Failure Mode Effects Analysis
FailureModeandEffectsAnalysis失效模式和影响分析

.1.Task / Objective目的-To define and establish basic requirements and a process to prepare, execute and follow-up Failure Mode and Effects Analyses.为了规定建立基本的要求和程序以便于对失效模式及后果分析的准备、执行和跟踪。
2.Scope of Application范围-Avim solar production Co.,Ltd, Gaomi/China埃孚光伏制造有限公司高密/中国3.Definitions术语和定义FMEA失效模式及后果分析The Failure Mode and Effects Analysis (FMEA) is an analytical method of preventive quality assurance. It helps to identify and evaluate risks in time, and to initiate or propose suitable actions for risk minimization. The FMEA consists of 5 steps: Structural analysis, functional analysis, failure analysis, risk assessment and optimization.失效模式及后果分析是预防性品质保障的一种分析方法,它可以帮助及时识别并评估风险,并启动或提议适当的行动把风险降低最低限度。
失效模式及后果分析有五个步骤,即结构分析,功能分析,失效分析,风险评估及优化。
Product FMEA产品的失效模式及后果分析The Product FMEA analyses the design of products, product parts and their interfaces with regard to their quality over the whole product life cycle.产品的FMEA是从产品寿命周期的角度来分析产品、产品部件、以及部件接合处的设计。
故障类型和影响分析方法

概率——严重度分析法:
危险度分析的目的在于评价每种故障类型的危险程度。通 常,采用概率一严重度来评价故障类型的危险度。概率是指故 障类型发生的概率,严重度是指故障后果的严重程度。采用该 方法进行危险度分析时,通常把概率和严重度分别划分为若干 等级。例如,美国的杜邦公司把概率划分为6 等级,危险程度划 分为3个等级(见表2-9中注)。
➢ 致命度分析一般是与故障类型影响分析合用。 ➢ 目的:给出某种故障类型的发生概率及故障严重度
的综合度量。
CA 分析方法
❖ 危害性分析有定性分析和定量分析两种方法。究竟 选择哪种方法,应根据具体情况决定。
❖ 在不能获得产品技术状态数据或故障率数据的情况 下,可选择定性的分析方法。若可以获得产品的这 些数据,则应以定量的方法计算并分析危害度。
⑤ 它可以在一定程度上反映人的因素(如操作上)所 引起的失误等;
⑥ 它是其他失效分析的基础之一,它既可以独立使用, 也可作为可靠性定量分析方法的补充和保证。若与其他失效 分析法综合使用,其收获会更大。
1)定性分析法。 在得不到产品技术状态数据或故障率数据的情况下,可以按 故障模式发生的概率来评价FMEA 中确定的故障模式。此时, 将各故障模式的发生概率按一定的规定分成不同的等级。故 障模式的发生概率等级按如下规定:
❖ A 级(经常发生)——在产品工作期间内某一故障模式的发生 概率大于产品在该期间内总的故障概率的20%。
损伤人员和
设备
接口不严、弹簧疲劳
能耗增加、压力 下降
弹簧疲劳、折断 锈蚀物堵住阀口
压力迅速下降
超压时失去安全 功能、系统 压力迅速增 高
听漏气噪声、 空气压缩 机频繁打 压
压力表度数下 降
压力表度数下 降
FMEA、DFMEA、PFMEA学习资料
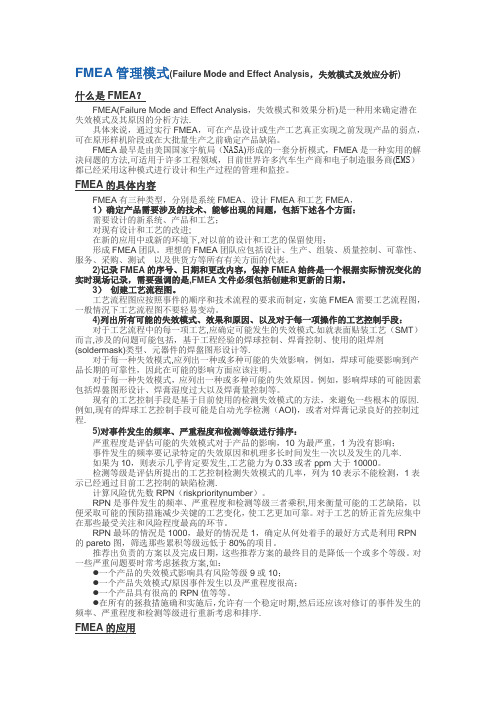
FMEA管理模式(Failure Mode and Effect Analysis,失效模式及效应分析)什么是FMEA?FMEA(Failure Mode and Effect Analysis,失效模式和效果分析)是一种用来确定潜在失效模式及其原因的分析方法.具体来说,通过实行FMEA,可在产品设计或生产工艺真正实现之前发现产品的弱点,可在原形样机阶段或在大批量生产之前确定产品缺陷。
FMEA最早是由美国国家宇航局(NASA)形成的一套分析模式,FMEA是一种实用的解決问题的方法,可适用于许多工程领域,目前世界许多汽车生产商和电子制造服务商(EMS)都已经采用这种模式进行设计和生产过程的管理和监控。
FMEA的具体内容FMEA有三种类型,分別是系统FMEA、设计FMEA和工艺FMEA,1)确定产品需要涉及的技术、能够出现的问题,包括下述各个方面:需要设计的新系统、产品和工艺;对现有设计和工艺的改进;在新的应用中或新的环境下,对以前的设计和工艺的保留使用;形成FMEA团队。
理想的FMEA团队应包括设计、生产、组装、质量控制、可靠性、服务、采购、测试以及供货方等所有有关方面的代表。
2)记录FMEA的序号、日期和更改内容,保持FMEA始终是一个根据实际情況变化的实时现场记录,需要强调的是,FMEA文件必须包括创建和更新的日期。
3)创建工艺流程图。
工艺流程图应按照事件的顺序和技术流程的要求而制定,实施FMEA需要工艺流程图,一般情況下工艺流程图不要轻易变动。
4)列出所有可能的失效模式、效果和原因、以及对于每一项操作的工艺控制手段:对于工艺流程中的每一项工艺,应确定可能发生的失效模式.如就表面贴装工艺(SMT)而言,涉及的问题可能包括,基于工程经验的焊球控制、焊膏控制、使用的阻焊剂(soldermask)类型、元器件的焊盤图形设计等.对于每一种失效模式,应列出一种或多种可能的失效影响,例如,焊球可能要影响到产品长期的可靠性,因此在可能的影响方面应该注明。
FMEA前期失效模式与效应分析

4
Failure Mode & Effects Analysis
简介( 1. FMEA 简介(续)
消除 减少 减少 保存
全风险
剩余风险
损失管制程序图 1) 消除,管制及减低风险的工作不只是工程部门的责任,更是 每一个部门甚至是每一个人的工作职责. 2) 风险允许存在, 但必须降低及控制在一定范围之内. 3) FMEA就是通过风险评估与计算来确认FMEA的执行效果.
