风力发电机组振动分析系统
风力机结构振动监测与模态分析

风力机结构振动监测与模态分析风力机结构振动监测与模态分析风力机结构振动监测与模态分析是风力发电行业中重要的研究领域之一。
通过对风力机结构振动的监测与模态分析,可以了解风力机的结构特性、故障诊断以及优化设计等方面的问题,为风力机的安全运行和提高发电效率提供重要依据。
以下是风力机结构振动监测与模态分析的步骤。
第一步:建立监测系统首先,需要建立一个风力机结构振动监测系统。
该系统通常由加速度传感器、位移传感器、应变传感器等组成,用于测量风力机结构的振动和变形情况。
传感器的位置和布置需要根据风力机的结构特点和关键位置进行确定。
第二步:数据采集与处理通过监测系统采集到的振动数据,需要进行数据处理和分析。
首先,对采集到的原始数据进行滤波和去噪处理,以提高数据的可靠性和准确性。
然后,对处理后的数据进行时域分析、频域分析和波形分析等,得到风力机结构的振动特性和频谱信息。
第三步:模态识别与分析基于振动数据的特征提取,可以进行模态识别与分析。
模态分析是通过分析风力机结构的固有振动模态(包括自由振动模态和强迫振动模态),来了解风力机结构的动力特性。
常用的模态分析方法包括主成分分析法、最小二乘法和模态参数识别法等。
第四步:故障诊断与预测通过监测和模态分析得到的振动数据,可以进行故障诊断与预测。
根据风力机结构的振动特征和频谱信息,可以判断出可能存在的故障类型,如轴承故障、齿轮故障等。
同时,可以通过分析振动数据的趋势和变化,预测未来可能发生的故障,从而采取相应的维修和保养措施,确保风力机的安全运行。
第五步:优化设计与改进通过振动监测与模态分析,可以发现风力机结构中存在的问题和不足之处。
基于分析结果,可以进行优化设计和改进,以提高风力机的结构强度、降低振动和噪音等。
优化设计可以包括材料选择、结构改进和动力系统调整等方面,以提高风力机的整体性能和可靠性。
综上所述,风力机结构振动监测与模态分析是确保风力机安全运行和提高发电效率的重要手段之一。
风力发电机组振动报警系统的设计与实现

自动根据文件名称 创建E c l ,不用 事 件结构 ,事 件源选择 确定 ,事件 选 程状态监测和故障诊断 目标 出发 , x e表 设计 进行 复杂 的编程 即可实现 数据 的 自动 择 值改变 。当按下确 定按钮 ,事件 结 并实现 了一种 振动报 警 系统 。 系统 具 换行 存储 。基于 以上优 点 ,采 用表单 构就被触 发 ,此时运 行 “ 取并显 示 有振 动信号 采集 、数 据传输 、报 警值 读 文件 技术进 行编程 实现 对实 时采集 的 报 警记 录”的程序 。程序设计如 图6 所 计算 与存储 、报警 历史查 询等 多项功 数据 存储 ,并在 存储数 据的 同时把 当 示 前时 间写入E cl 中。 xe 表 对应 的程序 框 图及前面 板分 别如
参 考 国 际 标 准 化 组 织 标 准
握手 的过程 进行 初始化 ,这个过 程使
在本 系统设计 中 ,定义 DSP 为服 I S02 7 3 2,选 取4. mm/ 为注 意 阈 5 s
序号 同步 ,并提供 两个 主机之 间建立 务 器 ( e v r ,上位 机监控系统为 值 ,l .mm/ 为报警 阈值 。 S r e) 12 s 虚拟 连接所 需的控 制信 息。一旦 初始 客 户端 ( i n )。服务 器端 先对指 Cle t 2报警程序设计 对 于 接 收 到 的 时 域 振 动 信 号 要
1报警值计算与设定 均 方根 值 ,又称 有效 值 ,是反映
相对 于其他 网络协议 ,TCP I /P
这种端 对端 的传输具 有两 大优点 。第 机组振 动信 号统计 特性 的重要 时域参 需 要把报 警信 息存储起 来 ,以便于 日
一
,
TC / P 其他协议S O ,显得简 量 。它是对 信号 取样段 的总体 能量 的 后 的历 史查询和 分析 。通过 统计数据 P I跟 HE 直接 反映 ,只要 取样长 度足够 ,它就 量 的大 小 ,本 系统采 用EX e 表作 为 Cl
浅析风力发电机组传动链振动监测系统的应用

浅析风力发电机组传动链振动监测系统的应用摘要:风力发电机组处于恶劣的环境下,运行工况复杂,由于风力发电机组的启停、偏航、变桨、调控时会产生很大的冲击,从而对风机的部件造成冲击振动,影响风力发电机组的安全稳定运行。
传动链作为风力发电机组关键的组成部分,其振动对风机安全稳定运行起到至关重要的作用。
因此,通过振动监测和故障诊断技术,及时、有效地对风力发电机组传动链运行状态作出诊断,避免重大事故的发生,有效保证风力发电机组安全稳定的运行。
关键词:风力发电机组;振动监测;传动链1 引言随着经济社会的发展和转型,人类越来越重视清洁能源的开发和利用。
风能作为一种清洁、无污染、蕴藏量丰富可再生能源,受到各国的重视,成为重点开发的能源之一。
风力发电机组通常处于高山、戈壁、草原、海上等场所,承受的工况条件复杂,常年处于昼夜温差大、载荷变化大、冲击载荷频繁的环境中,容易发生故障,目前,风力发电机组维修保养采用计划维修和事后维修两种方式,其缺点在于需要在维修期间停止风机运行,对于事后维修则需要更高维护成本[1]。
状态监测与故障诊断技术是在设备运行中或不拆卸设备的情况下,运用各种监测设备和方法判断设备的运行状态是否存在异常,准确判断设备故障部位提出预警,并可判断设备故障发展趋势的技术,是一门集力学、电子技术、测试技术、计算机技术等学科为一体的综合性技术。
相比计划维修和事后维修,状态监测与故障诊断技术作为预知性维修,可以根据设备的实际运行状态来安排维修作业,避免了维修不足和过剩维修的情况,防止事故的发生,保障了风力发电机组的稳定运行。
振动监测作为状态监测的必要技术,近年来在风力发电机组上得到广泛应用[2]。
2 风力发电机组风力发电机组主要是通过叶片捕获风能,再通过传动系统增速,最后驱动发电机发电,从而将风能转化为电能。
