动力电池自动化测试系统总体方案(修改)
动力电池自动化测试系统总体方案(修改)
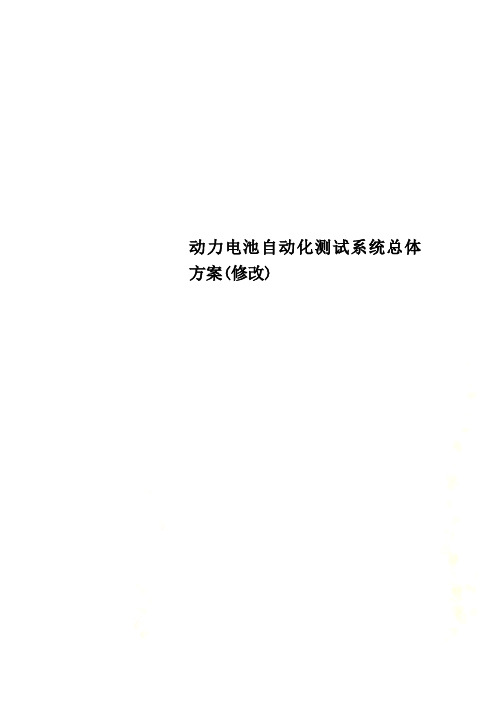
动力电池自动化测试系统总体方案(修改)动力电池自动化测试系统总体方案湖北德普电气股份有限公司(0710-*******、3276513)第一部分:模组来料OCV 检测系统方案一、简述本系统首先导入模组出厂数据到本地数据库,测试时通过条码扫描枪读取电池包的条码信息,按照预设好的测试方案,通过CAN 总线读取BMS 的电池OCV 信息,并将电池OCV 信息与出厂数据进行比对,按照预设的条件进行产品合格判定。
并把相关信息记录在数据库中,同时将不合格结果进行标签打印。
二、组成模组来料OCV 检测系统主要由以下设备组成,系统原理框图如图1所示。
1)研华工控机2)Honeywell 条码扫描枪 3)NI PCI CAN 通讯卡 4)明纬开关电源 5)NI PCI I/O 板卡 6)Zebra 标签打印机 7)扫描枪伺服系统 8)附属组件工控机PCI I/O 板卡PCICAN 通道卡MES以太网口标签打印机辅助接触器电池包…………12VDC+-扫描枪MSDUSB 通讯口开关电源BMSCAN 总线扫描枪伺服系统图1 模组来料OCV检测系统原理框图三、功能实现技术方案图2 来料OCV检测系统示意模组来料OCV检测系统由工控机通过软件进行设备集成。
用户登录后,根据权限编写测试流程,测试流程包含扫描枪伺服系统的控制、DBC文件的选择、不合格条件的设定等,并将测试流程与条码进行模糊绑定。
在进行具体测试过程中,当完成线束连接后,可以点击启动按钮,模组来料OCV 检测系统自动按照测试方案驱动扫描枪伺服系统,扫描枪到预设位置后读取相应的条形码填入对应位置。
条形码读取完毕后自动从数据库中搜索电池的相应出厂OCV值,并根据DBC文件,自动通过PCI CAN通讯卡读取并解析相应的电池OCV信息,按照预设的判定条件进行结果判定。
完成测试后,将不合格的测试结果按照预设格式进行打印。
同时出于满足手动调试的需要,所有的操作均可以单步手动操作。
动力电池自动化测试系统总体方案修改

动力电池自动化测试系统总体方案修改一、引言随着电动汽车的普及,动力电池作为其核心组成部分之一,具有重要的功能和安全性要求。
因此,对动力电池进行准确、快速、稳定的自动化测试,是保证电池质量和性能的重要环节。
本文对现有的动力电池自动化测试系统进行修改和完善,提出了一套全新的总体方案。
二、系统概述本次修改的动力电池自动化测试系统主要包括硬件设备、测试流程和软件系统三个方面。
硬件设备包括测试平台、测试电路和相关传感器等;测试流程包括测试过程和测试指标等;软件系统包括测试控制、数据处理和报告生成等。
通过对这三个方面进行修改和优化,提高测试系统的准确性、效率和稳定性。
三、硬件设备方案修改1.测试平台方面:本次修改将原有的测试平台进行优化改造,增加电池固定装置、升降装置和可调整平台等功能,以适应不同尺寸、不同类型的电池测试需求。
2.测试电路方面:在测试电路方面,本次修改将引入更先进和精确的测试仪器和传感器,以提高测试的准确性和可靠性。
同时,加强对测试电路的防护和安全性设计,避免因测试过程中出现的电路问题对电池和操作人员造成伤害。
3.传感器方面:本次修改将增加一些新型传感器,如温度传感器、湿度传感器和振动传感器等,以获取更全面、准确的测试数据。
同时,优化传感器的布置方式,保证测试数据的高可靠性和再现性。
四、测试流程方案修改1.测试过程方面:本次修改将对现有的测试过程进行优化,增加多项测试指标,如内阻测试、电能密度测试、循环寿命测试等,以更全面地评估电池的性能和健康度。
2.测试指标方面:通过对测试指标的优化和调整,建立更合理、准确的测试标准,以确保测试结果的可靠性和一致性。
同时,加强对测试指标的数据库管理,方便后续数据分析和比对。
五、软件系统方案修改1.测试控制方面:本次修改将优化测试控制软件,增加自动化测试的稳定性和可靠性。
通过引入更高级的控制算法和自适应控制策略,提高测试系统对电池参数变化的适应能力,并能够自动调整测试参数,以获得更准确和稳定的测试结果。
汽车电池自动化检测系统设计
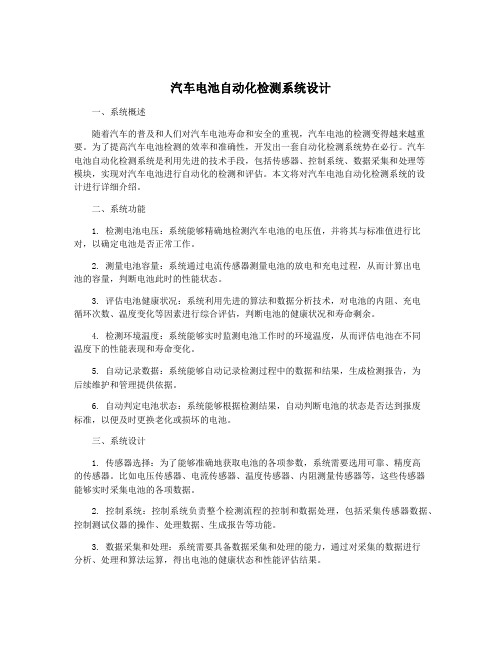
汽车电池自动化检测系统设计一、系统概述随着汽车的普及和人们对汽车电池寿命和安全的重视,汽车电池的检测变得越来越重要。
为了提高汽车电池检测的效率和准确性,开发出一套自动化检测系统势在必行。
汽车电池自动化检测系统是利用先进的技术手段,包括传感器、控制系统、数据采集和处理等模块,实现对汽车电池进行自动化的检测和评估。
本文将对汽车电池自动化检测系统的设计进行详细介绍。
二、系统功能1. 检测电池电压:系统能够精确地检测汽车电池的电压值,并将其与标准值进行比对,以确定电池是否正常工作。
2. 测量电池容量:系统通过电流传感器测量电池的放电和充电过程,从而计算出电池的容量,判断电池此时的性能状态。
3. 评估电池健康状况:系统利用先进的算法和数据分析技术,对电池的内阻、充电循环次数、温度变化等因素进行综合评估,判断电池的健康状况和寿命剩余。
4. 检测环境温度:系统能够实时监测电池工作时的环境温度,从而评估电池在不同温度下的性能表现和寿命变化。
5. 自动记录数据:系统能够自动记录检测过程中的数据和结果,生成检测报告,为后续维护和管理提供依据。
6. 自动判定电池状态:系统能够根据检测结果,自动判断电池的状态是否达到报废标准,以便及时更换老化或损坏的电池。
三、系统设计1. 传感器选择:为了能够准确地获取电池的各项参数,系统需要选用可靠、精度高的传感器。
比如电压传感器、电流传感器、温度传感器、内阻测量传感器等,这些传感器能够实时采集电池的各项数据。
2. 控制系统:控制系统负责整个检测流程的控制和数据处理,包括采集传感器数据、控制测试仪器的操作、处理数据、生成报告等功能。
3. 数据采集和处理:系统需要具备数据采集和处理的能力,通过对采集的数据进行分析、处理和算法运算,得出电池的健康状态和性能评估结果。
