Z-P3脑力激汤因果图
特性要因图

是否遵守标准? 作业效率是否良好? 是否具有问题意识? 是否具有技朮? 是否具责任感? 是否具有经验? 是否具改善适当? 是否具改善意识? 人际关系是否良好? 健康状况是否良好?
人、机、料、法、环、测(5M1E)
机具、设备(Machine)
是否能负荷生产能力? 是否具备制程能力? 有无充分点检? 保养、加油是否适当? 是否时常故站障、停止? 精密度是否足够? 是否发生异常? 机具配置是否适当? 数量是否过多或过少? 整理、整顿如何?
层次原因 (4) 在鱼骨图中标出必要信息
注意事项:
利用5个为什么进行追踪原因 (5WHY,为什么产品泛白)
特性要因图的使用
(1) 问题的整理 (2) 追查真正的原因 (3) 寻找对策 (4) 教育训练
绘制特性要因图应该注意的事项:
(1) 绘制特性要因图要把握脑力激荡法的原则,让所有的成员表达心声 (2) 列出的要因应给予层别化(4M+1E) (3) 绘制特性要因图时,重点应放在为什么会有这样的原因,并且依照
脑力激汤术构想十大原则(BS)
不要批评构想 欢迎自由联想 创意越多越好 欢迎搭便车,利用别人的灵感刺激创意 不要太早下结论 讨论要力求集中,针对某一问题 破除阶级尊卑的意念,无拘无束一起讨论 将提出的意见,利用特性要因图一一记录下来 不要以个人冒充大家的意见 想出来的创意,要加以整理评价运用
人、机、料、法、环、测(5M1E)
为
(1)决定问题的特性 特性要因图之画法
什 么
(2)画一粗箭头,表示制程
饭
(3)原因分类成几个大类,且以 圈起来---中骨
不
(4)加上箭头的大分枝,约60°插到母线--子枝
好
(5)寻求中、小原因,并圈出重点
特性要因图培训
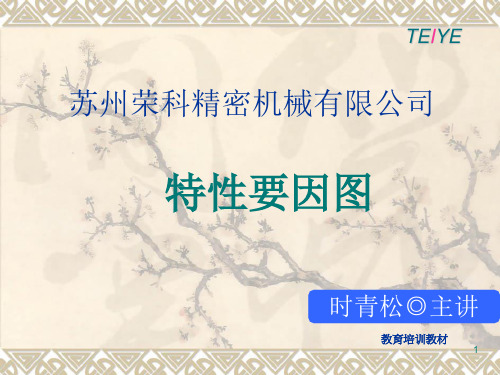
8
WHY: 为什么必要;
所 WHAT:目的何在;
谓 WHERE:在何处做;
5
WHEN:何时做;
W
1
WHO:谁来做;
H
HOW:如何做.
就 是
TEIYE
9
TEIYE
特性要因图的思考原则
(1)脑力激荡法 四原则: A.自由奔放 B.意见越多越好 C.严禁批评他人 D.搭便车 (2)5W1H法(WHAT WHERE WHEN WHO WHY HOW) (3)5M法(MAN、MACHINE、MATERIAL、METHOD、MEASUREMENT) (4)系统图法
TEIYE
1.确定问题 2.画粗箭头 3.因素即原因分类 常用:4M1E即人(员)、机(器)、料(原料)、法(工艺方法)、环 (境),有时还可以补充软(件)、辅(助材料)、公(用设施)三方面。 也可用:工序顺序等分类分类好后,用中箭头与主箭头成45°角画在主箭 头两侧。 4.对中箭头所代表的一类因素,要进一步将与其有关的因素以小箭头画到 中箭头上去,如有必要,可再次细分至可以直接采取行动为止。 5.检查所列因素有无遗漏,如有遗漏应予补充。 6.各箭头末端的因素中,凡影响重大的重要因????
5W1H
TEIYE
➢ 如何(How)
如何使方法、手段更简单? 情形到底是如何? 如何使作业方法简化,以减少劳力、降低成本? 要如何来做? 如何做才省力、省费用? 如何做最好?
