一种微生物复合菌剂的生产工艺流程及详细设计要求剖析教案资料
一种微生物复合菌剂的生产工艺流程及详细设计要求剖析

一种微生物复合菌剂的生产工艺流程及设计要求(附简图)一.生产前的准备工作(1)生产用菌种的鉴定:主要包括纯度鉴定,生产性能的检查,有无杂菌污染。
还有就是菌种的活性,重要特性有无退化等。
(2)如菌种已发生功能性改变或被杂菌污染,还需要进行菌种的纯化或或复壮。
(3)其次在规模生产之前,还要通过实验室中试,确定该菌群的最适生长温度,PH,发酵培养基的最适成分与比例;生长曲线的绘制与最适培养时间的确定。
我们一般选取对数生长期的菌体(丝)做为生产发酵用的菌种。
最佳接种量与装液量的控制。
二.实验室菌种的活化与种子培养阶段:(1)将冷冻保藏管中的菌种在斜面中活化(37℃ 24h),并在平板中进行纯化(37℃ 24h)。
最终得到斜面菌种或菌种斜面。
斜面培养基成份葡萄糖牛肉膏蛋白胨Nacl 琼脂PH组成比例0.1% 1% 1% 0.5% 2.0-2.5% 7.0-7.2(2)摇瓶培养阶段: 取一环纯化后的的菌种,接入装量为20mL种子培养基的250mL三角瓶中,置于180r/min中摇床中培养 (37℃ 18h)。
分别取1mL的种子液 ,接入五个盛有20mL发酵培养基的250 mL 三角瓶中。
置于180 r/ min摇床中培养(37℃ 24h)。
接种量为三角瓶实际培养基装量的4-5%.PH 控制在7.0-7.5之间。
培养基组成见下表:摇瓶种子培养基成分葡萄糖尿素硫酸镁磷酸氢二钾玉米浆硫酸亚铁硫酸锰PH各组成成分比例(%) 2.50.5 0.040.12.5-3.52ppm 2ppm 7.0(注;1ppm=1mg/l)三.生产车间多级种子罐发酵阶段:工艺流程工艺条件中控121℃~125℃蒸汽0.103MPa~0.168 MPa 0.5h~1.0h种子罐培养基加料体积50%~75%,实际为60%PH6.5~7.5 精密试纸或PH 计121℃~125℃蒸汽0.103MPa~0.168 MPa 0.5h~1.0h灭菌空气25℃~35℃常压全部设备灭菌一级种子罐配料一级种子罐PH 值检测一级种子罐灭菌一级种子罐降温摇瓶菌种物料量的0.5-5%.实际接种量为1%灭菌空气25℃~35℃镜检:24~36h菌体的形态、密度消泡剂芽孢形成率≧80% 搅拌转速:180r/min二级种子罐重复上述操作和参数控制其中,由摇瓶菌种向一级种子罐的接种量,控制在一级种子罐实际装料量的0.5%-5.0%;PH 控制在 6.5-7.5;发酵温度控制在25℃~35℃;装料量控制在种子罐公称容积的60%左右。
微生物复合菌剂及其处理方法和应用与设计方案
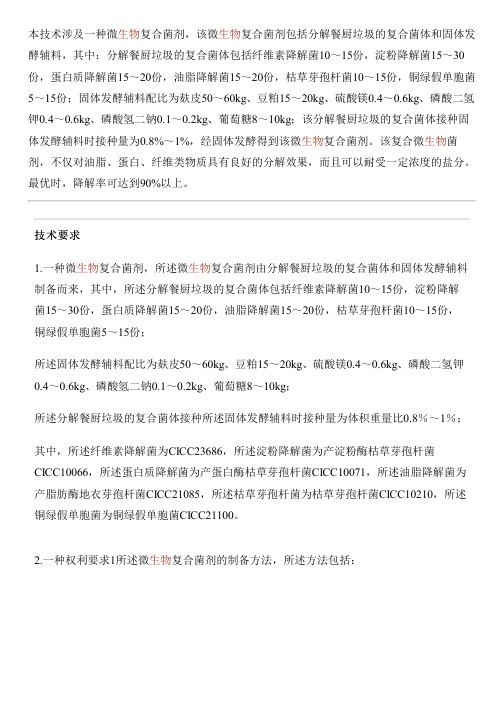
本技术涉及一种微生物复合菌剂,该微生物复合菌剂包括分解餐厨垃圾的复合菌体和固体发酵辅料,其中:分解餐厨垃圾的复合菌体包括纤维素降解菌10~15份,淀粉降解菌15~30份,蛋白质降解菌15~20份,油脂降解菌15~20份,枯草芽孢杆菌10~15份,铜绿假单胞菌5~15份;固体发酵辅料配比为麸皮50~60kg、豆粕15~20kg、硫酸镁0.4~0.6kg、磷酸二氢钾0.4~0.6kg、磷酸氢二钠0.1~0.2kg、葡萄糖8~10kg;该分解餐厨垃圾的复合菌体接种固体发酵辅料时接种量为0.8%~1%,经固体发酵得到该微生物复合菌剂。
