周期时间与节拍时间之间的计算
生产节拍测定管理规范

生产节拍测定管理规范文件编号:JF/QD-7.5.1-09文件版号:C0编制:顾海山审核:王辉批准:陶力晟受控状态:分发号:版本修订历史记录版本号修订内容修订者修订时间NO 1 2 3 4 5 6 7 8 9 10 11 12 13 14 15部门总经理常务副总生产副总营销副总总经办市场部技术开发部配套部品质部财务部制造一部制造二部会签部门分发部门总经理常务副总生产副总营销副总总经办市场部技术开发部配套部品质部财务部制造一部制造二部分发人数一、目的为公司生产节拍的测定提供规范化的管理准则,特制定本规范。
二、适用范围适用于产品作业标准节拍工时的测定。
三、管理职责3.1技术开发部负责本规范的制定、修改、废止等工作。
3.2 总经理负责本规范的批准工作。
四、管理内容4.1 标准工时的制定标准工时定义:某一加工工序,在正常的作业条件、正常的工作环境下,中等熟练程度的作业人员按正常的作业速度完成作业所需的时间,称为标准工时,单位为“分/人/件”或“秒/人/件”。
4.1.1 产品正式导入量产后,生产趋于稳定时(一般为生产一周后),由制造部门长对各工序进行工时测评,根据4.1.2条款进行测定方法和计算标准工时。
记录数据后提交技术开发部工艺工程师进行审核确认,常务副总进行批准。
4.1.2作业时间测定方法:(本公司测定的节拍标准工时是由秒表法设定)a. 测定工时人员准备秒表,笔和《现场测定观测记录表》b. 测定人员选择生产比较顺畅的拉线进行对每一工序作业时间进行实际测算。
1)在秒表记录时,需要连续测试5个产品以上的周期时间,并将每组的数据严格记录到记录表中。
2)周期时间定义:作业人员从取料开始到下一次取料的总时间,称为周期时间(CT),它包括人的作业时间与机器的作业时间。
周期时间=作业的时间+机器的时间c.在每个工序记录完成每组数据后,计算出每组工序的测试平均值,并记录到表格中。
1)测试完成后计算出平均实际测试时间.实测时间=测试总时间/测试周期数。
物料和信息流动图

双日12:00前 周度订单预测计划
物流管理科副科长 (负责核实)
欧曼生 产计划
科
3、10、17、25日 12:00前
月度需求计划
每月15日 月度调整计划
每月10日前
公 司 生 产 管 理 部
销 售 计 划 科
月度需求计划 每月15日
月每度月资15源日配置计划
月度生产计划 每月22日
网 上 发
当日12:00前
每日10:00反馈库存(发动机、变 速箱、桥)
送检单
3家
5天 库存日报表
每天上午十点报缺件 每天下午四点报缺件
按日计划
外检科
保管员 74人
物流管理科库房
微机操作员 8人
1天
车间领料定量不定 时
直送工位
每天上午十点报缺件 每天下午四点报缺件
每天上午十点报缺件 每天下午四点报缺件
生产计划科
27
在有两条或两条以上的生产线并行时, 以较长的生产线为主线计算过程周期时间, 其它并行的生产线只标出附加价值时间, 时间轴上的附加价值时间为各并行工序的 附加价值时间之和。
28
在画图时要有纵轴的概念,对于同一时 间段进行的内容,要纵向列下来与下边的 时间对应。
将问题点和要进行改善的内容用爆炸符 号在图中表示出来。
开发的过程周期时间
生产的过程周期时间
投资 资金回笼
4
2、节拍时间(TT): 节拍时间TT = 1天的工作时间(固定时间)/1 天的生产必要数
3、循环时间(CT): 1名工人在按照标准作业顺序操作的情况下,
操作1个循环所需的实际最短时间(包括步行时 间)。它是真正作业时间,不包含等待的时间。
5
指令周期,cpu周期,节拍周期之间的关系的关系

