CTCDRH62BF-221M中文资料
施奈德EOCR保护器新产品中文版

Emission
& 7
i3DM / iFDM, i3MZ/iFMZ, i3MS/iFMS, i3M420/iFM420, i3BZ/iFBZ
0.5~60A, 60A ,
i3MS/iFMS 0.5~20A, 20A ,
& TCC 0.5~32A, 32A
i3BZ iFBZ
2
0.5A
D-time O-time
3BZ2 / FBZ2 AC/DC 100~240V
DC/AC 24V 50/60 Hz
i3DM / iFD AC/DC 100~2
DC/AC 24 50/60 Hz
A, F, H
5 Digit 7 Segment -
/ 3DD, 3DE, 3DM FD, FDE, FDM
-
5 Digit 7 Segment -
DC/AC 24V 50/60 Hz
i3MZ / iFMZ AC/DC 100~240V
DC/AC 24V 50/60 Hz
i3BZ / iFBZ AC/DC 100~240V
DC/AC 24V 50/60 Hz
i3M420 / iFM420 AC/DC 100~240V
DC/AC 24V 50/60 Hz
EOCR-iFDM (Z, S, 420) Window type
EOCR-iFDM (Z, S, 420, BZ) Bottom hole type
EOCR-i3DM (Z, S, 420, BZ) Terminal type
EOCR-iFDM (Z, S, 420, BZ) Terminal type
IEC61000-4-2 IEC61000-4-3 IEC61000-4-6 IEC61000-4-4 IEC61000-4-5 CISPR11
美的 MRC-225W 双门冰箱 使用说明书

SJ-FTF23AVP-BK SJ-FX660S-BK
Refrigerant: R600a Insulation blowing gas: Cyclopentane 冷媒種類 :R600a 絕緣發泡材主要成份 : 環戊烷
Thank you very much for buying this SHARP product. Before using your SHARP refrigerator, please read this operation manual to ensure that you gain the maximum benefit from it. • This refrigerator is intended for making ice cubes, refrigerating and freezing food.
directly. Do not use an extension cord or adapter plug. ■■Connect the power plug to the socket with the required
rated voltage. ■■Connect the earth pin to the earth terminal properly.
• This refrigerator is for household use only, with ambient temperature indicated in the table. The climate class is specified on the rating plate. The refrigerator is fully functional at the ambient temperature range of the indicated climate class. If the refrigerator is used at colder temperatures, the refrigerator will not be damaged up to a temperature ;10°C to 32°C
MMPQ2222A;FFB2222A;中文规格书,Datasheet资料

ON CHARACTERISTICS
hFE DC Current Gain IC = 0.1 mA, VCE = 10 V IC = 1.0 mA, VCE = 10 V IC = 10 mA, VCE = 10 V IC = 150 mA, VCE = 10 V* IC = 150 mA, VCE = 1.0 V* IC = 500 mA, VCE = 10 V* IC = 150 mA, IB = 15 mA IC = 500 mA, IB = 50 mA IC = 150 mA, IB = 15 mA IC = 500 mA, IB = 50 mA 35 50 75 100 50 40
*Pulse Test: Pulse Width ≤ 300 µs, Duty Cycle ≤ 2.0%
Spice Model
NPN (Is=14.34f Xti=3 Eg=1.11 Vaf=74.03 Bf=255.9 Ne=1.307 Ise=14.34f Ikf=.2847 Xtb=1.5 Br=6.092 Nc=2 Isc=0 Ikr=0 Rc=1 Cjc=7.306p Mjc=.3416 Vjc=.75 Fc=.5 Cje=22.01p Mje=.377 Vje=.75 Tr=46.91n Tf=411.1p Itf=.6 Vtf=1.7 Xtf=3 Rb=10)
Thermal Characteristics
Symbol
PD RθJA
TA = 25°C unless otherwise noted
Characteristic
Total Device Dissipation Derate above 25°C Thermal Resistance, Junction to Ambient Effective 4 Die Each Die FFB2222A 300 2.4 415
CDRH62中文资料

CDRH621.外形1-1.寸法図(mm)* 公差のない寸法は、参考値とする。
1-2.捺印表示例 1-3. 推奨ランド寸法(mm)2.コイル仕様2-1.端子接続図(裏面図) 電極(端子)間の隙間はシルク処理をして御使用下さい。
捺印位置不定製造密番compliance Cd:Max.0.01wt%others:Max.0.1wt%RoHS12-2.電気的特性 Ⅰ(リール梱包の場合)NO. 品 名 表示 インダクタンス[以内]※1D.C.R.(Ω)[以下](at 20℃)定格電流(A)※2スミダコード01 CDRH62NP-6R8NC 6R8 6.8μH ± 25% 0.12 1.57 -006602 CDRH62NP-8R2NC 8R2 8.2μH ± 25% 0.13 1.38 -006703 CDRH62NP-1ØØMC 100 10 μH ± 20% 0.17 1.28 -006904 CDRH62NP-12ØMC 120 12 μH ± 20% 0.18 1.19 -007005 CDRH62NP-15ØMC 150 15 μH ± 20% 0.26 0.97 -007106 CDRH62NP-18ØMC 180 18 μH ± 20% 0.30 0.94 -007207 CDRH62NP-22ØMC 220 22 μH ± 20% 0.38 0.81 -007308 CDRH62NP-27ØMC 270 27 μH ± 20% 0.43 0.71 -007409 CDRH62NP-33ØMC 330 33 μH ± 20% 0.48 0.64 -007510 CDRH62NP-39ØMC 390 39 μH ± 20% 0.69 0.59 -007611 CDRH62NP-47ØMC 470 47 μH ± 20% 0.77 0.54 -007712 CDRH62NP-56ØMC 560 56 μH ± 20% 0.85 0.52 -007813 CDRH62NP-68ØMC 680 68 μH ± 20% 1.21 0.49 -008114 CDRH62NP-82ØMC 820 82 μH ± 20% 1.42 0.41 -008215 CDRH62NP-1Ø1MC 101 100μH ± 20% 1.50 0.39 -008316 CDRH62NP-121MC 121 120μH ± 20% 2.10 0.30 -008417 CDRH62NP-151MC 151 150μH ± 20% 2.33 0.28 -008518 CDRH62NP-181MC 181 180μH ± 20% 3.20 0.25 -008619 CDRH62NP-221MC 221 220μH ± 20% 3.69 0.23 -008720 CDRH62NP-271MC 271 270μH ± 20% 4.89 0.20 -008821 CDRH62NP-331MC 331 330μH ± 20% 5.42 0.18 -00892-3.電気的特性 Ⅱ (箱梱包の場合)NO. 品 名 表示 インダクタンス[以内]※1D.C.R.(Ω)[以下](at 20℃)定格電流(A)※2スミダコード22 CDRH62NP-6R8NB 6R8 6.8μH ± 25% 0.12 1.57 -009023 CDRH62NP-8R2NB 8R2 8.2μH ± 25% 0.13 1.38 -009224 CDRH62NP-1ØØMB 100 10 μH ± 20% 0.17 1.28 -009325 CDRH62NP-12ØMB 120 12 μH ± 20% 0.18 1.19 -009426 CDRH62NP-15ØMB 150 15 μH ± 20% 0.26 0.97 -009527 CDRH62NP-18ØMB 180 18 μH ± 20% 0.30 0.94 -009628 CDRH62NP-22ØMB 220 22 μH ± 20% 0.38 0.81 -009729 CDRH62NP-27ØMB 270 27 μH ± 20% 0.43 0.71 -009830 CDRH62NP-33ØMB 330 33 μH ± 20% 0.48 0.64 -009931 CDRH62NP-39ØMB 390 39 μH ± 20% 0.69 0.59 -010032 CDRH62NP-47ØMB 470 47 μH ± 20% 0.77 0.54 -010133 CDRH62NP-56ØMB 560 56 μH ± 20% 0.85 0.52 -010334 CDRH62NP-68ØMB 680 68 μH ± 20% 1.21 0.49 -010435 CDRH62NP-82ØMB 820 82 μH ± 20% 1.42 0.41 -010536 CDRH62NP-1Ø1MB 101 100μH ± 20% 1.50 0.39 -010637 CDRH62NP-121MB 121 120μH ± 20% 2.10 0.30 -010738 CDRH62NP-151MB 151 150μH ± 20% 2.33 0.28 -010839 CDRH62NP-181MB 181 180μH ± 20% 3.20 0.25 -010940 CDRH62NP-221MB 221 220μH ± 20% 3.69 0.23 -011041 CDRH62NP-271MB 271 270μH ± 20% 4.89 0.20 -011142 CDRH62NP-331MB 331 330μH ± 20% 5.42 0.18 -0112※1: 測定周波数 L 6.8μH ~ 8.2μH ; at 7.96 MHz10μH ~ 82μH ; at 2.52 MHz100μH ~ 330μH ; at 1 kHz※2: 定格電流は直流重畳特性に於て、インダクタンスが公称値より70%となる電流もしくは直流電流を 流した時のコイルの発熱が△t=40℃となる電流値の少ない方の値。
Modicon M221 TM221C16R 产品数据手册说明书

