ECOG2DP103D中文资料
OMEGA CN3390系列多环PID温度 过程控制器说明书

ߜ10 PID Control Loops with Auto-Tuning ߜJ, K, T, E, R or S Thermocouple, RTD and 4 to 20 mA Current Input TypesSelectable for Each Loopߜ 2 Alarm Setpoints Per LoopߜOptical Isolation for ElectricallyNoisy EnvironmentsProgram 28145679103Probes sold separately.KQSS-316G-12, $25 eachSee Section AߜRelay, Triac, 4 to 20 mA andac SSR Output CapabilityߜOptional RS-232, RS-422 andRS-485 Digital CommunicationsߜCoded Security Levels to PreventUnauthorized Access to ProgrammingߜModular Construction Allows FieldInstallation of Output, Alarm, andCommunications OptionsCN3390 Series$2480Basic UnitMulti-Loop PID Temperature/Process Controllers CN3390 SeriesACCEPTS10 INPUTS!P-129P-130Takes the Place of Ten ControllersThe OMEGA ®CN3390 ON/OFF, proportional, PID Multi-Loop Temperature/Process Controller,measuring only 95 mm (3.75") deep, features the inputs,outputs, programmable features and sophisticated control techniques typically found only in much larger controllers. The CN3390 requires only 30% of the mounting space required for 10 individual controllers. All hardwiring is done once on high quality plug-on terminal strips, so the unit can easily be installed or taken out of service.The CN3390, with its optical isolation of inputs, outputs and optional digital communications, is built to handle most real-world factory conditionswithout special filtering equipment, such as snubbers,isolated power supplies or noise suppressors.Digital Signal Processing (DSP) sets the CN3390controller apart from other multi-loop controllers. DSP maintains the integrity of the sensor input signals, resulting in more stable control. Over-sampling of inputs (92 times per second per input) and an input update rate of 0.5 seconds per loop ensure that theCN3390 responds quickly to process changes.Through simple programming selections, you can adjust the controller displays to establish the range and engineering units of indication for the current input.The CN3390 provides two alarm setpoints per loop (20 total), and an alarm LED for each loop. Any of these 20setpoints can be connected to the common alarm output or one of ten optional alarm outputs. The common alarm output can be turned off fromeither the front panel alarm acknowledge pushbutton or from a remote pushbutton.The CN3390 alarm setpoints can be mapped to an optional internal alarm board. The alarm board’s digital alarm outputs or the common alarm can be connected to a remote single relay alarm module or an external 10-relay alarm output board.All control selections and programmed information are selectable from the front panel pushbuttons. Straightforward cues and high resolution LED’s send clear messages regarding the operation,set-up and programming of the controller. The autoscan feature scrolls through each loop, displaying process temperature, setpoint and loop number.Optional RS-232C, RS-422A and RS-485 digital communications are available for all 10 loops. Using RS-422A or RS-485, you can address up to 255 controllers.CN3390 offers flexible mounting: remote mounting,panel door mounting, or basic sub-panel mounting. The front panel display plugs directly into the controller chassis so it can be mounted remotely or simply removed to prohibit tampering or unauthorizedprogramming. Remote connection cables are available in 450 mm (18"), 1.5 m (5') and 4.5 m (15') lengths.CN3390 shown with remote mounting cableP-131SpecificationsControl Modes (Field Selectable)Automatic:ON/OFF,proportional, proportional with automatic reset/integral and/or rate/derivative (PID, PI, PD)Manual:Bumpless, balanceless transfer with proportional control;disintegration time = 1 to 100 sec Control Adjustments (Field Selectable)Control Setpoint:Instrument sensor range (°F, °C, %)Setpoint Limits:Instrument sensor range Deadband:0.01 to 25.00%Proportional Band:0.1 to 999.9% of span Automatic Reset:0.00 to 99.99repeats/minute Rate:0 to 1000 secondsOutput Cycle Time:0.1 to 60.0 secondsOutput Limit:0 to 100% ON Control Outputs (Plug-In):Total 5outputs modules, 2 control loops per output module Relay:N.O., rated 1.0 A @120Vac or 0.5 A @ 230 VAc (resistive load)1 A SSR: 1 A continuous, 10 A in-rush current at 120 or 230 Vac (resistive load)Current/Voltage:Non-isolated:4to 20 mA into 0 to 800 Ωload;isolated: 4 to 20 mA into 0 to 400Ωload with 24 V power supply SSR Pulse:transistor output of 20Vdc nominal at 40 mAAlarm Outputs: 2 field assignable alarm setpoints per loop, each can be mapped to any one of 10 alarm outputs or the common alarmoutput; 1 common latching alarm output, current limited, emitterfollower transistor; optional 10 open collector transistor outputs,sink 40mAdc at 50VdcAlarm Modes:High and low, range 100% of span, non-latching; ±deviation, sensor span above/below control setpointReset Differential: 0 to 25%instrument sensor range, 0.01incrementsAlarm Relay Board (Optional):10 relays, rated 10 A @ 120 V, form C contacts; includes 24 Vdc power supply (unregulated) to power relay coils; requires 120 Vac or 240 Vac inputInput Update Rate: 2 updates per second (92 samples per second)CN3390 Multi-Loop PIDTemperature/Process ControllersP-132two relays, one 1 A SSR, one 4-20 mA isolated and one 20 Vdc pulse control outputs, with optional digital communications, $2480 + 85 + 370 = $2935Ordering Example: CN3390-R , ten loop controller with ten relay outputs = $2480OCW-1 OMEGACARE SM extends standard 1-year warranty to a total of 2 years ($150), $2480 + 150 = $2630Open Sensor andOut-Of-Range Conditions:Programmable for 0-100% output Digital Communications Option: RS-232C single drop, isolated;RS-422A, RS-485 multi-drop, isolated; baud rate 300, 600, 1200, 2400, 4800, 9600, 19,200; data string ASCII,asynchronous, one start, one parity, seven data and one stop bit or binary Instrument Power:120 or 230 Vac(+10%, -15%), 50 to 60 Hz, 7 VA nominal power consumptionOperating Environment:0 to 55°C (30 to 130°F) ambient temperature with relative humidity less than 95% non-condensing Dimensions:318 W x 292 D x 95 mm L (12.5 x 11.5 x 3.75")Weight: 10 lb (4.5 kg)†3390A-RS is equivalent to -2optionOMEGACARE SM extended warranty program is available for models shown on this page. Ask your sales representative for full details when placing an order.CANADA www.omega.ca Laval(Quebec) 1-800-TC-OMEGA UNITED KINGDOM www. Manchester, England0800-488-488GERMANY www.omega.deDeckenpfronn, Germany************FRANCE www.omega.frGuyancourt, France088-466-342BENELUX www.omega.nl Amstelveen, NL 0800-099-33-44UNITED STATES 1-800-TC-OMEGA Stamford, CT.CZECH REPUBLIC www.omegaeng.cz Karviná, Czech Republic596-311-899TemperatureCalibrators, Connectors, General Test and MeasurementInstruments, Glass Bulb Thermometers, Handheld Instruments for Temperature Measurement, Ice Point References,Indicating Labels, Crayons, Cements and Lacquers, Infrared Temperature Measurement Instruments, Recorders Relative Humidity Measurement Instruments, RTD Probes, Elements and Assemblies, Temperature & Process Meters, Timers and Counters, Temperature and Process Controllers and Power Switching Devices, Thermistor Elements, Probes andAssemblies,Thermocouples Thermowells and Head and Well Assemblies, Transmitters, WirePressure, Strain and ForceDisplacement Transducers, Dynamic Measurement Force Sensors, Instrumentation for Pressure and Strain Measurements, Load Cells, Pressure Gauges, PressureReference Section, Pressure Switches, Pressure Transducers, Proximity Transducers, Regulators,Strain Gages, Torque Transducers, ValvespH and ConductivityConductivity Instrumentation, Dissolved OxygenInstrumentation, Environmental Instrumentation, pH Electrodes and Instruments, Water and Soil Analysis InstrumentationHeatersBand Heaters, Cartridge Heaters, Circulation Heaters, Comfort Heaters, Controllers, Meters and SwitchingDevices, Flexible Heaters, General Test and Measurement Instruments, Heater Hook-up Wire, Heating Cable Systems, Immersion Heaters, Process Air and Duct, Heaters, Radiant Heaters, Strip Heaters, Tubular HeatersFlow and LevelAir Velocity Indicators, Doppler Flowmeters, LevelMeasurement, Magnetic Flowmeters, Mass Flowmeters,Pitot Tubes, Pumps, Rotameters, Turbine and Paddle Wheel Flowmeters, Ultrasonic Flowmeters, Valves, Variable Area Flowmeters, Vortex Shedding FlowmetersData AcquisitionAuto-Dialers and Alarm Monitoring Systems, Communication Products and Converters, Data Acquisition and Analysis Software, Data LoggersPlug-in Cards, Signal Conditioners, USB, RS232, RS485 and Parallel Port Data Acquisition Systems, Wireless Transmitters and Receivers。
COMOSO AGE-Z 三指中心抓取器 Z 补偿单元说明书

Compensation Compensation309C O M P E N S A T I O NAGE-ZLight LoadCompensation unit for handling of w orkpieces with different height t olerances. The compensation unit c ompensates the horizontal offset of the placing position.Compensation Unit AGE-Z 803-Finger Centric GripperPZN-plus 80 withworkpiece-specific gripper fingersSizes 050 .. 080Payload 1 kg .. 5 kg Compensation paths Z ± 10 mmExample for applicationAGE-ZLight LoadISO flange patternfor easy mounting to most robot types without additional adapter platesLocking devicefor rigid switching of the unit in a defined extended or retracted positionCompact designfor minimum overall heightCan be combined with AGE-XY without additionaladapter plateCompensation unit with Z-axis yielding.Compensation UnitArea of applicationMounting, palletizing and insertion of workpiecesBenefitsGeneral information on the seriesCompensation path Z-direction: up to 10 mm Guides Solid guides ActuationPneumatic, filtered compressed air (10 µm): dry, lubricated or non-lubricated Operating pressure range 2 bar to 8 barMonitoring of the Z-stroke By magnetic switchesAmbient temperature 5° to 60° C MaterialAluminum alloy, hard-anodized.Functional components of hardened steel.Warranty 24 months311AGE-ZLight LoadHousingweight-reduced due to use of a hard-anodized, high-strength aluminum alloy Compression Springsfor defined pressure forces during placingMonitoring GrooveStroke monitoring of the locking piston with magnetic switches Ball Guides are Free of Playfor large maximum moments at a minimum sizeThe compensation unit AGE-Z enables a Z-compensation of different pickup and p lacing positions.The compensation unit is guided by a ball guide without play.Compression springs define the rigidity of the AGE-Z. which can be increased bya dditional actuation of the pneumatic cylinder.The cylinder also enables locking of the unit during dynamic movements. The r etracted and extended positions are monitored by means of magnetic switches.Function descriptionSectional diagramAGE-ZLight LoadExtreme ambient conditionsPlease be aware that use under extreme conditions (e.g. with coolants, or in the presence of casting dust or abrasive dust) can significantly reduce the tool life of these units, for which we can make no guarantee. In many cases, however, we have a solution. Please contact us.General information on the seriesFittingsMagnetic switch MMSSensor cableAccessoriesThe specific size of the desired accessories, availability for the model and the name and ID no. can be found in the additional diagrams following each model.For further information on our accessories, please consult the “Accessories” section of the catalog.313AGE-Z 050Light LoadTechnical dataDesignationAGE-Z-050ID 0324452Workpiece weight (recommendation)[kg] 1.0 Compensation stroke[mm]8.0Mounting, round mechanical interface ISO 9409-50-4-M6Spring force[N]10 - 30Extend piston force at 6 bar [N]300Retract piston force at 6 bar [N]270Weight[kg]0.35Forces and momentsLoad diagram Deflection of the AGE-Z under loadAGE-Z 050Light LoadMain viewsA Connection lockedB Air connection unlocked ᕃ Connection, robot-side ᕄ Connection, tool-sideᕇ Through-bores for screw connection with screw (enclosed)315www .s c h u n k .c o m AGE-Z 050Light LoadSensor systemEnd position monitoring:Electronic magnetic switches, for mounting in C-slot Designation ID Recommended product MMS 22-S-M5-NPN 0301439MMS 22-S-M5-NPN-SA 0301449MMS 22-S-M5-PNP 0301438MMS 22-S-M5-PNP-SA 0301448MMS 22-S-M8-NPN 0301433MMS 22-S-M8-NPN-SA 0301443MMS 22-S-M8-PNP 0301432•MMS 22-S-M8-PNP-SA 0301442MMSK 22-S-NPN 0301435MMSK 22-S-PNP 0301434 Two sensors (closers/S) are required for each compensation unit, plus extension cables as an option.Extension cable for proximity switches/magnetic switches Designation ID GK 3-M80301622GK 3-M5-PNP/NPN 0301652KV 10-M120301596KV 10-M80301496KV 20-M120301597KV 20-M80301497KV 3-M120301595KV 3-M80301495W 3-M120301503W 5-M120301507W 3-M5-PNP/NPN 0301650WK 3-M80301594WK 3-M8 NPN 0301602WK 5-M80301502WK 5-M8 NPN 9641116Please note the minimum permitted bending radii for the sensor cables, which aregenerally 35 mm.AGE-Z 050Light Load317AGE-Z 063Light LoadTechnical dataDesignationAGE-Z-063ID 032465Workpiece weight (recommendation)[kg] 2.0Compensation stroke[mm]8.0Mounting,round mechanical interface ISO 9409-63-4-M6Spring force[N]20–60Extend piston force at 6bar [N]560Retract piston force at 6bar [N]500Weight[kg]0.6Forces and momentsLoad diagram Deflection of the AGE-Z underloadAGE-Z 063Light LoadMain viewsA Locked air connectionB Unlocked air connection ᕃ Robot-side connection ᕄ Tool-side connectionᕇ Through-bore for screw connection with screw (enclosed)AGE-Z 063Light LoadSensor systemEnd position monitoring:Electronic magnetic switches, for mounting in C-slot Designation ID Recommended product MMS 22-S-M5-NPN 0301439MMS 22-S-M5-NPN-SA 0301449MMS 22-S-M5-PNP 0301438MMS 22-S-M5-PNP-SA 0301448MMS 22-S-M8-NPN 0301433MMS 22-S-M8-NPN-SA 0301443MMS 22-S-M8-PNP 0301432•MMS 22-S-M8-PNP-SA 0301442MMSK 22-S-NPN 0301435MMSK 22-S-PNP 0301434 Two sensors (closers/S) are required for each compensation unit, plus extension cables as an option.Extension cable for proximity switches/magnetic switches Designation ID GK 3-M80301622GK 3-M5-PNP/NPN 0301652KV 10-M120301596KV 10-M80301496KV 20-M120301597KV 20-M80301497KV 3-M120301595KV 3-M80301495W 3-M120301503W 5-M120301507W 3-M5-PNP/NPN 0301650WK 3-M80301594WK 3-M8 NPN 0301602WK 5-M80301502WK 5-M8 NPN 9641116Please note the minimum permitted bending radii for the sensor cables, which aregenerally 35 mm.AGE-Z 063Light LoadAGE-Z 080Light LoadTechnical dataDesignationAGE-Z-080ID 0324482Workpiece weight (recommendation)[kg] 5.0Compensation stroke[mm]10.0Mounting,round mechanical interface ISO 9409-80-6-M8Spring force[N]40-240Extend piston force at 6bar [N]840Retract piston force at 6bar [N]600Weight[kg]1.1Forces and momentsLoad diagram Deflection of the AGE-Z underloadAGE-Z 080Light LoadMain viewsA Locked air connectionB Unlocked air connection ᕃ Robot-side connection ᕄ Tool-side connectionᕇ Through-bore for screw connection with screw (enclosed)AGE-Z 080Light LoadSensor systemEnd position monitoring:Electronic magnetic switches, for mounting in C-slot Designation ID Recommended product MMS 22-S-M5-NPN 0301439MMS 22-S-M5-NPN-SA 0301449MMS 22-S-M5-PNP 0301438MMS 22-S-M5-PNP-SA 0301448MMS 22-S-M8-NPN 0301433MMS 22-S-M8-NPN-SA 0301443MMS 22-S-M8-PNP 0301432•MMS 22-S-M8-PNP-SA 0301442MMSK 22-S-NPN 0301435MMSK 22-S-PNP 0301434 Two sensors (closers/S) are required for each compensation unit, plus extension cables as an option.Extension cable for proximity switches/magnetic switches Designation ID GK 3-M80301622GK 3-M5-PNP/NPN 0301652KV 10-M120301596KV 10-M80301496KV 20-M120301597KV 20-M80301497KV 3-M120301595KV 3-M80301495W 3-M120301503W 5-M120301507W 3-M5-PNP/NPN 0301650WK 3-M80301594WK 3-M8 NPN 0301602WK 5-M80301502WK 5-M8 NPN 9641116Please note the minimum permitted bending radi for the sensor cables, which aregenerally 35 mm.AGE-Z 080Light Load 。
德威2系列数据采集模块与设备产品说明书
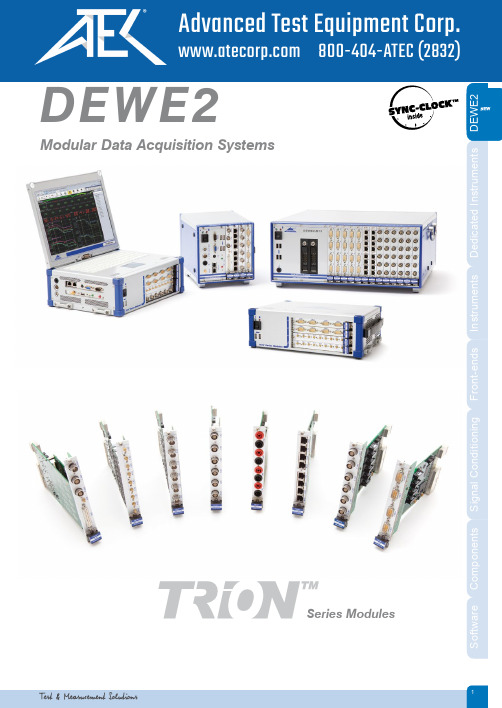
DEWE2Modular Data Acquisition SystemsemurtsnIdetacideDstnemurtsnIsdne-tnorFgninoitSeries Modules1H i g h s p e e d d a t a i n t e r f a ce2Data Acquisition ModuleSystem ArchitectureUser exchangeable TRION™ modulesSignal conditioning Flexible connectorpanelFiltering A/D conversionHigh speed data transfer and synchronizationDEWE2 System Architecture3Housing and Storage Controlling and AnalysisWide range of housingsDEWE2-A series All-in-one DEWE2-M series Mainframes DEWE2-F series Front-endsOne software for allFull hardware controlPowerful online or offline data processingAttractive online displays Fast data analysisPost processing and/or export to many file formats Simple reportsDEWE2 System Architecture4All-in-one instrumentsMainframesFront-endsMost compact, includes powerful i7 computer, brilliant display and keyboard, touchpad.Most convenient for all mobile applications like inspect-ing facilities, rotating machines, test stands, power generators, electrical machines, buildings, vehicles, aircrafts, trains, and anything else.Like the A-series but without display; keyboard and point-ing device are included loose.Very popular for applications where the instrument is installed in a poorly visible place for the user (e.g. in a car the instrument is often installed in the leg area of the passenger seat but the driver needs to see the screen) or laboratory applications and test rigs.F-series units don´t have a built-in computer but supply measurement data over a robust high-speed PCI Express bus. Multiple units can be daisy-chained.One popular application is to use F-series devices with a laptop computer for mobile applications.The second use of F-series devices is to expand A or M series instruments.A-seriesM-seriesF-seriesDEWE2 DefinitionsUse isolated inputs and differential inputs at the same timeInput connectors to match your sensorsAll TRION™ modules have a factory-exchangeable connector panelCustomized connector panels can be offered to match your sensors56ADC-clockB o a r d V o l t a g e [V ]7Fully battery poweredan internal buffer battery Need more battery time?Concerned about vibrations?Respectful of system restore?8SYNC it all!DEWE2 SynchronizationSynchronization of multiple DEWE2 systems via Sync-cableSync via TRION™ modulesTo use TRION-BASE or TRION-TIMING modules for synchronization of multiple units is the most convenient and easiest way.To create high channel count systems or for distributed measurements DEWE2 instruments sup-port multiple synchronization options. A special feature is the perfectly hardware synchronized video acquisition since also for data analysis the slogan ”a picture is worth a thousand words” istrue.Sync up to 1000 meters (IRIG DC, cable length delay compensation)Sync up to 100 meters via TRION-SYNC-BUSSync up to 100 meters via TRION-SYNC-BUSTwo DEWE2-A4 with option DW2-SYNCDEWE2-M13swith TRION-TIMING module DEWE2-M7swith TRION-BASE moduleDEWE2-A13with TRION-TIMING moduleDEWE2-A4with TRION-BASE moduleDEWE2-M7swith TRION-TIMING moduleExample:Two instruments synchronized via TRION-BASE modules (multiple units possible)Example: Three instruments synchronized via TRION-TIMING modules (multiple units possible)Sync via chassis optionsThese options do not block a module slot but need to be factory installed at time of initial order.Two instruments synchronized via DW2-SYNC option.WLANFactory installation only9VIDEO-SYNCHardware synchronized video of up to 200 frames per second(camera clocked by DEWE2 instrument):accurate per sample, no delaySoftware synchronized low-cost video (USB or PAL/NTSC cameras):optimized low latency, known delay of USB camera can be compensatedHigh speed video up to 500 000 frames per second:online sync for Photron cameras, post-sync for any high-speed .avi file.DEWE2 Synchronization Gigabit ethernet interface (up to 100 m cable length)SYNCDEWE2-A4 with optionTRION-BASE moduleDEWE-CAM-GIGE-120IRIGTwo instruments synchronizedto absolute IRIG timeGPSTwo instrumentssynchronized via GPSSynchronization to GPS or IRIG time-codeThere are 2 ways how to synchronize DEWE2 instruments very accurately to absolute time. Both, GPS time and IRIG time, enable execution of synchronized distributed measurements over unlimited distances. Each instrument (or array of instruments) must be connected to the time-code via a TRION-TIMING module. 