BMA208_10_tutorial_5
3500系列_中文手册
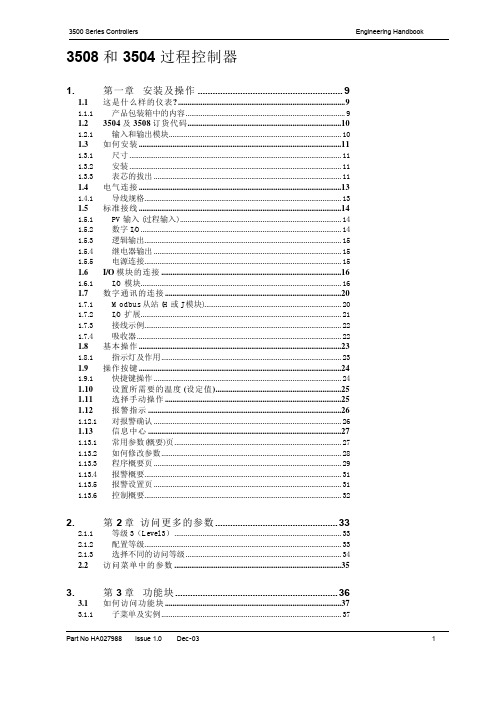
1.13.3 程序概要页 .................................................................................................... 29
1.13.4 报警概要......................................................................................................... 31
2.
2.1.1 2.1.2 2.1.3 2.2
第 2 章 访问更多的参数 .................................................33
等级 3(Level 3)......................................................................................... 33 配置等级......................................................................................................... 33 选择不同的访问等级................................................................................... 34 访问菜单中的参数 .........................................................................................35
1.1 这是什么样的仪表? .........................................................................................9
M218基础培训试验教材

M218 基础培训示例教材
M218 高速计数器示例
内容简介: 本文介绍如何通过M218的高速计数器功能实现冷弯成型机的定长裁剪控制。 1. 冷弯成型机控制系统描述: 冷弯成型机最基本的控制要求是将滚压成型完成的材料送到指定位置,然后进行压膜或 者裁切动作。 材料的输送电机由变频器控制。 在靠近压膜或者裁剪机构的滚轮上安装有用于 计长的旋转编码器,PLC实时检测该编码器的脉冲信号并换算成长度数值。当机器启动时, PLC将实际检测的长度数值与设定数值进行比较,控制变频器进行多段速定位。即当长度到 达阀值0时,变频器切换到低速;当长度到达阀值1时变频器输出0速。
Modicon M218 培训试验教材
植根中国 化繁为简的 SoMachine 平台
施耐德电气(中国)有限公司 LECA 市场部
M218 培训试验教程
目录
M218 基础培训示例教材 ................................................................................................................ 3 M218 高速计数器示例 ............................................................................................................ 3 PTO 使用示例 ......................................................................................................................... 17 PWM 示例 ............................................................................................................................... 47 串口 Modbus 通讯示例 ......................................................................................................... 52 自由协议通讯 ......................................................................................................................... 62 以太网通讯示例 ..................................................................................................................... 69 PID 示例 .................................................................................................................................. 77 RTC 实现示例 ......................................................................................................................... 84 M218 基础培训试验教材 ............................................................................................................ 103 试验一-SoMachine 软件入门 ............................................................................................ 103 试验二-开关量和模拟量试验 ........................................................................................... 113 试验三-PTO 试验 ............................................................................................................... 118 试验四-串口通信试验 ....................................................................................................... 128 试验五-以太网通信试验 ................................................................................................... 134
Moxa EDS-208系列产品说明书

P/N: 1802002080016*1802002080016*EDS-208 Series Quick Installation GuideMoxa EtherDevice SwitchVersion 5.2, January 2021Technical Support Contact Information/support2021 Moxa Inc. All rights reserved.OverviewThe EDS-208 series of Moxa EtherDevice™ Switches are entry-level8-port Ethernet Switches that provide a cost-effective solution for industrial Ethernet connections. EDS-208 provides a choice of 12 to 48 VDC power input. The switches can operate reliably in a temperature range of -10 to 60°C, and the rugged hardware design makes EDS-208 perfect for ensuring that your Ethernet equipment can be used in demanding industrial environments.Package ChecklistMoxa EDS-208 is shipped with the following items. If any of these items is missing or damaged, please contact your customer service representative for assistance.• 1 EDS-208 or EDS-208-M-SC or EDS-208-M-ST•Quick installation guide (printed)•Warranty cardFeaturesHigh Performance Network Switching Technology•10/100BaseT(X) (RJ45), 100BaseFX (SC/ST type, Multi-mode) •IEEE 802.3/802.3u/802.3x•Store and Forward switching process type, 1024 address entries Industrial Design•Operating temperature ranges from -10 to 60°C•Power inputs: 12 to 48 VDC•IP30, plastic case•DIN-Rail mounting abilityPanel Layout of EDS-2081.Heat dissipation orifices2.Terminal block for power inputand grounding3.Moxa Logo4.Power input LED5.10/100BaseT(X) Port6.TP port’s 100 Mbps LED7.TP port’s 10 Mbps LED8.DIN-Rail kitPanel Layout of EDS-208-M-SC/ST1.Heat dissipation orifices2.Terminal block for power inputand grounding3.Moxa Logo4.Power input LED5.10/100BaseT(X) Port6.TP port’s 100 Mbps LED7.TP port’s 10 Mbps LED8.FX port’s 100 Mbps LED9.100BaseFX Port10.DIN-Rail kitMounting Dimensions (unit = mm)DIN-Rail MountingThe plastic DIN-Rail attachment plate should already be fixed to the rear panel of EDS-208 when you take it out of the box. If you need to reattach the DIN-Rail attachment plate to EDS-208, make sure the DIN-Rail kit is situated towards the top, as shown in the figures below.STEP 1: Insert the top of the DIN-Rail into the slot. STEP 2:The DIN-Rail attachment unit will snap into place as shown below.To remove Moxa EDS-208 from theDIN-Rail, insert a flat-blade screwdriver horizontally into the DIN-Railkit under the EDS-208, and thenpull it upwards and releaseEDS-208 towards you away fromthe DIN-Rail.You may also take the following steps to remove the EDS-208 from the DIN-Rail.STEP 1: Press the middle of the flat side of the mounting kit as indicated. Pull the EDS-208 downwards.STEP 2:Release it towards you and away from the DIN-Rail.Wiring RequirementsYou should also pay attention to the following items:• Use separate paths to route wiring for power and devices. If powerwiring and device wiring paths must cross, make sure the wires are perpendicular at the intersection point.NOTE: Do not run signal or communications wiring and power wiring in the same wire conduit. To avoid interference, wires with different signal characteristics should be routed separately.• You can use the type of signal transmitted through a wire todetermine which wires should be kept separate. The rule of thumb is that wiring that shares similar electrical characteristics can bebundled together.• Keep input wiring and output wiring separated.•It is strongly advised that you label wiring to all devices in the system when necessary.Grounding EDS-208Grounding and wire routing help limit the effects ofnoise due to electromagnetic interference (EMI).Run the ground connection from the right mostcontact of the 3-contact terminal block to thegrounding surface prior to connecting devices.Wiring the Power InputsThe two left-most contacts of the 3-contact terminal block connector on EDS-208’s top panel are used for the DC input. Top and front views of one of the terminal block connectors are shown here.STEP 1: Insert the negative/positive DC wires intothe V-/V+ terminals.STEP 2: To keep the DC wires from pulling loose,use a small flat-blade screwdriver to tighten thewire-clamp screws on the front of the terminalblock connector.STEP 3: Insert the plastic terminal block connectorprongs into the terminal block receptor, which islocated on EDS’s top panel.Communication ConnectionsEDS-208 has 7 or 8 10/100BaseT(X) Ethernet ports, and 1 or 0 (zero) 100BaseFX (SC/ST-type connector) multi-mode fiber ports.10/100BaseT(X) Ethernet Port ConnectionThe 10/100BaseT(X) ports located on EDS-208’s front panel are used to connect to Ethernet-enabled devices.Below we show pinouts for both MDI (NIC-type) ports and MDI-X (HUB/Switch-type) ports, and also show cable wiring diagrams for straight-through and cross-over Ethernet cables.MDI Port PinoutsMDI-X Port Pinouts 8-pin RJ45 PinSignal 1Tx+ 2Tx- 3Rx+ 6 Rx- PinSignal 1Rx+ 2 Rx- 3 Tx+ 6 Tx-RJ45 (8-pin) to RJ45 (8-pin) Straight-Through Cable WiringRJ45 (8-pin) to RJ45 (8-pin) Cross-Over Cable Wiring100BaseFX Ethernet Port ConnectionThe concept behind the SC/ST port and cable is quite straightforward. Suppose you are connecting devices I and II. Contrary to electrical signals, optical signals do not require a circuit in order to transmit data.Consequently, one of the optical lines is used to transmit data from device I to device II, and the other optical line is used to transmit data from device II to device I, for full-duplex transmission.All you need to remember is to connect the Tx (transmit) port of device I to the Rx (receive) port of device II, and the Rx (receive) port of device I to the Tx (transmit) port of device II. If you make your own cable, we suggest labeling the two sides of the same line with the same letter (A-to-A and B-to-B, as shown below, or A1-to-A2 and B1-to-B2). SC-Port Pinouts SC-Port to SC-Port Cable WiringST-Port Pinouts ST-Port to ST-Port Cable WiringLED IndicatorsThe front panel of EDS-208 contains several LED indicators. The function of each LED is described in the table below.LED Color State DescriptionP AMBER OnPower is being supplied to the powerinputOffPower is not being supplied to thepower input10(TP) GREENOn TP port’s 10 Mbps link is active Blinking Data is being transmitted at 10 Mbps Off TP Port’s 10 Mbps link is inactive100(TP) GREENOn TP port’s 100 Mbps link is active BlinkingData is being transmitted at 100MbpsOff 100BaseTX Port’s link is inactive100M(FX) GREENOn FX port’s 100 Mbps link is active BlinkingData is being transmitted at 100MbpsOff 100BaseFX Port’s link is inactiveAuto MDI/MDI-X ConnectionThe Auto MDI/MDI-X function allows users to connect EDS-208’s10/100BaseTX ports to any kind of Ethernet device, regardless of how the Ethernet cable is wired. This means that you can use either astraight-through cable or cross-over cable to connect EDS-208 to Ethernet devices.Dual Speed Functionality and SwitchingEDS208’s 10/100 Mbps switched RJ45 port auto negotiates with the connected device for the fastest data transmission rate supported by both devices. All models of EDS-208 are plug-and-play devices, so that software configuration is not required at installation, or during maintenance. The half/full duplex mode for the switched RJ45 ports is user dependent and changes (by auto-negotiation) to full or half duplex, depending on which transmission speed is supported by the attached device.Switching, Filtering, and ForwardingEach time a packet arrives at one of the switched ports, a decision is made either to filter or to forward the packet. Packets with source and destination addresses belonging to the same port segment will be filtered, constraining those packets to one port, and relieving the rest of the network from the need to process them. A packet with destination address on another port segment will be forwarded to the appropriate port, and will not be sent to the other ports where it is not needed. Packets that are used in maintaining the operation of the network (such as the occasional multi-cast packet) are forwarded to all ports.EDS-208 operates in the store-and-forward switching mode, which eliminates bad packets and enables peak performance to be achieved when there is heavy traffic on the network.Switching and Address LearningEDS-208 has an address table that can hold up to 1,000 node addresses, which makes it suitable for use with large networks. The address tables are self-learning, so that as nodes are added or removed, or moved from one segment to another, EDS-208 automatically keeps up with new node locations. An address-aging algorithm causes the least-used addresses to be deleted in favor of newer, more frequently used addresses. To reset the address buffer, power down the unit and then power it back up. Auto-Negotiation and Speed SensingAll of EDS-208’s RJ45 Ethernet ports independently supportauto-negotiation for speeds in the 10BaseT and 100BaseTX modes, with operation according to the IEEE 802.3u standard. This means that some nodes could be operating at 10 Mbps, while at the same time, other nodes are operating at 100 Mbps.Auto-negotiation takes place when a “live” RJ45 cable is connected to the switch, and then each time a LINK is enabled. EDS-208 advertises its capability for using either 10 Mbps or 100 Mbps transmission speeds, with the device at the other end of the cable expected to similarly advertise. Depending on what type of device is connected, this will result in agreement to operate at a speed of either 10 Mbps or 100 Mbps.If an EDS-208 RJ45 Ethernet port is connected to a non-negotiating device, it will default to 10 Mbps speed and half-duplex mode, as required by the IEEE 802.3u standard.SpecificationsTechnologyStandards IEEE802.3, 802.3u, 802.3xProcessing Type Store and Forward, with IEEE802.3x fullduplex, non-blocking flow controlAddress Table Size 1,000 uni-cast addressesInterfaceRJ45 Ports 10/100BaseT(X) auto negotiation speed, F/Hduplex mode, and auto MDI/MDI-X connection Fiber Ports 100BaseFX ports (SC/ST connector)LED Indicators Power, 10/100 M (TP port), 100 M (FX port) PowerInput Voltage 12 to 48 VDCInput Current @ 24 VDC 0.07 A (EDS-208)0.1 A (EDS-208-M-SC/EDS-208-M-ST) Connection Removable 3-contact Terminal Block Overload CurrentPresentProtectionPresentReverse PolarityProtectionMechanicalCasing IP30 protection, plastic caseDimensions 40 x 109 x 95 mm (W x H x D)Weight 170 gInstallation DIN-RailEnvironmentOperating Temperature -10 to 60°C (14 to 140°F) Storage Temperature -40 to 70°C (-40 to 158°F)5 to 95% (non-condensing) Ambient RelativeHumidityRegulatory ApprovalsSafety UL 508EMI FCC Part 15, CISPR 32 class A EMS EN61000-4-2 (ESD),EN61000-4-3 (RS),EN61000-4-4 (EFT),EN61000-4-5 (Surge),EN61000-4-6 (CS)Shock IEC 60068-2-27Free Fall IEC 60068-2-32Vibration IEC 60068-2-6 WARRANTY 5 years。
MPLAB Code Configurator v2.25 1 产品说明书
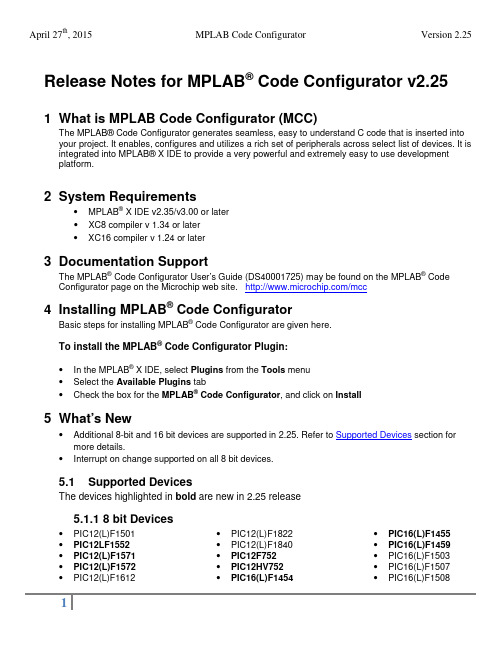
Release Notes for MPLAB® Code Configurator v2.251 What is MPLAB Code Configurator (MCC)The MPLAB®Code Configurator generates seamless, easy to understand C code that is inserted into your project. It enables, configures and utilizes a rich set of peripherals across select list of devices. It is integrated into MPLAB®X IDE to provide a very powerful and extremely easy to use development platform.2 System Requirements•MPLAB® X IDE v2.35/v3.00 or later•XC8 compiler v 1.34 or later•XC16 compiler v 1.24 or later3 Documentation SupportThe MPLAB® Code Configurator User’s Guide (DS40001725) may be found on the MPLAB® Code Configurator page on the Microchip web site. /mcc4 Installing MPLAB® Code ConfiguratorBasic steps for installing MPLAB® Code Configurator are given here.To install the MPLAB® Code Configurator Plugin:•In the MPLAB® X IDE, select Plugins from the Tools menu•Select the Available Plugins tab•Check the box for the MPLAB® Code Configurator, and click on Install5 What’s New•Additional 8-bit and 16 bit devices are supported in 2.25. Refer to Supported Devices section for more details.•Interrupt on change supported on all 8 bit devices.5.1 Supported DevicesThe devices highlighted in bold are new in 2.25 release5.1.1 8 bit Devices•PIC12(L)F1501 •PIC12LF1552 •PIC12(L)F1571 •PIC12(L)F1572 •PIC12(L)F1612 •PIC12(L)F1822•PIC12(L)F1840•PIC12F752•PIC12HV752•PIC16(L)F1454•PIC16(L)F1455•PIC16(L)F1459•PIC16(L)F1503•PIC16(L)F1507•PIC16(L)F1508•PIC16(L)F1509 •PIC16(L)F1512 •PIC16(L)F1513 •PIC16(L)F1516 •PIC16(L)F1517 •PIC16(L)F1518 •PIC16(L)F1519 •PIC16(L)F1526 •PIC16(L)F1527 •PIC16(L)F1574 •PIC16(L)F1575 •PIC16(L)F1578 •PIC16(L)F1579 •PIC16(L)F1613 •PIC16(L)F1614 •PIC16(L)F1615 •PIC16(L)F1618 •PIC16(L)F1619 •PIC16(L)F1703 •PIC16(L)F1704 •PIC16(L)F1705 •PIC16(L)F1707 •PIC16(L)F1708 •PIC16(L)F1709 •PIC16(L)F1713 •PIC16(L)F1716 •PIC16(L)F1717 •PIC16(L)F1718 •PIC16(L)F1719 •PIC16(L)F1764•PIC16(L)F1765•PIC16(L)F1768•PIC16(L)F1769•PIC16(L)F1782•PIC16(L)F1783•PIC16(L)F1784•PIC16(L)F1786•PIC16(L)F1787•PIC16(L)F1788•PIC16(L)F1789•PIC16(L)F1823•PIC16(L)F1824•PIC16(L)F1825•PIC16(L)F1826•PIC16(L)F1827•PIC16(L)F1828•PIC16(L)F1829•PIC16(L)F1847•PIC16(L)F1933•PIC16(L)F1934•PIC16(L)F1936•PIC16(L)F1937•PIC16(L)F1938•PIC16(L)F1939•PIC16(L)F1946•PIC16(L)F1947•PIC16F753•PIC16HV753•PIC16LF1554•PIC16LF1559•PIC18(L)F13K22•PIC18(L)F14K22•PIC18(L)F23K22•PIC18(L)F24K22•PIC18(L)F24K50•PIC18(L)F25K22•PIC18(L)F25K50•PIC18(L)F26K22•PIC18(L)F23K20•PIC18(L)F43K22•PIC18(L)F44K22•PIC18(L)F45K22•PIC18(L)F45K50•PIC18(L)F46K22•PIC18(L)F23K20•PIC18(L)F23K20•PIC18(L)F24K20•PIC18(L)F25K20•PIC18(L)F26K20•PIC18(L)F23K20•PIC18(L)F43K20•PIC18(L)F44K20•PIC18(L)F45K20•PIC18(L)F46K20April 27th, 2015 MPLAB Code Configurator Version 2.255.1.2 16 bit Devices•PIC24F08KA101 •PIC24FJ128GB202 •PIC24FJ64GA006•PIC24F08KA102 •PIC24FJ128GB204 •PIC24FJ64GA008•PIC24F(V)08KM101 •PIC24FJ128GB206 •PIC24FJ64GA010•PIC24F(V)08KM102 •PIC24FJ128GB210 •PIC24FJ64GA102•PIC24F(V)08KM202 •PIC24FJ128GC006 •PIC24FJ64GA104•PIC24F(V)08KM204 •PIC24FJ128GC010 •PIC24FJ64GA106•PIC24F(V)16KM102 •PIC24FJ16GA002 •PIC24FJ64GA108•PIC24F(V)16KM104 •PIC24FJ16GA004 •PIC24FJ64GA110•PIC24F(V)16KM202 •PIC24FJ192GA106 •PIC24FJ64GA202•PIC24F(V)16KM204 •PIC24FJ192GA108 •PIC24FJ64GA204•PIC24F16KA101 •PIC24FJ192GA110 •PIC24FJ64GA306•PIC24F16KA102 •PIC24FJ192GB106 •PIC24FJ64GA308•PIC24F(V)16KA301 •PIC24FJ192GB108 •PIC24FJ64GA310•PIC24F(V)16KA302 •PIC24FJ192GB110 •PIC24FJ64GB002•PIC24F(V)16KA304 •PIC24FJ256DA106 •PIC24FJ64GB004•PIC24F(V)32KA301 •PIC24FJ256DA110 •PIC24FJ64GB106•PIC24F(V)32KA302 •PIC24FJ256DA206 •PIC24FJ64GB108•PIC24F(V)32KA304 •PIC24FJ256DA210 •PIC24FJ64GB110•PIC24FJ128DA106 •PIC24FJ256GA106 •PIC24FJ64GB202•PIC24FJ128DA110 •PIC24FJ256GA108 •PIC24FJ64GB204•PIC24FJ128DA206 •PIC24FJ256GA110 •PIC24FJ64GC006•PIC24FJ128DA210 •PIC24FJ256GB106 •PIC24FJ64GC010•PIC24FJ128GA006 •PIC24FJ256GB108 •PIC24FJ96GA006•PIC24FJ128GA008 •PIC24FJ256GB110 •PIC24FJ96GA008•PIC24FJ128GA010 •PIC24FJ256GB206 •PIC24FJ96GA010•PIC24FJ128GA106 •PIC24FJ256GB210•PIC24FJ128GA108 •PIC24FJ32GA002•PIC24FJ128GA110 •PIC24FJ32GA004•PIC24FJ128GA202 •PIC24FJ32GA102•PIC24FJ128GA204 •PIC24FJ32GA104•PIC24FJ128GA306 •PIC24FJ32GB002•PIC24FJ128GA308 •PIC24FJ32GB004•PIC24FJ128GA310 •PIC24FJ48GA002•PIC24FJ128GB106 •PIC24FJ48GA004•PIC24FJ128GB108 •PIC24FJ64GA002•PIC24FJ128GB110 •PIC24FJ64GA0046 Repairs and Enhancements# ID Description Device(s)1. MCC-1456 Pin Names with special characters give warnings ingenerated code All devices2. MCC-1457 System Module EC Value does not reload All 16 bit devices3. MCC-1458 When ADC enabled and uses VREF+ and VREF- pinsmcc generates a source code where TRISA0 and TRISA1bits are cleared so it overwrites the connected referencevoltagePIC24FJ128GA204 andPIC24FJ128GB204 family4. MCC-1459 Pin 44 is not available as a PPS pin for SPI1 PIC24FJ128GC006April 27th, 2015 MPLAB Code Configurator Version 2.25 # ID Description Device(s)5. MCC-1460 Primary Oscillator range is incorrect PIC24FJ128GA204 and PIC24FJ128GB204 family6. MCC-1461 At SPI1 module SPI1_ExchangeBuffer() function uses theenhanced buffer mode of SPI but SPI1CON1L.ENHBUFbit is cleared.PIC24FJ128GA204 andPIC24FJ128GB204 family7. MCC-1284 Interrupt on change (IOC) not available All 8 bit devices8. MCC-910 Timer 0 – Incorrect Variables declared K20\K22 devices9. MCC-1290 Seed Value not getting loaded in the initializer function PIC16F161910. MCC-1470 RTCC module is missing PIC24FJ64GB004 family 7 Known IssuesThe following are enumerated issues for the MPLAB® Code Configurator.# ID Description Device(s)1. MCC-1419 Does not support both commas and periods entered in atextbox as decimal separator. Currently MCC accepts inputsonly with a period as decimal separator.All devices2. MCC-1190 Configuration setting ZCD compatible with XC8 v1.33 only PIC16(L)F161x devices3. MCC-1250MCC-1253 I2C driver errors when multiple initializer are used All 8 bit devices4. MCC-1259 Timer 2/4/6 input pins not configured as digital PIC16(L)F161x devices5. MCC-1295 I2C slave driver does not fit in RAM PIC12(L)F18226. MCC-1466 I2C PPS register value incorrect for RC3 PIC16(L)F161x devices7. MCC-1321 PPS register configuration is wrong. PIC16F17078. MCC-1102 CN\IOC functionality not supported All 16 bit devices9. MCC-1462 MCCP Compare Alert does not go away on selecting outputpin(s) All PIC24F KM devices 10. MCC-1455 Cannot set PWM2 on RA5 through APFCON PIC16(L)F1454/911. MCC-1434 Changing oscillator selection from INTOSC oscillator toexternal clock in Config1 bits does not show up 'ExternalClock' text box (in 'Clock' label) to input external clockfrequency values.PIC12LF1552,PIC16(L)F176xPIC16(L)F157x,PIC16(L)F161xApril 27th, 2015 MPLAB Code Configurator Version 2.25 8 Customer Support8.1 The Microchip Web SiteMicrochip provides online support via our web site at . This web site is used as a means to make files and information easily available to customers. Accessible by using yourfavorite Internet browser, the web site contains the following information:•Product Support – Data sheets and errata, application notes and sample programs, design resources, user’s guides and hardware support documents, latest software releases and archivedsoftware• General Technical Support – Frequently Asked Questions (FAQs), technical support requests, online discussion groups/forums (), Microchip consultant programmember listing• Business of Microchip – Product selector and ordering guides, latest Microchip press releases, listing of seminars and events, listings of Microchip sales offices, distributors and factoryrepresentatives8.2 Additional SupportUsers of Microchip products can receive assistance through several channels:•Distributor or Representative•Local Sales Office•Field Application Engineering (FAE)•Technical SupportCustomers should contact their distributor, representative or field application engineer (FAE) forsupport. Local sales offices are also available to help customers. A listing of sales offices andlocations is available on our web site.Technical support is available through the web site at: 。
PT208使用手册