TM221C16R.i s c l ai m e r : T h i s d o c u m e n t a t i o n i s n o t i n t e n d e d a s a s u b s t i t u t e f o r a n d i s n o t t o b e u s e d f o r d e t e r m i n i n g s u i t a b i l i t y o r r e l i a b i l i t y o f t h e s e p r o d u c t s f o r s p e c i f i c u s e r a p p l i c a t i o n sProduct datasheetCharacteristicsTM221C16Rcontroller M221 16 IO relayMainRange of productModicon M221Product or component type Logic controller [Us] rated supply voltage 100...240 V ACDiscrete input number 9 discrete input conforming to IEC 61131-2 Type 1Analogue input number 2 at input range: 0...10 V Discrete output type Relay normally open Discrete output number 7 relay Discrete output voltage 5...125 V DC 5...250 V AC Discrete output current2 AComplementaryDiscrete I/O number16Number of I/O expansion module <= 4 for transistor output <= 4 for relay output Supply voltage limits 85...264 V Network frequency 50/60 Hz Inrush current<= 40 APower consumption in VA <= 46 VA at 100...240 V with max number of I/O expansion module <= 31 VA at 100...240 V without I/O expansion module Power supply output current 0.325 A at 5 V for expansion bus 0.12 A at 24 V for expansion bus Discrete input logic Sink or source (positive/negative)Discrete input voltage 24 V Discrete input voltage type DC Analogue input resolution 10 bits LSB value 10 mVConversion time1 ms per channel + 1 controller cycle time for analog input Permitted overload on inputs+/- 30 V DC for analog input with 5 min maximum +/- 13 V DC for analog input permanentVoltage state1 guaranteed>= 15 V for inputCurrent state 1 guaranteed>= 2.6 mA for fast input>= 4.2 mA for discrete inputVoltage state 0 guaranteed<= 5 V for inputCurrent state 0 guaranteed<= 1.3 mA for discrete input<= 0.6 mA for fast inputDiscrete input current7 mA for discrete input5 mA for fast inputInput impedance 4.9 kOhm for fast input3.4 kOhm for discrete input100 kOhm for analog inputResponse time10 ms turn-on operation for output35 µs turn-off operation for input; I2...I5 terminal10 ms turn-off operation for output5 µs turn-on operation for fast input; I0, I1, I6, I7 terminal35 µs turn-on operation for input; other terminals terminal5 µs turn-off operation for fast input; I0, I1, I6, I7 terminal100 µs turn-off operation for input; other terminals terminal Configurable filtering time0 ms for input12 ms for input3 ms for inputOutput voltage limits125 V DC277 V ACCurrent per output common 6 A at COM 1 termnal7 A at COM 0 termnalAbsolute accuracy error+/- 1 % of full scale for analog inputElectrical durability Inductive AC-15, (cos phi = 0.35) 240 V / 120 VA : 100000 cyclesResistive DC-12, 24 V / 48 W : 100000 cyclesResistive AC-12, 120 V / 240 VA : 100000 cyclesInductive AC-15, (cos phi = 0.35) 240 V / 36 VA : 300000 cyclesResistive AC-12, 120 V / 80 VA : 300000 cyclesInductive (L/R = 7 ms) DC-13, 24 V / 24 W : 100000 cyclesResistive DC-12, 24 V / 16 W : 300000 cyclesInductive (L/R = 7 ms) DC-13, 24 V / 7.2 W : 300000 cyclesInductive AC-14, (cos phi = 0.7) 240 V / 240 VA : 100000 cyclesInductive AC-15, (cos phi = 0.35) 120 V / 60 VA : 100000 cyclesInductive AC-14, (cos phi = 0.7) 240 V / 72 VA : 300000 cyclesInductive AC-15, (cos phi = 0.35) 120 V / 18 VA : 300000 cyclesResistive AC-12, 240 V / 480 VA : 100000 cyclesInductive AC-14, (cos phi = 0.7) 120 V / 120 VA : 100000 cyclesResistive AC-12, 240 V / 160 VA : 300000 cyclesInductive AC-14, (cos phi = 0.7) 120 V / 36 VA : 300000 cycles Switching frequency20 switching operations/minute with maximum load Mechanical durability>= 20000000 cycles for relay outputMinimum load 1 mA at 5 V DC for relay outputProtection type Without protection at 5 AReset time 1 sMemory capacity256 kB for user application and data RAM with 10000 instructions256 kB for internal variables RAMData backed up256 kB built-in flash memory for backup of application and data Data storage equipment 2 GB SD card optionalBattery type BR2032 lithium non-rechargeable, battery life: 4 yrBackup time 1 year at 25 °C by interruption of power supplyExecution time for 1 KInstruction0.3 ms for event and periodic taskExecution time per instruction0.2 µs BooleanExct time for event task60 µs response timeMaximum size of object areas512 %M memory bits512 %KW constant words255 %TM timers255 %C counters8000 %MW memory wordsRealtime clock WithClock drift<= 30 s/month at 25 °CRegulation loop Adjustable PID regulator up to 14 simultaneous loopsCounting input number 4 fast input (HSC mode) (counting frequency: 100 kHz), counting capacity: 32 bitsControl signal type Frequency meterSingle phaseDual phase (pulse/direction)Dual phase (quadrature)Integrated connection type USB port with connector mini B USB 2.0Non isolated serial link "serial 1" with connector RJ45 and interface RS485Non isolated serial link "serial 2" with connector RJ45 and interface RS232/RS485Supply Serial serial link supply at 5 V 200 mATransmission rate 1.2...115.2 kbit/s (115.2 kbit/s by default) for bus length of 15 m - communication protocol: RS4851.2...115.2 kbit/s (115.2 kbit/s by default) for bus length of 3 m - communication protocol: RS232480 Mbit/s - communication protocol: USBCommunication port protocol USB port : USB protocol - SoMachine-NetworkNon isolated serial link : Modbus protocol master/slave - RTU/ASCII or SoMachine-Network Local signalling 1 LED green for SD card access (SD)1 LED red for BAT1 LED green for SL11 LED green for SL21 LED per channel green for I/O state1 LED red for module error (ERR)1 LED green for PWR1 LED green for RUNElectrical connection Mini B USB 2.0 connector for a programming terminalTerminal block, 3 terminal(s) for connecting the 24 V DC power supplyConnector, 4 terminal(s) for analogue inputsRemovable screw terminal block for inputsRemovable screw terminal block for outputsCable length<= 10 m shielded cable for fast input<= 30 m unshielded cable for output<= 30 m unshielded cable for digital input<= 1 m unshielded cable for analog inputInsulation2300 V AC between output and internal logicNon-insulated between analogue inputs500 V AC between input and internal logicNon-insulated between analogue input and internal logic1500 V AC between supply and ground500 V AC between sensor power supply and ground500 V AC between input and ground1500 V AC between output and ground2300 V AC between supply and internal logic500 V AC between sensor power supply and internal logic500 V AC between Ethernet terminal and internal logic2300 V AC between supply and sensor power supplyMarking CESensor power supply DC at 250 mA supplied by the controllerMounting support Top hat type TH35-15 rail conforming to IEC 60715Top hat type TH35-7.5 rail conforming to IEC 60715Plate or panel with fixing kitHeight90 mmDepth70 mmWidth95 mmProduct weight0.346 kgEnvironmentStandards EN/IEC 61010-2-201EN/IEC 61131-2EN/IEC 60664-1Product certifications RCMIACS E10DNV-GLcULusCSALRABSEACEnvironmental characteristic Ordinary and hazardous locationResistance to electrostatic discharge 4 kV on contact conforming to EN/IEC 61000-4-28 kV in air conforming to EN/IEC 61000-4-2Resistance to electromagnetic fields10 V/m ( 80 MHz...1 GHz) conforming to EN/IEC 61000-4-33 V/m ( 1.4 GHz...2 GHz) conforming to EN/IEC 61000-4-31 V/m ( 2...2.7 GHz) conforming to EN/IEC 61000-4-3Resistance to magnetic fields 30 A/m at 50...60 Hz conforming to EN/IEC 61000-4-8Resistance to fast transients2 kV for power lines conforming to EN/IEC 61000-4-42 kV for relay output conforming to EN/IEC 61000-4-41 kV for Ethernet line conforming to EN/IEC 61000-4-41 kV for serial link conforming to EN/IEC 61000-4-41 kV for I/O conforming to EN/IEC 61000-4-4Surge withstand2 kV for power lines (AC) in common mode conforming to EN/IEC 61000-4-52 kV for relay output in common mode conforming to EN/IEC 61000-4-51 kV for I/O in common mode conforming to EN/IEC 61000-4-51 kV for shielded cable in common mode conforming to EN/IEC 61000-4-50.5 kV for power lines (DC) in differential mode conforming to EN/IEC 61000-4-51 kV for power lines (AC) in differential mode conforming to EN/IEC 61000-4-51 kV for relay output in differential mode conforming to EN/IEC 61000-4-50.5 kV for power lines (DC) in common mode conforming to EN/IEC 61000-4-5Resistance to conducted disturbances,induced by radio frequency fields10 Vrms (0.15...80 MHz) conforming to EN/IEC 61000-4-63 Vrms (0.1...80 MHz) conforming to Marine specification (LR, ABS, DNV, GL)10 Vrms (spot frequency (2, 3, 4, 6.2, 8.2, 12.6, 16.5, 18.8, 22, 25 MHz)) conforming to Marine specification (LR, ABS, DNV, GL)Electromagnetic emissionConducted emissions conforming to EN/IEC 55011 power lines (AC), 0.15...0.5 MHz : 79 dBμV/m QP/66 dBμV/m AVConducted emissions conforming to EN/IEC 55011 power lines (AC), 0.5...300 MHz : 73 dBμV/m QP/60 dBμV/m AVConducted emissions conforming to EN/IEC 55011 power lines, 10...150 kHz : 120...69 dBµV/m QP Conducted emissions conforming to EN/IEC 55011 power lines, 150 kHz...1.5 MHz : 79...63 dBμV/m QPConducted emissions conforming to EN/IEC 55011 power lines, 1.5...30 MHz : 63 dBμV/m QP Radiated emissions conforming to EN/IEC 55011 class A 10 m, 30...230 MHz : 40 dBμV/m QP Radiated emissions conforming to EN/IEC 55011 class A 10 m, 200 MHz...1 GHz : 47 dBμV/m QP Immunity to microbreaks10 msAmbient air temperature for operation -10...55 °C for horizontal installation -10...35 °C for vertical installation Ambient air temperature for storage -25...70 °CRelative humidity 10...95 % without condensation in operation 10...95 % without condensation in storage IP degree of protection IP20 with protective cover in place Pollution degree <= 2Operating altitude 0...2000 m Storage altitude 0...3000 mVibration resistance3.5 mm (vibration frequency: 5...8.4 Hz) on symmetrical rail 1 gn (vibration frequency: 8.4...150 Hz) on symmetrical rail 3.5 mm (vibration frequency:5...8.4 Hz) on panel mounting 1 gn (vibration frequency: 8.4...150 Hz) on panel mounting Shock resistance98 m/s² (test wave duration:11 ms)Offer SustainabilitySustainable offer status Green Premium productRoHS (date code: YYWW)Compliant - since 1415 - Schneider Electric declaration of conformity Schneider Electric declaration of conformity REAChReference not containing SVHC above the threshold Reference not containing SVHC above the threshold Product environmental profileAvailableProduct environmental Product end of life instructionsAvailableEnd of life manualProduct datasheetTM221C16R Dimensions DrawingsDimensionsProduct datasheetTM221C16R Mounting and ClearanceMounting on a RailProduct datasheetMounting and ClearanceTM221C16RDirect Mounting on a Panel Surface(1)Install a mounting stripMounting Hole LayoutProduct datasheetTM221C16R Mounting and ClearanceMountingCorrect Mounting PositionAcceptable Mounting PositionIncorrect Mounting PositionProduct datasheetTM221C16R Mounting and ClearanceClearanceDigital InputsWiring Diagram (Positive Logic)(*)Type T fuseWiring Diagram (Negative Logic)(*)Type T fuseConnection of the Fast InputsI0, I1, I6, I7Relay OutputsNegative Logic (Sink)(*)Type T fuse(1)The COM1 and COM2 terminals are not connected internally.(2)To improve the life time of the contacts, and to protect from potential inductive load damage, you must connect a free wheeling diode in parallel to each in B Sink wiring (negative logic)Positive Logic (Source)(*)Type T fuse(1)The COM1 and COM2 terminals are not connected internally.(2)To improve the life time of the contacts, and to protect from potential inductive load damage, you must connect a free wheeling diode in parallel to each in A Source wiring (positive logic)Analog InputsUSB Mini-B ConnectionSL1 ConnectionSL1N.C.: not connected* : 5 Vdc delivered by the controller. Do not connect.SL2 ConnectionN.C.: not connectedPerformance CurvesDerating CurvesEmbedded Digital Inputs (No Cartridge)X :Ambient temperatureY :Input simultaneous ON ratioEmbedded Digital Inputs (with Cartridge)X :Ambient temperatureY :Input simultaneous ON ratioTM221C16R.。
埃尔克斯-霍尔斯 CN6221 限位控制器说明书

