济效益。
关键词:薄板坯连铸连轧;CSP技术;工艺流程中图分类号:TF777 文献标识码:B文章编号:1004-4620(2002)05-0003-03Construction and Process Flow of Thin Slab Continuous Casting and Rolling at Handan Iron and Steel Group Co.ZHAO Hai-feng1,CHEN Wei-ping2(1 The Equipment Making Company of Handan Iron and Steel Group Co.,Handan 056015;2 Publishing House of Hebei Metallurgy,Shijiazhuang 050031,China)Abstract:Introduces the features of thin slab continuous casting and rolling and the general situation of CSP line at Hangang.The CSP line has short time limit for a project,low cost and low rate of breaking out,fast velocity of trial producing and producing,the output in one month is up to 0.1 million tons,the mini rolling specification is 1.2mm,and can produce 15 kinds of steel grades.It has got ideal economic benefit. Key words:thin slab continuous casting and rolling;CSP technique;process flow1前言自1989年8月德国西马克公司设计制造的世界第一条薄板坯连铸连轧生产线在美国纽柯的格拉福特斯维尔厂投产以来,世界上已有36条生产线相继投产,总生产能力达到4825万t/a。
邯钢CSP轧辊的使用问题及解决措施
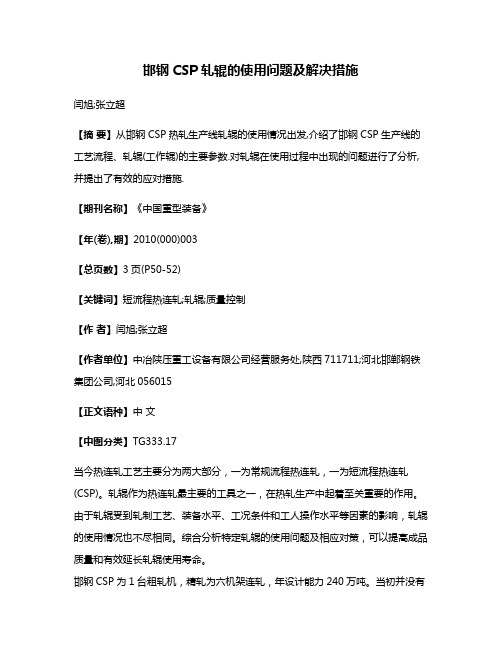
邯钢CSP轧辊的使用问题及解决措施闫旭;张立超【摘要】从邯钢CSP热轧生产线轧辊的使用情况出发,介绍了邯钢CSP生产线的工艺流程、轧辊(工作辊)的主要参数.对轧辊在使用过程中出现的问题进行了分析,并提出了有效的应对措施.【期刊名称】《中国重型装备》【年(卷),期】2010(000)003【总页数】3页(P50-52)【关键词】短流程热连轧;轧辊;质量控制【作者】闫旭;张立超【作者单位】中冶陕压重工设备有限公司经营服务处,陕西711711;河北邯郸钢铁集团公司,河北056015【正文语种】中文【中图分类】TG333.17当今热连轧工艺主要分为两大部分,一为常规流程热连轧,一为短流程热连轧(CSP)。
轧辊作为热连轧最主要的工具之一,在热轧生产中起着至关重要的作用。
由于轧辊受到轧制工艺、装备水平、工况条件和工人操作水平等因素的影响,轧辊的使用情况也不尽相同。
综合分析特定轧辊的使用问题及相应对策,可以提高成品质量和有效延长轧辊使用寿命。
邯钢CSP为1台粗轧机,精轧为六机架连轧,年设计能力240万吨。
当初并没有考虑为现在的冷轧提供原料,但随着邯钢冷轧的投产,每年需要CSP为冷轧提供130万吨原料,其余部分直接作为热轧商品卷销售。
由于冷轧对带钢的板形要求较高,故在轧辊的质量控制、磨削及使用维护方面提出了更高的要求。
本文主要对邯钢CSP工作辊在使用中出现的问题进行分析和研究,并提出相应的解决措施。
CSP的工艺流程为:薄板坯连铸→剪切→加热→除磷→粗轧→均热→剪切→除磷→精轧→层冷→卷取→取样→打捆→称重→喷号→入库。
2.1 工作辊的材质、硬度及主要尺寸在确定宽带钢工作辊材质与硬度时,需要综合考虑相关的轧制条件,其中包括精轧段机架的数量、轧辊的架次、带宽单位宽度上的轧制力、轧辊工作部位的最大预弯度、轧件温度以及辊面状况对产品表面质量的影响等。
这些要素决定了复合轧辊芯部和外层材质的选择。
邯钢CSP工作辊的材质、硬度及主要尺寸见表1。
薄板坯连铸连轧CSP生产低碳钢板的组织特征

第36卷 第6期2001年6月 钢 铁IR ON A N D ST EELV ol.36,N o.6June2001薄板坯连铸连轧CSP生产低碳钢板的组织特征*康永林 柳得橹 傅 杰 李 晶 于 浩 王元立(北京科技大学)王中丙 李烈军(广州珠江钢铁有限责任公司)摘 要 对珠钢CSP线生产的低碳钢(Z J400)连铸坯及轧后的组织特征观察和硬度测定表明:CSP线生产的连铸坯铸态组织为较细的树枝晶,枝晶宽度为几微米到30 m,靠近表面层的枝晶宽度与中心区域差别很小。
经第一道次50%变形后,板坯组织明显细化,具有局部“树枝晶”特征,“枝晶”宽度约5 m,中心区域硬度降低。
成品薄板的晶粒尺寸平均为5 m,大多呈尖角型。
变形区应力、应变及温度分布的有限元模拟分析结果与实际组织分析结果吻合。
