油品罐区DCS系统改造(材料相关)
基于SIS与DCS集成的罐区安全控制技术及应用
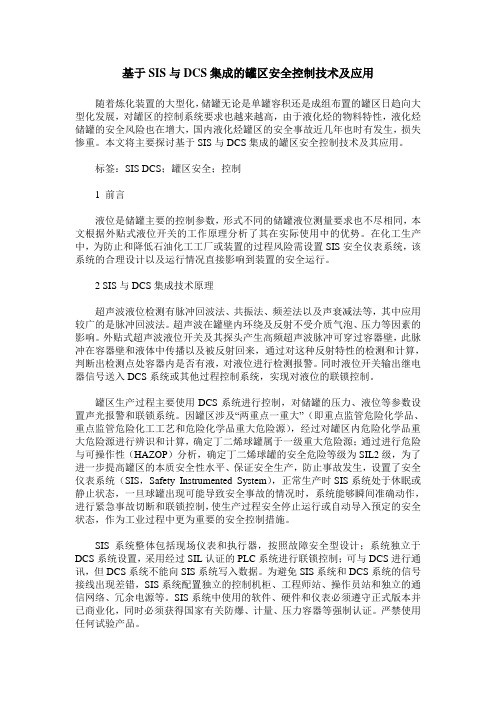
基于SIS与DCS集成的罐区安全控制技术及应用随着炼化装置的大型化,储罐无论是单罐容积还是成组布置的罐区日趋向大型化发展,对罐区的控制系统要求也越来越高,由于液化烃的物料特性,液化烃储罐的安全风险也在增大,国内液化烃罐区的安全事故近几年也时有发生,损失惨重。
本文将主要探讨基于SIS与DCS集成的罐区安全控制技术及其应用。
标签:SIS DCS;罐区安全;控制1 前言液位是储罐主要的控制参数,形式不同的储罐液位测量要求也不尽相同,本文根据外贴式液位开关的工作原理分析了其在实际使用中的优势。
在化工生产中,为防止和降低石油化工工厂或装置的过程风险需设置SIS安全仪表系统,该系统的合理设计以及运行情况直接影响到装置的安全运行。
2 SIS与DCS集成技术原理超声波液位检测有脉冲回波法、共振法、频差法以及声衰减法等,其中应用较广的是脉冲回波法。
超声波在罐壁内环绕及反射不受介质气泡、压力等因素的影响。
外贴式超声波液位开关及其探头产生高频超声波脉冲可穿过容器壁,此脉冲在容器壁和液体中传播以及被反射回来,通过对这种反射特性的检测和计算,判断出检测点处容器内是否有液,对液位进行检测报警。
同时液位开关输出继电器信号送入DCS系统或其他过程控制系统,实现对液位的联锁控制。
罐区生产过程主要使用DCS系统进行控制,对储罐的压力、液位等参数设置声光报警和联锁系统。
因罐区涉及“两重点一重大”(即重点监管危险化学品、重点监管危险化工工艺和危险化学品重大危险源),经过对罐区内危险化学品重大危险源进行辨识和计算,确定丁二烯球罐属于一级重大危险源;通过进行危险与可操作性(HAZOP)分析,确定丁二烯球罐的安全危险等级为SIL2级,为了进一步提高罐区的本质安全性水平、保证安全生产,防止事故发生,设置了安全仪表系统(SIS,Safety Instrumented System),正常生产时SIS系统处于休眠或静止状态,一旦球罐出现可能导致安全事故的情况时,系统能够瞬间准确动作,进行紧急事故切断和联锁控制,使生产过程安全停止运行或自动导入预定的安全状态,作为工业过程中更为重要的安全控制措施。
石油化工罐区自动控制系统和生产管理系统

石油化工罐区自动控制系统和生产管理系统张华莎【摘要】介绍了石油化工储运罐区自动控制系统的基本结构和功能,从工程设计角度讨论了罐区特有的设计内容和设计方法,库存量统计和信息管理是罐区特有的内容,从工程设计上考虑,罐区应配备相应的自动化仪表和储罐数据管理设备以实现罐容计算,提高罐区的控制和管理水平.特别介绍了储罐液位仪表和电动控制阀的通信连接方案及通信设备配置的注意事项,并给出了仪表接线的示例.阐述了罐区生产管理系统的结构、功能、各组成部分间的信号关系,列举了该系统应配备的基本硬件、软件,结合实际的罐区生产作业介绍了各软件的功能,提出了罐区自动控制系统和生产管理系统应遵循配置合理、功能齐全、层次清晰、管控兼顾的设计概念.【期刊名称】《石油化工自动化》【年(卷),期】2016(052)001【总页数】8页(P7-14)【关键词】石油化工罐区;罐区自动控制系统;储罐信号通信单元;电动阀通信单元;储罐数据管理单元;罐区生产管理系统【作者】张华莎【作者单位】中国石化工程建设有限公司,北京100101【正文语种】中文【中图分类】TP273近年来国内新建的石油化工厂储运罐区的自动化水平已经不仅局限于采用仪表测量加分散型控制系统(DCS),有些厂家还配有罐区生产管理系统。
将罐区的自动控制系统、生产管理系统与工厂信息管理系统结合起来,卓有成效地提高了储运系统的整体自动化水平和管理水平,实现了控制和管理的系统集成、数据共享、功能集成。
这是新建工厂储运系统的运行和管理模式,也是老厂改造的方向。
储运罐区在自控工程设计之初就应对将来的自动控制水平、设备和技术的先进程度、生产运行的管理层次和模式等多方面充分考虑,明确定位。
