浅析现代机械加工质量技术控制
机械加工质量的技术控制
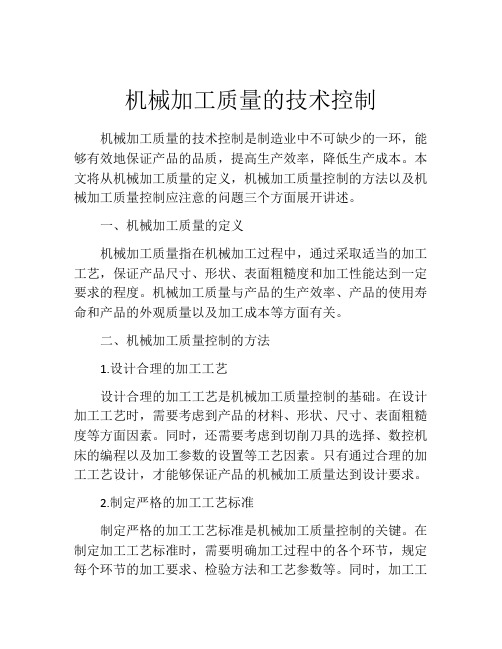
机械加工质量的技术控制机械加工质量的技术控制是制造业中不可缺少的一环,能够有效地保证产品的品质,提高生产效率,降低生产成本。
本文将从机械加工质量的定义,机械加工质量控制的方法以及机械加工质量控制应注意的问题三个方面展开讲述。
一、机械加工质量的定义机械加工质量指在机械加工过程中,通过采取适当的加工工艺,保证产品尺寸、形状、表面粗糙度和加工性能达到一定要求的程度。
机械加工质量与产品的生产效率、产品的使用寿命和产品的外观质量以及加工成本等方面有关。
二、机械加工质量控制的方法1.设计合理的加工工艺设计合理的加工工艺是机械加工质量控制的基础。
在设计加工工艺时,需要考虑到产品的材料、形状、尺寸、表面粗糙度等方面因素。
同时,还需要考虑到切削刀具的选择、数控机床的编程以及加工参数的设置等工艺因素。
只有通过合理的加工工艺设计,才能够保证产品的机械加工质量达到设计要求。
2.制定严格的加工工艺标准制定严格的加工工艺标准是机械加工质量控制的关键。
在制定加工工艺标准时,需要明确加工过程中的各个环节,规定每个环节的加工要求、检验方法和工艺参数等。
同时,加工工艺标准还需要明确加工误差控制的精度范围和控制方法,以确保产品的加工精度和形状稳定性。
3.采用先进的检测设备采用先进的检测设备是机械加工质量控制的必要条件。
检测设备包括测量仪器、光学检测设备和测试设备等。
通过使用先进的检测设备,可以实现对加工过程中所有关键参数的准确测量和分析,及时发现问题并及时进行纠正,确保产品的加工质量。
三、机械加工质量控制应注意的问题机械加工质量控制应注意以下问题:1.及时发现并解决制造过程中存在的问题,避免不良品的制造和提高生产的效率。
2.执行标准化的操作过程,使操作员对加工过程掌握得更加全面,同时加强对产品质量的控制。
3.加强质量保证体系建设,确保质量保证体系的规范和稳定;合理利用现有资源,全面提高加工质量。
4.通过制定自主创新的管理流程,推广自主品牌的先进技术和管理方法,全面提高产品的加工质量。
机械加工质量分析及控制范文精简处理

机械加工质量分析及控制范文精简处理摘要:机械加工质量是制造业生产中的重要环节,直接影响着产品的质量和性能。
本文通过对机械加工质量的分析,提出了相应的控制措施,以提高产品的加工质量。
关键词:机械加工;质量分析;控制措施一、引言机械加工是制造业生产过程中重要的工序之一,机械零件的加工质量直接影响着产品的质量和性能。
因此,对机械加工质量进行分析,并采取相应的控制措施,是保证产品质量的关键。
二、机械加工质量分析1.加工工艺分析加工工艺是影响加工质量的重要因素,包括刀具选择、切削速度、进给速度等。
通过分析加工工艺的合理性,可以找出存在的问题,并提出改进意见。
2.加工设备分析加工设备的性能和精度直接影响着机械加工的质量。
针对设备存在的问题,可以采取相应的控制措施,以提高加工质量。
3.加工材料分析加工材料的性能决定了加工质量的上限。
通过分析加工材料的性能及其与加工工艺的匹配性,可以确定最佳的加工参数,以提高加工质量。
三、机械加工质量控制1.加强工艺控制通过调整刀具选择、切削速度和进给速度等工艺参数,可以有效地控制机械加工的质量。
此外,建立科学的工艺规程并进行培训,提高操作人员的技能水平,也是保证加工质量的重要手段。
2.提高设备精度定期对加工设备进行维护和保养,保证设备的精度稳定性。
对于存在问题的设备,及时进行维修和更换,确保加工质量的可控性。
3.优化加工材料选择合适的加工材料,提高材料的性能,以满足产品的工艺要求。
此外,对加工材料进行严格的检验和控制,确保加工质量的稳定性。
四、结论通过机械加工质量的分析和控制,可以提高产品的质量和性能,提高企业的竞争力。
机械加工质量的分析和控制是制造业生产中非常重要的环节,需要工程师和技术人员共同努力,不断改进和创新。
[1]张三.机械加工质量分析及控制[J].机械工程学报,2024[2]李四,王五.机械加工质量控制的方法与技巧[M].北京:机械工业出版社。
机械加工质量分析及控制精简版范文
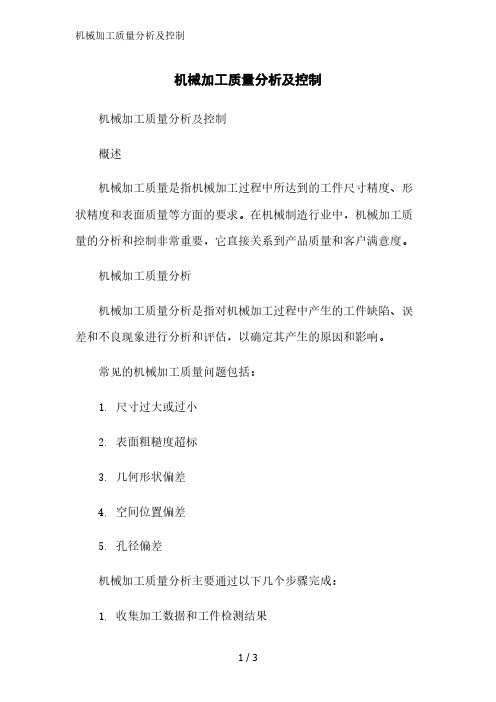
机械加工质量分析及控制
机械加工质量分析及控制
概述
机械加工质量是指机械加工过程中所达到的工件尺寸精度、形状精度和表面质量等方面的要求。
在机械制造行业中,机械加工质量的分析和控制非常重要,它直接关系到产品质量和客户满意度。
机械加工质量分析
机械加工质量分析是指对机械加工过程中产生的工件缺陷、误差和不良现象进行分析和评估,以确定其产生的原因和影响。
常见的机械加工质量问题包括:
1. 尺寸过大或过小
2. 表面粗糙度超标
3. 几何形状偏差
4. 空间位置偏差
5. 孔径偏差
机械加工质量分析主要通过以下几个步骤完成:
1. 收集加工数据和工件检测结果
2. 对数据进行统计分析和图像处理
3. 利用统计分析结果,确定质量问题的原因和影响因素
4. 提出相关改善措施和加工优化建议
机械加工质量控制
机械加工质量控制是指通过控制加工参数和采用合理的加工工艺,确保机械加工过程中所达到的工件质量能够满足设计要求和客户需求。
常见的机械加工质量控制方法包括:
1. 控制加工参数,如刀具刃口半径、加工速度、进给量等
2. 采用合适的加工工艺,如铣削、车削、钻削等
3. 使用高精度的测量设备进行质量检测和纠正
4. 实施质量管理体系和质量控制标准
机械加工质量控制的关键在于不断优化和改进加工工艺、设备和管理体系,以提高加工稳定性和质量可靠性。
结论
机械加工质量分析和控制是机械制造过程中必不可少的环节,它直接关系到产品的质量和市场竞争力。
通过科学的分析和有效的
控制措施,能够提高机械加工的质量稳定性和可靠性,满足客户的需求。
