烧结法硅渣烧成工试验研究艺
硅渣提炼工艺
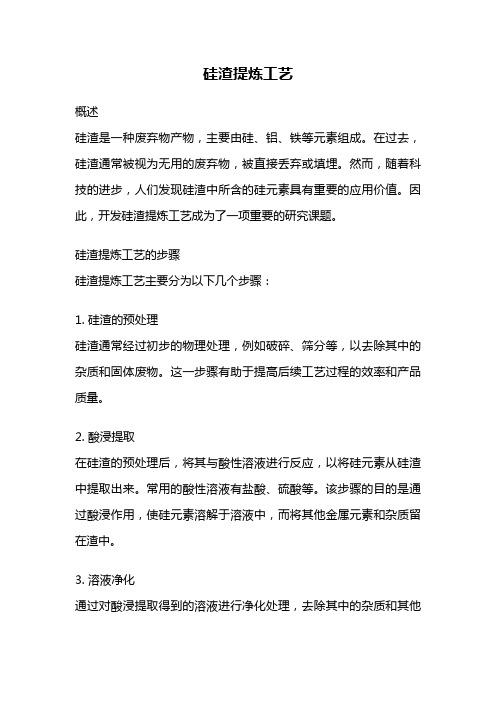
硅渣提炼工艺概述硅渣是一种废弃物产物,主要由硅、铝、铁等元素组成。
在过去,硅渣通常被视为无用的废弃物,被直接丢弃或填埋。
然而,随着科技的进步,人们发现硅渣中所含的硅元素具有重要的应用价值。
因此,开发硅渣提炼工艺成为了一项重要的研究课题。
硅渣提炼工艺的步骤硅渣提炼工艺主要分为以下几个步骤:1. 硅渣的预处理硅渣通常经过初步的物理处理,例如破碎、筛分等,以去除其中的杂质和固体废物。
这一步骤有助于提高后续工艺过程的效率和产品质量。
2. 酸浸提取在硅渣的预处理后,将其与酸性溶液进行反应,以将硅元素从硅渣中提取出来。
常用的酸性溶液有盐酸、硫酸等。
该步骤的目的是通过酸浸作用,使硅元素溶解于溶液中,而将其他金属元素和杂质留在渣中。
3. 溶液净化通过对酸浸提取得到的溶液进行净化处理,去除其中的杂质和其他金属元素。
常用的净化方法包括氧化、沉淀、过滤等。
这一步骤的目的是提高溶液中硅元素的纯度,以便后续的提纯工艺。
4. 硅元素的提纯对经过净化处理的溶液进行进一步的提纯,以获得高纯度的硅元素。
常用的提纯方法有电解法、熔盐电解法等。
这些方法能够将溶液中的杂质和其他金属元素进一步去除,从而获得纯度较高的硅元素。
5. 产品制备经过硅元素的提纯后,可以通过熔炼、晶体生长等方法制备硅单晶、硅棒、硅片等产品,用于半导体、太阳能电池、光纤通信等领域。
硅渣提炼工艺的优势与挑战硅渣提炼工艺具有以下优势:1. 资源利用:通过提炼硅渣,可以将其中的硅元素回收利用,减少资源浪费。
2. 环境友好:硅渣提炼工艺能够减少对环境的污染,避免硅渣被直接丢弃或填埋带来的环境问题。
然而,硅渣提炼工艺也面临一些挑战:1. 工艺复杂:硅渣中含有多种金属元素和杂质,提炼过程需要经过多个步骤,工艺复杂。
2. 能耗较高:硅渣提炼工艺需要消耗大量的能源,增加了生产成本和环境负担。
未来发展趋势随着科技的不断进步,硅渣提炼工艺也在不断发展。
未来的发展趋势主要包括以下几个方面:1. 工艺改进:研究人员将继续改进硅渣提炼工艺,提高工艺的效率和产品的质量,降低能耗和成本。
包钢铁精矿低硅烧结的实验研究
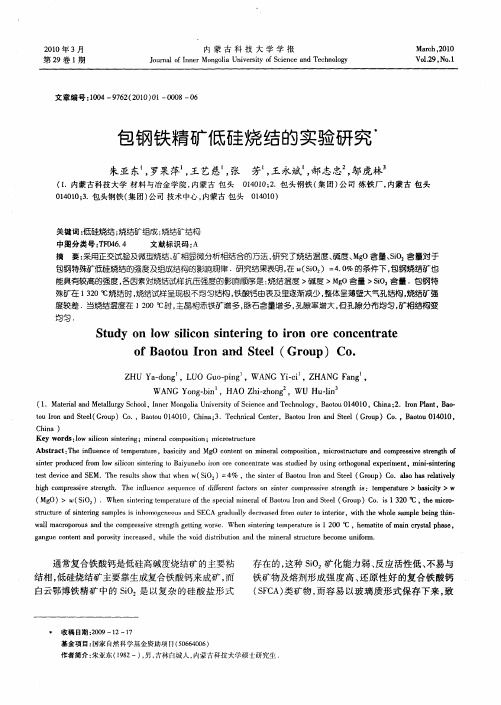
Ma c 2 l r h.0 O V0.9. o 1 1 2 N.
文 章编 号 :04—96 (0 0 0 — 0 8— 6 10 72 2 1 ) 1 0 0 0
包 钢铁精 矿低 硅 烧 结的 实验研 究
朱亚 东‘罗果萍 王艺慈‘张 芳‘王永斌‘郝 志忠 , , , , , , 邬虎林。
殊矿在 130 c 2 烧结时 , 烧结试样呈现极不均匀结构 , 铁酸钙 由表及里逐渐减少 , 整体呈薄壁大 气孔结构 , 烧结矿强
度较差 . 当烧结温度在 1 0 0℃时 , 2 主晶相赤铁矿增多 , 含量增多 , 脉石 孔隙率增大 , 但孔隙分布均匀 , 矿相结构 变
均匀 .