10DEWE2A ll-In-OneInstrumentsDEWE2 All-in-One InstrumentsDW2-UPS-150-DCThe hot-swappablebatteries guaranteecontinuous operation with-out an external power source.A-seriesDEWE2-A7DEWE2-A4 withRemovable Solid State Disk DEWE2-A13S Y N CP C IeP C I eDEWE-818DEWE2-F18DEWE2-F18DEWE2-F4sPCIe connection up to 7 metersPCIe connection up to 7 metersTRION-SYNC-busDEWE2-F7s with optionDW2-LINK-PCIE-2-S11DEWE2 Front-endsDEWE2 F ront-endsF-series12DEWE2 M ainframesM-seriesDC PowerRS-232DEWE2-M7sDW2-UPS-150-DCThe hot-swappable batteries guarantee continuousoperation without external power sourceDEWE2-M13DEWE2 Mainframes13DEWE2-M13-MK19“ mounting kit for the DEWE2-M13 series, 4U MOB-DISP-12-A Very rugged external displayDEWE2 Mainframes14DEWE2-A4 / M4DEWE2-A4 / M44 slots for TRION™ series modules Isolated wide range DC power supplyOptional internal buffer battery for ~10 minutes Fully battery-powered by stackable battery pack Removable solid state diskPowerful Intel ®Core™ i7 processorChannel ExpansionPCIe connection up to 7 metersTRION-SYNC-busDEWE2-F7s with option DW2-LINK-PCIE-2-SDEWE2-F7s with option DW2-LINK-PCIE-2-SDEWE2-A4 with two channel expansion chassis DEWE2-F7s15BAT-CHARGER-1BAT-CHARGER-4MOB-DISP-12 External displayDE-POWERBOX-12 DC Power distribution box FLEXRAY-INT-1 option DW2-LINK-PCIE-1-S optionSSD-32-64/128/256 Flash disk upgrade16DEWE2-A7 / A137 / 13 slots for TRION™ series modules Powerful Intel ® Core™ i7 processor Brilliant 17'' full-HD displayOptional fully battery poweredPCIe connection up to 7 meters PCIe connection up to 7 meters TRION-SYNC-busTRION-SYNC-busDEWE2-F7s with TRION-TIMING moduleDEWE2-F13s with option DW2-LINK-PCIE-2-SDEWE2-A7 with option DW2-LINK-PCIE-1-SDEWE2-A7 / A1317Shipping/carrying case for the DEWE2-A7 or DEWE2-A13 mainframe. Common-carrier rated, internal custom foam cut-out, high impact construction. Hasps for attaching padlocks, pull-out handle and wheels for easy transport External power supply, input voltage 10 to 36 V DC (max.), output 24 V DC 300 W Lithium-Ion battery, 14.4 V, 95 Wh, max. 8 ADesktop battery charger for 1 battery, incl. external AC adaptor Desktop battery charger for 4 batteries, incl. external AC adaptorBAT-CHARGER-1BAT-CHARGER-4DW2-A13-CC Shipping/carrying caseDEWE-DCDC-24-300-ISO Carrying bagDEWE2-A13DW2-SYNC optionDEWE2-A13 with DW2-A13-PS-BAT optionPCIe connection up to 7 meters (250 MB/s)TRION-SYNC-bus18DEWE2-M4s / M7s / M13sDEWE2-M4s / M7s / M13s4/7/13 slots for TRION™ series modules All connections at the frontIsolated wide range DC power supplyOptional internal buffer battery for ~10 minutes Powerful Intel ® Core™ i7 processorChannel ExpansionDEWE2-F13s with option DW2-LINK-PCIE-2-SDEWE2-M7s with option DW2-LINK-PCIE-1-SMOB-DISP-12 External display19BAT-CHARGER-1BAT-CHARGER-4DE-POWERBOX-12 DC Power distribution box DEWE2-M7s with option DW2-LINK-PCIE-1-S 4U 5UM13s installed into a 19” cabinet5 u required (4 u = system + 1 u = cooling)PCIe connection up to 7 metersTRION-SYNC-busDEWE2-F18 with option DW2-LINK-PCIE-2-SDEWE2-M13 with TRION-TIMING module and LINK-HOST-PCIE card20DEWE2-M1313 slots for TRION™ series modules Free PCI slots insideOne internal hard disk and 2 bays for removable disks 19” rack-mountable or benchtop useDEWE2-M13Channel Expansion21DEWE2-M13 with 2x option DW2-M13-BAY35-SATADEWE2-M13 and DEWE-TFT19-RM Rack-mounting 19“ display5 u required(4 u = system + 1 u = cooling)DEWE2-M13 with typical PCI slot configuration4U 5UPCIe connection up to 7 meters (250 MB/s)TRION-SYNC-bus 22DEWE2-F4s / F7s / F13sDEWE2-F4s / F7s / F13s4 or 7 slots for TRION™ series modulesPCI Express data link120 MB/s data transfer rateDEWE2-F13s withDW2-LINK-PCIE-2-S optionDEWE2-F7s withDW2-LINK-PCIE-2-S optionDEWE2-F4s withTRION-TIMING module Channel ExpansionBAT-CHARGER-1BAT-CHARGER-4DW2-UPS-150-DC,130 W UPS with 2 slots for batteries 23t i o n i n g F r o n t -e n d s I n s t r u m e n t s D LINK-HOST-PCIE DEWE2-F7s with optionDW2-PS-DC-150DEWE2-F13s with option DW2-LINK-PCIE-2-S DEWE2-F13s with optionDW2-PS-AC-REDDEWE-UPS-300-DC300 W UPS with 4 slots for batteriesDEWE2-F13s with optionDW2-F13x-MK24DEWE2-F1818 slots for TRION™ series modules PCI Express data link 120 MB/s data transfer rate19" rack-mountable or benchtop useDEWE2-F18Channel ExpansionSeries Modules Series Modules Overview25Series Modules26Series Modules27T R I O N -2402-d A C C -8-S M BT R I O N -2402-d A C C -6-B N C28Differential multi-function input moduleSampling: 24 bit; 204.8 kS/s per channelInput types:Voltage measurement from ±30 mV to ±70 V DC (46.7 V RMS AC)IEPEResistanceCurrent (using external shunt)Additional feature:AUX socketTRION-2402-dACCSeries Modules1)For safety reasons maximum allowed voltage: 70 V DC (46.7 V RMS AC)2930Differential universal input moduleSampling: 24 bit; 204.8 kS/s per channelInput types: Voltage up to ±10 VStrain gauge, bridge sensor, piezoresistive bridge IEPERTD; Pt100 to Pt2000Resistance, potentiometerTRION-2402-dSTG T R I O N -2402-d S T G -8-R JT R I O N -2402-d S T G -8-DT R I O N -2402-d S T G -6-L E M OSeries ModulesTRION-CBL-RJBN-01-00Isolated wide range voltage moduleSampling: 24 bit; 204.8 kS/s per channelInput types: Voltage ±300 mV to ±1000(2) VDCCurrentIsolation: 4 kVTRION-2402-VTRION-242-V-4-BTRION-242-V-8-BDAQ-SHUNT1(not compatible with TRION-x-V-4 modules)DAQ-SHUNT4DAQ-SHUNT5Shunts for TRION™ voltage input modulesCounter, DIO and synchronization moduleCounter channels: 2 SuperCounters™ Digital I/O: 8 DIO and 8 DISynchronization: IRIG code B, DC I/O and Sync I/OAdditional features:1 AUX socket (by default set to camera trigger)TRION-BASET R I O N -B A S ETiming and synchronization moduleTiming:Isolated IRIG input and output Synchronization: 2 TRION-SYNC-BUS interfaces Additional features:8x DIO, 1x counter, 1x AUXTRION-TIMINGT R I O N -T I M I N GIsolated SuperCounter™ moduleSampling 80 MHz time base204.8 kS/s per channelInput types Event, waveform timing and sensor modeProgrammable threshold and AC/DC coupling for ideal signal adaptionTRION-CNT T R I O N -C N T -6-L E MOCables for TRION-CNT modulesMating connectorIsolated digital input moduleNumber of channels: 48 isolated digital inputs (TRION-DIO-4800) Sampling:204.8 kS/s per channelTRION-DIO-4800T R I O N -D I O -4800TRION-CB24-B Options for TRION-DIO modulesTRION-CB24-SCIsolated high speed CAN interfaceInput types High speed, (low speed and single wire with optional converter)Listen only and programmable terminationDirect interface to CPAD2 module seriesTRION-CAN T R I O N -C A N -4-DT R I O N -C A N -2-DCables for TRION-CAN modulesADAP-CAN-LS-HS ADAP-LIN-CANOptionsARINC 429 module with up to 30 interfacesMIL-STD-1553 modules with up to 4 dual redundant channelsMixed modules with 8 ARINC and up to 5 dual redundant MIL-STD-1553 channelsT R I O N -A 429TRION-A429 / M1553 / MA4Model overviewAnalog output module2 channel TRION™ analog output module, based on NI PXI-6251voltage range max. ±10 V 16 bit resolutionUpdate rate max. 2.8 MS/sT R I O N -1628-A O -2TRION-1628-AO-2DEWETRONGmbH•Parkring4•A-8074Graz-Grambach•Tel(0043)31630700•Fax(0043)316307090•*****************。
Co-Evolving Application Code and Design Models by Exploiting Meta-Data

Co-Evolving Application Code and Design Models byExploiting Meta-DataWalter CazzolaDept.of Informatics andCommunication, Universit`a degli Studi di Milano cazzola@dico.unimi.itSonia PiniDept.of Informatics andComputer Science,Universit`a degli Studi di Genovapini@disi.unige.itAhmed Ghoneim,Gunter SaakeInstitute f¨ur T echnische undBetriebliche Informationssysteme,Otto-von-Guericke-Universit¨at Magdeburg{ghoneim|saake}@iti.cs.uni-magdeburg.deABSTRACTThe evolvability and adaptability are intrinsic properties of today’s software applications.Unfortunately,the urgency of evolving/adapt-ing a system often drives the developer to directly modify the ap-plication code neglecting to update its design models and docu-mentation.Even,most of the development environments support the code refactoring without supporting the automatic refactoring of the design information.Refactoring,evolution and in general every code changes should be reflected into the design models,so that these models consis-tently represent the application and can be used in the successive maintenance steps and for documenting the application.The code evolution should not evolve only the application code but also the application design models.Unfortunately,to co-evolve the applica-tion code and its design is an hard job to be carried out automati-cally,since there is a evident and notorious gap between these two representations.In this paper,we propose a new approach to code evolution(in particular code refactoring)that supports also the automatic co-evolution of the corresponding design models.The approach relies on a set of predefined meta-data that the programmer should use to annotate the application code and to highlight the refactoring performed on the code.Then,through reflection,these meta-data are retrieved and used to automatically and consistently update the application design models.KeywordsSoftware Evolution,Co-Evolution,Refactoring,Meta-Data,Re-flection.1.INTRODUCTIONSoftware maintenance covers most part of the software life cycle. Software maintenance takes place to tackle softwareflaws(correc-tive maintenance)and to adapt the application to new requirements (software evolution and refactoring).Normally,the software main-Permission to make digital or hard copies of all or part of this work for personal or classroom use is granted without fee provided that copies are not made or distributed for profit or commercial advantage and that copies bear this notice and the full citation on thefirst page.To copy otherwise,to republish,to post on servers or to redistribute to lists,requires prior specific permission and/or a fee.Copyright200X ACM X-XXXXX-XX-X/XX/XX...$5.00.Figure1:The development process is not bijective. tenance should follows exactly the same steps followed during the software development:starting by planning the maintenance on the application design models and then applying it on the code. This seldom happens since adapting the design models to satisfy the new requirements and then update the code takes more time than directly modify the code.Successively,sometimes,the design models are modified to match the changes performed on the code. Unfortunately,adapting the design models from the evolved code is difficult and prone to erroneous interpretations.Whereas de-scending through the different levels of abstraction is relatively straightforward and well supported by methods and tools,the syn-thesis of design information from an evolving implementation is far from obvious in particular if it should be automatically done.The development process,as shown in Fig.1,is not bijective or betterby reversing the implemented code we got a set of design models different from the original one.The developer implementing the design models interprets them and adopts programming techniques and patterns derived from his/her experience and skilling that can-not be replicated by any reverse engineering technique.Moreover, the design models rarely detail every aspect of the application that need the developer’s cleverness to be realized.These facts con-tribute to form a design/implementation gap[4]between the two representations(design models and code)that become wider when the code has been modified hampering the detection of the changes in the code and the corresponding updating of the design models. It is fairly evident that software maintenance and evolution im-pact on both the application code and design models.Since the de-sign/implementation gap the code evolution should not precede the design models evolution but they should evolve together(software co-evolution[5]:software evolution requires the synchronization between different views in the software development process).At least,the gap should befilled during the code evolution by pro-viding the necessary data to connect the evolved code to how the design models should evolve to match the evolution.In this paper,we propose a technique,based on our previous work[3],that permits to automatically update the application de-sign models after the code adaptation.In practice,when the pro-grammer changes the application code,he/she decorates the code with a set of pre-defined meta-data describing how the code has evolved.These meta-data will be successively retrieved through reflection and used to automatically update the application design models.In this way,the developer can focus on the code evolution, saving time,and with a little effort achieving also the evolution of the application design models.At the moment,the work focuses on the refactoring techniques(a special case of software evolution[6])since they provide catalogs of common and well defined evolutionary situations that can be easily used as a basis for the definition of our set of meta-data.In the future,the approach will be extended to support more general software evolution activities.Analogously,we consider the UML as the modeling language and Java as the application programming language but the approach can be easily applied to any modeling language and programming language with meta-data supports. The rest of the paper is structured as follows:section2,describes how meta-data can be used to trace code evolution and introduces our set of annotations.Section3shows on a case study how to annotate the application code to trace its refactoring.Section4 shows how the meta-data are used to update the application design models.Finally,in sections5and6we present some related work and draw our conclusions.2.REFACTORING AND META-DATAMany refactoring catalogs have been presented in the last few years.Martin Fowler in his book[6]has proposed one of the rich-est and most used collection of refactoring actions.Few of those actions involve applications details whose change little impacts on the application design models and will be neglected in this work. The kind of refactorings we consider are classified as follows: Type1-Physical Structure–rename;–move;–change signature;–to instance method;Type2-Class Level Structure–push down –pull up –extract interface–extract superclassType3-Structure Inside a Class–extract method;–form template method;–introduce parameter;–(self)encapsulatefieldThefirst group refers to refactoring actions quite general thatsimilarly affect all the application aspects.The second group refersto refactoring actions that affect the application structure only at theclass level.Whereas the third group refers to refactoring actionsthat affect only the code within a class.It should be well known that refactoring actions are carried outdirectly on the application code and that they are supported bymost of the development environments.Notwithstanding that thechanges performed on the code impact also on the application de-sign,the developer performing the refactoring rarely refactors thedesign models as well.A post-refactoring update of the design models is particularlydifficult since the refactoring actions change the code structure break-ing the link with the original design models,if any.Consider theextract method refactoring action it promotes some recurring pieceof code to be the body of a new method and replace all the occur-rence of that piece of code with a call to the new method.From thepoint of view of the design models,this impacts on the structuralmodels by introducing the new method and on the behavioral mod-els(such as the sequence and the activity diagrams)by substitutingthe description of the promoted code with a call to the new methodor simply by introducing a new referencing step in the ac-tions involving the new method.After the refactoring,the code isclean and the only clue of the piece of code presence is representedby the new method call but the removed code could crosscut manyuse cases and from this clue is not easy to go back to all those usecases.It becomes still more difficult when the developer performseveral refactoring actions on the code.As stated before,the urgency requirement renders difficult to co-evolve the design models contemporary to the code but mining thecode looking for the necessary data to evolve the design models isdifficult as well because there are not enough clues to reconstructthe whole history of the performed refactoring from the refactoredcode.What it is missing is an agile mechanism to document thecode refactoring against the application design without losing toomuch time in the operation or better that could be automated by thedevelopment environment.This mechanism should provide enoughdetails and clues to permit the automatic update of the design afterthe code evolution.To this respect,we propose to decorate the code with meta-data(our clues)tracing the performed refactoring.In the case of Ja-va,we exploit the annotation mechanism provided by the program-ming language.Each refactoring action differently affects the de-sign models and specific data characterize each occurrence of theaction,e.g.,a rename action applied to afield is different than whenapplied to a method and the old and new names characterize eachuse of the action and must be reported to reconstruct it on the de-sign models.Not only the effect of the refactoring can be scatteredall around the code as in the case of the extract method action andthe annotations must describe the role of the change,e.g.,the newmethod and where the code has been extruded.Therefore,to eachrefactoring action is associated a set of annotation that permits ofdocumenting all the aspects of the performed refactoring actions.During the code refactoring,the developer simply annotate the codewith the annotation corresponding to the refactoring action he/shehas performed andfilling in the data identifying the specific case.The annotations do not introduce an overhead in the applicationexecution and live inside the application since a specific tool stripthem of the code and update the design models consequently.2.1Meta-Data:Java AnnotationsSince Java5[9],the platform provides a general purpose and customizable annotation mechanism(also known as meta-data fa-cility)that allows the programmer to define and use user-defined annotation types.The facility consists of a syntactic mechanism to declare annotations and annotate declarations,APIs to retrieve annotations through reflection,and of a classfile representation for annotations.Each new annotation requires the definition of a corresponding annotation type.Annotation types are a sort of interfaces with an extra’@’(at)sign before the interface definition,then the annota-tions can be specified in the program source by using the annotation name prefixed by an’@’sign.Annotations are the corner stone of our approach to the code and design models co-evolution,but there is a significant limit into the Java annotation model,that is,its granularity.It is possible to annotate any kind of declarations(e.g.,classes andfields declara-tions)but it is impossible to annotate a genericstatementor codeblock,e.g.,to put annotations inside the body of a method1.Code block and statement annotations are useful to trace specificaspects of some refactoring actions(for example,to specify wherethe code has been removed by the extract method refactoring with-out conflicts)and to reduce the data passed to the annotation bynarrowing the area affected by the action.