23
(1)决定问题的特性 特性要因图之画法
(2)画一粗箭头,表示制程 (3)原因分类成几个大类,且以 圈起来---中骨 (4)加上箭头的大分枝,约60°插到母线--子枝 (5)寻求中、小原因,并圈出重点
2
TEIYE
质量管理新七种工具

整理课件
61
头脑案例1
整理课件
62
头脑案例2
整理课件
63
水平对比
水平对比法
水平对比法又叫标杆管理,是把产品或服务
的过程及性能与公认的领先者进行比较,以识
别改进机会的一种方法。
单一目的型 2 按结构形式分
中央集中型
单向汇集型
关系表示型
应用型
整理课件
9
多目的型
整理课件
10
单一目的
整理课件
11
中央集中1
整理课件
12
中央集中2
整理课件
13
单向汇总1
整理课件
14
单向汇总2
整理课件
15
关系表示
整理课件
16
应用型1
整理课件
17
应用型2
整理课件
18
关联步骤
关联图的绘制步骤
整理课件
32
因素步骤
因素展开型系统图的绘制步骤
1 明确主题 2 绘制图形 3 确定要素 4 进行评审
整理课件
33
措施展开
整理课件
34
因素展开
整理课件
35
PDPC法
过程决策程序图(PDPC)
为达到预期目的,事先预测过程可能发 生情况,采取相应预防纠正措施,提出实施 方案以达到目标的一种动态管理程序方法。
亲和图的绘制步骤
1 确定主题 2 收集资料 3 资料卡片化 4 汇总整理卡片 5 制作标签卡片 6 作图
整理课件
23
亲和案例
QCC品质工具
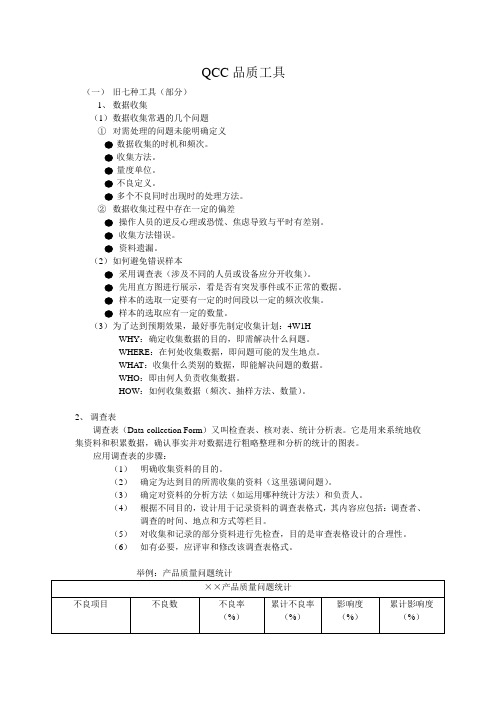
QCC品质工具(一)旧七种工具(部分)1、数据收集(1)数据收集常遇的几个问题①对需处理的问题未能明确定义数据收集的时机和频次。
收集方法。
量度单位。
不良定义。
多个不良同时出现时的处理方法。
②数据收集过程中存在一定的偏差操作人员的逆反心理或恐慌、焦虑导致与平时有差别。
收集方法错误。
资料遗漏。
(2)如何避免错误样本采用调查表(涉及不同的人员或设备应分开收集)。
先用直方图进行展示,看是否有突发事件或不正常的数据。
样本的选取一定要有一定的时间段以一定的频次收集。
样本的选取应有一定的数量。
(3)为了达到预期效果,最好事先制定收集计划:4W1HWHY:确定收集数据的目的,即需解决什么问题。
WHERE:在何处收集数据,即问题可能的发生地点。
WHAT:收集什么类别的数据,即能解决问题的数据。
WHO:即由何人负责收集数据。
HOW:如何收集数据(频次、抽样方法、数量)。
2、调查表调查表(Data-collection Form)又叫检查表、核对表、统计分析表。
它是用来系统地收集资料和积累数据,确认事实并对数据进行粗略整理和分析的统计的图表。
应用调查表的步骤:(1)明确收集资料的目的。
(2)确定为达到目的所需收集的资料(这里强调问题)。
(3)确定对资料的分析方法(如运用哪种统计方法)和负责人。
(4)根据不同目的,设计用于记录资料的调查表格式,其内容应包括:调查者、调查的时间、地点和方式等栏目。
(5)对收集和记录的部分资料进行先检查,目的是审查表格设计的合理性。
(6)如有必要,应评审和修改该调查表格式。
3、因果图因果图是表示质量特性波动与其潜在(隐含)原因的关系,即表达和分析因果关系的一种图表。
又称鱼骨图。
适用范围:对某一问题进行逐级分析,找出问题发生的根本原因,以促进问题的解决。
特点:(1)运用系统的方法(5M1E)找出可能导致问题产生的原因。
(2)能有效地从所有信息中识别最重要的影响因素。
(3)有效地运用有限的资源来处理问题。
QC七大手法
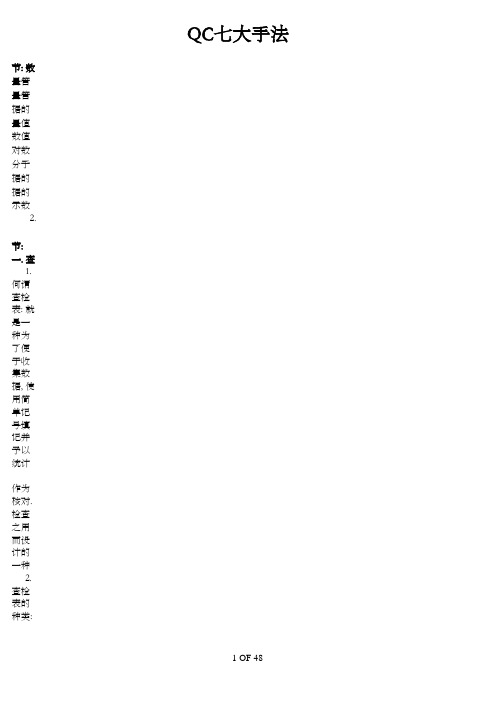
QC七大手法第一节: 数据的基本常识及其特性一. 质量管理常用的七种工具: 排列图. 因果分析图. 调查表. 直方图. 散布图. 管制图. 数据分层法.质量管理的"二图一表": 排列图. 因果分析图及我国传统的对策措施表.二. 数据的分类:1.计量值数据:可以连续取值的数据.如长度,重量等2.计数值数据:不能连续取值的,只能以个数计算的数据.它可细分为计件值数据和计点值数据3.相对数(即分数): 分子 / 分母当分子为计数值时, 则相对数为计数值; 当分子为计量值时, 则相对数为计量值.三. 数据的几个重要特征数数据的特征数可分为两类:1.表示数据集中位置的特征数.如平均数.中位数及中程众数等.2.表示数据离散的特征数.如极差.平均偏差.偏差平方和.方差和标准偏差等.第二节: QC七大手法一. 查检表(调查表/分析表/核对表):1. 何谓查检表: 就是一种为了便于收集数据, 使用简单记号填记并予以统计整理, 作进一步分析或 作为核对.检查之用而设计的一种表格或图表.2. 查检表的种类:2.1. 记录用(或改善用)检查表主要功用在于根据收集之数据以调查不良项目.不良主因.缺陷分布等情形.通常将数据分类 成数个项目, 以符号或数字记录作为分析问题及改善用的图或表.主要功用是为要确认作业实施.机械整备的实施情形或为预防不良事故, 确保安全时使用. 这 种点检表可以防止遗漏或疏忽的造成,检查作业基准,机械操作,机械部位等等是否正确. 亦即 把非做不可,非检查不可的工作或项目按点检顺序列出,逐一点检并记录之.二. 柏拉图(排列图):1. 