6
数字化·智能压力/差压变送器
测量开口容器液位时,变送器装在靠近容器的底部,以便测量其上方液面高度所对应的压力。容器液 位的压力,作用于变送器的高压侧,而低压侧通大气。如果被测液位变化范围的最低液位,在变送器安装 处的上方,则变送器必须进行正迁移。 密闭容器的液位测量 在密闭容器中,液体上面容器的压力 P0 影响容器底部被测的压力。因此,容器底部的压力等于液面 高度乘以液体的比重再加上密闭容器的压力 P0。为了测得真正的液位,应从测得的容器底部压力中减去容 器的压力 P0。为此,在容器的顶部开一个取压口,并将它接到变送器的低压侧。这样容器中的压力就同时 作用于变送器的高低压侧。结果所得到的差压就正比于液面高度和液体的比重乘积了。 导压连接方式 1)干导压连接 如果液体上面的气体不冷凝,变送器低压侧的连接管就保持干的。这种情况称为干导压连接。决定变 送器测量范围的方法与开口容器液位的方法相同。 2)湿导压连接 如果液体上面的气体出现冷凝, 变送器低压侧的导压管里就会渐渐地积存液体, 从而引起测量的误差。 为了消除这种误差,预先用某种液体灌充在变送器的低压侧导压管中,这种情况称湿导压连接。 上述情况,使变送器的低压侧存在一个压头,所以必须进行负迁移。 测量误差 导压管使变送器和流程工艺管道连在一起,并把流程工艺道上取压口处的压力传输到变送器。在压力 传输过程中,可能引起误差的原因如下: 1)泄漏; 2)摩擦损失(特别使用洁净剂时) ; 3)液体管路中有气体(引起压头误差) ; 4)气体管路中存积液体(引起压头误差) ; 5)两边导压管之间因温差引起的密度不同(引起压头误差) ; 减少误差的方法 1)导压管应尽可能短些; 2)当测量液体或蒸汽时,导压管应向上连到流程工艺管道,其斜度应小于 1/12 ; 3)对于汽体测量时,导压管应向下连接到流程工艺管道,其斜度应不小于 1/12 ; 4)液体导压管的布设要避免中间出现高点,气体导压管的布设要避免中间出现低点; 5)两导压管应保持相同的温度; 6)为避免摩擦影响,导压管的口径应足够大; 7)充满液体导压管中应无气体存在; 8)当使用隔离液时,两边导压管的液体要相同;
AB-208灯光智能控制使用说明

智能报警联动控制器安装指南
智能报警联动控制器只需一个常闭或常开输入:如红外探头,对射,紧急按钮等常闭端,即可联动另一端的强电开关(常开同样效果)。
1. 性能特点:
输出即时跟随输入功能(输入关输出也关;输入开输出也开)
输出延时跟随输入功能时间可由用户通过拨码设定(精确到5秒),最长10分钟
3.指示灯说明
●电源指示灯: 通电后就会亮
●状态指示灯: 即时联动(未拨码)情况下,快速闪烁;延时联动(拨码)情况下,1秒钟闪烁1次
●高压操作指示灯:高压继电器操作时变换指示
●低压操作指示灯:低压继电器操作时变换指示
4.使用说明
输出即时跟随输入功能不拨码,即2--8位拨码开关都是OFF
输出延时跟随输入功能拨码(见拨码开关对应时间表),最短延时为5秒,最长10分钟
具体的时间=下表的秒数* 基数(基数为5秒)
例:用户希望延时为30秒,应当拔开关数设成6,则实际继电器的闭合延迟时间将为:6 *5=30秒。
其它以此类推。
;用户想采用其他基数请在定购产品时说明。
拨码开关第1位用来设置输入端接法,1为OFF输入端接常闭,1为ON输入端接常开。
AVer Document Camera Setup Guide

Setup your AVer Document Camera from home!Please first identify which AVer document camera you are using to know what software to install.A+ Suite (Sphere2 on Win10/Mac) or Sphere Lite (Chromebooks): AVer U70+, AVer U50, AVer M70HD, AVer 300AFHD, AVer F70W, AVer F50-8M, AVer F17-8M, M17-13MAVerTouch (Win10/Mac): AVer M15W, AVer M15-13M, AVer M70WA+ Interactive Software (Old Version on Win/Mac): V300AF ASIC, SPC300 ASIC, SPC300 +, CP130, CP150, CP300, SPB350, SPB370, CP135, CP155, CP355, V355AF, V310AF, SPB350+, V300AF+, F30, F50, U10, U15, AP20,M50, W30Sphere (Old Version on Win/Mac): PL50, SPB350, SPB370, SPB350+, M50, M70, V300AF+, F50, F30, F15 U15, W30A+ Suite (Sphere2):1.Download the A+ Suite software on your computer, go to:https:///education/support/aplus-suiteSelect the OS you are using to download the software (we will use Win10 in this tutorial)2.Open the downloaded .exe file to start the installationFollow the setup wizard to install the A+ Suite software3.After installation is completed, open the Sphere2 software4.Plug in the power adapter to your document camera and turn it on by pressing the power button (does notapply to U-series doc cams, your document camera may look different than the one pictured)5.Locate a USB port on your computer and connect your camera to it via USB cable that is included6.Select the visualizer icon on the top right of the Sphere2 software and select your camera7.You are now connected to your AVer document camera and can begin teaching!If you own an AVer F70W and wish to connect to your computer wirelessly, please follow this guide: https:///education/downloads/F70WV2-Quick-Guide-EN-v5-2020-02-24.pdfSphere Lite (Chromebook):1.Download the Sphere Lite software on your Chromebook, go to:https:///webstore/detail/sphere-lite/bhmibpbadaengbikmoglphhlhioajdjn?hl=enunch Sphere Lite app after installing3.Plug in the power adapter to your document camera and turn it on by pressing the power button (does notapply to U-series doc cams, your document camera may look different than the one pictured)4.Locate a USB port on your Chromebook and connect your camera to it via USB cable that is included5.Select your camera on the bottom left. You are now connected to your AVer document camera and can beginteaching!AVerTouch:1.Download the AVerTouch software on your computer, go to:https:///education/support/avertouchSelect the OS you are using to download the software (we will use Win10 in this tutorial)2.Unzip the downloaded .zip file3.Open the extracted folder and run the .exe to start the installation4.Follow the setup wizard to install the AVerTouch software5.After installation is completed, open the AVerTouch software6.Plug in the power adapter to your document camera and turn it on by pressing the power button (yourdocument camera may look different than the one pictured)7.Locate a USB port on your computer and connect your camera to it via USB cable that is includedNote: For M15W/M70W users, please make sure WiFi is turned off when trying to do a USB connection 8.The connected visualizer will appear within the AVerTouch software. Click the play icon to connect to thecameraIf you own an AVer M15W/M70W and wish to connect to your computer wirelessly, please follow this guide: M15W: https:///education/downloads/M15W-instruction-manual-EN-2019-12-20.pdfM70W: https:///education/downloads/M70W-instruction-manual-EN-v1-2019-12-20.pdfA+ Interactive Software:1.Download the A+ Interactive Software on your computer, go to:https:///education/support/averplusSelect the OS you are using to download the software2.Unzip the downloaded .zip file3.Open the extracted folder and run the .exe to start the installation4.Follow the setup wizard to install the A+ Interactive Software5.After installation is completed, open the A+ Interactive Software6.Power on and connect your doc cam to your computer via USB cable7.Select your visualizer within the software and you are now connected!Sphere:1.Download the Sphere on your computer, go to:https:///education/support/sphereSelect the OS you are using to download the software2.Run the downloaded .exe to start the installation3.Follow the setup wizard to install the Sphere software4.After installation is completed, open the Sphere Software5.Power on and connect your doc cam to your computer via USB cable6.Select your visualizer within the software and you are now connected!Using your AVer Document Camera with other platforms (Zoom, Skype, Google Hangout).Open up your software of choice and connect your AVer document camera to your computer via USB cable.Select your AVer document camera as your visualizer and you are successfully connected!(Please refer to Zoom, Skype, or Hangout user guides to navigate through their software)Zoom:https:///hc/en-us/articles/201362033-Getting-Started-on-Windows-and-MacSkype:https:///en/skype/windows-desktop/start/Hangout:https:///hangouts/?hl=en#topic=6386410Note: The following AVer doc cams are not UVC compliant and are not compatible with other platforms: F50, M70, PL50, W30, W30HD, Tabcam, 355AF, M50More HelpFor FAQs, technical support, software and instruction manual download, please visit:https:///education/support/Contact InformationAVer Information Inc.668 Mission Ct. Fremont, CA 94539, USAToll-free: 1(877)528-7824Local: 1(408)263-3828********************。
AN208