@Java2is a simpleextension of the Java programming language,we developed af-ter our experience on[a]C#[2],that provides a Java5compliantannotation model supporting code block and statement annotations.The meta-data are strictly coupled with the refactoring actionthey should trace.Depending on how a refactoring actions impacton the design models,we have to trace different information.Fromcase to case the developer will have to use the appropriate set ofannotations.For sake of brevity we cannot explain all the cases butjust a couple of the refactoring actions present in the Fowler’s cata-log[6],further details can be read in the package documentations.2.1.1Move MethodThe move method refactoring action moves a method from aclass to another to simplify thefirst class or to decouple it fromthe second class.Thefirst effect on the application design is quite evident:themethod changes its position and the application class diagram mustreflect this fact.To post evolve the design after this kind of refac-toring we must know where the method is coming from and whichclass diagram should be changed.The attributes of the MoveMethod annotation stores these data.The name of the moved method and the destination class are datathat can be retrieved from the annotated element(i.e.,the movedmethod declaration)by using reflection.A secondary and less evident effect on the application designis represented by the changes to the calls to and from the movedmethod.After the refactoring,different actors are involved andsequence and activity diagrams must reflect this fact.It can be con-sidered a secondary effect since not always the behavioral modelsare so detailed but in the case they have to be accordingly updated.1Note that the C#annotation model suffers of the same problem.2The name@Java must be pronounced as at-java.To this respect,we need to know which calls were shown in thedesign models and which ones should be shown after the refactor-ing.To annotate each single method call does the trick since nonew method call is introduced by this refactoring action.This one is a specific@Java annotation3and should embrace allthe calls that changes in the design models.Its parameters specifythe necessary data that cannot be retrieved through reflection fromthe code:the old target name and class,in which diagram can befound and if it must be visible or not.2.1.2Extract MethodThe extract method refactoring actions turns fragments of redun-dant code into a method whose name explains its purpose.After this refactoring action,the application structure is enrichedwith a new methods and the design models(that is the class di-agram)should reflect this fact.To this respect,we need to tracewhich is the new method(i.e.,we have just to annotate it)andwhich diagram is affected by the change.Method name,declar-ing class,return type,and parameter names are data that can beretrieved through reflection.The parameter names are striped fromthe bytecode so if we want to put them in the diagram we have topass them to the annotation.Similarly to the move method refactoring action,the extract methoddoes not exhaust its effects on the class diagrams of the applicationbut it also impacts on the dynamic part of the application designmodels.The code extrusion leaves some gaps in the applicationcode that arefilled with an invocation to the extruded method.The ExtractMethodTrail annotation should be used to anno-tate those calls that should be modeled or should replace the pre-vious modeling.We have to trace to kind of data:i)data relatedto the new method call and ii)data related to the diagrams to ma-nipulate such as their identities and the position in the diagram thenew method call should have and if it replaces or not some otherdiagram portions.3The BLOCK element type can be set as a target for the annotationsonly by using@Java,In this case the annotation is a block anno-tation and can be used inside a method body to embrace by bracesone or more statements.next rentalshow figuresadd bonusesget chargesFigure 2:statement()and overprint activity diagram3.META-DATA AT WORKTo show our mechanism in action,we adopt the example pro-posed by Martin Fowler in the first chapter of his book [6].The program calculates and prints a statement of a customer’s charges at a video store.The program tells which movies a customer rented and for how long then it charges them.There are three kinds of movies:regular ,children’s and novelty .In addition to calculating charges,the statement also computes frequent renter points,which vary depending on whether the film is a new release.In its first release,the program is mainly composed of three classes:Movie ,Rental ,and Customer ,whose names should be self-explanatory of what they should represent.Customer also has the method statement()that produces the statement.Figure 2shows the code for the statement()method with overprint a draft of the activity diagram that describes its behavior.The statement()method that tends to be too long,clumsy and difficult to extend.Fowler’s cuts down its complexity by perform-ing several refactoring actions from his catalog.In our example we are just considering the first two steps:–extract method —it separates the amount calculation from the statement()method by extruding the switch into a new method named getCharge(),this method should take a rental as a parameter;–move method —the new method belongs to Customer but it uses information from the rental and not from the customer,the method should be moved to the right place.Figure 3shows the application application code and design (an ac-tivity diagram overprinted on the code)after these few steps of refactoring.We are not interested in judging the quality or the use-fulness of the refactoring (that is from the Fowler’s book)rather in showing how to use our approach to co-evolution of design and code.add bonuses{}{}get chargesnext rentalshow figuresFigure 3:code and design after the refactoringFigure 3shows,emphasized by curly red braces our meta-data in action as well.The first refactoring action has created the methoddouble getCharge(Rental aRental)in the Customer class.The annotation @ExtractMethod traces all the necessary data that could be used to add this method to the cor-responding class diagram.Whereas,the @ExtractMethodTrail traces the new call and the necessary data to update the correspond-ing diagrams (mainly the anchors in the diagram for the new ac-tion).The latter refactoring action moves the new method into the Rental class adjusting also the method signature.A combinations of the @MoveMethod and @ChangeSignature 4annotation traces the change.In the same way of the refactoring actions,the annota-tions refer to a context that depends on the effects of the previous 4Note @ChangeSignature traces the effects due to the change sig-nature refactoring actions since its simplicity we do not describe it in detail.annotations,e.g.,the MoveMethod annotation considers the con-texts after the application of the ExtractMethod annotation. From this small case study,we can notice that the annotating process is up to the developer that is updating the application.The developer knows which refactoring actions has performed and the relation between the application code and design models,so he/she knows which data are relevant to successively update the design models—not all the refactoring actions must have a visible ef-fect on the design models,e.g.,we do not use the@MoveMethod-Trail annotation even if we perform a move method refactoring action.Moreover,the developer can exploit his/her skill to reduce the amount of meta-data annotating the code even if the annotating process could be automated by an IDE supporting these refactoring actions.4.META-DATA AT THE RESCUEUp till now,we have explored how tofill the gap between the refactored code and the original design model to allow a sound refactoring of the design model as well.What it is still missing is to show how the meta-data can be used to perform this task.To this aim,we have developed a small tool,named refactoring script generator,that looks at the application bytecode for our an-notations and collects these meta-data.This tool is just exploiting Java reflection to get the annotations introduced by the developer during the coderefactoring.Thanks to the collected meta-data,it builds a script(a jRuby5script)that when run updates the design models after the trails left during the code refactoring.Tofinish the work,the tool strips all the meta-data to avoid inconsistent situa-tions at next code/design refactoring.The most critical point in this step is related to the fact that usu-ally the design models have a pictorical representation and UML diagrams are not an exception.This is quite important for the hu-man understandings but it renders the automatic manipulation an hard task.To overcome this problem,OMG provided the XMI representation for the UML diagrams6.In the RAMSES project7, we have developed a Java library called reification library that reifies the UML diagrams(i.e.,their XMI representation)and per-mits their manipulation from Java.It should be clear the benefits of the scripting programming languages when you are generating code on-the-fly.Moreover jRuby embeds the capability of invok-ing Java methods and manipulating Java objects that permits to use the reification library.To generate a script for updating the design model rather than update them directly from the tool is afirst step towards the inte-gration of the approach with a versioning system such as CVS or SVN.The XMIfiles could be stored in the versioning system to-gether with the source and the jRuby scripts provide the delta from the original and the refactored diagrams to pass from a release to another of the diagrams as well as of the code.Due to problems of space we cannot show and explain the whole jRuby script for the presented case study but we have to focus on the management of only one situation—we will show the case for the extrude method refactoring action./technology/documents/formal/xmi.htm7wwwiti.cs.uni-magdeburg.de/iti db/forschung/ ramses/Thefirst row loads the XMIfiles,the name of the XMIfile is passed to the script generator as a parameter.Rows2,3,7and10 reify the actors involved in the refactoring—it should not be amaz-ing the fact the names are hardwired in the script since it has been generated from the available meta-data.Rows from5to9prepare the data to be inserted for the new method in the class diagram and add it(row9).The code from row10updates the activity diagram after the data introduced by the@ExtractMethodTrail annotation.In our ex-ample,they add a new action call to the activity diagram for the extracted method(row13),and connect it to the right action calls (rows14and16)provided by the@ExtractMethodTrail annota-tion.After this snippet,the script goes on dealing with the remaining meta-data.As told,the script performs the updating from the inner to the outer annotation when more then one is attached to the same code element and the outer annotations must refer to the changes performed by the inner ones.Finally,a save()method will reflect onfile all the changes performed on the UML diagrams getting the desired co-evolution.5.RELATED WORKAlthough it is possible to do a manual refactoring,tool support is considered crucial.Today,a wide range of tools are available that automate various aspects of refactoring/software evolution.De-pending on the tool and the kind of support that is provided,the degree of automation can vary.However,a very small set of exist-ing tools tackle the problem of co-evolving the application design together with the code.In the ModelMarker8tool,the design is strictly related to and native expressed in C#target code.This way there is a seamless transition from design to implementations as currently not found in any other high level CASE tool.Many build-in refactorings are available on both structural and code level,e.g.,extract method, extract class/interface,rename parameter and so on.Unfortunately, it is integrated into industrial software development environment. France et al.in[7]propose an approach to software evolution based on transformations of object-oriented models and code,called multi-view software evolution.Changes are performed by evolving multiple views of a system represented as models,and propagating those changes to the implementation.Propagating changes across views requires well-defined relationships among the views and the implementation defined by the programmer.This approach is not compliant to the standard UML CASE tools but it can applied only if the system has been designed from the beginning with this ap-proach.8To have more control over the software evolution,D’Hondt et al.[5]introduce the logic-meta programming(LMP)as a develop-ment framework to express and enforce the synchronization pro-cess.The starting point of LMP is an existing programming envi-ronment(e.g.,Java,Small T alk),then LMP augments this environ-ment by a declarative meta-layer used to express the application de-sign information by rules and constraints.The design is expressed as a logic meta program over the implementation forcing the pro-grammer to implement this representation.The software develop-ment process needs a new phase:after the classical design phase and implementation phase they require to translate the classical de-sign into a logic meta-program.At this time the two levels,im-plementation(base-level)and new design(meta-level)are causally connected and every changes in the base level are mapped into the meta-level,but not on the classical design information losing the co-evolution.Mens et al.in[10]propose to use intensional source code views and relations as an active documentation technique to keep applica-tion code and design synchronized.In their approach design means design documentation and thefirst version of the design documen-tation remains a largely manual process,and the application re-mains not coupled with design information such as UML.Van Gorp et al.in[12]highlight that there is a historical gap be-tween UML tools and refactoring tools.That MDA tool vendors aim to bridge by regenerating program code form evolving UML OOAD models and vice versa.They propose a novel solution for implementing traditional OO source refactoring into the infrastruc-ture from UML tools.They use an extension of UML meta-model, called GrammiUML,that enables tool to keep their repository synchronized with the code while applying common refactorings. This idea is very interesting but it needs to adapt the original UML design to be used with the new UML meta-model.Fujaba[1]is an environment that aims to provide round-trip en-gineering support for UML and Java.It provides code generation from class diagrams,statechart and collaboration diagrams.It is a very promising tool,but it does not have features for adapting the model to a code refactoring.Exploiting meta-data is not a new idea in the area of automatic documenting the code,a couple of proposal can be found in[11] and[8]but in both cases they consider only the static part of the design model(i.e.,class and deployment diagrams)and only as a mechanism for self-documenting the code and not related to soft-ware evolution.6.FUTURE WORKS AND CONCLUSIONS This paper deals with the problem of co-evolving the application design models after the code refactoring.As known,the two rep-resentations are not tightly connected and it is quite hard to going back from the code to the original design models since a missing link between the code and the design models(design/implementa-tion gap).Unfortunately,the code continuously evolves to face new requirements and the its design models become soon obsolete.The approach we have proposed and realized is based on the key idea that the developer knows how to adapt the application design mod-els when evolves the application code.This knowledge is stored in the code as meta-data and can successively be used to evolve the design models as well without losing efficiency and waste time in updating the design model during the code evolution/refactoring. At the moment,even we have a working prototype,the approach is in its early stages.In the future,we are going to extend it to a more general case of software evolution than code refactoring and to automate the annotation process by IDE support.Moreover, we are planning to integrate this co-evolution mechanism with a versioning system such as CVS or SVN to store the various code versions with the corresponding design models. AcknowledgmentsThis work is part of the RAMSES project(SA465/31-1)funded by the DFG(German Science Foundation).7.REFERENCES[1]S.Burmester,H.Giese,M.Hirsch,D.Schilling,and M.Tichy.The Fujaba Real-Time Tool Suite:Model-DrivenDevelipment of Safety-Critical,Real-Time Systems.InProceedings of ICSE’05,pages670–671,St.Louis,MO,USA,May2005.ACM Press.[2]W.Cazzola,A.Cisternino,and D.Colombo.FreelyAnnotating C#.Journal of Object Technology,4(10):31–48,December2005.[3]W.Cazzola,A.Ghoneim,and G.Saake.Viewpoint forMaintaining UML Models against Application Changes.InProceedings of ICSOFT2006,Set´u bal,Portugal,September 2006.Springer.[4]W.Cazzola,S.Pini,and M.Ancona.The Role of DesignInformation in Software Evolution.In Proceedings ofRAM-SE’05,pages59–70,Glasgow,Scotland,July2005. [5]T.D’Hondt,K.De V older,K.Mens,and R.Wuyts.Co-Evolution of Object-Oriented Software Design andImplementation.In Proceedings of the InternationalSymposium on Software Architectures and ComponentTechnology,pages207–224,Twente,The Netherlands,January2000.Kluwer.[6]M.Fowler.Refactoring:Improving the Design of ExistingCode.Addison-Wesley,Reading,Massachusetts,June1999.[7]R.France and J.M.Bieman.Multi-View Software Evolution:a UML-Based Framework for Evolving Object-OrientedSoftware.In Proceedings of ICSM2001,pages386–397,Florence,Italy,November2001.IEEE Computer Society. [8]N.Fr¨o hlich and G.Paul.Lightweight Generation of UserInterfaces.In Proceedings of the2nd International Scientific Conference on Computer Science,Chalkidiki,Greece,September2005.[9]J.Gosling,B.Joy,G.Steele,and G.Bracha.The JavaLanguage Specification.Addison-Wesley,Reading,Massachusetts,third edition,2005.[10]K.Mens,A.Kellens,F.Pluquet,and R.Wuyts.Co-evolvingCode and Design Using Intensional Views-A Case Study.Journal of Computer Languages,Systems and Structures,32(2):140–156,July/October2006.[11]M.Torchiano,F.Ricca,and P.Tonella.A Comparative Studyon the Re-Documentation of Existing Software:CodeAnnotations vs.Drawing Editors.In Proceedings ofISESE’05,pages277–286,Noosa Heads,Australia,November2005.[12]P.Van Gorp,H.Stenten,T.Mens,and S.Demeyer.Enablingand Using UML for Model Driven Refactoring.InProceedings of the4th International Workshop on OOReengineering,pages37–40,Darmastadt,Germany,July2003.。
ECOG2DP223E中文资料

– EE188 –
元器件交易网
Aluminium Electrolytic Capacitors/GUP n Standard Products
W.V. (V) Cap.
