TPM设备自主保养课程
全员生产维护TPM-自主保养(AM)

一.TPM(全员生产性保全活动)
1、为什么要实施TPM
丰田等企业为什么会成功
(1).追求精细化管理,维护管理工具
丰田公司数十年如一日的不断追求精细化管理,追求 零库存、零缺陷、低成本和零损耗等。丰田公司有效地运 用了各种各样的管理工具,如5S体验活动,TQC、TPM、 IE、JIT等,为企业的管理提升服务。这些管理工具在丰 田都能得到有效的坚持,这是它获得成功的必要条件之一。
一、为什么要实施TPM
丰田等企业为什么会成功
(2).注重人才的培养
丰田公司注重人才的培育,也是它成功的重要方面。 它提倡的企业使命是“造物、育人”,经营理念则是“造 物先育人、先人后事”。人才开发重要的是营造一种学习 的环境,丰田对人才开发的重视不亚于对产品的开发。正 因为丰田培养的人才足以领导整个日本的制造业,所以才 会出现在日本企业中担任顾问的人员有70%来源于丰田汽车 公司的局面。
因为一个企业这么大,光 靠几个几十个工作人员维护, 就算是一天8个小时不停地巡 查,也很难防止一些显在或潜 在问题发生。
(3)、b、重复小团队是执行力的保证
TPM的推进组织为“重复小团队”。 重复小团队是指从最高层、到中层, 直至第一线上的小团队的各阶层互相协作 活动的组织。
5、TPM活动内容
世界最高竞争力公司
1971年,日本人引进了PM活动并将其改造成为现场部门的TPM改善活动, 即开始注重全员参与(total)。在全员保养时代与保养预防时代的区别就在于 所有的员工都应该对设备保养负责。此时的TPM主要以生产部门为主。
TPM的发展
(1) 、 从 美 国 式 的 P M 到 日 本 独 自 的 T P M
2、认识 TPM
tpm自主维护培训计划
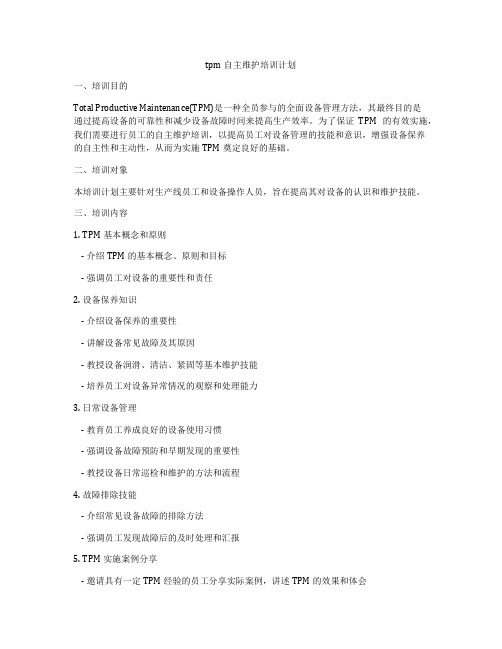
tpm自主维护培训计划一、培训目的Total Productive Maintenance(TPM)是一种全员参与的全面设备管理方法,其最终目的是通过提高设备的可靠性和减少设备故障时间来提高生产效率。
为了保证TPM的有效实施,我们需要进行员工的自主维护培训,以提高员工对设备管理的技能和意识,增强设备保养的自主性和主动性,从而为实施TPM奠定良好的基础。
二、培训对象本培训计划主要针对生产线员工和设备操作人员,旨在提高其对设备的认识和维护技能。
三、培训内容1. TPM基本概念和原则- 介绍TPM的基本概念、原则和目标- 强调员工对设备的重要性和责任2. 设备保养知识- 介绍设备保养的重要性- 讲解设备常见故障及其原因- 教授设备润滑、清洁、紧固等基本维护技能- 培养员工对设备异常情况的观察和处理能力3. 日常设备管理- 教育员工养成良好的设备使用习惯- 强调设备故障预防和早期发现的重要性- 教授设备日常巡检和维护的方法和流程4. 故障排除技能- 介绍常见设备故障的排除方法- 强调员工发现故障后的及时处理和汇报5. TPM实施案例分享- 邀请具有一定TPM经验的员工分享实际案例,讲述TPM的效果和体会6. 培训考核- 培训结束后进行知识和技能的考核四、培训方式1. 理论教学:通过课堂讲授、PPT演示等形式,介绍TPM的基本概念、设备保养知识等内容。
2. 案例分析:邀请具有TPM经验的员工分享实际案例,讲述TPM的效果和体会,以提高员工对TPM的认识和信心。
3. 实地操作:组织员工到生产现场进行设备实际操作和巡检维护演练,提高员工的实际操作技能。