Rev. 0.2 9/06Copyright © 2006 by Silicon LaboratoriesAN208AN208S E N S O R L E S S B R U S H L E S S DC M O T O R R E F E R E N C E D E S I G N1. IntroductionThis reference design provides a hardware and software solution for Sensorless Brushless dc motors. This document includes complete schematics, printed circuit board layout, and firmware. The Sensorless Brushless dc motor reference design may be used as a starting point for motor control system designers using Silicon Laboratories MCUs, significantly reducing the design time and time to market.Brushless dc motors consist of a permanent magnet rotor with a three-phase stator winding. Brushless dc motors evolved from conventional dc motors where the function of the brushes is replaced by electronics. Brushless dc motors offer longer life and less maintenance than conventional brushed dc motors.Most Brushless dc motor designs historically use Hall effect sensors to measure the position of the rotor. Hall effect sensors provide absolute position information required to commutate the motor. Using Hall effect sensors provides simple, robust commutation and performance roughly comparable to brushed dc motors. One of the major barriers limiting the market penetration of Brushless dc motors has been the cost of using Hall effect sensors. The Hall effect sensors themselves are not particularly expensive. However, the Hall effect assembly adds significant expense to the cost of manufacturing the motor. Hall effect sensors also typically require 5 additional wires, adding to the installation costs.A “Sensorless” Brushless dc motor does not have Hall effect sensors. Sensorless Brushless dc motors employ more sophisticated electronics using some alternative scheme to control the commutation of the motor. The most common scheme involves measuring the back EMF of the motor and using this information to control the commutation of the motor.Most computer hard disc drives use a sensorless brushless dc motor. However, these small motor drives use a linear regulator to control the voltage applied to the motor. This works well for small motors, but is too inefficient to use for motors greater than a few watts. Larger motors require PWM control for efficient operation. Using PWM control makes the task ofmeasuring the back EMF of the motor more difficult, due to noise coupled from the active windings.Sensorless Brushless dc motors are well suited for fans and rotary pumps from a few watts up to about 1 kW. Fans and pumps’ loads are predictable and fairly well behaved. Most Sensorless Brushless dc motors do notprovide the same level of dynamic speed control available from Hall effect controlled BLDC motors or dc motors. While it is theoretically possible to achieve high-performance from a sensorless BLDC motor using sophisticated vector control, most practical sensorless BLDC implementations address the much simpler fan and pump applications. This reference design is targeted for simple fan applications.Sensorless BLDC motor drives often compete against ac induction motors for certain applications. A system designer must consider the power level, efficiency requirements, and starting requirements when choosing between BLDC motors and ac induction motors. BLDC motors are most often used for small motors rangingfrom 1 watt to 1 kW. AC induction motors are readily available from 250 W to 10 kW or more. BLDC motors offer potentially higher efficiency than ac induction motors. This is due to the fact that ac motors have high rotor losses while BLDC motors do not waste energy in magnetizing the rotor. AC induction motors are much easier to start than sensorless BLDC motors. Thecomplexity of starting a fully loaded BLDC motor often makes the ac induction motor a better choice, particularly for piston pumps and compressors.AN2082Rev. 0.22. Theory of OperationBrushless dc motors have a dual personality. To fully understand Sensorless Brushless dc motor control it is necessary to understand both dc motor characteristics and Stepper motor characteristics. When commutated using Hall effect sensors, the torque speed characteristics of the Brushless dc motor are virtually identical to a conventional dc motor. The ideal no load speed is a linear function of the applied voltage. The torque and motor current are at a maximum at zero speed and decrease to zero at the maximum speed. The torque-speed characteristics of a dc motor are shown in Figure 1. Under ideal conditions, the characteristics of a sensorless BLDC motor are similar.The characteristics of a stepper motor are quite different. The motor current in a stepper motor is not proportional to the load torque. The motor winding resistance typically limits the current in a stepper motor. The motor winding resistance of a stepper motor is normally an order of magnitude higher than a BLDC motor. An ideal model for a stepper motor is shown in Figure 2.Figure 2. Stepper Motor ModelThe motor is driven with a constant voltage. When the motor is at a standstill, the back EMF is zero and the current is at its maximum value. As the motor speed increases the back EMF will increase, reducing the voltage across the motor resistance, and the motorcurrent will decrease. The available torque for a stepper motor is proportional to the current forced through themotor windings. The available torque is at its maximum value when the motor is at a standstill. The available torque decreases as the motor speed increases. If the load torque ever exceeds the available torque the motor will stall. Figure 3. Stepper Motor CharacteristicsThe performance of the stepper motor may be improved using a variable voltage drive. By increasing the voltageapplied to the stepper motor in proportion to the velocity,the available torque will remain constant and the fancan be driven to a higher velocity before stalling as shown in Figure 3.A BLDC motor can also be considered as an unusual stepper motor. A 4-pole 12 V BLDC motor is functionally equivalent to a 12-step per revolution stepper motor with a voltage rating of about 1 V. A typical Stepper motor has a much higher step count, higher voltage, and higher resistance. A typical hybrid permanent-magnet stepper motor has a step angle of 1.8º, or 200 steps per revolution. A 12 V stepper motor might have a resistance of 30 Ω, compared to less than 1 Ω for a similar size BLDC motor. The stepper motor is optimized for precise angular positioning and constant voltage drive. The BLDC motor is optimized for Hall effect commutation and variable voltage drive.2.1. PWM SchemeMost Hall effect BLDC motors use a three-phase bridge to drive the motor windings. A Three-Phase bridge isshown in Figure 4.AN208Rev. 0.23Figure 4. Three-Phase BridgeThe most common drive method is to use blockcommutation and apply a PWM signal to only thebottom transistors as shown in Table 1. Depending onthe position of the motor and the Hall effect code, theappropriate step pattern is applied to the motor. As themotor rotates, the step pattern will increment throughthe table entries. Using this method, at any point in timethere is only one top transistor in the continuous ONstate and only one bottom transistor being driven by thePWM signal.Considering the motor phases, one phase is drivenhigh, one phase is being pulse-width modulated, andone phase is open. The open phase is noted in thetable. However, there is a problem using the open-phase to sense the back EMF when pulse-widthmodulating only the bottom transistors.Figure 5. Low-Side PWM Back EMFConsider the BLDC motor winding shown in Figure 5. Inthis case the motor is at the first state of thecommutation table. A pulse-width modulated signal isapplied to phase A, phase B is driven high, andphase C is open. The back EMF that we are interestedin is actually the voltage from phase C to the centerconnection labeled point Y. The problem is that thecenter of the Y connection is not a constant dc voltage.Assuming that the resistance and inductance ofwindings A and windings B are the same, the voltage atpoint Y will be halfway between phase A and phase B.The voltage at point Y will be approximately half thesupply voltage when phase A is driven low. Whenphase A is high, the center point Y will be approximatelyequal to the upper supply voltage. The voltage on theopen phase C is now the voltage at center-point Y plusthe back EMF of the motor. The voltage at phase C isalso clamped to the upper rail by the MOSFET bodydiodes in the inverter bridge. The result is a pulse widthmodulated waveform where the minimum voltage levelis equal to the back EMF of the motor. While it ispossible to filter out the PWM signal or sample thevoltage during the PWM on-time, working with thiswaveform is problematic.A better approach is to use a symmetric PWM scheme.A symmetric PWM scheme is any PWM scheme wherethe active top and bottom transistors are turned on andoff together. The simplest method is to apply identicalPWM signals to the top and bottom transistorsaccording to Table 2. This commutation table is similarto the low side PWM commutation table except that thehigh side transistors are pulse-width modulated insteadof just being turned on.Table 1. Low-Side PWM CommutationTop Bottom OpenA B C A B C Phase0ON PWM C1ON PWM B2ON PWM A3ON PWM C4ON PWM B5ON PWM AAN2084Rev. 0.2During the first state of Table 2, an identical PWM signal is applied to both the A bottom transistor and the B top transistor. The result is that Phase A will go low when Phase B goes high and visa versa. If the A and B windings are balanced, the center point Y will remain mid-rail even though phase A and phase B are being pulse-width modulated. The voltage on phase C is now roughly equal to the back EMF voltage. There may be some residual PWM noise due to the second order effects of unbalanced windings and capacitive coupling. However, the unwanted PWM signal is reduced by at least an order of magnitude, as shown in Figure 6.Figure 6. Symmetric PWM Back EMF3. Back EMF WaveformsMost sensorless BLDC control systems use the back EMF zero crossing time as a control variable for a phase locked loop. Instead of using the zero-crossing time, this reference design measures the back EMF voltage at middle of the commutation period using the ADC and uses the voltage measurement to control the commutation. This method provides higher resolution and always provides a robust feedback signal even asthe motor approaches a stall condition. When using the zero-crossing time as a feedback signal, special measures must be taken when a zero crossing does not fall within the measurement window.The back EMF voltage for three different cases is shown in Table 3. If the voltage and speed are just right the voltage ramp will be centered within the commutation period and the midpoint voltage will measure half of the supply rail. If the voltage is too low or the speed is too fast the voltage ramp will be shifted up and to the right. If the voltage is too high or the speed is too slow, the voltage ramp will be shifted down and to the left. The feedback loop should work to keep the mid-point voltage at mid-rail.3.1. Safe Operating RangeWhen driving a Sensorless BLDC motor from a MCU there are two output variables, the motor Voltage V and the motor speed ω. Figure 7 shows the output voltage verses speed characteristics for a sensorless BLDC motor. Three lines are labeled in Figure 7. The middle line is the ideal “no load” line with V equal to ω times the motor constant K E . This line represents the optimum voltage for a perfect motor with no friction.Table 2. Symmetric PWM CommutationTop Bottom Open A B CA BCPhase 0PWMPWMC 1PWM PWM B 2PWMPWM A 3PWM PWMC 4PWM PWM B 5PWM PWMATable 3. Back EMF ControlAN208Rev. 0.25 Figure 7. Output Voltage and SpeedThe maximum current is normally limited by thecapability of the power transistors. The maximum boostvoltage is then the maximum inverter current times thewinding resistance. The upper line in Figure 7 is theideal voltage plus the maximum boost voltage. This linedefines the maximum bounds for safe operation. Thelower line is the ideal voltage minus the maximum boostvoltage. This line defines the minimum bounds for safeoperation. While not intuitive, it is quite possible to getan over-current condition by driving the motor with avoltage that is too low for a particular speed.Figure 8. Safe Operating AreaThe Safe Operating Area for the Sensorless BLDCmotor is shown in Figure 8. Above the maximum line thevoltage is dangerously too high. Below the minimum linethe voltage is dangerously too low. The area betweenthe ideal line and the max line is labeled the positivetorque region. In normal steady state operation, theoutput variables will operate in the positive torqueregion.The area below the ideal line is labeled the negativetorque region. While most simple fan and pumpapplications do not require negative torque, operation inthe negative area is permitted. If the motor speedcommand is decreased, the control system will outputvalues in the negative torque region until the operatingpoint is re-stabilized. While it is possible to prohibitoperation in the negative torque region, this mayadversely affect the stability of the control system.The safe operating area is important because it is veryeasy to exceed the limit using conventional controltechniques. If we ignore the safe operating area anduse a simple PI controller to regulate the output voltage,the control loop will output excessive voltage and thepower transistors may be damaged.If we drive the motor with a voltage corresponding to themaximum line, we are forcing maximum current into themotor at all times. This will provide the maximumavailable torque at all times and it is unlikely that themotor will stall. However, the no load efficiency will bevery low and cogging torque may be a problem.Cogging torque is the variation in torque caused by apulsating electromotive force. Stepper motors aredesigned to operate on the max line with low coggingtorque. Most BLDC motors are not designed for thiskind of operation. Excessive cogging torque can causevibration, noise, and stability problems.This reference design uses a novel control techniqueentitled “Constant Voltage Control with SpeedDependent Limiting”. The goal of this controlmethodology is to provide a simple and robust controlalgorithm using a single control loop while keeping theoutput speed and voltage within the Safe OperatingArea.The control technique is illustrated in Figure 9. Theinput speed control potentiometer controls the targetoperating point indicated by the dot on the ideal line. Ifthe error signal is zero, the output voltage and speedare set according to the speed potentiometer. As thespeed control is varied, the target operating point willvary along the ideal line.The bold line indicates variation in the output voltageand speed due to the error signal. A small positive errorsignal from the feedback control system will result in adecrease in speed while the voltage remains constant.The voltage will remain constant until the speed reachesthe limit set by the maximum line. If the error signal islarge enough to exceed the limit, both voltage andspeed are reduced according to the maximum limit.In a similar fashion, a small negative error signal willresult in an increase in speed. If the negative error isincreased beyond the bounds set by the minimum line,the voltage will be increased.The resulting control loop is very stable. The motor isdriven with a constant voltage, as long as the loadAN2086Rev. 0.2torque and acceleration are within the bounds set by the minimum and max limits. In this region the motor behaves like a dc motor with a constant voltage drive. A small increase in load torque will result in a small decrease in speed.For large positive errors signals, the motor voltage is reduced to keep the current below the maximum limits. In this region the motor behaves as a constant current or constant torque drive.Figure 9. Constant-Voltage with Limiting3.2. Starting One major problem with using the back EMF to control the commutation of a sensorless BLDC motor is that the back EMF is not present or is too small to be useful until the motor is rotating at some minimum speed. Thecommon solution is to drive the BLDC motor like astepper motor to align the motor and accelerate themotor up to some nominal speed. This requires that the control system have multiple modes of operation. While it is generally undesirable to have a control system withmultiple modes of operation, it is unavoidable in thiscase. A common pitfall of systems with multiple modesof operation is instability during the transition from one control mode to another. Special considerations are required in the running stage to ensure system stabilityduring the transitions.The motor state diagram is shown in Figure 10. The system is initially in the STOP state. Pressing the Start button will advance to the ALIGN state. The motor willthen advance automatically to the START and RUNstates. An over-current error will reset the motor to the STOP state. Figure 10. SBLDC State Diagram3.3. AlignmentThe alignment state consists of two stages—the Alignment Ramp and the Alignment Delay. During the Alignment Ramp, one of the motor windings is excited by PWMing the top of one phase and the bottom of another phase. The PWM duty cycle is initially at zero percent and is ramped up to 50% plus the starting boost voltage. The voltage is increased using a linear ramp with a fixed delay time between voltage increments. The current in the motor winding will depend on the motor inductance and winding resistance. For duty cyclesbelow 50% the current will be discontinuous. The current will increase while the transistors are on and decrease to zero after the transistors turn off as shown in Figure 11. The peak and average dc current for duty cycles equal to or less than 50% can be calculated using Equation 1.The PWM duty cycle will always be above 50% while running.I avg I peak VL---d×==AN208Rev. 0.27Equation 1. Peak and Average CurrentFor duty cycles above 50% the current will be continuous. Usually a higher current is desired for alignment. Above 50%, a small change in duty cycle will result in a much large change in average dc current. The starting boost voltage is typically a very small number.The second part of the alignment phase consists of asimple delay. The voltage is held constant for a period oftime. The alignment delay time should be long enough to allow the motor to align to the excited pole position. A one second ramp time and a two second delay time works well for the test motor with no fan. When using a large fan, a time of several seconds may be required. Finding the optimal delay time requires some experimentation.The alignment stage ensures that the motor starts froma known position. Without the alignment stage the motormight miss the first several critical commutations in the starting acceleration ramp. If the motor does not align during this stage a motor stall is more likely in the starting phase.During the alignment stage the system is in a relativelybenign state. The dc current is predictable and wellregulated. The power dissipated in the motor can becalculated from the motor winding resistance. A currentmeasurement is only needed to protect against wiringerrors.Most BLDC motors are optimized for high-speedoperation and have very limited torque in the alignmentphase. This is not too much of a problem for small fans,but it does preclude the use of sensorless control insome other applications. The torque is limited by theinverter current and motor design. Over-sizing the inverter or using a lower speed motor can increase the starting torque.3.4. Starting During the starting phase the BLDC motor is driven like a stepper motor. The motor is commutated at first very slowly and then velocity is increased linearly using a linear velocity ramp table. The voltage is also increasedin proportion to the velocity with additional boost voltageto keep the current at a constant value. The motor winding resistance normally limits the boost voltage.The acceleration ramp table ramps the motor speedover a 30:1 range from 25 to 750 rpm. The maximumvalue of 750 rpm was chosen to be one tenth of the maximum speed of the motor. The closed loop sensorless control will then operate over a 10:1 range from 750 to 7500 rpm. The back EMF at 750 rpm will be one tenth of the rated voltage.The key to getting the motor up to 750 rpm is to use alarge enough acceleration ramp table with a sufficiently large ratio of minimum to maximum. A ratio of 30:1 can be achieved using a table with only 192 bytes of data. This also permits the efficient use of an 8-bit table index. Experimental results using a smaller 16-byte table withan 8:1 range proved unsatisfactory. If the table is too small, the initial velocity will be too fast or the finalvelocity will be too slow.The voltage of the motor is also ramped during the acceleration phase. If the voltage were held constant at the alignment value, the current would decrease during the motor acceleration. Initially the current is only limited by the motor resistance. As the motor starts turning, the back EMF of the motor will subtract from the voltageacross the motor resistance. This results in a decrease in motor current and a corresponding decrease in theamount of available torque.Assuming the motor will accelerate in step with the commutation period, the back EMF will be proportional to the motor velocity and inversely proportional to themotor period. The motor voltage ramp may be calculated by dividing a constant by the value in theramp table. By increasing the voltage during theacceleration phase the motor current can be held at aconstant value. This ensures maximum available torqueduring the acceleration phase.If the motor stalls at any point, the back EMF will be zero, and the assumption of motor velocity is no longervalid. The resulting motor voltage will be too high andthe current may be much higher than expected. This isproblematic for small motors and can be disastrous forlarge motors.The solution is to monitor the dc motor current during acceleration and to shut down if the motor current getstoo high. The back EMF is not sufficiently large to detect if the motor is moving. A current limit is not neededduring the starting phase if the motor voltage is limited to the maximum inverter current times the motor resistance, though this will severely limit the starting torque on all but the smallest motors.3.5. RunningThe minimum Running speed and voltage are dictatedby the starting parameters. In this example, the minimum speed is 750 rpm. The minimum voltage is10% plus the boost voltage. At the lower operatingAN2088Rev. 0.2point, the motor is being over-driven by a voltage that is intentionally higher than necessary for stable closed loop operation. Since the motor is being driven like a stepper motor, the cogging torque and motor vibration will be higher in the starting phase.3.6. Back EMF MeasurementsThe back EMF is measured at three points, as shown in Figure 12. The midpoint voltage is the primary control variable for closed loop control. The two voltage measurements at one quarter and three fourths are used for stall detection. The current measurement is used for over current detection. The time slots are discussed in further detail in the software description.Stall detection is achieved by measuring the voltage at quarter points over two cycles. The difference betweenthe minimum and maximum of these four points is anindication of the back EMF of the motor. If the back EMFis greater than a certain value, we can deduce withreasonable certainty that the motor is indeed running. Ifthe back EMF is too small to give a usefulmeasurement, we cannot know for certain if the motor isstalled or running. Thus, the stall detection operatesonly in the running phase. The example implementationilluminates an LED when a stall condition is detected.4. Hardware DescriptionThe schematic diagram for the Sensorless BLDC Motor reference design is in Appendix A. The circuit consists of the C0851F310 Microcontroller, three-phase power MOSFET bridge, three dual gate drivers, sense voltage resistive dividers, current amplifier, speed control potentiometer, two function switches, USB-UART bridge, and voltage regulator.Port P1 is configured as push-pull outputs and is connected to the three dual gate drivers. The P1 port pins are sequenced, alternating between bottom and top starting with phase A in the least significant bit. P1.0-1.5 corresponds to A bottom, A top, B bottom, B top, C bottom, and C top respectively. This sequence facilitates commutation using a simple pattern with the Crossbar pin skip register.Each of the three output phases are connected to a simple resistive divider. The resistive divider will divide the phase output voltage by six. This ratio permits accurate ADC measurements up to 19.8 volts. The 5 V tolerant port pins offer protection against phase voltages up to 30 Volts. The motor supply is 12 V nominal when loaded with the motor turning at full-speed. The unloaded voltage may climb as high as 18 V for the recommended wall mounted transformer.A capacitor across the lower resistor of each divider forms simple single-pole low-pass RC filter. Each filter is tuned approximately one decade below the PWM frequency. Three test points are provided for the scaled voltages labeled VA, VB, and VC.A forth resistive divider is used to sense the voltage of the motor supply. This resistive divider has a ratio of one to twelve. A test point is provided on the scaled motor supply voltage labeled VM. A phase voltage of 12 volts will produce voltage of 2 V on the respective ADC input, while a supply voltage of 12 V will produce a sense voltage of 1.0 V on the VM ADC input. A differential ADC voltage measurement will be used relative to the VM ADC input. The resulting ADC reading will be a signed 16-bit value with 0x0000 corresponding to mid-rail.The sensorless BLDC motor reference design boardincludes a current sense resistor R25 and currentamplifier U7A. The sense resistor is a 20 m Ω surfacemount resistor in an 1812 package. The sense resistorwas chosen for a maximum RMS current of 5 amps witha power dissipation of 500 mW. The resulting sensevoltage of only 100 mV requires amplification to achievemore than 5 bits of resolution from the 10-bit ADC.The current amplifier is a variation of the classic differential amplifier circuit. In the classic circuit configuration, the second resistors on the non-inverting input would be connected to ground. In this variation,resistor R17 is connected to a 400mV voltage reference. The 0.4V reference compensates for the variation in the input offset voltage of the op amp and also keeps the output within the recommended output voltage range. The gain of 26 was chosen to fully utilize the output voltage span of the amplifier allowing forvariation in the input offset voltage. The op amp chosen for this circuit is the LMV358. This is a low-voltage version of the industry standard LM358 dual CMOS op amp. The second op amp in the dual。
Remote Terminal Units - Connections and Settings说明

Remote Terminal Units - Connections and Settings Binary output 520BOD01Application, characteristics and technical data have to be taken from the hardware data sheet:520BOD01 Data sheet1KGT 150 864OperationThe binary output module 520BOD01 can be usedfor the control of 8 binary process signals using relay contacts. The allocation of an output signal to the processing functions can be done according to the rules of configuration.Processing functionsThe module 520BOD01 is able to process the following types of signals:•Single or double commands (SCO or DCO) with 1 or2 pole output without (1 out of n) check•Single or double commands (SCO or DCO) with 1.5 or 2 pole output with (1 out of n) check •Regulation step command (RCO), 1 or 2 pole •Digital setpoints commands, 8 Bit without strobe (DSO8)•Bitstring output, 1 or 8 Bit (BSO1 or BSO8)The micro-controller on the module processes alltime critical tasks of the parameterized processing functions. Moreover it carries out the interactive communication with the RTU I/O bus. All configuration data and processing parameters are loaded by the communication unit via the RTU I/O bus.In connection with an I/O adapter (e. g. 520ADD01)or the RTU520 communication unit the module is interfaced to the RTU520 I/O bus.The binary output unit can execute the following processing functions on the individual signal types:•Control of the command output duration Command monitoring functions:•monitoring of the output bit patterns by reading back the output state•switching voltage monitoring (24 V DC coil voltage) before and during output only together with (1 out of n) control module•command output duration monitoringDuring initialization and operation the module carries out a number of tests. If a fault occurs it is reported to the communication unit. All fault conditions impairing the function of the module are displayed as common fault signal by a red LED. A failure of the module isdetected by the communication unit.Parameter name Default Parameter location Command pulse length 1 sec SCO, DCO, RCO - PDPparametersvalue range: 0.1... 25.5 secFor additional information on these configuration parameters in RTUtil500 refer to RTU500 series function description - part 5: SCADA functions (1KGT 150 797).SettingsThe device has no switches or jumpers.SignalingLED BO1... BO8The 520BOD01 has 8 yellow LED’s on the front plate indicating the state of the outputs.The LEDs are ON for the time an output is active (pulse or persistent).LED ERRThe module monitors and checks the own functionality as well as the dialog via the I/O bus. Detected errors are indicated by the red LED ERR on the front plate and transmitted via the I/O bus to the communication unit (CMU). Additional diagnostic messages are available using the Web-Server on the CMU.The LED ERR indicates module errors or I/O bus errors:•module runs initialization procedure•module is performing a cold or warm start •module has detected a memory error (RAM or Flash)•micro-controller is faulty•no dialog via the I/O bus for at least 2 minutes. The module is not polled by the CMU.ConnectionsI/O bus connectionThe module is connected to the RTU I/O bus via the connectors X1 and X2.Power supply U EThe electronic circuits on the process side are supplied by an external 24 V DC voltage input U E. The voltage input U Eis connected at X3.Process connectionThe process will be connected to the screw terminals X4 (see Fig. 2).The 1 pole connection is described in Fig. 7.For a 2 pole connection two relays (e.g. for double commands R01 and R03, R02 and R04) of the binary output board 520BOD01 are used (see Fig. 8 and Fig. 9).For the (1 out of n) check along with560CIG10/560CID11 the connection is shown in Fig. 10. Safety instructionsDangerous process voltagesEnvironmental conditionsFigure 1: 520BOD01front plateFigure 2: 520BOD01 labelFigure 3: RTU520 DIN rail mounting - step 1Figure 4: RTU520 DIN rail mounting - step 2Figure 5: RTU520 DIN rail mounting - step 31Insert upper edge into DIN rail and push downwards2Push lower edge towards DIN rail and snap in the module 3 + 4:Shift one module connector intothe other starting from right toleft5 + 6:Mount end stops at the left andright sideFigure 6: 520BOD01 connection diagramFigure 7: 1 pole process connection, single commandFigure 8: 2 pole process connection, single command1K G T 150 865 V 003 1Figure 9: 2 pole process connection, double commandX3-1X3-2+-Figure 10: (1 out of n) check, 1.5 pole connection, single commandABB AGPower Grids P.O. Box 10 03 5168128 Mannheim, Germany Tel. +49 621 381-3000/remote-terminal-units We reserve the right to make technical changes or modify the contents of this document without prior notice. With regard to purchase orders, the agreed particulars shall prevail. ABB AG does not accept any responsibility whatsoever for potential errors or possible lack of information in this document.We reserve all rights in this document and in the subject matter and illustrations contained therein. Any reproduction, disclosure to third parties or utilization of its contents – in whole or in parts – is forbidden without prior written consent of ABB AG. Copyright© 2019 ABB AG All rights reserved。
Tutorial_Guide_IGG_82_1-Acrov5