4. 人机交互界面:系统需要设置友好的人机交互界面,操作简便,能够实时显示检测过程和结果,便于操作人员进行观测和管理。
5. 敏捷性和稳定性:系统需要在保证检测精度和可靠性的前提下,提高系统的敏捷性和稳定性,以应对大量的汽车电池检测需求。
汽车电池自动化检测系统设计

汽车电池自动化检测系统设计随着汽车行业的快速发展,汽车电池作为关键的动力源之一,对其质量和性能的要求也越来越高。
为了确保汽车电池的质量和稳定性,开发一个高效而准确的汽车电池自动化检测系统是非常重要的。
汽车电池自动化检测系统主要包括以下几个方面的设计:数据采集、数据处理和结果判定。
在数据采集阶段,系统需要采集电压、电流以及温度等数据,这些数据可以反映出电池的实时状态。
为了实现数据采集功能,可以通过安装传感器在电池上获取电压、电流和温度等数据,并将这些数据传输到检测系统中。
检测系统还可以通过无线传输技术将数据传输到云端进行进一步的分析和处理。
在数据处理阶段,系统需要对采集到的数据进行分析和处理,以提取有用的信息和特征。
系统可以对电压、电流和温度等数据进行分析,判断电池的工作状态是否正常。
系统可以通过算法计算电池的容量和寿命等重要参数,以评估电池的性能和质量。
系统还可以通过与历史数据进行对比,判断电池的健康状况并预测其寿命。
在结果判定阶段,系统需要根据处理后的数据结果进行判定和分类。
如果电池的性能和质量符合要求,则判定为合格;如果不符合要求,则判定为不合格,并给出相应的处理建议。
系统可以通过设置阈值来判断电池的合格与否,这些阈值可以根据具体的要求和标准进行调整。
为了提高系统的自动化程度和检测效率,可以将系统与机器人技术相结合。
通过机器人的自动操作,可以实现电池的快速换装和测试,从而提高检测的效率和准确性。
还可以采用人工智能和机器学习技术对大量的数据进行分析和学习,从而优化系统的判定结果,提高系统的智能化程度。
在系统设计方面,需要考虑到以下几个关键因素:硬件设备的选择和布置、数据的传输和存储、算法的设计和优化、界面的设计和用户交互等。
还需要考虑到系统的稳定性、可靠性和安全性,确保系统可以长期稳定运行并保护用户的隐私和数据安全。
汽车电池自动化检测系统的设计是一个综合性的工程,需要考虑到多个因素,并且与其他技术相结合,才能实现对汽车电池质量和性能的准确检测。
汽车电池自动化检测系统设计
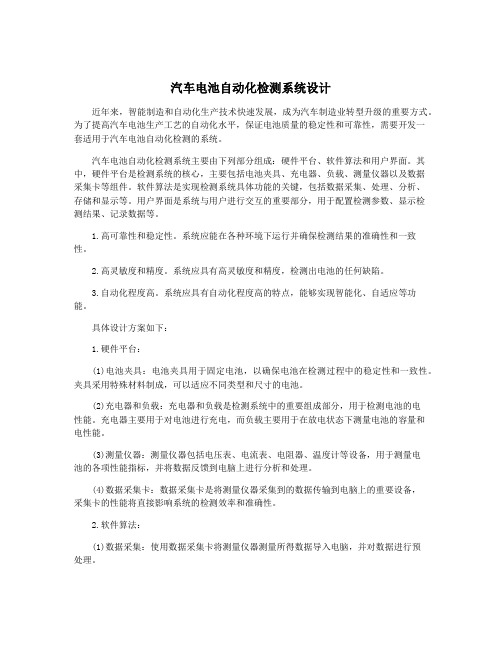
汽车电池自动化检测系统设计近年来,智能制造和自动化生产技术快速发展,成为汽车制造业转型升级的重要方式。
为了提高汽车电池生产工艺的自动化水平,保证电池质量的稳定性和可靠性,需要开发一套适用于汽车电池自动化检测的系统。
汽车电池自动化检测系统主要由下列部分组成:硬件平台、软件算法和用户界面。
其中,硬件平台是检测系统的核心,主要包括电池夹具、充电器、负载、测量仪器以及数据采集卡等组件。
软件算法是实现检测系统具体功能的关键,包括数据采集、处理、分析、存储和显示等。
用户界面是系统与用户进行交互的重要部分,用于配置检测参数、显示检测结果、记录数据等。
1.高可靠性和稳定性。
系统应能在各种环境下运行并确保检测结果的准确性和一致性。
2.高灵敏度和精度。
系统应具有高灵敏度和精度,检测出电池的任何缺陷。
3.自动化程度高。
系统应具有自动化程度高的特点,能够实现智能化、自适应等功能。
具体设计方案如下:1.硬件平台:(1)电池夹具:电池夹具用于固定电池,以确保电池在检测过程中的稳定性和一致性。
夹具采用特殊材料制成,可以适应不同类型和尺寸的电池。
(2)充电器和负载:充电器和负载是检测系统中的重要组成部分,用于检测电池的电性能。
充电器主要用于对电池进行充电,而负载主要用于在放电状态下测量电池的容量和电性能。
(3)测量仪器:测量仪器包括电压表、电流表、电阻器、温度计等设备,用于测量电池的各项性能指标,并将数据反馈到电脑上进行分析和处理。
(4)数据采集卡:数据采集卡是将测量仪器采集到的数据传输到电脑上的重要设备,采集卡的性能将直接影响系统的检测效率和准确性。
2.软件算法:(1)数据采集:使用数据采集卡将测量仪器测量所得数据导入电脑,并对数据进行预处理。
(2)特征提取:将所得数据进行特征提取,将电池的各项指标进行分析、提取和计算,获得电池的关键性能指标。
(3)数据分析:将所得数据进行数据分析和处理,判断电池的健康状况,对电池进行合格判定,提高检测的准确性和效率。
汽车电池自动化检测系统设计
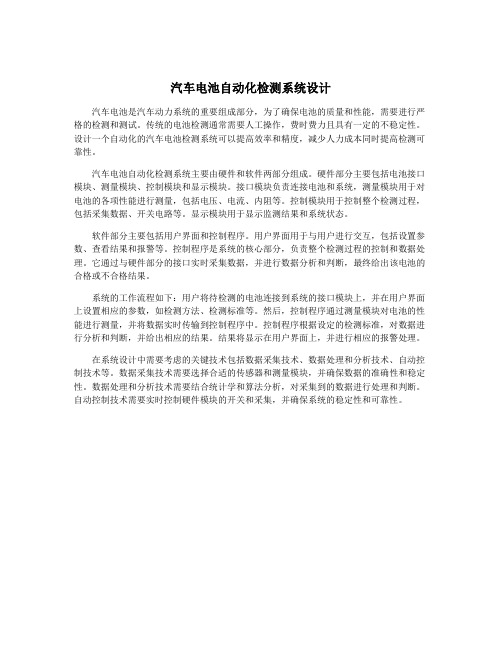
汽车电池自动化检测系统设计汽车电池是汽车动力系统的重要组成部分,为了确保电池的质量和性能,需要进行严格的检测和测试。
传统的电池检测通常需要人工操作,费时费力且具有一定的不稳定性。
设计一个自动化的汽车电池检测系统可以提高效率和精度,减少人力成本同时提高检测可靠性。
汽车电池自动化检测系统主要由硬件和软件两部分组成。
硬件部分主要包括电池接口模块、测量模块、控制模块和显示模块。
接口模块负责连接电池和系统,测量模块用于对电池的各项性能进行测量,包括电压、电流、内阻等。
控制模块用于控制整个检测过程,包括采集数据、开关电路等。
显示模块用于显示监测结果和系统状态。
软件部分主要包括用户界面和控制程序。
用户界面用于与用户进行交互,包括设置参数、查看结果和报警等。
控制程序是系统的核心部分,负责整个检测过程的控制和数据处理。
它通过与硬件部分的接口实时采集数据,并进行数据分析和判断,最终给出该电池的合格或不合格结果。
系统的工作流程如下:用户将待检测的电池连接到系统的接口模块上,并在用户界面上设置相应的参数,如检测方法、检测标准等。
然后,控制程序通过测量模块对电池的性能进行测量,并将数据实时传输到控制程序中。
控制程序根据设定的检测标准,对数据进行分析和判断,并给出相应的结果。
结果将显示在用户界面上,并进行相应的报警处理。
在系统设计中需要考虑的关键技术包括数据采集技术、数据处理和分析技术、自动控制技术等。
