精密和超精密加工技术第5章精密加工中的测量技术
精密和超精密加工技术

第一章精密和超精密加工技术及其发展展望精密和超精密加工代表了加工精度发展的不同阶段,通常,按加工精度划分,可将机械加工分为一般加工、精密加工、超精密加工三个阶段。
什么叫精密加工?加工精度在0.1~1µm,加工表面粗糙度在Ra0.02~0.1µm之间的加工方法称为精密加工。
什么叫超精密加工?加工精度高于0.1µm,加工表面粗糙度小于Ra0.01µm之间的加工方法称为超精密加工。
以下哪些是精密和超精密加工的分类?A.去除加工;B.结合加工;C.变形加工;D.切削加工;E.磨粒加工;F.特种加工;G.复合加工;影响精密与超精密加工的因素有哪些?加工机理、被加工材料、加工设备及其基础元部件、加工工具、检测与误差补偿、工作环境等。
我国今后发展精密与超精密加工技术的重点研究内容包括什么?(1)超精密加工的加工机理;(2)超精密加工设备制造技术;(3)超精密加工刀具、磨具及刃磨技术;(4)精密测量技术及误差补偿技术;(5)超精密加工工作环境条件。
第二章超精密切削与金刚石刀具举例说明超精密切削的应用范围有哪些?陀螺仪、激光反射镜、天文望远镜的反射镜、红外反射镜和红外透镜、雷达的波导管内腔、计算机磁盘、激光打印机的多面棱镜、录像机的磁头、复印机的硒鼓、菲尼尔透镜等由有色金属和非金属材料制成的零件。
超精密切削速度是如何选择的?超精密切削实际速度的选择根据所使用的超精密机床的动特性和切削系统的动特性选取,即选择振动最小的转速。
金刚石刀具的尺寸寿命甚高,高速切削时刀具磨损亦甚慢,因此刀具是否磨损以加工表面质量是否下降超差为依据,切削速度并不受刀具寿命的制约。
第二章超精密切削与金刚石刀具•举例说明超精密切削的应用范围有哪些?陀螺仪、激光反射镜、天文望远镜的反射镜、红外反射镜和红外透镜、雷达的波导管内腔、计算机磁盘、激光打印机的多面棱镜、录像机的磁头、复印机的硒鼓、菲尼尔透镜等由有色金属和非金属材料制成的零件。
精密与超精密加工-机械制造技术

≤0. 1
主轴轴向圆跳动 / μ m
≤0. 1
滑台运动的直线度 / μ m
≤1/150
横滑台对主轴的垂直度 / μ m
≤2/100
主轴前静压轴承(φ100mm)的刚 径向
度 /(N/μm)
轴向
1140 1020
主轴后静压轴承(φ80mm)的刚度 /(N/μm) 640
纵横滑台的静压支承刚度 /(N/μm)
基座
周缘 护板
T形布局的金刚石车床
11
➢ 金刚石车床主要性能指标
金刚石车床主要性能指标
最大车削直径和长度 /mm
400×200
最高转速 r/mm
5000~10000
最大进给速度mm /min
5000
数控系统分辩率 /μm
0. 1~0.01
重复精度(±2σ) / μ m
≤0. 2/100
主轴径向圆跳动 / μ m
3
◆ 精密加工与超精密加工的发展
加工误差(μm)
加工设备
测量仪器
102
普通加工
车床,铣床 精密车床
卡尺 百分尺
磨床
比较仪
101
精密加工
坐标镗床
气动测微仪
坐标磨床
光学比较仪
100
金刚石车床 光学磁尺
10-1 超精密加工
10-2
精密磨床
电子比较仪
超精密磨床 激光测长仪 精密研磨机 圆度仪轮廓仪
超高精密磨床 激光高精度
720
12
◆ 金刚石刀具
➢ 超精切削刀具材料:天然金刚石,人造单晶金刚石
➢ 金刚石的晶体结构:规整的单晶金刚石晶体有八面体、 十二面体和六面体,有三根4次对称轴,四根3次对称轴和 六根2次对称轴(图7-20)。
精密和超精密加工技术复习思考题答案
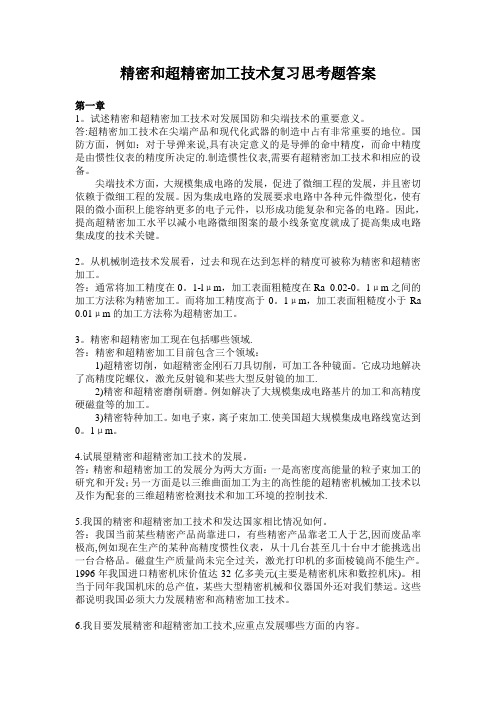
精密和超精密加工技术复习思考题答案第一章1。
试述精密和超精密加工技术对发展国防和尖端技术的重要意义。
答:超精密加工技术在尖端产品和现代化武器的制造中占有非常重要的地位。
国防方面,例如:对于导弹来说,具有决定意义的是导弹的命中精度,而命中精度是由惯性仪表的精度所决定的.制造惯性仪表,需要有超精密加工技术和相应的设备。
尖端技术方面,大规模集成电路的发展,促进了微细工程的发展,并且密切依赖于微细工程的发展。
因为集成电路的发展要求电路中各种元件微型化,使有限的微小面积上能容纳更多的电子元件,以形成功能复杂和完备的电路。