柏拉图: 点上累积不良次数(或累积不良率或累积影响度), 并以折线连接这些点则得柏拉图.2. 作柏拉图的步骤:最后,若"其他"项目太大时, 要检讨是否尚有其他重要因素要提出.2.2 将各不良项目不良数及累积不良百分比记入坐标, 用折线连结各累积不良百分比坐标点即得 柏拉图. 横轴代表"不良项目", 纵轴左侧代表"不良数或不良百分比", 纵轴右侧代表"累积不良3. 柏拉图之用途:3.1 作为降低不良的依据;3.2 决定改善的攻击目标;3.3 用于整理报告或记录;3.4 确认或调整特性要因图;3.5 可作不同条件下的评估;3.6 确认改善的效果(改善前后之比较);3.7 应用于发掘现场的重要问题点.4. 哪些数据可以整理为柏拉图:4.1 质量方面:a. 不良品发生数. 损失金额. 可依不良项目别, 发生常所别, 发生制程别, 原料别, 材料别, 机 械别,设备别, 作业者别, 作业方法别……等结果或要因区分出情形.b. 消费者的抱怨件数. 修理件数. 抱怨项目别……等.4.2 时间方面------效率a. 作业的效率------制程别或单位作业别.b. 故障率. 修理时间------机械别. 设备别.4.3 成本方面:a. 装配品的零件单价别.b. 商品的原价别.c. 材料或原材料的单价别.4.4 安全方面:火灾的件数------场所别. 职种别及人体部位别.4.5 营业方面:利润的损益------商品销售量别, 销售金额别, 营业所别, 业务员别.三. 特性要因图(因果分析图)1. 何谓特性要因图: 对于结果(特性)与(要因)间或所期望之效果(特性)与对策间的关系, 以箭头连接, 详细分析原因或对策的一种图形称为特性要因图. 该图为日本品管权威人士石川馨博士于1952 年所发明, 故又称"石川图"; 因其形状似鱼骨, 故亦称鱼骨图; 因其是在阐明原因于结果之关系, 故 亦称因果图. 任何现场产品质量发生异常时, 必定有其原因, 所以要解决质量问题时, 必须先找出 影响质量特性的原因, 并加以纠正, 使其恢复正常, 则质量自然正常.例: "为何验货速度慢"的特性要因图2. 特性要因图的基本形态2.2 追求对策型 (鱼骨图反转)3. 特性要因图的画法.3.1 决定问题 (或质量)的特性.例如: 不良率. 停机率. 送修率. 抱怨的发生率以及尺寸不良率等.3.2 画特性要因图的骨架., 将特性写在右端, 自左画上一条较粗的干线(称母线)作代表制程, 并在干 线的右端画一指向右方的箭头.母线, 此大分枝称为子枝, 较母线略细.大原因可依制程别分类, 一般分为人. 几械. 材料. 方法及其他.3.4 探讨大原因的原因, 再细分为中小原因, 将其记入小骨及枝骨上(称孙枝. 曾孙枝).细分中小原因时, 应注意必须能采取对策者为主要条件, 且有因果关系者归于同一中.小枝骨内.3.5 决定影响问题点之原因的顺序以集中思考自由讨论的方式, 在所列出的原因中认为影响较大的画上红圈, 再从划上红圈中指 出认为影响更大者再画上红圈, 一一检讨下去.4. 绘图注意事项4.1 集合全员的知识与经验4.2 应用脑力激汤术, 全员发言4.3 把要因层别4.4 把重点放在解决问题上, 依5W 1H(Who. Where. What. When. Why & How)的方法逐项列出4.5 应按特性别绘出多张特性要因图4.6 原因解析愈细愈好, 但下图没有小骨的鱼骨图是不行的.4.7 确认原因的重要程度, 应考虑其可行性. 价值, 并经讨论表决后决定4.8 应将圈出的重要原因整理出来, 重新制作另一个特性要因图4.9 记入必要的事项于图旁, 例如: 制品名称. 工程名称. 完成日期. 参与者. 上司的确认及特别状况等 4.10 质量特性的决定现场以第一线所发生的问题来考虑. 例如:Q (Quality 质量)------ 产品特性. 寿命. 市场抱怨等等C (Cost 成本)------ 工数. 原价等等D (Delivery 交期)------ 生产率. 操作率等等M(Morale 士气)------ 出劝率. 改善提案件数. 团队精神等等S (Safety 安全)------ 整理整顿. 伤害. 安全等等5. 特性要因图的用途5.1 管理用5.2 改善解析用5.3 制定作业标准用5.4 质量管理导入及教育用四. 直方图1. 何谓直方图: 将所收集的测定值或数据之全距分为几个相等的区间横轴, 并将各区间内之测定值或 数据所出现的次数累积, 用柱子排起来的图形.2. 直方图的制作:2.1 在全体数据中找出最大值(Max.)与最小值(Min.)2.2 求出全距(Max. - Min.)2.3 决定组数(N): 一般取N=102.4 决定组距h(组距 = 全距 / 组数 = "Max. - Min." / N): 组距最好取"整数"和奇数.2.5 决定各组之上下组界最小一组的下组界 = 最小值 - h/2最小一组的上组界 = 下组界 + 组距依此类推…….2.6 计算各组的组中点("上组界 + 下组界" / 2)2.7 作次数分配表2.8 制作直方图3. 直方图的准则3.1 组距是决定直方图图形的主要因子, 如果组距太大或太小, 图形都会失真.3.2 将数据归成数个组3.3 组数最好大于5而小于153.4 每个组距应该相同4. 