有杆泵抽油系统软件设计技术手册

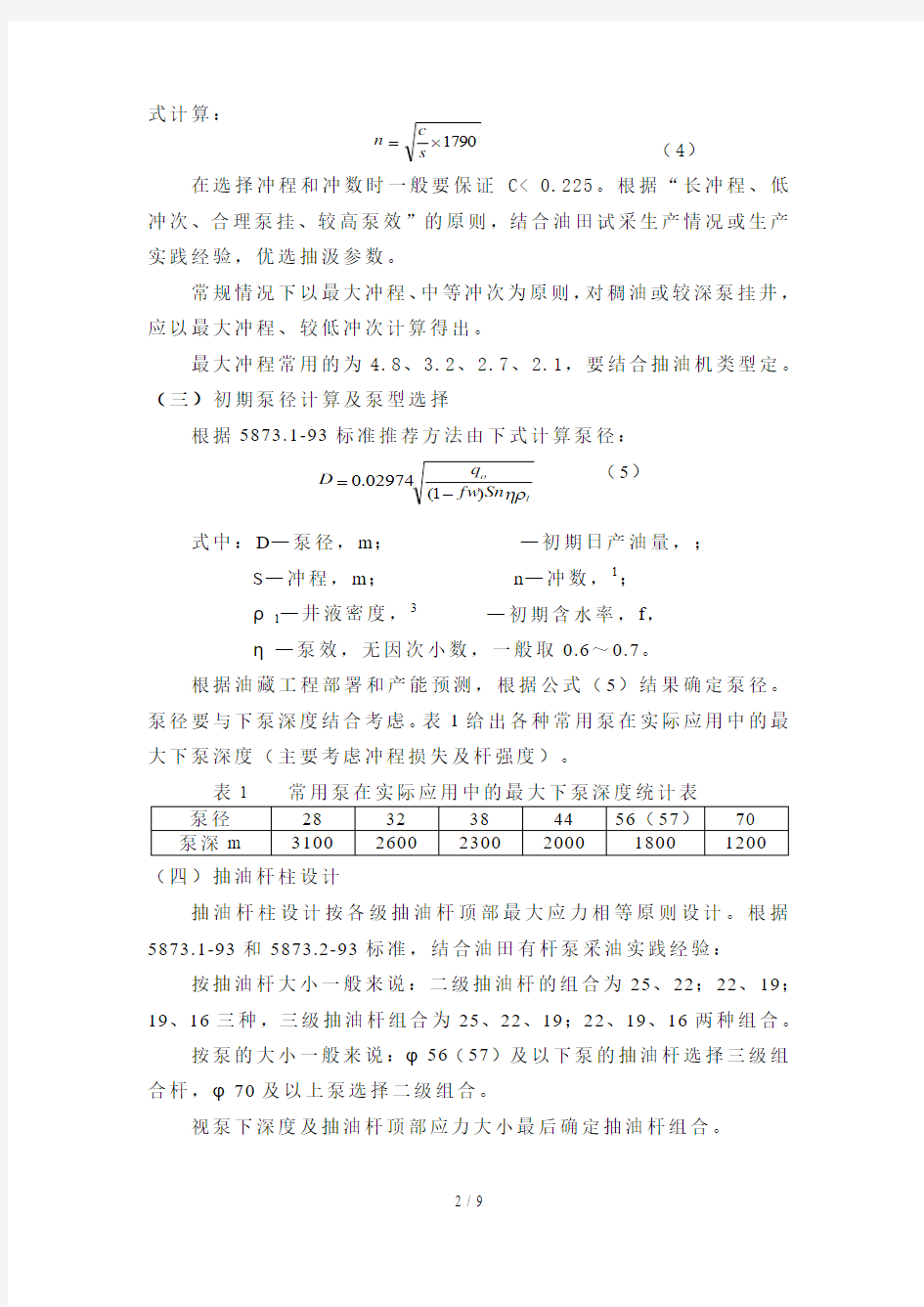
有杆泵抽油系统软件设计 技术手册及操作手册
一、技术手册
根据5873.1-93、5873.2-93标准和油井产能预测及生产或试油情况,结合有杆泵工艺技术水平和实践经验,进行有杆泵抽油系统设计。 (一)下泵深度计算
根据5873.1-93标准推荐方法计算有杆抽油泵下泵深度:
(1)
(2) )1(w o w w l f f -+=ρρρ (3) 式中:—下泵深度,m ; H —油层中部深度,m ;
—流压,; —井液初期含水率,f ; ρl —井液密度,3 ρw —水密度,
3
,一般取1.0
ρ
o —地面原油密度,
3
γl —井液重度, 3;(γρl ×9800) —生产油气比,m 33;
—饱和压力,;—泵挂深处压力,; —标准状况压力,取101×103; t —泵挂深处井温,℃;
β—要求的泵充满程度,无因次小数,取0.4~0.6。
以上公式中,油气比对下泵深度影响较大。
参考计算结果,结合油田实际生产情况,可对泵深进行适当调整,使其更能满足实际生产需要。 (二)有杆泵抽汲参数优选
根据《采油工程手册》推荐方法对抽油参数进行优选。为减轻抽油杆柱的疲劳,减少弹性变形影响和冲程损失,原则上按抽油机最大冲程来初选冲程。用加速度因子(C )计算初选冲数(n ),冲数由下
l
s
wf p p p H L γ--=293
/)273)(1()1/1(293
/)273)(1(t f p R p t f p p R p w sc tp b w b sc tp s +-+-+-=β
式计算:
(4)
在选择冲程和冲数时一般要保证C< 0.225。根据“长冲程、低冲次、合理泵挂、较高泵效”的原则,结合油田试采生产情况或生产实践经验,优选抽汲参数。
常规情况下以最大冲程、中等冲次为原则,对稠油或较深泵挂井,应以最大冲程、较低冲次计算得出。
最大冲程常用的为4.8、3.2、2.7、2.1,要结合抽油机类型定。 (三)初期泵径计算及泵型选择
根据5873.1-93标准推荐方法由下式计算泵径:
(5)
式中:D —泵径,m ; —初期日产油量,; S —冲程,m ; n —冲数,1;
ρl —井液密度,3
—初期含水率,f ,
η—泵效,无因次小数,一般取0.6~0.7。
根据油藏工程部署和产能预测,根据公式(5)结果确定泵径。泵径要与下泵深度结合考虑。表1给出各种常用泵在实际应用中的最大下泵深度(主要考虑冲程损失及杆强度)。
表1 常用泵在实际应用中的最大下泵深度统计表
(四)抽油杆柱设计
抽油杆柱设计按各级抽油杆顶部最大应力相等原则设计。根据5873.1-93和5873.2-93标准,结合油田有杆泵采油实践经验:
按抽油杆大小一般来说:二级抽油杆的组合为25、22;22、19;19、16三种,三级抽油杆组合为25、22、19;22、19、16两种组合。