TutorialsIGG™ v8.aDocumentation v8.aNUMECA International5, Avenue Franklin Roosevelt1050 BrusselsBelgiumTel: +32 2 647.83.11Fax: +32 2 647.93.98Web: ContentsTABLE OF CONTENTINTRODUCTIONTUTORIAL 1: Geometry Creation1-1 INTRODUCTION1-11-1.1 Introduction1-11-1.2 Prerequisites1-21-1.3 Preparation1-21-2 CARTESIAN POINT1-31-2.1 Create Cartesian Point1-31-2.2 Select Cartesian Point1-31-2.3 Delete Cartesian Point1-31-3 CURVES1-31-3.1 Create Curves1-31-3.2 Select Curves1-51-3.3 Visualize Curves1-51-3.4 Modify Curves1-61-3.5 Edit/Copy Curves1-71-3.6 Export Curves1-71-3 SURFACES1-81-3.1 Create Surfaces1-81-3.2 Select Surfaces1-101-3.3 Visualize Surfaces1-101-3.4 Modify Surfaces1-111-3.5 Edit/Copy Surfaces1-111-3.6 Export Surfaces1-11 TUTORIAL 2: 2D Airfoil Mesh Generation2-1 INTRODUCTION2-12-1.1 Introduction2-12-1.2 Prerequisites2-22-1.3 Presentation2-22-1.4 Preparation2-22-2 MESH GENERATION2-32-2.1 Define Project Configuration2-42-2.2 Define Geometry2-52-2.3 Create Blocks2-62-2.4 Define Clustering2-112-2.5 Generate Face Grid2-142-2.6 Control Mesh Quality2-162-2.7 Define Boundary Conditions2-172-2.8 Save Project2-18ContentsTUTORIAL 3: Pipe to Pipe Mesh Generation3-1 INTRODUCTION3-13-1.1 Introduction3-13-1.2 Prerequisites3-23-1.3 Presentation3-23-1.4 Preparation3-23-2 MESH GENERATION3-33-2.1 Define Geometry3-33-2.2 Create & Control Blocks3-53-2.3 Generate Block Grid3-133-2.4 Define Butterfly Topology3-143-2.5 Control Mesh Quality3-163-2.6 Define Boundary Conditions3-183-2.7 Define Full Non Matching Connection3-193-2.8 Save Project3-20TUTORIAL 4: Volute Mesh Generation4-1 INTRODUCTION4-14-1.1 Introduction4-14-1.2 Prerequisites4-24-1.3 Presentation4-24-1.4 Preparation4-24-2 MESH GENERATION4-34-2.1 Load Geometry4-34-2.2 Create & Control Blocks4-44-2.3 Generate Block Grid4-184-2.4 Control Mesh Quality4-194-2.5 Define Boundary Conditions4-204-2.6 Define Full Non Matching Connection4-224-2.7 Save Project4-23TUTORIAL 5: Axi Seal Leakage Mesh Generation5-1 INTRODUCTION5-15-1.1 Introduction5-15-1.2 Prerequisites5-25-1.3 Presentation5-25-1.4 Preparation5-25-2 MESH GENERATION5-35-2.1 Define Project Configuration5-35-2.2 Import Geometry5-45-2.3 Create & Control Blocks5-45-2.4 Define Clustering5-105-2.5 Control Mesh Quality5-135-2.6 Define Boundary Conditions5-155-2.7 Save Project5-18What’s in This Guide ?This Tutorial Guide contains a number of tutorials driving the user in IGG™ v8 to mesh different internal and external configurations. In each tutorial, features related to mesh generation are dem-onstrated.Tutorials 1 to 5 are detailed tutorials designed to introduce the beginner to IGG™ v8. These tutori-als provide explicit instructions for all steps of the mesh generation process. Tutorials 1 to 5 do not require any pre-requisite and can be treated separately, in any order. They address different types of applications, including both internal and external cases.Where to Find the Files Used in the Tutorials ?Each of the mesh generation starts from a geometry that is existing or is created. The appropriate files (and any other relevant files used in the tutorial) are stored on IGG™ v8 DVD-ROM, more precisely in the /DOC/_Tutorials directory.How to Use this Guide ?Depending upon your familiarity with computational fluid dynamics and your interest in some par-ticular configuration, you can use this tutorial guide in a variety of ways.For the BeginnerIf you are beginning user of IGG™, you should first read and solve tutorials 1 and 2, in order to familiarize yourself with the interface and basis of the mesh generation technique. You may then want to concentrate on a tutorial that demonstrates features that you are going to resolve. For exam-ple, if you are planning to mesh a volute, you should look at tutorial 4.For the Experienced UserIf you are an experienced user of IGG™, you can read and/or solve the tutorial(s) that demonstrate features that you are going to resolve. For example, if you plan to mesh a 2D airfoil, you should look at tutorial 2.Conventions Used in this GuideSeveral conventions are used in the tutorials to facilitate your learning process.Following a short introduction, each tutorial is divided into sections respectively related to the mesh generation steps from the geometry definition to the 3D mesh generation.Inputs required to execute the tutorials are restricted to the geometry, either in a ".dat" or CAD related format.The sequence of actions to be executed are described through a step-by-step approach, in the form of arabic numbers.Additional insight about some specific actions and/or features is frequently added to illustrate the tutorial further. This information is proposed for the purpose of clarity and completeness, and should not be executed. It appears in italicized type.Contact NUMECA support team at +32-2-647.83.11 or send an e-mail to sup-port@numeca.be for any question or information you may require. To allowNUMECA support to help you out within the shortest delays, please provide adetailed description of the observed behaviour and performed analysis.TUTORIAL 1:Geometry Creation1-1Introduction1-1.1IntroductionThe resolution of computational fluid dynamics (CFD) problems involves three main steps:•spatial discretization of the flow equations,•flow computation,•visualization of the results.To answer these questions, NUMECA has developed a F low IN tegrated E nvironment for internaland Turbomachinery assimilations. Called FINE™/Turbo, the environment integrates the followingtools:•IGG™ is an I nteractive G eometry modeler and G rid generator software, based on structured multi-block techniques,•AutoGrid™ is a three-dimensional Automated Grid generation software, dedicated to turboma-chinery applications. Similarly to IGG™, it is based on structured multi-block techniques,•Euranus is a state-of-the-art multi-block flow solver, able to simulate Euler and Navier-Stokes equations in the laminar, transitional and turbulent regimes,•CFView™ is a highly interactive flow visualization and post-treatment software,•FINE™ Graphical User Interface is a user-friendly environment that includes the different soft-wares. It integrates the concept of projects and allows the user to achieve complete simulations,going from the grid generation to the flow visualization, without the need of file manipulation.This tutorial is particularly adapted to the creation and modification of geometrical entities. Itmakes exclusive use of IGG™.In this tutorial you will learn how to:•Create Cartesian point,•Create and modify curve entities,•Create and modify surface entities,•Select and delete geometrical entities,Geometry Creation Introduction•Group/ungroup geometrical entities,•Save geometrical entities.1-1.2PrerequisitesThis tutorial does not require any particular prerequisite.1-1.3Preparation•Copy the files located in cdrom:\DOC\_Tutorials\IGG\Tutorial_1 to your working directory, where cdrom must be replaced by the name of your DVD-ROM.•Start IGG™ v8.xFor LINUX and UNIX systems, you can access IGG™ v8.x graphical user interface with thefollowing command lineigg -niversion 8x -print or igg -niversion autogrid8x -printFor WINDOWS systems, you can access IGG™ v8.x graphical user interface from the startmenu going to /Programs/NUMECA software/fine8x/IGG or /Programs/NUMECA software/autogrid8x/IGGMenu BarTool Bar3D ViewQuick Access PadControl Areakeyboard input areainformation areaYou’re now ready to start to create and modify geometrical entities!IGG™ v8 graphical user interface allows to visualize the geometry and mesh of the internal orexternal test case in a 3D view by default. The access to main menu and controls is proposedthrough a menu bar and a quick access pad, and is completed with a tool/icon bar and a control area(including the keyboard input area).Cartesian Point Geometry Creation1-2Cartesian Point1-2.1Create Cartesian Point1.Select the Geometry/Create Points/Cartesian Point menu to initiate the creation of aCartesian point2.Type the sequence <1 1 0> <Enter> in the keyboard input area. This action will create theCartesian point (black or white point is appearing in the graphics area)Cartesian points can also be defined as intersection between two selectedcurves or between a selected curve and a plane or between a selected curveand a surface (see User Manual for more details).3.Select the Geometry/Create Points/Cartesian Point menu to initiate the creation of a sec-ond Cartesian point4.Type the sequence <1 1 1> <Enter> in the keyboard input area. This action will create thesecond Cartesian point (second black or white point is appearing in the graphics area) 1-2.2Select Cartesian Point5.Select the Geometry/Select/Cartesian Points menu to select Cartesian points6.Move the mouse on the Cartesian point (1,1,1) and click-left on it when highlighted in blueto select it7.Click-right or <q> in the graphics area to end the selection1-2.3Delete Cartesian Point8.Select the Geometry/Delete/Cartesian Points menu to delete the selected Cartesian points(highlighted in blue)1-3Curves1-3.1Create CurvesThe following section describes how to:—create basic curves—use the keyboard or the mouse to input points—use the attraction featureThe below geometry, consisting of two polylines, one C-spline and one arc, will be created.Geometry Creation Curves9.Define a polyline curve:•Select the Geometry/Draw Polyline/Free menu (shortcut <p >) to initiate the creation of a polyline•Type the sequence <1 0 0> <Enter > in the keyboard input area . This action will create thefirst point of the polylineThe keystrokes are automatically echoed in the keyboard input area.•Enter a second point at position <1.2 0.5 0> and press <Enter >•Move the mouse near the Cartesian point. When close enough, the mouse will normally beattracted to this point if the attraction to points feature is enabled. If there is no attraction,press <a > in the graphics area. Then click-left to add this point to the polyline•Click-right or <q > in the graphics area to end the polyline creation•Repeat above steps to create another polyline passing through the points (0,0,0), (-0.2,0.5,0)and (0,1,0)10.Define a C-spline curve:•Select the Geometry/Draw CSpline/Free menu (shortcut <c >) to initiate the creation of aC-spline curve•Move the mouse near the point (0,0,0) of the second polyline. When close enough, themouse will normally be attracted to this point if the attraction to points feature is enabled. If there is no attraction, press <a > in the graphics area. Then click-left to add this point to the C-spline•Move the mouse somewhere between the points (0,0,0) and (1,0,0) and click-left to add apoint•Move the mouse near the point (1,0,0) of the first polyline. When close enough, the mousewill normally be attracted to this point if the attraction to points feature is enabled. If there is no attraction, press <a > in the graphics area. Then click-left to add this point to the C-spline•Click-right or <q > in the graphics area to end the C-spline creation11.Define a circular arc curve:•Select the Geometry/Circular Arc/Normal-Point-Point-Radius menu option to initiatethe creation of a circular arc. Several inputs will be requested to define the arcThe circular arc can be created using different methods (see User Manual for more details).•Enter <0 0 1> <Enter > to define the arc normalpolyline 1polyline2C-splinearcCurves Geometry Creation •Move the mouse near the Cartesian point. When close enough the point will be highlighted (if there is no attraction, press <a> in the graphics area). Click-left to define the arc startpoint•Move the mouse near the point (0,1,0) of the second polyline. When close enough the point will be highlighted (if there is no attraction, press <a> in the graphics area). Click-left todefine the arc end point•Enter <0.6> <Enter> to define the arc radius•Press <o> until the circle has the same shape as the one presented on above figure. Then click-left to create the arcClick-right or <q> in the graphics area to end the arc creation.1-3.2Select CurvesThe curve selection operation is used to activate one or more curves for subsequent operations ingeometry modelling or grid generation. When a curve is selected it appears highlighted in yellow(default). All the curves created in the previous steps are selected.12.Select the Geometry/Select/Curves option to initiate curve(s) selectionThe shortcut <s> can also be used to activate the option without accessing themenu.13.Press <a> to unselect all the curves, which become unhighlighted14.Move the mouse over the C-spline which is then highlighted. At the same time, the name,type of curve and approximate arc length of the curve appear in the information area15.Click-left to select it16.Repeat above step to select the first created polyline17.Click-right to quit the selectionSelection and deselection of all curves can be done by pressing <a> repeat-edly (toggle option).1-3.3Visualize CurvesWhen importing complex models, many curves may be created and visualized in IGG™, makingthe graphics unclear. It is possible to visualize only specific curves on the screen, hiding all others,in the following way:18.Select the Geometry/View/Curves option. A curve chooser appears with the name of allthe curves. All the names are highlighted since all the curves are visible19.Select the C-spline in the chooser (click-left on it) and press Apply. Only the C-splinecurve now appears in the view20.Select the first polyline in the chooser (click-left on it) while holding the <Ctrl> key. Thepolyline is highlighted in the chooser, together with the C-spline. Press Apply to visualizeboth curves21.Select the first and last curves in the chooser while holding the <Shift> key. All the curvesare now selected. Press Apply to visualize them all22.Close the chooserAfter selecting the curves by using the Geometry/Select/Curves menu, the selected curves can befurther investigated in the following way:Geometry Creation Curves23.Select the Geometry/View/Curve Orientation menu. The default orientation of theselected curves is shown. This orientation is important for other geometry modelling andgrid generation operations. These orientations can be hidden by selecting the menu onceagain (toggle option)24.Select the Geometry/View/Control Points menu. The control points of the selected curvesappear now. This options acts as a toggle (display on-off) on all selected curves25.Select the Geometry/Select/Control Points menu. A control point must be selected. Whenmoving the mouse near a control point, the point becomes highlighted. Click-left on a con-trol point to display the point coordinates in the information area26.Click-right to quit the option27.Select the Geometry/Distance menu (). A prompt appears to select two points betweenwhich the distance will be measured and displayed:•Press <c> to disable the attraction to curves (this can be verified by moving the cursor near the start point of the C-spline. Normally, there is no attraction to the curve. Otherwise, press<c> a second time)•Move and attract the cursor over the start point of the C-spline. If there is no attraction, press <a>. Click-left on curve to select the start point•When moving the mouse, the distance between the selected point and the cursor is indi-cated. Move the mouse over the last point of the C-spline. The cursor is attracted to thepoint and the distance is indicating d=1•Click-left to fix the distance on the screenThe above steps can be repeated to measure the distance between otherpoints.•Click-right to quit the option.1-3.4Modify CurvesExisting selected curves can be modified within IGG™ in the following way:28.Select the Geometry/Modify Curve/Add Control Point option to add control points onselected curve by click-left on itCurves Geometry Creation29.Select the Geometry/Modify Curve/Remove Control Point option to remove a controlpoint on selected curve by click-left on control point30.Select the Geometry/Modify Curve/Modify Point (On surface) option to move an exist-ing control point on selected curve (on surface) by click-left to select the point and click-left after moving the control point31.Select the Geometry/Modify Curve/Set Name... option to impose a userdefined name tothe selected entity (one curve should be selected)32.Select the Geometry/Modify Curve/Divide option to split the selected curve at a userde-fined location by click-left on it (one curve should be selected)33.Select the Geometry/Modify Curve/Reverse option to reverse the curve orientation plot-ted when selecting Geometry/View/Curve Orientation menu1-3.5Edit/Copy CurvesExisting selected curves can be moved or copied within IGG™ in the following way:34.Select the Geometry/Select/Curves menu to select all the curves (highlighted in yellow)35.Select the Geometry/Edit/Copy menu to copy all the selected entities with a translation,rotation, scaling or mirror operation36.Type <new> <Enter> to impose a userdefined prefix to the geometrical entities that will becreated37.Type <t> <Enter> to select a copy with a translation38.Type <1 0 0> <Enter> to impose the translation vectortranslation (1 0 0)The menus Geometry/Edit/Translate, Rotate, Scale or Mirror allow to moveand not to copy the selected geometry.1-3.6Export CurvesIt is possible to save during the work the curves created in the previous steps. Only the curvesselected are saved into a file:39.Select the Geometry/Select/Curves menu to select all the curves (highlighted in yellow)Geometry Creation Surfaces40.Select File/Export/Geometry Selection... menu. A file chooser is opened to specify the name of a file ".dat" (with corresponding Parasolid ™file "X_T"). This file can be readback using the File/Import/IGG Data... menu ().1-4Surfaces 1-4.1Create Surfaces In this section simple surface creation is described, starting from a set of curves. A new session will be opened to clear all previous drawings.41.Select File/New - yes to close the current project and open a new, empty, project.Opening a new project closes the current project without automatic saving.42.Define a lofted surface:•Select File/Import/IGG Data and choose the file "geometry_curves.dat" in the\DOC\_Tutorials\IGG\Tutorial_1 directory of the installation cdrom. Three curves are readand stored in the geometry repository•Select the curves using Geometry/Select/Curves (<s >) in the order indicated on the figure•Verify that the curves are well oriented by using the Geometry/View/Curve Orientationmenu otherwise you need to reverse the curves by using the Geometry/Modify Curve/Reverse menu in order to impose the same orientation to all the curves•Select the Geometry/Surface/Lofted menu in the Quick Access Pad . A NURBS surface,interpolating the curves is now created. Notice that two new curves, representing surfaceboundaries, are created. These curves automatically appear in the curve chooser (Geome-try/View/Curves ) when it is opened123Boundary curves automatically created1234Surfaces Geometry Creation43.Define a coons patch:A Coons surface is a surface interpolating 4 boundary curves using a bilinearinterpolation. To avoid overlapping with the lofted surface, the selected curveswill be copied and translated.•Select the four boundary curves (<s>) of the lofted surface, in the order indicated in the above figure•Select the Geometry/Edit/Copy menu in the Quick Access Pad. IGG™ interrogates whether the duplicated curves must be translated, rotated, scaled, mirror or not. To avoid overlappingwith the existing curves and surface, a translation will be performed•Type <new> <Enter> to impose a userdefined prefix to the geometrical entities that will be created•Type <t> <Enter> to select a copy with a translation•Type <1 1 1> <Enter> to impose the translation vectorThe selected curves are duplicated and the new curves are automaticallyselected (the other curves are now unselected)•Select the Quick Access Pad/Geometry/Surface/Coons menu. A new surface is created which interpolates the four selected curvesIt can be noticed that 4 additional curves have been created. These are curves following the parametricdirections of the surface and are used to provide a better visualization of the surface.44.Define a surface of revolution:A surface of revolution will be created by rotating a newly created curve aroundthe Y axis.•First create a C-spline (Geometry/Curve/CSpline) between the points (-0.5,-2,0.1), (-0.5,0,0.2) and (-0.5,2,0.1). These points were selected so that the surface of revolution thatwill be created intersects the lofted surface•Make this curve the only selected curve (Geometry/Select/Curves)•Select Geometry/Surface/Revolution in the Quick Access Pad to create a surface of revolu-tion by rotating this new curve around a line parallel to the Y axis. The rotation origin is takenso that the surface of revolution intersects the lofted surface•Type <0 1 0> <Enter> to select the rotation axis direction•Type <-0.5 0 -1> <Enter> to select the rotation axis origin•Type <300> <Enter> to select the angle of rotationGeometry Creation SurfacesAs it may be noticed, the curve used for the rotation constitutes the first boundary of the surface.Three other boundary curves are automatically created to delimitate the surface.1-4.2Select SurfacesThe surface selection operation is used to activate one or more surfaces for subsequent operations in geometry modelling (i.e surface-surface intersection) or grid generation (i.e. face grid mapping).When a surface is selected its boundary curves appear highlighted in red or yellow.45.Select the Geometry/Select/Surfaces menu to initiate surface(s) selectionThe <Ctrl-s> shortcut can also be used to activate the same option, withoutaccessing the menu.46.Press <a > to unselect all the surfaces (toggle option), which become unhighlighted (bound-ary curves are unhighlighted)47.Move the mouse over the lofted surface. The surface becomes highlighted in blue.48.Click-left to select the surface. The boundary curves remain now permanently in red or yel-low49.Repeat above steps to select the surface of revolution50.Click-right to quit the selectionSelection and deselection of all the visible surfaces can be done by pressing<a> repeatedly (toggle option).1-4.3Visualize SurfacesSurfaces stored in IGG ™ are by default visualized by displaying their boundaries. As soon as the boundary curves of a surface are visible, the surface is considered visible. The following step describes how to hide surfaces, hence hide their boundaries.51.Select the Geometry/View/Surfaces option. A surface chooser appears with the name ofall the surfaces in the geometry repository. All surfaces in the chooser are highlighted sincethey are all visible in the graphics area52.Select the lofted surface (click-left on it) in the chooser and press Apply . The lofted surface appears alone in the graphics area with all the previously created curvesboundary curvesSurfaces Geometry Creation53.Select the surface of revolution (click-left on it) in the chooser while holding the <Ctrl> key.The surface of revolution is highlighted in the chooser together with the lofted surface. PressApply to visualize both surfaces. Notice that the surface of revolution is now unselected inthe graphics area (highlighted in blue)54.Select the first and last surfaces (click-left on them) in the chooser while holding the <Shift>key. All surfaces are highlighted in the chooser. Press Apply to visualize them all in thegraphics area55.Close the chooser1-4.4Modify SurfacesWhen manipulating parametric surfaces, it is possible to create curves in the parametric directions ofthe surfaces. These curves can be used to better visualize the surfaces or for other geometry and gridmodelling operations.56.After selecting a surface, select the Geometry/Modify Surface/Representation menu.IGG™ requests the number of curves to be created in the u and v direction of each selectedsurface:•Type <15 15> <Enter> to plot 15 curves in both parametric directions of the selected surfaces•Repeat the previous step and specify 5 curves in each direction57.Select the Geometry/Modify Surface/Add uv Curves menu. Then a point must be selectedon the selected surfaces:•Move the mouse inside the limits of the selected surfaces. Two orthogonal curves appear at the mouse position. The attraction feature can be enabled, if needed•Click-left to add the two curves in the geometry repositoryThe curves created in the above steps are deleted when the surface is deleted,except if they are used by other entities.1-4.5Edit/Copy SurfacesExisting selected surfaces can be moved or copied within IGG™ as presented on the curves in section1-3.5.1-4.6Export SurfacesIt is possible to save during the work the curves and surfaces created in the previous steps. Only thecurves and surfaces selected are saved into a file:58.Select the Geometry/Select/Curves and Surfaces menu to select respectively the curves(highlighted in yellow) and the surfaces (highlighted in red or yellow)59.Select the File/Export/Geometry Selection... menu. A file chooser is opened to specify thename of a file ".dat" (with corresponding Parasolid™ file "X_T"). This file can be read backusing the File/Import/IGG Data... menu ()Geometry Creation SurfacesTUTORIAL 2:2D Airfoil MeshGeneration2-1Introduction2-1.1IntroductionThe resolution of computational fluid dynamics (CFD) problems involves three main steps:•spatial discretization of the flow equations,•flow computation,•visualization of the results.To answer these questions, NUMECA has developed a F low IN tegrated E nvironment for internaland Turbomachinery assimilations. Called FINE™/Turbo, the environment integrates the followingtools:•IGG™ is an I nteractive G eometry modeler and G rid generator software, based on structured multi-block techniques,•AutoGrid™ is a three-dimensional Automated Grid generation software, dedicated to turboma-chinery applications. Similarly to IGG™, it is based on structured multi-block techniques,•Euranus is a state-of-the-art multi-block flow solver, able to simulate Euler and Navier-Stokes equations in the laminar, transitional and turbulent regimes,•CFView™ is a highly interactive flow visualization and post-treatment software,•FINE™ Graphical User Interface is a user-friendly environment that includes the different soft-wares. It integrates the concept of projects and allows the user to achieve complete simulations,going from the grid generation to the flow visualization, without the need of file manipulation.A C-type block grid around an airfoil is proposed to explain the basic features of the major topol-ogy and grid generation modules within IGG™.The tutorial shows the successive steps that must be followed to generate a 2D mesh and to definethe boundary conditions required before starting a solver:•Set up a 2D project,•Import/Create geometry curves needed for meshing,•Define the topology before meshing,。
莫萨 EDS-208A 系列 8 口编程无管理以太网交换机产品介绍说明书