直方图的常见形态:正常型偏态型中部为顶峰, 左右两边低且近似对称一些有形位公差等要求的特性值是偏向型分布, 也有的是由于加工习惯造成. 例如由于加工者担心产生不合格品, 在加工孔时常常偏小而呈左偏型, 加工轴时常常偏大而呈右偏型双峰型锯齿型大多由于分组不当或检测数据不准而造成往往是不同材料, 不同设备, 不同操作者生产的两批产品混合在一起高原型测量有误或产生异常的因素而造成主要是由于生产过程中有缓慢变化因素而造成的. 如刀具的磨损, 操作者的疲劳等5. 制程能力分析五.层别法(分层法):1. 何谓层别法: 将不同作业者/作业群体的作业不良率.不同操作设备/原材料对产品的影响率以及不同的 操作环境对产品的影响等等用图表的形式层别出来.例如:下图为某缝纫极加工厂, 以同样的缝纫机予A. B. C三名作业员加工时之不良率情形, 取一个星期 的不良率(数据见下表), 经比较结果, 发现A作业员之不良率明显地高过B. C作业员, 反映在层别 图上表现为A曲线在B. C曲线之上., 应加以检讨.六. 散布图1. 何谓散布图: 为研究两个变量间之相关性, 而收集成对二组数据, 在方格纸上以点来表示出二个特性 值之间相关情形的图形.2. 图表的制作2.3 画出纵轴与横轴2.4 将各组数据点在坐标上2.5 必要时记入事项YX 3. 散布图之判读3.1 正相关3.1.1 显著正相关: X 增大 Y增大3.1.2 非显著性正相关: X 增大 Y 增大3.2 负相关3.2.1 显著性负相关: X 增大 Y减小3.2.2 非显著性负相关: X 增大 Y减小3.3 无相关3.3.1 X 与 Y 无关系3.3.2 X增大 Y不变3.4 曲线相关: X增大Y随之增大, 但达到某一值后, X增大Y却又减小.4. 散布图的功用4.1 知道两组数据间是否有相关及相关程度4.2 将人员. 机械. 材料. 方法等可能影响原因层别绘制成散布图, 可知何者影响结果4.3 找出相关特性, 依其关系简化检验, 以降低质量成本4.4 两者间呈直线, 可为订立标准之用七. 管制图1. 数据可分为以连续性之计量值(varible value)及以个数计算的间断性之计数值(attribute value)两种.2. 产品之差异主要有三大类:2.1 同体差异(Within-Piece Variation): 指在同一物体上所发生的差异.2.2 异体差异(Piece-to-Piece Variation): 指在同一时间制造的产品差异.2.3 时间性差异(Time-to-Time Variation): 指在不同时间制造的产品差异.3. 构成差异的主要因素有四:3.1 制程(Process): 这因素包括有工具的磨损.机器的震动.设计问题以及水力电力之波动等.3.2 原料(Material).3.3 操作人员(Operator)3.4 其他(Miscellaneous): 这方面包括环境因素如温度.亮度以及检查程序等.以上四个因素构成之差异渐趋于稳定及可预测时, 称之为机遇原因差异(Chance cause of variation). 机遇原因差异是不可避免的, 其通常都很细小, 而且较难测度. 相反, 有些因素构成的差异会很大及 易于测度, 称之为非机遇原因差异(Assignable cause of variation). 假如在生产过程中, 只有机遇原因差 异存在, 这生产过程便是在管制状态中, 否则便是不在管制状态中.4. 所谓管制图: 是一种以实际产质量特性与根据过去经验所判明的制程能力的管制界限比较, 而以时 间经过用图形表示者. 方法是将指示质量情况的统计指针在图上用点表示出来, 并在图中画出质量 管制界线(Control Limits)以作比较. 质量管制图是记录质量演变之时间表, 它显示出生产过程之稳定 情况. 如下简图示:5. 计量质量管理图有"X - R管制图". "X - R管制图"及X - Rs管制图三类.5.1 常用的X - R管制图X-Chart Central Line=XUpper Control Limit, UCL for X=X+3s=X+A2RLower Control Limit, LCL for X=X-3s=X-A2RUpper Warning Limit, UCL for X=X+2s=X+(2/3)A2RLower Warning Limit, LCL for X=X-2s=X-(2/3)A2RR-Chart Central Line=RUpper Control Limit, UCL for R=R+3s=D4RLower Control Limit, LCL for R=R-3s=D3RWhere A2,D3 and D4 are factors taken from standard table calculating control chart lines(See attached table A);标准偏差 s=算术平均值的标准偏差 s=例如: 作铁板厚度的 X-R Chart (See attached table B)Central Line=PUpper Control Limit, UCL for P=P+3 P(1-P)/nLower Control Limit, LCL for P=P-3 P(1-P)/nUpper Warning Limit, UCL for P=P+2 P(1-P)/nLower Warning Limit, LCL for P=P-2 P(1-P)/nP-Chart format see attached table C6.2 常用的C管制图Central Line=CUpper Control Limit, UCL for C=C+3 CLower Control Limit, LCL for C=C-3 CUpper Warning Limit, UCL for C=C+2 CLower Warning Limit, LCL for C=C-2 C例如: 布匹斑点不良数的C-Chart, see attached table D.7. 