数控化改造要求 g
龙门铣床数控化改造

龙门铣床数控化改造
一、龙门铣床数控化改造概述
龙门铣床数控化改造是指将普通的龙门铣床进行数控改造,使其能够
按照设置的程序自动运行,以实现自动化的外形加工功能,经过数控改造后,可实现多种加工模式及更高精度的加工结果。
数控化改造可以提高龙
门铣床的效率,节约大量加工时间,有效的提高企业的生产效率,进而提
升企业的经济效益。
二、数控化改造优势
1、操作简便:由于采用了数控技术,只需修改加工程序即可实现快
速更换产品,使操作更为简便,减少人工操作次数,大大提高了生产效率。
2、加工精度高:数控技术采用程序控制,可以准确控制尺寸加工参数,更加准确的实现各种尺寸的加工,提高工件的加工精度。
3、安全性高:数控化改造后可以保证操作更为安全可靠,无需有人
员手动操作铣刀,可以减少事故及伤害的几率,进而提高安全性。
三、数控化改造实施方案
(1)确定目标:首先要明确改造的目标,包括改造的设备、改造的
内容等。
(2)制定方案:根据改造的目标,要有完善的方案,应包括改造方案、技术规格及计划等。
(3)实施改造:根据方案进行数控化改造,完成安装及调试等工作,工作要求符。
普通铣床数控化改造设计

普通铣床数控化改造设计随着现代制造技术的发展,数控机床已经成为现代制造业中不可或缺的一部分。
普通机床通过进行数控化改造,可以大大提高机床的生产效率和生产质量,同时也可以节约生产成本,提高企业的竞争力。
本文将介绍普通铣床数控化改造的设计方案。
一、数控化改造的必要性普通铣床具有结构简单、成本低的特点,但是由于其操作人员需要进行繁琐的手动调节和操作,使得生产效率低下,并且生产过程容易出现误差,影响了产品的质量。
而通过进行数控化改造,可以将机床操作变为全自动化、智能化的过程,提高生产效率、减少生产成本、提高生产质量。
二、数控化改造方案1. 基础设施改造为了使普通铣床能够进行数控化改造,需要进行一些基础设施的改造。
首先需要对机床进行检查和维护,保证机床的各项性能稳定而可靠。
还需要更换一些传统机械设备,例如步进电机控制器、主轴马达等,以便与数控系统兼容。
2. 数控系统升级普通铣床数控化改造的核心是将其搭载上数控系统,此时该机床将变身为数控铣床。
数控系统包括软件和硬件两个部分。
在硬件方面,需要更换一些关键配件,例如控制器、转换器、数据采集卡等。
而在软件方面,需要安装数控程序,司机、可编程逻辑控制器(PLC)等。
3. 人机界面改造人机界面是指人员与机床进行交互操作的一种方式。
在数控化改造的过程中,必须更新和升级人机界面,设计一种更加符合人工智能化特点的操作系统。
这种新的人机界面一方面需要方便操作,另外一方面也要考虑到用户体验的舒适性。
三、数控化改造后的效果通过对普通铣床的数控化改造,可以大大提高机床的生产效率和生产质量。
一方面,由于取消了传统的人工调整和操作环节,使得生产效率得到了极大的提高。
另一方面,由于数控系统具有高度准确度和稳定性,生产过程中误差较少,从而提高了产品的质量。
同时,通过数控化改造,企业还可以获得以下优势:降低人员培训成本,减少错误发生的几率,提高内部交流和生产计划的灵活性。
这些优势都可以为企业的生产和发展带来实质性的帮助。
普通车床数控化改造的主要内容

普通车床数控化改造的主要内容
1.数控系统的安装与调试:将数控系统安装在车床上,并进行相关调试,确保其正常运行。
2. 电机和传动系统的更新:将传统的电机和传动系统替换为具有更高性能的电机和传动系统,以确保数控系统的稳定性和精度。
3. 自动化控制系统的集成:将自动化控制系统集成到数控系统中,以实现对车床的自动化控制和监控。
4. 床身和导轨的改造:对床身和导轨进行优化改造,以提高车床的刚性和稳定性,从而提高加工精度和效率。
5. 刀架和刀具系统的升级:升级刀架和刀具系统,以适应数控系统的要求,提高加工精度和效率。
6. 系统的集成和测试:将各个部分集成起来,并进行测试和调试,以保证整个数控化改造系统的正常运行。
通过上述内容的改造,普通车床能够实现数控化加工,提高加工精度和效率,满足市场对加工品质和效率的要求。
- 1 -。
数控机床改造方案的选择
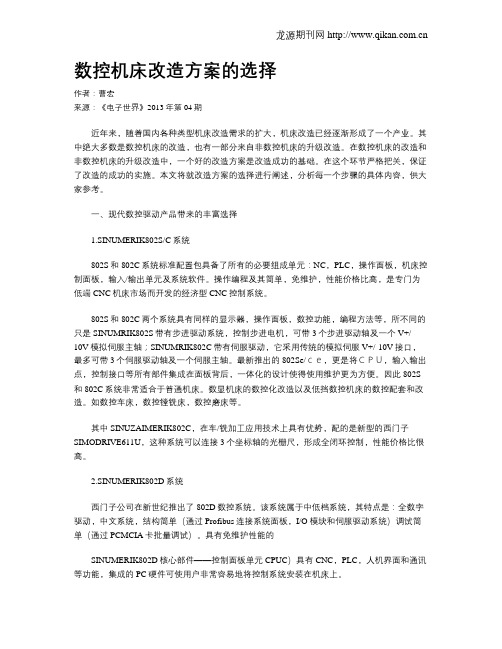
数控机床改造方案的选择作者:曹宏来源:《电子世界》2013年第04期近年来,随着国内各种类型机床改造需求的扩大,机床改造已经逐渐形成了一个产业。
其中绝大多数是数控机床的改造,也有一部分来自非数控机床的升级改造。
在数控机床的改造和非数控机床的升级改造中,一个好的改造方案是改造成功的基础。
在这个环节严格把关,保证了改造的成功的实施。
本文将就改造方案的选择进行阐述,分析每一个步骤的具体内容,供大家参考。
一、现代数控驱动产品带来的丰富选择1.SINUMERIK802S/C系统802S和802C系统标准配置包具备了所有的必要组成单元:NC,PLC,操作面板,机床控制面板,输入/输出单元及系统软件。
操作编程及其简单,免维护,性能价格比高,是专门为低端CNC机床市场而开发的经济型CNC控制系统。
802S和802C两个系统具有同样的显示器,操作面板,数控功能,编程方法等,所不同的只是SINUMRIK802S带有步进驱动系统,控制步进电机,可带3个步进驱动轴及一个V+/-10V模拟伺服主轴;SINUMRIK802C带有伺服驱动,它采用传统的模拟伺服V+/-10V接口,最多可带3个伺服驱动轴及一个伺服主轴。
最新推出的802Se/ce,更是将CPU,输入输出点,控制接口等所有部件集成在面板背后,一体化的设计使得使用维护更为方便。
因此802S 和802C系统非常适合于普通机床。
数显机床的数控化改造以及低挡数控机床的数控配套和改造。
如数控车床,数控镗铣床,数控磨床等。
