S在广汽丰田物流系统的应用及借鉴意义
【物流规划】-广汽丰田物流模式探究

【物流规划】-广汽丰田物流模式探究广汽丰田汽车的物流充分运用了丰田生产方式(TPS)的准时化(JIT)和働自动化理念,以实现最佳物流品质、最低物流成本为目标,践行准时化物流和TPS的持续改善,致力于追求世界第一的物流模式,特别是借助于股东方日本丰田的经验优势,这些理念和目标已深深融入到汽车物流运作的每一个环节,形成明显的特色。
丰田目前基本上专注于对汽车的研发、设计、制造、销售及售后服务等领域,而物流业务都是采取外包的方式,委托物流供应商来实现。
“丰田为了控制成本,实现平准化生产,在供应链管理中实行‘零库存’方式。
所谓的‘零库存’当然不是完全没有库存,而是指没有多余的不必要的库存,设定的库存是可以维持生产需要的最少量的库存。
丰田通过有效地降低物流过程的库存,很好地控制了各环节的成本。
”这种JIT物流方式和现在广州本田和东风日产等汽车厂家的模式有所不同。
在零部件物流方面,广汽丰田为满足顾客需求,实现市场动向、工厂生产和零部件采购的同期化管理,全面采用了同步物流和循环取货的零部件物流模式。
“同步物流,是生产和供应之间的最短连接,快速高效,库存最小,体现了精益物流的精髓——消除一切浪费。
广汽丰田在项目规划时,就将50%以上货量的零部件布局在工厂周边,建立同步物流体系。
同步物流的信息,由生产线控制系统直接传送,就是说,我们将周边供应商完全纳入厂内工程系统。
可以说,运用最新的理念,进行前瞻性的规划布局,是广汽丰田物流成功的起点。
”“循环取货的特点是高效、准确、灵活,是供应链物流最有效的运输模式,也是中国汽车零部件物流发展的方向。
广汽丰田是中国汽车物流业‘循环取货’的先行者,也是其理论和方法的集大成者。
早在2006年,广汽丰田第一款车‘凯美瑞’投产时,就以丰田全球样板工厂的定位,导入了‘循环取货’的物流模式。
而丰田式的‘循环取货’最大的特色,是每个环节融入丰田生产方式的JIT理念,作‘平准化’的物流供应。
比如物流中转仓(Cross Dock),除了进度吸收,更重要的功能是进行与生产同步的平准化作业,这是一个操作过程,而非单纯的仓储功能。
TPS在广汽丰田零部件厂内物流系统中的应用
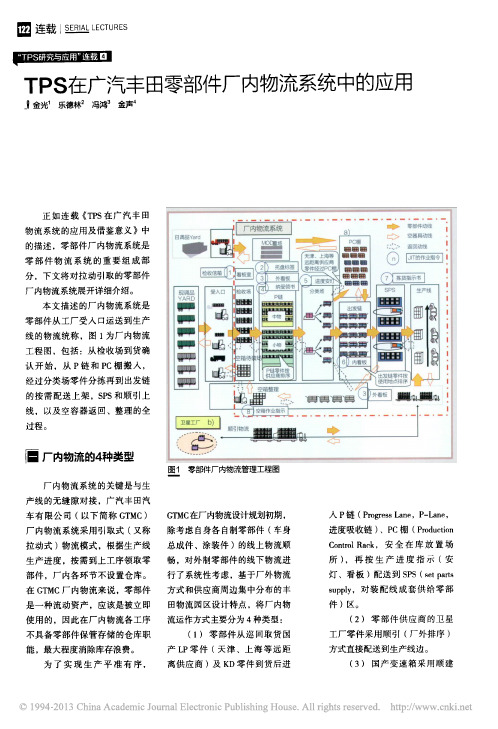
使 用状态
分割 进度 数进一 步细
化 就 是平 准 化 水 平 的 进 一 步 提
子
再 到 SP 区 ( 或 生 产线 ) S
广州地 区以外 因为运输周 期较长
( 如无 对策则 对应 生产计 划变更 的 响应 周期 长 ), 零 部件 出厂时 对应 的生产顺 序 尚未确定 , 这些 课 题都需 要在 厂 内物 流环节逐 一
产 线 出现 异 常, G M C 停 止 向供 T 应 商下达取 货指令使包 括空 器具 返 回的物流 停止 , 后续 恢复生产
四 连 互 生 CT E 载渔旦 LE U尺 二 S
在不同 的 P 链
表1 不同线路供应商取货便数及对应p 链数
. . 睡藏 差. . . . . 跪泣自. 口且四 到 . . 目画回 参曰
部件 几乎完全相同
生 产指示 在供 应商完 成排序 ( 分
类 ) 再 进 行 JI 引取 配送 T 对于 物 流距 离较远 (卫星工厂之外的 ,
使用, 则分割进度数> P 链数,
2加9 年再 次分 割进 度 数 二 ( 日 6 3 取货便数可为 l 2 3 4 6 9
12 13 18 36 ), P 链 数 二 , 29
参考
TPS
在广汽 丰 田物 流系统 的应 用及借 鉴 意义 (上 ) 中装车顺序图 ( 图
) 3 和本 文图 2 , 厂内运输链最多 可 容纳 16 个托 盘 , G M C 提 前 0 T 60 分钟 向供应商下 达进度需求 , 供 应 商 厂 内排 序 需要 1 分 钟 , 0 座椅 运 输 车 辆 在 供 应 商 装 车 一
内物流 , 图 2 是座椅 配送 的工 程
图
在库
供应商 没有空托 盘时 也会
智能仓储———丰田叉车带来无限可能

精挑细选的“尖子生”未来的智能物流和智能仓储的发展取决于第三方物流、电子商务、全冷链生鲜配送等新兴物流方式,这些改变会从纵向改变上下游客户市场,除了需要节约不断上涨的人工成本,更重要的是对于处理速度、管理效率和用户体验,这些需求在未来会急剧上升,自动化物流仓储系统是适应新兴物流方式的最佳解决方案。
作为叉车的主战场———装卸货环节,丰田推出了集丰田安心科技和出众耐久性于一身的8系列电动平衡重叉车,它可以实现更高效安心的作业———搭载丰田S A S 主动式稳定系统,不仅可以防止急转弯时的倾翻事故,还能提升高举升作业时的装卸稳定性和效率。
此外,I P X 4防水等级可实现360度的防水,可轻松应对雨天的室外装卸货作业。
在水平搬运环节,室内外可兼用、最大牵引重量达6吨的4C B T /C B T系列电动牵引车能为制造业实现多种类、少量化的高效点对点运输,包括零部件入库和上线补给作业。
得益于多样化的品牌背景,丰田产业车辆集团集结了欧、美、日市场仓储产品和存储理念之大成,能根据客户的保管量和品项、周转率、作业形态等做出贴合客户实际需求的解决方案。
