精密加工和超精密加工
精密超精密加工技术

精密超精密加工技术精密及超精密加工对尖端技术的发展起着十分重要的作用。
当今各主要工业化国家都投入了巨大的人力物力,来发展精密及超精密加工技术,它已经成为现代制造技术的重要发展方向之一。
本节将对精密、超精密加工和细微加工的概念、基本方法、特点和应用作一般性介绍。
一、精密加工和超精密加工的界定精密和超精密加工主要是根据加工精度和表面质量两项指标来划分的。
这种划分是相对的,随着生产技术的不断发展,其划分界限也将逐渐向前推移。
1.一般加工一般加工是指加工精度在10µm左右(IT5~IT7)、表面粗糙度为R a0.2µm~0.8µm的加工方法,如车、铣、刨、磨、电解加工等。
适用于汽车制造、拖拉机制造、模具制造和机床制造等。
2.精密加工精密加工是指精度在10µm~0.1µm(IT5或IT5以上)、表面粗糙度值小于R a0.1µm的加工方法,如金刚石车削、高精密磨削、研磨、珩磨、冷压加工等。
用于精密机床、精密测量仪器等制造业中的关键零件,如精密丝杠、精密齿轮、精密导轨、微型精密轴承、宝石等的加工。
3.超精密加工超精密加工一般指工件尺寸公差为0.1µm~0.01µm数量级、表面粗糙度R a 为0.001µm数量级的加工方法。
如金刚石精密切削、超精密磨料加工、电子束加工、离子束加工等,用于精密组件、大规模和超大规模集成电路及计量标准组件制造等方面。
二、实现精密和超精密加工的条件精密和超精密加工技术是一项内容极为广泛的制造技术系统工程,它涉及到超微量切除技术、高稳定性和高净化的工作环境、设备系统、工具条件、工件状况、计量技术、工况检测及质量控制等。
其中的任一因素对精密和超精密加工的加工精度和表面质量,都将产生直接或间接的不同程度的影响。
1.加工环境精密加工和超精密加工必须具有超稳定的加工环境。
因为加工环境的极微小变化都可能影响加工精度。
精密加工超精密加工和细微加工课件

➢超精密磨床的技术要求
很高的主轴回转精度和很高的导轨直线 度,以保证工件的几何形状精度;常常 采用大理石导轨增加热稳定性
应配备有微进给机构,以保证工件尺寸 精度以及砂轮修整时的微刃性和等高性
工作台导轨低速运动的平稳性要好,不 产生爬行、振动, 以保证砂轮修整质量 和稳定的磨削过程
精密加工超精密加工和细微加工课 件
IT5以上)、Ra<0.1µm的加工方法, 如金刚石车削、高精密磨削、研磨、 珩磨、冷压加工等
精密加工超精密加工和细微加工课 件
3.超精密加工 指加工精度在0.1µm ~0.01µm、Ra
为0.01µm的加工方法,如金刚石 精密切削、超精密磨料加工、电子 束加工、离子束加工等
精密加工超精密加工和细微加工课 件
防振:机床振动对精密加工和超精密 加工有很大的危害,为了提高加工系 统的动态稳定性,除了在机床设计和 制造上采取各种措施,还必须用隔振 系统来保证机床不受或少受外界振动 的影响。应能有效地隔离频率为 6Hz~9Hz、振幅为0.1µm~0.2µm的外 来振动
精密加工超精密加工和细微加工课 件
超净:在未经净化的一般环境下,尘 埃数量极大
切削时,其ap<lm,刀具可能处于工件 晶粒内部切削状态。切削力要超过分子 或原子间巨大的结合力,从而使刀刃承 受很大的剪切应力,并产生很大热量, 造成刀刃的高应力、高温的工作状态
金刚石精密切削的关键问题是如何均匀、 稳定地切除如此微薄的金属层
精密加工超精密加工和细微加工课 件
一、精密加工和超精密加工的界定 1.一般加工
指加工精度在10µm左右(IT5~IT7)、 表面粗糙度为Ra0.2µm~0.8µm的加工方 法,如车、铣、刨、磨、电解加工等。 适用于汽车制造、拖拉机制造、模具制 造和机床制造等
精密和超精密加工
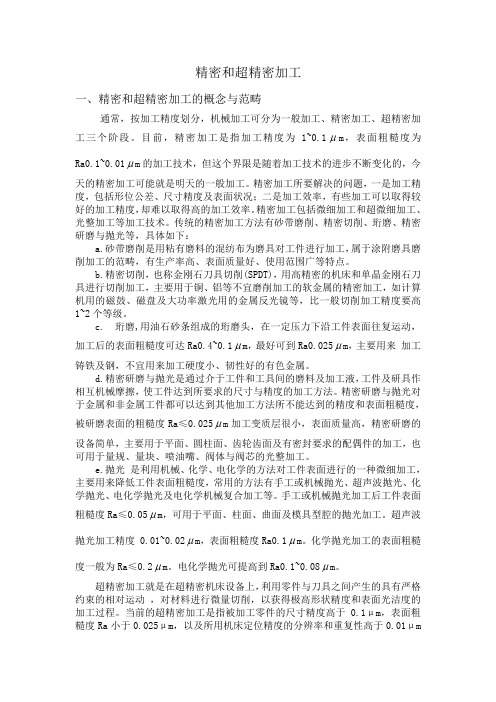
精密和超精密加工一、精密和超精密加工的概念与范畴通常,按加工精度划分,机械加工可分为一般加工、精密加工、超精密加工三个阶段。
目前,精密加工是指加工精度为1~0.1μm,表面粗糙度为Ra0.1~0.01μm的加工技术,但这个界限是随着加工技术的进步不断变化的,今天的精密加工可能就是明天的一般加工。
精密加工所要解决的问题,一是加工精度,包括形位公差、尺寸精度及表面状况;二是加工效率,有些加工可以取得较好的加工精度,却难以取得高的加工效率。
精密加工包括微细加工和超微细加工、光整加工等加工技术。
传统的精密加工方法有砂带磨削、精密切削、珩磨、精密研磨与抛光等,具体如下:a.砂带磨削是用粘有磨料的混纺布为磨具对工件进行加工,属于涂附磨具磨削加工的范畴,有生产率高、表面质量好、使用范围广等特点。
b.精密切削,也称金刚石刀具切削(SPDT),用高精密的机床和单晶金刚石刀具进行切削加工,主要用于铜、铝等不宜磨削加工的软金属的精密加工,如计算机用的磁鼓、磁盘及大功率激光用的金属反光镜等,比一般切削加工精度要高1~2个等级。
c. 珩磨,用油石砂条组成的珩磨头,在一定压力下沿工件表面往复运动,加工后的表面粗糙度可达Ra0.4~0.1μm,最好可到Ra0.025μm,主要用来加工铸铁及钢,不宜用来加工硬度小、韧性好的有色金属。
d.精密研磨与抛光是通过介于工件和工具间的磨料及加工液,工件及研具作相互机械摩擦,使工件达到所要求的尺寸与精度的加工方法。