EDS-208A Series8-port compact unmanaged Ethernet switchesFeatures and Benefits•10/100BaseT(X)(RJ45connector),100BaseFX(multi/single-mode,SC or STconnector)•Redundant dual12/24/48VDC power inputs•IP30aluminum housing•Rugged hardware design well suited for hazardous locations(Class1Div.2/ATEX Zone2),transportation(NEMA TS2/EN50121-4),and maritimeenvironments(DNV/LR/ABS/NK)•-40to75°C wide operating temperature range(-T models)CertificationsIntroductionThe EDS-208A Series8-port industrial Ethernet switches support IEEE802.3and IEEE802.3u/x with10/100M full/half-duplex,MDI/MDI-X auto-sensing.The EDS-208A Series has12/24/48VDC(9.6to60VDC)redundant power inputs that can be connected simultaneously to live DC power sources.These switches have been designed for harsh industrial environments,such as in maritime(DNV/LR/ABS/NK),rail wayside,highway,or mobile applications(EN50121-4/NEMA TS2/e-Mark),or hazardous locations(Class I Div.2,ATEX Zone2)that comply with FCC,UL,and CE standards.The EDS-208A switches are available with a standard operating temperature range from-10to60°C,or with a wide operating temperature range from-40to75°C.All models are subjected to a100%burn-in test to ensure that they fulfill the special needs of industrial automation control applications.In addition,the EDS-208A switches have DIP switches for enabling or disabling broadcast storm protection,providing another level of flexibility for industrial applications.SpecificationsEthernet Interface10/100BaseT(X)Ports(RJ45connector)EDS-208A/208A-T Models:8EDS-208A-M-SC/M-ST/S-SC Models:7EDS-208A-MM-SC/MM-ST/SS-SC Models:6All Models Support:Auto negotiation speedFull/Half duplex modeAuto MDI/MDI-X connection100BaseFX Ports(multi-mode SC connector)EDS-208A-M-SC Models:1EDS-208A-MM-SC Models:2100BaseFX Ports(multi-mode ST connector)EDS-208A-M-ST Models:1EDS-208A-MM-ST Models:2100BaseFX Ports(single-mode SC connector)EDS-208A-S-SC Models:1EDS-208A-SS-SC Models:2Standards IEEE802.3for10BaseTIEEE802.3u for100BaseT(X)and100BaseFXIEEE802.3x for flow controlOptical Fiber800Typical Distance4km5km40kmWavelengthTypical(nm)13001310TX Range(nm)1260to13601280to1340 RX Range(nm)1100to16001100to1600Optical PowerTX Range(dBm)-10to-200to-5 RX Range(dBm)-3to-32-3to-34 Link Budget(dB)1229 Dispersion Penalty(dB)31Note:When connecting a single-mode fiber transceiver,we recommend using anattenuator to prevent damage caused by excessive optical power.Note:Compute the“typical distance”of a specific fiber transceiver as follows:Linkbudget(dB)>dispersion penalty(dB)+total link loss(dB).Switch PropertiesMAC Table Size2KPacket Buffer Size768kbitsProcessing Type Store and ForwardPower ParametersConnection1removable4-contact terminal block(s)Input Current EDS-208A/208A-T,EDS-208A-M-SC/M-ST/S-SC Models:0.11A@24VDCEDS-208A-MM-SC/MM-ST/SS-SC Models:0.15A@24VDCInput Voltage12/24/48VDCRedundant dual inputsOperating Voltage9.6to60VDCOverload Current Protection SupportedReverse Polarity Protection SupportedDIP Switch ConfigurationEthernet Interface Broadcast storm protectionPhysical CharacteristicsHousing AluminumIP Rating IP30Dimensions50x114x70mm(1.96x4.49x2.76in)Weight275g(0.61lb)Installation DIN-rail mountingWall mounting(with optional kit) Environmental LimitsOperating Temperature Standard Models:-10to60°C(14to140°F)Wide Temp.Models:-40to75°C(-40to167°F) Storage Temperature(package included)-40to85°C(-40to185°F)Ambient Relative Humidity5to95%(non-condensing)Standards and CertificationsEMC EN55032/24EMI CISPR32,FCC Part15B Class AEMS IEC61000-4-2ESD:Contact:6kV;Air:8kVIEC61000-4-3RS:80MHz to1GHz:10V/mIEC61000-4-4EFT:Power:2kV;Signal:1kVIEC61000-4-5Surge:Power:2kV;Signal:2kVIEC61000-4-6CS:10VIEC61000-4-8PFMFHazardous Locations ATEXClass I Division2Maritime ABSLRNKDNVRailway EN50121-4Safety UL508Shock IEC60068-2-27Traffic Control NEMA TS2Vibration IEC60068-2-6Freefall IEC60068-2-31MTBFTime2,701,531hrsStandards Telcordia(Bellcore),GBWarrantyWarranty Period5yearsDetails See /warrantyPackage ContentsDevice1x EDS-208A Series switchDocumentation1x quick installation guide1x warranty cardDimensionsOrdering InformationModel Name 10/100BaseT(X)PortsRJ45Connector100BaseFX PortsMulti-Mode,SCConnector100BaseFX PortsMulti-Mode,STConnector100BaseFX PortsSingle-Mode,SCConnectorOperating Temp.EDS-208A8–––-10to60°C EDS-208A-T8–––-40to75°C EDS-208A-M-SC71––-10to60°C EDS-208A-M-SC-T71––-40to75°C EDS-208A-M-ST7–1–-10to60°C EDS-208A-M-ST-T7–1–-40to75°C EDS-208A-MM-SC62––-10to60°C EDS-208A-MM-SC-T62––-40to75°C EDS-208A-MM-ST6–2–-10to60°C EDS-208A-MM-ST-T6–2–-40to75°C EDS-208A-S-SC7––1-10to60°C EDS-208A-S-SC-T7––1-40to75°C EDS-208A-SS-SC6––2-10to60°C EDS-208A-SS-SC-T6––2-40to75°C Accessories(sold separately)Power SuppliesDR-120-24120W/2.5A DIN-rail24VDC power supply with universal88to132VAC or176to264VAC input byswitch,or248to370VDC input,-10to60°C operating temperatureDR-452445W/2A DIN-rail24VDC power supply with universal85to264VAC or120to370VDC input,-10to50°C operating temperatureDR-75-2475W/3.2A DIN-rail24VDC power supply with universal85to264VAC or120to370VDC input,-10to60°C operating temperatureMDR-40-24DIN-rail24VDC power supply with40W/1.7A,85to264VAC,or120to370VDC input,-20to70°Coperating temperatureMDR-60-24DIN-rail24VDC power supply with60W/2.5A,85to264VAC,or120to370VDC input,-20to70°Coperating temperatureWall-Mounting KitsWK-46-01Wall-mounting kit,2plates,8screws,46x66.8x2mmRack-Mounting KitsRK-4U19-inch rack-mounting kit©Moxa Inc.All rights reserved.Updated Sep19,2023.This document and any portion thereof may not be reproduced or used in any manner whatsoever without the express written permission of Moxa Inc.Product specifications subject to change without notice.Visit our website for the most up-to-date product information.。
Modicon Premium - 8 O 多范围模拟输出模块数据手册说明书

i s c l a i m e r: T h i s d o c u m e n t a t i o n i s n o t i n t e n d e d a s a s u b s t i t u t e f o r a n d i s n o t t o b e u s e d f o r d e t e r m i n i n g s u i t a b i l i t y o r r e l i a b i l i t y o f t h e s e p r o d u c t s f o r s p e c i f i c u s e r a p p l i c a t i o n sProduct data sheetCharacteristicsTSXASY800analog output module Modicon Premium - 8 O multirangeProduct availability : Stock - Normally stocked in distribution facilityPrice* : 3194.70 USDMainRange of productModicon Premium Automation platform Product or component type Analog output module Analogue output number 8Analogue output typeCurrent 0...20 mA Current 4...20 mA Voltage +/- 10 V Analog/Digital conversion13 bits + sign +/- 10 V 13 bits 0...20 mA 13 bits 4...20 mAComplementaryConversion time 5 msMeasurement resolution1.28 mV +/- 10 V2.56 µA 0...20 mA 2.56 µA 4...20 mA Electrical connection 1 SUB-D 25 connectorMeasurement error0.14 % of full scale +/- 10 V 25 °C 0.21 % of full scale 0...20 mA 25 °C 0.21 % of full scale 4...20 mA 25 °C 0.28 % of full scale +/- 10 V 0...60 °C 0.52 % of full scale 0...20 mA 0...60 °C 0.52 % of full scale 4...20 mA 0...60 °C Isolation between channels Common point Isolation between channels and bus 1000 Vrms Isolation between channels and ground 1000 VrmsProtection type Short-circuit protection Overload protection Output voltage limits <= 30 VLoad impedance ohmic< 600 Ohm 0...20 mA< 600 Ohm 4...20 mA> 1000 Ohm +/- 10 VLoad inductance< 300 µHLoad capacitance< 0.1 µFMarking CECurrent consumption200 mA 5 V DC300 mA 24 V DCModule format StandardTerminals description PLC n°1(2)OUT_ANA_CUR#0(10)OUT_ANA_VOLT#6(8)OUT_ANA_CUR#4(25)OUT_ANA_CUR#7(7)OUT_ANA_VOLT#4(21)OUT_ANA_VOLT#5(11)OUT_ANA_CUR#6(15)OUT_ANA_VOLT#1(5)OUT_ANA_CUR#2(14)OUT_ANA_COM#0(22)OUT_ANA_CUR#5(3)OUT_ANA_COM#1(4)OUT_ANA_VOLT#2(9)OUT_ANA_COM#5(16)OUT_ANA_CUR#1(20)OUT_ANA_COM#4PW_NEG#(1)OUT_ANA_VOLT#0PW_POS#(19)OUT_ANA_CUR#3(6)OUT_ANA_COM#3(13)IN_ANA_STD#(17)OUT_ANA_COM#2(23)OUT_ANA_COM#6(18)OUT_ANA_VOLT#3(12)OUT_ANA_COM#7(24)OUT_ANA_VOLT#7EnvironmentStandards89/336/EEC93/68/EECIEC 61131-292/31/EECCSA C22.2 No 213 Class I Division 2 Group B73/23/EECCSA C22.2 No 142UL 508CSA C22.2 No 213 Class I Division 2 Group ACSA C22.2 No 213 Class I Division 2 Group DCSA C22.2 No 213 Class I Division 2 Group C Product certifications RMRSABSGLRINALRDNVBVAmbient air temperature for operation32...140 °F (0...60 °C)Ambient air temperature for storage-13...158 °F (-25...70 °C)Relative humidity10...95 % without condensation for operation5...95 % without condensation for storage Operating altitude0...6561.68 ft (0...2000 m)Protective treatment TCIP degree of protection IP20Pollution degree2Ordering and shipping detailsCategory22558 - TSX PREMIUM, ATRIUM & PL7 PRODiscount Schedule PC22GTIN00785901876366Nbr. of units in pkg.1Package weight(Lbs) 1.03Returnability Y Country of originFROffer SustainabilitySustainable offer status Not Green Premium productRoHS (date code: YYWW)Compliant - since 0835 - Schneider Electric declaration of conformity Schneider Electric declaration of conformity REAChReference not containing SVHC above the threshold Reference not containing SVHC above the threshold Product end of life instructionsNeed no specific recycling operationsContractual warrantyWarranty period18 monthsDimensions DrawingsStandard and Extendable Racks for Modules MountingDimensions of Modules and Racks(1) With screw terminal block modules.(2) Maximum depth for all types of modules and their associated connectors.Connections and SchemaAnalog Output Module (8-Channel, Voltage/Current)Connector Pin AssignmentSTD: The "strap" between pins 3 and 13 detects disconnection.External Power Supply Terminal Block Pin AssignmentSome recommendations:●External supply must be of the type VLVS (very low voltage for safety) 24 V +/- 5 %, ripple < 1 V.●The connection lead must be a shielded cable (it is advised to connect the shielding braid on the supply side and as close as possible to the module, usinSupplies that are suitable: TSXSUP1011/1021/1051/1101 and TSXSUPA05.。
Quick Connect Basic Installation and user 说明书
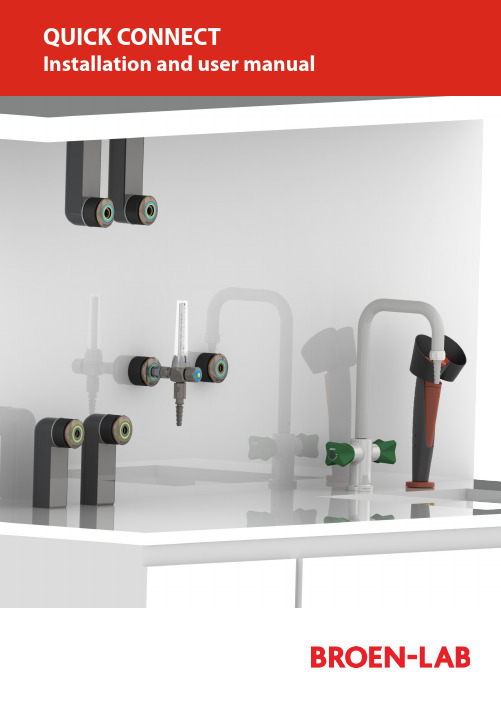
Easy to install Adaptable for changesSeveral labs in one 100 % safeEasy to installPre-install and decide laterServeral labs in one100 % safeThis is an installations guide for Quick Connect Basic.Quick Connect is the new, innovative and flexible lab solution.Quick Connect is based on the concept plug and play and easy to install. BROEN-LAB has furthermore made a drilling template which makes it easi-er to drill the mounting holes for the installation of Quick Connect. For futher information see page 23.Before installation please read the chapter, Purity on page 22.PANEL MOUNTEDBUILT-IN MOUNTEDBENCH MOUNTEDEXPOSED PIPECONCEALED PIPESUSPENDED MOUNTEDDISC MOUNTEDTable of Contents 4-5 Quick Connect Basicmounted 6-7 Panelmounted 8-9 Built-inBench mounted 10-11 Exposed pipe mounted 12-13 Concealed pipe mounted 14-15 Suspended mounted 16-17 Disc mounted 18-19 Changing media type 20-21 Purity 2.0, 4.0, 5.0 22 Drilling template 23 Trouble shooting guide 24-25 Accessories and datasheets 26-27Temperature range: 0-90o CMax. working pressure: 16 bar/232 psi Inlet: BROEN-LAB UniFlex TM Materials with media contact Metals: BrassNitrile (NBR) VITON (FKM) EPDM Panel thickness up to 26 mmAssemblyCartrid g eO-ringM4 (x2) screwFront partFront ringRear PartNutFemale BROEN-LABUniFlex TMSTEP 1STEP 2STEP 3MountingDatasheetTool: A wrench key+1All measurements are in mmTemperature range: 0-90o CMax. working pressure: 16 bar/232 psiPanel thickness 1-6 mm AssemblyCover ringO-ringFront partFront ringGASInlet: Femal e BROEN-LAB UniFlex TM Materials with media contactMetals: Brass Nitrile (NBR) VITON (FKM) EPDMg eDatasheetMountingTool: Allen key 3 mm for (2x) M5x8 screws Allen key 2,5 mm for (2x) M4 screws2,5 mm 3 mmNice to know!Built-in is delivered assembled and has to be disassembled before mounting - Follow the mounting backwardsPlace the rear part from theDepending on the wall thick-Place the locking plate Place the front part over the All measurements are in mmMount with (2x) M5x8 mmTemperature range: 0-90o CMax. working pressure: 16 bar/232 psiInlet: BROEN-LAB UniFlex TM Panel thickness 30-90 mm AssemblyCoverRear PartM3x12 ScrewInlet pipeUniFlex Connection (Need to be pre-mounted)Materials with media contactMetals: Brass Nitrile (NBR) VITON (FKM) EPDMDatasheetSTEP 1STEP 2STEP 3MountingTool: A Phillips screwdriver, size 21234All measurements are in mmTemperature range: 0-90o CMax. working pressure: 16 bar/232 psi Inlet: BROEN-LAB UniFlex TM Assemblyg eM4 (x2) screwFront partFront ringRear PartFemale BROEN-LAB UniFlex compression Materials with media contactMetals: Brass Nitrile (NBR) VITON (FKM) EPDMOnly for plates where threads can be drilled.MountingTool: Allen key for M3x25 (x4) screw s A llen key for M4 (x2) screwsFront: Use (4x) M3x25 mounting screws ( included) Rear: Use (4x) M4x25 screws (included)mm STEP 3STEP 4STEP 6STEP 7STEP 8STEP 1Front:Mounting with (4x) M3 mm screws Rear:Mounting with (4x) M4 mm screwsPush the cartrigde into therear partTighten the (2x) M4 screwsPush the front ring with light forceinto placeDraw a centerline and place the sticker with the drilling template e STEP 5Slide the black cover onDrill after the green marks on thestickerNice to know!Exposed isdelivered assembled and has to bedisassembled before mounting - Follow the mounting backwards3 mmCatridgeFemaleBROEN-LAB UniFlex TMFront partFront ringRear PartTemperature range: 0-90o CMax. working pressure: 16 bar/232 psiInlet: BROEN-LAB UniFlex TM AssemblyMaterials with media contactMetals: Brass Nitrile (NBR) VITON (FKM) EPDMFor furniture without space fortightening behind the wallMountingDatasheet6STEP 8Mounting with (4x) M3x25 mm screws Push the catridge into the rear partSlide the black cover on Push the front ring with light forceinto placeTool: Allen key for (4x) M3x25 screwsA llen key for (2x) M4 screws (front mounting and media changing- includedSTEP 3STEP 4STEP 5mmNice to know!Concealed isdelivered assembledand has to bedisassembled beforemounting - Follow themounting backwardsAll measurements are in mmSTEP 2STEP 1Drill after the green and redmarks on the stickerTemperature range: 0-90o CMax. working pressure: 16 bar/232 psiPanel thickness 30-90 mm AssemblyCoverRear PartM3x12 ScrewMounting plateLocking pinsInlet pipeHoseUniFlex ConnectionInlet: BROEN-LAB UniFlex TM Materials with media contactMetals: Brass Nitrile (NBR) VITON (FKM) EPDMMountingDatasheetSTEP 2STEP 3Tool: A Phillips screwdriver , size 21234mmSTEP 1Inlet: BROEN-LAB UniFlex TM /For porous wallsTemperature range: 0-90o CAssemblyCatridge Cover, Long O-ringFemaleTMM4 (x2) screw Front partFront ring(4x) M3x25Mounting discMaterials with media contactMetals: Brass Nitrile (NBR) VITON (FKM) EPDMFront mounting in soft material where threads not can be drilledDatasheetSTEP 3STEP 4STEP 6STEP 7STEP 8STEP 1Mount the mounting disc with screws - not included Moun t the rear part with the (4x) M3 x25 mm screwsTighten the (2x) M4 mm screwsPush the front ring with light forceinto placeDraw a centerline and place the sticker with the drilling template eSTEP 5Slide the black cover onDrill after the blue and red markson the sticker All measurements are in mmWith Quick Connect is it possible to make last minute changes.It is important only to change between the gases within the same category.There are 3 categories: Non-burning gases, burning gases and water.Types of mediaThe changeable mediaNon-burning gases Burning gases WaterNot possiblePossibleMedia changingSTEP 1STEP 2Move the front ring i.e. CA by pulling it out with lightforceLoosen the (2x) M4 mm screws - only a little bit.12Push the front ring with light force into placeTighten the (2x) M4 mm screws12Tool: 3 mmSTEP 5STEP 62.0, 4.0 and 5.0 indicate the purity of the gases.2.04.05.099 %99,99 %99,999 %Changes or modifications are not allowed to be made to the equipment without prior approval from BROEN -LAB .Improper handling or use can involve risks for the user and other persons as well as damage of the equipment.The equipment can only be used for the gas type it was manufactured and labelled for. Change can be made prior to start of use, provided that the new media is listed in the data sheet, or BROEN -LAB has approved the new media.Observe the maximum pressure & temperature ranges.The equipment cannot be used for gases in the liquid phase.The equipment must not be exposed to impact, vibrations or other mechanical forces that can damage the equipment. The equipment is designed for use in laboratories. The equipment is not designed for installing where there is a possibility of exposure to aggressive media.By installation avoid oil and grease contamination (Fire or explosion hazard). It is recommended to use a proper leak detection fluid or similar to check for leak when installing and using the Quick Connect.These valves do not contain a relief valve. In case of failure, the outlet pressure may rise above the adjusted value. Anyequipment connected to the equipment Purity 5.0 in useWhen changing the outletTo maintain a purity of 5.0, BROEN-LAB recommends to purge the system in 30 sec. before usage, when you change the outlet.Safety instructionsHandling of technical gases requires knowledge of the subject, operation instructions and special safety measures. Always check national and local laws, regulations and procedures regarding the installation and use of this type of equipment., ERROR CAUSE ACTIONERROR CAUSE ACTIONThe outlet is leaking There are leaksinside the outlet Replace the o utlet with a new oneAccessorie s Datasheet s97Pressure regulatorDatasheet sAccessorie sBROEN-LAB Ltd.BROEN-LAB Singapore Pte. Ltd.BROEN-LAB A/S BROEN-LAB GmbH BROEN-LAB Sverige AB broen-lab .comINTERNATIONAL OFFICESUnit 9 Navigation Point, Golds Hill Way Tipton • West Midlands DY4 OPY • U.K.Tel. +44 121 522 4515 • Fax +44 121 522 4535E-mail:*****************10 Bukit Batok Crescent #10-02 • The Spire • Singapore 658079Tel: +65 6298 0662 • Fax: +65 6298 0468 E-mail:*****************HEAD OFFICE Drejervænget 2 • DK-5610 AssensTel. +45 6376 6376 • Fax +45 6471 2476 E-mail:*****************Tel. +45 6376 6376 • Fax +45 6471 2476 E-mail:*****************Tel. +45 6376 6376 • Fax +45 6471 2476 E-mail:*****************BROEN-LAB A/S ISO 9001 certificationIn September 1991 BROEN-LAB A/S was certified according to ISO 9001 as one of the first Danishcompanies. The certification was carried out by Bureau Veritas, Denmark, for our Danish site in Assens.The quality management system of BROEN-LAB A/S now complies with detailed specifications laid down by the internationally acknowledged EN ISO 9001:2008. This certification will further contribute to reputationfor quality and reliability of BROEN-LAB A/S.94G0243 UK 109/12-2020。
GPS-208用户手册说明书