对于丰田叉车的客户来说,挑战的不是哪一种叉车,而是在每个区域采用哪种物料搬运的解决方案。
而丰田在这方面绝对是一个全能选手,正如丰田织机制定的服务行动———“亲切、切实、快速、合理”四个标准一样,产品所带来的亲和力也会朝着这个方向发展。
在入库环节,B T旗下有“仓库赛车手”之称的B TL P E 电动托盘车无疑是高负荷水平搬运工况的不二之选,最高负载可达2.5吨,最高行驶速度可达12k m /h ,得益于P o w e r t r a k 系统的驱动轮悬浮结构,在驾驶L P E 进行出入库作业时,几乎感觉不到任何路面的落差或不平整。
智能仓储———丰田叉车带来无限可能文/本刊记者郭浩2017年是丰田叉车母公司丰田自动织机成立91周年,91年历史沉淀的不仅仅是连续14年蝉联全球销量冠军的辉煌,更有以精益管理、精益制造、精益物流服务客户、贡献社会的企业理念。
浅谈丰田公司的实时物流
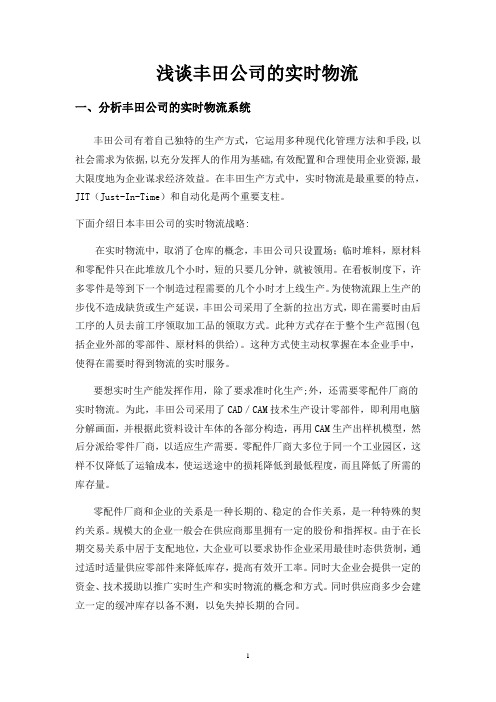
浅谈丰田公司的实时物流一、分析丰田公司的实时物流系统丰田公司有着自己独特的生产方式,它运用多种现代化管理方法和手段,以社会需求为依据,以充分发挥人的作用为基础,有效配置和合理使用企业资源,最大限度地为企业谋求经济效益。
在丰田生产方式中,实时物流是最重要的特点,JIT(Just-In-Time)和自动化是两个重要支柱。
下面介绍日本丰田公司的实时物流战略:在实时物流中,取消了仓库的概念,丰田公司只设置场;临时堆料,原材料和零配件只在此堆放几个小时,短的只要几分钟,就被领用。
在看板制度下,许多零件是等到下一个制造过程需要的几个小时才上线生产。
为使物流跟上生产的步伐不造成缺货或生产延误,丰田公司采用了全新的拉出方式,即在需要时由后工序的人员去前工序领取加工品的领取方式。
此种方式存在于整个生产范围(包括企业外部的零部件、原材料的供给)。
这种方式使主动权掌握在本企业手中,使得在需要时得到物流的实时服务。
要想实时生产能发挥作用,除了要求准时化生产;外,还需要零配件厂商的实时物流。
为此,丰田公司采用了CAD/CAM技术生产设计零部件,即利用电脑分解画面,并根据此资料设计车体的各部分构造,再用CAM生产出样机模型,然后分派给零件厂商,以适应生产需要。
零配件厂商大多位于同一个工业园区,这样不仅降低了运输成本,使运送途中的损耗降低到最低程度,而且降低了所需的库存量。
零配件厂商和企业的关系是一种长期的、稳定的合作关系,是一种特殊的契约关系。
规模大的企业一般会在供应商那里拥有一定的股份和指挥权。
由于在长期交易关系中居于支配地位,大企业可以要求协作企业采用最佳时态供货制,通过适时适量供应零部件来降低库存,提高有效开工率。
同时大企业会提供一定的资金、技术援助以推广实时生产和实时物流的概念和方式。
同时供应商多少会建立一定的缓冲库存以备不测,以免失掉长期的合同。
丰田公司将JIT生产体制和销售网络相结合,将日本全国经销商的电脑和丰田总公司的电脑连网,销售人员可以将客户定货的信息实时通知生产线,从而形成一个大规模的信息系统,订货手续大为简化,订单当天就可以传入总公司的电脑中,交货时间就可以减少10天以上,而且经销商的库存也减少70—80%,大幅度降低了存货成本。
丰田生产物流方式对提高自主体系经营能力的作用

丰田生产物流方式对提高自主体系经营能力的作用在汽车行业,业内人士提起管理的时候,几乎马上就能想到丰田生产方式;而在物流行业,业内人士提起供应链管理的时候,也同样会谈到丰田的物流管理。
由此可见,丰田在生产管理和物流管理上,确实有值得我们学习和借鉴的地方。
通过一汽自主品牌与丰田先进的物流管理相对照,笔者真切地感受到,深入学习丰田先进的生产、物流方式,不断提升自主体系的经营能力,是一汽发展自主事业必须尽快破解的重大课题。
一、丰田生产物流概要介绍对丰田略有了解的人都知道,丰田的发展史其实就是一部自主发展的历史。
它在自己弱小的时候,也曾向美国的通用和福特公司、欧洲的宝马和大众公司学习,也曾和其他汽车企业进行过合资合作,但有一点,就是丰田始终没有忘记自主造车的梦想。
徐建一总经理明确提出,要“统一思想干自主,统一目标干自主,统一资源干自主”,自主的事业是我们“必思、必想、必干、必争、必拼、必胜”的事业,这极大地坚定了广大员工谋划自主、干好自主的信心和决心。
丰田物流企划部的员工曾自豪地说:“丰田生产方式的发展史就是一部物流发展的历史。
”现任日本物流协会会长的丰田董事长张富士夫,在1982年就担任过丰田生产管理部物流管理室的第一任室长,作为大野耐一的主要弟子参与创建了丰田生产方式。
为使丰田全体员工牢记丰田生产物流方式的本质,张富士夫亲自在大野耐一最初创建TPS的本社机械工厂建成了TPS基本示范线,用于教育和加强全体员工对拉动式生产物流方式的理解。
丰田总部在2004年时设置有物流企划部;员工120人;生产零件物流部,员工180人;商品车物流部,员工114人;备品物流部,员工210人,可以说是构建了一个相对庞大的物流组织机构,配备了经验丰富的物流人才,并通过借助集团总部强有力的计划在全世界范围内进行物流的集中管理,以达到规模效应。