精密研磨与抛光对于金属和非金属工件都可以达到其他加工方法所不能达到的精度和表面粗糙度,被研磨表面的粗糙度Ra≤0.025μm加工变质层很小,表面质量高,精密研磨的设备简单,主要用于平面、圆柱面、齿轮齿面及有密封要求的配偶件的加工,也可用于量规、量块、喷油嘴、阀体与阀芯的光整加工。
e.抛光是利用机械、化学、电化学的方法对工件表面进行的一种微细加工,主要用来降低工件表面粗糙度,常用的方法有手工或机械抛光、超声波抛光、化学抛光、电化学抛光及电化学机械复合加工等。
精密和超精密加工

1、精密和超精密加工的三大领域:超精密切削、精密和超精密磨削研磨、精密特种加工。
2、金刚石刀具进行超精密切削时,适合加工铝合金、无氧铜、黄铜、非电解镍等有色金属和某些非金属材料。
3、最硬的刀具是天然单晶金刚石刀具。
金刚石刀具的的寿命用切削路程的长度计算。
4、超精密切削实际能达到的最小切削厚度和金刚石刀具的锋锐度、使用的超精密机床的性能状态、切削时的环境条件等直接相关。
5、影响超精密切削极限最小切削厚度最大的参数是切削刃钝圆半径r n。
6、金刚石晶体有3个主要晶面,即(100)、(110)、(111),(100)晶面的摩擦因数曲线有4个波峰和波谷,(110)晶面有2个波峰和波谷,(111)晶面有3个波峰和波谷。
以摩擦因数低的波谷比较,(100)晶面的摩擦因数最低,(111)晶面次之,(110)晶面最高。
比较同一晶面的摩擦因数值变化,(100)晶面的摩擦因数差别最大,(110)次之,(111)晶面最小。
7、实际金刚石晶体的(111)晶面的硬度和耐磨性最高。
推荐金刚石刀具的前面应选(100)晶面。
8、(110)晶面的磨削率最高,最容易磨;(100)晶面的磨削率次之,(111)晶面磨削率最低,最不容易磨。
9、金刚石的3个主要晶面磨削(研磨)方向不同时,磨削率相差很大。
现在习惯上把高磨削率方向称为“好磨方向”,把低磨削率方向称为“难磨方向”。
10、金刚石磨损本质是微观解离的积累;破损主要产生于(111)晶面的解离。
11、金刚石晶体定向方法:人工目测定向、X射线晶体定向、激光晶体定向。
其中激光晶体定向最常用。
12、金刚石的固定方法有:机械夹固、用粉末冶金法固定、使用粘结或钎焊固定。
13、精密磨削机理包括:微刃的微切削作用,微刃的等高切削作用,微刃的滑挤、摩擦、抛光作用。
14、超硬磨料砂轮修整的方法有:车削法、磨削法、滚压挤轧法、喷射法、电加工法、超声波振动修整法。
电解在线修锐法(ELID—electrolytic in—process dressing),原理是利用电化学腐蚀作用蚀出金属结合剂。
常用精密加工和超精密加工方法
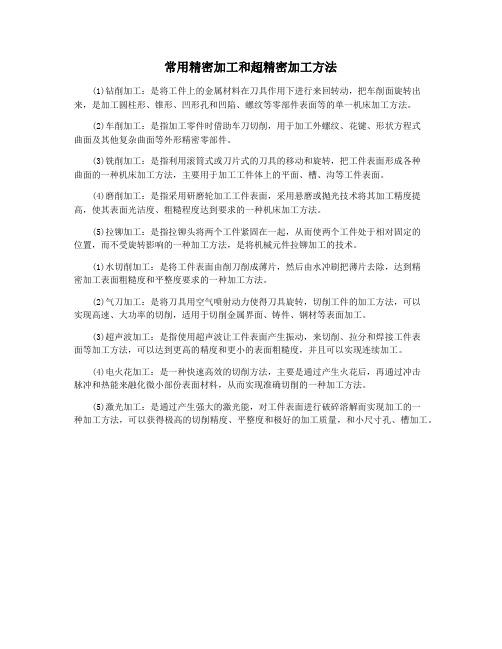
常用精密加工和超精密加工方法(1)钻削加工:是将工件上的金属材料在刀具作用下进行来回转动,把车削面旋转出来,是加工圆柱形、锥形、凹形孔和凹陷、螺纹等零部件表面等的单一机床加工方法。
(2)车削加工:是指加工零件时借助车刀切削,用于加工外螺纹、花键、形状方程式曲面及其他复杂曲面等外形精密零部件。
(3)铣削加工:是指利用滚筒式或刀片式的刀具的移动和旋转,把工件表面形成各种曲面的一种机床加工方法,主要用于加工工件体上的平面、槽、沟等工件表面。
(4)磨削加工:是指采用研磨轮加工工件表面,采用悬磨或抛光技术将其加工精度提高,使其表面光洁度、粗糙程度达到要求的一种机床加工方法。
(5)拉铆加工:是指拉铆头将两个工件紧固在一起,从而使两个工件处于相对固定的位置,而不受旋转影响的一种加工方法,是将机械元件拉铆加工的技术。
(1)水切削加工:是将工件表面由削刀削成薄片,然后由水冲刷把薄片去除,达到精密加工表面粗糙度和平整度要求的一种加工方法。
(2)气刀加工:是将刀具用空气喷射动力使得刀具旋转,切削工件的加工方法,可以实现高速、大功率的切削,适用于切削金属界面、铸件、钢材等表面加工。
(3)超声波加工:是指使用超声波让工件表面产生振动,来切削、拉分和焊接工件表面等加工方法,可以达到更高的精度和更小的表面粗糙度,并且可以实现连续加工。
(4)电火花加工:是一种快速高效的切削方法,主要是通过产生火花后,再通过冲击脉冲和热能来融化微小部份表面材料,从而实现准确切削的一种加工方法。
(5)激光加工:是通过产生强大的激光能,对工件表面进行破碎溶解而实现加工的一种加工方法,可以获得极高的切削精度、平整度和极好的加工质量,和小尺寸孔、槽加工。
第七讲精密加工和超精密加工

工艺过程的优化
五、游离磨料的高效加工
(一)超声研磨工艺
• 超声研磨是一种采用游离磨料(研磨膏或研磨液)进 行切削的加工方法。磨料通过研磨工具的振动产生切 削功能,从而把研磨头(工具)的形状传递到工件 上。 • 超声研磨正是利用脆性材料的这一特点。有目的有控 制地促进材料表层的断裂和切屑的形成。
二、金刚石车削技术及其应用
1. 金刚石车床的技术关键
• 除了必须满足很高的运动平稳性外,还必须具有很高 的定位精度和重复精度。镜面铣削平面时,对主轴只 需很高的轴向运动精度,而对径向运动精度要求较 低。金刚石车床则须兼备很高的轴向和径向运动精 度,才能减少对工件的形状精度和表面粗糙度的影 响。 • 目前市场上提供的金刚石车床的主轴大多采用气体静 压轴承,轴向和径向的运动误差在50nm以下,个别主 轴的运动误差已低于25nm。金刚石车床的滑台在90年 代以前绝大部分采用气体静压支承,荷兰的Hembrug 公司则采用液体静压支承。进入90年代以来,美国的 Pneumo公司(现已与Precitech公司合并)的主要产品 Nanoform600和250也采用了具有高刚性、高阻尼和高