双馈型风力发电机组传动链主要由主轴、主轴承、齿轮箱、制动盘、联轴器和发电机等主要部件组成,据相关统计数据可知,双馈机组的故障主要集中在齿轮箱、叶片、发电机、电气系统、偏航系统、传动链、控制系统等关键部件,对于电气系统故障,可以通过远程控制和及时更换配件的方式排除故障,但是对于传动链系统的故障检修难度较大,需要停机数天,需要高额的维修费用,会造成发电量的损失和巨大的经济损失。
风力发电机振动在线监测系统
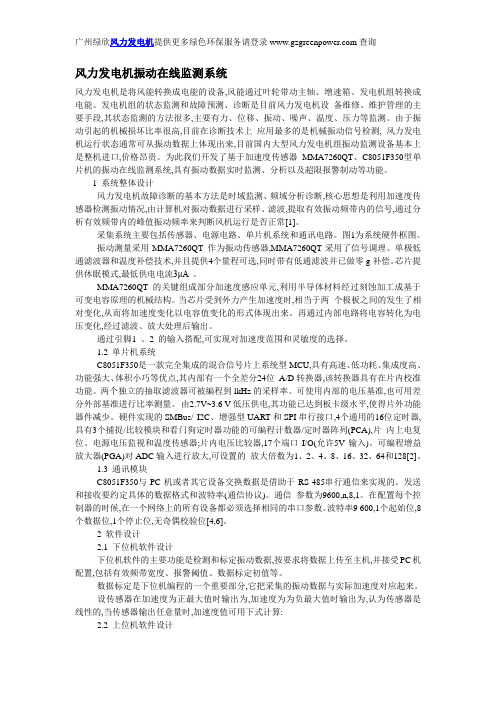
风力发电机振动在线监测系统风力发电机是将风能转换成电能的设备,风能通过叶轮带动主轴、增速箱、发电机组转换成电能。
发电机组的状态监测和故障预测、诊断是目前风力发电机设备维修、维护管理的主要手段,其状态监测的方法很多,主要有力、位移、振动、噪声、温度、压力等监测。
由于振动引起的机械损坏比率很高,目前在诊断技术上应用最多的是机械振动信号检测, 风力发电机运行状态通常可从振动数据上体现出来,目前国内大型风力发电机组振动监测设备基本上是整机进口,价格昂贵。
为此我们开发了基于加速度传感器MMA7260QT、C8051F350型单片机的振动在线监测系统,具有振动数据实时监测、分析以及超限报警制动等功能。
1 系统整体设计风力发电机故障诊断的基本方法是时域监测、频域分析诊断,核心思想是利用加速度传感器检测振动情况,由计算机对振动数据进行采样、滤波,提取有效振动频带内的信号,通过分析有效频带内的峰值振动频率来判断风机运行是否正常[1]。
采集系统主要包括传感器、电源电路、单片机系统和通讯电路。
图1为系统硬件框图。
振动测量采用MMA7260QT 作为振动传感器,MMA7260QT采用了信号调理、单极低通滤波器和温度补偿技术,并且提供4个量程可选,同时带有低通滤波并已做零g补偿。
芯片提供休眠模式,最低供电电流3μA 。
MMA7260QT的关键组成部分加速度感应单元,利用半导体材料经过刻蚀加工成基于可变电容原理的机械结构。
当芯片受到外力产生加速度时,相当于两个极板之间的发生了相对变化,从而将加速度变化以电容值变化的形式体现出来。
再通过内部电路将电容转化为电压变化,经过滤波、放大处理后输出。
通过引脚1 、2 的输入搭配,可实现对加速度范围和灵敏度的选择。
1.2 单片机系统C8051F350是一款完全集成的混合信号片上系统型MCU,具有高速、低功耗、集成度高、功能强大、体积小巧等优点,其内部有一个全差分24位A/D转换器,该转换器具有在片内校准功能。
风电机组振动检测系统设计及实施方案
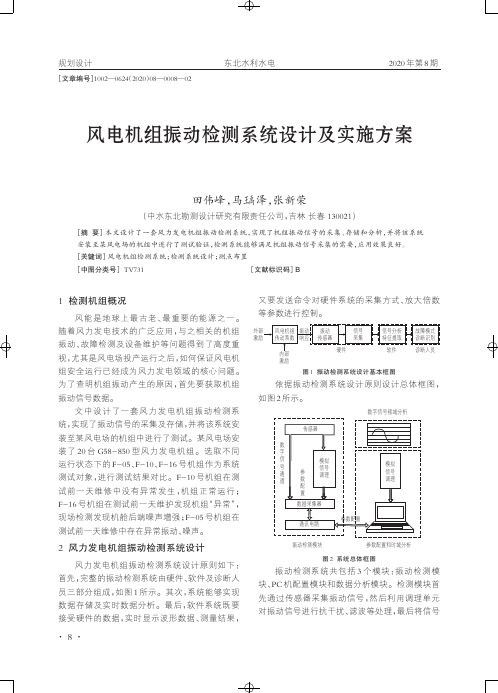
风电机组振动检测系统设计及实施方案田伟峰,马王禹泽,张新荣(中水东北勘测设计研究有限责任公司,吉林长春130021)[摘要]本文设计了一套风力发电机组振动检测系统,实现了机组振动信号的采集、存储和分析,并将该系统安装至某风电场的机组中进行了测试验证,检测系统能够满足机组振动信号采集的需要,应用效果良好。
[关键词]风电机组检测系统;检测系统设计;测点布置[中图分类号]TV731[文献标识码]B[文章编号]1002—0624(2020)08—0008—021检测机组概况风能是地球上最古老、最重要的能源之一。
随着风力发电技术的广泛应用,与之相关的机组振动、故障检测及设备维护等问题得到了高度重视,尤其是风电场投产运行之后,如何保证风电机组安全运行已经成为风力发电领域的核心问题。
为了查明机组振动产生的原因,首先要获取机组振动信号数据。
文中设计了一套风力发电机组振动检测系统,实现了振动信号的采集及存储,并将该系统安装至某风电场的机组中进行了测试。
某风电场安装了20台G58-850型风力发电机组。
选取不同运行状态下的F-05、F-10、F-16号机组作为系统测试对象,进行测试结果对比。
F-10号机组在测试前一天维修中没有异常发生,机组正常运行;F-16号机组在测试前一天维护发现机组“异常”,现场检测发现机舱后端噪声增强;F-05号机组在测试前一天维修中存在异常振动、噪声。
2风力发电机组振动检测系统设计风力发电机组振动检测系统设计原则如下:首先,完整的振动检测系统由硬件、软件及诊断人员三部分组成,如图1所示。
其次,系统能够实现数据存储及实时数据分析。
最后,软件系统既要接受硬件的数据,实时显示波形数据、测量结果,又要发送命令对硬件系统的采集方式、放大倍数等参数进行控制。
图1振动检测系统设计基本框图依据振动检测系统设计原则设计总体框图,如图2所示。
图2系统总体框图振动检测系统共包括3个模块:振动检测模块、PC机配置模块和数据分析模块。
风力发电机振动监测系统维修手册

风力发电机振动监测系统维修手册引言:风力发电机作为一种现代化的可再生能源发电设备,具有环保、高效、可持续的特点,在全球范围内得到广泛应用。
而风力发电机振动监测系统作为该设备的核心部件,对于确保设备的正常运行和减少损耗具有重要意义。
本维修手册旨在提供风力发电机振动监测系统的维修指导,从而帮助用户有效解决设备故障和提高系统性能。
一、系统概述风力发电机振动监测系统通过测量风力发电机振动参数,如振动加速度、振动速度和振动位移等,实时监测设备的运行状态,从而及时识别问题和进行预警。
该系统由传感器、数据采集模块、数据处理单元和显示控制终端等组成。
其主要功能包括:1. 监测风力发电机的振动水平,判断设备的工作状态和软硬件性能;2. 分析和识别设备振动异常,预警设备发生故障的潜在风险;3. 提供实时数据和报表,为维修和调试工作提供数据支持;4. 进行设备故障诊断,提供维修建议和方案。
二、振动监测系统的维护与维修振动监测系统的正常维护和维修对于确保其长期稳定运行和准确监测非常重要。
以下是相关的维护和维修指南:1. 传感器维护传感器是振动监测系统中非常关键的组成部分,其灵敏度和准确性直接影响系统的监测效果。
因此,传感器的维护非常重要。