管制图的看法制程是否在管制状态可用下列原则判断:7.1 管制图上的点都出现在管制界线内侧,并没有特别排法时,原则上认为制程是正常.这种状态谓之管制状态;7.2 管制图上有点超出管制界线外时,就判断制程有了异常变化,这种状态谓之非管制状态;7.3 管制图上的点虽然未超出管制界线,但点的出现有下列排法时,就判断有异常原因发生:7.3.1 点在中心线的单侧连续出现7点以上时;7.3.2 出现的点,连续11点中有10点,14点中有12点,17点中有14点,20点中有16点出现在中心线 的单侧时;7.3.3 7点连续上升或下降时;7.3.4 出现的点,连续3点中有2点,7点中有3点,10点中有4点出现在管制界线近旁(警界线外)时;7.3.5 出现的点有周期性变动时.8. 管制图的判读8.1 一个正常形态的三项特性如下:8.1.1 管制图上,大多数点子应在中心线附近;8.1.2 管制图上,有少数点子出现在管制界线附近;8.1.3 正常的管制图上没有跑出管制界线的点子.8.2 不正常型态管制图的特性UCL 8.2.1 单独有一个点子出现在3s区域之外者;A区8.2.2 连续三点中有二点落在A区或A区以外者;B区8.2.3 连续五点中有四点落在B区或B区以外者;C区CL8.2.4 连续有八点落在C区或C区以外者.9.制程精密度Cp及其指数Cpk9.1 Cp=(Su-Sl)/6s=(上限规格-下限规格)/6x标准偏差9.2 Cpk=min[(X-LSL)/3S,(USL-X)/3s]=(T-2|M-X|)/6sT=尺寸公差; X=测量值的平均数; M=(标注尺寸最大值+标注尺寸最小值)/2; s=标准偏差.9.3 Cp与Cpk的关系:9.3.1 Cp≧Cpk;9.3.2 Cp只反映数据的集中度(即精密度);9.3.3 Cpk不但反映数据的集中度,而且反映数据的平均值偏离标准中心值的程度(精确度).11 OF 11。
QC七大手法及其他常用图表介绍
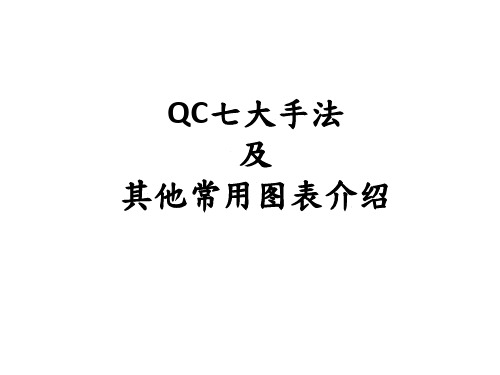
决定大要因
用四M一E来分类。 Man(作业人员)、Machine(机器)、 Material(材料)、Method(作业方式)等 四类,在再加上Environment(环境)。
决定中小要因 利用脑力激荡(Brain Storming)法。 决定影响问题点的主要原因: 检查是否有漏掉位未探讨的要因。 检查真正的原因是否写在适当的位置上。 词句的表现是否有抽象的字眼。
一,定义: 将一定期间所收集之不良数,缺点数, 故障数等数据,依项目别,原因别,位 置别加以分类,按其出现数据之大小 顺序列出,同时表示累积和之图形,称 为柏拉图,排列图,重点分析图或ABC 分析图.
柏拉图
柏拉图通常在办识出最重要的问题,因为
通常80%的总结果是来自20%的问题项目,
因此此图的优点是需要将关键少数特性一 目了然,以采取必要的手段来加以校正。
推挤感应力不足 抽风负压 吹倒 洗瓶机抽风 量太大 输送带速 度太慢 出口 孔太 小
极限开关跳脱
洗瓶机抽 风量太大
洗瓶机出口 处倒瓶
输送带速 满料无法有 度太慢 效推开铁片
出口后段 倒瓶
夹瓶器导轨夹 头脱落 导轨位 置不佳 导轨与夹头接触 夹瓶歪斜 距离太长 绞瓶 夹瓶器夹头材 质选用不当 支撑弹 簧弹性 差
星状轮凹槽端 撞击瓶身 星状轮设 星状轮设计不 计不佳 佳 出口星状轮 导入异常 定位方式无 标准 星状轮定位 位置不佳
输送带抖动
电眼无法侦测 固定力不足 未锁紧
停机电眼感 应方式不佳
设计不良 护栏固定夹 松脱 星状轮卡死 无运转
停机电眼感应 方式不佳
夹瓶器夹头材 夹瓶器夹头软防 质选用不当
蚀性不佳
查检表之分类
一般区分为二类: (1)检查用查检表: 将欲确认的各种事项全部列出而成的表格。 (2)记录用查检表: 将数据分为数个项目别后,用以符号或数 字记录成的表格或图。
Small group acitivities(SGA) Guide-Lean
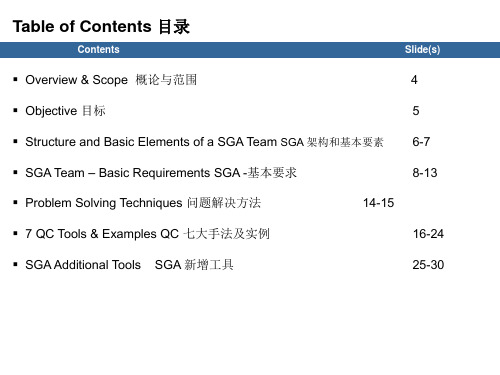
Objective 目标
▪ Motivate the shop floor operators , executives, superintendents as well as line Engineers to form small quality groups to focus on Defects, Inventory, Productivity, Lead Time, Scrap & Space improvement.