该复合微生物菌剂,不仅对油脂、蛋白、纤维类物质具有良好的分解效果,而且可以耐受一定浓度的盐分。
最优时,降解率可达到90%以上。
技术要求1.一种微生物复合菌剂,所述微生物复合菌剂由分解餐厨垃圾的复合菌体和固体发酵辅料制备而来,其中,所述分解餐厨垃圾的复合菌体包括纤维素降解菌10~15份,淀粉降解菌15~30份,蛋白质降解菌15~20份,油脂降解菌15~20份,枯草芽孢杆菌10~15份,铜绿假单胞菌5~15份;所述固体发酵辅料配比为麸皮50~60kg、豆粕15~20kg、硫酸镁0.4~0.6kg、磷酸二氢钾0.4~0.6kg、磷酸氢二钠0.1~0.2kg、葡萄糖8~10kg;所述分解餐厨垃圾的复合菌体接种所述固体发酵辅料时接种量为体积重量比0.8%~1%;其中,所述纤维素降解菌为CICC23686,所述淀粉降解菌为产淀粉酶枯草芽孢杆菌CICC10066,所述蛋白质降解菌为产蛋白酶枯草芽孢杆菌CICC10071,所述油脂降解菌为产脂肪酶地衣芽孢杆菌CICC21085,所述枯草芽孢杆菌为枯草芽孢杆菌CICC10210,所述铜绿假单胞菌为铜绿假单胞菌CICC21100。
2.一种权利要求1所述微生物复合菌剂的制备方法,所述方法包括:(1)分别培养所述纤维素降解菌,淀粉降解菌,蛋白质降解菌,油脂降解菌,枯草芽孢杆菌,铜绿假单胞菌,其中,所述纤维素降解菌为CICC23686,所述淀粉降解菌为产淀粉酶枯草芽孢杆菌CICC10066,所述蛋白质降解菌为产蛋白酶枯草芽孢杆菌CICC10071,所述油脂降解菌为产脂肪酶地衣芽孢杆菌CICC21085,所述枯草芽孢杆菌为枯草芽孢杆菌CICC10210,所述铜绿假单胞菌为铜绿假单胞菌CICC21100;(2)按所述比例混合所述培养的纤维素降解菌,淀粉降解菌,蛋白质降解菌,油脂降解菌,枯草芽孢杆菌,铜绿假单胞菌;(3)将步骤(2)中所述混合后的复合菌体加入固体发酵辅料中,经固体发酵,制得所述微生物复合菌剂。
菌复合微生态制剂的制备工艺及免疫功能研究

菌复合微生态制剂的制备工艺及免疫功能研究一、摘要本研究致力于开发和优化一种具有显著免疫调节作用的复合微生态制剂,该制剂结合了益生菌、益生元和合生元等多种微生物成分。
通过一系列体外和动物实验,我们深入探讨了该复合微生态制剂的制备工艺、免疫调节作用及其可能的作用机制。
在实验室条件下,我们成功地筛选并优化了微生物菌种组合和培养条件,以确保制剂的高效性和稳定性。
我们通过体内实验评估了该复合微生态制剂对免疫系统的改善效果,发现其能显著增强机体免疫功能,包括提高免疫细胞的活性、促进免疫因子的产生以及调节免疫细胞的生长和分化。
我们还对复合微生态制剂的安全性进行了评估,确认了其在正常使用剂量下的安全性。
研究结果表明,该复合微生态制剂具有良好的耐受性、稳定的生理活性和显著的免疫调节作用,为开发一种新型的免疫增强剂提供了有力支持。
相关结果已发表在国内外知名学术期刊上,并引起了广泛关注。
1. 微生态制剂简介微生态制剂,又称微生物发酵制剂,是一类由微生物、植物或动物或其代谢产物制成的生物活性制剂。
它们通过调节机体内的微生态平衡,提高动物机体的免疫力和抗病能力,促进生长和健康。
在兽医学领域,微生态制剂得到了广泛的研究和应用。
它们可以用于预防和治疗多种畜禽疾病,提高饲料利用率,降低养殖成本,保护生态环境。
随着研究的深入,微生态制剂的功能不断完善,从最初的益生菌补充剂逐渐发展成为具有调节肠道菌群、增强免疫功能、抑制有害菌生长等多种功效的综合制剂。
