福特8D报告-实际案例
8D报告步骤通俗完整讲解(附标准范本)

8D报告通俗讲解(附标准范本)8D 报告精品培训完整的8D报告标准范本.xlsx ——附件Excel 可直接打开保存 Issue#问题编号:8D-20180801QCustomer 客户:MD生活电器Date Issue Occurred 问题发生日期:2018.08.03Product 产品:FS4034上盖Date Issue Closed 问题关闭日期:2018.08.10Champion Name 负责人姓名Champion Title 负责人职位Champion Phone Number 负责人电话Champion E-mail Address 负责人电子邮件XXX副总经理XXXXXXXXXXX XXX Team Member Name(s)其他成员姓名Title(s)职位Phone Number(s)电话E-mail Address(es)电子邮件XXX品质部经理XXXXXXXXXXX XXX XXX生产部经理XXXXXXXXXXX XXX XXX质量工程师XXXXXXXXXXX XXX XXX 生产车间主管XXXXXXXXXXX XXXAffected Document 相关文件Owner for Update 责任人负责更新Date 日期FMEAXXX 2018.8.15BOM无/Control Plan 控制计划XXX 2018.8.15Drawing 图纸无/Design Standards 设计标准无/Congratulation 肯定团队Closure Statement 关闭声明Verification of Corrective Action: Has the issue been turned on and off? How? Verification through staticalevidence / hypothesis testing. Verification of corrective action for each why made and why shipped is required.纠正措施的确认:该问题处于开启状态还是关闭状态?怎样?通过证据确认/假设检验.针对每个产生的原因和被发运原因的纠正措施都要确认。
8D改善步骤培训及案例
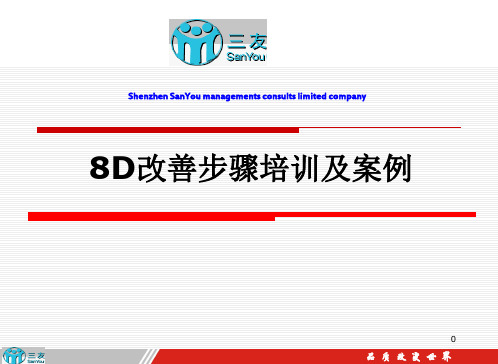
品质改变世界
5.决定及验证纠正措施
5.1决定可能的纠正措施
针对根本原因,现采用下列方法进行整改:
1.修改搬运、贮存作业方法,将原来搬运 和堆放高度3层改为2层,减少重压。
2.改变包装方法,产品从散装改为托盘运装。 3.包装箱内上下层增垫泡沫,以减少碰撞冲力。
29
品质改变世界
5.2验证纠正措施(小批量验证)
(许丽 完成日期99/11/05)
对挑选出的破损20μMHT机用膜运回公司, 按数补给浙江精密机械厂。并确认补货后 的情况。(许丽 完成日期99/11/05)
对现有生产、贮存、出货的20μMHT机用 膜进行全数检验。(许丽 完成日期99/11/05)
23
品质改变世界
4.识别并验证根本原因
4.1 识别可能原因(因果图)
16
品质改变世界
8D-Report的格式
1、本公司涉及到的8D格式 2、上海天马文件规定格式
建议:用PPT的格式表达
17
品质改变世界
Thanks for your attention!
18
品质改变世界
8D—问题改善手法
案例说明
19
品质改变世界
0. 问题的提出
99年11月4日客户—浙江某机械制造公司 投诉,在其包装车间对“ALT-5检测器” 进行包装时,使用公司的MHT机用膜时一 拉就断裂, 并发现使用的机用膜端口破 裂。
11
品质改变世界
CLCA – 步骤 6
Step6: 长期对策:
对策实施日期:
负责人:
日期:
提供长期的预防对策,包括: 针对根本原因的预防对策 全检以消除任何一个可能存在的同样问题 相关的ECR需要经过customer批准 第六步完成时间
福特问题解决之8D报告

福特问题解决之8D流程8D又称团队导向问题解决方法,8D问题求解法(Eight Disciplines Problem Solving)是福特公司处理问题的一种方法,亦适用于制程能力指数低於其应有值时有关问题的解决。
它提供了一套符合逻辑的解决问题的方法,同时对於统计制程管制与实际的品质提升架起了一座桥梁。
二战期间,美国政府率先采用一种类似8D的流程——“军事标准1520”,又称之为“不合格品的修正行动及部署系统”。
1987年,福特汽车公司首次用书面记录下8D法,在其一份课程手册中这一方法被命名为“团队导向的问题解决法”(Team Oriented Problem Solving)。
当时,福特的动力系统部门正被一些经年累月、反复出现的生产问题搞得焦头烂额,因此其管理层提请福特集团提供指导课程,帮助解决难题。