因此,提高超精密加工水平以减小电路微细图案的最小线条宽度就成了提高集成电路集成度的技术关键。
2。
从机械制造技术发展看,过去和现在达到怎样的精度可被称为精密和超精密加工。
答:通常将加工精度在0。
1-lμm,加工表面粗糙度在Ra 0.02-0。
1μm之间的加工方法称为精密加工。
而将加工精度高于0。
1μm,加工表面粗糙度小于Ra 0.01μm的加工方法称为超精密加工。
3。
精密和超精密加工现在包括哪些领域.答:精密和超精密加工目前包含三个领域:1)超精密切削,如超精密金刚石刀具切削,可加工各种镜面。
它成功地解决了高精度陀螺仪,激光反射镜和某些大型反射镜的加工.2)精密和超精密磨削研磨。
例如解决了大规模集成电路基片的加工和高精度硬磁盘等的加工。
3)精密特种加工。
如电子束,离子束加工.使美国超大规模集成电路线宽达到0。
1μm。
4.试展望精密和超精密加工技术的发展。
答:精密和超精密加工的发展分为两大方面:一是高密度高能量的粒子束加工的研究和开发;另一方面是以三维曲面加工为主的高性能的超精密机械加工技术以及作为配套的三维超精密检测技术和加工环境的控制技术.5.我国的精密和超精密加工技术和发达国家相比情况如何。
答:我国当前某些精密产品尚靠进口,有些精密产品靠老工人于艺,因而废品率极高,例如现在生产的某种高精度惯性仪表,从十几台甚至几十台中才能挑选出一台合格品。
精密加工课后习题答案
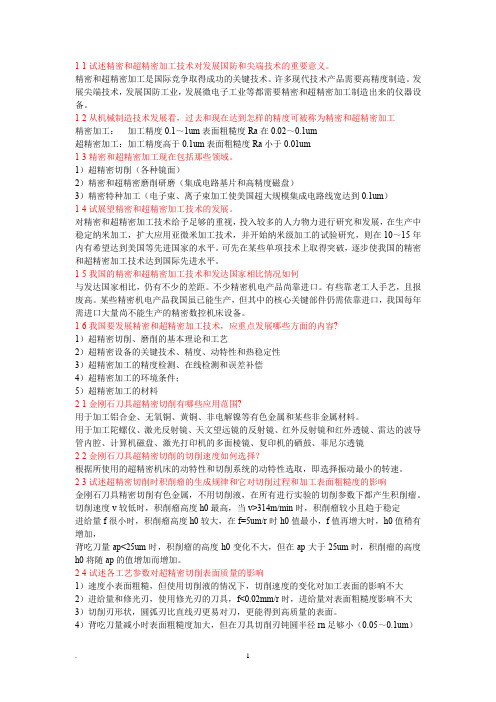
1-1试述精密和超精密加工技术对发展国防和尖端技术的重要意义。
精密和超精密加工是国际竞争取得成功的关键技术。
许多现代技术产品需要高精度制造。
发展尖端技术,发展国防工业,发展微电子工业等都需要精密和超精密加工制造出来的仪器设备。
1-2从机械制造技术发展看,过去和现在达到怎样的精度可被称为精密和超精密加工精密加工:加工精度0.1~1um表面粗糙度Ra在0.02~0.1um超精密加工:加工精度高于0.1um表面粗糙度Ra小于0.01um1-3精密和超精密加工现在包括那些领域。
1)超精密切削(各种镜面)2)精密和超精密磨削研磨(集成电路基片和高精度磁盘)3)精密特种加工(电子束、离子束加工使美国超大规模集成电路线宽达到0.1um)1-4试展望精密和超精密加工技术的发展。
对精密和超精密加工技术给予足够的重视,投入较多的人力物力进行研究和发展,在生产中稳定纳米加工,扩大应用亚微米加工技术,并开始纳米级加工的试验研究,则在10~15年内有希望达到美国等先进国家的水平。
可先在某些单项技术上取得突破,逐步使我国的精密和超精密加工技术达到国际先进水平。
1-5我国的精密和超精密加工技术和发达国家相比情况如何与发达国家相比,仍有不少的差距。
不少精密机电产品尚靠进口。
有些靠老工人手艺,且报废高。
某些精密机电产品我国虽已能生产,但其中的核心关键部件仍需依靠进口,我国每年需进口大量尚不能生产的精密数控机床设备。
1-6我国要发展精密和超精密加工技术,应重点发展哪些方面的内容?1)超精密切削、磨削的基本理论和工艺2)超精密设备的关键技术、精度、动特性和热稳定性3)超精密加工的精度检测、在线检测和误差补偿4)超精密加工的环境条件;5)超精密加工的材料2-1金刚石刀具超精密切削有哪些应用范围?用于加工铝合金、无氧铜、黄铜、非电解镍等有色金属和某些非金属材料。
用于加工陀螺仪、激光反射镜、天文望远镜的反射镜、红外反射镜和红外透镜、雷达的波导管内腔、计算机磁盘、激光打印机的多面棱镜、复印机的硒鼓、菲尼尔透镜2-2金刚石刀具超精密切削的切削速度如何选择?根据所使用的超精密机床的动特性和切削系统的动特性选取,即选择振动最小的转速。
精密和超精密加工技术课程设计

精密和超精密加工技术课程设计一、课程设计目的本课程设计旨在通过对精密和超精密加工技术的学习与研究,培养学生对于精密加工技术的理解和掌握,并能够通过实验操作提高技能水平。
二、课程设计内容2.1 精密加工技术1.精密加工技术概述2.精密加工的分类3.精密加工的工艺过程4.现代精密加工技术发展及应用2.2 超精密加工技术1.超精密加工技术概述2.超精密加工的分类3.超精密加工的工艺过程4.现代超精密加工技术发展及应用2.3 实验操作1.精密加工技术操作实验2.超精密加工技术操作实验三、课程设计要求3.1 实验操作要求1.实验前学生需要了解实验操作流程,明确实验目的,熟悉实验原理和安全注意事项。
