SIHFIZ24G-E3中文资料
三星Exynos 4 Quad (Exynos 4412) RISC微处理器用户手册

Samsung Exynos 4 Quad(Exynos 4412)RISC MicroprocessorRevision 1.00October 2012 U s e r's M a n u a l2012 Samsung Electronics Co., Ltd. All rights reserved.Important NoticeSamsung Electronics Co. Ltd. (“Samsung”) reserves the right to make changes to the information in this publication at any time without prior notice. All information provided is for reference purpose only. Samsung assumes no responsibility for possible errors or omissions, or for any consequences resulting from the use of the information contained herein.This publication on its own does not convey any license, either express or implied, relating to any Samsung and/or third-party products, under the intellectual property rights of Samsung and/or any third parties.Samsung makes no warranty, representation, or guarantee regarding the suitability of its products for any particular purpose, nor does Samsung assume any liability arising out of the application or use of any product or circuit and specifically disclaims any and all liability, including without limitation any consequential or incidental damages.Customers are responsible for their own products and applications. "Typical" parameters can and do vary in different applications. All operating parameters, including "Typicals" must be validated for each customer application by the customer's technical experts.Samsung products are not designed, intended, or authorized for use in applications intended to support or sustain life, or for any other application in which the failure of the Samsung product could reasonably be expected to create a situation where personal injury or death may occur. Customers acknowledge and agree that they are solely responsible to meet all other legal and regulatory requirements regarding their applications using Samsung products notwithstanding any information provided in this publication. Customer shall indemnify and hold Samsung and its officers, employees, subsidiaries, affiliates, and distributors harmless against all claims, costs, damages, expenses, and reasonable attorney fees arising out of, either directly or indirectly, any claim (including but not limited to personal injury or death) thatmay be associated with such unintended, unauthorizedand/or illegal use.WARNING No part of this publication may be reproduced, stored in a retrieval system, or transmitted in any form or by any means, electric or mechanical, by photocopying, recording, or otherwise, without the prior written consent of Samsung. This publication is intended for use by designated recipients only. This publication contains confidential information (including trade secrets) of Samsung protectedby Competition Law, Trade Secrets Protection Act and other related laws, and therefore may not be, in part or in whole, directly or indirectly publicized, distributed, photocopied or used (including in a posting on the Internet where unspecified access is possible) by any unauthorized third party. Samsung reserves its right to take any and all measures both in equity and law available to it and claim full damages against any party that misappropriates Samsung’s trade secrets and/or confidential information.警告本文件仅向经韩国三星电子株式会社授权的人员提供,其内容含有商业秘密保护相关法规规定并受其保护的三星电子株式会社商业秘密,任何直接或间接非法向第三人披露、传播、复制或允许第三人使用该文件全部或部分内容的行为(包括在互联网等公开媒介刊登该商业秘密而可能导致不特定第三人获取相关信息的行为)皆为法律严格禁止。
BDW24-S中文资料

●Designed for Complementary Use with BDW23, BDW23A, BDW23B and BDW23C ●50 W at 25°C Case Temperature ● 6 A Continuous Collector Current ●Minimum h FE of 750 at 2 A, 3 Vabsolute maximum ratings at 25°C case temperature (unless otherwise noted)NOTES:1.Derate linearly to 150°C case temperature at the rate of 0.4 W/°C.2.Derate linearly to 150°C free air temperature at the rate of 16 mW/°C.RATINGSYMBOLVALUE UNITCollector-base voltage (I E = 0)BDW24BDW24A BDW24B BDW24C V CBO -45-60-80-100V Collector-emitter voltage (I B = 0)BDW24BDW24A BDW24B BDW24CV CEO -45-60-80-100V Emitter-base voltage V EBO -5V Continuous collector current I C -6A Continuous base currentI B -0.2A Continuous device dissipation at (or below) 25°C case temperature (see Note 1)P tot 50W Continuous device dissipation at (or below) 25°C free air temperature (see Note 2)P tot 2W Operating junction temperature range T j -65 to +150°C Storage temperature rangeT stg -65 to +150°C Operating free-air temperature rangeT A -65 to +150°CNOTES:3.These parameters must be measured using pulse techniques, t p = 300 µs, duty cycle ≤ 2%.4.These parameters must be measured using voltage-sensing contacts, separate from the current carrying contacts.† Voltage and current values shown are nominal; exact values vary slightly with transistor parameters.electrical characteristics at 25°C case temperature (unless otherwise noted)P ARAMETER TEST CONDITIONSMIN TYPMAXUNITV (BR)CEOCollector-emitter breakdown voltageI C = -100 mA I B = 0(see Note 3)BDW24BDW24A BDW24B BDW24C -45-60-80-100VI CEOCollector-emitter cut-off currentV CE =-30VV CE =-30V V CE =-40V V CE =-50V I B =0I B =0I B =0I B =0BDW24BDW24A BDW24B BDW24C -0.5-0.5-0.5-0.5mA I CBOCollector cut-off current V CB =-45VV CB = -60 V V CB = -80 V V CB = -100 VI E =0I E =0I E =0I E =0BDW24BDW24A BDW24B BDW24C-0.2-0.2-0.2-0.2mA I EBO Emitter cut-off current V EB = -5 V I C =0-2mA h FE Forward current transfer ratio V CE = -3 V V CE = -3 V V CE = -3 V I C =-1A I C =-2A I C =-6A (see Notes 3 and 4)100075010020000V CE(sat)Collector-emitter saturation voltage I B = -8 mA I B = -60 mA I C =-2A I C =-6A (see Notes 3 and 4)-2-3V V BE(sat)Base-emitter saturation voltage I B = -8 mA I C = -2 A (see Notes 3 and 4)-2.5V V BE(on)Base-emitter voltage V CE = -3 V V CE = -3 V I C =-1A I C =-6A (see Notes 3 and 4)-2.5-3V V ECParallel diode forward voltageI E = -2 AI B = 0-1.8Vthermal characteristicsP ARAMETERMINTYPMAX UNIT R θJC Junction to case thermal resistance 2.5°C/W R θJAJunction to free air thermal resistance62.5°C/Wresistive-load-switching characteristics at 25°C case temperatureP ARAMETER TEST CONDITIONS †MINTYP MAXUNIT t on T urn-on time I C = -3 A V BE(off) = 4.5 VI B(on) = -12 mA R L = 10 ΩI B(off) = 12 mA t p = 20 µs, dc ≤ 2%1µs t offT urn-off time5µs。
si24r2h工作原理__理论说明

si24r2h工作原理理论说明1. 引言1.1 概述在当代科技领域中,无线通信技术正日益成为人们生活的重要组成部分。
其中,si24r2h作为一种高性能、低功耗的无线传输模块,在物联网等应用场景中得到了广泛应用。
本篇文章将对si24r2h的工作原理进行详细的理论说明,以帮助读者进一步了解该模块的运作机制。
1.2 文章结构本文将分为五个主要章节来阐述si24r2h的工作原理和相关内容。
其中,引言部分将对文章的背景和目标进行介绍。
接下来的章节将涵盖si24r2h工作原理、理论说明、实际应用场景分析以及总结与展望。
1.3 目的本文旨在深入探究si24r2h无线传输模块的工作原理,并解释其背后的关键概念。
通过对硬件组成、信号传输过程和数据处理算法等方面的详细介绍和分析,读者可以更好地理解si24r2h模块在各个领域中应用的基础知识。
此外,还将通过实际应用场景分析来展示该模块在工业和家庭自动化等领域的应用示例。
最后,在结论与展望部分,将总结已有研究成果,并对未来si24r2h模块的发展提出展望和建议。
通过这篇长文的阐述,读者能够获得全面深入的si24r2h工作原理的理论指导,以便更好地应用于实际生活和工作中。
2. si24r2h工作原理:2.1 硬件组成:si24r2h是一个具有多个组件的系统,主要包括以下部分:- Si24r2h MCU:这是整个系统的核心处理单元,它可以执行各种任务,并进行数据处理和控制操作。
- 射频模块:该模块负责收集和发送无线信号。
它能够接收来自外部设备的信号,并将其转化为数字信号以供MCU进一步处理。
同时,它还可以将MCU生成的数字信号转化为无线信号并发送到外部设备。
- 传感器:si24r2h配备了多种传感器,用于收集环境信息、检测物体和监测其他相关参数。
这些传感器包括但不限于温度传感器、湿度传感器、气压传感器等。
传感器将采集到的信息传递给MCU进行处理和决策。
- 存储装置:为了存储临时数据或长期使用的数据,在si24r2h中配置了存储装置,一般以闪存或EEPROM形式存在。
XP243E_chinese_NEW

1.2 特 长
1.2.1 泛用性的扩大
1) 吸嘴收存数的扩大 为了对应丰富的异型元件,在吸嘴置放台上准备了可以增加到17个收存数 的类型。(选项) 因为收存数的增加,机械夹具或者特殊吸嘴也可以时常搭载。
9个吸嘴
17个吸嘴
2 )
対 象 部 品 の 拡 大
2) 对象元件的扩大 由于采用了高像素相机并研发了8mm料带宽的马达供料器,可以贴装0603的 极小的芯片元件。
-8-
CNT-XP243-03S
2.要 素
2.1 要 素
1500
2058 .5
1408 .5
2362
项目 电 源※1
气 源※2
机器尺寸 机器重量
要素
3相200V±10%(50/60Hz) 4kVA
0.5MPa
128L/min(A.N.R.) +170L/min(排出空料盘时:5sec) +55L/min(使用真空支撑销时) +2.8L/850ms(料带切刀时)
-2-
CNT-XP243-03S
1.概 要
1.2.2 本公司独特的“MSA”
贴装元件的识别全部由前光处理,使用本公司独特的“MSA”影像处理系 统。具有对应影像劣化和杂讯的能力。可以以高速进行识别处理。另外, 使用了对比度补正功能后,取入影像的对比度即使很小也可以稳定地进行 影像处理。更进一步,对于CSP等检查全部的bump。 MSA是被用称作为查找线的线所画的模板进行与元件的图形匹配。查找线是 在虚拟画面上以任意的位置、角度以及长度设定的线段并按其测定亮度。 对于对象物的轮廓垂直地画查找线后,可以求出轮廓线的位置。
2) 影像处理相机安装在滑轨一侧,贴装工作头从吸取元件到贴装点为止的移 动期间必须通过镜面上方,相机可以在一定的时间内得到静止影像。因此 贴装头可以用最短距离从吸取移动到实装位置,不会因贴装点的影像取入 的而发生移动损失。
Z23S2445M01中文资料(AEROVOX)中文数据手册「EasyDatasheet - 矽搜」
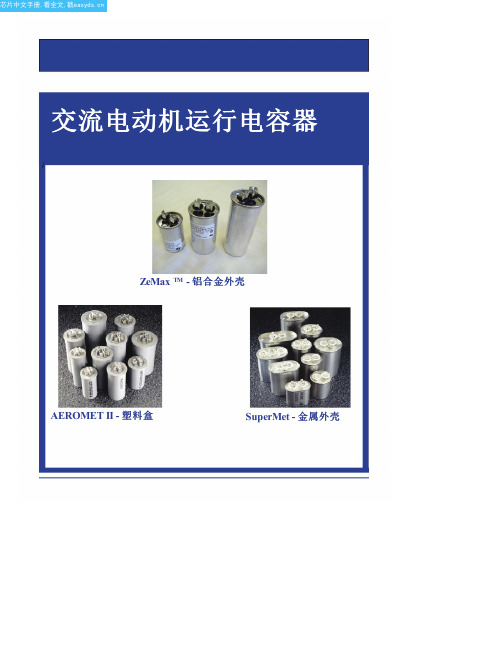
•单和双额定值 - 双额定值
在SuperMet仅
所有SuperMet和ZEMAX电容TM集成•
60000小时使用寿命.
UL认证压敏灭弧删除•
电容稳定性±整个人生3%
电容器从电路在生命尽头.
•自清除金属化聚丙烯薄膜.
• 专利压力灭弧符合UL810
每个电容器填充有环氧化Soybeanoil
要求.
电介液.大豆油已被证明可靠性
所有AEROMET II电容都可以用时间和成本节约
EIA RS-186-3E状态测试要求.
AeroMount系统.触点厂家触点厂家对于需要reycled了解详细信息.
认证证书
EIA RS-186-2E湿度测试要求(TropiCAL条件).
• UL文件号E51176
• CSA文件号058450
• VDE认证可用
电气特性
• 温度范围:-40〜+ 70℃.源自• 电容范围3至80μF.
• 电容公差±10%.
• 电压范围240至480 VAC,60赫兹.
• 损耗因数0.1%以下
@ 60赫兹和25℃.
• 绝缘电阻千M
●μF.
•耐电压.
• 期限至足月1.75×WVAC
• 期限到案2×WVAC + 1KVAC
应用
• 窗式空调 • 单元式空调 • 电动汽车 • 风扇与鼓风机 • Pumps • 洗衣房设备 • 除湿机
注入
P = Supernol(M系列) S = SuperSoy(Z系列)
电压编码 电压第一个两位数
24 = 240 V交流 33 = 330 V交流 37 = 370 V交流 44 = 440 V交流 48 = 480 V交流 60 = 600 Vac
Si24R1中文文档