4. 培训考核:培训结束后进行知识和技能的考核,确保员工掌握了必要的维护技能和知识。
五、培训计划1. 前期准备- 制定培训计划,并征得相关部门的支持和配合- 确定培训时间和地点- 邀请具有TPM经验的员工担任讲师2. 培训实施- 第一天:理论教学,介绍TPM的基本概念和原则- 第二天:设备保养知识的讲解- 第三天:设备管理和故障排除技能的培训- 第四天:实地操作演练- 第五天:培训考核3. 后期跟踪- 培训结束后,定期对员工的设备管理情况进行跟踪和指导- 鼓励员工提出改进建议和意见,不断优化培训内容和方法六、培训效果评估1. 培训后定期进行设备管理的巡检,并对员工设备保养情况进行评估2. 数据统计:统计员工设备故障率的变化情况,评估TPM培训的效果3. 员工反馈:定期进行员工满意度调查,收集员工对培训的反馈意见七、总结通过本次TPM自主维护培训,员工的设备管理能力和意识得到了提升,为实施TPM打下了坚实的基础。
TPM培训课程(经典)

3 STEP : 清扫/注油基准书的制定 清扫/注油基准的制定及注油困难地点的改善 学习正确的注油技能
4 STEP : 设备总点检 设备点检point及点检技能的学习 清扫/注油/点检技术的统合及点检困难地点的改善
TPM
(全员生产保全)
1. TPM 概论
TPM定义
TOTAL 全公司的
PRODUCTIVE 生产设备
MAINTENANCE 维护(保全)
由全员参与的生产维护活动
TPM(Total productive maintenance)= 全员生产保全
提高设备效率 提高人的效率 提高管理效率 提升品质 推进无人化
纵向:从高层到一线员工, 横向:所有部门 纵横: 小集团活动
TPM发展
事后保全BM
1950
1960
1970
1980
1990
预防保全PM
改良保全CM
保全预防MP
TPM
时间管理时代
状态管理时代
修理为主
预防故障
改进设备
设计设备
设备的 体质改善
人员的 体质改善
标 准 化
单纯/最佳化
5S, 提案, 小组活动
人员方面目的
设备方面目的
企业方面目的
容易感知异常的现场
定期锻炼,每天30分钟 散步
每天少食多餐胜过 每天两次大餐
每年一次体检,定期 血液和视力检查
我们自己的身体
我们使用的设备
每天对设备的清扫、 润滑、紧固
定期进行适当的润滑 或过滤器等零件更换
每月、季、半年进行 计划性维护
TPM设备维护TPM高级自主维护培训
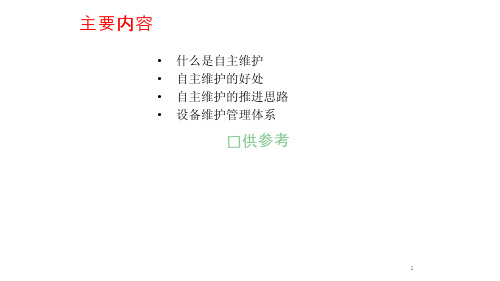
3
自主维护- 含义
专业维护和自主保全的关系?
即相互支撑又职责分担
我们的目标是 婴儿健康成长
供参考
保全工 (专业保全)
设备
操作工 (自主保全)
我们的目标是设备 高效运行
4
自主维护- 含义
专业维护和自主保全的关系?
• 1、相互支撑 专业保全对自主保全支援活动 红牌维修
站在专业保全立场对操作供员做参培考训的支援
▶ 腐蚀,变形,伤痕,炸裂
潜在缺陷
▶ 温度,振动,异音等
1. 强制劣化造成的故障>70% 2. 自然劣化造成的故障 30%,其中90%没有及时点检
(更换)而造,只有3%的很难早期发现的
----日本和美国对三万余家企业三年跟踪调查
19
清扫、点检、润滑的重要性
供参考
20
清扫、点检、润滑的重要性——故障冰山理论
Sun HQ
部门级 推进委员会
从下而 上
Line Mgr. TPM 组长
Line Mgr. TPM 组长
Line Mgr. TPM 组长
Line Mgr.
