热处理行标
热处理标准

51
JB/T 5073-91
热处理车间空气中有害物质的限值
52
JB/T 5074-91
低、中碳钢球化体评级
53
GB/T 18177-2000
钢的气体渗氮
54
GB/T 7232-1999
金属热处理工艺术语
55
GB/T 17358-1998
热处理生产电能消耗定额及其计算和测定方法
24
JB/T 9210-1999
真空热处理
25
JB/T 9211-1999
中碳钢与中碳合金结构钢马氏体等级
26
JB/T 8555-1997
热处理技术要求在零件图样上的表示方法
27
JB/T 4215-1996
渗硼(代替JB4215-86和JB4383-87)
28
JB/T 8418-1996
粉末渗金属
29
热处理盐浴有害固体废物无害化处理方法
45
JB/T 6048-92
盐浴热处理
ቤተ መጻሕፍቲ ባይዱ46
JB/T 6049-92
热处理炉有效加热区的测定
47
JB/T 6050-92
钢铁热处理零件硬度检验通则
48
JB/T 6051-92
球墨铸铁热处理工艺及质量检验
49
JB/T 5069-91
钢铁零件渗金属层金相检验方法
50
JB/T 5072-91
高温合金热处理
35
JB/T 7713-95
高温高合金钢制冷作模具显微组织检验
36
JB/T 4218-1994
硼砂熔盐渗金属(代替JB/Z235-85和JB4218-86)
焊缝热处理 国标

焊缝热处理国标一、背景介绍焊缝热处理是指对焊接过程中产生的焊缝进行一系列热处理工艺,以达到提高焊接接头性能和焊缝组织结构的目的。
在我国,焊缝热处理的相关标准由国家标准委员会制定和颁布,这些标准被广泛应用于各个行业的焊接工艺中。
二、国家标准概述国家标准对焊缝热处理的要求主要包括以下几个方面:1. 热处理类型国家标准根据焊缝热处理的方法和工艺,将其分为几种类型,如回火处理、正火处理、退火处理等。
这些不同的类型适用于不同的焊接接头和材料,以满足其特定的性能要求。
2. 热处理参数国家标准规定了焊缝热处理过程中的各项参数,包括热处理温度、保温时间、冷却速度等。
这些参数对焊接接头的性能和组织结构具有重要影响,其合理选择和控制是确保焊接接头质量的关键。
3. 检测要求国家标准要求对焊缝热处理后的焊接接头进行必要的检测和评定。
这些检测手段包括金相组织观察、硬度试验、冲击试验等,以确保焊接接头满足规定的性能要求。
4. 标准依据国家标准制定时参考了国际相关标准和国内先进经验,充分考虑了不同行业和材料的特点。
同时,标准还设立了相应的解释说明和技术指导,以帮助焊接工程师正确理解和应用这些标准。
三、焊缝热处理工艺焊缝热处理工艺是指按照国家标准要求对焊接接头进行热处理的具体操作步骤。
根据焊缝热处理的类型和焊接接头的材料等因素,工程师需要选择合适的工艺。
1. 回火处理工艺回火处理是对焊接接头进行高温加热后进行缓慢冷却的过程。
这种工艺主要适用于低合金钢焊接接头,可以消除焊接过程中产生的残余应力,并提高焊接接头的强度和韧性。
回火处理工艺步骤: - 加热温度控制在合适的范围内; - 保温时间根据焊接接头的厚度和材料选定; - 冷却速度要适当控制,防止产生过大的温度梯度。
2. 正火处理工艺正火处理是指对焊接接头进行高温加热后,快速冷却至室温的工艺。
这种工艺主要适用于高碳钢焊接接头,可以通过正火处理改善焊接接头的硬度和强度。
正火处理工艺步骤: - 提高温度至正火处理温度; - 将焊接接头迅速浸入冷却介质中; - 控制冷却速度,以达到理想的硬度和结构。
热处理的标注标准
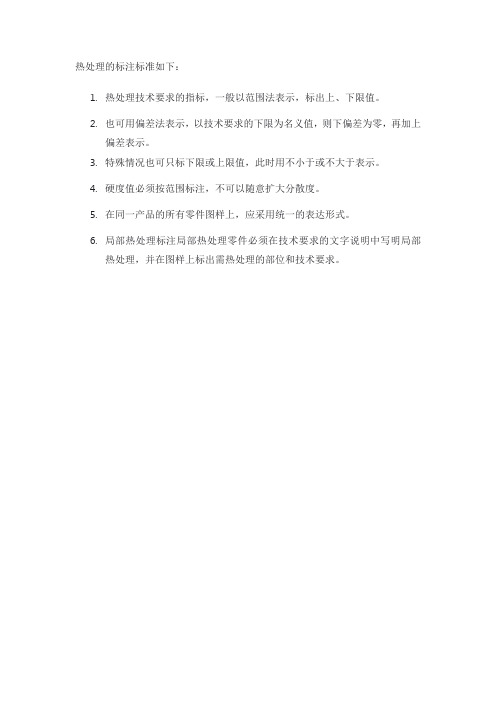
热处理的标注标准如下:
1.热处理技术要求的指标,一般以范围法表示,标出上、下限值。
2.也可用偏差法表示,以技术要求的下限为名义值,则下偏差为零,再加上
偏差表示。
3.特殊情况也可只标下限或上限值,此时用不小于或不大于表示。
4.硬度值必须按范围标注,不可以随意扩大分散度。
5.在同一产品的所有零件图样上,应采用统一的表达形式。
6.局部热处理标注局部热处理零件必须在技术要求的文字说明中写明局部
热处理,并在图样上标出需热处理的部位和技术要求。
热处理行标

1 目的为了公司铝合金热处理能实现精确控制,使热处理质量能有效保证,依此规范规定热处理工艺、设备及质量控制要求。
2 范围凡涉及我司铝合金产品热处理工序的相关部门及组织均适用.3 定义下列术语、定义适用于本规范。
3.1热处理本规范中所使用的“热处理”一词是本规范所包含的所有热处理的总称,例如:时效、固溶和退火。
3.2热处理批次一个热处理批次是指:由同一合金、同一产品形式、状态以及经历同一工艺过程的一定数量的一批零件。
3.3工作区工作区是指在一个热处理工艺的保温过程中,热处理设备被部件或原材料所占据的部分封闭空间。
该区通常(但不总是)占据整个封闭空间的大部分。
3.4固溶热处理造成的砂眼和气孔这种情况在过去被称为高温氧化。
现已公认,在固溶热处理过程中,进入到铝合金中的氢是造成表面砂眼和表层下面气孔出现的原因。
4 要求4.1 建立工艺操作规程和工艺操作规程重新审定4.1.1 基本原则生产前,热处理设备和工艺操作规程应达到本规范要求。
对于新建设备或维修后的设备,需进行检测,并建立或重新审定这些设备的工艺操作规程。
4.1.2 工艺操作规程重新审定的条件下列情形多次出现,则有必要重新审定工艺操作规程。
a. 原已验收的热处理设备,更换部件、彻底磨损、毁坏或改型需要磨合(见4.5.1~4.5.3);b. 现有热处理设备或其工艺操作规程不能满足本标准规定的质量要求(见5.6.4);c. 在定期工艺制度检查(见4.2)或定期产品监测过程中(见4.3)测出任何不合格(见5.1.3和5.6.4)。
4.2 定期工艺制度检查热处理设备和工艺操作规程应按表1规定进行检查。
4.3 定期产品监测应按表1规定对产品进行检验,以监测热处理设备的运行情况和工艺操作规程的适用性。
4.4 热处理设备4.4.1 热处理炉4.4.1.1 固溶热处理设备对于那些在有关热处理炉内进行固溶热处理(见A.3和3.4)而实验证明没有气孔产生的产品,可采用燃烧介质与金属接触的气室炉进行热处理。
热处理国家行业标准目录现行237项(2018版)
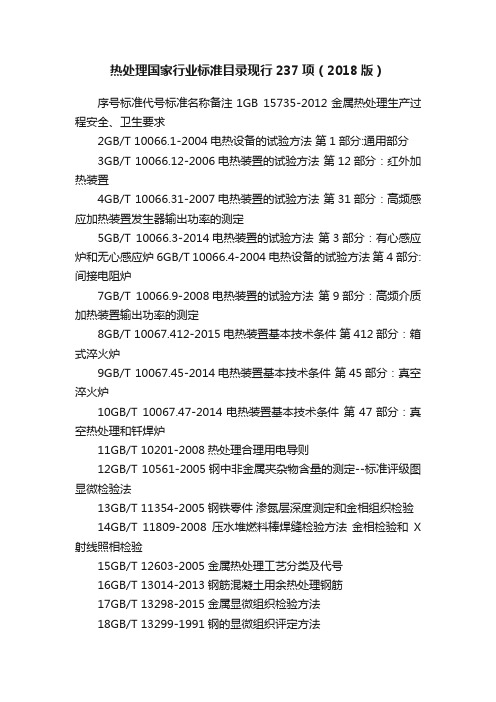
热处理国家行业标准目录现行237项(2018版)序号标准代号标准名称备注1GB 15735-2012金属热处理生产过程安全、卫生要求2GB/T 10066.1-2004电热设备的试验方法第1部分:通用部分3GB/T 10066.12-2006电热装置的试验方法第12部分:红外加热装置4GB/T 10066.31-2007电热装置的试验方法第31部分:高频感应加热装置发生器输出功率的测定5GB/T 10066.3-2014电热装置的试验方法第3部分:有心感应炉和无心感应炉6GB/T 10066.4-2004电热设备的试验方法第4部分:间接电阻炉7GB/T 10066.9-2008电热装置的试验方法第9部分:高频介质加热装置输出功率的测定8GB/T 10067.412-2015电热装置基本技术条件第412部分:箱式淬火炉9GB/T 10067.45-2014电热装置基本技术条件第45部分:真空淬火炉10GB/T 10067.47-2014电热装置基本技术条件第47部分:真空热处理和钎焊炉11GB/T 10201-2008热处理合理用电导则12GB/T 10561-2005钢中非金属夹杂物含量的测定--标准评级图显微检验法13GB/T 11354-2005钢铁零件渗氮层深度测定和金相组织检验14GB/T 11809-2008压水堆燃料棒焊缝检验方法金相检验和X 射线照相检验15GB/T 12603-2005金属热处理工艺分类及代号16GB/T 13014-2013钢筋混凝土用余热处理钢筋17GB/T 13298-2015金属显微组织检验方法18GB/T 13299-1991钢的显微组织评定方法19GB/T 13302-1991钢中石墨碳显微评定方法20GB/T 