GPS-208USER MANUALCES WIRELESS TECHNOLOGIES, CORP.925-122 South Semoran BoulevardWinter Park, Florida 32792GPS208 Manual v1p1.docRevision 1.1November 1, 2011© Copyright CES WIRELESS TECHNOLOGIES CORP. (2011)The information contained in this document is subject to change without notice and should not be construed as a commitment by CESWIRELESS TECHNOLOGIES CORP. unless such commitment is expressly given in a covering document.REGULATORY COMPLIANCEFCCThis device complies with Part 15 of the FCC Rules. Operation is subject to the following two conditions: (1) This device may not cause harmful interference, and (2) this device must accept any interference received, including interference that may cause undesired operation.This equipment has been tested and found to comply with the limits pursuant to Part 15 Subpart B, Part 22, and Part 24 of the FCC rules. These limits are designed to provide reasonable protection against harmful interference in an appropriate installation. This equipment generates, uses, and can radiate radio frequency energy and, if not used in accordance with instructions, can cause harmful radiation to radio communication. However, there is no guarantee that interference will not occur in a particular installation.RF EXPOSUREYour device is a radio transmitter and receiver. It is designed and manufactured not to exceed the emissions limits for exposure to radio frequency (RF) energy set by the Federal Communications Commission (FCC) of the U.S. Government. These limits are part of comprehensive guidelines and establish permitted levels of RF energy for the general population. These guidelines are based on the safety standards previously set by the U.S. and international standards bodies. The standards include a substantial safety margin designed to assure the safety of all persons, regardless of age and health.The exposure standard for wireless RF devices, such as the device, employs a unit of measurement known as the Specific Absorption Rate, or SAR. The SAR limit set by the FCC is 1.6W/kg. SAR values at or below that limit are considered safe for the general public. Before a wireless RF device is made available for sale to the Public, it must be tested and certified to the FCC that it does not exceed the SAR limits established by the FCC. Tests for SAR are conducted using the positions and locations (e.g., at the ear or worn on the body) as required by the FCC for each device model.The device has been tested and meets the FCC RF exposure guidelines when used against the body under normal usage conditions.R&TTEEffective with HW revision B, the device is in conformity with the requirements of the R&TTE directive 1999/5/EC. It has been fully tested and complies with all the requirements of EN301489-1, EN301489-3, EN301489-7 and EN60950-1. Compliance to EN301511 has been demonstrated by testing on both the device and the integrated module.The hardware revision of the device is identified on the label an also by the presence of the CE mark.ROHS COMPLIANCEThe device complies with the European Union Restriction of the Use of Certain Hazardous Substances in Electrical and Electronic Equipment ([RoHS) Directive (2002/95/EC), effective since July 1, 2006.DISCLAIMERThe information and instructions contained within this publication comply with all FCC, GCF, PTCRB, R&TTE, IMEI and other applicable codes that are in effect at the time of publication. Enfora disclaims all responsibility for any act or omissions, or for breach of law, code or regulation, including local or state codes, performed by a third party. Enfora strongly recommends that all installations, hookups, transmissions, etc., be performed by persons who are experienced in the fields of radio frequency technologies. Enfora acknowledges that the installation, setup and transmission guidelines contained within this publication are guidelines, and that each installation may have variables outside of the guidelines contained herein. Said variables must be taken into consideration when installing or using the product, and Enfora shall not be responsible for installations or transmissions that fall outside of the parameters set forth in this publication.BATTERY INFORMATION AND SAFETY REQUIREMENTSNOTE: Failure to comply with all of the following precautions could:•Cause personal injury or property damage•Cause abnormal chemical reactions which would make the battery over heat, smoke, distort, leak, or catch on fire•Destroy internal protections built into the battery•Shorten battery life•Reduce battery performancePrecautions•Read this entire manual and the label on the exterior of the battery.•Keep the battery away from sources of excessive heat such as fire, stoves, or direct sunlight.•Keep the battery away from sources of high voltage or static discharge.•Do not use or store the battery with other batteries or where it could touch metal.•Do not put the battery into a microwave oven.•Do not allow the battery to be crushed.•Keep the battery away from children.•Do not drop the battery.•Do not allow anything to touch any of the battery contacts, or to connect two or more of the contacts.•Do not disassemble, destroy, or attempt reassembly of the battery.•Do not place or leave the battery in a damp or wet environment.•Do not allow water to touch the battery.•Do not wrap the battery with conductive material.•Properly dispose of the battery.•Do not incinerate or burn the battery.•Do not leave or discard the battery where it could get wet or become submerged in water.•Do not damage the battery.•Do not weld or solder anything to the battery, the attached wires, or the connector.•Do not use this battery in any device other than supplied.•Do not touch a leaking battery. Avoid leaked-out materials. Do not allow it to touch your skin or clothes. If touched, immediately rinse affected areas thoroughly with water. Leaked materials may cause skin irritation. Seek medical attention if irritation persists. If it contacts your eyes, do not rub your eyes. Rinse the eyes thoroughly with water, and see a doctorimmediately.•Use of this battery in other devices could result in unsafe conditions.•Risk of explosion if battery is replaced by an incorrect type.CHANGE LOGDate Author Description09/20/11Doug Hamilton Initial Release (1.0)11/01/11Doug Hamilton Added info on the two wire harnesses available for the GPS-208Table of ContentsREGULATORY COMPLIANCE (2)FCC (2)RF EXPOSURE (2)R&TTE (2)ROHS COMPLIANCE (2)DISCLAIMER (2)BATTERY INFORMATION AND SAFETY REQUIREMENTS (2)Precautions (3)CHANGE LOG (4)Table of Contents (5) (5)1.0 Introduction (6)1.1 About the GPS-208 (6)1.2 About This Manual (6)1.3 Basic Package Contents (6)1.4 Accessories (6)1.5 System Requirements (6)1.6 GPS-208 Front View (6)1.7 Label (7)2.0 Specifications (8)2.1 System Information (8)2.2 GPRS Packet Data (8)2.3 GPS Functionality (8)2.4 Environment (8)2.5 Certifications (8)2.6 SIM Card/Interface/I/O (8)2.7 Power (8)2.8 Battery (8)3.0 Installation (9)3.1 Installing Cables (9)3.1.1 HRNS-062 - 16-Pin I/O Connector (9)3.2 Opening and Closing the GPS-208 (10)3.2.1 Opening the GPS-208 (10)3.2.2 Closing the GPS-208 (11)3.3 Installing the SIM (Subscriber Identity Module) Card (11)3.4 Connecting Power (12)3.5 Optional Backup Battery (13)3.6 GPS-208 Installation (13)4.0 Support (14)Index of TablesTable 1: 16-pin I/O Connector Functionality. HRNS062 is the Power only cable. HRNS063 is for Power (Cable 1) and I/O (Cable 2) (10)Table 2: Manufacturer Part Numbers to Build Cables (10)1.0IntroductionThe GPS-208 is one of the smallest and most economical GPS asset tracking devices available today. The devices is neither weather, dust or splash proof.GPS and event data is made available on-board the GPS-208 for transmission to FleetLinc™ (CES web based subscriber fleet management service).The GPS-208 can also be licensed for use with POWER-trak3™ PC/Server software. Please contact CES for further information on this.1.1About the GPS-208The GPS-208 is an Automated Vehicle Locating (A VL) device that utilizes a GSM/GPRS cellular modem and a Global Positioning Satellite (GPS) module. Working together, these technologies allow the GPS-208 to simultaneously act as a stand alone GPS reporting device and wireless data retrieval unit. The GPS-208 provides a flexible A VL solution with three inputs, an ignition input and two outputs. The GPS-208 is designed to work as a stand-alone device in a vehicle. It requires DC power. No antennas are required – the GPS and quad-band GSM antennas are built in to the GPS-208.The GPS-208 has a V0 fire rated plastic housing. The SIM holder is internal. The interface connector is a 16-pin MolexI/O connector. There are three LED indicators.1.2About This ManualThis manual contains instructions on how to install and configure the GPS-208. Please follow the instructions closely to avoid damaging the GPS-208.1.3Basic Package ContentsThe basic package will contain the following:•GPS-208 - GPS/GSM/GPRS Tracking and Fleet Management Device•16-pin interface connector with DC cable (HRNS-062)1.4AccessoriesThe following accessories are available from CES Wireless Technologies:•PRG-05: Programming Cable - 16-pin cable with USB Connector, power and ground•DP-1000S: Programming Software (can be downloaded from the CES FTP site, and is also available on CD-SOFT1 CD).1.5System RequirementsIt is necessary to have a computer running Windows 2000, Windows XP, Windows Server 2003 or Windows7 to program the device. The system must include a USB port in order to configure the GPS-208.1.6GPS-208 Front ViewFront View: On the front of the GPS-208 is the 16 pin interface connector. To the right of the connector are three LEDs. The functionality of these LEDs is:▪USR1 (Green) – This LED indicates the state of the GSM connection. If blinking the GPS206 is attempting to establish the connection. If solid the GSM connection has been established.▪PWR GPS (Red) – When this LED is illuminated it indicates that the GPS206 has power.USR2 (Blue) – This LED indicates the state of the GPS fix. If illuminated the GPS206 has established a position fix from satellites in the GPS satellite constellation that are viewable from its current location.1.7LabelThe GPS-208 has a printed label on its top side. It is important that when the GPS-208 is mounted that the label side is pointing towards the sky.Figure 2: Label indicating the top side of the GPS208Figure 1: Front view of the GPS-2082.0SpecificationsNote: Specifications subject to change without notice.2.1System InformationDimensions 3.23 x 1.81 x .83 inches (82 x 46 x 21 mm)WeightHousing:Rugged textured plastic enclosure, V0 fire ratedTX Power:Class 4 (2W @850/900 MHz)Class 1 (1W @1800/1900 MHz)Frequency:850/900/1800/19002.2GPRS Packet DataMode:Class B, Multislot 10Protocol:GSM/GPRS Rel 97 AMR Rel 99Coding Schemes:CS1-CS4Packet Channel:PBCCH/PCCCH2.3GPS FunctionalityAntenna:Built In2.4EnvironmentOperating:-30°C to +85°CStorage: -40°C to +85°CHumidity: Up to 95% non-condensingVibration: In accordance with SAE J12112.5CertificationsFCC: Part 15, 22 & 24GCF: Version 3.40.0PTCRB: Version 5.6Industry Canada RSS-210, 132, 133CE Mark Article 3.1a, 3.1b, 3.2Emark YesRoHS Compliant YesAnatel YesAT&T YesICASA Yes (pending)2.6SIM Card/Interface/I/OSIM Access: InternalGSM Antenna: Built InI/O Connector:16 Pin1 User Input (0-40V)Ignition Sense2 Outputs2.7PowerDC Voltage9-16V2.8BatteryBattery Optional rechargeable lithium-ion battery (230mA)3.0InstallationThe instructions in this section describe the hardware installation of the GPS-208. To install the GPS-208 in a vehicle follow these steps:•Choose a convenient location in the vehicle – either in the trunk or interior of a vehicle. Avoid locations that might expose the GPS-208 to excessive heat or moisture.•The GPS-208 as a printed label on the top side of the device. It is important that this label be facing towards the sky when the GPS-208 is installed.•An optional backup battery is available for the GPS-208. If the device is equipped with a battery it is important that the power switch for the battery be turned on. The image below shows the location of the power switch. In the image it is in the off state.3.1Installing CablesTo ensure proper operation of the GPS-208 please follow these precautions:•Remove power from the GPS-208.•Do not create sharp bends, loops or crimps in the cables.•Attach all cables to the vehicle and equipment in such a way as to reduce stress or wear caused by the vibration generated by moving vehicles.•No more than a combined total of ten (10) pounds force can be applied to the GPS-208 connector. •Properly terminate all power cables.3.1.1HRNS-062 - 16-Pin I/O ConnectorHRNS-062 is a 16-pin external I/O connector and cable. This connector provides power and can be used to interface the GPS-208 with inputs and outputs.CES Wireless Technologies can also provide optional cables with connectors. The part numbers vary with the cable’s intended use. Please contact your CES Wireless Technologies sales or support executive for more information.You may also build your own cable. Table 1 describes the functionality of this 16-pin connector. CES recommends using 20-gauge wire when building the connector. Pins that are not planned for usage should be left open without anything connected to them.The GPS-208 is NOT a waterproof or sealed device. Care must be taken to ensure that the device is kept away from water and other liquids. The GPS-208 can be mounted inside a weather proofed box if necessary.Figure 3: GPS-208 Power Switch for the optional backup batteryFigure 4: 16 Pin ConnectorFigure 5: Opening the enclosure of the GPS-2082) Apply gentle pressure upwards on the lever until the lid snaps open.Figure 6: Enclosure unsnapped on the GPS-2083) Carefully slide the cover off of the GPS-208.3.2.2Closing the GPS-208To close the GPS-208 place the cover onto the base as shown in Figure 6. Carefully slide the lid until it snaps into place.3.3Installing the SIM (Subscriber Identity Module) CardThe SIM card is an integral part of any GSM terminal device. On the GPS-208 the SIM card is internal. The enclosure must be opened in order to install the SIM card. Following the instructions in Section 3.2 open the GPS-208 enclosure. Insert the SIM card in the SIM holder.The SIM card is inserted into the GPS-208 with the notch on the SIM card on the right and going in last.NOTE: Not all GPS-208’s are provided with SIM cards. The SIM card will be provided by CES Wireless Technologies only if GSM/GPRS data service is purchased along with the device. If purchasing the SIM card separately take steps to ensure that the SIM card is provisioned by the operator for data.Figure 7: Internal view of the GPS-208. Note the orientation of the SIM card.3.4Connecting PowerThe GPS-208 has an input voltage range of 9-16 VDC. The power and ignition pins can support 9-16 VDC input voltage. The user has an option to connect these wires depending on the desired functionality. Described below are the desired•Connect the ignition wire of the GPS-208 to an auxiliary power source, i.e. ignition.•Device goes through a reset upon ignition on.3.5Optional Backup BatteryAn optional 230 mAH backup battery is available for the GPS-208. The battery may need to be connected during the installation process. The battery will need to be turned on via the power switch (see Section 3.0 for more information).3.6GPS-208 InstallationThe enclosure for the GPS-208 includes molded anchor points for mounting as shown. Also, it is very important that the top side of the GPS-208 (the side with the label) be facing towards the sky.The battery switch must be turned on prior to connecting any auxiliary I/O devices. Failure to do so mayresult in damage to the GPS-208 and/or the attached I/O device.Figure 9: GPS-208 optional backup battery and connector.Figure 8: GPS-208 optional backup battery connected to the main circuit board.Figure 10: GPS-208 mounting anchors.4.0SupportIf you need help, we are easily accessible ….Telephone:Call 407-679-9440, and ask for product support.Fax:407-679-8110Email:support@Skype: Please email support@ to obtain your currently assigned support engineer’s Skype address.Product support may ask you to E-MAIL a copy of the programmed parameters to us for analysis. To do this, go to FILE on the DP-1000S main menu, and click on SAVE AS. Note the path to the saved file in the save file dialog. Attach this file to an e-mail and send it to you product support representative or to the e-mail address noted above.Product support may ask you to PRINT a copy of the programmed parameters, and fax to for analysis. To do this, go to FILE on the DP-1000S main menu, and click on PRINT.Support Resources: FTP Site: Please go to and register for an FTP site User Name and Password。
Atlas 8 数字二氧化碳控制器说明书

Dealer/Customer’s Contact Name: __________________________________________________________________
1 Square = ____ Foot/Feet
®
Atlas® 8
Digital CO2 Controller with Fuzzy Logic
Instruction Manual
VANCOUVER, WASHINGTON U.S.A.
Revision G – 2/19/2013 © Titan Controls®
• Plug controller into surge protector to avoid potential damage to the unit.
• Confirm that your power source is 120 Volts/15 Amps prior to plugging controller into outlet.
• Do not use controller for purposes other than the unit was designed to function.
• Use controller within defined environmental specifications.
• Ask your Dealer for tips and techniques regarding the use of this controller.
GPDS207A_208Av01