工段级 执行小组
TPM 组员 TPM 组员 TPM 组员 TPM 组员 TPM 组员
班组 活动小组
12
特征五:自主管理、自主改善的哲学!
1. “My Machine”与“My Area” 2. 自己动脑、动手去改善现场的“不合理” 3. 团队(个人)设定自己的工作目标、指标,制定达成计划 4. 定期组织“小组会议”-“脑力风暴” 5. 自主学习、团队学习交流(OPL等)
能够对自己所担当的设备进行日常清扫、点检、给油、紧固、以一 定范围的备品更换、修理, 异常的早期发现、精度点检。
TPM自主保养

Lean Six Sigma
Copyright ? 2011 HP. All rights reserved4.
A
离
隔离污染物,不会污染设备或减 少污染面积
易
使设备清洁变容易
勤
勤于清洁设备
培养改善的意愿
切断发生源
Lean Six Sigma
Copyright ? 2011 HP. All rights reserved.
A
11
困难部位对策
如何降低加油时间、改善加油困难?
目视化:加油标示 顺序化:加油顺序 集中化:集中给油 简单化:加油简单
Lean Six Sigma
漏水\漏油\粉尘飞散\切削飞溅…….
整理第一步骤发生的污染源发生部位 ,分 析份量\材质\成份和对设备的伤害 …….
Copyright ? 2011 HP. All rights reserved.
A
7
什么是困难部位 ?
必须费时,且不易清扫、加油、点检的部位
清扫困难场所:
设备自主保全
刘世召
Lean Six Sigma
Copyright ? 2011 HP. All rights reserved.
A
1
前言
经过自主保养STEP 1 初期清扫活动后,设备虽然变的干净,但这只是短暂干净而已,如
未持续清扫,经过一段时间后,设备又会开始变脏,各项不具合点也会慢慢增多,因此,如
3、点检部位多且分散,点检费时。
Le4an、Six S1ig0ma分钟内无法完成点检。 A
TPM自主保养技能教育训练

3-4 小組集會不具合找出與對策(不具合與對
策一覽表)
3-5 實施不具合項目改善
自主保養第四步驟--總點檢
Step 4 各總點科目的標準化
4-1 制定日常點檢暫訂基準 4-2 核點檢技能(個人技能評價表) 4-3 自主診斷與診斷申請 4-4 實施診斷 4-5 指摘問題的處理
前言 電動機 減速機、變速機 軸承 軸聯結器 傳動裝置之操作與保養 傳動之目視管理
第1章 前言
所謂傳動,就是給予動力作動者,要學習由原動力
到作業位置之傳達機構的保養。
皮帶輪
軸聯結器
軸
軸承
電動機
皮 帶
軸
圖1 傳動機構
鏈條 軸
機械
鏈輪
第2章 電動機
1.電動機(馬達)的定義
電動機就是將電能轉換為工作能(轉動)之機器。
• 正確固定
• 相接部不得有過熱 之痕跡
• 接地線不得損傷或 脫落
(4)電動機之固定狀態是否良好 (如圖3,圖4)
圖3
固定螺帽不可遺忘
螺絲頭部下方一定要墊以平墊圈與彈簧墊圈。
圖4
不要遺漏彈簧墊圈
第3章 減速機
1.功能
從原動力要傳達其動力時,為配合機械設備而可獲得適
當之轉動力與轉數之裝置。 (1)變速機:在某一定速度比之範圍內,可做無段變速之
(2)給油量與換油時機
①檢查--確認油位在外殼油位計之上下限刻度之範圍內。
◎看不清楚時,應改善為容易觀察。
②給油--在停止狀態確認油位,加入至規定油位之必要量。
◎不要補給必要量以上的油。
③換油--運轉一個月後(新機)。
TPM自主保全讲义

MTTR与MTBF计算举例
负荷时间(133H)
动作
停止
30H
1.0H
30H
0.5H
10H
0.5H
60H
1.0H
1、MTBF=平均故障间隔
2、MTTR=平均修理时间
3H
133H
= 2.26%
3、故障停机率=
×100%
数值越大表示可靠性越好
数值越短越好——即易恢复性越好
两大基石
彻底的6S活动
重复性的小集团活动
对应
母亲
操作者
设备对应婴儿,婴儿的妈妈就是设备的操作者,那么给婴儿换尿布、喂奶、清洗、确认婴儿是否发热感冒就是妈妈必须做的事情,相对应的给设备给油、清扫、发现漏油、发热及振动不良就是设备操作者自主保全的内容。
设备部门相当于婴儿的医生,目的就是预防疾病发生和迅速处理问题。
初期清扫活动方法
清扫担当是谁?