S u y o o sl o i t r n o i o r o c n r t t d n l w i c n sn e i g t r n o e c n e t a e i
中图 分 类 号 :F 4 . T 06 4 文 献标 识码 : A
摘
要: 采用正交试验及微型烧结、 矿相显微分析相结合的方法 , 究了烧结温度 、 研 碱度 、 g M O含量 、i: SO 含量对 于
包钢特殊矿低硅烧结的强度及组成结构的影响规律 . 研究结果表明 , w SO) = .%的条 件下 , 在 (i: 40 包钢烧结矿也 能具有较高的强度 , 各因素对烧结试样抗压强度 的影O I I ̄ NI序是 : 结温度 >碱度 >Mg 烧 O含量 >SO 含 量 .包钢特 i
( .内蒙古科技大学 材料与冶金学 院 , 1 内蒙古 包头 0 4 1 ;.包头钢铁 ( 团) 司 炼 铁厂 , 10 0 2 集 公 内蒙 古 包头
041) 10 0 0 4 1 ;.包 头 钢 铁 ( 团 ) 司 技 术 中心 , 100 3 集 公 内蒙 古 包 头
氧化铝冶炼工艺流程简介
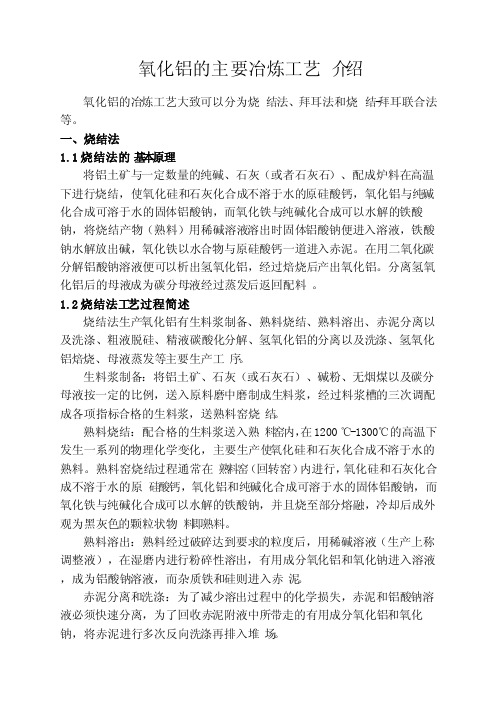
氧化铝的主要冶炼工艺介绍氧化铝的冶炼工艺大致可以分为烧结法、拜耳法和烧结-拜耳联合法等。
一、烧结法1.1烧结法的基本原理将铝土矿与一定数量的纯碱、石灰(或者石灰石)、配成炉料在高温下进行烧结,使氧化硅和石灰化合成不溶于水的原硅酸钙,氧化铝与纯碱化合成可溶于水的固体铝酸钠,而氧化铁与纯碱化合成可以水解的铁酸钠,将烧结产物(熟料)用稀碱溶液溶出时固体铝酸钠便进入溶液,铁酸钠水解放出碱,氧化铁以水合物与原硅酸钙一道进入赤泥。
在用二氧化碳分解铝酸钠溶液便可以析出氢氧化铝,经过焙烧后产出氧化铝。
分离氢氧化铝后的母液成为碳分母液经过蒸发后返回配料。
1.2烧结法工艺过程简述烧结法生产氧化铝有生料浆制备、熟料烧结、熟料溶出、赤泥分离以及洗涤、粗液脱硅、精液碳酸化分解、氢氧化铝的分离以及洗涤、氢氧化铝焙烧、母液蒸发等主要生产工序。
生料浆制备:将铝土矿、石灰(或石灰石)、碱粉、无烟煤以及碳分母液按一定的比例,送入原料磨中磨制成生料浆,经过料浆槽的三次调配成各项指标合格的生料浆,送熟料窑烧结。
熟料烧结:配合格的生料浆送入熟料窑内,在1200℃-1300℃的高温下发生一系列的物理化学变化,主要生产使氧化硅和石灰化合成不溶于水的熟料。
熟料窑烧结过程通常在熟料窑(回转窑)内进行,氧化硅和石灰化合成不溶于水的原硅酸钙,氧化铝和纯碱化合成可溶于水的固体铝酸钠,而氧化铁与纯碱化合成可以水解的铁酸钠,并且烧至部分熔融,冷却后成外观为黑灰色的颗粒状物料即熟料。
熟料溶出:熟料经过破碎达到要求的粒度后,用稀碱溶液(生产上称调整液),在湿磨内进行粉碎性溶出,有用成分氧化铝和氧化钠进入溶液,成为铝酸钠溶液,而杂质铁和硅则进入赤泥。
赤泥分离和洗涤:为了减少溶出过程中的化学损失,赤泥和铝酸钠溶液必须快速分离,为了回收赤泥附液中所带走的有用成分氧化铝和氧化钠,将赤泥进行多次反向洗涤再排入堆场。
烧结法的原理和基本流程

烧结法的原理和基本流程第一节烧结法的原理随着矿石铝硅比的降低,拜耳法生产氧化铝的经济效果明显恶化。
对于铝硅比低于7的矿石,单纯的拜耳法就不适用了。
处理铝硅比在4以下的矿石,碱石灰烧结法几乎是唯一得到实际应用的方法。
在处理SiO2含量更高的其它炼铝原料时,如霞石、绢云母以及正长石时,它也得到应用,可以同时制取氧化铝、钾肥和水泥等产品,实现了原料的综合利用。
据报导,国外以霞石为原料的烧结法企业,由于原料综合利用,实现了无废料生产,氧化铝的生产成本反而最低。
在我国已经查明的铝矿资源中,高硅铝土矿占有很大的数量,因而烧结法对于我国氧化铝工业具有很重要的意义。
我国第一座氧化铝厂——山东铝厂就是采用碱石灰烧结法生产的。
它在改进和发展碱石灰烧结法方面作出了许多贡献,其Al2O3的总回收率,碱耗等指标都居于世界先进水平。
法国人勒·萨特里在1858年提出了碳酸钠烧结法,即用碳酸钠和铝土矿烧结,得到含固体铝酸钠Na2O· Al2O3的烧结产物。
这种产物称为熟料或烧结块,将其用稀碱溶液溶出便可以得到铝酸钠溶液。
往溶液中通入CO2气体,即可析出氢氧化铝。
残留在溶液中的主要是碳酸钠,可以再循环使用。
这种方法,原料中的SiO2仍然是以铝硅酸钠的形式转入泥渣,而成品氧化铝质量差,流程复杂,耗热量大,所以拜耳法问世后,此法就被淘汰了。
用碳酸钠和石灰石按一定比例与铝土矿烧结,可以在很大程度上减轻SiO2的危害,使Al2O3和Na2O的损失大大减少。
这样就形成了碱石灰烧结法。
在处理高硅铝土矿时,它比拜耳法比越。
除了这两种烧结法外,还有单纯用石灰与矿石烧结的石灰烧结法,它比较适用干处理粘土类原料,特别是含有一定可燃成分的煤矸石、页岩等。
这时原料中的Al 2O 3,烧结成铝酸钙,经碳酸钠溶液溶出后,可得到铝酸钠溶液。
目前用在工业上的只有碱石灰烧结法。
它所处理的原料有铝土矿、霞石和拜耳法赤泥。
这些炉料分别称为铝土矿炉料。
低铝硅比烧结工艺研究
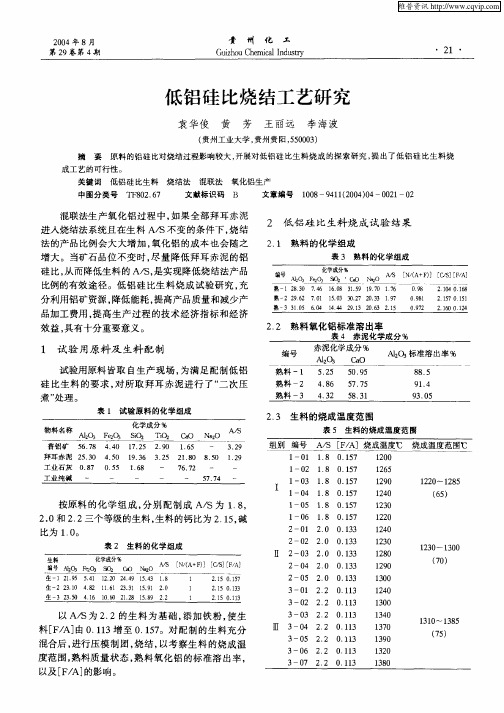
32 低 铝硅 比生料烧 成的可行性 .
混联 法生产 氧化 铝 , 过 降低拜 耳 法赤 泥铝 硅 通
比, 用低 A/ 采 S生 料烧 成 , 就可 以减 少烧 结法 产 品
A , 高熟料 质量和氧化铝溶 出率有较好效 果 。 ]对提
4 结 语
的 比例 , 大拜耳 法生 产 比例 , 而 降低 能耗 , 少 增 从 减
分利 用铝矿资源 , 降低能耗 , 提高产品质 量和减少产 品加 工费用 , 生产 过程 的技术 经 济指 标 和经济 提高 效益, 具有 十分重要意义 。
2 2 熟料氧化 铝标准溶 出率 .