其中SINUZAIMERIK802C,在车/铣加工应用技术上具有优势,配的是新型的西门子SIMODRIVE611U,这种系统可以连接3个坐标轴的光栅尺,形成全闭环控制,性能价格比很高。
2.SINUMERIK802D系统西门子公司在新世纪推出了802D数控系统。
该系统属于中低档系统,其特点是:全数字驱动,中文系统,结构简单(通过Profibus连接系统面板,I/O模块和伺服驱动系统)调试简单(通过PCMCIA卡批量调试)。
普通车床数控化改造
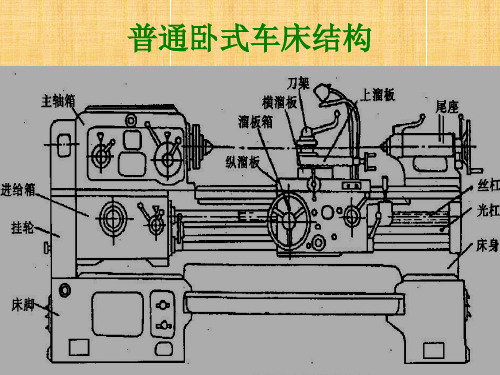
4.螺纹编码器的安装方案
螺纹编码器又称主轴脉冲发生器或 圆光栅。数控车床加工螺纹时,需 要配置主轴脉冲发生器,作为车床 主轴位置信号的反馈元件,它与车 床主轴同步转动。
1、同轴安装 同轴安装是指将编码器直接安装在主
轴后端,与主轴同轴,这种方式结构简单, 但它堵住了主轴的通孔。 2、异轴安装
异轴安装是指将编码器安装在床头箱
二、总体方案的确定
总体方案应考虑车床数控系统的运动方式、 进给伺服系统的类型、数控系统的选择,以 及进给传动方式和执行机构的选择等。
(1)普通车床数控化改造后应具有单坐标 定位,两坐标直线插补、圆弧插补以及螺纹 插补的功能。因此,数控系统应设计成连续 控制型。
(2)根据系统的功能要求,需要扩展 程序存储器、数据存储器、键盘与显示 电路、I/O接口电路、D/A转换电路、串 行接口电路等;还要选择电动机的驱动 电源以及主轴电动机的交流变频器等。 (3)为了达到技术指标中的速度和精 度要求,纵、横向的进给传动应选用摩 擦力小、传动效率高的滚珠丝杠螺母副; 为了消除传动间隙提高传动刚度,滚珠 丝杠的螺母应有预紧机构等。
(4)拆除四方刀架与上溜板总成,在横溜 板上方安装四工位立式电动刀架。 (5)拆除横溜板下的滑动丝杆螺母副,将 滑动丝杆靠刻度盘一段锯断保留,拆掉刻度 盘上的手柄,保留刻度盘附近的两个推力轴 承,换上滚珠丝杠副。 (6)将横向进给伺服电机通过法兰座安装 到横溜板后部的纵溜板上,并与滚珠丝杠的 轴头相联。 (7)拆去三杆(丝杆、光杆与操纵杆), 更换丝杆的右支承。
2.安装电动卡盘
为了提高加工效率,工件的夹紧 与松开采用电动卡盘,选用呼和 浩特机床附件总厂生产的 KD11250型电动三爪自定心卡 盘。卡盘的夹紧与松开由数控系 统发信控制。
普通车床的数控化改造方案
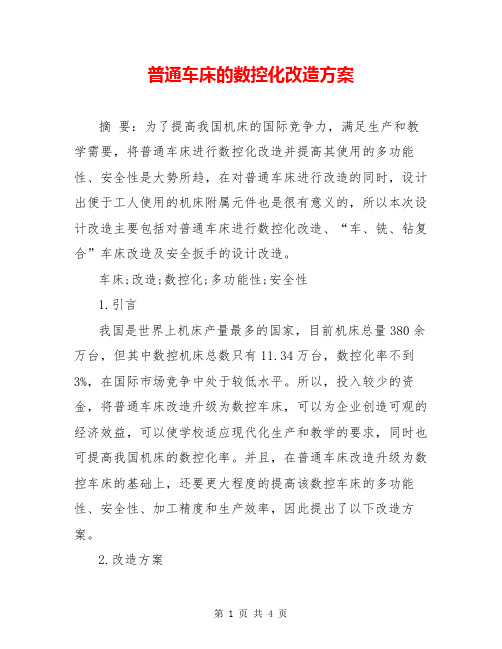
普通车床的数控化改造方案摘要:为了提高我国机床的国际竞争力,满足生产和教学需要,将普通车床进行数控化改造并提高其使用的多功能性、安全性是大势所趋,在对普通车床进行改造的同时,设计出便于工人使用的机床附属元件也是很有意义的,所以本次设计改造主要包括对普通车床进行数控化改造、“车、铣、钻复合”车床改造及安全扳手的设计改造。
车床;改造;数控化;多功能性;安全性1.引言我国是世界上机床产量最多的国家,目前机床总量380余万台,但其中数控机床总数只有11.34万台,数控化率不到3%,在国际市场竞争中处于较低水平。
所以,投入较少的资金,将普通车床改造升级为数控车床,可以为企业创造可观的经济效益,可以使学校适应现代化生产和教学的要求,同时也可提高我国机床的数控化率。
并且,在普通车床改造升级为数控车床的基础上,还要更大程度的提高该数控车床的多功能性、安全性、加工精度和生产效率,因此提出了以下改造方案。
2.改造方案2.1数控化改造方案对普通车床进行数控化改造,可以提高加工效率、加工精度和自动化程度,数控改造分为硬件设计和软件设计两个部分。
硬件设计主要包括液压卡盘、液压尾座的总体布局设计,及其主要零件形状、尺寸、材料的设计,在制造前还要对其进行有限元分析^p ,从而优化设计;软件设计主要包括PLC 和CNC系统的设计,包括CNC系统的选择及电气控制线的连接、PLC系统的选择及与CNC机床联接方式的确定,并设计与其配套的附属元件。
2.2“车、铣、钻复合”车床改造方案车铣复合是实现工件完整加工的有效方法,减少了零件在加工中重复拆卸、安装、找正所耗费的时间。
动力刀塔的设计是车铣复合车床的重要部分,它的性能将直接影响零件的加工精度、表面质量和机床生产率。
基于以上考虑,将动力刀塔设计如下:动力刀塔由步进电机、伺服电动机、横溜板、燕尾槽动导轨、立柱、动力头、刀具等组成,其中动力头是主要组成部分。
动力头部分可以安装十二把刀具,分别为车刀、铣刀、钻头、螺纹刀等;动力头安装在立柱上,可做旋转运动,方便了更换刀具;立柱可以沿着燕尾槽动导轨上下滑动,同时与主轴的旋转运动相配合,可以实现刀具与工件之间X向、Y向的相对运动。
普通车床数控化改造设计说明书
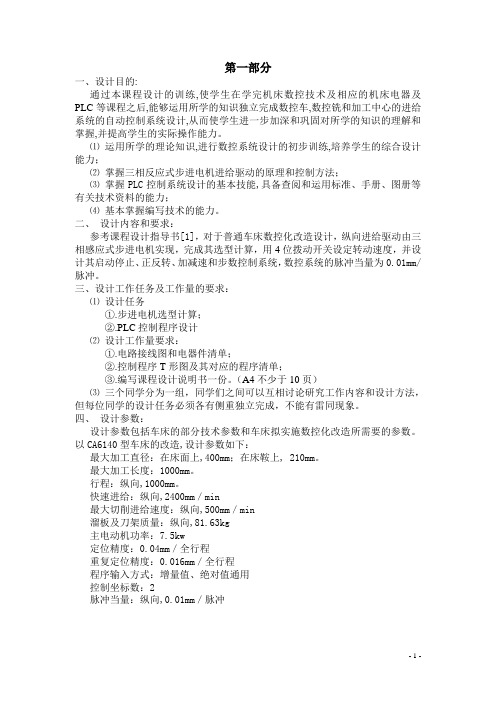
一、设计目的:通过本课程设计的训练,使学生在学完机床数控技术及相应的机床电器及PLC等课程之后,能够运用所学的知识独立完成数控车,数控铣和加工中心的进给系统的自动控制系统设计,从而使学生进一步加深和巩固对所学的知识的理解和掌握,并提高学生的实际操作能力。
⑴运用所学的理论知识,进行数控系统设计的初步训练,培养学生的综合设计能力;⑵掌握三相反应式步进电机进给驱动的原理和控制方法;⑶掌握PLC控制系统设计的基本技能,具备查阅和运用标准、手册、图册等有关技术资料的能力;⑷基本掌握编写技术的能力。
二、设计内容和要求:参考课程设计指导书[1],对于普通车床数控化改造设计,纵向进给驱动由三相感应式步进电机实现,完成其选型计算,用4位拨动开关设定转动速度,并设计其启动停止、正反转、加减速和步数控制系统,数控系统的脉冲当量为0.01mm/脉冲。
三、设计工作任务及工作量的要求:⑴设计任务①.步进电机选型计算;②.PLC控制程序设计⑵设计工作量要求:①.电路接线图和电器件清单;②.控制程序T形图及其对应的程序清单;③.编写课程设计说明书一份。