关键词 薄板坯连铸连轧 低碳钢 显微组织 有限元分析MICROSTRUCTURAL CHARACTERISTICSOF LOW CARBON STEEL STRIP PRODUCEDBY C SP TECHNOLOGYKANG Yonglin LIU Delu FU Jie LI Jing YU Hao WANG Yuanli(U niversity of Science and Technolog y Beijing)WANG Zhongbing LI Liejun(Guang zhou Zhujiang Iron and Steel Co.,Ltd.)ABSTRACT The microstructural characteristics and hardness have been studied on the lo w carbo n steel(ZJ400)thin slab and strip produced by CSP technolog y at Zhujiang Steel.The uniform fine dendrites w ith a w idth less than30 m are observ ed in continuously cast slab.After r eductio n of50%,the structure is obviously r efined and has partial“dendr itic feature”w ith a w idth of about5 m.T he hardness in central area decreases.M icr ostructure o f the ZJ400strip is mainly acicular fer rite,the averag e grain size is abo ut5 m.The finite element simulatio n of the stress,strain and tem peratur e distribution in defor matio n zone has been carried o ut.T he simulation results are in go od agreem ent w ith the ex perim ents.KEY WORDS co mpact str ip productio n,low carbon steel,m icrostructur e,finite element analysis1 前言薄板坯连铸连轧是当今世界钢铁工业具有革命性的前沿技术,它集科学、技术和工程为一体,将热轧板卷的生产在一条短流程生产线上完成,充分显示其先进性和科学性。
邯钢CSP线供冷轧用SPHC/CQ级热SLN带性能免检探究

成本低 等 特点 ,主要生 产优 质低 S H / Q级热轧钢 带 ,主要经过 P CC
碳 钢 、管线 钢 、汽车结 构 钢、优 转 炉 初 炼 和 L F精 炼
质碳素 结构 钢和 花纹板 等 系列产 及C P S 连铸和六机架
广
广— 一
品。 同时 ,为充 分 发挥该 生产 线 连续 轧制 、表 面质 量
命 中 率 20 08年 为 9 . %,20 81 6 09
-
21 0 0年 C P生 产 S H / Q 级 S P CC
年 为 9 . %,2 1 为 9 .1 热 轧 钢带不 同厚度 的屈 服强度 进 为 原 料 生 产 的 s C / Q冷 轧 钢 89 8 0 0年 91%。 P CC 同时 ,钢水 成分 的过程 控制 能力 行 过 程 特性 值 分 析 可见 ,S HC 带 ,在 经 过 了冷 轧 工 序 的酸洗 一 P /
按 取 进 力 厂 ■ _ 批 样, 行 学 — — 厂
L—T— L — —
—Hale Waihona Puke L— — 一 供 尺 寸精 度高 、表面质 量优 、性 性 能 检 验 ,合 格 后 方
能稳定 的优 质原 料 。邯 钢冷 轧工
序 主要 工 艺为 酸洗 . 连 轧、全 冷
可 行至 轧 。 放 冷 工序 在 轧 序 酸 、 冷 工 经 洗 L
S、 自由 N 和适 度 降低 Mn含量 C i Q级热轧钢带屈服强度 的高低对 判定 准则 判 断 ,显示 其抗 拉强 度 及 适 度粗 化 晶粒 等措 施 ,实 现 了 其 冷 加工 成型 性能也 产 生较 大影 和 延 伸 率 的落 点符 合 控 制 要 求 , 对 S H / Q级冷轧供料钢水 的成 响。邯钢 现行 QHG 0 1 P CC / n 15内控标 表明其过程控制稳 定。 分 控 制 ,并 制定 了专 门的工 艺 控 准规定 ,S HCC P /Q级热轧钢 带屈
邯钢CSP过程控制系统安全架构的实现

能力 , 目前在 中高档服务器所采用 。如 H P公司的 Ap a P R S 、 l 和 A— I h C
IM 公 司的 Pw rP MIS公 司 的 MIS和 S N 公 司 的 S  ̄e B o e C、 P P U pr。
邯钢 C P过程控制 系统安全架构 的实现 S
刘建飞 王 鹏 刘延伟 河北钢铁 集团邯郸钢铁股份有限公 司连铸连 ̄ V 06 1 t t , 50 5
【 要】 摘 以河北钢铁集 团连铸连轧生产线过程控制 系统为例 , 对二级过程控制 系统的安 全冗余性能进行 分析, 详细介绍利用设备 冗余技术 、 于 基
1 言 前 邯钢薄板坯连铸连轧生产线( 简称 C P 是引进德 国西马克 9 S) O年代
世界先进技术 , 为我 国最早与珠钢 、 包钢 同期 引进了三条 C P生产线之 S
一
务器的运行 , 然后用一定的时间切换 至备用服务器 上面进行运行 , 才能
进行维修和恢复。 22 2 双机 热 备 ..
活 , 证应 用 在 短 时 间 内完 恢 复 正 常使 用 。 保 2 2 3单机 容 错 ..
情况下 , 过程控制系统的安全性就显 的非常必要及 迫切 。
2影 响 过 程控 制 系统 安全 的 因素
2 1服 务 器 的硬 件 架 构 .