表 4 赤泥 化 学成 分 %
1 试验 用原 料及 生料 配制
试验用原 料 皆取 自生 产现 场 , 为满 足 配制低 铝
通常认为 , 随着熟料 A S的降低 , / 烧成温 度低 , 烧成温 度范 围变窄 , 物料粘 度增 大 , 烧成 过程 的物理
化学 反应 不能充分 进行 , 而且还会 造成窑 的结 圈 , 使 烧成窑 的操 作难 度增 大 。生产 实践 证 明 , 采取 一定 的技术 措 施 , 以克服 低 A S生 料 烧成 的 困难 , 可 / 烧
( p r n f c nlg , i o rsa C e cl o pC . Ld Qighn Guz o 5 4 2 Deat t h ooy Guz uC yt1 hmi u o , t, n z e , i u5 10 ) me o Te h a Gr h
粉煤灰烧结法化验项目及方法
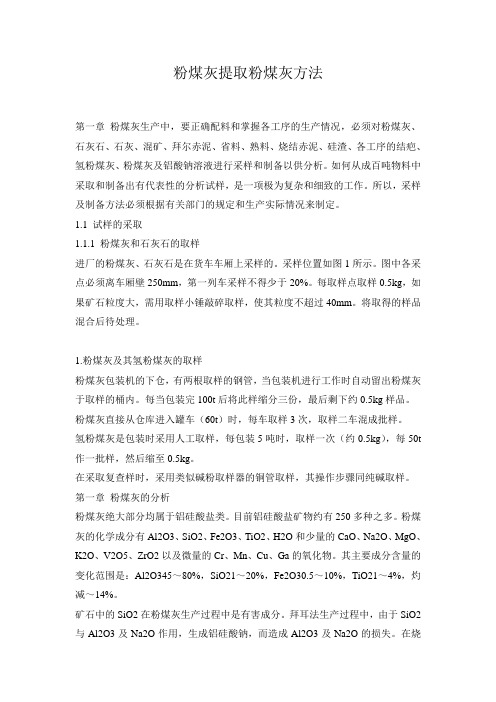
粉煤灰提取粉煤灰方法第一章粉煤灰生产中,要正确配料和掌握各工序的生产情况,必须对粉煤灰、石灰石、石灰、混矿、拜尔赤泥、省料、熟料、烧结赤泥、硅渣、各工序的结疤、氢粉煤灰、粉煤灰及铝酸钠溶液进行采样和制备以供分析。
如何从成百吨物料中采取和制备出有代表性的分析试样,是一项极为复杂和细致的工作。
所以,采样及制备方法必须根据有关部门的规定和生产实际情况来制定。
1.1 试样的采取1.1.1 粉煤灰和石灰石的取样进厂的粉煤灰、石灰石是在货车车厢上采样的。
采样位置如图1所示。
图中各采点必须离车厢壁250mm,第一列车采样不得少于20%。
每取样点取样0.5kg,如果矿石粒度大,需用取样小锤敲碎取样,使其粒度不超过40mm。
将取得的样品混合后待处理。
1.粉煤灰及其氢粉煤灰的取样粉煤灰包装机的下仓,有两根取样的钢管,当包装机进行工作时自动留出粉煤灰于取样的桶内。
每当包装完100t后将此样缩分三份,最后剩下约0.5kg样品。
粉煤灰直接从仓库进入罐车(60t)时,每车取样3次,取样二车混成批样。
氢粉煤灰是包装时采用人工取样,每包装5吨时,取样一次(约0.5kg),每50t 作一批样,然后缩至0.5kg。
在采取复查样时,采用类似碱粉取样器的铜管取样,其操作步骤同纯碱取样。
第一章粉煤灰的分析粉煤灰绝大部分均属于铝硅酸盐类。
目前铝硅酸盐矿物约有250多种之多。
粉煤灰的化学成分有Al2O3、SiO2、Fe2O3、TiO2、H2O和少量的CaO、Na2O、MgO、K2O、V2O5、ZrO2以及微量的Cr、Mn、Cu、Ga的氧化物。
其主要成分含量的变化范围是:Al2O345~80%,SiO21~20%,Fe2O30.5~10%,TiO21~4%,灼减~14%。
矿石中的SiO2在粉煤灰生产过程中是有害成分。
拜耳法生产过程中,由于SiO2与Al2O3及Na2O作用,生成铝硅酸钠,而造成Al2O3及Na2O的损失。
在烧结法生产过程中,为了除去SiO2,必须添加大量的石灰石或石灰,使之生成不溶性的硅酸钙,因而降低了设备的产能。
从硅渣中提取工业硅的新方法
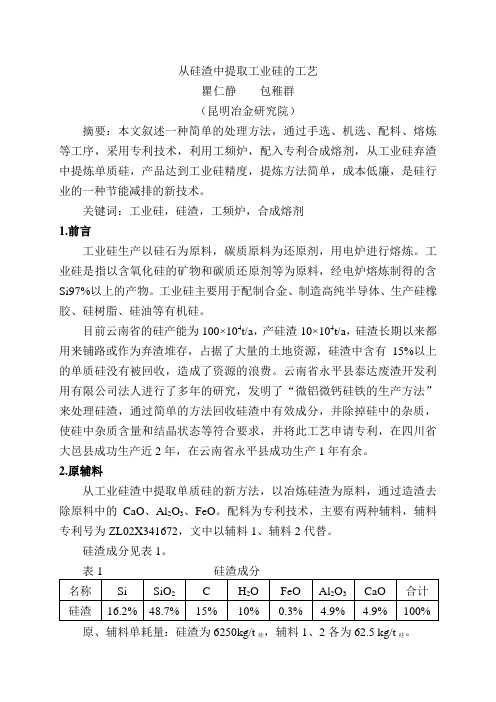
从硅渣中提取工业硅的工艺瞿仁静包稚群(昆明冶金研究院)摘要:本文叙述一种简单的处理方法,通过手选、机选、配料、熔炼等工序,采用专利技术,利用工频炉,配入专利合成熔剂,从工业硅弃渣中提炼单质硅,产品达到工业硅精度,提炼方法简单,成本低廉,是硅行业的一种节能减排的新技术。
关键词:工业硅,硅渣,工频炉,合成熔剂1.前言工业硅生产以硅石为原料,碳质原料为还原剂,用电炉进行熔炼。
工业硅是指以含氧化硅的矿物和碳质还原剂等为原料,经电炉熔炼制得的含Si97%以上的产物。
工业硅主要用于配制合金、制造高纯半导体、生产硅橡胶、硅树脂、硅油等有机硅。
目前云南省的硅产能为100×104t/a,产硅渣10×104t/a,硅渣长期以来都用来铺路或作为弃渣堆存,占据了大量的土地资源,硅渣中含有15%以上的单质硅没有被回收,造成了资源的浪费。
云南省永平县泰达废渣开发利用有限公司法人进行了多年的研究,发明了“微铝微钙硅铁的生产方法”来处理硅渣,通过简单的方法回收硅渣中有效成分,并除掉硅中的杂质,使硅中杂质含量和结晶状态等符合要求,并将此工艺申请专利,在四川省大邑县成功生产近2年,在云南省永平县成功生产1年有余。
2.原辅料从工业硅渣中提取单质硅的新方法,以冶炼硅渣为原料,通过造渣去除原料中的CaO、Al2O3、FeO。
配料为专利技术,主要有两种辅料,辅料专利号为ZL02X341672,文中以辅料1、辅料2代替。
硅渣成分见表1。
表1 硅渣成分原、辅料单耗量:硅渣为6250kg/t硅,辅料1、2各为62.5 kg/t硅。
3工业硅的杂质来源和性质工业硅中的杂质以单质和化合物的形态存在。
热力学计算表明,Fe2O3、SiO2、MgO、Al2O3、CaO等在常压下还原时,Fe2O3还原温度最低,其次是SiO2,再次是Al2O3、MgO和CaO。
因为还原温度不同,Fe2O3、SiO2绝大部分被还原,Al2O3、MgO和CaO只能部分还原。
提高高铁低硅烧结矿强度的实验研究

提高高铁低硅烧结矿强度的实验研究周国凡!杨!福!湖北省钢铁冶金重点实验室武汉科技大学"湖北武汉!"##$%#摘!要!在实验室条件下"对高铁低硅烧结原料"采用提高生石灰配比$燃料外配等措施"进行了旨在提高烧结矿强度和生产率等指标的实验研究%实验结果表明&全部用生石灰替代石灰石进行烧结"可提高烧结矿转鼓强度’用"#&的燃料外配时"可略微提高烧结生产率%关键词!烧结’高铁低硅’生石灰配比’燃料外配’转鼓强度中图分类号!’()*!!文献标识码!+!!文章编号!%##%,%!!-!*##-##*,###%,#"!"#$%&’$()*+,)-./0(&’#%01&(2)3$,)%$(2)3043&23&%0(*(.+056&7*,&()$%./01234,567"8+92(3!/3:;<=>47?6@<7A 67BC D ;;E ?6@<7A F ;G H 6:4>6D 4>G "I 3J 6717<K ;>L <D G 45C M <;7M ;67B ’;M J 74E 4A G "I 3J 67!"##$%"N J <76#89,)%*:)&(4>J <A J <>4767B E 4OC <0*L <7D ;><7A ?<P "67;P Q ;><?;7D 6E L D 3B G O 6L?6B ;<7E 6:4>6D 4>G 6<?<7A D 4<?Q >4K ;D J ;L D >;7A D J 67B Q >4B 3M D <K <D G 45L <7D ;>:G ?;67L 45D ;M J 74,E 4A <M 6E?;6L 3>;L L 3M J 6L <7M >;6L <7A D J ;:E ;7B >6D <445:3>7D E <?;67B 6Q Q ;7B <7A 6B B <D <47,6E 53;E R S P Q ;><?;7D 6E >;L 3E D L L J 4OD J 6D 3L <7A %##&:3>7D E <?;D 4>;Q E 6M ;E <?;L D 47;M 67<7M >;6L ;L <7D ;>L D >;7A D J67B <7D J ;M 47B <D <4745"#&6Q Q ;7B <7A 6B B <D <476E 53;E D J ;Q >4,B 3M D <K <D G <L <?Q >4K ;B L E <A J D E G R ;$/50%.,&L <7D ;><7A ’J <A J <>4767B E 4OC <0*’:E ;7B >6D <445:3>7D E <?;’6Q Q ;7B <7A 6B B <,D <476E 53;E ’B >3?,D ;L D L D >;7AD J 作者简介!