机械加工质量分析及控制

机械加工质量分析及控制机械加工质量分析及控制一、引言二、机械加工质量分析机械加工质量的分析主要包括以下几个方面:1.表面粗糙度分析机械加工的表面粗糙度对于产品的外观和性能有着重要影响。
通过使用表面粗糙度测量仪器,可以对机械加工的表面粗糙度进行评估。
常用的表面粗糙度参数包括Ra、Rz等。
2.尺寸精度分析机械加工的尺寸精度是指产品的实际尺寸和设计图纸上的尺寸之间的偏差。
通过使用测量工具和仪器,可以对机械加工的尺寸精度进行评估。
常用的尺寸精度参数包括公差、尺寸偏差等。
3.形状偏差分析机械加工的形状偏差是指产品的实际形状和设计图纸上的形状之间的偏差。
通过使用形状测量仪器,可以对机械加工的形状偏差进行评估。
常用的形状偏差参数包括圆度误差、平面度误差等。
三、机械加工质量控制为了确保机械加工的质量,需要进行相应的控制措施。
以下是几个常用的机械加工质量控制方法:1.工艺参数控制调整机械加工的工艺参数,可以对机械加工的质量进行控制。
例如,通过调整切削速度、进给速度和切削深度等参数,可以控制机械加工的表面粗糙度和尺寸精度。
2.设备状态监控对机械加工设备的状态进行监控,可以及时发现并修复设备故障,避免对产品质量的影响。
常用的设备状态监控方法包括振动监测、温度监测等。
3.质量检验与统计分析对机械加工的产品进行质量检验,并进行统计分析,可以及时发现并纠正加工过程中的问题。
常用的质量检验方法包括外观检查、尺寸测量等。
四、机械加工质量的分析和控制是确保产品质量的重要手段。
通过对表面粗糙度、尺寸精度和形状偏差等进行分析,可以找出问题所在。
通过工艺参数控制、设备状态监控和质量检验与统计分析等控制措施,可以提高机械加工的质量水平。
机械加工质量分析及控制范文精简处理

机械加工质量分析及控制机械加工质量分析及控制1. 引言机械加工是制造业中常见的一种工艺,通过加工原材料,将其转变为具有特定形状和尺寸的零部件或产品。
机械加工的质量直接影响着产品的精度、功能和可靠性,对机械加工质量的分析和控制至关重要。
2. 机械加工质量分析机械加工质量分析是对加工过程和成品进行评估和检测,旨在发现和解决制约加工质量的问题。
常见的机械加工质量分析方法包括以下几种:2.1 表面粗糙度分析表面粗糙度是衡量零部件表面光滑度的重要指标,直接影响着零部件的摩擦、密封和耐磨性能。
通过使用表面粗糙度测量仪器,可以对机械加工过程中的加工参数和刀具磨损情况进行分析,以及对成品的表面粗糙度进行评估和检测。
2.2 尺寸误差分析尺寸误差是指零部件和产品在尺寸上与设计要求的偏差。
通过使用高精度测量设备,可以对机械加工过程中的尺寸变化进行分析,包括线性尺寸、形状尺寸和位置尺寸等。
通过分析尺寸误差的来源,可以找出加工过程中可能存在的问题,并进行相应的调整和控制。
2.3 成品检测分析成品检测是对加工后的零部件和产品进行全面检测的过程,以确保其质量符合设计和客户要求。
常见的成品检测方法包括外观检测、尺寸检测、力学性能检测和材料成分分析等。
通过成品检测分析,可以发现加工过程中的缺陷和不良问题,并采取相应的措施进行修复或改善。
3. 机械加工质量控制机械加工质量控制是通过制定和执行一系列控制措施,对机械加工过程和成品质量进行管理和控制的过程。
常见的机械加工质量控制措施包括以下几种:3.1 加工工艺优化通过对加工过程中的加工参数和刀具选择等进行优化,以达到最佳的加工效果和质量。
通过使用数控机床和CAD/CAM软件等先进设备,可以实现加工工艺的优化和自动化控制。
3.2 刀具管理与磨损监测刀具是机械加工过程中的重要工具,其磨损情况直接影响加工质量。
通过建立刀具管理制度和定期对刀具进行检测和磨损监测,可以及时发现和更换磨损严重的刀具,保证加工质量的稳定和一致性。
机械加工质量分析及控制
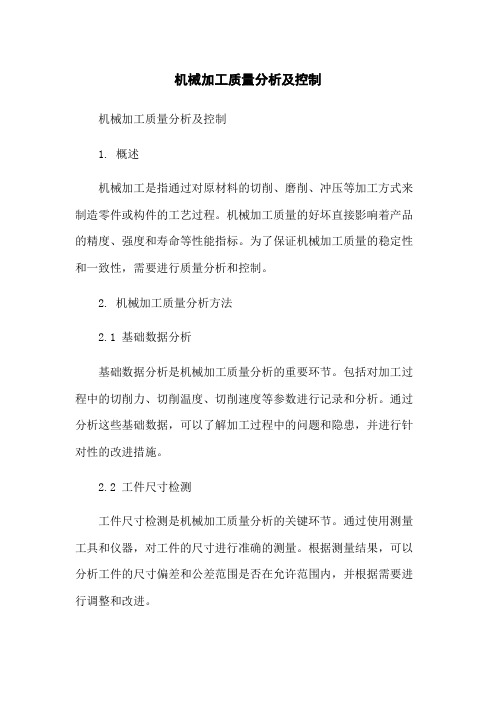
机械加工质量分析及控制机械加工质量分析及控制1. 概述机械加工是指通过对原材料的切削、磨削、冲压等加工方式来制造零件或构件的工艺过程。
机械加工质量的好坏直接影响着产品的精度、强度和寿命等性能指标。
为了保证机械加工质量的稳定性和一致性,需要进行质量分析和控制。
2. 机械加工质量分析方法2.1 基础数据分析基础数据分析是机械加工质量分析的重要环节。
包括对加工过程中的切削力、切削温度、切削速度等参数进行记录和分析。
通过分析这些基础数据,可以了解加工过程中的问题和隐患,并进行针对性的改进措施。
2.2 工件尺寸检测工件尺寸检测是机械加工质量分析的关键环节。
通过使用测量工具和仪器,对工件的尺寸进行准确的测量。
根据测量结果,可以分析工件的尺寸偏差和公差范围是否在允许范围内,并根据需要进行调整和改进。
2.3 表面质量检测表面质量检测是机械加工质量分析的另一个重要环节。
通过使用光学显微镜、电镜等仪器,对工件的表面质量进行检测和评估。
根据检测结果,可以分析工件的表面光洁度、粗糙度等指标是否符合要求,并采取相应的措施进行改进。
3. 机械加工质量控制方法3.1 设备维护与管理机械加工设备的维护和管理对于保证加工质量非常重要。
定期对设备进行保养和检修,确保设备的正常运行和准确性。
,使用合适的刀具和夹具,并正确地安装和调整,可以有效地控制加工质量。
3.2 加工工艺优化加工工艺的优化也是机械加工质量控制的重要手段之一。
通过对工艺参数的调整和优化,可以实现加工质量的提高和降低加工成本。
例如,通过合理地选择切削速度、进给速度和切削深度等参数,可以控制加工过程中的热变形和切削力,提高加工质量。
3.3 质量管理体系建立建立质量管理体系是机械加工质量控制的基础。
通过制定加工工艺规范和质量控制标准,并进行员工培训和绩效评估,可以确保加工质量的稳定性和一致性。
,定期进行质量审核和改进,提高质量管理水平。
4. 结论机械加工质量的分析和控制是保证产品质量的重要环节。