(A4不少于10页)⑶三个同学分为一组,同学们之间可以互相讨论研究工作内容和设计方法,但每位同学的设计任务必须各有侧重独立完成,不能有雷同现象。
四、设计参数:设计参数包括车床的部分技术参数和车床拟实施数控化改造所需要的参数。
以CA6140型车床的改造,设计参数如下:最大加工直径:在床面上,400mm;在床鞍上, 210mm。
最大加工长度:1000mm。
行程:纵向,1000mm。
快速进给:纵向,2400mm/min最大切削进给速度:纵向,500mm/min溜板及刀架质量:纵向,81.63kg主电动机功率:7.5kw定位精度:0.04mm/全行程重复定位精度:0.016mm/全行程程序输入方式:增量值、绝对值通用控制坐标数:2脉冲当量:纵向,0.01mm/脉冲一、 步进电机选型计算:(一)纵向进给传动链的设计计算 1、主切削力及其切削分力计算 ⑴ 计算主切削里z F已知机床主电动机的额定功率m P 为7.5KW,最大工件直径D=400mm,主轴计算转速n=85r /min 。
机床数控化改造

0 0 mm 的要 求 , 去 加 工 该零 件需 1 0个 工 时 ( .9 过 2 包 括 打磨 处 理 ) 数 控 化 改 造后 缩 短 为 2 个 工 时 ( 需 , O 不 打磨 ) 生 产效 率 为 改 造前 的6倍 。 , 2 .机 床 数 控 化 改 造 可 以 提 高 机 床 的性 能 和 质 量 , 工 出 普 通 机 床 难 以加 工 或 者 不 能 加 工 的 复 杂 加 型 面零 件 , 航空 发 动 机 叶 片 、 如 整体 涡 轮 等 。 3 .机 床 数控 化 改 造后 可实 现柔 性 自动 化 生产 。
速 , 方 兴 未艾 。 正
经 数 控 化 改 造 机 床 的 优 越 性
1 .机 床 数 控 化 改 造 可 以 提 高 零 件 的加 工 精 数 控 化 改 造 是 提 高 工 业 装 备 水 平 的 基 本 途 径 之 一
众 所 周 知 , 造业 是 国 民经 济 的 基 础产 业 和 支 制
制 造 大 量 数 控 机 床 的 同时 , 非 常 重 视 对 普 通 机 床 也
的数控 化 改 造 , 床 的技 术 改 造市 场 十 分 活跃 , 床 机 机 改 造业 正 逐 步从 机 床 制 造业 中分 化 出来 , 成 了用 形 数 控技 术 改 造 机床 和 生 产线 的新 的行 业 和 领域 。在
美 国 ,机 床 改 造 业 被 称 为 机 床 再 生
( ma u a tr g 业 ; 日本 , 床 改 造 业 被 称 为 Re n fcu i ) 在 n 机 机床 改 装 ( er f t g 业 。 R to i i ) tn
磨床数控化改造设计
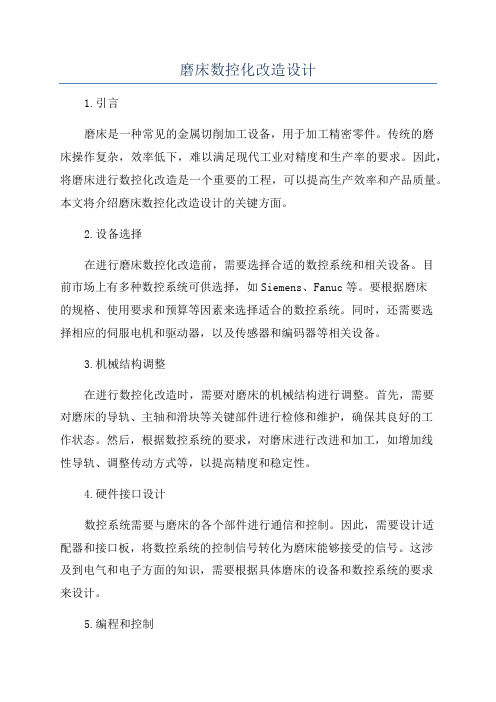
磨床数控化改造设计1.引言磨床是一种常见的金属切削加工设备,用于加工精密零件。
传统的磨床操作复杂,效率低下,难以满足现代工业对精度和生产率的要求。
因此,将磨床进行数控化改造是一个重要的工程,可以提高生产效率和产品质量。
本文将介绍磨床数控化改造设计的关键方面。
2.设备选择在进行磨床数控化改造前,需要选择合适的数控系统和相关设备。
目前市场上有多种数控系统可供选择,如Siemens、Fanuc等。
要根据磨床的规格、使用要求和预算等因素来选择适合的数控系统。
同时,还需要选择相应的伺服电机和驱动器,以及传感器和编码器等相关设备。
3.机械结构调整在进行数控化改造时,需要对磨床的机械结构进行调整。
首先,需要对磨床的导轨、主轴和滑块等关键部件进行检修和维护,确保其良好的工作状态。
然后,根据数控系统的要求,对磨床进行改进和加工,如增加线性导轨、调整传动方式等,以提高精度和稳定性。
4.硬件接口设计数控系统需要与磨床的各个部件进行通信和控制。
因此,需要设计适配器和接口板,将数控系统的控制信号转化为磨床能够接受的信号。
这涉及到电气和电子方面的知识,需要根据具体磨床的设备和数控系统的要求来设计。
5.编程和控制数控化改造后,磨床需要进行编程和控制。
编程是通过数控系统来告诉磨床如何进行加工操作和移动。
传统的编程方式是使用G代码和M代码,但随着技术的发展,现在还可以采用CAD/CAM软件来进行编程。
控制是指数控系统对磨床进行运动控制和参数调整。
数控系统可以通过插补算法来实现复杂的运动轨迹控制,同时也可以根据不同的工件进行参数调整,以实现更高的加工效率和精度。
6.总结磨床数控化改造可以提高加工效率和产品质量,是现代工业中的重要工程。
在进行数控化改造设计时,需要选择适合的数控系统和相关设备,调整磨床的机械结构,设计硬件接口,进行编程和控制。
这些关键方面的设计将直接影响磨床的数控化改造效果。
因此,在设计过程中需要充分考虑实际情况和需求,确保改造后的磨床能够满足生产要求。
机床的数控化改造

1 机 床 的 数 控 化 改 造 的 前 期 分 析
1 . 性 价 比分 析 1
纸 上 作 出 标 记 , 止 遗 漏 或过 拆 。在 拆 的 过 程 中 也 会 发 现 一 些 新 系 统 防
设计 中 的欠 缺 之处 , 及 时补 充 与修 正 。 补 的 系统 要 妥 善 保 管 , 应 拆 以备
【 摘 要】 本文通过机床 的数控化改造的前期分析 , 机床 数控 化改造的基本 内容、 基本步骤基本 方法等相 关内容 , 论述 了机床的数控化 改造
是 一 门 综合 性 的 系统 . 程 。 Y -
【 关键 词】 机床 ; 数控 化改造 ; 机械