周国凡!%T )*U #"男"武汉人"高级工程师"主要从事冶金技术研究R !!高铁低C <0*烧结矿的生产"促进了高炉冶炼的节焦增铁%但烧结原料中!!C <0*#降至)R #&以下之后"且烧结矿碱度一定时"烧结生产就会面临生产率降低$强度和还原粉化恶化等问题(%)%究其原因"是同时降低!!C <0*#和!!N 60#后"烧结过程中硅酸盐粘结相数量的减少"使得烧结矿局部区域矿物颗粒之间仅靠点接触粘结"呈松散状结构"加之再生赤铁矿增加"气孔率上升所致%本文在实验室条件下"以烧制!!’(;#V )$R )#&$"V %R $#倍的高碱度烧结矿为基准"采用提高生石灰配比$煤粉外配等措施"进行了提高高铁低硅烧结矿转鼓强度$改善生产率等技术经济指标的试验研究%!!试验方法试验是在烧结实验室中进行的%烧结杯规格为!*##??W X ##??%试验按烧结原料混合$加水造球$测混合料粒度$装入烧结杯$测料层透气性指数$点火$烧结$落下摔打$粒度筛分$测定转鼓强度等常规过程进行%烧结原料取自生产现场"混合料配比$烧结时的各工艺参数均参考武钢烧结厂现场近期生产实践为原型%烧结主要原$燃料成分及混合料配比见表%%按表%数据计算"烧结矿的成分为!!’(;#V )$R )#&$"V %R $#$!!C <0*#V!R X #&$!!N 60#V$R "#&$!!Y A0#V *R %&左右%"!提高生石灰配比的试验本试验方法为&逐步提高混合料中生石灰配比"直至用生石灰完全取代石灰石来保证烧结矿%R $#倍的碱度%以混合料的粒度组成$透气性指数$成品烧结矿的转鼓强度$生产率来考察生石灰配比的影响%试验结果见表*和图%%*!**##-年!!月第")卷第*期钢铁研究Z ;L ;6>M J47=>47[C D ;;E!!+Q>R *##-\4E R ")!94R *!!!!!!!!万方数据表%!烧结原料的成分!!]"及配比矿!!种配比!&成!!!分!&’(;C <0*N 60Y A 0/*0烧损!&精矿粉%T R ##"%T R )#X "R !*X R #$!R %$*R %T X R ###R #*澳大利亚矿"*R -#"""R ##X !R %!"R X $#R $*#R *#"R ##"R *$巴西矿*#R )#X -R #)%R $T #R $T #R %%!R --%R )T 海南矿$R ##)!R %)%*R !#"R "$*R *$"R ##*R *%白云石X R ###R ##%R X X "!R )#%$R *#*R #%"X R -#石灰石#R ##"-R $##R ##%R $#)%R X #%R ""%R -X !"R "#消石灰#R ##"X R $##R ##"R "*X %R -#%R *#%$R #!"X R %#煤!粉X R ###R ##!R *"#R --#R ##-R X X$T R !#表*!不同生石灰配比的试验结果生石灰配比!&混合料!"/*0#!&造球后"*??球比例!&成球性指数!&透气性指数!&烧结速度!"??$?<7U %#成品率!&生产率!"D$?U *$J U %#转鼓强度!&#X R **X R X *)R -%%R %%T R $"$*R #"%R $*-X %R --%R #X R !"X R X )*R *%%R T %T R T "$*R %%%R $T "X %R -$"R #X R -)*R "X !R "%*R X %T R -T $*R *X %R $)X X !R )*)R #-R %X )R "-T R %%!R )*#R X #$*R ))%R $X X X )R #)X R $$R "X $R !$"R )%!R $*%R #)$*R X -%R $")X X R #%X R $$R XX $R X$*R -%!R -*#R -X$*R !T%R $!*X )R --!!试验结果表明%随生石灰配比从#至X R $&"生石灰全部替代石灰石#的逐步增加&混合料的成球性指数也随之得以提高&造球后粒径大于*??的小球比例从*X R X &提高到最高时的X $R X &’烧结料层透气性指数由%%R %&提高至%!R -&’烧结后成品烧结矿的转鼓强度指数也随之趋高’当生石灰配比为X R $&(煤粉配比为X R #&(混合料水分为$R #&左右的条件下&烧结矿转鼓强度指数从最初的X %R --&提高到X X R #%&’因此&对高铁低C <0*烧结原料&用生石灰全部替代石灰石进行烧结&可以达到提高烧结矿转鼓强度指数的目的’资料)**表明%生石灰遇水消化后&呈极细的消石灰胶体颗粒&其比表面积可达"R #W %#)M ?*!A&它除了具有消石灰亲水胶体外&还由于N 60消化过程+夺取,和+吸出,结合得最弱的水分&颗粒间的水层厚度减小&固体颗粒进一步靠近&特别是在颗粒的边(角等活性最大的接触点上&可以靠近得足以产生较大的分子粘结力&使矿石颗粒与消石灰颗粒靠近&并产生较大的分子粘结力&使得混料时即有利物料成球&也能使料球的强度提高’减小过湿现象和制粒效果的提高&有效的改善了烧结过程的料层透气性’烧结料层氧位提高&促进铁酸钙的形成&从而有利于烧结矿强度的提高’对生产率而言&当生石灰配比由#增加至X R $&时&虽然烧结速度由%T R $"??!?<7提高至*%R #)??!?<7&但生产率并未增加反而略有降低’其原因是随着生石灰用量增大&混合料的堆比重会逐步减小&当此不利因素的影响超过烧结速度的影响时&就导致了烧结生产率略有降低’在本次试验的范围内&生产率降低的幅度很小&生石灰配比分别为%&("&()&与配比为X R $&时的相比&降低幅度分别为"&(%R %&和%R -&’可以认为&不会因为生产率上的这种微小降低&去否定采用添加大用量生石灰来提高烧结矿转鼓强度指数的方法’#!燃料分加的试验燃料分加是将烧结所需的燃料&分在混合料混合造粒之前和混合造粒之后分批加入’采用该方法的原因是%煤粉的制粒性能比较差&若制粒时物料中无燃料&则可提高制粒小球的强度&这样可改善物料的粒度和粒度组成&提高烧结料层的透气性’另外&普通全内配工艺而燃料粒度又较粗时&作为制粒核心的燃料成球后&会因其粒度较大易产生滚动&烧结布料时因易滚动而被布至料层$"$!!!!钢铁研究第")卷万方数据图%!生石灰配比实验底部!同时粗粒烧结料本身也会因偏析作用被布于料层下部"采用分加工艺后!燃料的偏析作用基本消失#其二是分加后!部分燃料分布于小球之表面上!实际是燃料分布于气流通过的通道上"这样就改善了燃料的燃烧条件!能提高燃料的利用率"将燃料分加工艺用在高铁低C <0*烧结矿的生产中!是欲提高制粒效果和使固体燃料在料层中分布合理!达到改善料层透气性!提高烧结料层氧位!促进烧结矿中铁酸钙相的形成!从而提高烧结矿转鼓指数的目的"本次试验条件为$外加煤粉的粒度小于%??%燃料比X R ##&%烧结矿的"V %R $#倍&生石灰配比"&’%!