本文针对工程设计的范畴,重点讨论在设计目标明确定位的基础上,如何合理配置自动化测量仪表,建立适用的测量基础,配备以DCS为核心的过程控制系统,在此基础上实施罐区生产管理系统的设计方案和设计方法。
十几年前,国内炼油工业储运系统的自动化水平较低,自动测量仪表较少,配备的仪表精度不高,罐区过程控制和生产操作多采用小型控制仪或工业控制机。
DCS控制系统的升级改造

D C S控制系统的升级改造李晓娟,杨芝军(中盐青海昆仑碱业有限公司,青海㊀德令哈817099)摘要:介绍我公司热电车间D C S控制系统升级改造的原因和改造方案,通过硬件和软件升级提升了自动控制设备的性能,并提高了D C S控制系统的操作稳定性和运行效率.关键词:D C S控制系统;控制器;组态;硬件;升级中图分类号:T Q056.22㊀㊀文献标识码:B㊀㊀文章编号:1005-8370(2018)05-43-031㊀系统概况中盐青海昆仑碱业有限公司热电车间D C S控制系统采用MA C S V系统,系统版本为MA C S V 5.2.3S P2,系统配置为:控制室:15台计算机主机,15台计算机显示器.电子间:10面主控机柜,7面扩展柜.D C S系统配置见表1.表1㊀D C S系统配置表设备名称10#站11#站12#站13#站14#站15#站16#站17#站18#站19#站F M148A9209209201292613F M151A2424242234F M147E1201201208814F M1433535351111113F M161-D I7111011711572029F M161-S O E3202322300F M171B595959551116总计415141514151454572692㊀原有控制系统存在的问题2.1㊀电子元件老化所有电子产品都有一定寿命,5~7年属于设备的老化峰期,模块经过多年运行,受空气㊁灰尘及腐蚀性气体侵蚀㊁老化后会出现工作不稳定的情况,各D P接头及节点处也会出现氧化㊁松动等现象,D P 链路阻抗会增大,如超过系统要求值,则会造成模块离线等情况,严重的会导致系统非计划停车,影响正常生产.热电车间D C S系统自2010年投产以来运行已有8年时间,近两年来D C S故障率明显增加,从2016年开始,运行期间曾多次出现模块离线㊁烧坏㊁通道坏㊁电路板小配件掉落等故障,严重影响设备安全稳定运行.2.2㊀服务器问题现有MA5系统采用的是服务器结构,服务器位于上位和控制器之间,将上位机的指令和现场数据通过服务器来交换.热电车间采用的上位机㊁服务器系统为X P,微软已于14年宣布X P系统退役,停止对该系统的更新,目前所有主流计算机厂家生产的计算机硬件无法识别X P系统.2014年服务器出现过无法切换㊁通讯故障,2015年出现过服务器无法登录在线下装故障,2017年服务器硬盘故342018年第5期㊀㊀㊀㊀㊀㊀㊀㊀㊀㊀㊀㊀李晓娟,等:D C S控制系统的升级改造障,D E L L厂家表示此型号已停产,无备件更换,这就意味着一旦服务器出现故障,无法购买备件,导致D C S系统瘫痪,造成非计划停车,存在严重安全隐患,急需解决.2.3㊀网络问题D C S系统中采用交换机构建实时数据网络.以太网最大的风险在于发生网络风暴,导致网络性能下降,甚至网络瘫痪,进而引起D C S系统崩溃导致机组发生跳闸事故.热电车间D C S系统已经连续运行近十年,操作站主机㊁网卡㊁交换机等已经进入不稳定运行阶段,因其质量或性能可能引起数据刷新速度缓慢,甚至演变成网络风暴造成系统崩溃情况发生,为了减少事故发生,防患于未然,需将操作站主机㊁交换机㊁网卡同时更换.2.4㊀控制器问题多年来D C S系统硬件扩展及软件组态的增补修改已经使C P U负荷超过了临界状态(实际平均负荷已达33%,和利时出厂规定正常负荷不能超过30%),不利于系统的稳定运行.D C S控制器负荷过重,容易造成控制器数据处理滞后,甚至造成整个系统的瘫痪.