2.实验时按正常操作方法和工艺参数,保证操作的准确性和实验成功率。
3.实验后需认真整理实验数据,撰写实验报告。
3.2 实验报告要求1.实验报告应清晰准确地展现实验目的、原理、实验流程和数据处理过程。
2.实验报告应具有系统性和科学性。
3.实验报告应具有合理的结论和推论,并对实验结果进行合理的分析和评价。
四、课程设计参考书目1.《精密加工技术》(第3版), 刘宗英等著, 机械工业出版社, 20182.《超精密加工技术概论》, 郁勇新著, 科学出版社, 20093.《现代制造工艺技术》(第5版), 翁启惠等著, 机械工业出版社,2014五、课程设计总结通过学习和研究精密和超精密加工技术,并进行实验操作,可以使学生加深对于精密加工技术的了解和掌握,提高技能水平,同时也对于现代制造工艺技术有更深刻的理解和认识。
第5章 精密、超精密加工技术

• 和表面粗糙度的检验,而且要测量加工设备 的精度和基础零部件的精度。 • 高精度的尺寸和几何形状可采用分辨率为 0.1~0.01µ m,的电子测微计、分辨率为 0.01~0.001µ m的电感测微仪或电容测微仪来 测量。圆度还可以用精度为0.01µ m的圆度仪 来测量。
加工设备必须具有高精度的主轴系统、进给 系统(包括微位移装臵),现在的超精密车 床,其主轴回转精度可达0.02µ m,导轨直线 度可达1000000:0.025,定位精度可达 0.013µ m,进给分辨率可达0.005µ m。其回转 零件应进行精密的动平衡。
• 2)高刚度
• 包括静刚度和动刚度,不仅要注意零件本身
• 精密和超精密磨料加工是利用细粒度的磨粒 和微粉主要对黑色金属、硬脆材料等进行加 工,按具体地加工方法分为精密和超精密磨 削,加工精度可达5~0.5µ m,表面粗糙度 Ra0.05~0.008µ m);精密和超精密研磨(加 工精度可达10~0.1µ m,表面粗糙度 Ra0.01~0.008µ m);
合金等刀具进行精密和超精密切削,这些刀
具材料的切削效果不如金刚石,但能加工黑
色金属。对黑色金属等硬脆材料的精密加工
和超精密加工,一般多采用磨削、研磨、抛
光等方法。
• 精密和超精密磨削时,通常采用粒度240#~W7
或更细的白刚玉或铬刚玉磨料和树脂结合剂
制成的紧密组织砂轮,经金刚石精细修整后
• 进行加工。
• 出现了精密电火花加工、精密电解加工、精
密超声波加工、分子束加工、电子束加工、
离子束加工、原子束加工、激光加工、微波
加工、等离子体加工、光刻、电铸及变形加
工等。
• 4.复合加工
• 复合加工是将几种加工方法叠合在一起,发 挥各种加工方法的长处,达到高质量(加工
精密加工中的测量技术

r()Ci sini(i) i2
31
圆度误差的图形表示
采用极坐标记录的圆度仪测的圆度误差曲线。
32
圆度误差的评定
33
二、圆度仪及其测量精度分析 圆度仪的工作原理及类型
2种方式。转轴式适用于测量大型工件,转 轴式测量时,工件不动,传感器测头绕主轴 轴线作旋转运动,测头在空间的运动轨迹形 成一理想圆。工件实际轮廓与此理想圆连续 进行比较,其半径变化由传感器测出,经电 路处理后,由记录器描绘出被测实际轮廓的 图形,或由计算机算出测量结果。转台式与 之相反,工件回转,而测头架不动。不易测 圆柱度、同轴度、平面度和垂直度。 TALYROND3 、 TALYROND73 、 HYQ-
13
3)光轴法
测微准直望远镜或自准直仪发出的光线为理想直线,测出被测直线相 对于该理想直线的偏差值,经数据处理求出被测线的直线度误差。
测量步骤: 1)将被测线两端点连线调整到与光轴测量
基线大致平行; 2)若被测线为平面线,则xi代表被测线长
度方向的坐标值, yi为被测线相对于测量基 线的偏差值。
若被测线移动瞄准靶2,同时记录各点示值 (yi)。再经数据处理求出直线度误差值。
2π为周期,因此可以用傅氏级数表示:
()r0Cisini(i) i1
由上式还可看出:圆形零件横截面的实际轮廓是由一半径为r0的圆 和若干个不同次数谐波波形所迭加而成。其中常数项r0为平均圆半径, 一次谐波表示偏心的影响,而反映表面粗糙度和表面波度的高次谐波 也不属于圆度误差,所以圆度误差可用下式表示:
