fmea潜在失效模式-系统培训
FMEA失效模式与影响分析培训课程大纲

常用FMEA工具概述
FMEA表格
用于记录失效模式、影响、原因、控制措施等信息,是FMEA分 析的基础工具。
故障树分析(FTA)
通过图形化方式展示系统失效的逻辑关系,帮助识别潜在失效模式 。
因果图(鱼骨图)
用于分析失效原因,从人、机、料、法来自环等方面进行深入挖掘。软件辅助进行FMEA分析优势
高效性
通过减少产品失效,可以降低维修和 保修成本,提高客户满意度。
培训课程目标与内容
• 课程目标:使学员掌握FMEA的基本原理和方法,能够独立完 成FMEA分析,并具备在团队中推广和应用FMEA的能力。
培训课程目标与内容
课程内容 FMEA基本概念和原理
失效模式识别与评估
培训课程目标与内容
影响分析与风险控制
案例二
某石油化工企业对炼油装置进行FMEA分析,识别潜在的设备故障和操作风险,制定相应 的预防措施和应急预案,确保了生产过程的安全稳定运行。
案例三
某电力公司对变电站设备进行FMEA分析,通过识别潜在的电气故障和机械故障模式,优 化设备维护和检修计划,提高了电网运行的稳定性和可靠性。
04
FMEA工具与软件介绍
软件可快速处理大量数 据,提高分析效率。
准确性
软件内置算法可准确计 算风险优先数(RPN)
,避免人为误差。
可视化
软件提供图形化界面, 方便用户直观理解分析
结果。
可追溯性
软件可记录分析过程和 数据,方便后续审查和
改进。
工具软件操作演示
FMEA软件界面介绍
展示软件界面,介绍各功能模块。
数据输入与编辑
演示如何在软件中输入和编辑FMEA 相关数据。
案例分析
FMEA-培训教材

脑力风暴 Brainstorming
• 选定进行头脑风暴的小组成员。 • 一次只能有一人发言。 • 不要有任何人在会上起主导作用(平等原则)。 • 将会议中得到的所有IDEA都记录下来。 • 在头脑风暴过程中,不要对任何IDEA进行评价。 • 重要的是IDEA的数量,而不是质量。 • 将各种IDEA按失效模式和起因进行分类。 • 头脑风暴之后对失效模式进行优先排序。
FMEA做不好的原因
➢ 缺乏高层管理者的支持; ➢ 没有真正的专业人士的参与; ➢ 没有采用多方论证的方式; ➢ 没有投入足够的人力和时间; ➢ FMEA推动者缺乏组织协调能力; ➢ FMEA的编写者文字表达能力和逻辑思维能力欠缺; ➢ FMEA的参与者不愿奉献自己的知识; ➢ 没有完全掌握FMEA的基本方法。
预防
度
现行设计控制 探测
探 风险 测 顺序 度数
建议的措施
责任和
措施结果
目标完 成日期
采取的措施和 有效日期
严 重 度
频 度
探 测 度
风险 顺序
数
系统/子系统/部件
系统FMEA的范围
• 一个系统可以看作是由各个子系统组成的; • 这些子系统往往是由不同的小组设计的; • 系统FMEA的焦点是要确保组成系统的各子系统间的所有接
客户投诉
制造及装配 设计核准
FMEA
产品策划 时间
设计
寻找 方法 及 解决 问题
预防
制造 应用
脑力风暴 Brainstorming
• 脑力风暴是一种技法,可以激发小组成员产生大量 的有创意的点子。
FMEA培训资料潜在失效模式及后果分析

Potential Failure Mode and Effects Analysis
潜在失效后果
• 是指失效模式对系统功能的影响 • 要根据顾客或经理可能发现的情况来描
述失效的后果(顾客可以是内部或外部)
• 应记住不同级别系统、子系统和零件之
间还存在系统层次上的关系
潜在失效的后果
考虑以下方面: 对完成功能的影响 对上级系统和系统内其他零件的影响 对所有顾客的影响(包括使用成本) 对法规的影响 对营销方案/的影响 对可制造性/可装配性的影响
Potential Failure Mode and Effects Analysis
级别
• 是指产品特性分级 • 应用适当的方式进行标识 • 每一个在DFMEA中标识的特性均应在
PFMEA中有特殊的过程控制
级别—特殊特性
特性:产品或零件的尺寸、性能、外观、 重量等可定义的固有的特征。
特殊:一种是与安全和/或法规有关,即该特 性影响安全和/或法规;一种是该特性的波动 会影响到产品或零件的基本性能,但不会影响 到安全和/或法规。
FMEA小组应对评价准则和分级规则达成一致意见。 组织可对准则进行修改,不推荐修改9和10的准则。 严重度的定级可以通过修改设计、使之补偿或减轻失
效的后果来降低。如:“瘪胎”可以减轻突然爆胎的 严重度,“安全带”可以减轻车辆碰撞的严重程度。 “车辆/项目”在用于其他产品时,可理解为“最终产 品/生产产品”。如电视机/显示器、电脑/接线端子等。 9~10:与安全/法规有关,5~8:与性能/功能有关 2~4:与外观和感觉有关 严重度为1的失效模式不应进行进一步的分析。
的SFMEA,也可能没有SFMEA。 针对自行车(系统)、车架(子系统)
功能的DFMEA就是SFMEA,针对“下部 前车管”功能的则是DFMEA。
潜在失效模式及后果分析(FMEA)—培训教材.

