etching 蚀刻概论
ETCH(PCB蚀刻培训教材)解析

膜不净;药水浓度高,会导致板面氧化。
褪膜段喷嘴要及时清洗,防止碎片堵塞喷嘴,
影响褪膜质量
二.碱性蚀刻 1.工艺流程 褪膜 蚀刻 新液洗 褪锡
(整孔)
注:整孔工序仅适用于沉金制板
2.工艺原理 -褪膜
定义:用褪菲林液将线路板面上盖住的菲林褪去,露 出未经线路加工的铜面. 经电镀工序后的干膜在碱性褪膜液下溶解或部分成 片状脱落,我司使用的是3% 0.5%氢氧化钠溶液.
水池效应
在蚀刻过程中,线路板水平通过蚀刻机时, 因重力作用在板上面新鲜药液被积水阻挠,无 法有效和铜面反应,称之水池效应。而下面 则无此现象。
蚀刻因子
蚀刻液在蚀刻过程中,不仅向下而且对左右各 方向都产生蚀刻作用,侧蚀是不可避免的。侧蚀宽 度与蚀刻深度之比称之为蚀刻因子。
A 铜线路 B D C
抗蚀层
原理:
CO3-2 + Resist COOH
HCO3- + Resist COO-
CO3-2 主要为Na2CO3 或K2CO3 Resist TOOH为干膜及油墨中反应官能基团 利用CO3-2与阻剂中羧基(COOH)进行酸碱中和反应, 形成COO-和H CO3- ,使阻剂形成阴离子团而剥离。
-蚀刻
³ ° å å » ú × Ô ¶ ¯ Ó Ò ¼ © ¸ × ´ ¿ Ê Ì » ú
400(800) 500X2
Ê Ä Í ¤
480(800)
Na2CO3 ý Å ³ Ý ¼ Á Cu2+± È Ö Ø HCl « Ñ Ë õ Ë ® H2O2 NaOH ý Å ³ Ý ¼ Á
3.2kg 640ml(640ml)
¸× ± ¢
冲板、褪膜、褪菲林换药和补药标准
ETCH 蚀刻

ETCH 蚀刻在集成电路的制程中,常需要将整个电路图案定义出来,其制造程序通常是先长出或盖上一层所需要之薄膜,再利用微影技术在这层薄膜上,以光阻定义出所欲制造之电路图案,再利用化学或物理方式将不需要之部分去除,此种去除步骤便称为蚀刻(ETCH)一般蚀刻可分为湿性蚀刻(WET ETCH)及干性蚀刻(DRY ETCH)两种。
所谓干性蚀刻乃是利用化学品(通常是盐酸)与所欲蚀刻之薄膜起化学反应,产生气体或可溶性生成物,达到图案定义之目的。
而所谓干蚀刻,则是利用干蚀刻机台产生电浆,将所欲蚀刻之薄膜反映产生气体由PUMP抽走,达到图案定义之目的。
ISOTROPIC ETCHING 等向性蚀刻在蚀刻反应中,除了纵向反应发生外,横向反应亦同时发生,此总蚀刻即称之为等向性蚀刻。
一般化学湿蚀刻多发生此种现象。
干式蚀刻,其实刻后的横截面具有异向性蚀刻特性(Anisotropic),即可得到较陡的图形。
PLASMA ETCHING 电浆蚀刻1.定义:在干蚀刻技术中,一班多采用电浆蚀刻与活性离子蚀刻,通常电浆蚀刻使用较高之压力(大于200mT)及较小之RF功率,当芯片浸在电浆之中,暴露在电将之表面层原子或分子与电浆中之活性原子接触并发生反应形成气态生成物而离开晶面造成蚀刻,此类蚀刻即称之为电浆蚀刻。
所谓电浆极为气体分子在一电场中被游离成离子(正、负电荷)、电子及中性基(Radical)等,在纯化学反应中,吾人取中性基为蚀刻因子,在R.I.E时,取活性离子作为中性因子。
REACTIVE ION ETCHING(R.I.E.)活性离子蚀刻1. 定义:在电浆蚀刻时,电浆里包含了活性原子、活性离子(正离子)及电子,当压力较低(小于100mT)且气体两端所加之电压够高时,活性离子即被迅速加速冲向电极上之芯片,而撞击晶面上暴露在电浆中的表层,将表层之原子击出,再与活性原子反应因而造成蚀刻,此类之蚀刻即称之为活性离子蚀刻。
目前我们已有的R.I.E蚀刻机台为8110、8130、8330等。
蚀刻详解
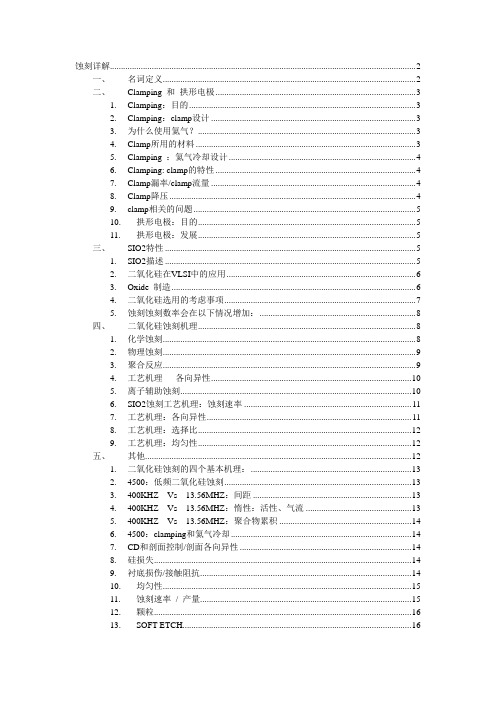
蚀刻详解 (2)一、名词定义 (2)二、Clamping 和拱形电极 (3)1. Clamping:目的 (3)2. Clamping:clamp设计 (3)3. 为什么使用氦气? (3)4. Clamp所用的材料 (3)5. Clamping :氦气冷却设计 (4)6. Clamping: clamp的特性 (4)7. Clamp漏率/clamp流量 (4)8. Clamp降压 (4)9. clamp相关的问题 (5)10. 拱形电极:目的 (5)11. 拱形电极:发展 (5)三、SIO2特性 (5)1. SIO2描述 (5)2. 二氧化硅在VLSI中的应用 (6)3. Oxide 制造 (6)4. 二氧化硅选用的考虑事项 (7)5. 蚀刻蚀刻数率会在以下情况增加: (8)四、二氧化硅蚀刻机理 (8)1. 化学蚀刻 (8)2. 物理蚀刻 (9)3. 聚合反应 (9)4. 工艺机理各向异性 (10)5. 离子辅助蚀刻 (10)6. SIO2蚀刻工艺机理:蚀刻速率 (11)7. 工艺机理:各向异性 (11)8. 工艺机理:选择比 (12)9. 工艺机理:均匀性 (12)五、其他 (12)1. 二氧化硅蚀刻的四个基本机理: (13)2. 4500:低频二氧化硅蚀刻 (13)3. 400KHZ Vs 13.56MHZ:间距 (13)4. 400KHZ Vs 13.56MHZ:惰性:活性、气流 (13)5. 400KHZ Vs 13.56MHZ:聚合物累积 (14)6. 4500:clamping和氦气冷却 (14)7. CD和剖面控制/剖面各向异性 (14)8. 硅损失 (14)9. 衬底损伤/接触阻抗 (14)10. 均匀性 (15)11. 蚀刻速率/ 产量 (15)12. 颗粒 (16)13. SOFT ETCH (16)蚀刻详解一、名词定义均匀性(Uniformity)-- 相对平均值的变化,常在描述蚀刻速率,CD和淀积物厚度时使用。
