伺服应用案例之PLC控制篇复旦大学
PLC控制伺服电机应用设计
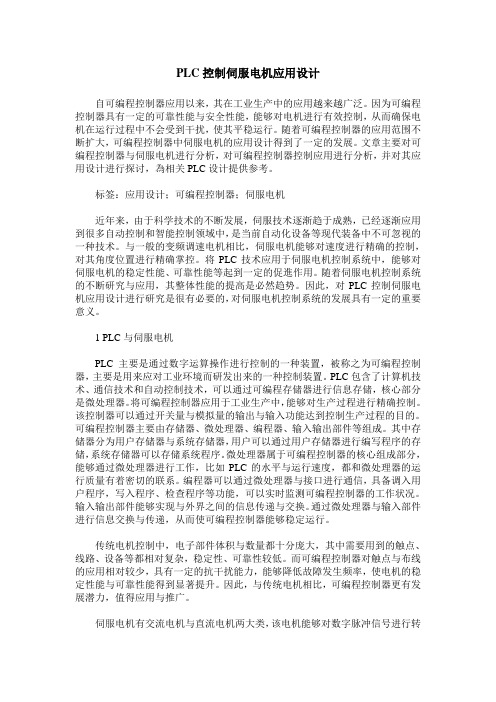
PLC控制伺服电机应用设计自可编程控制器应用以来,其在工业生产中的应用越来越广泛。
因为可编程控制器具有一定的可靠性能与安全性能,能够对电机进行有效控制,从而确保电机在运行过程中不会受到干扰,使其平稳运行。
随着可编程控制器的应用范围不断扩大,可编程控制器中伺服电机的应用设计得到了一定的发展。
文章主要对可编程控制器与伺服电机进行分析,对可编程控制器控制应用进行分析,并对其应用设计进行探讨,為相关PLC设计提供参考。
标签:应用设计;可编程控制器;伺服电机近年来,由于科学技术的不断发展,伺服技术逐渐趋于成熟,已经逐渐应用到很多自动控制和智能控制领域中,是当前自动化设备等现代装备中不可忽视的一种技术。
与一般的变频调速电机相比,伺服电机能够对速度进行精确的控制,对其角度位置进行精确掌控。
将PLC技术应用于伺服电机控制系统中,能够对伺服电机的稳定性能、可靠性能等起到一定的促進作用。
随着伺服电机控制系统的不断研究与应用,其整体性能的提高是必然趋势。
因此,对PLC控制伺服电机应用设计进行研究是很有必要的,对伺服电机控制系统的发展具有一定的重要意义。
1 PLC与伺服电机PLC主要是通过数字运算操作进行控制的一种装置,被称之为可编程控制器,主要是用来应对工业环境而研发出来的一种控制装置。
PLC包含了计算机技术、通信技术和自动控制技术,可以通过可编程存储器进行信息存储,核心部分是微处理器。
将可编程控制器应用于工业生产中,能够对生产过程进行精确控制。
该控制器可以通过开关量与模拟量的输出与输入功能达到控制生产过程的目的。
可编程控制器主要由存储器、微处理器、编程器、输入输出部件等组成。
其中存储器分为用户存储器与系统存储器,用户可以通过用户存储器进行编写程序的存储,系统存储器可以存储系统程序。
微处理器属于可编程控制器的核心组成部分,能够通过微处理器进行工作,比如PLC的水平与运行速度,都和微处理器的运行质量有着密切的联系。
编程器可以通过微处理器与接口进行通信,具备调入用户程序,写入程序、检查程序等功能,可以实时监测可编程控制器的工作状况。
基于PLC的全数字交流伺服位置控制
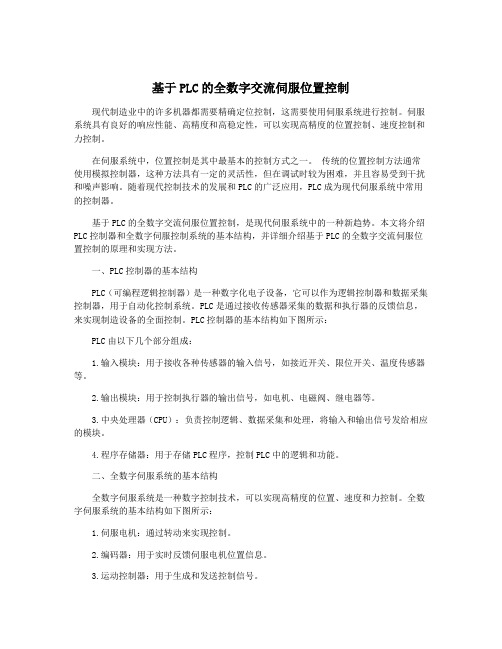
基于PLC的全数字交流伺服位置控制现代制造业中的许多机器都需要精确定位控制,这需要使用伺服系统进行控制。
伺服系统具有良好的响应性能、高精度和高稳定性,可以实现高精度的位置控制、速度控制和力控制。
在伺服系统中,位置控制是其中最基本的控制方式之一。
传统的位置控制方法通常使用模拟控制器,这种方法具有一定的灵活性,但在调试时较为困难,并且容易受到干扰和噪声影响。
随着现代控制技术的发展和PLC的广泛应用,PLC成为现代伺服系统中常用的控制器。
基于PLC的全数字交流伺服位置控制,是现代伺服系统中的一种新趋势。
本文将介绍PLC控制器和全数字伺服控制系统的基本结构,并详细介绍基于PLC的全数字交流伺服位置控制的原理和实现方法。
一、PLC控制器的基本结构PLC(可编程逻辑控制器)是一种数字化电子设备,它可以作为逻辑控制器和数据采集控制器,用于自动化控制系统。
PLC是通过接收传感器采集的数据和执行器的反馈信息,来实现制造设备的全面控制。
PLC控制器的基本结构如下图所示:PLC由以下几个部分组成:1.输入模块:用于接收各种传感器的输入信号,如接近开关、限位开关、温度传感器等。
2.输出模块:用于控制执行器的输出信号,如电机、电磁阀、继电器等。
3.中央处理器(CPU):负责控制逻辑、数据采集和处理,将输入和输出信号发给相应的模块。
4.程序存储器:用于存储PLC程序,控制PLC中的逻辑和功能。
二、全数字伺服系统的基本结构全数字伺服系统是一种数字控制技术,可以实现高精度的位置、速度和力控制。
全数字伺服系统的基本结构如下图所示:1.伺服电机:通过转动来实现控制。
2.编码器:用于实时反馈伺服电机位置信息。
3.运动控制器:用于生成和发送控制信号。
4.伺服驱动器:用于接收和执行控制信号。
基于PLC的全数字交流伺服位置控制,采用了先进的技术和数字控制理论,具有响应速度快、精度高、抗干扰能力强等特点。
其原理如下:1.编写控制程序:根据产品需要设置工作参数和控制策略,将控制程序写入PLC中。