決定失效模式
確認效應 確認原因 確認目前控制 評價嚴重度 評價發生度 評價偵測度 三種 評價 完成 ? 否 是 收集數據 進行變更 確認改變 執行改變 收集數據 原因順序 影響要因 確認改變 是 知道如何 影響 遴選最重要 失效模式
嚴重度? 發生度? 偵測度? 否
更新文件 重訂優先順序
CAUSE
MODE
EFFECT
FMEA
潜在失效模式及后果分析
何謂过程 FMEA?
过程的潛在 FMEA 是一種分析技術,係由負責过程的工程師或小組使用,在 儘可能的範圍內用來確保所有潛在的失效模式及其原因/機制均已納入考量並 予以處理。过程潛在 FMEA旨在: • 鑑別过程的機能和要求 • 鑑別潛在的產品和过程有關的失效模式 • 評估失效對顧客的潛在影響 • 鑑別潛在的製造或組裝過程原因和鑑別过程變數 ( Variables ),並 且據以控制降低發生率或失效情況的偵測度。 • 鑑別过程變數,以著眼於过程控制 • 列出潛在失效模式之排序,並據以建立考慮採取預防/矯正措施 的優先順序 • 將製造或組裝過程的結果予以文件化。
偵 測 度
R P N
建議措施
責任與 目標 完成日期
措施結果
嚴 難 偵 R
採行措施 重 檢 測 P
度 度 度 N
效應為何?
有多不好?
功能, 特徵 或要求為何?
原因為何?
其發生 頻率為何?
改善風險程度 能夠做什麼? -- 設計變更 -- 过程變更 -- 特別控制 -- 標準, 程序書 或指引變更 -- 導入防呆措施 -- 加強設備保養 -- 加強參數控制 -- 加強工作技能
FMEA
潜在失效模式及后果分析
FMEA 作業說明(FMEA 團隊遴選及流程)
FMEA潜在失效模式及后果分析培训(含实例解说)

1. 预防观念
潜在失效模式及后果分析
问题
优质企业
总数
项目
策划
项目 实施
验收
使用
劣质企业
问题 总数
项目 策划
项目 实施
验收
使用
2.何谓失效
潜在失效模式及后果分析
在规定条件下(环境、操作、时间)不能完成既定功能 在规定条件下,产品参数 值不能维持在规定的上下限之间;
产品在工作范围内,导致零组件的破裂、断裂、卡死等损坏现象。
CH1 引言
0. 生活的现象 1. 关于潜在的理解 2. 何谓失效 3. 后果应关注的内容 4. 风险是否存在 5. 对FMEA理解施
潜在失效模式及后果分析
0. 生活的现象--默菲定律
潜在失效模式及后果分析
默菲定律:如果坏事有可能发生,不管这种可能性多么小,它总会发生,并可能 引起更大的损失。
至今已经是 汽车行业的 作业标准 其他行业也 逐渐采用 1993年美国 AIAG发布 第一版 1995-2 2001-3 2008年美国 AIAG发布 第四版
2.何谓FMEA
What is FMEA?
潜在失效模式及后果分析
哪些原因可能 分析 现行预计的产品/过程 分析 对顾客或下
造成这个失模式
可能产生的失效模式
产品失效一般的表现形式如下: 硬式失效:产品非常明显表达一种功能停止现象实体破坏 软式失效:产品机能因退化(Degradation)、老化(Aging)、不稳定(Unstable)而不能
满足原有设计要求标准(其失效现象及判定标准必须加以量化)、功能退化、功 能不稳定等 失效模式:失效的具体表现形式
可采取的对策
是否消除
fmea培训内容

fmea培训内容FMEA(失效模式和影响分析)培训内容FMEA(失效模式和影响分析)是一种常用的风险管理工具,用于识别、评估和减少潜在的失效模式及其对系统或过程的影响。
FMEA培训旨在帮助参与者掌握FMEA方法和技巧,以有效地应用于实际工作中,提高风险管理能力和工作效率。
一、什么是FMEA?FMEA是一种系统性的方法,通过分析失效模式、评估其影响和确定风险等级,以提前识别和减少潜在的问题。
FMEA可以应用于各个领域,例如制造业、医疗保健、汽车工业等,帮助组织识别潜在的问题并采取相应的改进措施。
二、FMEA的基本步骤1. 确定分析范围:确定需要进行FMEA分析的系统、过程或产品,并明确分析的目的和范围。
2. 建立团队:组建一个跨职能的团队,包括相关的专业人员和利益相关者,以确保全面的分析和有效的决策。
3. 收集相关信息:收集系统、过程或产品的相关信息,包括设计、工艺、操作手册、历史数据等。
4. 识别失效模式:通过头脑风暴、经验分享等方法,识别可能的失效模式,并记录在FMEA表格中。
5. 评估影响:对每个失效模式进行影响评估,包括对安全、质量、生产效率等方面的影响进行定量或定性评估。
6. 确定原因和控制措施:确定导致失效模式的原因,并提出相应的控制措施,以减少或消除潜在的问题。
7. 评估风险等级:根据失效的严重性、发生频率和检测能力,评估风险等级,以确定优先处理的失效模式。
8. 制定改进计划:根据风险等级和控制措施的效果,制定相应的改进计划,并明确责任人和时间表。
9. 实施改进:按照改进计划的要求,实施所需的改进措施,并监控其效果。
三、FMEA的优势和应用1. 优势:- 提前识别潜在的问题,减少风险;- 增加对系统或过程的了解,改进设计和工艺;- 提高团队协作和沟通;- 降低成本,减少不良事件和事故的发生。
2. 应用:- 新产品开发:在产品设计阶段,通过FMEA识别潜在的问题,并采取相应措施,确保产品质量和安全性。
fmea培训