13305-2008不锈钢中α-相面积含量金相测定法21GB/T 13320-2007钢质模锻件金相组织评级图及评定方法22GB/T 13324-2006热处理设备术语23GB/T 13925-2010铸造高锰钢金相24GB/T 14999.1-2012高温合金试验方法第1部分:纵向低倍组织及缺陷酸浸检验25GB/T 14999.2-2012高温合金试验方法第2部分:横向低倍组织及缺陷酸浸检验26GB/T 15318-2010热处理电炉节能监测现行237项热处理国家行业标准目录(更新至20180101)序号标准代号标准名称备注27GB/T 15519-2002化学转化膜钢铁黑色氧化膜规范和试验方法28GB/T 15749-2008定量金相测定方法29GB/T 16840.4-1997电气火灾原因技术鉴定方法第4部分:金相法30GB/T 16923-2008钢件的正火与退火31GB/T 16924-2008钢件的淬火与回火32GB/T 17031.1-1997纺织品织物在低压下的干热效应第1部分:织物的干热处理程序33GB/T 17358-2009热处理生产电耗计算和测定方法34GB/T 17455-2008无损检测表面检测的金相复型技术35GB/T 17879-1999齿轮磨削后表面回火的浸蚀检验36GB/T 18177-2008钢件的气体渗氮37GB/T 18683-2002钢铁件激光表面淬火38GB/T 18876.1-2002应用自动图像分析测定钢和其他金属中金相组织、夹杂物含量和级别的标准试验方法第1部分:钢和其他金属中夹杂物或第二相组织含量的图像分析与体视学测定39GB/T 18876.2-2006应用自动图像分析测定钢和其它金属中金相组织、夹杂物含量和级别的标准试验方法第2部分:钢中夹杂物级别的图像分析与体视学测定40GB/T 18876.3-2008应用自动图像分析测定钢和其它金属中金相组织、夹杂物含量和级别的标准试验方法第3部分钢中碳化物级别的图像分析与体视学测定41GB/T 18983-2017淬火-回火弹簧钢丝42GB/T 1979-2001结构钢低倍组织缺陷评级图43GB/T 19944-2015热处理生产燃料消耗计算和测定方法44GB/T 20564.9-2016汽车用高强度冷连轧钢板及钢带第9部分:淬火配分钢45GB/T 21638-2008钢铁材料缺陷电子束显微分析方法通则46GB/T 21736-2008节能热处理燃烧加热设备技术条件47GB/T 225-2006钢淬透性的末端淬火试验方法(Jominy 试验)48GB/T 22560-2008钢铁件的气体氮碳共渗49GB/T 22561-2008真空热处理50GB/T 226-2015钢的低倍组织及缺陷酸蚀检验法序号标准代号标准名称备注51GB/T 22894-2008纸和纸板加速老化在80℃和65%相对湿度条件下的湿热处理52GB/T 24562-2009燃料热处理炉节能监测53GB/T 24733-2009等温淬火球墨铸铁件54GB/T 24743-2009技术产品文件钢铁零件热处理表示法55GB/T 25151.2-2010尿素高压设备制造检验方法第2部分:尿素级超低碳铬镍钼奥氏体不锈钢选择性腐蚀检查和金相检查56GB/T 25744-2010钢件渗碳淬火回火金相检验57GB/T 25745-2010铸造铝合金热处理58GB/T 25746-2010可锻铸铁金相检验59GB/T 26069-2010硅退火片规范60GB/T 26656-2011蠕墨铸铁金相检验61GB/T 26871-2011电触头材料金相试验方法62GB/T 26872-2011电触头材料金相图谱63GB/T 27945.1-2011热处理盐浴有害固体废物的管理第1部分:一般管理64GB/T 27945.2-2011热处理盐浴有害固体废物的管理第2部分:浸出液检测方法65GB/T 27945.3-2011热处理盐浴有害固体废物的管理第3部分:无害化处理方法66GB/T 27946-2011热处理工作场所空气中有害物质的限值67GB/T 28196-2011玻璃退火点和应变点测试方法68GB/T 28694-2012深层渗碳技术要求69GB/T 28838-2012木质包装热处理作业规范70GB/T 28909-2012超高强度结构用热处理钢板71GB/T 28992-2012热处理实木地板72GB/T 30067-2013金相学术语73GB/T 30583-2014承压设备焊后热处理规程74GB/T 30822-2014热处理环境保护技术要求75GB/T 30823-2014测定工业淬火油冷却性能的镍合金探头试验方法76GB/T 30824-2014燃气热处理炉温度均匀性测试方法序号标准代号标准名称备注77GB/T 30825-2014热处理温度测量78GB/T 30839.45-2015工业电热装置能耗分等第45部分:箱式淬火电阻炉79GB/T 30840-2014燃气罩式退火炉基本技术条件80GB/T 3203-2016渗碳轴承钢81GB/T 3246.1-2012变形铝及铝合金制品组织检验方法第1部分:显微组织检验方法82GB/T 3246.2-2012变形铝及铝合金制品组织检验方法第2部分:低倍组织检验方法83GB/T 32529-2016热处理清洗废液回收及排放技术要求84GB/T 32539-2016高温渗碳85GB/T 32540-2016精密气体渗氮热处理技术要求86GB/T 32541-2016热处理质量控制体系87GB/T 32869-2016纳米技术单壁碳纳米管的扫描电子显微术和能量色散X射线谱表征方法88GB/T 33040-2016热处理木材鉴别方法89GB/T 33161-2016汽车轴承用渗碳钢90GB/T 33522-2017渗碳轴承钢锻件技术条件91GB/T 33954-2017淬火-回火弹簧钢丝用热轧盘条92GB/T 33957-2017热处理炉热平衡测试与计算方法93GB/T 33967-2017免铅浴淬火钢丝用热轧盘条94GB/T 34484.1-2017热处理钢第1部分:非合金钢95GB/T 34560.4-2017结构钢第4部分:淬火加回火高屈服强度结构钢板交货技术条件96GB/T 34564.2-2017冷作模具钢第2部分:火焰淬火钢97GB/T 3488.1-2014硬质合金显微组织的金相测定第1部分:金相照片和描述98GB/T 34882-2017钢铁件的感应淬火与回火99GB/T 34883-2017离子渗氮100GB/T 34889-2017钢件的渗碳与碳氮共渗淬火回火101GB/T 34891-2017滚动轴承高碳铬轴承钢零件热处理技术条件102GB/T 3489-2015硬质合金孔隙度和非化合碳的金相测定序号标准代号标准名称备注103GB/T 34895-2017热处理金相检验通则104GB/T 36052-2018表面化学分析扫描探针显微镜数据传送格式105GB/T 4194-2017钨丝蠕变试验、高温处理及金相检查方法106GB/T 4296-2004变形镁合金显微组织检验方法107GB/T 4297-2004变形镁合金低倍组织检验方法108GB/T 5099.1-2017钢质无缝气瓶第1部分:淬火后回火处理的抗拉强度小于1100MPa的钢瓶109GB/T 5099.3-2017钢质无缝气瓶第3部分:正火处理的钢瓶110GB/T 5168-2008α-β钛合金高低倍组织检验方法111GB/T 5617-2005钢的感应淬火或火焰淬火后有效硬化层深度的测定112GB/T 5953.1-2009冷镦钢丝第1部分:热处理型冷镦钢丝113GB/T 5953.2-2009冷镦钢丝第2部分:非热处理型冷镦钢丝114GB/T 6462-2005金属和氧化物覆盖层厚度测量显微镜法115GB/T 6611-2008钛及钛合金术语和金相图谱116GB/T 7216-2009灰铸铁金相检验117GB/T 7232-2012金属热处理工艺术语118GB/T 7631.14-1998润滑剂和有关产品(L类)的分类第14部分:U组(热处理)119GB/T 8014.3-2005铝及铝合金阳极氧化氧化膜厚度的测量方法第3部分:分光束显微镜法120GB/T 8121-2012热处理工艺材料术语121GB/T 9095-2008烧结铁基材料渗碳或碳氮共渗层深度的测定及其验证122GB/T 9441-2009球墨铸铁金相检验123GB/T 9450-2005钢件渗碳淬火硬化层深度的测定和校核124GB/T 9451-2005钢件薄表面总硬化层深度或有效硬化层深度的测定125GB/T 9452-2012热处理炉有效加热区测定方法126CB/T 3385-2013船用钢铁零件渗氮层深度测定方法127JB/T 10174-2008钢铁零件强化喷丸的质量检验方法128JB/T 10312-2011钢箔测定碳势法。