指令周期,cpu周期,节拍周期之间的关系?周期:就是时间,完成一次任务的时间指令周期是执行一条指令所需要的时间,即CPU从内存取出一条指令并执行这条指令的时间总和。
一般由若干个机器周期组成,从取指令、分析指令到执行完所需的全部时间。
指令不同,所需的机器周期数也不同。
对于一些简单的的单字节指令,在取指令周期中,指令取出到指令寄存器后,立即译码执行,不再需要其它的机器周期。
对于一些比较复杂的指令,例如转移指令、乘法指令,则需要两个或者两个以上的机器周期。
通常含一个机器周期的指令称为单周期指令,包含两个机器周期的指令称为双周期指令。
CPU周期又称机器周期,CPU周期定义为从内存读取一条指令字的最短时间。
一个指令周期常由若干CPU周期构成。
时钟周期(节拍周期)时钟周期也称为振荡周期,定义为时钟脉冲的倒数(可以这样来理解,时钟周期就是单片机外接晶振的倒数,例如12M的晶振,它的时间周期就是1/12 us),是计算机中最基本的、最小的时间单位。
在一个时钟周期内,CPU仅完成一个最基本的动作。
对于某种单片机,若采用了1MHZ的时钟频率,则时钟周期为1us;若采用4MHZ的时钟频率,则时钟周期为250us。
由于时钟脉冲是计算机的基本工作脉冲,它控制着计算机的工作节奏(使计算机的每一步都统一到它的步调上来)。
显然,对同一种机型的计算机,时钟频率越高,计算机的工作速度就越快。
但是,由于不同的计算机硬件电路和器件的不完全相同,所以其所需要的时钟周频率范围也不一定相同。
我们学习的8051单片机的时钟范围是1.2MHz-12MHz。
在8051单片机中把一个时钟周期定义为一个节拍(用P表示),二个节拍定义为一个状态周期(用S表示)。
时钟周期时钟周期也称为振荡周期,定义为时钟脉冲的倒数(时钟周期就是单片机外接晶振的倒数,例如12M的晶振,它的时钟周期就是1/12us),是计算机中的最基本的、最小的时间单位。
在一个时钟周期内,CPU仅完成一个最基本的动作。
生产周期与节拍生产管理@管理课件

啤机 剪带 剪带
1.啤头及一字位 2.啤尾 3.啤尾孔 4.啤带身通花
1.啤头 2.啤尾 3.啤尾孔
剪带
剪带
1.啤带身爪钉孔 2.啤头皮 3.啤尾 4.啤尾孔
1.剪带身
1.贴带尾
2.啤带身机眼孔 2.啤带头一字
3.剪介子
位
/
油边 丝印 车位 车唛头
啤中间三角皮、油 边
1.丝印(logo) 2.油带身及介子 3.铲头
57000 82000
备注 备用 25台
节拍生产排期表
工序 工序 名称 序号
工序名称
标准产量(小 时产量)
节拍小时数/人
节拍 人数
现有 人数
订单数量
预计完成 时间
最佳节拍 人数
难度系数
安排人 数
时间进度
调整 人数
1
2 开料
3
4 合计
1
啤机 2 3
合计
1
油边 2 3
合计 1
车位 2
合计 1
装配 2
合计 包装 1
一、生产周期的计算:
组/名称 开料 啤机 油边 车位 装配 包装
一、生产周期的计算:
组/名称 开料
工序/名称 写牌仔 介料 开带 飞边
1.效率法—
A.同一工序抽三至五个熟练员工 B.每天四次、每次记录10件的生产时间 C.将10件生产时间相加平均 D.再将平均四次的时间相加再平均 E.将三至五个熟练员工时间相加再平均 备注: 如发觉某些数据差距大可省略或再测
12.5 288PCS/时
3600秒(1小时)/12.5=288
LK1589
产量 1000 人数 2000 人数 3000 人数 4000 人数
生产运作管理计算题标准步骤(2)