&’(;’V )$R )#&"燃料分加及分加比例的试验结果见表""试验结果表明$当外加燃料的比例为"#&时!烧结矿的转鼓强度指数%生产率分别为X !R -"&和%R $%#D (&?*)J ’"与燃料全部内配和分加比例为*#&时相比!转鼓强度指数是在同一数量级上!只是在生产率上略有提高"随着燃料分加比例超过"#&之后!烧结矿的转鼓强度指数%生产率等技术经济指标均呈逐渐降低之势"从本次试验结果看!燃料分加的效果并不明显"分析其原因为$&%’燃料分加工艺更适合以精矿粉为主要原料的烧结*"+#&*’在实验室中!人工往烧结杯里装烧结混合料与生产中通过布料器%下料槽布料相比!其原料在粒度上的再分布现象相差太大"因此!燃料分加工艺在本次试验中未显示出其优越性"表"!燃料分加比例对烧结的影响燃料分加比例内配比例(&外加比例(&烧结矿产质量指标转鼓强度(&生产率(&D )?U *)J U %’成品率(&烧结速度(&??)?<7U %’%###X !R -#%R -*X $*R *X %T R #T $#*#X !R -%%R -)*$"R ##%T R ")-#"#X !R -"%R $%#$%R T *%T R -X X #!#X !R !!%R X -%$#R T "%$R $"!#X #X "R "-%R -$T $%R T )*#R #""#-#X "R $$%R -$!$%R ##*#R !$*#$#X *R !#%R -$%$!R $)%T R %)$!结!语&%’随混合料中生石灰配比的增加!烧结矿的转鼓强度指数也有所提高"生石灰配比从#逐步增加至X R $&&生石灰全部替代石灰石’时!烧结矿转鼓强度指数可从X %R --&提高至X X R #%&"因此用生石灰全部替代石灰石进行烧结!可以提高高铁低C <0*烧结矿的强度"&*’混合料中生石灰配比为X R $&时!烧结的生产率为%R $")D (&?*)J ’"与生石灰其他几个配比相比!生产率略有下降!但降低幅度很小"其原因是生石灰用量增大后!混合料的堆比重逐步减小所至"&"’燃料分加试验表明$燃料内配与外加的分加比例以-#&$"#&时为好"此条件下!转鼓强度指数为X !R -"&!与燃料全部内配和分加比例为*#&时相比!转鼓强度指数保持不变!烧结的生产率略有提高!为%R $%#D (&?*)J ’"随着燃料分加比例超过"#&之后!烧结矿的转鼓强度指数%生产率等技术经济指标均呈逐渐降低之势"!参考文献"*%+!张克诚!李!健!朱德庆!等R 高铁低硅高料层研究*^+R 烧结球团!*##"!*&*$’$%,X R**+!周取定!孔令坛R 铁矿石造块理论及工艺*Y +R 北京$冶金工业出版社!%T $T R*"+!邱述明!贾光勇R 矾钛磁铁矿烧结燃料二次分加生产实践*^+R 烧结球团!%T T $!&*’$"),"$R&收稿日期$*##X ,#X ,#X’)#)第*期周国凡,等:提高高铁低硅烧结矿强度的实验研究!!万方数据。
4号烧结机降硅烧结生产实践
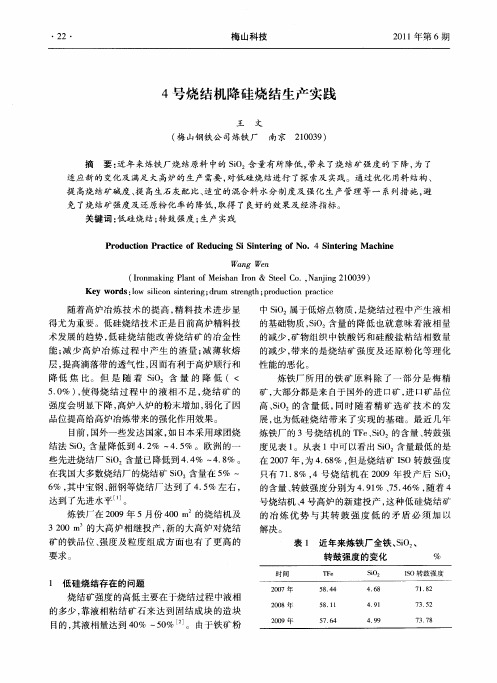
好操 作方 案 。
随着 高炉 冶炼 技 术 的提 高 , 料 技术 进 步 显 精 得尤 为重 要 。低硅烧 结技 术正 是 目前高 炉精料 技 术发 展 的趋 势 , 硅 烧结 能改 善 烧 结 矿 的 冶金 性 低
中 SO 属 于低熔 点物 质 , 烧 结过 程 中产 生 液相 i 是
的基础 物质 ,i, SO 含量 的降 低 也就 意 味 着 液 相量
低 到 。 . % 。 为 了强 化 制 粒 , 次 混 合 与 二 次 T6 7 一 混合 按 照 4 1的 比例 进行 加 水量 的控 制 , 本 能 : 基
升 了 0 4 ,R I .7 % D n R I 。分 别 上 升 了 D 05 % 、.5 。这说 明将 烧结 矿 SO .5 07 % i,含量 降 低
主要 由褐 铁 矿 组 成 , 有 较 多 的 结 晶 水 , 损 较 含 烧
在 对炼 铁 厂所 用 的各种 矿物 的理化性 能 进行 多项 指 标 的测试 后 , 矿 物 之 间 的 同化 性 能 及 促 从
进烧 结 液相 生成 的角 度 , 原料 矿 物进 行 了优 化 对
配 比。
大 , 利 于 形 成 致 密 的 宏 观 结 构 , 时 铁 品 位 不 同
的一 个关 键 因素 , 结矿粘 结 相 的抗 压强 度 、 烧 粘结 相 强度等 都会 随 着 碱度 的提 高 而 逐渐 增 强 , 高 提 碱度 有利 于促 进铁 酸钙 的生 成 , 结 矿 的宏 观 结 烧 构也 随之 由 自熔性 的多 空薄壁 结构 过渡 到高 碱度 的大孔厚 壁结 构 。有 研 究 表 明 j随 着烧 结 矿 碱 : 度 的提 高 , 结矿 矿物组 成 中 S C 明显增 多 , 烧 FA 玻 璃 相和残 余 脉 石减 少 , 结 矿 强 度 升高 。根 据 炼 烧 铁 厂 的生 产实 际 考 虑 , 将烧 结 矿 的碱 度控 制 由原
包钢低硅烧结工艺优化研究.doc

包钢低硅烧结工艺优化研究来源:烧结球团更新时间:09-11-4 16:47 作者: 郝志忠,吴胜利,郭卓团,罗果萍,王艺慈,张芳,王永斌摘要:为了提高入炉矿品位,降低高炉渣量,通过微型烧结试验研究了包钢低硅烧结条件下,烧结温度、配碳量、烧结矿碱度、SiO2 含量、MgO 含量等参数对烧结矿粘结相强度的影响,并在此基础上进行了烧结杯验证试验,为包钢优化低硅烧结工艺参数提供了依据。
关键词:低硅烧结,转鼓强度,工艺优化1 前言低硅烧结能改善烧结矿的冶金性能,减少高炉冶炼过程中产生的渣量,减薄软熔层,提高滴落带的透气性,因而有利于高炉顺行和降低焦比[1 ] 。
同时,减少渣量还有利于增加高炉的喷煤量。
一般认为铁矿石TFe 含量提高1 % ,高炉焦比降低2 % ,产量提高3 %。
因而,低硅烧结能给企业带来巨大的经济效益。
随着包钢选矿技术的不断进步,铁精矿品位日趋提高,目前自产白云鄂博铁精矿的SiO2 含量已降低到210 %~410 % ,为低硅烧结矿的生产及高炉采用低硅烧结矿冶炼提供了物质基础。
由于铁矿粉中的SiO2 是烧结过程中产生足够液相以使物料粘结的基础,也是保证烧结矿具有较高强度的前提,所以采用低硅铁矿粉烧结时,烧结矿质量特别是机械强度可能明显变差[2 ] 。
尤其对于白云鄂博铁矿粉来说,由于富含CaF2 、K2O、Na2O ,在烧结过程中CaF2 可吸收CaO 和SiO2 生成枪晶石,从而减少形成铁酸钙的有效CaO 数量,使铁酸钙的生成量显著降低; 而K2O 和Na2O 主要分布于硅酸盐玻璃质中, 是玻璃质的稳定剂,有利于玻璃质的形成,也会抑制铁酸钙的生成。
因此,在碱度一定的情况下,包钢铁矿粉生产的烧结矿铁酸钙含量远低于普通烧结矿[3 ] ,低硅烧结矿的强度问题就更加突出。
为此,我们通过微型烧结试验研究了包钢低硅烧结条件下,烧结温度、配碳量、烧结矿碱度、SiO2 含量、MgO 含量等参数对烧结矿粘结相强度的影响,并在此基础上进行了烧结杯验证试验,为包钢优化低硅烧结工艺参数提供了依据。
硅电极烧结实验报告
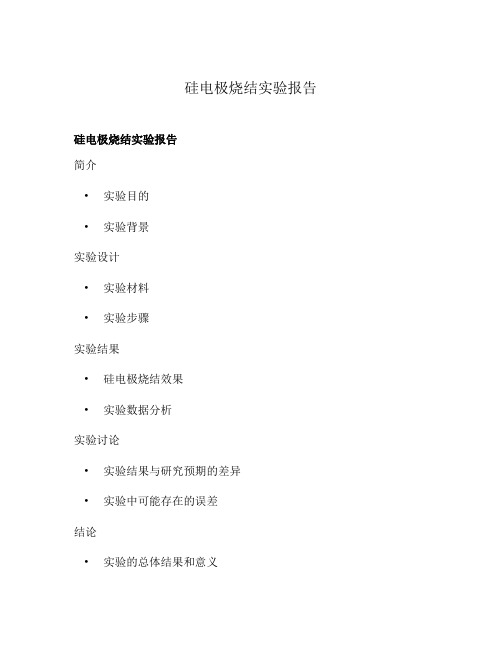
硅电极烧结实验报告硅电极烧结实验报告简介•实验目的•实验背景实验设计•实验材料•实验步骤实验结果•硅电极烧结效果•实验数据分析实验讨论•实验结果与研究预期的差异•实验中可能存在的误差结论•实验的总体结果和意义•进一步研究的方向参考文献请注意:根据提供的信息,我无法具体写出实验报告的内容。