Preliminary
Si24R1
描述 Auto Repeat-reQuest Auto ReTransmission Auto Retransmission Delay Bit Error Rate Chip Enable Cyclic Redundancy Check Chip Select Dynamic Payload Length Gaussian Frequency Shift Keying Interrupt Request Industrial-Scientific-Medical Least Significant Bit Megabit per second Micro Controller Unit Mega Hertz Master In Slave Out Master Out Slave In Most Significant Bit Power Amplifier Packet Identity Payload RX TX Power Down Power UP Radio Frequency Channel Received Signal Strength Indicator Receiver Receive Data Ready SPI Clock Serial Peripheral Interface Transmitter Transmit Data Sent Crystal
DI
芯片开启信号,激活 RX 或 TX 模式
DI
SPI 片选信号
DI
SPI 时钟信号
DI
SPI 输入信号
DO
SPI 输出信号
DO
可屏蔽中断信号,低电平有效
ZWS240PAF-24S中文资料(DENSEI-LAMBDA)中文数据手册「EasyDatasheet - 矽搜」

2 year warranty
型号名称
ZWS 100AF-5/
Series Name
Option
Output Power
Active Filter contained
Output Voltage
特征
marking (Low Voltage Directive) Active Filter contained, PFHC type Applicable to peakoutput wattage 120% (12V, 15V, 24V output) Low leakage current 0.5mA max Equipped with Remote ON/OFF control (with-cover type excluded) and output variable voltage 2 year warranty
产品阵容
Model name ZWS50AF ZWS75AF ZWS100AF ZWS150AF
ZWS50AF-5 ZWS50AF-12 ZWS50AF-15 ZWS50AF-24 ZWS75AF-5
ZWS75AF-12 ZWS75AF-15 ZWS75AF-24 ZWS100AF-5 ZWS100AF-12 ZWS100AF-15
芯片中文手册,看全文,戳
ZWS-AF -系列
单路输出50W〜150W
(Low Voltage Directive)
技术指标
1.输 入 电 压 范 围 2.功 率 因 数 3,输 出 电 压 范 围 4.冷 却 5.工 作 环 境
温度 (标准安装)
6.耐 压 7.安 全 标 准 8. CE标志 9. EMI 10.免 疫 11. PFHC 12.函 数
E34-2G4H20D 产品规格书说明书

E34-2G4H20D产品规格书nRF24L01+ 2.4GHz TTL 自动跳频无线模块目录第一章产品概述 (2)1.1产品简介 (2)1.2特点功能 (2)1.3应用场景 (2)第二章规格参数 (3)2.1极限参数 (3)2.2工作参数 (3)第三章尺寸与引脚定义 (4)第四章推荐连线图 (5)第五章功能详解 (5)5.1模块复位 (5)5.2AUX详解 (6)5.2.1 串口数据输出指示 (6)5.2.2 无线发射指示 (6)5.2.3 模块正在配置过程中 (7)5.2.4 AUX注意事项 (7)第六章工作模式 (7)6.1模式切换 (8)6.2半双工模式(模式0) (8)6.3全双工模式(模式1) (8)6.4预留模式(模式2) (9)6.5设置模式(模式3) (9)6.6快速通信测试 (9)第七章指令格式 (10)7.1出厂默认参数 (10)7.2工作参数读取 (10)7.3版本号读取 (10)7.4复位指令 (10)7.5参数设置指令 (11)第八章硬件设计 (12)第九章常见问题 (12)第十章焊接作业指导 (13)第十一章相关型号 (13)第十二章天线指南 (14)第十三章批量包装方式 (14)修订历史 (15)关于我们 (15)第一章产品概述1.1 产品简介E34-2G4H20D是一款基于nRF24l01+的无线数传模块,工作在2.4~2.518GHz 频段,发射功率100mW,半双工,TTL 电平输出,兼容3.3V 与5V 的IO 口电压,使用串口进行数据收发,降低了无线应用的门槛。
E34-2G4H20D具有自动跳频功能,抗干扰能力强,传输速率高,延迟小的特点;自动跳频技术是为了确保通信的秘密性和抗干扰性,与定频通信相比,跳频通信比较隐蔽也难以被截获。
跳频通信也具有良好的抗干扰能力,即使有部分频点被干扰,仍能在其他未被干扰的频点上进行正常的通信。
1.2 特点功能⚫支持自动跳频,大幅度提高通信抗干扰能力;⚫支持定频通信,速度快,延迟小;⚫支持丢包自动重发;⚫支持定点传输,易于组网通信;⚫支持全球免许可ISM 2.4GHz频段;⚫支持空中速率250k~2Mbps;⚫支持先进的GFSK调制方式;⚫最大发射功率100mW,通信距离可达2.5km;⚫支持2.3~5.5V供电,大于3.3V供电均可保证最佳性能;⚫工业级标准设计,支持-40~+85℃下长时间使用;⚫SMA-K接口,可方便连接同轴电缆或外置天线。
世图兹精密空调产品介绍
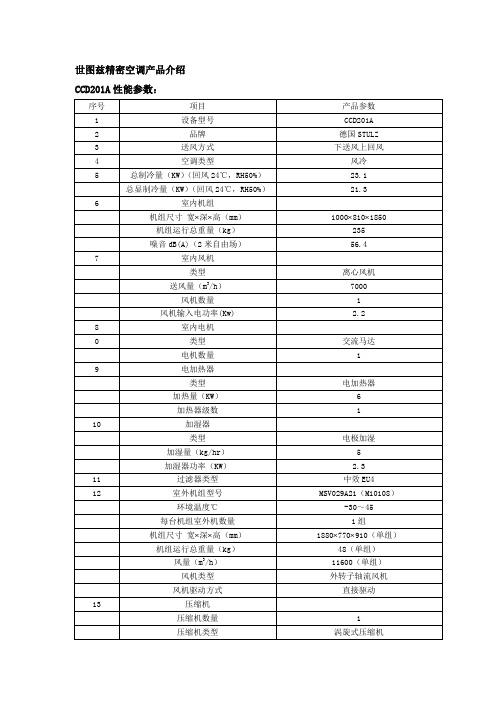
世图兹精密空调产品介绍CCD201A性能参数:德国世图兹Minispace系列机房专用空调介绍Minispace系列描述:高适应性:多项节能设计多种送风方式,满足不同气流组织需求多种冷却方式,包括风冷、水冷、冷冻水等,有利于适应现场的实际条件;监控管理方式多样,适合各种系统;占地面积小,制冷效果佳;采用符合EU4标准的高效空气过滤系统;风冷方式提供超远安装距离和超高落差的方案;前开门设计,便于安装和维护;Minispace机组特点:德国STULZ Minispace 产品,该产品系列在同行业产品中,技术成熟可靠,性价比高,产品系列晚辈,具有多种制冷方式机组,多种送风方式选择,具有高实用性、高稳定性的特点。
Minispace空调产品系列是在采用新的设计理念和创新技术而形成的经典一代高可靠性和高科技产品系列。
该系列产品具有独特的性能特点:节能、高可靠性、环保、低噪、风量大、方便。
1、STULZ Minispace系列空调具有高显热比特点:通讯机房内电子设备释放出大量的显热。
Minispace针对机房特点实现0.9以上的高显热比,在机房环境下使用,相对于普通舒适性空调节省20-30%的能耗,并因此避免过度除湿和送风带雾。
2、功能强大的新一代C5000微处理控制器控制器是空调系统的核心。
在以前C1002控制器的基础上性能有了进一步的提高,技术不断更新的STULZ新一代的控制器 C5000采用先进的“模糊”控制理论作为其控制的基础,可对机房环境-温度、湿度、洁净度进行连续的24小时精密控制,并具有自学习、分析、预测、自动控制功能,是一种新型智能控制器。
1)大屏幕汉语显示,方便用户使用;2)可显示24小时温、湿度曲线,简学、清晰、明显;3)可实现对空调机组的分散独立的智能化控制;4)记录各功能部件的运行时间,如制冷、加热、加湿、除湿等;5)80条报警记录,且有断电数据保护;6)在机组出现高压或者低压警告和停机,可实现自动重启功能,停电机组也具有来电自启动功能,避免不必要的到场工作,满足无人值守的要求;7)控制板可配置标准RS485通信接口,,与 BMS 连接时无需额外的硬件支出,可接打印机;8)机房参数的三级控制:参数新型的显示监控,报警参数的设置,系统基本功能的设置。
丹福斯温控器螺纹舵机型号数据手册说明书

