数控原理与系统知识点
《数控原理与系统》第7章__数控机床电气控制系统

第7章 数控机床电气控制系统
有些輔助功能只在本程式段內起作用, 當後續程式段到來時便失效,稱為當前輔 助功能,記為C類,例如M06等。還有一些 輔助功能一旦被執行便一直有效,直至被 注消或被取代為止,稱為保持類輔助功能, 記為H類,例如M10、M11等。對於不同動 作類型的輔助功能,在用邏輯電路或編寫 PLC程式實現時,其處理方法也將不同。
第7章 数控机床电气控制系统
第7章 數控機床電氣控制系統
7.1 概述
7.2 JBK-30型數控系統及其在 CJK0630A車床上的應用
7.3 FAGOR 8025/8030數控系統及 其在CK6150數控車床上的應用
7.4 數控系統中PLC的資訊交換及M、 S、T功能的實現
7.5 數控機床電氣圖的繪製方法 小結
第7章 数控机床电气控制系统
3.T功能 T功能即刀具功能,T代碼後跟隨2~ 5位數字表示要求的刀具號和刀具補償號。 數控機床根據T代碼,通過PLC可以管理刀 庫,自動更換刀具,也就是說根據刀具和 刀具座的編號,可以簡便、可靠地進行選 刀和換刀控制。
第7章 数控机床电气控制系统
7.1.3數控系統中的可編程控制器(PLC) 數控系統輔助控制功能以開關量順序控 制為主,可採用繼電器控制邏輯或可編程序 邏輯控制器(PLC)實現。在一些經濟型的數 控車床和輔助動作比較簡單的數控機床上, 為了簡單起見,其輔助動作的控制常用繼電 器邏輯實現。而在功能比較完善的數控機床 上,其輔助動作的控制邏輯一般都比較複雜, 如果仍使用繼電器實現,則電路的設計和調 試將比較困難,可靠性也差。因此,多數數 控機床都採用可編程控制器(PLC)來完成輔 助運動的控制。
机床数控原理与系统

机床数控原理与系统简介机床数控原理与系统是机械制造领域中的重要内容之一。
随着科技的不断发展,机床数控系统在工业生产中起着至关重要的作用。
本文将介绍机床数控原理的基本概念、发展历程以及常见的数控系统构成和工作原理。
机床数控原理的基本概念机床数控原理是指通过计算机控制机床的运动进行加工的一种加工方式。
其基本概念包括:1.机床数控系统:由计算机硬件、软件和相关元件组成的一套用于控制机床运动和加工加工工件的系统。
2.数控编程:将加工工艺和运动控制命令转化为机床数控系统可以理解和执行的指令序列。
3.数控加工:根据数控编程生成的指令序列,通过机床数控系统的控制,实现工件的加工、切削、钻孔等工艺过程。
机床数控原理的发展历程机床数控原理的发展经历了多个阶段:1.1950年代:数控技术开始出现,并逐渐应用于大型机床上。
2.1960年代:随着计算机技术的发展,数控系统逐渐进入实用化阶段,小型机床上开始应用。
3.1970年代:数控系统开始普及,并逐步取代传统的机床操作方式,提高了生产效率和加工精度。
4.1980年代:数控技术进一步发展,出现了多轴、多功能的数控系统和高速加工中心。
5.1990年至今:数控技术与计算机技术、传感器技术的融合,使得机床数控系统更加智能化和自动化。
机床数控系统的构成机床数控系统主要由以下几个部分构成:1.数控设备:包括数控控制器、电机驱动器、传感器等。
2.数控编程和操作界面:用于输入和编辑数控程序,控制机床的运动和加工过程。
3.运动控制系统:负责根据数控程序控制机床各个轴向的运动,如进给轴和主轴。
4.刀具和刀库系统:负责刀具的选取、刀具换装以及刀具状态的监测。
5.冷却液系统:用于冷却和润滑工件和切削刀具。
机床数控系统的工作原理机床数控系统的工作原理可以总结为以下几个步骤:1.数控编程:根据加工工艺和要求,编写数控程序,并通过数控编程软件输入到数控系统。
2.数控系统解释和执行:数控系统解释数控程序中的指令,并根据指令执行相应的运动控制和加工操作。
《数控原理与系统》第3章_数控位置检测装置
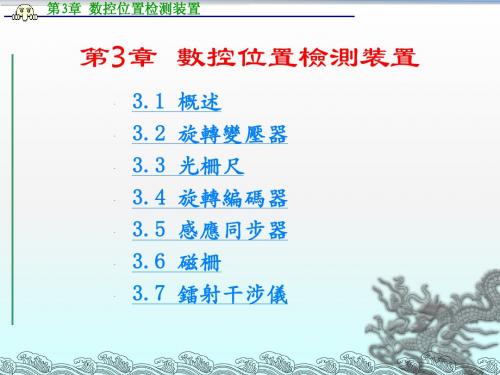
第3章 数控位置检测装置
3.2 旋轉變壓器
旋轉變壓器是一種角位移測量元件,外 形如圖所示。結構與兩相繞線式非同步電動 機相似,由定子和轉子組成,根據轉子繞組 引出方式不同,分為有刷和無刷兩種結構形 式。
(a) 旋轉變壓器外形圖 (b)有刷旋轉變壓器結構圖 (c) 無刷旋轉變壓器結構圖 圖3.1 旋轉變壓器外形結構圖
第3章 数控位置检测装置
U1 U m sin t
定子
U1 U m sin t
Φ1
U1 U m sin t
Φ1
Φ1
1
பைடு நூலகம்
转子
Φ2
Φ2
Φ2
0
E1 0
1
E1 nU m sin t sin 1
90
E1 nU m sin t
第3章 数控位置检测装置
u 21 k 21U1m sin t sin u 22 k 22U 1m sin t cos
第3章 数控位置检测装置
將勵磁信號和轉子繞組輸出信號送至解碼電 路輸入端,即可得到轉子轉角代碼。日本多摩川 公司推出的解碼電路集成晶片原理如圖3.3所示, 如果圖中usr=0,那麼θ= θrd,即可解碼出轉子轉 角。
旋轉編碼器、圓光柵, 絕對式旋轉編碼器,多極旋轉 旋轉變壓器、圓感應同步 變壓器 器、圓形磁尺 三速圓型感應同步器
直線型
光柵尺、直線型感應 編碼尺、多通道投射光柵, 同步器、磁尺,鐳射干涉 三速直線型感應同步器、絕對 儀 式磁尺
第3章 数控位置检测装置
3.1.3 位置檢測裝置的性能指標
1. 精度:檢測輸出值與實際位置的符合程度。 2. 解析度:可分辨的最小刻度值,一般按加工精度的1/ 3~1/10選取檢測裝置的解析度。 3. 靈敏度:檢測輸出值隨實際位置變化的及時程度。 4. 遲滯:同一實際位置,正行程與反行程的檢測輸出結果 不一致的現象,稱為遲滯,遲滯越小越好。 5. 測量範圍和量程:測量範圍要滿足系統的要求,並留有 餘地。 6. 零漂與溫漂:測量精度隨時間和溫度的變化而變化的現 象。
数控原理与系统数控原理概述总结

第一章 数控系统概述
1.2数控系统与计算机数控系统(CNC系统)
(2)数控装置—是数控系统的核心
o 由输入/输出接口线路、控制器、运算器和存储器等部分组成 o 作用是将输入装置输入的数据,通过内部的逻辑电路或控制软件进行编译、运算
第一章 数控系统概述
1.1数字控制技术
1.1.2NC机床、加工中心、FMC、FMS与CIMS
o 凡是采用了数控技术进行控制的机床统称NC机床 o 带有自动刀具交换装置(Automatic Tool Changer—ATC)的数控机床(带有回转刀架的 数
控车床除外)称为加工中心(Machine Center—MC) o 在加工中心的基础上,通过增加多工作台(托盘)自动交换装置(Auto Pallet Changer—APC)
第一章 数控系统概述
1.2数控系统与计算机数控系统(CNC系统)
•1.2.3 CNC系统的特点与功能 •C的特点 •1)灵活性 •2)通用性 •3)可靠性 •4)数控功能多样性 •5)使用维修方便 •6)易于实现机电一体化
第一章 数控系统概述
1.2数控系统与计算机数控系统(CNC系统)
o 2.CNC系统的功能
G92 X400. Z250.