以上只是一个报告的模板,您可以根据实际情况和要求填写相关内容。
硅电极烧结实验报告简介•实验目的:评估硅电极烧结的效果以及其在电子器件制造过程中的应用潜力。
•实验背景:硅电极烧结是一种常用的工艺,通过热压将多个硅片烧结在一起,以提高器件的性能和可靠性。
实验设计•实验材料:硅片、烧结压机、烧结模具、加热装置等。
•实验步骤:1.准备硅片样品,并对其进行表面处理。
2.将硅片样品放置在烧结模具中,并加入合适的填充材料。
3.将烧结模具放入烧结压机中,施加适当的温度和压力。
4.在预定条件下进行烧结过程,并记录相关数据。
5.完成烧结后,将样品取出并进行后续的性能测试和分析。
实验结果•硅电极烧结效果:经过实验烧结后,硅片样品成功烧结在一起,并形成了紧密的结合。
•实验数据分析:通过对烧结后样品的分析,得出了一些重要的数据参数,如硅电极的连接强度、热导率和电阻等。
实验讨论•实验结果与研究预期的差异:与预期相比,硅电极的连接强度和热导率达到了较好的效果,但在电阻方面还有待改进。
•实验中可能存在的误差:可能由于实验条件的局限性以及样品制备过程中的细微差异导致一定的误差。
结论•实验的总体结果和意义:通过本次实验,我们验证了硅电极烧结的可行性,并初步评估了其在电子器件制造过程中的应用潜力。
•进一步研究的方向:在未来的研究中,我们可以进一步优化烧结过程、改进填充材料的选择,以及探索其他影响硅电极性能的因素。
参考文献请根据您的实际实验情况和所需的参考文献,添加相应的引用信息。
烧结法氧化铝生产粗液脱硅新工艺研究
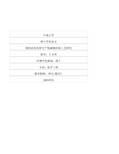
段常压脱硅中提出使用高效絮凝剂来降低一次精液的浮游物,从而提
高第二段脱硅的效果。 本研究提出的常压脱硅新工艺中,一段由加压改为常压,节约能 耗;二段改为钠硅渣分离后加石灰脱硅,并去掉第三段脱硅,不仅减
少了氧化铝损失及操作工序,而且得到的二次精液的4俗能够达到甚
至超过现在三次精液的水平。 一关键词烧结法,氧化铝生产,常压脱硅,种子活化,钠硅渣
including
process in Shandong
Aluminum
influences
Corporation.On the basis of this,the regularities of some
concentration,seed
quantity,activation of seeds,floating material the desilication
quantity,desilication time
on
quantity
is studied
and
the
technical situation during the first stage desilication is gained,gamely seed
quantity:100~1509/l;temperature:95~100。C;time:3~4
导师签名——日期:盏』年卫月三乏日
|
硕士学位论文
第一章文献综述
第一章文献综述
1.1前言
我国铝土矿绝大部分为一水硬铝石型矿(>985),且品位较低(鹏为4-6占
45%)“1,普遍含硅较高,现行的碱一石灰烧结法生产氧化铝的熟料溶出过程中, 由于会发生原硅酸钙引起的二次反应01:
2CaO・Si(h+2NaOH=2Ca(0H)2+2 Na2Si03
工业硅渣重选试验研究

工业硅渣重选试验研究
工业硅渣重选试验研究
张藜,毕红兴,赵兴凡,任承伟,张忠益,徐加雄
【摘要】工业硅精炼过程中产生的氧化硅、氧化铝、氧化钙合成渣因夹带一部分工业硅称为硅渣,硅渣约含20%左右的工业硅,具有极高的经济价值。
因此为对工业硅渣进行资源回收利用,试验采用颚式破碎机和锤式打砂机将硅渣进行破碎,并将破碎后特定粒度的硅渣在摇床上进行重选,最后将重选出来的精矿进行返包重熔。
试验取得了良好成效并已实现了产业化应用。
【期刊名称】云南冶金
【年(卷),期】2019(048)001
【总页数】5
【关键词】工业硅;硅渣;破碎;摇床;返包重熔
工业硅的生产方法理论上有热分解法、电解法和热还原法三种。
而目前,电热还原法是世界上生产工业硅的最常见的方法,该方法主要就是利用还原剂、硅与氧的亲和力的差异,将与氧亲和力强的还原剂把与氧亲和力较弱的硅从矿石中还原出来,但硅与氧的亲和力较强,因此该过程是在高温下进行的[1]。
由于硅石本身和还原剂都含有一定量的杂质(含Fe、Al、Ga、P),且所含杂质亲氧性不同,在工业硅精炼过程中便会产生氧化硅氧化铝氧化钙等杂质,这些杂质合成渣因夹带一部分工业硅称为硅渣[2],硅渣约含20%左右的工业硅,具有极高的经济价值。
现在大部分公司对硅渣的处理方法是采用人工破碎分拣出大颗粒工业硅,分拣后的硅渣仍有较高含量的工业硅无法回收。
此外,分拣后的硅渣以极低的价格外售或填埋,带来较大的经济损失,且造成一定的环境压力,因此开展对分拣。
落实“三同时”严把四道关

严把 安全评价关
司又组织专家进行技术评 审 ,
家评 审组 提 出评 审 意 见 。通 i =
司在 近年来完 成 的工 程建设 项 目中 , 注重贯 彻 国家及 地方 有关 “ 同时 ” 三 的 法 律 、法 规 。 到 2 1 0 0年 8月 份 ,
项 目可研 性报告 和安全预评价报告书 下 ,由设计 单位出具变更 项 目的可行 车前 ,对工程建设项 目,公司将对 照
及有关部 门的批 复意见编制 《 安全专 性报告 ,计划 部 门下发 项 目变更令 , 篇》 。中州分公 司铝土矿 旋流 一静 态 再 由承包商进行施工 。
设计 、预评价报告和安全专篇 ,组织
素 、氧化铝项 目安全防范措施 、落实 检 查 过 程 中 ,发 现 有不 按 施 工规 范 全卫生 、环境 保护设 备、设施应证件 安全预评价措施 的分析 、安全管理机 施 工 ,施 工过 程 存 在安 全 事 故 隐患 资料完整 ,且档案齐全 。
意见 ,企业进行 整改完善后 ,将验 收 评价报告报省安监局审批备案 。 进 行 ,未 达 到 国家 标 准 和设计 要 求
严把施工管理关
的 ,认 真 落 实 整 改 ,验 收 合格 后 方
严把 工程设计关
可进 行 单体 试 车 ,以确 保 所有 安 全 在 中州分公司 ,所有施工作业都 卫 生 、环 境 保 护设 备 、设施 应 证 件 要求严格按 图施工 ,在施工过程中进 资料完整 ,且档案齐全 。
计关 、施工管理关 、工程验收关这四道 的安全 与职业 健康风险进行讨论 ,提 与评价机构进行及时沟通 , 关 ,使工程项 目符合国家和地方政府的 出建设 意见 ; 在河南 省冶金研究所 出 专家对工程建设项 目运行过秸 有关规定 ,提高设备设施 的本质 安全 , 具安全 预评价 报告初 稿后 ,又组织 内 的和 潜在 的安全健 康风 险进; 最 大限度地减少或消除可能发生 的伤 部技术人员 和经验 丰富的岗位员 工进 提出改进意见 ,列入评 价报 害、事故以及对环境的影响,使工程建 行讨论评议 ,提 出改进意见 。 设项 目 投产后安全绩效显著。 持续改进的依据 ,并在评价 在安全预评价完 成后 ,中州分公 安全验收评价报告初稿后 ,
烧结法赤泥和硅渣沉降槽的运行和探讨