ETCHING技术

蚀刻(Etching)概念简介一. 前言:集成电路(IC)的制造流程,犹如一场精致细密的建筑结构施工,建筑师(Designer & Device Owner)将设计蓝图(LayOut)和施工流程(Process Flow)设计出来,经过工程部门(模块Module)制定施工法则(Setup Process)后,交由施工单位(制造部MFG)来执行建筑工事.空白的硅晶圆就像一块平整的大工地,经过不断的整地(平坦化;离子植入),灌浆混沙填土上钢架(薄膜沉积),再经过砌墙挖坑打洞筑沟(显影&蚀刻)等重复的制程(Process),一层一层堆栈而上,制作成拥有复杂结构和完善功能的集成电路.“晶圆”这块”工地”有多大呢? 这个超现代”工地”的大小尺吋演进,正代表着人类科技突飞猛进的新里程碑.从三吋晶圆到目前的十二吋晶圆,可用面积增加了16倍,在一个process cycle 后,晶粒产出量也提升了数十倍.基本上,一套Process flow约需经过数百个不同步骤(step),耗时一,二个月才得以完成.而模块(Module)工程师的任务就是负责开发(Setup),维护(Maintain)和改良(Improve)各个步骤.而蚀刻模块在这项工事中占有不可或缺的重要角色.本章将针对蚀刻制程作一简略介绍.二. 蚀刻技术概论:集成电路的制造需要在晶圆上做出极细微尺寸的图案(Pattern).而这些图案最主要的形成方式,乃是使用蚀刻(Etching)技术,将微影(Lithography)技术所产生的光阻图形,无论是线(Line),面(EtchBack)或是孔洞(Hole),以化学腐蚀反应(Chemical)的方式,或物理撞击(Physical)的方式,或上述两种方式的综合,忠实无误的移转到薄膜上,以定义出整个集成电路所需的复杂结构.下图是最基本的集成电路制作流程(Process Flow):a. 薄膜沉积(Film Deposition)b. 蚀刻制程(Etching)& 微影制程(Photo Lithography)2-1. 湿蚀刻(Wet Etching)与干蚀刻(Dry Etching):蚀刻方式主要分成湿蚀刻(Wet Etching)与干蚀刻(Dry Etching)两种方式.早期半导体制程是使用湿蚀刻的方法,也就是利用合适的化学溶液,腐蚀所要蚀刻的材质未被光阻覆盖的部分,并在完成蚀刻反应后,由溶液带走腐蚀物。
蚀刻技术
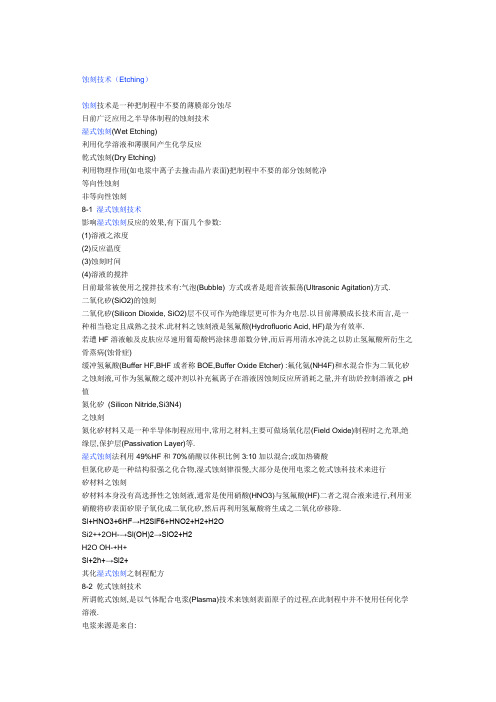
蚀刻技术(Etching)蚀刻技术是一种把制程中不要的薄膜部分蚀尽目前广泛应用之半导体制程的蚀刻技术湿式蚀刻(Wet Etching)利用化学溶液和薄膜间产生化学反应乾式蚀刻(Dry Etching)利用物理作用(如电浆中离子去撞击晶片表面)把制程中不要的部分蚀刻乾净等向性蚀刻非等向性蚀刻8-1 湿式蚀刻技术影响湿式蚀刻反应的效果,有下面几个参数:(1)溶液之浓度(2)反应温度(3)蚀刻时间(4)溶液的搅拌目前最常被使用之搅拌技术有:气泡(Bubble) 方式或者是超音波振荡(Ultrasonic Agitation)方式.二氧化矽(SiO2)的蚀刻二氧化矽(Silicon Dioxide, SiO2)层不仅可作为绝缘层更可作为介电层.以目前薄膜成长技术而言,是一种相当稳定且成熟之技术.此材料之蚀刻液是氢氟酸(Hydrofluoric Acid, HF)最为有效率.若遭HF溶液触及皮肤应尽速用葡萄酸钙涂抹患部数分钟,而后再用清水冲洗之以防止氢氟酸所衍生之骨蒸病(蚀骨症)缓冲氢氟酸(Buffer HF,BHF或者称BOE,Buffer Oxide Etcher) :氟化氨(NH4F)和水混合作为二氧化矽之蚀刻液,可作为氢氟酸之缓冲剂以补充氟离子在溶液因蚀刻反应所消耗之量,并有助於控制溶液之pH 值氮化矽(Silicon Nitride,Si3N4)之蚀刻氮化矽材料又是一种半导体制程应用中,常用之材料,主要可做场氧化层(Field Oxide)制程时之光罩,绝缘层,保护层(Passivation Layer)等.湿式蚀刻法利用49%HF和70%硝酸以体积比例3:10加以混合;或加热磷酸但氮化矽是一种结构很强之化合物,湿式蚀刻律很慢,大部分是使用电浆之乾式蚀科技术来进行矽材料之蚀刻矽材料本身没有高选择性之蚀刻液,通常是使用硝酸(HNO3)与氢氟酸(HF)二者之混合液来进行,利用亚硝酸将矽表面矽原子氧化成二氧化矽,然后再利用氢氟酸将生成之二氧化矽移除.Si+HNO3+6HF→H2SiF6+HNO2+H2+H2OSi2++2OH-→Si(OH)2→SiO2+H2H2O OH-+H+Si+2h+→Si2+其化湿式蚀刻之制程配方8-2 乾式蚀刻技术所谓乾式蚀刻,是以气体配合电浆(Plasma)技术来蚀刻表面原子的过程,在此制程中并不使用任何化学溶液.电浆来源是来自:(1)一个是带正电荷的离子(2)另外是带负电的电子团目前常用之电浆蚀刻技术有:1.活性离子蚀刻(Reactive Ion Etching, RIE).2.磁强化活性离子蚀刻(Magnetically Enhanced RIE, MERIE).3.活性离子蚀刻(Feactive Ion Beam Etching, RIBE).4.