位置等),其控制信息主要来源于数控加工或运动控制程序 o 数控系统的最基本组成应包括:程序的输入/输出装置、数控装置、
伺服驱动这三部分
第一章 数控系统概述
1.2数控系统与计算机数控系统(CNC系统)
(1)输入/输出装置—作用是进行数控加工或运动控 制程序、加工与控制数据、机床参数以及坐标轴 位置、检测开关的状态等数据的输入、输出
数控原理与系统复习文档

第一章A.什么是数控系统?机床数控系统的组成及各部分作用如何?1.数控系统的基本概念:数控是数字控制的简称。
从广义上讲,是指利用数字化信息实控制,也就是利用数控控制技术实现的自动控制系统,其被控对象可以是各种生产过程。
狭义上理解也就是利用数字化信息对机床轨迹和状态实行控制。
2.数控系统的组成:输入/输出装置、数控装置、伺服系统、机床电器控制装置、机床本体。
3.输入装置的作用:将数控加工程序等各种信息输入数控装置,输入的内容及数控系统的工作状态可以通过输出装置观察。
4.数控装置的作用:正确识别和解释数控加工程序,对解释结果进行各种数据计算和逻辑判断处理。
5.伺服系统的作用:按照数控装置发出的位置控制命令和速度控制命令正确驱动机床受控部件的移动。
6.机床电器控制装置的作用:接受数控装置发出的开关,主要完成机床主轴选速、起停和方向控制功能,换刀功能,工件装夹功能,冷却、液压、气动、润滑系统控制功能以及机床其他辅助功能。
7.机床本体的作用:B.简述数控机床坐标系的定义8.标准的数控机床坐标系统采用右手直角笛卡尔坐标系。
C.试简速数控系统的分类及各自的显著特点9.按数控机床运动轨迹分类:点位数控系统、直线数控系统、轮廓数控系统按数控机床伺服系统分类:开环数控系统、全闭环数控系统、半闭环数控系统按数控机床功能水平分类:经济型数控系统、普及型数控系统、高档型数控系统D.简述计算机数控系统的基本工作过程10.输入、译码、诊断、刀补计算、速度处理、插补计算、位置控制E.名词解释CNC---计算机数字控制装置 PLC---可编程逻辑控制器ISO(Internation Standard Organization)---国际标准化组织WOP---面向车间的编程 DNC---分布式数字控制 FMC---柔性制造单元FMS---柔性制造系统CIMS(Computer integrated Manufacturing System)---计算机集成制造系统CAD---计算机辅助设计 CAM---计算机辅助制造 CAPP---计算机辅助工艺过程设计CAQ---计算机辅助质量管理 LAN---工业局域网络TCP/IP ---传输控制协议/网际协议 MAP---制造自动化协议MRP---物料需求计划 ERP(Enterprise Resource Planning)SOSAS(Specificatiao for an Open System Architecture Standard)OSACA(Open System Architecture For Control Within Automation)---开放式系统应包括一组逻辑上可分的部件,部件间的接口及部件与执行平台间的接口要定义完备,并可实现不同开发商开发的部件可协调工作并组成一个完整的控制器OSEC(OSE for Controller)---第二章F.什么是内码?内码是按属性加编码构成的内部代码。
数控系统的基本原理及应用
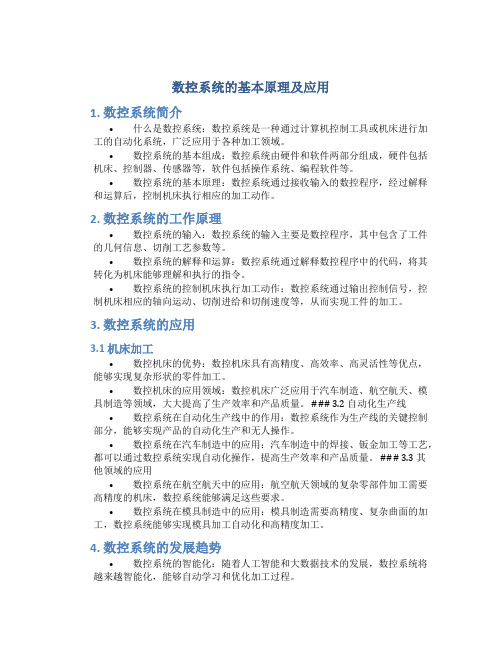
数控系统的基本原理及应用1. 数控系统简介•什么是数控系统:数控系统是一种通过计算机控制工具或机床进行加工的自动化系统,广泛应用于各种加工领域。
•数控系统的基本组成:数控系统由硬件和软件两部分组成,硬件包括机床、控制器、传感器等,软件包括操作系统、编程软件等。
•数控系统的基本原理:数控系统通过接收输入的数控程序,经过解释和运算后,控制机床执行相应的加工动作。
2. 数控系统的工作原理•数控系统的输入:数控系统的输入主要是数控程序,其中包含了工件的几何信息、切削工艺参数等。
•数控系统的解释和运算:数控系统通过解释数控程序中的代码,将其转化为机床能够理解和执行的指令。
•数控系统的控制机床执行加工动作:数控系统通过输出控制信号,控制机床相应的轴向运动、切削进给和切削速度等,从而实现工件的加工。
3. 数控系统的应用3.1 机床加工•数控机床的优势:数控机床具有高精度、高效率、高灵活性等优点,能够实现复杂形状的零件加工。
•数控机床的应用领域:数控机床广泛应用于汽车制造、航空航天、模具制造等领域,大大提高了生产效率和产品质量。
### 3.2 自动化生产线•数控系统在自动化生产线中的作用:数控系统作为生产线的关键控制部分,能够实现产品的自动化生产和无人操作。
•数控系统在汽车制造中的应用:汽车制造中的焊接、钣金加工等工艺,都可以通过数控系统实现自动化操作,提高生产效率和产品质量。
### 3.3 其他领域的应用•数控系统在航空航天中的应用:航空航天领域的复杂零部件加工需要高精度的机床,数控系统能够满足这些要求。
•数控系统在模具制造中的应用:模具制造需要高精度、复杂曲面的加工,数控系统能够实现模具加工自动化和高精度加工。
4. 数控系统的发展趋势•数控系统的智能化:随着人工智能和大数据技术的发展,数控系统将越来越智能化,能够自动学习和优化加工过程。
•数控系统的网络化:数控系统的网络化将使得远程监控和管理成为可能,提高生产效率和工作灵活性。
数控机床控制系统的原理与功能分析

数控机床控制系统的原理与功能分析一、引言数控机床控制系统是现代制造业中不可或缺的重要设备。