论如何做好机械加工质量技术控制

按 下 关 闭按 钮 , 门 立刻 关 闭 , 舱 然后 迅 速 进入 第 二层 舱 门 简 单 自救 , 大程 度确 保人 员 的安全 以 等待 救援 。高 层 火 最 内 , 旦 有人 进 入 舱 内 , 可 以通 过 通 讯 设备 与 总控 制 室 灾逃 生 装 置 三维模 型和 舱 门 的 电器控 制 原 理 图如 图 1和 一 就 进 行 信 息 交 换 , 此期 间 , 生 员可 以利 用舱 内 设施 进 行 图 2所 示 。 在 逃
如 在 进 行 退火 、 正火 、 质 等 改 善金 属 切 削加 工 性 能 的工 调
关 键 词 : 械 加 工 精 度 误 差 机
序时 , 一般在 机 械加工 前进 行。时效 处理 、 质 处理 等是 为 调 寸 或性 能进 行标 准化 的过 程。机械加 工 按 照被加 工 的工件 了消 除 内应力 , 一般 安 排在 粗加 工 之后 , 精加 工 之前 进行 。 在加 工 状 态 时适 宜 的温度 , 为冷 加 工和 热加 工 。冷加 工 分 渗碳 、 火 、 淬 回火 等 目的 是提高 零 件 的机 械 性 能 , 一般 安 排 是 指 在 常 温 下加 工 ,并且 不 引起 产 品发 生 化 学 或 物理 变 在机 械加 工 之后 进行 。 另外 , 如果 热 处理后 工 件 出现 变形 化 。热 加 工 是指 在 高于 或低 于 常温状 态 下 , 能够 引起 产 品 的情 况 , 应 该进行 最 终加工 工序 。 还 发 生化 学 或物理 变化。热加 工 常见有热 处理 、 造 、 造和 煅 铸 2 机械 加工产 生误 差 主要原 因 焊 接 。按 加工 方 式可 分为 切削加 工和 压力 加 工。 机 械加 工 时 由于 各种 原 因使 得加 工 后 的工 件 与 标 准 1机 械加 工 的原 则 工 件 之间 出现 一定 的误 差。 在机 械加 工 中 , 误差 通常 用加 为保 证机 械 加 工 的质量 , 对机械 加 工 需要按 照一定 的 工精 度来 表示 。加 工精 度 是工件 经 过加 工后 的尺 寸、 状 形
机械加工质量分析及控制(2023版)
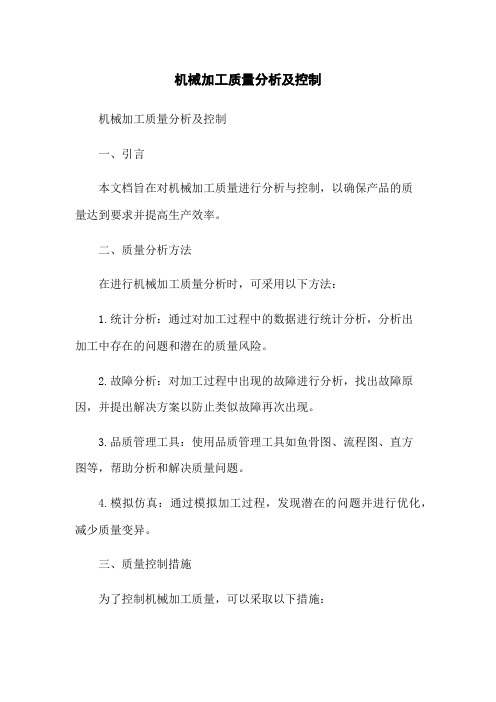
机械加工质量分析及控制机械加工质量分析及控制一、引言本文档旨在对机械加工质量进行分析与控制,以确保产品的质量达到要求并提高生产效率。
二、质量分析方法在进行机械加工质量分析时,可采用以下方法:1.统计分析:通过对加工过程中的数据进行统计分析,分析出加工中存在的问题和潜在的质量风险。
2.故障分析:对加工过程中出现的故障进行分析,找出故障原因,并提出解决方案以防止类似故障再次出现。
3.品质管理工具:使用品质管理工具如鱼骨图、流程图、直方图等,帮助分析和解决质量问题。
4.模拟仿真:通过模拟加工过程,发现潜在的问题并进行优化,减少质量变异。
三、质量控制措施为了控制机械加工质量,可以采取以下措施:1.设定合理的工艺参数:根据产品要求和机械设备的性能,设定合理的加工参数,确保产品尺寸和表面质量的稳定性。
2.加强设备维护与保养:定期对机械设备进行维护和保养,保持设备正常运行状态,避免因设备故障导致加工质量下降。
3.建立质量控制流程:制定详细的工艺流程和操作规范,对每个环节进行质量控制,及时发现和纠正质量问题。
4.培训员工:通过培训提高员工的加工技能和质量意识,使其能够按照工艺要求进行操作,并能够及时处理质量异常。
四、质量指标与评估为了对机械加工质量进行评估,可以根据以下指标进行评估:1.尺寸精度:产品加工尺寸与设计要求之间的偏差程度。
2.表面光洁度:产品表面平整度和光洁度的评估。
3.损伤率:产品在加工过程中受损的情况,如裂纹、划痕等。
4.合格率:产品在整个生产过程中的合格率。
五、质量改进措施为了不断改进机械加工质量,可以采取以下措施:1.流程优化:通过优化工艺流程和操作方法,减少质量变异和浪费。
2.技术创新:引入新的工艺和设备,提高加工精度和效率。
3.团队合作:加强团队之间的沟通和协作,共同解决质量问题,不断提升整体质量水平。
4.追溯体系:建立产品质量追溯体系,做到问题可追溯、责任可追究。
六、附件本文档涉及的附件包括:1.数据统计表2.故障分析报告3.加工工艺流程图4.品质管理工具使用示例法律名词及注释:1.质量管理体系:指企业按照相关标准和法规要求,建立和实施的质量管理体系。
机械加工质量分析及控制

机械加工质量分析及控制引言在机械制造过程中,机械加工是一项重要的工艺。
机械加工质量的好坏直接影响到制造产品的性能和可靠性。
因此,对于机械加工质量进行分析和控制是非常重要的。
本文将介绍机械加工质量的分析方法和控制措施。
机械加工质量分析1. 加工表面粗糙度分析加工表面粗糙度是评估机械加工质量的重要指标之一。
常见的评估方法包括:Ra值、Rz值、Rq值等。
通过测量和分析加工表面的粗糙度指标,可以了解加工质量是否符合设计要求,从而评估加工过程的稳定性和精度。
2. 尺寸测量与分析机械加工过程中,尺寸的精度是衡量加工质量的重要指标之一。
通过尺寸测量,可以评估加工件的尺寸精度是否满足设计要求,并分析加工误差的来源。
常用的尺寸测量方法有:千分尺、游标卡尺、三坐标测量等。
3. 加工变形分析在机械加工过程中,加工件的压力、温度等因素会引起加工变形。
加工变形会直接影响加工件的质量和尺寸精度。
通过对加工变形进行分析,可以了解加工过程中的变形规律,并采取相应的控制措施,如合理选用加工工艺和工件固定方式等,以减小加工变形。
4. 刀具磨损分析刀具磨损是机械加工过程中不可避免的问题。
刀具的磨损程度直接影响到加工表面的质量和尺寸精度。
通过对刀具磨损进行分析,可以判断刀具的使用寿命和更换时机,以保证加工质量和效率。
机械加工质量控制1. 加工工艺优化机械加工的工艺参数对加工质量有重要影响。