(1)定期校准传感器的灵敏度,确保其准确度和可靠性;(2)检查传感器与设备的连接接头,确保传感器与设备之间的电气连接良好;(3)在传感器正常工作时,及时清洁传感器并保持传感器周围环境清洁,防止灰尘和杂质影响传感器的运行。
2. 数据采集模块维护数据采集模块负责将传感器采集的数据进行模拟/数字转换,并传输至数据处理单元。
以下是数据采集模块的维护要点:(1)检查数据采集模块的电源和信号连接,确保其正常工作;(2)定期清理数据采集模块和连接线路的灰尘和杂质,保持其通畅和良好的接触性能;(3)及时更换损坏的数据采集模块,确保其正常功能。
3. 数据处理单元维护数据处理单元负责接收和处理数据采集模块传输的数据,并进行分析和判断。
风力发电机组振动状态监测与分析

风力发电机组振动状态监测与分析摘要:风力发电机组振动状态监测是根据所监测风电机组类型,选择不同的监测部位,监测风电机组振动状态的改变,评估风电机组的状态,早期发现并跟踪设备故障的一种方法。
加强对风电机组的状态监测与分析,作为保障机组可靠运行和寿命管理的重要手段,在风电领域越来越受到重视。
根据风电机组结构特点与运行状况的特殊性,重点监测风电机组主轴承、齿轮箱、发电机的振动特征,为解决风电机组实际运行状态监测和故障诊断,提供了有效的技术支持和保障。
关键词:风力发电机组振动状态监测;主轴承、齿轮箱、发电机振动分析目前,随着我国逐步向环境友好型社会发展思路的转变,清洁能源越来越受到重视。
风力发电已经日益受到政府、企业和用户各方面的关注,特别是大规模的风电并网已经成为一种趋势,新型风电场的容量在电力系统中的比重在增加,风电场在电力系统中的运行价值也在日益显现,对风电机组安全稳定运行提出更高的要求。
随着风电机组低速载重轴承、齿轮箱、发电机等组成部件随运行时间延长、工况交替变化都可能出现各种失效故障,为避免恶性故障的产生,同时最大限度的减少维修成本,就必须在这些部件进入加剧磨损期前通过维护措施延长其使用寿命,并在其即将损坏前及时更换。
因此加强对风电机组振动的监测,及时发现故障隐患、快速分析、诊断、处理故障,对保障风电机组安全运行有重要意义。
1 风力发电机组振动监测系统我场采用阿尔斯通ALSPA Care Drivetrain风力发电机组振动监测系统,ALSPA Care Drivetrain系统由多台数据采集器DAU,交换机或路由器,一台服务器构成,系统采用B/S架构,它将安装在风电机组上的振动传感器信号送给DAU数据采集器,处理、分析数据后,将数据以各种丰富的图谱形式展示在客户端,使用人员能够通过web浏览器登陆Drivetrain系统查看监测数据,分析机组的运行状态。
风电机组的振动测量主要分为启机、亚同步、超同步这三个工况,可以根据实际来调整风电机组振动报警阀值,发电机转速0-600转为风电机组启动过程,主要测量各轴承座附近的振动情况;发电机转速600-1000转时处于亚同步状态,由于振动与负荷相关,功率越大,振动越高为防止运行中误报,则在1000-1200转增设工况三,针对风电机组运行状态调整报警阀值。
风力发电机组振动分析
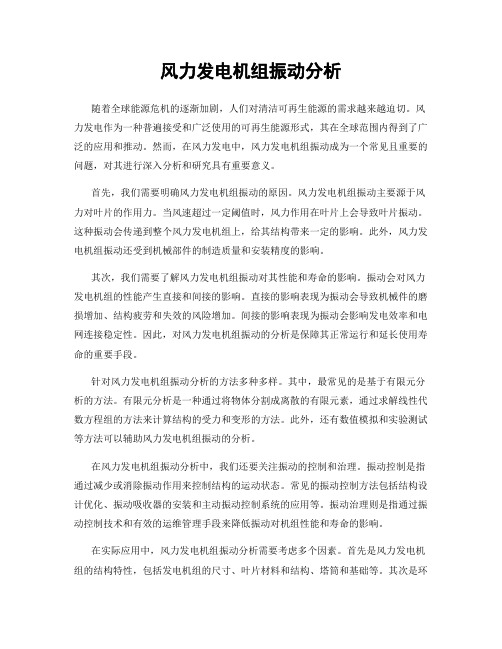
风力发电机组振动分析随着全球能源危机的逐渐加剧,人们对清洁可再生能源的需求越来越迫切。
风力发电作为一种普遍接受和广泛使用的可再生能源形式,其在全球范围内得到了广泛的应用和推动。
然而,在风力发电中,风力发电机组振动成为一个常见且重要的问题,对其进行深入分析和研究具有重要意义。
首先,我们需要明确风力发电机组振动的原因。
风力发电机组振动主要源于风力对叶片的作用力。
当风速超过一定阈值时,风力作用在叶片上会导致叶片振动。
这种振动会传递到整个风力发电机组上,给其结构带来一定的影响。
此外,风力发电机组振动还受到机械部件的制造质量和安装精度的影响。
其次,我们需要了解风力发电机组振动对其性能和寿命的影响。
振动会对风力发电机组的性能产生直接和间接的影响。
直接的影响表现为振动会导致机械件的磨损增加、结构疲劳和失效的风险增加。
间接的影响表现为振动会影响发电效率和电网连接稳定性。
因此,对风力发电机组振动的分析是保障其正常运行和延长使用寿命的重要手段。
针对风力发电机组振动分析的方法多种多样。
其中,最常见的是基于有限元分析的方法。
有限元分析是一种通过将物体分割成离散的有限元素,通过求解线性代数方程组的方法来计算结构的受力和变形的方法。
此外,还有数值模拟和实验测试等方法可以辅助风力发电机组振动的分析。
在风力发电机组振动分析中,我们还要关注振动的控制和治理。
振动控制是指通过减少或消除振动作用来控制结构的运动状态。
常见的振动控制方法包括结构设计优化、振动吸收器的安装和主动振动控制系统的应用等。
振动治理则是指通过振动控制技术和有效的运维管理手段来降低振动对机组性能和寿命的影响。
在实际应用中,风力发电机组振动分析需要考虑多个因素。
首先是风力发电机组的结构特性,包括发电机组的尺寸、叶片材料和结构、塔筒和基础等。
其次是环境因素,如风速、风向等。
此外,还需要进行动态模拟,考虑风力对发电机组的实际作用。
这些因素的综合考虑和对比分析对于振动分析的准确性和实用性至关重要。
风力发电机组在线振动监测系统及现场应用研究

风力发电机组在线振动监测系统及现场应用研究为了能够更好的避免和减少风力发电机故障带来的重大事故和安全隐患,并且在日常对风力发电机进行维护节省成本,在线振动监测系统必不可少。
本文介绍了在线监测系统的功能简介、工作原理、传感器测点选取和数据处理等关键技术及系统实际应用,对风电振动监测具有一定借鉴意义。
标签:风力发电机组;在线振动监测;现场应用1 系统功能简介风力发电机组工作条件通常比较艰苦,经常地处风沙四起的荒漠或海风盛行的海上,且在变速变载条件下运行。
因此,风电机组设备的相关零部件出故障的几率大大高出其他机械设备,为避免风电机组零件损坏造成的不必要经济损失,机组在线监测势在必行。