PLC控制伺服电机应用实例

PLC控制伺服电机应用实例,写出组成整个系统的PLC模块及外围器件,并附相关程序.PLC品牌不限。
以松下FP1系列PLC和A4系列伺服驱动为例,编制控制伺服电机定长正、反旋转的PLC程序并设计外围接线图,此方案不采用松下的位置控制模块FPG—-PP11\12\21\22等,而是用晶体管输出式的PLC,让其特定输出点给出位置指令脉冲串,直接发送到伺服输入端,此时松下A4伺服工作在位置模式。
在PLC程序中设定伺服电机旋转速度,单位为(rpm),设伺服电机设定为1000个脉冲转一圈。
PLC输出脉冲频率=(速度设定值/6)*100(HZ).假设该伺服系统的驱动直线定位精度为±0。
1mm,伺服电机每转一圈滚珠丝杠副移动10mm,伺服电机转一圈需要的脉冲数为1000,故该系统的脉冲当量或者说驱动分辨率为0.01mm(一个丝);PLC输出脉冲数=长度设定值*10。
以上的结论是在伺服电机参数设定完的基础上得出的.也就是说,在计算PLC发出脉冲频率与脉冲前,先根据机械条件,综合考虑精度与速度要求设定好伺服电机的电子齿轮比!大致过程如下:机械机构确定后,伺服电机转动一圈的行走长度已经固定(如上面所说的10mm),设计要求的定位精度为0。
1mm(10个丝)。
为了保证此精度,一般情况下是让一个脉冲的行走长度低于0。
1mm,如设定一个脉冲的行走长度为如上所述的0。
01mm,于是电机转一圈所需要脉冲数即为1000个脉冲。
此种设定当电机速度要求为1200转/分时,PLC应该发出的脉冲频率为20K。
松下FP1——-40T 的PLC的CPU本体可以发脉冲频率为50KHz,完全可以满足要求。
如果电机转动一圈为100mm,设定一个脉冲行走仍然是0。
01mm,电机转一圈所需要脉冲数即为10000个脉冲,电机速度为1200转时所需要脉冲频率就是200K。
PLC的CPU输出点工作频率就不够了。
需要位置控制专用模块等方式.有了以上频率与脉冲数的算法就只需应用PLC的相应脉冲指令发出脉冲即可实现控制了.假设使用松下A4伺服,其工作在位置模式,伺服电机参数设置与接线方式如下:一、按照伺服电机驱动器说明书上的“位置控制模式控制信号接线图”接线:pin3(PULS1),pin4(PULS2)为脉冲信号端子,PULS1连接直流电源正极(24V电源需串连2K左右的电阻),PULS2连接控制器(如PLC的输出端子)。
伺服电机的PLC控制方法

伺服电机的PLC控制方法伺服电机是一种高精度、高性能、可控性强的电机,可广泛应用于工业自动化领域。
在工业自动化应用中,PLC(可编程逻辑控制器)常用于控制伺服电机的运动。
本文将介绍伺服电机的PLC控制方法。
1.伺服电机的基本原理伺服电机是一种可以根据控制信号进行位置、速度或力矩控制的电机。
它由电机本体、编码器、位置控制器和功率放大器等组成。
通过反馈机制,控制器可以实时监控电机的运动状态,并根据实际需求输出控制信号调整电机的运行。
2.伺服电机的PLC控制器选型在使用PLC控制伺服电机之前,需要选择合适的PLC控制器。
PLC控制器需要具备足够的计算能力和接口扩展能力,以满足伺服电机复杂运动控制的需求。
同时,PLC控制器还需要具备丰富的通信接口,可以与伺服电机进行实时通信。
3.伺服电机的PLC控制程序设计PLC控制程序设计是实现伺服电机运动控制的关键。
在编写PLC控制程序时,需要考虑以下几个方面:(1)运动参数设定:根据实际应用需求,设置伺服电机的运动参数,包括速度、加速度、减速度、位置等。
(2)位置控制:根据编码器的反馈信号,实现伺服电机的位置控制。
根据目标位置和当前位置的差值,控制输出的电压信号,驱动电机按照设定的速度和加速度运动。
(3)速度控制:根据速度设定和编码器的反馈信号,实现伺服电机的速度控制。
通过调整输出的电压信号,控制电机的速度和加速度。
(4)力矩控制:根据力矩设定和编码器的反馈信号,实现伺服电机的力矩控制。
通过调整输出的电压信号,控制电机的力矩和加速度。
(5)运动控制模式切换:通过设定运动控制模式,实现伺服电机在位置控制、速度控制和力矩控制之间的切换。
4.伺服电机的PLC控制程序调试在编写完PLC控制程序后,需要进行调试以确保控制效果。
调试时可以通过监视编码器的反馈信号和控制输出,来验证伺服电机的运动控制是否准确。
