常用无损检测方法的能力范围和局限性
无损检测技术的原理及优缺点

无损检测技术的原理及优缺点本文介绍当前常规无损检测技术:包括射线、超声波、磁粉、渗透、TOFD等技术,并对各项检测技术的工作原理、优缺点进行论述。
无损检测定义:在不损检测对象的前提下,以物理或化学方法为手段,借助先进的技术和设备器材,对检测对象的内部及表面的结构、性质或状态进行检查和测试,并对其结果进行分析和评价。
随着现代工业的发展,对产品质量和结构安全性,使用的可靠性提出了越来越高的要求。
作为一种有效的检测手段,无损检测在我国已广泛应用于经济建设的各个领域,例如特种设备的制造和在用检验、机械、石化化工,航空航天,船舶,电力,核工业等,尤其是在保证承压类设备产品质量和使用安全方面,无损检测技术显得特别重要。
关键字:无损检测技术原理优缺点1.射线检测技术的原理:射线在穿透物体过程中会与物质发生相互作用,因吸收和散射而使强度减弱,强度减弱的程度取决于物质的衰减系数和射线在物质中穿越厚度。
如果被检试件的局部存在缺陷,构成缺陷物质的衰减系数又不同于试件,那么缺陷处透过射线强度就会与周围产生差异,把胶片放在适当位置使其在透过射线的作用下感光,经暗室处理得到底片。
射线检测技术的优点和局限性:1)、检测结果有直接记录-----------底片。
2)、可以获得缺陷的投影图像,缺陷定性定量比较准确。
3)、体积型缺陷检出率很高,而面积型缺陷的检出率受到多种因素影响。
4)、适宜检验较薄的工件而不适宜较厚的工件。
5)适宜检测对接焊缝,检测角焊缝效果较差,不适宜检测板材、棒材、锻件。
6)有些试件结构和现场条件不适合射线照相。
7)对缺陷在工件中厚度方向的位置及缺陷自身高度的确定比较困难。
8)射线照相检测速度慢,成本比较高且有辐射对人体有伤害。
1.超声波检测技术的原理:声源产生的脉冲波进入到工件中,超声波在工件中以一定方向和速度向前方传播,遇到两侧声阻抗有差异的界面时,部分声波被反射,检测设备接收和显示,分析声波幅度和位置等信息,评估缺陷是否存在或存在缺陷的大小、位置等。
浅析各种无损检测技术的优缺点
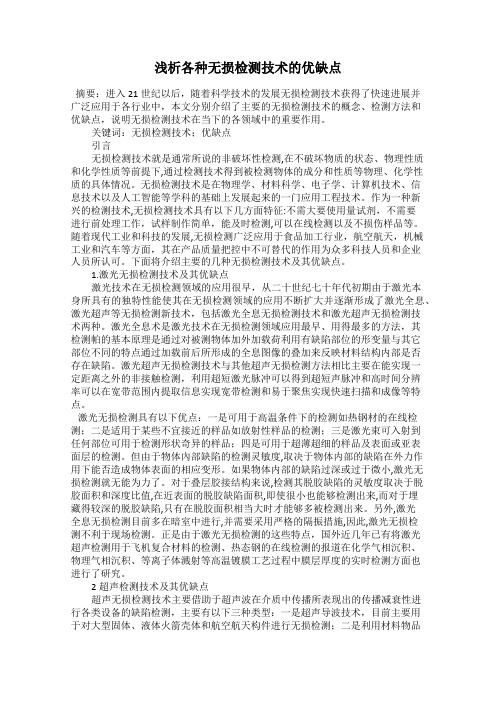
浅析各种无损检测技术的优缺点摘要:进入21世纪以后,随着科学技术的发展无损检测技术获得了快速进展并广泛应用于各行业中,本文分别介绍了主要的无损检测技术的概念、检测方法和优缺点,说明无损检测技术在当下的各领域中的重要作用。
关键词:无损检测技术;优缺点引言无损检测技术就是通常所说的非破坏性检测,在不破坏物质的状态、物理性质和化学性质等前提下,通过检测技术得到被检测物体的成分和性质等物理、化学性质的具体情况。
无损检测技术是在物理学、材料科学、电子学、计算机技术、信息技术以及人工智能等学科的基础上发展起来的一门应用工程技术。
作为一种新兴的检测技术,无损检测技术具有以下几方面特征:不需大要使用量试剂,不需要进行前处理工作,试样制作简单,能及时检测,可以在线检测以及不损伤样品等。
随着现代工业和科技的发展,无损检测广泛应用于食品加工行业,航空航天,机械工业和汽车等方面,其在产品质量把控中不可替代的作用为众多科技人员和企业人员所认可。
下面将介绍主要的几种无损检测技术及其优缺点。
1.激光无损检测技术及其优缺点激光技术在无损检测领域的应用很早,从二十世纪七十年代初期由于激光本身所具有的独特性能使其在无损检测领域的应用不断扩大并逐渐形成了激光全息、激光超声等无损检测新技术,包括激光全息无损检测技术和激光超声无损检测技术两种。
激光全息术是激光技术在无损检测领域应用最早、用得最多的方法,其检测帕的基本原理是通过对被测物体加外加载荷利用有缺陷部位的形变量与其它部位不同的特点通过加载前后所形成的全息图像的叠加来反映材料结构内部是否存在缺陷。
激光超声无损检测技术与其他超声无损检测方法相比主要在能实现一定距离之外的非接触检测,利用超短激光脉冲可以得到超短声脉冲和高时间分辨率可以在宽带范围内提取信息实现宽带检测和易于聚焦实现快速扫描和成像等特点。
激光无损检测具有以下优点:一是可用于高温条件下的检测如热钢材的在线检测;二是适用于某些不宜接近的样品如放射性样品的检测;三是激光束可入射到任何部位可用于检测形状奇异的样品;四是可用于超薄超细的样品及表面或亚表面层的检测。
RQ-1无损检测基础知识

RQ-1⽆损检测基础知识⽆损检测基础知识⼀、常⽤⽆损检测⽅法的基本原理1.概述⽆损检测的定义:⽆损检测是指在不损坏试件的前提下,以物理或化学⽅法为⼿段,借助先进的技术和设备器材,对试件的内部及表⾯的结构,性质,状态进⾏检查和测试的⽅法。
常⽤的⽆损检测⽅法有射线检测(简称RT)、超声检测(简称UT)、磁粉检测(简称MT)、渗透检测(简称PT)。