Actuators for modulating control AME 55, AME 56Data sheetDescriptionOrdering ActuatorsType Power supplyCode No.AME 5524 Vac082H3022AME 56082H3025AccessoriesTypeCode No.Stem heater 24 Vac/dc; 40W (VF, VL valves DN 65-80)065Z0315Stem heater 24 Vac/dc; 20W (VF, VL valves DN 100 and VFS2 valves DN 15-50)065Z7020Stem heater 24 Vac/dc; 40W(VF valves DN 125, 150 and VFS DN 65-100)065Z7022Adapter (VF, VL valves DN 65-80)065Z0312AME 56 clutch (VFS 2 DN 15-50)065Z7551The actuators are used with valves:• VFM 2 (DN 65-150) only in combination with AME 55,• VFS 2 (DN 15-50) only in combination with AME 56. Clutch available on special request,• VFS 2 (DN 65-100),• VL 2/3 (DN 100),• VF 2/3 (DN 100-150),• VL 2/3 & VF 2/3 (DN 65, 80) only in combination with AME 56 and adapter 065Z0312,• AFQM (DN 65-125) and AFQM 6 (DN 40-50)Features:• “Self adjustment” function• Load related “Switch off“ function that prevents valve or actuator to be overloaded • Diagnostic LEDMain data:• Nominal voltage: 24 Vac, 50/60 Hz • Control input signal:0(4)-20 mA,0(2)-10 Vdc • F orce:2000 N (AME 55), 1500 N (AME 56)• Stroke: 40 mm • Speed:8 s/mm (AME 55), 4 s/mm (AME 56)• Max. medium temperature: 200 °C by insolated valve • Manual operationData sheetAME 55, AME 56Technical dataType AME 55AME 56Power supply Vac 24; ± 10 %Power consumption VA919.5Duty cycle S3 60% ED (IEC 60034)Frequency Hz 50/60Control input Y Vdc 0-10 (2-10) Ri = 24 kΩmA 0-20 (4-20) Ri = 500 ΩOutput signal X Vdc 0-10 (2-10)Closing force N 20001500Max. stroke mm 40Speeds/mm84Max. medium temperature °C 200 Ambient temperature0 ... 55Storage and transport temperature –40 (70)Ambient humidity 95 % r.h., non-condensingProtection class III Grade of enclosure IP 54Weightkg 3.8- marking in accordance with standards Low Voltage Directive (LVD) 2014/35/EU: EN 60730-1, EN 60730-2-14Electromagnetic Compatibility Directive (EMC) 2014/30/EU: EN 61000-6-2,EN 61000-6-3InstallationMechanicalThe actuator should be mounted with the valve stem (use a 4 mm Allen key - not supplied) in either horizontal position or pointing upwards. Use a M8/SW13 key (not supplied) to fit the actuator to the valve body. Allow for necessary clearance for maintenance purposes.Red rings position indication should be pushed together before commissioning. They indicate the position of valve opening degree after self-adjustment.Arrange proper valve insulation in order to avoid direct heat transfer toward actuator.Wiring lengthRecommended square of the wiring0-50 m 0.75 mm 2> 50 m1.5 mm 2ElectricalElectrical connections can be accessed by removing the cover.Two M16 × 1.5 cable entries are provided. Both entries are provided with a rubber grommet for use with flexible cable. Note that in order to maintain the enclosure IP rating, appropriate cable glands must be used.Data sheetAME 55, AME 56DisposalThe actuator must be dismantled and the elements sorted into various material groups before disposal.DIP switch settingThe actuator has a selection of DIP switches under the removable cover.The switch provides the following functions:DIP1: U/I - Input signal type selector:• If set to OFF position, input signal Y is set to voltage (Y).If set to ON position, input signal Y is set to be current (mA).DIP2: 0/2 - Input signal range selector:• If set to OFF position, the input signal is in the range from 2 V to 10 V (voltage input) or from 4 mA to 20 mA (current input). If set to ON position, the input signal is in the range from 0 V to 10 V (voltage input) or from 0 mA to 20 mA (current input).DIP3: D/I - Direct or inverse acting selector: • If set to OFF position, the actuator is direct acting (actuator’s stem extends by voltage increase). If actuator is set to ON position the actuator is inverse acting (actuator’s stem retracts by voltage increase).DIP4: —/Seq - Normal or sequential modeselector:• Two actuators can be set to work parallel with one control signal. If the SEQUENTIAL is set than an actuator responds to split control signal (see 0(2) V … 5(6 V) / 5(6) V … 10 V).NOTE: T his combination works in combination with DIP5: 0(2) V… 5(6 V) / 5(6) V … 10 VData sheet AME 55, AME 56DIP5: 0-5 V/5-10 V - Input signal range insequential mode:• This function is available ifDIP4: --- / Sequential is set to ON, otherwisethe actuator operates in full controll range(0(2)-10V or 0(4)-20mA).• When DIP5 is set to Off the actuator will match the range of the control signal:2 … 6 V (when DIP1 and DIP2 are set to Off)0 … 5 V (when DIP1 is set to Off and DIP2 is set to ON)4 … 12 mA (when DIP1 is set to ON and DIP2 is set to Off)ON)is set to Off)mode selector:Actuator can operate in modulating (DIP 6to OFF) or in “simple” 3-point mode, if the3-point function is selected (DIP 6 to ON).Modulating mode; DIP 6 set to OFF(factory setting)• After the actuator has been connected to power supply, the actuator will start theself-adjustment procedure. The indicator LED flashes until self-adjustment is finished.• Actuator’s stem will run to its totally extended or retracted position by bridging SN signalto terminals 1 or 3 and will remain in thispositron as long as potential is present.It is not allowed to bridge SP to terminal 1 or 3 when DIP 6 is set to OFF .3-point mode; DIP 6 set to OnLook carefully wiring diagrams as wiring is different for controllers with triacs output (ECL) in comparison to controllers withrelay output.• Connect SN (Neutral) and power supply (24Vac) via controller to terminals 1 or 3.• Return signal X (depends on DIP 2, 3, 4 & 5) is possible if connected power supply to SP and SN.DIP7: L OG/LIN - Equal percentage or linear flow through valve selector1:• Characteristic of valve is unchanged by factory setting (DIP 7 OFF).Danfoss valves as VF, VFS and VFM thatare suitable to operate with actuatorhave logarithmic (equal percentage) flowcharacteristic. By setting switch to LIN flowthe characteristic of motorized valve willbe affected. Combination of actuator andvalve will work together as valve with LINEAR characteristic.DIP8: 100 % KVS/Reduced KVS- Flow reduction through valve selector 1):• If set to OFF position, the flow through valve is not reduced. If set to ON position, the he flow through valve reduced by half of incrementstandard KVSvalues (example: valve with KVS16 and DIP8 set to ON – maximum flowthrough the valve is KVS13 (middle betweenstandard KVS16 and KVS10).1)NOTE:T o be used only in combination with valves with equalpercentage characteristicDIP9: Reset:• Changing this switch position will cause the actuator to go through a self-adjustmentprocedure.DIP switch setting (continuous)Data sheetAME 55, AME 56WiringAutomatic self-adjustment procedure The actuator will automatically adjust to the stroke of the valve, when power supply is first time connected to the actuator or when the actuator is reset.The LED indicator flashes until self-adjustment is finished. The duration depends on the spindle travel and will normally last a few minutes.To restart self-adjustment, change the position of RESET switch (DIP9).If the supply voltage is switched off or falls below 80% in more than 0.1s, the current valve position will be stored in the memory also after a power supply cut-out.Signal on terminals 1 or 3 have priority toward Y input signal.Diagnostic LEDThe red diagnostic LED is located on the pcb under the cover. It provides indication of following operational states:Constant light - normal operation No light- no operation or no power supply Intermittent light (1 Hz)- self-adjusting-mode Intermittent light (3 Hz):- power supply too low- insufficient valve stroke (<20 s)- end-position cannot be reached.Data sheetAME 55, AME 56Complete the mechanical and electricalinstallation and perform the necessary checks and tests:• Isolate control medium. (e.g. self-adjustment in a steam application without suitable mechanical isolation could cause a hazard).• Apply the power. Note that the actuator will now perform the self-adjustment procedure.• Apply the appropriate control signal and check the valve stem direction is correct for the application.• Ensure that the actuator drives the valve over its full stroke, by applying the appropriate control signal. This action will set the valve stroke length.The unit is now fully commissioned.CommissioningCommissioning / testing featureThe actuator can be driven to the fully open or closed positions (depending on valve type) by connecting SN to terminals 1 or 3.Manual overrideThe manual override is applied by rotating the 4 mm Allen key (not supplied) to the required position. Observe the direction of the rotation symbol.• Disconnect power supply• Adjust valve position using an Allen key • Set valve to closed position •Restore power supplyIf manual override has been used then X and Y signal are not correct until the actuator reaches its end position. If this is not accepted reset the actuator, or apply accessory active return signal kit.Usage of electrical drill machine is not allowed.Data sheetAME 55, AME 56Actuator - valve combinationsDimensionsData sheet AME 55, AME 56。
费斯托纤维光纤单元SOE4产品目录说明书

Fibre-optic units SOE4Fibre-optic units SOE4Characteristics and product range overview• High precision fibre-optic units• Switching frequencies of up to 8000 Hz• Working ranges of up to 2000 mm• Variants with LED display, switching and analogue outputs• Setting via teach-in• Comprehensive range of light guidesSOE4-FO-L-... with LED SOE4-FO-D-... with LED displayProduct combination SOE4, SVE4, SDE32d Internet: /catalogue/...Subject to change – 2022/07Fibre-optic units SOE4 Peripherals overview3 2022/07 – Subject to change d Internet: /catalogue/...Fibre-optic units SOE4Type codes4d Internet: /catalogue/...Subject to change – 2022/07Fibre-optic units SOE4 Data sheet5 2022/07 – Subject to change d Internet: /catalogue/...Fibre-optic units SOE4Data sheet1)For information about the area of use, see the EC declaration of conformity at: /sp d Certificates.If the devices are subject to usage restrictions in residential, commercial or light-industrial environments, further measures for the reduction of the emitted interference may be necessary.2)Corrosion resistance class CRC 4 to Festo standard FN 940070Particularly high corrosion stress. Outdoor exposure under extreme corrosive conditions. Parts exposed to aggressive media, e.g. in the chemical or food industries. Such applications may need to be safeguarded by special tests(dalso FN 940082), using appropriate media.6d Internet: /catalogue/...Subject to change – 2022/07Fibre-optic units SOE4 Accessories – Ordering data1) With SOE4-FO-L and SOE4-FO-D in standard modeAn attempt was made to obtain a signal at 10% of the working range using a copper wire. The smallest wire diameter that was still detected corresponds to the diameter of the smallest detectable object.2)1) With SOE4-FO-L and SOE4-FO-D in standard mode2) An attempt was made to obtain a signal at 10% of the working range using a copper wire. The smallest wire diameter that was still detected corresponds to the diameter of the smallest detectable object.1) An adapter SASA is included in the scope of delivery for light guides with a light guide diameter of < 2.2 mm7 2022/07 – Subject to change d Internet: /catalogue/...Fibre-optic units SOE4Accessories – Ordering data1) With SOE4-FO-L and SOE4-FO-D in standard modeAn attempt was made to obtain a signal at 10% of the working range using a copper wire. The smallest wire diameter that was still detected corresponds to the diameter of the smallest detectable object.2)1) With SOE4-FO-L and SOE4-FO-D in standard mode2) An attempt was made to obtain a signal at 10% of the working range using a copper wire. The smallest wire diameter that was still detected corresponds to the diameter of the smallest detectable object.1) An adapter SASA is included in the scope of delivery for light guides with a light guide diameter of < 2.2 mm8d Internet: /catalogue/...Subject to change – 2022/07Fibre-optic units SOE4 Accessories – Ordering data1) Dependent on the light guide2)Light spot diameter 0.7 mm at a distance of 10 mm, dependent on the light guideH-Any light guide not listed here is not suitable for combining with an adapterlens.1) Bending tool for light guide sleeves9 2022/07 – Subject to change d Internet: /catalogue/...Fibre-optic units SOE4Accessories – Ordering data10d Internet: /catalogue/...Subject to change – 2022/07Festo - Your Partner in AutomationConnect with us/socialmedia 1Festo Inc.2Festo Pneumatic 3Festo Corporation 4Regional Service Center 5300 Explorer DriveMississauga, ON L4W 5G4CanadaAv. Ceylán 3,Col. Tequesquináhuac 54020 Tlalnepantla, Estado de México1377 Motor Parkway Suite 310Islandia, NY 117497777 Columbia Road Mason, OH 45040Festo Customer Interaction CenterTel:187****3786Fax:187****3786Email:*****************************Multinational Contact Center 01 800 337 8669***********************Festo Customer Interaction Center180****3786180****3786*****************************S u b j e c t t o c h a n g e。
24C04中文资料

24C02串行E2PROM的读写I2C总线是一种用于IC器件之间连接的二线制总线。
它通过SDA(串行数据线)及SCL(串行时钟线)两根线在连到总线上的器件之间传送信息,并根据地址识别每个器件:不管是单片机、存储器、LCD驱动器还是键盘接口。
1.I2C总线的基本结构采用I2C总线标准的单片机或IC器件,其内部不仅有I2C接口电路,而且将内部各单元电路按功能划分为若干相对独立的模块,通过软件寻址实现片选,减少了器件片选线的连接。
CPU不仅能通过指令将某个功能单元电路挂靠或摘离总线,还可对该单元的工作状况进行检测,从而实现对硬件系统的既简单又灵活的扩展与控制。
I2C总线接口电路结构如图1所示。
2.双向传输的接口特性传统的单片机串行接口的发送和接收一般都各用一条线,如MCS51系列的TXD和RXD,而I2C 总线则根据器件的功能通过软件程序使其可工作于发送或接收方式。
当某个器件向总线上发送信息时,它就是发送器(也叫主器件),而当其从总线上接收信息时,又成为接收器(也叫从器件)。
主器件用于启动总线上传送数据并产生时钟以开放传送的器件,此时任何被寻址的器件均被认为是从器件。
I2C总线的控制完全由挂接在总线上的主器件送出的地址和数据决定。
在总线上,既没有中心机,也没有优先机。
总线上主和从(即发送和接收)的关系不是一成不变的,而是取决于此时数据传送的方向。
SDA和SCL均为双向I/O线,通过上拉电阻接正电源。
当总线空闲时,两根线都是高电平。
连接总线的器件的输出级必须是集电极或漏极开路,以具有线“与”功能。
I2C总线的数据传送速率在标准工作方式下为100kbit/s,在快速方式下,最高传送速率可达400kbit/s。
3.I2C总线上的时钟信号在I2C总线上传送信息时的时钟同步信号是由挂接在SCL时钟线上的所有器件的逻辑“与”完成的。
SCL线上由高电平到低电平的跳变将影响到这些器件,一旦某个器件的时钟信号下跳为低电平,将使SCL线一直保持低电平,使SCL线上的所有器件开始低电平期。
VVZ24资料