这些制剂不仅对动物的健康有益,而且为畜牧业的可持续发展提供了有力支持。
2. 菌复合微生态制剂的背景和意义随着微生物技术的日新月异,人们对微生态制剂的认识逐渐深入。
菌复合微生态制剂作为一种新型的生物制剂,在调节肠道菌群平衡、增强机体免疫力等方面展现出了显著的应用前景。
在现实生活中,由于饮食结构的变化、环境条件的变迁以及抗生素等药物的广泛应用,人体肠道菌群平衡受到了一定程度的破坏。
这种失衡可能导致多种消化系统疾病的发生,如腹泻、便秘等。
微生物菌剂生产工艺详细

2.5-3.5%
2mg/l
2mg/l
6.8-7.2
3.3主体发酵阶段操作和参数控制
3.2.3.1最佳装液量为罐体容积的50%-75%;最佳接种量实际装液量的1%-5%;发酵温度控制在25℃-35℃;pH控制在6.8-7.2;搅拌转速180-200r/min。转速过快会对菌丝体产生破坏,转速过慢易产生发酵泡沫,而且会因为溶解氧不足而影响微生物的生长繁殖。
4发酵工作
由各生产岗位负责人按生产周期实施菌种活化、种子培养及主体发酵过程、分离纯化、干燥等流程。
6包装
将发酵生产线生产的粉剂、液体产品进行定量包装。包装过程需要保持环境的洁净和无菌,并且要按照规定的包装标准进行操作。
7储运
完成包装后的生物有机肥送至成品库并由送货人和库管分别签字确认成品数量,每批次产品单独存放,填写批次产品档案。
10记录和报告
在整个车间操作流程中,需要及时记录各项操作的相关数据和信息,包括菌种培养情况、发酵过程参数、质量检测结果等。
二、车间生产工艺流程
1生产车间设备准备工作
1.1车间环境准备
1.1.1温度控制:车间温度应保持在适宜微生物生长的范围内,通常为20-30摄氏度。
1.1.2湿度控制:车间湿度应保持在适宜微生物生长的范围内,通常为50-70%。
5.2包装密封:包装后进行密封操作,避免微生物菌剂受潮变质。
5.3存储条件:根据产品要求,选择适宜的存储条件,避免产品失效。5.4质量检验
5.4.1外观检查:对包装后的微生物菌剂进行外观检查,确保产品无异常。
5.4.2活菌数检测:进行活菌数检测,确保微生物菌剂活性符合标准。
5.4.3产品检测:对微生物菌剂产品进行综合检测,包括微生物成分、杂质等指标,确保产品质量合格。
一种复合菌剂及其制备方法和应用
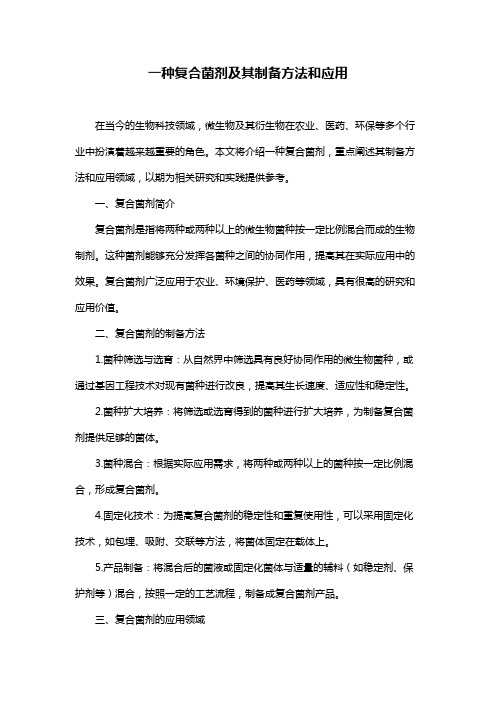
一种复合菌剂及其制备方法和应用在当今的生物科技领域,微生物及其衍生物在农业、医药、环保等多个行业中扮演着越来越重要的角色。
本文将介绍一种复合菌剂,重点阐述其制备方法和应用领域,以期为相关研究和实践提供参考。
一、复合菌剂简介复合菌剂是指将两种或两种以上的微生物菌种按一定比例混合而成的生物制剂。
这种菌剂能够充分发挥各菌种之间的协同作用,提高其在实际应用中的效果。
复合菌剂广泛应用于农业、环境保护、医药等领域,具有很高的研究和应用价值。
二、复合菌剂的制备方法1.菌种筛选与选育:从自然界中筛选具有良好协同作用的微生物菌种,或通过基因工程技术对现有菌种进行改良,提高其生长速度、适应性和稳定性。
2.菌种扩大培养:将筛选或选育得到的菌种进行扩大培养,为制备复合菌剂提供足够的菌体。
3.菌种混合:根据实际应用需求,将两种或两种以上的菌种按一定比例混合,形成复合菌剂。
4.固定化技术:为提高复合菌剂的稳定性和重复使用性,可以采用固定化技术,如包埋、吸附、交联等方法,将菌体固定在载体上。