1⁄16 DIN Limit ControllerU Dual Display U Universal Input U High or Low Limit U D igital Input for Remote Reset U R S485 Communications (Optional)U Alarms (Optional)U R etransmission Output (Optional)The CN6221 Series is an FM approved limit controller that can be configured either as a high limit or as a low limit controller. The CN6221 features universal input, 2 alarm outputs, retransmission output, a timer to count the total time the setpoint is exceeded, and a register to retain the maximum. The RS485 communication interface is availableas an option.Specifications Power SupplyVoltage: 100 to 240 Vac (±10%), Frequency: 50 or 60 HzMaximum Power Consumption: 8 Va max (4 W maximum)Memory: Non-volatile memory Withstanding Voltage (Between Primary and Secondary Terminals): 1500 Vac for 1 min (see Note 1)Insulation Resistance (Between Primary and Secondary Terminals): 20 M Ω or more at 500 Vdc (see Note 1)Note 1: The primary terminals are the power supply terminals and relay output terminals. The secondary terminals are the analog input and output terminals, the voltage pulse output terminals, and the contact input terminals.Contact InputFunction: Resetting “exceeded status”Input: 1 pointType: Non-voltage contact or transistor contact Contact Capacity: At least 12V/10 mA On/Off Judgment: On state for 1 k Ω or less; off state for 20 k Ω or greater Measured Value (PV)Input: 1 point Type: Universal; selectable by software Accuracy (At 23 ±2°C Ambient Temperature): Thermocouple: ±2°C ±1digit At -200 to -100°C: ±4°C At -100 to 0°C: ±3°C Types R and S: ±5°C [±9°C for 0 to 500°C (32 to 932°F)] Type B: ±9°C (accuracy is not guaranteed for 0 to 400°C) RTD: ±1°C ±1digit Voltage (mV, V): ±0.3% ±1digit Sampling Period for Measured Value Input: 500 ms Burn-Out Detection: Functions for thermocouple or RTD input (burn-out upscale only; cannot be switched off)Input Resistance: 1 M Ω or greater for thermocouple or DC mV inputs; approximately 1 M Ω for DC V input Maximum Allowable Signal Source Resistance: 250 Ω for thermocouple or DC mV input; 2 k Ω for DC V input Maximum Allowable Wiring Resistance for RTD Input: 10 Ω/wire (resistance values of 3 wires must be the same)Allowable Input Voltage: ±10 Vdc for thermocouple or DC mV input; ±20 Vdc for DC V input CN6221-R shown smaller than actual size.Noise Rejection Ratio:Normal Mode Noise: Minimum40 dB (50/60 Hz)Common Mode Noise: Minimum 120 dB (90 dB for DC V input) Reference Juction Error Compensation: ±1.5°C (at 15 to 35°C), ±2.0°C (at 0 to 50°C)Note: The reference junction compensation cannot be switched offApplicable Standards: RTD, Thermocouple, JIS/IEC/DIN (ITS90) Control OutputOutput: 1 pointType: Relay contactContact Capacity: 3 A @ 240 Vac or 3 A @ 30 Vdc (with resistance load) Note: The control output relay cannot be replaced by users.Alarm Functions (Optional) Alarm Types: 22 types (waiting action can be set by software): PV high-limit, PV low-limit, deviation high-limit, deviation low-limit, de-energized on deviation highdlimit, deenergized on deviation low-limit, deviation high- and low-limits, high- and low-limits within deviation, de-energized on PV high-limit, de-energized on PV low-limit, fault diagnosis output, fail outputAlarm Output: 2 relay contactsRelay Contact Capacity: 1 A @ 240 Vac or 1 A @ 30 Vdc (with resistance load) Note: The alarm output relays cannot be replaced by users. Retransmission Output (Optional)The retransmission output is provided only when the “/RET” option is specified. Output Signal: Measured value in4 to 20 mAdcMaximum Load Resistance: 600ΩOutput Accuracy: ±0.3% of span(at 23 ±2°C ambient temperature) Communication Interface Applicable Standards: Complies with EIA RS485Number of Controllers: Up to 31 Maximum Communication Distance: 1200 m (3937')Communication Method: 2-wirehalf-duplex, start-stop synchronization, non-proceduralConstruction, Mounting, and Wiring Construction: Dust-proof and drip-proof front panel conforming to IP65; for side-by-side close installation, controller loses its dust-proof and drip-proof protectionCasing: ABS resin and polycarbonate Case Color: BlackMounting: Flush panel mounting Environmental Conditions Normal Operating ConditionsWarm-Up Time: At least 30 minutesAmbient Temperature: 0 to 50°C(0 to 40°C when mounted side-by-side)Rate of Change of Temperature:10°C/h or lessAmbient Humidity: 20 to 90% RH(no condensation allowed)Magnetic Field: 400 A/m or lessContinuous Vibrations of 5 to 14 Hz:Amplitude of 1.2 mm or lessContinuous Vibrations of 14 to 150 Hz:4.9 m/s2 (0.5 G) or lessShort-Period Vibrations: 14.7 m/s2(1.5 G) for 15 seconds or lessShock: 98 m/s2 (10 G) for 11 ms or lessMounting Angle: Upward incline ofup to 30 degrees; no downward inclineAltitude:≤2000 m above sea levelMaximum Effects from OperatingConditionsTemperature EffectsThermocouple, mVdc and VdcInputs: ±2 µV/°C or ±0.02% ofFS/°C, whichever is the largerResistance TemperatureDetector: ±0.05°C/°CAnalog Output: ±0.05% of FS/°CEffect from Fluctuation of PowerSupply Voltage (Within RatedVoltage Range)Analog Input: ±0.2 µV/V or ±0.002%of FS/V, whichever is largerAnalog Output: ±0.05% of FS/VTransportation and StorageConditionsTemperature: -25 to 70°C (-13 to 158°F)Humidity: 5 to 95% RH(no condensation allowed)Shock: Package drop height 90 cm (35")(when packed in the dedicated package)Accessories (Field Installable)Ordering Example: CN6221-R-C4, single output limit controller, mechanical relay, RS485 communications.Dimensions: mm (inch)。
COM Express Type 6 PMC XMC Ultra Lite Carrier 用户指南