功能 项目
潜在的 失效模式
潜在的 失效原因
发 生 率
2 3
现行 管制方式
1.退料给成型重新确认 1.后制程CCD 100%测试
检 出 率
2 1
实际改善措施
端子/塑胶投入 标示不清或错误 signal pin端子 插入,折carrier 及打 kink 塑胶刮伤 缺pin
无法辨识产品 状态 客户无法使用
3 4
36 84
17
Failure Mode & Effects Analysis
7. FMEA 制作
7-2: 表格各栏位填写说明 7-2-1: FMEA编号 编号 FMEA之文件编号,以供查询,展开及追踪. 7-2-2: 系统 子系统或零部件的名称及编号 系统,子系统或零部件的名称及编号 7-2-3: Core Team(核心小组 核心小组) 核心小组 Core team 一般应由 ME/QE/RD/AUTO/FAE/PM等跨功 能团队组成,必要时可包括客户或/和分供方 7-2-4: 设计 制造单位 设计/制造单位 QS9000 FMEA手册中要求填入相应负责人的姓名&电话,此处 改为设计/制造单位名称.
5
Failure Mode & Effects Analysis
Failure Modes and Effects Analysis
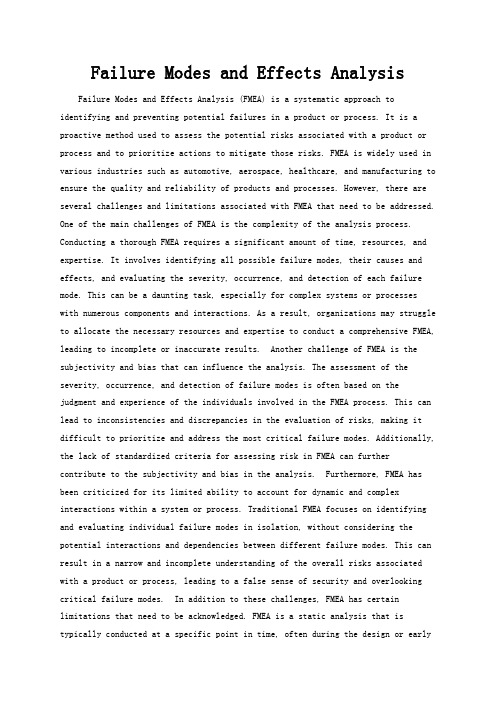
Failure Modes and Effects Analysis Failure Modes and Effects Analysis (FMEA) is a systematic approach to identifying and preventing potential failures in a product or process. It is a proactive method used to assess the potential risks associated with a product or process and to prioritize actions to mitigate those risks. FMEA is widely used in various industries such as automotive, aerospace, healthcare, and manufacturing to ensure the quality and reliability of products and processes. However, there are several challenges and limitations associated with FMEA that need to be addressed. One of the main challenges of FMEA is the complexity of the analysis process. Conducting a thorough FMEA requires a significant amount of time, resources, and expertise. It involves identifying all possible failure modes, their causes and effects, and evaluating the severity, occurrence, and detection of each failure mode. This can be a daunting task, especially for complex systems or processeswith numerous components and interactions. As a result, organizations may struggle to allocate the necessary resources and expertise to conduct a comprehensive FMEA, leading to incomplete or inaccurate results. Another challenge of FMEA is the subjectivity and bias that can influence the analysis. The assessment of the severity, occurrence, and detection of failure modes is often based on the judgment and experience of the individuals involved in the FMEA process. This can lead to inconsistencies and discrepancies in the evaluation of risks, making it difficult to prioritize and address the most critical failure modes. Additionally, the lack of standardized criteria for assessing risk in FMEA can furthercontribute to the subjectivity and bias in the analysis. Furthermore, FMEA has been criticized for its limited ability to account for dynamic and complex interactions within a system or process. Traditional FMEA focuses on identifying and evaluating individual failure modes in isolation, without considering the potential interactions and dependencies between different failure modes. This can result in a narrow and incomplete understanding of the overall risks associated with a product or process, leading to a false sense of security and overlooking critical failure modes. In