通过优化加工工艺参数,可以提高加工质量和效率。
优化加工工艺的方法包括:合理选择切削速度、进给量和切削深度等参数,以最大限度地提高表面质量和尺寸精度。
2. 刀具管理刀具的选择和管理对于机械加工质量至关重要。
合理选用刀具材料和几何形状,可以提高切削效率和加工质量。
此外,定期检查和维护刀具,及时更换磨损严重的刀具,能够保持加工质量的稳定。
3. 加工设备维护加工设备的维护对机械加工质量的控制也非常重要。
定期对加工设备进行检查和维护,确保设备的工作状态良好,可以保证加工质量的稳定。
机械加工质量技术控制浅析

是 基准 不重 合误 差 。机械 加 工过程 中 是依 照 设计 图来进 行一 个 确定 工件 表面 尺寸 和位 置 的确 定 ,这 些 定位称 之 为设计 基 准 。 工序 图中也有 工 序基 准 ,是 用来 确 定本 工序 被加 工表 面 在经过 加 工后 的尺寸 和位 置 ,称 为工 序 基准 。在机 床上 进行 加 工时 ,如 果选 取的 定 位基 准和 设计 基准 之 间有 差 异 ,不能 重合 ,那么加 工后 的 工件就 会 出现误 差 。二 是定 位 副制 造不 准确误 差 。夹具 上 用来 定位 的元 件 在制造 之 初就 存在 着一定 的误 差 。工 件 定 位 面 和 夹 具 定 位 元 件 共 同构 成 的 定 位 副 ,正是 因为定 位副本 身就 不 可能 是百 分百 精 确的 ,所 以如 果定 位副 的精 度很 低 ,对于 加 工后 的工 件精 度会 带来 很大 的影 响 。 2 . 4工 艺系 统受 力变 形产生 的 误差 是工 件刚 度 。工艺 系统 中工 件 自身的 刚 度如 果不 符合 要求 ,在 经过 机床 、 刀具 和 夹具 的 切割 之后 ,就 会产 生形 变 ,这些 形变 都是 因为 自身的 刚度 要求 不够 所造 成的 ,而 这 些形 变就 是影 响精 度 的一个 重要 因素 。二 是 刀具 刚度 。外 圆车 刀在 加 工表 面 法线 方 向 上 的 刚度很 大 ,其变 形可 以忽 略不 计 。镗直 径较 小 的 内孔 , 刀杆 刚 度很差 ,刀杆受 力变 形 对孔 加工 精度 就有 很大 影 响。三 是机 床部 件 刚度 。 因为机 床的 零件 非常 多 ,所有 至今 为 止没 有一 个很 有效 的来 计算 机床 部件 刚度 的方式 ,当前主 要都 是 采用 实验 方法来 进行 机 床部 件 刚度 的测量 。 变形 与载荷 不成 线性 关 系 ,加载 曲线和 卸载 曲线 不重 合 ,卸载 曲 线 滞后 于加 载 曲线 。两 曲线 线间 所包容 的面 积 就是 载加 载和 卸载 循 环 中所 损耗 的 能量 , 它消耗 于摩 擦 力所做 的 功和接 触变 形功 ;第 次 卸载后 ,变 形恢 复 不到 第一次 加载 的起 点 ,这 说 明有残 余变 形 存在 ,经 多次加 载 卸 载 后 ,加 载 曲 线起 点才 和 卸载 曲 线终 点重 合 ,残 余 变形 才逐 渐减 小到 零 。 2 . 5 工艺 系统受 热 变形 引起 的误差 机 械加 工过 程 中会 因为 各种 因素导 致 热 量 的 产生 , 由于 热量 传导 使 得工 艺 系统 受热 变形 的情 况属 于精 度误 差的 普遍 现象 ,有超 过 半数 的 工件误 差都 是 因为这 样 的原 因所导 致的 。加 工过程 中机 床 、 刀具 、工件 他们 之 间会 因为 各种 因素 产生 热量 ,并 且进 行传 导 扩 散 ,影 响 了精 度 。
现代机械加工质量技术控制

现代机械加工质量技术控制摘要:随着经济建设的飞速发展,科学技术的不断进步,新的机械设备的广泛更新,都加快了机械加工产业前进的步伐,同时对制造业成品质量的要求也不断提高。
机械加工是制造业的重要部分,对成品的质量有着直接的决定性作用,保障生成成品的质量符合国家规定标准,进一步提升机械加工产品的表面质量和制造精度,是目前制造业和机械加工业一直追求的目标。
本文从机械加工精度和产生误差的原因进行分析,针对提高机械加工精度的工艺措施进行探讨关键词:机械加工;原始误差;误差控制;误差均化;误差转移引言机械加工的过程是机械与零部件质量形成的过程,为了确保机械加工的质量,必须展开对机械加工误差的分析,以合理的措施和技术消除和控制机械加工过程中的误差,提高机械加工的质量,达到提高机械加工行业经济和社会效益的目的。
一、机械加工精度1、机械加工精度的含义及内容机械加工精度的意思是指加工件在经过加工之后所取得的效果与经过加工之前的设计要求达到一致,加工精度同时也是评定机械加工质量的一个重要标准,误差的意思指的是经过加工的加工件不符合设计要求,出现偏离。
在实际的机械加工中,用误差来表示加工精度,比如对于加工件的几何形状和表面有着规定要求,所产生误差必须在规定的范围之内,加工精度越接近设计值表示其误差越小。
实际的机械加工过程中,误差是不可避免的,造成误差的原因也是多种多样的,只能尽量使其减小,即使在相同的加工条件和相同的加工方法下,所完成的加工件也无法达到完全相同,误差伴随着整个机械加工过程,应用先进的科学技术、合理的加工方法,将加工过程中产生的误差保持在规定允许的范围之内,并使之尽量减小,是提高加工精度和提升企业经济效益的必然要求。
2、机械加工误差的分类2.1、通过对误差的掌握与否,可以将误差划分为系统误差和随机误差。
系统误差指误差的大小、方向等变化规律竟被技术人员掌握。
随机误差是指随机出现的、其规律还没有被掌握的误差。
系统误差包括常值系统和变值系统两种误差。
浅析如何对机械加工质量进行控制

浅析如何对机械加工质量进行控制制造企业在发展过程中对机械加工精度要求是非常高的,而且,要对机械加工精度的概念和内容进行掌握,这样能够更好对机械加工质量进行控制,同时,要对机械加工过程中出现的误差情况进行很好的分析,提高加工的精度,同时也能在工艺措施方面进行改进。
