第一章 精密和超精密加工技术及发展展望要点
超精密加工与超高速加工技术

超精密加工与超高速加工技术第一篇:超精密加工与超高速加工技术超精密加工与超高速加工技术一、技术概述超高速加工技术是指采用超硬材料的刃具,通过极大地提高切削速度和进给速度来提高材料切除率、加工精度和加工质量的现代加工技术。
超高速加工的切削速度范围因不同的工件材料、不同的切削方式而异。
目前,一般认为,超高速切削各种材料的切速范围为:铝合金已超过1600m/min,铸铁为1500m/min,超耐热镍合金达300m/min,钛合金达150-1000m/min,纤维增强塑料为2000-9000m/min。
各种切削工艺的切速范围为:车削700-7000m/min,铣削300-6000m/min,钻削200-1100m/min,磨削250m/s以上等等。
超高速加工技术主要包括:超高速切削与磨削机理研究,超高速主轴单元制造技术,超高速进给单元制造技术,超高速加工用刀具与磨具制造技术,超高速加工在线自动检测与控制技术等。
超精密加工当前是指被加工零件的尺寸精度高于0.1μm,表面粗糙度Ra小于0.025μ m,以及所用机床定位精度的分辨率和重复性高于0.01μm的加工技术,亦称之为亚微米级加工技术,且正在向纳米级加工技术发展。
超精密加工技术主要包括:超精密加工的机理研究,超精密加工的设备制造技术研究,超精密加工工具及刃磨技术研究,超精密测量技术和误差补偿技术研究,超精密加工工作环境条件研究。
二、现状及国内外发展趋势1.超高速加工工业发达国家对超高速加工的研究起步早,水平高。
在此项技术中,处于领先地位的国家主要有德国、日本、美国、意大利等。
在超高速加工技术中,超硬材料工具是实现超高速加工的前提和先决条件,超高速切削磨削技术是现代超高速加工的工艺方法,而高速数控机床和加工中心则是实现超高速加工的关键设备。
目前,刀具材料已从碳素钢和合金工具钢,经高速钢、硬质合金钢、陶瓷材料,发展到人造金刚石及聚晶金刚石(PCD)、立方氮化硼及聚晶立方氮化硼(CBN)。
第一章 精密和超精密加工技术概述 管文编著
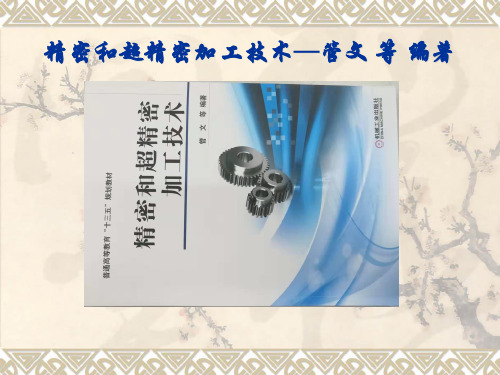
1.3 精密和超精密加工技术发展趋势
一、超精密加工技术基础理论和实验还需进一步发展
所谓超精密加工技术基础理论,是指在了解并掌握超精密 加工过程的基本规律和现象的描述后才能驾驭这一过程,取得 预期结果。例如上世纪 90 年代初,日本学者用金刚石车刀在 LLNL的DTM3上加工出最薄的连续切屑的照片,当时认为达到 了1nm的切削厚度,已成为世界最高水平,并至今无人突破 (见图1-4)。那么超精密切削极限尺度是多少、材料此时是 如何去除的,此外超精密加工工艺系统在力、热、电、磁、气 等多物理量/场复杂耦合下的作用机理是什么、此时系统的动态 特性、动态精度及稳定性如何保证等都需要得到新理论的支持。
1.2 精密超精密加工技术的作用
发动机喷嘴零件(如旋流槽、微小孔等特征)的精密 加工与检测技术、发动机叶片型面及进排气边的精密加工 与检测技术、整体叶盘的精密加工与检测技术等发展为航 空发动机零部件的加工与检测提供了可靠保证,促进了航 空发动机性能的提升。图1-3为发动机零部件专用五轴非 接触扫描精密测量机。
1.3 精密超精密加工技术发展趋势
三、微纳结构功能表面的超精密加工技术
微结构功能表面具有特定的拓扑形状,结构尺寸一般为 10~100μm ,面形精度小于 0.1μm,其表面微结构具有纹 理结构规则、高深宽比、几何特性确定等特点,如凹槽阵列、 微透镜阵列、金字塔阵列结构等,这些表面微结构使得元件 具有某些特定的功能,可以传递材料的物理、化学性能等, 如粘附性、摩擦性、润滑性、耐磨损性,或者具备特定的光 学性能等。在航空、航天飞行器宏观表面加工出微纳结构, 形成的功能性表面不仅可以减小飞行器的风阻、摩阻,减小 摩擦,还可以避免结冰层形成,提高空气动力学和热力学功 能,从而达到增速、增程、降噪等目的,同时表面特定的微 结构特征还能起到隐身功能,增强突防能力。
超精密加工技术的发展及对策
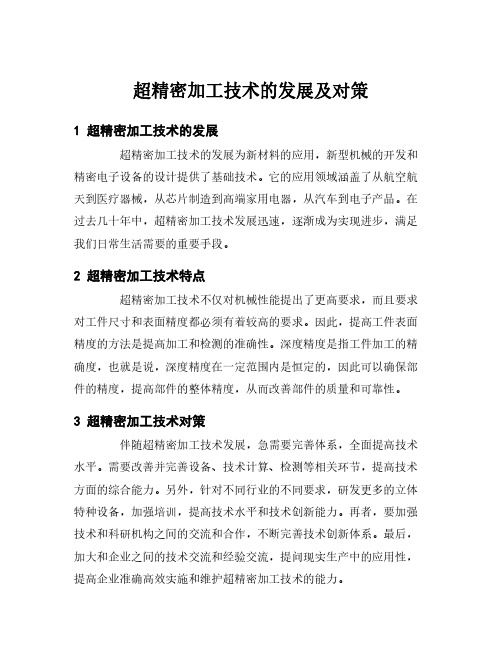
超精密加工技术的发展及对策
1超精密加工技术的发展
超精密加工技术的发展为新材料的应用,新型机械的开发和精密电子设备的设计提供了基础技术。
它的应用领域涵盖了从航空航天到医疗器械,从芯片制造到高端家用电器,从汽车到电子产品。