addition to these challenges, FMEA has certain limitations that need to be acknowledged. FMEA is a static analysis that is typically conducted at a specific point in time, often during the design or earlydevelopment stages of a product or process. This means that FMEA may not capture changes or new failure modes that emerge over time, such as during the manufacturing or operation of the product. As a result, FMEA may not provide a comprehensive and up-to-date assessment of risks throughout the lifecycle of a product or process. Moreover, FMEA may not always consider the broader organizational and contextual factors that can influence the occurrence and impact of failure modes. Factors such as organizational culture, management practices, and external environment can significantly affect the likelihood and consequences of failure modes, but these are often overlooked in traditional FMEA. This can result in a limited understanding of the root causes and systemic issues that contribute to failure modes, hindering the effectiveness of corrective and preventive actions. Despite these challenges and limitations, FMEA remains a valuable tool for identifying and addressing potential risks in products and processes. To overcome the challenges associated with FMEA, organizations can consider integrating advanced technologies and analytical methods to enhance the analysis process. For example, the use of data analytics, simulation tools, and artificial intelligence can help automate and streamline the identification and evaluation of failure modes, reducing the time and effort required for FMEA. Additionally, organizations can develop standardized criteria and guidelines for assessing risk in FMEA to minimize subjectivity and bias in the analysis. Furthermore, organizations can adopt a more holistic and dynamic approach to FMEA by incorporating systems thinking and risk management principles. This involves considering the interdependencies and interactions within a system or process, as well as the broader organizational and environmental factors that influence risk. By taking a more comprehensive view of risks, organizations can better prioritize and address the most critical failure modes, leading to more effective risk management and improved product and process quality. In conclusion, while FMEA has its challenges and limitations, it remains a valuable tool for identifying and preventing potential failures in products and processes. By addressing the complexity, subjectivity, and static nature of traditional FMEA, organizations can enhance the effectiveness of their risk management efforts and ensure the quality and reliability of their products and processes. Embracing advanced technologies,standardized criteria, and a holistic approach to FMEA can help organizations overcome these challenges and unlock the full potential of FMEA in improving product and process quality.。