烧结法赤泥和硅渣沉降槽的运行和探讨摘要:本文简单介绍了烧结法赤泥、硅渣的物料性质,以及用于分离两种物料的沉降槽运行情况总结和进一步的探讨,并且对于影响物料沉降的疏水性物料进行了分析。
关键词:赤泥硅渣沉降疏水性前言重力沉降槽作为一种料浆处理能力强、操作方便、工作效率高的液固分离设备逐步地为化工、冶金等行业所认可。
在氧化铝的生产中,沉降槽也逐渐地以其便于自动化操作、劳动强度小、物料适应能力强等优势逐渐取代以滤布为介质的过滤机,众多工程技术人员根据物料的性质对沉降槽的结构、传动等进行改进,以提高沉降槽的各项运行性能参数。
沉降槽的规格也随着对物料的适应和指标优化作着大量的改动,诸如:用于拜尔法氧化铝生产中的高帮深锥沉降槽,锥底的夹角、悬筒的长径比、絮凝剂的添加方式、帮高以及压缩锥底都根据物料性质和运行要求作了大量的改进。
烧结法氧化铝生产中用于赤泥、硅渣的沉降槽也进行了大量的改进和探索,并根据经验对老式沉降槽改造取得了较大的成功。
1 赤泥沉降槽的运行和探讨1.1 物料性质和化学反应1)、化学反应2CaO.SiO2不溶于水而进入赤泥,试验与实践证明会被NaOH分解,因此有部分SiO2以Na2SiO3的形式进入溶液。
熟料中游离的钙和上述反应生成的Ca(OH)2能使赤泥的沉降性能变坏,但在有Na2CO3的条件下则发生苛化反应,抑制反应的进行,达到一种平衡。
β-2CaO.SiO2被分解的产物Ca(OH)2,能与溶液中的NaAl(OH)4和Na2SiO3发生相互反应,生成难溶的含水铝酸三钙和水化石榴石固溶体。
3 Ca(OH)2+2 NaAl(OH)4→3CaO.Al2O3.6H2O+2NaOH3Ca(OH)2+2NaAl(OH)4+xNa2SiO3→3CaO.Al2O3.xSi02.(6-2x)H2O+2xNaOH在Na2Oc浓度足够时,可减少上述反应。
当溶出温度过高如大于95℃,溶液还会发生脱硅反应,而生成钠硅渣。
- 1、下载文档前请自行甄别文档内容的完整性,平台不提供额外的编辑、内容补充、找答案等附加服务。
- 2、"仅部分预览"的文档,不可在线预览部分如存在完整性等问题,可反馈申请退款(可完整预览的文档不适用该条件!)。
- 3、如文档侵犯您的权益,请联系客服反馈,我们会尽快为您处理(人工客服工作时间:9:00-18:30)。
烧结法硅渣烧成工艺试验研究娄东民1,2,李太昌1,刘国红(1.中国矿业大学,北京100083;2.中国铝业中州分公司,河南郑州454174)摘要:本研究以工厂烧结法硅渣为研究对象,研究了不同烧结法熟料配方、烧成技术条件下的溶出率指标变化情况,提出了硅渣熟料最佳配方及烧成技术条件。
关键词:硅渣;熟料;烧成;溶出中图分类号:TF802.67;X758 文献标识码:A 文章编号:100221752(2008)1221726Study on silica residue calcinations process in Sintering processLOU Dong-min1,2,L I Tai-chang and L IU Guo-hong(1.Chi na M i ni ng U niversity,Beiji ng100083,Chi na;2.Zhongz hou branchof Chalco,Zhengz hou454174,Chi na)Abstract:The paper studies the digestion rate performances under different recipe of clinker and calcination technology in Sintering process and puts for2 ward the optimum recipe and calcinations conditions of silica residue.K ey w ords:silica residue;clinker;calcinations;digestion 传统烧结法氧化铝生产工艺中,所产生的硅渣一般返回生料配料,以回收其中的碱和氧化铝。
但是硅渣返回配料使熟料氧化铝含量和熟料A/S大幅度降低,使整体烧结法工艺技术经济指标变差。
硅渣与烧结法料浆相比,具有粒度细的特点,在回转窑烧结过程中,固相反应容易进行,可以在较低温度、较短时间内完成。
中国铝业股份有限公司最新开发成功的SDCC工艺中,成功地采用固定式炉硅渣熟料烧成工艺,获得了较好的技术指标和经济效果。
本文在实验室条件下,详细研究了硅渣熟料配方及最佳烧成工艺技术条件,为产业化工业生产技术指标的确立,奠定了基础。
1 主要仪器设备混料装置一台,高温炉2台,烘箱一台,恒温水浴2套,抽滤装置一套,三口瓶2个,小烧杯若干。
2 试验原料混合硅渣:取自生产现场,烘干、磨细、分析化学成分备用。
化学分析结果列于表1。
石灰:取自生产现场,磨细至-100#筛,分析化学成分备用。
结果列于表1。
纯碱:分析纯表1 试验原料主要化学组成名称化 学 成 分,%SiO2Fe2O3Al2O3CaO Na2O K2O TiO2Na2Os 1#混合硅渣16.08 1.4624.025.6 6.4 2.60.4 1.85石灰 1.990.889.03 试验条件3.1 烧成试验条件烧成温度,℃:850、900、950、1000、1050、1200在烧成温度下停留时间,min:0.51、2、5、10、20熟料碱比〔N/R〕:0.4、0.6、0.8、0.92、0.96、110、1.1熟料钙比〔C/S〕′:1.3、1.4、1.5、1.7、1.9、2.0 3.2 溶出试验条件标溶条件:温度90℃;L/S=15;熟料细度-120#筛;所用调整液取自生产现场,Nk=15g/l Nc=5g/l;溶出时间30min。
工溶条件:温度88℃;时间30min;L/S=4.5;熟料细度-60#筛。
收稿日期:2002-08-264 试验方法4.1 熟料烧成试验方法在配好的硅渣生料中,加入适量水,调和均匀,用模具制成圆柱状团块,放入瓷坩埚内,置于高温炉中,以10℃/min升温速度,升至试验要求的烧成温度,停留规定时间后,关闭电源,自然降温至400℃以下,高温炉中取出,降至室温后,将熟料破碎、磨细、混匀,一部分过60#筛用于工业溶出试验,一部分过120#筛做标溶及成分分析。
4.2 溶出试验方法试验在1升三口瓶中进行。
取一定量配制好的调整液,装入1升三口瓶中,将三口瓶放入控温水浴中预热,并开启搅拌,当调整液的温度升到试验要求温度时,按要求加入熟料,溶出30min后出料,进行液固分离,固体洗净、烘干,送化学分析。
计算氧化铝、氧化钠的溶出率,工业溶出需分析溶液成分(N T、Nk、Al2O3、SiO2)。
5 试验结果与讨论5.1 烧成温度的影响以传统烧结法的低碱、高钙熟料配方为依据,用石灰和纯碱将混合硅渣配制成碱比为0.95~0.97,钙比为 1.98~2.0的生料,然后把生料制成Φ20mm、高20mm~25mm的锥体,分别在850℃、900℃、950℃、1000℃、1050℃、1200℃进行熟料烧成试验,烧成时间为20min。
然后将熟料分别进行标准溶出和工业溶出,试验结果见表2、表3、表4及图1、图2。