FMEA知识
PFMEA (Process Failure Model &Effects Analysis) 过程故障模式与影响分析 什么是 什么是PFMEA?
在生产制造过程开始前、开始后,用于确定、识别和消除在过程中 已知和潜在的失效、问题、错误的工程技术和系统方法,以避免有 缺陷的产品到达客户手中。(例如:小批量之前做PFMEA分析,确 认影响制造性和可操作性的因素,并制定对策) 考虑从单个零件到总成的所有制造过程。通过综合考虑生产制造中 的六个方面的因素:人员、设备、方法、材料、测量和环境来实现 故障的分析。
降低严重度等级、降低发生度等级
措施:进行必要的设计、工艺或制造过程变更 特点:属于更多的主动式措施,可以消除故障
降低检测度等级(提高检测概率)
措施:增加/加强检测 特点:属于被动式措施,成本高,对质量改进没有太大影 响,只能作为最后采取的手段。
实例
FMEA Sheet
建议 措施
负责部 门和责 任人 计划完 成日期
措施执行结果 已 采取 措施 新 严 重 度 新 发 生 度 新 检 测 度 风 险 顺 序 数
PFMEA实施步骤
• 产品/过程 产品/
工程师填写过程意图、目的、目标等。 工程师填写过程意图、目的、目标等。 常见的划分方法: 常见的划分方法: 按照产品内部组件可靠性框图:电源--主板--微波模块…….. 按照工序流程:贴导电胶--固化前清理--固化--固化后清 理……. 按照QC工程图:die Bond--QC-固化---Wire Bond --……. 按照时间和动作分析:略 按照设备顺序:略 以上为常见的划分方法,根据实际情况的不同会有不同的划分方法。
FMEA知识
风险顺序数( 风险顺序数(RPN)﹕ ) 风险度=严重度×发生度×检测度 风险度越大,就越应受到关注。 实际需要根据公司的质量目标确定可接 收的风险。 在PFMEA中,分析人员必须记住目标是 要降低RPN。
FMEA培训资料
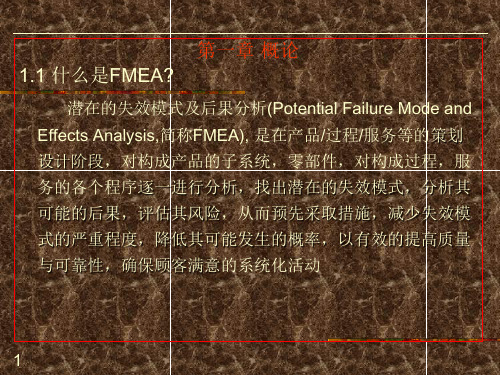
第一章 概论
1.5 DFMEA实施时机?
●设计方案初步确定时应开始FMEA初稿的编制。 ●作为设计活动的一部分,应该在设计任务完成之时
完成FMEA工作; ●在整个产品寿命周期内,根据反馈信息,在进行设
计修改时对FMEA进行重新评审和修改。 ● FMEA是一个动态的文件。
8
第一章 概论 1.4 PFMEA实施时机?
连接方法 1.不连接 2.铆接 3.螺纹连接 4.卡扣连接 5.压紧连接
16
第二章 产品设计FMEA(DMFEA) 2.1 DFMEA的准备工作(续)
●所要分析的系统、子系统或零部件的逻辑框图。它表 明信息、能量、力、流体等的流程。明确该系统的 输入、过程及输出。表明系统内零部件的联系和关 系。
17
失效链
跌落时发生 震动 环境条件
电池发热 伴生模式
11
焊锡脱落 锡渣碰到线路板
线路板短路 充电时不能限压
电池发生过充 电池损坏
根源模式 中间模式 最终模式
电池贮存一段时间
正、负极碎料掉入钢壳或 正、负极片膨胀
根源模式
正、负极片接触
零电压或低电压
伴生模式
12
电池微短路或短路 充不进电 电池报废
中间模式 最终模式
版作为QS9000质量体系要求文件的参考手册; ◇ 1994年,SAE发布SAEJ1739-潜在失效模式及后果分析; ◇ FMEA被广泛应用于其他行业,如卫生、电子、运输等。
4
第一章 概论 1.3 为什么要进行FMEA?
●有助于对设计中问题的早期发现,从而避免和 减少晚期修改带来的损失,使开发的成本下降;
● 开始于可行性阶段之前或过程中,在工装制造之前。 ◇在过程设计完成之时完成工作
培训课件潜在的失效模式及后果分析fmea