它通过将数字信号转换为机械运动控制信号,实现对机床各个运动轴的精确控制。
本文将从数控机床控制系统的原理和功能两个方面进行分析。
二、数控机床控制系统的原理1. 数字信号的生成数控机床控制系统的原理是基于数字信号的生成。
数字信号可以通过计算机或专用控制器生成。
在数控机床控制系统中,计算机或控制器负责处理输入的加工程序,并将其转化为数字信号,通过输出端口发送给伺服驱动器。
2. 伺服驱动器伺服驱动器是数控机床控制系统中的核心部件之一。
它接收来自计算机或控制器的数字信号,并根据信号的大小和方向,控制伺服电机的转速和位置。
伺服驱动器通过反馈装置获取电机的实际转速和位置信息,并将其与输入信号进行比较,从而实现对电机的闭环控制。
3. 伺服电机伺服电机是数控机床控制系统中的执行部件。
它接收伺服驱动器输出的控制信号,并根据信号的大小和方向,实现精确的机械运动。
伺服电机通常采用直流电机或交流伺服电机,具有高速响应和较好的运动平稳性。
三、数控机床控制系统的功能分析1. 运动控制数控机床控制系统的主要功能之一是实现对机床各个运动轴的精确控制。
通过控制伺服驱动器和伺服电机,可以实现机床的定位、插补、速度控制等运动控制功能。
数控机床控制系统可以根据加工程序中的指令,精确控制机床在不同轴向上的运动,实现复杂零件的加工。
2. 加工参数设置数控机床控制系统还具有加工参数设置的功能。
通过输入加工程序,操作人员可以设置加工的速度、进给量、切削深度等参数。
数控机床控制系统会根据这些参数,自动调整机床的运动轨迹和速度,实现对工件的精确加工。
3. 故障检测与报警数控机床控制系统还具有故障检测与报警功能。
在加工过程中,如果发生异常情况,如电机过载、电源故障等,数控机床控制系统会自动检测并发出警报信号。
这样可以及时发现并解决问题,保证机床的安全运行。
4. 数据管理与通信数控机床控制系统还可以实现数据管理与通信功能。
《数控原理与系统》第9章__典型数控系统

第8章 典型数控系统及应用
பைடு நூலகம்
主印刷電路板(MASTER PCB)
第 7 、 8軸控 制板
第8章 典型数控系统及应用
該系統除了通用的宏程式功能以外, 還增加了定制型用戶宏程式,這樣為用戶 提供了更大的個性化設計的空間。用戶可 以通過編程對顯示幕幕、處理過程控制等 進行編輯,以實現個性化機床的設計。
第8章 典型数控系统及应用
(4)高速高精度的控制 FANUC 0–C數控系統採用了多CPU方式進行 分散處理,實現了高速連續的切削。為了實現在 切削路徑中的高速、高精度,在系統功能中增加 了自動拐角倍率,伺服前饋控制等,大大地減少 了伺服系統的誤差。 對PLC的介面增加了高速M、S、T介面功能, 進一步縮短了執行時間,提高了系統的運行速度。 為了提高系統處理外部數據的速度, FANUC 0–C系統在硬體上增加了遠程緩衝控制, 系統可以實現高速的DNC操作。
第8章 典型数控系统及应用
9.1.2 FANUC 0系列數控系統 1.主要功能特點 FANUC 0系列數控系統分為A型、B型、 C型和D型產品,目前在國內使用較多的是 普及型FANUC 0–D和全功能型FANUC 0–C兩 個子系列,其功能特點如下。
第8章 典型数控系统及应用
第8章 典型数控系统及应用
2.基本構成 FANUC 0系統由數控單元本體,主軸和進給 伺服單元以及相應的主軸電機和進給電機,CRT 顯示器、系統操作面板、機床操作面板,附加的 輸入/輸出介面板(B2),電池盒,手搖脈衝發 生器等部件組成,下麵對它的主要部件的基本配 置做簡要的說明。
第8章 典型数控系统及应用
《数控原理与系统》第1章_绪论

伺服驱动 装置
机 床 本 体 位置 检测 装置
图1.3 数控系统的组成结构
第1章 绪论
1.1.2
數控系統的組成結構
Байду номын сангаас
各組成部分的功能
1. 數控裝置 其功能是從輸入裝置接收零件程式,並對其進行解碼、 插補等處理,最後輸出進給信號和主軸啟/停、刀具選擇等輔助 控制信號。 2. 輸入/輸出裝置 是操縱者和數控裝置間的“人—機”介面,用 來輸入編輯零件程式、操作命令,輸出顯示機床工作狀態、工作 座標等資訊。常見的輸入輸出裝置有:CRT顯示/MDI鍵盤、紙帶 閱讀機、上位電腦等。 3. 伺服驅動裝置 用來把數控裝置輸出的信號進行功率放大,以驅 動伺服電動機拖動機床運動。 4. 機床電氣控制邏輯 用來實現主軸起/停、換刀等輔助控制功能, 並零件程式的執行與這些輔助動作同步。 5. 位置檢測裝置 用來檢測工作臺的實際位置,輸出位置回饋資訊, 實現閉環或半閉環位置控制,提高控制精度。
第1章 绪论
1.2 數控技術的產生和發展
1.2.1 數控技術的產生
數控技術是 20 世紀 40 年代後期為適應複雜外形零件 的加工而發展起來的一種自動化技術,其研究起源於飛 機製造業。1949年美國帕森(Parsons)公司接受美國空 軍委託,研製一種計算控制裝置,用來實現飛機、火箭 等複雜零部件的自動化加工,於是Parsons公司提出了用 數字資訊來控制機床自動加工外形複雜零件的設想,並 與美國麻省理工學院(MIT)伺服機構研究所合作,於1952 年研製成功了世界上第一台數控機床 ---- 三座標立式數 控銑床,可控制銑刀進行連續空間曲面的加工,由此拉 開了數控技術研究的序幕。
0112
微型计算机
数控系统
数控技术原理与系统

数控技术原理与系统数控技术是一种通过计算机软硬件控制机床和工具进行自动加工的先进制造技术。
它在传统机床的基础上,引入了计算机数字控制系统,以提高加工精度、效率和自动化程度。
本文将对数控技术的原理和系统进行分析和探讨。