风电场中的在线监测系统,需对每一台机组都进行实时的状态监控与故障监测。
所以,监测系统采用分布式设计,主要由硬件和软件两个部分组成:硬件包括振动一体传感器、数据采集仪、现场服务器以及中心服务器等;软件部分包括数据传输和数据诊断分析与报警等功能。
系统软件设计较为复杂,数据传输功能,包括数据采集、数据存储、数据上传等单元;诊断分析功能,先进行信号提取,再进性处理,识别信号特征,接着对故障进行诊断,最后显示报警状态。
其中,采集的信号主要包括发电机前后轴承处的振动信号、发电机接地电压等信号。
2 系统工作原理目前,风力发电机组的故障检测与诊断技术有多种:振动检测、温度检测、声发射检测及润滑油分析检测等多种方法。
针对每种检测方法各有其优缺点:温度检测方法简单,但引起温度变化原因复杂多变;声发射检测技术通过故障设备本身发出的高频应力波信号检测,受周围环境噪声的干扰较小,但是相关测试设备费用贵、误报警率高,且对测试条件、测试环境以及测试信号的消噪预处理技术等环节要求较高;振动检测技术应用较为广泛,技术相对成熟,主要实时监测风电机组发电机前后轴承座表面的振动数据,这些实时的数据能够被规整在一个较长的周期内形成波形图,便于工作人员在这个周期内进行趋势分析,确定发电机前后轴承的工作情况,以及各个零件的健康状况,便于尽早发现发电机内部的零件损伤。
风力发电机组主机架振动分析

风力发电机组主机架振动分析风力发电机组主机架振动分析风力发电机组主机架振动分析是对风力发电机组运行过程中可能出现的振动问题进行研究和识别的过程。
振动是风力发电机组主机架运行时的常见现象,并且可能会对整个系统的稳定性和性能产生不利影响。
因此,进行振动分析是非常重要的,可以帮助工程师们确定振动的来源,并采取相应的措施来减小振动的影响。
以下是进行风力发电机组主机架振动分析的一些步骤:1. 收集数据:首先,需要收集风力发电机组运行过程中的振动数据。
这些数据可以通过传感器、监测设备或振动测量仪器进行收集。
数据的收集应该涵盖不同工作条件下的振动情况,包括不同风速、不同转速等等。
2. 数据处理:收集到的振动数据需要进行处理,以便更好地理解和分析。
可以使用数据处理软件进行数据的清洗、过滤和调整。
数据处理的目的是消除噪声和杂乱信号,使得振动特征更加清晰和可辨识。
3. 振动特征提取:在数据处理之后,需要提取出振动的特征参数。
这些特征参数可以包括振动的频率、幅值、相位等等。
通过振动特征的分析,可以帮助确定振动的来源和模式,进一步了解主机架的振动机制。
4. 振动源识别:通过振动特征的分析,可以确定振动的源头。
主机架振动的来源可能包括风扇、机械部件、电机等。
通过仔细观察振动特征的变化和振动频率的分析,可以识别出主机架振动的具体来源。
5. 振动控制措施:一旦确定了主机架振动的来源,可以采取相应的振动控制措施。
这些措施可能包括调整机械部件的平衡、加强固定、增加减振装置等。
振动控制的目标是减小振动的幅值和频率,提高系统的稳定性和性能。
6. 振动监测:在采取振动控制措施之后,需要对主机架进行定期的振动监测。
这可以通过在线监测系统或定期的振动测量来实现。
振动监测的目的是确保振动控制的有效性,并及时发现和解决可能的问题。
总之,风力发电机组主机架振动分析是一个复杂而重要的过程。
通过收集、处理和分析振动数据,确定振动的来源,并采取相应的措施来减小振动的影响,可以提高风力发电机组的稳定性和性能。
电力系统中的风力发电机组振动分析与优化
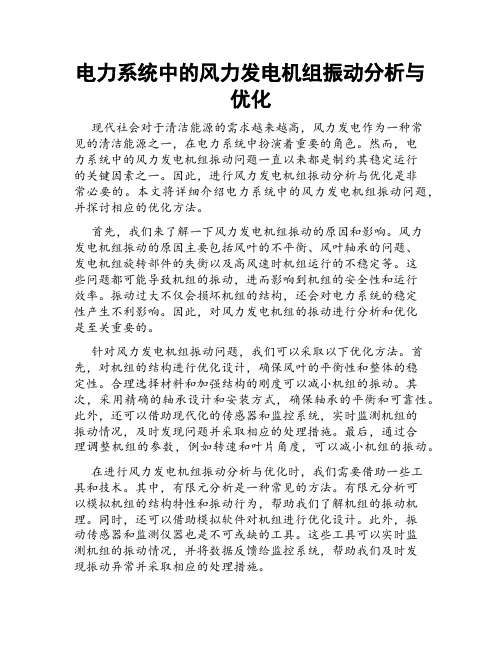
电力系统中的风力发电机组振动分析与优化现代社会对于清洁能源的需求越来越高,风力发电作为一种常见的清洁能源之一,在电力系统中扮演着重要的角色。
然而,电力系统中的风力发电机组振动问题一直以来都是制约其稳定运行的关键因素之一。
因此,进行风力发电机组振动分析与优化是非常必要的。
本文将详细介绍电力系统中的风力发电机组振动问题,并探讨相应的优化方法。
首先,我们来了解一下风力发电机组振动的原因和影响。
风力发电机组振动的原因主要包括风叶的不平衡、风叶轴承的问题、发电机组旋转部件的失衡以及高风速时机组运行的不稳定等。
这些问题都可能导致机组的振动,进而影响到机组的安全性和运行效率。
振动过大不仅会损坏机组的结构,还会对电力系统的稳定性产生不利影响。
因此,对风力发电机组的振动进行分析和优化是至关重要的。
针对风力发电机组振动问题,我们可以采取以下优化方法。
首先,对机组的结构进行优化设计,确保风叶的平衡性和整体的稳定性。
合理选择材料和加强结构的刚度可以减小机组的振动。
其次,采用精确的轴承设计和安装方式,确保轴承的平衡和可靠性。
此外,还可以借助现代化的传感器和监控系统,实时监测机组的振动情况,及时发现问题并采取相应的处理措施。
最后,通过合理调整机组的参数,例如转速和叶片角度,可以减小机组的振动。
在进行风力发电机组振动分析与优化时,我们需要借助一些工具和技术。
其中,有限元分析是一种常见的方法。
有限元分析可以模拟机组的结构特性和振动行为,帮助我们了解机组的振动机理。
同时,还可以借助模拟软件对机组进行优化设计。
此外,振动传感器和监测仪器也是不可或缺的工具。
这些工具可以实时监测机组的振动情况,并将数据反馈给监控系统,帮助我们及时发现振动异常并采取相应的处理措施。
此外,在风力发电机组振动分析与优化中,我们还需要考虑到振动对电力系统的影响。
大幅度的振动不仅会损坏机组自身,还会产生噪音和振动波动,对机组周围环境和人体健康造成影响。
因此,在设计风力发电机组时,我们需要充分考虑振动问题,通过采用合适的振动消除措施,减小振动对周围环境和人体的影响。
风力发电机组在线振动监测系统及现场应用研究

大陆桥视野·2016年第22期 123风力发电机组在线振动监测系统及现场应用研究冀赛龙 高 伟 / 沈阳华创风能有限公司【摘 要】近年来,风力发电机组振动状态在线监测技术在风电场发挥的重要作用越来越得到人们的重视。