数据采集技术需要选择合适的传感器和测量模块,并确保数据的准确性和稳定性。
数据处理和分析技术需要结合统计学和算法分析,对采集到的数据进行处理和判断。
自动控制技术需要实时控制硬件模块的开关和采集,并确保系统的稳定性和可靠性。
汽车电池自动化检测系统设计
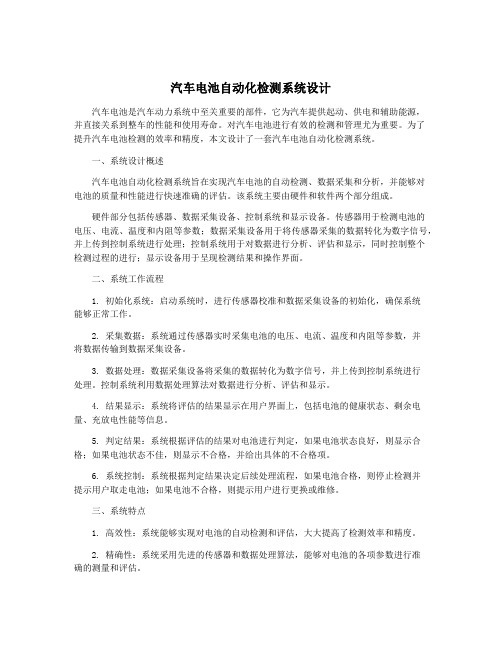
汽车电池自动化检测系统设计汽车电池是汽车动力系统中至关重要的部件,它为汽车提供起动、供电和辅助能源,并直接关系到整车的性能和使用寿命。
对汽车电池进行有效的检测和管理尤为重要。
为了提升汽车电池检测的效率和精度,本文设计了一套汽车电池自动化检测系统。
一、系统设计概述汽车电池自动化检测系统旨在实现汽车电池的自动检测、数据采集和分析,并能够对电池的质量和性能进行快速准确的评估。
该系统主要由硬件和软件两个部分组成。
硬件部分包括传感器、数据采集设备、控制系统和显示设备。
传感器用于检测电池的电压、电流、温度和内阻等参数;数据采集设备用于将传感器采集的数据转化为数字信号,并上传到控制系统进行处理;控制系统用于对数据进行分析、评估和显示,同时控制整个检测过程的进行;显示设备用于呈现检测结果和操作界面。
二、系统工作流程1. 初始化系统:启动系统时,进行传感器校准和数据采集设备的初始化,确保系统能够正常工作。
2. 采集数据:系统通过传感器实时采集电池的电压、电流、温度和内阻等参数,并将数据传输到数据采集设备。
3. 数据处理:数据采集设备将采集的数据转化为数字信号,并上传到控制系统进行处理。
控制系统利用数据处理算法对数据进行分析、评估和显示。
4. 结果显示:系统将评估的结果显示在用户界面上,包括电池的健康状态、剩余电量、充放电性能等信息。
5. 判定结果:系统根据评估的结果对电池进行判定,如果电池状态良好,则显示合格;如果电池状态不佳,则显示不合格,并给出具体的不合格项。
6. 系统控制:系统根据判定结果决定后续处理流程,如果电池合格,则停止检测并提示用户取走电池;如果电池不合格,则提示用户进行更换或维修。
三、系统特点1. 高效性:系统能够实现对电池的自动检测和评估,大大提高了检测效率和精度。
2. 精确性:系统采用先进的传感器和数据处理算法,能够对电池的各项参数进行准确的测量和评估。
3. 用户友好性:系统设计了直观简洁的用户界面,方便用户查看检测结果和操作系统。
BMS自动测试解决方案
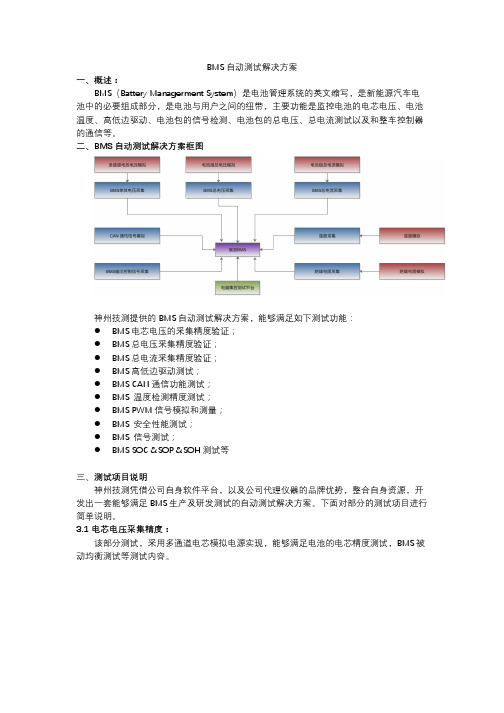
BMS自动测试解决方案一、概述:BMS(Battery Managerment System)是电池管理系统的英文缩写,是新能源汽车电池中的必要组成部分,是电池与用户之间的纽带,主要功能是监控电池的电芯电压、电池温度、高低边驱动、电池包的信号检测、电池包的总电压、总电流测试以及和整车控制器的通信等。
二、BMS自动测试解决方案框图神州技测提供的BMS自动测试解决方案,能够满足如下测试功能:●BMS电芯电压的采集精度验证;●BMS总电压采集精度验证;●BMS总电流采集精度验证;●BMS高低边驱动测试;●BMS CAN通信功能测试;●BMS 温度检测精度测试;●BMS PWM信号模拟和测量;●BMS 安全性能测试;●BMS 信号测试;●BMS SOC &SOP &SOH测试等三、测试项目说明神州技测凭借公司自身软件平台,以及公司代理仪器的品牌优势,整合自身资源,开发出一套能够满足BMS生产及研发测试的自动测试解决方案。
下面对部分的测试项目进行简单说明。
3.1电芯电压采集精度:该部分测试,采用多通道电芯模拟电源实现,能够满足电池的电芯精度测试,BMS被动均衡测试等测试内容。
电芯采样精度及被动均衡和线路漏电流检测原理电芯采样精度检测,闭合K1,K3继电器,被动均衡电流或者线路漏电流测试闭合K2,K4。
电流通过电阻采样,经过数字万用表(DMM)或者数据采集卡(DAQ)进行采样测量。
3.2BMS总电压采集精度测试BMS总电压采集,主要是为了检测BMS的电压采集精度,测量原理如下:神州技测具有多条电源产品线,能够满足客户的不同需求,具体规格指标需要根据客户的技术要求进行选定。
3.3BMS总电流采集精度测试通过K1,K2,K3,K4的4个继电器的控制,可以实现BMS正负电流的检测功能。
K1、K3闭合时,BMS检测电流为正,K2,K4闭合时,BMS检测电流为负。
其中霍尔传感器为神州技测自主研发设计的,万分之5精度的高精度计量级别电流传感器,能够提高测量的精度,保证测量的可靠性。
动力电池自动化测试系统总体方案(修改)剖析

“动力电池自动化测试系统总体方案(修改)剖析”一想到动力电池自动化测试系统,我脑海中瞬间涌现出十年来的经验积累。
这个方案,已经修改过无数次,但每一次都要力求完美,力求让系统运行得更加稳定、高效。
先从系统架构说起。
这个自动化测试系统,是由多个模块组成的复杂体系。
核心模块自然是测试控制模块,它就像大脑,指挥着整个系统的运作。
然后是数据采集模块,它负责收集电池的各项性能数据,包括电压、电流、温度等。
再然后是执行模块,它根据控制模块的指令,对电池进行充放电、加热、冷却等操作。
1.测试控制模块这个模块,是我心中的宝贝。
它采用了最新的算法,能够根据测试需求,自动测试流程。
这样一来,测试工程师只需要输入测试参数,系统就能自动完成整个测试过程。
而且,这个模块还能根据测试结果,自动调整测试流程,以达到最佳的测试效果。
2.数据采集模块这个模块,就像一只敏锐的眼睛,实时监控着电池的各项性能指标。
它采用了高精度的传感器,能够精确地测量电池的电压、电流、温度等数据。
同时,这个模块还具备强大的数据处理能力,能对采集到的数据进行实时分析,为测试控制模块提供决策依据。
3.执行模块这个模块,是整个系统的“手”和“脚”。
它负责执行测试控制模块的指令,对电池进行各种操作。
这个模块的设计,要求既要有足够的力度,又要有足够的精度。
因此,我们采用了高精度的电机和控制系统,确保每一个操作都能精确到位。
1.电池测试平台这个平台,是整个系统的核心硬件。