单机容错技术则是在一 台服务 器实现高性 能容错的。它的容错能 力要远 比双机热备份中容错能力要 高。容 错服务器是通 过采用 同步技
的服 务器 操作 系统 主要有 : nosU i、iu Widw 、 n Lnx和 O V 。 x  ̄ MS
Wnos i w 操作系统 由于其最具人性化 的界 面, 且操作直观易 于使 d 并 用 , 目前最普及的操作系统 因此安全性也最差。随着 M c s t 是 io f r o 不断的
薄板坯连铸连轧(4)—包钢CSP
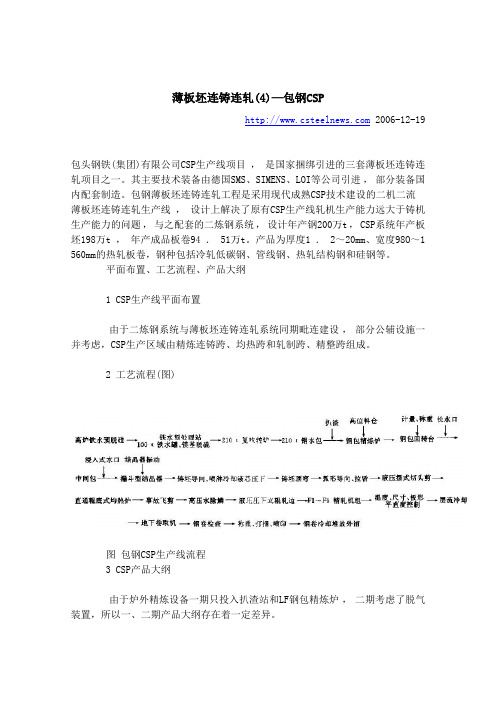
薄板坯连铸连轧(4)—包钢CSP 2006-12-19包头钢铁(集团)有限公司CSP生产线项目,是国家捆绑引进的三套薄板坯连铸连轧项目之一。
其主要技术装备由德国SMS、SIMENS、LOI等公司引进,部分装备国内配套制造。
包钢薄板坯连铸连轧工程是采用现代成熟CSP技术建设的二机二流薄板坯连铸连轧生产线,设计上解决了原有CSP生产线轧机生产能力远大于铸机生产能力的问题,与之配套的二炼钢系统,设计年产钢200万t,CSP系统年产板坯198万t,年产成品板卷94.51万t。
产品为厚度1.2~20mm、宽度98O~1 560mm的热轧板卷,钢种包括冷轧低碳钢、管线钢、热轧结构钢和硅钢等。
平面布置、工艺流程、产品大纲1 CSP生产线平面布置由于二炼钢系统与薄板坯连铸连轧系统同期毗连建设,部分公辅设施一并考虑,CSP生产区域由精炼连铸跨、均热跨和轧制跨、精整跨组成。
2 工艺流程(图)图包钢CSP生产线流程3 CSP产品大纲由于炉外精炼设备一期只投入扒渣站和LF钢包精炼炉,二期考虑了脱气装置,所以一、二期产品大纲存在着一定差异。
表1 一期产品大纲表2 二期产品大纲主要设备特点1 冶炼部分在转炉炼钢车间内布置一座210 t顶底复吹转炉,在精炼连铸跨内布置一座钢水扒渣站,一座200 t LF钢包精练炉以及两流薄板坏连铸机,分别预留了2号转炉和脱气装置的位置。
转炉采用首钢1997年购买的美国加州钢厂设备,具有顶底复吹工艺,装有副枪操作设备,可实现气动挡渣功能和溅渣护炉技术,冶炼过程可以实现动态计算机控制,抬炼和精炼部分配有专门的除尘装置,以保护环境。
两机两流的立弯式薄板坯连铸机由SMS公司提供,采用漏斗式结晶器,结晶器长度为1.1m;铸机冶金长度为7.14m,弯曲半径为3.25 m,采用了60t大容量双流中间罐。
结晶器可实现在线调宽和液面自动控制,浇铸过程还采用了保护浇铸、自动称量及液芯压下技术,通过流芯压下,可以把结晶器出口65 mm的铸坯厚度压至50 mm,以保证某些产品在质量方面的需求。
1.CSP连铸连轧的轧制工艺控制
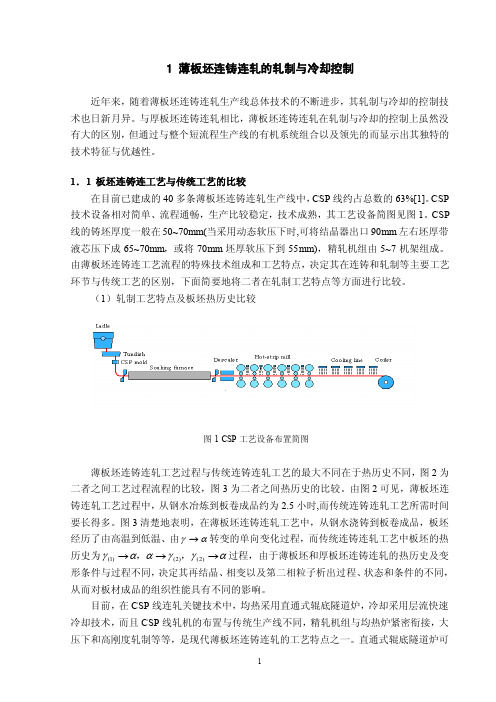
1 薄板坯连铸连轧的轧制与冷却控制近年来,随着薄板坯连铸连轧生产线总体技术的不断进步,其轧制与冷却的控制技术也日新月异。
与厚板坯连铸连轧相比,薄板坯连铸连轧在轧制与冷却的控制上虽然没有大的区别,但通过与整个短流程生产线的有机系统组合以及领先的而显示出其独特的技术特征与优越性。
1.1 板坯连铸连工艺与传统工艺的比较在目前已建成的40多条薄板坯连铸连轧生产线中,CSP 线约占总数的63%[1]。
CSP 技术设备相对简单、流程通畅,生产比较稳定,技术成熟,其工艺设备简图见图1。
CSP 线的铸坯厚度一般在50~70mm(当采用动态软压下时,可将结晶器出口90mm 左右坯厚带液芯压下成65~70mm ,或将70mm 坯厚软压下到55mm),精轧机组由5~7机架组成。
由薄板坯连铸连工艺流程的特殊技术组成和工艺特点,决定其在连铸和轧制等主要工艺环节与传统工艺的区别,下面简要地将二者在轧制工艺特点等方面进行比较。
(1)轧制工艺特点及板坯热历史比较薄板坯连铸连轧工艺过程与传统连铸连轧工艺的最大不同在于热历史不同,图2为二者之间工艺过程流程的比较,图3为二者之间热历史的比较。
由图2可见,薄板坯连铸连轧工艺过程中,从钢水冶炼到板卷成品约为2.5小时,而传统连铸连轧工艺所需时间要长得多。
图3清楚地表明,在薄板坯连铸连轧工艺中,从钢水浇铸到板卷成品,板坯经历了由高温到低温、由αγ→转变的单向变化过程,而传统连铸连轧工艺中板坯的热历史为αγγααγ→→→)2()2()1(,,过程,由于薄板坯和厚板坯连铸连轧的热历史及变形条件与过程不同,决定其再结晶、相变以及第二相粒子析出过程、状态和条件的不同,从而对板材成品的组织性能具有不同的影响。