fmea知识点

fmea知识点FMEA知识点详解1. 什么是FMEA•FMEA全称是Failure Mode and Effects Analysis,中文为失效模式与影响分析。
•FMEA是一种通过系统化的方法,识别和评估潜在失效模式的工具,目的是提前采取措施预防或减少失效对系统带来的影响。
2. FMEA的作用•预防潜在问题:通过分析失效模式,识别问题的潜在来源,以便在实施之前采取预防措施。
•减少产品风险:通过评估失效的后果和严重程度,降低不可接受的产品风险。
•提高产品质量:通过改进设计、工艺和控制方法,提高产品质量和可靠性。
•优化维修计划:通过了解失效的影响和维修难度,制定更有效的维修计划。
3. FMEA的步骤1.识别过程/系统:确定要进行FMEA分析的过程或系统。
2.列出功能:列出该过程或系统的功能,即它应该实现的目标或任务。
3.确定失效模式:对每个功能,确定可能的失效模式,即功能无法正常实现的原因。
4.评估失效后果:评估每个失效模式的后果和严重程度,包括安全、环境和经济等方面。
5.确定失效原因:识别每个失效模式发生的潜在原因。
6.评估现有控制措施:评估现有的控制措施是否足够有效,能够防止或减轻失效的影响。
7.确定改进措施:基于评估结果,制定改进措施来预防或减少失效对系统的影响。
8.应用改进措施:实施和验证改进措施的有效性。
9.更新FMEA:根据实施改进措施的结果,更新FMEA以反映最新的信息。
4. FMEA的关键术语•失效模式(Failure Mode):指组件或系统在执行功能时,无法实现设计意图的方式。
•失效效果(Failure Effect):指失效模式对产品性能、安全、环境或经济等方面的不利影响。
•失效原因(Failure Cause):指导致失效模式发生的潜在原因,可以是设计、制造、操作等方面的问题。
•严重程度(Severity):评估失效效果对产品或系统的重要性和影响程度。
•发生概率(Occurrence):评估失效模式发生的频率或概率。
电脑芯片分析中的故障模式与失效分析技术
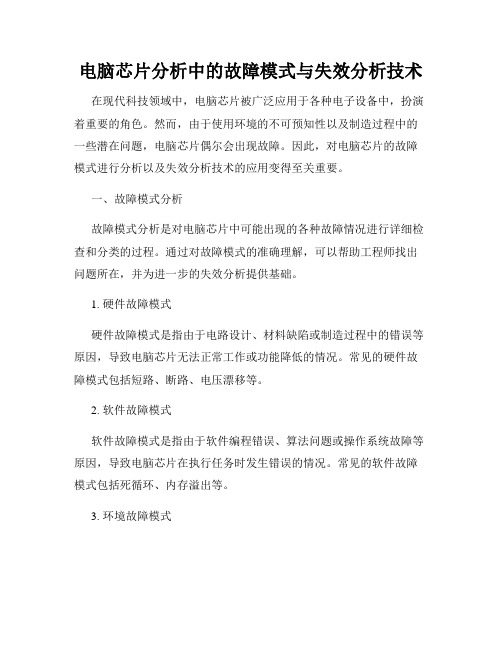
电脑芯片分析中的故障模式与失效分析技术在现代科技领域中,电脑芯片被广泛应用于各种电子设备中,扮演着重要的角色。
然而,由于使用环境的不可预知性以及制造过程中的一些潜在问题,电脑芯片偶尔会出现故障。
因此,对电脑芯片的故障模式进行分析以及失效分析技术的应用变得至关重要。
一、故障模式分析故障模式分析是对电脑芯片中可能出现的各种故障情况进行详细检查和分类的过程。
通过对故障模式的准确理解,可以帮助工程师找出问题所在,并为进一步的失效分析提供基础。
1. 硬件故障模式硬件故障模式是指由于电路设计、材料缺陷或制造过程中的错误等原因,导致电脑芯片无法正常工作或功能降低的情况。
常见的硬件故障模式包括短路、断路、电压漂移等。
2. 软件故障模式软件故障模式是指由于软件编程错误、算法问题或操作系统故障等原因,导致电脑芯片在执行任务时发生错误的情况。
常见的软件故障模式包括死循环、内存溢出等。
3. 环境故障模式环境故障模式是指电脑芯片由于使用环境的不可预测因素导致的故障。
例如,温度过高或过低、湿度过大或过小等。
环境故障模式需要特殊的测试设备和环境来模拟。
二、失效分析技术失效分析技术是为了找出电脑芯片故障的根本原因而进行的一系列操作和方法。
通过失效分析,可以确定故障模式的形成机制,以便采取相应的修复措施。
1. 故障模式与效应分析(Failure Mode and Effects Analysis,FMEA)FMEA是一种系统性的分析方法,用于识别并评估电脑芯片可能出现的故障模式及其对系统性能的影响。
通过FMEA,工程师可以评估故障的重要性并制定相应的修复策略。
2. 故障树分析(Fault Tree Analysis,FTA)FTA是一种通过构建逻辑门的树形结构来分析系统故障根本原因的方法。
通过FTA,可以确定电脑芯片故障的所有可能原因,并确定导致故障的关键因素。
3. 电镜分析(Electron Microscopy Analysis)电镜分析是利用电镜观察电脑芯片中微观结构的方法,以查找可能存在的故障点。
失效模式法评价维度
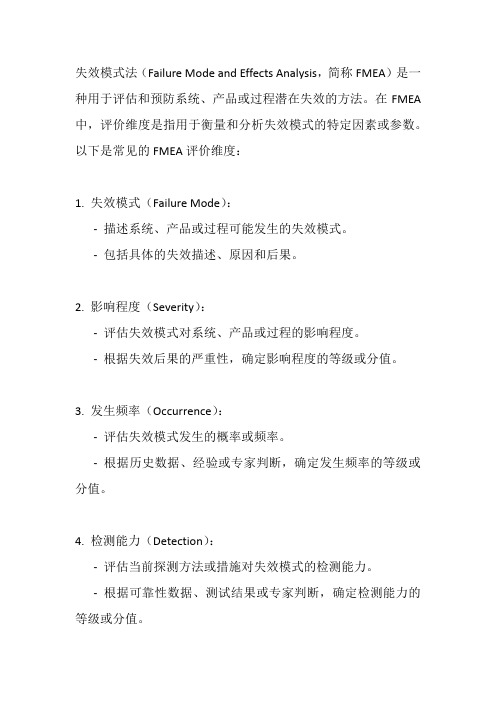
失效模式法(Failure Mode and Effects Analysis,简称FMEA)是一种用于评估和预防系统、产品或过程潜在失效的方法。
在FMEA 中,评价维度是指用于衡量和分析失效模式的特定因素或参数。
以下是常见的FMEA评价维度:1. 失效模式(Failure Mode):-描述系统、产品或过程可能发生的失效模式。
-包括具体的失效描述、原因和后果。
2. 影响程度(Severity):-评估失效模式对系统、产品或过程的影响程度。
-根据失效后果的严重性,确定影响程度的等级或分值。
3. 发生频率(Occurrence):-评估失效模式发生的概率或频率。
-根据历史数据、经验或专家判断,确定发生频率的等级或分值。
4. 检测能力(Detection):-评估当前探测方法或措施对失效模式的检测能力。
-根据可靠性数据、测试结果或专家判断,确定检测能力的等级或分值。
5. 风险优先级数(Risk Priority Number,简称RPN):-将影响程度、发生频率和检测能力综合考虑,计算出每个失效模式的RPN。
- RPN可以作为优先处理和改进失效模式的依据。
6. 预防措施(Preventive Actions):-根据评估结果,提出预防措施,旨在降低失效模式的发生概率或减轻其严重性。
7. 检测措施(Detective Actions):-根据评估结果,提出检测措施,旨在提高对失效模式的检测能力或快速识别失效。
8. 响应措施(Response Actions):-根据评估结果,提出响应措施,旨在降低失效模式的影响程度或减少后果。
以上是常见的FMEA评价维度,通过对这些维度的评估和分析,可以全面了解和识别系统、产品或过程中的潜在失效,并采取相应的措施进行预防和改进。
具体的评价维度和方法也可根据实际情况进行调整和补充。
FEMA分析
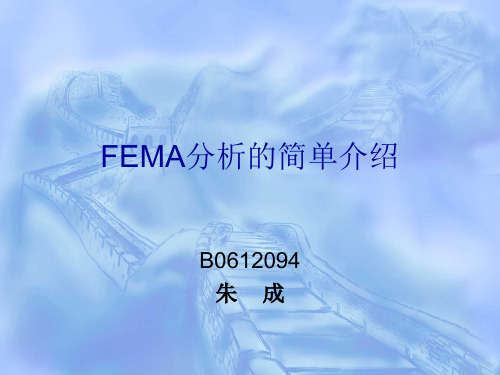
▪ 下表中列出了常见的一些典型故障模式
故障原因分析
▪ 故障模式分析只说明了产品将以什么模式发生故障,并未说 明产品为何发生故障的问题。因此,为了提高产品的可靠性, 还必须分析产生每一故障模式的所有可能原因。分析故障原 因一般从两个方面着手,一方面是导致产品功能故障或潜在 故障的产品自身的那些物理、化学或生物变化过程等直接原 因;另一方面是由于其他产品的故障、环境因素和人为因素 等引起的间接故障原因