低电压及电密度之电子回旋共振(Electron Cyclotron Resonance, ECR).5.螺旋波(Helicoid Wave).6.螺旋共振器(Helicoid Resonator).7.感应耦合电浆(Inductively Coupled Plasma, ICP).电浆之基本性质电浆可视为离子化之气态,这些带正负电粒子藉著静电力之交互作用,而呈现出集体化行为(Collective Behavior)激发气体成离子化态之方式有二种方式:(1)直流电浆(DC Plasma)(2)射频交流电浆(AC Plasma) :(1)无电荷蓄积现象及(2)离子化之效果比DC方式来的强(3)反应腔真空度不必太高乾式蚀刻方法1. 电浆蚀刻技术:2. 反应性离子蚀刻技术(Reactive lon Etching, RIE)为半导体制程之主流(结合物理和化学去除薄膜之机构,具非等向性蚀刻优点和选择性蚀刻技术)有下列几种蚀刻机制:(1)非活性粒子的物理溅击作用.(2)活性粒子的物理溅击作用.(3)电浆之化学反应.(4)活性离子之化学反应.物理作用化学作用基本上,乾蚀刻依反应器对操作形态可分下面几种:1.电容耦合式电浆反应器:2.磁加强性反应式离子蚀刻法(Magnetically Enchanced RIE, MERIE):3.电子回旋共振蚀刻技术(Electron Cyclotron Resonance, ECR):4.螺旋波(Helicoin Wave)蚀刻技术:5.感应耦合电浆蚀刻技术(Inductively Coupled Plasma, ICP):电浆蚀刻之主要效应1. 氢气效应(Hydrogen Effect):CF4电浆是蚀刻Si ,SiO2最常用到之气体,二者之蚀刻率非常接近,若加入少量氢气, Si的蚀刻率随加入H2量增加而急剧下降,而SiO2之蚀刻率却缓慢下降.H2分解成自由基及离子,H自由基和F自由基结合成HF以降低F自由基浓度,而降低对Si蚀刻率Si + 4F SiF4SiO2 + 4F SiF4 + O22. 氧气效应(Oxygen Effect):CF4+O COF2+2F含氧的生成物消耗电浆内的碳原子,使F/C比例升高,因此CF4+O2的电浆对Si之蚀刻率比单纯以CF4快3. 选择性之蚀刻:控制电浆的气体贮组成,控制CF4内之H2和O2含量H(g)+F(g)→HF(g)4. 负载效应(Loading Effect):整体负载效应: 和所要蚀刻之基材面积有关,蚀刻率和晶片数成反比微负载效应(区域负载效应) :由於蚀刻活性种传输不平均所致5. 深宽比之外观效应(Aspect Ratio Dependent Etching, ARDE): 不同宽度的深沟所蚀刻的深度不尽相同,宽度较宽蚀刻后之深度较深6. 电浆蚀刻之天线效应(Antenna Effect):8-3 蚀刻技术未来走向乾式蚀刻技术之发展,在确保半导体制程线宽0.2μm以下扮演极为重要之角色,以目前所研发蚀刻技术之重点,不外乎在改善蚀刻机之非等向性,选择性与蚀刻率之问题.让电浆内离子密度和能量独立进行控制和调整以强化乾式蚀刻之非等向性,选择性与蚀刻率。
etching原理

Etching原理概述Etching(蚀刻)是一种通过化学反应去除材料表面的方法,通常用于制造微电子器件、集成电路和光学元件等领域。
本文将详细介绍Etching的原理及其在实际应用中的一些关键技术。
什么是EtchingEtching是指通过一系列化学反应将材料表面的一部分或全部物质去除的过程。
这一过程主要依靠一种叫作蚀刻剂的化学溶液或者气体对材料进行腐蚀,从而使材料发生化学变化并且减少其厚度或形状上的一些特征。
Etching广泛应用于半导体工艺、微加工以及一些高精度制造领域。
它可以精确控制材料的尺寸、形状和表面特性,为后续的工艺步骤提供了关键的基础。
Etching的原理Etching的原理主要涉及材料与蚀刻剂之间的化学反应。
常见的Etching方法有湿法Etching和干法Etching两种。
湿法Etching原理湿法Etching利用液体蚀刻剂与材料表面发生化学反应,实现材料的去除。
一般情况下,液体蚀刻剂由溶剂和蚀刻剂组成。
溶剂主要是一种能够稳定蚀刻剂的液体,而蚀刻剂则是导致材料发生化学反应的物质。
蚀刻剂可分为酸性和碱性两种类型,选择合适的蚀刻剂取决于需要蚀刻的材料以及所期望的蚀刻速率和精度。
湿法Etching的过程可以通过以下步骤概括: 1. 材料表面与液体蚀刻剂接触,形成蚀刻剂的保护层。
2. 蚀刻剂与材料表面发生反应,导致材料发生溶解或与蚀刻剂发生化学反应。
3. 被蚀刻的物质溶解或从材料表面去除。
4. 溶液中新的蚀刻剂取代被腐蚀的物质,继续进行蚀刻。
干法Etching原理干法Etching在低压、高温或者简单的干燥条件下使用气体蚀刻剂进行材料去除。
干法Etching的过程可以分为以下几个步骤: 1. 气体蚀刻剂通过化学反应生成反应物。
2. 反应物在材料表面发生吸附和反应。
3. 受到化学反应的影响,材料表面产生新的化学物种。
4. 这些化学物种通过反应或扩散离开材料表面,并被辅助气体带走。
Etching(刻蚀)

plate electrodes with overlapped “fingers”:
● DRIE process may produce deep trenches with θ ≈ 0 (i.e., near perfect vertical walls).