GENERALPLUS TECHNOLOGY INC. reserves the right to change this documentation without prior notice. Information provided by GENERALPLUS TECHNOLOGY INC. is believed to be accurate and reliable. However, GENERALPLUS TECHNOLOGY INC. makes no warranty for any errors which mayGAudio Decoder with Card ReaderP r e l i m i n a r yMAY 14, 2009 Version 0.1P D S 207A /G P D S 208ATable of ContentsPAGE1.GENERAL DESCRIPTION (3)2.BLOCK DIAGRAM (3)3.FEATURES (3)4.SIGNAL DESCRIPTIONS (4)4.1.PIN M AP (6)4.2.PAD L OCATIONS (7)5.FUNCTIONAL DESCRIPTIONS (8)5.1.CPU (8)5.2.PLL,C LOCK,P OWER M ODE (8)5.2.1.PLL (Phase Lock Loop) (8)5.2.2.System Clock (8)5.3.P OWER S AVINGS M ODE (8)5.4.I NTERRUPT (8)5.5.I/O (8)5.5.1.GPIO (8)5.6.T IMER /C OUNTER (8)5.7.W ATCHDOG (8)5.8.S ERIAL I NTERFACE (9)5.8.1.Serial Peripheral Interface (SPI) (9)B Mini-host/Device Function (9)5.8.3.I2C Function (9)5.9.SD/MMC C ONTROLLER (9)5.10.R EAL T IME C LOCK (RTC) (10)5.11.A NALOG C ONTROL (10)5.11.1.D AC Control (10)5.11.2.A DC Control (10)6.ELECTRICAL SPECIFICATIONS (11)6.1.A BSOLUTE M AXIMUM R ATING (11)6.2.DC C HARACTERISTICS (11)6.3.DAC C HARACTERISTICS (11)6.4.10B ITS ADC C HARACTERISTICS (VDD=3.3V,T A=25℃) (12)6.5.R EGULATOR C HARACTERISTICS (12)7.RECOMMENDED BOARD LAYOUT (13)7.1.P OWER AND G ROUND (13)7.2.C RYSTAL AND PLL (13)8.PACKAGE/PAD LOCATIONS (14)8.1.O RDERING I NFORMATION (14)8.2.P ACKAGE I149.1610.R EVISION HISTORY (17)4. SIGNAL DESCRIPTIONS Left SideNo Name Type Normal Function Description PackagePinGPIO Group1 DVSS PDigitalGround 48 -2 RESETB I/O Reset input pin (Low active) 1 -3 GPIO7 I/OGPIO7 2 IOA74 GPIO12 I/OGPIO12 3 IOA125 DVCC18 P 1.8V power for core logic 46 INT1 I/O External Interrupt 1 5 IOB37 INT2 I/O External Interrupt 2 6 IOB48 SPICSN I/O SPI Chip Select, low active 7 IOA89 SPICLK I/O SPI Clock pins 8 IOB710 SPITX I/O SPI transmit data pin 9 IOB811 SPIRX I/O SPI receive data pin 10 IOB912 KEYA I/O Key change pin A 11 IOB1013 DVCC33 P 3.3V IO Power 1214 AVDD P3.3VADCPower 1215 LINEIN0 A/I/O ADC Line in 0 13 IOB1116 LINEIN1 A/I/O ADC Line in 1 - IOC13 Bottom SideNo Name Type Normal Function Description PackagePinGPIO Group17 LINEIN2 A/I/O ADC Line in 2 - IOC1418 LINEIN3 A/I/O ADC Line in 3 - IOC1519 AVSS PADCGround 1420 DVSS PDigitalGround 1421 SDDAT2 I/O SD Data 2 15 IOA1022 SDDAT3 I/O SD Data 3 16 IOA1123 SDCMD I/O SDCommand 17 IOB0 24 SDCLK I/OSDClock 18 IOB125 SDDAT0 I/O SD Data 0 19 IOB226 SDDAT1 I/O SD Data 1 20 IOA927 TEST I/O Test Mode Selection, high active 2128 DVCC18 P 1.8V power for core logic 2229 I2CSDA I/O I2C Data Pin 23 IOB530 I2CSCL I/O I2C Clock Pin 24 IOB631 DVCC33 P 3.3V IO Power 2532 BM2 I Boot mode selection -33 ICECK I/OICEClock -34 ICEDA I/OICEData -35 KEYB I/O Key Change pin B - IOB1236 IOB13 I/OIOB13 - IOB13Right SideNo Name Type Normal Function Description PackagePinGPIO Group37 AVDD P 3.3V DAC Power 2538 DACOL A DAC Left output 2639 DACVREF A DACVREF 2740 DACOR A DAC Right Output 2841 AVSS PDACGround 29 42 AVSS PUSBPHYGround 2943 DN I/O DN pin of USB PHY 3044 DP I/O DP pin of USB PHY 3145 AVDD P 3.3V USB PHY Power 3246 DVCC33 P 3.3V Regulator Power 3247 DVCC33 P 3.3V Regulator Power 3248 AVSS PRegulatorGround 33 49 DVCC18 P 1.8Vregulatoroutput 3450 DVCC18 P 1.8V power for core logic 3451 PLLV18 P 1.8V power for PLL 3452 X6MO O 6M Crystal output53 X6MI I 6M Crystal input 3554 PLLVSS P PLLGround 36 Top SideNo Name Type Normal Function Description PackagePinGPIO Group55 X32KI I 32768HzCrystalInput 3756 X32KO O 32768HzCrystalOutput 3857 PLLV33 P 3.3V power for 32768Hz crystal 3958 DVCC33 P 3.3V IO Power 3959 GPIO0 I/OGPIO0 40 IOA060 GPIO1 I/OGPIO1 41 IOA161 GPIO2 I/OGPIO2 42 IOA262 GPIO3 I/OGPIO3 43 IOA363 GPIO4 I/OGPIO4 44 IOA464 GPIO5 I/OGPIO5 45 IOA565 GPIO6 I/OGPIO6 46 IOA666 DVCC18 P 1.8V power for core logic 4767 DVSS PDigitalGround 4868 NC NC -4.2. PAD LocationsThis IC substrate should be connected to VSSNote1: To ensure that the IC functions properly, please bond all of VDD and VSS pins.Note2: The 0.1μbe interrupted by a FIQ, but not by another IRQ. A FIQ cannot be interrupted by any other interrupt sources. Some of the interrupt5.8. Serial Interface5.8.1. Serial Peripheral Interface (SPI)The SPI interface is a master/slave interface that enables synchronous serial communication with slave/master peripherals.Two 8-byte FIFOs are used for transmitting and receiving data.Four types of timing are supported and shown in the following diagram.MSBLSBSCLKSFRMSSPTXDSSPOE8bitsMSBLSBSSPRXDQSPO = 0, SPH = 0, only this mode is supported in SPI slave mode.M SBLSBSCLKSFRMSSPTXDSSPOE8 bitsM SBLSBSSPRXDQQSPO = 0, SPH = 1MSBLSBSCLKSFRMSSPTXDSSPOE8bitsMSBLSBSSPRXDQSPO = 1, SPH = 0MSBSCLKSFRMSSPTXDSSPOE8bitsMSB LSB SSPRXD Q QLSBSPO = 1, SPH = 15.8.2. USB Mini-host/Device FunctionGPDS207A/ GPDS208A provides both USB mini-host and device function which is compatible with USB 1.1 and USB 2.0 full speed standard. The mini-host and device function are not allowed to be activated concurrently. An USB transceiver is built-in for both host and devices function. A FIFO with size of 128x8 is used for bulk-in and bulk-out transfer and an 8-bytes FIFO is used forcontrolling pipe-transfer. Interrupt pipe is also supported. The DMA transfer is enabled for bulk-in and bulk-out to maximize thetransfer performance.5.8.3. I 2C FunctionGPDS207A/ GPDS208A provides an I 2C controller which supports master read/write transfer, slave read/write transfer and 7-bit address mode. Multi-master mode is also supported. The following diagram shows the I 2C bus read/write timing.5.9. SD/MMC ControllerGPDS207A/ GPDS208A features a SD/MMC controller which isMemory Card specification 1.1. Both 1-bit mode and 4-bit mode are supported. The controller supports automatically CRC generation and check, 1 bit and four bits transfer, interrupt generation when buffer empty/full, DMA transfer for page read/write.5.10. Real Time Clock (RTC)The RTC block offers alarm function, schedule function, and hour/minute/second/half-second interrupt function.5.11. Analog Control5.11.1. DAC ControlA 16-bit DAC is embedded in GPDS207A/ GPDS208A. For both left and right channel, a 16x16 FIFO is used to prevent the sound glitch when CPU is busy. The left and right channel must have the same sample rate.5.11.2. ADC ControlA 10-bit ADC is embedded in GPL162002A for AD key detection application. The ADC has four inputs which can be selected by software programming with maximum 60KkHz sample rate.6. ELECTRICAL SPECIFICATIONS6.1. Absolute Maximum RatingRating Symbol Value Unit Supply Voltage 1 DVCC33PLLV33-0.3 to 4.0 V Supply Voltage 2 AVDD -0.3 to 4.0 VSupply Voltage 3 DVCC18PLLV18-0.3 to 2.16 V Input Voltage V IN-0.3 to 4.0 VOperating Temperature T A0 to 85 ℃Storage Temperature T STG-40 to +150 ℃6.2. DC CharacteristicsLimitsCharacteristic SymbolMin. Typ. Max.Unit ConditionOperating Voltage 1 DVCC33PLLV33 2.73.033.0 3.6 V -Operating Voltage 2 AVDD 2.7 3.0 3.3 V -Operating Voltage 3 DVCC18PLLV18 1.62 1.8 1.98V -Operating Current I OP- TBD - mA @48MHz, 3.3V, all clocks on Power Down Current I PD- TBD - μA HaltMode High Input Voltage V IH0.7DVCC33- DVCC33V -Low Input Voltage V IL VSS - 0.8 V -Crystal Frequency 1 - -32768 - Hz - Crystal Frequency 2 F CRYSTAL- 6.01- MHz -System Clock F SYS256Hz248 48MHz -Note1: 6M Crystal is used only when die form is selected.Note2: By setting clock divider and changing system clock to 32768Hz mode.Note3: When USB function is enabled, the minimum voltage of DVCC33 is 3.0V.6.3. DAC CharacteristicsLimitsCharacteristicMin. Typ. Max.Unit Condition Resolution - 16 - Bit -Full Scale Output Voltage - 2 - Vp-p -THD+N (f = 1kHz) - TBD - %-Noise at No Signal -85 90 - dBv -Frequency Response 20 - 19200 Hz -6.4. 10 Bits ADC Characteristics (VDD = 3.3V, T A = 25℃)UnitUnit Characteristics SymbolMin. Typ. Max.ADC Power Dissipation IADC - 1.8 - mAADC Input Voltage Range VINL (Note1) VSS - 0.3- VDD + 0.3 VResolution of ADC RESO - - 12 bitsSignal-to-Noise Plus Distortion of ADC from Line in SINAD (Note3)- TBD - dBEffective Number of Bit ENOB (Note4)8.0 9 - bits(Note2) Integral Non-Linearity of ADC INL - ±1.0 - LSB Differential Non-Linearity of ADC DNL (Note5) - ±1.0 - LSB AD Conversion Rate F CONV F CPU / 2048- F CPU / 256 HzNote1: Internal protection diodes clamp the analog input to VDD and VSS. These diodes allow the analog input to swing from (VSS - 0.3V) to (VDD + 0.3V) without causing damage to the devices.Note2: LSB means Least Significant Bit (at 10 bits resolution). With VINL = 2.0V, 1LSB = 2.0V / 2^10 = 1.953mV.Note3: The SINAD testing condition at VINLp-p = 0.8 * VDD, F CONV = 100KHz, Fin = 1.0KHz Sine waves at VDD = 3.0V from the ADC input.Note4: ENOB = (SINAD - 1.76) / 6.02.Note5: This ADC can guarantee no missing code at 10 bits resolution.6.5. Regulator CharacteristicsUnitUnit Characteristics SymbolMin. Typ. Max.InputVoltage VREGI 2.7 3.0 3.6 V Maximum Current Output IREGO - 50 60 mAOutput Voltage VREGO 1.351 1.8 1.89 V StandbyCurrent IREGS - 10 - - Note1: By software program, it is not allowed to switch the voltage below 1.35 V when system is running at full speed (>48MHz).Please refer to following diagram to connect the crystal circuitwhen the die form is selected and 6M crystal is used.diagram to connect the crystal circuit.Please refer to the crystal’s application circuit.8. PACKAGE/PAD LOCATIONS8.1. Ordering InformationProduct Number Package TypeGPDS207A - NnnV - C Chip FormGPDS208A - NnnV - QL15x Halogen Free PackageNote1: Code number is assigned for customer.Note2: Code number (N = A - Z or 0 - 9, nn = 00 - 99); version (V = A - Z).Note3: x = 0 - 9, serial number.8.2. Package InformationLQFP 48MillimeterSymbolMin. Nom. Max.A - - 1.60A1 0.05 - 0.15A2 1.35 - 1.45c1 0.09 0.16BSC.D 9.00D1 7.00BSC.E 9.00BSC.MillimeterSymbolMin. Nom. Max.BSC.E1 7.00BSC.e 0.5b 0.17 - 0.27L 0.45 - 0.75REF L1 1.009. DISCLAIMERThe information appearing in this publication is believed to be accurate.Integrated circuits sold by Generalplus Technology are covered by the warranty and patent indemnification provisions stipulated in the terms of sale only. GENERALPLUS makes no warranty, express, statutory implied or by description regarding the information in this publication or regarding the freedom of the described chip(s) from patent infringement. FURTHERMORE, GENERALPLUS MAKES NO WARRANTY OF MERCHANTABILITY OR FITNESS FOR ANY PURPOSE. GENERALPLUS reserves the right to halt production or alter the specifications and prices at any time without notice. Accordingly, the reader is cautioned to verify that the data sheets and other information in this publication are current before placing orders. Products described herein are intended for use in normal commercial applications. Applications involving unusual environmental or reliability requirements, e.g. military equipment or medical life support equipment, are specifically not recommended without additional processing by GENERALPLUS for such applications. Please note that application circuits illustrated in this document are for reference purposes only.10. REVISION HISTORY# Description Page Date RevisionMAY 14, 2009 0.1 Preliminary version. 17。
Numonia Digital Torque Tester M的说明文档说明书

TESTER
DIGITAL TORQUE TESTERTM (DTT)
TEST THE HEALTH OF YOUR TORQUE WRENCHES - ANYWHERE WITH THE DIGITAL TORQUE TESTER. Utilizing the testing protocol and standards developed by the American Society of Mechanical Engineers (ASME)
Features
• Integral Transducer and sturdy housing allow mounting in virtually any position • Integral Transducer: Full bridge strain gage, 350 ohm, 1500uE, 3mV/V F.S, 3.75 excitation. • Units of Torque: Nm, kgcm, ft.lb., in.lb., in-oz. • Audible (tone) and LED light-bar Present Alerts • Torque Accuracy: ±0.5% ±1 count CW and CCW from 10 to 100% of full scale at 25° C • LCD Touch Screen: 4.7 in. color graphics display • Screen resolution: 480 X 272 pixels • Display Accuracy: 4 digits, 9999 cycle counts • Six “AA” Alkaline cells for battery power included • Track, Peak and First Peak modes of operation • Operating Temperature: 40 to 110° F (5 to 42° C) • Storage Temperature: 0 to 122° F (-20 to 50° C) • Humidity up to 85% non-condensing • EU/CE-DE, ES, FR, IT, NL, PT, UK and Japanese language manual • Certificate of N.I.S.T. traceability from 10% to 100% of full scale • Includes storage case, AC adapter and USB cable
Datavideo DAC-80 音频隔离变压器说明书

Instruction Manualw w w.d a t a v i d e o.c o mAUDIO ISOLATIONTRANSFORMER DAC-80Table of ContentsFCC COMPLIANCE STATEMENT (3)WARNINGS AND PRECAUTIONS (3)WARRANTY (5)S TANDARD W ARRANTY (5)T HREE Y EAR W ARRANTY (5)DISPOSAL (6)1.INTRODUCTION (7)F EATURES (7)S YSTEM D IAGRAM (8)2.CONNECTIONS & CONTROLS (9)F RONT P ANEL (9)R EAR P ANEL (10)3.ELECTRONIC CIRCUIT DIAGRAM (11)4.SPECIFICATIONS (11)SERVICE & SUPPORT (12)Disclaimer of Product and ServicesThe information offered in this instruction manual is intended as a guide only. At all times, Datavideo Technologies will try to give correct, complete and suitable information. However, Datavideo Technologies cannot exclude that some information in this manual, from time to time, may not be correct or may be incomplete. This manual may contain typing errors, omissions or incorrect information. Datavideo Technologies always recommend that you double check the information in this document for accuracy before making any purchase decision or using the product. Datavideo Technologies is not responsible for any omissions or errors, or for any subsequent loss or damage caused by using the information contained within this manual. Further advice on the content of this manual or on the product can be obtained by contacting your local Datavideo Office or dealer.FCC Compliance StatementThis device complies with part 15 of the FCC rules. Operation is subject to the following two conditions:(1)This device may not cause harmful interference, and(2)This device must accept any interference received, including interferencethat may cause undesired operation.Warnings and Precautions1.Read all of these warnings and save them for later reference.2.Follow all warnings and instructions marked on this unit.3.Unplug this unit from the wall outlet before cleaning. Do not use liquid oraerosol cleaners. Use a damp cloth for cleaning.4.Do not use this unit in or near water.5.Do not place this unit on an unstable cart, stand, or table. The unit mayfall, causing serious damage.6.Slots and openings on the cabinet top, back, and bottom are provided forventilation. To ensure safe and reliable operation of this unit, and to protect it from overheating, do not block or cover these openings. Do not place this unit on a bed, sofa, rug, or similar surface, as the ventilation openings on the bottom of the cabinet will be blocked. This unit should never be placed near or over a heat register or radiator. This unit should not be placed in a built-in installation unless proper ventilation is provided.7.This product should only be operated from the type of power sourceindicated on the marking label of the AC adapter. If you are not sure of the type of power available, consult your Datavideo dealer or your local power company.8.Do not allow anything to rest on the power cord. Do not locate this unitwhere the power cord will be walked on, rolled over, or otherwise stressed.9.If an extension cord must be used with this unit, make sure that the totalof the ampere ratings on the products plugged into the extension cord do not exceed the extension cord rating.10.Make sure that the total amperes of all the units that are plugged into asingle wall outlet do not exceed 15 amperes.11.Never push objects of any kind into this unit through the cabinetventilation slots, as they may touch dangerous voltage points or short out parts that could result in risk of fire or electric shock. Never spill liquid of any kind onto or into this unit.12.Except as specifically explained elsewhere in this manual, do not attemptto service this product yourself. Opening or removing covers that are marked “Do Not Remove” may expose you to dangerous voltage points or other risks, and will void your warranty. Refer all service issues to qualified service personnel.13.Unplug this product from the wall outlet and refer to qualified servicepersonnel under the following conditions:a.When the power cord is damaged or frayed;b.When liquid has spilled into the unit;c.When the product has been exposed to rain or water;d.When the product does not operate normally under normal operatingconditions. Adjust only those controls that are covered by the operatinginstructions in this manual; improper adjustment of other controls mayresult in damage to the unit and may often require extensive work by aqualified technician to restore the unit to normal operation;e.When the product has been dropped or the cabinet has been damaged;f.When the product exhibits a distinct change in performance, indicatinga need for service.WarrantyStandard Warranty•Datavideo equipment are guaranteed against any manufacturing defects for one year from the date of purchase.•The original purchase invoice or other documentary evidence should be supplied at the time of any request for repair under warranty.•The product warranty period beings on the purchase date. If the purchase date is unknown, the product warranty period begins on the thirtieth day after shipment from a Datavideo office.•Damage caused by accident, misuse, unauthorized repairs, sand, grit or water is not covered under warranty.•Viruses and malware infections on the computer systems are not covered under warranty.•Any errors that are caused by unauthorized third-party software installations, which are not required by our computer systems, are not covered under warranty.•All mail or transportation costs including insurance are at the expense of the owner.•All other claims of any nature are not covered.•Cables and batteries are not covered under warranty.•Warranty only valid in the country or region of purchase.•Your statutory rights are not affected.Three Year Warranty•All Datavideo products purchased after July 1st, 2017 arequalified for a free two years extension to the standardwarranty, providing the product is registered withDatavideo within 30 days of purchase.•Certain parts with limited lifetime expectancy such as LCD panels, DVD drives, Hard Drive, Solid State Drive, SD Card, USB Thumb Drive, Lighting, Camera module, PCIe Card are covered for 1 year.•The three-year warranty must be registered on Datavideo's official website or with your local Datavideo office or one of its authorized distributors within 30 days of purchase.DisposalFor EU Customers only - WEEE MarkingThis symbol on the product indicates that it will not betreated as household waste. It must be handed over tothe applicable take back scheme for the recycling ofWaste Electrical and Electronic Equipment. For moredetailed information about the recycling of this product,please contact your local Datavideo office.CE Marking is the symbol as shown on the left of this page.The letters "CE" are the abbreviation of French phrase"Conformité Européene" which literally means "EuropeanConformity". The term initially used was "EC Mark" and itwas officially replaced by "CE Marking" in the Directive 93/68/EEC in 1993. "CE Marking" is now used in all EU official documents.1. IntroductionDAC-80 is designed to remove hum and buzz created by ground loops. Normal voltage differences in the system grounding points between different pieces of equipment cause small AC power currents to flow in the shield of audio cables. Capacitance between a power transformer’s primary and secondary windings introduce signals to the circuit ground which will also create small current flows in the cable shield. Either of these problems will create hum in audio signals. DAC-80 breaks the inter-equipment ground path and greatly increases the rejection in the input circuits while remaining transparent to the audio signal. Features•Easy to use•Eliminate audio noise caused by ground loops•Designed for low signal loss and low distortion•Passive device (No power required)System Diagram2. Connections & Controls Front PanelCH1 / CH2 Audio InputXLR Balanced Audio input (Channel 1 / 2)LIFT Toggle SwitchThese switches turn to UP position, audio ground not connected. Breaks ground loops, provides audio isolation.These switches turn to DOWN position, for chassis shield and audio ground connected. Corrects balance on audio lines.(Left switch =CH2, Right switch = CH1)Rear PanelCH1 /CH2 Audio OutputXLR Balanced Audio output (Channel 1/ 2).113.Electronic Circuit Diagram4. SpecificationsImpedance600Ω+/- 10%(Input & output)Bandwidth Frequency 20Hz ~20KHz ±0.5dB THD: 1 KHz < 0.015% @ +4dBu; 20Hz: 0.05% @+4dBu Insertion loss <0.5dB Turns Ratio 1:1Input 2 XLR Audio Input Channels Output 2 XLR Audio Output ChannelsDimensions 85mm x 45.2mm x 111.5mm (W x H x D)All the trademarks are the properties of their respective owners. Datavideo Technologies Co., Ltd. All rights reserved 2018Service & SupportJul-07.2017Please visit our website for latest manual /product/DAC-80It is our goal to make your products ownership a satisfying experience. Our supporting staff is available to assist you in setting up and operating your system. Please refer to our web site for answers tocommon questions, support requests or contact your local office below.DATAVIDEO WORLDWIDE OFFICES Tel: +1-562-696 2324Fax:+1-562-698 6930E-mail:*******************E-mail:******************Datavideo Technologies China Co601,Building 10,No.1228,Rd.Jiangchang,Jingan District,Shanghai Tel: +86 21-5603 6599Fax:+86 21-5603 6770E-mail:********************Datavideo Visual Technology(S) Pte Ltd No. 178 Paya Lebar Road #06-07Singapore 409030Tel: +65-6749 6866Fax:+65-6749 3266E-mail:****************************Datavideo Technologies Co. Ltd 10F. No. 176, Jian 1st Rd.,Chung Ho District, New Taipei City 235, Taiwan Tel: +886-2-8227-2888Fax:+886-2-8227-2777E-mail:*********************.tw Datavideo Corporation 7048 Elmer Avenue.Whittier, CA 90602, U.S.A.Datavideo UK LimitedBrookfield House, Brookfield Industrial Estate, Peakdale Road, Glossop, Derbyshire, SK13 6LQ Tel: +44-1457 851 000Fax:+44-1457 850 964E-mail:******************.uk Datavideo Technologies China Co 902, No. 1 business building, Xiangtai Square, No. 129,Yingxiongshan Road, Shizhong District, Jinan City, Shandong Province, China Tel: +86 531-8607 8813E-mail:********************Datavideo France s.a.r.l.Cité Descartes 1, rue Albert Einstein Champs sur Marne 774477 –Marne la Vallée cedex 2Tel: +33-1-60370246Fax:+33-1-60376732E-mail:*****************Datavideo Hong Kong Ltd G/F.,26 Cross Lane Wanchai, Hong KongTel: +852-2833-1981Fax:+852-2833-9916E-mail:******************.hk Datavideo India NoidaFax:+91-0120-2427338E-mail:******************Tel: +91-0120-2427337A-132, Sec-63,Noida-201307, IndiaDatavideo India KochiTel: +91 4844-025336Fax:+91 4844-0476962nd Floor- North Wing, Govardhan Building,Opp. NCC Group Headquaters, Chittoor Road, Cochin- 682035Datavideo Technologies Europe BV Floridadreef 1063565 AM Utrecht,The NetherlandsTel: +31-30-261-96-56Fax:+31-30-261-96-57E-mail:*****************Datavideo Technologies China Co No. 812, Building B, Wankai Center,No.316, Wan Feng Road, Fengtai District, Beijing, ChinaTel: +86 10-8586 9034Fax:+86 10-8586 9074E-mail:********************Datavideo Technologies China CoA1-2318-19 Room,No.8, Aojiang Road,Taijiang District,Fuzhou,Fujian,China Tel**************,*************Fax**************E-mail:********************Datavideo Technologies China Co B-823,Meinian square,No.1388,Middle of Tianfu Avenue,Gaoxin District,Chengdu,SichuanTel: +86 28-8613 7786Fax:+86 28-8513 6486E-mail:********************Datavideo Technologies (S) PTE Ltd No. 178 Paya Lebar Road #06-03Singapore 409030Tel: +65-6749 6866Fax:+65-6749 3266E-mail:******************。
博世安防 B208-CHI SDI2 8 输入扩展模块说明书