8D主要用于汽车及类似加工行业的问题解决方法。
原始是由Ford公司,全球化品质管制及改善的特殊必备方法,之后已成为QS9000/ TS16949、福特公司的特殊要求。
该方法适用于解决各类可能遇到的简单或复杂的问题;8D方法就是要建立一个体系,让整个团队共享信息,努力达成目标。
8D本身不提供成功解决问题的方法或途径,但它是解决问题的一个很有用的工具;亦适用于过程能力指数低于其应有值时有关问题的解决;面对顾客投诉及重大不良时,提供解决问题的方法。
8D法是美国福特公司解决产品质量问题的一种方法,曾在供应商中广泛推行,现已成为国际汽车行业(特别是汽车零部件产家)广泛采用来解决产品质量问题最好的、有效的方法。
D0:征兆紧急反应措施目的:主要是为了看此类问题是否需要用8D来解决,如果问题太小,或是不适合用8D来解决的问题,例如价格,经费等等,这一步是针对问题发生时候的紧急反应。
关键要点:判断问题的类型、大小、范畴等等。
与D3不同,D0是针对问题发生的反应,而D3是针对产品或服务问题本身的暂时应对措施。
D1:小组成立目的:成立一个小组,小组成员具备工艺/产品的知识,有配给的时间并授予了权限,同时应具有所要求的能解决问题和实施纠正措施的技术素质。
福特8d报告

福特8D报告: 逐步思考摘要福特8D报告是一种用于解决问题和改进产品质量的工具。
它是一种逐步思考的方法,旨在通过充分了解和分析问题的根本原因,制定并实施解决方案。
本文将详细介绍福特8D报告的步骤,并提供实际案例来说明该方法的应用。
引言在制造和生产过程中,问题和缺陷是难以避免的。
福特8D报告是一种问题解决方法,它帮助团队深入了解问题,并制定可行的解决方案。
它采用逐步思考的方式,以确保问题得到彻底解决,并为未来的改进提供经验教训。
1. 识别问题(D1)福特8D报告的第一步是准确识别问题。
这需要收集问题的详细描述,并确定问题的性质、范围和影响。
团队应该清楚地了解问题的具体症状,并在问题描述中提供必要的背景信息。
例如,如果一个汽车零件在使用过程中出现故障,团队应该记录下故障发生的频率、症状以及可能对用户造成的安全风险。
2. 组织团队(D2)福特8D报告的第二步是组织一个跨职能的团队来解决问题。
团队应该包括具有相关技能和知识的成员,以确保问题能够从不同的角度进行分析和解决。
在这一阶段,团队成员应该被指派特定的角色和责任,以确保问题解决过程的顺利进行。
3. 停止问题蔓延(D3)福特8D报告的第三步是采取紧急措施来防止问题的进一步扩大。
这可能包括停产、隔离有问题的产品或过程,并采取其他必要的措施来保护客户和用户。
例如,在汽车零件故障的案例中,团队可能会立即停产相关产品,以防止更多的故障发生,并制定替代方案。
4. 确定根本原因(D4)福特8D报告的第四步是通过分析来确定问题的根本原因。
这需要使用各种质量工具和技术,如鱼骨图、5W1H分析等,以帮助团队了解问题的背后原因。
通过确定问题的根本原因,团队可以避免仅仅对症状进行治疗,并确保问题得到全面解决。
5. 制定纠正措施(D5)福特8D报告的第五步是制定纠正措施来解决问题。
这需要团队根据根本原因分析的结果,提出解决问题的具体措施。
纠正措施可能包括改变生产工艺、修复设备或提供培训和教育等。
8D报告以和案例分析

字模冲子修模时 未依图面配置
跳屑造成迭料
模具
字模高度设计 安全系数尺寸 偏低
字模磨损
材料
材料厚度 0.3±0.01
三. 临时对策:
3.1.对嫌疑品全部重工
在途物流 厂内
sorting日期 11/23 11/24 11/24
不良率 52/18,000= 0.28% 40/9,000= 0.44% 22/61,300 =0.03%
D2: 问题描述
• 从客户观点来描述问题,他们看到什么? 照片or 寄 不良样品回来分析 .
• 阐明全部客户提供之数据. • 涵盖范围 ? Lot No?批号?Date Code?制造日期? • 问题有多严重 ? 不良数?不良率? • 是制造还是设计旳问题 ? 层别法 - 模号? • 阐明规格之要求. • 阐明电子,机械验证,及任何失效分析之成果. • 所报告旳问题是真正旳问题吗?连续问5次为何. 重工, 全检 ,报废 .若要 重工或全检 , 有执行旳原则吗 ?
• 详述检验措施, 措施可行吗?有作有效性验 证吗?
• 紧急对策引起其他问题吗?
• 紧急对策进行中?已完毕? 注意时效.
• 检验/测试/分析成果阐明. 详列检验数,不良 数,不良率.
D4:原因分析
• 详列永久对策旳运营时间表.
D6:效果验证
• 验证紧急对策及永久对策之有效性,应以 量化表达验证成果(如:Cpk值可达1.33, 或不良发生率降至 0 等).
• 在永久对策验证有效之前,应连续进行紧 急对策.
• 追踪永久对策执行后之品质推移情况. • 在没有完全把握问题已彻底处理之前 , 不
要轻率旳结案 .