这四种⽅法是承压类特种设备制造质量检验和在⽤检验最常⽤的⽆损检测⽅法。
其中RT和UT主要⽤于探测试件内部缺陷,MT和PT主要⽤于探测试件表⾯缺陷。
其他⽤于承压类特种设备的⽆损检测⽅法有涡流检测(ECT)、声发射检测(AE)、衍射时差法超声检测(TOFD)、X射线数字成像检测(DR)等1.1 ⽆损检测⽬的及应⽤特点(1)⽆损检测⽬的①保证产品质量②保障使⽤安全③改进制造⼯艺④降低⽣产成本(2)⽆损检测应⽤特点①⽆损检测要与破坏性检测相配合②正确选⽤实施⽆损检测的时机③选⽤最适当的⽆损检测⽅法④综合应⽤各种⽆损检测⽅法1.2 ⽆损检测技术的发展阶段第⼀阶段称为⽆损探伤(NDI)。
其主要作⽤就是在不损伤材料和设备产品的前提下,检出内、外部缺陷,以满⾜设备⼯程设计的强度要求,这是⽆损检测技术发展的初级阶段,其主要特征是以质量控制为中⼼。
第⼆阶段称为⽆损检测(NDT)。
对于⼯业发达国家来说,该阶段始于上个世纪70年代,其任务不仅是检测设备产品的内外部缺陷,⽽且测定材料和焊缝的组织结构,如晶粒度、⽯墨形态、⾦相组织、硬度和残余应⼒⽔平;同时还测定各种过⼯艺参数诸如温度、压⼒、粘度和密度等。
这时的⽆损检测技术表现为系统性质量控制概念,远⽐第⼀阶段具有更为丰富的内涵。
第三阶段称为⽆损评价(NDE)。
由于设计⽔平的不断提⾼,断裂⼒学等学科技术的发展和推⼴,以及极限设计寿命思想的进步和实⽤化,因此要求⽆损检测技术不仅能检出危险缺陷,⽽且要对缺陷进⾏定性,并测定其⾃⾝⾼度(通常指壁厚⽅向的尺⼨),以便采⽤断裂⼒学对带缺陷设备的安全性和使⽤寿命进⾏评价。
各种无损检测技术的优缺点分析

各种无损检测技术的优缺点分析发布时间:2021-06-01T01:53:57.948Z 来源:《中国电业》(发电)》2021年第4期作者:房爱伟[导读] 不同方法的特点以及应用范围有所不同。
工程人员需参照实际,深度掌握各检测技术的性能特征,并结合检测的对象和检测的要求灵活选择无损检测技术。
国网新源控股有限公司检修分公司 100053摘要:无损检测是基于不损坏检测对象结构和性能,检测被检测对象表面及内部结构的方法。
无损检测的方法较多,不同方法的特点以及应用范围有所不同。
工程人员需参照实际,深度掌握各检测技术的性能特征,并结合检测的对象和检测的要求灵活选择无损检测技术。
关键词:种无损检测技术;分类和应用;优缺点分析一、无损检测方法的分类及应用(一)射线射线检测技术主要是指使用射线检测零件内部与外部性能的方法。
该技术是利用不同射线穿透性和衰减程度的差异,将其投射于零件表面,以密度和厚度的差异完成检测的方式。
如检测物质密度较大,部分射线的吸收量较大,出现了较为显著的筛衰减现象。
而射线穿透空气时,空气吸收量明显减少,此时观察底片时会发现底片的光感程度较为明显。
通过底片的光感度判断物体内部是否存在质量问题,也可结合感光程度确定缺陷的程度和位置。
射线检测技术在体积性缺陷检测中十分常见。
(二)超声超声检测利用超声波震动和介质传播,可从多个方向收集能量,收集穿透于介质之中的震动,将震动转变为声波,声波在介质面中发生折射或反射等多种物理现象,检测零件是否存在损伤。
在工业检测中,检测用超声波频率主要在0.4-25兆赫兹之间。
精细材料及高敏感度材料主要以高频率声波检测,粗糙、衰减明显的材料则以低频率声波检测。
(三)渗透渗透探伤是利用毛细现象来检查材料表面是否存在明显缺陷的一种无损检验方式。
上世纪初期,主要利用具备渗透能力的煤油检查机车零件裂缝问题,上世纪40年代初期美国则发明一种更为先进的荧光渗透液。
液体渗透检测主要用来检查工件或材料表面缺陷,打破了材料磁性的限制,相较于磁粉探伤应用更为广泛。
对常规无损检测方法选择的分析
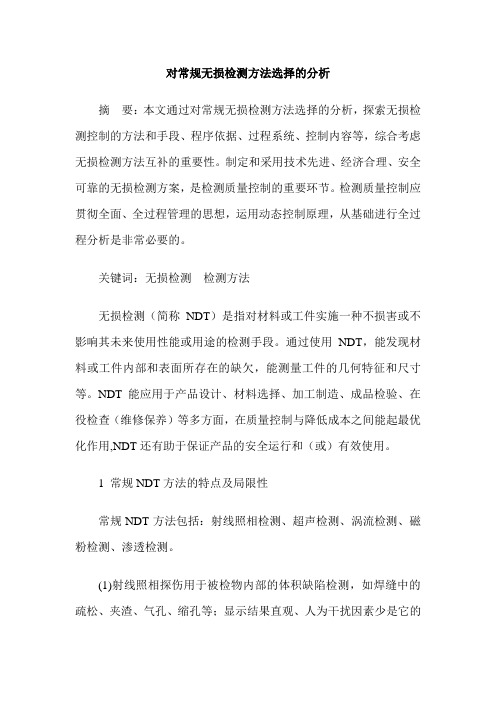
对常规无损检测方法选择的分析摘要:本文通过对常规无损检测方法选择的分析,探索无损检测控制的方法和手段、程序依据、过程系统、控制内容等,综合考虑无损检测方法互补的重要性。
制定和采用技术先进、经济合理、安全可靠的无损检测方案,是检测质量控制的重要环节。
检测质量控制应贯彻全面、全过程管理的思想,运用动态控制原理,从基础进行全过程分析是非常必要的。
关键词:无损检测检测方法无损检测(简称NDT)是指对材料或工件实施一种不损害或不影响其未来使用性能或用途的检测手段。
通过使用NDT,能发现材料或工件内部和表面所存在的缺欠,能测量工件的几何特征和尺寸等。
NDT能应用于产品设计、材料选择、加工制造、成品检验、在役检查(维修保养)等多方面,在质量控制与降低成本之间能起最优化作用,NDT还有助于保证产品的安全运行和(或)有效使用。