COM Express® PMC/XMC Ultra LiteCarrierConnect Tech Inc.Tel:519-836-129142 Arrow Road Toll:800-426-8979 (North America only)Guelph, Ontario Fax:519-836-4878N1K 1S6 Email:********************* *********************** CTIM-00431 Revision 0.06 2018-01-08Table of ContentsPreface (4)Disclaimer (4)Customer Support Overview (4)Contact Information (4)Limited Product Warranty (5)Copyright Notice (5)Trademark Acknowledgment (5)ESD Warning (6)Revision History (6)Introduction (7)Product Features and Specifications (7)Product Overview (8)Block Diagram (8)Connector Locations (9)Connector Summary (10)Jumper Summary (11)Detailed Feature Pinouts and Functional Descriptions (11)Serial/GPIO Connector (11)VGA Video Connector (12)COM Express Module Connector (12)LVDS Video Connector (13)miniPCIe/mSATA Slots (14)Dual Function miniPCIe/mSATA Slots (14)Jumper Selection (14)Half and Full Length miniPCIe/mSATA module Installation (14)External SATA Connector (16)CPU Fan (16)System and Miscellaneous Connector (17)SIM Socket (17)HD Audio Connector (18)Software Support for the CS4207 (18)USB 2.0 Connector (18)DisplayPort Connector (19)HDMI / DVI / VGA from DisplayPort++ (19)10/100/1000 Ethernet (GBE) (20)USB 3.0/2.0 Connector (20)microSD CARD Connector (21)Power Connector (21)SATA/LVDS Power Connector (22)XMC Connector (22)PMC Connector (23)Typical Hardware Installation Procedure (24)On-board Indicator LEDs (24)Jumper Settings (25)J1 Jumper – LVDS PANEL (25)J2 Jumper – RTC Battery (25)J3 Jumper – RTC Battery (25)J6 Jumper – Shutdown Battery (25)J6 Jumper – Power Control (26)J4 Jumper – mSATA/miniPCIe (26)J8 Jumper – USB (26)J7 Jumper – GPIO-V (26)Thermal & Current Consumption Details (27)Thermal Details (27)Mechanical Details (27)Cables and Cable Kit Information (28)Cable Kits (28)CKG028 –“Full” Cable Kit (28)CKG021 –“Starter” Cable Kit (28)PrefaceDisclaimerThe info rmation contained within this user’s guide, including but not limited to any productspecification, is subject to change without notice.Connect Tech assumes no liability for any damages incurred directly or indirectly from anytechnical or typographical errors or omissions contained herein or for discrepancies between theproduct and the user’s guide.Customer Support OverviewIf you experience difficulties after reading the manual and/or using the product, contact theConnect Tech reseller from which you purchased the product. In most cases the reseller can help you with product installation and difficulties. In the event that the reseller is unable to resolveyour problem, our highly qualified support staff can assist you. Our support section is available24 hours a day, 7 days a week on our website at: /support/resource-center/.See the contact information section below for more information on how to contact us directly. Our technical support is always free.Contact InformationMail/CourierConnect Tech Inc.Technical Support42 Arrow RoadGuelph, OntarioCanada N1K 1S6Email/Internet********************************************Telephone/FacsimileTechnical Support representatives are ready to answer your call Monday through Friday, from8:30 a.m. to 5:00 p.m. Eastern Standard Time. Our numbers for calls are:Toll Free: 800-426-8979 (North America only)Telephone: 519-836-1291 (Live assistance available 8:30 a.m. to 5:00 p.m. EST,Monday to Friday)Facsimile: 519-836-4878 (on-line 24 hours)Limited Product WarrantyConnect Tech Inc. provides a two-year Warranty for the COM Express® PMC/XMC Ultra LiteCarrier. Should this product, in Connect Tech Inc.'s opinion, fail to be in good working orderduring the warranty period, Connect Tech Inc. will, at its option, repair or replace this product atno charge, provided that the product has not been subjected to abuse, misuse, accident, disaster or non-Connect Tech Inc. authorized modification or repair.You may obtain warranty service by delivering this product to an authorized Connect Tech Inc.business partner or to Connect Tech Inc. along with proof of purchase. Product returned toConnect Tech Inc. must be pre-authorized by Connect Tech Inc. with an RMA (Return MaterialAuthorization) number marked on the outside of the package and sent prepaid, insured andpackaged for safe shipment. Connect Tech Inc. will return this product by prepaid groundshipment service.The Connect Tech Inc. Limited Warranty is only valid over the serviceable life of the product.This is defined as the period during which all components are available. Should the product prove to be irreparable, Connect Tech Inc. reserves the right to substitute an equivalent product ifavailable or to retract the Warranty if no replacement is available.The above warranty is the only warranty authorized by Connect Tech Inc. Under nocircumstances will Connect Tech Inc. be liable in any way for any damages, including any lostprofits, lost savings or other incidental or consequential damages arising out of the use of, orinability to use, such product.Copyright NoticeThe information contained in this document is subject to change without notice. Connect TechInc. shall not be liable for errors contained herein or for incidental consequential damages inconnection with the furnishing, performance, or use of this material. This document containsproprietary information that is protected by copyright. All rights are reserved. No part of thisdocument may be photocopied, reproduced, or translated to another language without the priorwritten consent of Connect Tech, Inc.Copyright 2016 by Connect Tech, Inc.Trademark AcknowledgmentConnect Tech, Inc. acknowledges all trademarks, registered trademarks and/or copyrights referred to in this document as the property of their respective owners.Not listing all possible trademarks or copyright acknowledgments does not constitute a lack ofacknowledgment to the rightful owners of the trademarks and copyrights mentioned in thisdocument.ESD WarningElectronic components and circuits are sensitive toElectroStatic Discharge (ESD). When handling any circuitboard assemblies including Connect Tech COM Expresscarrier assemblies, it is recommended that ESD safetyprecautions be observed. ESD safe best practices include,but are not limited to:∙Leaving circuit boards in their antistatic packaginguntil they are ready to be installed.∙Using a grounded wrist strap when handling circuitboards, at a minimum you should touch a groundedmetal object to dissipate any static charge that maybe present on you.∙Only handling circuit boards in ESD safe areas,which may include ESD floor and table mats, wriststrap stations and ESD safe lab coats.∙Avoiding handling circuit boards in carpeted areas.∙Try to handle the board by the edges, avoidingcontact with components.Revision HistoryIntroductionConnect Tech’s PMC/XMC Ultra Lite Carrier is an extremely small carrier board featuringrugged, locking connectors and offers the ultimate durability. The PMC/XMC Ultra Lite Carrier is ideal for space constrained applications, harsh environments, demanding conditions and supports extended temperature ranges of -40°C to +85°C.Product Features and SpecificationsProduct Overview Block DiagramConnector LocationsConnector SummaryJumper SummaryDetailed Feature Pinouts and Functional Descriptions Serial/GPIO ConnectorThe CCG013 allows access to the COM Express modules GPIO by routing them out to a GPIO header. Also present is a direct connected RS-232 signal that utilizes the COM Express module’s UART.VGA Video ConnectorTo allow for greater flexibility, the CCG013 provides a VGA Video output. Routed directly from the COM Express Type 6, this provides additional video output formats for operation.COM Express Module ConnectorThe processor and chipset are implemented on the CCG013s COM Express Type 6 module, whichconnects to the CCG013 Carrier Board via a Tyco fine pitch stacking connector.LVDS Video ConnectorThe CCG013 provides dual 18 or 24 bit LVDS display channels via P9, which are connected directly from the COM Express Type 6 module.Note [1]: This voltage can be selected from Jumper J2 to be +3.3V, +5V, or +12VminiPCIe/mSATA SlotsDual Function miniPCIe/mSATA SlotsThe CCG013 has two special dual purpose miniPCIe/mSATA slots. Each of these slots can accept either a miniPCIe module or an mSATA SSD module. These slots have special circuitry that allows for the selection between connecting PCIe lanes or SATA lanes.Each of these slots are also provided with a USB 2.0 in addition to the PCIe as per the mini PCIe specification, see below for a block diagram of the slots functionality.miniPCIe/mSATA Dual Functionality Diagram**Please note, a SIM card is only availabe on miniPCIe/mSATA slot 0Jumper SelectionHalf and Full Length miniPCIe/mSATA module InstallationThe CCG013 comes with dual mounting solutions to allow for the population of a half and a full length module. If you would prefer to have a single slot or both slots populated with half-length hardware at the ****************************************************************************.External SATA ConnectorThe CCG013 provides two SATA plugs that are SATA-PCIe/104 switched. Please see SATA-PCIe/104 switching description for additional details.CPU FanSystem and Miscellaneous ConnectorThe System header can be used to connect the power button, reset button, and LED’s required to monitor the module performance or state.SIM SocketHD Audio ConnectorThe CCG013s features HD Audio capabilities with the assistance of the Cirrus Logic CS4207 Codec device. From the codec, 1 microphone input and 1 headphone output are available.Software Support for the CS4207The audio codec used on the PMC/XMC Ultra Lite Carrier board is the CS4207 from Cirrus Logic.Additional drivers will be needed to properly operate audio on the PMC/XMC Ultra Lite Carrier . Some downloadable links can be found below.Windows XP Driver :/en/support/lic/lic3.html?uri=/en/pubs/software/CS4207_WinXP_1-0-0-38.zip Windows 7/8 Driver :/en/support/lic/lic3.html?uri=/en/pubs/software/CS4207_LogoedDriverPackage_6-6001-1-39.zipLinux Driver : Included in kernels 2.6.30 and up.USB 2.0 ConnectorThe CCG013 has multiple USB Ports. USB 2.0 Port 6 is sourced directly from the COM Express module. USB 2.0 Port 7 however has multiple functionality options. Using Jumper J727, Port 7 can either be a Client USB, or it can be used to connect the SD Card to the COM Express module.Note [2]: USB 2.0 Port 7 can be optionally be used as client USB. Simply remove the Jumper from J8A to enable Note [3]: USB 2.0 Port 7 can be optionally be used to enable the SD Card. Simply remove the Jumper from J8B to enableDisplayPort ConnectorTwo DisplayPort++ connections from the COM Express module are available and can be configured to output DisplayPort, or HDMI/DVI/VGA through the use of a dongle. The configuration of each interface is setup via the COM Express module’s BIOS settings. Refer to the COM Express module’s documentation for more details.Note [4]: Cable assembly must tie high (+3.3V) for adapter output (HDMI/DVI/VGA) and low (GND) for DisplayPort outputHDMI / DVI / VGA from DisplayPort++The COM Express Type 10 Mini Carrier’s DisplayPort++ connector can be used for display outputs other than DisplayPort. The use of HDMI, DVI or VGA can be done through a simple dongle or cable assembly like the ones shown below. These can be purchased from any OEM vendor (such as ) or directly through Connect Tech.10/100/1000 Ethernet (GBE)The CCG013 features dual 10/100/1000 Ethernet Ports. GBE 0 is sourced from the COM Express module. Meanwhile, GBE 1 is sourced from an Intel 82574 PCIe PHY Controller located on the CCG013 Carrier Board, connected via PCIe x1 to the COM Express module.USB 3.0/2.0 ConnectorThe CCG013 provides up to a maximum of 4 USB 3.0 Ports. The USB 3.0 signals are sourced directlyfrom the COM Express Type 6 module, and run through a Pericom Semiconductor PI3EQX7502AIZDE re-driver. Over current protection, power supply filtering and ESD protection is provided.microSD CARD ConnectorThe CCG013 provides a microSD Card Slot. This microSD can be accessed by the COM Express module[9]Note [9]: USB 2.0 Port 7 can be optionally be used to enable the SD Card. Simply remove the Jumper from J8B to enablePower ConnectorThe CCG013 accepts a single power input to power all on-board devices. The CCG013 accepts a wide input range of +12V to +48V for operation.SATA/LVDS Power ConnectorThe CCG013 also provides power for external SATA Hard Drives and/or LVDS screens. The power connectors can be found next the External SATA connectors.XMC ConnectorThe CCG016 allows for I/O expansion with two XMC slots, both capable of x8 PCI Express connectivity.The XMC connectors comply with the VITA 42.0/42.3 standard. +VPWR is +5V, with an option to move to +12V +VPWR power.PMC ConnectorThe CCG016 allows for I/O expansion with two PMC slots, both capable of 32bit PCI connectivity. TheTypical Hardware Installation Procedure1.Ensure all external system power supplies are OFF.2.Install the necessary cables for the application. At a minimum, this would include:a)Power cable to the input power connectorb)Connect a video display cablec)Keyboard and mouse via USBd)SATA or mSATA hard driveFor additional information on the relevant cables, please see the Cables and Interconnects section of this manual.3.Connect the power cable to power supply4.Ensure your power supply is in the range of +12V to +48V DC5.Switch ON the power supply. DO NOT power up your system by plugging in live power.On-board Indicator LEDsThe CCG013 has 10 on-board indicator LEDs.** D32 Only on when on-board NAND option is implemented.Jumper SettingsThe CCG013 utilizes jumper blocks to control various features like LVDS, mSATA/miniPCIe switching, and Client USB.J1 Jumper – LVDS PANELJ2 Jumper – RTC BatteryJ3 Jumper – RTC BatteryJ6 Jumper – Shutdown BatteryJ6 Jumper – Power ControlJ4 Jumper – mSATA/miniPCIeNote [11]: See mSATA/miniPCIe Slots for detailed description of functionalityJ8 Jumper – USBJ7 Jumper – GPIO-VThermal & Current Consumption DetailsBelow are measurements taken with the CCG013 running in various configurations. Some values will change depending on what COM Express module, and what PMC/XMC modules are installed. Please refer to the module or card m anufacturer’s manual for full details on the current consumption of the particular module or peripheral you are using.Note [12]: COM Express Type 6 Module used for measurements - 4th Gen i7-4700Thermal DetailsAll components on the CCG013 are rated to a maximum operating temperature of -40°C to +85°C. Mechanical DetailsA complete 3D STEP Model file of the carrier can be downloaded here:/ftp/3d_models/CCG013_3D_MODEL.zipCables and Cable Kit InformationCable KitsThe following tables summarize the PMC/XMC Ultra Lite Carrier’s available cable kits from Connect Tech.CKG062 –“Full” Cable KitCKG021 –“Starter” Cable Kit。
5500FE安全与音频双导22AWGBC CMRC安全系统电缆说明说明书

24 AWG (7x32) TC
Outer Jacket
Material
Nom. Thickness Nom. Diameter Ripcord
PVC - Polyvinyl Chloride 0.017 in (0.43 mm) 0.126 in (3.20 mm) Yes
Overall Cable Diameter (Nominal):
5500FE 008U500 Gray UnReel
500 ft 612825423836
5500FE 0081000 Gray Reel
1,000 ft 612825162803
5500FE 008U1000 Gray UnReel
1,000 ft 612825162780
5500FE 008Z1000 Gray ReelTuff Box 1,000 ft 612825162810
Product: 5500FE Security & Sound, 2 Conductor 22 AWG, BC, CMR
Product Description Security & Sound Cable, Riser-CMR, 2-22 AWG stranded bare copper conductors with polypropylene insulation, Beldfoil® shield and PVC jacket with ripcord
UL Temperature Operating
75°C
-20°C to +75°C
Bend Radius Stationary Min. Installation Min. 1.3 in (33 mm) 1.3 in (33 mm)
六区位通过式金属探测门说明书

六区位通过式金属探测门说明书mc022§1 主要技术参数电源:AC 220V 功耗:P≤50W重量:75 kg放射频率:6.99~11KHZ 8 个可供选择频率通道尺寸:2023mm×750mm×510mm 〔高×宽×深〕外型尺寸:2200mm×860mm×510mm 〔高×宽×深〕区位:从下至上门体内分6 个独立探测区位符合标准:GB15210-2023§2 六区位通过式金属探测门介绍该通过式金属探测门是一款高性能金属探测仪器。
该产品为六区位通过式金属探测门,整个探测通道内由下而上平均分为六个独立探测区,由于承受先进的微芯片处理技术,在探测区内无盲点,不存在特别灵敏区和特别弱区,各点探测均匀性很好,能直接显示报警金属物所在的具体位置,给检查人员带来了极大的便利,提高了人员通过率,提高了工作效率。
面板设计简洁明白,操作便利,整体美观耐用。
该产品主要用于安全检查和金属防盗检查,如检查隐蔽的违禁刀具、枪支,硬币、金银首饰、贵重金属等。
当被检人员从门内通过时,其所携带的金属物品超过设定的数值时,安检门马上报警。
应用场所:机场、展览馆、体育馆、庆典会、大型会议活动、监狱、法庭、看管所、夜总会、迪厅、消遣场所的安全检查,还可用于电子企业、五金企业、贵重首饰生产企业的产品或原材料的防盗检查。
本型号通过式金属探测门由两块侧板〔探头〕及顶端的横梁〔电器箱〕组成。
两侧的探头内分别装有多个传感器,横梁内装有信号处理的电器局部,以及嵌在横梁板上的操作显示面板。
仪器使用声音和灯光指示报警。
显示面板有六条红色区位指示灯,以及一排十个信号强度指示灯。
当携带金属物的量超过预先设定时,区位灯就点亮。
例如金属物在脚踝处,第一区区位灯就会点亮,金属物在腰间,则第三区区位灯就会点亮,同时蜂鸣器鸣叫,‘报警灯’点亮,‘等待灯’熄灭。
信号强度指示灯能够显示探测金属信号的强弱。
Maxcell称重显示器使用说明书