在过去几十年中,超精密加工技术发展迅速,逐渐成为实现进步,满足我们日常生活需要的重要手段。
2超精密加工技术特点
超精密加工技术不仅对机械性能提出了更高要求,而且要求对工件尺寸和表面精度都必须有着较高的要求。
因此,提高工件表面精度的方法是提高加工和检测的准确性。
深度精度是指工件加工的精确度,也就是说,深度精度在一定范围内是恒定的,因此可以确保部件的精度,提高部件的整体精度,从而改善部件的质量和可靠性。
3超精密加工技术对策
伴随超精密加工技术发展,急需要完善体系,全面提高技术水平。
需要改善并完善设备、技术计算、检测等相关环节,提高技术方面的综合能力。
另外,针对不同行业的不同要求,研发更多的立体特种设备,加强培训,提高技术水平和技术创新能力。
再者,要加强技术和科研机构之间的交流和合作,不断完善技术创新体系。
最后,加大和企业之间的技术交流和经验交流,提问现实生产中的应用性,提高企业准确高效实施和维护超精密加工技术的能力。
随着科技的进步,超精密加工技术在日常生活中起到了重要的作用,它的发展能够直接带来更佳的生活质量。
同时为了更好的发展,要加强技术支持,提升技术水平,增加技术的应用性,从而让超精密加工技术发挥更大的作用。
超精密加工的关键技术及发展趋势

车辆工程技术90机械电子1 超精密加工的技术范畴 在工业的加工领域当中,通常情况下按照加工的精度来划分的话,可以将机械加工一般可以分为三类,分别是:一般加工、精密加工和超精密加工。
随着生产技术的飞速发展,关于加工精度的划分标准也在随着时间的发展而变化,加工的进程也会随之而向前推移,可能过去的精密加工已经沦落为现今社会当中的一半加工的程度了。
因此,可以知道这个划分界限并不是一定的,它是会随着科学技术的发展而提高的,毕竟在如今的数据记录当中并没有主体的数值限制。
超精密加工的环境是在机床设备上进行的,利用刀具与零件之间产生的具有严格约束性的相对运动,从而达到加工出精度超高的产品,接着需要对加工好的材料进行相应的摩擦和去除毛刺,从而获得高形状、高精度的零件。
一般在学术界领域,超精度加工的加工精度通常在0.1μm 以上的,其表面的粗糙度也都是低于0.025μm的。
近年来,随着纳米技术的兴起,超精密加工目前已经进入纳米级精度阶段,逐渐的出现了纳米加工及其相关联的纳米技术。
经过近年来对纳米技术的使用和完善,这项技术已经逐渐的走向成熟,形成了一整套的超精密加工体系,其中包含了超精密切削、超精密磨削、超精密微细加工以及超精密计量等等,慢慢的向更高层次进行突破。
但是影响超精密加工的因素很多,目前只有在现有的基础上,经过研究和采用各种各样新型的技术、并且能够在各个方面融入这些新型技术,真正做到精益求精,达到更高的精度,才能突破传统加工模式的加工精度的界限。
实际上超精密的加工技术就是超精度切削、磨削和细微加工技术的综合应用。
2 超精密加工的关键技术2.1 主轴 目前阶段,在超精密加工机床的使用过程中,使用最高精度的主轴是空气静压轴承主轴,就我国制作出来的磁悬浮列车的轴承也远远达不到空气静压轴承主轴的加工精度,因此磁悬浮列车至今为止还是需要利用空气轴承。
就目前的超精密加工技术而言,空气静压轴承主轴的精度可以达到0.05μm,国内已经达到了这个加工精度的水平,然而国外甚至可以达到0.03μm,即使已经达到了如此精确的加工精度,却依旧不能满足纳米加工技术对于主轴的加工精度要求。
精密与超精密加工技术课件

珩磨效果受到多种因素的影响 ,如磨石的粒度、粘结剂的类 型、珩磨头的转速和压力等。
电解加工工艺
电解加工工艺概述
电解加工是一种利用电化学反应去除 工件材料的加工方法,具有加工精度 高、表面质量好等特点。
电解加工工艺流程
电解加工工艺通常包括工件表面处理 、电解液的选择和调整、电解加工设 备的设置以及加工参数的控制等步骤 。
、汽车和航空领域。
陶瓷材料
陶瓷材料具有高硬度、高耐磨性和 耐高温等特点,常用于制造刀具、 磨具和高温部件。
复合材料
复合材料由两种或多种材料组成, 具有优异的综合性能,如碳纤维复 合材料具有高强度和轻质的特点。
复合材料
玻璃纤维复合材料
玻璃纤维复合材料具有高 强度、高刚性和耐腐蚀等 特点,广泛应用于建筑、 船舶和汽车领域。
抛光效果受到抛光轮的材料、转速、抛光膏或抛光液的成分以及抛光 压力等因素的影响。
珩磨工艺
珩磨工艺概述
珩磨是一种利用珩磨头上的磨 石与工件表面进行摩擦,以去 除表面微小凸起和划痕的加工
方法。
珩磨材料