(二)超声研磨加工玻璃
• 在玻璃上钻孔时,超声加工已经可以与金刚石钻削竞 争,优化后的超声钻孔已经达到金刚石钻削时的材料 切除速度。根据孔径和孔深的不同,超声钻孔时的进 钻速度可也达到20~40mm/min。 • 用金刚石钻削玻璃上的孔时,需要从两面进刀,以免 钻透时出现玻璃崩裂,采用超声钻孔时,则可从一侧 直接钻通,工具出口时不会出现玻璃的崩裂。从而可 以省去金刚石钻孔时的校正和倒角等加工工序。 • 在玻璃上钻小孔时,超声研磨的作用变得更为重要。 普通的金刚石钻孔,最小孔径大约在2mm左右。超声 钻孔时的最小孔径几乎没有任何限制,目前在实验室 中进行的实验表明,用超声研磨可在3mm厚的玻璃上 钻出直径为0.5~1.0mm的小孔
精密和超精密加工技术

1、通常将加工精度在0.1-1um、加工表面粗糙度R在0.02-0.1um之间的加工方法称为精密加工。
而将加工精度高于0.1um、加工表面粗糙度R小于0.01um的加工方法称为超精密加工。
2、提高加工精度的原因:提高制造精度后可提高产品的性能和质量,提高其稳定性和可靠性;促进产品的小型化;增强零件的互换性,提高装配生产率,并促进自动化装配。
3、精密和超精密加工目前包含三个领域:超精密切削;精密和超精密磨削研磨‘精密特种加工。
4、金刚石刀具的超精密切削加工技术,主要应用于两个方面:单件的大型超精密零件的切削加工和大量生产的中小型零件的超精密切削加工技术。
5、金刚石刀具有两个比较重要的问题:晶面的选择;切削刃钝圆半径。
6、超稳定环境条件主要是指恒温、防振、超净和恒湿五个方面的条件。
7、我国应开展超精密加工技术基础的研究,其主要内容包括以下四个方面:1)超精密切削、磨削的基本理论和工艺。
2)超精密设备的关键技术、精度、动特性和热稳定性。
3)超精密加工的精度检测、在线检测和误差补偿。
4)超精密加工的环境条件。
5)超精密加工的材料。
8、超精密切削实际选择的切削速度,经常是根据所使用的超精密机床的动特性和切削系统的动特性选取,即选择振动最小的转速。
9、超精密切削实际能达到的最小切削厚度和金刚石刀具的锋锐度、使用的超精密机床的性能状态、切削时的环境等都直接有关。
10、为实现超精密切削,刀具应具有如下性能:1)极高的硬度、极高的耐磨性和极高的弹性模量,以保证刀具有很长的寿命和很高的尺寸耐用度。
2)切削刃钝圆能磨得极其锋锐,切削刃钝圆半径r值极小,能实现超薄切削厚度。
3)切削刃无缺陷,切削时刃形将复印在加工表面上,能得到超光滑的镜面。
4)和工件材料的抗粘结性好、化学亲和性小、摩擦因素低,能得到极好的加工表面完整性。
11、SPDT——金刚石刀具切削和超精密切削。
12、晶体受到定向的机械力作用时,可以沿平行于某个平面平整地劈开的现象称为解理现象。
精密和超精密加工代表了加工精度发展的不同阶段

1、精密和超精密加工代表了加工精度发展的不同阶段,通常,按加工精度划分,可将机械加工分为一般加工、精密加工、超精密加工三个阶段2、什么叫精密加工?加工精度在0.1~1µm,加工表面粗糙度在Ra0.02~0.1µm之间的加工方法称为精密加工。
3、什么叫超精密加工?加工精度高于0.1µm,加工表面粗糙度小于Ra0.01µm之间的加工方法称为超精密加工。
4、以下哪些是精密和超精密加工的分类?A.去除加工B.结合加工;C.变形加工;D.切削加工;E.磨粒加工F.特种加工;G.复合加工;5、影响精密与超精密加工的因素有哪些?加工机理、被加工材料、加工设备及其基础元部件、加工工具、检测与误差补偿、工作环境等。
6、我国今后发展精密与超精密加工技术的重点研究内容包括什么?(1)超精密加工的加工机理;(2)超精密加工设备制造技术;(3)超精密加工刀具、磨具及刃磨技术;(4)精密测量技术及误差补偿技术;(5)超精密加工工作环境条件。
7、举例说明超精密切削的应用范围有哪些?陀螺仪、激光反射镜、天文望远镜的反射镜、红外反射镜和红外透镜、雷达的波导管内腔、计算机磁盘、激光打印机的多面棱镜、录像机的磁头、复印机的硒鼓、菲尼尔透镜等由有色金属和非金属材料制成的零件。
8、超精密切削速度是如何选择的?超精密切削实际速度的选择根据所使用的超精密机床的动特性和切削系统的动特性选取,即选择振动最小的转速。
9、金刚石刀具的尺寸寿命甚高,高速切削时刀具磨损亦甚慢,因此刀具是否磨损以加工表面质量是否下降超差为依据,切削速度并不受刀具寿命的制约。
10、单晶金刚石刀具破损或磨损不能继续使用的标志是?加工表面粗糙度超过规定值。
11、简述超精密切削时切削参数对积屑瘤生成的影响?见书本P13-14。
12、简述超精密切削时积屑瘤对切削力和加工表面粗糙度的影响?见书本P14-15。
13、分别用1-2句话总结切削速度、进给量、修光刃、切削刃、背吃刀量变化对加工表面质量的影响?在常用超精密切削速度范围内,切削速度对加工表面粗糙度基本无影响;带有修光刃的刀具,当f<0.02mm/r时,进给量再减小对表面粗糙度影响不大;修光刃的长度过长,对加工表面粗糙度影响不大。
第5章 精密、超精密加工技术

• 和表面粗糙度的检验,而且要测量加工设备 的精度和基础零部件的精度。 • 高精度的尺寸和几何形状可采用分辨率为 0.1~0.01µ m,的电子测微计、分辨率为 0.01~0.001µ m的电感测微仪或电容测微仪来 测量。圆度还可以用精度为0.01µ m的圆度仪 来测量。