而一旦控制系统瘫痪必须厂家专业技术人员到现场处理,势必给企业造成停产损失.18#站公用系统多次出现主控单元故障,导致A㊁B主控在故障情况下无法进行无扰切换,一旦A 主控有任何故障,将导致整个公用系统瘫痪,无法运行,严重影响设备的安全㊁稳定运行.2.5㊀系统局限性随着自动化水平不断升级,原有MA C S V5.2.3因系统局限性,无法实现在线下装,生产运行中遇到的修改量程㊁修改通道等问题无法及时解决,只能等到全厂大修才能进行修改,造成备件的极大浪费,对生产带来极大不便.3㊀升级方案及优势因公司生产需求无法长时间停车,此次升级面临最大的问题是工作时间紧㊁工作量大,为保证在仅有的4天全厂停车检修时间内完成此次D C S系统升级任务,决定按照以下方案进行改造:3.1㊀软件升级将现有D C S系统软件部分由MA C S V5.2.3S P2升级为MA C SV6.5.3.新的系统软件提供合法㊁专用的软件授权.由和利时公司提供升级后的MA C SV6.5.3系统软件升级资料和全套电子版系统资料.服务器㊁操作员站安装微软正版授权的W i nGd o w s7操作系统.MA C SV6.5.3与原有F M系列模块具有很好的兼容性,所以原有F M系列模块不更换,直接将D C S系统升级改造到MA C S V6.5.3+K主控工作,不更改原有的D C S系统各站的所有功能(操作㊁显示㊁报警㊁趋势显示㊁历史趋势历史数据显示和查询等).3.2㊀硬件升级1)取消服务器I O通讯的功能点对点结构:操作站直接与控制站直接通讯,系统更加稳定,风险更加分散,减轻了网络数据负荷,提高了系统的稳定度.操作员站直接访问控制器真正的点对点结构.2)所有操作员站升级工程师站使用和利时公司验证的工作站主机平台T5810㊁液晶显示器㊁双口网卡.操作员站硬件采用D E L L5050MT维塔式工作站,主要技术参数为:C P U,I n t e l酷睿i57500,3.4G H z;内存,2ˑ4G;硬盘,500G B.3)网络交换机升级将原有的4台交换机更换为最新的GM010-I S W-24L系列,此交换机为和利时有自主研发的防网络风暴交换机,可明显的抑制网络风暴,大大提高或改善网络运行性能,更利于系统的稳定运行.3.3㊀控制器升级D C S控制器的升级主要是将原有的F M801控制器升级为K-C U01控制器.和利时公司K-C U01控制器是K系列硬件的控制器模块,是系统的核心控制部件,支持两路冗余I O-B U S和从站I/O模块进行通讯,支持两路冗余以太网和上位机进行通讯,实时上传过程数据以及诊断数据.可以在线下装和更新工程,且不会影响现场控制.比F M801控制器具有更强大的运算能力,完全兼容F M系列I/O卡件.因为F M801控制器和K-C U01控制器都是MA C S V系列硬件,所以升级时组态只需要用自带软件工具导入就可以,不会改变原有的控制策略.由于F M801控制器和K-C U01控制器安装结构44纯㊀碱㊀工㊀业相同,因此,只需将原F M801控制器机架拆除,在相同位置安装K-C U01控制器即可,原有I/O卡件和端子接线不变,从而能以最短的时间㊁最低的风险实现系统升级.3.4㊀系统升级优势1)MA C SV6安全可靠的控制器软硬件H E R O S操作系统 内置防火墙功能.双网故障不影响控制.优化的控制软件 完善的冗余机制等改进保证控制的可靠性.专业的算法库 符合行业使用需要的算法库,便于使用.100M通信网络 高速以太网保证了系统的高可靠性.2)MA C SV6灵活可靠的网络结构单层单层控制网 结构简洁,操作方便,安全可靠网络结构.可靠的监控功能 操作员与控制器点对点通讯,保证可靠的数据采集和操作.便携的下装过程 增加测点,修改画面或方案页,下装操作站和控制站直接生效.安全的历史站 提供丰富的历史数据.可与控制站通信,提供数据采集的备份功能.