中 国是 一 个 传 统 的机 械 制 造 大 国 目前 一 些 建 厂 历 史 悠 久 的机 械 度 地 提 高 水 平 和 档 次 的 更 新 改 造 。 制 造 厂 大 量 使 用 着 相 当 数 量 役 龄 较 长 的 机 床 , 备 水 平 落 后 , 远 不 设 远 能 满 足 现代 复 杂 零 件 的加 工 要 求 。 因 此 , 传 统 机 械 制造 设 备 进 行 改 对 造 , 决 机 械 制 造 业 中 的历 史 遗 留 问题 。 现 代 先进 技 术 对 旧设 备 进 行 31 原 机 床 的 全 而 保 养 。原 机 床 经 长 期 使 用 后 , 要 进 行 全 面 保 养 。 解 用 . 需 改 造 和 提 升 , 我 国机 械 制 造 业 丞 待 解 决 的现 实 问 题 。 采 用 先 进 的工 其 次 , 对 机 床 作 一 次 改 前 的几 何 精 度 、 寸 精 度 测 量 , 记 录 在 案 。 是 应 尺 并
科技信息
0机械 与电子 O
S I N E&T C N L G F R TO CE C E H O O YI O MA I N N
数控机床改造的必要性及改造技术要求
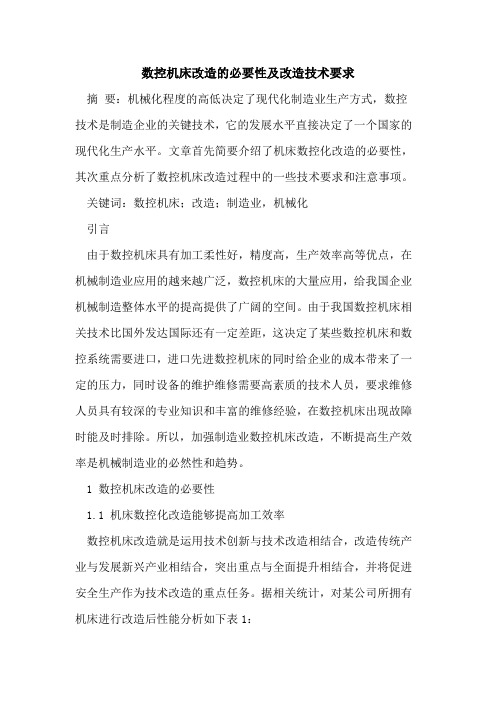
数控机床改造的必要性及改造技术要求摘要:机械化程度的高低决定了现代化制造业生产方式,数控技术是制造企业的关键技术,它的发展水平直接决定了一个国家的现代化生产水平。
文章首先简要介绍了机床数控化改造的必要性,其次重点分析了数控机床改造过程中的一些技术要求和注意事项。
关键词:数控机床;改造;制造业,机械化引言由于数控机床具有加工柔性好,精度高,生产效率高等优点,在机械制造业应用的越来越广泛,数控机床的大量应用,给我国企业机械制造整体水平的提高提供了广阔的空间。
由于我国数控机床相关技术比国外发达国际还有一定差距,这决定了某些数控机床和数控系统需要进口,进口先进数控机床的同时给企业的成本带来了一定的压力,同时设备的维护维修需要高素质的技术人员,要求维修人员具有较深的专业知识和丰富的维修经验,在数控机床出现故障时能及时排除。
所以,加强制造业数控机床改造,不断提高生产效率是机械制造业的必然性和趋势。
1 数控机床改造的必要性1.1 机床数控化改造能够提高加工效率数控机床改造就是运用技术创新与技术改造相结合,改造传统产业与发展新兴产业相结合,突出重点与全面提升相结合,并将促进安全生产作为技术改造的重点任务。
据相关统计,对某公司所拥有机床进行改造后性能分析如下表1:由上表可以看出,机床数控化改造以后加工精度提高了20%,废品率由12%减少到6%,工人的劳动强度大大降低,节省了劳动力,产品的生产周期明显缩短,给企业带来了巨大的经济利益。
1.2 机床数控化改造能够提高数控机床的安全水平目前,我国数控机床安全问题是一直以来困扰其发展的一大阻碍,机床数控化程度不高,安全水平较低,容易造成人员伤害事故。
进行数控化改造后,操作系统和操作界面越来越符合人机工程的要求,不仅仅能够提高机床的加工效率和自动化、智能化水平,更重要的是能够大幅降低操作人员接触危险部位的可能性,减少因失误产生的事故,安全性能得到明显改善,事故率显著降低。
1.3 机床数控化改造能够减少机床成本对于大型、价格较高的机床进行数控改造是较佳地选择,不仅可以节省较多资金,还可以缩短购置时间。
普通机床数控化改造中要考虑的主要问题

3 机床 机械 部件 的改 造
作者简介 : 刘丽云( 9 7 ) , 1 6 一 女 河北人 , 高级讲师 , 主要从事机械制造与设计 的教学 和研究 。
家 的数 控 系 统 。
把原有机床进行升级改造 , 使之变成数控 机床 , 就成 了解决 问 题的最好办法。 现在 , 机床的改造 , 特别是把普通机床改造成经 济型数控机床 , 已成为企业设备投资的重要组成部分 。现将机
床改造 中要考虑的主要 问题介绍如下 :
另外 , 在资金允 许 的条件 下 , 尽量 向著名厂家型号 系列靠 拢 。一般著名厂商此类 系统零件筛选更严格 , 制造工艺更规范
可靠 , 性能稳定 , 能更好 地预防 电器元 件的故障或提前失效 引
起 的设备故障 , 也有利于维修 。
1 数控 系统 的选择
数控系统是数控机床 的中枢 , 是其 中最关键 的环节。 目前 ,
市场上数控系统 的类 型较多 , 选择 时要保证能购得最适合 的系
2 伺服 系统 的选择
为开环控 制系统 、 半闭环控制系统和闭环控制 系统 三类 。在普
统, 就必须要充分考虑改造中各方 面的因素 。 首先 , 要考虑机床的功能要求 。根据机床 的功能要求选择 数控系统 , 以使数控系统所具有 的功能与准备改造的机床所能
达到的功能相匹配。既要避免 因面追求 数控 系统 的高性能指
确定 其步距精度 , 然后再对 它的转矩进行选 择 , 最后选定 步进
电机 驱 动 器 。
其次, 要考虑数控 系统 的制造厂商 。老牌著名跨国公司主 要有德国的西门子、 日本 的发 那科和三菱 、 国的 N M等 , 法 V 国 内公 司主要有 中华数控 、 中国珠峰 、 北京航天等 。 目前 , 口系 进
CA6132车床的进给系统数控化改造(GSK系统)

目录目录 (1)摘要 (2)1 绪论 (3)2 CA6132数控改造总体方案 (5)2.1CA6132概述 (5)2.2拟定总体改造方案 (7)3 进给伺服系统机械改造 (11)3.1进给系统机械结构改造设计 (11)3.2进给伺服系统机械部分的计算与选型 (11)3.3步进电机的选择 (15)4 CA6132车床控制系统设计 (18)4.1CA6132控制要求分析 (18)4.2CA6132车床电气控制设计 (18)总结 (22)参考文献 (23)摘要装备制造业和数控技术是现代工业的基础,随着我国国民经济的的快速发展,国民经济的各个部门对所生产的产品的性能要求越来越高,采用数控机床是实现多品种小批量生产的主要途径。
然而,高速、高精度、高自动化的数控机床价格仍然较为昂贵,且订货周期较长,无法满足生产急需。
采用数控改造技术对原有普通机床进行改造是提高机床的加工范围、加工精度,提高自动化生产水平的重要途径。