5.产品制备:将混合后的菌液或固定化菌体与适量的辅料(如稳定剂、保护剂等)混合,按照一定的工艺流程,制备成复合菌剂产品。
三、复合菌剂的应用领域1.农业:复合菌剂在农业领域具有广泛的应用,如土壤改良、生物肥料、生物农药等。
通过提高土壤肥力、防治病虫害、促进作物生长等方面,实现农业可持续发展。
2.环境保护:复合菌剂在环境保护领域主要用于污水处理、生物修复等。
通过降解有机污染物、去除重金属离子等作用,改善环境质量。
3.医药:复合菌剂在医药领域具有一定的应用潜力,如制备微生态制剂、治疗肠道菌群失调等。
4.食品工业:复合菌剂可用于发酵食品的生产,如酸奶、泡菜等。
通过调节菌群结构,提高食品的营养价值和口感。
总结:复合菌剂作为一种具有广泛应用前景的生物制剂,其制备方法和应用领域的研究具有重要意义。
复合菌剂的制备

复合菌剂的制备复合菌剂(Compound microbial agents)是一种集多种菌种于一体的微生物制剂,它可以同时具有多种生理作用和促进植物生长的效果。
它可以促进土壤新陈代谢,增加土壤肥力和植物生长的营养素水平,同时还可以抑制土壤病原微生物和有害生物的生长,提高植物的免疫力。
本文将介绍复合菌剂的制备过程。
一、菌种的选取制备复合菌剂的第一步是选取菌种。
一般来说,复合菌剂应包含多种性能良好的微生物,例如产酶菌、氮固定菌、磷解菌、铁螯合菌等,而这些菌株应具有高效、广谱、安全与稳定等特点。
二、制备主菌种制备复合菌剂的第二步是制备主菌种。
它通常指生物活性高、生长速度快、菌量多的微生物,可采用流动培养方式进行制备。
流动培养方式通常采取发酵罐或滚筒式发酵设备,通过将发酵罐或滚筒内部通过外层水环境不断流动,使菌体充分接触营养物质,从而使菌体生长繁殖。
主菌种在发酵过程中要对发酵条件进行控制,如温度、酸碱度、氧气含量、营养物浓度等,以达到最佳生长状态。
三、筛选菌种制备复合菌剂的第三步是筛选菌种。
做法主要是将颇有活性的发酵菌种通过筛子或压缩机进行筛选,然后采用菌株定植方法进行培养,获得隔离的纯菌株。
通过纯菌株的检测和鉴定,筛选出具有产酶、氮固定、磷解、铁螯合等基本功能的菌株,以便在接下来的制剂工艺中进行混合,以达到最佳的增产效果。
四、制剂混合制备复合菌剂的第四步是制剂混合。
可将筛选出的多种菌株按比例混合,在一定时间内进行培养,以获得充分的联合效应。
制剂培养过程中还应注意典型细菌的限制因素,如养分匮乏、高温、驱杀物等,以免影响微生物复合菌剂的正常发酵过程。
五、沉淀和包装制备复合菌剂的第五步是沉淀和包装。
在减速离心机或超速离心机上,以3,000-5,000转/分离去除未完全分离的半固体发酵物质。
制剂的沉淀物通过灭菌、真空干燥等方式处理后,即可进行包装,并在包材防潮性较好的密闭条件下进行保存。
综上所述,复合菌剂的制备需要经历菌种的选取、制备主菌种、筛选菌种、制剂混合、沉淀和包装等多个步骤。
- 1、下载文档前请自行甄别文档内容的完整性,平台不提供额外的编辑、内容补充、找答案等附加服务。
- 2、"仅部分预览"的文档,不可在线预览部分如存在完整性等问题,可反馈申请退款(可完整预览的文档不适用该条件!)。
- 3、如文档侵犯您的权益,请联系客服反馈,我们会尽快为您处理(人工客服工作时间:9:00-18:30)。
一种微生物复合菌剂的生产工艺流程及设计要求(附简图)一.生产前的准备工作(1)生产用菌种的鉴定:主要包括纯度鉴定,生产性能的检查,有无杂菌污染。