生产运作管理共有五道计算类型题:标黄色的表示做题时,必须要阐述写清的。
一、装配线平衡的方法1.(在答题纸上划出题中要求的网络图)2.节拍计算:节拍r=计划期有效工作时间/计划期计算产量3.计算满足节拍需要的工作地的最小数量理论值。
S min=[工序时间之和/节拍](最终结果进位取整)4.组织工作地。
按节拍要求分配组织各工作地的工序(在网络图上标)。
分配时要遵循:保证各工序之间的先后顺序;各工作地的作业时间应尽量接近或等于节拍;工作地数目尽量少。
5.评价装配平衡的效率:装配线的效率=完成作业所需时间/实际工作地数*节拍二、用代表产品法或假定产品法计算设备生产能力1.代表产品法的步骤:①选定代表产品。
因*产品计划产量(或计划产量与台时定额之积)最大,故选*产品为代表产品。
②计算换算系数。
见表中第③项。
(以代表产品的台时定额为分母,其它产品的台时定额为分子,计算每种产品的换算系数。
)(将每个产品的换算系数填入表格中)③计算表中第④项。
(用每种产品的计划产量乘换算系数,得出用代表产品表示的产量。
并填入表中。
)④计算产量比重。
见表中第⑤项。
每个产品的产量/总产量⑤计算生产能力:表中第⑥项设备生产能力=设备年有效工作小时数/代表产品台时定额 = **=年有效工作日*每天工作小时数*设备台数*(1-设备检修率)/代表产品台时定额(生产能力取整,小数部分只舍不入),结果填入表中。
⑥按产量比重计算各产品生产能力⑦=生产能力⑥*比重⑤/换算系数③,将各产品生产能力填入表中。
⑦如生产能力大于计划产量,则表示能力满足计划需求;•(或如生产能力小于计划产量,则表示生产能力不足,企业应想办法增加生产能力来满足需求。
)2.假定产品法的步骤:①计算假定产品台时定额。
③=(每种产品的计划产量与台时定额乘积的和/总产量)=①A*②A+①B*②B+①C*②C+①D*②D/总产量②计算产量比重。
见表中第④项。
每个产品的产量/总产量③计算设备生产能力=设备年有效工作小时数/代表产品台时定额 = **=年有效工作日*每天工作小时数*设备台数*(1-设备检修率)/代表产品台时定额(生产能力取整,小数部分只舍不入),结果填入表中。
流水线生产节拍计算公式

流水线生产节拍计算公式
流水线生产是一种快速、高效的生产模式,它被广泛应用于制造行业。
流水线生产的节拍计算可以更好地规划生产,并为企业提供更有效的管理。
在本文中,我们将介绍流水线生产节拍的计算公式,以及如何利用其进行生产规划。
一、节拍计算公式
流水线生产节拍的计算公式为:节拍(BPM)= 60 000/生产周期(m)。
节拍单位为每分钟多少次,也就是每分钟多少次生产(组装、测试、检查等),即BPM(节拍),而生产周期(m)指的是一个工序的生产耗时,单位为分钟,即生产一件产品所消耗的时间。
根据流水线生产节拍计算公式,可以计算出每分钟需要完成多少次生产以及生产一件产品所需要的时间。
例如:若需要每分钟完成6次生产,那么生产一件产品所需要的时间就是10分钟: BPM=
60 000/10 = 6 000。
二、流水线生产计划
利用流水线生产节拍计算公式,可以更好地规划流水线生产,以便提高企业的效率和产量。
首先,对制造技术进行分析,确定生产每件产品的工序及时间,即计算出m的值,确定每分钟需完成的生产次数,计算出BPM (每分钟节拍)。
其次,需根据每分钟节拍规划工装,确定每台设备的产能,即确定每台设备每分钟最大能生产多少件产品,并组合各
机台,形成一条完整的流水线,以确定最大产量。
最后,可根据实际情况,调整看板设置、设备速度等,调整每分钟的节拍,实现企业的最佳生产效果。
三、结论
流水线生产节拍计算公式为60 000/m,可以根据该公式,计算出每分钟完成多少次生产以及生产一件产品所需要的时间。
此外,也可以利用该公式,进行流水线生产计划,调整每分钟节拍,以实现企业的最佳生产效果。
时间和周期的关系

时间和周期的关系
#### 时间和周期的关系
1. 时间和周期的关系是指物理现象之间的重复性关系。
时间用来定义
现象发生的顺序,也可以称之为顺序观念。
而周期用来定义现象发生
的节拍,也就是现象的重复性。
2. 时间和周期都有精确度的区别,计时一般按照秒,分,小时,天,周,月,季,年来划分,而周期一般按照振动次数划分,比如每秒100次,每分100次,每小时100次,等等。
3. 时间和周期是相互联系的,比如一个振动次数的频率为100次每秒,则其的周期时间应该是1/100秒。
同样,一个现象时间的频度为1/100秒,则其的周期次数应该是100次。
4. 时间和周期是客观物理现象的发展过程中必不可少的概念,它们不
仅约束着物理现象的发展方向,而且也使我们能够有效地观察和分析
物理现象。
5. 可以用实验证明,时间和周期是有一定关系的,当一个现象的发生
率达到特定的中止点时,其发生的频率也可以用特定的数值换算而得到。
改变物理现象的发生速度,也就能让其所处的环境产生相应的变化,从而影响到物理现象的发展。
6. 另外,相对于时间,周期主要是用来测量一个物理现象的重复性,
比如对流动的空气来说,它的周期可能是每小时一次、每天一次或每
季一次,而这个周期与时间息息相关,反映出物理现象客观存在的频
率和重复性。
7. 时间和周期共同支配着物理现象的进展,它能有效地帮助我们预测物理现象的发展过程,从而作出相应的调整,实现对物理现象的有效控制。
8. 总之,时间和周期都是客观物理现象观测和控制的关键要素,它们的互相协调关系极为重要,只有充分掌握这种关系,才有可能更好地把握物理现象的发展变化趋势。
节拍与周期