机械零部件热处理相关标准
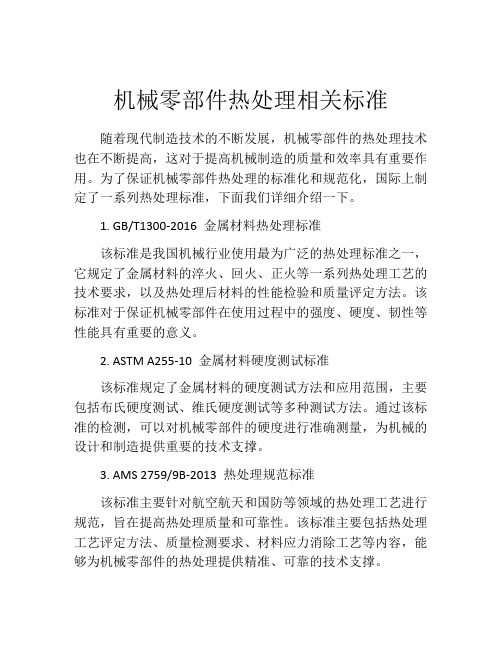
机械零部件热处理相关标准随着现代制造技术的不断发展,机械零部件的热处理技术也在不断提高,这对于提高机械制造的质量和效率具有重要作用。
为了保证机械零部件热处理的标准化和规范化,国际上制定了一系列热处理标准,下面我们详细介绍一下。
1. GB/T1300-2016 金属材料热处理标准该标准是我国机械行业使用最为广泛的热处理标准之一,它规定了金属材料的淬火、回火、正火等一系列热处理工艺的技术要求,以及热处理后材料的性能检验和质量评定方法。
该标准对于保证机械零部件在使用过程中的强度、硬度、韧性等性能具有重要的意义。
2. ASTM A255-10 金属材料硬度测试标准该标准规定了金属材料的硬度测试方法和应用范围,主要包括布氏硬度测试、维氏硬度测试等多种测试方法。
通过该标准的检测,可以对机械零部件的硬度进行准确测量,为机械的设计和制造提供重要的技术支撑。
3. AMS 2759/9B-2013 热处理规范标准该标准主要针对航空航天和国防等领域的热处理工艺进行规范,旨在提高热处理质量和可靠性。
该标准主要包括热处理工艺评定方法、质量检测要求、材料应力消除工艺等内容,能够为机械零部件的热处理提供精准、可靠的技术支撑。
4. JIS G 3193-2008 热轧产品的尺寸、重量及形状公差标准该标准主要规定了热轧产品的尺寸、质量和形状公差等要求,为机械零部件的制造提供标准化的技术要求和检测方法。
以上是目前机械零部件热处理相关的几个标准,它们的制定和实施,为机械制造行业的高效、精准生产提供了可靠保障。
在实际应用中,机械制造企业需要根据自身的生产需求和技术条件,选择合适的标准进行执行,并加强对标准的监督和检查,确保机械零部件的热处理达到标准化和规范化的要求。
热处理国家标准大全
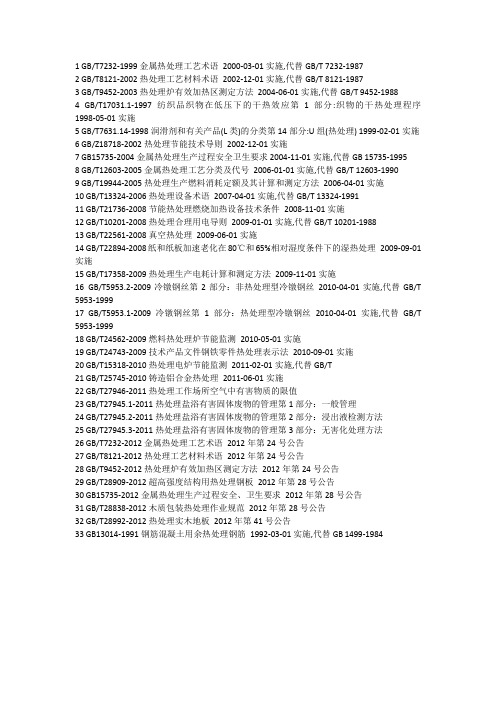
1 GB/T7232-1999金属热处理工艺术语2000-03-01实施,代替GB/T 7232-19872 GB/T8121-2002热处理工艺材料术语2002-12-01实施,代替GB/T 8121-19873 GB/T9452-2003热处理炉有效加热区测定方法2004-06-01实施,代替GB/T 9452-19884 GB/T17031.1-1997纺织品织物在低压下的干热效应第1部分:织物的干热处理程序1998-05-01实施5 GB/T7631.14-1998润滑剂和有关产品(L类)的分类第14部分:U组(热处理) 1999-02-01实施6 GB/Z18718-2002热处理节能技术导则2002-12-01实施7 GB15735-2004金属热处理生产过程安全卫生要求2004-11-01实施,代替GB 15735-19958 GB/T12603-2005金属热处理工艺分类及代号2006-01-01实施,代替GB/T 12603-19909 GB/T19944-2005热处理生产燃料消耗定额及其计算和测定方法2006-04-01实施10 GB/T13324-2006热处理设备术语2007-04-01实施,代替GB/T 13324-199111 GB/T21736-2008节能热处理燃烧加热设备技术条件2008-11-01实施12 GB/T10201-2008热处理合理用电导则2009-01-01实施,代替GB/T 10201-198813 GB/T22561-2008真空热处理2009-06-01实施14 GB/T22894-2008纸和纸板加速老化在80℃和65%相对湿度条件下的湿热处理2009-09-01实施15 GB/T17358-2009热处理生产电耗计算和测定方法2009-11-01实施16 GB/T5953.2-2009冷镦钢丝第2部分:非热处理型冷镦钢丝2010-04-01实施,代替GB/T 5953-199917 GB/T5953.1-2009冷镦钢丝第1部分:热处理型冷镦钢丝2010-04-01实施,代替GB/T 5953-199918 GB/T24562-2009燃料热处理炉节能监测2010-05-01实施19 GB/T24743-2009技术产品文件钢铁零件热处理表示法2010-09-01实施20 GB/T15318-2010热处理电炉节能监测2011-02-01实施,代替GB/T21 GB/T25745-2010铸造铝合金热处理2011-06-01实施22 GB/T27946-2011热处理工作场所空气中有害物质的限值23 GB/T27945.1-2011热处理盐浴有害固体废物的管理第1部分:一般管理24 GB/T27945.2-2011热处理盐浴有害固体废物的管理第2部分:浸出液检测方法25 GB/T27945.3-2011热处理盐浴有害固体废物的管理第3部分:无害化处理方法26 GB/T7232-2012金属热处理工艺术语2012年第24号公告27 GB/T8121-2012热处理工艺材料术语2012年第24号公告28 GB/T9452-2012热处理炉有效加热区测定方法2012年第24号公告29 GB/T28909-2012超高强度结构用热处理钢板2012年第28号公告30 GB15735-2012金属热处理生产过程安全、卫生要求2012年第28号公告31 GB/T28838-2012木质包装热处理作业规范2012年第28号公告32 GB/T28992-2012热处理实木地板2012年第41号公告33 GB13014-1991钢筋混凝土用余热处理钢筋1992-03-01实施,代替GB 1499-1984。
不锈钢 热处理 标准
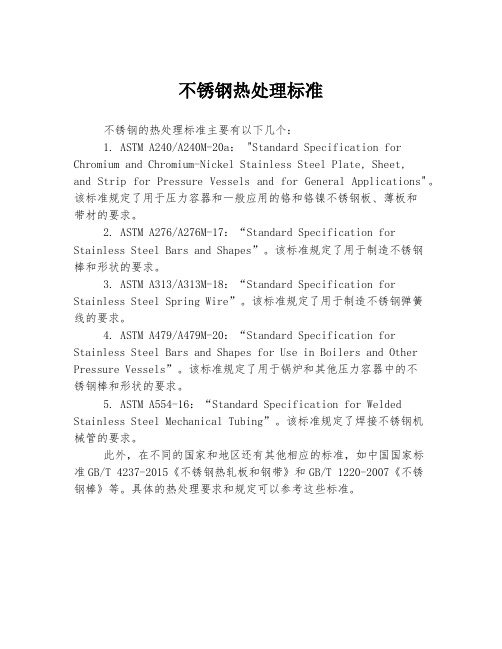
不锈钢热处理标准不锈钢的热处理标准主要有以下几个:1. ASTM A240/A240M-20a: "Standard Specification for Chromium and Chromium-Nickel Stainless Steel Plate, Sheet,and Strip for Pressure Vessels and for General Applications"。
该标准规定了用于压力容器和一般应用的铬和铬镍不锈钢板、薄板和带材的要求。
2. ASTM A276/A276M-17:“Standard Specification for Stainless Steel Bars and Shapes”。
该标准规定了用于制造不锈钢棒和形状的要求。
3. ASTM A313/A313M-18:“Standard Specification for Stainless Steel Spring Wire”。
该标准规定了用于制造不锈钢弹簧线的要求。
4. ASTM A479/A479M-20:“Standard Specification for Stainless Steel Bars and Shapes for Use in Boilers and Other Pressure Vessels”。
该标准规定了用于锅炉和其他压力容器中的不锈钢棒和形状的要求。
5. ASTM A554-16:“Standard Specification for Welded Stainless Steel Mechanical Tubing”。
该标准规定了焊接不锈钢机械管的要求。