I dAVM =27 AV RRM =1200-1600 VV RSM V RRM TypeV DSMV DRM V V 13001200VVZ 24-12io1 15001400VVZ 24-14io1 17001600VVZ 24-16io1Symbol Test Conditions Maximum RatingsI dAV T K = 100°C; module 21A I dAVMmodule 27A I FRMS , I TRMS per leg 16A IFSM , I TSMT VJ = 45°C;t = 10 ms (50 Hz), sine 300A V R = 0t = 8.3 ms (60 Hz), sine 320A T VJ = T VJM t = 10 ms (50 Hz), sine 270A V R = 0t = 8.3 ms (60 Hz), sine 290A I 2tT VJ = 45°C t = 10 ms (50 Hz), sine 450A 2s V R = 0t = 8.3 ms (60 Hz), sine 430A 2s T VJ = T VJM t = 10 ms (50 Hz), sine 365A 2s V R = 0t = 8.3 ms (60 Hz), sine350A 2s (di/dt)crT VJ = T VJM repetitive, I T = 50 A 150A/m sf =400 Hz, t P =200 m s V D = 2/3 V DRM I G = 0.3 A,non repetitive, I T = 1/3 • I dAV 500A/ms di G /dt = 0.3 A/m s(dv/dt)cr T VJ = T VJM ; V DR = 2/3 V DRM1000V/m s R GK= ¥; method 1 (linear voltage rise)V RGM 10V P GM T VJ = T VJM t p=30m s £10W I T = I TAVMt p =500m s £5W t p =10ms£1W P GAVM 0.5W T VJ -40...+125°C T VJM 125°C T stg -40...+125°C V ISOL 50/60 Hz, RMS t = 1 min 3000V~I ISOL £ 1 mA t = 1 s 3600V~M d Mounting torque (M5)2-2.5Nm (10-32 UNF)18-22lb.in.Weighttyp.28gFeaturesq Package with DCB ceramic base plate q Isolation voltage 3600 V~q Planar passivated chips q Soldering terminals qUL registered E 72873ApplicationsqInput rectifier for switch mode power supplies (SMPS)q Softstart capacitor charging qElectric drives and auxiliariesAdvantagesq Easy to mount with two screws q Space and weight savingsqImproved temperature and power cyclingData according to IEC 60747 and refer to a single thyristor/diode unless otherwise stated.IXYS reserves the right to change limits, test conditions and dimensions.Dimensions in mm (1 mm = 0.0394")303Three Phase Half Controlled Rectifier Bridge28574Symbol Test Conditions Characteristic ValuesI R , I D V R = V RRM ; V D = V DRM T VJ = T VJM £5mA T VJ = 25°C£0.3mA V F , V T I F , I T = 30 A, T VJ = 25°C £1.45VV T0For power-loss calculations only 1V r T (T VJ = 125°C)16m W V GT V D = 6 V;T VJ = 25°C £ 1.0V T VJ = -40°C £ 1.2V I GTV D = 6 V;T VJ = 25°C £65mA T VJ = -40°C £80mA T VJ = 125°C £50mA V GD T VJ = T VJM ;V D = 2/3 V DRM £0.2V I GD T VJ = T VJM ;V D = 2/3 V DRM £5mA I LI G = 0.3 A; t G = 30 m s T VJ = 25°C £150mA di G /dt = 0.3 A/m sT VJ = -40°C £200mA T VJ = 125°C£100mA I H T VJ = 25°C; V D = 6 V; R GK = ¥£100mA t gd T VJ = 25°C; V D = 1/2 V DRM £2m s I G = 0.3 A; di G /dt = 0.3 A/m st q T VJ = 125°C; I T = 15 A, t p = 300 m s, -di/dt = 10 A/m s typ.150m s Q r V R = 100 V, dv/dt = 20 V/m s, V D = 2/3 V DRM 75m C R thJC per thyristor (diode); DC current 2.1K/W per module0.35K/W R thJH per thyristor (diode); DC current 2.7K/W per module0.45K/Wd S Creeping distance on surface 7mm d A Creepage distance in air 7mm aMax. allowable acceleration50m/s 2Fig. 1Surge overload current per chipIFSM: Crest value, t: durationFig. 3Gate trigger characteristicsTriggering:Fig. 2I2t versus time (1-10 ms)per chip11010010000.1110IGVGmAV。
SIHLZ44-E3中文资料

Power MOSFETIRLZ44, SiHLZ44Vishay SiliconixFEATURES•Dynamic dV/dt Rating •Logic-Level Gate Drive•R DS(on) Specified at V GS = 4 V and 5 V •175 °C Operating Temperature •Fast Switching •Ease of Paralleling •Simple Drive Requirements •Lead (Pb)-free AvailableDESCRIPTIONThird generation Power MOSFETs from Vishay provide the designer with the best combination of fast switching,ruggedized device design, low on-resistance and cost-effectiveness.The TO-220 package is universally preferred for all commercial-industrial applications at power dissipation levels to approximately 50 W. The low thermal resistance and low package cost of the TO-220 contribute to its wide acceptance throughout the industry.Notesa.Repetitive rating; pulse width limited by maximum junction temperature (see fig. 11).b.V DD = 25 V, starting T J = 25 °C, L = 179 µH, R G = 25 Ω I AS = 51 A (see fig. 12).c.I SD ≤ 51 A, dV/dt ≤ 250 A/s, V DD ≤ V DS , T J ≤ 175 °C.d. 1.6 mm from case.e.Current limited by the package, (die current = 51 A).PRODUCT SUMMARYV DS (V)60 VR DS(on) (Ω)V GS = 5.0 V0.028Q g (Max.) (nC)66Q gs (nC)12Q gd (nC)43ConfigurationSingleTO-220GDSORDERING INFORMATIONPackage TO-220Lead (Pb)-free IRLZ44PbF SiHLZ44-E3SnPbIRLZ44SiHLZ44ABSOLUTE MAXIMUM RATINGS T C = 25 °C, unless otherwise notedARAMETER SYMBOL LIMIT UNITGate-Source Voltage V GS ± 10VContinuous Drain Current e V GS at 5.0 VT C = 25 °C I D50A Continuous Drain Current T C = 100 °C36Pulsed Drain Current a I DM 200Linear Derating Factor1.0W/°C Single Pulse Avalanche Energy b E AS 400mJ Maximum Power Dissipation T C = 25 °CP D 150WPeak Diode Recovery dV/dt cdV/dt 4.5V/ns Operating Junction and Storage Temperature Range T J , T stg- 55 to + 175°C Soldering Recommendations (Peak Temperature)d for 10 s 300Mounting Torque6-32 or M3 screw10 lbf · in 1.1N · m * Pb containing terminations are not RoHS compliant, exemptions may applyIRLZ44, SiHLZ44Vishay SiliconixNotesa.Repetitive rating; pulse width limited by maximum junction temperature (see fig. 11).b.Pulse width ≤ 300 µs; duty cycle ≤ 2 %.c.Current limited by the package, (die current = 51 A).THERMAL RESISTANCE RATINGSARAMETER SYMBOL TY.MAX.UNITMaximum Junction-to-Ambient R thJA -62°C/W Case-to-Sink, Flat, Greased Surface R thCS 0.50-Maximum Junction-to-Case (Drain)R thJC- 1.0IRLZ44, SiHLZ44Vishay Siliconix TYPICAL CHARACTERISTICS 25 °C, unless otherwise notedFig. 1 - Typical Output Characteristics, T C = 25 °C Fig. 2 - Typical Output Characteristics, T C = 175 °C Fig. 3 - Typical Transfer CharacteristicsFig. 4 - Normalized On-Resistance vs. TemperatureIRLZ44, SiHLZ44 Vishay SiliconixFig. 5 - Typical Capacitance vs. Drain-to-Source Voltage Fig. 6 - Typical Gate Charge vs. Gate-to-Source Voltage Fig. 7 - Typical Source-Drain Diode Forward VoltageFig. 8 - Maximum Safe Operating AreaIRLZ44, SiHLZ44Vishay SiliconixFig. 9 - Maximum Drain Current vs. Case Temperature Fig. 10a - Switching Time Test CircuitFig. 10b - Switching Time WaveformsFig. 11 - Maximum Effective Transient Thermal Impedance, Junction-to-CaseFig. 12a - Unclamped Inductive Test CircuitFig. 12b - Unclamped Inductive WaveformsIRLZ44, SiHLZ44Vishay SiliconixFig. 12c - Maximum Avalanche Energy vs. Drain CurrentFig. 13a - Basic Gate Charge WaveformFig. 13b - Gate Charge Test CircuitIRLZ44, SiHLZ44Vishay Siliconix Array Fig. 14 - For N-ChannelVishay Siliconix maintains worldwide manufacturing capability. Products may be manufactured at one of several qualified locations. Reliability data for Silicon Technology and Package Reliability represent a composite of all qualified locations. For related documents such as package/tape drawings, part marking, andreliability data, see /ppg?91328.Disclaimer Legal Disclaimer NoticeVishayAll product specifications and data are subject to change without notice.Vishay Intertechnology, Inc., its affiliates, agents, and employees, and all persons acting on its or their behalf (collectively, “Vishay”), disclaim any and all liability for any errors, inaccuracies or incompleteness contained herein or in any other disclosure relating to any product.Vishay disclaims any and all liability arising out of the use or application of any product described herein or of any information provided herein to the maximum extent permitted by law. The product specifications do not expand or otherwise modify Vishay’s terms and conditions of purchase, including but not limited to the warranty expressed therein, which apply to these products.No license, express or implied, by estoppel or otherwise, to any intellectual property rights is granted by this document or by any conduct of Vishay.The products shown herein are not designed for use in medical, life-saving, or life-sustaining applications unless otherwise expressly indicated. Customers using or selling Vishay products not expressly indicated for use in such applications do so entirely at their own risk and agree to fully indemnify Vishay for any damages arising or resulting from such use or sale. Please contact authorized Vishay personnel to obtain written terms and conditions regarding products designed for such applications.Product names and markings noted herein may be trademarks of their respective owners.元器件交易网。
IS42S32200E-6TL;IS42S32200E-7TLI;IS42S32200E-7BLI;IS42S32200E-7TL-TR;中文规格书,Datasheet资料