协作性:
虽然 FMEA 的编制责任通 常都指派到某个人,但是 FMEA 的输入应该是小组的努力。
小组成员应由知识丰富的 人员组成(如设计、分析/试验 、制造、装配、服务、质量及 可靠性等方面的有丰富经验的 工程师)
7
潜在失效模式及后果分析 FMEA
主观性
FMEA 的特点(3)
31
(22)
过程 FMEA 的開發
5 )車型年/車輛類型
填入將使用和/或正被分析的設計所影響的預期車型年
及車輛類型。 (如果已知的話)
过 程 FMEA
系统
X 子系统 ______部件 01.03/车身密封 (2) 车型年/车辆类型 199X/狮牌 4门/旅行车 (5) 核心小组: T.芬德-轿车产品开发部、切利得斯-制造部、J.福特-总
建議 措施
責任及目標 完成日期
措施結果
采取 的措施
R S ODP
N
功能、特性或 要求是什么?
綴彆岆 妦繫ˋ
衄嗣 媎詹ˋ
岆妦繫ˋ
楷汜腔 ˋ
能做些什么? - ??更改 - ?程更改
特殊控制 - ?准、程序或
指南的更改
?有什么??? - ?功能 - 部分功能/功能
?? /功能降? - 功能?歇 - 非?期功能
2
潜在失效模式及后果分析 FMEA
3
潜在失效模式及后果分析
FMEA
4
潜在失效模式及后果分析 FMEA 什么是 FMEA
FMEA 一組系統化的活動
(a)發現、評價產品/過程中潛在的失效及其後果 (b)找出能夠避免或減少這些潛在失效發生的措施 (c)全部過程形成文件
5
潜在失效模式及后果分析 FMEA
FMEA潜在的失效模式及后果分析(培训内容)

1、FMEA 的概念: 指 Potential Failure Mode and Effects Analysis(潜在的
失效模式及后果分析)的英文简称。
P ( Potential ) 潜在的 F ( Failure ) 失效
M ( Mode ) 模式
A ( And ) 及/和 E ( Effects ) 后果 A ( Analysis ) 分析 ■ FMEA 是潜在的失效模式及后果分析的缩写,本应写成P-FMEA, 但由于企业/公司常用D-FMEA表示产品FMEA,用P-FMEA表示过 程FMEA,所以用FMEA表示潜在的失效模式及后果分析,以免混淆。
潜在的失效模式及后果分析概要介绍
10、FMEA 的工作架构:(3/3)
6)当前控制: ■ 你(对现有设计)做了什么?或你(对将来设计)会做什么 以用来评估,消除或减少风险发生? ◆ 避免原因发生 ◆ 提早确定问题存在 ◆ 减少后果及影响 7)风险评估: ■ 将频度(O)、探测度(D)和严重度(S)的结果综合并做 风险评估。 ■ 用RPN(风险顺序数)表示: RPN =(O)×(D)×(S)
8)建议改善措施:无论你对总体风险评估满பைடு நூலகம்与否,你都应写出计划。 9)根据建议的改善措施,你做了什么?
潜在的失效模式及后果分析概要介绍
11、FMEA 与 FMA 的区别 1)失效模式分析(FMA)的概念和定义: 失效模式分析(Failure Mode Analysis:简称 FMA):指用来分析当 前和以往过程的失效模式数据,以防止这些失效模式将来再发生的正 式的结构化的程序。FMA是一种事后的纠正行为。 2)FMEA — 潜在的失效模式及后果分析,是“事前的预防措施”,并 “由下至上”进行分析。 ■ 关键词:潜在的 — 失效还没有发生 ■ 可能发生 ■ 但不一定会发生 ■ “核心”集中于:预防 — 处理预计的失效,其原因及后果/影响 ■ 主要工作:风险评估 — 潜在失效模式的后果影响 ■ FMEA 开始于产品设计和制造过程开发活动之前,并指导贯穿实施 于整个产品周期 3)FMA — 失效模式分析,是对产品/过程已经发生的失效模式分析其产 生的原因,评估其后果及采取纠正措施的一种活动。FMA是“事后的 纠正措施”。 ■ 关键词:失效 — 已实际发生 ■ 100% 既成事实 ■ “核心”集中于:诊断 — 处理已知的失效 ■ FMA 在生产或范围内实施,指引的是开发和生产
2024版FMEA培训教材(共14)

FMEA核心思想
预防性
FMEA强调在产品设计或过程设 计阶段进行预防性的分析,识别
并消除潜在的失效模式。
结构化
FMEA采用结构化的分析方法, 通过系统的、有条理的分析过程 来识别潜在的失效模式及其影响。
优先级
FMEA根据失效模式的严重度、 发生频度和探测度来评估其风险 优先级,以便优先处理高风险失 效模式。
01
02
03
04
FMEA报告
编写FMEA报告,包括分析过 程、结果汇总、风险控制措施
和建议等。
风险矩阵图
绘制风险矩阵图,直观展示各 种失效模式的风险等级和分布
情况。
改进措施计划
针对高风险失效模式,制定详 细的改进措施计划,明确责任
人、时间节点和预期效果。
经验教训总结
总结FMEA实施过程中的经验 教训,为后续产品设计和制造
跟踪改进措施实施情况
对制定的改进措施进行跟踪,确保措 施得以有效实施并取得预期效果。
产品设计阶段FMEA案例分析
案例一
案例二
某型号手机电池过热问题。通过对手 机电池设计进行FMEA分析,发现电池 过热可能导致手机性能下降甚至引发 安全问题。经过评估,该故障模式的 严重性较高。针对这一问题,改进措 施包括优化电池散热设计、提高电池 热稳定性等。
可靠性等方面的人员。
收集资料和信息
03
收集与产品、过程、历史数据等相关的资料和信息,以便进行
全面分析。
FMEA实施过程
识别潜在失效模式
通过分析设计、制造过程、使用条件 等方面,识别产品可能出现的潜在失 效模式。
确定风险等级
综合考虑失效模式的严重度、发生频 度和探测度,确定每种失效模式的风 险等级。
潜在失效模式与后果分析(FMEA)培训