导入准备
开始到实施
导入准备阶段
导入开始
6. TPM 决议宣言
(KICK OFF)
主办单位、
相关部门、形成共识协力组织
区分
步骤
要 点
区分
导入实施阶段
稳定阶段
8.建立新制品,新设
备的初期管理体质
9.建立品质保全体制
10.建立间接管理部
分的效率化体制
11.建立安全, 卫生和
环境管理体制
7.4运转, 保养 技能提高训练
向方进推
TPM活动的体系
一个目标
(一)什么是自主保全
自主保全是以设备的操作者为主,在对其进行保全技术的教育训练后,通过定人、定点、定量、定周期、定“点检计划表”、定记录格式、定“检修业务流程”,以个人的五感(看、触、听、嗅、味)按照事先规定的设备特性值标准、点检标准、润滑标准、保全作业标准等管理标准,来对设备的日常养护和常见故障做简单、快速的修复工作。自主保全不是单纯地将设备保全的责任转移给操作者,而是专业保全人员与操作者的一项团队合作。其目的在于提升操作者对他所使用的设备和作业环境的责任感。
[精选]TPM培训之自主保养教材
![[精选]TPM培训之自主保养教材](https://img.taocdn.com/s3/m/9a98d33678563c1ec5da50e2524de518964bd30e.png)
1、管理标签---工具
1、管理标签---备件
2、管理接线标志---报警灯
2、管理接线标志---油位计
3、故障地图
4、人员动态标识
4、人员动态标识
5、颜色管理---管路
5、颜色管理
TPM活动如何应用目视化管理
TPM活动如何应用目视化管理
TPM活动如何应用目视化管理
TPM活动如何应用目视化管理
改善 企业体质
比设备强的人
设备能力的最大发挥
TPM的理念
目 录
TPM的定义及理念自主保养定义自主保养目的自主保养展开七大步骤自主保养三大工具目视化管理
5S 活动
一、TPM的八大支柱
个别改善
生 产 损 失 之消灭
教育训练
人 员 素 质 之提升
自主保养
设备应有状态 之维持
计划保养
设备零故障 之达成
即使完美的一套套三表,如果不不在生产现场验验证,就无法获获得真正效果,生产现场 就会流于形式式。
现场验证
主管和作业人员使用一套三表逻辑关系
目录
自主保养的三大工具
目录
目视化管理的定义
目视化管理的起源
目视化管理的目的
目视化管理的做法
事态表达效果优劣强度
目视化管理的工具方法
1、管理标签
何谓发生源、困难部位
效果的确认
第三步骤暂定基准书的建立
“一套三表”
清扫、点检项目制作原则
暂定基准书所含项目
一套三表的使用
一套三表的使用
一套三表的使用
一套三表的使用
暂定基准书的修订
暂定基准书的修订
暂定基准书的修订
修订后效果评估
点检记录
复原反馈
第9讲 TPM之二:自主保养

第9讲 TPM之二:自主保养【本讲重点】自主保养的基本概念自主保养的展开步骤自主保养的基本概念自主保养的定义自主保养是指企业员工自主地对企业实施全面的管理、维护和保养。
自主保养的关键之处在于真正做到“自主”,使现场设备的保养、维护成为操作人员的自觉行为,使之成为工作人员一种良好的工作习惯和内在素质。
自主保养是以生产现场操作人员为主,按照人的感觉(听、触、嗅、视、味)对于设备进行检查,并对加油、紧固等维修技能加以训练,使员工有能力对小故障进行修理。
通过不断的培训和学习,使现场操作人员逐渐熟悉设备构造和性能,不但会正确操作、保养和诊断故障,而且会处理小故障。