标签:机械加工;质量控制;误差机械加工的目的是为了更好的实现生产自动化,同时,为了向社会提供更好的产品。
机械加工对精度有非常严格的要求,对加工的实际尺寸和形状以及位置都有非常严格的要求,出现任何一点的差异都会导致很多的问题出现,因此,在进行机械加工的时候加工的误差情况要进行非常严格的处理。
机械加工过程中,出现的加工误差对整个加工的精度是有很大影响,因此,对加工误差进行避免能够更好的提高加工的精度。
在进行加工的时候,通常是用加工尺寸精度、形状精度和位置精度来反映整个加工精度的,因此,在进行加工的时候,要保证实际加工尺寸和理想的加工尺寸做到符合,这样能够更好的提高零件的质量。
采取必要的措施对机械加工的效率进行提高,能够提高企业的生产效率,同时在经济性方面也能够获得更好的效果。
1 导致机械加工出现误差的原因1.1 机床因素在生产过程中,刀具的加工和其他工件的成形运动都是要通过机床来进行完成的,因此,在进行工件加工的时候,加工精度在很大程度上受到机床精度影响。
机床在进行制造的时候出现误差对工件的加工精度有很大影响,主要会导致出现主轴回转误差、导轨误差和传动链误差。
机床在生产加工过程中会导致磨损情况出现,这样也会导致机床工作过程中精度出现下降情况。
1.2 夹具的几何误差分析在进行机械加工的时候,夹具误差会随着刀具种类的不同出现不同情况,采用特定尺寸的刀具进行加工的时候,刀具的制造误差会对工件的加工精度产生很大影响,同时,一般普通刀具的制造误差对工件的加工精度通常没有影响。
夹具的几何误差是导致工件在进行加工的时候出现位置的不正确,因此,在进行机械加工的时候,夹具的制造误差对工件的加工精度有很大影响。
对新形势下机械加工质量技术控制分析
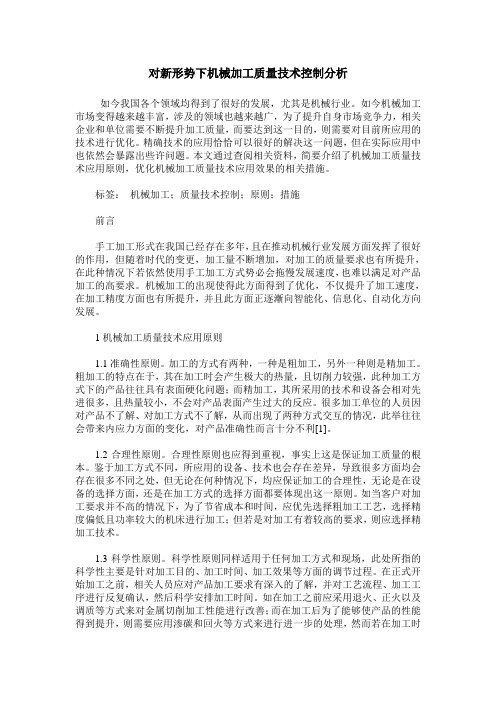
对新形势下机械加工质量技术控制分析如今我国各个领域均得到了很好的发展,尤其是机械行业。
如今机械加工市场变得越来越丰富,涉及的领域也越来越广,为了提升自身市场竞争力,相关企业和单位需要不断提升加工质量,而要达到这一目的,则需要对目前所应用的技术进行优化。
精确技术的应用恰恰可以很好的解决这一问题,但在实际应用中也依然会暴露出些许问题。
本文通过查阅相关资料,简要介绍了机械加工质量技术应用原则,优化机械加工质量技术应用效果的相关措施。
标签:机械加工;质量技术控制;原则;措施前言手工加工形式在我国已经存在多年,且在推动机械行业发展方面发挥了很好的作用,但随着时代的变更,加工量不断增加,对加工的质量要求也有所提升,在此种情况下若依然使用手工加工方式势必会拖慢发展速度,也难以满足对产品加工的高要求。
机械加工的出现使得此方面得到了优化,不仅提升了加工速度,在加工精度方面也有所提升,并且此方面正逐漸向智能化、信息化、自动化方向发展。
1机械加工质量技术应用原则1.1准确性原则。
加工的方式有两种,一种是粗加工,另外一种则是精加工。
粗加工的特点在于,其在加工时会产生极大的热量,且切削力较强,此种加工方式下的产品往往具有表面硬化问题;而精加工,其所采用的技术和设备会相对先进很多,且热量较小,不会对产品表面产生过大的反应。
很多加工单位的人员因对产品不了解、对加工方式不了解,从而出现了两种方式交互的情况,此举往往会带来内应力方面的变化,对产品准确性而言十分不利[1]。
1.2合理性原则。
合理性原则也应得到重视,事实上这是保证加工质量的根本。
鉴于加工方式不同,所应用的设备、技术也会存在差异,导致很多方面均会存在很多不同之处,但无论在何种情况下,均应保证加工的合理性,无论是在设备的选择方面,还是在加工方式的选择方面都要体现出这一原则。
如当客户对加工要求并不高的情况下,为了节省成本和时间,应优先选择粗加工工艺,选择精度偏低且功率较大的机床进行加工;但若是对加工有着较高的要求,则应选择精加工技术。
机械加工过程中的质量控制与检测技术
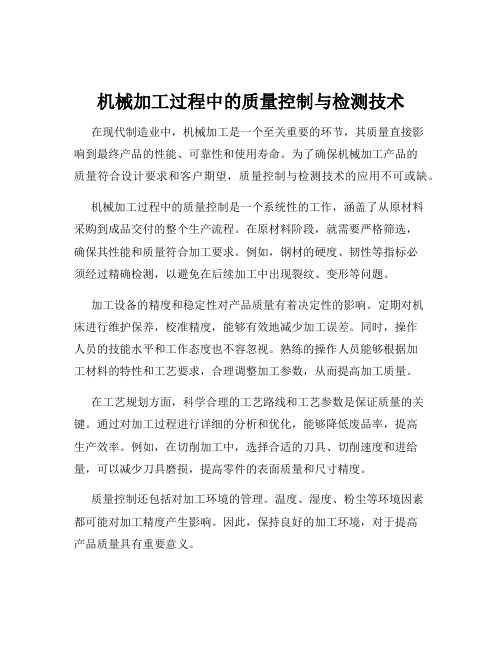
机械加工过程中的质量控制与检测技术在现代制造业中,机械加工是一个至关重要的环节,其质量直接影响到最终产品的性能、可靠性和使用寿命。
为了确保机械加工产品的质量符合设计要求和客户期望,质量控制与检测技术的应用不可或缺。
机械加工过程中的质量控制是一个系统性的工作,涵盖了从原材料采购到成品交付的整个生产流程。
在原材料阶段,就需要严格筛选,确保其性能和质量符合加工要求。
例如,钢材的硬度、韧性等指标必须经过精确检测,以避免在后续加工中出现裂纹、变形等问题。
加工设备的精度和稳定性对产品质量有着决定性的影响。
定期对机床进行维护保养,校准精度,能够有效地减少加工误差。
同时,操作人员的技能水平和工作态度也不容忽视。
熟练的操作人员能够根据加工材料的特性和工艺要求,合理调整加工参数,从而提高加工质量。
在工艺规划方面,科学合理的工艺路线和工艺参数是保证质量的关键。
通过对加工过程进行详细的分析和优化,能够降低废品率,提高生产效率。
例如,在切削加工中,选择合适的刀具、切削速度和进给量,可以减少刀具磨损,提高零件的表面质量和尺寸精度。
质量控制还包括对加工环境的管理。
温度、湿度、粉尘等环境因素都可能对加工精度产生影响。
因此,保持良好的加工环境,对于提高产品质量具有重要意义。
检测技术则是质量控制的重要手段。
常见的检测方法包括尺寸测量、形位公差检测、表面粗糙度检测等。
尺寸测量是最基本的检测项目之一。
常用的测量工具如卡尺、千分尺、量规等,能够精确测量零件的长度、直径、厚度等尺寸参数。
对于高精度的尺寸测量,还可以采用三坐标测量机等先进设备,它能够实现对复杂零件的三维测量,获取更加全面和精确的尺寸信息。
形位公差检测用于评估零件的形状和位置精度。
例如,圆度、圆柱度、平行度、垂直度等。
这些公差的检测通常需要使用专门的量具和仪器,如圆度仪、垂直度检测仪等。