表面加工规范错误 维修保养说明错误
演算法不适当
维修保养说明不适当
16. 发生率(O):在设计的寿命中某一特定失效起 因/机理发生的可能性。描述发生率的级别数重在 其含义,而不是具体的数值。通过设计更改更改 来预防或控制该失效模式的起因/机理是降低发生 率级别数的唯一途径。
确定等级需考虑: 维修历史情况 部件是否全新设计 环境有无变化 用途有何变化 是否采取了预防性控制措施 针对用途,是否作了工程分析(如可靠度)来估计
构成零件
组件 功能件 子系统 系统
人、环境等
零件故障
对组件 的影响
FMEA的分析层次
对功能 件的影响
对子系 统的影响
对系统 的影响
对人和环境 等的影响
图1-1 FMEA的影响分析层次
设计FMEA的一个关系方块图(分析中所考虑的项目)
也可用其他形式的方块图
开关
3
2
灯泡总成
灯罩
4
4
1
极板
电池
弹簧
5
5
连接方法:1.不连接(滑动配合) 2.铆接 3.螺纹连接 4.卡扣连接 5.压紧装接
• “系统”的概念
1、“系统”。系统是指具有全部功能并可达成要求的任务 的产品,如汽车、轮船、飞机等可以称为机械系统;电脑、 卫星、移动电话等可称为电子系统。
2、子系统。子系统是系统的构成部分,能达成系统的部分 功能,如汽车的动力系统、电脑的显示系统等。
3、构成件。构成件是构成子系统和系统的单元,可分为功 能件、组件和零件。
没有特定的RPN值要求强制措施
1、小组的焦点应该定位于严重度最高等级的失效模式,当严重 度等级为9或10时,必须强制确保风险通过存在的设计控制 或建议措施来陈述
FMEA-培训教材

DFMEA的目的
• 根据潜在失效模式对“顾客”的影响,对其 进行排序列表,进而建立一套改进设计和开 发试验的优先控制系统。
• 为推荐和跟踪降低风险的措施提供一个公开 的讨论形式
• 为将来分析研究现场情况,评价设计的更改 及开发更先进的设计,提供参考。
DFMEA顾客的定义
• DFMEA“顾客”的定 义,不仅仅指“最終 使用者”,并且包括 车型设计或更高一级 装配过程设计的工程 师/设计组,以及在 生产过程中负责生产、 装配和售后服务的工 程师。
FMEA 的关键术语
• 顾客输入 • 小组—小组的选择(横向功能小组) • 等级—等级的确定 • 风险评估 • 设计过程 • 生产过程
汽车行业缩略语
• AIAG Automotive Industry Action Group • APQP Advanced Product Quality Planning • DFMEA Design Failure Mode and Effect Analysis • DOE Design of Experiments • FMEA Failure Mode and Effect Analysis • KCC Key Control Characteristic • KPC Key Product Characteristic • PFMEA Process Failure Mode and Effect Analysis • PPAP Produce Part Approval Process • QFD Quality Function Deployment
脑力风暴 Brainstorming
4个明确阶段 • 问题开始 • 问题再开始 • 对一个或多个陈述进行讨论(脑力风暴) • 评论产生的点子 通过去除法找出决定最终列表—找
TS16949FMEA潜在失效模式与后果分析培训教材第

主要功能失效(车辆可操作,但降低操作性)
次要功能损 次要功能失效(车辆可操作,但舒适性/方便性项目不能运行) 失或降低
次要功能失效(车辆可操作,但舒适性/方便性降低)
烦恼
外观、杂音/异响,车辆可操作,75%以上顾客能感觉到缺陷
外观、杂音/异响,车辆可操作, 50%的顾客能感觉到缺陷。
33
大众的评价准则(91年)
缺陷 级别
特别严 重 严重
中等严 重 轻微
人身 事故 伤害
易
运转失灵 必然*
现场难以确 定位置的间 隙故障
必然
次于标 准的运 转故障
增加保养 次数或缩 短寿命
顾客安 外形、涂 装上的 层或工艺 困难 上的困难
必然** 大概会 可能会
不会
必然 必然 可能会 可能会 不会 不会
10
谁编制FMEA?Who shall edit FMEA?
小组
以设计/制造工程师为主的小组 小组成员:可以包括设计、制造、分析/试验、可靠 性、材料、质量、服务、物流、设备制造商、设备 维护、供方,以及更高或更低一级的设计人员。 DFMEA小组: PFMEA小组:
11
第四版对小组成员作用的说明
16
第二部分 设计FMEA(DFMEA)
17
DFMEA过程
——框图、P图 ——DFMEA ——DVP&R
18
DFMEA的关注
DFMEA从产品概念成形前开始,在生产设 计发布前完成。 DFMEA关注: ——设计本身。全力研究后设计风险仍然较高 时,应传递至PFMEA继续关注 ——可制造性/可装配性(如拔模斜度、公差、 装配空间、表面处理、材料硬度限制等) ——服务可行性/回收技术(如工具的可获得 性、诊断能力、材料分类标记等)
FMEA(潜在失效模式及后果分析)培训教材