自主保养的范围自主保养主要围绕现场设备进行保养,包括清洁、整顿、维修等基础工作,它的基本范围可以区分为五种,如表9-1所示。
每次开动设备之前,确认此设备是否具备开机条件,并将所有的关键部位检查一遍。
养成这个习惯后,就可以降低故障产生的途径。
作业中的点检就是在机器运行的过程中,确认机器的运行状态、参数是否正常,如果出现异常应该立即排除故障或者停机检修。
如果对小问题不重视,这些小问题往往会变成大问题,进而酿成事故。
作业后的点检是在一个生产周期结束后进行停机,然后定期对设备进行检查和维护,为下一次开机做好准备。
保养得好的机器,寿命往往可以延长几倍。
设备的维护观念自主保养观念的建立不仅对设备的维护有益,也提升了员工的技能,培养了员工的自觉意识和主人翁意识。
在企业中,意识的培养是一件难度较大、又必须做好的工作,意识的培养对于企业效益、企业文化都会产生不可估量的影响。
图9-1展示了自主保养观念的成效。
图9-1 自主保养观念的成效自主保养的阶段自主保养主要分为三个阶段:防止劣化阶段、发现和测试劣化阶段、改善劣化阶段,这三个阶段是保养设备的一般方法。
具体内容就是:开始时进行预防,一旦发现故障,就应尽快找出故障发生的原因,进行维修,在故障排除后要进行总结,避免类似故障再次发生。
TPM4 -自主维护第一步

2
TPM的自主维护和计划维护 消除强制劣化,从而在自然劣化的状 态下测定其劣化状态,当劣化已经达 到某种程度以上时,则必须彻底使其 恢复原状.
什么是自然劣化
自然劣化: 除去人为因素和环境因素, 设备在使用过程中, 自然损耗的过程
3
什么是强制劣化
强制劣化:因错误操作,或没有遵守标准 操作条件,而造成对设备或部 件的损坏.如使用不正确的工 具,用力过大,松动,漏油,缺油, 灰尘,污垢等.
好 自己的设备
6
AM 的定义(II)
以生产现场操作人员为主, 对于设备按照人的感官
(目视/手触/问诊/听声/嗅诊) 来进行检查,并对清洁/
润滑/紧固/点检等维修技能 加以训练,使之能对小故障 进行自主修理及适合操作工 做的改善,以维护设备基本状况。
冰山一角
故障
灰尘/污垢/原料黏附/ 松动/泄漏/
腐蚀/变形/裂纹/ 缺油/磨损
• 不要对运行设备进行清扫和加油 • 清扫前必需关闭电源主开关 • 必需清楚在该区域是否还有他人工作 • 检查所有安全装置是否能正常发挥作用 • AM活动结束后必需恢复所有安全防护装置 • 熟悉SOP
AM 0 -- 检查清单
序号
检查内容
机器周围 1 地面 2 通道
3 材料供应
4 废物桶 5 SOP 6 应急开关 7 气动
• 在干燥的环境运行,污染,更正不清楚地润滑剂,不合适的润滑油,泄漏 • 已被污染的涂抹润滑脂的喷头和加油口,堵塞,破损,变形或凹陷的管道,缺
陷的累积,错误的润滑设备
• 污垢,破损,泄漏,错误的液面指示 • 紧固件:松动,脱落,不合理的使用,太长,压碎,腐蚀,使用错误的垫圈,
螺栓安装方向错误,杂乱的蝶形螺母
TPM的上课OHP(自主保养)

第四步驟:總點檢
第五步驟:自主點檢 第六步驟:整理、整頓(標準化) 第七步驟:自主管理的徹底化 ●整理不使設備發生不良的條件 並推行其維持管理
5
ETPM
自主保養活動的目標
●正確的操作 ●日常點檢
●劣化的復原 ●基本條件整合
培養發現異常能力
防止劣化的活動
培養條件設定能力 培養維持管理能力