数控机床伺服系统是影响数控机床系统加工性能的重要指标,围绕伺服系统动态特性与静态特性的提高,近年来发展了多种伺服驱动技术。
针对把CA6132车床改造为经济型数控车床的目标,对车床的进给系统进行设计。
其设计的思路是根据执行件所受到的载荷,选择并校核其相关的零部件,包括滚珠丝杠螺母副、减速齿轮和电机,本文还对机构的重要零件作了比较详细地介绍。
最后,本文针对改造后的CA6132数控车床的电气控制系统提出了设计方案。
关键字:数控改造;装备制造;进给系统;1 绪论机械装备制造业是国民经济的支柱产业之一,直接影响着国民经济各部门的技术进步,同时反映了国家科学技术发展水平和国民经济的实力。
近年来,结合机电技术、液压技术、气动技术为一体的数控机床在机械装备制造业中广泛应用,已成为不可或缺的加工设备。
帮助人们解决了机械加工制造过程中的许多问题,使结构复杂、批量小、精度高、形状多变的零件的加工变得简单,提高了生产效率和机械自动化程度。
浅谈普通机床的数控化改造

浅谈普通机床的数控化改造摘要:本文重点介绍了普通机床数控化改造的必要性及数控化改造的内容及其优缺点,以及如何进行普通机床的数控化改造,包括数控系统的选择要素,并对数控改造中如何对主要机械部件进行改造进行了探讨,列举了普通机床数控改造的主要步骤。
最后说明了普通机床数控改造中经常遇到的问题及其解决方案。
关键词:机床数控改造集成性能调整1946年世界上第一台计算机诞生了,开创了机器部分代替“人脑”的先河,为当今信息社会的产生及数控技术的应用奠定了基础。
随着1952年计算机技术在机床上的应用,人类历史上诞生了第一台数控机床。
在数控技术发展过程中,数控技术在机加工领域的应用经历了两个阶段。
第一阶段为数控(NC)阶段—此阶段为数控技术应用的初期阶段,起源于1952年。
当时,人们仅采用数字逻辑电路搭成机床专用计算机作为数控系统,简称为数控(NC)。
第二阶段为计算机数控(CNC)阶段—此阶段起源于1970年,随着小型计算机的诞生,人们开始将其移植到机床的数控系统作为数控的核心部件。
1 普通机床的数控化过程随着计算机技术的发展和应用,数控技术在机加工领域的应用也在不断的提高和创新。
在进入20世纪70年代年以后,随着集成化电路的应用,使计算机的硬件实现了集成化和小型化。
20世纪90年代以后,随着小型计算机的发展,使得小型个人计算机(PC)作为前端机来处理人机界面、编程、联网通信等变的更加方便。
随着智能化技术的应用,数控系统的智能化水平也在不断提高。
例如,人们应用自适应控制技术来检测数控过程中的一些重要信息,并自动调整系统的有关参数,达到改进系统运行状态的目的;将加工的一般规律和特殊规律存入系统中,以工艺参数数据库为平台,建立具有人工智能的操作系统等等。
数控系统在机加工领域的应用,大大提高了机床的性能。
如何提高和改善普通机床性能,成为机床行业的一个新课题。
图1描绘了普通机床的数控化改造过程。
2 普通机床数控改造的必要性数控机床有许多优于普通机床的特性,这些特性主要来自数控系统的控制能力和计算能力。
车床的数控化改造方案(精简)
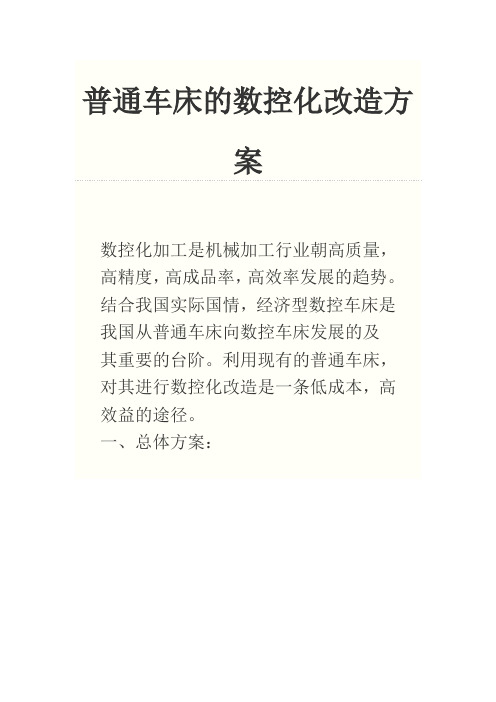
普通车床的数控化改造方案数控化加工是机械加工行业朝高质量,高精度,高成品率,高效率发展的趋势。
结合我国实际国情,经济型数控车床是我国从普通车床向数控车床发展的及其重要的台阶。
利用现有的普通车床,对其进行数控化改造是一条低成本,高效益的途径。
一、总体方案:图1 数控系统的总体框架配置总体框架说明:1、PC机可采用工控PC机,可满足该控制系统的控制要求。
2、运动控制卡。
我们采用了由ADVANTECH公司生产的PCL运动控制卡。
该卡是一种高速三轴步进电机运动控制卡,它有16位的数字输入、输出口,可实现三轴联动。
因此,它可以满足车床X,Z轴联动,实现直线,圆弧插补。
3、光电耦合电路是自己设计的,它的作用是能够隔离外部干扰信号对运动控制卡的信号冲击,提高系统的稳定性。
4、机床本体是由C613改造而来,拆除原来的丝杆,溜板箱,变速箱等,保留原来的三爪卡盘等。
5、步进电机及其驱动器是采用南京四通公司的。
驱动器的输入电压式45V,考虑步进电机的步距角和丝杆的螺距,本系统X轴的脉冲当量是0.00125,Z 轴的脉冲当量是0.0025。
完全能够达到0.005mm的加工精度要求。
6、各种限位开关,减速开关,回零开关均安装在机床本体上,限位开关是起这硬件硬限位的作用,当车床加工工件超出加工范围时,车床自动停止加工。
减速开关的作用是当车床刀架回零并走到车床零点附近时,减速开关被开启并通知车床减速走到零位置。
二、进给系统的设计考虑到该数控系统是开环控制,没有位置反馈,故进给系统尽可能的要减少中间传动环节。
本车床的X,Z两轴进给系统去掉了原来的进给系统的中间传动环节,直接采用了步进电机+刚性联轴器+滚珠丝杆的传动方案。
拆除原来的丝杆,增加少量的机械附件,就可安装步进电机及滚珠丝杆螺母副。
根据计算,要求步进电机的扭距是5 Nm。
我们选用步进电机是南京四通公司的86BYG250C-SAFRBC-0302,步距角选用0.9/1.8,扭距是7.5Nm。
浅谈普通车床的数控化改造
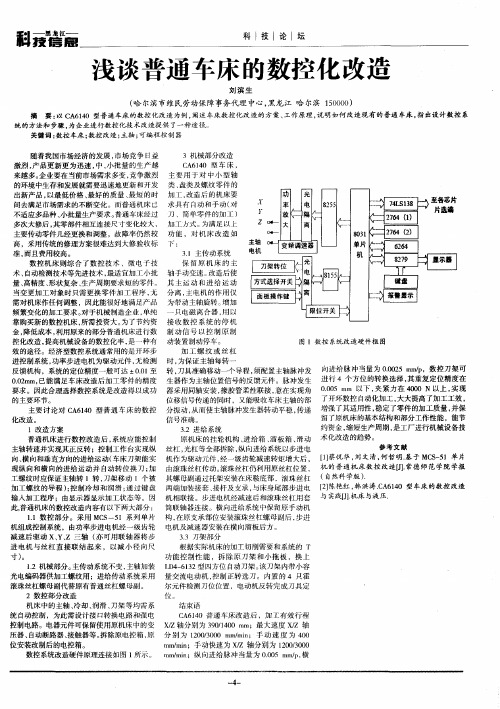
Z.大 _ 离 0 _
回
方选开 黼 式择关
I
囤
一