19
90度角尺第一位置测得导轨的不垂直误差-1.25μm,90度角 尺翻转后的不垂直误差+0.25 μm。不垂直误差为Δ=0.5[-1.25(+0.25)]=-0.75 μm。
精密和超精密加工
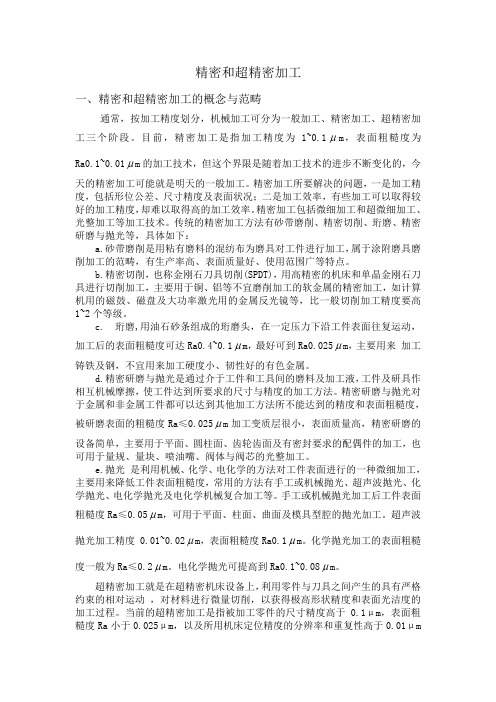
精密和超精密加工一、精密和超精密加工的概念与范畴通常,按加工精度划分,机械加工可分为一般加工、精密加工、超精密加工三个阶段。
目前,精密加工是指加工精度为1~0.1μm,表面粗糙度为Ra0.1~0.01μm的加工技术,但这个界限是随着加工技术的进步不断变化的,今天的精密加工可能就是明天的一般加工。
精密加工所要解决的问题,一是加工精度,包括形位公差、尺寸精度及表面状况;二是加工效率,有些加工可以取得较好的加工精度,却难以取得高的加工效率。
精密加工包括微细加工和超微细加工、光整加工等加工技术。
传统的精密加工方法有砂带磨削、精密切削、珩磨、精密研磨与抛光等,具体如下:a.砂带磨削是用粘有磨料的混纺布为磨具对工件进行加工,属于涂附磨具磨削加工的范畴,有生产率高、表面质量好、使用范围广等特点。
b.精密切削,也称金刚石刀具切削(SPDT),用高精密的机床和单晶金刚石刀具进行切削加工,主要用于铜、铝等不宜磨削加工的软金属的精密加工,如计算机用的磁鼓、磁盘及大功率激光用的金属反光镜等,比一般切削加工精度要高1~2个等级。
c. 珩磨,用油石砂条组成的珩磨头,在一定压力下沿工件表面往复运动,加工后的表面粗糙度可达Ra0.4~0.1μm,最好可到Ra0.025μm,主要用来加工铸铁及钢,不宜用来加工硬度小、韧性好的有色金属。
d.精密研磨与抛光是通过介于工件和工具间的磨料及加工液,工件及研具作相互机械摩擦,使工件达到所要求的尺寸与精度的加工方法。
精密研磨与抛光对于金属和非金属工件都可以达到其他加工方法所不能达到的精度和表面粗糙度,被研磨表面的粗糙度Ra≤0.025μm加工变质层很小,表面质量高,精密研磨的设备简单,主要用于平面、圆柱面、齿轮齿面及有密封要求的配偶件的加工,也可用于量规、量块、喷油嘴、阀体与阀芯的光整加工。
e.抛光是利用机械、化学、电化学的方法对工件表面进行的一种微细加工,主要用来降低工件表面粗糙度,常用的方法有手工或机械抛光、超声波抛光、化学抛光、电化学抛光及电化学机械复合加工等。
精密机械加工中的测量与检测技术
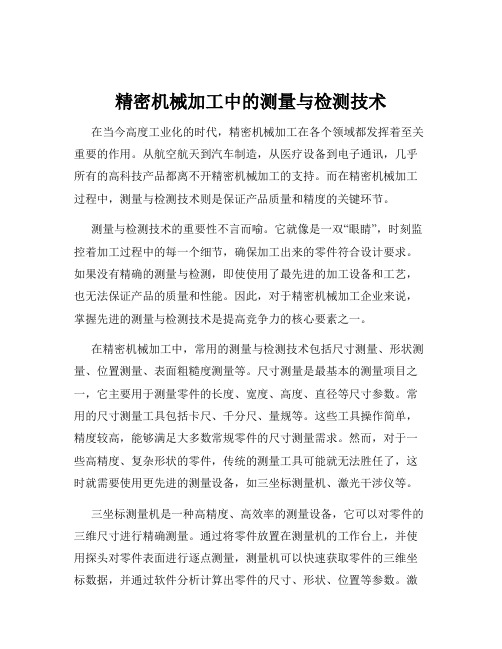
精密机械加工中的测量与检测技术在当今高度工业化的时代,精密机械加工在各个领域都发挥着至关重要的作用。
从航空航天到汽车制造,从医疗设备到电子通讯,几乎所有的高科技产品都离不开精密机械加工的支持。
而在精密机械加工过程中,测量与检测技术则是保证产品质量和精度的关键环节。
测量与检测技术的重要性不言而喻。
它就像是一双“眼睛”,时刻监控着加工过程中的每一个细节,确保加工出来的零件符合设计要求。
如果没有精确的测量与检测,即使使用了最先进的加工设备和工艺,也无法保证产品的质量和性能。
因此,对于精密机械加工企业来说,掌握先进的测量与检测技术是提高竞争力的核心要素之一。
在精密机械加工中,常用的测量与检测技术包括尺寸测量、形状测量、位置测量、表面粗糙度测量等。
尺寸测量是最基本的测量项目之一,它主要用于测量零件的长度、宽度、高度、直径等尺寸参数。
常用的尺寸测量工具包括卡尺、千分尺、量规等。
这些工具操作简单,精度较高,能够满足大多数常规零件的尺寸测量需求。
然而,对于一些高精度、复杂形状的零件,传统的测量工具可能就无法胜任了,这时就需要使用更先进的测量设备,如三坐标测量机、激光干涉仪等。
三坐标测量机是一种高精度、高效率的测量设备,它可以对零件的三维尺寸进行精确测量。
通过将零件放置在测量机的工作台上,并使用探头对零件表面进行逐点测量,测量机可以快速获取零件的三维坐标数据,并通过软件分析计算出零件的尺寸、形状、位置等参数。
激光干涉仪则是一种基于激光干涉原理的测量设备,它可以用于测量零件的直线度、平面度、垂直度等几何精度。
激光干涉仪具有测量精度高、测量范围大等优点,在精密机械加工中得到了广泛的应用。
形状测量也是精密机械加工中非常重要的一个环节。
零件的形状精度直接影响着其装配性能和工作性能。