實現設備應有形態
20
生產部門保全道場技能教育實施計畫表
1995年4月7日 TPM推進課
ETPM ●實施目的: 為有效提昇本公司員工對機械設備本體及周邊設備機構能有充分認識, 以達成「自己的設備自己來維護」這種基本理想, 因此, 擬在本期 實施一系列自主保全之基本技能教育訓練。
●預期效果: 有效降低設備常態性故障50%以上, 減少設備維修工時, 並延長設備部品之壽命。 ●實施對象: 製造本部中壢工場及新竹工場之班組長。 ●實施日程:
15
ETPM
自主保養七步驟
步驟三:製作自主保養暫定基準
目的
改善垃圾、塵埃、污垢的發生源及防止飛散,改善清掃、點檢、 給油、鎖緊螺栓之困難部位,謀求縮短點檢時間。 學習改善設備的想法,以提高實質上的效果。
16
ETPM
STEP3
自主保養基準的作成
設備系統
• 空壓系 統 • 潤滑系 統 • 油壓系 統
-(作業LOSS+SD LOSS+工程變換LOSS+刃具LOSS+量產開始LOSS+故障LOSS)] /稼動時間
---- LOSS時間 *[(固定費+變動人件費)
-(作業LOSS+SD LOSS+工程變換LOSS+刃具LOSS+量產開始LOSS+故障LOSS)] /稼動時間
TPM改善生产管理的利器—全面生产设备维护培训课程大纲

TPM改善生产管理的利器—全面生产设备维护培训课程大纲课程简介:TPM是什么?TPM就是工厂通过全面改善活动,将工厂所有损耗降低为零,挑战四大零化极限目标。
TPM的根本目标就是“把生产线作业员培养成设备操作能手;把设备人员培养成维修医生;把产品设计和工程技术人员培养成各方面的专家”。
日本和韩国所有知名企业都推行TPM,世界500强企业视TPM为企业成功的制胜法宝。
日产汽车,员工用一只手拿着秒表寻找生产线中的浪费;丰田汽车,在全球丰田组织中推进持续改善的社风;三星公司推进TPM 已经有20多年历史,还要求供应商和合作伙伴推进TPM。
中国企业从上世纪90年代陆续引进TPM,TCL、联想、美的、康佳、海信、长城、方正、志高、华菱、青岛啤酒、金龙啤酒、健力宝、东风柳州汽车等国有或民营企业已经收到巨大成效。
中外企业之所以热衷于推进TPM活动,是因为TPM帮助制造企业提高生产效率,降低损耗和浪费,压缩成本和费用,减少、预防灾害与故障,消减不良或异常,形成全员参与自主管理的改善文化。
课程特色:第一,系统性和全面性。
本课程融合了日、韩TPM活动各自的长处,以全新的视觉,在可操作性基础上,坚持TPM八大支柱的完整性和全面性,是企业全面了解和选择运用TPM的参考依据。
第二,独创性。
TPM内容过于复杂,面面俱到,很难看到效果。
为解决该难题,向老师在国内第一个创造性地提出了“TPM四大心脏模式”,该模式既兼顾了TPM的全面性,又凸现了TPM的重点,同时也解决了企业推进TPM的方法和策略问题。
“TPM四大心脏模式”是经过实践检验过的普遍适合中国工厂的“良方”。
第三,实用性。
“挑战零损耗极限的武器—TPM”是中国工厂各级管理者推进TPM活动的工具箱。
本课程吸收向老师在世界著名企业推进TPM的优秀做法,坚持采用“案例介绍法”,为了体现TPM带来的直观效果,课件中收录了近150幅现场案例、现场图片和简单易操作的表格,以图文并茂的形式展示给学员,帮助企业推进TPM各取所需,直接引用。
设备保养-TPM培训(企业经典)

2.TPM的定义
TPM是什么?