在线振动监测系统可以及时发现风力发电机组故障的早期振动征兆,揭示故障的原因、程度、部位、发展趋势等,便于风力机维护,避免和减少重大事故的发生,节约成本。
【关键词】风力发电机组;在线震动监测;现场应用引言风电机组工况与一般机械相比较为复杂,时常在变速变载的条件下工作。
风电机组在线振动监测系统在风电机组各部件(齿轮、轴、轴承)损坏之前,便能给出设备的运行状态报告进行预报警,使现场 人员能够制定合理的维修计划,及时对设备进行维修,从而避免了由损坏部件的运转造成关联部件的损伤。
一、风力发电机组在线振动监测系统架构对于单个风电机组的发电机,在线监测系统设计包括:声发射/振动一体传感器,数据传输线,数据采集终端,数据处理软件。
主要采集传动系统和发电机前后轴承处的声发射/振动信号,发电机的接地电压等信号。
对于某风电场,采用分层的管理架构对每一台机组进行实时的状态监控和故障诊断,监测系统主要分为硬件和软件两部分,硬件主要包括振动传感器、8通道数据采集仪、现场服务器和中心服务器,软件部分如下图1:图1 风力发电机组在线振动监测系统软件组成部分二、监测系统工作原理本监测系统主要实时测试布置在风电机组发电机前后轴承座表面的声发射和振动数据。
对于声发射数据,通过时域信号特征参数统计的分析方法记录下每一时刻的测试结果,在一个较长的监测周期内进行趋势分析,确定发电机前后轴承的健康状况,提早发现发电机内部损伤。
对于振动数据,通过频域信号处理分析确定振动幅值是否超过相关标准要求,并结合机组当前工作状态,判断下一步需要进行的动作。
经过对风电机组发电机状态的长期监测,最终形成一个完整机组部件故障数据库,为进一步采用FEMA故障诊断方案确定发电机故障来源奠定基础。
风力发电机组振动特性分析与优化设计

风力发电机组振动特性分析与优化设计一、引言随着环境意识的增强和对可持续能源的需求日益增加,风力发电作为一种可再生能源正得到广泛关注和应用。
而风力发电机组作为风力发电的核心设备,其中的振动特性对风力发电机组的性能和寿命起着至关重要的影响。
因此,进行风力发电机组振动特性的分析与优化设计对于提高其工作效率和可靠性具有重要意义。
二、风力发电机组振动特性分析1. 振动特性的分类风力发电机组的振动特性可分为结构振动和机电耦合振动。
结构振动主要指风力发电机组在运行过程中由于外部环境或内部因素引起的结构本身的振动情况。
机电耦合振动则是指风力发电机组在工作状态下,由于风轮叶片和发电机等设备的相互作用而引起的振动。
2. 振动特性的影响因素风力发电机组的振动特性受多种因素影响,其中主要包括以下几个方面:(1) 风轮叶片特性:风轮叶片的质量、弹性模量、自然频率等参数直接影响振动特性。
(2) 发电机质量和结构:发电机的转子质量均衡性、轴承刚度和阻尼等因素对振动特性有重要影响。
(3) 塔筒和机座:塔筒和机座的刚度和阻尼是风力发电机组振动特性中不可忽视的因素。
(4) 外界环境:风速、风向、地震等外界环境因素也会对风力发电机组的振动特性产生影响。
三、风力发电机组振动特性优化设计1. 结构优化通过采用合理的材料、结构和工艺,可以降低风力发电机组的结构振动。
例如,优化风轮叶片的形状、增加叶片的刚度和质量均衡,都可以有效减小风力发电机组的结构振动。
2. 整体设计优化在风力发电机组的整体设计中,应考虑机电耦合振动问题。
通过合理设计发电机转子和轴承系统,增加系统的阻尼,可以减少机电耦合振动对整个风力发电机组的影响。
3. 控制系统优化合理的控制系统可以起到减小风力发电机组振动的作用。
通过引入主动振动控制技术,使用传感器和执行器对发电机组进行实时调节,可以减小振动对整个系统的影响。
四、案例分析以一台某型号2MW风力发电机组为例,进行振动特性分析与优化设计。
风力发电机组故障诊断系统说明书
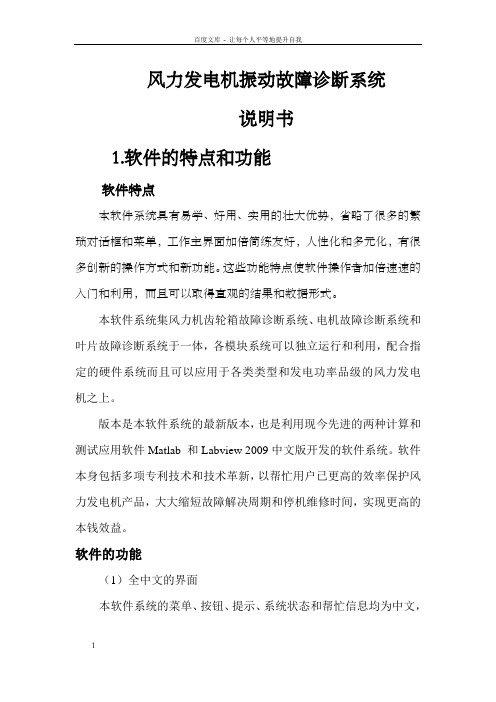
风力发电机振动故障诊断系统说明书1.软件的特点和功能软件特点本软件系统具有易学、好用、实用的壮大优势,省略了很多的繁琐对话框和菜单,工作主界面加倍简练友好,人性化和多元化,有很多创新的操作方式和新功能。
这些功能特点使软件操作者加倍速速的入门和利用,而且可以取得直观的结果和数据形式。
本软件系统集风力机齿轮箱故障诊断系统、电机故障诊断系统和叶片故障诊断系统于一体,各模块系统可以独立运行和利用,配合指定的硬件系统而且可以应用于各类类型和发电功率品级的风力发电机之上。
版本是本软件系统的最新版本,也是利用现今先进的两种计算和测试应用软件Matlab 和Labview 2009中文版开发的软件系统。
软件本身包括多项专利技术和技术革新,以帮忙用户已更高的效率保护风力发电机产品,大大缩短故障解决周期和停机维修时间,实现更高的本钱效益。
软件的功能(1)全中文的界面本软件系统的菜单、按钮、提示、系统状态和帮忙信息均为中文,降低操作者的门坎。
(2)采用国际标准单位本软件系统中提供的计算数据、图形信息及标识信息均采用国际标准单位,便于查询和换算。
(3)故障报表生成软件系统在对数据进行处置,可以生成故障报表即图例,和打印机连接可以直接输出。
(4)多种数据接口软件系统具有丰硕数据接口,程序可以对多种数据格式进行处置,而且以多种格式进行输出。
2.软件的安装系统要求为了保证系统能够正常运行,建议计算机应知足以下配置:(1)操作系统:中文Windows9X/2000/XP/vista,(西文环境需外挂中文平台)。
(2)运行配置:奔腾Ⅲ以上微机、CPU主频800MHz以上、内存256MB以上、光驱或接口(3)安装介质:CD-ROM、U盘(4)硬盘空间:需60M左右,软件安装本软件系统的编程语言为MathWorks公司的Matlab 和NI公司的Labview 2009中文版,所以在运行时需要预先安装比两种语言更高版本的软件应用程序。
浙江中自庆安新能源风电远程在线振动监测与分析系统ppt课件

分工况监测技术