常见的形状测量项目包括圆度、圆柱度、平面度、线轮廓度、面轮廓度等。
圆度测量通常使用圆度仪进行,圆柱度测量可以使用圆柱度仪或三坐标测量机,平面度测量则可以使用平板和千分表、三坐标测量机等设备。
精密和超精密加工技术
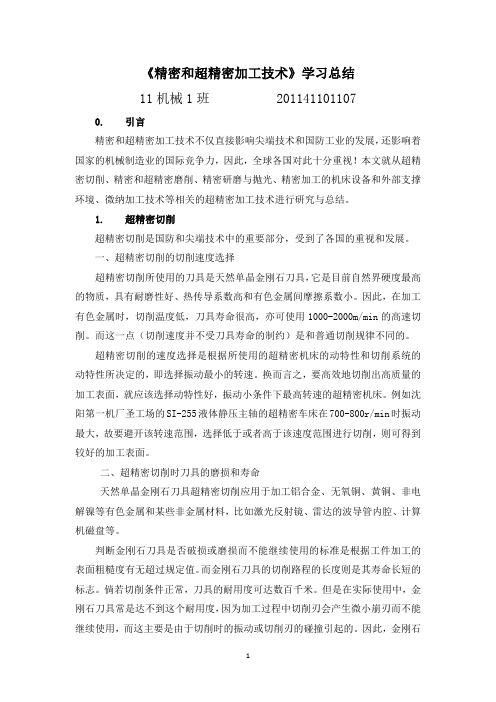
《精密和超精密加工技术》学习总结11机械1班 2011411011070. 引言精密和超精密加工技术不仅直接影响尖端技术和国防工业的发展,还影响着国家的机械制造业的国际竞争力,因此,全球各国对此十分重视!本文就从超精密切削、精密和超精密磨削、精密研磨与抛光、精密加工的机床设备和外部支撑环境、微纳加工技术等相关的超精密加工技术进行研究与总结。
1. 超精密切削超精密切削是国防和尖端技术中的重要部分,受到了各国的重视和发展。
一、超精密切削的切削速度选择超精密切削所使用的刀具是天然单晶金刚石刀具,它是目前自然界硬度最高的物质,具有耐磨性好、热传导系数高和有色金属间摩擦系数小。
因此,在加工有色金属时,切削温度低,刀具寿命很高,亦可使用1000-2000m/min的高速切削。
而这一点(切削速度并不受刀具寿命的制约)是和普通切削规律不同的。
超精密切削的速度选择是根据所使用的超精密机床的动特性和切削系统的动特性所决定的,即选择振动最小的转速。
换而言之,要高效地切削出高质量的加工表面,就应该选择动特性好,振动小条件下最高转速的超精密机床。
例如沈阳第一机厂圣工场的SI-255液体静压主轴的超精密车床在700-800r/min时振动最大,故要避开该转速范围,选择低于或者高于该速度范围进行切削,则可得到较好的加工表面。
二、超精密切削时刀具的磨损和寿命天然单晶金刚石刀具超精密切削应用于加工铝合金、无氧铜、黄铜、非电解镍等有色金属和某些非金属材料,比如激光反射镜、雷达的波导管内腔、计算机磁盘等。
判断金刚石刀具是否破损或磨损而不能继续使用的标准是根据工件加工的表面粗糙度有无超过规定值。
而金刚石刀具的切削路程的长度则是其寿命长短的标志。
倘若切削条件正常,刀具的耐用度可达数百千米。
但是在实际使用中,金刚石刀具常是达不到这个耐用度,因为加工过程中切削刃会产生微小崩刃而不能继续使用,而这主要是由于切削时的振动或切削刃的碰撞引起的。
因此,金刚石刀具只能使用在机床主轴转动非常平稳的高精度机床上,而刀具的维护对机床的要求亦是如此。
超精密加工与检测一体化技术

超精密加工与检测一体化技术一、概述超精密加工与检测一体化技术是一种集合了超精密加工、检测、误差补偿等多项技术于一体的综合性技术。
它在航空航天、光学、微电子等领域具有广泛的应用前景。
本文将从加工方法、检测技术、误差补偿技术、材料特性研究、设备与系统集成、环境控制技术、智能化技术和跨学科技术等八个方面进行阐述。
二、加工方法超精密加工方法主要包括磨削、铣削、车削和激光加工等。
这些方法在超精密加工中各有优缺点,选择合适的加工方法要根据具体零件的材质、形状、尺寸和精度要求来决定。
在加工过程中,需要对温度、压力、切削液等工艺参数进行精确控制,以保证加工精度和表面质量。
三、检测技术超精密加工的检测技术主要包括光学测量、电子测量和激光测量等。
这些检测技术在精度、速度和可靠性等方面都有很高的要求。
在检测过程中,需要对测量环境、测量设备、测量方法和数据处理等方面进行全面考虑,以保证测量结果的准确性和可靠性。
四、误差补偿技术误差补偿技术是超精密加工中一项非常重要的技术,它通过对加工过程中产生的误差进行精确测量和补偿,可以有效提高加工精度和表面质量。
误差补偿技术主要包括硬件补偿和软件补偿两种方式,具体实现方法需要根据实际情况进行选择。
五、材料特性研究超精密加工中,材料特性的研究也是非常重要的一环。
不同材料具有不同的物理和化学性质,加工过程中需要对材料的硬度、韧性、热导率等参数进行精确控制,以保证加工质量和效率。
同时,还需要对材料的表面粗糙度、热膨胀系数等进行研究,以实现更加精确的加工和检测。
六、设备与系统集成超精密加工与检测一体化技术需要各种设备和系统的集成,包括加工设备、检测设备、控制系统等。
这些设备和系统的集成需要考虑到设备间的兼容性和通信协议,保证整个系统的高效稳定运行。
同时,还需要对设备和系统的可靠性、可维护性等进行全面考虑,以降低运行成本和维护成本。