二、对标丰田,查找差距,及时改善对标绝不是简单的对比。
开展对标首先要做到“知己”,然后才是对现状进行准确把握的基础上的“知彼”,只有这样才能真正发现差距进而找到解决问题、弥补差距的方法。
广州丰田的三种物流模式

广州丰田的三种物流模式帮助丰田汽车实现JIT的不仅仅是台车、飞翼车和集装箱物流这三驾马车,还有一套贯穿从供应商布局到拉动式生产线始终的物流体系。
独特的物流体系是丰田汽车在中国扩张市场时的竞争利器,在广州丰田汽车有限公司(简称“广州丰田”),这一点已经开始体现。
广州丰田汽车有限公司成立于2004年9月1日,是由广州汽车集团股份有限公司和丰田汽车公司各出资一半,合资建设、经营的整车项目。
它与天津的生产基地一南一北遥相呼应,并与海内外的零部件供应商相连接,构成了丰田汽车在中国紧密无隙的供应链网络。
作为日系车厂的典型代表,广州丰田在入厂物流环节别具特色。
广州丰田目前有三种零部件物流模式:台车物流(含顺引卡车物流),主要适用于主机厂周边厂家;飞翼车物流,主要适用于国内非主机厂周边厂商;海运集装箱物流,主要适用于海外进口的零部件。
这三类物流是广州丰田入厂物流的三驾马车,与相应的生产布局和厂内物流一起,构成了丰田汽车在中国精益而高效的物流体系。
距离决定模式大致来讲,供应商距离广州丰田的远近决定了其物流模式。
台车物流面对的是广州丰田工厂周围2公里内的供应商,使用专用容器,零部件可以直接上装配线;飞翼车物流面对的是距离广州丰田2公里以外的所有国内厂商,比如在上海和天津的供应商,这部分支撑了广州丰田的Milk-run系统;集装箱物流面对的则是海外供应商。
三种物流模式构成了广州丰田整体的厂外物流,在丰田的供应体系中,对适用不同物流模式的零部件已做了分类和规划,零部件被分为顺引件、台车件、看板件、海外件。
顺引件是供应商按照车辆下线顺序排列零部件的装载顺序,直接送到线上装配的零部件,如发动机、座椅、轮胎、玻璃等,这些零部件体积大或质量大,是非标准件,它们使用台车和专用卡车运输,使用专用通道,特点是定量不定时。
车辆顺序在车辆从涂装进入总装时就最终确定,该顺序指示会同步传送给供应商,作为供应商排序的依据,丰田根据生产的实际进度去供应商处引取。
案例3:丰田汽车——备件物流配送系统

⼀、“天⼤”的秘密 早在20世纪80年代,⽇本丰⽥汽车公司就把⼤批⽣产线发展到国外。
由于澳⼤利亚政府从1987年起就降低关税,⾄2005年,澳⼤利亚对进⼝汽车及其零部件⾄多收取10%关税,所以,澳⼤利亚已成为丰⽥汽车公司产品的主要销售和出⼝地。
在过去的10年多时间⾥,⽇本丰⽥汽车公司⼀直在澳⼤利亚发展全⽅位的汽车零部件配送系统和物流链管理服务。
如果现在有⼀辆汽车在澳⼤利亚的草原或者荒漠中抛锚,⽆论是丰⽥还是其它什么牌号,只要把求助信息发到丰⽥汽车备件公司所属配送中⼼,不需等候多久,附近的丰⽥汽车零部件销售商就会以最快的速度把急需且正宗的汽车零部件送到出事地点,如果必要的话,随⾏的专业技术⼈员会帮助把汽车修好,收费合理,绝不乘机“斩⼀⼑”。
迄今丰⽥汽车备件公司在澳⼤利亚的物流服务已经成为⽇本其它汽车⼚商在全球各个⾓落发展经营交易的典范。
丰⽥汽车公司把零部件物流服务看成是“售后”市场的主体,其重要意义与制造、销售汽车同样重要,因为公司知道“好事不出门,坏事传千⾥”,对于⼴⼤消费者来讲,最容易损害某种牌⼦汽车信誉的莫过于到处买不到这种汽车的关键零部件。
现在出售⼀辆新汽车的利润并不⾼,因此汽车产品能否吸引远来的⼴⼤消费者已经成为汽车⼚商加快促销、减少库存、降低成本、增加效益最关键的⼀招。
精于市场动态调查的丰⽥汽车公司早就发现⼀个“天⼤的秘密”:消费者⼀旦享受到某种牌⼦汽车的汽车⼚商提供的售后服务,就会对⾃⼰购置的该牌⼦的汽车赞不绝⼝,在客观上为汽车⼚商⼤做义务⼴告,于是买这种牌⼦汽车的消费者就会接踵⽽来。
丰⽥汽车公司⼜发现,⼤约有86%的消费者在购置某牌号汽车的第1年内会回头向该牌号的汽车⼚商购买汽车零部件,但是5年以后回头购买该牌号汽车零部件的消费者骤降到20%。
⼆、改⾰陈旧的汽车零部件经营观念 从20世纪90年代初起,为了把⼤部分消费者变成“回头客”,丰⽥汽车公司及时变换经营理念,调整机制,给企业和产品重新定位,于是下决⼼改⾰陈旧的汽车零部件的经营⽅式,开始在澳⼤利亚市场开拓和重新组合丰⽥汽车零部件销售服务渠道。
OSHMS在广汽丰田备件仓库中的应用-彩页版
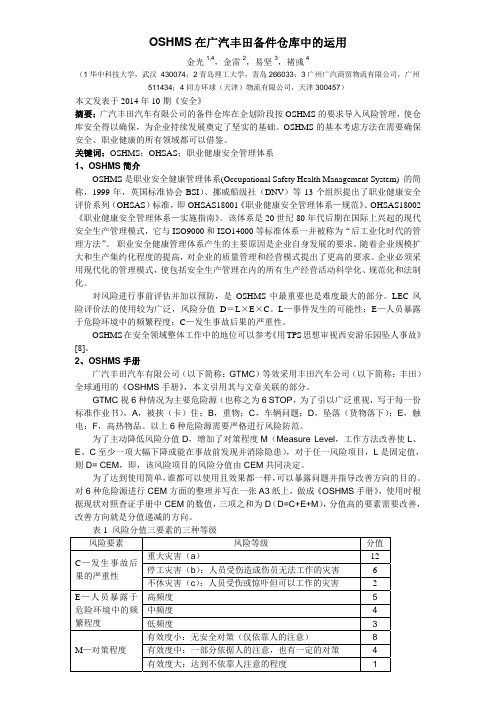
库安全得以确保,为企业持续发展奠定了坚实的基础。OSHMS 的基本考虑方法在需要确保 安全、职业健康的所有领域都可以借鉴。
关键词:OSHMS;OHSAS;职业健康安全管理体系
1、OSHMS 简介
OSHMS 是职业安全健康管理体系(Occupational Safety Health Management System) 的简
称,1999 年,英国标准协会 BSI)、挪威船级社(DNV)等 13 个组织提出了职业健康安全 评价系列(OHSAS)标准,即 OHSAS18001《职业健康安全管理体系—规范》、OHSAS18002