按泵的大小一般来说:φ56(57)及以下泵的抽油杆选择三级组合杆,φ70及以上泵选择二级组合。
视泵下深度及抽油杆顶部应力大小最后确定抽油杆组合。
l
o Sn fw q D ηρ)1(02974
.0-=1790
?=
s c
n
一般采用D 级抽油杆,超深抽井采用H 级杆或玻璃钢杆。 常用抽油泵杆组合可参考《采油技术手册》给出的数值(见表2、表3),然后根据油田(区块)的具体情况和各级杆柱强度校核值再进行适当调整。
表2 各级泵在最大允许下深的情况下D 级杆抽油杆组合推荐值
表3 各级泵在最大允许下深的情况下H 级杆抽油杆组合推荐值
在交变载荷作用下,抽油杆柱往往由于疲劳而发生破坏,所以应进行抽油杆柱强度校核。根据5873.1-93标准,应用原苏联奥金格计算方法进行抽油杆强度校核计算。
(6)
(7) (8)
式中:
σc — 折算应力,2;σ—抽油杆顶部最大应力,2; σ—抽油杆顶部最小应力,2;σa —应力幅度,2; [σ
-1]—抽油杆的许用应力,D
级抽油杆许用应力为902;
H 级抽油杆许用应力为100~1202;
—各级杆悬点最大载荷,N ;—各级杆悬点最小载荷,N ; —抽油杆柱截面积,2。
一般认为抽油杆应力利用率范围在0.60-0.95之间为合理,根据强度校核计算,各级抽油杆折算应力均应小于抽油杆许用应力,且应力利用率要比较均衡地分布在合理范围之内。如果各级应力大小分布差别较大或折算应力比抽油杆许用应力小很多,要考虑对抽油杆的组
r
a f
P P 22min
max min max -=-=σσσ[]
1-≤σσc a
c σσσmax =
合重新进行调整。 (五)抽油机选择
选择抽油机主要参考抽油机载荷利用率和扭矩利用率两项参数,故选择抽油机应根据前面优选的工作参数及杆组合计算出最大悬点载荷和最大扭矩,并进行载荷利用率和扭矩利用率计算。各型号抽油机的额定悬点载荷和额定扭矩见表4
一般认为抽油机载荷利用率和扭矩利用率合理范围为4080%,所选抽油机应满足载荷和扭矩要求。
表4 常用抽油机的额定载荷、扭矩及配套电机一览表
1、载荷计算:根据5873.1-93标准,悬点最大、最小载荷由下式计算:
(9) (10) 式中:—悬点最大载荷,N ;;
—悬点最小载荷,N ;
—抽油杆在空气中的重力, ,N ;
’
—液柱在柱塞面积上的重力,’ρl ,N ;
S —冲程,m ; n —冲次,1。
2、扭矩计算:根据《采油工程手册》推荐经验公式计算最大扭
)1790
1)((2
'
m ax
Sn W W P l r ++=)1790
1(2
m in Sn W P r -=
矩。其计算公式如下:
)(202.01800min max max P P S S M -+= (11)
式中:—减速箱输出轴最大扭矩,;其余符号同前。 3、电动机功率计算:
根据5873.1-93标准计算电动机功率。计算公式如下:
(12) 式中:N —电动机功率,;
η—总传动效率,及减速箱传动效率与皮带轮传动效率
的乘积,取0.85;