u 可编程输入防区功能u 易于读取的地址开关u 2 个互连布线连接器u提供 8 个防区B208 8路输入模块是一个八防区扩展设备,可通过SDI2总线连接到报警主机。
此模块受到全面监测并将所有防区状态更改传回至报警主机。
模块扩展防区的操作与报警主机上的防区大操作相同。
工业、商业和机构设施是B208 模块的典型安装。
B208使用SDI2端子或使用互连电缆连接到报警主机上的SDI2总线。
您可以将多个B208 模块连接到一个报警主机。
B208地址开关实现了轻松设备寻址。
系统概述B208 8路输入模块通过SDI2总线连接到报警主机。
此模块受到全面监测并将所有防区状态更改传回至报警主机。
此模块的扩展防区的操作与报警主机上的防区的操作相同。
功能回路输入B208最多使用8个输入,这些输入可为“常开”(NO)或“常闭”(NC),带有1k Ω EOL 电阻进行监控。
安装/配置说明布线注意事项模块与报警主机的接线使用螺丝接线板或互连布线连接器连接到报警主机上的PWR 、A 、B 、COM 端子。
从模块到报警主机使用12 AWG 至22 AWG (1.5毫米至0.6毫米)缆线。
兼容性随附部件技术指标特性环境要求电源要求接线回路输入订购信息B208-CHI SDI2 8输入扩展模块提供8个可编程输入。
订单号 B208-CHI2供应商:中国:博世(上海)安保系统有限公司上海市长宁区虹桥临空经济园区福泉北路333号203幢8,9楼邮编:200335电话:+86 21 2218 1111传真:+86 21 2218 2099 服务热线:400-8310-669服务邮箱:*****************.com© 博世安防系统 2018 | 数据如有更改,恕不另行通知42172080267 | zh-CHS, V3, 10. 七月 2018。
Interra 电脑视频与音频输入模块用户指南说明书

1INTRODUCTIONThis manual covers:ISC2000-W – VGA & Audio (white) Line Driver ISC2000-I – VGA & Audio (ivory) Line Driver400-0087-00421Please read this manual carefully before using your ISC2000-W/ISC2000-I . Keep this manual handy for future reference. These safety instructions are to ensure the long life of your ISC2000-W/ISC2000-I and to prevent fire and shock hazard. Please read them carefully and heed all warnings.1.1 GENERAL• Qualified Altinex service personnel, or theirauthorized representatives must perform all service.1.2 INSTALLATION• To prevent fire or shock, do not expose this unitto rain or moisture. Do not place the ISC2000-W/ISC2000-I in direct sunlight, near heaters or heat radiating appliances, or near any liquid.Exposure to direct sunlight, smoke, or steam can harm internal components.• Handle the ISC2000-W/ISC2000-I carefully.Dropping or jarring can damage internal components.• Never install the ISC2000-W/ISC2000-I in thesame enclosure with high voltage wires or their associated components, such as power sockets,dimmers or switches. Always use proper isolation techniques to ensure that the ISC2000-W/ISC2000-I is never installed in an enclosure that has high voltages within it.1.3 CLEANING• Clean surfaces with a dry cloth. Never usestrong detergents or solvents, such as alcohol or thinner. Do not use a wet cloth or water to clean the unit.1.4 FCC / CE NOTICE• This device complies with part 15 of the FCCRules. Operation is subject to the following two conditions: (1) This device may not cause harmful interference, and (2) this device must accept any interference received, including interference that may cause undesired operation.• This equipment has been tested and found tocomply with the limits for a Class A digital device, pursuant to Part 15 of the FCC Rules.These limits are designed to provide reasonable protection against harmful interference when the equipment is operated in a commercial environment. This equipment generates, uses,and can radiate radio frequency energy and, if not installed and used in accordance with the instruction manual, may cause harmful interference to radio communications. Operation of this equipment in a residential area is likely to cause harmful interference in which case the user will be required to correct the interference at his own expense.• Any changes or modifications to the unit notexpressly approved by Altinex, Inc. could void the user’s authority to operate the equipment.400-0087-00432The ICS2000 is a 1-in, 1-out VGA and Audio Line Driver designed for installation into a wall. The unit provides a method of transmitting signals to a remote display and audio receiver or amplifier.The ISC2000 offers a female VGA-type 15-pin HD input connector and a stereo audio mini jack on its front panel. The rear panel offers two terminal block connectors. One is for the connection of balanced stereo audio and the other is for low voltage input power. Additionally, there is a 10-pin IDC connector for use with either the 5-BNC connector cable provided or the VGA output connector that is also included.The computer video RGB signals are passed through the ISC2000, but the video sync signals are buffered to ensure signal quality over long cable runs. Likewise, the incoming unbalanced stereo audio signal is converted to a balanced stereo audio on the output. This ensures better signal transmission over long cable runs.3FEATURES/DESCRIPTION ISC2000-W/ISC2000-IGENERAL InputsComputer Video Input 15-pin HD Female Audio Input Connector 3.5mm stereo audio OutputsVideo Output Connector 5 BNC/15pin HD Audio Output Connector Terminal BlockPower DC Source 2-pin terminal patibilityVGA/SVGA/XGA UXGA MAC/SUN/SGI and other analog computer video sourcesTable 1. ISC2000-W/ISC2000-I GeneralMECHANICAL ISC2000-W/ISC2000-I Depth (inches) 1.2 in. (30.5mm)Width (inches) 1.5 in (38.1mm)Height (inches) 2.6 in. (66mm)Weight (pounds).2 lb. (.12kg)Ship Weight (pounds) 1.6 lb. (.73kg)Material Steel FinishBlack Zinc Front Panel White or Ivory T° Operating 10°C -35°C T° Maximum 50°CHumidity90% non-condensingMTBF (calculations)40,000 hrs.Table 2. ISC2000-W/ISC2000-I MechanicalELECTRICAL ISC2000-W/ISC2000-I Input Video Signal Pass Thru Input Sync Signals Horizontal & Vertical TTL (+/-)Impedance 10 kOhms Output Video Signals Pass Thru Output Sync Signals Horizontal, & Vertical TTL (+/-)Impedance 75 Ohms Bandwidth -3dB @ 350MHz Audio Input Impedance 10k Ohms Max Level 0dBu Audio Throughput Gain Balanced / Unbal.+6dB / 0dB Freq. Response 10Hz-20kHz, +/- .05 dB Noise Floor -98dB @ 20kHz CMRR <40dB, 10Hz - 20kHz Audio Output Impedance 50 Ohms Drive >10dBu External Power 9VDC 500mA supply Table 3. ISC2000-W/ISC2000-I Electrical400-0087-00444400-0087-00454.1 VIDEO INPUTThe computer input is a 15-pin HD connector on the front of the ICS2000-W/ISC2000-I . It is connected to the video output of a desktop computer or similar device.PIN No.Input signals on 15-pin HDfemale connector1RED 2GREEN 3BLUE4SIGNAL RETURN 5SIGNAL RETURN 6SIGNAL RETURN 7SIGNAL RETURN 8SIGNAL RETURN 9VESA POWER INPUT 10SIGNAL RETURN 11SIGNAL RETURN12SDA13HORIZONTAL 14VERTICAL 15SCLTable 4. ISC2000-W/ISC2000-I ’s Video Input Pins4.2 VIDEO OUTPUTThe ISC2000-W/ISC2000-I offers a video output through a 10-pin IDC connector on the back of the ISC2000-W/ISC2000-I . The Distribution Amplifier allows a connection to different types of projectors or monitors using Altinex breakout cables.PIN No.VIDEO OUTPUTS ON 10-PIN IDCBLOCK1RED2GROUND 3GREEN 4GROUND 5BLUE 6GROUND 7HORIZONTAL 8GROUND 9VERTICAL10SIGNAL RETURNTable 5. 10-Pin IDC Connector Video Output Pins4.3 AUDIO INPUT & OUTPUTThe ISC2000-W/ISC2000-I accepts computer audio input and offers balanced stereo output through a terminal block connector on the back. There is a 3.5mm jack for computer audio input. A 5-pin terminal block is available for stereo audio transmission to the main sound system. These connectors are easily adaptable to stereo mini or RCA type connectors.PIN No.AUDIO OUTPUTS ON 5-PIN MALETERMINAL BLOCK1L+IN (Left Channel)2L-IN (Left Channel)3SIGNAL RETURN4R+IN (RIGHT Channel)5R-IN (RIGHT Channel)Table 6. 5-Pin Male Terminal Block for Audio Output4.4 POWER INPUT CONNECTORThe ISC2000-W/ISC2000-I has a power terminal block for connection to a 9VDC 500mA external adapter. Power regulation is provided inside the unit.PIN No.INPUT POWER ON 2-PIN MALETERMINAL BLOCK1+9VDC 2GNDTable 7. 2-Pin Male Terminal Block for Power Input400-0087-00465TYPICAL SETUPBREAKOUT VIDEO CABLE CONNECTION400-0087-00476PREPARATIONStep 1.There are a few common items to checkbefore testing the setup connections:a.Make sure the monitor and sound system work with the source computer before using the ISC2000.b.Ensure the source computer screen-savers do not shut down the video source during the system check.c.Verify the source audio level isreasonable, not too low or too high.VERIFICATIONStep 2.In order to verify proper connections andoperation before final installation, the following may be used to verify setup connections:a.Video InputsA video source such as a computer works well.b.Audio InputsA computer with a sound card is a convenient audio source.c.Video OutputsA standard computer monitor.d.Audio OutputsExternal computer speakers with built-in audio amplifier are sufficient.OUTPUT CONNECTIONSStep 3.Determine the proper breakout cablerequired for the video signal.Two special breakout cables that attach to the ISC2000 video output connector are included. One allows connection to a VGA 15 pin HD type connector cable. The other connects to RGBHV coaxial cables.Step 4.Attach the breakout cable to the videooutput connector. Make sure the breakout cable's connector mounting hole aligns with the ISC2000 screw hole and secure it with the screw provided. See Application Diagram 2 for details.Step 5.Connect the video breakout cable to thereceiving display device.Step 6The audio output from the ISC2000 can be balanced or unbalanced.If a balanced or unbalanced signal is needed, use a four-conductor cable with overall shield.For an unbalanced signal, connect one of the wires to ground. Use only the positive output form the ISC2000 to drive unbalanced signals. The negative output does not need to be connected to ground.INPUT CONNECTIONSStep 7. A 9VDC, 500mA power supply is neededto power the ISC2000. Connect the 9VDC power to the ISC2000 power input terminal block. The LED will turn red,indicating power is ON.Step 8.Connect an active video source to thefront of the ISC2000. If the cabling on the back of the ISC2000 is connected to a display, you should see an image.Step 9.Connect an active audio source to thefront of the ISC2000. If the cabling on the back of the ISC2000 is connected to an audio amplifier with speakers, you should hear sound.7There are no settings or adjustments on the ISC2000. The unit will operate successfully as long as cables are properly attached and other technical specifications are followed.400-0087-00488We have carefully tested and have found no problems in the supplied ISC2000 unit; however,we would like to offer the following suggestions:8.1 LED IS NOT LIT Cause 1:There is no 9VDC.Solution:Verify the 9VDC adapter is connected to the 2 pin terminal block input. If it is and the LED is not on,see Solution 2.Solution 2:Ensure there is AC power applied tothe power adapter and that the cables are plugged in all the way. If there is AC power and the cabling is correct, see Solution 3.Solution 3:Verify the power adapter is capableof supplying 500mA. If it is and the LED is still not on, call ALTINEX at (714) 990-2300.8.2 NO DISPLAY Cause 1:The source has a problem.Solution:Check the source and make sure that there is a signal present and all source connections are correct.Make sure that the input amplitude of the video analog signals are less than 1.5V and that the SYNC levels are TTL. If the source is good and there is still no display, see Cause 2.Cause 2:Cable connections are incorrect.Solution:Make sure that the cables are properly connected. Also, make sure that the continuity and wiring are good. If there is still no display present, see Cause 3.Cause 3:The display has a problem.Solution:Ensure the display has power and is ON. If there is still no display, call Altinex at (714) 990-2300.8.3 NO SOUND/BAD SOUND QUALITYNOTE:For very small audio signals, the amplifier for the speakers must necessarily amplify both the signal and any noise in the system. For very large audio output signals,distortion and clipping may occur. The source and the audio amplifier function best when the audio levels are set to midrange values. This is normal for an audio system regardless of whether an ISC2000 is used.If unwanted noise is heard on the audio circuit,consider alternate ways of wiring the audio output. Also, examine the system for possible sources of noise and route the audio signals as far as possible from the noise sources.Cause 1:The source has a problem.Solution :Check the source and make sure that it is working at an appropriate volume level and all source connections are correct. If the source is working and there is still no sound, see Cause 2.Cause 2:Audio devices are not compatible.Solution:Make sure that the audio devices are compatible. If so, see Solution 2.Solution 2:Connect the receiving device directlyto the source and verify proper operation. If there is still no sound,see Cause 3.Cause 3:Cable connections are incorrect.Solution:Make sure that all cables are connected properly. Also, make sure that the continuity and wiring are good. If there is still no sound present, see Cause 4.400-0087-0049Cause 4:Destination amplifier is bad.Solution 1:Make sure that the destinationamplifier is powered. If there is still no sound, see Solution 2Solution 2:Set the volume of the destinationamplifier to a reasonable level. If there is still no sound, call ALTINEX at (714) 990-2300.99.1 LIMITED WARRANTY/RETURN POLICYPlease see the Altinex website at for details on warranty and return policy.9.2 CONTACT INFORMATION ALTINEX, INC 592 Apollo Street Brea, CA 92821 USA TEL: 714 990-2300TOLL FREE: 1-800-ALTINEX WEB: E-MAIL: *********************。
- 1、下载文档前请自行甄别文档内容的完整性,平台不提供额外的编辑、内容补充、找答案等附加服务。
- 2、"仅部分预览"的文档,不可在线预览部分如存在完整性等问题,可反馈申请退款(可完整预览的文档不适用该条件!)。
- 3、如文档侵犯您的权益,请联系客服反馈,我们会尽快为您处理(人工客服工作时间:9:00-18:30)。
}
People
• Part of the 7 Ps - related to the interaction of staff with customers and stakeholders • What skills and experience do your staff need to service your customers • How do you integrate your human resources with your automated processes
______ refers to a model for assessing the quality of the online customer experience.
• • • • • The Long Tail SERVQUAL The Tipping Point -Price transparency None of the above.
• Promotion 1.personal promotion 2. direct marketing
• Place 1.Direct distribution channel 2. new intermediary
2. Critically evaluate the impact of the Internet on the marketing mix for an industry sector of your choice.
Tipping point 倾卸点
Ghosh (1998) describes methods of creating digital value by adding to the ______ element of the mix by asking questions such as, "can I offer additional information or transaction services to my existing customer base?" • • • • • Place Product Promotion Price None of the above.
Processes
• Part of the 7 Ps – related to methods and procedures companies use to achieve its marketing functions • Increase customer’s satisfaction and to minimise costs by increase efficiency, productivity and moral/motivation
Physical evidence
• Part of the 7 Ps – often referred to as the tangible expression of a product and how it’s purchased and used • In an online context – it’s refers to as the customer’s experience of the company through the website
The ______ customer concern from the 4Cs is equivalent to the Price element of the marketing mix.
• • • • • needs and wants convenience cost communications techniques None of the above.
• How customer interactions are managed
process
• Where the products are delivered or distributed to place • Different product pricing for different categories
______ refers to how word of mouth communication has a tremendous impact on the rate of adoption of new products • • • • • The Long Tail SERVQUAL The Tipping Point -Price transparency None of the above
______ refers to the impact of comparison websites and aggregator intermediaries.
• • • • • The Long Tail SERVQUAL The Tipping Point 倾卸点 Price transparency None of the above.
Extended Product
Additional
DHL
1.Core benefit: 2.deliver parcels 3.Basic product: 4.collect parcels form sender and deliver parcels to receivers 5.extened product: 6.tracking system make the customers know where their parcels have been delivered.
• Product: new digital products and valueadds. • Price: price reduction, new pricing models. • Place: new representation on intermediaries, direct-selling. • Promotion: integration of online and offline techniques.
price
The ______ customer concern from the 4Cs is equivalent to the Place element of the marketing mix
• • • • • needs and wants convenience cost communications techniques None of the above.
4C
• • • • Customer needs and wants (from product) Cost to the customer (price) Convenience (relative to place) Communication (promotion)
1. Select the two most important changes introduced by the Internet for each of the 4Ps.
• • • • • Disintermediation Countermediation Star Alliance Localisation None of the above.
Match the definition to the issue relating to Place in the online marketing mix. ______ refers to 'cutting out the middleman' through selling-direct.
Explain two applications of dynamic pricing on the Internet.
• selling ‘distressed inventory’, for example, flight tickets, which must be used by a fixed date. • varying prices for different segments.
BMA208
Tutorial 5 Toby
What is marketing mix?
• • • • • • • • • Traditional marketing mix is 4P But for internet marketing mix is 7P Product How are the marketing mix Promotion varied online? Price Place People better reflect Process service delivery Physical evidence
How word of mouth communication has a tremendous impact on the rate of adoption of new products, Using the science of social epidemics explains principles that underpin the rapid spread of ideas, products through a population. Domino effect
Match the definition to the issue relating to Place in the online marketing mix. ______ refers to the creation of country or region-specific content (often involving translation).
Product Price Place Promotion People Physical evidence Process
• A. How the brand is presented. Physical evidence • B. The mix of traditional and online Promotion communications • C. Opportunities for modifying the core or extended product Product • D. How customer service affects the experience people