此外,在不同的国家和地区还有其他相应的标准,如中国国家标准GB/T 4237-2015《不锈钢热轧板和钢带》和GB/T 1220-2007《不锈钢棒》等。
具体的热处理要求和规定可以参考这些标准。
中国热处理标准大全

中国热处理标准大全机械部热处理标准JB/T 10174-2000 钢铁零件强化喷丸的质量检验方法JB/T 10175-2000 热处理质量控制要求JB/T 3999-1999 钢件的渗碳与碳氮共渗淬火回火JB/T 4155-1999 气体氮碳共渗JB/T 4202-1999 钢的锻造余热淬火回火处理JB/T 4390-1999 高、中温热处理盐浴校正剂JB/T 7951-1999 淬火介质冷却性能试验方法JB/T 8929-1999 深层渗碳JB/T 9197-1999 不锈钢和耐热钢热处理JB/T 9198-1999 盐浴硫氮碳共渗JB/T 9199-1999 防渗涂料技术要求JB/T 9200-1999 钢铁件的火焰淬火回火处理JB/T 9201-1999 钢铁件的感应淬火回火处理JB/T 9202-1999 热处理用盐JB/T 9203-1999 固体渗碳剂JB/T 9204-1999 钢件感应淬火金相检验JB/T 9205-1999 珠光体球墨铸铁零件感应淬火金相检验JB/T 9206-1999 钢件热浸铝工艺及质量检验JB/T 9207-1999 钢件在吸热式气氛中的热处理JB/T 9208-1999 可控气氛分类及代号JB/T 9209-1999 化学热处理渗剂技术条件JB/T 9210-1999 真空热处理JB/T 9211-1999 中碳钢与中碳合金结构马氏体等级JB/T 8555-1997 热处理技术要求在零件图样上的表示方法JB/T 4215-1996 渗硼(代替JB4215-86和JB4383-87)JB/T 8418-1996 粉末渗金属JB/T 8419-1996 热处理工艺材料分类及代号JB/T 8420-1996 热作模具钢显微组织评级JB/T 7709-1995 渗硼层显微组织、硬度及层深测定方法JB/T 7710-1995 薄层碳氮共渗或薄层渗碳钢铁显微组织检验JB/T 7711-1995 灰铸铁件热处理JB/T 7712-1995 高温合金热处理JB/T 7713-1995 高碳高合金钢制冷作模具用钢显微组织检验JB/T 4218-1994 硼砂熔盐渗金属(代替JB/Z235-85和JB4218-86)低温化学热处理工艺方法选择通则JB/T 7519-1994 热处理盐浴(钡盐、硝盐)有害固体废物分析方法JB/T 7529-1994 可锻铸铁热处理JB/T 7530-1994 热处理用氩气、氮气、氢气一般技术条件JB/T 6954-1993 灰铸铁件接触电阻淬火质量检验和评级JB/T 6955-1993 热处理常用淬火介质技术要求JB/T 6956-1993 离子渗氮(代替JB/Z214-84)JB/T 6047-1992 热处理盐浴有害固体废物无害化处理方法JB/T 6048-1992 盐浴热处理JB/T 6049-1992 热处理炉有效加热区的测定JB/T 6050-1992 钢铁热处理零件硬度检验通则JB/T 6051-1992 球墨铸铁热处理工艺及质量检验JB/T 5069-1991 钢铁零件渗金属层金相检验方法JB/T 5072-1991 热处理保护涂料一般技术要求JB/T 5074-1991 低、中碳钢球化体评级中国国家热处理标准GB/T 18177-2000 钢的气体渗氮GB/T 7232-1999 金属热处理工艺术语GB/T 17358-1998 热处理生产电能消耗定额及其计算和测定方法GB/T 16923-1997 钢的正火与退火处理GB/T 16924-1997 钢的淬火与回火处理GB 15735-1995 金属热处理生产过程安全卫生要求GB/T 15749-1995 定量金相手工测定方法GB/T 13321-1991 钢铁硬度锉刀检验方法GB/T 13324-1991 热处理设备术语GB/T 12603-1990 金属热处理工艺分类及代号GB/T 11354-1989 钢铁零件渗氮层深度测定和金相组织检验GB/T 9450-1988 钢铁渗碳淬火有效硬化层深度的测定和校核GB/T 9451-1988 钢件薄表面总硬化层深度或有效硬化层深度的测定GB/T 9452-1988 热处理炉有效加热区测定方法GB/T 8121-1987 热处理工艺材料名词术语GB/T 5617-1985 钢的感应淬火或火焰淬火后有效硬化层深度的测定。
碳素结构钢热处理标准

碳素结构钢热处理标准
碳素结构钢的热处理标准主要包括淬火、正火、回火等步骤,具体标准可能因钢种和用途的不同而有所差异。
以下是一般情况下的碳素结构钢热处理标准:
1.淬火:将钢加热到临界点以上的某一温度,保温一段时间,然后以适当的速度
冷却,以获得马氏体或贝氏体组织,从而提高钢的硬度和强度。
淬火温度、保温时间和冷却速度等参数应根据钢种和用途进行选择。
2.正火:将钢加热到临界点以上的某一温度,保温一段时间,然后在空气中冷却,
以获得珠光体组织,提高钢的强度和韧性。
正火温度也应根据钢种和用途进行选择。
3.回火:将淬火或正火后的钢加热到某一温度,保温一段时间,然后以适当的速
度冷却,以消除内应力、稳定组织和提高钢的韧性。
回火温度和时间等参数应根据钢种和用途进行选择。
此外,对于某些特殊用途的碳素结构钢,可能还需要进行其他热处理操作,如表面淬火、化学热处理等。
需要注意的是,热处理过程中应严格控制加热温度、保温时间、冷却速度等参数,以获得理想的组织和性能。
同时,热处理后的钢材应进行适当的检验和测试,以确保其质量和使用性能符合标准要求。
机床铸件热处理标准
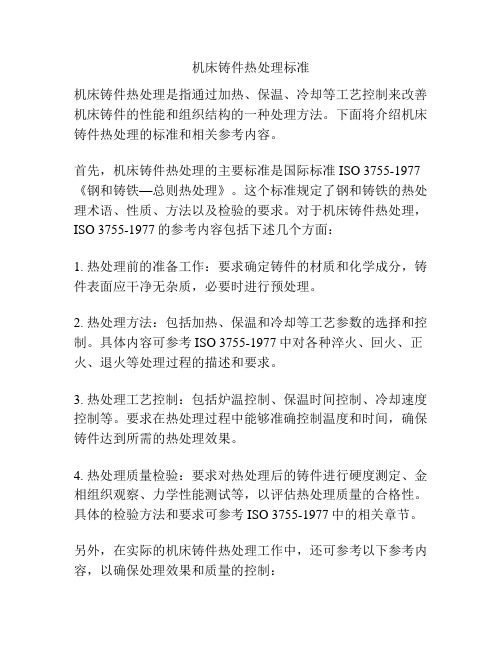
机床铸件热处理标准机床铸件热处理是指通过加热、保温、冷却等工艺控制来改善机床铸件的性能和组织结构的一种处理方法。
下面将介绍机床铸件热处理的标准和相关参考内容。
首先,机床铸件热处理的主要标准是国际标准ISO 3755-1977《钢和铸铁—总则热处理》。
这个标准规定了钢和铸铁的热处理术语、性质、方法以及检验的要求。
对于机床铸件热处理,ISO 3755-1977的参考内容包括下述几个方面:1. 热处理前的准备工作:要求确定铸件的材质和化学成分,铸件表面应干净无杂质,必要时进行预处理。
2. 热处理方法:包括加热、保温和冷却等工艺参数的选择和控制。
具体内容可参考ISO 3755-1977中对各种淬火、回火、正火、退火等处理过程的描述和要求。
3. 热处理工艺控制:包括炉温控制、保温时间控制、冷却速度控制等。
要求在热处理过程中能够准确控制温度和时间,确保铸件达到所需的热处理效果。
4. 热处理质量检验:要求对热处理后的铸件进行硬度测定、金相组织观察、力学性能测试等,以评估热处理质量的合格性。
具体的检验方法和要求可参考ISO 3755-1977中的相关章节。
另外,在实际的机床铸件热处理工作中,还可参考以下参考内容,以确保处理效果和质量的控制:1. GB/T 5613-2014《铸件热处理技术要求》:这个国家标准规定了铸件热处理的术语和定义、工艺要求、热处理工艺选择和控制、金相组织和力学性能的检验方法等。
是机床铸件热处理的指导性文件。
2. 机床铸件技术规范:根据具体的机床铸件要求,制定专门的技术规范。
这些规范包括对铸件材质、热处理工艺、质量检验等方面的详细要求,以确保热处理的实施和效果。
3. 机床铸件热处理操作规程:编制热处理操作规程,明确每个环节的操作要求和注意事项,从而保证人员能够按照规程进行热处理过程。
4. 机床铸件热处理工艺文件:编制详细的工艺文件,包括工艺流程、温度曲线和保温时间等参数,以方便操作人员进行控制和操作。
我国现行的热处理标准