(±20%)
Case size
Dia. (mm) Length (mm)
Specification
Ripple D.F. current (120Hz) (120Hz) (+85°C) (+20°C) (A)
For general-purpose inverter, power supply for backup system, motor-control, inverter -25 to + 85°C 160 to 450 V .DC 2700 to 56000 µ F ±20% (120Hz/+20°C) (µA) or 5(mA) whichever, smaller, after 5 minutes application of rated working 3 CV voltage at +20°C C:Capacitance(µF) V: W.V. (V.DC) Please see the attached standard products list After 5000 hours application of DC voltage with specified ripple current (< rated DC working voltage ) at +85°C, the capacitor shall meet the following limits.(160 to 250 W.V. : 2000 hours at +85°C)
GeoWEPP for ArcGIS 10.x版本概述手册说明书
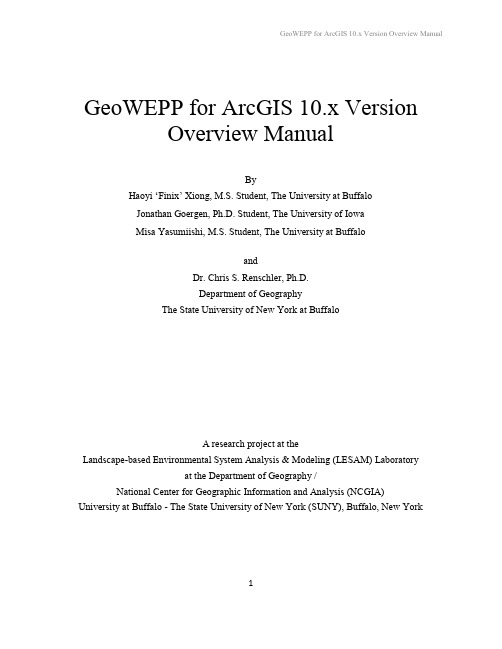
GeoWEPP for ArcGIS 10.x VersionOverview ManualByHaoyi ‘Finix’ Xiong, M.S. Student, The University at BuffaloJonathan Goergen, Ph.D. Student, The University of IowaMisa Yasumiishi, M.S. Student, The University at BuffaloandDr. Chris S. Renschler, Ph.D.Department of GeographyThe State University of New York at BuffaloA research project at theLandscape-based Environmental System Analysis & Modeling (LESAM) Laboratoryat the Department of Geography /National Center for Geographic Information and Analysis (NCGIA) University at Buffalo - The State University of New York (SUNY), Buffalo, New York1Copyright (C) 2014 LESAM Research Group, University at Buffalo. All rights reserved. Revision Date: 01/31/2014.Please ALWAYS review the GeoWEPP derived model input before running the WEPP model. All information, computer software, and database containing this GeoWEPP release are believed to be accurate and reliable. The Landscape-based Environmental System Analysis Modeling (LESAM) Laboratory of Department of Geography at the University at Buffalo, The State University of New York, accepts no liability or responsibility of any kind to any user, other person, or entity as a result of installation or operation of this software. GeoWEPP is provided'AS IS', and you, the user, who assumes all risks, when using GeoWEPP.If you have any questions, suggestions, or comments regarding GeoWEPP, visit the following web site: /contact/ and fill out the inquiry form, or send email to: *******************.The GeoWEPP ArcGIS 10.1 Development TeamHaoyi ‘Finix’ Xiong, University at BuffaloJonathan Goergen, University of IowaMisa Yasumiishi, University at BuffaloDr. Chris S. Renschler, University at BuffaloFor questions and suggestions for this manual, please contact: *******************2Table of Contents1. System Requirements (4)2. GeoWEPP Installation (4)3. GeoWEPP Input Data Requirements (4)4. Launching GeoWEPP (6)5. GeoWEPP Basics (10)Folder Structure (10)Core Functions (10)Toolbar (11)6. GeoWEPP Steps (12)7. Product Note and Known Issues (20)Reference (22)31. System Requirements∙Windows Operation System∙ArcGIS 10.1 Desktop. ArcGIS 10.1 doesn't work with ArcGIS's previous versions or ArcGIS 10.2 or higher.∙ArcGIS Spatial Analysis Extension∙Spatial Analysis Extension∙Most Recent version of WEPP (for application information and download go to /Research/docs.htm?docid=10621)∙.NET Framework∙250 MB hard disk space. A larger disk space will be required if example sets are used (approximately 50MB for each set).2. GeoWEPP InstallationGeoWEPP applications can be downloaded at https:///versions/. Please fill out the password request form of the version you wish to install.Once you have downloaded an application zip file, unzip the zip file. The zip file can then be downloaded and installed to the local hard drive or external drive such as the flash drive. Important Note: The location you provide should not contain any spaces in the folder names. For Example, you shoul dn’t use “C:\My GeoWEPP”, but you should use “C:\MyGeoWEPP” or “C:\My_GeoWEPP”. This also means you can not save the GeoWEPP folder on to your desktop, since its location is actually “C:\Documents and Settings\All Users\Desktop”. It is also recommended that you limit the folder name to no more than 13 characters. Both of these have to do with the way pathways were used and created in older operating systems and in older versions of ArcGIS.3. GeoWEPP Input Data RequirementsMinimum Requirement Files∙Elevation data file in ASCII format (.asc) of the area.4Soil data files and landcover data files can be added for precise modeling. For details about how to create the data sets, please refer to GeoWEPP for ArcGIS 9.x Full Version Manual (/training/arcgis-9-x/documentation/) Important Note:1.Raster files of DEM, soil and landcover have to be ASCII format (.asc). You can convertraster files to ASCII format using the ArcGIS [Raster to ASCII] tool.2.For a DEM ASCII file: All the elevation values in the DEM should be between 1.0 to9999.0 meters3.There must be NO scientific expression in the ASCII files.4.There should be NO holes in ASCII files, which means that NoData values can beallowed inside the boundary of study area.5.Values having a comma are not allowed. For example, "1,234" is not allowed but "1234"is permitted.6.UTM easting of DEM (xllcorner) should be positive value no more than 1,000,000meters. UTM northing of DEM (yllcorner) should be no more than 10,000,000 meters. .54. Launching GeoWEPPBefore launching:∙Please make sure that the Spatial Analysis extension is enabled on ArcGIS.∙Please check the UTM zone of the area. You will be prompted to enter the number later.∙We recommend that you read the "Product Notes and Known Issues" section in this document before starting GeoWEPP.1.Go to the folder you unzipped GeoWEPP zip file.2.Double click 'GeoWEPP.esriAddIn' BEFORE opening GeoWEPP application. This willadd the GeoWEPP toolbar to ArcGIS.Note: If you don't see the GeoWEPP tool bar when ArcGIS is opened later, go to the top menu > Customize> Toolsbars and turn on [GeoWEPP].3.Double click 'Launch GeoWEPP.exe' to launch GeoWEPP.4.Start up screen will now appear.6Figure 1: Start up screen[Use Example GIS Data button]GeoWEPP contains four example data sets. To familiarize yourself with GeoWEPP, you can choose among the examples and run the processes.[Use your own GIS ASCII Data]This screen allows you to upload your own data files. To upload files, click on each file path box. Windows Explorer will appear.78<Input file locations and samples>2 - DEM ASCII file3 - Soil ASCII file4 - Landcover ASCII file*Please refer to GeoWEPP forArcGIS 9.x Full Version Manualabout how to create these text files6 - Soil database text file7 - Landcover description text file8 - Landcover database text file9[Load Previously Saved Project]Once a project is created on GeoWEPP, the project is saved as .mxd file. The next time you can click this button and select the .mxd file in the project folder. You won't need to upload the source data files again.[Exit GeoWEPP]Closes GeoWEPP.5. GeoWEPP BasicsFolder StructurePlease review the folder structure to be familiarized with GeoWEPP.Core FunctionsGeoWEPP combines three different functions to calculate soil erosion.1.TOPAZ (Topographic Parameterization) for topographic evaluation, drainageidentification, watershed identification, watershed segmentation, and subcatchmentparameterization102.PRISM (Parameter-elevation Regressions on Independent Slopes Model) for editingexisting climate data.3.WEPP (Water Erosion Prediction Project) for soil erosion calculationToolbarFigure 2: GeoWEPP 10.1 toolbar<TOPAZ part>1 - Defines CSA (Critical Source Area) and MSCL (Minimum Source Channel Length) to delineate streams2 - Specifies the outlet point of watershed<PRISM part>3 - Opens PRISM to select/edit existing climate data<WEPP part>4 - Obtains the erosion pattern in the watershed5 - Displays reports6 - Saves GeoWEPP project7 - Changes tolerable value of erosion8 - Shows the information of hillslope in the watershed area (click on hillslope)9 - Changes the associated landuse and soil type10 - Returns WEPP after changing hillslope parameter1111 - Loads a single hillslope on WEPP12 - Goes to WEPP13 - Saves project and exit6. GeoWEPP Steps1.Enter Critical Source Area (CSA) and Minimum Source Channel Length (MSCL).Figure 3: CSA, MSCL setting window. Default values are CSA - 5, MSCL - 100.122.Click on a pixel of an outlet point.Note:You are not able to select a source cell of a channel. It will return an error.Figure 5: When you asked UTM Zone, enter UTM Zone number for the areaFigure 6: Subcatchments are delineated3.Select and/or edit the existing climate data.13Figure 7: Climate file selection windowFigure 8: PRISM screen. You can edit the existing climate parameters.14154.Enter parameters to obtain erosion patterns in the watershed.Figure 9: WEPP will ask cligen climate station. Select one.Figure 10: Successful message appearsFigure 11: WEPP Mangement and Soil Lookup window over delineated watersheds. You can edit Landuse, Soils, Channels types by clicking on the line you want to change.Figure 12: Review the setting. Change setting, including Number of Years, and check Return Periods if necessary.1617Figure 13: WEPP onsite and offsite output5.Displays reports.Figure 14: Select reports you want to displayFigure 15: Reports are displayed in text format6.Save your GeoWEPP project.7.Change tolerable value of erosion, if necessary.8.Shows the information of hillslope in the watershed area (click on hillslope).9.Change the associated landuse and soil type, if necessary.10.Returns to WEPP after changing hillslope parameter11.Click on a hillslope to run WEPP on a single hill slope. Click [OK] on message pop-ups. WEPP window appears.1812.Click this button when you want to open a new blank WEPP project.13.Save the project and exit.197. Product Note and Known IssuesNote:1) Common errors are associated with an original raster file. It is recommended that you eliminate NoData cells.2) A standard area for GeoWEPP is about 5 hectors. When you process a large area, please consider decreasing the DEM resolution such as from 10m to 30m, 30m to 50m, etc.3) If a user does not upload soil or landover ASCII files, a default file (uniform) will be generated.4) If a user does not upload soil or landcover ASCII files, a description file will be created with an entry for each unique value. All landcover and soil values will be set to a default value if the user doesn't offer a database file. Users may change these settings when modeling a subcatchment area.5) If users are familiar with how to create a description and database file for GeoWEPP ArcGIS 9.x version, they may create them by referring to the ArcGIS 9.x manual.6) Please use the [Load Previous Saved Project] button to open your .mxd file if you move your whole GeoWEPP folder to a different place to make sure some directory files inside are correct.7) Please do not use any scientific notations to represent pixel elevation values in a raster file. All values in scientific notation will be treated as NoData Value.Known Issues:1) Occasionally an ArcMap error occurs when GeoWEPP tries to delete a layer. When this occurs, save and exit the project and then re-open.2) PRISM may report an error the first time you attempt to use it during a project. Re-running PRISM often fixes the problem.3) A large DEM files (over 200,000 cells) may fail to process. If GeoWEPP freezes while running DEDNM.exe, try resampling your input raster.4) Occasionally when a project opens on ArcMap for the first time the layers don't appear although the layer names appear in the left Table of Contents pane. When this happens, please save the project, close ArcMap, and re-open the project. The layers should appear.208. SupportEmail: *******************For detailed instructions about GeoWEPP functions and how to set up data sets: /training/arcgis-9-x/documentation/For general inquires: /contact/For bug report: /contact/bug-report/For suggestions: /contact/suggestions/21ReferenceCligen/nicks/nicks.htmGlossary of Hydrologic Terms/om/hod/SHManual/SHMan014_glossary.htm PRISM/PRISM Generator//cgi-bin/fswepp/rc/rockclim.plSoil Series Descriptionhttps:///osdquery.aspxTOPAZask.ca/~lwm885/topaz/overview.htmlWeb Soil Survey/App/HomePage.htmWEPP/Research/docs.htm?docid=1062122。
XGB系列产品说明书

No. NameDescriptions① LED IndicatorsShows the operation status②RS-232C Connector The connector for external connection③ RS-422/RS-485 ConnectorThe connector for external connectionNo. Switch status Switch status descriptions④All on Normal operatingAll off OS Download Mode (If you want to OS Download, Please contact us)LED NameLED Descriptions LED status LED status descriptions On Normal operating(a) How to connect RS-232C connector to the external modemCnet I/F module can communicate with devices of long distance through a modem at this time modem and channel RS-232C must be connected as shown in below tableCnet(9-PIN) Connection No. and Signal DirectionModem Pin No. Name Name 1 CDCD 2 RXD RXD 3 TXD TXD 4 DTR DTR 5 SG SG 6 DSR DSR 7 RTS RTS 8 CTS CTS 9 RI RI(b) How to connect RS-232C connector in null modem mode.In null modem mode, connector is able to be connected in 3-line (without handshake) type. Cnet(9-PIN) Connection No. and Signal DirectionComputer /Communicationdevice Pin No. Name Name 1 CDCD 2 RXD RXD 3 TXD TXD 4 DTR DTR 5 SG SG 6 DSR DSR 7 RTS RTS 8 CTS CTS 9RIRI(2) RS-422/485 Interface (XBL-C41A)RS-422 channel uses 5-pin terminal block for communication with external devices. Thenames and functions of pins, and data directions are as shown in the following table. Pin No. Name Signal direction (Cnet<-->External device) Function 1 TX+ Transmitted data (+) 2 TX- Transmitted data (-) 3 RX+ Received data (+) 4 RX- Received data (-) 5 SG Signal ground line [Pin assignment of RS-422 5-pin connector]RS-422 channel makes connection external devices and RS-422 and RS-485(Multi-drop)possible. When RS-422 channel is used as multi-drop, set channel RS-422 to RS-485communication in setting menu of RS-422 communication type of XG-PD, and connect the terminal of RS-422 as shown in the [RS-485 connection] table. Cnet Signal direction(Cnet<--->External device) External device Pin No. Name1 TX+ RX+2 TX- RX-3 RX+ TX+4 RX- TX-5 SG SG [RS-422 connection] Cnet Signal direction (Cnet<--->External device) External devicePin No. Name1 TX+ RX+2 TX- RX-3 RX+ TX+4 RX- TX-5 SG SG [RS-485 connection]Above figure shows how to connect RS-485 multi-drop communication. In the case of RS-485 communication, the TX+ and RX+ terminals should be shortened and TX- and RX- terminals should be shortened, then connected to the other devices. At this time,RS-485 should be selected by using the XG-PD. (3) Terminator (RS-422/485)(a) When the communication via channel RS-422 terminal resistor from external must beconnected. (b) Terminal resistor has the function to prevent distortion of signal by reflected wave of cable when long distance communication, the same resistor (1/2W) as characteristic impedance of cable must be connected to terminal of network.(c) When using the recommended cable in the section 3, connect terminal resistor ofusing another cable than recommended one, the same resistor (1/2W) as characteristic impedance of cable must be connected to both ends of cable.(e) How to connect terminal resistor [RS-485 connection]6. Cautions for system and network connection(1) All the stations in whole network should not have duplicated station number. Otherwise,it can cause serious communication error.(2) Use cable complying with specification in this data sheet. Otherwise, it can serious communication error.8. Warranty(1) Warranty periodLSIS provides an 18-month-warranty from the date of the production. (2) Warranty conditionsFor troubles within the warranty period, LSIS will replace the entire PLC or repair the troubled parts free of charge except the following cases.(a) The troubles caused by improper condition, environment or treatment exceptthe instructions of LSIS.(b) The troubles caused by external devices.(c) The troubles caused by remodeling or repairing based on the user’s owndiscretion.(d) The troubles caused by improper usage of the product.(e) The troubles caused by the reason which exceeded the expectation fromscience and technology level when LSIS manufactured the product. (f) The troubles caused by natural disaster.(3) This warranty is limited to the PLC itself only. It is not valid for the whole systemwhich the PLC is attached to.Be sure to check the rated voltage and terminal arrangement for the► The symbols which are indicated in the PLC and User’s Manual mean as follows. This symbol means paying attention because of danger of electric shock.Store this datasheet in a safe place so that you can take it out and read it whenever necessary. Always forward it to the end user Do not contact the terminals while the power is applied.Warning Caution ∙ HEAD OFFICELS Tower, 127, LS-ro, Dongan-gu, Anyang-si,Gyeonggi-do, 431-848, Korea Tel: 82-2-2034-4870 Fax: (82-2)2034-4648 e-mail: ****************∙ LSIS(ME) FZE _ Dubai, U.A.E. Tel: 971-4-886-5360 Fax: 971-4-886-5361 e-mail: ******************∙ LSIS Tokyo Office _ Tokyo, Japan Tel: 81-3-3582-9128 Fax: 81-3-3582-2667 e-mail: ****************∙ LSIS Shanghai Office _ Shanghai, ChinaTel: 86-21-5237-9977(609) Fax: 89-21-5237-7189 e-mail: ***************.cn∙ LSIS Beijing Office _ Beijing, ChinaTel: 86-10-5825-6027(666) Fax: 86-10-5825-6028 e-mail: **************.cn∙ LSIS Guangzhou Office _ Guangzhou, China Tel: 86-20-8328-6754 Fax: 86-20-8326-6287 e-mail: ***************.cn∙ LSIS Chengdu Office _ Chengdu, China Tel: 86-20-8328-6754 Fax: 86-20-8326-6287 e-mail: ***************∙ LSIS Qingdao Office _ Qingdao, China Tel: 86-532-8501-6068 Fax: 86-532-8501-6057 e-mail: ***************.cn∙ LSIS Europe B.V., Netherlands Tel: +31 (0)20 654 1420 Fax: +31(0)20 654 1429 e-mail: ******************- When using LSIS equipment, thoroughly read this datasheet and associated manuals introduced in thisdatasheet. Also pay careful attention to safety and handle the module properly.- Store this datasheet in a safe place so that you can take it out and read it whenever necessary..。