普通机床进行数控改造后 , 系统应 能控 制 原 机 床 的 挂 轮 机 构 、 给 箱 、 板 箱 、 动 进 溜 滑 主轴转速并实现其正反转 ;控制工作台实现纵 丝杠 , 光杠 等全 部 拆 除 , 向进 给 系统 以步 进 电 纵 向、 横向和垂直方向的进给运动 ( 车床刀架能实 机作为驱动元件 , 经一级齿轮减速转矩增大后 , 现纵 向和横 向的进给运动并 自动转位换刀 ; 加 由滚珠丝杠传动。 滚珠丝杠仍利用原 丝杠位置, 工螺纹时应保证主轴转 1转 , 刀架移动 1个被 其螺母副通过托架安装在床鞍底部 ,滚珠丝杠 加工螺纹的导程 )控制冷却 和润 滑 ; ; 通过键盘 两端加装接套 、 接杆及支承 , 与床身尾部步进 电 输 入 加工 程 序 ;由显 示 器显 示 加 工状 态 等 。 因 机相联接 。步进电机经减速后和滚珠丝杠用套 此, 普通机床的数控改造内容有以下两大部分: 简 联轴 器 连接 。横 向 进 给 系统 中保 留原 手 动 机 1 . 1数控部分 。采用 MC -5 S 1系列单片 构 , 原 支 承部 位 安 装 滚珠 丝 杠 螺母 副后 , 进 在 步 机组成控制系统 ,由功率步进电机经一级齿轮 电机及减速器安装在横向溜板后方。 减速后驱动 x、 z三轴 ( Y、 亦可用联轴器将 步 3 刀架 部 分 3 进 电机与丝杠直 接联结起 来 ,以减 小径 向尺 根据实际机床的加工切削需要和系统的 T 寸 ) 。 功 能控制性能 ,拆除原 刀架和小 拖板 ,换 上 1 . 2机械部分 。 主传动系统不变 , 主轴加装 L 4 6 3 四方位 自动 刀 架 。 D — 12型 陔刀架 内带 小 容 控制正转选刀。内置的 4 只霍 光电编码器供加工螺纹用 ; 进给传动系统采用 量交流电动机 , 滚珠丝杠螺母副代替原有普通丝杠螺母 副。 尔 元 件检 测 刀 位 位 置 ,电 动机 反 转 完 成 刀 具定 2 数 控 部分 改 造 位。 机床 中的主轴 、 、 冷却 润滑 、 刀架等均需系 结 束 语 统 自动 控 制 ,为 此需 设 计 接 口转 换 电路 和 强 电 C 6 4 普通 车 床 改 造 后 ,加 工有 效 行 程 A 10 控制 电路。电器元件可保留使用原机床 中的变 X Z轴分别为 3 010 m;最大速度 XZ 轴 / 9 /4 0 m / 压器 、 自动 断路 器 、 触 器 等 。 除原 电控 箱 , 分 别 为 10 /00 mmmi; 手 动 速 度 为 4 0 接 拆 原 2 03 0 / n 0 位安装改制后的电控箱 。 m / i;手动快速为 XZ轴分别为 10 / 0 m mn / 20 00 3 数控系统改造硬件原理连接如图 l 所示。 rmri;纵 向进 给脉 冲 当量 为 005 m / , a /n a .0 m p横
普通机床的数控化改造
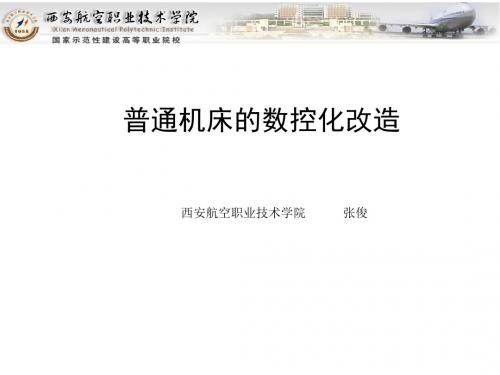
图7-5 消隙联轴器 1—套筒 2、3—锥环 4—压盖 5—轴 6—螺钉
图7-5 消隙联轴器 1—套筒 2、3—锥环 4—压盖 5—轴 6—螺钉
图7 工作台加平衡 液压缸或配重
3)升降台式铣床工作台重,而且铣削力也较大,垂直丝杠要配备 功率较大的驱动电动机,且比较难选,因此可在工作台上加配重 或平衡液压缸来平衡(见图7)。
2.铣床的数控化改造
(1)工作台的进给运动 因为改造后的机床主要加工圆弧、凸轮一
类平面曲线轮廓,所以采用微机数控系统实现三坐标两轴联动控 制,工作台纵向(X轴)、横向(Y轴)及垂直方向(Z轴)的运动分别 由步进电动机经过一级齿轮减速后由滚珠丝杠副拖动。
(2)结构设计 1)应尽量消除齿轮副和丝杠副的间隙,齿轮采用双片薄齿轮错齿 法消除间隙。 2)若采用直流伺服电动机作驱动元件,伺服电动机的轴端为光轴, 齿轮与电动机轴、电动机轴与传动轴采用锥环无键连接较方便。
3)导轨副。 4)主轴脉冲发生器。 5)安装电动卡盘或液压卡盘。
(5)安装调整中应注意的问题 1)利用螺母的间隙调整装置调整丝杠副间隙时,应使调整后产生 的预紧力为丝杠副最大负载的 1/3 为宜。
2)传动丝杠轴线上各联轴套上的锥销孔应按十字分布方式进行配 作。 3)消除齿轮间隙的方法很多,调整中心距的方法是最简便的一种。 4)滚珠丝杠副的制造精度要求较高,加工工艺比较复杂,都是由 专业工厂按系列化进行生产。 5)主轴脉冲发生器的引出轴与车床主轴按1∶1无间隙柔性连接传 动,连接后应保证两者有很好的同步性。
1)纵向滚珠丝杠。
图2 车床纵向传动的支承结构 1、4—推力球轴承 2、10—径向滑动轴承 3—左端轴承座 5—左接杆 6、9—联轴套 7— 滚珠丝杠副 8—螺母座 11—丝杠托架 12—消隙变速箱 13—步进电动机
普通车床数控化系统改造方案
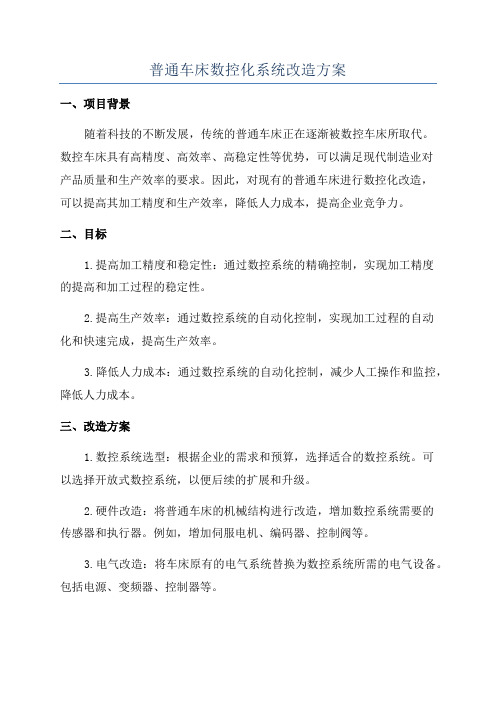
普通车床数控化系统改造方案一、项目背景随着科技的不断发展,传统的普通车床正在逐渐被数控车床所取代。
数控车床具有高精度、高效率、高稳定性等优势,可以满足现代制造业对产品质量和生产效率的要求。
因此,对现有的普通车床进行数控化改造,可以提高其加工精度和生产效率,降低人力成本,提高企业竞争力。
二、目标1.提高加工精度和稳定性:通过数控系统的精确控制,实现加工精度的提高和加工过程的稳定性。
2.提高生产效率:通过数控系统的自动化控制,实现加工过程的自动化和快速完成,提高生产效率。
3.降低人力成本:通过数控系统的自动化控制,减少人工操作和监控,降低人力成本。
三、改造方案1.数控系统选型:根据企业的需求和预算,选择适合的数控系统。
可以选择开放式数控系统,以便后续的扩展和升级。
2.硬件改造:将普通车床的机械结构进行改造,增加数控系统需要的传感器和执行器。
例如,增加伺服电机、编码器、控制阀等。
3.电气改造:将车床原有的电气系统替换为数控系统所需的电气设备。
包括电源、变频器、控制器等。
4.编程与调试:根据加工工艺要求,编写数控程序,并进行相关工艺参数的设置和调试。
确保数控系统能够准确地控制车床的运动。
5.操作与维护培训:对操作人员进行相关培训,使其熟悉数控系统的操作和维护方法。
确保数控系统的正常运行和维护。
四、预期效果1.加工精度提高:通过数控系统的精确控制,可以实现加工精度的提高,减少加工误差,提高产品质量。