一、数控技术原理数控技术的核心原理是通过编程指令将加工工艺要求转化为机床的加工轨迹和切削参数,并通过计算机控制系统实现对机床的自动控制。
数控技术的原理主要包括以下几个方面:1. 数字化表示和储存:数控系统将机床的加工轨迹和切削参数等信息以数字的形式进行表示和储存。
通过数字化的数据表示,方便了工艺参数的调整和加工过程的优化。
2. 程序控制:数控系统通过编程指令实现对机床运动轨迹和切削参数的控制。
通过编程,可以指定机床的加工路径、进给速度、刀具的切削深度等参数,从而实现工件的精确加工。
3. 传感器反馈:数控系统通过传感器实时感知机床和工件的状态,并将感知到的信息反馈给控制系统进行处理。
传感器可以监测机床的位置、速度、加速度等参数,以及工件的尺寸和表面质量等指标,从而实现对加工过程的实时监控和调整。
4. 闭环控制:数控系统采用闭环控制的方式对机床进行控制。
即通过传感器反馈的信息进行实时比较,将实际加工结果与期望结果进行对比,从而对控制指令进行修正和调整,以达到更高的加工精度和稳定性。
二、数控系统数控系统是数控技术实现的关键,它由硬件和软件两部分组成。
数控系统的硬件包括计算机、控制器、伺服电机等主要设备,而软件则包括编程软件、操作系统以及相应的应用软件。
1. 计算机:计算机是数控系统的核心设备,它负责将加工工艺的要求转化为机床的控制指令,并实时监控和调整加工过程。
计算机采用高性能的处理器和大容量存储器,以满足复杂加工任务的需求。
2. 控制器:控制器是数控系统的指挥中心,它接收计算机发送的控制指令,并对机床的运动和切削参数进行实时控制。
控制器通常采用专用的硬件电路,以实现高速稳定的信号处理和输出。
《数控原理与系统》第6章_主轴驱动及控制

2. 開關量信號 (1) RDY準備好信號: 欲使主軸驅動工作,可 閉合RDY觸點,主軸驅動進入正常工作狀態。 (2) EMG急停信號: 當EMG常閉觸點打開時, 電動機立即制動至停轉。 (3) FOR、 REV信號: 用於指定主軸正反轉, 其與模擬量的極性組合見表6.1。
KI f
第6章 主轴驱动及控制
( 1 )在基速 n0 以下,採用調壓調速,即在勵 磁電流If不變,Φ為常數的情況下,用改變電樞 電壓Ua的方法調速。 這時輸出的最大轉矩Mmax 取決於電樞電流最大值Imax, 即 Mmax=CMΦImax 而對一臺主軸電動機來說,最大電流為恒 定,因此所能輸出最大轉矩是恒定的,而輸出 功率隨轉速升高而增加,因此基速n0以下稱為 恒轉矩調速。
第6章 主轴驱动及控制
6.1.2 主軸系統的分類與特性 1. 主軸系統的分類 根據變速方式的不同,主軸系統可分為有 級變速、 無級變速和分段無級變速三種形式。 其中,有級變速僅用於經濟型數控機床, 大多 數數控機床均採用無級變速或分段無級變速。
第6章 主轴驱动及控制
為滿足變速的要求,早期的數控機床常採用 直流主軸驅動系統。由於直流電動機存在體積大、 恒功率調速範圍窄、電刷易磨損、維護比較麻煩 等缺點,而逐漸被交流主軸驅動系統所取代。目 前,絕大多數數控機床均採用鼠籠式交流非同步 電動機配置向量變頻調速器,構成主軸驅動系統。
U a I a Ra E E Ce n M C M I a
KI t
第6章 主轴驱动及控制
+
Ia If Ra +
U a
E
M
- M
n
-
圖6.1 主軸電動機電路模型
数控基础知识点总结
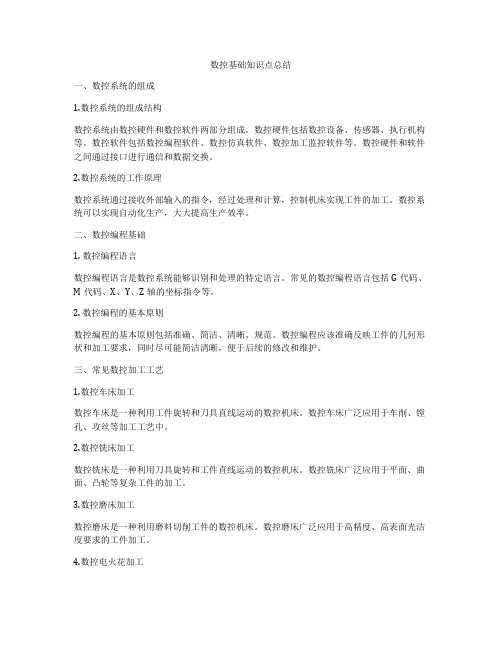
数控基础知识点总结一、数控系统的组成1.数控系统的组成结构数控系统由数控硬件和数控软件两部分组成。
数控硬件包括数控设备、传感器、执行机构等。
数控软件包括数控编程软件、数控仿真软件、数控加工监控软件等。
数控硬件和软件之间通过接口进行通信和数据交换。
2.数控系统的工作原理数控系统通过接收外部输入的指令,经过处理和计算,控制机床实现工件的加工。
数控系统可以实现自动化生产,大大提高生产效率。
二、数控编程基础1. 数控编程语言数控编程语言是数控系统能够识别和处理的特定语言。
常见的数控编程语言包括G代码、M代码、X、Y、Z轴的坐标指令等。
2. 数控编程的基本原则数控编程的基本原则包括准确、简洁、清晰、规范。
数控编程应该准确反映工件的几何形状和加工要求,同时尽可能简洁清晰,便于后续的修改和维护。
三、常见数控加工工艺1.数控车床加工数控车床是一种利用工件旋转和刀具直线运动的数控机床。
数控车床广泛应用于车削、镗孔、攻丝等加工工艺中。
2.数控铣床加工数控铣床是一种利用刀具旋转和工件直线运动的数控机床。
数控铣床广泛应用于平面、曲面、凸轮等复杂工件的加工。
3.数控磨床加工数控磨床是一种利用磨料切削工件的数控机床。
数控磨床广泛应用于高精度、高表面光洁度要求的工件加工。
4.数控电火花加工数控电火花加工是一种利用电火花放电去除工件材料的加工方法。
数控电火花加工适用于超硬材料、复杂曲面等加工。
四、数控机床的基本原理1.数控机床的运动控制数控机床的运动控制包括轴线性插补、圆弧插补、螺旋线插补等。
通过数控系统计算,控制各个轴向的运动,实现工件的加工。
2.数控机床的加工功能数控机床的加工功能包括车削、铣削、磨削、切割等。
数控机床可以通过不同的刀具、工艺参数实现各种不同形式的加工。
3.数控机床的自动化程度数控机床实现自动化生产的程度取决于数控系统的功能。
高级数控机床具有自动换刀、自动测量、自动校正等功能。
五、数控技术的发展趋势1.智能化随着人工智能、大数据等技术的发展,数控技术将更加智能化,能够自动学习和调整加工参数,实现更高效、更稳定的加工。
数控知识点总结大全集
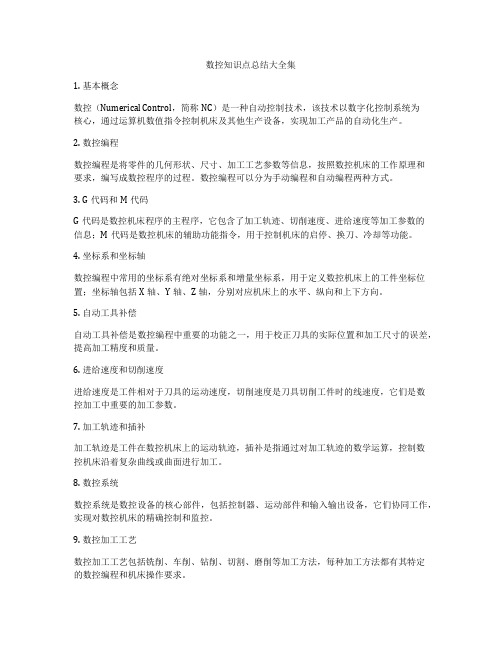