3Bxxxxx-xxx-10CB中文资料
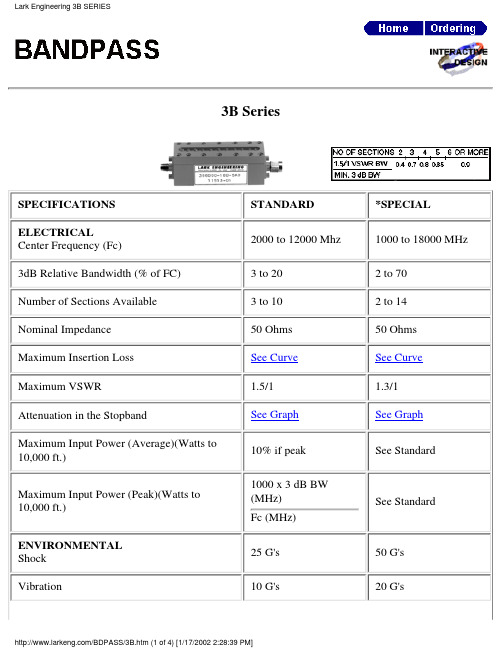
3B SeriesSPECIFICATIONS STANDARD *SPECIAL ELECTRICALCenter Frequency (Fc)2000 to 12000 Mhz 1000 to 18000 MHz 3dB Relative Bandwidth (% of FC) 3 to 20 2 to 70Number of Sections Available 3 to 10 2 to 14Nominal Impedance 50 Ohms 50 Ohms Maximum Insertion Loss See Curve See Curve Maximum VSWR 1.5/1 1.3/1Attenuation in the StopbandSee Graph See Graph Maximum Input Power (Average)(Watts to 10,000 ft.)10% if peak See StandardMaximum Input Power (Peak)(Watts to 10,000 ft.)1000 x 3 dB BW (MHz)Fc (MHz)See StandardENVIRONMENTAL Shock 25 G's 50 G's Vibration10 G's20 G'sHumidity90% relative100% relative Altitude Unlimited UnlimitedTemperature Range (Operating)-25 to + 50 degreescelsius-54 to + 100 degreescelsiusTemperature Range (Non-Operating)-54 to + 70 degreescelsius-62 to +150 degreescelsiusMECHANICALApproximate Weight in oz.0.8 x H x L0.7 x H x LMounting Provisions See below See belowSpecial Configurations Consult Factory Consult FactoryINSERTION LOSS:The Maximum Insertion Loss atcenter frequency is equal to :LF x (N + 0.5) / % 3 dB BW + 0.1Where:LF= Loss Factor, N= Number ofSections% 3dB BW:3dB BW (MHz) x 100divided byCenter Frequency (MHz)Example:A 5 section 3B with a centerfrequency of 10000 MHz and a 3dBBW of 500 MHz would have,.9 x 5.5 / 5 = 0.990.99 + 0.1 = 1.1 dBMECHANICAL SPECIFICATIONSL Dimension = N x (0.3 + 0.5 / %BW)+ 1.0 inch Approx H Dimension = 1450 / Fc(MHz) + 0.6 inch Approx.Connectors Available on 3B SeriesLark Code Type C DIM.Inches & MMLarkCodeType C DIM.Inches & MMA SMA JACK.375 & 9.5*G N JACK.736 & 18.7B SMA PLUG.507 & 12.9*H N PLUG.819 & 20.8*C TNC JACK.750 & 19.1S SPECIAL*D TNC PLUG.844 & 21.4* Not recommended for use with this SeriesThe size shown is a standard used by Lark to facilitate a low cost, easily reproducible unit. Should you require another size, please submit all of your requirements-both electrical and mechanical. This will enable Lark Engineering to quote theoptimum design for your application.STOPBAND SPECIFICATIONSThe graphs on the following pages define the normal specification limits on attenuation Lark bandpass filter series 2B, 3B, and 4B. The minimum level of attenuation in dB is shown as a "number of 3dB bandwidths from centerfrequency".Since the frequency characteristics vary for differing bandwidths, it is necessary to establish specifications for each bandwidth of filter. The different graphs represent various 3dB percentage bandwidths. Intermediate values should be interpolated. The 3dB percentage bandwidth is defined as follows:3dB Bandwidth (MHz) x 100divided byCenter Frequency (MHz)The exact relationship is as follows:1. 3dB Bandwidths From Center Frequency= Rejection Frequency (Mhz) -Center Frequency (Mhz) divided by 3dB Bandwidth (Mhz)Example:Given:2. Center Frequency = 5000 MHz Minimum 3dB Bandwidth = 500 MHzNumber of Sections = 5Find: Minimum attenuation levels at 4250 MHz and 5800 MHz.3dB BW's from Fc = 4250 - 5000 / 500 = - 1.5and 5800 - 5000 / 500 = + 1.6The answer can be read directly from the 10% graph. Using the 5 section curve at the point -1.5 (4250 MHz) we find the minimum level of attenuation is 40dB.At +1.6 (5800 MHz) the minimum level of attenuation is 50dB.For special requirements, please contact our Application EngineeringDepartment.STOPSP3.HTM元器件交易网STOPBAND SPECIFICATIONSSTOPBAND SPECIFICATIONSSTOPSP3.HTM元器件交易网STOPBAND SPECIFICATIONS。
ECO2WIN中文使用手册

ECO2WIN中文使用手册目录一、简介1.文档说明2.包含部件3.系统配置要求二、软件安装介绍三、软件运行1.通讯连接和设置2.创建一个新项目3.打开一个新项目4.工作窗口介绍四、软件功能框架1.设备状态(DEVICE STATUS)2.电机控制3.电机控制参数设置4.示波器5.子程序编程(SEQUENCER PROGRAMMING)6.设备配置7.参数直接寻址8.系统管理9.数据输出10.数据载入五、控制器调整六、通信协议说明七、附录1、ECOSTEP技术规格和注意事项2、对象词典参数详细注释3、术语表4、应用范例一、简介1、文档说明此文档专为使用KINCO系列伺服系统所设计,在系统开发过程中请一步步按文档要求执行软件功能。
该文档主要描述的是软件ECO2WIN V2.27的功能。
2、包含部件一张带有ECO2WIN的CD;PEAK公司的CAN-DONGLE(并口适配器)或PCAN-USB(USB口适配器);相关的与控制器间的通讯连接线缆3、操作系统和硬件要求奔腾CPU(最少200MHz)内存大于64MBCD-ROM带有232串口、并口或USB接口WIN98/2000/XP二、软件安装介绍当你将ECO2WIN软件光盘放入光驱中,系统将自动运行安装程序,如下图,请选择“ENGLISH‖语言进行安装:注意,所安装的软件除包含有ECOSTEP相关软件,主要包括ECO2WIN和ECOFLASH,其中ECO2WIN是我们必须安装的ECOSTEP驱动器的控制软件,ECOFLASH是用来下载最新的软件RELEASE。
另外,光盘中还有附加的其它软件,如下图,包括ADOBE 阅读器软件和PEAK系列CAN适配器驱动软件,用户可自行决定是否安装。
注意,如果用户选择基于PEAK公司技术的CAN适配器进行控制,则一定要安装相应的驱动软件(包括并口、USB 口等),见下图:重要说明:当软件在WIN98下安装完毕后,需利用厂家提供的ECO2WIN.INI文件对旧文件进行覆盖后方可工作,WIN2000/XP下无此问题。
高德威产品手册(解决方案)V0.2
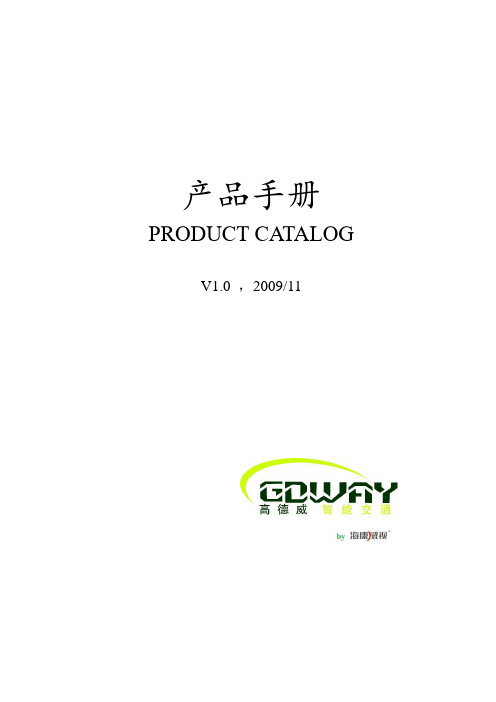
产品手册PRODUCT CA TALOGV1.0 ,2009/11产品手册目录CONTENTS1.GW-PR-9902T汽车牌照识别器 (5)1.1 产品简介 (5)1.2 权威检测 (5)1.3 产品特点 (5)1.4 主要功能 (5)1.5 应用领域 (6)1.6 解决方案 (6)1.6.1标清独立处理单元车牌识别方案 (7)1.6.1.1 主要特性 (8)1.6.1.2 订货型号 (8)1.6.1.3 硬件接口 (8)1.6.1.4 技术参数 (8)1.6.1.5 应用场合 (9)1.6.1.6 应用举例-高速公路收费系统 (9)1.6.1.6.1 方案特点 (9)1.6.1.6.2 系统框图 (10)1.6.1.6.3 设备清单 (10)1.6.2标清板卡处理单元车牌识别方案 (11)1.6.2.1 主要特性 (11)1.6.2.2 订货型号 (11)1.6.2.3 硬件接口 (11)1.6.2.4 技术参数 (11)1.6.2.5 应用场合 (12)1.6.2.6 应用举例-高速公路收费系统 (12)1.6.2.6.1 方案特点 (12)1.6.2.6.2 系统框图 (13)1.6.2.6.3 设备清单 (13)1.6.3标清独立处理单元LED补光车牌识别方案 (14)1.6.3.1 主要特性 (14)1.6.3.2 订货型号 (14)1.6.3.3 硬件接口 (14)1.6.3.4 技术参数 (14)1.6.3.5 应用场合 (15)1.6.3.6 应用举例-高速公路收费系统 (16)1.6.3.6.1 方案特点 (16)1.6.3.6.2 系统框图 (16)1.6.3.6.3 设备清单 (16)1.6.4标清板卡处理单元LED补光车牌识别方案 (17)1.6.4.1 主要特性 (17)1.6.4.2 订货型号 (17)1.6.4.3 硬件接口 (17)1.6.4.4 技术参数 (18)1.6.4.5 应用场合 (19)1.6.4.6 应用举例-高速公路收费系统 (19)1.6.4.6.1 方案特点 (19)1.6.4.6.2 系统框图 (20)1.6.4.6.3 设备清单 (20)1.6.5标清独立处理单元双摄像头车牌识别方案 (20)1.6.5.1 主要特性 (21)1.6.5.2 订货型号 (21)1.6.5.3 硬件接口 (21)1.6.5.4 技术参数 (21)1.6.5.5 应用场合 (22)1.6.5.6 应用举例-高速公路收费系统 (23)1.6.5.6.1 方案特点 (23)1.6.5.6.2 系统框图 (24)1.6.5.6.3 设备清单 (24)1.6.6标清板卡处理单元双摄像头车牌识别方案 (25)1.6.6.1 主要特性 (25)1.6.6.2 订货型号 (25)1.6.6.3 硬件接口 (25)1.6.6.4 技术参数 (25)1.6.6.5 应用场合 (26)1.6.6.6 应用举例-高速公路收费系统 (26)1.6.6.6.1 方案特点 (26)1.6.6.6.2 系统框图 (27)1.6.6.6.3 设备清单 (27)1.6.7高清车牌识别方案 (28)1.6.7.1 主要特性 (28)1.6.7.2 订货型号 (28)1.6.7.3 硬件接口 (28)1.6.7.4 技术参数 (29)1.6.7.5 应用场合 (30)1.6.7.6 应用举例-高速公路收费系统 (30)1.6.7.6.1 方案特点 (30)1.6.7.6.2 系统框图 (31)1.6.7.6.3 设备清单 (31)1.6.8高清LED补光车牌识别方案 (32)1.6.8.1 主要特性 (32)1.6.8.2 订货型号 (32)1.6.8.3 硬件接口 (32)1.6.8.4 技术参数 (33)1.6.8.5 应用场合 (34)1.6.8.6 应用举例-高速公路收费系统 (34)1.6.8.6.1 方案特点 (34)1.6.8.6.2 系统框图 (35)1.6.8.6.3 设备清单 (35)1.6.9 高清含终端服务器车牌识别方案 (36)1.6.9.1 主要特性 (36)1.6.9.2 订货型号 (36)1.6.9.3 硬件接口 (37)1.6.9.4 技术参数 (37)1.6.9.5 应用场合 (39)1.6.9.6 应用举例-治安查报站系统 (39)1.6.9.6.1 方案特点 (39)1.6.9.6.2 系统框图 (40)1.6.9.6.3 设备清单 (40)1.6.10高清含终端服务器LED补光车牌识别方案 (41)1.6.10.1 主要特性 (41)1.6.10.2 订货型号 (42)1.6.10.3 硬件接口 (42)1.6.10.4 技术参数 (42)1.6.10.5 应用场合 (44)1.6.10.6 应用举例-治安查报站系统 (44)1.6.10.6.1 方案特点 (44)1.6.10.6.2 系统框图 (45)1.6.10.6.3 设备清单 (45)2. GDW-VM-2003车辆智能监测记录系统 (46)2.1 产品简介 (46)2.2 权威检测 (46)2.3 产品特点 (47)2.4 设备功能 (47)2.5 应用领域 (47)2.6 解决方案 (48)2.6.1标清卡口方案 (49)2.6.1.1 主要特性 (49)2.6.1.2 订货型号 (49)2.6.1.3 硬件接口 (49)2.6.1.4 技术参数 (49)2.6.1.5 应用场合 (50)2.6.1.6 应用举例-治安卡口系统 (51)2.6.1.6.1 方案特点 (51)2.6.1.6.2 系统框图 (51)2.6.1.6.3 设备清单 (51)2.6.2标清硬盘录像一体卡口方案(预告) (56)2.6.2.1 主要特性 (56)2.6.2.2 订货型号 (56)2.6.2.3 硬件接口 (56)2.6.2.4 技术参数 (56)2.6.2.5 应用场合 (57)2.6.3高清卡口SIC1G方案 (58)2.6.3.1 主要特性 (58)2.6.3.2 订货型号 (58)2.6.3.3 硬件接口 (59)2.6.3.4 技术参数 (59)2.6.3.5 应用场合 (61)2.6.3.6 应用举例-治安卡口系统 (61)2.6.3.6.1 方案特点 (61)2.6.3.6.2 系统框图 (62)2.6.3.6.3 设备清单 (62)2.6.4高清LED补光卡口方案 (63)2.6.4.1 主要特性 (63)2.6.4.2 订货型号 (64)2.6.4.3 硬件接口 (64)2.6.4.4 技术参数 (64)2.6.4.5 应用场合 (66)2.6.4.6 应用举例-治安卡口系统 (67)2.6.4.6.1 方案特点 (67)2.6.4.6.2 系统框图 (68)2.6.4.6.3 设备清单 (68)2.6.5高清卡口(不含终端服务器)方案 (69)2.6.5.1 主要特性 (69)2.6.5.2 订货型号 (69)2.6.5.3 硬件接口 (70)2.6.5.4 技术参数 (70)2.6.5.5 应用场合 (71)2.6.5.6 应用举例-ETC收费系统 (72)2.6.5.6.1 方案特点 (72)2.6.5.6.2 系统框图 (73)2.6.5.6.3 设备清单 (73)2.6.6高清LED补光卡口(不含终端服务器)方案 (74)2.6.6.1 主要特性 (74)2.6.6.2 订货型号 (74)2.6.6.3 硬件接口 (74)2.6.6.4 技术参数 (75)2.6.6.5 应用场合 (76)2.6.6.6 应用举例-超速预警提醒系统 (77)2.6.6.6.1 方案特点 (77)2.6.6.6.2 系统框图 (78)2.6.6.6.3 设备清单 (78)高德威产品手册1.GW-PR-9902T汽车牌照识别器1.1 产品简介GW-PR-9902T汽车牌照识别器系列产品,采用先进的数字图像处理和模式识别技术,基于嵌入式的硬件处理平台和包含智能补光技术的专用成像系统,可实现车辆牌照的自动识别及图像抓拍。
PCN-105D3中文资料

RoHS compliant (Directive 2002/95/EC) as per product date code 0424F0258-A Centralized and decentralized heating control, extremely narrow interfaceelements, interface technology, timers, PLC's, I/O modules, I/O-portsV REG.-Nr. 6166; Z E82292Contact dataContact configuration 1NOContact set bifurcated contactType of interruption micro disconnectionRated current3ARated voltage / max.switching voltage AC 250/277VACLimiting continuous current3AMaximum breaking capacity AC 750VALimiting making capacity, max 4 s, duty factor 10%5AContact material AgNi90/10Minimum contact load 5V / 1mAMechanical endurance20x106cyclesRated frequency of operation with / without load 10 / 1200min-1Contact ratingsType Load CyclesPCN-1..D3M.(-,H).(-,Z)3A, 250VAC resistive, 70°C, 20 cycles/min, EN61810-11x105PCN-1..D3M.(-,H).(-,Z)3A, 30VDC, resistive, 70°C, 20 cycles/min, EN61810-11x105PCN-1..D3M.(-,H).(-,Z)Pilot Duty B300 240VAC, UL508 6x103PCN-1..D3M.(-,H).(-,Z)Pilot Duty B300 120VAC, UL5086x103PCN-1..D3M.(-,H).(-,Z), 001 5A, 250 VAC res. 85°C, 10 cycles/min, EN61810-1 3x104Coil dataRated coil voltage range DC coil DC5...24VDCCoil power DC coil typ 120mWOperative range 1Coil versions,DC-coilcode voltage voltage voltage resistance powerVDC VDC VDC Ohm mW0055 3.50.5208+10%1200066 4.20.6300+10%1200099 6.30.9675+10%120012128.4 1.21200+10%1200242416.8 2.44800+10%120Other coil voltages on requestPCB layout / terminal assignmentBottom view on solder pinsDimensionsS0471-AAS0471-ABS0472-AInsulationDielectric strength coil-contact circuit3000V rms open contact circuit750V rmsClearance /creepage coil-contact circuit W 3,5 / 3,5mmMaterial group of insulation parts ITracking index of relay base PTI 600Type of insulation coil-contact circuitreinforced open contact circuitfunctional Rated insulation voltage 277V Pollution degree2Rated voltage system277V Overvoltage category as basic insulationIII Overvoltage category as reinforced insulationIIOther dataRoHS - Directive 2002/95/EC compliant as per product date code 0424Flammability class according to UL94V-0Ambient temperature range -30...+70°C Operate- / release time typ. 5/2ms Bounce time NO / NC contact < 1ms Vibration resistance (function) NO / NC contact 10g Shock resistance (function) NO / NC contact 10g Shock resistance (destruction)100g Category of protection RTIII - wash tight Mounting pcb Mounting position any Minimum mounting distance 0mm Resistance to soldering heat wash tight version 260°C / 5s Relay weight 3g Packaging unit 25 / 2000pcs。
D3+中文手册

Room 1701 Kerry Everbright City Tower 2, No.218 Tianmu Road West, Shanghai, P. R. China 200070Tel: (86 21) 6317 2505, 6317 2606; Fax: (86 21) 6317 1583; E-mail: master@ DEPOLOX 3 PLUS余氯分析仪上海中之良实业有限公司二○○一年三月Room 1701 Kerry Everbright City Tower 2, No.218 Tianmu Road West, Shanghai, P. R. China 200070Tel: (86 21) 6317 2505, 6317 2606; Fax: (86 21) 6317 1583; E-mail: master@ 第一节技术数据1.1 D3+电工学特性1.电源: 230V± 10%,50/60Hz,14VA。
保险F规格:T160mA,50×20mm2.CL2测量范围:0.2/0.5/1.00/2.00/5/00/10.00/20.0mg/lPH 测量范围:PH4.0~PH10.00, PH0~PH14(随选)氟化物测量范围: 0.2~2.00mg/l (随选)3.测量信号输入:氯、PH、氟化物各一个输入点(探头),对地电工学绝缘特性达50V。
4.mA输出:氯、PH、氟化物的测量各有一个mA输出点,对地电工学绝缘性50V,最大1000Ω负载。
5.开关量输出:氯、PH、氟化物各有两个可自由配置的报警触点,电子学对地绝缘500V。
6.继电器额定值触点: 5A,16HP,125,250AC或5A,30V DC 30W(最大值),用抑制二极管消除干扰。
7.1×数字输入:对于样水或循环泵监测以干式触点方式输入,非绝缘。
8.环境温度:0~50℃1.2 自由氯测量单元1.测量室:恒电势三电极测量室。
Baumer POG 10 增量编码器商品说明书

POG 10Features–TTL output driver for cable length up to 500 m –High resistance to shock and vibrations –EURO flange B10 / solid shaft ø11 mm –Large terminal box, turn by 180°Technical data - electrical ratings Voltage supply 9...30 VDC 5 VDC ±5 %Consumption w/o load ≤100 mA Pulses per revolution 300...5000Phase shift 90° ±20°Duty cycle 40...60 %Reference signal Zero pulse, width 90°Sensing method OpticalOutput frequency ≤120 kHz≤300 kHz (on request)Output signals K1, K2, K0 + inverted Error output (option EMS)Output stages HTL-P (power linedriver) TTL/RS422Interference immunity EN 61000-6-2Emitted interference EN 61000-6-3ApprovalsCE, UL approval / E256710POG 10Technical data - mechanical design Size (flange)ø115 mmShaft typeø11 mm solid shaft Admitted shaft load ≤300 N axial ≤450 N radial FlangeEURO flange B10Protection DIN EN 60529IP 66Operating speed ≤12000 rpm (mechanical)Operating torque typ. 2 Ncm Rotor moment of inertia 212 gcm²MaterialsHousing: aluminium die-cast Shaft: stainless steelOperating temperature-40...+100 °C-25...+100 °C (>3072 pulses per revolution)-50...+100 °C (optional)ResistanceIEC 60068-2-6Vibration 20 g, 10-2000 Hz IEC 60068-2-27 Shock 200 g, 6 ms Corrosion protection IEC 60068-2-52 Salt mist for ambient conditions C4 according to ISO 12944-2Explosion protectionII 3 G Ex nA IIC T4 Gc (gas) II 3 D Ex tc IIIC T135°C Dc (dust)Connection Terminal box2x terminal box (with option M)Weight approx.1.9 kg,2.1 kg (with option M)Optional–Function control with EMS–Redundant sensing with two terminal boxes –Second shaft end / Housing foot (B3) –With heating up to -50°CS u b j e c t t o m o d i fi c a t i o n i n t e c h n i c a n d d e s i g n . E r r o r s a n d o m i s s i o n s e x c e p t e d .S u b j e c t t o m o d i fi c a t i o n i n t e c h n i c a n d d e s i g n . E r r o r s a n d o m i s s i o n s e x c e p t e d .POG 10Part number POG10DNMounting type EURO flange B10B3Housing foot B3Voltage supply / signalsI 9...30 VDC / output stage HTL with inverted signals TTL 5 VDC / output stage TTL with inverted signals R 9...30 VDC / output stage TTL with inverted signalsPulse number - see tableOutput signals DN K1, K2, K0Redundant sensingWithout redundant sensingM With redundant sensing (not possible at version with housing foot B3)EMS - Enhanced Monitoring System Without EMS .2With EMSAccessoriesConnectors and cables HEK 8Sensor cable for encoders Mounting accessoriesK 35Spring washer coupling for solid shaft ø6...12 mm K 50Spring washer coupling for solid shaft ø11...16 mm K 60Spring washer coupling for solid shaft ø11...22 mm Diagnostic accessories 11075858Analyzer for encoders HENQ 1100Other pulse numbers on request.Incremental encoder Pulse number 30010002048409650010242500500051212003072Terminal assignmentPOG 10Output signals+UB Voltage supply (for the device); Ground (for the signals); Earth ground (housing)K1; A; A+ Output signal channel 1K1; A; A- Output signal channel 1 invertedK2; B; B+ Output signal channel 2 (offset by 90° tochannel 1)K2; B; B- Output signal channel 2 (offset by 90° tochannel 1) invertedK0; C; R; R+ Zero pulse (reference signal)K0; C; R; R- Zero pulse (reference signal) invertedErr; Err- Error output (option EMS)dnu Do not useTerminal significanceSubjecttomodificationintechnicanddesign.Errorsandomissionsexcepted.S u b j e c t t o m o d i fi c a t i o n i n t e c h n i c a n d d e s i g n . E r r o r s a n d o m i s s i o n s e x c e p t e d .DimensionsPOG 10 - Version with housing foot (B3)POG 10 (POG 10.2, POG 10 M, POG 10.2 M) - Version with Euro flange (B10)POG 10。