其余符号同前。 4、抽油机型号选择
根据上述悬点载荷和扭矩计算选择油机型号时,除要求能满足目前生产需要,还应考虑油田开发后期含水上升和提液需要,故抽油机型号应选偏大些。
抽油机选择应遵循以下原则:
a.选择抽油机应该在油井经济生产期内满足最大供液能力的需要;
b.应在使用期内有较高的载荷、扭距利用率在40-80%之间;
c.一般条件下油井应选用常规型抽油机,对稠油井或产能较高而套管直径相对较小的井,应选用具有较大冲程的抽油机;
d.所选抽油机应进行区域统筹,对同一区域或同一采油矿区所选机型尽量不要太杂。 (六)油管柱选择
参考5873.1-93标准和《采油工程手册》推荐方法,结合油田实际应用情况,油管一般选择φ89、φ73油管(以73油管为主),钢级为J55或N80(以J55油管为主)。
表5 根据抽油泵选择油管尺寸一览表
二、操作手册
当用户正确启动了这个程序之后,将会出现下面的窗体:
3m ax 10602-?=zc
n M N ηπ
本程序主要用于有杆泵抽油系统杆、管、泵及抽油机设计。
1.程序菜单
从上图可以看出,本程序有五个菜单项,从左到右分别是"参数输入"、"抽油杆柱最佳匹配"、"帮助"、"切换"。各项按钮功能介绍如下:(从左到右介绍)
(1)当用户打开"参数输入"时,出现"基础参数输入"、"输入合理值"菜单项:
①单击"基础参数输入"菜单项,将会出现如上的窗体:表中E3:E15、F15:G16数据要输入。
E1:输入冲程数据,要结合抽油机型号定,初期选4.8或3.2或2.7。
E2:输入油层中部深度数据。
E3:输入井液初期含水率数据,要根据油藏实际定,如没有一般选0.1。
E4:输入生产油气比数据,这个数据很重要,对泵下深度影响较大。
E5:输入饱和压力数据,注意单位为。
E6:输入流压数据,注意单位为,该值一般由油藏工程提供,如果没有,可以按饱和压力的8085%给值。
E7:输入泵挂深处井温数据,该值一般由油藏工程提供的油藏中部温度折算。
E8:输入初期日产油量数据,该值一般由油藏工程单井产能设计结果确定。
E9:输入泵效数据,一般取0.6-0.7。
E10:输入地面油密度数据,该值一般由油藏工程提供。
E11:输入油井最大产液含水率数据,该值一般由油藏工程开发指标预测结果提供。
E12:输入抽油杆钢级别数据,初选D级杆。
E15:G15:自上而下输入抽油杆直径选择数据,二级抽油杆的组合为25、22、22;22、19、19;19、16、16三种,三级抽油杆组合为25、22、19;22、19、16两种。
F16:G16:自上而下输入抽油杆占的比例。如不输则计算机默认给定。如果要抽杆最佳匹配,则可以不输。
②单击"输入合理值"菜单项,将会出现如上的窗体:
F4:G4:输入两种不同冲次。根据“长冲程、低冲次、合理泵挂、较高泵效”的原则,根据E4提供的计算结果,所选的值要小于计算值。
F5:输入下泵深度。根据E5提供的计算结果,所选的值要大于等于计算值,计算值(E5)不要超过右表提供的最大下泵深度值。