1.创造生产系统效率化的极限追求(综合效率化)的企业体质
为目标
2.在现场构筑预先防止生产系统的 Life Cycle 全体为对象的
灾害ZERO,不良ZERO,故障ZERO等全部LOSS的组织
3.生产部属首先通过开发,营业,管理等的全部部属, 4.从TOP开始到第一线监督者全员参加 5. 指的是因重复小集团所 LOSS ZERO的达成
一个整洁的工作场所; 2.改善造成灰尘、脏污的源头并改善周围恶劣的 环境; 3.通过整理、整顿、清扫,使设备潜在的缺陷、 异常显性化,并恢复其机能; 4.彻底清扫设备的各个角落,切身体验“清扫也 是点检”,做到“自己的设备自己维护”; 5.按照计划推进整理、整顿、清扫,提高全员的 管理水平,形成“能遵守已决定事项”的工作氛围。
对策—针对困难源的改善对策如下: 把机械移动安全的地方或设置落脚的位置及栏杆; 设置入口、点检口,对设备改善,使其能够拆卸; 整顿附着的电缆、软管等,按照顺序进行修理。
自己发现的问题点尽量自己去处理,但需要焊接、电钻等超过 自身能力的工作时,由设备维护专员协助
发生源与困难源的对策顺序
图表1—发生源与困难源的对策顺序 (1)防止发生对策 发生源对策 (2)防止飞散对策
3.TPM的特点
三个“全”,即全效率、全系统和全员参加。 全效率:指设备寿命周期费用评价和设备综合 效率。 全系统:指生产维修系统的各个方法都要包括 在内。即是PM、MP、CM、 BM等都要包含。 全员参加:指设备的计划、使用、维修等所有 部门都要参加,尤其注重的是操作 者的自主小组活 动。
促进目的
不用品的清除 已发现浪费的清除 发现缺陷 能力的培养 改善能力的培养
- 1、下载文档前请自行甄别文档内容的完整性,平台不提供额外的编辑、内容补充、找答案等附加服务。
- 2、"仅部分预览"的文档,不可在线预览部分如存在完整性等问题,可反馈申请退款(可完整预览的文档不适用该条件!)。
- 3、如文档侵犯您的权益,请联系客服反馈,我们会尽快为您处理(人工客服工作时间:9:00-18:30)。
调查项目
2
2.调查润滑油添加记录 3.调查润滑油路
○暂停 ●不良 ○其它
核准
做成
基准
实际
判定
密闭良好 密闭良好 OK
有添加记录
无添加记 录
NG
无异物堵塞
无异物堵 塞
OK
WHY1 WHY2 WHY3 WHY4 WHY5
对策
原因分析 3
无润滑油添加更换记录添加油品不明确 误添加不同品号润滑油 操作人员常识缺乏
设备自主保养教育训练
现况分析案例
设备名称 设备编号
故障分析表
精密车床
单位 维修时间
机加 2015.4.12
发生日 分析日
集中润滑器
变质润滑油
2015.4.12 2015.4.12
○故障
初发
●
再发
调查项目
1.调查润滑油箱密封性
发生内容 与
缩略图
1 发生现象:在进行设备定期点检保养时
发现集中润滑器中有絮状物质
人员的意识改变
改善活动(设备问题点的复原)
培养发现异常能力 培养条件设定能力 培养维护管理能力 培养改善、复原能力
自己的设备自己保养 成为对设备专精的操作人员
自主保养基本想法
基本想法
1.关于设备功能停止或者功能劣化,如果和设备相 关的所有的人改变其想法或行动即可达成「零不 良」、「零故障」。
2.设备改变人即改变,人改变了现场亦改变。 3.在公司领导成员的主导下,以全体人员参与的方
4.判定。正常(OK) 异常(NG)
防止再发
5
项目
区分
内容
点检基准修 要 ●不要 订
技能训练 ●要 不要 新进员工的教育训练
对策水平展 ●要 开
不要 全厂设备点检的加强
日期
负责人
现况分析案例
故障分析表
设备名称 精密数控车床 设备编号
单位 维修时间
机加 2015.4.12
发生日 分析日
尾座
油压马达
2015.4.12 2015.4.12
实施过程 与
4.班组长加强日常点检宣导
NG
使用材料
WHY5 负责人点检意识欠缺
NG
对策
车间设备班长加强设备日常点检的督导,对于 新近人员进行岗前教育训练
OK
4 使用材料:68#液压油30L
1.構造、機能、正確使用方法、正確使用順序都要列入分 析。 问题解析 2.原因分析要針對設備、材料、方法等反覆進行解析 注意事项 3.分析结果需要现场操作人员确认。