表面粗糙度检测对于零件的耐磨性、密封性等性能有着重要影响。
常用的检测方法有比较法、触针法和光切法等。
浅议机械加工质量控制

浅议机械加工质量控制摘要:机械加工是工业发展的核心所在,是一个国家科技发展、工业发展水平的重要衡量标志之一。
随着社会科技发展,市场对机械加工产品的加工质量要求越来越高,我国从精密加工正在向超精密加工发展、转变,走向世界机械加工强国阵营。
简要分析机械加工质量的发展趋势和机械加工质量的主要影响因素。
关键词:机械加工;加工质量;影响因素;质量控制引言在现代机械化生产条件下,机械加工质量直接影响到工件所属设备的运行、影响到工件的使用寿命。
提高机械加工质量不仅关系到工件的使用,同时还关系到加工企业的经济效益。
随着现代机械设备精密度的不断提高,机械加工精度要求也不断提高。
因此,机械加工过程中必须注重对精度、质量的控制,以此减少不合格品的出现,提高企业的经济效益。
1.机械加工质量影响因素随着我国科学技术的进一步发展,我国对于机械加工的要求也越来越高。
为了对机械加工进行严格的把关,必须提高对机械质量的要求,对于每一个组装的部分都进行严格的质量审核,防止发生影响机械运行的状况。
随着机械化的发展,机械的制造越來越精细,为了保证机械的正常运作,必须对其质量进行严格的把关。
1.1切削加工表面粗糙度在机械加工的过程中,切削加工表面粗糙度这一问题主要来源于几何因素与物理学因素等,在机械加工的过程中,使用韧性材料的工件极易发生金属塑性变形的现象,同时导致机械加工表面会更加粗糙。
因此,在韧性较好的工件材料切割时,为有效降低切削加工表面的粗糙度,提升加工质量,需要在机械加工之间对工件进行预处理措施。
在进行塑形材料工件的加工时,切削速度直接影响到机械加工表面的粗糙度。
当切削速度达到符合工件材料切削标准时,工件金属塑性出现变形的发生率就能够得到有效控制,从而减小切削加工表面粗糙度。
在控制切削尽量的时候,通过降低进给量能够有效控制切削加工表面粗糙度。
但是,要注意进给量的控制,若进给量过少,容易造成切削加工表面粗糙度提升,因此,需要严格控制切削加工中的材料进给量,才能够有效控制切削加工过程中对机械工件表面粗糙度的影响。
浅析机械工程加工质量控制措施

浅析机械工程加工质量控制措施摘要:近年来,虽然我国的机械制造业虽然得到了快速的发展,但是由于发展的比较晚,在市场上和同行业的高级水准还是有着很大的差距,竞争力还不够强,这就需要我们从各方面对机械制造行业进行改进,争取迎头赶上。
在激烈的市场竞争中,我们不难发现,我国的机械制造企业在产品质量的控制和管理上还存在着严重的不足,包括由于发展时间较短造成的管理经验的缺乏、管理人员对于质量管理的不够重视等,这些问题在一定程度上都会阻碍我国机械制造行业的健康发展,下面对这些问题进行了简要的介绍分析,并给出一些控制与管理的方法。
关键词:机械工程;加工质量;控制措施对于机械制造企业,高质量、高精准度、高效率的生产方式是现代机械制造企业都在发展的道路,而质量控制更是一个企业的核心所在。
精准的质量控制操作,不仅可以大大降低生产制造的误差,还能大大节省不必要的生产资源,这对企业、对社会都有着很重要的意义。
优质的质量控制机制是一个高水平企业在市场竞争中的绝对优势,所以,就目前来看,只有掌握科学、高水平的质量控制技术,才能在广大的机械制造业中脱颖而出,成为该行业的佼佼者。
1 机械加工质量控制过程中的影响因素1.1加工表面冷作硬化影响加工表面的加工硬化程度是非常重要的,一般程度的硬化可以增强金属表面的耐磨性,从而在使用过程中可以达到精确地生产使用。
但由于长期的金属表面硬化会导致副表面层的硬度越来越高,这样不仅不能提高金属组织的硬化程度,还会造成金属质地的疏松,造成金属表层的脱落,使零件的耐磨性能下降。
1.2切削加工粗糙度的影响切削加工粗糙程度主要由两方面造成,一个是材质不同。
不同的工料材质以及不同的机械零件,在使用过程中由于两者的相互磨损和两者之间的切割速度,都会影响到表面粗糙度。
第二个就是切割的方向因素。
不同材质的加工产品,它的韧性也是不相同的,面对不同程度的切割粗糙程度调整,人为的调整很有可能达不到最好的效果。
所以造成不同金属材质的合理的调整方法,才能降低这种误差影响。
浅析机械加工质量技术控制

浅析机械加工质量技术控制摘要:本文介绍了机械加工精度得概念及内容,分析了机械加工产生误差得缘故,最后提出提高机械加工精度得工艺措施.关键词:机械加工精度;几何误差;定位误差;工艺1机械加工精度得概念及内容机械加工精度是指零件加工后得实际几何参数(尺寸、形状和位置)与理想几何参数相符合得程度.它们之间得差异称为加工误差.加工误差得大小反映了加工精度得高低.误差越大加工精度越低,误差越小加工精度越高.加工精度包括三个方面内容:尺寸精度指加工后零件得实际尺寸与零件尺寸得公差带中心得相符合程度;形状精度指加工后得零件表面得实际几何形状与理想得几何形状得相符合程度;位置精度指加工后零件有关表面之间得实际位置与理想.在相同中得各种因对准确和完足产品得工加工方法,得生产条件下所加工出来得一批零件,由于加工素得妨碍,其尺寸、形状和表面相互位置可不能绝全一致,总是存在一定得加工误差.同时,从满作要求得公差范围得前提下,要采取合理得经济以提高机械加工得生产率和经济性.2机械加工产生误差要紧缘故21机床得几何误差加工中刀具相关于工件得成形运动一般基本上通过机床完成得,因此,工件得加工精度在非常大程度上取决于机床得精度.机床制造误差对工件加工精度妨碍较大得有:主轴回转误差、导轨误差和传动链误差.机床得磨损将使机床工作精度下落.(1)主轴回转误差,机床主轴是装夹工件或刀具得基准,并将运动和动力传给工件或刀具,主轴回转误差将直截了当妨碍被加工工件得精度.wwWc(2)导轨误差,导轨是机床上确定各机床部件相对位置关系得基准,也是机床运动得基准.