加工设备必须具有高精度的主轴系统、进给 系统(包括微位移装臵),现在的超精密车 床,其主轴回转精度可达0.02µ m,导轨直线 度可达1000000:0.025,定位精度可达 0.013µ m,进给分辨率可达0.005µ m。其回转 零件应进行精密的动平衡。
• 2)高刚度
• 包括静刚度和动刚度,不仅要注意零件本身
• 精密和超精密磨料加工是利用细粒度的磨粒 和微粉主要对黑色金属、硬脆材料等进行加 工,按具体地加工方法分为精密和超精密磨 削,加工精度可达5~0.5µ m,表面粗糙度 Ra0.05~0.008µ m);精密和超精密研磨(加 工精度可达10~0.1µ m,表面粗糙度 Ra0.01~0.008µ m);
合金等刀具进行精密和超精密切削,这些刀
具材料的切削效果不如金刚石,但能加工黑
色金属。对黑色金属等硬脆材料的精密加工
和超精密加工,一般多采用磨削、研磨、抛
光等方法。
• 精密和超精密磨削时,通常采用粒度240#~W7
或更细的白刚玉或铬刚玉磨料和树脂结合剂
制成的紧密组织砂轮,经金刚石精细修整后
• 进行加工。
• 出现了精密电火花加工、精密电解加工、精
密超声波加工、分子束加工、电子束加工、
离子束加工、原子束加工、激光加工、微波
加工、等离子体加工、光刻、电铸及变形加
工等。
• 4.复合加工
• 复合加工是将几种加工方法叠合在一起,发 挥各种加工方法的长处,达到高质量(加工
《现代制造技术》ppt 第3章 精密加工和超精密加工

度、高外表质量、高寿命的一种高效加工方法。 可有效地提高尺寸精度、形状精度和减小Ra值, 但不能提高孔与其他外表的位置精度。
② 可加工铸铁件、淬硬和不淬硬钢件及青铜 件等,但不宜加工韧性大的有色金属件。
③ 珩磨主要用于孔加工。在孔珩磨加工中, 是以原加工孔中心来进行导向。加工孔径 范围为φ5~ φ500,深径比可达10。
3.1.3 工艺特点
1.精密加工和超精密加工都是以精密元件为 加工对象,与精密元件密切结合而开展起 来的。
2.精密加工和超精密加工不仅要保证很高的 精度和外表质量,同时要求有很高的稳定 性或保持性,不受外界条件变化的干扰, 因此,要注意以下几个方面:
〔1〕工件材料本身的均匀性和性能的一致性,不允 许存在内部或外部的微观缺陷,甚至对材料组织 的纤维化有一定要求,如精密磁盘的铝合金盘基 就不允许有组织纤维化,精密金属球也是一样。
精密切削加工
3.2.1 精密切削加工
精密、超精密切削加工主要是利用立方氮 化硼〔CBN〕、人造〔聚晶〕金刚石和单晶 金刚石刀具进行的切削加工。
3.2.2 精密、超精密切削加工应用实例
尖端产品和现代化武器依赖于超精密加工, 如:
(1)导弹的命中精度,由惯性仪决定,而惯性 仪是超精密加工产品,1Kg重的陀螺转子, 其质量中心偏离其对称轴0.5nm,会引起 100m的射程误差和50m的轨道误差;
3.3.3 精密磨削加工实例
1〕圆柱形镜面磨削加工方法:磨削速度选 V=25~35m/s,粗磨时fr=0.02~0.07mm,精 磨时fr=3~10µm;当用油石研、抛时, V=10~50m/min,材料的去除速度为 0.1µm~1µm/min。超精磨削可到达0.01µm的 圆度和Ra 0.002µm的外表粗糙度。
现代制造技术第3章 精密加工和超精密加工
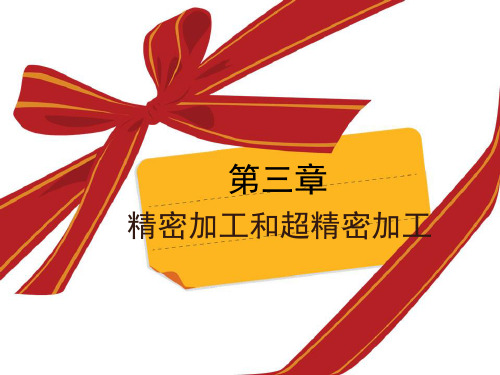
3.6 研磨
3.6.1 研磨 研磨是一种简便可靠的精密加工方法,研 磨后的表面的尺寸误差和几何形状误差, 在研具精度足够高的情况下可以小到0.1~ 0.3,表面粗糙度可达Ra0.04~0.01。在现 代工业中往往采用研磨作为加工最精密和 最光洁的零件的终加工方法。 3.6.2 超精密研磨 超精密研磨是一种加工精度达0.1以下,表 面粗糙度Ra在0.02以下的研磨方法。
3.4.3珩磨的用途 珩磨主要用于加工孔径为5~500毫米或更 大的各种圆柱孔,如缸筒、阀孔、连杆孔 和箱体孔等,孔深与孔径之比可达10,甚 至更大。在一定条件下,珩磨也能加工外 圆、平面、球面和齿面等。圆柱珩磨的表 面粗糙度一般可达Ra0.32~0.08微米,精 珩时可达Ra0.04微米以下,并能少量提高几 何精度,加工精度可达IT7~4。平面珩磨的 表面质量略差。
(2)哈脖望远镜重量达900Kg的大型反射镜的 加工 (3)精密雷达、精确制导、电子对抗、TMD、 NMD、间谍卫星等 (4)人造卫星仪表轴承 (5)红外导弹中红外线反射镜 (6)超小型计算机等
(7)海湾战争、克索沃战争、伊拉克战争中美 国及其盟国武器系统中大部分与超精密加 工技术有关。如:精密雷达、精确制导、 电子对抗、隐形飞机、夜战能力、间谍卫 星、红外制导等。 (8)美国及其盟国的胜利在某种意义上看,可 以说是高技术战争、是高科技的胜利。没 有超精密加工技术,就没有真正的国防工 业。
3.超精密加工 超精密加工是指被加工零件的尺寸公差为 0.001数量级,表面粗糙度Rz为0.001数量 级的加工方法,加工中所使用的设备,其 分辨率和重复精度应为0.01数量级。目前, 超精密加工的精度正从微米工艺向纳米工 艺提高。微米工艺是指精度为1~10-2的 微米、亚微米级工艺,而纳米工艺是指精 度为10-2~10-3的纳米级工艺(1= 103nm,nm称纳米)。
发展精密和超精密加工技术的重要性