Integrated Silicon Solution, Inc. — — 1-800-379-47741Rev.00D 06/02/08IS42S32200ECopyright © 2006 Integrated Silicon Solution, Inc. All rights reserved. ISSI reserves the right to make changes to this specification and its products at any time without notice. ISSI assumes no liability arising out of the application or use of any information, products or services described herein. Customers are advised toobtain the latest version of this device specification before relying on any published information and before placing orders for products.FEATURES•Clock frequency: 200, 166, 143 MHz •Fully synchronous; all signals referenced to a positive clock edge •Internal bank for hiding row access/precharge •Single 3.3V power supply •LVTTL interface•Programmable burst length:(1, 2, 4, 8, full page)•Programmable burst sequence:Sequential/Interleave •Self refresh modes•4096 refresh cycles every 64 ms•Random column address every clock cycle •Programmable CAS latency (2, 3 clocks)•Burst read/write and burst read/single write operations capability •Burst termination by burst stop and precharge command •Available in Industrial temperature grade •Available in 400-mil 86-pin TSOP II and 90-ball BGA •Available in Lead free•Power Down and Deep Power Down Mode •Partial Array Self Refresh•Temperature Compensated Self Refresh •Output Driver Strength SelectionPlease contact Production Manager for Mobile function detail.OVERVIEWISSI 's 64Mb Synchronous DRAM IS42S32200E is organizedas 524,288 bits x 32-bit x 4-bank for improved performance.The synchronous DRAMs achieve high-speed data transfer using pipeline architecture. All inputs and outputs signals refer to the rising edge of the clock input.512K Bits x 32 Bits x 4 Banks (64-MBIT)SYNCHRONOUS DYNAMIC RAMADVANCED INFORMATIONJUNE 2008KEY TIMING PARAMETERSParameter -5-6-7Unit Clk Cycle Time CAS Latency = 3567ns CAS Latency = 2101010ns Clk Frequency CAS Latency = 3200166143Mhz CAS Latency = 2100100100Mhz Access Time from Clock CAS Latency = 3 4.5 5.5 5.5ns CAS Latency = 27.57.58nsIS42S32200E GENERAL DESCRIPTIONThe 64Mb SDRAM is a high speed CMOS, dynamic random-access memory designed to operate in 3.3V memory systems containing 67,108,864 bits. Internally configured as a quad-bank DRAM with a synchronous interface. Each 16,777,216-bit bank is organized as 2,048 rows by 256 columns by 32 bits.The 64Mb SDRAM includes an AUTO REFRESH MODE, and a power-saving, power-down mode. All signals are registered on the positive edge of the clock signal, CLK. All inputs and outputs are LVTTL compatible.The 64Mb SDRAM has the ability to synchronously burst data at a high data rate with automatic column-address generation, the ability to interleave between internal banks to hide precharge time and the capability to randomly change column addresses on each clock cycle during burst access.A self-timed row precharge initiated at the end of the burst sequence is available with the AUTO PRECH ARGE function enabled.Precharge one bank while accessing one of the other three banks will hide the precharge cycles and provide seamless, high-speed, random-access operation. SDRAM read and write accesses are burst oriented starting at a selected location and continuing for a programmed number of locations in a programmed sequence. The registration of an ACTIVE command begins accesses, followed by a READ or WRITE command. The ACTIVE command in conjunction with address bits registered are used to select the bank and row to be accessed (BA0, BA1 select the bank; A0-A10 select the row). The READ or WRITE commands in conjunction with address bits reg-istered are used to select the starting column location for the burst access.Programmable READ or WRITE burst lengths consist of 1, 2, 4 and 8 locations or full page, with a burst terminate option.FUNCTIONAL BLOCK DIAGRAM2Integrated Silicon Solution, Inc. — — 1-800-379-4774Rev.00DIntegrated Silicon Solution, Inc. — — 1-800-379-47743Rev.00D 06/02/08IS42S32200EPIN CONFIGURATIONS86 pin TSOP - Type II for x32PIN DESCRIPTIONSA0-A10Row Address Input A0-A7Column Address Input BA0, BA1Bank Select Address DQ0 to DQ31Data I/OCLK System Clock Input CKE Clock Enable CS Chip SelectRAS Row Address Strobe Command CASColumn Address Strobe CommandWEWrite EnableDQM0-DQM3x32 Input/Output Mask V DD Power Vss GroundV DDQ Power Supply for I/O Pin Vss Q Ground for I/O Pin NCNo ConnectionIS42S32200EPIN CONFIGURATIONPACKAGE CODE: B 90 BALL FBGA (Top View) (8.00 mm x 13.00 mm Body, 0.8 mm Ball Pitch)PIN DESCRIPTIONSA0-A10Row Address InputA0-A7Column Address InputBA0, BA1Bank Select AddressDQ0 to DQ31Data I/OCLK System Clock InputCKE Clock EnableCS Chip SelectRAS Row Address Strobe Command CAS Column Address Strobe Command WE Write EnableDQM0-DQM3x32 Input/Output Mask V DD PowerVss GroundV DDQ Power Supply for I/O Pin Vss Q Ground for I/O PinNC No Connection4Integrated Silicon Solution, Inc. — — 1-800-379-4774Rev.00DIntegrated Silicon Solution, Inc. — — 1-800-379-47745Rev.00D 06/02/08IS42S32200EPIN FUNCTIONSSymbol Pin No. (TSOP)Type Function (In Detail)A0-A1025 to 27Input PinAddress Inputs: A0-A10 are sampled during the ACTIVE60 to 66command (row-address A0-A10) and READ/WRITE command (A0-A724with A10 defining auto precharge) to select one location out of the memory array in the respective bank. A10 is sampled during a PRECHARGE command to determine if all banks are to be precharged (A10 HIGH) or bank selected by BA0, BA1 (LOW). The address inputs also provide the op-code during a LOAD MODE REGISTER command.BA0, BA122,23Input Pin Bank Select Address: BA0 and BA1 defines which bank the ACTIVE, READ,WRITE or PRECHARGE command is being applied.CAS 18Input Pin CAS , in conjunction with the RAS and WE , forms the device command. See the "Command Truth Table" for details on device commands.CKE67Input PinThe CKE input determines whether the CLK input is enabled. The next rising edge of the CLK signal will be valid when is CKE HIGH and invalid when LOW. When CKE is LOW, the device will be in either power-down mode, clock suspend mode,or self refresh mode. CKE is an asynchronous i nput.CLK 68Input Pin CLK is the master clock input for this device. Except for CKE, all inputs to this device are acquired in synchronization with the rising edge of this pin.CS20Input PinThe CS input determines whether command input is enabled within the mand input is enabled when CS is LOW, and disabled with CS is HIGH. The device remains in the previous state when CS is HIGH.DQ0 to 2, 4, 5, 7, 8, 10,11,13DQ PinDQ0 to DQ15 are DQ pins. DQ through these pins can be controlled in byte units DQ3174,76,77,79,80,82,83,85using the DQM0-DQM3 pins45,47,48,50,51,53,54,5631,33,34,36,37,39,40,42 DQM016,28,59,71Input PinDQMx control thel ower and upper bytes of the DQ buffers. In read mode,DQM3the output buffers are place in a High-Z state. During a WRITE cycle the input data is masked. When DQMx is sampled HIGH and is an input mask signal for write accesses and an output enable signal for read accesses. DQ0 through DQ7 are controlled by DQM0. DQ8 throughDQ15 are controlled by DQM1. DQ16 through DQ23 are controlled by DQM2. DQ24 through DQ31 are controlled by DQM3.RAS 19Input Pin RAS , in conjunction with CAS and WE , forms the device command. See the "Command Truth Table" item for details on device commands.WE 17Input Pin WE , in conjunction with RAS and CAS , forms the device command. See the "Command Truth Table" item for details on device commands.V DDQ 3,9,35,41,49,55,75,81Supply Pin V DDQ is the output buffer power supply.V DD 1,15,29,43Supply Pin V DD is the device internal power supply.GND Q 6,12,32,38,46,52,78,84Supply Pin GND Q is the output buffer ground.GND44,58,72,86Supply PinGND is the device internal ground.IS42S32200EFUNCTION (In Detail)A0-A10 are address inputs sampled during the ACTIVE (row-address A0-A10) and READ/WRITE command (A0-A7 with A10 defining auto PRECHARGE). A10 is sampled during a PRECHARGE command to determine if all banks are to be PRECHARGED (A10 HIGH) or bank selected by BA0, BA1 (LOW). The address inputs also provide the op-code during a LOAD MODE REGISTER command.Bank Select Address (BA0 and BA1) defines which bank the ACTIVE, READ, WRITE or PRECH ARGE command is being applied.CAS, in conjunction with the RAS and WE, forms the device command. See the “Command Truth Table” for details on device commands.The CKE input determines whether the CLK input is enabled. The next rising edge of the CLK signal will be valid when is CKE HIGH and invalid when LOW. When CKE is LOW, the device will be in either power-down mode, CLOCK SUSPEND mode, or SELF-REFRESH mode. CKE is an asynchronous input.CLK is the master clock input for this device. Except for CKE, all inputs to this device are acquired in synchroni-zation with the rising edge of this pin.The CS input determines whether command input is enabled within the device. Command input is enabled when CS is LOW, and disabled with CS is H IGH. The device remains in the previous state when CS is H IGH. DQ0 through DQ7 are controlled by DQM0. DQ8 through DQ15 are controlled by DQM1. DQ16 through DQ23 are controlled by DQM2. DQ24 through DQ31 are controlled by DQM3. In read mode, DQMx control the output buffer. When DQMx is LOW, the corresponding buffer byte is enabled, and when HIGH, disabled. The outputs go to the HIGH Impedance State when DQMx is HIGH. This function corresponds to OE in conventional DRAMs. In write mode, DQMx control the input buffer. When DQMx is LOW, the corresponding buffer byte is enabled, and data can be written to the device. When DQMx is HIGH, input data is masked and cannot be written to the device.RAS, in conjunction with CAS and WE , forms the device command. See the “Command Truth Table” item for details on device commands.WE , in conjunction with RAS and CAS , forms the device command. See the “Command Truth Table” item for details on device commands.V DDQ is the output buffer power supply.V DD is the device internal power supply.GND Q is the output buffer ground.GND is the device internal ground.READThe READ command selects the bank from BA0, BA1 inputs and starts a burst read access to an active row. Inputs A0-A7 provides the starting column location. When A10 is H IGH, this command functions as an AUTO PRECHARGE command. When the auto precharge is selected, the row being accessed will be precharged at the end of the READ burst. The row will remain open for subsequent accesses when AUTO PRECHARGE is not selected. DQ’s read data is subject to the logic level on the DQM inputs two clocks earlier. When a given DQM signal was registered HIGH, the corresponding DQ’s will be High-Z two clocks later. DQ’s will provide valid data when the DQM signal was registered LOW.WRITEA burst write access to an active row is initiated with the WRITE command. BA0, BA1 inputs selects the bank, and the starting column location is provided by inputs A0-A7. Whether or not AUTO-PRECH ARGE is used is deter-mined by A10.The row being accessed will be precharged at the end of the WRITE burst, if AUTO PRECHARGE is selected. If AUTO PRECHARGE is not selected, the row will remain open for subsequent accesses.A memory array is written with corresponding input data on DQ’s and DQM input logic level appearing at the same time. Data will be written to memory when DQM signal is LOW. When DQM is HIGH, the corresponding data inputs will be ignored, and a WRITE will not be executed to that byte/column location.PRECHARGEThe PRECH ARGE command is used to deactivate the open row in a particular bank or the open row in all banks. BA0, BA1 can be used to select which bank is precharged or they are treated as “Don’t Care”. A10 determined whether one or all banks are precharged. After executing this command, the next command for the selected banks(s) is executed after passage of the period tRP, which is the period required for bank precharging. Once a bank has been precharged, it is in the idle state and must be activated prior to any READ or WRITE commands being issued to that bank.AUTO PRECHARGEThe AUTO PRECH ARGE function ensures that the precharge is initiated at the earliest valid stage within a burst. This function allows for individual-bank precharge without requiring an explicit command. A10 to enables the AUTO PRECHARGE function in conjunction with a spe-cific READ or WRITE command. For each individual READ or WRITE command, auto precharge is either6Integrated Silicon Solution, Inc. — — 1-800-379-4774Rev.00DIntegrated Silicon Solution, Inc. — — 1-800-379-47747Rev.00D 06/02/08IS42S32200Eenabled or disabled. AUTO PRECHARGE does not apply except in full-page burst mode. Upon completion of the READ or WRITE burst, a precharge of the bank/row that is addressed is automatically performed.AUTO REFRESH COMMANDThis command executes the AUTO REFRESH operation.The row address and bank to be refreshed are automatically generated during this operation.The stipulated period (t RC )is required for a single refresh operation, and no other commands can be executed during this period.This com-mand is executed at least 4096 times every 64ms. During an AUTO REFRESH command, address bits are “Don’t Care”. This command corresponds to CBR Auto-refresh.SEL F REFRESHDuring the SELF REFRESH operation, the row address to be refreshed, the bank, and the refresh interval are generated automatically internally. SELF REFRESH can be used to retain data in the SDRAM without external clocking, even if the rest of the system is powered down.The SELF REFRESH operation is started by dropping the CKE pin from HIGH to LOW. During the SELF REFRESH operation all other inputs to the SDRAM become “Don’t Care”.The device must remain in self refresh mode for a minimum period equal to t RAS or may remain in self refresh mode for an indefinite period beyond that.The SELF-REFRESH operation continues as long as the CKE pin remains LOW and there is no need for external control of any other pins.The next command cannot be executed until the device internal recovery period (t RC ) has elapsed.Once CKE goes H IGH , the NOP command must be issued (minimum of two clocks) to provide time for the completion of any internal refresh in progress. After the self-refresh, since it is impossible to determine the ad-dress of the last row to be refreshed, an AUTO-REFRESH should immediately be performed for all addresses.BURST TERMINATEThe BURST TERMINATE command forcibly terminates the burst read and write operations by truncating either fixed-length or full-page bursts and the most recently registered READ or WRITE command prior to the BURST TERMINATE.COMMAND INHIBITCOMMAND INHIBIT prevents new commands from being executed. Operations in progress are not affected, apart from whether the CLK signal is enabledNO OPERATIONWhen CS is low, the NOP command prevents unwanted commands from being registered during idle or wait states.LOAD MODE REGISTERDuring the LOAD MODE REGSITER command the mode register is loaded from A0-A10. This command can only be issued when all banks are idle.ACTIVE COMMANDWhen the ACTIVE COMMAND is activated, BA0, BA1inputs selects a bank to be accessed, and the address inputs on A0-A10 selects the row. Until a PRECHARGE command is issued to the bank, the row remains open for accesses.IS42S32200ETRUTH TABLE – COMMANDS AND DQM OPERATION(1)FUNCTION CS RAS CAS WE DQM ADDR DQs COMMAND INH IBIT (NOP)H X X X X X X NO OPERATION (NOP)L H H H X X X ACTIVE (Select bank and activate row)(3)L L H H X Bank/Row X READ (Select bank/column, start READ burst)(4)L H L H L/H(8)Bank/Col X WRITE (Select bank/column, start WRITE burst)(4)L H L L L/H(8)Bank/Col Valid BURST TERMINATE L H H L X X Active PRECHARGE (Deactivate row in bank or banks)(5)L L H L X Code X AUTO REFRESH or SELF REFRESH(6,7)L L L H X X X (Enter self refresh mode)LOAD MODE REGISTER(2)L L L L X Op-Code X Write Enable/Output Enable(8)————L—Active Write Inhibit/Output H igh-Z(8)————H—High-Z NOTES:1.CKE is HIGH for all commands except SELF REFRESH.2.A0-A10 define the op-code written to the mode register.3.A0-A10 provide row address, and BA0, BA1 determine which bank is made active.4.A0-A7 (x32) provide column address; A10 HIGH enables the auto precharge feature (nonpersistent), while A10 LOW disablesauto precharge; BA0, BA1 determine which bank is being read from or written to.5.A10 LOW: BA0, BA1 determine the bank being precharged. A10 HIGH: All banks precharged and BA0, BA1 are “Don’t Care.”6.AUTO REFRESH if CKE is HIGH, SELF REFRESH if CKE is LOW.7.Internal refresh counter controls row addressing; all inputs and DQs are “Don’t Care” except for CKE.8.Activates or deactivates the DQs during WRITEs (zero-clock delay) and READs (two-clock delay).8Integrated Silicon Solution, Inc. — — 1-800-379-4774Rev.00DIntegrated Silicon Solution, Inc. — — 1-800-379-47749Rev.00D 06/02/08IS42S32200ETRUTH TABLE – CURRENT STATE BANK n, COMMAND TO BANK n (1-6)CURRENT STATE COMMAND (ACTION)CS RAS CAS WE Any COMMAND INHIBIT (NOP/Continue previous operation)H X X X NO OPERATION (NOP/Continue previous operation)L H H H IdleACTIVE (Select and activate row)L L H H AUTO REFRESH (7)L L L H LOAD MODE REGISTER (7)L L L L PRECHARGE (11)L L H L Row ActiveREAD (Select column and start READ burst)(10)L H L H WRITE (Select column and start WRITE burst)(10)L H L L PRECHARGE (Deactivate row in bank or banks)(8)L L H L Read READ (Select column and start new READ burst)(10)L H L H (Auto WRITE (Select column and start WRITE burst)(10)L H L L Precharge PRECHARGE (Truncate READ burst, start PRECHARGE)(8)L L H L Disabled)BURST TERMINATE (9)L H H L Write READ (Select column and start READ burst)(10)L H L H (Auto WRITE (Select column and start new WRITE burst)(10)L H L L Precharge PRECHARGE (Truncate WRITE burst, start PRECHARGE)(8)L L H L Disabled)BURST TERMINATE (9)LHHL TRUTH TABLE – CKE (1-4)CURRENT STATE COMMANDn ACTIONnCKEn-1CKEn Power-Down X Maintain Power-Down L L Self Refresh X Maintain Self Refresh L L Clock Suspend XMaintain Clock Suspend L L Power-Down (5)COMMAND INHIBIT or NOP Exit Power-Down L H Self Refresh(6)COMMAND INHIBIT or NOP Exit Self Refresh L H Clock Suspend (7)XExit Clock Suspend L H All Banks Idle COMMAND INHIBIT or NOP Power-Down Entry H L All Banks IdleAUTO REFRESH Self Refresh Entry H L Reading or WritingVALIDClock Suspend EntryH L See TRUTH TABL E – CURRENT STATE BANK n, COMMAND TO BANK nHHNOTES:1.CKEn is the logic state of CKE at clock edge n ; CKEn-1 was the state of CKE at the previous clock edge.2.Current state is the state of the SDRAM immediately prior to clock edge n .MANDn is the command registered at clock edge n , and ACTONn is a result of COMMANDn.4.All states and sequences not shown are illegal or reserved.5.Exiting power-down at clock edge n will put the device in the all banks idle state in time for clock edge n+1 (provided that t CKS is met).6.Exiting self refresh at clock edge n will put the device in all banks idle state once t XSR is met. COMMAND INHIBIT or NOP commands should be issued on clock edges occurring during the t XSR period. A minimum of two NOP commands must be sent during t XSR period.7.After exiting clock suspend at clock edge n , the device will resume operation and recognize the next command at clock edge n+1.IS42S32200ENOTE:1.This table applies when CKE n-1 was HIGH and CKE n is HIGH (see Truth Table - CKE) and after t XSR has been met (if theprevious state was SELF REFRESH).2.This table is bank-specific, except where noted; i.e., the current state is for a specific bank and the commands shown are thoseallowed to be issued to that bank when in that state. Exceptions are covered in the notes below.3.Current state definitions:Idle:The bank has been precharged, and t RP has been met.Row Active:A row in the bank has been activated, and t RCD has been met. No data bursts/accesses and no register accesses are in progress.Read:A READ burst has been initiated, with auto precharge disabled, and has not yet terminated or been terminated.Write:A WRITE burst has been initiated, with auto precharge disabled, and has not yet terminated or been terminated.4.The following states must not be interrupted by a command issued to the same bank. COMMAND INHIBIT or NOP commands, orallowable commands to the other bank should be issued on any clock edge occurring during these states. Allowable commands to the other bank are determined by its current state and CURRENT STATE BANK n truth tables.Precharging:Starts with registration of a PRECHARGE command and ends when t RP is met. Once t RP is met, the bank will be in the idle state.Row Activating:Starts with registration of an ACTIVE command and ends when t RCD is met. Once t RCD is met, the bank will be in the row active state.Read w/AutoPrecharge Enabled:Starts with registration of a READ command with auto precharge enabled and ends when t RP has been met.Once t RP is met, the bank will be in the idle state.Write w/AutoPrecharge Enabled:Starts with registration of a WRITE command with auto precharge enabled and ends when t RP has been met.Once t RP is met, the bank will be in the idle state.5.The following states must not be interrupted by any executable command; COMMAND INHIBIT or NOP commands must beapplied on each positive clock edge during these states.Refreshing:Starts with registration of an AUTO REFRESH command and ends when t RC is met. Once t RC is met, the SDRAM will be in the all banks idle state.Accessing ModeRegister:Starts with registration of a LOAD MODE REGISTER command and ends when t MRD has been met. Once t MRD is met, the SDRAM will be in the all banks idle state.Precharging All:Starts with registration of a PRECHARGE ALL command and ends when t RP is met. Once t RP is met, all banks will be in the idle state.6.All states and sequences not shown are illegal or reserved.7.Not bank-specific; requires that all banks are idle.8.May or may not be bank-specific; if all banks are to be precharged, all must be in a valid state for precharging.9.Not bank-specific; BURST TERMINATE affects the most recent READ or WRITE burst, regardless of bank.10.READs or WRITEs listed in the Command (Action) column include READs or WRITEs with auto precharge enabled and READsor WRITEs with auto precharge disabled.11.Does not affect the state of the bank and acts as a NOP to that bank.10Integrated Silicon Solution, Inc. — — 1-800-379-4774Rev.00D分销商库存信息:ISSIIS42S32200E-7TL IS42S32200E-6TL IS42S32200E-7TLIIS42S32200E-7BLI IS42S32200E-7TL-TR IS42S32200E-6TL-TR IS42S32200E-7TLI-TR IS42S32200E-7BL-TR IS42S32200E-6BL-TR IS42S32200E-6TLI-TR IS42S32200E-7BL IS42S32200E-7BLI-TR IS42S32200E-6TLI IS42S32200E-6BL IS42S32200E-6BLI-TR IS42S32200E-6B-TR IS42S32200E-6BLI IS42S32200E-6BIS42S32200E-6BI-TR IS42S32200E-6BI。
2444中文资料