珩磨头上的磨石由硬质颗粒和 粘结剂组成,具有较高的硬度 和耐磨性。
珩磨工艺流程
珩磨工艺通常包括工件表面处 理、涂敷润滑剂、珩磨头的旋 转运动以及工件的往复运动等 步骤。
碳纤维复合材料
碳纤维复合材料具有高强 度、轻质和耐高温等特点 ,常用于制造航空器和体 育用品。
金属基复合材料
金属基复合材料以金属为 基体,加入增强纤维或颗 粒,以提高材料的强度、 刚度和耐磨性。
04
精密与超精密加工工艺
研磨工艺
研磨工艺概述
研磨材料
研磨是一种通过研磨剂去除工件表面微小 凸起和划痕的加工方法,以达到平滑表面 的效果。
《精密与超精密加工技术》知识点总结

《精密与超精密加工技术》知识点总结1. 加工的定义:改变原材料、毛坯或半成品的形状、尺寸及表面状态,使之符合规定要求的各种工作的统称。
规定要求:加工精度和表面质量。
2. 加工精度:是指零件在加工以后的几何参数(尺寸、形状、位置)与图纸规定的理想零件的几何 参数相符合的程度。
符合程度越高,加工精度则越高。
3. 表面质量:指已加工表面粗糙度、残余应力及加工硬化。
4. 精密加工定义:是指在一定时期,加工精度和表面质量达到较高程度的加工技术(工艺) 。
5. 超精密加工:是指在一定时期,加工精度和表面质量达到最高程度的加工技术(工艺) 。
6. 加工的划分 普通加工(一般加工)、精密加工和超精密加工。
普通加工:加工精度在 2m 以上(粗加工IT13〜IT9、半精加工IT8〜IT7、精加工IT6〜IT5),粗糙度 Ra0.1-0.8m 。
加工方法: 车、 铣、刨、磨等。
适用于:普通机械(汽车、拖拉机、机床)制造等。
精密加工: 加工精度在1〜0.1」m ,粗糙度 RaO.Vm 以下(一般Ra0.1〜0.01」m )的加工方法。
加工方法:车削、磨削、研磨及特种加工。
适用于:精密机床、精密测量仪器等中的关键零件 的制造。
超精密加工:加工精度在 0.1〜0.01」m ,粗糙度小于 Ra0.01」m (Ra0.01〜Ra0.001m )的加工方 法。
加工方法:金刚石刀具超精密切削、超精密磨削、超精密特种加工。
造、计量标准元件、集成电路等的制造。
(工艺过程)①压坏廈) 7. 精密加工影响因素8. 切削、磨削加工:精密切削和磨削、超精密切削与磨削。
9. 特种加工:是指一些利用热、声、光、电、磁、原子、化学等能源的物理的,化学的非传统加工 方法。
10. 精密加工和超精密加工的发展趋势:向高精度方向发展、向大型化,微型化方向发展、向加工检 测一体化发展、研究新型超精密加工方法的机理、新材料的研究。
11. 精密加工和超精密加工的特点:形成了系统工程 它是一门多学科的综合高级技术;它与特种加工关系密切 传统加工方法与非传统加工方法相结合;加工检测一体化 在线检测并进行实时控制、 误差补偿;与自动化技术联系密切 依靠自动化技术来保证;与产品需求联系紧密 加工质量要求 高、技术难度大、投资大、必须与具体产品需求相结合。
精密和超精密加工论文

精密和超精密加工论文(6000个字)一、精密和超精密加工的概念与范畴通常,按加工精度划分,机械加工可分为一般加工、精密加工、超精密加工三个阶段。
目前,精密加工是指加工精度为1~0.1?;m,表面粗糙度为Ra0.1~0.01?;m的加工技术,但这个界限是随着加工技术的进步不断变化的,今天的精密加工可能就是明天的一般加工。
精密加工所要解决的问题,一是加工精度,包括形位公差、尺寸精度及表面状况;二是加工效率,有些加工可以取得较好的加工精度,却难以取得高的加工效率。
精密加工包括微细加工和超微细加工、光整加工等加工技术。
传统的精密加工方法有砂带磨削、精密切削、珩磨、精密研磨与抛光等。
a.砂带磨削是用粘有磨料的混纺布为磨具对工件进行加工,属于涂附磨具磨削加工的范畴,有生产率高、表面质量好、使用范围广等特点。
b.精密切削,也称金刚石刀具切削(SPDT),用高精密的机床和单晶金刚石刀具进行切削加工,主要用于铜、铝等不宜磨削加工的软金属的精密加工,如计算机用的磁鼓、磁盘及大功率激光用的金属反光镜等,比一般切削加工精度要高1~2个等级。
c.珩磨,用油石砂条组成的珩磨头,在一定压力下沿工件表面往复运动,加工后的表面粗糙度可达Ra0.4~0.1?;m,最好可到Ra0.025?;m,主要用来加工铸铁及钢,不宜用来加工硬度小、韧性好的有色金属。
d.精密研磨与抛光通过介于工件和工具间的磨料及加工液,工件及研具作相互机械摩擦,使工件达到所要求的尺寸与精度的加工方法。