还有就是菌种的活性,重要特性有无退化等。
(2)如菌种已发生功能性改变或被杂菌污染,还需要进行菌种的纯化或或复壮。
(3)其次在规模生产之前,还要通过实验室中试,确定该菌群的最适生长温度,PH,发酵培养基的最适成分与比例;生长曲线的绘制与最适培养时间的确定。
我们一般选取对数生长期的菌体(丝)做为生产发酵用的菌种。
最佳接种量与装液量的控制。
二.实验室菌种的活化与种子培养阶段:(1)将冷冻保藏管中的菌种在斜面中活化(37℃ 24h),并在平板中进行纯化(37℃ 24h)。
最终得到斜面菌种或菌种斜面。
(2)摇瓶培养阶段: 取一环纯化后的的菌种,接入装量为20mL种子培养基的250mL三角瓶中,置于180r/min中摇床中培养 (37℃ 18h)。
分别取1mL的种子液 ,接入五个盛有20mL发酵培养基的250 mL 三角瓶中。
置于180 r/ min摇床中培养(37℃ 24h)。
接种量为三角瓶实际培养基装量的4-5%.PH控制在7.0-7.5之间。
培养基组成见下表:(注;1ppm=1mg/l)三.生产车间多级种子罐发酵阶段:工艺流程工艺条件中控121℃~125℃0.103MPa~0.168 MPa0.5h~1.0h加料体积50%~75%,实际为60%PH6.5~7.5精密试纸或PH计121℃~125℃0.103MPa~0.168 MPa0.5h~1.0h25℃~35℃常压物料量的0.5-5%.实际接种量为1%25℃~35℃镜检:24~36h 菌体的形态、密度芽孢形成率≧80%搅拌转速:180r/min二级种子罐重复上述操作和参数控制其中,由摇瓶菌种向一级种子罐的接种量,控制在一级种子罐实际装料量的0.5%-5.0%;PH控制在6.5-7.5;发酵温度控制在25℃~35℃;装料量控制在种子罐公称容积的60%左右。
搅拌转速控制为180r/min.二级种子罐的具体工艺操作和参数控制和一级种子罐大体相同。
二级种子罐培养基成分应尽可能的接近主体发酵罐培养基成分。
通过上述二级种子罐发酵培养,我们大致可以得到450L的发酵种子液。
(计算如下:0.6*0.01*V=0.225L由此可得V=37.5L即通过一级种子发酵,我们可以得到22.5L的发酵菌体或菌丝。
二级种子罐的接种量为5%。
即0.6*0.05*V=22.5L)即V=750L.即通过二级种子发酵,我们大致可以得到450L的二级种子发酵液。
二级种子罐培养基成分如下表四.主体发酵阶段(1)发酵罐主要部件的设计与选型(具体设计部分见附页)主要部件包括:罐体,搅拌器,联轴器,轴承,轴封,挡板,空气分布器,换热装置,传动装置,消泡器,人孔试镜,以及管路等。
(2)通过实验我们可以知道:最佳装液量为(50%-75%)罐体公尺容积;最佳接种量(1%-5%)实际装液量;发酵温度控制在25℃~35℃;PH控制在6.8-7.2;搅拌转速180-200r/min.转速过快会对菌丝体产生破坏,转速过慢易产生发酵泡沫,而且会因为溶解氧不足而影响微生物的生长繁殖。
(3)具体发酵时间和发酵终点的确定,要通过镜检来观察微生物菌体的形态,密度,以及芽孢形成率≧80%。
最终来确定发酵时间和发酵终点。
我们一般选取对数生长末期的菌体菌丝做为发酵终点。
因为此时微生物代谢活性最高,菌体数目最多。
(4)主体发酵罐培养基成分及比例:(5)主体发酵罐操作工艺流程框图50%~75%PH6.5~7.5精密试纸或PH计℃~125℃25℃~35℃常压25℃~35℃镜检:24~36h 菌体的形态、密度芽孢形成率≧80%常温常压液态菌剂固形物含量10~20% 附页部分一。