精密加工超精密加工和细微加工
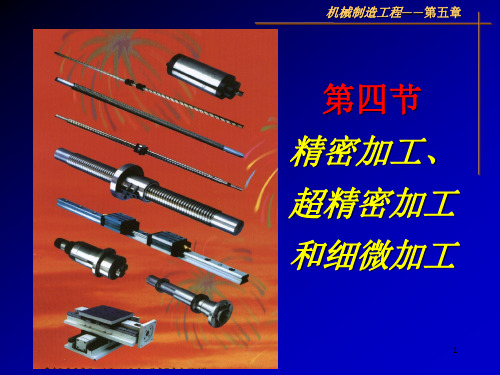
超净:在未经净化的一般环境下,尘 埃数量极大,绝大部分尘埃的直径小 于1µm,也有不少直径在1µm以上甚 至超过10µm的尘埃。这些尘埃如果落 在加工表面上,可能将表面拉伤;如 果落在量具测量表面上,就会造成操 作者或质检员的错误判断。因此,精 密加工和超精密加工必须有与加工相 对应的超净工作环境
则可达0.02µm 金刚石精密切削铜和铝时
v=200~500m/min αp=0.002~0.003mm f=0.01~0.04mm/r。
18
2.精密磨削及金刚石超精密磨削 精密磨削是指加工精度为1~0.1m,
Ra为0.16~0.006m的磨削方法;而 超精密磨削则是指加工精度高于 0.1m,Ra<0.04 ~0.02m的磨削方 法
25
细微加工技术是指制造微小尺寸零 件、部件和装置的加工和装配技术, 属精密、超精密加工的范畴。其工 艺技术包括:精密和超精密的切削 与磨削方法;绝大多数的特种加工 方法;与特种加工有机结合的复合 加工方法等三类
26
常用的细微加工方法及其应用参见 表5-15
电子束曝光光刻加工过程
27
返回
28
制和工艺过程优化等生产自动化技术
11
四、常用的精密加工和超精密加工和细 微加工方法
采用金刚石刀具对工件进行超精密的微 细切削和应用磨料磨具对工件进行珩磨、 研磨、抛光、精密和超精密磨削等
采用电化学加工、三束加工、超声波加 工等特种加工方法及复合加工
微细加工是指制造微小尺寸零件的生产 加工技术
IT5以上)、Ra<0.1µm的加工方法, 如金刚石车削、高精密磨削、研磨、 珩磨、冷压加工等
3
3.超精密加工 指加工精度在0.1µm ~0.01µm、Ra
第五章精密超精密及特种加工技术幻灯片课件

2022/4/12
6
第五章 精密超精密及特种加工技术
关键技术2
② 微/纳加工表面/亚表面完整性的评价与控制 纳 米级加工过程的理论及表层形成机理,微/纳表面 及表层完整性评价理论、指标体系及其控制方法;表 面完整性的控制的工程新方法;不同光学材料与加工 参数对亚表面特征的影响与控制的方法;原子级表面 平坦化加工新原理及方法;超光滑表面加工新技术和 实验方法。
2022/4/12
3
第五章 精密超精密及特种加工技术
超精密加工关键技术
3.在线检测与误差补偿
4.超精密加工的工作环境
超精密加工必须在超稳定的环境下进行。超稳定 环境主要是指恒温、超净和防振三个方面。
2022/4/12
5
Байду номын сангаас 第五章 精密超精密及特种加工技术
关键技术1
① 光学自由曲面制造技术的理论和方法 光学自 由曲面零件高精度机械测量与光学测量新原理, 新方法;大镜面测量方法,工件的高精度定位、 自由曲面的轮廓误差评定、海量数据处理新的数 学工具和新的算法;自由曲面光学表面成形、修 形和抛光新原理和新方法;光学自由曲面超精密 机床关键技术与方法。
2022/4/12
1
第五章 精密超精密及特种加工技术
超精密加工特点
超精密加工时,对刀具的刃磨、砂轮修整和机床调整 均有很高要求。
超精密加工是一门综合性高技术,凡是影响加工精度 和表面质量的因素都要考虑。
超精密加工一般采用计算机控制、在线控制、自适应 控制、误差检测和补偿等自动化技术来保证加工精度 和表面质量。
超精密加工不仅有传统的切削和磨削加工,只有综合 应用各种加工方法,才能得到很高的加工精度和表面 质量。
2022/4/12
精密和超精密加工技术PPT课件

精密和超精密加工技术
1
教材:《精密和超精密加工技术》(第2版) 袁哲俊、王先逵主编 机械工业出版社
➢ 学时:28 ➢ 周二下午5-6节(H514) ➢ 周四上午1-2节(H514)
参考材料: 1、张建华主编《精密与特种加工技术》 2、王先逵编《精密加工技术实用手册》,
8
1.1 发展精密和超精密加工技术的重要性
精密和超精密加工是先进制造技术的基础和关键
作为制造技术的主战场,作为真实产品的实 际制造,必然要靠精密加工和超精密加工技术, 例如,计算机工业的发展不仅要在软件上,还要 在硬件上,即在集成电路芯片上有很强的能力, 应该说,当前,我国集成电路的制造水平约束了 计算机工业的发展。美国制造工程研究者提出的 汽车制造业的“两毫米工程”使汽车质量赶上欧、 日水平,其中的举措都是实实在在的制造技术。