精密研磨与抛光对于金属和非金属工件都可以达到其他加工方法所不能达到的精度和表面粗糙度,被研磨表面的粗糙度Ra≤0.025?;m加工变质层很小,表面质量高,精密研磨的设备简单,主要用于平面、圆柱面、齿轮齿面及有密封要求的配偶件的加工,也可用于量规、量块、喷油嘴、阀体与阀芯的光整加工。
e.抛光是利用机械、化学、电化学的方法对工件表面进行的一种微细加工,主要用来降低工件表面粗糙度,常用的方法有:手工或机械抛光、超声波抛光、化学抛光、电化学抛光及电化学机械复合加工等。
精密与超精密加工技术及其发展趋势
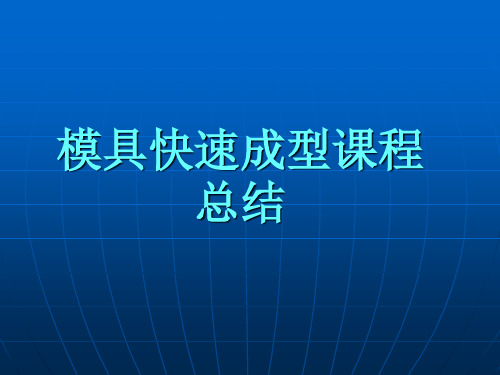
电化学过程 利用电能转换为化学能对材料进行加工,如电解加工、电铸加
工(金属离子沉积)等。 化学过程
利用化学溶剂对材料的腐蚀、溶解,去除材料,如化学蚀 刻、化学铣削等。
复合过程 利用机械、热、化学、电化学的复合作用,去除材料。
不损耗
30/3000 20/200 100/10000
1/50
1/100
0.03/0.003 10/0.04
从数微米的孔、槽到数 米的超大型模具、工件 等,如各种类型的孔、 各种类型的模具
0.02/0.002 5/0.32
切割各种二维及三维直 纹面组成的模具及零件, 也常用于钼、钨、半导 体材料或贵重金属切削
材料去除法—零件的最终几何形状局限在毛坯的初始 几何形状范围内,零件形状的改变是通过去除一部分材 料,减少一部分重量来实现的。如切削与磨削,电火花 加工、电解加工等特种加工等。
材料累加法—传统的累加方法有焊接、粘接或铆接等, 通过不可拆卸连接使物料结合成一个整体,形成零件。 近几年才发展起来的快速原型制造技术(RPM),是材 料累加法的新发展。
0.1/0.01
1.25/0.16
从微小零件到超大型工 件、模具的加工,如型 孔、型腔、抛光、去毛 刺等
硬质合金钢等难加工材
0.02/0.001 1.25/0.04 料的磨削,如硬质合金
刀具、量具等
几种常见特种加工方法的综合比较
加工 方法
超声 加工
激光 束加 工
电子 束加 工
离子 束加 工
加工 材料
计算机仿真和模拟来完善模具 结构,返修少,成本低
先进制造技术定义
精密和超精密加工技术的新进展
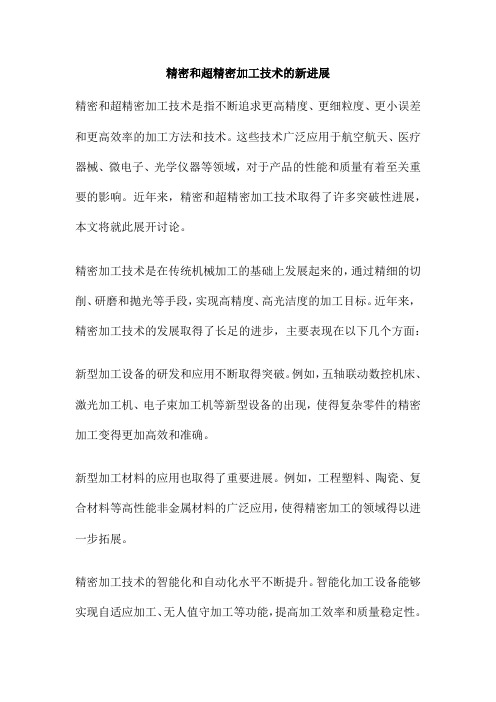
精密和超精密加工技术的新进展精密和超精密加工技术是指不断追求更高精度、更细粒度、更小误差和更高效率的加工方法和技术。
这些技术广泛应用于航空航天、医疗器械、微电子、光学仪器等领域,对于产品的性能和质量有着至关重要的影响。
近年来,精密和超精密加工技术取得了许多突破性进展,本文将就此展开讨论。
精密加工技术是在传统机械加工的基础上发展起来的,通过精细的切削、研磨和抛光等手段,实现高精度、高光洁度的加工目标。
近年来,精密加工技术的发展取得了长足的进步,主要表现在以下几个方面:新型加工设备的研发和应用不断取得突破。
例如,五轴联动数控机床、激光加工机、电子束加工机等新型设备的出现,使得复杂零件的精密加工变得更加高效和准确。
新型加工材料的应用也取得了重要进展。
例如,工程塑料、陶瓷、复合材料等高性能非金属材料的广泛应用,使得精密加工的领域得以进一步拓展。
精密加工技术的智能化和自动化水平不断提升。
智能化加工设备能够实现自适应加工、无人值守加工等功能,提高加工效率和质量稳定性。
超精密加工技术是指比精密加工技术更为精细、精确的加工方法和技术。
随着科技的不断进步,超精密加工技术的应用越来越广泛,主要包括以下几个方面:超精密加工技术广泛应用于微电子领域。
微电子产业对于芯片的精度和光洁度要求极高,超精密加工技术能够实现高精度、高效率的微米级加工,对于提升微电子产业的发展水平和竞争力具有重要意义。
超精密加工技术在光学仪器领域也有着广泛的应用。
光学仪器对于透镜、反射镜等光学元件的精度和表面质量要求极高,超精密加工技术能够实现高精度、高稳定性的光学元件加工,对于提高光学仪器的性能和精度具有重要作用。
再次,超精密加工技术在航空航天领域也有着重要的应用。
航空航天领域对于零件的精度和可靠性要求极为严格,超精密加工技术能够实现高精度、高稳定性的零件加工,对于提升航空航天领域的产品质量和性能具有重要意义。
近年来,精密和超精密加工技术的研究和应用不断取得新的进展,在新型加工设备、新型加工材料和智能化加工等方面都取得了重要突破。
精密和超精密加工现状与发展趋势.doc