如有误差,可以通过调整运动参数或控制算法进行修正。
此外,在PLC控制伺服电机过程中,还需要注意以下几点:(1)合理选择采样周期:采样周期越短,控制精度越高,但同时也会增加PLC的计算负担。
PLC在伺服控制系统中的应用
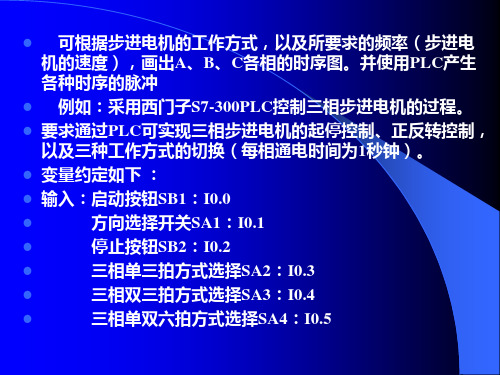
在不同的工作方式下赋予MW10不同的初值。
程序段2:三相单三拍或三相单双六拍工作方式, 此时均从M11.0开始移位,两种工作方式均为 M11.6为“1”时返回。 程序段3:三相双三拍工作方式,此时从M11.1 开始因为,而在M11.7时返回。 程序段4:若按下停止按钮或没有选择工作方式 时,MW10中的内容为“0”,则不会有输出。
输出: A相加电压:Q0.0 B相加电压:Q0.1 C相加电压:Q0.2 启动指示灯:Q0.3 三相单三拍运行方式:Q0.4 三相双三拍运行方式:Q0.5 三相单双六拍运行方式:Q0.6 输出脉冲显示灯: Q0.7
三相单三拍
正向时序图
三相双三拍
正向时序图
三相单双六拍正向时序图
编程方法1:
参数SET_DO:数字量输出控制端。当 MAN_DO端的状态为“1”时,可通过SET_DO 端控制指定通道的状态是为高电平“1”,还是 低电平“0”。如果MAN_DO端的状态为“0”, 则SET_DO端的状态不起作用,不会影响通道 的状态。 参数OUTP_VAL:输出值设置。输出值参数 数据类型为整数。在硬件设置中我们只指定了 脉冲的周期,延时时间以及最小脉宽等,并没 有指定脉冲的占空比。参数OUTP_VAL就是 用来指定脉冲占空比的。
在不同的工作方式下,将移位指令移动的位数 保存在MW20中。
MW20
程序段5:三相单三拍或三相双三拍,每次应移 动2位。 程序段6:三相单双六拍,每次应移动一位。 程序段7:为移位指令,由于T1的周期为1秒钟, 因此每间隔1秒钟,移位指令左移指定的位数。 再将MW10中对应的位控制相应的输出,可实 现步进电机的控制。步进电机的反向控制可根 据相同的办法来实现。
PLC控制伺服电机应用实例
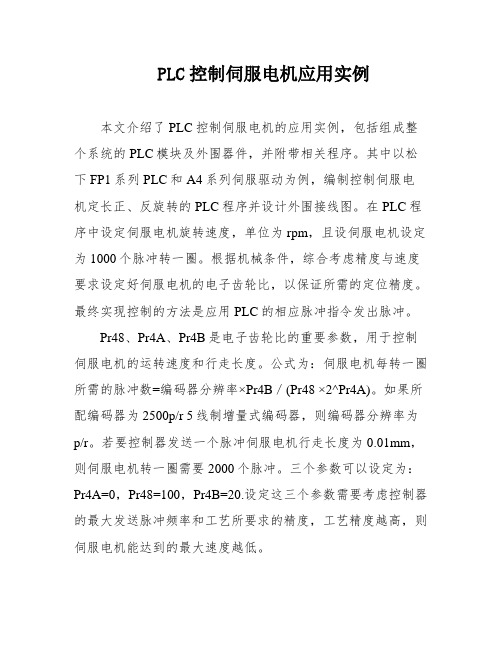
PLC控制伺服电机应用实例本文介绍了PLC控制伺服电机的应用实例,包括组成整个系统的PLC模块及外围器件,并附带相关程序。
其中以松下FP1系列PLC和A4系列伺服驱动为例,编制控制伺服电机定长正、反旋转的PLC程序并设计外围接线图。
在PLC程序中设定伺服电机旋转速度,单位为rpm,且设伺服电机设定为1000个脉冲转一圈。
根据机械条件,综合考虑精度与速度要求设定好伺服电机的电子齿轮比,以保证所需的定位精度。
最终实现控制的方法是应用PLC的相应脉冲指令发出脉冲。
Pr48、Pr4A、Pr4B是电子齿轮比的重要参数,用于控制伺服电机的运转速度和行走长度。
公式为:伺服电机每转一圈所需的脉冲数=编码器分辨率×Pr4B/(Pr48 ×2^Pr4A)。
如果所配编码器为2500p/r 5线制增量式编码器,则编码器分辨率为p/r。
若要控制器发送一个脉冲伺服电机行走长度为0.01mm,则伺服电机转一圈需要2000个脉冲。
三个参数可以设定为:Pr4A=0,Pr48=100,Pr4B=20.设定这三个参数需要考虑控制器的最大发送脉冲频率和工艺所要求的精度,工艺精度越高,则伺服电机能达到的最大速度越低。
松下FP1-40 T型PLC的程序梯型图如下:S7-200 PLC在数字伺服电机控制中的应用。
首先需要了解PLC如何控制伺服电机。
本应用实例选择的是位置控制模式,采用差动驱动方式的脉冲输入回路,方便实现对两部电机的控制。
PLC与伺服放大器的接线图如下:L+为公共PLC端子,接24VDC正端,通过控制内部晶体管的开关使得输出Q呈现不同的电平信号或发出脉冲信号。
L+一PG—P lM—L+为脉冲输入回路,PLC控制该回路中的发光二极管的亮灭,形成脉冲编码输入。
L+一NG—NP一1M—L+为电机旋转方向控制回路,当该回路的发光二极管点亮时,电机正转,否则反转。
为防止电流过大烧坏内部的发光二极管,需要外接电阻R,其阻值的计算如下:根据公式(1),可以选择R=3.9KO。
PLC控制伺服电机实例分析
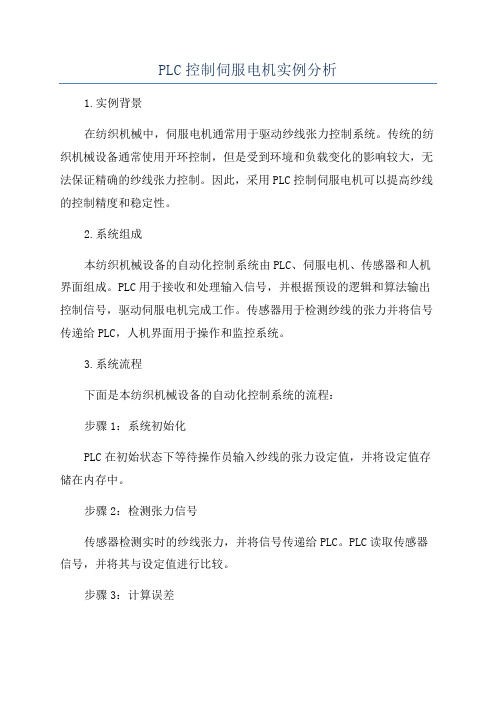