我国现行的热处理标准序号标准级别号标准名称1 JB/T 10174-2000 钢铁零件强化喷丸的质量检验方法2 JB/T 10175-2000 热处理质量控制要求3 JB/T 3999-1999 钢件的渗碳与碳氮共渗淬火回火4 JB/T 4155-1999 气体氮碳共渗5 JB/T 4202-1999 钢的锻造余热淬火回火处理6 JB/T 4390-1999 高、中温热处理盐浴校正剂7 JB/T 7951-1999 淬火介质冷却性能试验方法8 JB/T 8929-1999 深层渗碳9 JB/T 9197-1999 不锈钢和耐热钢热处理10 JB/T 9198-1999 盐浴硫氮碳共渗11 JB/T 9199-1999 防渗涂料技术要求12 JB/T 9200-1999 钢铁件的火焰淬火回火处理13 JB/T 9201-1999 钢铁件的感应淬火回火处理14 JB/T 9202-1999 热处理用盐15 JB/T 9203-1999 固体渗碳剂16 JB/T 9204-1999 钢件感应淬火金相检验17 JB/T 9205-1999 珠光体球墨铸铁零件感应淬火金相检验18 JB/T 9206-1999 钢件热浸铝工艺及质量检验19 JB/T 9207-1999 钢件在吸热式气氛中的热处理20 JB/T 9208-1999 可控气氛分类及代号21 JB/T 9209-1999 化学热处理渗剂技术条件22 JB/T 9210-1999 真空热处理23 JB/T 9211-1999 中碳钢与中碳合金结构马氏体等级24 JB/T 8555-1997 热处理技术要求在零件图样上的表示方法25 JB/T 4215-1996 渗硼(代替JB4215-86和JB4383-87)26 JB/T 8418-1996 粉末渗金属27 JB/T 8419-1996 热处理工艺材料分类及代号28 JB/T 8420-1996 热作模具钢显微组织评级29 JB/T 7709-1995 渗硼层显微组织、硬度及层深测定方法30 JB/T 7710-1995 薄层碳氮共渗或薄层渗碳钢铁显微组织检验31 JB/T 7711-1995 灰铸铁件热处理32 JB/T 7712-1995 高温合金热处理33 JB/T 7713-1995 高碳高合金钢制冷作模具用钢显微组织检验34 JB/T 4218-1994 硼砂熔盐渗金属(代替JB/Z235-85和JB4218-86)35 JB/T 7500-1994 低温化学热处理工艺方法选择通则36 JB/T 7519-1994 热处理盐浴(钡盐、硝盐)有害固体废物分析方法37 JB/T 7529-1994 可锻铸铁热处理38 JB/T 7530-1994 热处理用氩气、氮气、氢气一般技术条件39 JB/T 6954-1993 灰铸铁件接触电阻淬火质量检验和评级40 JB/T 6955-1993 热处理常用淬火介质技术要求41 JB/T 6956-1993 离子渗氮(代替JB/Z214-84)42 JB/T 6047-1992 热处理盐浴有害固体废物无害化处理方法43 JB/T 6048-1992 盐浴热处理44 JB/T 6049-1992 热处理炉有效加热区的测定45 JB/T 6050-1992 钢铁热处理零件硬度检验通则46 JB/T 6051-1992 球墨铸铁热处理工艺及质量检验47 JB/T 5069-1991 钢铁零件渗金属层金相检验方法48 JB/T 5072-1991 热处理保护涂料一般技术要求49 JB/T 5074-1991 低、中碳钢球化体评级50 GB/T 18177-2000 钢的气体渗氮51 GB/T 7232-1999 金属热处理工艺术语52 GB/T 17358-1998 热处理生产电能消耗定额及其计算和测定方法53 GB/T 16923-1997 钢的正火与退火处理54 GB/T 16924-1997 钢的淬火与回火处理55 GB15735-1995 金属热处理生产过程安全卫生要求56 GB/T 15749-1995 定量金相手工测定方法57 GB/T 13321-1991 钢铁硬度锉刀检验方法58 GB/T 13324-1991 热处理设备术语59 GB/T 12603-1990 金属热处理工艺分类及代号60 GB/T 11354-1989 钢铁零件渗氮层深度测定和金相组织检验61 GB/T 9450-1988 钢铁渗碳淬火有效硬化层深度的测定和校核62 GB/T 9451-1988 钢件薄表面总硬化层深度或有效硬化层深度的测定63 GB/T 9452-1988 热处理炉有效加热区测定方法64 GB/T 8121-1987 热处理工艺材料名词术语65 GB/T 5617-1985 钢的感应淬火或火焰淬火后有效硬化层深度的测定(本文数据由液压英才网袁工分享)。
热处理检验方法国家标准
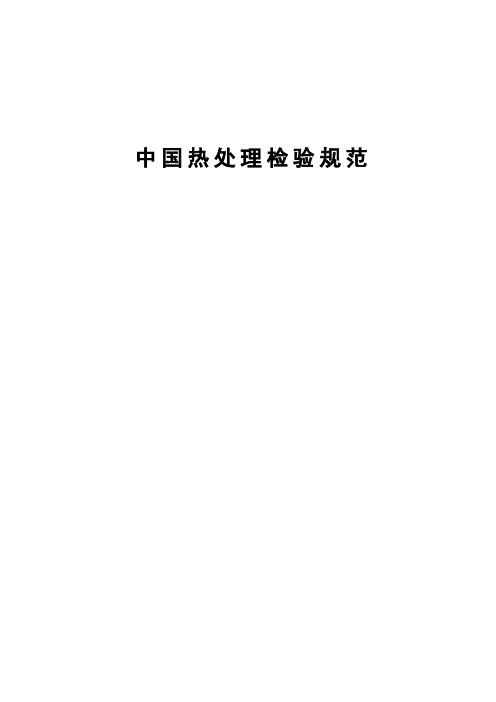
中国热处理检验规范热处理检验方法和规范金属零件的内在质量主要取决于材料和热处理。
因热处理为特种工艺所赋予产品的质量特性往往又室补直观的内在质量,属于“内科”范畴,往往需要通过特殊的仪器(如:各种硬度计、金相显微镜、各种力学性能机)进行检测。
在GB/T19000-ISO9000系列标准中,要求对机械产品零部件在整个热处理过程中一切影响因素实施全面控制,反映原材料及热处理过程控制,质量检验及热处理作业条件(包括生产与检验设备、技术、管理、操作人员素质及管理水平)等各方面均要求控制,才能确保热处理质量。
为此,为了提高我公司热处理产品质量,遵循热处理相关标准,按零件图纸要求严格执行,特制定本规范一、使用范围:本规范适用于零件加工部所有热处理加工零件。
二、硬度检验:通常是根据金属零件工作时所承受的载荷,计算出金属零件上的应力分布,考虑安全系数,提出对材料的强度要求,以强度要求,以强度与硬度的对应关系,确定零件热处理后应具有大硬度值。
为此,硬度时金属零件热处理最重要的质量检验指标,不少零件还时唯一的技术要求。
1、常用硬度检验方法的标准如下:GB230 金属洛氏硬度试验方法GB231 金属布氏硬度试验方法GB1818 金属表面洛氏硬度试验方法GB4340 金属维氏硬度试验方法GB4342 金属显微维氏硬度试验方法GB5030 金属小负荷维氏试验方法2、待检件选取与检验原则如下:为保证零件热处理后达到其图纸技术(或工艺)要求,待检件选取应有代表性,通常从热处理后的零件中选取,能反映零件的工作部位或零件的工作部位硬度的其他部位,对每一个待检件的正时试验点数一般应不少于3个点。
通常连续式加热炉(如网带炉):应在连续生产的网带淬火入回火炉前、回火后入料框前的网带上抽检3-5件/时。
且及时作检验记录。
同时,若发现硬度超差,应及时作检验记录。
同时,若发现硬度越差,应及时进行工艺参数调整,且将前1小时段的零件进行隔离处理(如返工、检)。
热处理方面的现行国家标准

热处理方面的现行国家标准热处理方面的现行国家标准1 GB/T7232-2012金属热处理工艺术语2013-03-01实施,代替GB/T 7232-19992 GB/T8121-2002热处理工艺材料术语2002-12-01实施,代替GB/T 8121-19873 GB/T9452-2003热处理炉有效加热区测定方法 2004-06-01实施,代替GB/T 9452-19884 GB/T17031.1-1997纺织品织物在低压下的干热效应第1部分:织物的干热处理程序 1998-05-01实施5 GB/T7631.14-1998润滑剂和有关产品(L类)的分类第14部分:U 组(热处理) 1999-02-01实施6 GB/Z18718-2002热处理节能技术导则 2002-12-01实施7 GB15735-2004金属热处理生产过程安全卫生要求2004-11-01实施,代替GB 15735-19958 GB/T12603-2005金属热处理工艺分类及代号2006-01-01实施,代替GB/T 12603-19909 GB/T19944-2005热处理生产燃料消耗定额及其计算和测定方法 2006-04-01实施10 GB/T13324-2006热处理设备术语2007-04-01实施,代替GB/T 13324-199111 GB/T21736-2008节能热处理燃烧加热设备技术条件2008-11-01实施12 GB/T10201-2008热处理合理用电导则2009-01-01实施,代替GB/T 10201-198813 