《职业健康安全管理体系—实施指南》。该体系是 20 世纪 80 年代后期在国际上兴起的现代 安全生产管理模式,它与 ISO9000 和 ISO14000 等标准体系一并被称为“后工业化时代的管
停工
运输车辆、试验车辆
度逐一度量。 等角度逐一度
灾 害 6 略 略 等 ( 最 大 速 度 < 略 略 略 量。本文不展 本文不展开。
(b)
10km/h)
开。
不休
灾害 2 略 略 —
略略略
(c)
表 4 E(暴露于危险环境的频繁程度)的量化
频繁程度
安全相关
作业频率 作业环境相关
作业姿势相关
高频度 5 1 次/周以上
理方法”。 职业安全健康管理体系产生的主要原因是企业自身发展的要求。随着企业规模扩
大和生产集约化程度的提高,对企业的质量管理和经营模式提出了更高的要求。企业必须采
用现代化的管理模式,使包括安全生产管理在内的所有生产经营活动科学化、规范化和法制
化。
对风险进行事前评估并加以预防,是 OSHMS 中最重要也是难度最大的部分。LEC 风
TPS在广汽丰田物流系统的应用及借鉴意义_下

笔 者认
销 (销
门日 ) ( 门白
售
当的
生产
物流 ) 体系
才是恰
下 工序 ) 的思想 , 使
包括 经销 商
供应 商
工厂
运
输商在 内所有 的工序 紧密结成一
T p S 在 物流 系 统应 用 的重 点 难点及其借 鉴意 义
企业 ( 组织 ) 如 同有生命 的 生物 , 有其本 身应有 生存环 境和 运行规 律 , 符 合规律 就会健 康发 展 , 违 背规律 就会付 出健康 甚至 生命 的代价 不 同国界 的人 , 尽 管生存 环境 等不尽相 同但其 生物 本质 相 同 ( 需 要 衣食 住 行等 )
反而会成为累赘
在 市场爆 发式 增长期 或不可预测
时 , 有观点认 为 只有 大量 改造厂 房 设 备达 到 G M C 的水平 且 T 投人 巨资 打造计算机 系统才 能推 行 TPs , 笔者 以为 , 只有 思想 先 行 才是 正道 , 丰 田当年推 行 TP S 并没 有一 次性 大量改 造设 备 , 甚 至很 多设 备长期处 于同行落 后水
断解决 问题 和意识 革命 , 丰 田以
非 常强 , 根本不需要换装 例 如 , 油 漆线如果 连续更换 颜色会 造成
点带 面坚定信 念不 断解决 问题 ,
在 解 决 问 题 中培 养 人 才 并 推 进 TPS , 缺失 了 JIT 就不是 TPS 还有 观点认 为 TP 就是 看板 S
在 各环 节削减 库存 和资金 占用 的 同时 , 也 面临订 单交 付响应时 间
但滞 销会带来 实质 的损失 二者
翻译 成
精益 , 远 没 有表 达 出 笔者认 为 , 为 了真实 表
的 原 意 , 可 把 L a 翻译 e n (音 : 动心 ) , 即感 动
SPS基本理论及SPS环境下的物料配送方式

SPS 基本理论及SPS 环境下的物料配送方式(卡车销售/)SPS 的基本概念14SPS(Set Parts Supply)是丰田生产方式发展过程中又一具有里程碑意义的创新,是丰田自本世纪以来对总装生产线这一问题进行不断解决与改善的成果。
由于丰田在海外的快速扩张以及因顾客喜好多样化而带来的新车型的逐渐增加,人才的需求不断增加,尤其是在海外工厂,丰田公司经常要面临对海外工厂进行人才支援的问题,面对着这样的巨大压力,丰田公司海外工厂的自立化就成为当务之急,同时也必须在短时间内尽可能培养多数需要的人才。
因此,丰田急需革新,通过实现装配线的集约化及简约化,加速人才的培养。
在这种背景下,SPS系统就应运而生了。
SPS,即零件分拣系统,也被译为成套精益物流配送系统,是丰田为解决与改善总装生产线而提出的一种高效率精益物流生产模式,由于其来源于日本,且该系统如今已在日系汽车企业中广泛应用,也被成为“日系SPS”。
简单来讲,SPS就是将总装生产线上组装作业与零部件选取作业分离开(这也是SPS最大的特点),分拣人员只负责将某一型号车辆所需的零部件选取出来,装入相应的SPS料车上,并按生产顺序向生产线单辆份配送,料车与所装配车辆同步前行,装配作业人员直接拿取料车内零部件进行装配,待装配完毕后,在指定工位撤出并进入下一循环。
这一方式充分体现了适应多品种混流的精益思想,即集成需要的数量,在需要的时间将需要的零部件配送至需要的地点。
通过生产管理系统将配货指示单发送至物料配送区内,采用自动化输送系统送至线边,最终实现整车的装配。
SPS 虽然也是将零部件供应给装配线工作人员方法的一种,但与传统的物料批次15配送方式相比却又不尽相同。
SPS 与传统方式的比较采用SPS 后传统方式装配作业者的步行距离可以定点取出,减少走动距离定点取出困难,拿取时间长,工人步行距离相对较长物流距离易送到SPS 区域,搬送距离短,且不受零件大小的影响能送到线边,但搬运距离长。
丰田供应链管理
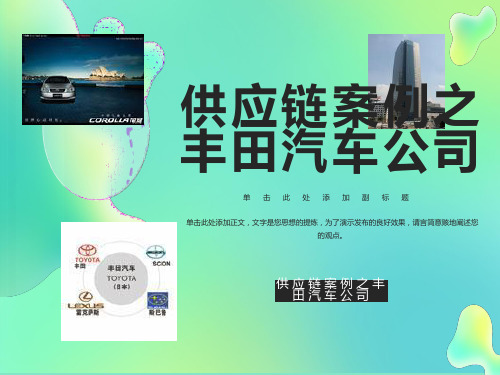
供应链案例之丰田汽车公司
三、案例启示
信息化建设的重要性 eg:国际价格比较系统 丰田的灵活销售体系
不能照搬别人的模式
eg:福特的传送带思想 →丰田JIT生产
、、、、、、
聪明的你,收获了什 么???