复合菌剂生产工艺流程简图二。
发酵罐主体部件的设计发酵罐的种类很多,但是由于其他类型发酵罐应用的产品范围较窄,其流行程度远不如机械搅拌发酵罐,约92%的发酵工厂在使用机械搅拌发酵罐。
它的主要部件包括:罐体,搅拌器,联轴器,轴承,轴封,挡板,空气分布器,换热装置,传动装置,消泡器,人孔试镜,以及管路等。
(一)几何尺寸1.罐体计算:设计月生产量270吨,则日平均产量为9吨。
设计有效装液量为罐体公称容积的60%。
则可知V=15000L一般H/D=2.5较好,现在发展趋势是H/D 越来越小,已达1.8左右。
现设计H/D=2(其中H 罐体高度,D 为发酵罐内径),则由22215.04)]61(2[4D H D D h H D V b +≈++=ππ;H/D=2.可知罐体高度H=4m;发酵罐内径D=2m 。
罐体各部分材料多采用不锈钢,如1Cr18Ni9Ti,0Cr18Ni9,或瑞典316L 。
罐体必须能承受发酵工作时和灭菌时的工作压力和温度。
通常要求耐受130度和0.25MPa 的绝压。
2、搅拌器直径和几何尺寸高径比:对于档数:通用罐D/D 1=3,只能适合罐容积不太大的场合;当罐较大时,D/D 1=3-4。
根据需要,现设计采用圆盘涡轮式搅拌器。
搅拌器叶轮直径D1=1/3D=2/3m 。
3、封头:采用椭圆形或碟形封头,当V <5m 3时,封头与罐体间采用法兰连接;当V >5m 3时,封头与罐体间采用焊接;4、挡板:挡板的作用是防止液面中央产生旋涡,促使液体激烈翻动,提高溶解氧。
挡板宽度为(0.1-0.12)D 。
当满足全挡板条件时,增加罐内附件,轴功率不变。
WZ/D=0.5 即:(0.1-0.12)Z=0.5 即挡板宽度W=0.2m5、管口位置:人孔:为了便于操作和维修,封头上的人孔离操作层高度在0.7m左右,大小为500×450cm ;封头上其它管口,在满足工艺的同时应方便操作。
检测点:在下搅拌与第二档搅拌之间。
空气管:可开在封头上,也可开在罐身上。
取样口:开在罐身上。
冷却水管口:夹套冷却,冷却水进口在罐底,出口在罐身上部;冷却管冷却,进出口多在上部。
物料出口:开在罐底,稍微偏离罐底中心,也可开在罐身或罐顶,由一根管插入接近罐底最底处。
补料管:消泡、流加糖从罐顶加入;补氨水、液氨从空气管道加入。
消泡电极:接口在罐顶封头上。
6、罐装料容积的计算公称容积:罐身部分和底封头的容积之和(与贮罐相区别)。
V=V1+V2=π·D2(H0+h a+D/6)/4(h a可忽略不计)罐实际装料量:V0=V ·η(η=0.6-0.85)圆筒部分装料高度:H L=4(V ·η–V封)/ πD2液柱高度:H= H L + h a+h b7、空气分布装置(1) 单孔管:布置于罐底,结构简单,开口向下式可消除罐底固形物积淀,但对封头冲蚀严重;开口向上式对罐底物料混合不好;(2) 多孔环管:在环形管底部钻有许多小孔,气体分布比较均匀,但易使物料堵塞小孔,引起灭菌不彻底;(3) 环形多支管:在环形管底部设置4-6根“L”型支管,开口均朝发酵罐中心线,结构简单.但对罐底沉积物的清除往往不彻底。
(4)一般在发酵工业中通常采用单管空气分布器。
空气分布器在搅拌器下方的罐底中间位置,管口向下,空气直接通入发酵罐的底部。
管口与罐底距离为40mm,管径可按空气流速20m/s左右计算。