1 常规NDT方法的特点及局限性常规NDT方法包括:射线照相检测、超声检测、涡流检测、磁粉检测、渗透检测。
(1)射线照相探伤用于被检物内部的体积缺陷检测,如焊缝中的疏松、夹渣、气孔、缩孔等;显示结果直观、人为干扰因素少是它的主要优点,探伤对象基本不受零件材料、形状、外廓尺寸的限制;主要局限是:三维结构二维成像,前后缺陷重叠;射线束夹角与被检裂纹取向不宜超过10°。
(2)超声探伤适用于被检物内部的面积型缺陷,如锻件中的裂纹、白点、分层和焊缝中的未融合等。
主要优点是能定位缺陷的相对尺寸和坐标位置;适用焊缝、管材、板材等多种材料与制件的检测;检测大厚度件的能力超出其它方法;并且可携设备现场操作。
但用纵波脉冲反射法对近表面与表面缺陷检测存在盲区;检测复杂形状的试件可实施性影响较大;操作者需具备有较丰富的实践经验。
(3)磁粉探伤可发现的主要缺陷有:各种裂纹、夹杂、夹渣、折叠、白点、分层、气孔、未焊透、疏松、冷隔等。
主要能确定缺陷在被检物表面的形状、大小和位置,磁粉探伤机性能安全可靠,易于操作、对小开口至微米级的裂纹检测灵敏度高。
常规无损检测技术优缺点分析

常规无损检测技术优缺点分析无损检测是指在不损害或不影响被检测对象使用性能,不伤害被检测对象内部组织的前提下,利用材料内部结构异常或缺陷存在引起的热、声、光、电、磁等反应的变化,以物理或化学方法为手段,借助现代化的技术和设备器材,对试件内部及表面的结构、性质、状态及缺陷的类型、性质、数量、形状、位置、尺寸、分布及其变化进行检查和测试的方法[1]。
目前应用较为广泛的无损检测技术主要有渗透检测(PT)、磁粉检测(MT)、射线检验(RT)、涡流检测(ET)、漏磁检测(MFT)等。
1、渗透检测(PT)渗透检测(PT)是检测非孔隙固体材料中表面不连续性的最广泛使用的无损检测方法之一,可用于磁性材料和非磁性材料的检测。
其主要的工作原理是:通过对工件表面施涂含有荧光染料或着色染料(渗透剂),渗透剂利用毛细作用渗入表面开口缺陷中;去除工件表面多余的渗透剂,经干燥后,再在工件表面施涂吸附介质(显像剂);同样在毛细作用下,显像剂将吸出缺陷中的渗透剂,即渗透剂回渗到显像剂中;在一定的光源下(黑光或白光),缺陷处的渗透剂痕迹被显示(黄绿色荧光或鲜艳红色),从而探测出缺陷的形貌及分布状态。
这种方法的主要优点是:可检出表面裂纹、针孔、折叠、缝隙、泄漏等表面开口缺陷。
主要缺点是:需对表面进行细致的清洗和去污,而且只能检出表面上的开口缺陷;浅的擦伤和污迹将会形成假指示;无法显示不连续的深度;使用的渗透剂和显像剂有毒。
2、磁粉检测(MT)磁粉检测(MT)主要用于检测铁磁性构件与结构表面或近表面的线性不连续性。
磁粉检测遵循磁学规律,仅对铁磁性材料有效。
其主要工作原理是:铁磁性材料工件被磁化后,由于不连续性的存在,使工件表面和近表面的磁感应线发生局部畸变而产生漏磁场,吸附施加在工件表面的磁粉,在合适的光照下形成目视可见的磁痕,从而显示出不连续性的位置、大小、形状和严重程度,不连续性处漏磁场分布。
这种方法的主要优点是:能检测出缺陷的位置和表面的长度、操作简便、直观、灵敏度高,而且检测成本较低。
介绍几种常见的无损检测技术及其优缺点

介绍几种常见的无损检测技术及其优缺点无损检测技术是一种非破坏性检测方法,可用于检测工件内部和表面缺陷,而无需破坏工件的结构完整性。
它在工业、航空航天、汽车、建筑等领域广泛应用,以确保产品质量和安全性。
以下是几种常见的无损检测技术及其优缺点的介绍。
1. 超声波检测(Ultrasonic Testing):超声波检测是一种利用超声波传播和反射原理检测和评估材料内部缺陷的技术。
它通过发送超声波脉冲到被测物体,根据超声波在材料中传播的速度和反射情况来确定缺陷的位置和形状。
优点包括高灵敏度、无损伤、能检测小缺陷和定位准确。
缺点是对材料的声波传播特性敏感,受材料密度和纹理等因素影响。
2. 磁粉检测(Magnetic Particle Testing):磁粉检测是一种利用磁场和铁磁材料的磁性特性检测表面和近表面缺陷的方法。
它通过在被检测物体表面施加磁场,并在其上涂敷磁性颗粒,当有磁场漏磁或磁场被打断时,磁性颗粒会聚集在缺陷处,从而可视化缺陷的位置和形态。
优点包括简单易行、高灵敏度、能检测细小缺陷和形状多样化。
缺点是只能检测铁磁材料,灵敏度受表面状态和磁场均匀性影响。
3. 射线检测(Radiographic Testing):射线检测是一种利用X射线或γ射线穿透物体并投射到感光介质上的方法,从而检测物体内部缺陷的技术。
它通过感光介质上的黑化程度来评估缺陷的大小和位置。
优点包括能检测较深的缺陷,适用于各种材料。