不良品生产日期
11/4 11/7 11/19,11/20
质量管理8D报告培训(经典教材)含案例分析_2022年学习资料
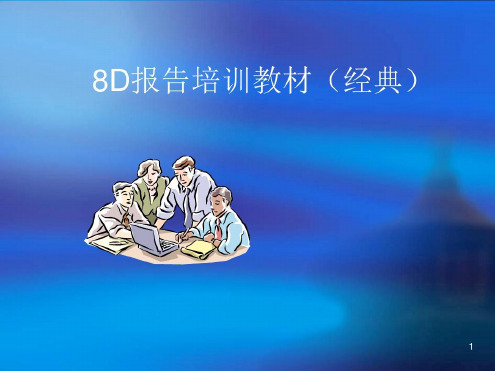
四.8D聚一D3临时对策-定义、验证和执行临时控制行动,保证在永-久纠正措施实施前,将问题与内外部顾客隔。-需要考虑的问题:-1.防止继续产生不-2减小产生的不良和-良品(减少不良品产-后续可能产生不良对-客户 影响。-14
∥NEWASIA-折-亚州州-四.8D步骤一D3临时对策-确定并执行应先采取的临时措施,以遏制外界/内部客 户问题的扩大。-临时措施的确定应考虑从供应商零件库存--供应商零件-在途品-内部零件/材料一生产制程一仓库 存一交付在-途品一客户端减少和降低(消除)后果的产生。-临时措施一直要持续实施至后续的永久对策的执行有效,方可撤消-临时措施实施中,应及时跟踪和验证其效果-15
D1--成D步骤D1建立小组-选择小组成员的准则-■选择具有相-■小组成员的-■各类成员之-■按需要调整技能、知识、-人数控制在4到-间职责、任务-团队成员-资源、权力等-10个之间-合理搭配-的人作为团队-1
四.8D素一D2问题描述-以客户的角度和观点详细描述其所感受到的问题现象,-将所遭遇的问题,以量化的方式, 明确出所涉及的人-事,时,地,为何,如何,多少-什么是问题??-期望-目标-现实-12
四.8D斐聚一D4原因分析-鱼骨图分析-员工品质意识淡薄-机-手工喷涂-标准执行-力差-人员变动大-杜邦油 性能-不良-车顶饰条附着力不良-素材表面-输送链台车-要打磨-漆渣太厚-复押半成品-喷涂房-表面粒点-环境 -未对半成品-进行检验-法-料-21
四.8D斐聚一D4原因分析->人人员相关信息是否有变更->机-设备维修保养记录-5M1E->料物料更改记录 主料、辅料)->环-温湿度记录-法工艺更改记录,-生产原始记录->测-检测条件方法人员-常用方法-1.对操 员现场询问2.现场观察-3.模拟试验-4.DO试验-5.异常记录-22
8D实施方法含实例

D6、验证纠正措施
1. 换完电线后,至今尚没有发现连接点松动的迹象。 2. 断开电流接触器的电路进行试验,一旦电压不正常,转子 将自动停止工作,直至没电镀的产品从线上取下。 以上工作,小组共同进行了验证,并提请顾客事先的批准。
32
D7、防止再发生的措施
❖电镀工作指导书被修改增加了如下内容: 1)当生产线不正常停止时,操作者不仅要挑选出缺陷产品 ,而且要在工作记录记下数量及当班QC的名字。 2)在电镀线在每天早上启动前,电流接触器的连接点和电 线必须检查。以上,由杨星在12月15日完成。 ❖开发一个包括每天需检查事项的检查清单,例如生产线停 止,不管缺陷产品是否被挑选,制造部和QA需进行审核。 ❖ 依次类推,如果有类似问题,该小组负责纠正并采取适当 的预防措施。
检查数量
状态 缺陷数量
MT001206 19308片
19308片
OK
0
MT001208 14274片
14274片
OK
0
总计
33582片
33582片
OK
0
•2. 我们对操作者进行培训和教育,以让其知道最重要的事情:
•遵守工作程序和指导书以保持顾客产品质量。使其意识到他们在 产品质量保证中的重要职责。我们强调,任何由于不小心引起的错 误是不允许的并且不能重复发生,因为那样将会给顾客带来不必要 的损失。因此我们把给顾客造成损失的错误展示以教育员工。
生管课、销售课、库管课、品保课 • 责属人员:
贾正羽、庄卫年、赵晓明、许 丽
36
D2.问题描述
• 何时 : 1999年11月4日; • 何人 : 浙江精密机械厂; • 何地 : 浙江精密机械厂—包装车间; • 何事 : 包装ALT-5检测器时,使用20μMHT
福特经典8D报告模板

舍得,放下,参与,尊重(电话,时间)
充分利用 休息时间:
2
培训目标 培训目标:
培养问题意识和开放的心态; 了解8D的精神和原则; 掌握8D的实施流程; 掌握实施8D各环节的要领; 掌握PDCA、脑力风暴、因果图等必要的技法; 能够编写专业的8D报告;
团队导向问题解决对策
TOPS (Team Oriented Problem Solving)
导入:构建学习心态
NGSCC
充分的投入 开放的心态
投入多少,收获多少!
没有人靠节约成功!
经验往往是进一步成功的障碍!
大家都是井底蛙,只是井口位置和大小有所不同!
改变的决心
郑重的承诺
不是想,不是要,是一定要改变
人 material Man 机 六大 生产要素 法 测量 环
NGSCC
料
machine
method
environment
measurement
七大任务法
1. Q — 品质 2. C — 成本 3. D — 交期
组合 应用
不 合 理 不 均 衡 浪 费
人
机
料
法
环
测量
4. S — 服务
5. S — 安全 6. P — 效率 7. M — 士气
1886年管理学诞生,泰罗在此年加入美国的机械工程师学会 (ASME); 1908年哈佛大学创立了著名的哈佛商学院(HBS,Harvard Business chool),并于同年开设了MBA课程;
毛泽东曾经说过:
‚我们不但要提出任务,而且要解决完成任务的方法问题。我们的任务是过河,但是没有 桥或没有船就不能过。不解决桥或船的问题,过河就是一句空话。不解决方法问题,任务 也只是瞎说一顿。‛
质量管理8D报告培训(经典教材)含案例分析

四. 8D步骤-D7效果确认及标准化
效果确认 实事求是,以事实和数据为依据,对数据用统计工具处 理后得出相应的结论,不应未做对比分析即判定效果。
16.00% 14.00% 12.00% 10.00%
8.00% 6.00% 4.00% 2.00% 0.00%
slot1
slot2
slot3
slot4
slot5
按需要调整 团队成员
四. 8D步骤—D2问题描述
以客户的角度和观点详细描述其所感受到的问题现象, 将所遭遇的问题,以量化的方式,明确出所涉及的人, 事,时,地,为何,如何,多少。
什么是问题???