它采用了模块化设计,可以根据测试需求,灵活配置不同类型的电池。
同时,平台还具备自动校准功能,确保测试数据的准确性。
2.传感器传感器是系统的重要组成部分,它们负责采集电池的各项性能数据。
我们选择了高精度的传感器,确保数据的准确性。
同时,传感器还具有抗干扰能力强、响应速度快等特点,保证了数据的实时性。
3.控制系统控制系统是整个系统的神经中枢,它负责指挥各个模块协同工作。
我们采用了最新的PLC技术,确保控制系统的稳定性和可靠性。
汽车电池自动化检测系统设计
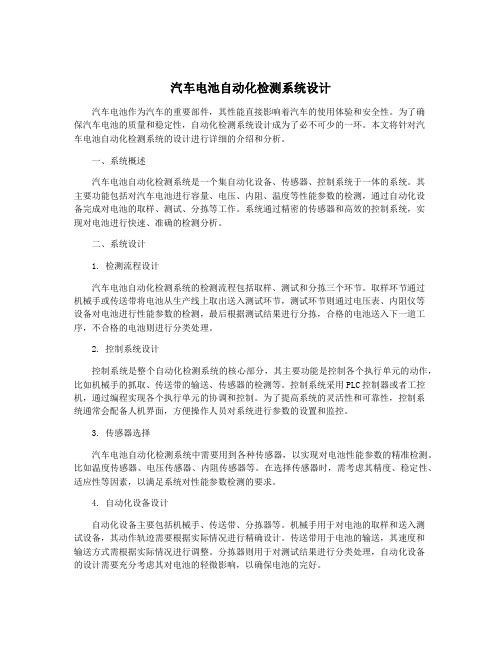
汽车电池自动化检测系统设计汽车电池作为汽车的重要部件,其性能直接影响着汽车的使用体验和安全性。
为了确保汽车电池的质量和稳定性,自动化检测系统设计成为了必不可少的一环。
本文将针对汽车电池自动化检测系统的设计进行详细的介绍和分析。
一、系统概述汽车电池自动化检测系统是一个集自动化设备、传感器、控制系统于一体的系统。
其主要功能包括对汽车电池进行容量、电压、内阻、温度等性能参数的检测,通过自动化设备完成对电池的取样、测试、分拣等工作。
系统通过精密的传感器和高效的控制系统,实现对电池进行快速、准确的检测分析。
二、系统设计1. 检测流程设计汽车电池自动化检测系统的检测流程包括取样、测试和分拣三个环节。
取样环节通过机械手或传送带将电池从生产线上取出送入测试环节,测试环节则通过电压表、内阻仪等设备对电池进行性能参数的检测,最后根据测试结果进行分拣,合格的电池送入下一道工序,不合格的电池则进行分类处理。
2. 控制系统设计控制系统是整个自动化检测系统的核心部分,其主要功能是控制各个执行单元的动作,比如机械手的抓取、传送带的输送、传感器的检测等。
控制系统采用PLC控制器或者工控机,通过编程实现各个执行单元的协调和控制。
为了提高系统的灵活性和可靠性,控制系统通常会配备人机界面,方便操作人员对系统进行参数的设置和监控。
3. 传感器选择汽车电池自动化检测系统中需要用到各种传感器,以实现对电池性能参数的精准检测。
比如温度传感器、电压传感器、内阻传感器等。
在选择传感器时,需考虑其精度、稳定性、适应性等因素,以满足系统对性能参数检测的要求。
4. 自动化设备设计自动化设备主要包括机械手、传送带、分拣器等。
机械手用于对电池的取样和送入测试设备,其动作轨迹需要根据实际情况进行精确设计。
传送带用于电池的输送,其速度和输送方式需根据实际情况进行调整。
分拣器则用于对测试结果进行分类处理,自动化设备的设计需要充分考虑其对电池的轻微影响,以确保电池的完好。
汽车电池自动化检测系统设计

汽车电池自动化检测系统设计汽车电池自动化检测系统是一种用于检测汽车电池性能的系统,主要用于提高汽车电池生产效率和质量。
本文将介绍汽车电池自动化检测系统的设计。
汽车电池是汽车的重要组成部分,其性能直接影响汽车的续航里程和使用寿命。
对汽车电池的性能进行检测是非常重要的。
汽车电池自动化检测系统主要包括以下几个方面的设计:电池参数测试、电池容量测试、充放电测试和电池内阻测试。
首先是电池参数测试。
该测试主要是对电池的一些基本参数进行测量,比如电压、电流、温度等。
通过这些参数的测量,可以判断电池的工作状态和性能是否正常。
其次是电池容量测试。
电池容量是指电池储存和释放电能的能力,是评估电池性能的重要指标。
电池容量测试可以通过充放电测试来进行。
在充放电测试中,将电池充满电然后放电,测量电池在放电过程中的时长和电压变化,从而确定电池的容量。
在设计汽车电池自动化检测系统时,需要考虑以下几点:测试精度、自动化程度、数据处理和记录。
测试精度是衡量检测系统性能的重要指标。
为了提高测试精度,可以采用高精度的测量仪器,比如高精度的示波器和电压表。
还可以采用精确的测量算法和校正方法来消除测量误差。
自动化程度是指检测系统的自动化程度。
为了实现自动化测试,需要采用自动化控制器和执行机构,比如自动化电流源和负载。
还需要开发相应的软件来控制测试流程、数据采集和结果分析。
数据处理和记录是指对测试数据的处理和记录。
为了方便数据处理和记录,可以采用计算机和数据库来存储和管理测试数据。
还可以开发相应的数据分析和报告生成软件来进行数据分析和报告生成。
汽车电池自动化检测系统的设计主要包括电池参数测试、电池容量测试、充放电测试和电池内阻测试。
在设计过程中,需要考虑测试精度、自动化程度、数据处理和记录等方面的要求。
通过合理的设计和实施,可以提高汽车电池生产效率和质量。
动力电池远程TBOX检测应用电池快换系统解决方案

05
实施方案和计划
实施步骤和时间表
步骤一
需求分析(1周):对现有动力电池远程 TBox检测应用和电池快换系统进行详细 的需求分析,明确改进目标。
步骤五
后期维护与升级(长期):对系统进行持 续的维护和升级,确保系统的长期稳定运 行。
步骤二
方案设计(2周):根据需求分析结果, 设计出具体的实施方案和计划,包括硬件 和软件的设计、系统集成方案等。
TBox检测系统能够实时监测动力电 池的工作状态,包括电压、电流、温 度等参数。
数据记录与分析
系统能够记录和分析电池的工作数据, 为电池维护和故障诊断提供依据。
预警与报警
当电池工作状态异常时,系统能够及 时发出预警或报警信号,提醒用户采 取相应措施。
远程控制与诊断
通过与上位机的通信,TBox检测系 统可以实现远程控制和诊断功能,方 便对电池进行管理和维护。
TBox检测系统的优势和局限性
优势
实时监测、远程控制、数据记录 与分析、预警与报警等功能强大 ,能够提高动力电池的安全性和 可靠性,延长电池寿命。
局限性
TBox检测系统的成本较高,对于 一些小型车辆或特定应用场景可 能不太适用;同时,系统的稳定 性和可靠性也需要进一步提高。
03
动力电池快换系统解决方案
THANKS
感谢观看
全可靠。
快换系统的应用场景
物流车队
出租车队
对于需要频繁更换电池的物流车队,快换 系统能够大大提高工作效率。
对于出租车队而言,快换系统能够快速更 换电池,减少车辆停驶时间。
公共交通
共享汽车