缺点是设备昂贵,对操作人员和环境安全要求高。
4. 渗透检测(Dye Penetrant Testing):渗透检测是一种利用润湿性液体浸渍到表面开裂或孔隙处,然后涂覆上显色剂来检测这些表面缺陷的方法。
它通过液体的渗透和表面张力效应来展现缺陷的位置和形状。
优点包括简单易行、能够检测各种材料和形状的缺陷。
缺点是只能检测表面缺陷,对材料的清洁要求高。
5. 热红外检测(Thermal/Infrared Testing):热红外检测是一种利用热辐射和红外辐射原理检测表面和内部缺陷的技术。
无损检测方法总结

常用的无损检测方法无损检测方法很多,据美国国家宇航局调研分析,其认为可分为六大类约70余种。
但在实际应用中比较常见的有以下五种,也就是我们所说的常规的无损检测方法:一、常规无损检测方法目视检测 Visual Testing (缩写 VT);超声检测 Ultrasonic Testing(缩写 UT);射线检测 Radiographic Testing(缩写 RT);磁粉检测 Magnetic particle Testing(缩写 MT);渗透检测 Penetrant Testing (缩写 PT);涡流检测 Eddy Current Testing (缩写 ET);声发射 Acoustic emission (缩写 AE)。
1、目视检测(VT)目视检测,是国内实施的比较少,但在国际上非常重视的无损检测第一阶段首要方法。
按照国际惯例,目视检测要先做,以确认不会影响后面的检验,再接着做四大常规检验。
例如BINDT的PCN认证,就有专门的VT1、2、3级考核,更有专门的持证要求。
经过国际级的培训,其VT检测技术会比较专业,而且很受国际机构的重视。
VT常常用于目视检查焊缝,焊缝本身有工艺评定标准,都是可以通过目测和直接测量尺寸来做初步检验,发现咬边等不合格的外观缺陷,就要先打磨或者修整,之后才做其他深入的仪器检测。
例如焊接件表面和铸件表面较多VT做的比较多,而锻件就很少,并且其检查标准是基本相符的。
2、射线照相法(RT)是指用X射线或g射线穿透试件,以胶片作为记录信息的器材的无损检测方法,该方法是最基本的,应用最广泛的一种非破坏性检验方法。
1、射线照相检验法的原理:射线能穿透肉眼无法穿透的物质使胶片感光,当X射线或r射线照射胶片时,与普通光线一样,能使胶片乳剂层中的卤化银产生潜影,由于不同密度的物质对射线的吸收系数不同,照射到胶片各处的射线能量也就会产生差异,便可根据暗室处理后的底片各处黑度差来判别缺陷。
无损检测技术优势与局限性分析

无损检测技术优势与局限性分析无损检测技术,即利用某种方法和设备对被测对象进行检测和评价,而无需破坏或影响被测对象的完整性和可用性。
这种技术在工业生产、产品质量监控以及安全评估方面起到了至关重要的作用。
本文将对无损检测技术的优势和局限性进行分析。
首先,无损检测技术具有许多显著的优势。
其一是非破坏性。
与传统的有损检测方法相比,无损检测技术不会破坏被测对象的完整性。
这意味着无损检测技术可以在不影响产品正常使用的情况下进行检测,大大减少了检测对被测对象的影响。
其二是高效性。
无损检测技术采用了先进的仪器设备和信号处理技术,能够快速、准确地评估被测对象的质量和可靠性。
这不仅提高了检测效率,还降低了人工操作的错误率。
其三是适用性广泛。
无损检测技术可以应用于金属、陶瓷、塑料、复合材料等各种材料的检测,适用于不同形状、不同尺寸的被测对象,具有很高的适应性。
然而,无损检测技术也存在一些局限性。
首先是设备成本高。
无损检测技术需要使用先进的仪器设备,这些设备的研发和购买成本较高,对于一些小型企业或发展中国家来说可能难以承担。
其次是操作技术要求高。
虽然无损检测设备已经越来越智能化,但其操作仍需要具备一定的专业知识和技能。
严格的操作要求使得无损检测技术的推广应用受到了一定的限制。
此外,无损检测技术在某些情况下可能无法提供完全准确的结果。
例如,对于一些隐蔽部位或复杂结构的被测对象,无损检测技术的能力可能受到限制,无法完全发现和评估隐藏的缺陷。
然而,针对这些局限性,无损检测技术也在不断发展和改进。
首先,随着科技的不断进步,无损检测设备的成本正在逐渐降低。
新型材料和技术的应用也为无损检测技术提供了更为经济、高效的解决方案。
其次,操作技术的要求也在不断降低,许多无损检测设备通过智能化系统提供操作指导和分析报告,使得操作更加简单和易于掌握。
此外,无损检测技术也借鉴了其他相关领域的技术,如人工智能和大数据分析等,进一步提高了检测精度和准确性。
常规无损检测技术的特点和适用范围
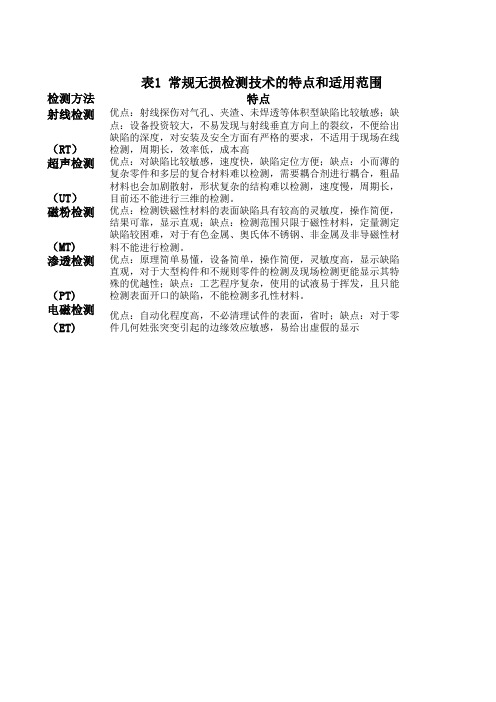