Wet etching
Dry etching
Dry etching involves the removal of substrate materials by gaseous etchants.
It is more a physical than chemical process.
3 dry etching techniques ● Ion etching.(离子刻蚀)
Dry etching
Working principle: ● The DRIE process provides thin films of a few micrometer protective coatings of special polymer on the sidewalls during the etching process. ● It involves the use of a high-density plasma source. ● The process allows alternating process of plasma (ion) etching of the substrate material and the deposition of etching- protective material on the sidewalls. ● Special polymers are frequently used for side-wall protective films.
Alkaline etching
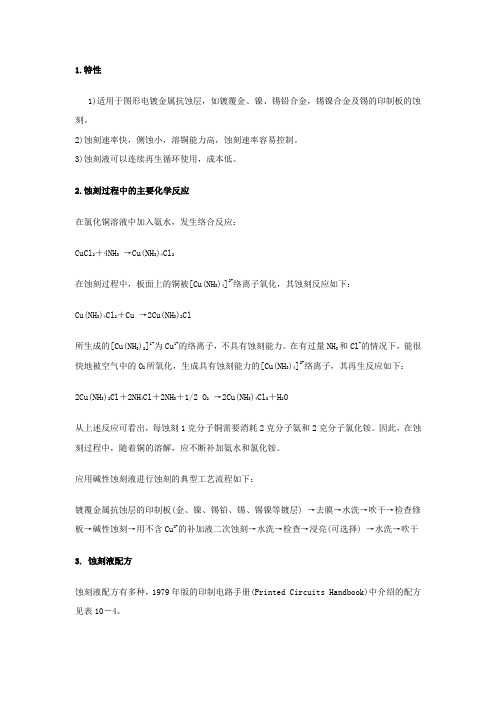
1.特性1)适用于图形电镀金属抗蚀层,如镀覆金、镍、锡铅合金,锡镍合金及锡的印制板的蚀刻。
2)蚀刻速率快,侧蚀小,溶铜能力高,蚀刻速率容易控制。
3)蚀刻液可以连续再生循环使用,成本低。
2.蚀刻过程中的主要化学反应在氯化铜溶液中加入氨水,发生络合反应:CuCl2+4NH3→Cu(NH3)4Cl2在蚀刻过程中,板面上的铜被[Cu(NH3)4]2+络离子氧化,其蚀刻反应如下:Cu(NH3)4Cl2+Cu →2Cu(NH3)2Cl所生成的[Cu(NH3)2]1+为Cu1+的络离子,不具有蚀刻能力。
在有过量NH3和Cl-的情况下,能很快地被空气中的O2所氧化,生成具有蚀刻能力的[Cu(NH3)4]2+络离子,其再生反应如下:2Cu(NH3)2Cl+2NH4Cl+2NH3+1/2 O2→2Cu(NH3)4Cl2+H2O从上述反应可看出,每蚀刻1克分子铜需要消耗2克分子氨和2克分子氯化铵。
因此,在蚀刻过程中,随着铜的溶解,应不断补加氨水和氯化铵。
应用碱性蚀刻液进行蚀刻的典型工艺流程如下:镀覆金属抗蚀层的印制板(金、镍、锡铅、锡、锡镍等镀层) →去膜→水洗→吹干→检查修板→碱性蚀刻→用不含Cu2+的补加液二次蚀刻→水洗→检查→浸亮(可选择) →水洗→吹干3. 蚀刻液配方蚀刻液配方有多种,1979年版的印制电路手册(Printed Circuits Handbook)中介绍的配方见表10-4。
表10-4 国外介绍的碱性蚀刻液配方国内目前大多采用下列配方:CuCl2·2H2O 100~150g/l 、NH4Cl 100g/l 、NH3·H2O 670~700ml/12配制后溶液PH值在9.6左右。
溶液中各组份的作用如下:NH3·H2O的作用是作为络合剂,使铜保持在溶液里。
NH4Cl的作用是能提高蚀刻速率、溶铜能力和溶液的稳定性。
(NH4)3PO4的作用是能保持抗蚀镀层及孔内清洁。
4.影响蚀刻速率的因素蚀刻液中的Cu2+的浓度、PH值、氯化铵浓度以及蚀刻液的温度对蚀刻速率均有影响。
半导体技术-蚀刻

蚀刻(ETCH)微影只是将光罩图案转移到光阻上,接下来利用这层光阻为罩幕(mask),以便对光阻下的薄膜或Si片进行选择性蚀刻或离子注入。
蚀刻即是利用化学反应或物理作用,把光阻上的图案转移到薄膜上。
蚀刻的机制,按发生顺序可概分为「反应物接近表面」、「表面氧化」、「表面反应」、「生成物离开表面」等过程。
所以整个蚀刻,包含反应物接近、生成物离开的扩散效应,以及化学反应两部分。
整个蚀刻的时间,等于是扩散与化学反应两部分所用时间的总和。
二者之中孰者所用时间较长,整个蚀刻快慢也卡在该者,故有「reaction limited」与「diffusion limited」两类蚀刻之分。