数控知识点总结大全集1. 基本概念数控(Numerical Control,简称NC)是一种自动控制技术,该技术以数字化控制系统为核心,通过运算机数值指令控制机床及其他生产设备,实现加工产品的自动化生产。
2. 数控编程数控编程是将零件的几何形状、尺寸、加工工艺参数等信息,按照数控机床的工作原理和要求,编写成数控程序的过程。
数控编程可以分为手动编程和自动编程两种方式。
3. G代码和M代码G代码是数控机床程序的主程序,它包含了加工轨迹、切削速度、进给速度等加工参数的信息;M代码是数控机床的辅助功能指令,用于控制机床的启停、换刀、冷却等功能。
4. 坐标系和坐标轴数控编程中常用的坐标系有绝对坐标系和增量坐标系,用于定义数控机床上的工件坐标位置;坐标轴包括X轴、Y轴、Z轴,分别对应机床上的水平、纵向和上下方向。
5. 自动工具补偿自动工具补偿是数控编程中重要的功能之一,用于校正刀具的实际位置和加工尺寸的误差,提高加工精度和质量。
6. 进给速度和切削速度进给速度是工件相对于刀具的运动速度,切削速度是刀具切削工件时的线速度,它们是数控加工中重要的加工参数。
7. 加工轨迹和插补加工轨迹是工件在数控机床上的运动轨迹,插补是指通过对加工轨迹的数学运算,控制数控机床沿着复杂曲线或曲面进行加工。
8. 数控系统数控系统是数控设备的核心部件,包括控制器、运动部件和输入输出设备,它们协同工作,实现对数控机床的精确控制和监控。
9. 数控加工工艺数控加工工艺包括铣削、车削、钻削、切割、磨削等加工方法,每种加工方法都有其特定的数控编程和机床操作要求。
10. 数控机床类型数控机床主要包括数控车床、数控铣床、数控磨床、数控切割机、数控车削加工中心等类型,它们适用于不同的加工工件和工艺要求。
11. 数控机床适用范围数控机床广泛应用于模具制造、航空航天、汽车制造、船舶建造、电子设备制造等行业,为工业生产和制造业提供高效、精密的加工解决方案。
数控技术知识点

数控技术知识点数控技术作为现代制造业中的重要组成部分,已经成为提高生产效率和产品质量的重要手段。
数控技术的应用范围日益广泛,对于制造业的发展起着至关重要的作用。
下面将介绍一些数控技术的知识点。
一、数控系统的基本构成数控系统主要由数控设备、数控程序、数控执行系统和输入输出设备等组成。
数控设备包括数控主机和外围设备,数控程序是控制加工过程的程序指令,数控执行系统负责接收数控程序并控制机床进行加工,输入输出设备包括键盘、显示屏等。
二、数控系统的工作原理数控系统通过接收数学模型和加工过程参数等输入,将其转换为相应的程序指令,经过数控主机进行处理后,通过数控执行系统控制机床进行自动加工。
数控系统具有高精度、高效率的特点,提高了生产制造的精度和效率。
三、数控编程数控编程是指根据零件的图样和工艺要求,编写数控加工程序的过程。
数控编程包括手工编程和自动编程两种方式,手工编程需要编程人员具备较强的数学基础和编程能力,而自动编程则由专门的软件进行生成。
四、数控加工工艺数控加工是指通过数控系统控制机床进行加工,包括铣削、钻孔、车削、磨削等多种加工工艺。
数控加工具有高精度、高质量和高效率的特点,广泛应用于航空航天、汽车制造、模具加工等行业。
五、数控机床分类数控机床根据其加工方式和结构特点可分为铣床、车床、磨床、钻床等多种类型。
不同类型的数控机床适用于不同的加工要求,能够实现各种零件的精密加工。
六、数控系统的应用领域数控技术在机床制造、汽车制造、航空航天等领域得到广泛应用,有效提高了生产效率和产品质量。
随着科技的发展,数控技术将继续发展壮大,推动着制造业的进步。
综上所述,数控技术是现代制造业中不可或缺的重要技术,掌握数控技术知识点对于提高生产效率和产品质量具有重要意义。
希望以上内容能为您对数控技术有更深入的了解。
《数控原理与系统》第4章__伺服驱动系统
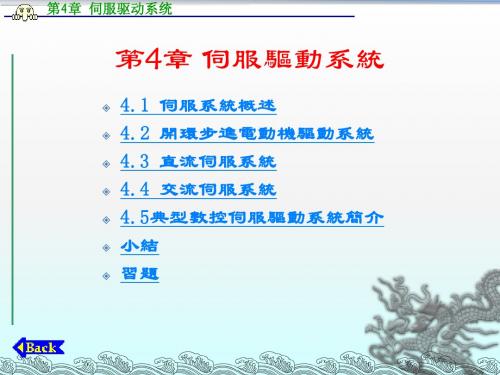
第4章 伺服驱动系统
4.2.1 步進電動機 1. 步進電動機的特點 步進電動機是一種將電脈衝信號 轉換成相應角位移的機電執行元件。給 一個電脈衝信號,步進電動機就回轉一 個固定的角度,稱為一步,所以稱為步 進電動機。由於其轉動角度由脈衝個數 控制,不需要回饋環節,所以在經濟型 數控機床上得到了廣泛的應用。概括起 來步進電機具有如下優點:
第4章 伺服驱动系统
第4章 伺服驅動系統
4.1 伺服系統概述 4.2 開環步進電動機驅動系統 4.3 直流伺服系統 4.4 交流伺服系統 4.5典型數控伺服驅動系統簡介 小結 習題
第4章 伺服驱动系统
4.1 伺服系統概述
1. 基本概念 伺服(Servo)系統又叫隨動系統, 是一種能 夠跟隨指令信號的變化而動作的自動控制裝置, 根據實現方法不同, 可以分為機械隨動(仿形) 系統、 液壓伺服系統、 電氣伺服系統等, 目前 的數控機床均採用電氣伺服系統。
第4章 伺服驱动系统
在數控機床中,CNC裝置是發佈命令的“大 腦”, 而伺服系統則是數控機床的“四肢”, 是一種執行機構, 它能夠準確地執行來自 CNC 裝置的運動指令。 伺服系統由伺服驅動裝置、伺服電動機、位 置檢測裝置等組成。伺服驅動裝置的主要功能是 功率放大和速度調節,將弱信號轉換為強信號, 並保證系統的動態性能;伺服電動機用來將電能 轉換為機械能,拖動機械部件移動或轉動。
第4章 伺服驱动系统