在公共交通领域,快车而言,快换系统能够实现快 速电池更换,提高车辆使用效率。
集,提高监控的准确性和及时性。
汽车电池自动化检测系统设计

汽车电池自动化检测系统设计随着电动汽车的普及和发展,汽车电池的质量和性能要求越来越高,使得对汽车电池的测试和检测变得更加重要。
为了提高汽车电池的质量和性能,降低车主的使用成本和安全隐患,需要设计一个汽车电池的自动化检测系统。
汽车电池自动化检测系统主要包括以下几个方面的设计:电池选配、电池容量测试、电池内阻测试、电池充放电测试和电池循环寿命测试等。
首先是电池选配。
由于电池的品质和性能有差异,需要从大量的电池中选取出符合要求的电池。
电池选配的关键在于对电池的容量、内阻、内存效应、自放电等性能的测试和评估。
通过对电池的测试和分析,选择出质量优良、性能稳定的电池。
其次是电池容量测试。
电池容量是衡量电池性能的重要指标之一。
电池容量测试根据用户需求和标准要求,采用不同的测试方法和设备。
常用的测试方法有恒流放电法和恒功率充放电法。
通过电池容量测试,可以准确评估电池的储能能力和使用寿命。
第三是电池内阻测试。
电池内阻是影响电池性能和工作稳定性的关键参数之一。
电池内阻测试可以通过交流法、直流法和脉冲法等不同的测试方法来进行。
通过电池内阻测试,可以准确测量电池的内阻,并评估电池的老化和损耗情况。
第四是电池充放电测试。
电池充放电测试可以评估电池的充电和放电性能,包括充电速率、充电效率、放电能力等。
通过电池充放电测试,可以评估电池的充放电性能,并检测电池的容量损失和劣化情况。
最后是电池循环寿命测试。
电池循环寿命测试可以模拟电池在实际使用中的循环充放电过程,评估电池的寿命和性能稳定性。
通过电池循环寿命测试,可以预测电池的使用寿命,提前发现电池的老化和劣化情况。
汽车电池自动化检测系统的设计需要考虑到测试精度、测试信号准确性、测试速度和测试稳定性等因素。
还需要考虑到系统的易用性、可靠性和安全性等要求。
为了实现这些要求,可以采用先进的测试设备和自动化控制系统,提高测试效率和测试精度。
BMS自动测试解决方案

BMS自动测试解决方案随着信息技术的快速发展和软件应用的广泛使用,软件测试的重要性日益凸显。
传统的软件测试通常采用人工测试的方法,但由于人工测试的效率低、成本高,以及测试精度的不稳定等问题,引入自动化测试技术已成为软件测试的重要发展方向之一、BMS(Battery Management System,电池管理系统)作为一种重要的电池控制设备,需要进行大量而复杂的测试工作,因此,BMS的自动测试也是非常关键的。
本文将介绍BMS自动测试的解决方案。
一、背景介绍BMS是一种用于控制、监测和保护电池的设备,其功能非常复杂,包括电池状态检测、电池充放电管理、故障诊断和保护等。
由于BMS所承载的重要性,其软件需要进行全面的测试以保证其功能的可靠性和稳定性。
二、自动测试的优势与传统的人工测试相比,BMS自动测试具有以下几个优势:1.提高测试效率:自动测试可以通过编写、运行和分析测试脚本来替代人工测试过程,大大提高了测试效率。
2.提高测试精度:自动测试可以精确控制测试环境和执行动作,减少了测试过程中的人为误差。
3.减少测试成本:自动测试可以在测试的早期发现问题,减少了测试周期和成本。
4.可重复性强:自动测试可以重复运行测试脚本,确保每次测试结果一致,方便进行回归测试和性能测试。
5.可扩展性强:自动测试可以根据需要扩展测试范围,增加新的测试用例和测试脚本,提高测试覆盖率。
BMS的自动测试解决方案主要包括测试目标确定、测试环境搭建、测试工具选择和测试脚本编写等步骤。
1.测试目标确定在进行自动化测试之前,首先需要明确测试的目标和需求,包括测试的覆盖范围、测试的重点和测试的标准等,以便能够有针对性地进行后续的测试计划和测试脚本的编写。
2.测试环境搭建BMS的自动测试需要搭建相应的测试环境,包括硬件环境和软件环境。
硬件环境包括BMS设备、模拟器、示波器等,软件环境包括测试工具和测试框架等。
3.测试工具选择选择合适的测试工具是进行BMS自动测试的关键。
电动汽车动力电池检测系统设计
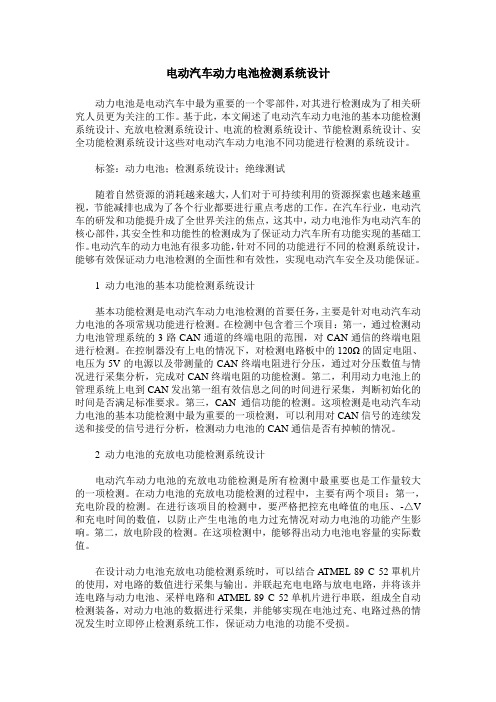
电动汽车动力电池检测系统设计动力电池是电动汽车中最为重要的一个零部件,对其进行检测成为了相关研究人员更为关注的工作。
基于此,本文阐述了电动汽车动力电池的基本功能检测系统设计、充放电检测系统设计、电流的检测系统设计、节能检测系统设计、安全功能检测系统设计这些对电动汽车动力电池不同功能进行检测的系统设计。
标签:动力电池;检测系统设计;绝缘测试随着自然资源的消耗越来越大,人们对于可持续利用的资源探索也越来越重视,节能减排也成为了各个行业都要进行重点考虑的工作。
在汽车行业,电动汽车的研发和功能提升成了全世界关注的焦点,这其中,动力电池作为电动汽车的核心部件,其安全性和功能性的检测成为了保证动力汽车所有功能实现的基础工作。
电动汽车的动力电池有很多功能,针对不同的功能进行不同的检测系统设计,能够有效保证动力电池检测的全面性和有效性,实现电动汽车安全及功能保证。
1 动力电池的基本功能检测系统设计基本功能检测是电动汽车动力电池检测的首要任务,主要是针对电动汽车动力电池的各项常规功能进行检测。
在检测中包含着三个项目:第一,通过检测动力电池管理系统的3路CAN通道的终端电阻的范围,对CAN通信的终端电阻进行检测。
在控制器没有上电的情况下,对检测电路板中的120Ω的固定电阻、电压为5V的电源以及带测量的CAN终端电阻进行分压,通过对分压数值与情况进行采集分析,完成对CAN终端电阻的功能检测。
第二,利用动力电池上的管理系统上电到CAN发出第一组有效信息之间的时间进行采集,判断初始化的时间是否满足标准要求。
第三,CAN通信功能的检测。
这项检测是电动汽车动力电池的基本功能检测中最为重要的一项检测,可以利用对CAN信号的连续发送和接受的信号进行分析,检测动力电池的CAN通信是否有掉帧的情况。
2 动力电池的充放电功能检测系统设计电动汽车动力电池的充放电功能检测是所有检测中最重要也是工作量较大的一项检测。