CONSUMER PRODUCTS
Consumer Products
LCD TV & PLASMA TV COMPONENTS
SLOT SMT 200 W
Series 2652 – Resonant-type Power Supply Switch-Mode Transformer
Applications
Features
● Magnetic circuit of this transformer consists of two (asymmetrical) E-type ferrite cores having a rectangular central leg where the windings and the air gap are placed
38.1
18.5 25 20 15 15 16.25 16.25 15 20 16.25 20.32 20.32 27
Pitch Power Input (mm) @ 50 kHz (W)
7.5
30
5
40
4
40
5
40
5
40
5
0
5
130
4
40
4
40
5
60
5
90
5
120
5
200
5
250
5
70
5
300
5
90
5
170
5,08/ 15,24
350
5
4
5
30
4
30
3.75
8
3.75
8
5
18
5
18
3.75
IZ-SMW29EN条形离子器系列IZS40 41 42安装与维护手册安全指南说明书

Installation and Maintenance Manual Bar Type Ionizer Series IZS40/41/421 Safety InstructionsThis manual contains essential information for the protection of users and others from possible injury and/or equipment damage.∙ Read this manual before using the product, to ensure correct handling, and read the manuals of related apparatus before use. ∙ Keep this manual in a safe place for future reference.∙ These instructions indicate the level of potential hazard by label of “Caution”, “Warning” or “Danger”, followed by important safety information which must be carefully followed.∙ To ensure safety of personnel and equipment the safety instructions in this manual and the product catalogue must be observed, along withWarning∙ The compatibility of pneumatic equipment is the responsibility of thepersonwho designsthepneumaticsystem ordecides its specifications.Since the products specified here canbe used in various operating conditions, their compatibility with the specific pneumatic system must be based on specifications or after analysis and/or tests to meet specific requirements.∙ Only trained personnel should operate pneumatically operated machinery and equipment.Compressed air can be dangerous if an operator is unfamiliar with it. Assembly, handling or repair of pneumatic systems should be performed by trained and experienced personnel.∙ Do not service machinery/equipment or attempt toremove components until safety is confirmed.1) Inspection and maintenance of machinery/equipment should only be performed after confirmation of safe locked-out control positions.2) When equipment is to be removed, confirm the safety process as mentioned above. Switch off air and electrical supplies and exhaust all residual compressed air in the system.3) Before machinery/equipment is re-started, ensure all safety measures to prevent sudden movement of cylinders etc. (Supply air into the system gradually to create back pressure, i.e. incorporate a soft-start valve).∙ Do not use this product outside of the specifications. Contact SMC if it is to be used in any of the following conditions:1) Conditions and environments beyond the given specifications, or if the product is to be used outdoors.2) Installations in conjunction with atomic energy, railway, air navigation, vehicles, medical equipment, food and beverage, recreation equipment, emergency stop circuits, press applications, or safety equipment.3) An application which has the possibility of having negative effects on people, property, or animals, requiring special safety analysis.1.1 SelectionWarning∙ These products are intended for use in general factory automation equipment.Consult SMC before hand when using this product for other intentions. ∙ Use within the specified voltage and temperature range. Operation with a voltage other than that specified can cause malfunction, damage to the product, electric shock or fire. ∙ Use clean compressed air as fluid.Never use flammable or explosive gas as fluid. This may lead to fire or explosion. If fluid other than compressed air is used, consult SMC.1 Safety Instructions (Continued)∙ The product is not designed to be explosion proof.Never use in an atmosphere of potential dust explosion, flammable gas or explosive gas. It may cause fire.Caution∙ Clean specification is not available with this product.This product has not been cleaned. When using this product in a clean room environment, flush and confirm the product’s purification level before use. A minute amount of particles are generated due to wearing of the electrodes while the ionizer is operating.1.2 InstallationWarning∙ Secure enough space for maintenance, inspection and wiring.When routing cables and tubings, secure sufficient maintenance space for the installation and removal of connector and One-touch fitting. Consider the minimum bending radius of the cables and tubings and avoid bending them at an acute angle so that unreasonable stress is not applied to the mounting parts of the connectors and One-touch fittings. Position the connectors and One-touch fittings as close as possible.Routing of the wiring and cables in unreasonable positions may cause malfunction, broken cables, and fire.[Minimum bending radius] Power supply cable: 38mmTransition wiring cable: 38mm Sensor cable: 25mmNote:This is the minimum bend radius at 20o C. If the installation is at a lower temperature, the radium will be higher. When the cables are bent at a lower temperature than 20 o C, it may cause unreasonable force to be applied to the connectors.Refer to the tubing operation manual for minimum bending radius of tubing.∙ Mount to a flat surface.Mounting on an uneven surface will apply excessive force to the housing and bracket, which may lead to damage or failure. Do not drop the product or subject it to a strong impact. This may cause an injury or accident.∙ Install the product so that the entire bar does not have an excessive deflection.For a bar length of 820mm or more, support the bar at both ends and in the middle by using brackets (IZS40-BM). If the bar is held only at the both ends, self-weight of the bar causes deflection, resulting in damage to the bar.∙ Avoid using in a place where noise (electromagnetic wave and surge) is generated.It may cause malfunction, deterioration or damage to internal components. Take measures to prevent noise at its source and avoid power and signal lines from coming into close contact. ∙ Use a correct tightening torque.If the screws are tightened in excessive of the specified torque range, it may damage the mounting screws, mounting brackets, etc. If the tightening torque is insufficient, the mounting screws and brackets may become loose.∙ Do not directly touch the electrodes with your finger or tools. Do not directly touch the electrode with your finger. If the electrode sticks to your finger, or electrical shock makes an instantaneous rapid body motion to escape from the shock, your body may touch the equipment around you, causing injury. If electrode or cartridge isdamaged by tools, etc., it may interfere with the specified function and performance, and may also cause operation failure and accident.1 Safety Instructions (Continued)∙ Do not adhere tape or sticker onto the product body.If the tape or sticker contains conductive adhesive or reflective paint, it is possible that due to the dielectric effect, charge could build up causing an electro-static discharge or electrical leakage.∙ Be sure to remove power supply and air supply to the product before starting the product installation.Caution∙ Install the IZS4* series ionizer maintaining distance from a wall, etc. as shown in the Fig. below.When there is a wall or an object within the area shown in the Fig. below, generated ions may not reach the workpiece effectively, resulting in deterioration of efficiency.∙ Make sure to confirm the effect of de-ionization after installation. The effect of the ionizer varies depending on the surrounding installation and operating conditions. Confirm the effect of static electricity elimination after installation.∙ When installing IZS41 or IZS42 in proximity with an ionizer which operates in DC mode, they should be positioned at least 2 meters away from each other. When IZS41 or IZS42 isused close to an ionizerwhich operates in DCmode, separate theionizers at least 2 meters.Ion balance may not be adjusted by the internal sensor due to the ions which are discharged from the DC mode ionizer.1.3 Wiring and PipingWarning∙ Ensure that the power supply capacity is large enough, and thatvoltage is within specification before wiring.∙ To maintain product performance, a DC power supply shall be connected per UL listed Class 2 certified by National Electric Code (NEC) or evaluated as a limited power source provided by UL60950. ∙ To maintain the product performance, ground the product with an earth ground cable with a resistance of 100 ohm or less according to this manual.∙ Remove the power supply before wiring (including the connector plug in/out).∙ Use a cable with sensor for connection of the ionizer, feedback sensor or auto balance sensor (high accuracy type), and do NOT disassemble or retrofit.∙ Ensure the safety of wiring and surrounding conditions before supplying power.∙ Do not connect or disconnect the connectors (including power source) while the power is being supplied. The ionizer may malfunction.∙ Malfunctions induced by noise may occur if the wire is installed in the same route as that of power or high-voltage cable. Wire the ionizer independently.∙ Confirm that there is no error in wiring before operation. Incorrect wiring will lead to a malfunction or breakage of the product.∙ Flush the piping before connecting. Verify that all dust, moisture, oil, etc. are eliminated from the piping before connecting.1.4 Operating and Storage EnvironmentWarning∙ Operate the product in the specified fluid temperature range and ambient temperature range.Fluid temperature and ambient temperature ranges are; 0 to 40 o C for Ionizer, 0 to 50 o C for feedback sensor and auto balance sensor (high accuracy type), 0 to 40 o C for AC adapter, and 0 to 45 o C for remote controller. Avoid sudden temperature change even within specified temperature range, as it may cause condensation.1 Safety Instructions (Continued)∙ Do not use this product in an enclosed space.This product utilizes the corona discharge phenomenon. Although the amount is very small, Ozone and NOx are generated. Do not use in an enclosed space.∙ Environments to avoidNever use or store under the following conditions, as these cause product failure.a. Areas where ambient temperature exceeds the operating temperature range.b. Areas Where ambient humidity exceeds the operating humidity range.c. Areas where abrupt temperature changes may cause condensation.d. Areas where corrosive gas, flammable gas or other volatile flammable substances are stored.e. Areas where the product may be exposed to conductive powder such as iron powder or dust, oil mist, salt, organic solvent, machining chips, particles or cutting oil (including water and any liquids), etc.f. Paths of direct air flow, such as air conditioners.g. Enclosed or poorly ventilated areas.h. Locations that are exposed to direct sunlight or heat radiation.i. Areas where strong electromagnetic noise is generated, such as strong electrical and magnetic fields or supply voltage spikes.j. Areas where the product is exposed to static electricity discharge. k. Locations where strong high frequency is generated. l. Locations that are subject to potential lightning strikes.m. Areas where the product may be exposed to direct impact or vibration. n. Areas where the product may be subjected to forces or weight that could cause physical deformation.∙ Do not use air containing mist and/or dust.Air containing mist and/or dust may cause performance deterioration, and reduce the maintenance cycle.Install a dryer (IDF series), air filter (AF/AFF series), or mist separator (AFM/AM series) to obtain clean compressed air (air quality of Class 2.6.3 or higher according to ISO 8573-1: 2001 is recommended for operation). ∙ Ionizer, feedback sensor, auto balance sensor (high accuracy type), remote controller, and AC adapter are not resistant to lightening surge.1.5 Maintenance and InspectionWarning∙ Perform maintenance regularly to keep the electrodes clean.Perform regular maintenance of the product to prevent undetected failures. The maintenance must be carried out by an operator who has sufficient knowledge and experience. If the product is used for an extended period of time with dust is present on the electrodes, the product’s abili ty to eliminate static electricity will be reduced.If the electrodes become worn and the product’s ability to eliminate static electricity is not restored after cleaning, replace the cartridge.