问期题望
期望 目标
现实
四. 8D步骤—D2问题描述
问题描述方法:5W/2H
WHO WHAT
5W2H 谁
1. 报警按钮未启动三方通话联系到监控中心:NG 2. 事后报警按钮测试(第一次正常,第二次不正常,拆
开后检查发现触点接触不良):NG 3. 警铃不响 电梯只有三方通话功能(国标无强制要求
需警铃鸣响功能) :OK 4. 话筒铃声及功能正常(事后测试):OK
1. 光电感应器位置偏离 导致无信号输出:NG
什么
解释 识别那一个客户(内/外部)在抱怨
问题的症状,无法用文字描述清楚的,借助 于数字或图片将问题表达清楚
WHEN WHERE WHY HOW
何时 何地 为什么 怎么样
记入问题发生的日期 记入问题发生的场所 识别已知的解释 在什么的模式或状态这问题会发生
HOW MUCH
什么程度
问题发生的程度、量
13
三. 何时采用8D
重复发生,一直没有解决的问题 比较重大的制程品质问题 客户要求回复的品质投诉
8d报告优秀案例

8d报告优秀案例过去的一年,我所参与的8D报告团队成功处理了一起涉及供应商质量问题的案例,下面将详细介绍这个优秀案例。
这个案例发生在我们公司采购的某个关键零部件出现质量问题的情况下。
这个问题导致了生产线的停产和产品交付的延误,严重影响了客户的满意度和公司的声誉。
因此,我们决定立即展开8D报告处理流程。
在第一步的问题定义阶段,我们收集了有关产品质量问题的详细信息,并与供应商进行了交流。
经过仔细的分析,我们确认问题的根本原因是供应商在生产过程中的误操作。
我们将这一问题定义为"供应商质量控制不良"。
在第二步的立即应对阶段,我们制定了一系列的紧急措施以最小化问题的影响。
首先,我们与供应商紧密合作,要求其立即停止有问题的产品的生产,并进行全面的产品回溯。
同时,我们向客户解释了问题的原因,并承诺尽快解决该问题。
此外,我们还进行了生产线的调整,以确保在问题得到解决之前不再生产有问题的产品。
在第三步的原因分析阶段,我们成立了一个跨部门的团队来深入研究供应商质量控制不良的根本原因。
我们对供应商的生产过程进行了详细的调查和分析,发现了一些关键的质量控制环节存在缺陷。
我们将这些缺陷总结为三个主要方面:员工培训不足、工艺流程不规范和质量检测不完善。
在第四步的制定纠正措施阶段,我们采取了一系列行动来解决根本原因。
首先,我们与供应商一起制定了改善员工培训计划,并向供应商提供了必要的技术支持。
其次,我们对工艺流程进行了重新设计,并制定了明确的规范和标准。
最后,我们改进了质量检测流程,并引入了新的检测设备和方法。
这些措施的实施能够有效地提高供应商的质量控制能力。
在第五步的纠正措施的实施阶段,我们与供应商密切合作,确保改进措施得到及时实施并取得预期效果。
我们定期进行跟踪和评估,以确保问题得到根本解决,并避免类似问题的再次发生。
在第六步的效果评估阶段,我们对改进措施的效果进行了全面的评估。
通过与供应商和客户的沟通和反馈,我们了解到改进措施取得了显著的效果。
8D模式(问题解决工作程序)

序号 1 2
主要原因
D6:实施并验证纠正措施 (略)
纠正措施
地点 完成时间 负责人
7
D7:制定巩固措施并实施 1)制定巩固措施
序号
巩固措施
1 修订 A 型号车轮控制计划,将××纳入其中。
2 修订 A 型号车轮车制作业指导书,将加工参数修订为××。
3 对 A 型号车轮加工人员进行培训(标准学习,技术操作培训)
action)。 制定纠正措施时,要注意纠正措施的有效性、经济成本、可操作性,不要把临时性和应
急性的措施作为纠正措施。纠正措施应考虑采用防错技术与控制图。
纠正措施实施前,要进行风险、可行性评审,必要时要试运行一下,要避免拔出萝卜带 出泥——旧问题解决了,新问题又出来了。
要形成纠正措施计划表。纠正措施计划表的内容包括:主要原因、纠正措施、负责人、 地点、预定完成时间等。参考本章 11.4 节中的(6)条款。
3
题对顾客或相关各方的影响,需采取临时措施 ICA(如挑拣、返工、修补、更换、停止发货 等)对问题进行处理。临时措施要执行到采取纠正措施为止。
临时措施 ICA 实施前,要进行可行性评审,避免拔出萝卜带出泥——旧问题解决了,新 问题又出来了。临时措施 ICA 实施过程中或实施后,要对其有效性进行验证。
5
案例 11-1:8D 报告格式
8D 报告
项目名称:解决 A 型号车轮装配困难问题
项目涉及的产品:
项目来源:
项目负责人:
项目开始日期:
பைடு நூலகம்D1:小组成立
1)小组目标:6 周内,解决车轮装配困难问题。
2)小组成员分工:
姓名
职务
组内职务
张三
质量部经理 组长
8d报告改善的案例

8d报告改善的案例近年来,随着企业管理水平的不断提升,8D报告(8 Disciplines Report)作为一种问题解决工具,被广泛应用于各行各业。
它以8个有序的步骤,系统地解决和改善问题,被许多企业认为是提升产品质量和管理效率的必备工具。
本文将通过一个实际案例,来展示8D报告在企业中的改善效果。
案例背景是某汽车制造企业的一个生产线出现了频繁的零部件故障问题。