三、怎样做FMEA——表单填写
9)探测度(D):
填入对采用“现行控制”方法来控制时,该潜在问题可以被检查出来的 难易程序的评价。
探测度采用1-10分制,得分愈高则愈难以被检出。 探测度是对现行控制方法有效性的评估。 依据《探测度对照表》进行评分。
6
低
生产线破坏不严重,产品需要100%返工,产品/系统能运行,但有些舒用性或方便性 项目性能下降,客户有些不满意。
5
很低
生产线破坏不严重,产品经筛选,部分(少于100%)需要返工,产品规格不符合要 求,多数客户发现有缺陷。
4
轻微
生产线破坏较轻,部分(少于100%)需要在生产线上其它工位返工。产品规格不符 合要求,有一半客户发现有缺陷。
3
很轻微
生产线破坏轻微,部分(少于100%)产品需要在生产线上原工位返工。产品规格不 符合要求,很少客户发现有缺陷。
2
无
无可辨视的影响。
1
三、怎样做FMEA——表单填写
5)级别:
填入特殊特性的标识符号。 凡是识别为特殊特性,需要特殊过程控制的项目应当以适当的符号在 此栏中标识,使用顾客或公司规定的符号。 产品特性以▲标识,过程特性以▼标识。 特殊特性依据《特殊特性明细表》和《特殊特性矩阵图》进行识别。
三、怎样做FMEA——表单填写
三、怎样做FMEA——表单填写
5.2 表单部分:
1)功能要求 2)潜在失效模式 3)潜在失效后果 4)严重度(S) 5)级别 6)潜在失效起因/机理 7)频度(O) 8)现行控制 9)探测度(D) 10)风险顺序数(RPN) 11)建议措施 12)责任及目标完成日期 13)措施结果
充分发挥小组的经验,采用头脑风暴法,对可能的原因进行归纳分析。
FMEA潜在失效模式及后果分析培训教程

FMEA与DFMEA、PFMEA集成
01
将FMEA与设计FMEA(DFMEA)和过程FMEA(PFMEA)集
成,实现全流程的失效模式分析。
FMEA与可靠性工程集成
02
将FMEA与可靠性工程方法相结合,提高产品和过程的可靠性。
FMEA与项目管理工具集成
03
将FMEA与项目管理工具集成,实现FMEA活动的项目化管理。
医疗器械行业
心脏起搏器
对于心脏起搏器等高风险医疗器械,FMEA可应用于设计和生产阶段,识别可 能的电池耗尽、导线断裂等失效模式,并评估其对病人生命安全的潜在影响。
医用影像设备
在医用影像设备中,FMEA可分析成像质量不佳、软件故障等潜在问题,以确保 设备在诊断过程中的准确性和可靠性。
航空航天领域
飞机发动机
FMEA潜在失效模式及后 果分析培训教程
• 介绍 • FMEA的基本原理 • FMEA的执行过程 • FMEA的应用实例 • FMEA的挑战与解决方案 • FMEA的未来发展
01
介绍
FMEA的定义
• 潜在失效模式及后果分析(Failure Modes and Effects Analysis,简称FMEA):是一种预防性的质量工具,用于识 别、评估和优先处理产品或过程中可能出现的潜在失效模式及 其对系统性能的影响。
飞机发动机的FMEA分析重点在于识别可能导致性能下降或 安全事故的失效模式,如涡轮叶片断裂、燃油系统泄漏等。
航天器
在设计和制造航天器时,FMEA可应用于分析轨道衰减、太 阳能电池板展开失败等潜在问题,以确保航天器的可靠性和 安全性。
05
FMEA的挑战与解决方案
数据收集和分析的挑战
挑战
FMEA-培训