微缺陷造成的灾难 一颗螺丝钉的脱落 造成华航客机在那霸机场爆炸
2007/8/20 9:30中華航空CI 120的波音737-800在日本沖繩 那霸機場降落時起火爆炸。
自主保养目标
活动目标
.劣化的复原 .基本条件整合
.正确的操作 .日常点检
防止设备强制劣化
.小集团活动 .保养技能教育
实现设备应有的状态
将劣化复原 的活动
1.小故障、小异常(简单的零件更换或紧急处置) 2.迅速而且正确的判断故障与异常的发生。 3.突发故障的协助维修。
这是最 重点
以五感為主
保养活动概要
保养部门的活动
活动分类
活动手段
防止劣化 的活动
1.改良保养(信赖性) (1)提升強度 (2)减轻負荷
2.对于操作部门的支援(点检标准的指导)
4.判定。正常(OK) 异常(NG)
防止再发
5
项目
区分
内容
点检基准修 要 ●不要 订
技能训练 ●要 不要 新进员工的教育训练
对策水平展 ●要 开
不要 全厂设备点检的加强
日期
负责人
自主保养由来
TPM
英文Total Productive Maintenance的缩略语,中
文译名叫
。
体系综述
TPM管理的系统是包含以6S和全员参与为基础,自主保养、
清洗润滑油箱,清洗油泵过滤棉,更换润滑油
判定 NG NG Байду номын сангаасG
OK
实施过程 与
使用材料
1.清洗润滑油箱和油泵过滤棉 2.添加32#润滑油 3.设备动作检查轨道油量
4 使用材料:32#润滑油2L
1.構造、機能、正確使用方法、正確使用順序都要列入分 析。 问题解析 2.原因分析要針對設備、材料、方法等反覆進行解析 注意事项 3.分析结果需要现场操作人员确认。
操作部门的活动
活动分类
活动手段
基本条件准 备活动
1.強制劣化的排除(清扫、给油、点检) 2.正确操作(人为错误的防止) 3.基本条件的准备(清扫、给油、锁紧) 4.设备安全参数的明确与规范使用 5.设备异常问题点的汇总记录。 6.对于保养部门的协助
判定强制劣 化的活动
1.日常点检 2.个别部分的定期点检
○故障
初发
●
再发
调查项目
1.检查油压管路
发生内容 与
缩略图
1 发生现象:设备加工尾座在进行伸缩操作时,设备产 生异音,且动作迟缓
调查项目
2
2.检查尾座油缸 3.检查油压输出系统
○暂停 ●不良 ○其它
核准
做成
基准
实际
接头与管路 无破损漏油
无异常变形 卡顿
马达运转正 常无异音抖 动
无破损漏 油 无异常变 形卡顿
式确实实施,以谋求自我提高和价值的体现。
保养意识的转变
操作.保养一体化 在所谓「我是生产的人」、「你是修理的人」的分 工体制下不能达成真正提高生产力。不管多么有干 劲,只要设备因故障而停止就无计可施。
我们只有将设备操作部门‧保养部门成为一体才能达 成设备可信赖度的最大化,生产效益的最大化。
保养活动概要
马达异音
判定 OK OK NG
3 原因分析
判定
1.加注68#液压油到油箱上限
WHY1 油压马达异常抖动异音
NG
2.启动设备进行操作,检查有无漏油
WHY2 WHY3 WHY4
液压油箱油量下限,油量不足 设备漏油故障后为及时检查油位添加液压油 设备负责人日常点检不到位
NG
3.加油状况记录与日常点检表
NG
测定劣化 的活動
1.定期点检(要求高度技能、技术的领域) 2.定期檢查 3.分解檢查
将劣化复原 的活动
1.定期维保 2.不定期维保 3.突发维修 4.维保作业改善 5.提高维保品质 6.对于操作部门的支援(简单维修的指导)
这是最 重要点
保养活动概要
保养部门的活动
活动分类
教育‧训练 及其他
活动手段
1.对于操作部门自主活动的支援 (1)在第1步骤~第3步骤的支援 设备的功能、构造、润滑、油种 (2)在第4步驟~第5步驟的支援 总点检教育的讲师、点检技能的教育、自主点检基准书的 调整
计划保养、个别改善、初期管理、品质保全、事务管理、教 育培训、环境安全在内的8个体系为支柱,
。TPM管理的 自主保养体系是推行TPM管理极为重要的一个支柱。
TPM管理是全员参与维护的设备管理工具,不少企业都借此取得了很大
的效益,当然重点是要
。领导支持,员工配合,才能实现生
产效率最大化,成本支出最小化,他能够形成一套完整的管理机制。