在动力电池的充放电功能检测的过程中,主要有两个项目:第一,充电阶段的检测。
动力电池系统方案书
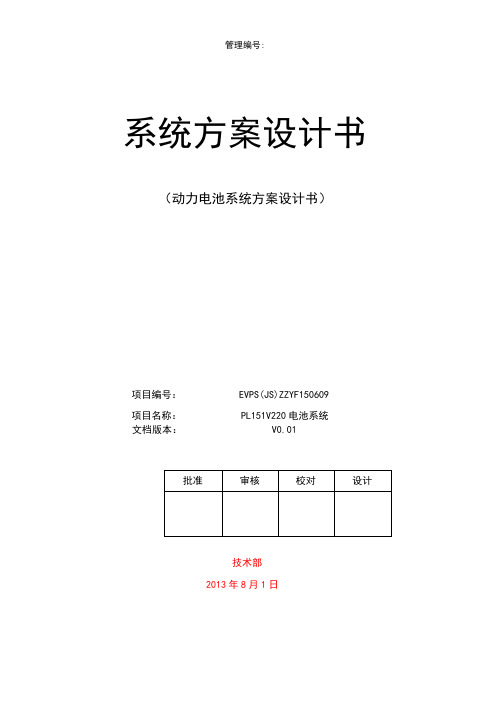
V0.01管理编号:系统方案设计书(动力电池系统方案设计书)文档版本:技术部 2013年8月1日项目编号: EVPS(JS)ZZYF150609 项目名称:PL151V220电池系统版本履历目录一、前言4二、概述4三、系统部件清单5四、电池组性能指标5五、电池系统结构规格6六、蓄电池控制单元技术要求76.1蓄电池控制单元基本功能76.2电池管理系统技术指标76.3蓄电池控制单元策略及动作参数86.4控制方式96.5充电方式10七、国家标准10本方案采用的主要技术符号和术语:C1:1小时率额定容量(Ah);I1:1小时率放电电流,其数值等于5(A);Cn1:1小时率实际放电容量(Ah);In1:1小时率实际放电电流,其数值等于(A);BCU(BMS):蓄电池控制单元,控制、管理、检测或计算蓄电池电和热相关参数,并提供蓄电池系统和其他车辆控制器通讯的电子装置;单体蓄电池:直接将化学能转换为电能的基本单元装置,包括电极、隔膜、电解质、外壳和端子,并被设计成可充电;蓄电池包:通常包括蓄电池组,蓄电池管理模块(不含BCU),蓄电池箱及相应附件,具有从外部获得电能并可对外输出电能的单元,亦称之为电池包;蓄电池系统:一个或一个以上蓄电池包及相应附件(管理系统、高压电路、低压电路、热管理设备以及机械总成等)构成的能量存储装置;高压盒:用来集中放置高压接触器、继电器、汇流排、保险丝、BMS等部件,实现蓄电池系统电能集中管理和分配的部件;二、概述本方案约定的电池系统(以下可简称本系统或系统)名称为PL151V220锂离子电池系统,型号为:PL151V220,额定电压为151.2V,额定容量为220Ah,额定能量33.2度。
电池系统由100并42串,合计4200只规格为18650的单体蓄电池成组,在部件上包含1个蓄电池包以及配套的高、低压线束线缆。
本系统在电气组成上由BMS、电流传感器、温度传感器、高压接触器、保险丝、MSD(内嵌保险丝)、单体蓄电池、高压连接器、高压线缆、加热元件等主要部件组成。
汽车电池自动化检测系统设计

汽车电池自动化检测系统设计
汽车电池是汽车工业的一个重要组成部分,它的性能稳定与否直接影响着汽车的使用
寿命和安全性。
为了保证汽车电池的质量,需要对电池进行严格的检测。
为了提高检测效
率和准确性,需要设计一个自动化检测系统。
汽车电池自动化检测系统主要包括以下几个方面的设计:检测流程设计、硬件设备设计、软件系统设计和数据处理设计。
对汽车电池进行检测的流程需要设计。
检测流程应包括电池外观检测、电池综合性能
测试和电池寿命测试等步骤。
在设计流程时,需要考虑到检测的快速性和准确性,尽量减
少不必要的操作和时间浪费。
需要设计硬件设备来完成对汽车电池的检测。
硬件设备主要包括电池测试台、传感器、电压表等。
电池测试台应具备稳定可靠的供电功能,并能够对电池进行充放电操作。
传感
器能够实时监测电池的温度、电压、电流等参数,电压表能够准确测量电池的电压。
然后,需要设计软件系统来控制和管理硬件设备。
软件系统应具备良好的用户界面和
操作逻辑,使操作人员能够方便地完成对电池的检测。
软件系统应能够实时显示电池的检
测结果,并将结果保存到数据库中进行记录。
设计数据处理系统来分析和处理检测数据。
数据处理系统可以对电池的检测结果进行
统计和分析,以评估电池的质量。
数据处理系统还可以根据检测结果对电池进行分类和分级。
汽车电池自动化检测系统设计

汽车电池自动化检测系统设计
近年来,随着汽车产业的快速发展,汽车电池作为汽车重要的能源装置,也越来越得
到关注。
为了保证汽车电池的质量,提高生产效率,自动化检测技术成为了汽车电池生产
线上不可或缺的一环。
因此,汽车电池自动化检测系统的设计就显得尤为重要。
本文介绍一种汽车电池自动化检测系统的设计,并详细分析其主要功能、硬件和软件
的设计。
该系统主要包括四个模块,包括电池检测模块、电池传输模块、数据处理模块和
显示模块。
一、电池检测模块
电池检测模块采用多种传感器,包括温度传感器、电压传感器、电流传感器和电阻传
感器等。
在电池不同状态下,通过这些传感器可以实时采集电池的各项参数,如电池温度、电压、电流和电阻等。
同时,该模块还能够进行正负极的判断,自动判断电池是否合格。
二、电池传输模块
电池传输模块采用自动化传输机械臂,将电池从电池检测模块自动传输到数据处理模块。
系统能够自动识别电池的尺寸和重量,并根据不同的电池尺寸和重量进行相应的传输
操作。
三、数据处理模块
数据处理模块接收电池传输模块传来的数据并进行处理,将检测到的电池各项参数与
结果进行记录、统计和分析,并自动生成测试报告。
系统能够自动判断电池是否合格,并
将不合格的电池进行分类存储。
四、显示模块
显示模块通过显示屏和语音提示等方式,将测试结果实时输出显示,用户可以通过界
面操作看到电池的检测情况,同时系统还具备报警功能,当检测到异常情况时即可自动报警。
汽车电池自动化检测系统设计
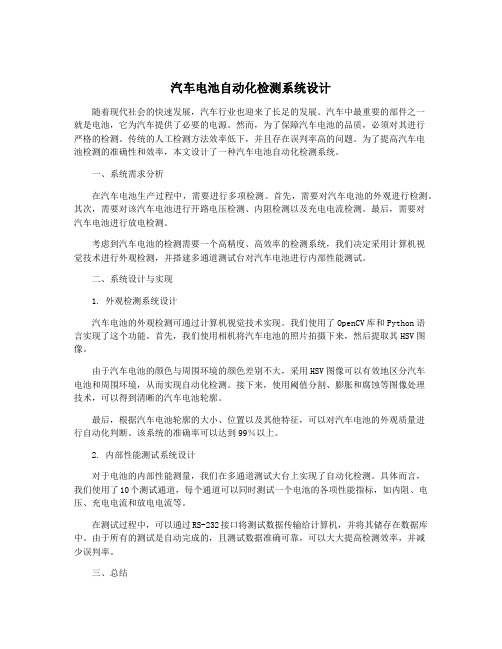
汽车电池自动化检测系统设计随着现代社会的快速发展,汽车行业也迎来了长足的发展。
汽车中最重要的部件之一就是电池,它为汽车提供了必要的电源。
然而,为了保障汽车电池的品质,必须对其进行严格的检测。
传统的人工检测方法效率低下,并且存在误判率高的问题。
为了提高汽车电池检测的准确性和效率,本文设计了一种汽车电池自动化检测系统。
一、系统需求分析在汽车电池生产过程中,需要进行多项检测。
首先,需要对汽车电池的外观进行检测。
其次,需要对该汽车电池进行开路电压检测、内阻检测以及充电电流检测。
最后,需要对汽车电池进行放电检测。
考虑到汽车电池的检测需要一个高精度、高效率的检测系统,我们决定采用计算机视觉技术进行外观检测,并搭建多通道测试台对汽车电池进行内部性能测试。