0.05 g @ 137 kW 0.3 g @ 564 kW
振动与负荷相关,功率越大,振动越高。
分工况监测技术
分工况监测技术
分工况监测技术
分频段跟踪技术
滚动轴承故障特征频率
•
• FTF=保持架通过频率 • BPFI=滚珠内环通过频率 • BPFO=滚珠外环通过频率 • BSF=滚珠旋转频率
• 利用信息技术、降低工作强度:可在现场 或远程直接监测风机运行工作状态及相关 数据,从而大大降低机组日常监测强工作 强度。
• 风场地处偏远,通讯不便;专业诊断人员 少,而风机数量巨大。通过对振动数据的 分析,及早发现设备的潜在隐患,遏制故 障发展,避免重大事故发生,大幅减少维 修成本。
风电监测系统结构总图
远程升级和远程维护
远程升级
通过远程拨号或INTERNET 同时实现对RMD2000下所有硬件的软件及固件升级 数据库以及操作系统的升级 目的:让用户的系统永远是最新的、功能最强大的
F0 = 0.4485 Hz
FG3 =705 Hz
Pignon Z = 20
F3 = 25.18 Hz FG2 = 204.37 Hz
F2 = 10.22 Hz
F1 = 2.62 Hz
Solaire Z = 19
Roue Z = 78
分频段跟踪技术
分频段跟踪技术
主要监测参数
• 总振值:各振动测点的振动速度或加速度有效值 • gD值(加速度解调值):采用加速度解调技术获得gD值(对轴承和齿
振动监测点图
振动监测点
通道 Ch1 Ch2 Ch3 Ch4 Ch5 Ch6 Ch7 P1
位置 主轴承 齿轮箱输入轴轴承 齿轮箱环形内齿圈 齿轮箱输出轴轴承 齿轮箱输出轴轴承 发电机前轴承 发电机后轴承 齿轮箱输出轴转速
基于小波包神经网络的风力发电机组振动故障诊断系统设计

基于小波包神经网络的风力发电机组振动故障诊断系统设计发布时间:2022-01-10T02:49:24.925Z 来源:《科技新时代》2021年11期作者:彭兴国郑海波[导读] 分析轴承缺陷信息造成的故障频率成分的变化规律。
上述方法在风力发电机组的不同故障模式下有着不同的应用。
粤电集团贵州有限公司贵州省贵阳市邮编550000摘要:随着“碳中和”战略的提出,对可再生能源的需求越发迫切。
作为一种分布广泛、获取相对容易的可再生能源,风能在我国取得了飞速发展。
但是,风力发电机组常处于交变载荷的恶劣工作环境下,可靠性不高,迫切需要一种针对其真实工况下的风力发电机组智能故障诊断系统。
针对这一问题,本文基于小波包神经网络进行风力发电机组振动故障诊断系统设计,根据工程现场完成了硬件系统的搭建,使用小波包神经网络算法完成了诊断系统的实现流程,最后通过实际案例验证了本文提出的风力发电机组诊断故障诊断系统能够准确实现振动故障诊断功能,对风力发电机组提高发电效益,提升机组稳定性有着重要意义。
关键词:风力发电机组,振动故障,设计,小波包神经网络0 引言风力发电作为新兴的清洁能源,发展时间较短,针对于风力发电机组的振动故障诊断系统的研究尚处于初级阶段[1]。
Yang W等[2]基于EMD方法设计了风力发电机组动力传动系统状态监测与故障诊断系统,有效处理了风力发电机组的不平稳振动信号。
Ricci R 和 Pennacchi P[3]在EMD方法的基础上引入了择优指数实现IMF的自动选取,该方法对于瞬时信号有着更好的处理效果。
Eren L[4]使用小波包分析处理定子电流,分析轴承缺陷信息造成的故障频率成分的变化规律。
上述方法在风力发电机组的不同故障模式下有着不同的应用。
然而,由于真实环境下,风力与风速的随机性,导致风力发电机组常在不定载荷和交变载荷下工作,发电机组的齿轮箱、主轴、轴承等零部件经常受到冲击载荷作用,因此针对于风力发电机组的故障诊断系统设计尤为重要。
风力发电机组振动特性分析与控制
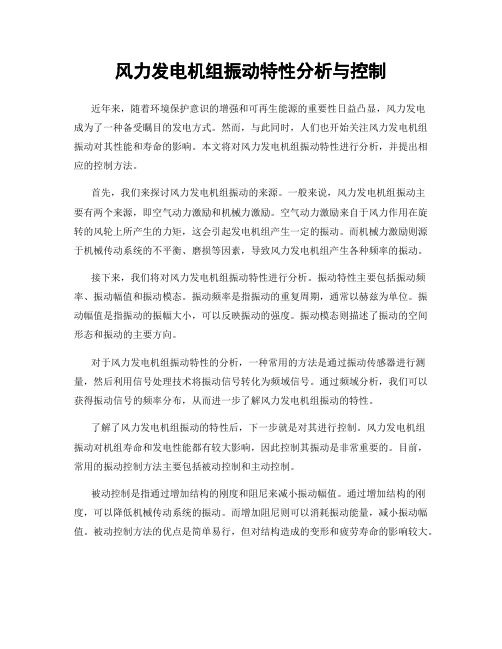
风力发电机组振动特性分析与控制近年来,随着环境保护意识的增强和可再生能源的重要性日益凸显,风力发电成为了一种备受瞩目的发电方式。
然而,与此同时,人们也开始关注风力发电机组振动对其性能和寿命的影响。
本文将对风力发电机组振动特性进行分析,并提出相应的控制方法。
首先,我们来探讨风力发电机组振动的来源。
一般来说,风力发电机组振动主要有两个来源,即空气动力激励和机械力激励。
空气动力激励来自于风力作用在旋转的风轮上所产生的力矩,这会引起发电机组产生一定的振动。
而机械力激励则源于机械传动系统的不平衡、磨损等因素,导致风力发电机组产生各种频率的振动。
接下来,我们将对风力发电机组振动特性进行分析。
振动特性主要包括振动频率、振动幅值和振动模态。
振动频率是指振动的重复周期,通常以赫兹为单位。
振动幅值是指振动的振幅大小,可以反映振动的强度。
振动模态则描述了振动的空间形态和振动的主要方向。
对于风力发电机组振动特性的分析,一种常用的方法是通过振动传感器进行测量,然后利用信号处理技术将振动信号转化为频域信号。
通过频域分析,我们可以获得振动信号的频率分布,从而进一步了解风力发电机组振动的特性。
了解了风力发电机组振动的特性后,下一步就是对其进行控制。
风力发电机组振动对机组寿命和发电性能都有较大影响,因此控制其振动是非常重要的。
目前,常用的振动控制方法主要包括被动控制和主动控制。
被动控制是指通过增加结构的刚度和阻尼来减小振动幅值。
通过增加结构的刚度,可以降低机械传动系统的振动。
而增加阻尼则可以消耗振动能量,减小振动幅值。
被动控制方法的优点是简单易行,但对结构造成的变形和疲劳寿命的影响较大。
主动控制则是指通过控制系统主动地对振动进行干扰或补偿来实现振动控制。
主动控制方法可以更灵活地对振动进行控制,并且对结构的影响较小。
常见的主动控制方法有阻尼器、质量调节器和振动补偿器等。
除了被动控制和主动控制外,还可以结合智能控制方法来实现风力发电机组的振动控制。
直驱风力发电机组在线振动监测系统技术方案(最终确认版)20130527