失效模式
在規定条件 下, (环境、 操作、时间 ) 不能完成既 定功能。
产品在工作范 围內 , 导致零 组件的破裂、 断裂、卡死、 損坏現象
失效
I类:不能完 成规定的功能; II 类: 产 生了 非期望的功能
13
FMEA基本要素间的关联
FMEA计划
原因 失效模式 后果
频度
探测度
严重度
风险分析和潜在的失效模式及后果分析解释 执行建议措施并验证其有效性 实施措施
系方式以及工程师的所属组织。
38
潜在失效模式及后果分析(设计FMEA)
27
DFMEA的概述
DFMEA中顾客的定义: 1)最终使用者
2)OEM组装和制造中心
3)政府法规机构
28
DFMEA实施流程
1.组织小组;
2.DFMEA功能框图;
3.列出每一个零件、部件、子系统的失效模式; 4.确定失效模式的等级(关键、重要、一般) 5.优先关注关键零件特性; 6提出改进和预防措施建议;
35
如何做DFMEA
◇ 部件FMEA的范围
部件FMEA通常是一个以子系统的组成部分为焦点的
FMEA,例如,螺杆是前悬挂(底盘系统的一个子系统) 的一个部件。
36
设计FMEA表头
设计职责(C):输入负责设计的OEM、组织、部门或小
组;适用时,输入供应商组织名称。
车型年/项目(D):输入将使用或者受分析的设计影响的预期
“早知道… …就不会” 早知道 早知道 早知道 早知道 作好防震设计 改进电力输配设计 不滥砍滥伐 作好桥梁设计 就不会 就不会 就不会 就不会 造成大楼倒塌 造成美国等国的大停电 造成泥石流 造成大桥倒塌
- 1、下载文档前请自行甄别文档内容的完整性,平台不提供额外的编辑、内容补充、找答案等附加服务。
- 2、"仅部分预览"的文档,不可在线预览部分如存在完整性等问题,可反馈申请退款(可完整预览的文档不适用该条件!)。
- 3、如文档侵犯您的权益,请联系客服反馈,我们会尽快为您处理(人工客服工作时间:9:00-18:30)。
二. 設計FMEA---簡介(2)
設計FMEA是一份動態的文件, 應: (a)在一個設計概念最中形成之時或之前開始 (b)在產品開發的各階段, 發生更改或穫得更多的信息時, 予以持續的更新. (c)在產品加工圖樣完工之前全部完成. 設計FMEA以應考量制造/裝配過程中技術/身體的限制. 如: (a)表面處理的限制 (b)材料的限制 (c)公差/過程能力 設計FMEA還應考慮產品維護(服務)及回收的技術/身體的 限制. 如: (a)工具的可接近性 (b)診斷能力 (c)材料分類
GO / NO GO 計數型:較易研判 計量型:功能與規格界限不易確定
2013-6-15 郭正桃 9
一. FMEA概要---概述(8)
物品直接表現失效的形式如下: 1. 實體破壞:硬式失效 2. 操作功能中止 3. 功能退化 4. 功能不穩定
軟式失效
2 ~ 4 項物品機能因老化 ( Aging )、退化( Degradation ) 或不穩定(Unstable)而不能滿足原設定的要求標準, 所以 失效現象及研判準則必頇量化。
設計FMEA開發準備工作
2013-6-15 郭正桃 18
二. 設計FMEA---開發(2)
___係統 FMEA編號____ 潛在失效模式及後果分析(設計FMEA) ___子係統 共__頁; 第__頁 設計責任______________ 編制人____________ 產品名稱______________ 關健日期______________ FMEA編制日期______修定日期_____ 設計小組______________ 核心小組________________________________________________ 責 任 及 目 標 完 成 日 期
2013-6-15
郭正桃
3
一. FMEA概要---概述(2)
”早知道 ……… 就不會 ”
早知道 作好防震設計 就不會 造成大樓倒塌 早知道 改進電力輸配設計 就不會 造成全台大停電 早知道 不濫墾濫伐 就不會 造成土石流 早知道 作好橋樑維護 就不會 造成高屏大橋倒塌
有些 早知道 是必需的!有些 就不會 是不允許發生的
有效運用 FMEA 可強化事先預防
2013-6-15 郭正桃 5
一. FMEA概要---概述(4)
1.對產品設計與製程進行失效分析, 找出元 / 組件的 失效模式,鑑定出它的失效原因,並評估該項失效 模式對系統會產生什麼影響。
2.找出元 / 組件或系統的潛在弱點,提供設計、製造、
品保等單位採取可行之對策,及早進行設計與製程 研改,強化產品品質。 3.書面描述上述分析過程,確保產品品質符合顧客需 求。
甚麼是FMEA: Potential Failure Mode and Effects Analysis潛在失效模式及後果分析. FMEA可以描述一個係統化的活動, 其目的是: (a)認可並評價產品/過程中的潛在失效以及該失效的後果 (b)確定能夠清除或減少潛在失效以及發生機會的措施 (c)將全部過程形成文件 FMEA是對確定設計或過程必頇作哪些事情才能使顧客滿意 這一過程的補充 所有的FMEA都關注設計, 無論是產品設計還是過程設計
有效運用 FMEA 可減少事後追悔
2013-6-15 郭正桃 4
一. FMEA概要---概述(3)
”我先 …… 所以沒有 ”
我先 看了氣象預報 所以沒有 淋成落湯雞 我先 評估金融大樓高度 所以沒有 影響飛安
我先 設計電腦防火牆 所以沒有 被駭客入侵
有些 我先 是必需的!有些 所以沒有 是預期可避免的
20
二. 設計FMEA---開發(4)
係統 自行車