Takt Time生产节拍又称客户需求周期、产距时间,是指在一定时间长度内,总有效生产时间与客户需求数量的比值,是客户需求一件产品的市场必要时间。
节拍时间是20世纪30年代德国飞机制造工业中使用的一个生产管理工具。
(Takt是一个德语词汇,表示像音乐节拍器那样准确的间隔时间),指的是把飞机移动到下一个生产位置的时间间隔。
这个概念于20世纪50年代开始在丰田公司被广泛应用,并于60年代晚期推广到丰田公司所有的供应商。
丰田公司通常每个月评审一次节拍时间,每10天进行一次调整检查。
从生产节拍的定义可以看出,生产节拍与生产周期不同,生产节拍实际是一种目标时间,是随需求数量和需求期的有效工作时间变化而变化的,是人为制定的。
节拍反映的是需求对生产的调节,如果需求比较稳定,则所要求的的节拍也是比较稳定的,当需求发生变化时节拍也会随之发生变化,如需求减少时节拍就会变长,反之则变短。
生产周期则是生产效率的指标,比较稳定,是受到一定时期的设备加工能力、劳动力配置情况、工艺方法等因素影响决定的,只能通过管理和技术改进才能缩短。
对生产的调节控制 1.生产节拍对生产的作用首先体现在对生产的调节控制,通过节拍和生产周期的比较分析,在市场稳定的情况下,可以明确需要改进的环节,从而采取针对性的措施进行调整。
如当生产节拍大于生产周期时,生产能力相应过剩;如果按照实际生产能力安排生产就会造成生产过剩,导致大量中间产品积压,引起库存成本上升、场地使用紧张等问题。
如果按照生产节拍安排生产,就会导致设备闲置,劳动力等工等现象,造成生产能力浪费。
当生产节拍小于生产周期的情况下,生产能力不能满足生产需要,这时就会出现加班、提前安排生产、分段储存加大等问题。
因此,生产周期大于或小于生产节拍都会对生产造成不良影响。
生产管理改进的目的就是要尽可能地缩小生产周期和生产节拍的差距,通过二者的对比分析安排生产经营活动。
韩总在职代会报告中提出的建立标准生产周期的目的就是要通过不断的改进使生产周期与市场需要的生产节拍相适应,从而保证均衡有序的生产。
TT,CT及LT
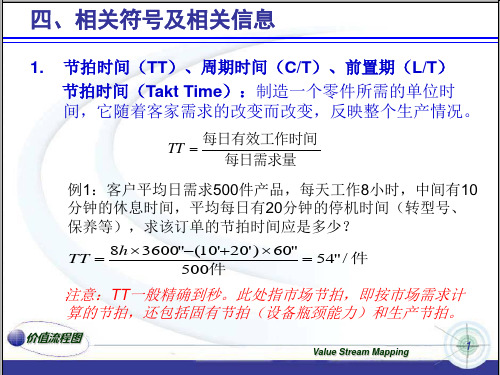
机器C/T=6个×5秒/个=30秒
人的C/T=5秒
价值流程图 工序的C/T=12秒+1秒+30秒+3秒=46秒
Value Stream Mapping
2
四、相关符号及相关信息
1. 节拍时间(TT)、周期时间(C/T)、前置期(L/T) 前置时间(Lead Time):指从定单发出到收到货物的整 个时间,由信息、生产、运输和等待四部分组成。
信息L/T指定单发出到供应商确认的时间。 生产L/T指从物料开始投入到第一个产品出产的时间。 运输L/T指物料在运输途中的时间。 等待L/T指所有物流和信息流停滞时间,包括库存、报关等 例3:定单发出到客户确认用时0.5天,客户生产用时0.5天, 生产中半产品及成品库存为3天,装卸货及运输用时1天, 报关及交付等待0.5天,则该货物的前置期是多长? L/T=0.5+0.5+1+(3+0.5)=5.5天
周期时间(Cycle Time):分为机器C/T,人的C/T和 工序的C/T。
机器C/T指机器加工完成一批(个)产品所需的时间。 人的C/T指人完成一个周期动作所需时间。
工序的C/T指该工序完成2个产品的间隔时间。
例2:某操作员用12秒将6个托盘夹具的产品放入机器的6个 加工头中(托盘夹具位),1秒按下开关,机器每5秒钟 流出1个托盘产品,操作员用3秒将每托盘新产品递给下 工序,问该机器、人、工序的C/T各是多少?
四、相关符号及相关信息
1. 节拍时间(TT)、周期时间(C/T)、前置期(L/T)
节拍时间(Takt Time):制造一个零件所需的单位时 间,它随着客家需求的改变而改变,反映整个生产情况。
每日有效工作时间 TT 每日需求量
精益生产术语中英文版