.................................. 37
1
Maxcell
2-3-12 RS485 ID 输入 (选配功能)
............................................. 38
命令格式说明 ...................................................................................................................... 39
2-3-9 RS232 一般或简易输出重量 6 位或 7 位选择
..................... 35
2-3-10 RTC 时间调整
............................................................... 36
2-3-11 调整打印时年月日或日月年显示方式
2-3-3 输出格式选择
.................................................................... 29
2-3-4 传送方式设定
.................................................................... 30
使用前之准备工作
一. 请将本机放置于稳固且平坦之桌面上使用,勿放于摇动或振动之台架上。 二. 避免将本机放置于温度变化过大或空气流动剧烈之场所,如日光直射或冷气机之出风口。 三. 请使用独立之电源插座,以避免其它电器用品干扰。 四. 打开电源时,秤盘上请勿放置任何东西。 五. 产品使用时,秤物之重心须位于秤盘之中心点,且秤物不超出秤盘范围,以确保其准确度。 六. 使用本机前,请先温机 15 ~ 20 分钟。 七. 请注意当低电源警示之符号( )闪烁时,则表示须再行充电。 八. 如对本产品有任何建议,请不吝指正。
CSD22SM

CSD 22A数字式综合采集装置说明书一、概述本装置系由微处理器构成的数据采集装置,可采集40路模拟量,其中包括24路电压和16路电流采集,作为8组功率测点采集;并有42路开关量(或电度量)采集。
可满足35~110KV变电站两台三卷变或三台两卷变功率测点采集的需要。
是一种功能强大的采集装置,可作为CSC 2000综合自动化系统的配套产品,与CSD 12A共同使用,可满足整个变电站采集的需要,亦可作为单独的采集装置使用。
装置功能详见第六章 装置功能说明 。
本装置硬件是在总结国内WXB及WXH系列01型及11型微机保护装置的基础上设计的第三代微机保护装置的通用硬件。
它采用了当前世界上VLSI技术的最新成就,主要特点如下:a) 采用不扩展的单片机,总线不出芯片,抗干扰能力大大提高,制造和调试都大大简化。
b) 采用第三代模数变换技术,分辨率高达14位。
c) 每个装置都带有一个高速数据通信接口,可以直接联网。
d) 装置面板上除了LCD显示和简易的四方键盘外,还提供了一个RS-232接口,用于连接PC机,从而给调试带来了很多方便。
例如:用PC机有汉化文字说明,可以离线地利用PC机整定再通过RS-232接口输入保护装置的EPPROM,还可以将故障记录转入PC机存盘并利用PC机离线分析软件包对录波结果进行各种分析。
二、主要技术数据2.1 额定数据2.1.1 额定直流数据:220V或110V(订货注明)2.1.2 额定交流数据:a) 交流电压100V;b) 交流电流5A或1A(订货注明);1CSD 22A数字式综合采集装置说明书c) 额定频率50Hz;2.1.3 功率消耗a) 直流回路不大于25Wb) 交流电压回路不大于0.2VA/ϕc) 交流电流回路不大于0.75VA/ϕ2.2 交流量输入测量两条线路测量内容:U、I、P、Q、cosϕ测量误差:≤0.5%线性范围:0~120%I N、U N过载能力:电压回路承受2倍额定电压,电流回路承受20倍额定电流。
HP LaserJet Pro MFP M225, M226 用户指南说明书
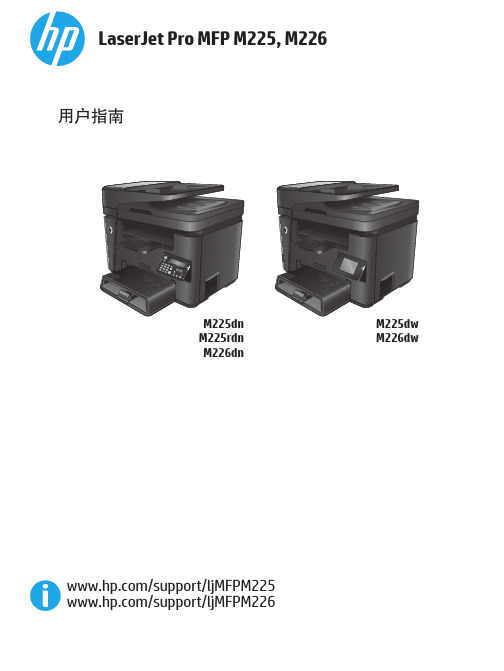
商标声明
Adobe®、Adobe Photoshop®、Acrobat® 和 PostScript® 是 Adobe Systems Incorporated 的商标。
Apple 和 Apple 徽标是 Apple Computer, Inc. 在美国以及其它国家/地区注册的商 标。iPod 是 Apple Computer, Inc. 的商 标。iPod 只能用于合法复制,或在版权 所有者的授权下复制。请勿盗用音乐作 品。
3 部件、耗材和附件 ...................................................................................................................................... 23 订购部件、附件和耗材 ..................................................................................................................................... 24 订购 ................................................................................................................................................... 24 耗材和附件 ....................................................................................................................................... 24 更换碳粉盒 ......................................................................................................................................................... 25
55-CRQ2 Series II 2 G Rotary Actuator 迷你说明书

Instruction Manual Rotary ActuatorII 2 GMarking Description:II2GEx hThe intended use of this Rotary Actuator is to convert potential energyprovided by compressed air into a force which causes mechanicalNote 1: The X at the end of the certificate number represents that this product issubject to “Special Conditions of Use”, please see Section 2.3.1 Safety InstructionsThese safety instructions are intended to prevent hazardous situationsand/or equipment damage. These instructions indicate the level ofpotential hazard with the labels of “Caution,” “Warning” or “Danger.”They are all important notes for safety and must be followed in additionto International Standards (ISO/IEC) *1), and other safety regulations.*1) ISO 4414: Pneumatic fluid power - General rules relating to systems.ISO 4413: Hydraulic fluid power - General rules relating to systems.IEC 60204-1: Safety of machinery - Electrical equipment of machines.(Part 1: General requirements)ISO 10218-1: Robots and robotic devices - Safety requirements forindustrial robots - Part 1: Robots.Refer to product catalogue, Operation Manual and HandlingPrecautions for SMC Products for additional information.Keep this manual in a safe place for future reference.WarningAlways ensure compliance with relevant safety laws andstandards.All work must be carried out in a safe manner by a qualified person incompliance with applicable national regulations.2 SpecificationsThis product is suitable for use in Zones 1 and 2 only.2.1 Product Specifications:Refer to the operation manual for this product;2.1.2 Energy and Speed Specification:WarningEnsure a speed is selected that is within the products allowable kineticenergy limit.In the case that the kinetic energy value exceeds the specification usean external method of absorbing the energy e.g. a shock absorber, ifthere are still concerns, please contact SMC.Do not stop or hold the product at the midpoint by keeping air pressurein the product, this is not an acceptable use of the product.If the product is used at low speed below the specified speedadjustment range, it can introduce problems such as the stick-slipphenomenon or stop movement altogether.2.2 Production Batch Code:The batch code printed on the label indicates the month and the year ofproduction as per the following table;2.3 Special Conditions of Use:Products are suitable for sub-divisions IIC.Products are suitable for Zones 1 and 2 only.2.3.1 Temperature Marking:2.3.1.1 Standard Product:In the normal ambient temperature range (+0°C to +40°C) the productis rated to temperature class T6.In the special ambient temperature range (+40°C to +60°C) the productis rated to temperature class T5.3 Installation3.1 InstallationWarningDo not install the product unless the safety instructions have been readand understood.Do not twist or bend the cylinder or mount the product when subject totension.Do not use in an application where the product is stopped mid-stroke,via an external stop.Do not use where cylinders are being synchronised to move a singleload.For direct mounting, use standard hexagon socket head cap screws3.1.1 Direct Loading to the ShaftAlthough applying static loads as shown in the table below areallowable, it is recommended that they are not applied directly to theIn order to improve operating conditions, it is recommended that a3.1.2 Axis Alignment on Extended ShaftsWhen the rotary actuator is used with an extended shaft, ensure thatthe axis centres of the rotary actuator and its counterpart are aligned.If they are off-centred, the load factor becomes large and an excessivebending moment may be applied to the shaft. In such a condition, theassembly may not perform a stable operation and the shaft may be3.2 EnvironmentWarningDo not use in an environment where corrosive gases, chemicals, saltwater or steam are present.Do not use in an explosive atmosphere except within the specifiedrating.Do not expose to direct sunlight. Use a suitable protective cover.Do not install in a location subject to vibration or impact in excess ofthe product’s specifications.Do not mount in a location exposed to radiant heat that would result intemperatures in excess of the product’s specifications.Do not use in wet environments, where water can remove the presenceof the lubrication.Do not use in case of heavy dusty environments where dust canpenetrate into the cylinder and dry the grease.Do not allow dust layers to build up on the cylinder surface and insulatethe product.3.3 PipingCautionBefore connecting piping make sure to clean up chips, cutting oil, dustetc.When installing piping or fittings, ensure sealant material does notenter inside the port. When using seal tape, leave 1 thread exposedon the end of the pipe/fitting.Tighten fittings to the specified tightening torque.Port Size ModelThe rotary actuator port is equipped with a fixed size orifice. Do notenlarge the hole. Enlarging the hole will increase the operation speedof the actuator and the consequent impact at the end of each strokecould lead to the actuator failure.3.4 LubricationCautionSMC products have been lubricated for life at manufacture, and do notrequire lubrication in service.If a lubricant is used in the system, refer to catalogue for details.3.5 Basic CircuitPlugging one of the ports on the actuator is considered a non-intendeduse, and could relate to an increase in maximum surface temperatureabove what the product specification declares.3.6 Electrical ConnectionThe product should be grounded by the piston rod and the body inorder to create an electrically conductive path to the system/application.Ground the product in accordance with applicable regulations.Do not pass an electrical current through the product.4 SettingsRefer to the standard product catalogue for general setup precautions.5 How to OrderRefer to catalogue for ‘How to Order’.6 Outline DimensionsRefer to catalogue for outline dimensions.ORIGINAL INSTRUCTIONS7.1 General maintenanceCautionNot following proper maintenance procedures could cause the product to malfunction and lead to equipment damage.If handled improperly, compressed air can be dangerous.Maintenance of pneumatic systems should be performed only by qualified personnel.Before performing maintenance, turn off the power supply and be sure to cut off the supply pressure. Confirm that the air is released to atmosphere.After installation and maintenance, apply operating pressure and power to the equipment and perform appropriate functional and leakage tests to make sure the equipment is installed correctly.If any electrical connections are disturbed during maintenance, ensure they are reconnected correctly and safety checks are carried out as required to ensure continued compliance with applicable national regulations.Do not make any modification to the product.Do not disassemble the product, unless required by installation or maintenance instructions.Do not use a product which looks or contains damage, this will invalidate the certification. If damage is seen, please replace the product immediately.Periodically check the product for any damage or rust appearing. This could result in an increase in friction and lead to dangerous conditions. Replace the whole actuator if any of these conditions appear.8.1 Limited warranty and disclaimer/compliance requirements Refer to Handling Precautions for SMC Products.Caution8.2 Obligations of the end-userEnsure the product is used within the specification outlined.Ensure that the maintenance periods are suitable for the application. Ensure any cleaning processes to remove dust layers are made with the atmosphere in mind (e.g. using a damp cloth to avoid static build up).Ensure that the application does not introduce additional hazards by mounting, loading, impacts or other methods.Ensure that there is sufficient ventilation and air circulation around the product.If the product is subject to direct heat sources in the application, they should be shielded so that the actuator temperature stays within the stated operating range.DangerDo not exceed any of the specifications listed in Section 2 of this document as this will be deemed improper use.Air equipment has an air leakage during operation within certain limits. Do not use this equipment when the air itself introduces additional hazards and could lead to an explosion.Use only Ex certified auto switches. These should be ordered separately.Do not use this product in the presence of strong magnetic fields that could generate a surface temperature higher than the product specification.Avoid applications where the shaft and the adjoining part in the application can create a possible ignition source.Do not install or use these actuators where there is the possibility for the shaft and adjoining parts to impact foreign objects.In the event of damage or failure of any parts located in the vicinity where this product has been installed, it is the responsibility of the user to determine whether or not this has compromised the safety and condition of this product and/or the application.External impact on the cylinder body could result in a spark and/or cylinder damage. Avoid any application where foreign objects can hit or impact the cylinder. In such situations the application should install a suitable guard to prevent this occurrence.Do not use this equipment where vibration could lead to failure.This product shall not be disposed of as municipal waste. Check your local regulations and guidelines to dispose this product correctly, in order to reduce the impact on human health and the environment.Refer to or www.smc.eu for your local distributor/importer.URL : https:// (Global) https:// www.smc.eu (Europe) SMC Corporation, 4-14-1, Sotokanda, Chiyoda-ku, Tokyo 101-0021, JapanSpecifications are subject to change without prior notice from the manufacturer. © 2023 SMC Corporation All Rights Reserved. Template DKP50047-F-085M。
National LMC6062 数据手册