精密和超精密加工现状与发展趋势核心提示:当前精密和超精密加工精度从微米到亚微米,乃至纳米,在汽车、家电、IT电子信息高技术领域和军用、民用工业有广泛应用。
同时,精密和超精密加工技术的发展也促进了机械、模具、液压、电子、半导体、光学、传感器和测量技术及金属加工工业的发展。
一、精密和超精密加工的概念与范畴通常,按加工精度划分,机械加工可分为一般加工、精密加工、超精密加工三个阶段。
目前,精密加工是指加工精度为1~0.1μm,表面粗糙度为Ra0.1~0.01μm的加工技术,但这个界限是随着加工技术的进步不断变化的,今天的精密加工可能就是明天的一般加工。
精密加工所要解决的问题,一是加工精度,包括形位公差、尺寸精度及表面状况;二是加工效率,有些加工可以取得较好的加工精度,却难以取得高的加工效率。
精密加工包括微细加工和超微细加工、光整加工等加工技术。
传统的精密加工方法有砂带磨削、精密切削、珩磨、精密研磨与抛光等。
a. 砂带磨削是用粘有磨料的混纺布为磨具对工件进行加工,属于涂附磨具磨削加工的范畴,有生产率高、表面质量好、使用范围广等特点。
b. 精密切削,也称金刚石刀具切削(SPDT),用高精密的机床和单晶金刚石刀具进行切削加工,主要用于铜、铝等不宜磨削加工的软金属的精密加工,如计算机用的磁鼓、磁盘及大功率激光用的金属反光镜等,比一般切削加工精度要高1~2个等级。
c. 珩磨,用油石砂条组成的珩磨头,在一定压力下沿工件表面往复运动,加工后的表面粗糙度可达Ra0.4~0.1μm,最好可到Ra0.025μm,主要用来加工铸铁及钢,不宜用来加工硬度小、韧性好的有色金属。
d. 精密研磨与抛光通过介于工件和工具间的磨料及加工液,工件及研具作相互机械摩擦,使工件达到所要求的尺寸与精度的加工方法。
精密研磨与抛光对于金属和非金属工件都可以达到其他加工方法所不能达到的精度和表面粗糙度,被研磨表面的粗糙度Ra≤0.025μm加工变质层很小,表面质量高,精密研磨的设备简单,主要用于平面、圆柱面、齿轮齿面及有密封要求的配偶件的加工,也可用于量规、量块、喷油嘴、阀体与阀芯的光整加工。
超精密加工的发展与展望
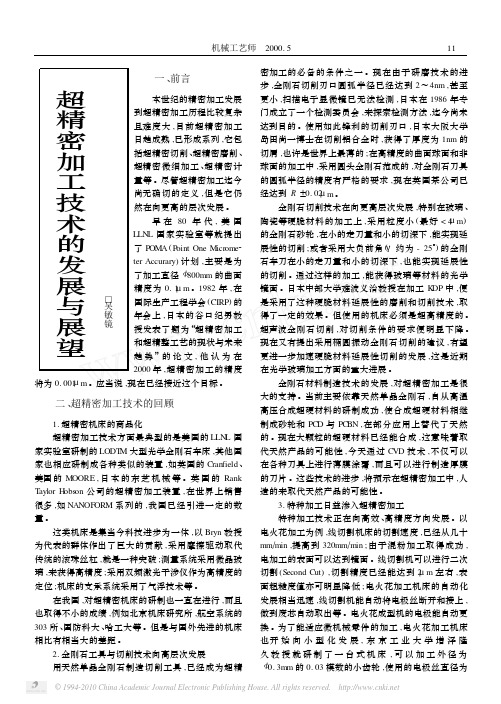
□吴敏镜 超精密加工技术的发展与展望 一、前言本世纪的精密加工发展到超精密加工历程比较复杂且难度大,目前超精密加工日趋成熟,已形成系列,它包括超精密切削、超精密磨削、超精密微细加工、超精密计量等。
尽管超精密加工迄今尚无确切的定义,但是它仍然在向更高的层次发展。
早在80年代,美国LLN L 国家实验室等就提出了POMA (P oint One Microme 2ter Accurary )计划,主要是为了加工直径<800mm 的曲面精度为0.1μm 。
1982年,在国际生产工程学会(CIRP )的年会上,日本的谷口纪男教授发表了题为“超精密加工和超精整工艺的现状与未来趋势”的论文,他认为在2000年,超精密加工的精度将为0.001μm 。
应当说,现在已经接近这个目标。
二、超精密加工技术的回顾1.超精密机床的商品化超精密加工技术方面最典型的是美国的LLN L 国家实验室研制的LODT M 大型光学金刚石车床,其他国家也相应研制成各种类似的装置,如英国的Cran field 、美国的MOORE ,日本的东芝机械等。
英国的Rank T aylor H obs on 公司的超精密加工装置,在世界上销售很多,如NANOFORM 系列的,我国已经引进一定的数量。
这类机床是集当今科技进步为一体,以Bryn 教授为代表的群体作出了巨大的贡献,采用摩擦驱动取代传统的滚珠丝杠,就是一种突破;测量系统采用微晶玻璃,来获得高精度;采用双频激光干涉仪作为高精度的定位;机床的支承系统采用了气浮技术等。
在我国,对超精密机床的研制也一直在进行,而且也取得不小的成绩,例如北京机床研究所,航空系统的303所、国防科大、哈工大等。
但是与国外先进的机床相比有相当大的差距。
2.金刚石工具与切削技术向高层次发展用天然单晶金刚石制造切削工具,已经成为超精密加工的必备的条件之一。
现在由于研磨技术的进步,金刚石切削刃口圆弧半径已经达到2~4nm ,甚至更小,扫描电子显微镜已无法检测,日本在1986年专门成立了一个检测委员会,来探索检测方法,迄今尚未达到目的。
精密与超精密加工技术现状和发展展望

精密与超精密加工技术现状和发展展望精密加工技术是一种在当今制造业中非常重要的技术,它的发展与制造业的发展息息相关。