ECO Spot LED10 使用手册说明书
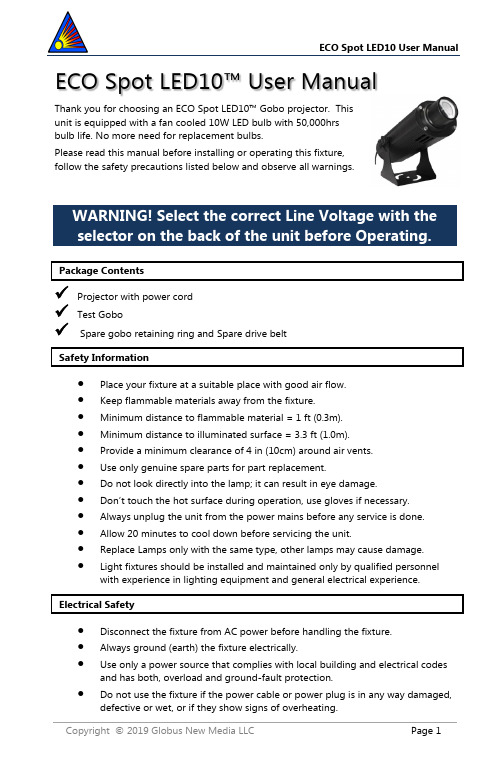
Thank you for choosing an ECO Spot LED10™ Gobo projector. This unit is equipped with a fan cooled 10W LED bulb with 50,000hrs bulb life. No more need for replacement bulbs.Please read this manual before installing or operating this fixture, follow the safety precautions listed below and observe all warnings.✓Projector with power cord ✓Test Gobo✓Spare gobo retaining ring and Spare drive beltECO Spot LED10™ User Manual•Place your fixture at a suitable place with good air flow.•Keep flammable materials away from the fixture.•Minimum distance to flammable material = 1 ft (0.3m).•Minimum distance to illuminated surface = 3.3 ft (1.0m).•Provide a minimum clearance of 4 in (10cm) around air vents.•Use only genuine spare parts for part replacement.•Do not look directly into the lamp; it can result in eye damage.•Don’t touch the hot surface during operation, use gloves if necessary.•Always unplug the unit from the power mains before any service is done.•Allow 20 minutes to cool down before servicing the unit.•Replace Lamps only with the same type , other lamps may cause damage.•Light fixtures should be installed and maintained only by qualified personnel with experience in lighting equipment and general electrical experience.•Disconnect the fixture from AC power before handling the fixture.•Always ground (earth) the fixture electrically.•Use only a power source that complies with local building and electrical codes and has both, overload and ground-fault protection.•Do not use the fixture if the power cable or power plug is in any way damaged,defective or wet, or if they show signs of overheating.One Year from Date of Purchase. For warranty, contact your dealer or Globus New Media LLC at 1-800-213-1092 or 1-831-431-8800•Power up the projector by pressing the larger switch in the back.•Turn on the gobo rotator with the smaller switch in the back and switch it off when the gobo projects in the desired position.•Focus the projection by twisting the lens in and out until the image is well focused.When used for the first time, the lens will often need to be twisted outwards many rotations to reach the focusing point.•Before the initial start-up, please unpack and carefully check for damage caused during transportation.•Place your fixture at a suitable place with good air flow.•Make sure there are no flammable materials close to the lamp.•When suspending the fixture above ground level, verify that the structure can hold at least 10 times the weight of all installed devices.•Verify that all external covers and rigging hardware are securely fastened and use an approved means of secondary attachment such as a safety cable.•The gobo rotator can be turned on/off with the small switch on the back plate.•There are no controls for rotating speed or direction.•The yoke can slide over the whole length of the fixture body to accommodate multiple pointing directions.•The yoke acts as a stand foot.•The yoke can be screwed to a wall or ceiling or fastened with a C-clamp•Unscrew the four thumbscrews to remove the front cover with the projection lens.•Push the two pins of the gobo retaining ring together and pull out the retaining ring. Carefully remove the old gobo and replace it with the newgobo.•If you have a glass gobo, place the more reflective side towards the light bulb.•Replace the retaining ring and make sure it evenly pushes the gobo all the way back.•Replace the front cover and adjust the focus.Use the Line Voltage Selector in the back to select the correct line voltage. US Setting (120V)90-130V, 60Hz, 14WInternational Setting (220V)200-240V, 50Hz, 14W10 x 4.33 x 3.5in (L x W x H)(254 x 110 x 90mm)Add 0.5 to 2in (12 to 50mm) to the length depending on the projection lens. Height with yoke: 5.7in (145mm) Weight 4.7lbs (2.1kg)Outer Diameter (OD): 37.5mm (1.47in) Max. Image Diameter (ID): 25mm (1.0in)Max Thickness: 4mm (0.16in)The projector can be equipped with different projection lenses. The more narrow the lens, the smaller and brighter the image will be at a given distance. Currently these lenses are available:Not Dimmable•Extremely high light density for ultra-efficient projection.•Power: 10W•Bulb life 50,000h•Color Temperature 5,500k•Rated Luminous flux: 850lm•Effective luminous flux: 400lm(average)•Wide 25 degree•Medium 20 degree•Medium Narrow 15 degree•Narrow 10 degree。
赫尔恩国度三点设备旋转裁缸说明书

STATEMENT OF POLICYpolicy of Behlen Country to improve its products where it is possible and practical to Country reserves the right to make changes or improvements in design and construction without incurring the obligation to make these changes on previously manufactured units.CUSTOMER SERVICE CENTERTAKE NOTE!IS FOUNDTHIS SYMBOLATTENTIONDANGER:Indicates immediate hazardous situation that,could resultinjury Critical Termto the situations,machine components for functional purposes,cannotWARNING:Indicates potentially hazardous situation that,could resultinjury includes hazards exposed removed.used unsafe practices. CAUTION:Indicates potentially hazardous situation that,may result moderate injury.be usedunsafeEQUIPMENT GUIDELINESattempting tractor thata live momentum created blades causeto be pushed Do NOTthis mower tractor independentrotating blades,and operators being knocked off the tractor by low hanging limbs and then being run over by the mower.Accidents are most likely to occur with machines that are loaned or rented to someone who has not read the owner’s manual and is not familiar with a Rotary Cut Mower.•Install and secure all guards and shields before starting or operating.The discharge chute, flaps,driveline guards and tractor guards should be used and maintained in good working condition.They should be inspected carefully before each use for missing or broken cables,chain links,shields,and guards.Worn items must be replaced at once to reduce the possibility of injury.•Disengage Power Take Off(PTO)and place tractor transmission in neutral before attempting to start the tractor engine.•Many varied objects,such as wire,cable,rope, or chains can become entangled in the working parts of the mower.These objects could then swing outside the housing at a greater velocity than the rotating blades.Such an occurrence is extremely hazardous.Never allow the cutting blades to contact objects which may cause damage to the mower or serious injury to the operator.Cut higher at first,allowing mower to clear such hidden objects.Never assume an area is clear.Always Check!•Always stop the tractor,disengage PTO,allow mower blades to come to a complete stop, lower implement to the ground,set brake,shut off the tractor engine and remove the ignition key before dismounting tractor.Never leave equipment unattended while the tractor is running.•Never place hands or feet under mower.Stay clear of all moving parts.•Do not reach or place any part of your body under the equipment until it is blocked securely.•Do not allow riders on the Rotary Cut Mower or tractor at any time.There is no safe place for riders.PREPARATION •Never operate the tractor and mower until you have read and completely understand this manual,the Tractor Operator’s Manual,and each of the safety messages found on the safety decals on the tractor and mower.•Personal protection equipment including hard hat,safety glasses,safety shoes,and gloves are recommended during assembly, installation,operation,adjustment, maintenance,repairing,removal,or moving the implement.Do not wear loose fitting clothing or jewelry and be sure to contain long hair around equipment.•PROLONGED EXPOSURE TO LOUD NOISE MAY CAUSE PERMANENT HEARING LOSS!Tractors with or without mowers attached can often create enough noise to cause permanent hearing loss.We recommend that you use hearing protection if the noise in the operator’s position exceeds80db.Long-term exposure to noise levels over90db adjacent to the operator may cause permanent total hearing loss.•NOTE:Hearing loss from loud noises(from tractors,chain saws,radios,and other sources close to the ear)is cumulative over a lifetime,with no chance of natural recovery.•Always wear your seat belt.Serious injury or even death could result from falling off the tractor-particularly during a rollover when the operator could be trapped under the ROPS or the tractor.•Clear area to be cut of stones,branches and other debris that might be thrown causing injury or damage.•Operate only in daylight or good artificial light.•Ensure mower is properly mounted, adjusted and in good operating condition.•Ensure that all safety guards and safety decals are properly installed and in good condition.•Do not operate unless all personnel, livestock,and pets are several hundred feet away to prevent injury by thrown objects. Never direct the discharge chute toward anyone.•Never operate tractor and Rotary Cut Mower under trees with low hanging limbs. Operators can be knocked off the tractor and then run over by the rotating blades.•The rotating parts of this machine have been designed and tested for rugged use. However,they could fail upon impact with heavy,solid objects such as steelguardrails,concrete abutments,and tree stumps.Such an impact could cause broken objects to be thrown outward at very high velocities.To reduce the possibility of property damage,serious injury,or even death,never allow the cutting blades to come in contact with such objects.•Stop cutter and tractor immediately upon striking an obstruction.Turn engine off,remove key,then inspect and repair any damage before resuming operation.•Stay alert for uneven terrain,holes,rocks,roots and other hidden hazards.Keep away from drop-offs and hazards that could cause rollover. Use extreme care and maintain minimum ground speed when transporting or operating on hillsides,over rough ground and when operating close to ditches or fences.Be careful and slow down when turning sharp corners and changing direction on slopes.Do not start or stop suddenly on slopes and avoid operating on steep slopes.In extremely uneven terrain, rear wheels weights,front tractor weights,and/or tire ballast should be used to improve stability.•Drive Rotary Cut Mower diagonally over sharp dips and avoid sharp drops to prevent tractor and Rotary Cut Mower from“hanging up”. Always cut downward on slopes,never cut across the face.Always check tractor manual for proper use on slopes.Practice will improve your skills in maneuvering on rough terrain.•A minimum of20%of the tractor and equipment weight must be on the tractor's front wheels. Without this weight,the tractor could tip over, causing personal injury or death.The weight may be attained with a front-end loader,front wheel weights,ballast in the tires or front tractor weights.When attaining a minimum20%of the tractor and equipment weight on the front wheels,you must not exceed the ROPS weight certification.Weigh the tractor and equipment. Do NOT guess or estimate!•Some Category0tractors have very short lift arms or5/8"diameter(Cat0)lift arm ball ends. These tractors are not usually suitable for using the Heavy Duty Rotary Cut Mowers.Check with your dealer on the Medium Duty Rotary Cut Mowers that have the Category1hitch that fits the Category0tractors.•This manual covers two types of Rotary Cut Mowers-the Heavy Duty and Medium Duty Mowers.The Heavy Duty Mower has a slip clutch attached to the gearbox.The MediumDuty and Sub Compact Mowers have a shear bolt.Slip Clutch Adjustment(when unit is supplied with one) The Slip Clutch is designed to slip so that the gearbox and driveline are protected if the mower strikes an obstruction.A new slip clutch or one that has been in storage over the winter may seize.Before operating the mower,make sure it will slip by performing the following:1.Turn off tractor engine and remove key.2.Remove driveline from tractor PTO.3.Loosen the six10mm cap screws to removeall tension from the spring plate.4.Hold clutch hub solid and turn shaft tomake sure clutch slips.5.If clutch does not slip freely,dissemble andclean the thrust plate faces,flange yoke,and clutch hub.6.Reassemble clutch.7.Tighten spring until it is against the thrustplate of the clutch and then back off each of the six nuts by two full rotations.The gapbetween the spring and thrust plate should be1/8".8.If clutch continues to slip when the spring iscompressed to1/8"gap,check frictiondiscs for excessive wear.Discs are1/8"when new.Replace discs after1/16"wear.Minimum disc thickness is1/16".Shear Bolt Replacement1.Slide yoke shield back.2.Realign holes in yolk and shaft and removeshear bolt with hammer and punch.3.Install new shear bolt.Lock yolk shield intoe only genuine Behlen Countryreplacement bolts.BOLTNOTE:Due to the many variations in tractor hitch points and distances between equipment gearbox input shaft and tractor PTO output shafts,some combinations will require PTO shafts to be shortened.If it is determined thatis the case,follow the instructions in the next steps.1.Raise and lower the Mower in order to locatethe shortest distance between gearbox input shaft and tractor PTO output shaft.With theMower in the shortest distance position,shut down the tractor and securely block themower in place.See Blocking Requirements.WARNINGIf the Mower is raised up so that the PTO shaft is an an angle sharper than35degrees,PTO MUST BE STOPPED!ing the cut section of the shield as a guide,cut the same amount off of each shaft.(See Fig.2A,2B &2C).NOT overfill This could damage to causepermanent gearbox.will not under warranty.Fig.2CFig.2BFig.1Fig.2Astand,else to between the Rotary Cut while tractor upAttach3-Pointto install clip on gearbox input allow the driveline to swing bolt is sheared causing injury or death.disengage enginerpm.Always tractor tobefore PTO. MOWER CUTTINGsure spring-activated or collarfreely firmly in tractorspline groove.sure driveline bottom out shortest length at leastat themower adjusted transport position,stop on quadrant to preventfrom contacting driveline whenMAINTENANCE SAFETY •Good maintenance is your responsibility. Poor maintenance is an invitation to trouble.•Keep service area clean and dry.•Be sure electrical outlets and tools are properly grounded.•Use adequate light for the job at hand.•Make sure there is ample ventilation.Never operate the tractor engine in a closed building.The exhaust fumes may cause asphyxiation.•Before working on this mower,disengage the PTO,be certain all moving parts on attachments have come to a complete stop, shut off the engine,set the brakes,and remove the ignition keys before attempting to perform maintenance.