1.湿蚀刻最普遍、也是设备成本最低的蚀刻方法,主要有三方面因素影响蚀刻速率 (etching rate):蚀刻液浓度、蚀刻液温度、及搅拌 (stirring) 的有无。
定性而言,增加蚀刻温度与加入搅拌,均能有效提高蚀刻速率,但浓度影响则较不明确。
一个选用湿蚀刻配方的重要观念是「选择性」(selectivity),指进行蚀刻时,对被蚀物去除速度与连带对其他材质(如蚀刻掩膜「etching mask」或承载被加工薄膜基板「substrate 」) 的腐蚀速度之比值。
一个具有高选择性的蚀刻系统,应该只对被加工薄膜有腐蚀作用,而不伤及一旁蚀刻掩膜或其下的基板材料。
(1) 等向性蚀刻 (isotropic etching)大部分的湿蚀刻液均是等向性,换言之,对蚀刻接触点的任何方向腐蚀速度并无明显差异。
故一旦定义好蚀刻掩膜的图案,暴露出来的区域,便是往下腐蚀的所在;只要蚀刻配方具高选择性,便应当止于所该止之深度。
然而有鉴于任何被蚀薄膜皆有其厚度,当其被蚀出某深度时,蚀刻掩膜图案边缘的部位渐与蚀刻液接触,故蚀刻液也开始对蚀刻掩膜图案边缘的底部,进行蚀掏,这就是所谓的下切或侧向侵蚀现象(undercut)。
该现象造成的图案侧向误差与被蚀薄膜厚度同数量级,换言之,湿蚀刻技术因而无法应用在类似「次微米」线宽的精密制程技术!(2) 非等向性蚀刻 (anisotropic etching)湿蚀刻「选择性」观念,是以不同材料的受蚀快慢程度来说明。
电感耦合等离子体蚀刻原理
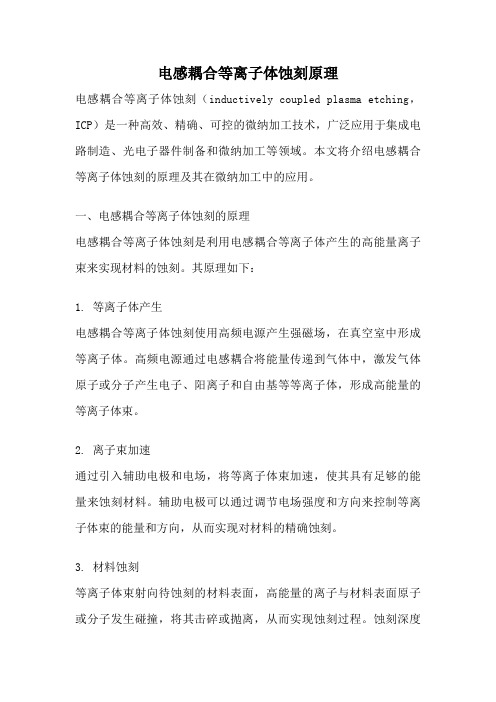
电感耦合等离子体蚀刻原理电感耦合等离子体蚀刻(inductively coupled plasma etching,ICP)是一种高效、精确、可控的微纳加工技术,广泛应用于集成电路制造、光电子器件制备和微纳加工等领域。
本文将介绍电感耦合等离子体蚀刻的原理及其在微纳加工中的应用。
一、电感耦合等离子体蚀刻的原理电感耦合等离子体蚀刻是利用电感耦合等离子体产生的高能量离子束来实现材料的蚀刻。
其原理如下:1. 等离子体产生电感耦合等离子体蚀刻使用高频电源产生强磁场,在真空室中形成等离子体。
高频电源通过电感耦合将能量传递到气体中,激发气体原子或分子产生电子、阳离子和自由基等等离子体,形成高能量的等离子体束。
2. 离子束加速通过引入辅助电极和电场,将等离子体束加速,使其具有足够的能量来蚀刻材料。
辅助电极可以通过调节电场强度和方向来控制等离子体束的能量和方向,从而实现对材料的精确蚀刻。
3. 材料蚀刻等离子体束射向待蚀刻的材料表面,高能量的离子与材料表面原子或分子发生碰撞,将其击碎或抛离,从而实现蚀刻过程。
蚀刻深度和形状可以通过控制离子束的能量、入射角度和蚀刻时间等参数来调节。
二、电感耦合等离子体蚀刻在微纳加工中的应用电感耦合等离子体蚀刻具有高精度、高选择性、高速度和低损伤等优点,因此广泛应用于微纳加工领域,主要包括以下几个方面的应用:1. 集成电路制造在集成电路制造中,电感耦合等离子体蚀刻被用于制备衬底材料、金属层、氧化物层和硅层等的精确蚀刻。
通过控制蚀刻参数和掩膜工艺,可以实现微米甚至纳米级别的线路、孔洞和结构的制备。
2. 光电子器件制备电感耦合等离子体蚀刻在光电子器件制备中的应用主要包括光纤、光波导、光栅和MEMS器件等的制备。
通过精确控制蚀刻参数,可以实现光子器件的精细加工和微纳结构的制备。
3. 微纳加工在微纳加工领域,电感耦合等离子体蚀刻被用于制备微流体芯片、微机械结构和纳米材料等。
通过控制蚀刻参数和掩膜工艺,可以实现微米和纳米级别的结构和器件的制备。
第八章 (2)刻蚀
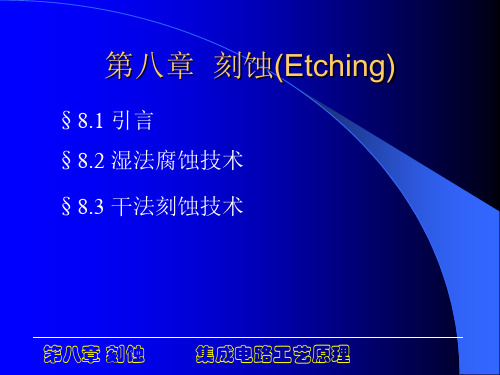
第八章 刻蚀
集成电路工艺原理
等离子体刻蚀设备
(a)筒式(Barrel Etchers)
• 纯化学反应 • 多孔屏蔽罩 使等离子体区域在罩和器壁 之间发生,靠 长寿命活性基扩散进入内层 与样品进行反应 • 优点:产量大,选择性好,没有辐照损伤 • 缺点:各向同性腐蚀,只适用于5um以上工艺,工艺参 数难控制,均匀性,重复性差 • 常用于光刻胶去胶和对Si3N4钝化层开窗口 第八章 刻蚀 集成电路工艺原理
第八章 刻蚀
集成电路工艺原理
第八章 刻蚀
集成电路工艺原理
湿法腐蚀的缺点
(1)湿法腐蚀需大量的腐蚀性化学试剂,对人体和环境 有害 在ULSI电路制造中,湿法腐蚀正被干法刻蚀所替代。 (2)湿法腐蚀需大量的化学试剂去冲洗腐蚀剂剩余物, 不经济 (3)干法腐蚀能达到高的分辨率,湿法腐蚀较差 (4)湿法腐蚀是各向同性,干法可以是各向异性