(二) 换热装置(1)换热方式:1、夹套换热:应用于V<20m3,结构简单,死角少,但壁厚,降温效果差。
加导流板可增大传热系数。
2、罐内竖式蛇管换热:传热系数高,但弯曲部位易蚀穿。
3、罐内竖式列管换热:适用于水源充足的地方,传热系数低于蛇管,用水量大。
4、罐外半圆管为主,罐内竖式蛇管补偿或板式换热器补偿。
可增大罐内有效容积,减少死角,此为将来发展趋势。
除以上换热方式外,还可采用安装在罐外的板式或螺旋板式换热器进行换热。
(2)发酵过程热量计算通常以一年中最热的半个月中每小时放出的热量作为设计冷却面积的根据。
1、通过冷却水带走的热量进行计算测定冷却水的流量及进出口的温度,按公式计算:Q最大=4.186WC(t2-t1)/V2、通过发酵液温度升高进行计算在最热季节,选择产热量最大最快的时刻,先控制温度恒定,关闭冷却水,测定发酵液在半小时内升高的温度,由公式计算:Q最大=2×4.186(GCt+G1C1t)/V3、通过生物合成热进行计算:Q总=Q发+Q搅-Q汽Q发=Q呼+Q代Q呼=15659W呼(KJ/h)Q代=4857W代(KJ/h)Q搅=4.186×860P (KJ/h)Q汽=4.186G(I出-I进) (KJ/h)W —单位时间耗糖量(kg/h ) P —搅拌功率(KW ) I —空气的热焓(KJ/kg ) (4) 通过燃烧热进行计算: Q 总=∑Q 作用物燃烧-∑Q 产物燃烧 (三)安全生产 ( 1)壁厚的设计:采用夹套的发酵罐,按外压容器进行壁厚计算: S= []2PDC P σϕ+-封头壁厚: S= S=[]P 20.5K DgCPϕσ+-设(2)死角和泄漏的消除1、罐体及封头内壁加工应光滑,焊接时采用双面焊,内外焊缝应打磨光滑;2、流加、接种及取样管道应能单独灭菌;3、排污管和排气管应独立排空;4、应尽量减少罐内的附件,减少死角;5、管口连接尽量采用焊接或法兰连接;6、与罐直接相连的阀门采用抗生素截止阀,在阀门上安装排汽考克,保证阀门能彻底灭菌,或隔膜阀;7、发酵过程保持正压,防止微生物渗入;8、冷却水管采用不锈钢,防止腐蚀穿孔;9、搅拌系统轴密封采用机械密封为好;(3)消泡装置泡沫形成的因素有:通气和搅拌、培养基成分、菌体自溶。
泡沫的危害:1、减少发酵罐有效容积25-30%;2、造成大量发酵液逃溢;3、渗漏后易造成染菌;4、影响通气和搅拌的效果;5、妨碍微生物的呼吸,使代谢不正常,导致菌体自溶;常用消泡方法有化学消泡和机械消泡:化学消泡:流加泡敌消除泡沫。
机械消泡:利用机械消泡装置来打碎、分离泡沫,常用的装置有:耙式消泡器、离心式消泡器、刮板式消器、射流消泡器、碟片式消泡器等。
消泡装置给罐内带来了死角,同时还消耗能量,不如化学消泡效果好,若消泡剂对后处理影响较小,可单用化学消泡。
常用的化学消泡剂是天然油脂类和聚醚类物质。
(四)搅拌系统搅拌系统由轴、搅拌桨、联轴器、轴密封、减速机、电机、轴承等组成。
1、搅拌桨:发酵工程中常用的是涡轮搅拌桨,属径向搅拌器,分平叶、弯叶、箭叶,叶片数为3-8,常用的是六叶。
径向混合:平叶>弯叶>箭叶轴向混合:平叶<弯叶<箭叶功率消耗:平叶>弯叶>箭叶由于涡轮搅拌桨功率消耗较大,同时剪切作用对微生物的损伤也大,现在对轴向流搅拌桨的研究正在展开,如:螺旋桨搅拌桨和翼型搅拌桨。
由于轴向流搅拌桨的混合效果差于径向流搅拌桨,容易在罐内造成死区,气泡分散也不好,单纯使用轴向流搅拌桨的情况不多。