LMC6062Precision CMOS Dual Micropower Operational AmplifierGeneral DescriptionThe LMC6062is a precision dual low offset voltage,mi-cropower operational amplifier,capable of precision single supply operation.Performance characteristics include ultra low input bias current,high voltage gain,rail-to-rail output swing,and an input common mode voltage range that in-cludes ground.These features,plus its low power consump-tion,make the LMC6062ideally suited for battery powered applications.Other applications using the LMC6062include precision full-wave rectifiers,integrators,references,sample-and-hold circuits,and true instrumentation amplifiers.This device is built with National’s advanced double-Poly Silicon-Gate CMOS process.For designs that require higher speed,see the LMC6082precision dual operational amplifier.PATENT PENDINGFeatures(Typical Unless Otherwise Noted)n Low offset voltage 100µVn Ultra low supply current 16µA/Amplifier n Operates from 4.5V to 15V single supply n Ultra low input bias current 10fAn Output swing within 10mV of supply rail,100k load n Input common-mode range includes V −n High voltage gain 140dB n Improved latchup immunityApplicationsn Instrumentation amplifiern Photodiode and infrared detector preamplifier n Transducer amplifiersn Hand-held analytic instruments n Medical instrumentation n D/A converternCharge amplifier for piezoelectric transducersConnection DiagramOrdering InformationPackage Temperature RangeNSC Drawing Transport Media Military Industrial −55˚C to +125˚C −40˚C to +85˚C 8-Pin LMC6062AMNLMC6062AIN N08ERailMolded DIP LMC6062IN 8-Pin LMC6062AIM M08ARail Small Outline LMC6062IMTape and Reel8-Pin LMC6062AMJ/883J08A RailCeramic DIP8-Pin DIP/SODS011298-1Top ViewNovember 1994LMC6062Precision CMOS Dual Micropower Operational Amplifier©1999National Semiconductor Corporation 查询LMC6062供应商Absolute Maximum Ratings(Note1)If Military/Aerospace specified devices are required, please contact the National Semiconductor Sales Office/ Distributors for availability and specifications. Differential Input Voltage±Supply Voltage Voltage at Input/Output Pin(V+)+0.3V,(V−)−0.3V Supply Voltage(V+−V−)16V Output Short Circuit to V+(Note11) Output Short Circuit to V−(Note2) Lead Temperature(Soldering,10sec.)260˚C Storage Temp.Range−65˚C to+150˚C Junction Temperature150˚C ESD Tolerance(Note4)2kV Current at Input Pin±10mA Current at Output Pin±30mA Current at Power Supply Pin40mA Power Dissipation(Note3)Operating Ratings(Note1)Temperature RangeLMC6062AM−55˚C≤T J≤+125˚C LMC6062AI,LMC6082I−40˚C≤T J≤+85˚C Supply Voltage 4.5V≤V+≤15.5V Thermal Resistance(θJA)(Note12)8-Pin Molded DIP115˚C/W 8-Pin SO193˚C/W Power Dissipation(Note10)DC Electrical CharacteristicsUnless otherwise specified,all limits guaranteed for T J=25˚C.Boldface limits apply at the temperature extremes.V+=5V, V−=0V,V CM=1.5V,V O=2.5V and R L>1M unless otherwise specified.Typ LMC6062AM LMC6062AI LMC6062ISymbol Parameter Conditions(Note5)Limit Limit Limit Units(Note6)(Note6)(Note6)V OS Input Offset Voltage100350350800µV12009001300Max TCV OS Input Offset Voltage 1.0µV/˚C Average DriftI B Input Bias Current0.010pA10044Max I OS Input Offset Current0.005pA10022Max R IN Input Resistance>10TeraΩCMRR Common Mode0V≤V CM≤12.0V85757566dB Rejection Ratio V+=15V707263Min +PSRR Positive Power Supply5V≤V+≤15V85757566dB Rejection Ratio V O=2.5V707263Min −PSRR Negative Power Supply0V≤V−≤−10V100848474dB Rejection Ratio708171Min V CM Input Common-Mode V+=5V and15V−0.4−0.1−0.1−0.1V Voltage Range for CMRR≥60dB000MaxV+−1.9V+−2.3V+−2.3V+−2.3VV+−2.6V+−2.5V+−2.5Min A V Large Signal R L=100kΩSourcing4000400400300V/mVVoltage Gain(Note7)200300200MinSinking300018018090V/mV7010060MinR L=25kΩSourcing3000400400200V/mV(Note7)15015080MinSinking200010010070V/mV355035Min 2DC Electrical Characteristics(Continued)Unless otherwise specified,all limits guaranteed for T J=25˚C.Boldface limits apply at the temperature extremes.V+=5V,V−=0V,V CM=1.5V,V O=2.5V and R L>1M unless otherwise specified.Typ LMC6062AM LMC6062AI LMC6062ISymbol Parameter Conditions(Note5)Limit Limit Limit Units(Note6)(Note6)(Note6)V O Output Swing V+=5V 4.995 4.990 4.990 4.950VR L=100kΩto2.5V 4.970 4.980 4.925Min0.0050.0100.0100.050V0.0300.0200.075MaxV+=5V 4.990 4.975 4.975 4.950VR L=25kΩto2.5V 4.955 4.965 4.850Min0.0100.0200.0200.050V0.0450.0350.150MaxV+=15V14.99014.97514.97514.950VR L=100kΩto7.5V14.95514.96514.925Min0.0100.0250.0250.050V0.0500.0350.075MaxV+=15V14.96514.90014.90014.850VR L=25kΩto7.5V14.80014.85014.800Min0.0250.0500.0500.100V0.2000.1500.200MaxI O Output Current Sourcing,V O=0V22161613mAV+=5V8108MinSinking,V O=5V21161616mA788MinI O Output Current Sourcing,V O=0V25151515mAV+=15V91010MinSinking,V O=13V35242424mA(Note11)788MinI S Supply Current Both Amplifiers32383846µAV+=+5V,V O=1.5V604656MaxBoth Amplifiers40474757µAV+=+15V,V O=7.5V705566Max3AC Electrical CharacteristicsUnless otherwise specified,all limits guaranteed for T J=25˚C,Boldface limits apply at the temperature extremes.V+=5V, V−=0V,V CM=1.5V,V O=2.5V and R L>1M unless otherwise specified.Typ LMC6062AM LMC6062AI LMC6062ISymbol Parameter Conditions(Note5)Limit Limit Limit Units(Note6)(Note6)(Note6) SR Slew Rate(Note8)35202015V/ms8107Min GBW Gain-Bandwidth Product100kHz θm Phase Margin50Deg Amp-to-Amp Isolation(Note9)155dBe n Input-Referred Voltage Noise F=1kHz83nV/√Hzi n Input-Referred Current Noise F=1kHz0.0002pA/√HzT.H.D.Total Harmonic Distortion F=1kHz,A V=−5R L=100kΩ,V O=2V PP0.01%±5V SupplyNote1:Absolute Maximum Ratings indicate limits beyond which damage to the device may occur.Operating Ratings indicate conditions for which the device is in-tended to be functional,but do not guarantee specific performance limits.For guaranteed specifications and test conditions,see the Electrical Characteristics.The guaranteed specifications apply only for the test conditions listed.Note2:Applies to both single-supply and split-supply operation.Continous short circuit operation at elevated ambient temperature can result in exceeding the maxi-mum allowed junction temperature of150˚C.Output currents in excess of±30mA over long term may adversely affect reliability.Note3:The maximum power dissipation is a function of T J(Max),θJA,and T A.The maximum allowable power dissipation at any ambient temperature is P D=(T J(Max)−T A)/θJA.Note4:Human body model,1.5kΩin series with100pF.Note5:Typical values represent the most likely parametric norm.Note6:All limits are guaranteed by testing or statistical analysis.Note7:V+=15V,V CM=7.5V and R L connected to7.5V.For Sourcing tests,7.5V≤V O≤11.5V.For Sinking tests,2.5V≤V O≤7.5V.Note8:V+=15V.Connected as Voltage Follower with10V step input.Number specified is the slower of the positive and negative slew rates.Note9:Input referred V+=15V and R L=100kΩconnected to7.5V.Each amp excited in turn with100Hz to produce V O=12V PP.Note10:For operating at elevated temperatures the device must be derated based on the thermal resistanceθJA with P D=(T J–T A)/θJA.Note11:Do not connect output to V+,when V+is greater than13V or reliability witll be adversely affected.Note12:All numbers apply for packages soldered directly into a PC board.Note13:For guaranteed Military Temperature Range parameters,see RETSMC6062X.4Typical Performance CharacteristicsV S =±7.5V,T A =25˚C,Unless otherwise specifiedDistribution of LMC6062Input Offset Voltage (T A =+25˚C)DS011298-15Distribution of LMC6062Input Offset Voltage (T A =−55˚C)DS011298-16Distribution of LMC6062Input Offset Voltage (T A =+125˚C)DS011298-17Input Bias Current vs Temperature DS011298-18Supply Current vs Supply Voltage DS011298-19Input Voltagevs Output VoltageDS011298-20Common Mode Rejection Ratio vs FrequencyDS011298-21Power Supply Rejection Ratio vs Frequency DS011298-22Input Voltage Noise vs FrequencyDS011298-235Typical Performance CharacteristicsV S =±7.5V,T A =25˚C,Unless otherwisespecified (Continued)Output Characteristics Sourcing CurrentDS011298-24Output Characteristics Sinking CurrentDS011298-25Gain and Phase Response vs Temperature (−55˚C to +125˚C)DS011298-26Gain and PhaseResponse vs Capacitive Load with R L =20k ΩDS011298-27Gain and PhaseResponse vs Capacitive Load with R L =500k ΩDS011298-28Open LoopFrequency ResponseDS011298-29Inverting Small Signal Pulse Response DS011298-30Inverting Large Signal Pulse Response DS011298-31Non-Inverting Small Signal Pulse ResponseDS011298-32 6Typical Performance CharacteristicsV S =±7.5V,T A =25˚C,Unless otherwisespecified (Continued)Applications HintsAMPLIFIER TOPOLOGYThe LMC6062incorporates a novel op-amp design topology that enables it to maintain rail-to-rail output swing even when driving a large load.Instead of relying on a push-pull unity gain output buffer stage,the output stage is taken directly from the internal integrator,which provides both low output impedance and large gain.Special feed-forward compensa-tion design techniques are incorporated to maintain stability over a wider range of operating conditions than traditional micropower op-amps.These features make the LMC6062both easier to design with,and provide higher speed than products typically found in this ultra-low power PENSATING FOR INPUT CAPACITANCEIt is quite common to use large values of feedback resis-tance for amplifiers with ultra-low input current,like the LMC6062.Although the LMC6062is highly stable over a wide range of operating conditions,certain precautions must be met to achieve the desired pulse response when a large feedback resistor is rge feedback resistors and even small values of input capacitance,due to transducers,photo-diodes,and circuit board parasitics,reduce phase margins.When high input impedances are demanded,guarding of the LMC6062is suggested.Guarding input lines will not only re-duce leakage,but lowers stray input capacitance as well.(See Printed-Circuit-Board Layout for High Impedance Work ).The effect of input capacitance can be compensated for by adding a capacitor.Place a capacitor,C f ,around the feed-back resistor (as in Figure 1)such that:orR 1C IN ≤R 2C fSince it is often difficult to know the exact value of C IN ,C f can be experimentally adjusted so that the desired pulse re-sponse is achieved.Refer to the LMC660and the LMC662for a more detailed discussion on compensating for input capacitance.Non-Inverting Large Signal Pulse ResponseDS011298-33Crosstalk Rejection vs FrequencyDS011298-34Stability vs Capacitive Load,R L =20k ΩDS011298-35Stability vs Capacitive Load R L =1M ΩDS011298-367Applications Hints(Continued)CAPACITIVE LOAD TOLERANCEAll rail-to-rail output swing operational amplifiers have volt-age gain in the output stage.A compensation capacitor is normally included in this integrator stage.The frequency lo-cation of the dominate pole is affected by the resistive load on the amplifier.Capacitive load driving capability can be op-timized by using an appropriate resistive load in parallel with the capacitive load (see typical curves).Direct capacitive loading will reduce the phase margin of many op-amps.A pole in the feedback loop is created by the combination of the op-amp’s output impedance and the ca-pacitive load.This pole induces phase lag at the unity-gain crossover frequency of the amplifier resulting in either an os-cillatory or underdamped pulse response.With a few exter-nal components,op amps can easily indirectly drive capaci-tive loads,as shown in Figure 2.In the circuit of Figure 2,R1and C1serve to counteract the loss of phase margin by feeding the high frequency compo-nent of the output signal back to the amplifier’s inverting in-put,thereby preserving phase margin in the overall feedback loop.Capacitive load driving capability is enhanced by using a pull up resistor to V +(Figure 3).Typically a pull up resistor con-ducting 10µA or more will significantly improve capacitive load responses.The value of the pull up resistor must be de-termined based on the current sinking capability of the ampli-fier with respect to the desired output swing.Open loop gain of the amplifier can also be affected by the pull up resistor (see Electrical Characteristics).PRINTED-CIRCUIT-BOARD LAYOUT FOR HIGH-IMPEDANCE WORKIt is generally recognized that any circuit which must operate with less than 1000pA of leakage current requires special layout of the PC board.When one wishes to take advantage of the ultra-low bias current of the LMC6062,typically less than 10fA,it is essential to have an excellent layout.Fortu-nately,the techniques of obtaining low leakages are quite simple.First,the user must not ignore the surface leakage of the PC board,even though it may sometimes appear accept-ably low,because under conditions of high humidity or dust or contamination,the surface leakage will be appreciable.To minimize the effect of any surface leakage,lay out a ring of foil completely surrounding the LMC6062’s inputs and the terminals of capacitors,diodes,conductors,resistors,relay terminals etc.connected to the op-amp’s inputs,as in Figure 4.To have a significant effect,guard rings should be placed on both the top and bottom of the PC board.This PC foil must then be connected to a voltage which is at the same voltage as the amplifier inputs,since no leakage current can flow between two points at the same potential.For example,a PC board trace-to-pad resistance of 1012Ω,which is nor-mally considered a very large resistance,could leak 5pA if the trace were a 5V bus adjacent to the pad of the input.This would cause a 100times degradation from the LMC6062’s actual performance.However,if a guard ring is held within 5mV of the inputs,then even a resistance of 1011Ωwould cause only 0.05pA of leakage current.See Figure 5for typi-cal connections of guard rings for standard op-amp configurations.DS011298-4FIGURE 1.Canceling the Effect of Input Capacitance DS011298-5FIGURE 2.LMC6062Noninverting Gain of 10Amplifier,Compensated to Handle Capacitive Loads DS011298-14FIGURE pensating for Large Capacitive Loadswith a Pull Up ResistorDS011298-6FIGURE 4.Example of Guard Ring in P .C.BoardLayout8Applications Hints(Continued)The designer should be aware that when it is inappropriate to lay out a PC board for the sake of just a few circuits,there is another technique which is even better than a guard ring on a PC board:Don’t insert the amplifier’s input pin into the board at all,but bend it up in the air and use only air as an in-sulator.Air is an excellent insulator.In this case you may have to forego some of the advantages of PC board