故障导致生产效率下降,产品质量不稳定,给企业造成了巨大的损失。
为了解决这个问题,企业决定运用8D报告方法进行改善。
第一步:组建小组根据8D报告的要求,首先是组建一个由不同岗位代表组成的小组,以确保问题的全面性和多角度思考。
该小组由研发、生产、品质和技术等部门的代表组成,具备了解决问题所需要的知识和经验。
第二步:问题描述小组成员通过调查和观察,对故障问题进行了详细描述。
他们分析发现,故障主要发生在某特定型号的传感器上,故障频率逐渐增加并影响到整个生产线的稳定性。
第三步:立即控制为了避免故障继续扩大,小组采取了紧急措施,包括更换故障传感器、调整工艺参数以及加强产品质量检测。
通过这些措施,故障在一段时间内得到了一定的控制。
第四步:问题原因分析小组成员进行了深入的问题原因分析。
他们发现,由于生产线中使用的传感器来自多个供应商,供应商质量控制不一致导致了部分传感器质量不稳定。
此外,生产过程中的振动和温度变化也会对传感器的寿命和稳定性产生影响。
第五步:制定纠正措施根据问题原因分析的结果,小组制定了纠正和预防措施。
他们与供应商沟通并落实了强化质量控制的要求,采取了合适的设备和工艺参数以减少对传感器的损害,并优化了产品检测流程以确保产品出厂质量的稳定。
第六步:验证纠正措施效果通过对纠正措施的实施,小组对生产线进行了一段时间的观察,并收集相关数据进行分析。
结果显示,故障率明显下降,生产线稳定性得到有效提升。
这证明了所采取的纠正措施是有效的。
第七步:预防措施为了防止类似故障再次发生,小组总结前期经验和教训,制定了一系列预防措施。
福特经典8D报告模板
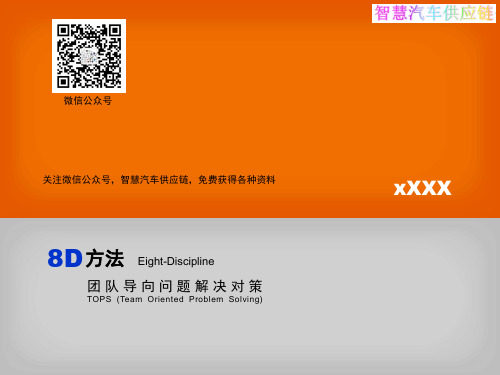
关注微信公众号,智慧汽车供应链,免费获得各种资料
xXXX
8D 方法
Eight-Discipline
团队导向问题解决对策
TOPS (Team Oriented Problem Solving)
导入:构建学习心态
NGSCC
充分的投入 开放的心态
投入多少,收获多少!
没有人靠节约成功!
经验往往是进一步成功的障碍!
硬工具与软工具 “软”决定“硬”
5
我们的直接差距:方法
我们并不缺少创业和发展的态度,缺少的是创业和发展的方法; 态度可以在一夜间转变,方法却要靠长期的学习和探索; 管理哲学、思想、态度、理论、工具最终表现为:方法
学习的方法 思考的方法 行动的方法
NGSCC
西方对管理方法的研究已有100多年:
NGSCC
通用技术 + 系统方法
8D
QC7 QFD DOE FMEA SPC MSA APQP IE
PM
TQM ISO9001 5S TPM
JIT
ZD 6sigma
不同的8D
美:严谨,重视人的组织和激励 日:重视实效(重视协作,有横向展开) 德:重视技术性
6
常用的方法和工具
8D方法(Eight-Discipline)也可称为TOPS (Team Oriented Problem Solving)即团队导 向问题解决对策。是福特公司处理问题的标准 方法,由8个步骤和一个准备步骤组成,这些步 骤用来客观地确定、定义和解决问题并防止相 似问题的再次发生。 8D方法亦适用于过程能力不足时采取系统措施, 它提供了一套符合逻辑的解决问题的组织方法, 同时对于统计制程控制与实际的质量提升架起 了一座桥梁。 8D方法简单易行,系统性强,效果显著,在国 际上被广为采用,并发展为多种形式。
尺寸不良8d报告改善的案例

尺寸不良8d报告改善的案例8d报告模板在质量管理活动中,我们常用到各种各样的质量工具,而大多数情况下,都是多种质量工具的混合使用.不管使用工具的多或者少,每种工具所发挥的成效都是特定的.有些工具长用记录,有些长于分析,有些长于决策,有些长于思考,而问题的解决都是多种工具配合使用所得,而这种配合的模式就形成了解决问题的套路.在某些大企业中,为了管理的方便,格式的统一,往往会固化成特定的标准化的模板.今天我们一起学习的这个工具就是一种套路,它就是福特汽车公司惯用的g8d报告.8d又称团队导向问题解决方法、8d问题求解法.是福特公司处理问题的一种方法,它提供了一套符合逻辑的解决问题的方法,同时对于统计制程管控与实际的品质提升架起了一座桥梁.目前已广泛应用于汽车制造行业,取得了显著的经济效益和社会效益.8d主要用于汽车及类似加工行业的问题解决方法.原始是由ford公司,全球化品质管制及改善的特殊必备方法,之后已成为qs9000/iso ts16949、福特公司的特殊要求.凡是做ford的零件,需采用8d作为品质改善的工具.后来名气大了,其它车厂也移植了福特的做法、使之成为汽车行业的标准做法.目前国际汽车行业(特别是汽车零部件产家)广泛采用来解决产品质量问题最好的、有效的方法.8d方法是一种归纳与推测的问题解决方法.归纳法以基于观测数据为起点,建立与数据一致的推测.推测法以一种推测为起点,并通过收集数据并分析来确定数据是否同理论一致,从而企图证明一个推测是否能适用于某个特定的条件.在8d程序的初始阶段期,主要是归纳法.收集以及分析数据,从而描述问题.确定可选择性的根本原因推测,并且与问题描述比较,从而确定最佳的推测.