Leaders Role 领导者角色 ▪ Conduct all Team meetings. 主导所有团队会议; ▪ Lead the try-storming sessions of the Team. 主持脑力风暴会议 ▪ Identify area of opportunity for the group’s project. 识别项目改善机会. ▪ Encourage and guide team members to contribute and develop their ideas.
teamworktrystorming团队合作脑力风暴尝试攻坚collectiondata收集数据primerqctools基本qc工具paretodiagram柏拉图分析causeeffectishikawadiagramfishbonediagram因果图graphs图表checksheet检查表scatterdiagram散布图histogram柱状图controlcharts控制图smallgroupactivitysmallgroupactivityproblemsolvingprocedureproblemsolvingprocedure问题解决程序问题解决程序selectthemeselecttheme选择主题graspproblemareas确定问题的范围objectives确定目标establishtargetestablishtarget设立目标organizationstructure指派组织架构planactivityplanactivity计划行动problem分析问题现状findmaincausefindmaincause找出主要原因improvementplan调查改善计划examineimprovementmethods调查改善计划setupimprovementactivity设立改善行动implementimprovementplan执行改善行动confirmeffectivenessconfirmeffectivenessaction确认效果保持checkfollowupimprovementresults确认和跟进改善结果smallgroupactivitysmallgroupactivityqctoolsqctools7种种qcqc工具工具qctoolscommonlyusedcollecteddata
PDCA循环图及应案例46272
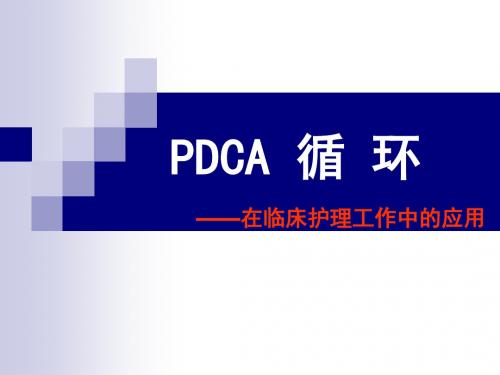
的手或敷料。 5、脐部护理未按常规要求进行。 6、产前宫内感染。
P3:主要原因1、2、4
P4:制定护理计划
1、加强产程管理,加强无菌操作意识。 2、脐周围严格消毒后再断脐,残端严格消毒,
(三)鱼骨图分析法的步骤
1、查找要解决的问题,把问题写在鱼骨的头上; 2、讨论问题出现的可能原因,尽可能多的找出问题。 3、把相同的问题分组,在鱼骨上标出; 4、根据不同问题,总结出正确的原因; 5、拿出任何一个问题,研究为什么会产生这样的问
题。
(四)绘图过程
1、填写鱼头(按为什么不好的方式描述),画 出主骨(鱼脊)。
D (执行)
执行计划
C (检查)
A (效果)
检查计划的 执行结果
总结成功经验 制定标准
把未解决的/ 新出现的问题 转入下一个
PDCA循环
四、PDCA的四个特点
1、大环套小环,小环保大环,互相促进,推 动大循环
AP CD
AP CD
AP CD
2、PDCA循环是爬楼梯上升式的循环,每转动 一周,质量就提高一步
PDCA循环实际上是有效进行任何一项工作的合 乎逻辑的工作程序。
六、鱼骨图简介
(一)定义
鱼骨图是一种发现问题“根本原因”的方 法,称之为“因果图”。因其形状如鱼骨,所 以又叫鱼骨图。
(二)头脑风暴法的基本概念
头脑风暴法( Brain Storming ——BS) 又 称脑力激荡法或自由思考法(畅谈法,畅谈会,集 思法)等 ,它是一种通过集思广益、发挥团体智 慧,从各种不同角度找出问题所有原因或构成会 议的要素方法,BS有四大原则:严禁批评、自由 奔放、多多益善、搭便车。
企业创新管理ppt课件

最新版整理ppt
(二)创新时代产品品质观念 (六个希格玛原理S4)
顾客
厂商
效用
Utility
价值
Worth
可利用性
Availability
外 合功 知 情 经 数 时
观 适能 识 绪 济 量 间
37
最新版整理ppt
廿一、环球几家大企业创新情况
麦当劳: -把所有经理的椅子靠背锯掉;
肯德基 -用“特别顾客”监督分店;
企业家创新管理
1
最新版整理ppt
一、经济生产五要素 (Factors of Production)
1、自然资源 natural resources
2、劳动力 labor 包括劳力与劳心之人的努力
3、实物资本 physical capital 工具、机具、其他生产装备
4、人力资本 human capital
19
最新版整理ppt
十、讨论:
Q. 企业的成功关键需要怎样的人才?
20
最新版整理ppt
十一、创新概论
(一)、创新: 人们为了发展的需要,运用已知的信息,不
断突破常规;发现或产生某种有价值的新事物、 新思想的活动。
NEW!