二、系统设计与实现1. 外观检测系统设计汽车电池的外观检测可通过计算机视觉技术实现。
我们使用了OpenCV库和Python语言实现了这个功能。
首先,我们使用相机将汽车电池的照片拍摄下来,然后提取其HSV图像。
由于汽车电池的颜色与周围环境的颜色差别不大,采用HSV图像可以有效地区分汽车电池和周围环境,从而实现自动化检测。
接下来,使用阈值分割、膨胀和腐蚀等图像处理技术,可以得到清晰的汽车电池轮廓。
最后,根据汽车电池轮廓的大小、位置以及其他特征,可以对汽车电池的外观质量进行自动化判断。
该系统的准确率可以达到99%以上。
2. 内部性能测试系统设计对于电池的内部性能测量,我们在多通道测试大台上实现了自动化检测。
具体而言,我们使用了10个测试通道,每个通道可以同时测试一个电池的各项性能指标,如内阻、电压、充电电流和放电电流等。
在测试过程中,可以通过RS-232接口将测试数据传输给计算机,并将其储存在数据库中。
由于所有的测试是自动完成的,且测试数据准确可靠,可以大大提高检测效率,并减少误判率。
三、总结本文设计了一种基于计算机视觉技术和多通道测试的汽车电池自动化检测系统。
该系统具有高精度、高效率以及准确可靠的特点,可以有效地提高汽车电池的检测质量和生产效率。
- 1、下载文档前请自行甄别文档内容的完整性,平台不提供额外的编辑、内容补充、找答案等附加服务。
- 2、"仅部分预览"的文档,不可在线预览部分如存在完整性等问题,可反馈申请退款(可完整预览的文档不适用该条件!)。
- 3、如文档侵犯您的权益,请联系客服反馈,我们会尽快为您处理(人工客服工作时间:9:00-18:30)。
动力电池自动化测试系统总体方案湖北德普电气股份有限公司(、3276513)第一部分:模组来料OCV检测系统方案一、简述本系统首先导入模组出厂数据到本地数据库,测试时通过条码扫描枪读取电池包的条码信息,按照预设好的测试方案,通过CAN总线读取BMS的电池OCV信息,并将电池OCV信息与出厂数据进行比对,按照预设的条件进行产品合格判定。
并把相关信息记录在数据库中,同时将不合格结果进行标签打印。
二、组成模组来料OCV检测系统主要由以下设备组成,系统原理框图如图1所示。
1)研华工控机2)Honeywell条码扫描枪3)NI PCI CAN通讯卡4)明纬开关电源5)NI PCI I/O板卡6)Zebra标签打印机7)扫描枪伺服系统8)附属组件图1 模组来料OCV检测系统原理框图三、功能实现技术方案图2 来料OCV检测系统示意模组来料OCV检测系统由工控机通过软件进行设备集成。
用户登录后,根据权限编写测试流程,测试流程包含扫描枪伺服系统的控制、DBC文件的选择、不合格条件的设定等,并将测试流程与条码进行模糊绑定。
在进行具体测试过程中,当完成线束连接后,可以点击启动按钮,模组来料OCV检测系统自动按照测试方案驱动扫描枪伺服系统,扫描枪到预设位置后读取相应的条形码填入对应位置。
条形码读取完毕后自动从数据库中搜索电池的相应出厂OCV值,并根据DBC文件,自动通过PCI CAN通讯卡读取并解析相应的电池OCV 信息,按照预设的判定条件进行结果判定。
完成测试后,将不合格的测试结果按照预设格式进行打印。
同时出于满足手动调试的需要,所有的操作均可以单步手动操作。
工控机内安装PCI接口的CAN通讯卡、I/O板卡。
工控机通过PCI I/O板卡控制的接触器对BMS上电、下电控制。
工控机通过PCI CAN通讯卡与BMS进行通讯,完成数据的读取与解析。
按照功能划分,软件具备如下功能:3.1人机界面提供用户的登入登出、新用户的建立、管理等功能。
软件提供了测试流程的编辑、检查、载入等功能。
并提供测试方案的启动、停止、暂停、回复等按钮,用于测试流程控制。
软件提供了电池条码信息、接触器状态、BMS信息、测试流程的状态等信息。
界面大致如下:图3 模组来料测试系统主界面示意图3.2 测试流程控制软件能根据预先编制好的测试方案,按照用户的命令启动测试方案,并能按照测试方案自动的执行测试流程,并完成结果判定。
模组条码扫描查找入厂OCV 开始测试读取当前OCVOCV 差值计算结果判断连接线束接插件数据保存断开线束接插件工控机CAN 卡BMU网卡被测模组CMU被测模组CMU被测模组CMU被测模组CMU被测模组CMU被测模组CMUMES 数据服务器条码扫描枪图4系统及流程3.3 数据存储、管理、查询功能记录用于对电池包设备的OCV 测试信息,并存储在数据库中,并提供查询界面,用于用户查询。
图5 数据管理功能示意3.4标签打印通过以太网接口,将电池包的测试结果按照定制好的格式用标签打印机打印出来,粘贴在流程卡上,便于直接查看电池包状态。
打印格式由客户定制。
四、接口及形式◆对MES的以太网通讯接口◆对电池包的CAN通讯接口◆对电池包的12VDC电源接口第二部分:绝缘测试系统方案一、简述本系统通过条码扫描枪读取电池包的条码信息,按照预设好的测试方案,依次闭合电池包引线与耐压测试仪之间的连线,并启动高压绝缘测试仪对电池包进行绝缘测试,并根据测试结果进行产品合格判定。
并把相关信息记录在数据库中,同时将结果进行标签打印。
二、组成绝缘测试系统主要由以下设备组成,系统原理框图如图1所示。
1)研华工控机2)Honeywell条码扫描枪3)Chroma 绝缘耐压测试仪4)NI PCI I/O板卡5)Zebra标签打印机6)附属组件图1 绝缘测试系统原理框图三、功能实现技术方案绝缘测试系统由工控机通过软件进行设备集成。
用户登录后,根据权限编写测试流程,测试流程包含绝缘耐压仪的参数设定、辅助接触器的闭合与断开、绝缘测试的启动停止、绝缘测试结果的判定条件等,并将测试流程与条码进行模糊绑定。
在进行具体测试过程中,当完成线束连接后,可以点击启动按钮,绝缘测试系统自动按照测试方案闭合对应的接触器、完成对绝缘耐压仪参数的设定后,自动启动绝缘耐压仪对电池包进行绝缘测试,并将测试结果按照预设好的条件进行判定。
完成测试后,将测试结果按照预设格式进行打印。
同时出于满足手动调试的需要,所有的操作均可以单步手动操作。
工控机内安装PCI接口的I/O板卡。