F6:输入泵径。根据E6提供的两个冲次计算的泵径结果,所选的值要大于或等于计算值。
(2)当用户打开"抽油杆柱最佳匹配"时,将出现"要最佳匹配时请按此"菜单项,单击"要最佳匹配时请按此"菜单项,计算机自动计算并给出最合理抽油杆比例值。
(3)当用户打开"结果表"时,将出现"结果表"、"最下级抽杆比例图"、"中间级抽杆比例图"、"下泵深度与气油比关系图"菜单项:
①单击"结果表"时,进入"结果"工作表,显示3种计算结果:
a :有杆泵采油系统设计表:冲次、下泵深度、泵径、悬点最大载荷、悬点最小载荷、减速箱输出轴最大扭矩、电动机功率、选定抽油机型号、油管外径选择、钢级等。
b :抽油杆柱设计表:抽油杆直径、抽油杆长度、抽油杆重量、液柱在柱塞面积上的重力(0.9)、液柱在柱塞面积上的重力(0.1) 等应力。
c :抽油杆柱许用应力计算表:不同冲次三级抽油杆最大、最小,应力幅度,抽油杆的许用应力等。其中上中下三个级别抽油杆的许用应力应该满足以下条件:许用应力相近且不超过最大许用应力(D级抽油杆许用应力为902、H级抽油杆许用应力为100-1202)
②单击"最下级抽杆比例图"时,进入"3"工作图,显示最下级抽杆最大比例值及最下级抽杆比例与应力关系曲线。
③单击"中间级抽杆比例图"时,进入"2"工作图,显示中间级抽杆最大比例值及中间级抽杆比例与应力关系曲线。
④单击"下泵深度与气油比关系图"时,进入"下泵深度图"工作图,显示气油比与下泵深度关系曲线。
(4)当用户打开"帮助"时,将出现"帮助"菜单项,单击"帮助"时,则进入帮助。
(5)当用户打开"切换"时,将出现一个"返回到"的菜单项:如果用户单击,将退出本软件主菜单,进入主菜单。在主菜单按"切换"的"切换到采油工程计算软件"菜单项,可进入本软件主菜单。这样可来回切换。
2.程序使用:
该程序的实际使用主要借助于"采油工程计算软件"菜单栏中的各按钮进行。具体使用步骤如下:
(1)单击"参数输入"中的"基础参数输入",:表中E3:E15、F15:G15数据要输入,F16:G16数据可根据情况输,如不输则计算机默认。
(2)单击"参数输入"中的"输入合理值",:表中F4、G4、F5、F6数据要输入。。(3)单击"抽油杆柱最佳匹配"中的"要最佳匹配时请按此",计算机自动计算并给出最合理抽油杆比例值。此项步骤视情况再定。如果用户自己输入抽油杆比例则该步骤不操作,如果要计算机自动给出抽油杆比例则进行此操作
(4)单击"结果"中的"结果表",列出计算结果表。
(5)单击"结果"中的"最下级抽杆比例图",显示最下级抽杆最大比例值,并可
打印曲线。
(6)单击"结果"中的"中间级抽杆比例图",显示中间级抽杆最大比例值,并可打印曲线。
(7)单击"结果"中的"下泵深度与气油比关系图",显示曲线并可打印曲线。(8)在完成后,单击"切换"中的"返回到"的菜单项时,可对文件进行保存。(9)完成以上工作后可单击"文件"的"退出"按钮,退出该程序。