con-struction,but the advantages are sometimes well worth the effort of using point-to-point up-in-the-air wiring.See Figure tchupCMOS devices tend to be susceptible to latchup due to theirinternal parasitic SCR effects.The(I/O)input and output pinslook similar to the gate of the SCR.There is a minimum cur-rent required to trigger the SCR gate lead.The LMC6062and LMC6082are designed to withstand100mA surge cur-rent on the I/O pins.Some resistive method should be usedto isolate any capacitance from supplying excess current tothe I/O pins.In addition,like an SCR,there is a minimumholding current for any latchup mode.Limiting current to thesupply pins will also inhibit latchup susceptibility. Typical Single-SupplyApplications(V+=5.0V DC)The extremely high input impedance,and low power con-sumption,of the LMC6062make it ideal for applications thatrequire battery-powered instrumentation amplifiers.Ex-amples of these types of applications are hand-held pHprobes,analytic medical instruments,magnetic field detec-tors,gas detectors,and silicon based pressure transducers. Figure7shows an instrumentation amplifier that featureshigh differential and common mode input resistance(>1014Ω),0.01%gain accuracy at A V=100,excellent CMRR with1kΩimbalance in bridge source resistance.In-put current is less than100fA and offset drift is less than2.5µV/˚C.R2provides a simple means of adjusting gainover a wide range without degrading CMRR.R7is an initialtrim used to maximize CMRR without using super precisionmatched resistors.For good CMRR over temperature,lowdrift resistors should be used.DS011298-7 (a)Inverting AmplifierDS011298-8(b)Non-Inverting AmplifierDS011298-9(c)FollowerFIGURE5.Typical Connections of Guard RingsDS011298-10 (Input pins are lifted out of PC board and soldered directly to components.All other pins connected to PC board).FIGURE6.Air Wiring 9Typical Single-SupplyApplications(Continued)DS011298-11 If R1=R5,R3=R6,and R4=R7;then∴A V≈100for circuit shown(R2=9.822k).FIGURE7.Instrumentation AmplifierDS011298-12FIGURE8.Low-Leakage Sample and HoldDS011298-13FIGURE9.1Hz Square Wave Oscillator10Physical Dimensions inches(millimeters)unless otherwise noted8-Pin Ceramic Dual-In-Line PackageOrder Number LMC6062AMJ/883NS Package Number J08A8-Pin Small Outline PackageOrder Number LMC6062AIM or LMC6062IMNS Package Number M08A11Physical Dimensions inches(millimeters)unless otherwise noted(Continued)LIFE SUPPORT POLICYNATIONAL’S PRODUCTS ARE NOT AUTHORIZED FOR USE AS CRITICAL COMPONENTS IN LIFE SUPPORT DE-VICES OR SYSTEMS WITHOUT THE EXPRESS WRITTEN APPROVAL OF THE PRESIDENT OF NATIONAL SEMI-CONDUCTOR CORPORATION.As used herein:1.Life support devices or systems are devices or sys-tems which,(a)are intended for surgical implant intothe body,or(b)support or sustain life,and whose fail-ure to perform when properly used in accordancewith instructions for use provided in the labeling,canbe reasonably expected to result in a significant injuryto the user.2.A critical component is any component of a life supportdevice or system whose failure to perform can be rea-sonably expected to cause the failure of the life supportdevice or system,or to affect its safety or effectiveness.National SemiconductorCorporationAmericasTel:1-800-272-9959Fax:1-800-737-7018Email:***************National SemiconductorEuropeFax:+49(0)180-5308586Email:**********************Deutsch Tel:+49(0)180-5308585English Tel:+49(0)180-5327832Français Tel:+49(0)180-5329358Italiano Tel:+49(0)180-5341680National SemiconductorAsia Pacific CustomerResponse GroupTel:65-2544466Fax:65-2504466Email:*******************National SemiconductorJapan Ltd.Tel:81-3-5639-7560Fax:81-3-5639-75078-Pin Molded Dual-In-Line PackageOrder Number LMC6062AIN,LMC6062AMN or LMC6062INNS Package Number N08ELMC662PrecisionCMOSDualMicropowerOperationalAmplifierNational does not assume any responsibility for use of any circuitry described,no circuit patent licenses are implied and National reserves the right at any time without notice to change said circuitry and specifications.。
EMS22A 非接触式绝对编码器产品说明书
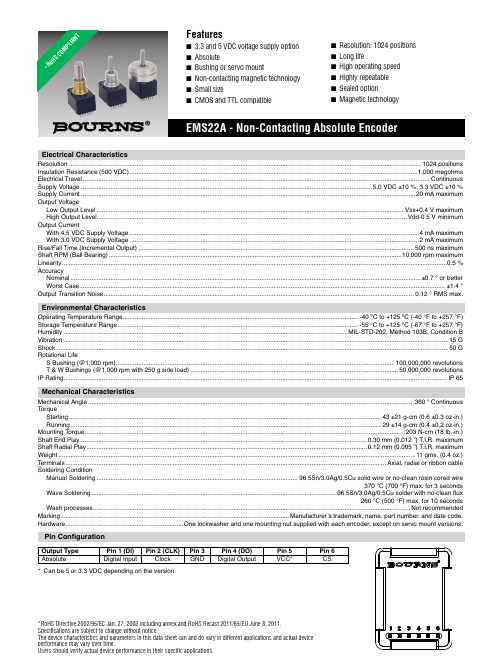
*RoHS Directive 2002/95/EC Jan. 27, 2003 including annex and RoHS Recast 2011/65/EU June 8, 2011. Specifi cations are subject to change without notice.The device characteristics and parameters in this data sheet can and do vary in different applications and actual device performance may vary over time.Users should verify actual device performance in their specifi c applications.*Ro H S C O MP L I A NTInsulation Resistance (500 VDC) ......................................................................................................................................................................1,000 megohms Electrical Travel ........................................................................................................................................................................................................Continuous Supply Voltage ........................................................................................................................................................................5.0 VDC ±10 %, 3.3 VDC ±10 %Supply Current .................................................................................................................................................................................................20 mA maximum Output VoltageLow Output Level .................................................................................................................................................................................Vss+0.4 V maximum High Output Level...................................................................................................................................................................................Vdd-0.5 V minimum Output CurrentWith 4.5 VDC Supply Voltage .......................................................................................................................................................................4 mA maximum With 3.0 VDC Supply Voltage .......................................................................................................................................................................2 mA maximum Rise/Fall Time (Incremental Output) ...............................................................................................................................................................500 ns maximum Shaft RPM (Ball Bearing) .........................................................................................................................................................................10,000 rpm maximum Linearity ..............................................................................................................................................................................................................................0.5 %AccuracyNominal ..........................................................................................................................................................................................................±0.7 ° or better Worst Case ...................................................................................................................................................................................................................±1.4 °Output Transition Noise ...................................................................................................................................................................................0.12 ° RMS max.Environmental CharacteristicsOperating Temperature Range ........................................................................................................................................-40 ºC to +125 ºC (-40 °F to +257 °F)Storage Temperature Range ...........................................................................................................................................-55 °C to +125 °C (-67 °F to +257 °F)Humidity -STD-202, Method 103B, Condition B Vibration ..............................................................................................................................................................................................................................15 G Shock ..................................................................................................................................................................................................................................50 G Rotational LifeS Bushing (@1,000 rpm) .................................................................................................................................................................100,000,000 revolutions T & W Bushings (@1,000 rpm with 250 g side load) ........................................................................................................................50,000,000 revolutions IP Rating .............................................................................................................................................................................................................................IP 65Mechanical CharacteristicsMechanical Angle ............................................................................................................................................................................................360 ° Continuous TorqueStarting ....................................................................................................................................................................................43 ±21 g-cm (0.6 ±0.3 oz-in.) Running ...................................................................................................................................................................................29 ±14 g-cm (0.4 ±0.2 oz-in.)Mounting Torque .........................................................................................................................................................................................203 N-cm (18 lb.-in.)Shaft End Play ......................................................................................................................................................................0.30 mm (0.012 ”) T.I.R. maximum Shaft Radial Play ..................................................................................................................................................................0.12 mm (0.005 ”) T.I.R. maximum Weight ..............................................................................................................................................................................................................11 gms. (0.4 oz.)Terminals .........................................................................................................................................................................................Axial, radial or ribbon cable Soldering ConditionManual Soldering ....................................................................................................................96.5Sn/3.0Ag/0.5Cu solid wire or no-clean rosin cored wire 370 °C (700 °F) max. for 3 seconds Wave Soldering .............................................................................................................................................96.5Sn/3.0Ag/0.5Cu solder with no-clean fl ux 260 °C (500 °F) max. for 10 seconds Wash processes .......................................................................................................................................................................................Not recommended Marking ....................................................................................................................................Manufacturer’s trademark, name, part number, and date code.Hardware ....................................................................One lockwasher and one mounting nut supplied with each encoder, except on servo mount versions.Pin ConfigurationOutput Type Pin 1 (DI)Pin 2 (CLK)Pin 3Pin 4 (DO)Pin 5Pin 6Absolute Digital Input Clock GND Digital Output VCC*CS* Can be 5 or 3.3 VDC depending on the version.Specifi cations are subject to change without notice.The device characteristics and parameters in this data sheet can and do vary in different applications and actual device performance may vary over time.Users should verify actual device performance in their specifi c applications.Output Type Waveform and Variant TableApplications■ Material handling equipment ■ Brushless DC motor commutation ■ Robotics ■ Automotive ■ Industrial automation ■ Petroleum refi nery■ Medical ■ Offi ce equipment■Audio and broadcast equipmentD0Daisy Chain Hardware ConfigurationDaisy Chain Mode Data TransferData ContentDescriptionD9:D0Absolute angular position data S1End of offset compensation algorithm S2Cordic overfl ow indicating an error in cordic partS3Linearity alarm S4Increase in magnitude S5Decrease in magnitudeP1Even parity for detecting bits 1-15 transmission errorAbsolute OutputConsult factory for options not shown, including:• Wire lead or cable options • Special shaft/bushing sizes and features• Connectors • Special performance characteristics• Non-standard resolutions • PCB mounting bracketProduct DimensionsShaft Style D (Bushing T)PANEL LAYOUT Shaft Style B (Bushing S)PANEL LAYOUT Specifi cations are subject to change without notice.The device characteristics and parameters in this data sheet can and do vary in different applications and actual device performance may vary over time.Users should verify actual device performance in their specifi c applications.Product DimensionsDIMENSIONS:MM(INCHES)Cable AssemblyMAX.2 PLCS.24 AWG (7X32) STRANDED, TOP COAT 6 CIRCUITS, P.V.C. INSULATIONSpecifi cations are subject to change without notice.The device characteristics and parameters in this data sheet can and do vary in different applications and actual device performance may vary over time.Users should verify actual device performance in their specifi c applications.How To OrderREV. 05/14Specifi cations are subject to change without notice.The device characteristics and parameters in this data sheet can and do vary in different applications and actual device performance may vary over time. Users should verify actual device performance in their specifi c applications.。
Modicon M221 TM221C16T 产品数据手册说明书