2.生产效率提高:数控系统具有自动化控制功能,可以实现加工过程的自动化和快速完成,提高生产效率。
3.降低人力成本:数控系统的自动化控制减少了人工操作和监控,可以降低人力成本。
4.提高企业竞争力:数控化系统能够提高产品质量和生产效率,提高企业竞争力,获得更好的市场发展空间。
五、风险与挑战1.成本风险:数控化系统改造需要一定的投资,成本较高。
需要评估投资回报率和风险控制。
2.技术难题:数控化改造涉及机械、电气、编程等多个领域的知识,对技术人员的技能要求较高。
- 1、下载文档前请自行甄别文档内容的完整性,平台不提供额外的编辑、内容补充、找答案等附加服务。
- 2、"仅部分预览"的文档,不可在线预览部分如存在完整性等问题,可反馈申请退款(可完整预览的文档不适用该条件!)。
- 3、如文档侵犯您的权益,请联系客服反馈,我们会尽快为您处理(人工客服工作时间:9:00-18:30)。
普通机床数控化改造的刚度要求中国南车襄樊牵引电机有限公司罗隆满摘要:当前,我国有许多企业在考虑把旧设备改造成数控机床,但并不是所有的旧机床都能进行数控化改造。
本文主要从机床传动精度的问题,来阐述普通机床数控化改造对机床进给传动链的刚度要求,及其设计计算。
关键词:普通机床数控化改造传动链刚度设计计算Require of the Rigidty for Reformed the Common Machine Tool to Numerical Controlledabstract: Today, many enterprises are planning to reform the old common machine tool to numerical controlled in our country, but it is impossible that all of the old machine tool can be reformed.This paper is mainly illustrated the require of the drive system’s rigidty for reformed the common machine tool to numerical controlled in the respect about the precision of the machine tool’s feeding drive system, and the calculation of its design.Keywords:Common machine tool Numerical controlled reformed Drive system the Rigid Calculation of design1. 普通机床数控化改造的条件当前,我国的机械行业正处于技术改造和设备更新时期,有许多企业在考虑如何把旧设备改造成数控机床,但并不是所有的旧机床都能进行数控化改造,也不是把原有的旧机床配上数控系统,换上伺服电机就成为数控机床。
旧机床进行数控化改造须具备以下三个条件:(1)机床必须是分离传动;(2)机床原有的刚度要好,几何精度要基本符合数控机床的要求;(3)导轨具有改为低摩擦导轨的可能性。
2. 普通机床数控化改造的重点对旧机床进行数控化改造的重点是进给运动,具体就是机床导轨和传动链的改造。
导轨改造就是把原来普通滑动导轨改为低摩擦导轨,如滚动导轨、静压导轨、氟带导轨以及滚滑复合低摩擦导轨等;导轨以外的传动链部分改造,首先要选择传动链的形式,如丝杆、蜗轮蜗杆或齿轮齿条传动,依据原机床的结构、行程大小、加工能力等因素来全面衡量决定。
确定传动链的形式后,就要根据数控机床的动静特性的要求,具体计算传动链的结构参数。
3. 伺服进给传动链的刚度设计计算由于是旧机床改造,所以这里着重介绍传动链的最后环节(输出端)的计算方法,采用工程计算方法的刚度分配法进行设计计算。
3.1 刚度分配法的分配原理在传动系统中各个环节的刚度有高有低,对于按强度设计的传动系统,其总刚度会因系统的最薄弱环节而大大降低。
因此,我们须找出各环节受力变形所占的比例,并按这种变形比例关系来相应分配各环节的刚度值,从而使传动链的结构合理,即符合强度设计的要求,又满足刚度设计的要求,这就是刚度分配的主要原理。
据资料[1]介绍,过去按强度设计的传动系统,一般扭曲变形占60%~80%;齿轮接触变形和支承的弯曲变形引起齿隙产生的扭角占10~20%;键与键槽的接触变形占10%~25%,我们可以把这种变形的比例关系参考运用到刚度分配上。
3.2 传动各环节的刚度与总刚度的关系设传动链的传传动关系如图一所示,由n 对齿轮和n+1根轴组成,并假定机械间隙已消除,则每个齿轮的弹性转角具有如下关系:φ+φ=φ21222φ+φ=φ32333……φ+φ=φ++++)1n ()1n (n )1n )(1n (根据传动关系可得:1112φ=φi 2223φ=φ……i n n )1n (n φ=φ+φ1、φ2 ……φ(n+1)——第1、2 …… (n+1)根轴的弹性转角φ12、φ23 ……φn (n+1)——第1、2 …… n 根轴的弹性转角通过传动传递至第2、3 …… (n+1) 根轴的转角φ22、φ33 ……φ(n +1)(n+1)——第2、3 …… (n+1)根轴的总弹性转角i 1、i 2 ……i n ——每对齿轮的传动比故末端丝杆轴上的总变形量φ∑为:=φ∑+⋅⋅⋅φi i i n 211+⋅⋅⋅φi i i n 322……i n n φ+φ++)1n (K M iii =φφi 、M i 、K i ——各轴的转角、传动扭矩、扭曲刚度假定各轴的传动效率η=1,以简化推导:i i i M M n 21s 1⋅⋅⋅=;i i i MM n 32s2⋅⋅⋅= ……i M M nsn =M 1、M 2、…… M n ——第1、2 …… n 轴的传动扭矩M s ——丝杆轴输出扭矩K M s ∑∑=φ 代入后得: =∑K 1+⋅⋅⋅)i i i (K 12n 211)i i i (K 12n 322⋅⋅⋅+……+i K 12n n K 1ts + (式1) K Σ——传动链在末端总扭曲刚度 K 1、K 2 ……K n ——第1、2…… n 根轴的扭曲刚度 K ts ——丝杆的扭曲刚度从式1中可以看出,各轴的刚度折算到输出端时,其刚度减低i 2倍(i 为输出端到各轴的升速比)。