FEMA分析的来源
FMEA作为一种可靠性分析方法起源于美国。早在5 0 年代初,美国格鲁门飞机公司在研制飞机主操纵系统 时就采用FMEA方法,取得了良好的效果。 到了60年代后期和70年代初期,FMEA方法开始广泛 地应用于航空、航天、舰船、兵器等军用系统的研制 中,并逐渐渗透到机械、汽车、医疗设备等民用工业 领域,取得显著的效果。
故障影响分析
▪ 复杂系统通常具有层次性结构,随着系统设计的进展,系统 的层次划分方式也是不同的。一般情况下在设计的早期按系 统的功能划分层次关系,随着设计的深入则既可按系统的功 能也可按系统的结构化分层次关系,因此,FMEA既可以基 于功能层次关系进行,也可以基于结构层次关系进行。
▪ 图 1-3给出了某型步话机的功能层次与结构层次的对应关系。
使输出结果失真
生产设计不符合
6
规格
5
3
63
4
84
1
21
1
20
3
72
2
56
2
56
3
90
风险分析
▪ 风险分析的目的是按每一故障模式的严重程度及该故障模 式发生的概率所产生的综合影响对系统中的产品划等分类, 以便全面评价系统中各种可能出现的产品故障的影响,它 是一种相对定量的分析方法,通常借助图形工具(如矩阵 图)来辅助分析。
fmea是什么意思_fmea的中文意思

fmea是什么意思_fmea的中文意思【fmea】abbr. 故障模式与理象分析(Failure Mode and Effects Analysis) 【网络释义】失效模式与影响分析失效模式与影响分析(FMEA)是一种确定和预防产品及工艺过程问题的系统方法。
FMEA以预防缺陷、强化安全性以及提高客户满意度为重点。
失效模式与效应分析失效模式与效应分析(FMEA)作为一种风险分析方法在设计、制造中用以预防、避免差错的应用早已为人们所熟悉。
近.失效模式与效果分析(Failure Mode And Effect Analysis)预先危险分析(PHA Preliminary Hazard Analysis失效模式分析(Failure Model Effectiveness Analysis)参与新机型的导入和延伸机型的设计,针对产品客诉问题进行产品结构方面的改善;FMEA(失效模式分析)的制作等。
【词组短语】功能FMEA Functional FMEAProcess FMEA 程失效模式及后果分析; 过程; 工艺FMEA 工艺FMEA Process FMEA-PFMEA ; process FMEAFMEA ACI 美国混凝土学会标准structured FMEA 结构; 结构FMEAFMEA设计Design FMEA(Fail Mode and Effect Analysis)FMEA introduction 文件名称D FMEA 第三十八章FMEA方法FMEA method【例句】Is the process FMEA prepared and have improvement measures been established?准备和改善措施是建立在这个故障模式影响分析过程中吗?MetsoAutomation has implemented a Failure Mode and Effect Analysis (FMEA) programmeto extend the lifecyles and lower the cost of ownership of its products.Metso自动化已经实现了一个FailureModeandEffectAnalysis (故障模式和影响分析FMEA)程序,以便扩展其产品的生命周期并降低拥有权成本。
failure modes and effects analysis

failure modes and effects analysis 《失效模式及影响分析》(FailureModesandEffectsAnalysis,FMEA)是一种常见的风险管理工具。
它通过系统地识别、评估和控制可能的失效,以减少产品或过程中的潜在问题。
本文将介绍FMEA的定义、流程、应用和局限性。
FMEA是一种结构化的方法,用于识别和评估可能的失效模式及其潜在影响。
通过该方法,可以在设计、生产和维护阶段,对各种潜在问题进行识别和解决。
FMEA通常被用于制造业、医疗设备、航空航天、汽车和软件工程等领域。
FMEA的流程包括:确定要分析的系统或过程、识别可能的失效模式、评估失效的潜在影响、确定潜在原因和控制措施、评估控制效果并持续改进。
在这个过程中,需要考虑多种因素,如失效的概率、影响的严重程度、检测措施的可行性等。
FMEA的应用有很多方面。
在设计阶段,FMEA可以帮助设计师识别并解决可能出现的问题,减少产品开发中的延误和成本。
在生产阶段,FMEA可以帮助生产厂商识别并解决生产过程中的潜在问题,确保产品质量。
在维护阶段,FMEA可以帮助识别可能出现的故障,减少设备停机时间和修理成本。
然而,FMEA也存在一些局限性。
首先,它只是一种预测性的方法,无法完全覆盖所有可能的失效情况。
其次,FMEA需要依赖专业知识和经验,对于没有经验或知识不足的人员来说,使用FMEA可能会出现失误。
此外,FMEA过程比较复杂,需要一定的时间和人力资源。
总之,《失效模式及影响分析》是一种常见的风险管理工具,它可以帮助企业在设计、生产和维护阶段,识别和解决各种潜在问题。
但同时,也需要认识到FMEA的局限性,避免在使用过程中出现失误。
FEMA失效模式分析

发布的日期。
7、FMEA日期
填入编制FMEA原始稿的完成日期及最新修订的日期。
2021/5/27
19
8、核心小组 列出被授权以确定和/或执行任务的责任个人和部门名称(建议所有小 组人员的姓名、部门、电话、地址等,都记录在一分发表上)。 9、项目/功能 填入将被分析项目的名称和其他适切的信息(如编号、零件等级等)。 利用工程图纸上标明的名称并指明设计等级。在最初发布之前(如在概 念形成阶段),应该使用临时性编号。 填入时,用尽可能简洁的文字来说明被分析项目要满足设计意图的功能, 包括该系统运行的环境相关信息(如指定温度、压力、湿度范围、设计 寿命等,是计量值/可量测的)。如果该项目有多种功能,且有不同的 失效模式,要把所有功能都单独列出。
2021/5/27
5
圖一 潛 在 失 效 模 式 與 效 應 分 析 作 業 序 列
項 目 /失 效
潛在 失效模式
失效 潛在效應
嚴 重 度
等 級
潛在原因/ 失效機制
發 生 度
現行的 設計管制
預防 檢測
難R
檢P 度N
建議措施
責任與 目標
完成日期
行動結果
嚴難檢 R
採行措施 重 檢 驗 P
度度度 N
效應為何?