•Never work under equipment unless it is blocked securely.See Blocking Requirements in this manual.•Always use personal protection devices such as eye,hand and hearing protectors when performing any service or maintenance.•Frequently check mower blades.They should be sharp,free of nicks and cracks and securely fastened in place.•Periodically tighten all bolts,nuts,screws and check that all cotter pins are properly installed to make certain unit is safe to operate.•When completing maintenance or service, make sure all safety guards and devices are installed before using the Rotary Cut Mower.•After servicing,be sure all tools,parts and service equipment are removed from the Rotary Cut Mower.•Do not allow debris,grease or oil to build up on any deck or platform surfaces.•Where replacement parts are necessary for periodic maintenance and servicing,factory replacement parts must be used to restore your equipment to original specifications.•The manufacturer and/or distributor will not be responsible for injuries or damages caused by use of unapproved parts and/or accessories.•A first aid kit should be kept readily accessible while performing maintenance on this equipment.STORAGE SAFETY •Following use,or when unhooking the mower,disengage the PTO,stop the tractor, set the brakes,shut off the engine and remove the ignition keys.•Store the unit in an area away from human activity.•Do not park equipment where it can be exposed to direct contact with livestock for long periods of time.Damage to mowerand/or livestock injury could result.•Make sure all parked machines are on a hard, level surface and that all safety devices are engaged.WARRANTYThis unit carries a1year warranty,with the exception of wear parts.Dated proof of purchase required on all claims.TROUBLESHOOTING GUIDEPROBLEM POSSIBLE CAUSE POSSIBLE REMEDYLeaves a streak of uncut or partially cutgrass1.Mower not level side to side.Level3Point Hitch linkage on tractor.2.Blades dull or bent.Sharpen or replace blades.3.Carrier RPM too e correct PTO speed.4.Field conditions are so wet that thetractor tire is pushing grass intomud.Too wet to mow.Stop operation and waituntil it is drier.5.Ground speed too fast.Reduce ground speed by shifting to a lowergear.6.Blades lock back.Free blades.7.Blades riding up due to blade boltwear or loose bolts.Replace blade bolts.8.Grass is down from previous weatherconditions.Mow in only one direction.9.Possible build up of material undermower.Clean mower.10.Weed and grass stems are pusheddown by tractor tires and do notrebound up so they can be cut(thiscan happen when weed/grass ishigh).Mow again in opposite direction.Mow back and forth with enough overlap tomow tire track of previous cut again.Offset mower to left4"-6”by adjustingstabilizer bars.Then mow in counterclockwise direction(rotation direction ofblades will help cut stems pushed forward).Grass cutlower in center of swath thanat edge Height of mower lower at rear or front.Adjust mower height and attitude so thatmower rear and front are within½”of sameheight.See tailwheel adjustment instructions.Material discharges from mowerunevenly; bunches of material alongswath.1.Material too high and too muchmaterial.Reduce ground speed but maintain540rpmat tractor PTO,or make two passes overmaterial.Raise mower for the first pass andlower to desired height for the second andcut a90°to first pass.Raise rear of mowerhigh enough to permit material to discharge,but not so high that conditions listed aboveoccur.2.Grass Wet.Allow grass to dry before mowing.Slowground speed of tractor but keep enginerunning at full PTO rpm.Cutting lower willhelp.3.Rear of cutter too low,trappingmaterial under mower.Adjust mower height and attitude.(seeinstructions).Gearbox overheating 1.Low on lubricant.Fill to proper level.2.Improper type lubricant.Replace with proper lubricant.3.Excessive trash build-up aroundgearbox.Remove trash.Blade is scalping ground 1.Mower too low.Raise mower-reset tail wheel and3Pointcontrol stop.2.Field is ridged.Cut field at a different angle.3.Field is too wet.Stop and wait until it is drier.Mower will notcut.(Shearbolt driveonly)Shear bolt sheared.Install new shear e Grade2ONLY. Mower movesfrom side to side whencutting Loose tractor sway chains or bars,orsway blocks improperly installed.Adjust sway chains,bars,or sway blocks.PTO contactscutter front frame when raised Raising mower too high or incorrectadjustment of tractor top link.Adjust top link or tractor lift stops.(seeattachment instructions).Blade bolts come loose 1.Bolts not tightened.Tighten bolts to350ft./lb.2.Bolt hole elongated or oversized.Replace blade carrier.3.Blade bolt threads are worn ordamaged.Replace blade bolt,lockwasher,and nut.Blade wears too fast 1.Cutting in sandy conditions.Increase cutting height.2.Cutting in rocky conditions.Increase cutting height.3.Blades hitting ground.Increase cutting height.Mower seems to require excessivepower 1.Advancing into grass or brush toorapidly.Reduce forward travel speed.2.Hitting ground.Raise mower and reset tailwheel.3.Worn or dull blades.Sharpen or replace blades.4.Tractor not large e more horsepower tractor.Excessive vibration 1.Check gearbox bolts.Tighten if loose.2.Check for loose nuts on bladeholderand blades.Tighten if loose.3.Check for bent output shaft.If shaft isbent,oil will normally leak frombottom seal.Replace shaft if bent.4.Check to see if blades arefree-swinging.Free blades so they swing.5.Check for even wear on each bladetip.Were both blades changed atthe same time?Weigh blades.Weight should be within1oz.ofeach other.Always replace both blades.6.Blade broken.Replace blades,in sets.7.Blade beam bent.Replace blade beam.8.New blade or bolts matched withworn blade or bolts.Replace blades or bolts in sets.Excessive vibration9.Drivelines not placed correctly.Implement and tractor yokes mustbe in line.Replace driveline.10.Wire or rope wrapped around bladebeam.Remove wire or rope.11.Blades worn and are out of balance.Replace blades,in sets.Gearbox noisy 1.Rough gears.Run in or change gears.2.Worn bearings.Replace bearings.3.Low oil in gearbox.Check level and add oil.Gearbox leaking 1.Damaged oil seal.Replace seal.2.Bent shaft.Replace oil seal and shaft.3.Shaft rough in oil seal area.Replace or repair shaft.4.Oil seal installed wrong.Replace seal.5.Oil seal not sealing in the housing.Replace seal or use a sealant on outsidediameter of seal.6.Oil level too high.Drain oil to proper level.7.Hole in gearbox.Replace gearbox.8.Gasket damaged.Replace gasket.9.Bolts loose.Tighten bolts.Excessivewear of tailwheel tire 1.Tire not turning properly.Check wheel assembly for proper lubrication.2.Tailwheel not castering properly.Check tailwheel yoke assembly for properlubrication or for mechanical binding.Front hitch“A”frame bending sideways 1.Operator turning sharply hittingobjects with tailwheel frame ofmower deck.Drive carefully and plan turns to avoid hittingbuildings,posts,trees,etc.2.Tailwheel not castering properly.Check tailwheel yoke(see above under tire wear).3.Mower is being operated too low andmower deck is contacting groundduring turns.A.Raise mower(especially on rough ground)B.Set stop on hitch controls lever so hitch liftarms do not drop mower on ground.4.Tractor3point hitch is leaking downand mower deck is contactingground.A.Repair tractor hitch hydraulic system.e limit chains to keep lift arms from goinglower than set limit.Parts List for all Rotary Cut MowersItem No.Rotary Cut MowerDescription Cat.1Lift PinPTOShaftGearBoxStumpJumperCutterBladesBladeBoltBladeNutBladeWasherSafety DecalSheet8011030ORG4'Sub Compact172801130184338011040YEL4'Medium Duty3018433。
Ecostrad数字加热元件用户手册说明书
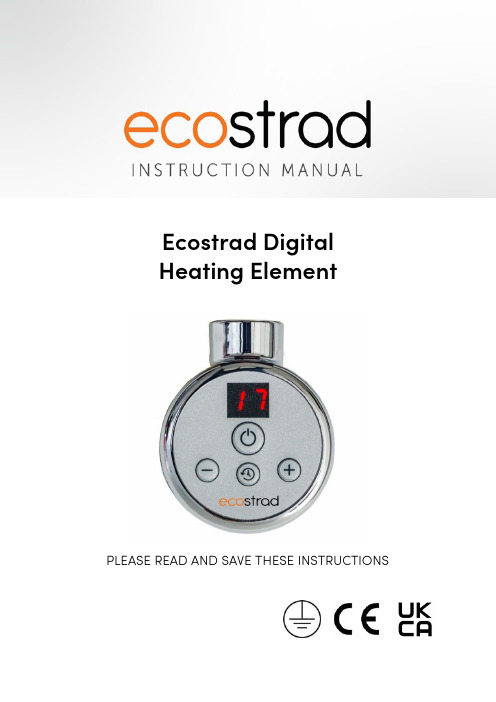
Ecostrad DigitalHeating ElementPLEASE READ AND SAVE THESE INSTRUCTIONSSymbolsWarningThis symbol indicates a hazard with an average risk level which, if notavoided, could result in serious injury or death.Warning of electrical voltageThis symbol indicates danger to the life and health of persons due toelectrical voltage.Hot surfaceThis symbol located on the device indicates that its surfaces are hot duringand immediately after operation. Hot surfaces should not be touched:danger of burns.Observe instructions in manualThis symbol located on the device indicates that instructions in the operatingmanual must be observed when installing and using the device.Contents1 |About the Manual - - - - - - - - - - - - - - - - - - - - 42 |Warnings & Precautions- - - - - - - - - - - - - - - - - 43 |Technical Information - - - - - - - - - - - - - - - - - - 74 |Installation- - - - - - - - - - - - - - - - - - - - - - - - - 74-1Fitting instructions - - - - - - - - - - - - - - - - 85 |Control Dial - - - - - - - - - - - - - - - - - - - - - - - - 115-1Display- - - - - - - - - - - - - - - - - - - - - - - - 115-2Standby mode - - - - - - - - - - - - - - - - - - - 115-3Heating mode - - - - - - - - - - - - - - - - - - - 115-4Timer mode - - - - - - - - - - - - - - - - - - - - 126 |Troubleshooting - - - - - - - - - - - - - - - - - - - - - 137 |Warranty- - - - - - - - - - - - - - - - - - - - - - - - - - 138 |Disposal - - - - - - - - - - - - - - - - - - - - - - - - - - 141 | About the ManualThis manual describes the Ecostrad Digital Heating Element and details how to install and use the product. It is important to thoroughly review this manual before using the product. Ecostrad declines all responsibility for any operations effected on the appliance without respecting the instructions reported in this manual.Please contact your supplier for technical advice. For additional information regarding any aspect of the Ecostrad Digital Heating Element, contact: Ecostrad Ltd.Firecrest HouseLingerfield Business ParkMarket Flat LaneKnaresboroughNorth YorkshireHG5 9JAhttps:///2 | Warnings & PrecautionsRead this manual carefully before using or installing the heating element. Always store the manual in the immediate vicinity of the element or its site of use.Read all safety warnings and all instructions.Failure to follow the warnings and instructions may result in electric shock, fire, serious injury, or all of the above. Save all warnings and instructions for future reference.NOTE - This element cannot be used as part of a central heating system or in a dual source towel rail. The electric towel rail must be powered by the heating element only.WarningChildren of less than 3 years should be kept away unless continuouslysupervised. Children aged from 3 years and less than 8 years shall onlyswitch on/off the appliance provided that it has been placed or installed inits intended normal operating position and they have been givensupervision or instruction concerning use of the appliance in a safe way andunderstand the hazards involved. Children aged from 3 years and less than8 years shall not plug in, regulate, or clean the appliance, or performmaintenance.WarningIn order to avoid a hazard due to inadvertent re-setting of the thermalcut-out, this appliance must not be supplied through an external switchingdevice, such as a timer, or connected to a circuit that is regularly switchedon and off by the utility.WarningSome parts of this product can become very hot and cause burns.Do not touch the surface when in operation. Do not install close tocurtains or other combustible materials. Particular attention should begiven where children and vulnerable adults are present.WarningDo not use the device in enclosed spaces if persons are present who cannotleave the room independently and are not under constant supervision.•Fluid-filled towel rails for space heating and towel drying are the only suitable appliances in which to install the element.•The element must NEVER be used unless it has been professionally installed insidea towel rail filled with fluid to the correct level. The element will cease functioningwithin 5 seconds if it is not fully submerged in a suitable fluid during operation.•The element is designed for use in vertical towel rails. Use in horizontal towel rails is not recommended because the long horizontal bars can impede heatcirculation.•It is imperative that the towel rail intended for use with the heating element has the correct volume of fluid. The recommend quantity of fluid with the towel rail is 90% of the unit's total volume. If you are installing the element in towel rail that has been pre-filled for use with this element, do not allow fluid to escape when the element is fitted. In the case of loss of heating fluid, contact your supplier. •This device is intended for home use only.•The element must be installed by a licensed electrician in accordance with current IEE wiring regulations.•The element must be connected to a 220-240 Volt AC mains power supply via a switched fused spur cable outlet, and must be earthed.•The element is a Class I unit and therefore must always be earthed.•Ensure the element's power cord does not touch the hot parts of the device or the towel rail.•Do not use the device if you detect damage to the mains plug or power cable. If the supply cord is damaged, it must be replaced by the manufacturer, its service agent or similarly qualified persons to avoid a hazard. All repairs and servicing must be carried out by a qualified person.•The towel rail in which the element is installed must be permanently fixed to the wall. Do not fit the towel rail below or in front of an electric socket.•The element can be installed in bathrooms in Zone 1, as defined by applicable law, subject to any additional regulations concerning electrical installations in wet areas, as shown in Figure 1.•The element must be placed where the switches and controllers cannot be touched by a person in a bathtub or shower.•The element must be disconnected from the mains during cleaning and maintenance.•Never attempt to disconnect the control head from the heating element. The product is an integrated unit that has been factory sealed. •Do not open the casing of the element — any interference with internal components will invalidate the warranty.•Towel rails fitted with the element can be very hot and can cause burns. Pay special attention when used in the presence of children or people with disabilities. •If the towel rail is used to dry clothing or towels, ensure the fabrics have only been washed in water, to prevent the device coming into contact with harsh chemicals. •Do not allow children to play with the element. This appliance is not a toy. •The unit is not to be used by persons (including children) with reduced physical, sensory or mental capabilities. Such persons may only use the device if they are supervised by a responsible person.•For the safety of very small children, install the towel rail so that the lowest rail is at least 60cm above the floor.