目前,在CSP 线连轧关键技术中,均热采用直通式辊底隧道炉,冷却采用层流快速冷却技术,而且CSP 线轧机的布置与传统生产线不同,精轧机组与均热炉紧密衔接,大压下和高刚度轧制等等,是现代薄板坯连铸连轧的工艺特点之一。
邯钢CSP轧机主传动常见故障及处理措施
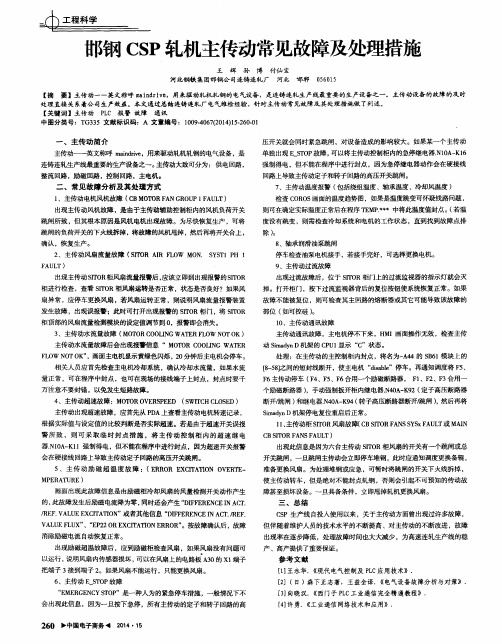
单独出现 E _ S T O P故障, 可以将主传动控制柜内的急停继电器. N I O A — K I 6
强制得电 , 但不 能在程序中进行 封点 ,因为急停继 电器动作会在硬接线 回路上导致主传动定子和转子回路的高压开关跳闸。
二、常见故障分析及其处理方式
1 、主传 动电机风机故障 ( C BM O T O RF A NG R O U P1 F A U L T ) 出现主传动风机故障 , 是 由于主传动辅助控 制柜 内的风机负荷 开关
相关 人员应 首先检查主电机冷却 系统 ,确认冷却水流量 ,如果水流 量正常 ,可在程 序中封点 ,也可在现场 的接线端子上封点 , 封点时要千
处理 :在主传动 的主控制柜 内封点 , 将名为一 A 4 4的 S B 6 1 模块上的 『 8 - 5 8 ] 之间的短封线断开 , 使主电机 “ d i s a b l e ”停车。再通知调度将 F 5 、 F 6 主传动停 车 ( F 4 、 F 5 、 F 6 合用一个励磁断路器 , F 1 、 F 2 、 F 3 合用一 个励磁断路器 ) ,手动强制扳开柜内继 电器. N 4 0 A - K 9 2( 定子高压 断路器 断开 b 闸) 和继电器. N 4 0 A — K 9 4 ( 转子高压断路器断开 & 闸) , 然后再将 S i m a d y n D机架停电复位重启后正 常。
跳闸所致 , 但其根本原因是风机 电机 出现故障。为尽快恢复生产 , 可将
7 、主传动温度报警 ( 包括绕组温度 、 轴承温度 、 冷却风温度 ) 检查 C O R O S 画面的温度趋势图,如果是温度跳变可怀疑线路问题 ,
则可在确定实际温度正常后在程序 T EM P . 中将此温度值封点。 ( 若温 度没有跳变 ,则需检查冷却系统和电机的工作状态 ,直到找到故 障点排
CSP生产线介绍

冷轧用带卷、一般结构和焊接结构用带卷、汽车结构用带卷、 高耐候结构用带卷以及 管线用带卷等
包钢CSP线产品规格主要集中在3.0mm以上,约占总产量的80%,厚度2.0mm已经能规模生 产。由于包钢CSP线建成时间较短,加上市场等原因,包钢在产品开发方面相对滞后, 钢种主要以普碳钢为主,少量的低合金钢,产品执行的标准主要是国标 GB700-1988、 GB/T699-1999和GB/T1591-1994。在其它钢种如管线钢、集装箱用板、汽车结构钢还处 于 研 发 阶 段 。 其 它 标 准 还 有 JIS G3141 ,API 5L,JIS G3131,GB 699 ,JIS G3101,GB 700,GB 1591,JIS G 3106,GB 4171,JIS G3113,JIS G 3112,GB 6653 ,JIS G2552;目前 包钢尚待开发。
一、概述
连轧培训_MWY
• 为达到较小的终轧厚度,CSP技术又发展出一种半无头 轧制的CSP设备方案。可实现奥氏体轧制和铁素体轧制。 这种半无头轧制的布置在后部还可以加上常规的卷取 机,使整条生产线具有轧各种不同钢种的功能,使生 产组织更加灵活,见图2[1]
一、概述
连轧培训_MWY
作半无头轧制的CSP方案
马鞍山钢铁股份有限公司
建筑用薄板技术改造项目
连轧培训_MWY
• CSP介绍
连轧培训_MWY
一、概述 二、马钢CSP 三、自动化系统
一、概述
连轧培训_MWY
•
现代热轧板带生产,除了继续提高产品的尺寸精度, 板形质量,表面质量、力学性能和加工工艺性能外, 朝着生产的自动化、连续化和高效化的方向发展。常 规热轧工艺在不断完善的同时,新技术新工艺不断出 现,其中流程短、投资少、效益高的新技术,如薄板 坯连铸连轧,有望成为主导热轧带钢生产的新流程。 在轧制工艺,轧机形式和控制技术方面也出现了一系 列新技术、新工艺、新设备。
CSP 连铸机降低漏钢率在邯钢的生产实践