网络安全方案 和利时定制交换机预防网络风暴,已申请专利.4㊀升级后D C S系统现状1)MA C S V6系统报警及日志记录数量较MA C SV5增加表2㊀报警及日志记录数量比较名称升级前MA C SV5最大缓冲区容量升级后MA C SV6最大缓冲区容量全日志记录10000条30000条S O E日志记录2000条5000条简化日志记录2000条5000条操作日志记录1000条5000条设备日志记录1000条1000条工艺报警记录无5000条设备报警记录无5000条开关量抖动记录无5000条强制表记录无1000条2)MA C S V6系统C P U负荷较MA C S V5系统大幅下降表3㊀C P U负荷比较站号升级前MA C SV5C P负荷升级后MA C SV6C P负荷1030%7.59%1132%9.09%1230%7.59%1329%9.4%1429%7.59%1533%9.79%1629%7.59%1729%7.09%1834%9.00%1934%9.50%5㊀结㊀语本次D C S控制系统升级改造保留原有D C S系统各站的所有功能,保留原有I/O点数,C P负荷保持在10%以内,保证D C S控制系统升级改造后整个系统的完整性㊁可靠性㊁安全性,系统可用性达到99.99%,升级后的工作站的硬件和软件都具有高可靠性,系统升级后未改变原系统I/O卡件及通道编号,方便升级改造后的维护.通过此次升级改造,提高了D C S控制系统的数据处理速度,优化了软㊁硬件,提升了D C S控制系统的可用率和运行效率,用最小的投入换取最大的经济回报.参考文献[1]㊀邢建春,杨启亮,王平.新技术形势下D C S的发展对策[J].自动化仪表,2003,24(1)[2]㊀王美英.热工仪表及自动装置[M].北京:中国电力出版社,2012收稿日期:2018-06-20作者简介:李晓娟(1987 ),中国矿业大学毕业,热能与动力工程专业,本科,助理工程师,现任中盐青海昆仑碱业有限公司热电车间热工专工.542018年第5期㊀㊀㊀㊀㊀㊀㊀㊀㊀㊀㊀㊀李晓娟,等:D C S控制系统的升级改造。
DCS系统升级施工方案

目录一、编制说明 0二、编制依据 0三、工程概况 0四、施工部署 (1)4.1、主要设备、机具需用及要求 (1)4.2、劳动力需用及要求 (2)五.主要施工工艺及控制要求 (4)5.1、电气安装工程施工方案 (3)5.2、仪表安装工程施工方案 (4)六.质量保证措施 (7)6.1质量保证体系 (7)6.2、质量控制措施 (8)6.3质量控制点 (9)七、TNPM管理 (9)7.1、施工现场管理规定 (9)八、项目HSE专篇 (10)8.1 编制依据 (10)8.2 项目HSE管理方针与目标 (10)8.3 项目HSE管理制度 (11)8.4 项目HSE组织机构 (11)8.5 项目HSE组织人员管理职责 (12)8.6 HSE管理措施 (20)8.7现场各项作业活动的危害分析及HSE管理措施 (20)九、文明施工保证措施 (30)9.1文明施工的目标 (30)9.2文明施工组织机构 (30)9.3文明施工管理措施 (30)十、应急预案 (31)10.1成立项目HSE应急管理组织机构 (31)10.2应急预案处理要求 (31)10.3职责分工 (31)10.4应急措施 (31)10.5紧急事件联系 (32)10.6应急资源 (32)10.7 JHA危害分析评估组及危害分析表(附件) (32)10.8环境因素识别表(附件) (32)10.9危险源/残留物识别清单(附件) (32)一、编制说明本文件是SFCC为中国石化广州石化分公司乙烯装置DCS系统升级改造施工而制定的方案。
SFCC 为保证本单项工程进度、质量、安全所采取一系列的措施。
严格执行招标文件所规定的国家的法律、法规,国家和行业的施工验收标准和规范,以及业主各项管理规定,使交付的产品达到顾客的要求和期望,增强顾客的满意程度。