选择性S (Selectivity) 各项异性度A (Anisotropy) 掩膜版下刻蚀 (Undercut) Uniformity U
一个硅片或多个硅片或多批硅片上刻蚀 速率的变化 不同材料之间的刻蚀速率比
刻蚀的方向性 A=0, 各项同性;A=1, 各项异性 Measure of the lateral extent of the etch per side
CF4中添加少量O2可增加
对Si,SiO2和Si3N4的腐蚀速率
第八章 刻蚀
集成电路工艺原理
离子增强刻蚀-Ion Enhanced etching
无离子,XeF2对Si 不刻蚀;
纯Ar离子,对Si不 刻蚀; Ar离子和XeF2相互 作用,刻蚀速率很 快。
等离子体刻蚀的化学和物理过程并不是两 个相互独立的过程,而且相互有增强作用
蚀刻

开料---素材清洗---上油墨(涂布)---烘烤---曝光 (固化)--显影---描油---烘烤---蚀刻---去膜清洗(脱膜)---贴 保护膜---检验---包装
微蚀(溶液为碱)---溢流水洗---市水洗---酸洗---溢流水洗2---溢流水洗3-市水洗---吸干---强风吹---热风烘干 先在产品上涂上感光油,放入隧道炉;1号炉94度烘烤(温范围65度120度)---2号炉120度烘烤(温范围95度-120度)---3号炉120度烘烤 (温范围95度-120度)---4号炉120度烘烤(温范围95度-120度)---5号 炉88度烘烤(温范围80度-120度)---产品出来过程总时间5分钟。 先将菲林片(印有所需图案)放在产品上贴合,有曝光人员放入曝光 机的玻璃板上用特有的工具压平,再把产品推入机内(曝光温度根据 产品厚度而定,温度在30度属正的,但产品0.8以上,则曝光温度150 度) 曝光时间10秒
将产品放在显影海绵轮上,传送到显影机内,产品间隔5CM。显影温度在2540度(溶液为工业碳酸钠和水浓度在0.8%-1.5%),产品在传送轮上向前传动, 此过程到显影药水区为60秒,最后检查并放在待蚀刻放置区。待蚀刻之前由修 改人员把产品漏白点处用油默或油漆笔填补好,放入铁架里待蚀刻。 产品放入蚀刻机内过程5分钟(蚀刻溶液为三氯化铁CL) 蚀刻过的产品放入纯硝酸槽里1分钟30秒,出来再放入硝酸10%槽里1分钟,再用 清水冲洗干净,最后把产品放进清洗机温度在70+/-10度,浸泡时间控制在5-6 分钟后OK. 最后检验成品有无变形,水痕和手痕,确定为良品后包装。 不锈钢,不锈 铁,铜和铝 铝材:酸和铝反应快,尺寸不好管控。不锈钢:尺寸好管控 蚀刻的良率为95%,铝材在95% 3D的蚀刻油墨损耗比2D大,差异在涂布油墨耗损3D比2D 2-2.5倍 蚀刻的温度一般在32-37度 一般蚀刻的精度可控制在+/-0.1
蚀刻技术(Etching Technology)
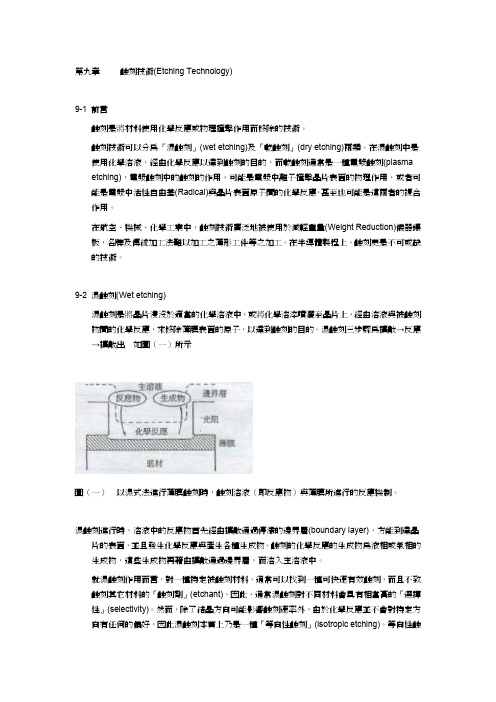
第九章蝕刻技術(Etching Technology)9-1 前言蝕刻是將材料使用化學反應或物理撞擊作用而移除的技術。
蝕刻技術可以分為『濕蝕刻』(wet etching)及『乾蝕刻』(dry etching)兩類。
在濕蝕刻中是使用化學溶液,經由化學反應以達到蝕刻的目的,而乾蝕刻通常是一種電漿蝕刻(plasma etching),電漿蝕刻中的蝕刻的作用,可能是電漿中離子撞擊晶片表面的物理作用,或者可能是電漿中活性自由基(Radical)與晶片表面原子間的化學反應,甚至也可能是這兩者的複合作用。
在航空、機械、化學工業中,蝕刻技術廣泛地被使用於減輕重量(Weight Reduction)儀器鑲板,名牌及傳統加工法難以加工之薄形工件等之加工。
在半導體製程上,蝕刻更是不可或缺的技術。
9-2 濕蝕刻(Wet etching)濕蝕刻是將晶片浸沒於適當的化學溶液中,或將化學溶淬噴灑至晶片上,經由溶液與被蝕刻物間的化學反應,來移除薄膜表面的原子,以達到蝕刻的目的。
濕蝕刻三步驟為擴散→反應→擴散出 如圖(一)所示圖(一) 以濕式法進行薄膜蝕刻時,蝕刻溶液(即反應物)與薄膜所進行的反應機制。
濕蝕刻進行時,溶液中的反應物首先經由擴散通過停滯的邊界層(boundary layer),方能到達晶片的表面,並且發生化學反應與產生各種生成物。
蝕刻的化學反應的生成物為液相或氣相的生成物,這些生成物再藉由擴散通過邊界層,而溶入主溶液中。