发展精密和超精密加工技术的重要性精密和超精密加工代表了加工精度发展的不同阶段,通常,按加工精度划分,可将机械加工分为一般加工,精密加工,超精密加工三个阶段精密加工;加工精度在0.1 -1um,讲表面粗糙度在Ra 0.02-0.1um之间的加工方法称为精密加工超精密加工;加工精度高于0.1um,加工表面粗糙度小于Ra 0.01um的加工方法称为超精密加工。
(微细加工、超微细加工、光整加工、精整加工等)二提高加工精度的原因提高制造精度后可提高产品的性能和质量,提高产品稳定性和可靠性;促进产品小型化;增强零件的互换性,提高装配生产率,并促进自动化装配。
三发展超精密加工的重要性1 超精密加工是国家制造工业水平的重要标志之一超精密加工所能达到的精度、表面粗糙度、加工尺寸范围和几何形状是一个国家制造技术水平的重要标志之一。
金刚石刀具切削刃钝圆半径的大小是金刚石刀具超精密切削的一个关键技术参数,日本声称已达到2nm,而我国尚处于亚微米水平,相差一个数量级(国际上公认0.1nm~100nm为纳米尺度空间,100nm~1000nm为亚微米体系,小于1个纳米为原子团簇);金刚石微粉砂轮超精密磨削在日本已用于生产,使制造水平有了大幅度提高,突出地解决了超精密磨削磨料加工效率低的问题。
2 精密和超精密加工是先进制造技术的基础和关键计算机工业的发展不仅要在软件上,还要在硬件上,即在集成电路芯片上有很强的能力,我国集成电路的制造水平约束了计算机工业的发展。
美国制造工程研究者提出的汽车制造业的“两毫米工程”(车身尺寸变动量控制在2mm以内)使汽车质量赶上欧、日水平,其中的举措都是实实在在的制造技术。
3 国防工业上的需求陀螺仪的加工涉及多项超精密加工,导弹系统的陀螺仪质量直接影响其命中率,1kg的陀螺转子,其质量中心偏离其对称轴0.0005μm,则会引起100m的射程误差和50m的轨道误差。
大型天体望远镜的透镜、直径达 2.4m,形状精度为0.01μm,如著名的哈勃太空望远镜,能观察140亿光年的天体(六轴CNC研磨抛光机)(图)。
2.3精密和超精密加工技术
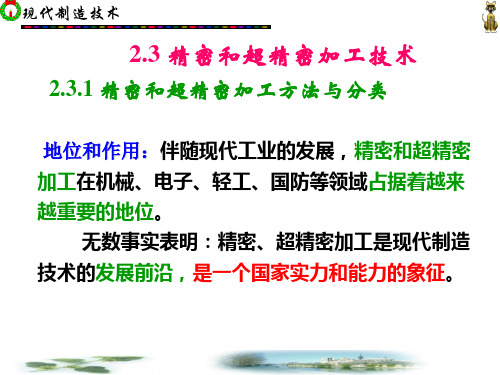
现代制造技术
2. 非机械超精密加工技术——特种精密加工方法
包括精密电火花加工、精密电解加工、精密超声加工、
电子束加工、离子束加工、激光束加工等一些非传统加工方 法;
3. 复合超精密加工方法
传统加工方法的复合 特种加工方法的复合 传统加工方法和特种加工方法的复合
(例如机械化学抛光、精密电解磨削、精密超声珩磨等)。
1~0.1 0.1~ 0.001 0.1~ 0.01 1~0.1 1~0.1 5 5 1~0.1
0.025~ 0.008 0.025~ 0.008 0.025~ 0.008 0.01 0.01 0.01 0.01~ 0.02 0.01~ 0.008
黑色金属、铝合金 黑色金属、非金属 材料 黑色金属、非金属 材料、有色金属 黑色金属、非金属 材料 黑色金属、非金 属材料、有色金属 黑色金属等 黑色金属等 黑色金属、非金属 材料、有色金属
发展:超精密磨削应用比较成熟的首推金刚石微粉砂轮 超精密磨削。
现代制造技术 1)金刚石微粉砂轮 采用粒度为F240~F1000的金刚石微粉作为磨料,树脂、 陶瓷、金属为结合剂烧结而成;也可采用电铸法和气相沉积 法制作。 用筛选法分级,粒度号以磨粒通过的筛网上每英寸长度 内的孔眼数来表示。如60 # 的磨粒表示其大小刚好能通过每 英寸长度上有60孔眼的筛网。对于颗粒尺寸小于40 μ m的磨 料,称为微粉。 • 用显微测量法分级,用W和后面的数字表示粒度号,其W后 的数值代表微粉的实际尺寸。如W20表示微粉的实际尺寸为 20 μ m
• 精密加工是指加工精度达到1~0.1μm,表面粗
糙度Ra在0.1~0.01μm的加工工艺。
• 超精加工则是指加工尺寸精度高于0.1μm,表 面粗糙度Ra小于0.025μm的精密加工方法。
对精密和超精密加工技术的认识
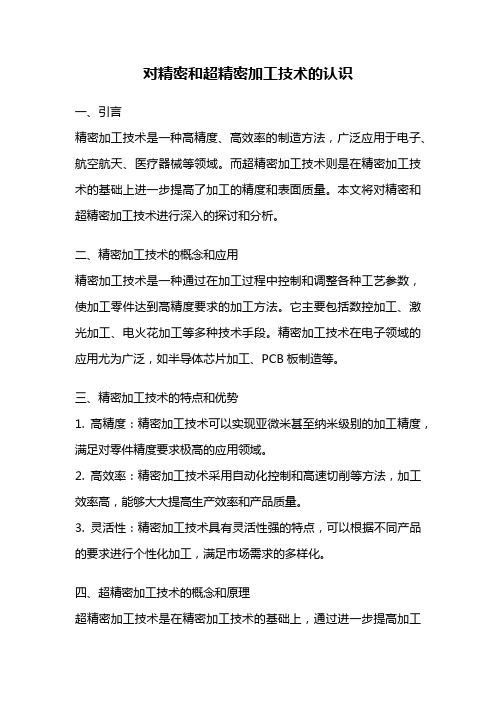
对精密和超精密加工技术的认识一、引言精密加工技术是一种高精度、高效率的制造方法,广泛应用于电子、航空航天、医疗器械等领域。
而超精密加工技术则是在精密加工技术的基础上进一步提高了加工的精度和表面质量。
本文将对精密和超精密加工技术进行深入的探讨和分析。
二、精密加工技术的概念和应用精密加工技术是一种通过在加工过程中控制和调整各种工艺参数,使加工零件达到高精度要求的加工方法。
它主要包括数控加工、激光加工、电火花加工等多种技术手段。
精密加工技术在电子领域的应用尤为广泛,如半导体芯片加工、PCB板制造等。
三、精密加工技术的特点和优势1. 高精度:精密加工技术可以实现亚微米甚至纳米级别的加工精度,满足对零件精度要求极高的应用领域。
2. 高效率:精密加工技术采用自动化控制和高速切削等方法,加工效率高,能够大大提高生产效率和产品质量。
3. 灵活性:精密加工技术具有灵活性强的特点,可以根据不同产品的要求进行个性化加工,满足市场需求的多样化。
四、超精密加工技术的概念和原理超精密加工技术是在精密加工技术的基础上,通过进一步提高加工设备的精度和加工工艺的控制精度,实现更高精度加工的一种技术手段。
超精密加工技术主要包括超精密车削、超精密磨削、超精密拓扑等方法。
五、超精密加工技术的应用领域超精密加工技术在光学仪器、航空航天、精密仪器等领域具有广泛的应用。