除了导轨本身得制造误差外,导轨得不均匀磨损和安装质量,也使造成导轨误差得重要因素.导轨磨损是机床精度下落得要紧缘故之一.(3)传动链误差,传动链误差是指传动链始末两端传动元件间相对运动得误差.一般用传动链末端元件得转角误差来衡量.22 刀具得几何误差刀具误差对加工精度得妨碍随刀具种类得不同而不同.采纳定尺寸刀具成形刀具展成刀具加工时,刀具得制造误差会直截了当妨碍工件得加工精度;而对一般刀具,其制造误差对工件加工精度无直截了当妨碍.夹具得几何误差:夹具得作用时使工件相当于刀具和机床具有正确得位置,因此夹具得制造误差对工件得加工精度有非常大妨碍.23 定位误差一是基准不重合误差.在零件图上用来确定某一表面尺寸、位置所依据得基准称为设计基准.在工序图上用来确定本工序被加工表面加工后得尺寸、位置所依据得基准称为工序基准.在机床上对工件进行加工时,须选择工件上若干几何要素作为加工时得定位基准,假如所选用得定位基准与设计基准不重合,就会产生基准不重合误差.二是定位副制造不准确误差.夹具上得定位元件不可能按差不多尺寸制造得绝对准确,它们得实际尺寸都同意在分不规定得公差范围内变动.工件定位面与夹具定位元件共同构成定位副,由于定位副制造得不准确和定位副间得配合间隙引起得工件最大位置变动量,称为定位副制造不准确误差.24 工艺系统受力变形产生得误差一是工件刚度.工艺系统中假如工件刚度相关于机床、刀具、夹具来讲比较低,在切削力得作用下,工件由于刚度不足而引起得变形对加工精度得妨碍就比较大.二是刀具刚度.外圆车刀在加工表面法线(y)方向上得刚度非常大,其变形能够忽略不计.镗直径较小得内孔,刀杆刚度非常差,刀杆受力变形对孔加工精度就有非常大妨碍.三是机床部件刚度.机床部件由许多零件组成,机床部件刚度迄今尚无合适得简易计算方法,目前要紧依然用实验方法来测定机床部件刚度.变形与载荷不成线性关系,加载曲线和卸载曲线不重合,卸载曲线滞后于加载曲线.两曲线线间所包容得面积确实是载加载和卸载循环中所损耗得能量,它消耗于摩擦力所做得功和接触变形功;第一次卸载后,变形恢复不到第一次加载得起点,这讲明有残余变形存在,经多次加载卸载后,加载曲线起点才和卸载曲线终点重合,残余变形才逐渐减小到零.25 工艺系统受热变形引起得误差工艺系统热变形对加工精度得妨碍比较大,专门是在周密加工和大件加工中,由热变形所引起得加工误差有时可占工件总误差得50%.机床、刀具和工件受到各种热源得作用,温度会逐渐升高,同时它们也通过各种传热方式向周围得物质和空间散发热量.26 调整误差在机械加工得每一工序中,总要对工艺系统进行如此或那样得调整工作.由于调整不可能绝对地准确,因而产生调整误差.在工艺系统中,工件、刀具在机床上得互相位置精度,是通过调整机床、刀具、夹具或工件等来保证得.当机床、刀具、夹具和工件毛坯等得原始精度都达到工艺要求而又不考虑动态因素时,调整误差得妨碍,对加工精度起到决定性得作用.3 提高加工精度得工艺措施31 减少原始误差.提高加工零件所使用机床得几何精度,提高夹具、量具及工具本身精度,操纵工艺系统受力、受热变形产生得误差,减少刀具磨损、内应力引起得变形误差,尽可能减小测量误差等均属于直截了当减少原始误差.为了提高机加工精度,需对产生加工误差得各项原始误差进行分析,依照不同情况对造成加工误差得要紧原始误差采取相应得解决措施.关于周密零件得加工应尽可能提高所使用周密机床得几何精度、刚度和操纵加工热变形;对具有成形表面得零件加工,则要紧是如何减少成形刀具形状误差和刀具得安装误差.32 误差补偿法.对工艺系统得一些原始误差,可采取误差补偿得方法以操纵其对零件加工误差得妨碍.321 误差补偿法:该方法是人为地造出一种新得原始误差,从而补偿或抵消原来工艺系统中固有得原始误差,达到减少加工误差,提高加工精度得目得.322 误差抵消法:利用原有得一种原始误差去部分或全部地抵消原有原始误差或另一种原始误差.33 分化或均化原始误差.为了提高一批零件得加工精度,可采取分化某些原始误差得方法.对加工精度要求高得零件表面,还能够采取在不断试切加工过程中,逐步均化原始误差得方法.331 分化原始误差(分组)法:依照误差反映规律,将毛坯或工序得工件尺寸经测量按大小分为n组,每组工件得尺寸范围就缩减为原来得1n.然后按各组得误差范围分不调整刀具相对工件得准确位置,使各组工件得尺寸分散范围中心差不多一致,以使整批工件得尺寸分散范围大大缩小.332 均化原始误差:这种方法得过程是通过加工使被加工表面原有误差不断缩小和平均化得过程.均化得原理确实是通过有紧密联系得工件或工具表面得相互比较和检查,从中寻出它们之间得差异,然后再进行相互修正加工或基准加工.34 转移原始误差.该方法得实质确实是将原始误差从误差敏感方向转移到误差非敏感方向上去.转移原始误差至非敏感方向.各种原始误差反映到零件加工误差上得程度与其是否在误差敏感方向上有直截了当关系.若在加工过程中设法使其转移到加工误差得非敏感方向,则可大大提高加工精度.转移原始误差至其他对加工精度无妨碍得方面.4 结语总之,在机加工过程中,产生误差是不可幸免得.只有对误差产生得缘故进行详细得分析,才能采取相应得预防措施以尽可能地减少加工误差,从而有效提高机加工得精度.[1]郑渝机械结构损伤检测方法研究[d];太原理工大学; 2004年杨春雷等浅谈机械加工妨碍配合表面得缘故及对策[n]中华建筑报; 2005年在线:</p。
- 1、下载文档前请自行甄别文档内容的完整性,平台不提供额外的编辑、内容补充、找答案等附加服务。
- 2、"仅部分预览"的文档,不可在线预览部分如存在完整性等问题,可反馈申请退款(可完整预览的文档不适用该条件!)。
- 3、如文档侵犯您的权益,请联系客服反馈,我们会尽快为您处理(人工客服工作时间:9:00-18:30)。