No Std Work means no Kaizen … Std Work is the Mother of all Kaizen 没有标准作业就没有改善„„标准作业是改善之母
5
How to start the Takt Time Calculation Based On Customer Demand 怎样根据客户需求计算节拍时间 • Step 1: Calculate Takt time Based on Customer Demand
Lean Hand Book 精益生产手册
1
Kaizen Workshop ETE (End to End) Goal 改善目标
Productivity Improvement 端到端(从头到尾)产能提高
Double the Good 好的加倍 Halve the Bad 坏的减半 Double the Speed 改善速度加倍 ETE Zero Defect (Quality, TPM, OEE & etc.) 端到端(从 头到尾)零缺陷(质量,全面生 产维护,全局设备利用率等) Defect : 缺陷降低90% Inventory : 库存减半 Productivity : 生产效率翻倍 Lead Time : 生产周期减半 Scrap : 报废降低90% Space : 面积减半
10
What is Standard WIP 什么是标准WIP The purpose of Standard WIP is: 标准WIP的目的:
1. Separation between machine job and man job 区分机器作业和手动作业 2. Ensures quality requirements 确保质量要求 3. Ensures smooth flow based on Takt time
301标准作业七步骤

步骤七:持续性
7 改善
MUDA = 浪费
增值
改善
目前状况 分析后 改善后
标准作业总结
流程是可重复的,可以一步一步照做, 被观察和记录的;
可靠性是标准作业的关键;
4 布局
一个好的流程是值得文件化, 得到 大家一致意见作为标准。 (没有文件就没有标准)
流程
1
节拍 3
作业平衡
2 作业序列 4
标准
▪ 问题很难诊断因为过程差异
标准作业
▪所有班次完成任务的时间和方法一致 ▪标准培训方法 ▪品质和安全内建 ▪问题很容易诊断 ▪偏差和改善可以按目标衡量 ▪能够平衡流程以满足客户要求
传统的工作方法
递送数量
递送冰激凌
最迟送货时间
最早送货时间
Of 13 deliveries only 4 were on target(13 次送货有4次达标)
▪要素时间 (基本动作时间)
▪完成人工作业时间内的某一要素所需的时间
▪总周期时间 (总操作时间)
▪一个产品所有的人工作业时间的总和
▪目标周期时间 (目标操作时间)
▪和节拍时间类似,但在总生产时间中减掉机器的效率损失和换型时间
步骤二回顾
1 流程
2 节拍时间
从前两步骤我们研究了两个标准作业的重要环节:
Bridgend Engine Plant
Daily Load Lorry
为什么要用流程图?
记录实际流程 显示流程步骤之间关系 识别不良品位置 确定流程中增值与非增值步骤 引导下一步改善. 沟通信息 培训员工流程知识
细节流程图可以用于任何流程,并且是一种实时更新的文件
流程版本
你认为是这样…
生产节拍计算例题