精密加工技术是通过对材料进行高精度的加工来制造出各种精密零部件,这些精密零部件被广泛应用于汽车、航空航天、医疗器械、电子产品等各个领域。
现阶段,精密加工技术已经取得了很大的进步,各种高精度的加工设备和加工工艺层出不穷。
在这些技术发展的基础上,超精密加工技术应运而生。
超精密加工技术是一种相对于精密加工技术更加高端、更加精密的加工技术,它可以实现对材料的超高精度加工,甚至可以达到纳米级的精度。
这种技术对于一些特殊材料的加工非常重要,比如硬质合金、钢、陶瓷等材料。
超精密加工技术的发展展望是非常乐观的。
随着科学技术的不断进步,各种先进的加工设备和工艺将不断涌现。
在这种趋势下,超精密加工技术将会得到更加广泛的应用。
在汽车工业中,超精密加工技术可以用于制造高压油泵的零部件,提高汽车发动机燃油的利用率;在医疗器械领域,超精密加工技术可以用于制造各种医疗器械的零部件,提高医疗器械的精度和安全性。
在未来的发展中,我们还可以看到超精密加工技术将会在航空航天领域得到更广泛的应用。
超精密加工技术可以制造出更加轻巧和高强度的航空零部件,提高航空器的性能和安全性。
超精密加工技术在电子产品领域也有很大的潜力,它可以制造出更小巧、更精密的电子元件,提高电子产品的性能和可靠性。
精密加工技术和超精密加工技术的发展是非常重要的。
它们直接关系到制造业的发展和产品的质量。
相信随着科学技术的不断进步,这些技术将会取得更大的突破,为各个领域带来更多的创新和发展。
精密与超精密加工技术的现状和发展展望精密加工技术是制造业中至关重要的一环,它的发展与制造业的发展密不可分。
精密加工技术通过对材料进行高精度的加工,制造出各种精密零部件,广泛应用于汽车、航空航天、医疗器械、电子产品等各个领域。
当前,精密加工技术已取得了长足的发展,各种高精度加工设备和工艺不断涌现。
超精密加工的发展动向和展望

超精密加工的发展动向和展望超精密加工技术是机械制造领域的重要方面,它的发展是尖端技术的基础,它的成就将是推动整个科技向更高层次发展的重要手段,也是现阶段必须突破的关键技术,因此及时借助于当前的有关各项技术的进步,综合加以利用才能突破。
这就是本文的初衷。
1综述超精密加工技术是一门综合性的系统工程,它的发展综合地利用了机床、工具、计量、环境技术、微电子技术、计算机技术、数控技术等的进步。
日本的津和秀夫教授形象地将超精密加工比作富士山的山顶,所以在某种意义上说,已到达了精密加工的顶峰。
日本的文献上,经常出现向极限靠拢的提法。
虽然从技术的角度来说,有些模糊,但是很形象化。
实际上,加工精度在现有的水平上再提高一步已是相当困难。
以现在的产品而言,凡是要求高的尺寸,大部分是超越现有标准的,这从另一个侧面反映了超精密的实际情况,相当多的要求,均以技术条件的形式来表示,或标明具体的特殊公差,而今天除了精度以外,对表面还提出了新的要求——表面完整性。
日本谷口纪男教授往往将超精密加工技术与微细加工综合在一起来加以介绍,客观上反映了两种技术的交叉,也体现了时代的特征。
本文想就超精密加工发展的趋势,说明一些个人的看法。
超精密加工技术随着时间的推延,精度、难度、复杂性等都在向更高层次发展,使加工技术也随之需要不断加以更新,来与之相适应。
以金刚石切削为例,其刃口圆弧半径一直在向更小的方向发展,因为它的大小直接影响到被加工表面的粗糙度,与光学镜面的反射率直接有关,而今反射率要求越来越高,如激光陀螺反射镜的反射率已提出了99.99%,必然要求金刚石刀具更加锋利,根据日本大阪大学岛田尚一博士介绍,为了进行切薄试验,目标是达到切屑的厚度1nm,其刃口圆弧半径趋近2~4nm。
直至今日,这个水平仍为世界最高的。
为了达到这个高度,促使金刚石研磨机也改变了传统的结构,而采用了空气轴承作为支承,研磨盘的端面跳动能在机床上自行修正,使其端面跳动控制在0.5μm以下,我国航空系统303所研制的刃磨机就是一例。
精密和超精密加工技术PPT课件

精密和超精密加工技术
1
教材:《精密和超精密加工技术》(第2版) 袁哲俊、王先逵主编 机械工业出版社
➢ 学时:28 ➢ 周二下午5-6节(H514) ➢ 周四上午1-2节(H514)
参考材料: 1、张建华主编《精密与特种加工技术》 2、王先逵编《精密加工技术实用手册》,
8
1.1 发展精密和超精密加工技术的重要性
精密和超精密加工是先进制造技术的基础和关键