∙ Make sure to remove power and air supply from the product before cleaning the electrodes or replacing the cartridges.If the electrodes are touched while the product is energized, this may cause an electric shock or accident.If an attempt to replace the cartridges is performed before removing air supply, the cartridges may eject unexpectedly due to presence of the supply air. Remove air supply before replacing the cartridges. If cartridges are not securely mounted to the bar, they may eject or release when air is supplied to the product. Securely mount or remove the cartridges referencing the instructions shown below.∙ Perform contamination detection of the electrode without workpiece. (IZS41 and IZS42)While electrode detects contamination, ionizer discharges positive ions and negative ions for contamination detection. ∙ Do not disassemble or modify the product.This may lead to accidents such as electric shock, failure, fire or etc. If the product is disassembled and/or modified, the functions andperformance in the specifications may not be achieved and the product will not be guaranteed.∙ Do not operate the product with wet hands. This may cause an electric shock or accident.Unit: mm 150 150 200 200 High voltage is applied to the electrodes. Never touch thegenerating High voltage cautionM4 screwM4 screwEnd bracket Intermediate bracket Part A2.1 Mounting and installation of the bracket1) End bracketMount an end bracket to both ends of the ionizer body using the M4 screws supplied as accessories.Tightening torque: 1.3 to 1.5Nm2) Intermediate bracket (for bar lengths of 820mm or more)Match the groove of the ionizer body and protrusion of the intermediate bracket, and slide the bracket from the end of the ionizer body. Intermediate brackets should be mounted at the same intervals.3) Installation of the ionizer (when using brackets)Tap (M5) screws at the bracket mounting positions for installation of the Ionizer and fix the ionizer body and brackets with M5 screws.IZS40 and IZS41 are constructed such that the brackets at the bracket mounting positions on both ends of the bar are shared with F.G. Use caution to avoid short-circuit with the +24V power supply when installing and supplying power.4) Mounting angle adjustmentAdjust the angle of the ionizer body for effective de-ionizing and fix the ionizer with the rotating set screw (M4) at each bracket.End bracket tightening torque: 1.3 to 1.5 NmIntermediate bracket tightening torque: 0.73 to 0.75Nm2.2 InstallationWarning∙Do not install the product unless the safety instructions have been readand understood.2.3 PipingCaution∙Before piping make sure to clean up chips, cutting oil, dust etc.∙When installing piping or fittings, ensure sealant material does not enterinside the port. When using seal tape, leave 1.5 to 2 threads exposed onthe end of the pipe/fitting.∙Tighten fittings to the specified tightening torque.2.4 EnvironmentWarning∙Do not use in an environment where corrosive gases, chemicals, saltwater or steam are present.∙Do not use in an explosive atmosphere.∙Do not expose to direct sunlight. Use a suitable protective cover.∙Do not install in a location subject to vibration or impact. Check theproduct specifications.∙Do not mount in a location exposed to radiant heat.3 WiringWire cables according to the circuitry and wiring chart.3.1 Grounding of F.G. cableMake sure to ground the F.G. cable (green) with a resistance of100 ohms or less.The F.G. cable is used as a reference electric potential for de-ionization. If the ground terminal F.G. is not grounded, the ionizer willnot be able to achieve the optimal ion balance.3.2 Grounding during operation in DC modeApplicable models:IZS40 and IZS41When an ionizer is used in DC mode, make sure to ground the F.G.cable (green) and GND cable (blue) of the input power supply with aresistance of 100 ohms or less. Without grounding the GNDterminal, the ionizers and/or power supply may be damaged.3.3 Circuit (Wiring of IZS40)e-con is adopted for the connector of IZS40. Connector with cableor without cable maybe selected when placing an order for the powersupply cable.When only an e-con is required, place an order for it as a part.Cable is not supplied.)Wiring1) Cut the cable as shown in theFigure to the right.applicable wire size.Applicable wire3.4 Circuit (Wiring of IZS41 and IZS42)2) Insert the cable which was cut intothe back of the connector.3) Confirm that the cable is insertedinto the back of the connector andpress part A with your finger tohold tentatively.4) Use a tool such as pliers to firmlytighten the center of Part A.5) The connector cannot be reusedonce crimped. If cable insertionfails, use a new connector.DescriptionRB5B1A5A1When an ionizer is used in DC mode, make sure to ground the F.G. cable (green) and GND cable (blue) of the input power supply with aresistance of 100 ohms or less. Without grounding the GND terminal, the ionizers and/or power supply in connection may be damaged.If cables are prepared by the user, the cable colors shown in the diagram may change according to the cable colors by the user.Signal name Signal direction1) NPN typeRefer to the operation manual for this product.5 Settings5.1 Descriptions and Functions of the Panel (IZS40)When an ionizer (IZS41) is used in DC mode, make sure to ground the F.G. cable (green) and GND cable (blue) of the input power supply with a resistance of 100 ohms or less. Without grounding the GND terminal, the ionizers and/or power supply in connection may be damaged. When an ionizer (IZS41) is used in DC mode, make sure to ground the F.G. cable (green) and GND cable (blue) of the input power supply with a resistance of 100 ohms or less. Without grounding the GND terminal, the ionizers and/or power supply in connection may be damaged.2 1 53 45.2 Descriptions and Functions of the Panel (IZS41, IZS42)Refer to the operation manual for this product.11 10 9 8 7 6 5 4 3 2 1 14 13 12"N", and order a part (Part No.: ZS-28-C) separately.option number. (A cable is attached to the AC adapter)- Input/ Output function cannot be used when the AC adapter isbeing used.- To use AC adapter, specify "N", and select AC adapter with theRefer to the operation manual for this product. 7.1 IZS407.2 IZS41 / IZS428.1 General MaintenanceCaution∙ Not following proper maintenance procedures could cause the product to malfunction and lead to equipment damage.∙ If handled improperly, compressed air can be dangerous. Maintenance of pneumatic systems should be performed only by qualified personnel.∙ Before performing maintenance, turn off the power supply and be sure to cut off the supply pressure. Confirm that the air is released to atmosphere. ∙ After installation and maintenance, apply operating pressure and power to the equipment and perform appropriate functional and leakage tests to make sure the equipment is installed correctly. ∙ Do not make any modification to the product.∙ Do not disassemble the product, unless required by installation or maintenance instructions.8.2 Detection and cleaning of contamination on the electorodeCaution∙ If the ionizer is used for a long time, contamination such as dust can stick to the electrodes, reducing the static electricity elimination performance. For this reason, IZS41 and IZS42 have a contamination detecting function. ∙ Dirt detection is performed when a contamination detection signal from an electrode is input. When the electrode requires cleaning due to deterioration of de-ionizing ability, the maintenance signal turns ON and maintenance LED also turns ON to notify the timing of cleaning. When the maintenance LED turns ON, make sure to clean the electrode. (Ionizer keeps operating even after the maintenance signal and maintenance LED turn ON.)∙ Dirt detection of electrodes should be performed without a workpiece, as it is performed with ions discharged from the ionizer at a regular cycle and this may electrify the workpiece.∙ Clean the electrodes with the electrode cleaning kit [IZS30-M2] or a cotton swab soaked in alcohol.∙ In cases where the electrode contamination detecting function is not used or when the IZS40 does not have a contamination detecting function,, as contamination on the electrodes may vary depending on the installation environment and supply pressure, etc., confirm the product performance and set a maintenance cycle for a periodic cleaning.∙ Make sure to turn OFF the power and air supply before cleaning the electrodes. If the electrodes are touched while the product is energized, it may cause an electric shock or accident. Do not touch the end of the electrodes. As electrodes have a sharp end, touching them directly with your fingers may cause injury.∙ If the maintenance signal is output upon completion of cleaning the electrode, it may not have been cleaned sufficiently or it may have been worn or damaged. If wear or damage of the electrode is detected, replace the electrode cartridge with a new one. (If the electrode is worn out or damaged, the static electricity elimination performance will decrease.)∙ Refer to the Fig. below for mounting, removal and cleaning of an electrode cartridge.Warning∙ Do not exceed any of the specifications laid out in section 4 of this document or the specific product catalogue.10 Disposal informationThe remote controller IZS41-RC used for this ionizer is a product sold separately. For this reason it is classified as Waste Electrical or Electronic Equipment according to the WEEE Directive 2012/19 / EU and should not be disposed of as municipal waste, in order to reduce the impact on human health and the environment. Remove and dispose of old batteries and the remaining electrical or electronic equipment according to local environmental regulations.11 ContactsAUSTRIA (43) 2262 62280-0 LATVIA (371) 781 77 00 BELGIUM (32) 3 355 1464 LITHUANIA(370) 5 264 8126 BULGARIA (359) 2 974 4492 NETHERLANDS (31) 20 531 8888 CZECH REP. (420) 541 424 611 NORWAY (47) 67 12 90 20 DENMARK (45) 7025 2900 POLAND (48) 22 211 9600 ESTONIA (372) 651 0370 PORTUGAL (351) 21 471 1880 FINLAND (358) 207 513513 ROMANIA (40) 21 320 5111 FRANCE (33) 1 6476 1000 SLOVAKIA (421) 2 444 56725 GERMANY (49) 6103 4020 SLOVENIA (386) 73 885 412 GREECE (30) 210 271 7265 SPAIN (34) 945 184 100 HUNGARY (36) 23 511 390 SWEDEN(46) 8 603 1200 IRELAND (353) 1 403 9000 SWITZERLAND (41) 52 396 3131 ITALY(39) 02 92711UNITED KINGDOM(44) 1908 563888URL : http// (Global) http// (Europe) Specifications are subject to change without prior notice from the manufacturer. © 2010 SMC Corporation All Rights Reserved.counter-clockwise direction. Removal of electrode cartridge 2) Pull to remove. IZS30-M2 Cleaning of electrode 1) Insert the cartridge into the barso that the longer side of the cartridge is mounted at a right angle to the bar.Mounting of electrode cartridge2) Rotate the cartridge degrees in the clockwise and ma tch the ma rkings on the the ca rtridge to fix.。
焊丝对照表
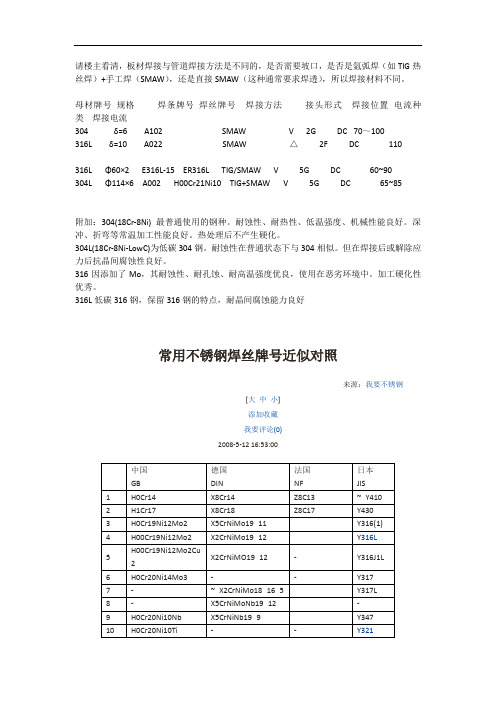
请楼主看清,板材焊接与管道焊接方法是不同的,是否需要坡口,是否是氩弧焊(如TIG热丝焊)+手工焊(SMAW),还是直接SMAW(这种通常要求焊透),所以焊接材料不同。
母材牌号规格焊条牌号焊丝牌号焊接方法接头形式焊接位置电流种类焊接电流304 δ=6 A102 SMAW V 2G DC 70~100316L δ=10 A022 SMAW △ 2F DC 110316L Φ60×2 E316L-15 ER316L TIG/SMAW V 5G DC 60~90304L Φ114×6 A002 H00Cr21Ni10 TIG+SMAW V 5G DC 65~85附加:304(18Cr-8Ni) 最普通使用的钢种。
耐蚀性、耐热性、低温强度、机械性能良好。
深冲、折弯等常温加工性能良好。
热处理后不产生硬化。
304L(18Cr-8Ni-LowC)为低碳304钢。
耐蚀性在普通状态下与304相似。
但在焊接后或解除应力后抗晶间腐蚀性良好。
316因添加了Mo,其耐蚀性、耐孔蚀、耐高温强度优良,使用在恶劣环境中。
加工硬化性优秀。
316L低碳316钢,保留316钢的特点,耐晶间腐蚀能力良好常用不锈钢焊丝牌号近似对照来源:我要不锈钢[大中小]添加收藏我要评论(0)2008-5-12 16:53:00中国德国法国日本GB DIN NF JIS1H0Cr14X8Cr14Z8C13~ Y4102H1Cr17X8Cr18Z8C17Y4303H0Cr19Ni12Mo2X5CrNiMo19 11Y316(1)4H00Cr19Ni12Mo2X2CrNiMo19 12Y316L5H00Cr19Ni12Mo2Cu2X2CrNiMO19 12-Y316J1L6H0Cr20Ni14Mo3--Y317 7-~ X2CrNiMo18 16 5Y317L 8-X5CrNiMoNb19 12-9H0Cr20Ni10Nb X5CrNiNb19 9Y347 10H0Cr20Ni10Ti--Y32111H0Cr21Ni10X5CrNi19 9Y308(1)12H00Cr21Ni10X2CrNi19 9Y308L(1)13H1Cr24Ni13X12CrNi22 12Y30914-X2CrNi24 12Y309L15H1CrNi13Mo2--Y309Mo16H0Cr26Ni21X2CrNiNb24 12--17H1Cr26Ni21X12CrNi25 20Y31018-X40CrNi25 21--19-常用不锈钢焊丝牌号近似对照来源:我要不锈钢[大中小]添加收藏我要评论(0)2008-5-12 16:53:00中国德国法国日本GB DIN NF JIS1H0Cr14X8Cr14Z8C13~ Y4102H1Cr17X8Cr18Z8C17Y4303H0Cr19Ni12Mo2X5CrNiMo19 11Y316(1)4H00Cr19Ni12Mo2X2CrNiMo19 12Y316L5H00Cr19Ni12Mo2Cu2X2CrNiMO19 12-Y316J1L6H0Cr20Ni14Mo3--Y3177-~ X2CrNiMo18 16 5Y317L8-X5CrNiMoNb19 12-9H0Cr20Ni10Nb X5CrNiNb19 9Y34710H0Cr20Ni10Ti--Y32111H0Cr21Ni10X5CrNi19 9Y308(1)12H00Cr21Ni10X2CrNi19 9Y308L(1)13H1Cr24Ni13X12CrNi22 12Y30914-X2CrNi24 12Y309L15H1CrNi13Mo2--Y309Mo16H0Cr26Ni21X2CrNiNb24 12--17H1Cr26Ni21X12CrNi25 20Y31018-X40CrNi25 21--19-序号牌号型号序号牌号型号可以用型号和牌号来反映焊丝的主要性能特征及类别。
电子热继ZEV