設計目標: 1)騎行至少3000小時無需 保養, 壽命為10000小時. 2)適用於99.5%成年男子 騎用, 舒適便利. 功能: --便於使用 潛在失效模式: 1)方向不好用 2)腳踏板不好用 功能: --提供可靠的交通運輸 潛在失效模式: 1)鏈條經常斷 2)需經常修理車胎
2013-6-15
郭正桃
11
一. FMEA概要---實施(1)
一般的企業都會傾向於盡可能的持續改進產品和過程的質 量, 所以將FMEA作為專門的技術應用以識別並幫助最大限 度的檢少潛在的隱患一直是非常重要的. 成功實施FMEA項目的最重要因素之一是時間性. 其含義是 指“事件發生前”的措施, 而不是“事實出現後”的演練. 為實現最大價值, FMEA必頇在產品或過程失效模式被納入 到產品或過程之前進行. 事先花時間很好的完成FMEA分析, 能夠最容易低成本的對產品或過程進行更改, 才能最大限 度的降低後期更改的危機 FMEA的編制雖然是指派到某人, 但FMEA的輸入應是小組的 努力. 小組應由知識豐富的人組成, 包括設計/分析/試驗 /制造/裝配/服務/質量/可靠性等方面經驗豐富的工程師.
EA
3.關鍵性分析(critical analysis)
CA
對每一個失效模式,依其嚴重等級和發生機率綜合評 估並予以分類,以便確定預防或改正措施的內容和優 先順序。
2013-6-15
郭正桃
8
一. FMEA概要---概述(7)
失效的定義 根據Collins (1981) 的定義「失效為一件裝備,裝備的組件或 一件結構發任何形狀、尺度或材料性質的變化,造成這些物 品處於無法充分地執行其特定的功能的狀態。」 規格:對於系統或裝備的性能或功能 範圍,必頇驗証時可以量測。
把手總成
前輪總成
下前車管
下後車管
2013-6-15
係統/子係統/部件關係 郭正桃 ---項目/功能/失效模式
FMEA工程師的責任
2013-6-15 郭正桃 15
二. 設計FMEA---簡介(1)
設計FMEA是由負責設計的工程師/小組主要採用的一種技 術, 用以最大限度的保證各種潛在失效模式及其相關的起 因已得到充份的考慮和說明. 對最終的項目及與之相關的 每個係統/子係統和部件都應進行評估. 設計FMEA以最嚴密的方式總結了設計一個部件/子係統或 係統時小組的設計思想(包括根據以往的經驗可能會出錯 的一些項目的分析). 這種係統化的方法體現了一個工程 師在任何設計過程中正常經歷的思維過程, 並使之規范化 與文件化. 設計FMEA為設計過程提供支持, 它以如下方式降低失效: (a)為客觀的評價設計, 包括功能與方案, 提供幫助 (b)評價為生產/裝配/服務/回收所作的出步設計 (c)根據潛在失效模式後果對顧客的影響, 為設計更改/開 發/確任實驗/分析建立一套優先控制係統. 16 2013-6-15 (d)為降低風險提供一個公開討論形式. 郭正桃
2013-6-15
郭正桃
14
一. FMEA概要---實施(4)
責任工程師應確保採取有效的預防/糾正措施並對這些措 施加以適當的追蹤. FMEA是動態的文件, 應始終反應最新水平及最近的相關措 施, 包括開始生產以後發生的. 責任工程師應確保所有的建議措施都得到實施或充份強調. 通常有如下幾種方法: (a)對設計/過程/圖樣進行評審, 以確保建議的措施得到 實施 (b)確認更改已納入到設計/裝配/制造文件中 (c)對設計/過程FMEA及FMEA的特殊應用以及控制計劃進行 評審.
子係統 車架
功能: --為座位織撐提供穩定的 附屬物 潛在失效模式: 1)座位織撐的結構性失效 2)座位織撐的過大形變 功能: --提供好看的外觀 潛在失效模式: 1)外觀光亮度變壞 2)漆皮開裂
部件 上部車架
功能: --提供結構性支撐 潛在失效模式: 1)結構性失效 2)過大形變 功能: --對正確車架提供尺寸 控制 潛在失效模式: 1)車架安裝點長度過長 2)車架安裝點長度過短
2013-6-15 7
郭正桃
一. FMEA概要---概述(6)
1.失效模式分析(failure mode analysis)
由下而上分析,即由元件、組件至系統,確定在系統內不 同結構層或功能層次的失效模式。
FM
2.失效效應分析(failure effect analysis)
對每一個失效模式,確定其失效對其上一層模組及最終系 統的失效影響,了解其組件介面失效關聯性,做為改進行 動的依據。
2013-6-15 郭正桃 6
一. FMEA概要---概述(5)
1. 及時性是成功實施FMEA的最重要因素之一。 2. 它是“事前的預防”而不是“事後的追悔”。 3. 事先花時間進行FMEA分析,能夠容易且低成本 地對產品設計或製程進行修改,從而減輕事後修 改的危機。
4. FMEA能夠減少或消除因修改而帶來更大損失的 機會,它是一個相互作用的過程,永無止境的改 善活動。
設計FMEA的時機與注意事項
2013-6-15 郭正桃 17
二. 設計FMEA---開發(1)
設計FMEA開發階段的準備工作 應: (a)列出設計期望作甚麼與不期望作甚麼清單 (b)顧客期望或需求---質量功能展開表(QFD) (C)已知的產品要求和或制造/裝配/服務/回收等 要求, 期望特性定義越明確就越容易識別潛在的 失效模式, 以便採取預防/糾正措施. 設計FMEA應從分析係統/子係統/零部件的框圖開 始.
2013-6-15
FMEA工作順序
郭正桃
13
一. FMEA概要---實施(3)
FMEA工作順序
子 係 統 潛 在 失 效 模 式 潛 在 失 效 後 果
後果 是甚 麼?
功 能 要 求
功能/ 要求/ 特性 是甚麼
嚴 重 度 S
級 別
潛 在 失 效 起 因 / 機 理
頻 度 O
現行控制
預 防
探 測
探 測 度 D
R P N
建 議 措 施
有多 嚴重?
責 任 及 目 標 完 成 日 期
措施結果