PLC控制伺服电机实例分析1.实例背景在纺织机械中,伺服电机通常用于驱动纱线张力控制系统。
传统的纺织机械设备通常使用开环控制,但是受到环境和负载变化的影响较大,无法保证精确的纱线张力控制。
因此,采用PLC控制伺服电机可以提高纱线的控制精度和稳定性。
2.系统组成本纺织机械设备的自动化控制系统由PLC、伺服电机、传感器和人机界面组成。
PLC用于接收和处理输入信号,并根据预设的逻辑和算法输出控制信号,驱动伺服电机完成工作。
传感器用于检测纱线的张力并将信号传递给PLC,人机界面用于操作和监控系统。
3.系统流程下面是本纺织机械设备的自动化控制系统的流程:步骤1:系统初始化PLC在初始状态下等待操作员输入纱线的张力设定值,并将设定值存储在内存中。
步骤2:检测张力信号传感器检测实时的纱线张力,并将信号传递给PLC。
PLC读取传感器信号,并将其与设定值进行比较。
步骤3:计算误差PLC将读取的传感器信号与设定值进行比较,并计算出误差。
误差是实际张力与设定值之间的差值。
通过计算误差,PLC可以决策如何调整伺服电机的运行状态。
步骤4:控制信号输出根据计算得到的误差,PLC将输出相应的控制信号给伺服电机。
控制信号的特点是它根据误差大小进行调整,使伺服电机的速度和方向能够满足预设的需求。
步骤5:伺服电机驱动伺服电机接收PLC的控制信号,并据此调整自己的运行状态。
伺服电机具有精确的速度和方向控制功能,可以根据控制信号精细调节自己的转速和转向,以达到精确的纱线张力控制。
步骤6:监控系统状态PLC会不断监控系统中各个组件的状态,并根据需要采取相应的措施。
如果系统出现异常或故障,PLC会发送警报信号并执行相应的应急程序。
步骤7:人机交互通过人机界面,操作员可以设定纱线的张力目标值、监控系统的状态、调整参数等。
人机界面可以提供实时数据显示和操作界面,使操作员能够方便地调整系统参数和监测系统状态。
以上就是PLC控制伺服电机的一个实例分析。
plc控制伺服电机毕业论文

plc控制伺服电机毕业论文PLC控制伺服电机毕业论文摘要:本文阐述了PLC控制伺服电机的基本原理,介绍了伺服电机的基本结构和特性,探讨了PLC在伺服电机控制中的应用及其优势,详细阐述了PLC控制伺服电机的具体实现方法,最后通过实验验证了PLC控制伺服电机的有效性和可行性。
关键词:PLC;伺服电机;控制;应用;优势一、引言伺服电机是一种精密、高性能的电动机,可以广泛应用于工业自动化、机床、机器人、医疗设备等众多领域。
伺服电机具有极高的控制精度和响应速度,可以精确控制电机的转速、转矩等参数,实现复杂的高精度运动控制。
PLC(可编程逻辑控制器)作为一种常见的工业控制器,也被广泛应用于各种自动化系统中。
PLC以其高效、稳定、可靠等优势,在伺服电机控制中也有着广泛的应用。
本文将从PLC控制伺服电机的基本原理、应用及优势、具体实现方法等方面进行探讨,并通过实验验证PLC控制伺服电机的有效性和可行性,以期为相关研究提供参考和借鉴。
二、伺服电机的基本结构和特性伺服电机是一种具有高精度、快速响应、可靠性高等特点的电机。
伺服电机通常采用电磁转子、光栅或编码器等装置,可以对转子位置、转速、转矩等参数进行高精度控制。
伺服电机常用的控制方式包括位置环控制、速度环控制、转矩环控制等,其中位置环控制的精度最高。
伺服电机具有响应速度快、精度高、适应性强等优点,广泛应用于自动控制系统、机器人等领域。
三、PLC在伺服电机控制中的应用及优势PLC作为一种常见的工业控制器,可以实现各种复杂的控制任务。
在伺服电机控制中,PLC也有着广泛的应用。
PLC在伺服电机控制中的应用包括位置控制、速度控制、转矩控制等。
PLC控制伺服电机的优势主要体现在以下几个方面:1.高精度控制PLC可以实现高精度的运动控制,通过编程控制伺服电机的转速、转矩、位置等参数,可以实现高精度的位置、速度、转矩控制。
2.快速响应PLC的响应速度快,可以实时控制伺服电机的运动状态,对于需要快速响应的应用场景尤为适用。
伺服应用案例之PLC控制篇复旦大学
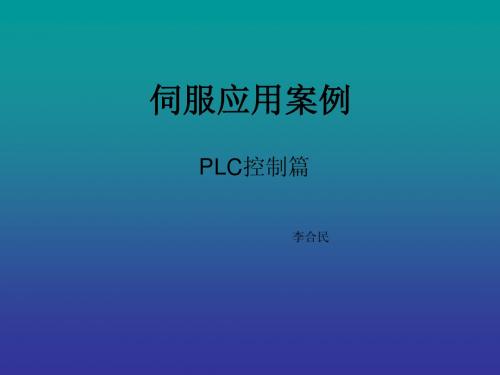
2、PLC实现控制的模式—三类
脉冲输出控制 模拟量输出控制 开关量输出控制
脉冲输出控制
1、集电极开路脉冲输出(24V) 主机模块自带,通常是两路输出,一共 4个段子,分别对应脉冲输出两个段子,方 向输出两个段子。 此时主机模块必须是晶体管输出型 2、差分脉冲输出(5V) 一般需要加差分脉冲输出扩展模块。