热流动加工(高频电流、热射流、电子束、激光) 液体、气体流动加工(压铸、挤压、喷射、浇铸) 微粒子流动加工
5
精密和超精密加工方法分类(2)
分类 切削加工 磨料加工
特种加工
复合加工
加工方法
等离子体切削 微细切削 微细钻削
微细磨削 研磨 抛光 弹性发射加工 喷射加工
电火花成形加工 电火花切割加工 电解加工 超声波加工 微波加工 电子束加工 粒子束去除加工 激光去除加工 光刻加工
段,通常,按加工精度划分,可将机械加工分为一般 加工、精密加工、超精密加工三个阶段。
➢精密加工:加工精度在0.1~1µm,加工表面粗糙
度在Ra0.02~0.1µm之间的加工方法称为精密加工;
➢超精密加工:加工精度高于0.1µm,加工表面粗糙
精密与超精密加工技术

刀具种类:金刚石刀具; 超精密磨削砂轮
金刚石刀具
1、金刚石刀头的特性: 颜色:有红色和绿色等多种颜色,其硬
度随颜色而不同; 硬度:显微硬度值比其他物质高许多; 热传导率:在矿物中最大。
金刚石刀具
2、金刚石刀头的制造: 成形:采用研磨加工方法; 研磨方法:用空气轴承的研磨机; 特殊刀头的形状
第三章 先进制造工艺技术
第一节 精密与超精密加工技术
一、 精密与超精密加工技术概述
1、精密加工与超精密加工定义
精密加工是指加工精度在0.1~lμm之间, 表面粗糙度Ra在0.lμm以下(称微米加工)
超精密加工的加工精度在0.lμm以下,表面 粗糙度在0.02μm以下(称为亚微米加工)
2、精密加工与超精密加工的特点
光纤测微仪 更小测量范围的测量仪器:扫描隧道显微
镜 、扫描电子显微镜、原子力显微镜
激光干涉仪
SPA-400 多功能扫描探针显微镜
回顾
一、 精密与超精密加工技术概述 二、 超精密加工方法 三、 超精密加工刀具 四、 超精密加工设备 五、 精密加工环境 六、 超精密加工精度的在线检测及计量测试
五、精密加工环境
超精密加工必须在超稳定的环境下进 行。
超稳定环境:恒温、超净和防振。
六、超精密加工精度的在线检测及计量测试
对加工误差进行在线检测,实时建模与 动态分析预报,再根据预报数据对误差 源进行补偿,从而消除或减少加工误差。
六、超精密加工精度的在线检测及计量测试
大距离的测量仪器:双频激光干涉仪 小距离的测量仪器:电容式、电感式测微仪、
超精密磨削砂轮
超精密磨削质量控制方面的首要因素: 砂轮磨料:应与工件材料选配适当; 磨料粒度:具备形成微刃的粒度; 砂轮硬度:硬度中软。
答案精密加工课后习题—黄

.
.
液压喷砂法,用高压泵打出流量为20L/min、压力为150Pa的冷却液,进入喷嘴的漩涡室时,形成低压,从
边孔中吸入碳化硅或刚玉等磨粒及空气,与冷却液形成混合液,并以高速喷嘴喷射到转动的砂轮上。
晶面。
网面最小单元不同,100是正方形,110为矩形,111为三角形,网面密度100:110:111为1:1.414:2.308
网面距不同:100与110为均匀分布,分别为D/4=0.089mm,sqrt(2)D/4=0.126mm,111为宽窄交替宽为
sqrt(3)D/4=0.154mm,窄为sqrt(3)D/12=0.1051mm
光刃的长度对表面加工质量效果不大,对刀不易
圆弧刃容易对刀,半径可取R=2~5mm。可加工高质量的超光滑表面,缺点是刀具制造复杂
2-19试述金刚石刀具的前面应选哪个晶面
选用100面,111面硬度高,而微观破损强度并不高,研磨加工困难。
选用100面的原因:
1)100面耐磨性高于110面,刀具使用寿命长
2)100面微观破损强度高于110面,产生崩刃的机会小
解理现象:111面的面网宽面距比100和110都大,最易解理。
好磨难磨方向可用图表示:
.
.
好磨方向
难磨方向
100磨削率:111磨削率:110磨削率=5.8:1:12.8
2-15金刚石晶体有哪些定向方法?
1)人工目测定向2)X射线定向3)激光定向
2-16试述金刚石晶体的激光定向原理和方法。
利用金刚石在不同晶面方向上,晶体结构不同,对激光反射形成的衍射图像不同而进行。
小后面与加工表面间的摩擦
2-10工件材料的晶体方向对切削变形和加工表面质量的影响如何?