CSP 连铸机降低漏钢率在邯钢的生产实践摘要:所谓漏钢是指浇铸过程中,铸坯坯壳凝固情况不好或者外力作用引起坯壳断裂导致内部钢水流出的现象。
漏钢事故发生的时间不同以及发生在铸坯上位置不同,可分为多种形式,包括:开浇漏钢、粘接漏钢、裂纹漏钢、卷渣漏钢等等。
漏钢事故发生的原因也各不相同,包括设备因素、工艺操作因素、钢水原因等等。
通过对每一起漏钢事故的原因分析,制定出了切实可行的防范措施。
关键词:保护渣;漏钢;措施一、比较国内连铸机的先进性(一)自动化程度高(1)连铸机设计年产能130万吨,投产初期班组定员10人/班,目前定员6~7人/班,远低于国内同产能连铸机班组定员。
(2)中包开浇只需要检查主控电脑上浇注条件具备后,在中间包操作箱上点“浇注”按钮,待中间包内钢水流入结晶器后就自动开浇。
开浇过程结晶器液位和拉速控制,结晶器油润滑全部由电脑自动控制,不需要人为操作和干预。
(3)切割和出坯系统全自动,出坯系统有冷床和热送两种模式,现场没有切割和出坯操作室,只有一个切割和出坯操作台。
铸坯自带“信号”,铸坯定尺长度使用编码器跟踪,到定尺后自动切割,切割完成后,切割输送辊道有铸坯“信号”自动转辊,当铸坯“信号”到达翻钢机自动翻钢,当满足移坯车推坯条件后,移坯车自动推坯到冷床或者热送台架,移坯车自动返回,冷床或者热送台架自动出坯。
(4)生产过程所有数据和设备动作全程可控。
一级ERP主要记录主要生产数据。
二级包括工程师数据站和操作数据站,所有生产数据和技术参数均可输入二级,二级自动控制生产过程。
三级终端数据分析站,生产过程所有数据指标和设备动作情况均可监控,特别是出现异常情况和事故后,可以直接查看终端数据分析站,快速、准确找出故障原因。
(二)一台连铸机可实现多种断面生产,降低投资成本;生产不同断面铸坯,轧钢产品多元化,提高经济效益(1)连铸机设计可生产铸坯断面100×100~180×180,现场配备可生产130×130和150×150两种断面铸坯。
钢铁厂CSP轧线F3轧机牌坊磨损后应如何修复

1.设备简介在CSP薄板坯连铸连轧生产过程中对板带成品率影响最大的就是板型控制技术,CSP轧区是控制带钢成型的重要区域,CSP轧区主要由F1—F7七架轧机、高压水除磷装置、AGC、CVC、活套组成。
其设备的好坏直接影响产品的成品率,一旦轧机牌坊开口尺寸超差势必会造成轧机运行状态难以控制、轧机机架刚度减弱,导致产品轧制质量下降,影响轧制精度及设备使用寿命。
CSP薄板坯连铸连轧生产轧区设备2.设备问题及原因分析某钢铁企业CSP薄板坯连铸连轧车间F3轧机出现轧机牌坊磨损问题,该轧线F3轧机牌坊与工作辊出口弯辊缸配合面、工作辊出口弯辊缸与衬板配合面共计4个配合面出现磨损腐蚀情况,磨损量约3mm。
由于轧机工况恶劣,在轧制时需用冷却水对轧辊进行冷却降温,轧机牌坊与衬板的配合间隙会导致轧辊冷却水会夹杂着轧件表面的氧化铁皮进入配合面进而加剧磨损,腐蚀是该轧机损坏的重要原因。
3.设备问题的修复工艺3.1传统修复模式的优势及可行性分析机械加工去除法。
即在线通过机加工方法清除牌坊表面受损层加工出配合面,通过加大底板厚度的方式来达到要求标高尺寸。
使用该方法修复后使用一段时间后又会出现磨损,还要再次进行机械加工。
多次机加工后对牌坊强度和刚度产生不利影响,该方法不能从根本上修复磨损。
需要补焊后在现场机加工,加工出结合面。
大面积堆焊容易造成牌坊受热应力变形、弯曲。
且修复好之后结合面和衬板在冲击、腐蚀作用下又会出现磨损。
也不能根本上解决磨损,且工期长。
消耗了企业大量人力、物力、财力。
激光熔覆。
与传统堆焊、喷涂、电镀相比,激光熔覆具有稀释度小、组织致密、涂层与基体结合好、适合熔覆材料多、粒度及含量变化大等特点,因此激光熔覆技术应用前景十分广阔,但是往往因为造价高,工期长等原因无法在短时间内完成修复。
传统检修所需的维修劳务费用、设备运输和机加工费用等综合费用较现场修复高,同时受现场空间的局限较大,但修复精度相对较高。
3.2现场修复模式的优势及可行性分析在不适用机加工环节的前提下,采用福世蓝高分子复合材料修复技术在现场进行修复。
3[1].4 薄板坯连铸连轧(3)
![3[1].4 薄板坯连铸连轧(3)](https://img.taocdn.com/s3/m/c00bc5c80975f46527d3e1c6.png)
3.薄板坯连铸连轧工艺理论与实践
[课后体会]
结合平面图讲解
结合漏斗型结晶器特点介绍优点
结合图形形象教学