检测方法特点
射线检测(RT)优点:射线探伤对气孔、夹渣、未焊透等体积型缺陷比较敏感;缺点:设备投资较大,不易发现与射线垂直方向上的裂纹,不便给出缺陷的深度,对安装及安全方面有严格的要求,不适用于现场在线检测,周期长,效率低,成本高
超声检测(UT)优点:对缺陷比较敏感,速度快,缺陷定位方便;缺点:小而薄的复杂零件和多层的复合材料难以检测,需要耦合剂进行耦合,粗晶材料也会加剧散射,形状复杂的结构难以检测,速度慢,周期长,目前还不能进行三维的检测。
磁粉检测(MT)优点:检测铁磁性材料的表面缺陷具有较高的灵敏度,操作简便,结果可靠,显示直观;缺点:检测范围只限于磁性材料,定量测定缺陷较困难,对于有色金属、奥氏体不锈钢、非金属及非导磁性材料不能进行检测。
渗透检测(PT)优点:原理简单易懂,设备简单,操作简便,灵敏度高,显示缺陷直观,对于大型构件和不规则零件的检测及现场检测更能显示其特殊的优越性;缺点:工艺程序复杂,使用的试液易于挥发,且只能检测表面开口的缺陷,不能检测多孔性材料。
电磁检测(ET)优点:自动化程度高,不必清理试件的表面,省时;缺点:对于零件几何姓张突变引起的边缘效应敏感,易给出虚假的显示表1 常规无损检测技术的特点和适用范围
适用范围
铸件、焊接件、非金属制品和复合材料
锻件、焊接件、胶接街头及非金属材料
表面和近表面缺陷的无损检测
表面开口缺陷检测,适用于各种非疏松材质
导电材料。
如何选择适合的无损检测技术方法

如何选择适合的无损检测技术方法无损检测技术方法是一种使用非破坏性的手段来评估材料、构造或设备的完整性和性能的方法。
它适用于各种行业,如航空航天、汽车、能源、建筑等,可以帮助我们发现潜在的结构缺陷,避免事故的发生。
然而,在选择适合的无损检测技术方法时,我们需要考虑以下几个方面。
首先,我们需要了解不同的无损检测技术方法及其原理。
目前常用的无损检测技术方法包括超声波检测(UT)、磁粉检测(MT)、涡流检测(ET)、射线检测(RT)和热红外检测(IRT)等。
每种技术方法都有自己的优缺点和适用范围。
超声波检测适用于对材料内部缺陷的检测,包括裂纹、气孔等;磁粉检测主要用于检测金属表面的缺陷,如裂纹和疲劳裂纹;涡流检测主要用于检测导电材料中的缺陷;射线检测适用于对密集材料中的缺陷进行检测;热红外检测可以检测热辐射的分布情况,从而推测材料内部的状况。
因此,在选择适合的无损检测技术方法时,需要根据具体的检测对象和要求来进行选择。
其次,我们还需要考虑无损检测技术方法的应用范围和限制。
不同的无损检测技术方法在应用范围上有所差异。
例如,超声波检测适用于大多数材料和构造的测试,但不适用于非导电材料;磁粉检测主要适用于表面检测,不适用于非磁性材料。
此外,每种技术方法还存在一些局限性,比如无法检测非表面和非平行缺陷、对检测环境有一定的要求等。
因此,在选择适合的无损检测技术方法时,我们需要综合考虑其应用范围和限制,并根据实际情况进行选择。
另外,我们还需要考虑无损检测技术方法的准确性和可重复性。
无损检测技术方法的准确性和可重复性是评估其可靠性的重要指标。
在使用无损检测技术方法之前,我们需要了解该方法的准确性和可重复性,并确保其能够满足我们的检测要求。
同时,我们还需要了解无损检测技术方法的误差范围,并根据具体的情况进行误差控制和数据分析。
最后,我们还需要考虑无损检测技术方法的成本和时间要求。
不同的无损检测技术方法在成本和时间上也有所差异。
无损检测技术的优势与局限性全面解读

无损检测技术的优势与局限性全面解读无损检测技术(Non-Destructive Testing,NDT)是一种非破坏性的材料或组件检验方法,其主要目的是在不影响被检测物体完整性的情况下,获取关于其内部结构、缺陷和性能的信息。
这种技术被广泛应用于各行业,包括航空航天、汽车、能源和建筑等领域。
本文将对无损检测技术的优势和局限性进行全面解读。
无损检测技术的优势主要表现在以下几个方面:首先,无损检测技术能实现对被检测物体的非破坏性检验。
相比于传统的破坏性检测方法,无损检测技术能够保持被检测物体的完整性,避免了不必要的材料损失和生产成本的增加。
这种方法具有很高的经济效益和质量控制价值。
其次,无损检测技术可以实现对多种材料的检测。
无损检测技术可以适用于各种材料,包括金属、塑料、陶瓷和复合材料等。
无论是有机材料还是无机材料,无损检测技术都能够提供准确可靠的检测结果。
第三,无损检测技术具有快速高效的特点。
相比起传统的破坏性检测方法,无损检测技术能够快速地检测出材料或组件的缺陷,并提供及时的解决方案。
这种快速高效的特点使得生产过程更加流畅,极大地提高了生产效率。
此外,无损检测技术还能够实现对大型和复杂结构的检测。