• CLICK HERE TO ADD A TITLE
供应链案例之丰田汽 车公司
单击此处添加文字,文字是您思想的提炼
供应链案例之丰田汽车公司
提高竞争力,增加公司整体利润
降低成本,减少库存
柔性组织,适应环境Fra bibliotek准时化生产
看板管理
均衡生产
全面质量管理
小批量生产
同步化生产
质量保障
人员弹性配备
设备配置
供应标准化
公司全员参与,合理化分工合作,改善劳动组合,改进流程 丰田汽车公司JIT流程示意图
供应链案例之丰田汽车公司
1.废品量最低(零废品)。JIT要求消除各种引起不合理的原因,在加工 过程中每一工序都要求达到最好水平。
2. 尽量采用成组技术与流程式生产。 3. 与原材料或外购件的供应者建立联系,以达到JIT供应原材料及采购零部件的目
的。
供应链管理之丰田汽车公司
2.2 "看板"方式管理方法
看板管理,指为了达到及时生产(JIT)方式控制现场生产流程的工具。 及时生产方式中的拉式(Push)生产系统可以使信息的流程缩短,并 配合定量、固定装货容器等方式,而使生产过程中的物料流动顺畅。 及时生产方式的看板旨在传达信息:“何物,何时,生产多少数量, 以何方式生产、搬运”。
供应链案例之丰田汽车公司
3.1 零部件厂商对整车企业的实时物流供应
(1)在实时物流中,取消了仓库的概念
浅谈丰田管理方式在物流中的应用

浅谈丰田管理方式在物流中的应用(作者:___________单位: ___________邮码: ___________)论文关键词:物流丰田汽车TPS论文摘要:丰田汽车作为物流业的先驱将自己优秀的生产和管理系统融入到了物流配送体系中,大大降低了物流成本同时又提高了公司整体运作的效率。
其以TPS为管理精髓的模式中与物流相关的JIT及时生产方式,标准化作业,5S,可视化管理都非常值得我们研究与借鉴。
近年来,物流业迅速崛起已经成为中国最有前景、最有潜力的新兴行业之一。
作为物流业的先驱者丰田汽车,将自己优秀的生产和管理系统融人到了物流配送体系中,大大降低了物流成本同时又提高了公司整体运作的效率。
一、丰田汽车的生产管理方式丰田汽车的生产管理方式主要是以TPS为管理精髓的一系列的管理模式,JIT的生产方式、看板的管理方法等等。
TPS丰田生产系统又称为TOYOTAWAY,目的是消除运营中所有的过载、不均衡、浪费,通过PDCA—计划、执行、检查、纠正的方法解决问题,改善质量、成本、交货期,突现零故障,零事故、零人力资源浪费等等。
从TPS中衍生出很多细化的管理概念,在这里我们挑一些与物流紧密相关的来介绍一下。
1.JIT及时制生产JIT生产方式的基本思想是:在需要的时候、提供需要的产品、提供需要的量,这种生产方式的目标就是追求零库存,或者说库存达到最小的生产系统。
2.标准化作业标准化作业就是将作业流程首先进行整体规划,确定作业目标、内容、重点以及安全问题,再将整个流程细化成为各个小的部分,有时会细化到每一个动作。
统一标准不仅可以方便管理.更重要的是可以很容易的发现作业中的错误。
3.5S5S即整理、整顿、清洁、清扫和素养。
在丰田管理体系中,5S是对作业场所最基本的管理。
4.可视化管理可视化管理也是丰田管理的一大特色。
所谓可视化管理就是将标准化作业书等一系列作业管理资料都贴在工作场所的管理板上。
这样做可以使每一个人对各个工位的作业情况一目了然,同时也便于管理者及时发现问题。
3S集成技术及其在物流系统中的应用

浅谈3S集成技术及其在物流系统中的应用摘要:阐述全球定位系统GPS(Global Position System)、地理信息系统G1S(Geographic Information System)、遥感RS(Remote Sensing)的组成、原理及特点。
并针对现代物流系统的状况和发展趋势,借助3S集成技术的优势,研究3S集成技术在物流系统中的应用。
关键字:3S集成技术;GPS技术;GIS技术;RS技术;物流系统随着社会经济的不断发展,物流供应链变得越来越庞大,物流系统对信息化的要求越来越高,单纯的不依赖信息技术的货物空间位移已不复存在,用全面的信息系统特别是空间信息系统来支持物流运作在各个层次都显得特别重要。
3S集成技术是一门新兴的空间信息技术,它对物流系统的配送中心选址、配送路径选择及特种车辆监护等有着十分重要的意义。
应用3S技术可以很好地解决物流系统中存在的一些问题,基于3S技术的物流系统是物流行业的一个新的发展方向。
1. 3S集成技术3S集成技术是将全球定位系统(Global Positioning System,GPS)地理信息系统(Geographic Information System,GIS)及遥感(Remote Sensing,RS)三项既独立发展又相互间渗透的现代信息技术融合于一体的技术,它是一门非常有效的空间信息技术。
就在集成体中的作用及地位而言,GIS相当于人的大脑,对所得的信息加以管理和分析;RS和GPS相当于人的两只眼睛,负责获取海量信息及其空间定位。
RS、GPS、和GIS三者的有机结合,构成了整体上的实时动态对地观测、分析和应用的运行系统,为科学研究、政府管理、社会生产提供了新一代的观测手段、描述语言和思维工具。
1.1 GPS技术1.1.1 GPS定义及组成GPS又称为全球定位系统,是美国从20世纪70年代开始研制,于1994年全面建成,具有海、陆、空全方位实时三维导航与定位能力的新一代卫星导航与定位系统。
简论丰田公司管理下的物流管理运作模式论文.doc

简论丰田公司管理下的物流管理运作模式论文丰田公司管理下的物流管理运作模式论文导读:本论文是一篇关于丰田公司管理下的物流管理运作模式的优秀论文范文,对正在写有关于丰田论文的写有一定的参考和指导作用,摘要:供应链概念提出以后,越来越多的企业将主要精力集中在核心业务,纷纷将物流业务外包。
但外包物流能否达到企业的要求,是否会造成物流成本上升?不同的企业有着不同的体会。