半閉環伺服系統一般將位置檢測元件安裝在電動機 軸上(一般電機生產商已裝好),用以精確控制電動機的角 度,然後通過滾珠絲杠等傳動機構,將角度轉換成工作臺 的直線位移。半閉環的閉環環路短,不包括傳動機構等大 慣性環節,因而系統容易達到較高的位置增益,不發生振 盪現象。且其快速性好,動態精度高,傳動機構的非線性 因素對系統的影響小。因此被廣泛採用。但如果傳動機構 的誤差過大或其誤差不穩定,則數控系統難以補償。如由 傳動機構的扭曲變形所引起的彈性間隙,因其與負載力矩 有關,故無法補償。由製造與安裝所引起的重複定位誤差 以及由於環境溫度與絲杠溫度變化所引起的絲杠螺距誤差 也是不能補償的。因此要進一步提高精度,只有採用全閉 環控制方式。
数控系统原理介绍

数控系统原理介绍数控系统原理介绍数控系统是一种在机床加工或其他工业领域中使用的先进加工工具,可以大大提高生产效率和制造质量。
数控系统是由软件和硬件两部分组成,它的核心部分是控制器。
控制器通过图形化界面、编程语言和运算器等方式,将计算机程序转化为机器指令,控制机床进行加工操作。
下面我们来介绍数控系统的原理。
一、数控系统的基本组成数控系统由五大基本部分组成:电源系统、机床及工作台部分、传感器及执行器部分、数控装置及软件系统部分、执行机构。
电源系统提供所需的电源电压和电流,以保证数控系统运行所需的稳定电力供应。
机床及工作台部分是数控系统的重要组成部分,包括各类机床、传动装置、定位装置、夹紧装置、转载装置和其他辅助装置等,用于在不同的加工条件下完成加工操作。
传感器及执行器部分包括各种传感器和执行器,能够对各种物理量进行测量和控制。
数控装置及软件系统部分是数控系统的核心部分,由计算机、处理器、输入输出设备组成,主要负责进行控制指令的运作和数据传输。
执行机构包括各种驱动装置和执行机构,如步进电机、伺服电机等,主要用于控制零件的移动位移和加工力度。
二、数控系统的基本工作原理数控系统的基本工作原理是通过输入控制指令,驱动执行机构完成零件的加工操作。
首先,根据工件的设计图纸,制定数控程序。
数控程序一般采用高级编程语言,比如G代码和M代码。
G代码用于描述加工轨迹,M代码用于控制机床运行状态。
接下来,将数控程序输入电脑,通过计算机进行处理和解析。
计算机将程序转换为机器指令,并将其发送到数控装置。
数控装置根据指令的类型和内容,对执行机构进行控制,并将指令转换成相应的控制信号送给执行机构。
执行机构接收信号后,根据指令进行动作,控制零件的受力和轨迹,实现零件的加工操作。
加工过程中,传感器可以实时的监测加工状态,并将监测结果反馈给数控装置,以便下一步的程序控制。
最后,加工完成后,数控系统自动停机,操作人员可以通过电脑或连接到数控机床的监视系统对加工质量进行检查,以确保零件符合要求。
《数控原理与系统》第5章_进给运动的控制
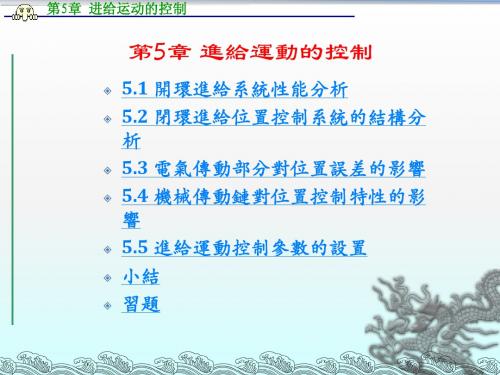
第5章 进给运动的控制
5.1 開環進給系統性能分析
由於開環進給系統中沒有位臵回饋檢 測裝臵,其前向通道中的各種誤差就無法 通過回饋資訊來加以補償,從而會引起輸 出位臵誤差。因此,需要找出造成輸出位 臵誤差的主要因素,並採取一些必要的措 施來加以改善,從而提高系統的控制性能。
第5章 进给运动的控制
第5章 进给运动的控制
3. 數學模型的構成 (1) 跟隨誤差E。 跟隨誤差E實際 上就是指令位臵Xi與實際位臵Xf的差值。 (2) 開環增益K。 K為整個系統的 開環增益, K=Kv Kda KmKa(1/s), 其中:
第5章 进给运动的控制
· Kv為位臵放大係數(軟體增益), 它是由 CNC內部的參數設臵的, 單位為數字/數字。 可 通過設臵Kv值來調整整個回路的開環增益。 · Kda為數模轉換係數。 CNC裝臵通過DAC 數模轉換器輸出-10~+10 V的電壓來控制伺服電 動機的運動。 Kda的單位為V/數字, 它描述了 CNC內每一個數值“1”對應的電壓值。 開環增益K是決定整個系統性能的重要參數, 在機床調試時需進行調整。由上可以看出,當設 備選定後,調整開環增益的唯一方法就是調整軟 體增益KV和伺服放大倍數Km。
第5章 进给运动的控制
第5章 进给运动的控制
(2)選用高性能的驅動裝臵。選用性能好,與 步進電機匹配的驅動裝臵,可有效地改善步進電 機的動態性能,防止失步和震盪。此外,也可選 用帶細分的驅動裝臵,以提高進給解析度。 (3)合理的進行補償。根據齒隙誤差的特點, 當工作臺運動方向改變時可利用CNC裝臵的間隙 補償功能進行補償;對於滾珠絲杠的螺距誤差, 可利用CNC裝臵的螺距誤差補償功能進行校正。
数控机床数控原理与系统课件

码后4位十进制来指定主轴转速。 ➢ 3. T功能的实现 ➢ T功能即刀具功能,T代码后跟随2-5位数字表示刀具号和
刀具补偿号。图5-23所示为采用固定存取换刀控制方式 的T功能处理框图。
返回
上页
下页
➢ 数控机床中独立型PLC本身是一个控制器,是一个完 整的系统。其特点是使用灵活;要进行PLC与CNC装置 I/O联结,控制功能更强大。
返回
上页
下页
图5-22 内装型PLC的CNC框图
返回
上页
下页
5.5 辅助机能控制与PLC
➢ 四、M、S、T功能的实现 ➢ 1. M功能的实现 ➢ M 功能又称辅助功能,其代码用“M”后跟2位数表示。
命令。
返回
上页
下页
5.4数控系统的接口
▪ 一、接口解决的问题
➢ 从功能角度去分,接口电路解决的问题有两类。 ➢ 1. 单台机床内部各部件之间的信息交换问题 ➢ 2. 机床与机床之间或机床与计算机之间的信息交换问题。
▪ 二、接口分类规范
“机床/数控接口”国际标准指出了数控装置,电气控制设备与机床 之间的接口范围,他们共分为四类,如图5-17. ➢ A、B类接口交换的信息是数控装置与驱动电动机,位置、速度检测 之间的控制信号。
(1)减法计算 ▪ 在位置计数器中预置给定的位移量,坐标移动时进行减 法计算。