就濕蝕刻作用而言,對一種特定被蝕刻材料,通常可以找到一種可快速有效蝕刻,而且不致蝕刻其它材料的『蝕刻劑』(etchant),因此,通常濕蝕刻對不同材料會具有相當高的『選擇性』(selectivity)。
然而,除了結晶方向可能影響蝕刻速率外,由於化學反應並不會對特定方向有任何的偏好,因此濕蝕刻本質上乃是一種『等向性蝕刻』(isotropic etching)。
等向性蝕刻意味著,濕蝕刻不但會在縱向進行蝕刻,而且也會有橫向的蝕刻效果。
蚀刻
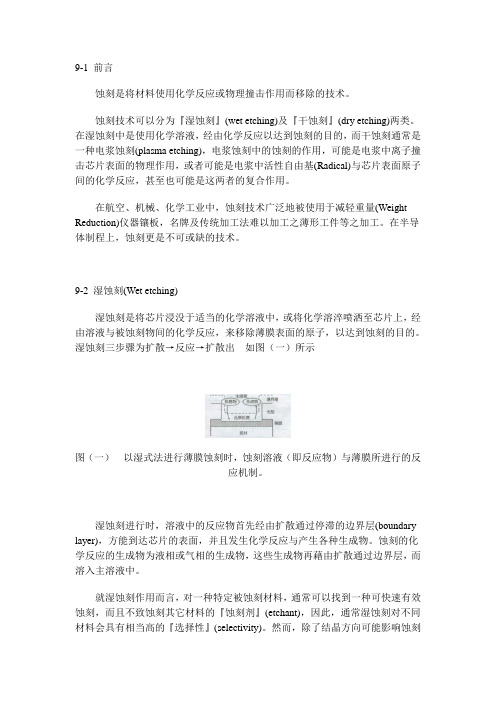
9-1 前言蚀刻是将材料使用化学反应或物理撞击作用而移除的技术。
蚀刻技术可以分为『湿蚀刻』(wet etching)及『干蚀刻』(dry etching)两类。
在湿蚀刻中是使用化学溶液,经由化学反应以达到蚀刻的目的,而干蚀刻通常是一种电浆蚀刻(plasma etching),电浆蚀刻中的蚀刻的作用,可能是电浆中离子撞击芯片表面的物理作用,或者可能是电浆中活性自由基(Radical)与芯片表面原子间的化学反应,甚至也可能是这两者的复合作用。
在航空、机械、化学工业中,蚀刻技术广泛地被使用于减轻重量(Weight Reduction)仪器镶板,名牌及传统加工法难以加工之薄形工件等之加工。
在半导体制程上,蚀刻更是不可或缺的技术。
9-2 湿蚀刻(Wet etching)湿蚀刻是将芯片浸没于适当的化学溶液中,或将化学溶淬喷洒至芯片上,经由溶液与被蚀刻物间的化学反应,来移除薄膜表面的原子,以达到蚀刻的目的。
湿蚀刻三步骤为扩散→反应→扩散出如图(一)所示图(一)以湿式法进行薄膜蚀刻时,蚀刻溶液(即反应物)与薄膜所进行的反应机制。
湿蚀刻进行时,溶液中的反应物首先经由扩散通过停滞的边界层(boundary layer),方能到达芯片的表面,并且发生化学反应与产生各种生成物。
蚀刻的化学反应的生成物为液相或气相的生成物,这些生成物再藉由扩散通过边界层,而溶入主溶液中。
就湿蚀刻作用而言,对一种特定被蚀刻材料,通常可以找到一种可快速有效蚀刻,而且不致蚀刻其它材料的『蚀刻剂』(etchant),因此,通常湿蚀刻对不同材料会具有相当高的『选择性』(selectivity)。
然而,除了结晶方向可能影响蚀刻速率外,由于化学反应并不会对特定方向有任何的偏好,因此湿蚀刻本质上乃是一种『等向性蚀刻』(isotropic etching)。
等向性蚀刻意味着,湿蚀刻不但会在纵向进行蚀刻,而且也会有横向的蚀刻效果。
横向蚀刻会导致所谓『底切』(undercut)的现象发生,使得图形无法精确转移至芯片,如图(二)所示。
光蚀刻加工

生產鈑金零件應用上,與傳統之沖壓技術比較,光蝕刻擁有以下之優點:
樣本製作生產:光刻工具之製作,比較一般之沖壓,工具成本廉宜,快捷,精確度更高。另光蝕工具較具彈性,在產品之設計需要更改時,更改光工具較更改傳統模具容易。因此,光刻工藝對鈑金樣本製作最適合不過。特別在高檔科技工業中,此環節之需料求特別高。
可光刻加工之材料種類:幾乎任何金屬及其合金皆可作光刻加工之材料,計有鋼材,不鏽鋼、黃銅、青銅、鈹、鎳、鎳合金、鉆合金、鋁合金、鎂合金、鈦合金、鎢、鉬、帶磁之合金、金、銀等。某些非金屬材料亦可光刻加工。
常用於不鏽鋼門、板,美化外觀或是電路板,手機MOTO V3按鍵即應用蝕刻方式加工。
適用各項金屬材質如不鏽鋼、鋁、銅等。
由於上述原因,蝕刻後之尺寸是跟影像尺寸略有些微差別,外圍尺寸縮而內圍尺寸擴大,內尖角位置是會變成小圓角,這些毛病是要經過矯正後方後達至預期之精密度,另外矯正尺寸變化亦可在預留圖案草稿中進行。當然,最重要因素還是倚靠累積經驗,才能控制準確精密度。
剝脫:黏膜剩餘渣宰經蝕刻後用適當溶劑擦洗。
清洗:工序至此大致上完成,再以水清洗。
十數年前,電腦技術尚未發達,製作光工具都是採用照相工程方法,將原稿用手倍數放大繪畫,再用倍數縮小攝影而成,此方法需時,及到某程度其準繩度便不可靠,故現時巳被棄用。
現在多採用電腦輔助設計繪圖(CAD)及激光打印(LaserPlotting),以製作光工具。高解像度之打印及電腦高速繪圖既可提供可靠之準繩度,又可將製作時間縮減。
小數量之生產:由於生產沖壓工具成本高昂,往往作小數量生產時,便不符合成本經濟效益。採用光刻工具作小數量生產便是其解決辦法。