借丰田(中国)公司管理模式,以及丰田(中国)公司与同方环球(天津)物流有限公司合作案例寻找中国第三方物流未来发展方向及趋势。
关键词:丰田公司;物流管理;运作模式1673-291X(2014)09-0245-02研究表明,有效的供应链管理总是能够使供应链上的企业获得并保持稳定持久的竞争优势,进而提高供应链的整体竞争力。
统计数据显示,供应链管理的有效实施可以使企业总成本下降20%左右,供应链上的节点企业生产率增值提高15%以上,供应链上的节点企业按时交货率提高15%以上,订货到生产的周期时间缩短20%~30%。
合理借鉴各国第三方物流的成功经验,有助于推进中国第三方物流产业的发展。
本文为此提出相应的结论及倡议。
一、供应链管理下的丰田公司目前状况丰田汽车的供应链管理模式于丰田生产方式—TPS,TPS—丰田生产系统,全称为Toyota Production System 又称为TOYOTA (精益生产系统),即将必要的产品,在必要的时间,生产出必要的数量。
丰田精益生产方式所要求的精益供应链体系,能够实现生产数量和交货时间的精准性。
这不仅使得丰田汽车供应链体系效率一直高于美国公司,并且大大降低了供应链成本。
相关统计数据显示,在全球金融危机爆发之前,丰田的供应链成本比美国汽车公司低8%左右。
2007年同方环球(天津)物流有限公司(以下简称TFGL)的成立,亦使丰田进一步降低了物流成本。
据估算,同方环球2008年为丰田汽车的中国业务降低了超过1亿元人民币的物流成丰田公司管理下的物流管理运作模式论文资料由.提供,地址.本。
《丰田汽车物流管理系统介绍》课件讲义
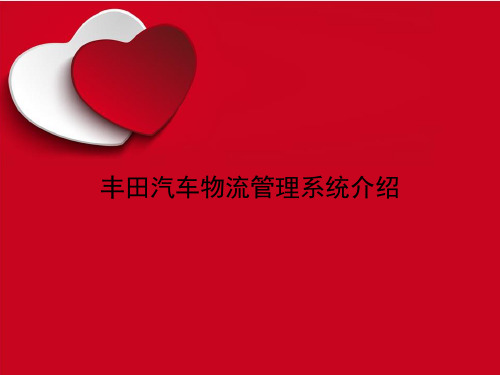
生産計画 内示
安排。箱种类管理
部品定单
模拟/ 物流费报价
物流計画策定
计算货量
基本时间 表
装载。连接 接收计划
每日时间 表
供应商地图 / 路线编组
物流実績履歴管理
物流現場指示 分期基地・验收作业
司机/卡车编排 卡车运行管理
出货信息 / 线路管理
考评/成本管理
评价
成本 管理 付款
5.TLMS导入的目的及必要的运用
靠近顺引
1.高负荷 2.适应变化
5. TLMS导入的目的及必要运用
1.平准化节拍 & 根据客户根据GUI 进行修正 2.遵守“FIFO”
b.细致的厂外物流计划(出发、配送计划)的制定
基本时间表(创建出发时间)
供应商
供应商出 发时间
工厂
开车时间
到收货仓
验收时间 工厂出发时间
5. TLMS导入的目的及必要运用
Quick countermeasure to keep reasonable route & truck
Investigation of the reason Expedite
原因调查
特車安排
为了保持最合适的路线.班次 而采取最合适的对策
Suggestion Information
建议
信息
Information 信息
a.支持以TPS为基础的全球丰田的标准运作.系统
包含进度吸收分割LANE的总体工程印象(例:TMT)
厂外物流区域
厂内物流区域
供应商
共同/中转物流
#丰田安排
供应商
供应商
按计划交货
多频次配送
・没有交付货物的订单 直接存储到分巷
厂内物流支援系统的应用及效果

第47卷 第7期 2020年7月天 津 科 技TIANJIN SCIENCE & TECHNOLOGYV ol.47 No.7Jul. 2020收稿日期:2020-06-04管理与创新厂内物流支援系统的应用及效果钟 磊,赵宏鹏(天津一汽丰田汽车有限公司 天津300457)摘 要:厂内物流支援系统是面向零部件供给合理分配工作量,追求一人工的物流企划类辅助系统,现应用于丰田全球事业体的多个工厂中。
立足于研究丰田某工厂总装车间的物流区域,以丰田特有的生产方式来考虑,将厂内物流支援系统应用到零部件供给环节中,实现高效的零部件运送,同时获得作业人员及作业面积递减的效果,大幅提高了生产能率。
关键词:厂内物流支援系统 一人工 直供 能率中图分类号:F252 文献标志码:A 文章编号:1006-8945(2020)07-0019-04Application and Effect of Internal Logistics Support SystemZHONG Lei ,ZHAO Hongpeng(Tianjin FAW Toyota Motor Co.,Ltd.,Tianjin 300457,China )Abstract :The internal logistics support system is a kind of logistics planning auxiliary system for parts supply and reason-able workload allocation, which pursues work done by one person. It is now used in many factories of Toyota global busi-ness. Based on the study of the logistics area of the general assembly workshop of Tianjin FAW Toyota Motor Co.,Ltd. (hereinafter referred to as TFTM ),this paper applies the internal logistics support system to the parts supply link based on the consideration method of Toyota production mode ,so as to realize the efficient parts delivery ,obtain the effect of reduc-ing the number of operators and the operation area ,and greatly improve the production efficiency. Key words :internal logistics support system ;work done by one person ;direct supply ;efficiency0 引 言一般生产物流系统分为2个部分:一部分是由供应商至工厂之间的物流系统,以供应商为起点,以工厂物流区为终点,称之为厂外物流;另一部分是工厂内部的物流系统,以工厂物流区为起点,以生产线物料使用位置为终点,称之为厂内物流。