作为制造技术的主战场,作为真实产品的实 际制造,必然要靠精密加工和超精密加工技术, 例如,计算机工业的发展不仅要在软件上,还要 在硬件上,即在集成电路芯片上有很强的能力, 应该说,当前,我国集成电路的制造水平约束了 计算机工业的发展。美国制造工程研究者提出的 汽车制造业的“两毫米工程”使汽车质量赶上欧、 日水平,其中的举措都是实实在在的制造技术。
热流动加工(高频电流、热射流、电子束、激光) 液体、气体流动加工(压铸、挤压、喷射、浇铸) 微粒子流动加工
5
精密和超精密加工方法分类(2)
分类 切削加工 磨料加工
特种加工
复合加工
加工方法
等离子体切削 微细切削 微细钻削
微细磨削 研磨 抛光 弹性发射加工 喷射加工
电火花成形加工 电火花切割加工 电解加工 超声波加工 微波加工 电子束加工 粒子束去除加工 激光去除加工 光刻加工
段,通常,按加工精度划分,可将机械加工分为一般 加工、精密加工、超精密加工三个阶段。
➢精密加工:加工精度在0.1~1µm,加工表面粗糙
度在Ra0.02~0.1µm之间的加工方法称为精密加工;
➢超精密加工:加工精度高于0.1µm,加工表面粗糙
精密和超精密加工技术及其发展展望共32页文档
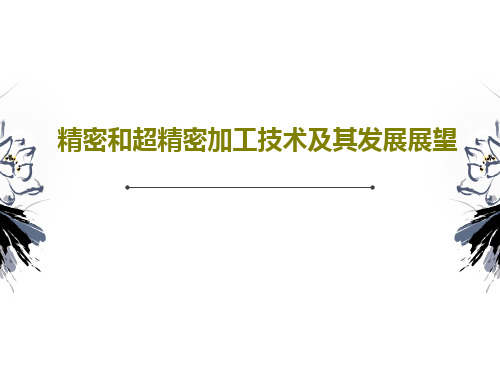
36、“不可能”这个字(法语是一个字 ),只 在愚人 的字典 中找得 到。--拿 破仑。 37、不要生气要争气,不要看破要突 破,不 要嫉妒 要欣赏 ,不要 托延要 积极, 不要心 动要行 动。 38、勤奋,机会,乐观是成功的三要 素。(注 意:传 统观念 认为勤 奋和机 会是成 功的要 素,但 是经过 统计学 和成功 人士的 分析得 出,乐 观是成 功的第 三要素 。
39、没有不老的誓言,没有不变的承 诺,踏 上旅途 ,义无 反顾。 40、对时间的价值没有没有深切认识 的人, Байду номын сангаас不会 坚韧勤 勉。
谢谢
11、越是没有本领的就越加自命不凡。——邓拓 12、越是无能的人,越喜欢挑剔别人的错儿。——爱尔兰 13、知人者智,自知者明。胜人者有力,自胜者强。——老子 14、意志坚强的人能把世界放在手中像泥块一样任意揉捏。——歌德 15、最具挑战性的挑战莫过于提升自我。——迈克尔·F·斯特利
- 1、下载文档前请自行甄别文档内容的完整性,平台不提供额外的编辑、内容补充、找答案等附加服务。
- 2、"仅部分预览"的文档,不可在线预览部分如存在完整性等问题,可反馈申请退款(可完整预览的文档不适用该条件!)。
- 3、如文档侵犯您的权益,请联系客服反馈,我们会尽快为您处理(人工客服工作时间:9:00-18:30)。
精密与超精密加工技术概述
◆精密加工 —— 在一定的发展时期,加工精度和表面质量 达到较高程度的加工工艺。
超精密加工 —— 在一定的发展时期,加工精度和表面质 量达到最高程度的加工工艺。
◆瓦特改进蒸汽机 —— 镗孔精度 1mm 20 世纪 40 年代 —— 最高精度 1μm 20 世纪 末 —— 精密加工:≤0.1μm,Ra ≤0.01μm(亚微米加工) 超精密加工:≤ 0.01μm ,Ra≤ 0.001μm(纳米加工)
◆微细加工 —— 微小尺寸的精密加工 超微细加工 ——微小尺寸的超精密加工
几种典型精密零件的加工精度
零件 激光光学零件
多面镜 磁头 磁盘 雷达导波管 卫星仪表轴承 天体望远镜
加工精度 形状误差 0.1μm 平面度误差 0.04μm 平面度误差 0.04μm 波度 0.01 ~0.02μm 平面度垂直度误差 < 0.1μm 圆柱度误差 <0.01μm 形状误差 < 0.03μm
• 超精密加工的对象
– 有色金属及合金 – 硬脆材料 – 黑色金属 – 复合材料
中小型精密零件的加工精度
加工零件 (μm)
激光光学零件 磁头 多面镜 磁盘 磁盘 非球面模具
Ra (μm)
0.01~0.006 0.02 0.01~0.02 0.01~0.004 0.01~0.004 0.01
形状精度
0.1
平面度 0.04 平面度 0.04 波度0.02~0.01 波度0.02~0.01
1~0.3
超精密加工的设备
• 美国LLL实验室的 DTM-3、LODTM超 精密金刚石车床
• 英国Cranfield的OAGM2500超精密金 刚石车床
• 欧洲COLATH的超精密金刚石切削机床 • 日本小型超精密金刚石切削机床
精密加工的种类
微切削加工
微蚀刻技术
微电火花加工
微成型加工
激光加工
LIGA技术
精密和超精密举例