二、编制依据1、《聚乙烯PLC系统隐患治理项目》施工图纸2、《石油化工静电接地设计规范》 SH3097-20003、《石油化工仪表工程施工技术规程》 SH/T3521-20134、《自动化仪表工程施工及验收规范》 GB50093-20135、《建筑电气工程施工质量验收规范》 GB50303-20126、《电气装置安装工程接地装置施工及验收规范》 GB50169-20067、《电气装置安装工程电缆线路施工及验收规范》GB50168-2006三、工程概况3.1、工程名称:乙烯装置DCS系统升级改造3.2、建设单位:中国石油化工股份有限公司广州分公司3.3、监理单位:广州石化建设监理有限公司3.4、设计单位:南京金凌石化工程设计有限公司3.5、施工单位:中石化第五建设有限公司3.6、工程介绍3.6.1、乙烯装置DCS系统升级改造在2015年随炼油一系列大修,化工二部及各专业部门就存在的问题进行了讨论并确立了解决方案,以满足装置的生产操作要求及原则,需对装置的工艺流程进行相应的优化。
DCS控制系统升级改造实践

DCS控制系统升级改造实践黑龙江哈尔滨150000摘要:经济在快速发展,社会在不断进步,DCS控制系统是一种典型的工业控制系统,它的系统原理基本结构是在微处理器的基础上,可以使控制功能实现分散性,使可显示的操作集中在一起,兼顾所有操作的同时还能够分而治之。
DCS控制系统是目前比较流行的分散控制系统,在国内,DCS控制系统称作是集散控制系统。
近些年随着国内、外工业自动化的普及和自动化技术的不断发展、提高,我国很多企业和公司普遍采用DCS控制系统。
随着科技不断进步,DCS控制系统也在不断完善和发展,性能也在迅速提高而且DCS系统的价格在逐渐下降,对DCS控制系统的升级改造也随之增多。
关键词:DCS控制系统;自动化;升级改造引言进入新世纪以来,我国的社会主义市场经济持续发展,为石油炼化企业带来了前所未有的发展机遇和挑战。
一方面,现代技术不断发展,优化了石油炼化企业的控制系统。
另一方面,工作环境日益复杂,增加了机组故障发生频率。
在炼化企业中,DCS系统的应用最为广泛。
就目前来看,大部分炼化企业对DCS系统进行了升级改造,在很大程度上提高了内控水平。
为了进一步促进炼化企业的发展,必须对DCS系统故障进行分析和处理。
1、改造的必要性每套控制系统都是冗余的服务器运行,某催化DCS系统现为HONEYWELL PKS PMIO结构,下层IO卡件均为2008年投用,至2023年将使用18年,超年限服役,经多次扩容改造,系统负荷大,故障率升高,网络不稳定,同时HM、NIM、服务器等关键部件急需改造升级。
单台服务器故障时,备用服务器会立刻切换为主服务器,不会立刻影响生产,但也存在2台服务器同时故障的可能性,服务器故障会切断操作员站与现场设备的实时数据连接,严重影响生产的稳定运行。
2、DCS控制系统升级改造实践2.1数据库和逻辑组态原有的点名以及点信息不变的情况下,按照NT+系统的数据库格式和要求重新生成数据库并下载,控制逻辑以目前机组实际控制逻辑为本,进行逻辑组态,对每个DPU站,重新绘制逻辑图,将原有DCS/DEH系统的LOOP,LADDER以及TEXT算法用更加方便的图形化工具进行绘制,最终生成NT+系统需要的SAMA图。
基于DCS的汽油在线调合系统的设计与实现

调 合 服务 器 的 给定 自动 完 成 , 合 服 务 器 与 D S通 过 开 放 的 调 C O C接 口实 现 数 据 传输 通讯 。 析 仪 器 工 作 站 通 过 MO B S P 分 D U
通 讯 方 式 给 D S传 输 数 据 。 系统 构 成 如 图 1 示 。 C 所
APNBED S E L N 在线调合控制系统 近红外分析仪 — DS E 控制系统
来 达 到 卡 边 控 制 各 个 质 量 指 标 的 目 的 。D ls根 据 预 测 MC P u
跟踪 和优化 . 用 A M 利 B L提 供 的调 合 规 则 对 各 个 质 量 指 标 进
行 计 算 , 用 多 变 量 预 估 控 制 技 术 同 时 对 各 个 质 量 指 标 进 行 采 实 时 控 制 。完 成 对 不 同 质 量 指 标 的 不 同 方 向 的 卡 边 生 产 。 A P N B E D调 合 软 件 系 统 具 备 很 好 的 集 成 能 力 ,方 便 实 SE L N