金风直驱风力发电机组TCM在线振动监测系统技术方案(仅适用于国华赤城六期、柳山一期项目)北京观为时代科技有限公司(为丹麦格莱音(Gram&Juhl)中国合资公司中方母公司,建有MHCC TM设备健康体检中心)二零一三年五月目录一. 技术方案与系统主要设备指标 (3)1.1丹麦格莱音TCM®集成的风机状态监测系统简介 (3)1.2 金风直驱风机在线振动监测系统方案及主要技术指标 (4)1.2.1在线振动监测仪(M-System)技术性能指标 (5)1.2.2 加速度振动传感器的主要技术指标 (5)1.2.3 转速信号的获取 (6)1.2.4 在线振动监测仪安装与供电 (6)1.2.5在线振动监测仪的通讯 (8)1.2.6格莱音TCM在线振动监测与故障诊断分析软件系统 (8)1.2.7在线振动监测系统与SCADA系统的对接 (10)二. 技术支持与培训 (10)三. 质量保证与软件升级服务 (10)四. 供货范围 (10)签字页: (12)一.技术方案与系统主要设备指标1.1丹麦格莱音TCM®集成的风机状态监测系统简介丹麦格莱音(Gram&Juhl) 是全球风力发电机状态监测领域的领导者。
自1999年以来,格莱音已经为全球超过6000台风力发电机装备了其先进的TCM®风机状态监测系统,并提供及时可靠的远程诊断分析服务,是目前全球装机量最大的风力发电机组状态监测系统提供商。
格莱音(Gram&Juhl)也是全球最大的海上风力发电机状态监测系统提供商。
TCM®系统已经为全球超过1,500台海上风力发电机组提供在线振动监测和诊断分析服务。
格莱音(Gram&Juhl) TCM®系统为全球主要风机制造商和风电运营商广泛应用。
TCM®在中国已经成功应用于国电龙源、中国大唐、国华能源等风电场。
格莱音(Gram &Juhl)的TCM®系统通过了ISO 9001质量体系认证,取得了德国劳氏(GL)认证、美国UL认证以及丹麦FORCE认证,通过对超过5000台风机振动监测和分析实践,特别是对海上风力发电机组状态监测的规模应用经验,使TCM®成为目前响应能源局《导则》最佳的系统。
风力发电机组的振动与稳定性分析

风力发电机组的振动与稳定性分析随着清洁能源的快速发展,风力发电已经成为了世界各地的一种重要的可再生能源。
风力发电机组作为关键组成部分,其振动和稳定性的分析与研究具有重要的意义。
本文将从风力发电机组的振动来源、对振动进行分析和评估的方法以及提高稳定性的措施等方面展开讨论。
首先,风力发电机组的振动主要源于四个方面:风力荷载、机械传动、转子不平衡和地震荷载。
风力荷载是最主要的振动来源之一,风的速度和方向的变化将对风力机的振动产生直接影响。
机械传动中的轴承、齿轮等零部件的不均匀裂纹或损伤也会引起机组的振动,严重时可能导致设备故障。
转子的不平衡是机组振动的常见问题,其主要原因是转子重量分布不均匀或装配质量不精确。
地震荷载对风力发电机组的振动也具有重要影响,尤其是位于地震多发地区的机组。
其次,对于风力发电机组的振动进行分析和评估是保证其稳定性的重要工作。
一种常用的方法是利用加速度传感器测量振动信号,再通过数字信号处理等技术手段对振动信号进行分析。
通过对机组振动数据的采集和分析,可以揭示机组在运行过程中的振动特性和振动频谱,为机组的参数优化和故障诊断提供依据。
此外,还可以利用有限元分析方法对机组的结构进行仿真模拟,通过对模拟结果的分析,对机组的振动情况进行评估和优化。
最后,为了提高风力发电机组的稳定性,需要采取一系列的措施。
首先,可以通过优化风力机的结构设计,减小风力机的振动幅值。
例如,在风力机的旋翼和塔筒结构中采用合适的材料和结构设计,可以有效地减小机组的振动。
其次,对风力机组的传动机构进行定期维护和检修,确保机组运行时的传动系统处于良好的工作状态,减少振动源的产生。
另外,在地震多发地区,可以采用增加机组的抗震设备,提高机组在地震荷载下的稳定性。
综上所述,风力发电机组的振动与稳定性分析对于提高风力发电系统的可靠性和性能具有重要意义。
通过对振动来源的分析和评估方法的运用,可以有效地优化风力发电机组的设计和维护,从而提高其振动和运行的稳定性。
- 1、下载文档前请自行甄别文档内容的完整性,平台不提供额外的编辑、内容补充、找答案等附加服务。
- 2、"仅部分预览"的文档,不可在线预览部分如存在完整性等问题,可反馈申请退款(可完整预览的文档不适用该条件!)。
- 3、如文档侵犯您的权益,请联系客服反馈,我们会尽快为您处理(人工客服工作时间:9:00-18:30)。
XiA nW eridaM easurement& C ontrolC o.,ltd
★ 便方快捷的风电机组现场测试功能(巡检计划) ★ 持支长时间数据采集:3MBytes/测点,60秒@ 5.26kSPS ★ 高灵敏度:微弱信号的检测能力 ★ 数大据量存储:高达1G的存储空间 ★ 便简易用:体积小巧、便于携带、友好的图形化用户界面 ★ 电池供电:连续工作8小时,适应风电场长时间采集的要求 ★ 固坚耐用:IP65 ★ 磁电兼容:CE认证
w iD A Q ce性
能
特
点
适
针对风电机组低速部件进行有效的振动监测
用
风力发电机组在达到额定功率时,主轴的转
速仅有 10 ̄30RPM ,低速转动部件的冲击信号幅
于
值很小,传统的硬件解调分析方法基本无效。
WTAnalyser 配备了高性能数据采集器
风
wiDAQce ,可以提供高精度、 长时间数据采集能
力;同时上位分析软件提供了威锐达独有的
电
gPK 数 字 解 调 技 术 , 通 过 该 技 术 能 够 检 测 非 常 微 时域波形无法观察到冲击
振
弱的冲击信号,适用于低速轴承(如风电主轴承) 的损伤检测。
动 变工况监测诊断
通过gPK可以检测到微弱的冲击信号
分
由于现场风况的变化,风电机组在运行中会出现转速和负荷的变化,这就导致传
风
巡 检 管 理
户 可用以创建、 管理风电场,可以针对风机类型制定合适的测量方案,并根据机