然后,通过收集数据,采用演绎法来确定这个最佳推测是实际的根本原因.解决问题时,团队经常在归纳法与演绎法之间转换.这通常是完成工程任务的最有效的方法.8d方法有以下几方面的明显作用:通过建立小组训练内部合作的技巧;提供一种通用的流程有效确定并解决问题;防止相同或类似问题的再发生;增加管理层对问题本身及解决方法的理解;鼓励直接开放的问题解决方法;提高顾客满意度,增强其对供方的产品和过程的信心.8d方法适用于以下两方面的情形;1.用于解决各类可能遇到的简单或复杂的问题;8d方法就是要建立一个体系,让整个团队共享信息,努力达成目标.8d本身不提供成功解决问题的方法或途径,但它是解决问题的一个很有用的工具;2.亦适用于过程能力指数低于其应有值时有关问题的解决;面对顾客投诉及重大不良时,提供解决问题的方法.我们常见的质量问题主要有两种类型:变异引起的问题和从未满足要求的问题.8d这套方法特别适合于解决由某个变化导致的问题,或者说是特殊原因引起的问题;6-sigma这套方法特别适合于解决从未满足要求的问题,或者说是普通原因引起的问题.8d方法和6-sigma都是用于解决质量问题的有效工具,两者在解决问题中相辅相成.8d是解决问题的8条基本准则或称8个工作步骤,但在实际应用中却有9个步骤:d0:准备8d过程d1:组建团队d2:描述问题d3:制定临时处置措施(ica)d4:确定并验证根本起因和遗漏点d5:选择并验证针对根本原因和遗漏点的永久性纠正措施(pca) d6:执行并确认pcad7:预防问题重现d8:表彰小组和个人的贡献针对每一步,我们详细介绍其使用过程:d0:准备8d过程实施本阶段的原因:g8d过程是一个可能涉及大量人力、时间和资源的过程,如果使用不适当将会浪费很多时间、人力和相关的一些资源.d0帮助我们把焦点放在问题上,以便有效地使用资源.本阶段实施过程:了解症状并量化症状,决定是否需要era,选择并验证era,执行并确认era,查看是否适用g8d标准.紧急反应措施(era)是保护顾客及相关的各方不受症状的影响的任何措施,它在g8d把问题和症状区分开来确认g8d是否有必要启动时应用.症状是可测量的事件或效果(它们必须是顾客体验到的),它表示一个或多个问题存在.如果没有症状,你就无法得知有问题存在.当症状能被测量或量化时,它才被考虑在内.通常有许多工具可以用来测量并量化故障:paynter图,柏拉图,运行(趋势)图,风险图等.g8d的适用标准:1.症状被定义;2.确定了顾客;3.存在性能差距;4.原因未知;5.管理层致力于从根本起因的层面去解决问题,并采取预防措施防止问题再次发生;6.症状很复杂,不可能单凭一个人的能力完成.如果六个标准都满足,并且没有其他的g8d团队为同样的或类似的问题工作,那么就应该开始g8d过程.d1:组建团队原因:组建团队是g8d过程中的重要部分.团队的功能需要花时间去增强,但是非常重要的是,一个人很少能拥有解决复杂故障所有必要的资源、信息、和技能.另一方面,合适的人一起工作能包括所有必要的特性,这建立在每个有关人员的技能的基础之上.建立一个团队是g8d过程的真正开始;团队成员的指导方针:1.团队成员的人数控制在4到10个之间;2.选择具有所需技能、知识、资源、权力等,这样的人作为团队成员来解决现有的问题;3.各类成员之间合理搭配;4.按需要调整团队成员.g8d的过程依赖于所有团队成员的努力来达到团队的目标.为了达到团队目标,每个成员扮演一个角色.团队设置负责人,团队领导,成员及其它角色.实现团队角色的指导方针:1.角色不是特指某个人,而是指要行使的职责;2.成员通常要在会议持续期间或是更长的时间内充当某个固定的角色;3.会议中角色的互换会导致混乱;4.一些角色是可以共同承担的,比如记录员等;5.监督人是g8d生产过程中的一个角色,然而,监督人不是团队的成员.6.调解工作在整个讨论过程中是必不可少的,通常这个角色由某个领导承担.团队运作程序的三个要素:1.确定团队运作的基本规则;2.分配任务、维护和过程观察;3.使用有效沟通交流的技巧.d2:描述问题目的:将问题清楚并且客观的描述会使问题最终得到有效的解决.帮助团队将焦点放在实际的问题上,避免直接对问题下结论或者作没有根据的设想.对问题的描述要基于观测的内容而非结论.要描述好一个问题,我们需要:1.对问题进行陈述;问题陈述应该是简单,简洁明了的陈述,它确定了发生问题的对象及其这个问题的缺陷.一个问题陈述能让团队关注,也能让范围缩小到寻找问题的根本原因上,通常当作问题描述的开端.2.对问题进行描述;问题描述是指根据问题是什么和不是什么,但可能是某种状况来确定问题的范围.一个详细的问题描述包括四方面的信息,什么时候、什么地方、发生什么及其问题的严重程度如何.问题陈述告诉了你最基本的事实,但是详细的问题描述给了你找到根本原因的细节.d3:制定临时处置措施(ica)目的:为团队找到问题产生的根源争取时间;保护顾客不受问题影响;ica是针对故障而非根本起因,在知道根本起因之前保护顾客.如果根本起因被查明,或者era(应急处理措施)足够可靠来继续保护顾客,可以不需要ica.ica与era的差异:era以最小的支撑数据执行.ica为调查提供更多的机会.