分切机
三、其他问题的解答
1、我们的伺服精度 2500线,4倍频,10000个脉冲转一圈, 精度达到万分之一转。 10000约=2E13 大于13位,小于14位。
• 2、我们伺服能不能进行自动增益调节 不能,但可以实现增益按条件自动切换, 我们可以称其为简单的自动增益调节
•
结束
运动控制板卡
工控板卡:研华、凌华、研祥
位置脉冲模式
位置脉冲模式------接收的是脉冲信号 (外部给定位置信号脉冲) (类似于变频器的脉冲调速) 脉冲信号种类:差分脉冲信号(5V) 集电极开路信号(24V)--PLC 脉冲信号形式: 脉冲+方向 正向脉冲+反向脉冲 正交脉冲
脉冲信号的形式
模拟量模式
模拟量模式---------接收的的是模拟量电压信 号(0-10V) (类似于变频器的模拟量调速) 模拟量转矩模式----控制力矩输出 模拟量速度模式----控制速度输出 (外部给定速度转矩值)
经编机改造
电子送经系统主要功能在于控制各种 纱线的送经速度及张力的控制,不至于将 纱线送断,造成断纱而无法进行织花。采 用plc、变频器、三相异步电机、伺服电机、 编码器等组成闭环控制,来实现主轴恒速 运转同时调节经轴转速,进而实现恒定送 经。
经编机改造原理图
纱盘1 纱线 纱线
M 织 机 变 频 器 M
基于PLC的全数字交流伺服位置控制
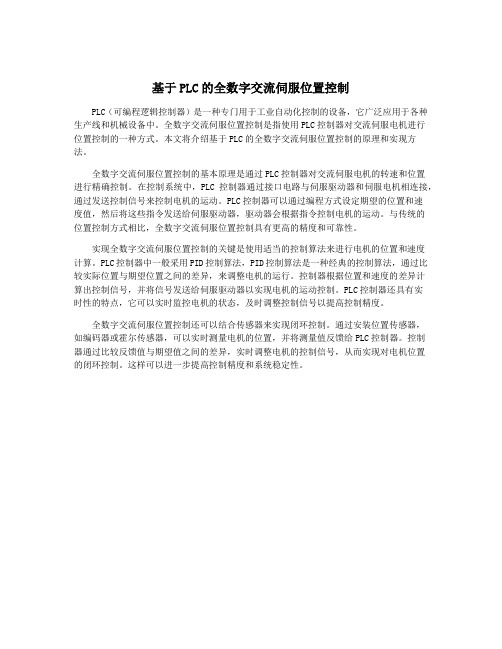
基于PLC的全数字交流伺服位置控制PLC(可编程逻辑控制器)是一种专门用于工业自动化控制的设备,它广泛应用于各种生产线和机械设备中。
全数字交流伺服位置控制是指使用PLC控制器对交流伺服电机进行位置控制的一种方式。
本文将介绍基于PLC的全数字交流伺服位置控制的原理和实现方法。
全数字交流伺服位置控制的基本原理是通过PLC控制器对交流伺服电机的转速和位置进行精确控制。
在控制系统中,PLC控制器通过接口电路与伺服驱动器和伺服电机相连接,通过发送控制信号来控制电机的运动。
PLC控制器可以通过编程方式设定期望的位置和速度值,然后将这些指令发送给伺服驱动器,驱动器会根据指令控制电机的运动。
与传统的位置控制方式相比,全数字交流伺服位置控制具有更高的精度和可靠性。
实现全数字交流伺服位置控制的关键是使用适当的控制算法来进行电机的位置和速度计算。
PLC控制器中一般采用PID控制算法,PID控制算法是一种经典的控制算法,通过比较实际位置与期望位置之间的差异,来调整电机的运行。
控制器根据位置和速度的差异计算出控制信号,并将信号发送给伺服驱动器以实现电机的运动控制。
PLC控制器还具有实时性的特点,它可以实时监控电机的状态,及时调整控制信号以提高控制精度。
全数字交流伺服位置控制还可以结合传感器来实现闭环控制。
通过安装位置传感器,如编码器或霍尔传感器,可以实时测量电机的位置,并将测量值反馈给PLC控制器。
控制器通过比较反馈值与期望值之间的差异,实时调整电机的控制信号,从而实现对电机位置的闭环控制。
这样可以进一步提高控制精度和系统稳定性。
伺服控制器与PLC的联动控制技术

伺服控制器与PLC的联动控制技术伺服控制器与PLC的联动控制技术是现代工业自动化领域中重要的技术之一。
伺服控制器是一种专门用于电机定位控制的装置,可以精确控制电机的位置、速度和力矩,而PLC(可编程逻辑控制器)则具有逻辑控制、数据处理和通信等功能,被广泛应用于工业自动化系统中。
将这两种控制器进行联动控制,可以实现更高级别的自动化生产过程,提高生产效率和产品质量。
在伺服控制器与PLC联动控制技术中,主要有三个方面需要考虑:通信接口、数据传输以及控制策略。
首先,通信接口是伺服控制器与PLC进行信息交换的关键。
目前常用的通信接口协议有串行通信协议和以太网通信协议。
串行通信协议常见的有RS-232和RS-485,具有简单和稳定的特点;而以太网通信协议具有传输速度快、可靠性高的优点。
选择适合系统需求的通信接口协议,是保证伺服控制器和PLC联动控制的基础。
其次,数据传输是伺服控制器与PLC之间信息交互的重要环节。
在联动控制中,PLC需要将控制信号传输给伺服控制器,伺服控制器将实时反馈的电机状态信息传输给PLC。
数据传输可以通过点对点连接、总线通信或者以太网通信等方式实现。