GB/T22561-2008真空热处理 2009-06-01实施14 GB/T22894-2008纸和纸板加速老化在80℃和65%相对湿度条件下的湿热处理 2009-09-01实施15 GB/T17358-2009热处理生产电耗计算和测定方法2009-11-01实施16 GB/T5953.2-2009冷镦钢丝第2部分:非热处理型冷镦钢丝2010-04-01实施,代替GB/T 5953-199917 GB/T5953.1-2009冷镦钢丝第1部分:热处理型冷镦钢丝2010-04-01实施,代替GB/T 5953-199918 GB/T24562-2009燃料热处理炉节能监测 2010-05-01实施19 GB/T24743-2009技术产品文件钢铁零件热处理表示法 2010-09-01实施20 GB/T15318-2010热处理电炉节能监测2011-02-01实施,代替GB/T21 GB/T25745-2010铸造铝合金热处理 2011-06-01实施22 GB/T27946-2011热处理工作场所空气中有害物质的限值23 GB/T27945.1-2011热处理盐浴有害固体废物的管理第1部分:一般管理24 GB/T27945.2-2011热处理盐浴有害固体废物的管理第2部分:浸出液检测方法25 GB/T27945.3-2011热处理盐浴有害固体废物的管理第3部分:无害化处理方法26 GB/T7232-2012金属热处理工艺术语 2012年第24号公告27 GB/T8121-2012热处理工艺材料术语 2012年第24号公告28 GB/T9452-2012热处理炉有效加热区测定方法 2012年第24号公告29 GB/T28909-2012超高强度结构用热处理钢板2012年第28号公告30 GB15735-2012金属热处理生产过程安全、卫生要求 2012年第28号公告。
热处理标准

其正火温度一般为800~920℃,回火温度为600~650℃。
2GB3087及GB8163之20钢均注明热轧以热轧状态或热处理状态交货,冷轧以热处理状态交货。
其正火温度一般为800920回火温度为600650gb3087及gb8163之20钢均注明热轧以热轧状态或热处理状态交货冷轧以热处理状态交货
不同标准的区别
常
GB8162
(结构管)
常用10、20、35、45、Q345,
热轧或热处理状态交货;,双方协商也可以冷拔(轧)状态交货。
20钢抗拉强度≥390MPa,屈服强度≥225-245MPa;其它见标准。
GB8163(流体管)
常用10、20、Q295、Q345。
热轧或热处理状态交货。冷拔(扎)以热处理状态交货。
20钢抗拉强度410-550MPa,屈服强度≥235-245MPa;其它见标准。
GB5310
(高压锅炉管)
优质碳素结构钢:20G、20MnG、25MnG;合金结构钢:15MnG、20MoG、12CrMoG、15CrMoG、12Cr1MoVG等;不锈耐热钢:1Cr18Ni9
3Ar3---高温奥氏体的亚共析钢冷却时铁素体开始析出的温度
按标准规定的热处理制度进行热处理后交货。
当D≥76mm且S≥14mm的钢管应作纵向冲击试验;20G抗拉强度410-550MPa,屈服强度≥245MPa;其它见标准。
GB3087 (低中锅)
10、20
热轧或热处理状态交货;热轧状态交货终轧温度不低于Ar3。
20钢抗拉强度410-550MPa,屈服强度≥225-245MPa;其它见标准。
热处理执行标准讲解

九江消防装备有限公司结构钢热处理执行标准1.目的:规范本公司热处理车间结构钢的热处理作业流程,对结构钢的热处理过程、产品质量、成本等进行合理的控制。
2.适用范围:适用于本公司钢结构产品热处理的首件鉴定、产品过程的质量控制。
3.职责与权限:3.1车间主任:车间相关记录的审核确认,异常事件的协调处理。
3.2班组长:协助车间主任管理好本班组人员,保质保量完成生产任务。
3.3作业员:产品首件的检验、记录,完成下达的生产任务。
3.4设备管理员:对管辖的设备进行维护、维修,对操作设备的作业员进行设备维护要点培训。
4.编制依据:JB/T 10175-2000《热处理质量控制要求》JB/T 3999-1999《钢件的渗碳与渗氮共渗淬火回火》JB/T 3999-1999《热处理常用淬火介质技术要求》JB/T 6049-1992《热处理炉有效加热区的测定》JB/T 6050-1992《钢铁热处理零件硬度检测通则》GB/T 16924-1997《钢的淬火与回火处理》GB/T 15735-1995《金属热处理生产过程安全卫生要求》5.热处理方式按加热和冷却条件不同,结构钢件的主要热处理方式有:退火、正火、均匀化处理、淬火、回火、固溶处理、沉淀硬化、消除应力处理及除氢处理。
6.热处理操作要求6.1.退火退火是将结构钢件加热到Acs 以上20~30℃,保温一定时间,冷却的热处理工艺。
退火的目的是为消除钢件组织中的柱状晶、粗等轴晶、魏氏组织和树枝状偏析,以改善铸钢力学性能。
碳钢退火后的组织:亚共析结构钢钢为铁素体和珠光体,共析钢为珠光体,过共析钢为珠光体和碳化物。
适用于所有牌号的钢件。
图1—1为几种退火处理工艺的加热规范示意图。
表l—1为结构钢常用退火工艺类型及其应用。
表1-2结构钢退火工艺及退火后的硬度。
图1—1为几种退火处理工艺的加热规范示意图类别主要内容规格应用范围完全退火细化组织,软化结构钢组织,消除钢件内应力加热到Ac3以上30~50℃,保温后,炉冷(对高合金或厚大钢件冷速度控制小于50℃/h),炉冷至小于500℃后空冷一般工程用结构钢不完全退火降低硬度,改善切削性能,消除应力,但组织细化程度略低于完全退火加热到Ac1以上30~50℃,保温后,炉冷(对高合金或厚大钢件冷速度控制小于50℃/h),炉冷至小于500℃后空冷由于加热温度低、工艺过程短,提高了热处理炉的利用率,故使用较广对于工具钢或其他特殊条件的过共晶钢件,可作为淬火前的预处理球化退火使碳化物球化,降低硬度,改善切削性能加热到Ac1以上20~40℃,保温后,冷却到略低于共析钢或过共析钢件,可作为淬火前的预处理表1-2结构钢钢件退火工艺及退火后的硬度6.2.正火正火是将钢件目口热到Ac。
热处理作业标准书范本

火
炉
1-4区温度设定
510°C±10*4
当第一区回火温度在低于允许温度IO(TC时,第二区回火温度在低于允许50C,如第二区回火温度在低于允许温度50C以上时,需停止前进或将网带网速减慢。第三、四区允许温度在±10°Co
(备注;回火温度以淬火后所测硬度值可做相应的做一些调整)
回火时间设定
214Omin
淬火介质
KRlI8油
搅拌器
打开
喷射管
上中下全开
滓火后
检验
硬度
HRC50-55
100OKG以下检验一次,检验4个,每个打3点。100OKG以上每增加100OKG检验一次依次类推。。
清洗槽
清洗
喷射清洗
1.当压力降为0.1MPa时,需派人清洗过滤网。
2.每星期清洗二次喷射管,下料人员注意将油污及时排放出去。保持清洗槽固有水量和水温。
冷却槽
冷却
水冷
水槽定期加亚硝酸钠冷却避免生锈
回火后
检验
硬度
HRC32-36
硬度25分钟左右检测1次,每次检测3个,每个检测3点,100OKG以下检验一次』OOOKG以上每增加1000KG检验一次,依次类推。
核准
复核
*******
日期
*****
热处理作业标准书
版次
第二版
制订日期ห้องสมุดไป่ตู้
∩
品名规格
*******
材质
40Cr
品质要求
HRC32-36
工艺
调质
工程名称
作业条件
作业条件
注意事项
加料方法
入炉摆放二层,或WlOCm
铺料厚度均匀一致
淬
热处理的相关国家标准明细