2021/5/27
18
3、设计责任
填入整车厂(OEM)、部门和小组。如果适用,还要包括供货商的名
称。
4、编制者
填入负责FMEA准备工作的工程师姓名、电话和所在公司的名称。
5、产品型号/项目
填入将使用和/或将被分析的设计冲击的预期车型年型/项目(如果
已知的话)。
6、关键日期
填入FMEA初次预定完成的日期,该日期不应该超过计划的量产设计
失效模式与效应分析(failure modes and effects analysis,FMEA)
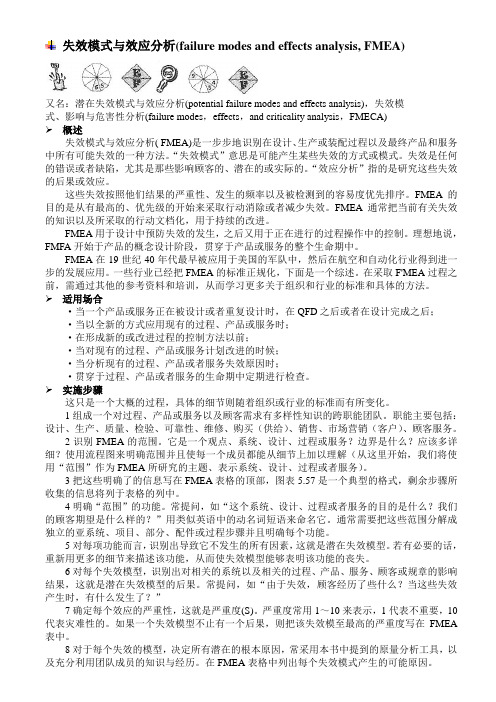
失效模式与效应分析(failure modes and effects analysis, FMEA)又名:潜在失效模式与效应分析(potential failure modes and effects analysis),失效模式、影响与危害性分析(failure modes,effects,and criticality analysis,FMECA)概述失效模式与效应分析( FMEA)是一步步地识别在设计、生产或装配过程以及最终产品和服务中所有可能失效的一种方法。
“失效模式”意思是可能产生某些失效的方式或模式。
失效是任何的错误或者缺陷,尤其是那些影响顾客的、潜在的或实际的。
“效应分析”指的是研究这些失效的后果或效应。
这些失效按照他们结果的严重性、发生的频率以及被检测到的容易度优先排序。
FMEA的目的是从有最高的、优先级的开始来采取行动消除或者减少失效。
FMEA通常把当前有关失效的知识以及所采取的行动文档化,用于持续的改进。
FMEA用于设计中预防失效的发生,之后又用于正在进行的过程操作中的控制。
理想地说,FMFA开始于产品的概念设计阶段,贯穿于产品或服务的整个生命期中。
FMEA在19世纪40年代最早被应用于美国的军队中,然后在航空和自动化行业得到进一步的发展应用。
一些行业已经把FMEA的标准正规化,下面是一个综述。
在采取F'MEA过程之前,需通过其他的参考资料和培训,从而学习更多关于组织和行业的标准和具体的方法。
适用场合·当一个产品或服务正在被设计或者重复设计时,在QFD之后或者在设计完成之后;·当以全新的方式应用现有的过程、产品或服务时;·在形成新的或改进过程的控制方法以前;·当对现有的过程、产品或服务计划改进的时候;·当分析现有的过程、产品或者服务失效原因时;·贯穿于过程、产品或者服务的生命期中定期进行检查。
实施步骤这只是一个大概的过程,具体的细节则随着组织或行业的标准而有所变化。
fmea失效模式分析范文英文版

fmea失效模式分析范文英文版FMEA (Failure Mode and Effects Analysis) is a systematic method for identifying and preventing potential failures in a product or process. It is used to analyze and evaluate the possible failure modes and their effects, in order to prioritize them and develop a plan for corrective actions.The FMEA process involves identifying potential failure modes, determining their causes and effects, assigning a severity rating to each potential failure mode, determining the likelihood of the failure occurring, and assigning a detection rating to each potential failure mode to estimate the likelihood of the failure being detected before it affects the customer.The purpose of FMEA is to improve the quality and reliability of a product or process by proactively identifying and addressing potential failure modes before they occur. By conducting an FMEA, organizations can reduce the risk of product failures, improve customer satisfaction, and reduce costs associated with warranty claims and product recalls.The FMEA process typically involves a multidisciplinary team of experts who analyze the product or process, identify potential failure modes, and develop action plans to prevent these failures.The team may include engineers, quality assurance professionals, design engineers, production engineers, and other relevant stakeholders.The FMEA process can be applied to various industries, including automotive, aerospace, manufacturing, healthcare, and many others. It is a valuable tool for continuous improvement and risk management in any organization.In conclusion, FMEA is an essential tool for identifying and preventing potential failures in products or processes. By analyzing and evaluating potential failure modes, organizations can proactively address issues to improve product quality, customer satisfaction, and overall competitiveness. FMEA is a valuable method for risk management and continuous improvement in any industry.。
前期失效模式及效应分析
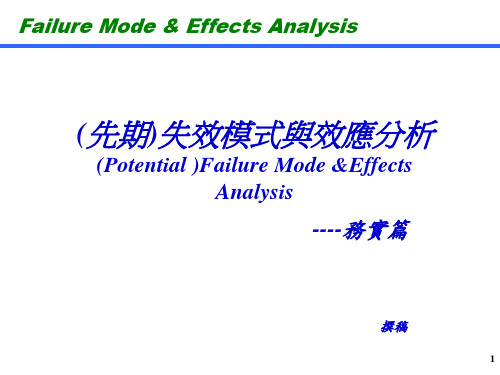
共面度不良
影響客戶焊接 6
power pin
塑膠刮傷
裁切,壓入及打
kink
客戶不滿意
4
(外觀方面)
1.打kink機構異常(上 下刀配合位置不佳)
1.自動機流道不順使 產品在運動時刮傷
共面度不良
影響客戶焊接 6
1.打kink機構異常(上 下刀配合位置不佳)
CCD檢測& 終檢/包裝
端子裁切毛邊 歪針
失效模式 失效效應 重
失效原因 生
項目
度級
率
現行 管制方式
端子/塑膠投入 標示不清或錯誤 無法辨識產品 2
狀態
signal pin端子 缺pin
客戶無法使用 7
插入,折carrier
及打 kink
塑膠刮傷
客戶不滿意
4
(外觀方面)
人為疏忽
1.電鍍制程中測試時 取樣
2.換端子時碰掉 1.自動機流道不順使
7. FMEA 制作
7-1: FMEA表格格式 (見下頁)
在QS9000六大冊之一 << FMEA Manual >>中有標準表格, 在實 際運作中在保證 FMEA總體架構與精神不變的前提下可允許有 局部的細微改變. 建議 :除表頭以外的內容不要修改.