对于一些大型和复杂的结构,如桥梁、飞机和核电站等,传统的破坏性检测方法往往是不可行的,而无损检测技术则能够轻松应对这些挑战。
通过无损检测技术,工程师可以在不破坏结构的情况下,对其进行全面的检测和评估。
尽管无损检测技术有着诸多的优势,但它也存在一些局限性。
首先,无损检测技术的应用受制于其本身的特性。
不同的无损检测技术适用于不同类型的缺陷,对于一些特殊缺陷的检测可能存在一定的局限性。
此外,无损检测技术的操作复杂性也可能限制了其在某些领域的应用。
其次,无损检测技术的正确操作需要具备专业的技术和经验。
无损检测技术的正确操作和结果解读需要经验丰富的技术人员,他们需要熟悉不同的检测方法和设备,并能够识别和评估不同类型的缺陷。
从实践中总结出无损检测技术的优势和局限性
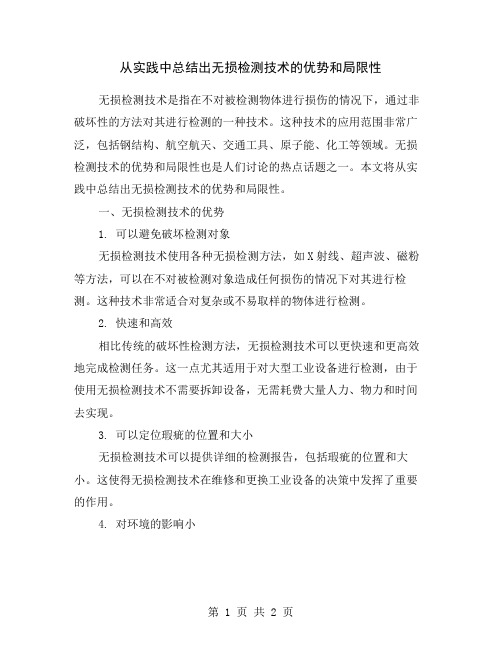
从实践中总结出无损检测技术的优势和局限性无损检测技术是指在不对被检测物体进行损伤的情况下,通过非破坏性的方法对其进行检测的一种技术。
这种技术的应用范围非常广泛,包括钢结构、航空航天、交通工具、原子能、化工等领域。
无损检测技术的优势和局限性也是人们讨论的热点话题之一。
本文将从实践中总结出无损检测技术的优势和局限性。
一、无损检测技术的优势1. 可以避免破坏检测对象无损检测技术使用各种无损检测方法,如X射线、超声波、磁粉等方法,可以在不对被检测对象造成任何损伤的情况下对其进行检测。
这种技术非常适合对复杂或不易取样的物体进行检测。
2. 快速和高效相比传统的破坏性检测方法,无损检测技术可以更快速和更高效地完成检测任务。
这一点尤其适用于对大型工业设备进行检测,由于使用无损检测技术不需要拆卸设备,无需耗费大量人力、物力和时间去实现。
3. 可以定位瑕疵的位置和大小无损检测技术可以提供详细的检测报告,包括瑕疵的位置和大小。
这使得无损检测技术在维修和更换工业设备的决策中发挥了重要的作用。
4. 对环境的影响小传统的破坏性检测方法会产生许多废弃物和环境污染物,而使用无损检测技术则不会对环境造成大的影响。
这使得无损检测技术得到了越来越广泛的应用。
二、无损检测技术的局限性1. 精度低无损检测技术的精度受到很多因素的影响,包括设备精度、环境影响等因素,因此其精度和准确性相对传统破坏性检测技术较低。
2. 昂贵的设备和培训无损检测设备的制造成本非常高,因此需要投入巨大的资金和时间。
同时,人员的培训成本同样较高,这也成为了限制其发展的一个主要问题。
3. 不能检测所有类型的瑕疵无损检测技术只能检测一部分类型的瑕疵,而不能检测所有类型的瑕疵。
例如在某些情况下,无法检测瑕疵的尺寸、深度等信息。
4. 针对特定情况的应用无损检测技术需要不同的方法来适应不同的应用情况,因此需要针对特定情况进行调整和选择。
这需要有一定的专业知识和经验。
三、结论无损检测技术是一项十分重要的技术,具有非常广泛的应用。
介绍几种常见的无损检测技术及其优缺点

介绍几种常见的无损检测技术及其优缺点无损检测技术是一种在不破坏被检物理性能的情况下,对物体的内部或表面进行检测、评价和控制质量的方法。
它被广泛应用于工程、制造业、航空航天、能源、交通运输等各个领域。
本文将介绍几种常见的无损检测技术及其优缺点。
首先,超声波检测是一种常见的无损检测技术。
这种技术通过将超声波的脉冲传递到被检测物体中,然后测量超声波反射或传播速度的变化来检测物体的内部缺陷。
超声波检测具有检测深度大、分辨率高、对不同材料具有良好适应性等优点。
然而,它也存在着检测速度慢、对被检材料有一定要求等缺点。
其次,射线检测是另一种常见的无损检测技术。
射线检测主要利用X射线或γ射线穿透被检材料,通过感光材料或电子束探测器来测量射线的衰减情况,以检测物体的缺陷。
射线检测具有检测速度快、可以检测多种材料、对内部缺陷有较高的分辨率等优点。
但是,由于射线具有辐射危害,对操作人员保护要求较高。
电磁检测是第三种常见的无损检测技术。
电磁检测基于电磁感应原理,通过改变磁场来检测被测物体的内部缺陷。
这种技术具有非接触性、检测速度快、对复杂几何形状具有良好适应性的优点。
然而,电磁检测也存在着对导电材料的限制、对操作环境的电磁干扰敏感等缺点。
另外,磁粉检测是一种常用的无损检测技术。
这种技术通过在被检测物体表面涂覆磁粉或将磁粉溶解在液体中,在外部施加磁场的作用下,通过观察或测量磁粉在缺陷区域的积聚情况来检测缺陷。
磁粉检测具有对各种材料适用、操作简便、成本低等优点。
然而,它只能检测表面缺陷,对缺陷深度的评估能力较弱。
最后,涡流检测是一种常用的无损检测技术。
涡流检测基于涡流感应原理,通过感应导体中的涡流来检测被检测物体的缺陷。