(2)比较计算 ▪ 将给定的位移量存入指令寄存器,坐标移动时位置计数 器以零开始进行加法计算,两者相比较,在计数值与给 定值相符时停止进给。 ▪ 位置计算与比较的软件控制流程如图5-8所示
- 1、下载文档前请自行甄别文档内容的完整性,平台不提供额外的编辑、内容补充、找答案等附加服务。
- 2、"仅部分预览"的文档,不可在线预览部分如存在完整性等问题,可反馈申请退款(可完整预览的文档不适用该条件!)。
- 3、如文档侵犯您的权益,请联系客服反馈,我们会尽快为您处理(人工客服工作时间:9:00-18:30)。
CH11.数控是数字控制系统的简称:广义上讲,是指利用数字化信息实行控制,也就是利用数字控制技术实现的自动控制系统,其被控对象可以是各种生产过程。
狭义上理解,是利用数字化信息对机床轨迹和状态实行控制。
2.计算机数字控制系统都是由输入、决策、输出组成。
C:计算机数控系统。
PLC:可编程逻辑控制器。
DNC:分布式数字控制系统。
CIMS:计算机集成制造系统。
FMC:柔性制造单元。
FMS:柔性制造系统。
CAD:计算机辅助设计。
CAM:计算机辅助制造。
CAPP:计算机辅助工艺过程设计。
CAQ:计算机辅助质量管理。
MAP:制造自动化协议。
LAN:工业局域网络。
ISO:国际标准化组织。
WOP:面向车间的编程系统。
MRP:物料需求计划。
ERP:企业资源规划。
TCP/IP:传输控制协议/网际协议。
4.数控装置是数控系统的核心,主要功能:正确识别和解释数控加工程序,对解释结果进行各种数据计算和逻辑判断处理,完成各种输入、输出任务。
5.数控机床右手坐标系,确定坐标系时一律看做工件相对静止而刀具产生运动,还规定增大刀具与工件之间距离的方向为正方向。
6.数控系统分类:(1)按数控机床运动轨迹分①点位数控系统②直线数控系统③轮廓数控系统(2)按数控机床伺服系统分①开环数控系统②全闭环数控系统③半闭环数控系统7.数控系统的主要任务是进行刀具和工件之间相对运动的控制,通电后对机床各组成部分工作状态进行检查和诊断,并设置初始状态。
8.数控系统软件实现对输入的数控加工程序进行译码,刀补处理及插补运算等。
硬件和各功能程序的接口是由数控系统的管理软件实现的。
9.现代机械制造系统中,生产率和柔性是系统自动化程度的两个主要因素CH21.输入方式包括光电式纸带阅读机输入,键盘方式输入,存储器方式输入和通信方式输入。
2.键盘分为全编码键盘(指由硬件逻辑直接提供被按键相应的ASCII码或其他编码的键盘)和非编码键盘(只提供行列矩阵位置)。
3.通信是指计算机与计算机或计算机与外部设备间的信息交换。
4.ISO与EIA代码大致分为数字码,字母码和功能码三大类。
5.译码的过程主要包括代码识别和功能码翻译两大部分。
6.功能码翻译过程:①建立一个与数控加工程序缓冲器相对应的译码结果缓冲器②考虑缓冲器规模③约定存储格式。
7.由于准备功能代码G(6组)和辅助功能代码M(4组)具有互斥性,因此可按功能分组。
8.数控加工程序诊断是指CNC装置在程序输入或译码过程中对不规范的指令格式进行检查,监控及处理的服务操作,其目的是防止错误代码的读入。
9.语法错误:是指程序段格式或程序字格式不规范的错误。
逻辑错误:是指整个数控加工程序或一个程序段中功能代码之间相互排斥,互相矛盾的错误。
10.刀具补偿:刀具实际参与切削的部分是刀尖或刀刃边缘。
它们与刀具中心或刀架参考点之间存在偏差,因此需要通过数控系统计算偏差量并将控制对象由刀具中心或刀架参考点变换到刀尖或刀刃边缘上,以满足加工需求。
11.刀具中心轨迹始终在编程轨迹的左边时称为左刀补G41,在右边为右刀补G42。
12.刀具半径补偿执行过程①刀具半径补偿建立②刀具半径补偿进行③刀具半径补偿撤销CH31.脉冲增量(行程标量)插补算法是通过向各个运动轴分配脉冲,控制机床坐标轴相互协调运动,从而加工出一定轮廓形状的算法。
2.数据采样(时间标量)插补算法是根据数控加工程序编写的进给速度,先将零件轮廓曲线插补周期分割为一系列首尾相连的微小直线段,然后输出这些微小直线段对应的位置数据增量,用以控制伺服系统实现坐标轴的进给。
与脉冲增量插补算法相比数据采样插补算法结果不再是单个脉冲,而是位置增量的数字量。
3.逐点比较法四个工作节拍①偏差判别②坐标进给③偏差计算④终点判别。
4.终点判别方法①总步长法②投影法③终点坐标法。
5.为使圆弧插补能够自动过象限可采用①绝对坐标值法②代数坐标值法。
6.与直线插补相比,数字积分法(DDA)圆弧插补的不同①被积函数寄存器与坐标轴关联关系不同②被积函数寄存器存放的数据形式不同。
7.左移规格化:就是将被积函数寄存器中存放的坐标值前i位零移出寄存器,并使之成为最高位或次高位为“1”得规格化数,然后再进行累加从而达到稳定进给速度的目的。
8.数据采样法:利用一系列首尾相连的微小直线段逼近给定曲线(时间分割法)。
9.通常取插补周期T S≥T C位置控制周期。
10.插补误差e r,即T S越长,F越大,R越小,圆弧插补误差越大,反之,误差越小。
CH41.数控机床用伺服驱动装置分为开环和闭环两大类。
开环控制系统采用步进电机作为驱动元件,无位置反馈回路和速度控制回路,但进给速度和精度较低。
闭环控制系统分为半闭环和全闭环,采用直流或交流伺服电机驱动,半闭环:快速性好,动态精度高,传动机构的非线性因素对系统影响小,但如果传动系统误差过大或其误差不稳定,则数控系统难以补偿。
全闭环不受机械传动精度影响。