例如,在光学仪器领域,超精密加工技术可以用于制造高精度的光学元件,提高光学系统的分辨率和成像质量。
六、精密和超精密加工技术的发展趋势随着科技的进步和工业制造的需求,精密和超精密加工技术也在不断发展和创新。
未来的发展趋势主要包括以下几个方面:1. 加工精度的提高:随着需求的增加,对加工精度的要求也越来越高,未来的精密和超精密加工技术将进一步提高加工的精度和表面质量。
2. 加工效率的提高:随着自动化技术和智能化技术的发展,精密和超精密加工技术将更加高效,加工速度更快,生产效率更高。
04精密与超精密加工技术

微量进给装置二
压电陶瓷式微进给装置
1—刀夹 2—机座 3—压电陶瓷 4—后垫块 5—电感测头 6—弹性支承
五、精密加工环境
超精密加工必须在超稳定的环境下进 行。 超稳定环境:恒温、超净和防振。
六、超精密加工精度的在线检测及计量测试
对加工误差进行在线检测,实时建模与 动态分析预报,再根据预报数据对误差 源进行补偿,从而消除或减少加工误差。
1、去除加工(分离加工)
从工件上去除一部分材料。
超精密切削加工形面示例 (图为各种镜面切削加工的形面)
2、结合加工
利用物理和化学方法,将不同材料结合在一起。 利用物理和化学方法,将不同材料结合在一起。按结合的 机理、方法、强弱等,分为附着、注入和连接三种。 机理、方法、强弱等,分为附着、注入和连接三种。
3、变形加工(流动加工)
利用力、热、分子运动等手段,使工件 产生变形,改变其尺寸、形状和性能。
3.3.2 超精密切削加工
超精密切削对刀具的要求 • 极高的硬度、极高的耐用度和极高的弹性模量,保证 刀具寿命和尺寸耐用度; • 刃口能磨得极其锋锐,刃口半径ρ值极小,能实现超 薄的切削厚度; • 刀刃无缺陷,避免刃形复印在加工表面; • 抗粘结性好、化学亲和性小、摩擦系数低、能得到极 好的加工表面完整性。
3、精密与超精密加工的应用与进展
美国是研究最早的国家,处于世界领先地位,以 民品应用为主要对象 英国的克兰菲尔德精密工程研究所有较高声誉 日本起步较晚,发展最快,以发展国防尖端技术 为主要目标。 我国在70年代末期有长足进步,80年代中期出现 了具有世界水平的超精密机床和部件
二、 超精密加工方法
六、超精密加工精度的在线检测及计量测试
大距离的测量仪器:双频激光干涉仪 小距离的测量仪器:电容式、电感式测微仪、 光纤测微仪 更小测量范围的测量仪器:扫描隧道显微 镜 、扫描电子显微镜、原子力显微镜
精密和超精密加工,精密加工的技术手段有什么?

精密和超精密加工,精密加工的技术手段有什么?制造业是一个国家或地区国民经济的重要支柱,所谓先进制造技术,就是将机械工程技术、电子信息技术(包括微电子、光电子、计算机软硬件、现代通信技术)和自动化技术,以及材料技术、现代管理技术综合集成的生产技术。
先进制造技术追求的目标就是实现优质、精确、省料、节能、清洁、高效、灵活生产,满足社会需求。
精密加工技术是为适应现代高技术需要而发展起来的先进制造技术,是其它高新技术实施的基础。
精密加工技术的发展也促进了机械、液压、电子、半导体、光学、传感器和测量技术以及材料科学的发展。
精密和超精密加工通常,按加工精度划分,机械加工可分为一般加工、精密加工、超精密加工三个阶段。
目前,精密加工是指加工精度为1~0.1µ;m,表面粗糙度为Ra0.1~0.01µ;m的加工技术,但这个界限是随着加工技术的进步不断变化的,今天的精密加工可能就是明天的一般加工。
精密加工所要解决的问题,一是加工精度,包括形位公差、尺寸精度及表面状况;二是加工效率,有些加工可以取得较好的加工精度,却难以取得高的加工效率。
超精密加工就是在超精密机床设备上,利用零件与刀具之间产生的具有严格约束的相对运动,对材料进行微量切削,以获得极高形状精度和表面光洁度的加工过程。
当前的超精密加工是指被加工零件的尺寸精度高于0.1μm,表面粗糙度Ra小于0.025μm,以及所用机床定位精度的分辨率和重复性高于0.01μm的加工技术,亦称之为亚微米级加工技术,且正在向纳米级加工技术发展。
超精密加工包括微细加工、超微细加工、光整加工、精整加工等加工技术。
微细加工技术是指制造微小尺寸零件的加工技术;超微细加工技术是指制造超微小尺寸零件的加工技术,它们是针对集成电路的制造要求而提出的,由于尺寸微小,其精度是用切除尺寸的绝对值来表示,而不是用所加工尺寸与尺寸误差的比值来表示。
光整加工一般是指降低表面粗糙度和提高表面层力学机械性质的加工方法,不着重于提高。
精密与超精密加工技术

刀具种类:金刚石刀具; 超精密磨削砂轮
金刚石刀具
1、金刚石刀头的特性: 颜色:有红色和绿色等多种颜色,其硬
度随颜色而不同; 硬度:显微硬度值比其他物质高许多; 热传导率:在矿物中最大。
金刚石刀具
2、金刚石刀头的制造: 成形:采用研磨加工方法; 研磨方法:用空气轴承的研磨机; 特殊刀头的形状
第三章 先进制造工艺技术
第一节 精密与超精密加工技术
一、 精密与超精密加工技术概述
1、精密加工与超精密加工定义
精密加工是指加工精度在0.1~lμm之间, 表面粗糙度Ra在0.lμm以下(称微米加工)
超精密加工的加工精度在0.lμm以下,表面 粗糙度在0.02μm以下(称为亚微米加工)
2、精密加工与超精密加工的特点
光纤测微仪 更小测量范围的测量仪器:扫描隧道显微
镜 、扫描电子显微镜、原子力显微镜
激光干涉仪
SPA-400 多功能扫描探针显微镜
回顾