这种技术具有对导电和磁性材料适用、对小缺陷具有高灵敏度、无需接触被检材料等优点。
然而,涡流检测也受到导体材料和几何形状的限制,对操作人员的技术要求较高。
总而言之,无损检测技术在各个领域中发挥着重要的作用。
超声波检测、射线检测、电磁检测、磁粉检测和涡流检测是常见的无损检测技术,每种技术都有其独特的优点和缺点。
无损检测技术的优势和限制分析

无损检测技术的优势和限制分析无损检测技术是一种不破坏物体外观和内部结构的测试方法,它通过利用电磁、声波、热量等原理,对材料和构件进行检测,从而发现其中的缺陷、损伤和变形等问题。
这种检测方法具有许多优势,但同时也存在一定的限制。
本文将分析无损检测技术的优势和限制。
无损检测技术的优势主要集中在以下几个方面:1. 非破坏性:无损检测技术是一种非破坏性的检测方法,不会对被测物体产生二次损伤。
相比传统的破坏性检测方法,如断口检测和截面检测,无损检测技术能够保持被测物体的完整性和可靠性。
2. 检测全面性:无损检测技术能够对整个被测物体进行全面的检测,不仅能够发现表面上的缺陷,还可以查找内部的隐蔽缺陷,确保被测物体的完整性。
而传统的检测方法常常只能针对特定的局部进行测试,容易漏检或误判。
3. 高灵敏度:无损检测技术具有较高的灵敏度,能够检测到微小的缺陷和变形。
例如,超声波检测技术可以检测到毫米级的孔洞和裂纹,红外热像仪可以测量目标物体的温度异常,这些都是肉眼无法察觉的。
4. 高准确性:无损检测技术在检测结果的准确性方面表现出色。
它不受人为因素、主观意识和环境条件的影响,能够提供客观、可靠的检测数据。
这对于许多对材料、构件质量有严格要求的行业,如航空航天、核能等,尤为重要。
然而,无损检测技术也存在一定的限制:1. 有限的适用范围:无损检测技术并非适用于所有材料和构件。
一些特殊材料,如复合材料和陶瓷材料,由于其特殊的结构和性质,可能对某些无损检测技术不敏感,或者无法进行有效的测试。
2. 设备和人力成本:无损检测技术所需要的专用设备和高素质的人力资源相对较为昂贵。
这对于一些中小型企业和发展中国家来说,可能是一个限制因素。
同时,对于进行无损检测技术培训和不断更新知识的要求也提高了人力成本。
3. 某些缺陷难以检测:有些缺陷,特别是微小的或者深埋于材料内部的缺陷,可能会被无损检测技术忽略或难以检测到。
这类缺陷可能会对材料的机械性能和结构安全性产生潜在威胁。
无损检测方法的能力范围和局限性
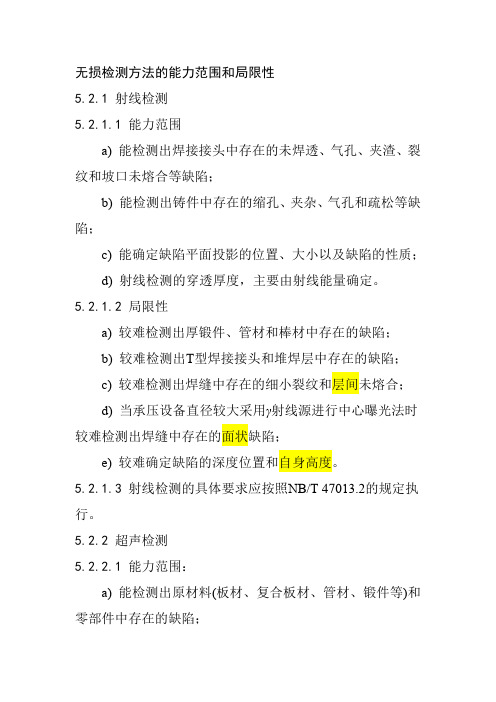
无损检测方法的能力范围和局限性5.2.1射线检测5.2.1.1能力范围a) 能检测出焊接接头中存在的未焊透、气孔、夹渣、裂纹和坡口未熔合等缺陷;b) 能检测出铸件中存在的缩孔、夹杂、气孔和疏松等缺陷;c) 能确定缺陷平面投影的位置、大小以及缺陷的性质;d) 射线检测的穿透厚度,主要由射线能量确定。
5.2.1.2局限性a) 较难检测出厚锻件、管材和棒材中存在的缺陷;b) 较难检测出T型焊接接头和堆焊层中存在的缺陷;c) 较难检测出焊缝中存在的细小裂纹和层间未熔合;d) 当承压设备直径较大采用γ射线源进行中心曝光法时较难检测出焊缝中存在的面状缺陷;e) 较难确定缺陷的深度位置和自身高度。
5.2.1.3射线检测的具体要求应按照NB/T 47013.2的规定执行。
5.2.2超声检测5.2.2.1能力范围:a) 能检测出原材料(板材、复合板材、管材、锻件等)和零部件中存在的缺陷;b) 能检测出焊接接头内存在的缺陷,面状缺陷检出率较高;c) 超声波穿透能力强,可用于大厚度(100mm以上)原材料和焊接接头的检测;d) 能确定缺陷的位置和相对尺寸。
5.2.2.2局限性a) 较难检测粗晶材料和焊接接头中存在的缺陷;b) 缺陷位置、取向和形状对检测结果有一定的影响;c) A型显示检测不直观,检测记录信息少;d) 较难确定体积状缺陷或面状缺陷的具体性质。
5.2.2.3超声检测的具体要求应按NB/T 47013.3的规定执行。
5.2.3磁粉检测5.2.3.1能力范围能检测出铁磁性材料中的表面开口缺陷和近表面缺陷。
5.2.3.2局限性:a) 难以检测几何结构复杂的工件;b) 不能检测非铁磁性材料工件。
5.2.3.3磁粉检测的具体要求应按照NB/T 47013.4的规定执行。
5.2.4渗透检测5.2.4.1能力范围能检测出金属材料中的表面开口缺陷,如气孔、夹渣、裂纹、疏松等缺陷。
5.2.4.2局限性较难检测多孔材料。
5.2.4.3渗透检测的具体要求应按NB/T 47013.5的规定执行。
常用无损检测方法的特点及应用选择
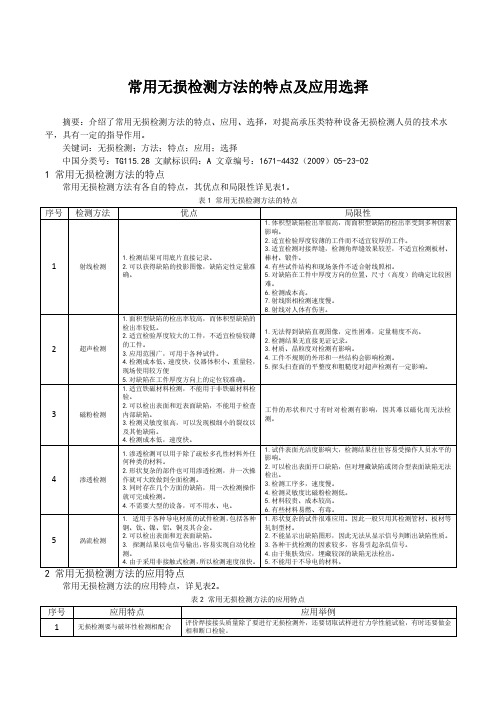