21
最新版整理ppt
(二)、创新讨论
Q. 创新与创意及发明有何差异?
22
最新版整理ppt
Andrew S: Grove:
“10倍速的时代已经来临,我们的失败和成功都以10倍速 的节奏进行”
“80%的危机和20%的机会” “只有偏执狂才能生存”
12
Henry Ford: “不创新,就灭亡” 最新版整理ppt
(三)、利润=收入>成本
收入=产品价格与销售数量的函数 价格=产品属性及销售数量的函数 所以,关键在于创新(Innovation)
QC培训(鱼骨图和头脑风暴)解析

应注意事项:
1.确定原因时通过大家集思广益,充分发扬民 主,以免疏漏 2.确定原因,尽可能具体 3.无因果关系者,予以剔除,不予分类 4.验证:如果分析出的原因不能采取措施,说明 问题还没有得到解决.要想改进有效果,原因必 须细分 5.重点放在解决问题上,并依结果提出对策,依 5W2H原则执行
(what,when,who,where,why,how,how much
特性要因图 (鱼骨图)
为了更好的提供线索和贡献,先了解 一下什么是:
脑力激荡术 (头脑风暴)
脑力激荡术(Brain storming)最先的含 义是精神病患者的头脑错误状态
大家所知精神病患者最大的特征是在言语与肢体行 为上随心所欲的表现,而无视他人的存在,此行为 固然不合乎社会行为礼节的规范,但从创造思考的 角度来看:摆脱世俗礼教与传统观念的束缚,得到 无拘无束的构想。
(3)准备必要的用具,在开会时将大家的创 意要点迅速的记录下来。
2.引发和产生创造思维的阶段 注意要点: (1)与会者都是平等的,无领导和被领导之分; (2)与会的成员依次发表意见; (3)成员可以相互补充各自的观点,但不能评论、更不能批驳 别人的观点;创意或发言内容的正误、好坏完全不要去批评, 如果创意或意见被批评,与会者就不会提意见了。开会时, 如有批评者,组织者要暗示制止;
脑力激荡术是集体思考的方式,形式上 与一般会议相似,一组人运用开会的方 式,由一人主持,一人将所提出的构想 以书面的方式呈现在会议人面前,以期 待激荡出创造性问题解决方案
脑力激荡术(头脑风暴法)的应用步骤:
1.准备阶段 (1)准备会场,安排时间.会议时间以一小时为宜, 不要超过2小时.时间过长,与会人员疲倦,少有 创意,同时也失去兴趣. (2)确定会议的组织者,明确会议的议题和目的. 应用头脑风暴法的目的在于为与会者创造一 个激发思想的氛围,让与会者 “眉头一皱,计 上心来”,积极发表自己的意见和看法,做 到“知无不言,言无不尽”
因果关系图模型
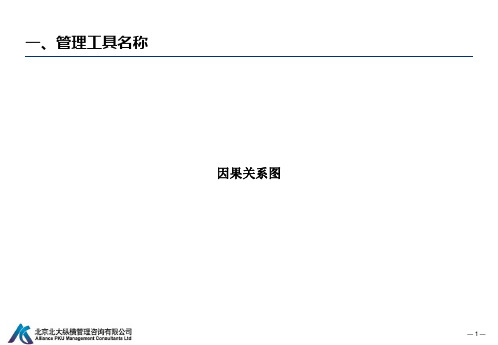
三、管理工具操作介绍(在企业战略目标分解过程中的应用为例)
说明:X、Y、Z仅为代码
—3—
因果关系图
因果图的三种类型 1)整理问题型鱼骨图(各要素与特性值间不存在原因关系,而是结构构成关系) 2)原因型鱼骨图(鱼头在右,特性值通常以“为什么……”来写) 3)对策型鱼骨图(鱼头在左,特性值通常以“如何提高/改善……”来写)
问题1:经过统计商贸公司2001年9月—2002年3月的销售,总体毛利率为不到8%,注意:此毛利率是在公 司无低毛利的家电以及百货毛利率近20%的基础上产生的总体毛利率,相对于市场状况以及竞争对手 来讲,此毛利率偏低,从中反映了占销售比重近80%的超市经营毛利不正常。
问题2:经过进一步的市场调查,针对超市每个业种安排如下数量的市调(按销售数量排名),得出以下数 据比较:
因果图的制作 制作鱼骨图分两个步骤:分析问题原因/结构、绘制鱼骨图。 1)分析问题原因结构 针对问题点,选择层别方法 按头脑风暴分别对各层别类别找出所有可能原因(因素)
—4—
因果关系图
分析选取重要因素 检查各要素的描述方法,确保语法简明、意思明确 分析要点: 1)确定大要因(大骨)时,管理类问题一般从“人事时地物”层别,应视具体情况决定; 2)大要因必须用中性词描述(不说明好坏),中、小要因必须使用价值判断(如…不良);
— 18 —
具体措施与目标: 1、在解决主要问题的基础上,逐步改进存在的问题,加强内部管理。公司正面临ISO9000的改版,可以通
过此次改版的规范努力改善相应管理秩序的问题;时间:3个月 2、加强专题培训,提高全员素质。主要为以下几方面的专题:A、采购原则与谈判;B、促销;C、陈列;
D、市场调查。时间:2周 3、科学有效的进行市调安排,充分了解和把握市场:由于前面市调数据具有片面性,应该将现有500余家
头脑风暴及因果图
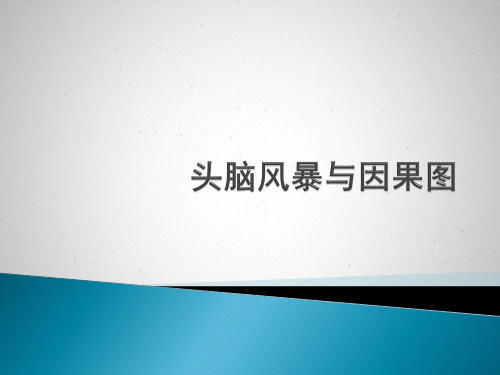
4
…
5
…