采用比较法
用实例讲解
重点介绍主要设备
了解
解释为什么设置
结合平面图讲解
与CSP比较进行讲解
结合唐钢FTSRQ工艺技术讲解
指明除鳞点
采用图形讲解
举例
了解
三、典型的薄板坯连铸连轧工艺
[课堂小结]
通过本次课的学习,熟悉几种典型的薄板坯连铸连轧技术,掌握主要生产技术的工艺流程及设备特点。
[布置作业]
1.FTSRQ工艺技术有哪些特点
2.FTSRQ工艺技术中结晶器是什么形状?
3.什么叫液芯压下技术?有何优点?
4.叙述ISP工艺的技术特点。
5采用电磁闸技术的目的是什么?
[参考资料]
1.薄板坯连铸连轧-----冶金工业出版社
(3)热卷箱可提供9min的缓冲时间。并允许铸轧过程和精轧过程各以不同的速度同时进行,使精轧机以最佳的轧速度和温度完成轧制过程。
(4)热卷箱开卷后首尾倒换,板卷温度均匀,精轧机不用升速轧制,操作简化,厚度均匀。
3. FTSRQ工艺技术(意大利达涅利D anieli):1996~1997年投产。
Flexible Thin Slab Rolling for Quality---高质量的灵活性薄板坯轧制
四、薄板坯连铸连轧其它工艺技术
1.TSP工艺技术:美国蒂金斯公司开发的热轧带钢生产技术。
(Tippins Somsung Process)
特点:该工艺流程简化、紧凑,省掉了粗轧机,采用了传统的板坯连铸技术,用平行板型结晶器,生产100~250mm厚、宽900~2500mm的板坯均热后进炉卷轧机,生产1.5~2.0mm的热轧带卷。
CSP生产线摆式剪系统在邯钢连轧中的应用

CSP生产线摆式剪系统在邯钢连轧中的应用摘要:摆式剪位于连铸连轧生产线的拉矫机和加热炉之间,是连铸连轧生产线上的一个非常重要的设备,其主要作用有两个:①将连铸机生产出来的连续的铸坯切成轧机所需要的预先设定的长度;②当生产线发生故障时,将剩余铸坯碎断,从而将剩余铸坯清除出生产线或为发生故障的设备争取出抢修时间。
关键词:连铸连轧;摆式剪我们分两部分来介绍摆式剪系统:系统组成和控制原理。
1系统组成整个摆式剪控制系统由很多部分组成,是机械、电气、液压的综合体。
摆式剪本体主要由下列设备构成:摆式剪主电机(H01 MSL)、飞轮和抱闸/离合单元(U30)、减速箱(H01 BWL)、偏心轴、上下剪刃、摆框(H03)、压下辊(hold down roller)、水平辊(levelling roller)、入口辊(entry roll)、传送辊(transport roller)、出口辊(exit roller)。
除此以外,还有为摆式剪提供动力的主液压站、抱闸/离合液压站以及提供润滑的摆式剪稀油润滑系统。
下面我们来详细介绍各组成部分的作用:1.1摆式剪主电机和飞轮摆式剪主电机和飞轮为摆式剪的切割动作提供动力,正常情况下,电机带动飞轮恒速运转,切割时,靠飞轮积攒的惯性完成切割动作,减轻了切割动作对电机所造成的冲击。
由于电机功率很大,在电机主回路中安装了软启动器用来启动电机。
1.2抱闸/离合单元抱闸/离合单元位于飞轮和减速箱之间,用于使减速箱耦合到飞轮上或使二者脱离耦合并在抱闸作用下使减速箱减速直至停止。
1.3抱闸/离合液压站抱闸/离合液压站用于向抱闸/离合单元提供液压动力,控制抱闸/离合单元的动作。
当有液压压力提供给抱闸/离合单元时,抱闸就会打开,同时离合器耦合,使减速箱耦合到飞轮上;当没有液压压力提供给抱闸/离合单元时,离合器打开,使减速箱和飞轮脱离耦合,而抱闸在弹簧的作用下关闭,抱住减速箱使之减速直至停止。
液压压力的供给和切断是通过控制两个电磁阀而实现的。
CSP薄板坯连铸连轧厂实习报告

6.经轧制成型后的钢材进入水冷段进行层流冷却;
7.经过层流冷却后的钢材进入卷取机中卷取;
8.卷成卷筒状的钢材由天车运送入成品库中存放。
图1.2.邯钢CSP生产流程
与世界已建成的CSP线相比,这条生产线具有独特的工艺技术特点:
1)是世界上首条采用转炉钢水供应的CSP生产线;
2
邯钢CSP生产线是国内首批引进的薄板坯连铸连轧生产线之一,同时也是世界范围内第一家采用转炉工艺向CSP提供钢水的生产线。薄板坯连铸机是该生产线的主要组成部分,邯钢在对引进技术的消化、吸收的基础上,对工艺和设备不断地进行优化和创新,虽然投产已逾十年,但技术装备和功能应用依然保持了较好的状态,保证了薄板坯连铸机的各项技术指标长期处于国内外同类机型的先进水平,保证了整条生产线பைடு நூலகம்产能发挥和各项技术经济指标的稳步提高。