工控机通过PCI I/O板卡控制的接触器实现对绝缘耐压仪输出正对电池包主正、电池包主负、MSD In、MSD Out引线的互锁与切换,并利用接近开关及PC I/O板卡判定线束是否在位,进行操作命令的锁定。
工控机通过RS232口实现对绝缘耐压仪参数的传递、启停的控制等功能。
按照功能划分,软件具备如下功能:3.1人机界面提供用户的登入登出、新用户的建立、管理等功能。
软件提供了测试流程的编辑、检查、载入等功能。
并提供测试方案的启动、停止、暂停、回复等按钮,用于测试流程控制。
软件提供了电池条码信息、接触器状态、绝缘耐压仪状态及信息、测试流程的状态等信息,用于用户掌握绝缘测试系统的实时状态。
图2 测试流程设置示意3.2测试流程控制软件能根据预先编制好的测试方案,按照用户的命令启动测试方案,并能按照测试方案自动的执行测试流程,并完成结果判定。
图3 结果判定示意3.3数据存储、管理、查询功能记录用于对电池包设备的绝缘耐压测试信息,并存储在数据库中,并提供查询界面,用于用户查询。
查询方式同第一部分。
3.4标签打印通过以太网接口,将电池包的测试结果按照定制好的格式用标签打印机打印出来,粘贴在流程卡上,便于直接查看电池包状态。
四、接口及形式◆对MES的以太网通讯接口◆对电池包的耐压测试接口◆对电池包的12VDC电源接口第三部分:软件刷写测试系统方案一、简述本系统通过条码扫描枪读取电池包的条码信息,控制电源对设备上电后,调用预设好的用户程序完成对电池包的控制器应用层程序的刷写,刷写完成后控制电源重新对电池包BMS上电,检查确认系统基本参数,并将物流信息写入控制器中。
并把相关信息记录在数据库中,同时将结果进行标签打印。
二、组成软件刷写测试系统主要由以下设备组成,系统原理框图如图1所示。
1)研华工控机2)Honeywell条码扫描枪3)NI PCI CAN通讯卡4)明纬开关电源5)NI PCI I/O板卡6)Zebra标签打印机7)附属组件图1 软件刷写测试系统原理框图三、功能实现技术方案软件刷写测试系统由工控机通过软件进行设备集成。
用户登录后,根据权限编写测试流程,测试流程包含选择需要刷写的用户程序、用于解析BMS协议的DBC文件、系统基本参数的合理性的判定条件、需要写入的物流参数的设定,并将测试流程与条码进行模糊绑定。
在进行具体测试过程中,当完成线束连接后,可以点击启动按钮,软件测试系统自动完成软件的刷写、BMS的重上电、系统基本参数的判定、物流参数的写入等功能,完成测试后,将测试结果按照预设格式进行打印。
同时出于满足手动调试的需要,所有的操作均可以单步手动操作。
工控机内安装PCI接口的CAN通讯卡、I/O板卡。
工控机通过PCI I/O板卡控制的接触器对BMS上电、下电控制。
工控机通过PCI CAN通讯卡与BMS进行通讯,完成程序刷写、系统基本参数读取、物流参数的写入等功能。
按照功能划分,软件具备如下功能:3.1人机界面;提供用户的登入登出、新用户的建立、管理等功能。
软件提供了测试流程的编辑、检查、载入等功能。
并提供测试方案的启动、停止、暂停、回复等按钮,用于测试流程控制。
软件具备电池包基本参数显示、刷写过程显示、物流参数显示等,提供刷写过程中的一些必要信息。
操作名称快捷操作功能载入载入方案启动启动运行停止停止运行暂停暂停运行恢复恢复运行3.2测试流程控制软件能根据预先编制好的测试方案,按照用户的命令启动测试方案,并能按照测试方案自动的执行测试流程,并完成结果判定。
3.3数据存储、管理、查询功能;记录用于对电池包设备的操作信息,并存储在数据库中,并提供查询界面,用于用户查询。
查询功能同第一部分。
3.4标签打印;通过以太网接口,将程序的刷写结果与电池包的测试结果,按照定制好的格式用标签打印机打印出来,粘贴在流程卡上,便于直接查看电池包状态。
打印内容用户定义。
四、接口及形式◆对MES的以太网通讯接口◆对电池包的CAN通讯接口◆对电池包的12VDC电源接口第四部分:电池包EOL测试系统方案一、简述电池包EOL综合测试系统是针对目前电池Pack测试过程自动化程度较低,记录分析能力较差的问题,开发的一种全智能化测试平台。
将电池充放电测试、电池安规检测、电池参数测试、BMS测试、辅助功能测试等多种功能,通过设备集成的方式,实现整个工作流程全智能化、自动化,以达到减少操作人员、提高测试效率的目的。
测试范围包含电池本体及相关辅件、BMS系统等。
二、功能、组成2.1 测试功能EOL系统的主要测试功能及分配如下表所示。
表1 EOL系统测试功能及分配列表注:开路电压测试根据精度要求不同,可用充放电测试仪或仪表进行测试2.2 组成EOL综合测试平台主要由以下设备组成,系统原理框图如图1所示。
1)充放电测试仪2)Pack自动测试柜3)研华工控机(含触摸屏显示器等)4)可编程五位半高性能数字万用表5)标准电阻模块6)NI PCI CAN通讯卡7)NI PCI AI/DI/DO接口板卡8)NI cDAQ数采板卡9)Honeywell条码扫描枪10)标签打印机11)线束在位传感器12)明纬开关电源13)附属组件如图1所示,EOL综合测试系统主要由上位机、充放电测试仪及Pack测试柜组成,其中PACK自动测试柜主要包含工控机、五位半高性能数字万用表、NI cDAQ数采板卡和标准电阻模块等。
标准电阻模块万用表标准电阻模块万用表图1 EOL 系统原理图三、功能实现技术方案 3.1 总体设计方案电源系统EOL 综合测试平台主要由上位机、充放电测试仪及Pack 自动测试柜组成,总体设计方案如下: 3.1.1 上位机方案上位机作为系统控制中心,完成人机界面功能、工艺流程编制及指令的下发、数据显示和保存等功能。
设计方案如下: a )上位机硬件方案上位机采用研华工控机,其硬件配置不低于下列要求: 1)CPU :Intel 双核3.0G 以上 Dual core above 3.0GHZ 2)硬盘:≥1T GB Hard drive above 1TGB 3)RAM :≥4 GB4)有相应的接口与电池测试系统通讯,PCI 插槽≥2通道,RS232接口≥1通道。