具体的传输方式可以根据系统结构和需求进行选择,以保证数据传输的实时性和稳定性。
最后,控制策略是伺服控制器与PLC联动控制的核心。
控制策略应根据具体的生产需求来进行设计。
通常,PLC负责整个生产线的逻辑控制、生产计划和数据处理等任务,而伺服控制器则负责电机的精确控制。
通过定时、协议、信号触发等方式,PLC可以发送指令给伺服控制器,实现对电机位置、速度和力矩的精细控制。
同时,伺服控制器可以实时感知电机的状态,并将反馈的信息传输给PLC进行数据处理和决策。
在伺服控制器与PLC联动控制技术的应用中,有很多成功的实际案例。
例如,在机械加工行业中,传统的数控加工中心通常使用伺服控制器和PLC单独进行控制,但通过联动控制技术,可以实现电机位置和刀具路径的动态匹配,提高加工精度和加工效率。
基于PLC的全数字交流伺服位置控制

基于PLC的全数字交流伺服位置控制
全数字交流伺服位置控制系统是一种基于PLC(可编程逻辑控制器)的控制系统,用于实现对伺服电机位置的精确控制。
该系统通过采集传感器数据、执行控制指令和反馈控制信号来实现对伺服电机位置的闭环控制。
本文将详细介绍基于PLC的全数字交流伺服位置控制系统的工作原理和实现方法。
全数字交流伺服位置控制系统由以下几个关键部分组成:传感器模块、PLC控制器、驱动器模块和伺服电机。
传感器模块用于采集伺服电机位置的反馈信号,常用的传感器包括编码器和位置传感器。
PLC控制器负责解析传感器数据、计算控制指令并发送给驱动器模块。
驱动器模块将控制指令转换成电压或电流信号,驱动伺服电机实现位置的精确控制。
全数字交流伺服位置控制系统具有以下几个优点:采用全数字控制和闭环控制结构,使得控制性能更加稳定和精确。
通过PLC控制器的编程,可以方便地实现不同位置控制算法的切换和参数调整。
PLC控制器具有多个输入输出接口,可以方便地与其他外部设备进行通信和联动控制。
在实际应用中,全数字交流伺服位置控制系统可以广泛应用于自动化生产线、机床加工和物流设备等领域。
在自动化生产线中,该系统可以用于控制机械臂的位置,实现对产品的高精度定位。
在机床加工中,该系统可以用于控制主轴的位置和转速,实现对零件的精确加工。
在物流设备中,该系统可以用于控制输送带的位置和速度,实现对物料的精确运输。
基于PLC的全数字交流伺服位置控制
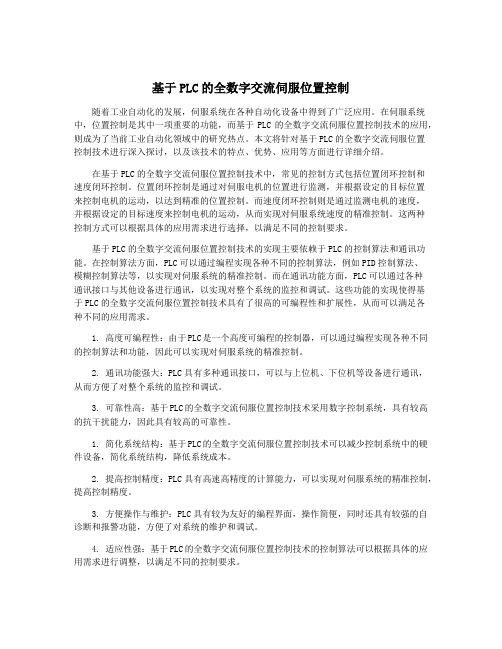
基于PLC的全数字交流伺服位置控制随着工业自动化的发展,伺服系统在各种自动化设备中得到了广泛应用。
在伺服系统中,位置控制是其中一项重要的功能,而基于PLC的全数字交流伺服位置控制技术的应用,则成为了当前工业自动化领域中的研究热点。
本文将针对基于PLC的全数字交流伺服位置控制技术进行深入探讨,以及该技术的特点、优势、应用等方面进行详细介绍。
在基于PLC的全数字交流伺服位置控制技术中,常见的控制方式包括位置闭环控制和速度闭环控制。
位置闭环控制是通过对伺服电机的位置进行监测,并根据设定的目标位置来控制电机的运动,以达到精准的位置控制。
而速度闭环控制则是通过监测电机的速度,并根据设定的目标速度来控制电机的运动,从而实现对伺服系统速度的精准控制。
这两种控制方式可以根据具体的应用需求进行选择,以满足不同的控制要求。
基于PLC的全数字交流伺服位置控制技术的实现主要依赖于PLC的控制算法和通讯功能。
在控制算法方面,PLC可以通过编程实现各种不同的控制算法,例如PID控制算法、模糊控制算法等,以实现对伺服系统的精准控制。
而在通讯功能方面,PLC可以通过各种通讯接口与其他设备进行通讯,以实现对整个系统的监控和调试。
这些功能的实现使得基于PLC的全数字交流伺服位置控制技术具有了很高的可编程性和扩展性,从而可以满足各种不同的应用需求。
1. 高度可编程性:由于PLC是一个高度可编程的控制器,可以通过编程实现各种不同的控制算法和功能,因此可以实现对伺服系统的精准控制。
2. 通讯功能强大:PLC具有多种通讯接口,可以与上位机、下位机等设备进行通讯,从而方便了对整个系统的监控和调试。
3. 可靠性高:基于PLC的全数字交流伺服位置控制技术采用数字控制系统,具有较高的抗干扰能力,因此具有较高的可靠性。
1. 简化系统结构:基于PLC的全数字交流伺服位置控制技术可以减少控制系统中的硬件设备,简化系统结构,降低系统成本。