2.直流伺服电机的工作区域分三部分,连续工作区(转矩转速任意组合都可长期连续工作),间断工作区(电动机可根据附在周期曲线决定允许的工作时间与断电时间做间歇工作),瞬时加减速区(电动机只能在加减速时工作于其中,只能在该区域工作极短的一段时间)。
3.步进电动机分类①运动方式:旋转、平面、直线、滚切运动式②转矩产生原理:反应式、永磁式、永磁感应式(混合式)③输出转矩大小:伺服式、功率式④结构:单段式(径向式)、多段式(轴向式)、印制绕组式⑤相数:二、三、四、五、六相⑥使用频率:高频、低频。
4,步进电动机特点:①送给步进电动机定子绕组一个电流脉冲,其定子就转过一个角度,并称之为步距角θ②有脉冲就走无脉冲则停③随脉冲数增加角位移量增加④脉冲频率越高电机转速越快⑤脉冲变化太快会引起失步或过冲⑥改变分配脉冲的相序可改变电动机旋转方向⑦运行状态是步进式⑧定子绕组所加电源要求是脉冲电流形式⑨输出转角精度高,并且一般只有相邻误差而无累积误差。
5.脉冲分配器作用:是将插补输出脉冲按步进电动机所要求的规律分配给步进电动机驱动电路的各相输入端,用以控制绕组中电流的开通与关断。
6.步进电动机自动升降速的方法分为定时法和定步法。
7.精度分析。
8.数控系统位置控制的任务是准确控制数控机床各坐标轴的位置。
9.误差分析。
10.三环系统:电流环,速度环及位置环。
11.传动反转间隙补偿,螺距误差补偿。
CH51.主轴无级变速作用:要求主轴在整个范围内均能提供切削所需的功率,并尽可能在全速度范围内提供主轴电机最大功率。
即恒功率范围要宽,为满足数控机床低速强力切削需求,采用分段无级变速。
如何实现:数控机床变速是依指令自动进行的,在低速段采用机械减速装置。
2.两种常用的换挡方法:液压拨叉和电磁离合器。
3.主轴准停:为满足加工中心自动换刀以及某些加工工艺的需求,要求主轴具有高精度的准停控制。
机械控制方法:V型槽轮定位盘准停结构,端面螺旋凸轮准停等。
4.脉冲编码器:是精密数字控制系统与伺服控制设备中常用的角位移数字化检测器件,具有高精度结构简单工作可靠等优点。
编码器可分为增量式和绝对式、接触式和非接触式(光电式、电磁式)5.增量式脉冲编码器,指脉冲发生器每次测量的角位移都是相对于上一次角度位置的增量。
CH61.数控系统内部处理信息分为①连续数字信息(控制坐标轴运动)②逻辑离散信息(刀具更换,主轴准停等)2.PLC组成由中央处理器CPU,存储器,输入输出单元,编程器,电源和外部设备等,内部通过总线相连。
3.存储器主要用于存放系统程序,用户程序和工作数据。
4.编程器是用来开发,调试,运行程序的特殊工具,一般由键盘、显示器、智能处理器、外部设备(如硬盘/软盘驱动器等)组成,通过通信接口与PLC相连。
5.PLC基本软件包括系统软件和用户应用软件。
系统软件一般包括操作系统,语言编译系统以及各种功能软件等。
6.采用PLC实现控制时可分为内装型和独立型。
内装型:指PLC内含在CNC装置内,PLC 的硬件和软件都被作为CNC系统的基本功能统一设计,并且其性能指标也由CNC系统确定。
独立型:实际上是一个通用型PLC,完全独立于CNC装置,具有完备的硬件和软件,能够独立完成CNC系统所要求的控制任务。
总的来讲,独立型多用于多微处理器CNC,内装型多用于单微处理器CNC,作用是配合CNC装置实现刀具轨迹控制和机床顺序控制。
7.数控系统中PLC的信息交换就是指以PLC为中心,在CNC、PLC之和机床之间信息传递。
8.S功能主要完成主轴转速的控制,并且常用S2位代码形式和S4位代码形式来进行编程。
S2代码编程是指S代码后跟随2位十进制数字来指定主轴转速。
S4试制4位十进制数。
9.根据取/还刀位置是否固定可将换刀功能分为随机存取换刀控制和固定存取换刀控制。
CH71.数控系统为用户提供的接口从功能上分①数控装置与上位系统的接口②数控装置与用户间交互设备的接口③数控装置与下位系统的接口。
上位系统是DNC系统、FMS或CIM系统的单元或上位计算机。
下位系统指驱动器和执行机构、传感器和机床控制器。
2.数控装置是整个系统的核心①其硬件结构按CNC装置中各印制电路板插接方式不同分为大板式结构和功能模块式结构②按硬件制造方式不同可分为专用型结构和个人计算机式结构③按CNC装置中微处理器个数不同可分为单微和多微处理器结构。
3.单微处理器结构,CNC装置的功能将受微处理器的字长、数据宽度、寻址能力和运算速度等因素的影响和限制。
提高速度措施:①采用高性能处理器②采用协处理器来增强运算功能,提高运算处理速度③采用大规模集成电路完成一些实时性要求高的任务,如插补计算和位置控制④采用带微处理器的CRT控制和PLC等智能部件。
4.多微处理器结构:主从式系统,总线式多主CPU系统和分布式系统。
5.典型I/O模板电路由总线接口逻辑,输入缓冲器和输出缓冲器三部分组成。
6.每进行一次数据传输都要三个阶段①建立电路阶段②交换数据阶段③释放电路阶段。
C装置是一个计算计算机控制系统,其数控系统软件必须完成管理和控制两种任务。
C装置系统软件具有多任务型和实时性两大特点。
9.并行处理:指计算机在同一时刻或同一时间间隔完成两种或以上性质相同或不同的工作。
10.实时:在一个确定的有限时间里对外部产生的随机事件作出响应,并在确定的时间里完成这种响应或处理。
11.软件总体结构①前后台型软件结构②多重中断型软件结构③功能模块型软件结构。
12.软件开发阶段①定义期②开发期③使用维护期13.常见的用户界面操作形式:程序控制界面,数据输入界面和交互输入界面。
14.监测过程包括状态获取和状态比较两方面。
15.对机床有关机械部件的诊断有:各种液压、气压及温度阀检查,刀具专用夹具检查,导轨检查。
在高速机床中还要对承受大负载的部件(联动装置和主轴轴承)进行检查等。