常用无损检测方法的特点及应用选择
摘要:介绍了常用无损检测方法的特点、应用、选择,对提高承压类特种设备无损检测人员的技术水平,具有一定的指导作用。
关键词:无损检测;方法;特点;应用;选择
中国分类号:TG115.28 文献标识码:A 文章编号:1671-4432(2009)05-23-02
1 常用无损检测方法的特点
常用无损检测方法有各自的特点,其优点和局限性详见表1。
表1 常用无损检测方法的特点
常用无损检测方法的应用特点,详见表2。
表2 常用无损检测方法的应用特点
3.1 制造过程中常用无损检测方法的选择
制造过程包括原材料检测和焊接检测,详见表3。
表3 制造过程中常用无损检测方法的选择
3.2 常用无损检测方法和检测对象的适应性
常用无损检测方法和检测对象是否适应,直接影响到检测结果的正确与否。
表4 列出了常用无损检测方法和检测对象的适应性。
表4 常用无损检测方法和检测对象的适应性
掌握常用无损检测方法的特点、应用、选择,对提高承压类特种设备缺陷检出率、确保无损检测质量,必将起着重要的作用。
参考文献:
[1]强天鹏.压力容器检验.北京.新华出版社.2008,5
[2]王晓雷.锅郑压力容器无损检测相关知识。
全国锅炉压力容器无损检测考委会.2001.。
- 1、下载文档前请自行甄别文档内容的完整性,平台不提供额外的编辑、内容补充、找答案等附加服务。
- 2、"仅部分预览"的文档,不可在线预览部分如存在完整性等问题,可反馈申请退款(可完整预览的文档不适用该条件!)。
- 3、如文档侵犯您的权益,请联系客服反馈,我们会尽快为您处理(人工客服工作时间:9:00-18:30)。
d)能确定缺欠的平面投影位置和大小,以及缺欠的种类。
GB/T 5616—鬃鬃
注:400kV X射线的透照厚度可达85 mm左右,钴60伽玛射线的透照厚度可达200 mm左右,9 MeV高能X射线的透照厚度可达400 mm左右。
2.2局限性:
较难检测出锻件和型材中存在的缺欠;
b)较难检测出焊缝中存在的细小裂纹和未熔合;
c)不能检测出垂直射线照射方向的薄层缺欠;
d)不能确定缺欠的埋藏深度和垂直高度。超声检测()
能力范围:
能检测出锻件中存在的裂纹、白点、分层、大片或密集的夹杂等缺欠;
注:
b)能检测出焊缝中存在的裂纹、未焊透、未熔合、夹渣、气孔等缺欠;
注:
c)能检测出型材(包括板材、管材、棒材及其他型材)中存在的裂纹、折叠、分层、片状夹渣等
1.3
1.4射线照相检测常被用于检测金属铸件和焊缝,超声检测常被用于检测金属锻件、型材、焊缝和某些金属铸件。在对焊缝中缺欠的检测能力上,超声检测通常要优于射线照相检测。射线照相检测()
能力范围:
能检测出焊缝中存在的未焊透、气孔、夹渣等缺欠;
b)能检测出铸件中存在的缩孔、夹渣、气孔、疏松、热裂等缺欠;
能力范围:
能检测出铁磁性材料(包括锻件、铸件、焊缝、型材等各种工件)的表面和(或)近表面存在
b)能确定缺欠在被检工件表面的位置、大小和形状。
5.2局限性:
a)不适用于非铁磁性材料,如奥氏体钢、铜、铝等材料;
b)不能检测出铁磁性材料中存在于远离测面的内部缺欠;
c)难以确定缺欠的深度。渗透检测()
能力范围:
.本文源自:中国无损检测论坛
1每种NDT方法均有其能力范围和局限性,各种方法对缺欠的检测概率既不会是100 %,也不会完全相同。例如射线照相检测和超声检测,对同一被检工件的检测结果不会完全一致。
1.2常规NDT方法中,射线照相检测和超声检测可用于检测被检工件内部和表面的缺欠;涡流检测和磁粉检测用于检测被检工件表面和近表面的缺欠;渗透检测仅用于检测被检工件表面开口的缺欠。
能力范围:
能检测出导电材料(包括铁磁性和非铁磁性金属材料、石墨等)的表面和(或)近表面存在的裂
b)能测定缺欠的坐标位置和相对尺寸。
4.2局限性:
a)不适用于非导电材料;
b)不能检测出导电材料中存在于远离检测面的内部缺欠;
c)较难检测出形状复杂的工件表面或近表面存在的缺欠;
d)难以判定缺欠的性质。磁粉检测()
缺欠;
注:
d)能检测出铸件(如形状简单、表面平整或经过加工整修的铸钢件或球墨铸铁)中存在的热裂、
冷裂、疏松、夹渣、缩孔等缺欠;
e)能测定缺欠的埋藏深度和自身高度。局限性:
较难检测出粗晶材料(如奥氏体钢的铸件和焊缝)中存在的缺欠;
b)较难检测出形状复杂或表面粗糙的工件中存在的缺欠;
c)较难判定缺欠的性质。涡流检测()
a)能检测出金属材料和致密性非金属材料的表面存在开口的裂纹、折叠、疏松、针孔等缺欠;
b)能确定缺欠在被检工件表面的位置、大小和形状。
6.2局限性:
a)不适用于疏松的多孔性材料;
b)不能检测出表面未开口而存在于材料内部和(或)近表面的缺欠;