GB/T18099.1-2001 金属努氏硬度试验第1部分:试验方法GB/T18499.2-2001 金属努氏硬度试验第2部分:硬度计的检验GB/T18499.3-2001 金属努氏硬度试验第3部分:标准硬度块的标定GB/T18517-2001 制冷术语GB/T4341-2001 金属肖氏硬度试验方法GB/T6807-200I 钢铁工件涂装前磷化处理技术条件GB/T9637-2001 电工术语磁性材料与元件GB/T10123-2001 金属和合金的腐蚀基本术语和定义GB/T18579-2001 高碳铬轴承钢丝GB/T3808-2002 摆锤式冲击试验机的检验GB/T18658-2002 摆锤式冲击试验机检验用夏比(ChaRPy)V型缺口标准试样GB/T228-2002 金属材料室温拉伸试脸方法GB/T18254-2002 高碳铬轴承钢G别T18681-2002 热喷涂低压等离子喷徐镍-钻-铬-铝-钇-钽合金涂层GB/T18682-2002 物理金相沉积TIN薄膜技术条件GB/T18683-2002 钢铁件激光表面淬火GB/T 18694-2002 无损检验超声检验探头及其声场的表征GB/T8121-2002 热处理工艺材料术语GB/T9096-2002 烧结金属材料(不包括硬质合金)冲击试验方法GB/T9097.l-2002 烧结金属材料(不包括硬度合金)表观硬度的测量第l部分,截面硬度基本均匀的材料GB/T10418-2002 碳化钨钢结硬质合金横向断裂慷鹊牟舛?/p>GB/T10419-2002 碳化钨钢结硬质合金冲击韧度的测定GB/T1042O-2002 碳化鸽钢结硬质合金洛氏硬度(c和A)的测定GB/T10422-2002 烧结金属摩攘材料横向断裂强度的测定GB/T10423-2002 烧结金属率据材料抗拉强度的测定GB/T10424-2002 烧结金属摩攘材料抗压强度的测定GB/T10425-2002烧结金属率擦材料表观硬度的测定GB/T13912-2002金属筱盖层钢铁制件热浸锌层技术要求及试验方法GB/T15519-2002化学转化膜铆铁黑色氧化膜规范和试验方法GB/T2100-2002 一般用途耐蚀钢铸件单位GB/T8492-2002 一般用途耐热钢和合金铸件些GB/T18718-2002 热处理节能技术导则GB/T18719-2002 热喷涂术语分类GB/T4553-2002 工业硝酸纳作GB/T238-2002 金属材料线材反复弯曲试验方法GB/T10126-2002 铁-铬-镍合金在高温水中应力腐蚀试验方法GB/T10127-2002 不锈钢三氯化铁缝隙腐蚀试验方法GB/T1617-2002 工业氯化钡GB/T18851-2002 无损检测渗透检验标准试块GB/T18852-2002 无损检测超声检验测量接触探头声束特性的参考试块的方法GB/T230.1-2004 金属洛氏硬度试验第1部分:试验方法(A、B、C、D、E、F、G、H、K、N、T标尺)GB/T230.2-2002 金属洛氏硬度试验第2部分:硬度计(A、B、C、D、E、F、G、H、K、N、T标尺)的检验与校准GB/T230.3-2002 金属洛氏硬度试验第3部分:标准硬度块(A、B、C、D、E、F、G、H、K、N、T、标尺)的标定GB/T231.1-2002 金属布氏硬度试验第1部分:试验方法GB/T231.2-2002 金属布氏硬度试验第2部分:硬度计的检验与校准GB/T231.3-2002 金属布氏硬度试验第3部分:标准硬度块的标定GB/T6394-2002 金属平均晶粒度测定法GB/T18907-2002 透射电子显微镜选区电子衍射分析方法GB/T王8930-2002 耐火材料术语GB/T18931-2002 残炭含量小于7%的碱性耐火制品分类GB/T5462-2003 工业盐GB/T18880-2002 粘结钕铁硼永磁材料(2003.6.1.实施)GB/T18876.1-2002 应用自动图像分析侧定钢和其它金属中金相组织、夹杂物含最和级别的标准试验方法第1部分:钢和其它金属中夹杂物或第二相组织含量的图像分析与体视学侧定GB/T 9452-2003 热处理炉有效加热区测定方法GB 15735-2004 金属热处理生产过程安全卫生要求JB/T 6048-2004 金属制件在盐浴中的加热和冷却GB/T 4160-2004 钢的应变时效敏感性试验方法(夏比冲击法)。
热处理符合含义

热处理类型——代号——表示方法举例
退火——Th——标注为Th
正火——Z——标注为Z
调质——T——调质后硬度为200-250HB时,标注为T235
淬火—— C——淬火后回火至45-50HRC时,标注为C48
油淬——Y——油淬+回火硬度为30-40HRC,标注为Y35
高频淬火——G——高频淬火+回火硬度为50-55HRC,标注为G52
调质+高频感应加强淬火—— T-G——
调质+高频淬火硬度为52-58HRC,标注为T-G54
火焰表面淬火—— H——火焰表面淬火+回火硬度为52-58HRC,标注为H54
氮化——D——氮化层深0.3mm,硬度>850HV,标注为D0.3-900
渗碳+淬火——S-C——氮化层深0.5mm,淬火+回火硬度为56+62HRC,标注为S0.5-C59 氰化——Q——氰化后淬火+回火硬度为56+62HRC,标注为Q59
渗碳+高频淬火——S+G——渗碳层深度0.9mm,高频淬火后回火硬度为56-62HRC,标注为S0.9-G59
CHD=case hardening depth(表面硬化深度)
EH-有效硬化层深度,为图样的技术要求。
用显微硬度表示。
EHT-有效硬化层深度,为图样的技术要求。
用显微硬度表示。
CHD-渗碳淬硬层深度,是对热处理工艺过程控制的要求,同样用显微硬度表示。
EHT=CHD-磨削余量。
当渗碳淬火后不进行磨削加工,那么EHT=CHD。
- 1、下载文档前请自行甄别文档内容的完整性,平台不提供额外的编辑、内容补充、找答案等附加服务。
- 2、"仅部分预览"的文档,不可在线预览部分如存在完整性等问题,可反馈申请退款(可完整预览的文档不适用该条件!)。
- 3、如文档侵犯您的权益,请联系客服反馈,我们会尽快为您处理(人工客服工作时间:9:00-18:30)。
1 目的为了力野公司铝合金热处理能实现精确控制,使热处理质量能有效保证,依此规范规定热处理工艺、设备及质量控制要求。
2 范围凡涉及我司铝合金产品热处理工序的相关部门及组织均适用.3 定义下列术语、定义适用于本规范。
3.1热处理本规范中所使用的“热处理”一词是本规范所包含的所有热处理的总称,例如:时效、固溶和退火。
3.2热处理批次一个热处理批次是指:由同一合金、同一产品形式、状态以及经历同一工艺过程的一定数量的一批零件。
3.3工作区工作区是指在一个热处理工艺的保温过程中,热处理设备被部件或原材料所占据的部分封闭空间。
该区通常(但不总是)占据整个封闭空间的大部分。
3.4固溶热处理造成的砂眼和气孔这种情况在过去被称为高温氧化。
现已公认,在固溶热处理过程中,进入到铝合金中的氢是造成表面砂眼和表层下面气孔出现的原因。
4 要求4.1 建立工艺操作规程和工艺操作规程重新审定4.1.1 基本原则生产前,热处理设备和工艺操作规程应达到本规范要求。
对于新建设备或维修后的设备,需进行检测,并建立或重新审定这些设备的工艺操作规程。
4.1.2 工艺操作规程重新审定的条件下列情形多次出现,则有必要重新审定工艺操作规程。
a. 原已验收的热处理设备,更换部件、彻底磨损、毁坏或改型需要磨合(见4.5.1~4.5.3);b. 现有热处理设备或其工艺操作规程不能满足本标准规定的质量要求(见5.6.4);c. 在定期工艺制度检查(见4.2)或定期产品监测过程中(见4.3)测出任何不合格(见5.1.3和5.6.4)。
4.2 定期工艺制度检查热处理设备和工艺操作规程应按表1规定进行检查。
4.3 定期产品监测应按表1规定对产品进行检验,以监测热处理设备的运行情况和工艺操作规程的适用性。
4.4 热处理设备4.4.1 热处理炉4.4.1.1 固溶热处理设备对于那些在有关热处理炉内进行固溶热处理(见A.3和3.4)而实验证明没有气孔产生的产品,可采用燃烧介质与金属接触的气室炉进行热处理。
4.4.1.2 时效热处理设备进行时效热处理的设备应能满足本标准规定的所有要求,同时生产出的产品能满足相应标准要求。
4.4.1.3 炉温均匀性检验炉温均匀性应符合有关工艺要求的规定。
4.4.1.4 温度均匀性在保温期间,保温区内任何一点的加热介质的温度都应受到控制,确保金属温度不会超过4.6.1规定的保温温度范围最大值、固溶热处理温度范围、时效温度范围(见4.9)。