2. 提高控制精度:PLC具有高速高精度的计算能力,可以实现对伺服系统的精准控制,提高控制精度。
基于PLC的全数字交流伺服位置控制
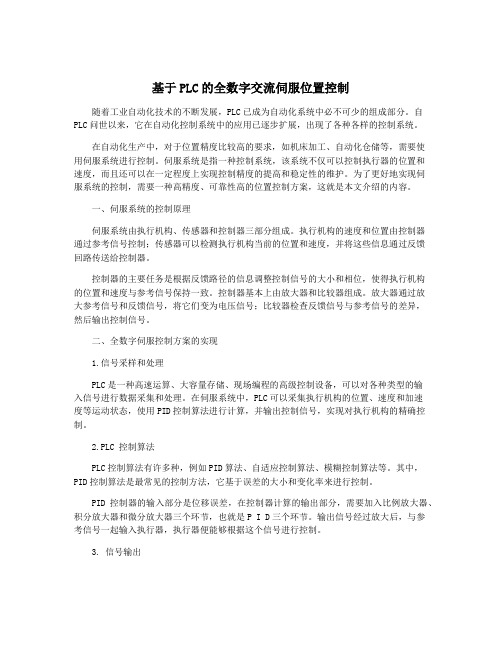
基于PLC的全数字交流伺服位置控制随着工业自动化技术的不断发展,PLC已成为自动化系统中必不可少的组成部分。
自PLC问世以来,它在自动化控制系统中的应用已逐步扩展,出现了各种各样的控制系统。
在自动化生产中,对于位置精度比较高的要求,如机床加工、自动化仓储等,需要使用伺服系统进行控制。
伺服系统是指一种控制系统,该系统不仅可以控制执行器的位置和速度,而且还可以在一定程度上实现控制精度的提高和稳定性的维护。
为了更好地实现伺服系统的控制,需要一种高精度、可靠性高的位置控制方案,这就是本文介绍的内容。
一、伺服系统的控制原理伺服系统由执行机构、传感器和控制器三部分组成。
执行机构的速度和位置由控制器通过参考信号控制;传感器可以检测执行机构当前的位置和速度,并将这些信息通过反馈回路传送给控制器。
控制器的主要任务是根据反馈路径的信息调整控制信号的大小和相位,使得执行机构的位置和速度与参考信号保持一致。
控制器基本上由放大器和比较器组成。
放大器通过放大参考信号和反馈信号,将它们变为电压信号;比较器检查反馈信号与参考信号的差异,然后输出控制信号。
二、全数字伺服控制方案的实现1.信号采样和处理PLC是一种高速运算、大容量存储、现场编程的高级控制设备,可以对各种类型的输入信号进行数据采集和处理。
在伺服系统中,PLC可以采集执行机构的位置、速度和加速度等运动状态,使用PID控制算法进行计算,并输出控制信号,实现对执行机构的精确控制。
2.PLC 控制算法PLC控制算法有许多种,例如PID算法、自适应控制算法、模糊控制算法等。
其中,PID控制算法是最常见的控制方法,它基于误差的大小和变化率来进行控制。
PID控制器的输入部分是位移误差,在控制器计算的输出部分,需要加入比例放大器、积分放大器和微分放大器三个环节,也就是P I D三个环节。
输出信号经过放大后,与参考信号一起输入执行器,执行器便能够根据这个信号进行控制。
3. 信号输出在控制信号计算完成后,需要将控制信号转换为电流或电压信号,输出给执行机构,可以采用PWM调制技术或DAC转换技术来实现这一步骤。
基于PLC的全数字交流伺服位置控制
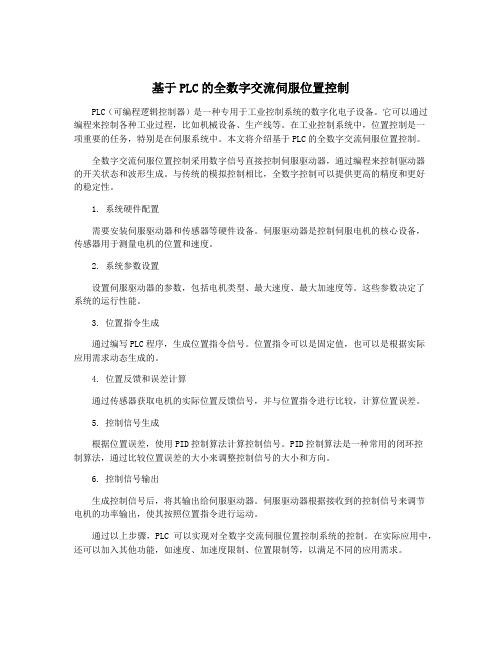
基于PLC的全数字交流伺服位置控制PLC(可编程逻辑控制器)是一种专用于工业控制系统的数字化电子设备。
它可以通过编程来控制各种工业过程,比如机械设备、生产线等。
在工业控制系统中,位置控制是一项重要的任务,特别是在伺服系统中。
本文将介绍基于PLC的全数字交流伺服位置控制。
全数字交流伺服位置控制采用数字信号直接控制伺服驱动器,通过编程来控制驱动器的开关状态和波形生成。
与传统的模拟控制相比,全数字控制可以提供更高的精度和更好的稳定性。
1. 系统硬件配置需要安装伺服驱动器和传感器等硬件设备。
伺服驱动器是控制伺服电机的核心设备,传感器用于测量电机的位置和速度。
2. 系统参数设置设置伺服驱动器的参数,包括电机类型、最大速度、最大加速度等。
这些参数决定了系统的运行性能。
3. 位置指令生成通过编写PLC程序,生成位置指令信号。
位置指令可以是固定值,也可以是根据实际应用需求动态生成的。
4. 位置反馈和误差计算通过传感器获取电机的实际位置反馈信号,并与位置指令进行比较,计算位置误差。
5. 控制信号生成根据位置误差,使用PID控制算法计算控制信号。
PID控制算法是一种常用的闭环控制算法,通过比较位置误差的大小来调整控制信号的大小和方向。
6. 控制信号输出生成控制信号后,将其输出给伺服驱动器。
伺服驱动器根据接收到的控制信号来调节电机的功率输出,使其按照位置指令进行运动。
通过以上步骤,PLC可以实现对全数字交流伺服位置控制系统的控制。
在实际应用中,还可以加入其他功能,如速度、加速度限制、位置限制等,以满足不同的应用需求。
基于PLC的全数字交流伺服位置控制可以实现高精度、高稳定性的位置控制,适用于各种工业应用场景。
它提供了灵活的编程方式和强大的控制功能,可以满足不同的应用需求。
用PLC完成对伺服轴的运动控制
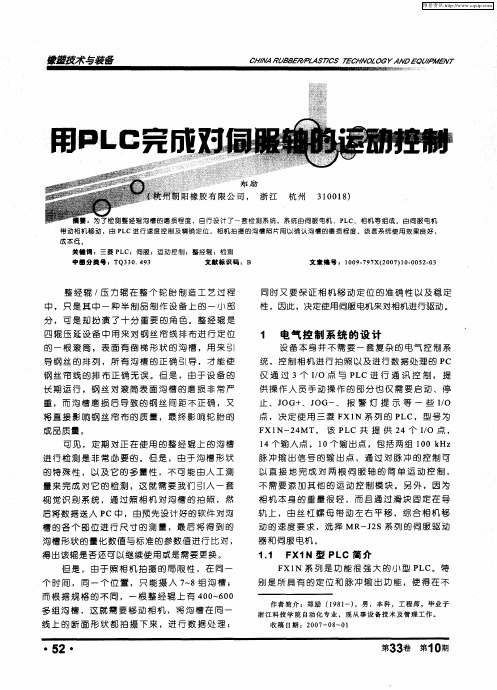