16
Failure Mode & Effects Analysis
1957工程手冊中正式列出 FMEA程序
Nation Aeronautics and Space Administration(NASA)
Chrysler,Ford, G.M. ASQC,AIAG
Defense Department
International Electrical Commission(IEC)
failure mode and effects analysis

failure mode and effects analysisFailureModeandEffectsAnalysis(FMEA)是一种过程改进和失效模式分析(FMEA)工具,用于预先分析失效模式和其可能后果的可能性,从而实现更高的质量和安全性。
它通常用于减少成本,提高客户满意度和改进产品或服务的质量。
FMEA流程的重点是识别和正确评估潜在的质量和安全隐患,并纳入管理流程来改进产品,服务或过程的性能。
FMEA的目的是为了用尽可能有效的举措来减少失效的可能性。
它会从使用失效模式分析和可能后果的可能性,识别其中可能导致产品失效的因素,并采取有效的措施来改善它们。
FMEA包括在表具中记录和协调失效模式,其后果以及对每个失效模式分析可能采取的纠正措施。
传统FMEA流程涵盖四个主要阶段:失效模式分析,失效模式可能性和后果,纠正行动分析和FMEA报告。
在FMEA失效模式分析阶段,需要确定系统的各个组件,以及其可能失效的模式。
这可以通过分析现有产品的失效模式,实际施工及使用中的问题和经验积累等来完成。
在FMEA失效模式和可能的后果阶段,需要为每个失效模式确定可能的后果,以及可能导致失效的各种可能性。
此阶段还可以评估当前防止失效模式发生的控制,并确定可能会发生的最糟糕情况。
在FMEA纠正行动分析阶段,需要对每个失效模式及其可能后果,分析可能采取的纠正措施,以及改进控制的效果。
这些纠正措施可以确定为以下三种:改进系统,改善测试流程,或采取新技术。
最后,在FMEA报告阶段,将所有信息整合并生成报告,以记录每个失效模式,以及可能后果和纠正措施。
这些报告可以用于跟踪实施进程,以及评估纠正措施的有效性。
总而言之,FMEA是一个有效的,有用的流程改进工具,它可以分析失效模式和可能的后果,确定可能用于纠正的策略,从而实现产品可靠性的提高和更高的客户满意度。
它能够确保企业永远保持最高的质量和安全标准,以及融入新技术,让企业业务达到新的高度。
失效模式及后果分析 Failure Mode and Effects Analysis
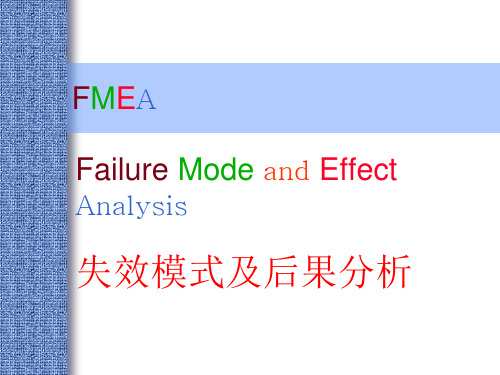
²É È¡ µÄ ´ë Ê©
R S O DP
N
³µ ÃÅ ÄÚ ²¿ ÈË ¹¤Í¿ À¯
³µ ÃÅ ÊÙ Ãü ½µ
7
µÍ £¬ µ¼ ÖÂ
¡£ ²à Ãæ
Ϊ £¬ Í¿
¸² ³µ ÒÔ
¸Ç ³µ ÃÅ ÏÂ × î С
ÃÅ ²ã ºñ
ÄÚ ± í ¶È
¹æ ²»
¶¨± í Ãæ × ã
Í¿
À¯
280
¸ø Éî ʹ
Åç ¶È Åç
À¯ ÏÞ À¯
Æ÷¼Ó λ × Ô ¶¯
× ° »¯
ÖÆ Ôì ¹¤³Ì ²¿ 98/10/15
Ôö ¼Ó ÏÞ Î» Æ÷£¬ ÔÚ Ïß
对产品生产线有較微小的破坏性 影响 ,部分产品有可能需要在生产线返工,产品的 不足被很敏銳的客戶所注意
等級 10
9 8 7 6 5 4 3 2 1
可测度
探测度 绝对不 肯定 很极少 极少 很少 少 中等 中上 多 很多 几乎肯 定
准则:设计控制可能探测出来的可能性 设计控制将不能和/或不可能找出潜在的起因/机理及后续的失效模式,或根 本没有设计控制 设计控制只有很极少的机会能找出潜在的起因/机理及后续的失效模式 设计控制只有极少的机会能找出潜在的起因/机理及后续的失效模式 设计控制有很少的机会能找出潜在的起因/机理及后续的失效模式 设计控制有较少的机会能找出潜在的起因/机理及后续的失效模式 设计控制有中等的机会能找出潜在的起因/机理及后续的失效模式 设计控制有中上多的机会能找出潜在的起因/机理及后续的失效模式 设计控制有较多的机会能找出潜在的起因/机理及后续的失效模式 设计控制有很多的机会能找出潜在的起因/机理及后续的失效模式
FMEA:Failure Mode and Effects Analysis

FMEA:Failure Mode and Effects AnalysisFMEA是一种可靠性设计的重要方法。
它实际上是FMA(故障模式分析)和FEA(故障影响分析)的组合。
它对各种可能的风险进行评价、分析,以便在现有技术的基础上消除这些风险或将这些风险减小到可接受的水平。
缩写FMEA(失效模式与影响分析)F ailure M ode and E ffects A nalysis潜在失效模式与后果分析历史50年代初,美国第一次将FMEA思想用于一种战斗机操作系统的设计分析;60年代中期,FMEA技术正式用于航天工业(Apollo计划);1976年,美国国防部颁布了FMEA的军用标准,但仅限于设计方面。
70年代末,FMEA技术开始进入汽车工业和医疗设备工业。
80年代初,进入微电子工业。
80年代中期,汽车工业开始应用过程FMEA确认其制造过程。
1988年,美国联邦航空局发布咨询通报要求所有航空系统的设计及分析都必须使用FMEA。
1991年,ISO-9000推荐使用FMEA提高产品和过程的设计。
1994年,FMEA又成为QS-9000的认证要求。
产品分类概要由于产品故障可能与设计、制造过程、使用、承包商/供应商以及服务有关,因此FMEA又细分为:DFMEA:设计FMEAPFMEA:过程FMEAEFMEA:设备FMEASFMEA:体系FMEA其中设计FMEA和过程FMEA最为常用。
DFMEA:设计FMEA设计FMEA(也记为d-FMEA)应在一个设计概念形成之时或之前开始,并且在产品开发各阶段中,当设计有变化或得到其他信息时及时不断地修改,并在图样加工完成之前结束。
其评价与分析的对象是最终的产品以及每个与之相关的系统、子系统和零部件。
需要注意的是,d-FMEA在体现设计意图的同时还应保证制造或装配能够实现设计意图。
因此,虽然d-FMEA不是靠过程控制来克服设计中的缺陷,但其可以考虑制造/装配过程中技术的/客观的限制,从而为过程控制提供了良好的基础。
- 1、下载文档前请自行甄别文档内容的完整性,平台不提供额外的编辑、内容补充、找答案等附加服务。
- 2、"仅部分预览"的文档,不可在线预览部分如存在完整性等问题,可反馈申请退款(可完整预览的文档不适用该条件!)。
- 3、如文档侵犯您的权益,请联系客服反馈,我们会尽快为您处理(人工客服工作时间:9:00-18:30)。
Proprietary Material of Duracell Global Business Management
5
FMEA History and Types
History
50’ 60’ 70’ 80’ 90’
Fighter Plane Design Apollo Plan Automobile/Medical Instrument Micro-electronic QS9000, ISO9000
Recommended Action(s) Area/Individual Responsible & Completion Date Actions Taken
(Rev.) Action Results s e v o c c d e t S * O R P N
Proprietary Material of Duracell Global Business Management
Recommended to be Process Owner
Must be Empowered to implement actions Functional experts can be pulled in as needed Smaller “Core” group may be useful initially to provide framework.