- 1、下载文档前请自行甄别文档内容的完整性,平台不提供额外的编辑、内容补充、找答案等附加服务。
- 2、"仅部分预览"的文档,不可在线预览部分如存在完整性等问题,可反馈申请退款(可完整预览的文档不适用该条件!)。
- 3、如文档侵犯您的权益,请联系客服反馈,我们会尽快为您处理(人工客服工作时间:9:00-18:30)。
TPS在广汽丰田物流系统的应用及借鉴意义摘要:丰田汽车公司源于物流平准化的持续改善凝结成TPS,TPS在丰田汽车公司的全面应用使其得到快速发展,全球掀起学习TPS的浪潮。
TPS在广汽丰田物流系统的成功运用,使生产得到有效保障,现场运行有条不紊,做到了安全、质量、环境保护、5S和成本等各方面的精益,有着非常值得学习的地方。
希望本文能为学习TPS 的企业和个人有所给力。
1. 引言长期以来,丰田一直将物流管理、营销管理及财务管理等同视之为核心管理技术。
丰田物流企划部的员工自豪地说:“ TPS(Toyota Production System,丰田生产体系)的发展史就是一部物流发展的历史。
”日本物流协会前会长、丰田前总经理、现董事长张富士夫(TPS的创始人大野耐一的弟子之一,曾参与创建TPS)曾担任丰田生产管理部物流管理室的第一任室长,由有物流管理从业背景的人出任企业最高管理者在世界汽车界也是绝无仅有的,足见丰田汽车公司对物流的重视和物流在TPS中的重要性。
本文描述的物流系统是指按照采购订单有组织地将零部件从供应商以多种物流服务方式输送至汽车生产工厂指定位置暂时停放及卸货,并有序、准确地向生产车间进行零部件上线,以及完成汽车生产后商品车运输管理的整个物流过程。
广汽丰田汽车有限公司(以下简称GTMC)的物流模式,是基于TPS思想构筑的物流管理体系,用计算机系统辅以人的智慧制定切实可行、精益的物流计划,用最简单和容易理解的方式在最恰当的时间把恰到好处的作业指令在最恰当的场所传递给每一个合格作业人员(即JIT的作业指令,或称恰到好处的作业指令),其形式上可以是指示牌、作业指示书等作业指令和附着在物品或器具上的看板或其他形式的管理道具,很多看板可以及时暴露问题。
当工作条件恰当,工作内容简单、易于执行可以及时发现不良,整个系统的每个人都知道什么时间干什么,工作时间被安排得有条不紊、忙而不乱时,全面彻底的包含各管理要素的标准作业(安全、质量、环境保护、5S和成本等)就能使各方面都做到最精益。
如物流系统的YARD、P链、PC棚、看板等都堪称TPS的经典运用。
在TPS思想的指导下,GTMC得以快速发展,现地(指中国本地)管理人员和员工也得到快速成长。
中外专家根据中国地大物博和消费现状率先开发出“销售·物流整合管理系统”(通称SLIM:Sales Logistics Integrated Management),SLIM旨在将制造物流与营销管理衔接起来,从生产计划到整车制造、下线在库、发车运输、到店交付、客户交车的全过程进行“可视化”管理,该系统正在向丰田全球其他企业进行推广。
现任丰田汽车公司总经理丰田章男将其称为21世纪的看板管理和新一代的TPS。
由此可见,TPS在中国不但可以生存,更可以发展,并为TPS添加新的元素。
2.TPS及其思想在物流系统的表现形式丰田汽车公司于1937年由丰田喜一郎创立,当时日本劳动生产率是美国的1/9,1945年8月15日(日本战败日)丰田喜一郎提出:“要三年赶上美国!否则,日本的汽车工业就建立不起来”。
大野耐一认为:并不是美国人付出了日本人十倍的体力,一定是日本人生产中存在着严重的浪费和不合理现象,需要彻底消除浪费。
他在工厂车间运用工业工程的手法发现很多问题,如原材料到货不均衡导致忙闲不均、不必要的库存、产品质量不合格等,这些问题造成了很多浪费。
通过推进拉动式生产并实施“根据生产计划,用看板及时、准确地下达作业指令,后工序在必要的时间去上工序取必要数量的产品”、“自働化”(绝对不能翻译成“自动化”,“働”原本是中文汉字,丰田赋予的含义见表一)等一系列措施,使问题可视化并得到及时改善,这一改善体系逐步被总结成TPS。
但在TPS使用范围扩大的过程中,因为思想冲突,丰田内部很多部门领导都不理解其思想,甚至到丰田喜一郎处强烈投诉这一管理体系。
结合劳资纠纷等原因丰田喜一郎主动辞职承担了“高层干部的责任”,并承揽了针对大野耐一的指责使其能顺利展开工作。
直到1963年,借着丰田推进TQM的东风,时任副总经理的大野耐一才在工厂、经销商、供应商全面推行TPS,前后花了20年时间。
自上世纪七十年代起,日本经济长期处于低增长状态,但在全面应用TPS19年之后, 1982年丰田汽车公司却取得了骄人的业绩,劳动生产率是通用的9.17倍,人均利润是通用的10倍。
此时TPS引起了全世界的关注,丰田因此成为日本制造业的标杆,引领日本经济快速发展,大野耐一在日本也被冠以“日本复活之父”、“生产管理的教父”等桂冠。
表1:丰田对TPS的定义丰田对自働化的解释:赋予机器人的智慧(带发现异常自动停止装置的机器)。
因为很多工作由人完成,笔者添加解释:赋予人机器的标准化能力。