Modicon M221 Logic controller 24 V DC 9 discrete input conforming to IEC 61131-2 Type 1 including 4 fast input 2 at input range: 0...10 V Transistor 7 transistor including 2 fast output 24 V DC 0.5 A
0 ms for input 12 ms for input 3 ms for input
Positive logic (source)
3.5 A
100 kHz for fast output (PWM/PLS mode) at Q0...Q1 termnal 5 kHz for output at Q2...Q3 termnal 0.1 kHz for output at Q4...Q6 termnal
4 fast input (HSC mode) (counting frequency: 100 kHz), counting capacity: 32 bits
A/B Pulse/direction Single phase
USB port with connector mini B USB 2.0 Non isolated serial link "serial 1" with connector RJ45 and interface RS485 Non isolated serial link "serial 2" with connector RJ45 and interface RS232/RS485
Eutronic Arc 552 铝铜线说明书

An Aluminum - Bronze Wire Made Exclusively for the Twin Wire Arc Spray Process• High bond strength• Self-bonding to most metals including copper-base alloys • Good abrasion and corrosion resistance • Widely used for machine element repairEuTronic Arc 552 Wire®DESCRIPTION:Eutronic Arc 552 is an aluminum-bronze wire designed specifically for the Twin Wire Arc process. The coatings produced are characterized by high bond strength and are considered self-bonding to most metals including copper-base alloys. Eutronic Arc 552 will produce extremely dense coatings which exhibit good, general resistance to abrasion and corrosion. In addition, the coatings produced are readi-ly machined to a 30-35 micro inch finish with standard high speed steel tooling. Eutronic Arc 552 coatings are widely used for machine element repair applications.APPLICATIONS:• Bond Coating• Rebuild Propeller Shafts (Aluminum Bronze Components)• Rebuild Worn Bearing Areas • Pump Shafts and Housings • Air SealsPROCEDURE FOR USE:Surfaces should be clean, white metal, with no oxides (rust), dirt, grease, or oil in the coating area.Note: It is best not to handle parts after cleaning.The recommended method of surface preparation is to grit blast with 24 mesh aluminum oxide.TECHNICAL WIRE PROPERTIES:Melting Point:1800°F (982°C)HEALTH & SAFETY:To insure a safe work environment observe normal spraying practices, provide appropriate respiratory pro-tection and pay attention to air flow patterns. For gene-ral spray practices, see AWS Publications AWS C2. 1-73, “Recommended Safe Practices for Thermal Spraying’ and AWS TSS-85, “Thermal Spraying, Practice, Theory and Application.” Thermal spraying is a completely safe process when performed in accordance with proper safety measu-res. Become familiar with local safety regulations before starting spray operations.DO NOT operate your spraying equipment or use the spray material supplied, before you have thoroughly read the equipment instruction manual.Refer to the Eutectic web site for Material Safety Data Sheet (MSDS) information.DISREGARDING THESE INSTRUCTIONS MAY BE HAZARDOUS TO YOUR HEALTHTYPICAL COATING CHARACTERISTICS:Nominal Hardness: 67 HRB Bond Strength: 7000 psiDeposit Rate: 9 lbs/hr/100 amps Deposit Efficiency: 75%Wire Coverage: 0.9 oz/ft 2/0.001 inches thick Coating Density: 6.3 gm/ccSPRAY PARAMETERS:Diameter: 1.6 mm Air Pressure: *50 – 60 psi Voltage: *20 – 21Amperage: *100-200Standoff: *4-8 in.* Parameters are typical and may vary depending on the equipment used. Contact your equipment manufacturer for optimum spray parameters.Statement of Liability: Due to variations inherent in speci fi c applications, the technical information contained herein, including any information as to suggested product applications or results, is presented without representation or warranty, expressed or implied. Without limitation, there are no warranties of merchantability or of fi tness for a particular purpose. Each process and application must be fully evaluated by the user in all respects, including suitability, compliance with applicable law and non-infringement of the rights of others, and Eutectic Corporation and its af fi liates shall have no liability in respect thereof.YOUR RESOURCE FOR PROTECTION, REPAIR AND JOINING SOLUTIONSEutectic CorporationN94 W14355 Garwin Mace Drive Menomonee Falls, WI 53051 USA P 800-558-8524 • F EAS552 10-15 © 2008, Eutectic Corporation, ® Reg. T.M., Printed in the U.S.A.Eutectic Services12300 Carmen Avenue Milwaukee, WI 53225 USAP 800-558-8524 • F 262-255-5542。
智能建筑设计方案

《30MHz-1GHz声音和电视信号电缆分配系统》GB1498-94;
《民用闭路监视电视系统工程技术规范》GB50198-94;
《高层民用建筑设计防火规范》GBJ50116-98
大楼通信综合布线系统》YD/T926.1-97
《建筑与建筑群综合布线系统工程设计规范》GB50311—2000;
1.1
1.1.1
**大厦位于*****,其南临北三环路、北接广州、东靠番禺中心市桥、西邻迎宾路,地理位置优越,交通便捷。
**大厦计划建成集科研、办公、发展与良好生活环境于一体的科技大厦,以科技、节能、环保等高新技术研发厂房为主,辅以相关配套服务内容的综合性科技大厦。主要附近配套建筑有科技产业基地、研发中心和服务中心、商务及公共配套设施、高级湖滨公寓等共同组成,园内建筑物超过40幢,且主要是大型建筑物。园区全部建成后,预计常驻人口约7,000-8,000人,办公及流动人口约13,000-20,000人左右。
EIA/TIA569《建筑通讯线路间距标准》;
EIA/TIA606《商业建筑通信基础结构管理规范》;
EIA/TIA607《商业建筑通信基础结构管理规范》;
EIA/TIAIS11801《用户建筑综合布线》;
ANSIFDDI《光纤分布式数据接口高速局域网标准》;
ANSITPDDI《铜线分布式数据接口高速局域网标准》;
198.2
218.8
厂房04
206
187
193
196.7
200.4
204.1
207.8
211.5
215.2
235.5
厂房05
195
201
204.7