邯钢CSP连铸机采用漏斗型结晶器、铸坯薄、冷却强度大、拉速高,漏钢的几率相对其他板坯连铸机要大得多,邯钢CSP连铸机常见的漏钢形式有:开浇裹渣漏钢和悬挂漏钢,浇注过程中的粘结漏钢、裹渣漏钢、凹陷漏钢、纵裂漏钢、角裂漏钢。无论哪种形式的漏钢,其漏钢的机理都是指在连铸过程中,凝固坯壳出结晶器后,坯壳抵挡不住钢水静压力和拉坯力的作用,在坯壳薄弱处发生断裂而使钢水流出。
连铸连轧工艺现今只在轧制板材、带材中得到应用。
目前世界上的主流的连铸连轧生产线有德国西马克公司CSP(Compact Strip Production),意大利达涅利公司FTSC(Flexible Thin Slab Casting),奥钢联CONROLL。
图1.1德国西马克公司薄板厂连铸连轧CSP生产线
表1.1邯钢CSP产品应用及主要品种牌号
- 1、下载文档前请自行甄别文档内容的完整性,平台不提供额外的编辑、内容补充、找答案等附加服务。
- 2、"仅部分预览"的文档,不可在线预览部分如存在完整性等问题,可反馈申请退款(可完整预览的文档不适用该条件!)。
- 3、如文档侵犯您的权益,请联系客服反馈,我们会尽快为您处理(人工客服工作时间:9:00-18:30)。
薄板坯连铸连轧(3)—邯钢CSP 2006-12-19
邯钢薄板坯连铸连轧生产线于1997年11月18日开工建设,1999年12月10日生产出第一卷热轧卷板,建设工期历时两年零一个月。
该生产线引进德国西马克90年代世界先进技术,总生产能力为250万t。
生产线的特点
1 主要工艺特点
邯钢薄板坯连铸连轧生产线主要包括薄板坯连铸机、1号辊底式加热炉、粗轧机(R1)、2号辊底式加热炉、精轧机组(F1~F5)、带钢层流冷却系统和卷取机。
产品规格为1.2~20mm厚、900~1680mm宽的热轧带钢钢卷。
钢卷内径为762mm,外径为1100~2025mm,最大卷重为33.6t,最大单重为20kg/mm。
工艺流程为:100t氧气顶底复吹转炉钢水—LF钢水预处理—钢包—中间包—结晶器—二冷段—弯曲/拉矫—剪切—1号加热炉—除鳞—粗轧(R1)—2号加热炉—除鳞—精轧[F1~
F5(F6)]—冷却—卷取—出卷—取样—打捆—喷号—入库。
图邯钢CSP工艺流程示意图
2 主要技术参数
1)薄板坯连铸机
该连铸机为立弯式结构。
中间包容量36t,结晶器出口厚度70mm,结晶器长度1100mm,铸坯厚度60~80mm,铸坯宽度900~1680mm,坯流导向长度9325~
9705mm,铸速(坯厚70mm)低碳保证值最大4.8m/min、高碳保证值最大4.5m/min、最小2.8m/min,弯曲半径3250mm。
2)加热炉
该生产线包括两座辊底式加热炉,位于粗轧机前后。
1号加热炉炉长178.8m,由加热段、输送段、摆动段、保温段组成,炉子同时具有加热、均热、储存(缓冲)的功能,可容纳4块38m长的板坯,单机生产的缓冲时间20~30min,最高炉温1200℃,铸坯入炉温度870~1030℃,出炉温度1100~1150℃。
2号加热炉炉长66.8m,由一段构成,主要起均热、保温作用,最高炉温1150℃,铸坯最高入炉温度1120℃,最高出炉温度1130℃。
加热炉燃料为混合煤气,烧嘴型式为热风烧嘴。
3)粗轧机
粗轧机为单机架四辊不可逆式轧机,其作用是将铸坯一道轧成所需坯厚。
最大轧制力42000kN,工作辊尺寸880/790mm×1900mm,支撑辊尺寸1500/1350×1900mm,主电机功率8300kW,轧出坯厚33.0~52.5mm。
4)精轧机组
精轧机组有五架四辊不可逆式轧机(F1~F5),剪机为液压曲柄连杆式,除鳞为高压水除鳞,最大轧制力为4200kN,主电机功率均为8300kW,机架间距5500mm,F5最大出口速度12.6m/s,板带厚1.2~20mm,板带宽900~1680mm,终轧温度900~950℃。
5)冷却区
冷却方式为层流冷却,在一定时间内将带钢由终轧温度900~950℃冷却到550~650℃。
冷却区长度为43200mm,另有一个4800mm的空冷段。
最大水量约为
5240m3/h,水压为0.07MPa(喷淋区水压为1MPa)。
6)卷取机
卷取机为液压三辊卷板机,卷取温度一般在550~650℃,最大卷取速度15m/s,芯轴驱动电机功率为800kW,最大卷重33.6t。