大數量之生產:若只論生產速度運作,光刻加工確是遜於高速沖床,故此,生產形狀簡單之鈑金零件時,光刻加工是不能跟沖壓技術作競爭,但零件形狀複雜難度提高時,沖壓工具成本便相應提高,又數量要求(中數量)並未達到足以平衡工具成本效益者,便應採用光刻加工生產。現時一般作大數量生產複雜形狀之鈑金零件已採用自動化形式之光刻加工,其中一例便是生產電子行業中之集成線路引線框架(Leadframe)。
蚀刻因子ipc标准

蚀刻因子ipc标准全文共四篇示例,供读者参考第一篇示例:蚀刻因子(etching factor)是制造工艺中一个非常重要的参数,它对于半导体工艺的精度和稳定性有着至关重要的影响。
虽然蚀刻因子的概念并不复杂,但它在半导体行业中的应用却是十分广泛的。
为了确保不同制造厂家之间的产品具有一致性和可比性,国际半导体产业协会(IPC)制定了一系列蚀刻因子的标准,以规范行业内蚀刻工艺的要求。
在半导体工艺中,蚀刻是一种常用的加工技术,通过蚀刻可以实现对半导体器件表面的精确处理和雕刻。
蚀刻因子是描述蚀刻速率的一种物理量,一般用于表示在蚀刻过程中所去除的材料与所消耗的蚀刻剂的比率。
蚀刻因子的大小决定了蚀刻过程的速度和精度,是衡量蚀刻工艺质量和稳定性的重要参考指标。
IPC制定的蚀刻因子标准主要是为了保证不同厂家生产的半导体产品在蚀刻工艺方面具有可比性和一致性。
在制定这些标准时,IPC考虑了多种因素,包括蚀刻剂的种类和浓度、蚀刻温度、蚀刻时间等因素。
通过这些标准,不同厂家可以按照统一的要求进行蚀刻工艺的设计和优化,从而提高产品的稳定性和质量。
除了规定蚀刻因子的数值范围外,IPC的标准还包括了蚀刻过程中的其他技术要求和控制参数。
对于硅等常见半导体材料的蚀刻工艺,IPC要求蚀刻过程中要保持恒定的蚀刻速率,避免出现“步进”效应和“侧向腐蚀”等问题。
IPC还规定了蚀刻工艺的温度、压力、流速等参数,以确保蚀刻过程的稳定性和可控性。
在实际应用中,遵守IPC的蚀刻因子标准可以为半导体制造厂家带来诸多好处。
遵守标准可以提高产品的质量和稳定性,减少生产过程中的不确定性和变异性,从而降低生产成本。
遵守标准可以提高厂家在市场上的竞争力,赢得更多客户的信任和认可。
遵守标准还有助于厂家加强与供应链的合作,建立更加稳定和可靠的供应关系。
蚀刻因子是半导体工艺中一个至关重要的参数,它直接影响着产品的质量和稳定性。
IPC制定的蚀刻因子标准为行业提供了统一的参考依据,有助于各厂家提高生产工艺的一致性和可比性。
(工艺技术)蚀刻工艺
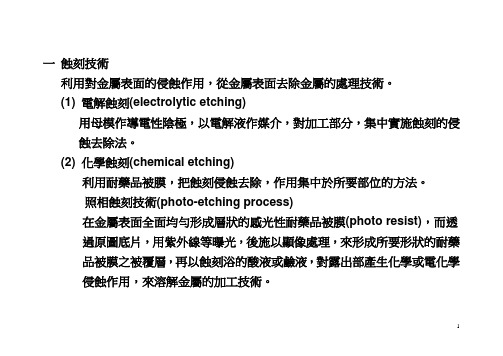
一蝕刻技術利用對金屬表面的侵蝕作用,從金屬表面去除金屬的處理技術。
(1) 電解蝕刻(electrolytic etching)用母模作導電性陰極,以電解液作媒介,對加工部分,集中實施蝕刻的侵蝕去除法。
(2) 化學蝕刻(chemical etching)利用耐藥品被膜,把蝕刻侵蝕去除,作用集中於所要部位的方法。
照相蝕刻技術(photo-etching process)在金屬表面全面均勻形成層狀的感光性耐藥品被膜(photo resist),而透過原圖底片,用紫外線等曝光,後施以顯像處理,來形成所要形狀的耐藥品被膜之被覆層,再以蝕刻浴的酸液或鹼液,對露出部產生化學或電化學侵蝕作用,來溶解金屬的加工技術。
(3) 化學蝕刻技術之特性a. 不需要電極、母型(master)等工具,故無需此等工具之維護費。
b. 由規劃到生產間所需時間短,可作短期加工。
c. 材料之物理、機械性質不受加工影響。
d. 加工不受形狀、面積、重量之限制。
e. 加工不受硬度、脆性之限制。
f. 能對所有金屬(鐵、不銹鋼、鋁合金、銅合金、鎳合金、鈦、史泰勒合金)實施加工。
g. 可高精度加工。
h. 可施複雜、不規則、不連續之設計加工。
i. 面積大,加工效率良好,但小面積時,其效率比機機械加工差。
j. 水平向之切削易得高精度,但深度、垂直方向不易得到同機機械加工之精度。
k. 被加工物之組成組織宜均勻,對不均質材,不易加工順利。
二蝕花加工(咬花加工)演進(1) 第1階段:補助目的掩飾成形品上之缺陷。
(2) 第2階段:裝飾目的提高商品價值。
(3) 第3階段:應用複合花紋邁入更高度的意匠設計時代。
(4) 第4階段:應用立體花紋進入更高品質之時代。
三咬花加工之特性(針對模具)(1) 加工時,幾乎不產生熱量,故不會引起熱變形或熱變質。
(2) 大型模具亦可加工。
(3) 加工時不會產生毛邊、應變、硬化等不良現象。
(4) 曲面、側面之加工容易。
(5) 同一加工面上,花紋之強弱可達所需之要求。