(历史故事:丰田汽车公司的前身是丰田喜一郎的父亲丰田佐吉先生创立的丰田纺织公司,丰田佐吉先生为了解决其母亲手动织布的痛苦发明了自动织布机极大地提高了生产效率,但断纱没有及时发现会造成大量废品,因而发明了自动发现断纱并停机的装置。
该故事成为自働化和如同对待父母般对待顾客的原型)笔者对表1中“必要”的认识是“恰到好处”。
为了使文章简捷和连贯,以下保留“必要”的表述。
TPS 中Just In Time不仅仅包含时间上的恰到好处,还包括为了准时生产所需要的产品、数量、场所等要素的“恰到好处”。
笔者也把JIT解读为“如同锦囊妙计般完美的恰到好处”。
TPS思想的关键词在物流系统中的解读有如下几点:□顾客至上在GTMC中,上工序视下工序为顾客(简称“上工序、下工序”),即不仅消费者是顾客,销售店也是GTMC 的顾客,甚至供应商、物流服务商也是顾客。
各部门、各级管理人员都要站在下级、下工序,最终站在作业人员能够有效工作的立场去思考、展开工作、培训作业人员并为作业人员创造必要的工作条件和下达JIT的作业指令,像对待顾客一般服务于作业人员。
顾客至上的理念,在GTMC的生产、销售及物流系统以“上工序、下工序”的形式得到了充分的体现。
按照交付产品或服务的流程绘制的上、下工序很容易理解,供应商→GTMC→销售店→顾客,但各工序正常运作又必须有必要的前提条件,以信息传递流程为例,与前述流程正好相反:顾客→销售店→GTMC→供应商、物流服务商等,此时GTMC是供应商、物流服务商的上工序,要用“顾客至上”的理念服务于供应商、物流服务商。
GTMC要求每个物流单元在物流起始的时刻就做出可以清晰指导该物流单元所有下工序的物流作业看板。
如供应商的零部件装车前就要按照GTMC的要求,对每个EU箱做看板,指示以EU箱为物流单元全过程的物流活动,EU箱捆绑成托时即做出托看板,指示以托为物流单元全过程的物流活动,飞翼挂车以“便次号(便:卡车往返运输一趟,通常翻译成便)”的方式加以管理。
整车物流的物流单元是单台商品车,在物流开始即发行“物流管理票”(看板)与商品车的VIN一一对应,指导所有下工序进行必要的操作,直至到达销售店。
看板同时体现了“上工序、下工序”和“彻底消除浪费”的思想。
管理人员是直接作业人员的上工序,管理人员要用“顾客至上”的理念服务于作业人员,直接作业人员接受的作业指令必须是JIT的作业指令才能确保有序的作业和工作质量。
从此意义上讲,上级是下级的上工序,才不难理解“出了问题管理者先检讨”的思考方式。
□彻底消除浪费物流系统的浪费涵盖人的浪费(不能充分发挥人的智力、能力和改善积极性)和现场的七种浪费【不良品的浪费、库存的浪费、动作的浪费、搬运的浪费、等待的浪费、制造过多(早)的浪费、加工的浪费】,要做到高品质的物流,并在物流系统彻底消除一切浪费,需要平准化的、周期短、循环往复、高效、可以灵活对应变化的简单标准作业,同时辅以JIT的作业指令,才能消除无效的工作并在有效工作时间内提高稼働率(稼働率=工作日有效工作时间/工作日时间,这里不但强调工作,更强调“品质·智慧”的有效工作),才能实现有质量的低成本。
可以看见的浪费容易消除,看不见的浪费是最可怕也是最难入手的,GTMC全面采用可视化管理,暴露各种问题并加以解决,是问题意识的完美体现[7]。
□自働化自働化也称之为自工序完结,物流系统的每一个工序都必须做到自工序完结,包含“良品条件”和“标准作业”两部分。
其中,“良品条件”是优化工作流程及工作的设计使工作简单化、为作业人员提供必要的标准作业培训和包含机器、物料、工作方法、环境等要素的工作条件,下达JIT的作业指令,自工序能够发现并消除不良;“标准作业”是通过良品条件、作业观察、激励等一系列活动,使所有过程的作业彻底标准化,人人都能在规定的时间完成确保安全、质量、5S等的作业。
在PDCA的任何阶段发现自工序完结的不足,都可以作为改善的切入点。
GTMC有着确保安全为前提品质最优先的基本方针,一系列自働化的措施确保了物流品质的稳定和无差错。
□准时生产(JIT)平准化的准时化生产是TPS最具有挑战性的内容之一,准时化生产的发展基础是物流系统的发展。
准时化生产的前提是高品质和平准化,平准化是使所有的工作平均分布,平均得越精益,越能体现其好处,月度工作平准化到每天,再将每天的工作拆分成恰当的单元,对于每个单元的工作在同一场地投入相同的设备和人员,在物流系统各环节实施JIT的信息传递和下达JIT的作业指令,均衡、不断重复地工作,提高人、设备和场地的使用效率,从而实现平准化的准时化生产。
物流全过程的自働化加上准时化生产,消除了物流质量不合格、忙闲不均的现象,同时消除了库存和作业等浪费,达到彻底消除浪费的目的,实现顾客至上的根本理念。
3.GTMC发展历程及物流系统概述GTMC成立于2004年9月1日,是由广州汽车集团股份有限公司和丰田汽车公司共同投资建设和经营的企业,2006年投产当年,创造了产销双双超过61000辆的佳绩,此后,产销额一直保持良好增势。
2011年8月4日迎来第100万辆整车,成为最快实现百万辆下线的企业之一。
可见,坚实的物流系统根基,为GTMC的快速发展提供了基础。
笔者认为,基于TPS思想确定物流系统的基本原则包括周期性、周期短、高效率、柔性。
物流系统的理想状态是:构筑满足顾客需求的体制,追求安全事故为零、无运输损坏、差错和延迟,遵守先进先出的原则,并追求环境保护和低成本。
构筑“JIT、可视化、简单化、循环往复”的物流作业体系,通过减少在库、少人化、少器材、少场地化、少物流动线、提高车辆装载率和运行效率等措施,达到降低成本的目的。
GTMC的物流系统由零部件物流系统和整车物流系统两大部分组成。
其中,零部件物流系统支撑着供应链的输入体系,整车物流系统构筑起供应链的输出体系。
零部件物流系统分为厂外物流系统与厂内物流系统两大领域。
厂外物流系统是指工厂受入口以外所有的零部件物流,包括供应商的集货和空箱返回、中继地的中转、中继地—YARD、YARD—工厂受入口的交付等。