表2 硅渣生料及不同温度烧成熟料主要化学成分及配比编号烧成温度℃熟料化学成分,%熟料配比SiO2Fe2O3Al2O3CaO TiO2K2O Na2O Na2O s〔N/R〕〔C/S〕A/S 生 料13.93 1.1621.226.20.37 2.612.8 1.620.97 1.99 1.52185016.38 1.4624.8310.43 3.415.5 2.40.98 2.01 1.51 290016.52 1.4625310.43 3.615.25 2.40.97 1.99 1.51 395016.82 1.4625.231.80.43 3.515.4 2.350.97 2.01 1.50 4100016.69 1.4225.231.60.42 3.515.6 2.50.97 2.01 1.51 5105016.52 1.422531.20.42 3.515.25 2.50.96 2.00 1.51 6120017.06 1.4625.4320.43 3.615.5 2.50.96 1.99 1.49表3 烧成温度对熟料标准溶出率的影响试验结果编号烧成温度℃标准溶出赤泥主要化学成分,%标准溶出率,% SiO2Fe2O3Al2O3CaO K2O Na2OηA标ηN标185021.19 2.18 4.649.60.3 2.188.4191.53 290020.59 2.144490.3 2.189.8891.29 395025.9 2.35452.40.3 2.290.3791.33 4100026.57 2.47 3.654.20.1 2.191.6792.15 5105027.39 2.46 3.454.40.1 1.692.293.98 6120027.04 2.54 4.654.20.1 1.589.3194.29〗表4 烧成温度对熟料工业溶出率的影响试验结果编号熟料烧成温度℃赤泥主要化学化学成分,%工业溶出率,%工业溶出溶液主要化学成分,g/L Al2O3CaO Na2OηA工ηN工N T A2O3SiO2αk18509.245.6 2.274.7890.3599.6102.63 4.07 1.35 29008.647.6 1.977.6091.89100.7105.75 4.297 1.32 3950650.6 1.985.0492.25103.3109.7 4.573 1.29 41000 5.452.2 1.687.0393.79103.5111.02 4.799 1.28 51050 5.253.4 1.587.8594.25103.9109.54 4.92 1.29 61200 5.254.2 1.887.4493.91103.9107.89 4.417 1.24从表3、表4及图1、图2的试验结果可以明显的看出,在本试验条件下,烧成温度小于1050℃时,随着温度的升高,不论是氧化铝的标溶、工溶还是氧化钠的标溶、工溶均有不断升高的趋势,但当烧成温度升高到1200℃,氧化铝的标准溶出率有降低的趋势,工业溶出率和氧化钠的溶出率变化不大。
因为在进行熟料烧成时,固体中的质点处于不断振动状态,提高温度它们的振幅增大,当温度升高到一定程度后振幅增大到足以超越自己的位置进入相邻质点的位置,并且随着温度升高而愈益强烈,这时两种能够相互反应的物质就发生了固相反应。
因此当烧成温度较低(小于950℃)时,硅渣中的氧化铝只有一部分生成可溶性的氧化铝,熟料具有一定的标准溶出率,但工业溶出效果较差,二者相差12个百分点以上。
而当温度升高到1000℃以上时,固体反应较为剧烈,硅渣中绝大部分氧化铝生成了可溶性的氧化铝,氧化铝的标准溶出率和工业溶出率比较高,二者相差只有4~5个百分点左右;再升高温度到1200℃,对熟料的氧化铝和氧化钠溶出率影响,且温度高还增大热耗。
因此在本试验条件下烧成温度在1000℃~1050℃比较合适。
5.2 烧成时间的影响在5.1中选定的较佳的烧成温度(1050℃)下,把碱比为0.95~0.97、钙比为1.98~2.0的硅渣生料制成Φ20mm、高20mm~25mm的锥体,然后进行不同时间的烧成试验,烧成时间分别为0.5min、1 min、2min、5min、10min、20min,然后将熟料分别进行标准溶出和工业溶出试验,试验结果见表5、表6、表7及图3、图4。
表5 硅渣生料及不同烧成时间熟料主要化学成分及配比编号时间min熟料化学成分,%SiO2Fe2O3Al2O3CaO TiO2K2O Na2O Na2Os〔N/R〕〔C/S〕A/S 生 料13.93 1.1621.2026.200.37 2.6012.80 1.620.97 1.99 1.5210.5016.12 1.2924.1030.600.41 3.2015.00 2.400.97 2.01 1.502 1.0016.25 1.4024.3030.300.40 3.4014.95 2.500.96 1.98 1.503 2.0016.22 1.3724.1030.300.40 3.3015.00 2.350.98 1.98 1.494 5.0016.29 1.4724.6030.500.42 3.4015.25 2.500.97 1.99 1.51 510.0016.66 1.4525.2031.400.42 3.5015.40 2.400.96 2.00 1.51 620.0016.52 1.4225.0031.200.42 3.5015.25 2.400.96 2.00 1.51表6 烧成时间对熟料标准溶出率的影响试验结果编号烧成时间min标准溶出赤泥主要化学成分,%SiO2Fe2O3Al2O3CaO K2O Na2OηA标%ηN标%10.5023.81 2.40 3.6055.200.25 1.6091.7294.092 1.0023.50 2.35 3.6054.600.25 1.7091.7893.693 2.0024.38 2.40 3.2055.600.20 1.6092.7694.194 5.0023.60 2.34 3.4055.000.18 1.5092.3494.55 510.0023.85 2.37 3.5055.000.18 1.6092.0794.07 620.0023.75 2.36 3.4054.400.18 1.6092.2093.98表7 烧成时间对熟料工业溶出率的影响试验结果编号烧成时间min工溶赤泥化学成分,%Al2O3CaO Na2OηA工%ηN工%工业溶出溶液主要化学成分,g/LN T A2O3SiO2αk10.50 5.6054.40 1.7086.9393.63113.60114.14 5.18 1.282 1.00 5.8053.80 1.8086.5693.22110.50111.02 5.04 1.303 2.00 5.2054.80 1.6088.0794.10109.40112.00 5.08 1.284 5.00 5.4054.40 1.7087.6993.75109.50110.20 5.00 1.28 510.00 5.3054.40 1.5087.8694.38106.00106.91 4.69 1.31620.00 5.2053.40 1.5087.8594.25103.90107.89 4.42 1.24从表5、表6、表7及图3、图4的试验结果可以看出:在本试验条件下,保温时间为0.5min时,熟料氧化铝标溶已达到了91.7%以上,熟料氧化铝的工业溶出率也在86.5%以上,当保温时间达到2min 时熟料的氧化铝标溶、工溶最高分别为92.7%和88%,再延长保温时间对熟料的氧化铝溶出率影响不大。