1
!"#$
LCD !"#$%&'()*+,!"#$%&' !"
!"#$%&'()*+,!"# $%& 05-06 ! 07-08
!"#$%&'() !"#$% !" ! !"#$% !
!
ZEV AC/DC !"#$ 24-240V 50/60 Hz !"#$%&'()*
!"#$%&
!"#$ZEV !
2
ZEV
ZEV-XSW-25 -
ZEV-XSW-65 -25/+60 -25/+40 2-65
ZEV-XSW-145 -25/+60 -25/+40 10-145
ZEV-XSW-820 -25/+60 -25/+40 8000 1000 1000 40-820
/
) !"
-25/+60 -25/+40 1-820 4000 1x(0.5-2.5) 250 240 240 6 3/3 1 0.85-1.1Us -25/+60 -25/+40 1-25
15 ! 24.5 17.7 13.9 11.5 9.5 8.6 6.9
20 32.5 23.5 18.4 15.2 12.6 11.3 9.0
25 40.6 29.2 22.9 18.8 15.6 14.0 11.1
30 48.6 35.0 27.4 22.5 18.6 16.7 13.3
35 56.6 40.7 31.9 26.2 21.6 19.4 15.4
- 1、下载文档前请自行甄别文档内容的完整性,平台不提供额外的编辑、内容补充、找答案等附加服务。
- 2、"仅部分预览"的文档,不可在线预览部分如存在完整性等问题,可反馈申请退款(可完整预览的文档不适用该条件!)。
- 3、如文档侵犯您的权益,请联系客服反馈,我们会尽快为您处理(人工客服工作时间:9:00-18:30)。
Power MOSFETIRFIZ24G, SiHFIZ24GVishay SiliconixFEATURES•Isolated Package•H igh Voltage Isolation = 2.5 kV RMS (t = 60 s;f = 60 Hz)•Sink to Lead Creepage Distance = 4.8 mm •175 °C Operating Temperature •Dynamic dV/dt Rating•Low Thermal Resistance •Lead (Pb)-free Available DESCRIPTIONThird generation Power MOSFETs from Vishay provide the designer with the best combination of fast switching,ruggedized device design, low on-resistance and cost-effectiveness.The TO-220 FULLPAK eliminates the need for additional insulating hardware in commercial-industrial applications.The molding compound used provides a high isolation capability and a low thermal resistance between the tab and external heatsink. This isolation is equivalent to using a 100micron mica barrier with standard TO-220 product. The FULLPAK is mounted to a heatsink using a single clip or by a single screw fixing.Notesa.Repetitive rating; pulse width limited by maximum junction temperature (see fig. 11).b.V DD = 25 V, starting T J = 25 °C, L = 595 µH, R G = 25 Ω, I AS = 14 A (see fig. 12).c.I SD ≤ 17 A, dI/dt ≤ 140 A/µs, V DD ≤ V DS , T J ≤ 175 °C.d. 1.6 mm from case.PRODUCT SUMMARYV DS (V)60R DS(on) (Ω)V GS = 10 V 0.10Q g (Max.) (nC)25Q gs (nC) 5.8Q gd (nC)11ConfigurationSingleORDERING INFORMATIONPackage TO-220 FULLPAK Lead (Pb)-free IRFIZ24GPbF SiHFIZ24G-E3 SnPbIRFIZ24G SiHFIZ24GABSOLUTE MAXIMUM RATINGS T C = 25 °C, unless otherwise notedPARAMETER SYMB O L LIMITUNIT Drain-Source Voltage V DS 60VGate-Source Voltage V GS ± 20 Continuous Drain Current V GS at 10 VT C = 25 °C I D14A T C = 100 °C10Pulsed Drain Current a I DM 56Linear Derating Factor0.24W/°C Single Pulse Avalanche Energy b E AS 100mJ Maximum Power Dissipation T C = 25 °CP D 37WPeak Diode Recovery dV/dt cdV/dt 4.5V/ns Operating Junction and Storage Temperature Range T J , T stg- 55 to + 175°C Soldering Recommendations (Peak Temperature)for 10 s 300d Mounting Torque6-32 or M3 screw10 lbf · in 1.1N · m * Pb containing terminations are not RoHS compliant, exemptions may applyIRFIZ24G, SiHFIZ24GVishay SiliconixNotesa.Repetitive rating; pulse width limited by maximum junction temperature (see fig. 11).b.Pulse width ≤ 300 µs; duty cycle ≤ 2 %.THERMAL RESISTANCE RATINGSPARAMETER SYMBL TYP.MAX.UNIT Maximum Junction-to-Ambient R thJA -65°C/WMaximum Junction-to-Case (Drain)R thJC- 4.1IRFIZ24G, SiHFIZ24GVishay SiliconixIRFIZ24G, SiHFIZ24GVishay SiliconixFig. 9 - Maximum Drain Current vs. Case TemperatureFig. 10a - Switching Time Test CircuitFig. 10b - Switching Time WaveformsFig. 11 - Maximum Effective Transient Thermal Impedance, Junction-to-CaseIRFIZ24G, SiHFIZ24GVishay SiliconixFig. 13a - Basic Gate Charge WaveformFig. 13b - Gate Charge Test CircuitIRFIZ24G, SiHFIZ24GVishay Siliconix Array Fig.14 - For N-ChannelVishay Siliconix maintains worldwide manufacturing capability. Products may be manufactured at one of several qualified locations. Reliability data for Silicon Technology and Package Reliability represent a composite of all qualified locations. For related documents such as package/tape drawings, part marking, andreliability data, see /ppg?91187.Disclaimer Legal Disclaimer NoticeVishayAll product specifications and data are subject to change without notice.Vishay Intertechnology, Inc., its affiliates, agents, and employees, and all persons acting on its or their behalf (collectively, “Vishay”), disclaim any and all liability for any errors, inaccuracies or incompleteness contained herein or in any other disclosure relating to any product.Vishay disclaims any and all liability arising out of the use or application of any product described herein or of any information provided herein to the maximum extent permitted by law. The product specifications do not expand or otherwise modify Vishay’s terms and conditions of purchase, including but not limited to the warranty expressed therein, which apply to these products.No license, express or implied, by estoppel or otherwise, to any intellectual property rights is granted by this document or by any conduct of Vishay.The products shown herein are not designed for use in medical, life-saving, or life-sustaining applications unless otherwise expressly indicated. Customers using or selling Vishay products not expressly indicated for use in such applications do so entirely at their own risk and agree to fully indemnify Vishay for any damages arising or resulting from such use or sale. Please contact authorized Vishay personnel to obtain written terms and conditions regarding products designed for such applications.Product names and markings noted herein may be trademarks of their respective owners.元器件交易网。