• 陀螺仪 • 人造卫星仪表的真空无润滑轴承 • Hubble望远镜 • 飞机发动机叶片 • 大规模集成电路 • 计算机存储介质 • 民用产品
陀螺仪
右边的圆球就是石英制的转子, 近乎完美的球体
飞机发动机的叶片
• 精密切削 • 精密磨削和研磨 • 特种精密加工 • 微细加工
精密加工方法及发展预测
超精密加工技术的现状
• 超精密加工技术的新发展 • 超精密加工的设备 • 超精密加工机理研究 • 检测和误差补偿 • 工作环境
超精密加工技术的新发展
• 超精密的加工集成系统
– 设备 – 测量、检测 – 计算机控制、补偿 – 环境
表面粗糙度
Ra 0.01~0.05μm Ra <0.02μm Ra <0.02μm Ra <0.02μm Ra <0.02μm Ra <0.002μm Ra <0.01μm
精密加工与超精密加工的发展
加工误差(μm)
102 101 100 10-1 10-2 10-3
1900
普通加工
加工设备 车床,铣床
– 光波干涉测量 – 隧道扫描显微镜
• 机床本身精度检测
– 主轴工作台径向跳动
• 机床重复定位精度检测
• 温度 • 振动 • 洁净度 • 噪声 • 湿度 • 其它
工作环境
超精密加工技术发展展望
• 国外发展尖端
– 按材料分
• 传统有色金属 • 难切削材料 • 非金属硬脆材料
– 按加工分
• 切削加工 • 带检测反馈 • 带表面涂层处理以及综合应用
精密制造工程
2008.9
第一章 精密和超精密加 工技术及发展展望
本章内容
• 发展精密和超精密加工技术的重要性 • 超精密加工技术的现状 • 超精密加工技术发展展望
发展精密和超精密加工技术的重要性
• 我国机械行业落后主要体现
– 高度的自动化技术 – 精密和超精密加工技术
• 精密和超精密加工技术应用范围
LODTM超精密金刚石车床
LODTM超精密金刚石车床
Lawrence Livermore Laboratory
我国研发的纳米级超精密数控车床 NAM-800
超精密加工机理研究
• 切削工具
– 金刚石刀具——有色金属 – 磨削、研磨——黑色金属
• 工件材料的处理方式
检测和误差补偿
• 工件检测
大规模集成电路的芯片技术
大规模集成电路
芯片局部显微图像
单晶硅切片制造芯片
切割封装
大规模集成电路的芯片技术
• 目前0.25-0.18μm已开始进入大生产。 0.15-0.13μm大生产技术也已完成开发.
• 集成电路技术是近50年来发展最快的技术, 其设计规则从1959年以来40年间缩小了140 倍,而平均晶体管价格降低了107倍。
我国超精密加工技术发展展望
• 超精密切削磨削的机理研究 • 超精密设备性能 • 超精密加工检测以及误差补偿 • 超精密加工环境控制 • 超精密加工材料研究
本课程内容
1. 精密加工技术及展望 2. 精密切削技术 3. 精密磨削技术 4. 精密加工设备 5. 精密加工中的测量技术 6. 在线检测与误差补偿技术 7. 精密研磨和抛光 8. 微细加工技术 9. 精密加工的支撑环境 10. 纳米技术
精密车床 磨床
测量仪器 卡尺
百分尺 比较仪
精密加工
坐标镗床 坐标磨床
气动测微仪 光学比较仪
金刚石车床 光学磁尺
精密磨床
电子比较仪
超精密加工
超精密磨床 激光测长仪 精密研磨机 圆度仪轮廓仪
超高精密磨床 激光高精度 超精密研磨机 测长仪
1920 1940
1960 1980
离子束加工 扫描电镜
分子对位加工 电子线分析
• 集成电路自发明以来,集成电路芯片的集成 度每3年提高4倍,而加工特征尺寸缩小√2 倍。这Intel公司创始人之一的Gordon E. Moore博士1965年总结出的摩尔定律 .
Hubble望远镜
微细齿轮
计算机存储介质
剃须刀网刃的精密电铸
光刻 弯曲成形 电镀沉积 分离
精密制造的主要研究领域
2000
年份
仪
精密和超精密的作用
• 提高综合性能和质量 • 提高稳定性和可靠性 • 小型化 • 装配互换性好,易于实现自动装配
精密与超精密加工地位
➢是一个01μm;超大规模集成 电路最小线宽0.1μm
➢是先进制造技术基础和关键 例:陀螺仪球圆度0.1μm,粗糙度Ra0.01μm,导弹命 中精度控制在50m范围内;飞机发电机转子叶片加工误 差从60μm降至12μm,发电机压缩效率从89%提高到94%; 齿形误差从3-4μm减小1μm,单位重量齿轮箱扭矩可提 高一倍 ➢是新技术的生长点 精密制造涉及多种基础学科和多种新兴技术,其发展将 会带动和促进这些相关科学技术的发展