不 需 要 添 加 其他 的 运 动 控 制 模 块 。 另 外 ,因为
相 机 本 身 的 重 量 很 轻 ,而 且 通 过 滑 块 固 定 在 导
轨 上 ,由 丝 杠 螺 母 带 动 左 右 平 移 ,综 合 相 机 移 动 的 速 度要 求 ,选 择 MR- 2 J S系 列 的伺 服 驱 动 器和 伺服 电机 。
・
11 F . X1 N型 P C简 介 L
F N 系 列 是 功 能 很 强 大 的 小 型 P C。特 X1 L 别 是 所 具有 的定 位 和 脉 ; 出 功 能 ,使 得 在 不 中输
作 者简 介 :郑 励 ( 9 一) 1 81 ,男 ,本科 ,工程 师, 毕业于
浙 江 科 技 学 院 自动 化 专 业 ,现 从 事 设 备 技 术 及 管 理 工 作 。 收 稿 日期 : 2 0 -0 -01 07 8
中 田 分 类号 tTQ3 0 4 3 3 . 9 文 献 标 识 码 :B 文 章 编 号 。 l 0 —9 X( 0 7 l -0 2 0 0 9 7 7 2 0 )0 0 5 -3
整 经 辊 / 力 辊 在 整 个 轮 胎 制 造 工 艺过 程 压 中 ,只 是 其 中 一种 半 制 品 制作 设 备 上 的 一小 部 分 ,可 是 却 扮 演 了十 分 重 要 的 角 色 。整 经 辊 是 四 辊压 延 设备 中 用来 对 钢 丝 帘 线排 布进 行 定位 的 一根 滚 筒 ,表 面 有 倒 梯 形 状 的 沟 槽 ,用 来 引 导 钢 丝 的排 列 ,所 有 沟 槽 的 正 确 引 导 ,才 能 使
沟槽 形 状 的量 化 数值 与 标准 的 参数 值 进行 比对 ,
得 出该辊是 否 还可 以 继续使 用 或是 需要 更换 。 但 是 ,由 于 照 相 机 拍 摄 的 局 限 性 ,在 同 一 个 时 间 ,同 一 个 位 置 ,只 能 摄 人 7 8组 沟 槽 ;  ̄ 而 根 据 规 格 的不 同 ,一根 整 经 辊 上 有 4 0 6 0 0  ̄ 0 多 组 沟 槽 ,这 就 需 要 移 动 相 机 ,将 沟 槽在 同 一 线 上 的 断 面 形 状 都 拍 摄 下 来 ,进 行 数 据 处 理 ;
伺服驱动的PLC控制
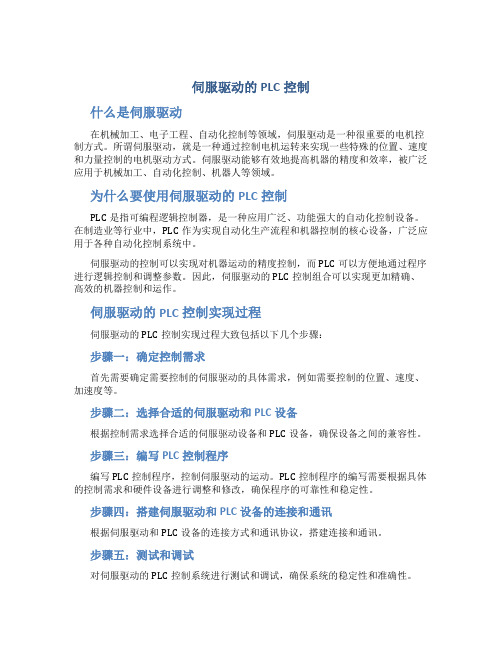
伺服驱动的PLC控制什么是伺服驱动在机械加工、电子工程、自动化控制等领域,伺服驱动是一种很重要的电机控制方式。
所谓伺服驱动,就是一种通过控制电机运转来实现一些特殊的位置、速度和力量控制的电机驱动方式。
伺服驱动能够有效地提高机器的精度和效率,被广泛应用于机械加工、自动化控制、机器人等领域。
为什么要使用伺服驱动的PLC控制PLC是指可编程逻辑控制器,是一种应用广泛、功能强大的自动化控制设备。
在制造业等行业中,PLC作为实现自动化生产流程和机器控制的核心设备,广泛应用于各种自动化控制系统中。
伺服驱动的控制可以实现对机器运动的精度控制,而PLC可以方便地通过程序进行逻辑控制和调整参数。
因此,伺服驱动的PLC控制组合可以实现更加精确、高效的机器控制和运作。
伺服驱动的PLC控制实现过程伺服驱动的PLC控制实现过程大致包括以下几个步骤:步骤一:确定控制需求首先需要确定需要控制的伺服驱动的具体需求,例如需要控制的位置、速度、加速度等。
步骤二:选择合适的伺服驱动和PLC设备根据控制需求选择合适的伺服驱动设备和PLC设备,确保设备之间的兼容性。
步骤三:编写PLC控制程序编写PLC控制程序,控制伺服驱动的运动。
PLC控制程序的编写需要根据具体的控制需求和硬件设备进行调整和修改,确保程序的可靠性和稳定性。
步骤四:搭建伺服驱动和PLC设备的连接和通讯根据伺服驱动和PLC设备的连接方式和通讯协议,搭建连接和通讯。
步骤五:测试和调试对伺服驱动的PLC控制系统进行测试和调试,确保系统的稳定性和准确性。
伺服驱动的PLC控制的应用伺服驱动的PLC控制被广泛应用于各种机器控制和自动化控制领域,例如:•机床加工控制•包装机械控制•机器人控制•自动化生产线控制在这些领域中,伺服驱动的PLC控制通过实现对机器位置、速度、加速度等的精确控制,提高了机器的精度和效率,使生产过程更加自动化、高效。
伺服驱动的PLC控制作为一种有效的控制方式,在自动化控制领域中得到了广泛的应用。