- 1、下载文档前请自行甄别文档内容的完整性,平台不提供额外的编辑、内容补充、找答案等附加服务。
- 2、"仅部分预览"的文档,不可在线预览部分如存在完整性等问题,可反馈申请退款(可完整预览的文档不适用该条件!)。
- 3、如文档侵犯您的权益,请联系客服反馈,我们会尽快为您处理(人工客服工作时间:9:00-18:30)。
第3节 直线度、平面度和垂直度的测量
一、直线度的测量
1.线差法
线差法的实质是:用模拟法建立 理想直线,然后把被测实际线上 各被测点与理想直线上相应的点 相比较,以确定实际线各点的偏 差值,最后通过数据处理求出直 线度误差值。
1)干涉法
对于小尺寸精密表面的直线度误差。把 平晶(光学玻璃或石英玻璃)置于被测表 面上,在单色光的照射下,两者之间形 成等厚干涉条纹,然后读出条纹弯曲度 a及相邻两条纹的间距b值,被测表面的 直线度误差为 a 。
2018/6/30
第2节 长度尺寸测量
三、工厂自己专用的长度基准
美国穆尔公司经过实践和反复研究,采用圆 柱端面规作为长度基准。外圆柱面可磨到很高 圆柱度,水平放在V形支架内,可旋转以校验 端面和外圆柱面的垂直度,容易达到两端面的 高度平行。
既圆柱端面规后又制成步距规,英制的步距 规每一步距的增量为1in(全长18和16in),公 制的步距规每一步距的增量为30mm(全长 480mm)。全长步距的误差不超过0.05µ m。
条纹向外弯,表面是凸的,反之,则表 2018/6/30 面是凹的。
b
2
第3节 直线度、平面度和垂直度的测量
1)干涉法
用平晶测平尺的直线度
对于较长的研磨表面,如研磨平尺,可采用圆形平晶 进行分段测量,即所谓3点连环干涉法测量。若被测平尺 长度为200mm,则可选用Φ100mm的平晶,将平尺分成4段 进行测量,每次测量以两端点连线为准,测出中间的偏差。 测完一次,平晶向前移动50mm(等于平晶的半径)。然后 通过数据处理,得出平尺的直线度误差。
第5章 精密加工中的测量技术
5.1 精密测量技术概述 5.2 测量基准 5.3 直线度、平面度和垂直的测量 5.6 激光测量 5.7 自由曲面的测量
2018/6/30
第1节 精密测量技术概述
一、精密测量的意义
精密测量技术是机械工业发展的基础和先决条件之一。由于 有了千分尺类量具,使加工精度达到了0.01mm,有了测微比较 仪,使加工精度达到了1µm左右;有了圆度仪等精密测量一起, 使加工精度达到了0.1µm;有了激光干涉仪,使加工精度达到了 0.01µm。 目前在基础工业的某些领域,精密测量已成为不可分割的重 要组成部分。在电子工业部门,精密测量技术也被提到从未有 过的高度。例如制造超大规模集成电路,目前半导体工艺的典 型线宽为0.25µm,正向0.18µm过渡,2009年的预测线宽是 0.07µm。此外,在高纯度单晶硅的晶格参数测量中,以及对生 物细胞、空气污染微粒、石油纤维、纳米材料等基础研究中, 无不需要精密测量技术。
第2节 长度尺寸测量
2.测量平台的支承
大型测量平台常采用多 点支承法。如图,有 9 个受力支承点,实际上 仍是采用三点支承一平 面的原理。采用该种方 法各支撑点间距离缩小, 平台受力变形减小,测 量精度提高。
3.测量平台的本身的精度检验
常用三块平台轮流对研,找出凸起进行刮研,直到接触斑点分布均匀。对高 精度测量平台用电子水平仪、自准直光管或双频激光干涉仪,测出平台的水平 倾角,经过数据处理,可得到平台各处不平面度误差的具体数值。
三、量具和量仪材料的选择 1.根据材料热膨胀系数选择 2.根据材料的稳定性和耐磨性选择
(过去量具常用淬火轴承钢GCr15,有较高的硬度和耐磨 性,但该材料的淬火马氏体中有残留奥氏体,长期使用会 因残生相变使体积和尺寸变化,每年每100mm约为0.02µm, 尺寸稳定性差;近年很多量具改用氮化钢(38CrMoAl)制 2018/6/30 造)
1983年11月第 17届国际计量大会上,批准了米的最 新定义。 新定义的内容:米是光在真空中在 1/299 792 458 s的时间间隔内所行走的路程长度。
2018/6/30
第2节 长度基准
二、量块的检定
量块是由两个平行的测量面之间的距离来确 定其工作长度的高精度量具,其长度为计量器 具的长度标准。按JJG2056- 1990《长度计量器 具(量块部分)检定系统》的规定,量块分为 00、0、K、1、2、3六级。我国对各类量块的检 定按JJG146-1994进行。 为了使用上的需要常将各级精度的量块进行 检定,得到量块的实际长度,将检定量块长度 实际值的测量极限误差作为误差处理。
第2节 测量基准
一、长度基准和米定义 米制是18世纪法国最早提出的,“以经过巴黎的地 球子午线自北极至赤道这一段弧长的一千万分之一为 一米”。1880年国际计量局又制作了 30多根铂铱合金 的高精度米尺——国际米原器。
1960 年 10 月 14 日在巴黎通过用氦 Kr86 在真空中的波 长作为长度基准:1m=1650763.73 * Kr86的波长。
2018/6/30
第2节 长度尺寸测量
四、平台---测量基准
1.平台的选择 1)平台精度等级 测量平台采用00或0级,生产中使用的平台的测量表面多数为 矩形,长宽比约为 4 : 3 ,高精度的平台采用正方形台面,平 面度达到0.6µ m。 2)平台结构 过去采用平板下加加强筋,有三个支承点架在底架上,刚度 不高。现在多数采用箱式结构,扁平的箱中有加强筋支承, 刚度高。 3)测量平台的材料 铸铁:耐磨性,短期稳定性,受潮生锈但不变形,碰撞后表 面会出毛刺; 花岗岩:耐磨性,长期稳定性,受潮变形但不生锈,碰撞后 表面可能出小坑。 2018/6/30
2018/6/30
第1节 精密测量技术概述
一、精密测量的发展
1.极高精度测量方法的测量仪器的发展
(用双频激光测量系统和X射线干涉仪测量长度能达到0.1nm, 用扫描隧道显微镜和原子力显微镜测量表面微观形貌可达 0.1nm,精密测角仪可达0.01")
2.精密在线自动测量技术的发展
(新的三坐标测量机都有精密数控系统,可自动完成复杂零件 的全部测量)
3.测量数据的自动采集处理技术的发展
(很多测量仪器都具备数据处理软件,可将复杂的测量结果数 据处理后显示并打印出来)
2018/6/30
第1节 精密测量技术概述
二、精密测量的环境条件 1.恒温条件 2.隔振条件 3.气压、自重、运动加速度和其他环境条件
(100mm长的刚棒垂直放置,由于自重会使材料产生压缩 变形,长度约缩短0.002µm)