说明:每项得分1-9分 预期效果好、容易实现、实施成本低、所需时间短的得分高(单项最高9分) 预期效果差、不易实现、实施成本高、所需时间长的得分低(单项最低1分)
✓ 组织者将因果图得出的重要提案汇总成表格,组织相关人员评估。 ✓ 评估结果按优先级排序。
明确议题 头脑风暴 分析评估 确定方案
① 电源不耐久; ② 防水性能不佳,水洗时即报废; ③ 抗撞击性能不好; 。。。 ✓ 确定出3-5点重点关注事项。
步骤7 整理记录,编制实施方案或方案。
1、提案再分析 组织者采纳优先级靠前的几个提案; 有必要对提案再次讨论的可开展二次头脑风暴或质疑头脑风暴。 对一次BS产生的提案进展二次开发还经常采用质疑BS;质疑BS是指参 与者根据组织者确定的的提案提出质疑,评论有碍提案实现的所有限制 性因素;组织者将质疑BS的结果整理成评论意见一览表,用于形成可行 性分析报告。 2、确定实施方案 组织者根据BS产生的记录,查阅有关文献,组织语言,编制实施方案。
➢ 简介
脑风暴法是当今最负盛名、最实用的一种集体式创造性解 决问题的方法。“头脑风暴〞〔Brain Storm〕原意是:“突 发性的精神错乱〞,表示精神病患者处于大脑失常状态的情形。 “头脑风暴法〞亦简称“BS法〞,是将少数人召集在一起,以 会议的形式,对于某一问题进展自由地思考和联想,提出各自 的设想和提案。
3
1
1
1
6
3
4
…
5
…
说明:每项得分1-9分 预期效果好、容易实现、实施成本低、所需时间短的得分高(单项最高9分) 预期效果差、不易实现、实施成本高、所需时间长的得分低(单项最低1分)
步骤6 经过评估确定对“能耗计算记录装置〞进展研发。 组织者还可组织质疑头脑风暴,收集更多相关信息。 如:“能耗计算记录装置〞质疑头脑风暴:
- 1、下载文档前请自行甄别文档内容的完整性,平台不提供额外的编辑、内容补充、找答案等附加服务。
- 2、"仅部分预览"的文档,不可在线预览部分如存在完整性等问题,可反馈申请退款(可完整预览的文档不适用该条件!)。
- 3、如文档侵犯您的权益,请联系客服反馈,我们会尽快为您处理(人工客服工作时间:9:00-18:30)。
6. 散佈圖
5. 柏拉圖
4
鱼骨图
• 1952年日本Dr.石川馨首先应用于QC分析上 • 透过数人脑力激荡方式作成,事倍功半,效果最佳 • 鱼骨图(特性要因图):即是原因和结果关系的表示方
法,将产生问题的要因加以整理成为相互关系并有条 理的图形
5
镀膜制程改善要因图
提升产品良率
提高抽样检查水平
接着剂里的异物 接着剂里的气泡 镀膜品不良 接着剂粘度
材料
*环境中存在灰尘附着时,肉眼无法辨认的灰尘(注意生物的界面活性分子膜)
胶合失效 (气泡、异物、刮伤)
11
表面检查标准由30μm 提高到25μm
镀膜靶台熔料需确实 镀膜参数设定得当
镀膜制程的确认
镀膜环境改善 净化房改善
机台内部清理
实施镀膜专业培训
实施质量意识
人员教育训练
6
1.切割制程问题分析要因切图 割异常要因分析(1)
人员操作 操作标准化
进料检查 点检不到料
单片式污染(胶合时) 尺寸设定及公差
切割速度
材料
胶合失效 (气泡、异物、刮伤)
8
鱼骨图 制作要点
主类别
次类别
子类别
异常
9
镀膜异物要因分析(3)
3.镀膜异物问题分析要因图
人员操作 操作不当
点检不到位
机器
监控系统失控 设施故障
(水、电、气) 均匀板
镀膜参数
镀膜前附着 移动中附着 镀膜时附着
原材质不良 加工时造成
镀膜不良 (镀膜、光谱偏移、膜层色异、溅镀)
环境
ห้องสมุดไป่ตู้
材料
*原材料及加工后,肉眼无法辨识,但造成镀膜不良
10
胶合异常要因分析(4)
4.胶合制程问题分析要因图
单片式污染 (胶合前加工) 洗净不洁 清洗干燥时附着 搬运时附着
作业者附着
单片式污染(胶合时) 单片保管中附着
搬运中附着
胶合时附着 作业者手、衣服、 道具
胶合时产生气泡 环境不良 光照不当 涂接着方法 胶合制程
脑力激荡
三车间培训课程(P3) 1
2007-4-12 6-8 pm
老人 與 美女
2
脑力激荡原则
•
禁止批评
•
自由奔放
•
点子多多亦善
•
欢迎搭便车
•
全员发言
3
x
1. 管制圖
LSL
USL
2. 直方圖
Day shift Night shift
7. 層別法
鱼骨图
3. 特性要因圖 / 魚骨圖
item 4. 查檢表
残留油渍 尺寸不良 刮伤 崩边 制程不良
光轴角度 晶片异物 针孔 刀具不良
材料
切割不良 (尺寸不良、刮伤)
7
研抛异常要因分析(2) 2.研抛制程问题分析要因图
人员操作 操作标准化
点检不到位
机器 厚度设定及公差
倒边量设定 光圈、平行度
残留抛光液 刮伤 厚度不良 光圈不良 制程不良
研磨剂 抛光膜 清洗剂