一、 精密与超精密加工技术概述 二、 超精密加工方法 三、 超精密加工刀具 四、 超精密加工设备 五、 精密加工环境 六、 超精密加工精度的在线检测及计量测试
五、精密加工环境
超精密加工必须在超稳定的环境下进 行。
超稳定环境:恒温、超净和防振。
六、超精密加工精度的在线检测及计量测试
对加工误差进行在线检测,实时建模与 动态分析预报,再根据预报数据对误差 源进行补偿,从而消除或减少加工误差。
六、超精密加工精度的在线检测及计量测试
大距离的测量仪器:双频激光干涉仪 小距离的测量仪器:电容式、电感式测微仪、
超精密磨削砂轮
超精密磨削质量控制方面的首要因素: 砂轮磨料:应与工件材料选配适当; 磨料粒度:具备形成微刃的粒度; 砂轮硬度:硬度中软。
精密和超精密加工的机床设备

精密和超精密加工的机床设备简介精密加工和超精密加工是现代制造业中非常重要的工艺,为了实现高精度和高质量的产品制造,需要使用精密和超精密加工的机床设备。
本文将介绍精密和超精密加工的定义、应用领域、常见机床设备及其特点。
精密加工与超精密加工的定义精密加工是指在小尺寸范围内实现高精度、高表面质量的加工过程。
超精密加工则是在精密加工的基础上,进一步提高加工精度和表面质量,通常使用的是非常细小的工具进行加工。
精密加工与超精密加工的应用领域精密加工和超精密加工广泛应用于各个领域,特别是需要高精度和高质量的产品制造领域。
以下是一些典型的应用领域:1.光学器件加工:如镜片、棱镜、透镜等光学组件的加工需要极高的精度和表面质量。
2.高精密模具加工:精密模具通常用于制造电子产品、汽车零部件等需要高精度的零件。
3.精密五金零部件加工:如手表零部件、医疗设备零部件等,需要高精度和高质量的加工。
4.微电子器件加工:微电子器件通常要求极高的精度和表面质量,用于生产集成电路、传感器等。
常见的精密和超精密加工机床设备下面介绍一些常见的精密和超精密加工机床设备及其特点:CNC铣床CNC铣床是一种通过计算机控制的自动化机床,能够在三个轴向上进行加工。
精密加工中常用的是数控铣床,而超精密加工则需要使用高速铣床。
CNC铣床具有高精度、高刚性、高自动化程度等特点。
高精度车床高精度车床是一种用来加工圆柱形工件的机床。
它能够在工件上进行精确的车削、镗削、钻削等操作。
高精度车床具有高工作精度、高生产效率和良好的刚性。
光学加工机光学加工机是用激光或电子束等光学器件进行加工的机床设备。
它能够实现非常高的加工精度和表面质量,常用于光学器件加工和微电子器件加工。
超精密磨床超精密磨床是一种用磨粒对工件进行加工的机床设备。
它能够实现非常高的加工精度和表面质量,常用于精密模具加工和高精度五金零部件加工。
EDM电火花机床EDM电火花机床是一种利用电火花腐蚀的原理进行加工的机床设备,能够实现非常高的加工精度和表面质量。
精密与超精密加工
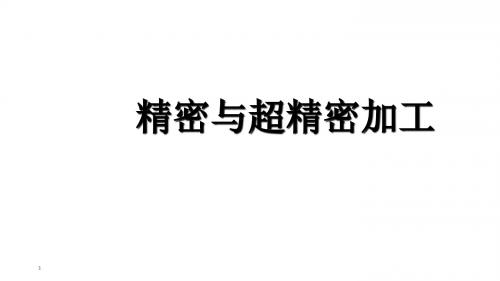
1
第一节
概述
在高精度加工范围内,根据加工精度水平的不同, 可进一步划分为精密加工、超精密加工和纳米加工三个 档次。
精密加工----加工公差为10.0~0.1μm,表面粗糙
度Ra0.30~0.03μm的加工精密加工
超精密加工----加工公差为0.1~0.01μm、表面粗
糙度Ra0.03~0.005μm的加工超精密加工;
形状误差 0.1μm
平面度误差 0.04μm 平面度误差 0.04μm 波度 0.01 ~0.02μm 平面度垂直度误差 < 0.1μm 圆柱度误差 <0.01μm 形状误差 < 0.03μm
Ra 0.01~0.05μm
Ra <0.02μm Ra <0.02μm Ra <0.02μm Ra <0.02μm Ra <0.002μm Ra <0.01μm
8
第二节 金刚石超精密加工技术
◆ 机理、特点 切削在晶粒内进行(吃刀量a p 1m) 切削力>原子结合力(剪切应力达 13000 N/ mm2) 刀尖处温度极高,应力极大,普通刀具难以承受 高速切削(与传统精密切削相反),工件变形小,表 层高温不会波及工件内层,可获得高精度和好表面质量 ◆ 应用 用于铜、铝及其合金精密切削(切铁金属,由于亲合 作用,产生“碳化磨损”,影响刀具寿命和加工质量) 加工各种红外光学材料如锗、硅、ZnS和ZnSe等 加工有机玻璃和各种塑料 典型产品:光学反射镜、射电望远镜主镜面 、 大型投 影电视屏幕、照像机塑料镜片、树脂隐形眼镜镜片等
超高精密磨床 激光高精度 超精密研磨机 测长仪
1900
4
1920
1940
1960 1980 精密加工与超精密加工的发展
- 1、下载文档前请自行甄别文档内容的完整性,平台不提供额外的编辑、内容补充、找答案等附加服务。
- 2、"仅部分预览"的文档,不可在线预览部分如存在完整性等问题,可反馈申请退款(可完整预览的文档不适用该条件!)。
- 3、如文档侵犯您的权益,请联系客服反馈,我们会尽快为您处理(人工客服工作时间:9:00-18:30)。
微刃的微切削作用 微刃的等高切削作用 微刃的滑挤、摩擦、抛光作用
超精精磨削机理:
1、超精磨削是一种极薄切削,切屑厚度极小,磨削 深度可能小于晶粒的大小,磨削就在晶粒内进行,因此 磨削力一定要超过晶体内部非常大的原子、分子结合力, 从而磨粒上所承受的切应力就极速地增大,可能接近被 磨削材料的剪切强度极限。同时,磨粒切削刃处收到高 温和高压的作用,要求磨粒材料有很高的高温强度和高 温硬度。