•Ensure the heating element control head is not exposed to leaking water. Figure 1 | Bathroom installation zones3 | Technical Information4 | InstallationThese are general-purpose instructions for fitting your element into a suitable towel rail. Always check with the towel rail manufacturer to ensure the product is suitable for use with the element, and follow any additional installation guidance provided with the unit. Installation must be completed by a qualified electrician. Do not attempt installation DIY.WARNING – Do not attempt to operate the element before it has been installed in a fluid-filled towel rail. Switching on the element in an empty towel rail or in open air will cause the element to cease functioning.WARNING – Do not attempt to install the heating element whilst it is connected to electricity. Disconnect device from mains prior to installation.WARNING – Please take every precaution when filling the towel rail or fitting the element in order to avoid being burnt by hot liquid.WARNING – Remove the protective coating on the plastic enclosure before use.Table 1 | Specifications Voltage230V AC / 50Hz Wattage200-600W Room temperature setting10–35 °C IP RatingIP44Appliance classClass I Power cable length1.5m Thread sizeG ½ "Certification These products are in compliance with 2014/30/EU Electromagnetic Compatibility Directive and 014/35/EU Low Voltage Directive.These products carry CE mark accordingly.4-1 | Fitting instructionsIf you have purchased a pre-filled towel rail with the element already installed, skip to step 7 below.1.Read all safety instructions and warnings stated in the preceding section of this manual. Failing to follow these instructions can cause damage to life or property.2.Identify the inlet where the element will be fitted in the towel rail. The element is fitted vertically, in the bottom left or right vertical strut. Never fit the element at the top of a towel rail or in horizontal towel rails (see Figure 3).Control HeadHeating Element Power CordFigure 2 | Ecostrad Digital componentsFigure 3 | Correct and incorrect installation positions of the element3.Tilt the towel rail until the fitting location is at the highest point, as shown in Figure4. This prevents any fluid escaping if your towel rail is pre-filled.4.Slowly, so as not to displace any fluid, remove the cap from the inlet and push the heating element into the towel rail.5.Tighten the element at the main nut, using a size 26 spanner (Figure 5, right).Ensure the connection between the towel rail and the heating element is tight and there is a firm seal. This prevents leakage after installation.WARNING — Never attempt to tighten the element by twisting the control head or product housing by hand. Always use the correct tools as directed in the instructions.6.If the towel rail has been pre-filled by the manufacturer, skip to the next step. Do not tamper with the heating medium in pre-filled towel rails.If the towel rail is yet to be filled, tilt the towel rail so the next free filling cap is at the highest point. Ensure the towel rail is not resting on the heating element controller, power cable or any other parts of the connection. Remove the cap and fill the towel rail to 90% of its volume with a suitable heating medium (Figure 6 & Figure 7). This should be a glycol-based formulation approved by the towel rail manufacturer. Replace cap when done.NOTE — It is critical that the correct volume of heating medium is used. Underfilling the towel rail will impede circulation and prevent the unit from heating up. Overfilling the towel rail can cause a dangerous build up of pressure as the fluid heats up. A suitable air cushion must be maintained. Calculating the volume of heating medium is a job for a professional electrician or heating engineer and should not be attempted DIY. If unsure, use the element only with a pre-filled towel rail. Figure 4 | Inlet tilted to its highest point before opening..Figure 5 | Tighten element at main nut7.Rotate the towel rail to its correct orientation and hang on the wall, according to the instructions provided with the unit.8.Connect the element electrics to the power supply. The element should be hardwired to a switched fused spur. This is a task for a qualified electrician and should not be attempted DIY. Risk of electric shock. Figure 6 | Removing towel rail cap and using funnel to fillFigure 7 | Air cushion requirement (image for illlustrative purposes only)5 | Control Dial 5-1 | DisplayWhen the Digital is first turned on after being disconnected from the mains, the screen will show a countdown from 3 before entering standby mode.5-2 | Standby modeIn standby mode the element does not heat. You can use thebutton to switch between standby and on. When the element is in standby, the screen will show “--”. 5-3 | Heating modePress the button to switch the element on. The element will show the set temperature. After a few seconds the element will switch to showing the current room temperature.Use and to decrease and increase the set temperature between 10 and 35 °C. After the set temperature is selected, the element will again resume showing the current room temperature. If the room temperature is lower than the set temperature, the element will begin heating.The time it takes for the room to reach the set temperature depends on many factors, including the size of the room and the power of the heating element.Figure 8 | Control dial display Temperature/Timer Standby Button Decrease/IncreaseTemperatureTimer Button5-4 | Timer modeWhen the timer is set, the element will heat to the set roomtemperature for the time period selected. When the period ends, the element will switch to standby mode and cease heating.When the timer is running, the element displays a small flashing light between the numbers of the room temperature. Set timer range is 0 - 5 hours, in steps of one hour, and can be adjusted as below:1.Press the button. The display will show the numberof set hours for the timer.2.Repeatedly press the button to increase the timerperiod.If you need to cancel the timer, press until the display shows "0". The element will resume heating to the set temperature indefinitely.6 | Troubleshooting7 | WarrantyThe Ecostrad Digital element carries a 2-year guarantee. Within the stated period, starting from the date the customer receives their unit, Ecostrad guarantee to repair or replace the unit where a fault is due to defects in materials or manufacturing. The warranty does not cover any defect arising from damage, negligence, usage outside the product’s intended purpose or fair wear and tear. The warranty is only valid when the unit has been used at the specified supply voltage, and in accordance with all conditions specified in this manual. The warranty will be void if the element has been tampered with or opened in any way; if it has been used in open air, or in an unsuitable vessel; or if the ratings label has been removed.The warranty does not cover failures and faults due to force majeure, accidental damage, mishandling, external impact, chemical agents or atmospheric phenomena, incorrect use of the device, the purchaser’s faulty electrical installations, transporting the device or problems caused by the device being handled by persons not authorised by Ecostrad. The element is not a DIY product; an invoice may be required to confirm installation was carried out by a qualified professional. Ecostrad cannot accept responsibility for damage, loss or injury caused by incorrect installation, maintenance, cleaning or covering the device.Error CodePossible Cause Action to take E01This might be caused by:•Heating sensor cable might be disconnected.•Heating probe might be damaged.•Heating element might be damaged. The product should be reset. Cut power to the device then restore.If the fault continues, disconnect the product and contact Ecostrad by the contact details in section 1E02This code shows that the device has detected an overheat state and has cut power. This might be because:•Electronic control unit might be damaged.•Heating element might be damaged.•Voltage change in the electric supply system might have affected the unit.The product should be reset. Cut power to the device then restore.If the fault continues disconnect the product and contact Ecostrad by the contact details in section 1.The warranty is a contract with the original purchaser and does not transfer if the unit is re-sold, gifted or inherited. Proof of purchase, including order number and order confirmation or invoice, will be required if a claim is made.The warranty covers only the model shown on the purchase invoice. The warranty covers the repair or replacement of the defective product only and Ecostrad shall have no liability for installation costs or consequential losses however incurred. Claims must be made with the establishment where the device was purchased. This warranty does not affect the customer’s consumer rights.8 | DisposalIn accordance with WEEE Directive 2012/19/EU, the icon with thecrossed-out waste bin on electrical or electronic equipmentstipulates that this equipment must not be disposed of withhousehold waste at the end of its life. You will find collection pointsfor free return of waste electrical and electronic equipment in yourvicinity. The addresses can be obtained from your local authority.The separate collection of waste electrical and electronicequipment enables the re-use, recycling and other forms ofrecovery of waste equipment, and prevents any negative effectsfor the environment or human health caused by the disposal ofhazardous substances potentially contained in the equipment.。
XERUN XD10 Pro 3D打印机说明书
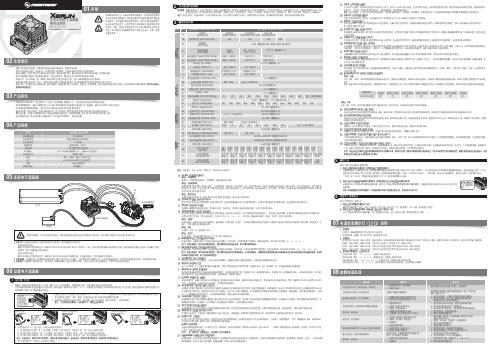
· 内置强大的开关模式BEC,最大电流10A,支持5-7.4V线性调整(调整量0.1V),更好的适应不同电压要求的舵机及设备。
· 独立的参数编程插口,连接LCD编程盒或OTA Programmer模块时无需从接收机中拔出油门线,更加便捷,该插口亦可为第2个风扇进行供电。
· 油门驱动和刹车频率的变频调节,满足车手对马达前进动力和制动力进行精准调节的要求。
· 多重保护功能:电压过低保护、电机及电调过热保护、油门失控保护。
电池防反接保护(常规外挂电容包仍会因电池接反而损坏!)· 数据记录功能:可以用LCD编程盒或HW Link读出电调和电机最高温度、最高转速等数据,便于车手对动力系统运行情况进行分析。
· 支持电调固件升级(需另购多功能LCD编程盒或OTA Programmer模块),享用最新功能。
持续/峰值电流支持电机类型100A/800A有感无刷电机和无感无刷电机型 号XERUN XD10 Pro参数设定接口独立编程口XERUN XD10 Pro车用无刷电子调速器使用说明书01声明备注:4B设置为”自动“方式时,表格中4C、4D两项为不可设置项。
选项2:自动设为“自动”方式时,Boost进角值根据当前油门量来动态分配。
只有全油门时,Boost实际开启值才为Boost设置值。
1A:运行模式(Running Mode):选项1:正转带刹车此模式下,车辆仅能前进和刹车,但不能倒车,该模式通常用于竞赛。
选项2:正反转带刹车此模式则提供了倒车功能,通常用于训练。
“正反转带刹车”模式采用“双击式倒车”方式,即油门摇杆在第一次从中点区域推至反向区域时,电机只是刹车,不会产生倒车动作;当油门摇杆快速回到停止才会倒车,中立点区域并第二次推至反向区域时,如果此时电机已停止,则产生倒车动作,如果电机未停止,则不会倒车,仍是刹车,此时如果电机已经这样做的目的是防止车辆行驶过程中因多次点刹而造成误 倒车。
Ecotect生态模拟大师 教程

Ecotect界面简介
5.可视化设置面板(Visualisation Settings Panel) 如图所示的可视化设置面板,此面板主要用于控制可 视化视图中的各种显示设置,例如可以在这里设置可视化 页面中的背景色、线宽、草图以及雾化等效果。 6.投影设置面板(Shadow Settings Panel) 如图所示的投影设置面板,此面板用于调整与太阳投 影相关的各种设置和选项,例如可以隐藏或打开太阳投影 、调节投影时间范围以及设置投影动画等。 7.分析网格面板(Analysis Grid Panel) 如图所示的分析网格面板,此面板用于管理和编辑分 析网格的各种属性以及调整其显示方式和状态,例如可以 在这里设置分析网格的位置、单元大小以及数据的颜色和 级差等。 8.声波线和粒子面板(Rays and Particles Panel) 如图所示的声波线和粒子面板,此面板用于调整模型 中声波线和粒子的显示状态和效果,其中包括了声波线和 粒子的数量、发射方式以及状态等选项。
Ecotect界面简介
(3)区域/指针工具条
此工具条用于设置日照、遮阳等热工计算用的日期、时间、地理经纬度和加 载当地气象数据等,同时其右上角将显示当前设置的地理经纬度等信息,如图所 示。另外在绘制模型状态下,区域/指针工具条变成物体的坐标数据输入框。
(4)捕捉工具条
地理经纬度设置
此工具条提供了捕捉距离、角度以及控制点的快速调整通道,另外通过它 还可以调整原点设置和显示当前操作区域。
(8)控制面板选择器
在用户界面右侧一共排列有12个控制面板,用户可以通过 它们对模型进行快速的操作和设置,控制面板选择器用于在上 述面板中进行切换。需要注意的是部分面板命令在菜单中是没 有的。
Ecotect界面简介
TOP QUALITY COWHIDE GREY DOCKER GLOVE 10说明书
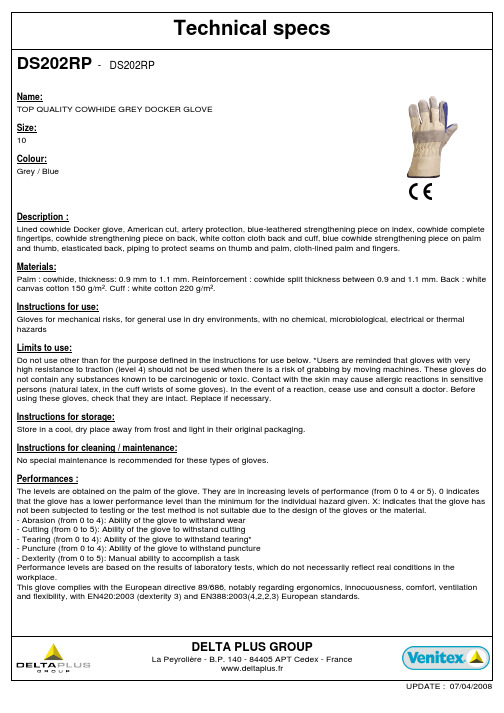
DS202RP - DS202RP
Name: TOP QUALITY COWHIDE GREY DOCKER GLOVE
Size: 10
Colour: Grey / Blue
Description : Lined cowhide Docker glove, American cut, artery protection, blue-leathered strengthening piece on index, cowhide complete fingertips, cowhide strengthening piece on back, white cotton cloth back and cuff, blue cowhide strengthening piece on palm and thumb, elasticated back, piping to protect seams on thumb and palm, cloth-lined palm and fingers.
DELTA PLUS GROUP
La Peyrolière - B.P. 140 - 84405 APT Cedex - France www.deltaplus.fr
UPDATE : 07/04/2008
Materials: Palm : cowhide, thickness: 0.9 mm to 1.1 mm. Reinforcement : cowhide split thickness between 0.9 and 1.1 mm. Back : white canvas cotton 150 g/m². Cuff : white cotton 220 g/m².
- 1、下载文档前请自行甄别文档内容的完整性,平台不提供额外的编辑、内容补充、找答案等附加服务。
- 2、"仅部分预览"的文档,不可在线预览部分如存在完整性等问题,可反馈申请退款(可完整预览的文档不适用该条件!)。
- 3、如文档侵犯您的权益,请联系客服反馈,我们会尽快为您处理(人工客服工作时间:9:00-18:30)。
Terminal Pitch
Part No.
( ):Mounting No
Clamp
Yes
(V)
(µF) 12000 15000 18000 22000 27000
(mm)
(mm)
64 64 64 64 77 64 77 77 90 77 90 77 90 90 64 64 64 64 77 64 77 77 90 77 90 90 90 64 64 64 77 64 77 77 90 77 90 90 90 64 64 64
Freq.(Hz)
n Frequency Correction Factor for Ripple Current
W.V.(V)
φD(mm)
160, 200 250, 350 400, 450
64 77, 90 64 77, 90 64 77, 90
50 0.86 0.90 0.83 0.85 0.81 0.85
28.6 28.6 28.6 28.6 31.8 28.6 31.8 31.8 31.8 31.8 31.8 31.8 31.8 31.8 28.6 28.6 28.6 28.6 31.8 28.6 31.8 31.8 31.8 31.8 31.8 31.8 31.8 28.6 28.6 28.6 31.8 28.6 31.8 31.8 31.8 31.8 31.8 31.8 31.8 28.6 28.6 28.6
N N N N N N N N N N N N N N N N N N N N N N N N N N N N N N N N N N N N N N N N N N
F F F F F F F F F F F F F F F F F F F F F F F F F F F F F F F F F F F F F F F F F F
For general-purpose inverter, power supply for backup system, motor-control, inverter -25 to + 85°C 160 to 450 V .DC 2700 to 56000 µ F ±20% (120Hz/+20°C) (µA) or 5(mA) whichever, smaller, after 5 minutes application of rated working 3 CV voltage at +20°C C:Capacitance(µF) V: W.V. (V.DC) Please see the attached standard products list After 5000 hours application of DC voltage with specified ripple current (< rated DC working voltage ) at +85°C, the capacitor shall meet the following limits.(160 to 250 W.V. : 2000 hours at +85°C)
103 125 145 168 125 222 150 168 150 190 168 222 190 222 103 125 145 168 125 222 150 168 150 222 168 190 222 125 145 168 125 222 150 190 150 222 168 190 222 103 125 145
15.9 17.2 19.4 21.3 21.3 22.4 22.4 23.7 25.0 25.7 25.7 28.2 28.2 30.7 14.7 15.8 18.1 19.8 19.8 22.0 22.0 23.0 23.0 25.4 25.4 27.6 30.3 12.8 14.7 16.6 16.6 19.0 19.0 19.7 19.7 21.8 21.7 24.0 26.5 10.3 12.1 14.3
Endurance : 160 to 250V.W. : 85°C 2000 h 350 to 450V.W. : 85°C 5000 h
Design, Specifications are subject to change without notice. Ask factory for technical specifications before purchase and/or use. Whenever a doubt about safety arises from this product, please inform us immediately for technical consulation without fail. Mar. 2005
60 0.91 0.95 0.88 0.90 0.87 0.90
120 1.00 1.00 1.00 1.00 1.00 1.00
300 1.05 1.05 1.07 1.05 1.07 1.05
360 1.06 1.06 1.08 1.06 1.08 1.06
1k 1.08 1.08 1.13 1.11 1.13 1.11
160 33000 39000 47000 56000 10000 12000 15000 18000 22000 200 27000 33000 39000 47000 8200 10000 12000 15000 250 18000 22000 27000 33000 3900 350 4700 5600
n Recommended Applications n Specifications
Category temp. range Rated W.V. Range Nominal Cap. Range Capacitance Tolerance DC Leakage Current Dissipation Factor
Endurance
Shelf Life Withstand Voltage
Capacitance change ±20 % of initial measured value D.F. < 200 % of initial specified value DC leakage current < initial specified value After storage for 1000hours at +85±2 °C with no voltage applied and then being stabilized at +20 °C, capacitors shall meet the limits specified in ìEnduranceî.(With voltage treatment) Application of 1500 V.AC between V-block and terminals for 1 minute, there shall be no abnormalities like destruction of insulator.
– EE187 –
元器件交易网
Aluminium Electrolytic Capacitors/GUP n Standard Products
W.V. Cap.
(±20%)
Case size
Diaபைடு நூலகம் Length (mm)
Specification
Ripple D.F. current (120Hz) (120Hz) (+85°C) (+20°C) (A)
– EE188 –
元器件交易网
Aluminium Electrolytic Capacitors/GUP n Standard Products
W.V. (V) Cap.
(±20%)
Case size
Dia. (mm) Length (mm)
Specification
Ripple D.F. current (120Hz) (120Hz) (+85°C) (+20°C) (A)
ECOG2CP123D( ) ECOG2CP153D( ) ECOG2CP183D( ) ECOG2CP223D( ) ECOG2CP223E( ) ECOG2CP273D( ) ECOG2CP273E( ) ECOG2CP333E( ) ECOG2CP333F( ) ECOG2CP393E( ) ECOG2CP393F( ) ECOG2CP473E( ) ECOG2CP473F( ) ECOG2CP563F( ) ECOG2DP103D( ) ECOG2DP123D( ) ECOG2DP153D( ) ECOG2DP183D( ) ECOG2DP183E( ) ECOG2DP223D( ) ECOG2DP223E( ) ECOG2DP273E( ) ECOG2DP273F( ) ECOG2DP333E( ) ECOG2DP333F( ) ECOG2DP393F( ) ECOG2DP473F( ) ECOG2EP822D( ) ECOG2EP103D( ) ECOG2EP123D( ) ECOG2EP123E( ) ECOG2EP153D( ) ECOG2EP153E( ) ECOG2EP183E( ) ECOG2EP183F( ) ECOG2EP223E( ) ECOG2EP223F( ) ECOG2EP273F( ) ECOG2EP333F( ) ECOG2VP392D( ) ECOG2VP472D( ) ECOG2VP562D( )
φD1 76.0
W1 8.0 8.0 8.0
W2 13.0 14.0 14.0
Design, Specifications are subject to change without notice. Ask factory for technical specifications before purchase and/or use. Whenever a doubt about safety arises from this product, please inform us immediately for technical consulation without fail. Mar. 2005