电
组分布情况制定巡检计划。
机
组
振
动
风电场编辑管理
分
测量方案管理
析 数 据 分 析
巡检计划管理
软
◆ 便 易 用方的 查 询 功 能 , 支 持 起止时间、 ◆支持时域、 频谱、 包络、 包络谱等分析方法。
XiA nW eridaM easurement& C ontrolC o.,ltd
XiA nW eridaM easurement& C ontrolC o.,ltd
分析案例 1:主轴承磨损 STEP 1
信号原始数据,由于转速波动,传统的包络谱方式难以有效应用
谱线杂乱,无法进行分析
STEP 2 提取瞬时转速
STEP3
采用威锐达转速提取技术后通过gPK包络谱 可 以 清 晰 识别主轴承磨损故障。
分析案例2:齿轮箱输入级故障诊断
STEP 1 信号原始时域波形,由于转速波动,传统频谱图难以进行有效分析。
谱线杂乱,无法进行分析
分 析 案 例
STEP 2
通过威锐达转速提取技术对数据进行处理后可以清晰识别齿轮磨损故障特征
机组列表、 信号类型、 测量位置等自定义
件
查询。
◆ 单 游 标 、 带游标、 峰值游标、 倍频游标、 边 频游标功能,方便进行分析。
◆ 丰 富 的 右 键分析 功能: 多 种 单 位选择、 创 建注释以及分析图像 导出功能。
u 可以将多条数据同时进行分析,方便进行比对;分析窗口下部数据区可实时显示测量信息、 总值、 游标测量值等信息。
XiA nW eridaM easurement& C ontrolC o.,ltd
自动状态评估
风
动 状 态 评自估功能集成德国成熟的VDI评估标准,可以快速了解机组振动状况 , 评 估 结 果 可 以
导出为Excel文件,方便存档、 汇报、 管理。
电
机
组
振
动ห้องสมุดไป่ตู้
分
智能统计分析
计 分 析 功统能提供灵活的统计变量设置功能,可以对数据进行时域、 频域、 包络及包络谱统计,
1振动通道 + 步1通同道 3.6mA @4 V2 加速度,速度,位移 谱图,时域波形,相位,RMS,峰值,峰-峰值 ±40V 是 16bit > 09dB 最大40 HKz 在0.5 zH  ̄0 H2Kz范围内设置 在0.1 zH  ̄0 H4Kz范围内设置 最大102.4kHz 400  ̄56 020线(单通道) 最长3Mbytes每测点,60Sec@25.6kSPS 信号范围:±40V,传感器供电电源:+5V,测量范围:0.1Hz  ̄00 01Hz
威锐达将为用户提供专业化的产品和服务,助力用户企业的发展。
风电机组状态监测的意义 风机振动监测系统主要针对风力发电机组的主轴轴承,齿轮箱轴承,齿轮和发电
机前后轴承进行监测。对风力发电机组进行振动监测具有以下意义:
n 提高设备可用性,避免非计划停机 n 优化维修工作计划,减少停机损失 n 避免部件间接损害,减少维修成本 n 分析部件失效原因,为设计和制造的改进提供依据
统频谱分析技术无法得以使用,威锐达采用基于瞬态转速跟踪的阶次分析技术,可消
析
除转速波动对分析结果的影响。
的
变工况状态自动评估
采用国际标准对变工况情况下的风电机组振动状态进行定量评估,方便快速了解
解
机组振动健康状况。
决
方
案
迄 今 已 协 助 龙 源 电 力 完 成300余台 风 电 机 组 的 测 试
析
可以设置多条变量进行统计分析。系统对统计数据可进行自动偏差报警。
软
件
统计数据自动偏差报警
自定义统计变量
报表生成
表 生 成 功报能 允 许 用 户 自 由 定 义 报 表 中 的 项 目 , 并 对 用 户 选 择 的 多 条 数 据 进 行 图 谱 的 运 算 处 理 并输出到报表中,方便用户形成机组振动诊断报告。
wiDAQce技术参数
测量参数 输入信号通道 ICP恒流电源 测量参数 测量类型 输入信号范围 自动量程功能 A/D 动态范围 频率范围 高通滤波器 低通滤波器 采样频率 FFT分辨率 采样长度 转速输入 硬件参数 处理器 操作系统 SDRAM 闪存 MMC/SD卡 显示 按键 封装 电池 工作时间 通信 规格 重量 温度 湿度 标准配置
XiA nW eridaM easurement& C ontrolC o.,ltd
自定义报表,灵活定义输出项目
自动计算图谱,生成word报告
ARM9@ 040MHz Windows EC.Net .24 64MB 1GB 可支持的最大存储容量为2GB(可选配) 3.5寸TFT彩色液晶屏,320 x40 ,265536色,带背光 24个按键(带数字和字母输入),自动背光 IP65(防尘防水) 锂电池组,3500mAH@7.4V >8小时 USB,RS232 190 x10 1x8 m3m 700 g -10 ot +0 5℃ 作工温度,-20 ot +0 6℃ 存保温度 95% HR非冷凝 手持仪器、电源适配器、振动传感器、USB电缆、护套、用户手册等
风力发电机组振动分析系统
WTAnalyser
(传真)
风 力 发 电 机 组 振 动 分 析 系 统
关于威锐达
西安威锐达测控系统有限公司是一家专注于先进测量技术开发、 应用的高科技公 司,拥有非常成熟的高性能手持振动测量仪器系列及风电振动分析系统解决方案, 针对风力发电机组振动监测的特殊性,威锐达形成了专有的技术体系,能够解决风 力发电机组振动监测的技术难点问题。威锐达是通过国家认定的高新技术企业,自 成立以来,先后获得了科技部中小企业创新基金扶持、 陕西省重大科技创新项目立 项等荣誉。
风力发电机组振动分析系统构成 系 统 由 风 电 机 组 状 态 分 析 软 件 单 机 版 及 手 持 数 据 采 集 终 端wiDAQce构成 。
风电机组状分析系统单机版
振动分析工程师 -巡检计划制定 -振动分析诊断 -分析报告生成
巡检工程师
wiDAQce -现场数据采集
……
系统构成方案
XiA nW eridaM easurement& C ontrolC o.,ltd