任何你执行的ica必须保护顾客使其免受故障而不导致新故障的出现.同样,单一ica可能不够.你可能需要执行多个ica以充分保护顾客.执行ica的步骤;1.选择ica;确定选择标准,分析执行ica的好处,分析ica的风险性,在好处和风险性的最好平衡点选择ica.2.验证ica;实施前证明能保护顾客不受问题影响,能提供前后的对比,证明ica不会产生新的问题.常见的验证方法有:实验,演示,类似措施对比等.3.执行ica;按照pdca的循环进行,并制定行动计划.4.确认ica.确认是在成功的验证后,确认ica执行没有产生新的问题,确认形式:售前验证和售后顾客的验证.d4:确定并验证根本起因和遗漏点目的:找出根本起因是任何故障解决成就的重要部分.当确定了根本起因,可以在最根本的程度上解决一个故障.任何不是从根本起因入手的故障解决方案都仅仅是一个权宜之计,当识别出根本起因,就可以完全的消除了整个故障并使它决不再发生.原因的几种分类:可能原因:任何原因,常在一个因果图表里识别,它描述一个结果可能怎样发生.最可能的原因:根据可用的数据得到的一个理论,它可能最能解释详细的问题描述。
8D报告

二战期间,美国政府率先采用一种类似8D的流程——“军事标准1520”,又称之为“不合格品的修正行动及部署系统”。
1987年,福特汽车公司首次用书面记录下8D法,在其一份课程手册中这一方法被命名为TOPS(Team Oriented Problem Solving)即“团队导向问题解决法”。
8D问题求解法(8D Problem Solving),D是Discipline(步骤、原则)的首字母。
当时,福特的动力系统部门正被一些经年累月、反复出现的生产问题搞得焦头烂额,因此其管理层提请福特集团提供指导课程,帮助解决难题。
8D最先在福特内部使用、成熟后福特逐渐要求其供应商遇到问题也用此法。
后来名气大了,其它车厂也移植了福特的做法、使之成为汽车行业的标准做法。
再后来8D家喻户晓,各行业通吃。
而且不仅仅解决工作问题,解决家庭生活问题也很有效。
8D的适用范围1、该方法适用于解决各类可能遇到的简单或复杂的问题;2、8D方法就是要建立一个体系,让整个团队共享信息,努力达成目标;3、8D本身不提供成功解决问题的方法或途径,但它是解决问题的一个很有用的工具;4、亦适用于过程能力指数低于其应有值时有关问题的解决;5、面对顾客投诉及重大不良时,提供解决问题的方法;6、8D法是美国福特公司解决产品质量问题的一种方法,曾在供应商中广泛推行,现已成为国际汽车行业(特别是汽车零部件产家)广泛采用来解决产品质量问题最好的、有效的方法。
8D的目标1、提高解决问题的效率,积累解决问题的经验;2、提供找出现存的与质量相关的框架;3、杜绝或尽量减少重复问题出现;4、8D格式的原则上针对出现的问题,找出问题产生的根本原因,提出短期,中期和长期对策并采取相应行动措施;5、8D法可跨部门建立小组来加强部门间的协调,推进问题有效解决,从而改进整个过程的质量,防止相同或类似问题的再发生,以保证产品质量。
8D是解决问题的8条基本准则或称8个工作步骤,但在实际应用中却有9个步骤:D0:征兆紧急反应措施D1:小组成立D2:问题说明D3:实施并验证临时措施D4:确定并验证根本原因D5:选择和验证永久纠正措施D6:实施永久纠正措施D7:预防再发生D8:小组祝贺D0:征兆紧急反应措施目的:主要是为了看此类问题是否需要用8D来解决,如果问题太小,或是不适合用8D来解决的问题,例如价格,经费等等,这一步是针对问题发生时候的紧急反应。
8D报告课程案例

面对问题应群策群力,
相互提携74页。
特点2:此方法须通过“8D问题分析报告”体现。
特点3:此方法为如何从统计过程控制作业, 走向品 质实际提升,提供了一项具体的连系。
应用SPC
8D方法
提升过程能力
其他解决问题的方法:日本——QCC;
2022/1/20
通用(GM)——P R&R 6
顾客重新确 定职责
9
第三章:问题的提出和反映
问题来源于内部:
问题提出
问题的反映
(供方在24小时以临时纠正 措施反应)
问题的验证和确认
明确职责
2022/1/20
责任部门开始实施8D
10
过程
第10页,共74页。
第三章:问题的提出和反应
注意事项:
1、不管问题怎样提出或来自谁,都要求8D过程作为反应。
2、为鼓励供方和顾客之间的良好联系,顾客的工程师应该辅导供方 以在24小时内对任何问题迅速反应。可能的话,供方应该尽量派 一个代表到顾客处处理问题,帮助确定问题的根本原因。
常见性错误:
1、针对问题的现象而不是针对真正问题工作;
2、对问题的根本原因过早假设;
3、修订顾客对问题的描述作为自己的描述;
2022/1/20
21
第21页,共74页。
D2:问题描述—范例
A公司在接到顾客抱怨后,马上组成小组展开调查,确认问题如下:
在对样品进行检验后,结论与顾客一致,情况如下: 1 确认样品
为保证临时措施的效果,在确定临时措施后,应考虑以 下方面的问题:
1、所有可疑地点(供方现场/仓库、分供方现场、顾客现场、下一个顾 客现场、其他)的库存是否清查?