4.4.2 温度控制设备4.4.2.1 基本原则所有热处理设备都应装有符合工艺控制要求的温控仪和记录仪,以确保加热过程和保温过程的温度控制均达到规范的要求。
4.4.2.2 温度控制和记录传感器的位置应由热处理炉的特性决定,并且传感器应置于能够准确测量工件和加热介质温度的位置。
记录应能正确反应温度控制情况,并可存贮记录以备查阅。
4.4.2.3 精确度应保证仪表的精确度,并进行定期检定。
4.4.3 淬火设备和介质4.4.3.1 基本原则淬火介质为水,并为这些介质配备适当的设备,如:循环,搅拌。
4.4.3.2 淬火槽淬火槽具备足够尺寸以保证材料能够完全浸没在淬火介质中,并保证能充分除去待淬火的预期载荷内的热量。
4.4.3.2.1 循环淬火槽应具备内部或外部循环系统,以保证淬火介质流动,如果搅拌充分,能保证淬火均匀,同时满足所有的要求。
根据5.2可对其监控,来效验。
4.4.3.2.2 加热和冷却淬火槽应具备足够的冷却能力,以保证淬火介质的温度达到4.7规定的范围。
同时,应配备必要的仪表以确保对温度进行控制。
该仪表读数与实际温度的偏差应在±3℃范围内。
4.4.3.2.3 浸没速度淬火系统应有控制固溶处理部件进入淬火介质速度的方法,如果该控制方法作为所要求的热处理工艺规程的一部分,不应超过所允许的最大淬火转移时间(见4.7.3)。
4.4.3.3 淬火设备的位置淬火设备和装卸装备的安装位置应保证淬火转移时间不得超过表5规定的最大淬火转移时间。
4.4.4 支撑架、固定装置及其它工件架持装置的结构铺设支承架时应当最低限地减少金属在固溶热处理时的振动或滑动。
支架、固定装置、底座、吊篮的安装应保证在热处理时不会对所处理的产品表面产生影响。
4.4.5 校准所有设备按有关热处理设备校准规定进行。
4.5 固溶热处理参数及工艺规程4.5.1 固溶热处理变形铝合金产品应按表2所规定的金属温度范围进行固溶热处理。
4.5.2 重复固溶热处理4.5.2.1包铝材料重复热处理次数不应超过表3的规定。
4.5.2.2重复固溶热处理的保温时间,可缩短至表4规定时间的一半。
4.5.2.3若连续式热处理炉加热速度足够快,只要不出现严重的包铝层扩散,则允许在表3的基础上增加一次重复固溶热处理。
4.5.2.4下列由材料生产厂提供的状态,除经批准外,在零件制造厂不应进行重复固溶热处理或退火。
4.5.2.4.1 HX6、HX4、T0、T73状态通常由材料生产厂提供,零件制造厂无法获得;4.5.2.4.2重复固溶热处理后,其抗拉强度会降低10N/mm2~20N/mm2。
4.5.3 热处理操作热处理操作应对整个工件进行,而不是局部。
进行热处理时应在材料外形限制范围内,且性能均匀。
4.5.4 清洁度固溶热处理后,产品表面不应有影响用户使用的其他外来物质。
4.5.5 炉料操作要求装炉前,应保证加热介质达到合金要求的温度,除非所有仪表均显示炉子已达到表2所规定的温度范围(包括较低的温度),才能在降温趋势下装炉,如果炉子是自动控制的,而且能确保在装入任何金属前炉温降至保温温度,可随时进行装炉.4.5.6 保温时间炉料已达到要求的固溶热处理温度范围后,应当在该温度范围内进行必要的保温,以确保合金元素尽可能固溶,以及效时后的性能,产品进行时效能达到该产品所适用的规范要求。
保温时间见表4,当炉料包含不同厚度的截面的产品时,保温时间按其中最大厚度的截面确定(见A.3.1)。
4.6 淬火参数和工艺规程4.6.1 非锻造变形产品的淬火2×××和7×××变形合金产品淬火参数和工艺规程应按4.7.1.2的规定执行。
4.6.1.1 水槽内全部浸没使用水槽时,水槽容积和水循环都应保证完成淬火时水槽温度不超过40℃。
淬火转移时间、产品和淬火液接触持续时间应分别按4.6.3和4.6.4的规定执行。
决定能否满足这些要求的试验程序应遵照表7的相应程序进行。
4.6.2 锻件淬火锻件可进行水淬火,只要淬火产品经过时效处理后达到规定的状态,能通过相关试验,满足技术标准规定的所有要求。
4.6.2.1 2014和2024锻件的淬火除非图纸或订货合同有规定,否则2014和2024锻件应当采用在60℃~80℃的水中完全浸没的方式进行淬火。
4.6.2.2 T41和T61状态除非图纸或订货合同有规定,否则热处理达到T41和T61状态的锻件和冷挤压件应当采用在沸腾的水中完全浸没的方式进行淬火。
4.6.3 淬火转移时间淬火产品浸没前所允许的最大转移时间应遵照表5规定,按产品截面厚度对应转移时间执行。
4.6.4 产品在淬火液中停留时间采用浸没淬火的产品,在淬火液中停留时间,按其厚度或其中最厚截面部分计算,每25mm厚度或不得少于2min。
或者说,沸腾停止后,产品在淬火液中的浸没时间不得少于2min。
4.7 装架和间距产品应进行装架,并保持间距,以允许加热和(或)淬火介质充分进入所有载荷区内的产品表面。
加热和淬火工艺规程的充分程度应当通过积累足够的数据,来证明符合相应的材料规范。
进行浸没淬火时,见5.4.2.1和5.4.2.3。
4.7.1 锻件的装架与间距除4.8.3规定外,锻件应相互间隔开,间距大于最大截面厚度,或按特殊装架工艺规程规定执行,保证产品经过充分加热或淬火。
4.7.1.1 固定装置固定装置应经过专门设计以保证对加热和淬火产生的影响最小,其定位应避免蒸汽截流,确保淬火液自由循环,防止蒸汽破坏淬火效果。
装炉量应加以限制,使水温升高不超过10℃。
如果经过试验和资料证明,产品能满足相应的材料规范的要求,允许温度升高超出上述规定。
4.7.1.2 随机装架厚度小于等于25mm的锻件,其随机装架或分层允许达到最大厚度75mm,架层之间最小间距为75mm,这样才能保证采取浸没方式淬火的产品质量。
如果产品能达到相应的材料规范的要求,上述情况允许有例外。
采用其他情况装架的产品试验结果记录应予以保留。
4.8 建议时效热处理表6列出了所推荐的时效温度和时间,对于不同外形、尺寸及生产方式都是典型的,对某种特定产品而言,可能不是最佳处理方法。
4.9 推荐的退火工艺表7列出了加工硬化变形铝合金的推荐退火制度。
对于特定产品要达到预期的结果,需确定最佳退火制度。
为避免过量氧化和晶粒生长,退火温度不应超415℃。
5 质量保证措施5.1 检查责任根据客户图纸要求制定检查项目。
除合同或订单另有规定外,质量监督部门不允许有的情况除外,生产厂家应使用自己的或其它适合的检查工具进行检查(按本文规定执行)。
质量监督部门保留本标准所规定的任何一项检查的执行权。
如果认为这些检查项目对保证供货和遵守服务规定要求是十分必要的,则应进行检验。
5.1.1 合格责任我司应保证客户所有产品符合合同规定所有的要求。
抽样检查作为生产管理的一部分,是确定产品符合要求的验收方法,不过抽样检查时,既不允许委托可能存在缺陷的或实际存在缺陷的材料,也不能提交使用方验收有缺陷的材料。
5.1.2 检查记录的保管除非另有规定,否则从检查之日起5年内检查记录及样品都应归档,以备查阅。
5.1.2.1 建立工艺规程和工艺规程重新审定记录建立工艺规程和工艺规程重新审定的记录应当归档保存直至废除或更换,然后再继续归档保存5年。
5.1.2.2 试验结果除客户有特殊要求,我司所有试验的结果都应保存5年(从试验之日算起),样品保存3年(从试验之日算起)。
5.1.2.3 生产过程记录除客户有特殊要求,生产过程记录都应从产品检验之日起归档保存5年,以备查阅。
5.1.2.4 热处理炉和淬火设备记录每台热处理炉和淬火设备的记录都应保存,以证明符合本标准的规定。
这些记录包括:炉号或热处理炉名称、工作区容量、使用的温度范围、是否用于固溶热处理、时效热处理或二者兼有、设备大修日期或更换元件型号,这些记录应归档保存以备查阅,一直保存到工艺规程重新审定后的5年。
5.1.3 热处理偏差能导致产品与本标准不符的任何热处理工艺变化或设备变化都构成偏差,除非这种偏差经客户书面认可,否则应当制止产品发货,直到该偏差(或这些偏差)得到纠正,并重新达到令人满意的性能。
5.2 热处理设备的温度检测根据设备验收标准及本规范相关要求,对热处理设备进行定期温度审定。