3 工艺创新点
1)在国内首先采用了转炉供应钢水模式
邯钢结合华北地区电力资源和国内废钢资源情况,在有转炉炼钢的条件下,首先采用转炉为薄板坯连铸提供钢水的新模式,打破了当时已投产的CSP薄板坯连铸连轧生产线均采用电炉供应钢水的传统生产工艺。
为使转炉钢水质量满足薄板坯连铸的苛刻要求,邯钢对转炉炼钢和LF炉精炼工艺进行了数十次技术攻关。
转炉出钢时,实行挡渣出钢,使下渣量控制在3kg/t以下;开发了新型顶渣,在出钢过程中进行顶渣脱氧及改性;通过LF炉精炼,进一步脱氧、脱硫,攻克了喂铝钙线改变钢水中酸溶铝形态的技术难关等,最终使钢水温度、成分、流动性及钢水中[O]、[N]、[S]、[P]等有害元素和气体含量完全满足了CSP工艺对钢水质量的要求。
2)连铸结晶器出口厚度由50mm增加到70mm
世界上已投产的CSP薄板坯连铸结晶器的出口厚度均为50mm。
其存在的问题主要有:结晶器断面小,拉速快,不利于夹杂物上浮和保护渣熔化,铸坯易产生表面及内在缺陷;对于轧制厚规格产品,压缩比小,限制了品种范围的扩大;结晶器出口厚度小,连铸机单位时间内的通钢量相对较少,生产能力受到限制等。
为了有效解决这些问题,邯钢将结晶器出口厚度增加到了70mm。
实践表明,这一创新,在保持薄板坯连铸连轧先进技术特性的同时,使品种规格范围进一步扩大,产品质量明显改善,生产能力提高了23%,用较少的投入获得了较大的收益。
3)将传统的6连轧模式改为“1+5”轧制模式(即1架粗轧机加5架精轧机)
受卷取机穿带速度的影响,传统的6机架连轧模式不能满足铸坯厚度增加的要求。
为此,邯钢在世界上首次将6机架连轧改为单机架带立辊不可逆粗轧机加5机架连轧(1+5)模式,并在粗轧机前增加了一次除鳞装置。
这一生产工艺的创新在实践中取得了显著效果:生产组织更加灵活;精轧机组入口带坯厚度减薄,提高了入口速度,改善了第一架精轧机(F1)的工作条件;改善了板带边部组织结构及板带表面质量。
该生产工艺于2001年申报了国家发明专利。
4)对2号均热炉设计进行完善和创新
由于带坯未完全离开粗轧机前已经进入2号均热炉,易发生轧件冲撞炉墙事故。
为解决这一问题,邯钢对传统均热炉的设计进行了完善和创新。
主要包括:设计可倾动炉顶、加宽炉膛、增加摄象机监控系统和事故处理装置等。
该炉型结构于2001年申报了国家实用新型专利。
5)开发了连铸动态二次冷却模型
由于CSP薄板坯连铸机原二次冷却模型采用比水量控制法,仅根据拉速一个参数来调节喷淋水量,对铸坯表面温度控制的效果不佳,达不到最优的质量控制。
为此,邯钢开发了以钢种、铸坯几何尺寸、拉速、结晶器水温、中间包钢水温度、顶弯辊后铸坯表面温度等为入口参数,以铸坯表面温度的最优控制为目标的专家模型系统,实现了动态调节喷淋水量,有效地控制了铸坯的表面温度,进而有效控制了铸坯液芯长度。
动态模型采用后,铸坯出顶弯辊后的温度波动降低了25%,表面及内部裂纹由1.02%降到了0.50%以下。
6)开发了板坯收缩率在线修正程序
原CSP薄板坯连铸连轧依据固定的铸坯收缩率设定结晶器宽度,带钢超宽比例较大。
为此,邯钢开发了板坯收缩率在线修正程序,采用优化的遗传算法,综合考虑钢种、成品厚度、板坯宽度等因素,挖掘大量历史数据,以确定最优的板坯收缩率,再按照实测产品的宽度,在线调整结晶器宽度和锥度,有效地降低了带钢宽度超限比例,减少了堆钢事故。
宽度超限比例由0.94%降到0.2%以下。
炼钢配置和生产钢种情况
100t氧气顶底复吹转炉3座,120tLF精炼炉3座。
邯钢薄板坯连铸连轧生产线投产以来,配合设备功能调试和结合市场需求,生产了十多个钢种及多个规格的热轧卷板。
具体情况见表1。
表1 钢种及规格
邯钢薄板坯连铸连轧工艺优化和创新,相当程度上完善并发展了薄板坯连铸连轧技术,在随后建设的几条生产线中均不同程度的借鉴了邯钢经验。
针对薄板坯连铸连轧生产线(一期)生产实践中存在的问题,结合当今世界薄板坯连铸连轧技术发展的方向,邯钢在续建工程中又采用了以下新技术:连铸结晶器出口厚度由70mm增加到90mm;增加了结晶器电磁制动;扇形段采用了新的动态液芯压下技术;结晶器液面控制增加了涡流检测方式;两线连铸生产时,均热炉采用摆动过钢方式,实现向轧机供坯的工艺衔接;精轧机组增加F6机架,产品最小厚度由原来的1.2mm 降至1.0mm;精轧机组采用CVCPLUS技术;精轧机组采用辊缝润滑技术;在精轧机出口处设置了压带风机等。