因此,我们只要使输出端的刚度满足要求即可。
其他轴因对输出轴的刚度影响较小,只要满足强度要求,并消除间隙即可。
3.3 输出端丝杆的刚度组成多数旧机床数控改造的主要对象是中、小型机床,行程一般不会太大,且大都为丝杆传动,下面就以输出端为丝杆传动的计算做一介绍。
丝杆传动的总刚度包括5个元件的刚度,即:(1) 丝杆的拉压刚度=⋅K a s βsm K 。
由于拉压变形是丝杆轴向变形的主要部分,故取拉压刚度分配系数βs =0.6~0.8。
a 为丝杆强度修正系数,由丝杆支承形式决定,支承刚度较好时取a=4,反之取a=1或2;K m 为所需的传动刚度。
(2) 螺母传动刚度K n 。
一般当丝杆的拉压刚度确定后,丝杆的几何参数如直径ds 、珠子直径d Z 以及珠子数Z 即可决定,螺母刚度K n 也可求出。
再按βn K K n m =求出螺母的刚度分配系数βn 。
(3) 螺母座轴向刚度=K cn βcnm K 。
因支座的刚度可以设计的高一些,故取刚度分配系数βcn ≤0.05。
(4) 轴承支座轴向刚度=⋅K b cb βcbm K 。
同理可把支座的刚度设计得比螺母座更高,故取刚度分配系数βcb ≤0.02;b 为轴承支座数量。
(5) 推力轴承轴向刚度=⋅K c b βbm K 。
因此类轴承的刚度较高,故取刚度分配系数βb ≤0.1;c 为推力轴承的数量。
(6)各类刚度的分配系数βi 之和须满足:β+β+β+β+β=β∑cb cn b n s i ≤1 (式2)3.4丝杆各环节刚度的计算公式(1) 丝杆的拉压刚度KsL ds E 4K s2s s ⋅⨯π=(N/mm ) (式3) d s ——丝杆底径 L s ——丝杆支承间长度 E s ——丝杆的弹性模量(2) 滚动螺母传动刚度K n10Z d P 54.0K 432z n ⨯⋅⋅⨯=∑ (N/mm ) (式4)P ——丝杆允许的最大轴向负荷 dz ——滚珠直径 Z ∑——承载区内有效滚珠总数(3) 推力滚子轴承的轴向刚度K b1.0a 9.008.0a 3b P Z L 1051.18K ⨯⨯⨯⨯= (N/mm) (式5)L a ——滚子长度 Z 0——滚子数 P a ——轴承允许的轴向载荷(4)螺母座或轴承座的轴向刚度Kcn 及Kcb4t cn cb 10k )C B (L K K ⨯-== (N/mm ) (式6)k t ——接触角柔度切线系数=10 B ——支承座宽度 L ——支座长度 C ——宽度方向中间的空刀宽3.5 计算步骤3.5.1 设定参数设定参数就是机床改造所要达到的一些性能要求,如主轴允许最大扭矩M z 、转速范围n 、最大刀具直径D dmax 、数控加工要达到的轮廓精度Δ、脉冲当量Δm 、点动灵敏度和死区∆0、进给速度范围V Tmax 和V Tmin 、允许加工的最小曲率半径R gmin 、最小刀具半径R min d 、运动部件重量W 、导轨摩擦系数f 以及采用什么控制系统(即开环、半闭环、闭环)等。
3.5.2 计算刀齿接触频率范围ωn转速上限取决于精切,转速下限取决于粗切,计算刀齿接触频率范围为:Z n 2c c z ⋅⋅π=ω~Z n 2j j ⋅⋅π (rad/sec )Z c ——粗切刀具刀齿数 Z j ——精切刀具刀齿数 n c ——粗切主轴转速 n j ——精切主轴转速可取传动链的谐振频率ωn ≤0.7ωz 或ωn ≥1.4ωz若要改造的机床即能切削钢,又能切削有色金属,则:1.4ωz 钢≤ωn ≤0.7ωz 有色3.5.3 坐标最大进给力QsQs = 丝杆允许的最大轴向负荷P3.5.4 要求位置环开环的最低放大倍数k vk v ≥22T g 2V R ρ'∆ (1/sec) V T ——进给速度 ρ——刀具或工件的中心移动曲率半径 R g ——工件半径 ∆'——设定的轮廓加工误差 ,取∆'=(1/3~1/5)Δ(Δ为加工要达到的轮廓精度)3.5.5 运动部件的加速度a 与加速度力Fa=V Q k v (m/sec 2)a gW F = (N ) V Q ——启动速度 W ——运动部件的重量 g ——重力系数=9.81N/g3.5.6 要求的低速性能与速度控制范围(1)最小位移角Δφ)R 1(cos gmin min 1∆+ρρ=∆-φ ρmin ——刀具或工件的中心最小移动曲率半径(2) 最小启动速度V Qmin∆⨯=φsin V V m in T m in Q (mm/min)V Tmin ——最小进给速度(3)坐标的速度控制范围R sV V R minQ max T s = V Tmax ——最大进给速度3.5.7 要求传动链的谐振值ωn(1)由齿频要求ωn1≥ωz(2)由ωc =k v 要求ωn2≥12ωc =12k v(3)比较ωn1、ωn2取大的作为ωn ,但如果按ωn1≤0.7ωz 取,则要校核ω2n 是否与之有矛盾。
若有矛盾,则改取ωn2≥1.4ωz 再比较确定ωn1。
3.5.8 所需的传动刚度K m(1)由死区Δ0要求的刚度K m1∆⋅⋅=∆=00f1m g f W 2P 2K (N/mm) 取Δ0=(1/2~1/3)Δd Δd ——定位误差P f 、f ——导轨的摩擦力、摩擦系数 W ——运动部件重量在计算垂向时,如果运动部件的重量在平衡后还比最大的切削力大得多,则死区无意义,不必计算此要求。