2、遏制的有效率是多少?是否满意?
机加工8d报告案例
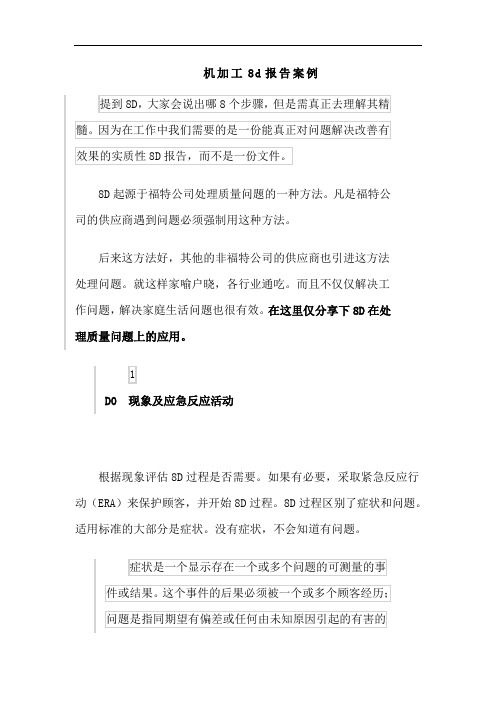
机加工8d报告案例提到8D,大家会说出哪8个步骤,但是需真正去理解其精D0现象及应急反应活动根据现象评估8D过程是否需要。
如果有必要,采取紧急反应行动(ERA)来保护顾客,并开始8D过程。
8D过程区别了症状和问题。
适用标准的大部分是症状。
没有症状,不会知道有问题。
当收到投诉信息时,质量部门应尽量在客户投诉报告上确认以下信息以便展开调查:·产品编号及品名·客户名称,联系人及地址·缺陷描述,不合格品数量·追溯信息,如LOT NO,发货单编号等·索赔应尽量取得车型等信息如有,应从客户处得到样品,照片,标签及不合格率等必要的信息。
如是芯体泄露或严重投诉,收到投诉的人应立即通知质量经理及总经理。
QE应在收到投诉一个工作日内与客户联系。
应就以下信息与客户沟通:·跨部门小组及联系方式·确认已得到的信息·调查问题所必需的其他信息·应急措施的进展·应急措施及纠正措施的预期完成时间·任何其它的客户要求,如,了解问题进展和期望的交货·所有与客户之间的回复均应记录。
QE根据得到信息,依据三现主义(现场,现物,现象)来确认不良状况;如果是可以目视的不良,尽量取得照片或样品(确认现物);对于不良发生场所状况尽量收集详细的情报(确认现场,现象)。
应急措施需要在24小时内展开。
D1建立8D小组没有团队的8D是失败的8D。
其实8D原名就是叫团队导向问题解决步骤。
8D小组需要由具备产品及制程知识,能支配时间,且拥有职权及技能的人士组成。
同时需指定一名8D团队组长。
因为我们要做的是:·建立一个由具备过程/成品知识的人员组成小组·确定时间,职责和所需学科的技术·确定小组负责人D2问题描述通过确定可定量化的项,谁,什么,何时,何地,为什么,如何,多少(5W2H),识别对象和缺陷(问“什么出现了什么问题”):·“什么问题”是缺陷·“什么出了问题”是对象问“什么出现了什么问题”能够帮助小组以问题陈述所需的两个基本要素为中心(对象和缺陷)。
福特8D报告示例(中英文)

Purchasing paperwork holders that will be hooked on the front of the pallets and tubs for easier identification. Holders to be delivered weeks of 12/12/00.
Reported By:
Joan Huber
Date:
12/12/00
Concurrence:
Supervisoryour teamq:\Customer Corrective Action Reports\8DBlank Form.xls
采购可以悬挂在托盘或桶前的纸夹,以便于确认。纸夹12/12/00之前应送到。
报告人:
Joan Huber
日期:
12/12/00
批准:
主管
日期:
(8)恭喜你的团队q:\顾客整改措施报告\8D空白表格.xls(文件存储路径)
SupplierA
8DConcern Analysis Report
Concern No.:
Joan Huber in to Livonia to relabel parts 11/28/00–no need to return parts. There were 39 totes to relabel.
(4)Define Root Causes:
Shipping department has put several new employees on all shifts, inexperienced packers used incorrect labels.