Operator involvement is imperative at this step!
Proprietary Material of Duracell Global Business Management 12
Severity Rating
Severity Severity is a rating corresponding to the seriousness of an effect of a potential failure mode. No Effect Very Slight Effect Slight Effect Minor Effect Moderate Effect Significant Effect Major Effect Serious Effect Very Serious Effect Hazardous Effect 1 2 3 4 5 6 7 7 8 9 9 10 10 4 1 No effect on system or output performance or on subsequent processes. Customer will probably not notice the failure. Nuisance Fault noticed. Slight effect on output performance. Customer slightly annoyed. Nuisance fault obvious. Minor effect on output or process performance. Slight deterioration. Chronic nuisance fault. Moderate effect on performance. Customer dissatisfied. Nuisance repair required. Performance degraded but safe. Discomfort. Repair required. Non-vital part nonfunctional. Rework/Repairs necessary. Performance severely affected but safe. Dissatisfied customer. Subsystem inoperable. Equipment damaged. System inoperable but safe. Very dissatisfied customer. Potentially hazardous failure. Safety related but gradual failure. Hazardous failure. Safety related – sudden failure, Government regulation non-compliance. Proprietary Material of Duracell 13 Global Business Management
Types
DFMEA PFMEA
Proprietary Material of Duracell Global Business Management
6
Process FMEA Form
Process Process Cell Size Cell Size Cell Chemistry Cell Chemistry
Proprietary Material of Duracell Global Business Management 10
Process FMEA Flow
Team Selection
Define Process
Detail Failure Mode Causes Effects
Calculate Risk Numbers
Failure Mode Effects Analysis (FMEA)
Abbr. Version
DTQS-NPQ
July 2000
FAILURE
What’s the failure
Failure class Failure occurrence
What’s the reason for failure
FMEA A systematic group of activities intended to:
Recognize the potential failure(s) of a product or process and the severity of effect of that failure(s). Identify critical characteristics. Rank order potential design and process deficiencies. Identify actions that can eliminate or reduce the chance of the potential failure from occurring and reaching the customer. Document the process.
Proprietary Material of Duracell Global Business Management
4
FMEA Purpose
To eliminate the cause of failure …if this is not possible
reduce how often the failure occurs improve the ability to detect the failure before it reaches the customer
Potential cause(s) of Failure O c c Current Controls D e t S * O R P N
Page 1 of 1 Prepared by Page 1 of 1 Prepared by FMEA Date (Orig.) Date (Orig.) (Rev.) FMEA
Process Function Potential Failure Mode Potential Effect(s) of Failure S e v C l a s s
Process Responsibility FMEAProcess Responsibility Due Date FMEA Due Date FMEAFMEA Number Number
7
Process FMEA Flow
Team Selection
Define Process
Detail Failure Mode Causes Effects
Calculate Risk Numbers
Build Pareto Chart
Proprietary Material of Duracell Global Business Management
Develop Recommended Actions
8
Process FMEA Flow
Team Selection
Define Process
Detail Failure Mode Causes Effects
Calculate Risk Numbers
Build Pareto Chart
Proprietary Material of Duracell Global Business Management
Develop Recommended Actions
9
Process FMEA
Team Selection
Cross Functional and Multilevel
Operators, Mechanics, Engineers, Leaders Team Leader Designated
Build Pareto Chart
Proprietary Material of Duracell Global Business Management
Develop Recommended Actions
11
Process FMEA