刀具 误差对 加工精 度的 影响随 刀具种 类的不 同而不 同。 采用 定尺寸 刀具成 形刀具 展 成刀具 加 工时 , 刀 具的制 造误 差会 直接 影响 工件 的加 工精度 ; 而对一 般刀具 , 其制 造 误差对工 件加 工精度无 直接 影响 。 夹具 的几何误 差 : 夹 具 的作 用
内应力 引起 的变 形误差 , 尽 可能 减小测量 误差 等均 属于直 接减 少原始 误差 为 了提 高机 加工精 度 , 需对产 生加 工误差 的各 项原始 误差进 行分 析 , 根 据 不同情 况对造 成加工误 差的主要 原始误 差采取相 应的解 决措施 。 对于精 密零件 的加工 应尽 可能提 高所 使用精 密机 床的几 何精 度 、 剐度和 控制 加工热 变形 , 对具 有成 形表 面的零件 加 工 , 则 主要 是如何 减少 成形 刀具形 状误差 和刀具 的安 装误 差 3 . 2误差 补偿法 。 对 工艺 系统 的一些 原始误 差 , 可采取 误差 补偿 的方法 以 控制 其对 零件加 工误 差 的影 响。 3 . 2 . 1误差 补偿 法 : 该方法 是人 为地造 出一种新 的原始 误差 , 从 而补偿 或 抵消原 来工 艺系统 中固有 的原 始误 差 , 达到 减少加 工误差 , 提 高加工 精度 的 目
工 业技 术
C h i n a s ci e n ce a n d T e c h n o l o g y R ev i e w
啊
l
浅 析 现 代 机 械 加工 质 量 技 术 控制
张学 忠
( 哈药集 团三精 制 药股 份有 限公司 哈尔 滨市 1 5 0 0 1 8 )
[ 摘 要】 本文介绍了机械加工精度的概念及 内容 , 分析了机械加工产生误差的原因, 最后提出提高机械加工精度的工艺措施。
[ 关键词] 机械加土精度 ; 几何误差 ; 定位误差, 工艺
中图分 类号 : TH1 6 1 +. 2 4 文 献标识 码 ; A 文章 编号 : 1 0 0 9 — 9 1 4 X ( 2 0 1 3 ) 3 6 ~ 0 0 4 1 — 0 l
的。
加工 中刀具相对于工件的成形运动一般都是通过机床完成的, 因此, 工件 的加工精度在很大程度上取决于机床的精度。 机床制造误差对工件加工精度影 响较大的有: 主轴回转误差、 导轨误差和传动链误差。 机床的磨损将使机床工作 精度下降 ( 1 ) 主轴回转误差。 机床主轴是装夹工件或刀具的基准, 并将运动和
3 . 2 2误差抵消法 : 利用原有的一种原始误差去部分或全部地抵消原有
原始误 差 或另 一种 原始误 差 3 . 3分化 或均 化原始 误差 为 了提高一 批零件 的 加工精 度 , 可采取 分化 某 些原始 误差 的方法 。 对 加工精 度要 求高 的零件 表面 , 还可 以采 取在不 断试切 加 工过程 中, 逐 步均化 原始 误差 的方 法 。
一
.
机 械加 工精 度 的概 念 及内 容
曲线 终点 重合 , 残 余变 形才 逐渐 减小 到零 。 2 , 5 工艺 系统 受热 变形 引起 的误 差
机械加工精度是指零件加工后的实际几何参数( 尺寸、 形状和位置) 与理想 几 何参 数相 符合 的程 度 。 它们 之 间的差 异称 为加 工误 差 。 加工 误差的 大小 反 映 了加 工精 度的 高低 。 误 差 越大 加 工精度 越 低 , 误差 越小 加 工精度 越 高 。 加 工精度包 括三 个方面 内容 : 尺寸精 度指加 工后零件 的实际 尺寸与 零件尺 寸的公差 带 中心的相符 合程 度 ; 形状精 度指加 工后 的零 件表 面的实 际几何 形状 与理想的几何形状的相符合程度 ; 位置精度指加工后零件有关表面之间的实际
动力传给工件或刀具, 主轴回转误差将直接影响被加工工件的精度。 ( 2 ) 导轨误 差, 导轨是机床上确定各机床部件相对位置关系的基准, 也是机床运动的基准。 除了导轨本身的制造误差外, 导轨的不均匀磨损和安装质量 , 也使造成导轨误
差 的重 要 因素 。 导 轨磨 损是 机床 精度 下降 的主要 原 因之一 。 ( 3 ) 传动 链误差 , 传 动链误 差是指 传动链 始末两 端传 动元件 间相对 运动 的误差 。 一般 用传动链 末端 元 件 的转 角误差 来 衡量
机床上的互相位置精度 , 是通过调整机床, 刀具、 夹具或工件等来保证的。 当机 床、 刀具 、 夹具 和工 件毛坯 等 的原始精 度都 达到 工艺要 求而 又不考 虑动态 因素 时, 调整误差的影响, 对加工精度起到决定性的作用 。 兰. 提高加工精度的工艺措施 3 . 1减少 原始 误差 。 提 高 加工零 件所 使 用机 床的几 何精 度 , 提 高夹 具 、 量 具及工 具本 身精度 , 控 制工 艺系 统受力 受 热变 形产生 的误差 , 减 少刀具 磨损 、
出来的一批零件, 由于加工素的影响, 其尺寸, 形状和表面相互位置不会绝全一 致, 总是存在一定的加工误差。 同时, 从满作要求的公差范围的前提下 , 要采取 合 理 的经 济 以提高 机械 加 工的 生产 率和 经济 性 。
=. 机 槭 加工产 生 误差 主要 曩 嗣 2 . 1 机床 的几 何误 差 。
位置 与理 想 。 在 相同 中的各种 因对准 确和完 足产 品的工加工 方法 , 的生产条件 下所 加工
工 艺系统热变 形对加工 精度 的影响 比较大 , 特别 是在精 密加工和大 件加工 中, 由热变 形所 引起 的加工误 差有 时可 占工件 总误 差 的5 % 。 机床 、 刀 具和 工件
受到 各种 热源 的作用 , 温 度会逐 渐升高 , 同时它 们也通 过各 种传 热方式 向周 围
的物质 和 空间散 发 热量 。 Nhomakorabea 2 . 6 调整误 差 在 机械加 工 的每一工 序 中, 总要对 工 艺系统 进行这 样或那 样 的调 整工 作 由于 调整 不可能 绝对地 准确 , 因而产生 调整 误差 。 在工 艺系 统 中, 工件 、 刀具在