生产节拍计算例题含解答
生产节拍计算通常涉及到生产线上的生产速度、生产周期等参数。
以下是一个简单的例题和解答,假设我们有一个生产线,每小时能够生产一定数量的产品。
我们来计算一下生产节拍。
例题:
假设一条生产线每小时能够生产100个产品,而整个生产流程包括生产、检验、包装等环节,总共需要4个小时完成一个产品的生产周期。
请计算该生产线的生产节拍。
解答:
生产节拍是指每个产品从生产开始到下一个产品开始生产的时间间隔。
它可以通过生产周期和单位时间内的生产数量来计算。
生产节拍= 生产周期/ 单位时间内的生产数量
在这个例子中,生产周期是4小时,单位时间内的生产数量是每小时100个产品。
生产节拍= 4小时/ 100产品/小时= 0.04小时/产品
因此,该生产线的生产节拍为0.04小时/产品。
这表示每个产品的生产时间间隔为0.04小时,或者说每隔0.04小时就可以开始下一个产品的生产。
请注意,实际的生产节拍可能会受到生产线调整、故障维修等因素的影响,因此这只是一个简单的计算示例。
在实际应用中,需要综合考虑多种因素来确定最佳的生产节拍。
OEE的计算公式

OEE是一个独立的测量工具,它用来表现实际的生产能力相对于理论产能的比率。
国际上对OEE的定义为:OEE是Overall Equipment Effectiveness(全局设备效率)的缩写,它由可用率(Availability time),表现性(Performance)以及质量指数(Quality)三个关键要素组成。
OEE的计算公式(不考虑设备加工周期的差异)=?OEE= 时间开动率×性能开动率×合格品率[1],[4]其中,时间开动率 = 开动时间/负荷时间而,负荷时间 = 日历工作时间-计划停机时间开动时间 = 负荷时间–故障停机时间–设备调整初始化时间(包括更换产品规格、更换工装模具、更换刀具等活动所用时间)性能开动率 = 净开动率×速度开动率而,净开动率 = 加工数量×实际加工周期/开动时间速度开动率 = 理论加工周期/实际加工周期合格品率 = 合格品数量/ 加工数量在OEE公式里,时间开动率反映了设备的时间利用情况;性能开动率反映了设备的性能发挥情况;而合格品率则反映了设备的有效工作情况。
反过来,时间开动率度量了设备的故障、调整等项停机损失,性能开动率度量了设备短暂停机、空转、速度降低等项性能损失;合格品率度量了设备加工废品损失。
例1: 设某设备1天工作时间为8h, 班前计划停机20min, 故障停机20min, 更换产品型号设备调整40min, 产品的理论加工周期为0.5min/件, 实际加工周期为0.8min/件, 一天共加工产品400件, 有8件废品, 求这台设备的OEE。
计算:负荷时间 = 480-20 = 460 min开动时间 = 460 – 20 – 40 = 400 min时间开动率 = 400/460 = 87%速度开动率 = 0.5/0.8 = 62.5%净开动率 = 400×0.8/400 = 80%性能开动率 = 62.5%×80% = 50%合格品率 = (400-8)/400 = 98%于是得到 OEE = 87%×50%×98% = 42.6%。
设备OEE计算方法

设备OEE计算方法(Overall Equipment Effectiveness), 即设备综合效率,其本质就是设备负荷时间内实际产量与理论产量的比值。
企业在进行OEE计算时常常遇到很多迷惑的问题,如工厂停水、停电、停气、停汽使设备不能工作,等待定单、等待排产计划、等待检查、等待上一道工序造成的停机,不知如何计算。
本文引入非设备因素停机的概念,修改了OEE的算法,使计算得到的OEE更能够真实反映设备维护的实际状况,让设备完全利用的情况由完全有效生产率这个指标来反映。
本文同时介绍了在不同情况下如何分析设备损失的PM分析流程。
1、 OEE表述和计算实例OEE= 时间开动率×性能开动率×合格品率其中,时间开动率 = 开动时间/负荷时间而,负荷时间 = 日历工作时间-计划停机时间开动时间 = 负荷时间–故障停机时间–设备调整初始化时间性能开动率 = 净开动率×速度开动率而,净开动率 = 加工数量×实际加工周期/开动时间速度开动率 = 理论加工周期/实际加工周期合格品率 = 合格品数量/ 加工数量在OEE公式里,时间开动率反映了设备的时间利用情况;性能开动率反映了设备的性能发挥情况;而合格品率则反映了设备的有效工作情况。
反过来,时间开动率度量了设备的故障、调整等项停机损失,性能开动率度量了设备短暂停机、空转、速度降低等项性能损失;合格品率度量了设备加工废品损失。
OEE还有另一种表述方法,更适用于流动生产线的评估, 即OEE= 时间开动率×性能开动率×合格品率而,时间开动率 = 开动时间/计划利用时间而,计划利用时间 = 日历工作时间-计划停机时间开动时间 = 计划利用时间–非计划停机时间性能开动率 = 完成的节拍数/计划节拍数其中,计划节拍数 = 开动时间/标准节拍时间合格品率 = 合格品数量/加工数量这与前述的OEE公式实际上是同一的。
计算:停机时间 = 115+12 = 127 min计划开动时间 = 910 – 127 = 783 min时间开动率 = 783/910 = 86%计划节拍数 = 开动时间/标准节拍时间 = 783/3 = 261性能开动率 = 203/261 = 77.7%合格品率 = 一次合格品数/完成产品数 = 152/203 = 74.9%于是得到 OEE = 86% ×77.7%×74.9% = 50%2、 OEE的实质如果追究OEE的本质内涵,其实就是计算周期内用于加工的理论时间和负荷时间的百分比。
301标准作业七步骤