利用粒度为W63~W28的砂带可进行精密磨削,其 加工精度可达1µm,表面粗糙度可达Ra0.025µm。利用 粒度为W28~W3的砂带可进行超精密砂带磨削,其加工 精度可达0.1µm,表面粗超度可达Ra0.025~0.008µm。
六、砂带磨削特点:
弹 冷高 制工
砂
性 态效 作艺
带
磨 磨磨 简性
结
桂林理工大学南宁分校机械与控制工程系
二、金刚石刀具的特点
金刚石刀具拥有很高的高温强度和硬度,而且材质 细密,经过精细研磨,切削刃可磨得极为锋利,表面粗糙 度值很小,因此可进行镜面切削。金刚石刀具超精密切削 主要用于加工铜、铝等有色金属,如高密度硬磁盘的铝合 金基片、激光器的反射镜、复印机的硒鼓、光学平面镜, 凹凸镜、抛物面镜等。
精密加工
加工精度在10 ~0.1µ之间, IT5以上,表面粗超度Ra0.3 ~0.03µm; 用于精密机床、精密测量仪器等中的关键零件加工; 金刚车、镗,研磨,珩磨,超精研,砂带磨,镜面磨削,冷压加工等。
超精加工
加工精度在0.1 ~0.01µ之间, IT5以上,表面粗超度Ra0.03 ~0.005µm; 用于镜面加工,大规模集成电路基片及上面图形加工, 金刚石刀具超精密切削、超精密磨削和研磨、超精密特种加工
球面(球轴承)车削,复印机硒 鼓(圆柱面)车削,磁盘基片的 车削。
四、发展趋势
高精度、高效率 极端化 智能化
工艺整合化 在线加工检测一体化
绿色化
2.3 精密、超精密磨削加工
一、概念
精密砂轮磨削:利用精细修正的粒度为60#~80#的普 通砂轮进行磨削,其加工精度可达1µm,表面粗糙度可达 Ra0.025µm。
立方氮化硼(CBN)
硬度莫氏硬度9.8-10
导热系数、热膨胀系数和研磨 能力也很突出;
稳定性和化学惰性大大优于金 刚石
适合加工普通磨料难以加工且 金刚石又不宜加工的硬而韧的 金属材料如工具钢、模具钢、 不锈钢、耐热合金等特别是高 钒高速钢、铝高速钢等对磨削 温度较为敏感的金属材料。
三、加工原理
精密磨削机理:
2、磨削运动
由于弹性弹性让刀量的存在,磨削系统要求高刚度, 砂轮修锐质量好,形成切屑的磨削深度小。利用无火花磨 削状态,可以降低表面粗超度。
四、超精密磨床的特点:
Text in here
高精度
高刚度
高稳定性
微进给装置
计算机数控
砂带磨削 珩磨
超精研 研磨
ቤተ መጻሕፍቲ ባይዱ
五、砂带磨削:
根据工件的形状,用与之相应的接触方式,借助 于张紧机构使之张紧,和驱动轮使之高速运动,并利 用砂带上的磨粒对工件加工表面进行高效磨削的一种 新工艺。
削 削削 单和
构
、应
价用
格范
便围
宜广
2.4 珩磨 超精研 研磨和超精密磨料加工
一、绗磨 珩磨
1、概念
珩磨是利用安装在珩磨头圆周上的若干条细粒度 油石,由张开机构将油石沿径向张开,使其压向工件 孔壁,以便产生一定的面接触,同时珩磨头做回转和 轴向往复运动,由此实现对孔的低速磨削。
一、绗磨 珩磨
1、加工机理
桂林理工大学南宁分校机械与控制工程系
三、工艺特点
1 2
以精密元件为加工对象 加工不受外界条件变化的干扰
3
要有相应的精密测量手段
4
常常与微细加工结合在一起
5
常常和自动控制联系在一起
6
常常采用复合加工技术
桂林理工大学南宁分校机械与控制工程系
2.2 精密、超精密切削加工 一、起源
60年代初,由于宇航用的陀螺,计算机用的磁鼓、磁 盘,光学扫描用的多面棱镜,大功率激光核聚变装置用的 大直径非圆曲面镜,以及各种复杂形状的红外光用的立体 镜等等,各种反射镜和多面棱镜精度要求极高,使用磨削、 研磨、抛光等方法进行加工,不但加工成本很高,而且很 难满足精度和表面粗糙度的要求。为此,研究、开发了使 用高精度、高刚度的机床和金刚石刀具进行切削加工的方 法加工。
三、影响超精密切削的因素
液体静压轴承主轴
空气静压轴承主轴
主轴
磁悬浮轴承
污染
振动
工作环境
工件材质 均匀
温度
导轨
液体静压导轨
空气静压导轨
四、应用
平面镜的切削 多面镜的切削 其它零件的切削
平面度<0.06 µm, 表面粗糙度Rmax<0.02 µm。
面分度精度7.5”,面倾斜精度3.6”, 平面度<0.07 µm,表面粗糙度 Rmax < 0.02µm。用于激光印刷 机、复印机。
超精密砂轮磨削:利用经过仔细修正的粒度为W40~ W5的砂轮进行磨削,可以获得加工精度为0.1µm,表面粗 糙度为Ra0.025~Ra0.008µm的加工表面。
特点:表面变质层和残余应力较小,加工效率比切削加工高。
普通刚玉、碳化硅 磨料、粘合剂、气孔
工作层、基体、过渡层
工作层(金刚石层):磨料、结合剂、气孔
是砂轮的工作部分
过渡层(非金刚石层):结合剂、金属粉、气孔
将金刚石层牢固地连接在基体上
基体
承接磨料层,并在使用时用法兰盘牢固地夹持在磨 床主轴上
二、磨料
金刚石
自然界人类认识的最坚硬的物 质,莫氏硬度10;
导热系数、热膨胀系数和研磨 能力都很突出; 加工很多硬而脆的材料如硬 质合金、陶瓷、宝石玛瑙、 玻璃、石材、建材、混凝土 和半导体材料等及砂轮的修 整; 不适宜加工铁族金属材料。
精密加工和超精密加工
2.1 概述
一、概念
精密加工:在一定的发展时期,加工精度和表面 质量达到很高程度的加工工艺。
超精密加工:加工精度和表面质量达到极高程 度的精密加工工艺。
二、分类
一般加工
加工精度在10µ左右,IT7~IT5,表面粗超度Ra0.8 ~0.2µm; 用于汽车、拖拉机制造等工业,车铣磨刨绞等。