Bridgend Engine Plant
Daily Load Lorry
为什么要用流程图?
记录实际流程 显示流程步骤之间关系 识别不良品位置 确定流程中增值与非增值步骤 引导下一步改善. 沟通信息 培训员工流程知识
细节流程图可以用于任何流程,并且是一种实时更新的文件
流程版本
你认为是这样…
标准作业
可预见的,规则的结果…包含可接受的偏差 递送冰激凌
最迟送货时间 最早送货时间
递送数量
标准作业的目标
标准作业想达到的结果是如下流程
可重复
可靠的
有能力
这也提供了持续改善的基础
标准作业模型
1-5 按顺序显示如何 建立标准作业
4 布局
必须充分理解每一步 才能走到下一步
流程
1
节拍 3
作业平衡
2 作业序列 4
Despatch Office
Books load, phone PMC A/N & T.No.
PMC
Update Darwin With delivery details
Despatch Office Print packing list
Despatch Office Pr源自nt despatch label
= 安全警示
步骤四:布局
4 布局
动作经济性要考虑以下因素:
▪ 减少动作数量 ▪ 双手操作 ▪ 减少移动距离 ▪ 使动作更容易
拆分工作顺序,利用合并表可以给出改进方向
步骤四:布局
Layout example
步骤五:标准作业指导书
4 布局
作业序列 4
标准
5
作业书
当对操作业序列和布局图达成了一致后: 即制作标准作业书和标准布局; 没有记录性的文件就没有标准。
- 1、下载文档前请自行甄别文档内容的完整性,平台不提供额外的编辑、内容补充、找答案等附加服务。
- 2、"仅部分预览"的文档,不可在线预览部分如存在完整性等问题,可反馈申请退款(可完整预览的文档不适用该条件!)。
- 3、如文档侵犯您的权益,请联系客服反馈,我们会尽快为您处理(人工客服工作时间:9:00-18:30)。
周期时间与节拍时间之间的计算
为了与节拍时间进行比较合确定完成操作或工序所需要的工人数量。
确定标准化操作需要的周期时间。
实施者:
熟悉相关操作或者工序的任何人都可以确定周期时间。
实施时间:
15分钟到30分钟,具体时间取决于工序的复杂程度。
周期时间的含义:
周期时间是完成任务所需要的时间。
不应将周期时间与节拍时间相混淆,周期时间表示工序的速率。
周期时间:
可以清楚地了解需要多少操作者(条件是知道节拍时间)在标准化操作组合表中应得到使用,为了在整个节拍时间充分地利用操作者,可以将几个周期与一个操作者结合起来有两种类型的周期时间:
1.个别周期时间——个别操作的完成速率:例如,包装或者焊接。
2.总周期时间——操作工序的完成速率。
通过在一个确定的工序中将所有的个别周期时间相加,可以计算出总周期时间。
根据周期时间计算作业员人数:
1、通过将个别操作中的所有任务相加,可以获得操作者周期时间。
2、将操作者的周期时间相加,获得总周期时间(TCT)。
3、计算节拍时间。
记住,通过用可用的生产时间除以每日所需要的总数量,您就可以计算出节拍时间。
(参阅节拍时间)
4、通过用总周期时间除以节拍时间。
您就可以得到完成任务所需要的工人总数。
要点
·确定生产线所需要工人的最佳数量被称为平衡生产线。
通过这一步骤,您可以在所有操作者之间分配工作要素。
·当确定所需要的最佳数量的工人时:如果小数大于0.5,就进上去如果小数小于0.5,就舍
掉利用改善尽可能地减少周期时间。