时所 需 要 完 成 的泵 、 等 的 启 动 和停 止 动 作 由 D S系 统 根 据 阀 C
1 项 目实施 的必 要性
在 实 施 调 合 项 目之 前 条 件 比较 落 后 , 采 用 的 是 手 动 罐 调 , 经 过 人 工 运 算 或 查 表 得 出 调 合 配 方 后 . 不 同 的 组 分 即 把
调合头 添加剂系统
直 接 输 送 到 指 定 的成 品罐 。 装 在 成 品 罐 里 的 搅 拌 器 进 行 搅 安 拌 均 匀 , 验 室 化 验 后 如 果 不 合 格 则 再 加 入 相 关 组 分 , 后 实 然 继 续 搅 拌 均 匀 。 此 循 环 直 到 成 品合 格 。 这 种 原 始 的调 合 方 如
DCS系统改造安全施工方案

DCS系统改造安全施工方案DCS(分散控制系统)是一种用于工业自动化控制的先进控制系统。
在进行DCS系统改造时,需要特别关注安全施工方案,以确保改造过程顺利进行,并保障人员和设备的安全。
首先,安全施工方案应包括人员培训和安全意识教育。
所有参与改造工作的人员都应接受相关的培训,了解DCS系统改造项目的安全要求和操作规程。
培训内容应包括DCS系统的安全控制和操作,紧急情况下的应急措施等。
此外,还应对施工现场人员进行安全意识教育,强调他们在施工过程中的安全责任和注意事项。
其次,安全施工方案应设计安全防护措施。
在进行DCS系统改造时,施工现场可能存在一些安全风险,如电气危险、火灾风险等。
为了预防事故的发生,应在施工现场设置相应的安全防护设施,如防护栅栏、灭火器等。
同时,施工人员应佩戴必要的个人防护装备,如安全帽、防护眼镜、绝缘手套等,以保障个人安全。
同时,安全施工方案还应考虑物料和设备的安全管理。
在进行DCS系统改造时,会涉及到一些特殊工具和设备,如焊接设备、电缆等。
这些物料和设备的选择和使用应符合相关标准,确保其安全性。
此外,还应加强对物料和设备的管理和监管,避免其滋生潜在的安全风险。
此外,安全施工方案还应包括施工现场的安全管理措施。
在进行DCS系统改造时,施工现场可能会出现一些危险情况,如高温、高压等。
因此,在施工现场应设置相应的警示标识,明确标识危险区域,并在必要时设置安全警报装置。
同时,还应定期进行施工现场的安全检查和巡视,确保施工过程中的安全。
最后,安全施工方案还应考虑项目的安全监控和事故应急预案。
在DCS系统改造过程中,应设置相应的安全监控系统,对施工现场的安全状况进行实时监测和记录。
一旦发生事故,应根据预先计划的应急预案,立即采取相应的措施,防止事故扩大,并确保人员的安全。
总之,DCS系统改造安全施工方案应包括人员培训和安全意识教育、安全防护措施、物料和设备的安全管理、施工现场的安全管理措施以及安全监控和事故应急预案等内容。
dcs改造可行报告

DCS改造可行报告一、问题背景在现代工业生产中,DCS(分散控制系统)扮演着至关重要的角色,它通过集中监控和分散控制的方式,实现对工业过程的自动化管理。
然而,随着工业技术的不断更新和发展,传统DCS系统在面对复杂工艺、大规模生产等挑战时逐渐显露出一些局限性和不足,因此对DCS系统的改造迫在眉睫。
二、问题分析1. 传统DCS系统存在的问题-功能受限:传统DCS系统功能较为单一,无法满足复杂工艺的需求。
-通讯瓶颈:DCS系统中的通讯方式相对陈旧,导致数据传输速度慢。
-安全性不足:随着网络攻击技术的不断进步,传统DCS系统的安全性风险增加。
2. DCS改造的必要性-提升生产效率:通过改造DCS系统,实现生产过程的智能化管理,提升生产效率。
-降低运营成本:新型DCS系统可以更好地利用资源,降低运营成本。
-加强安全保障:升级DCS系统可以增强系统的安全性,保障工业生产过程的安全稳定运行。
三、改造方案1. 引入先进技术-工业互联网技术:利用工业互联网技术构建智能化生产系统,实现设备之间的信息共享和协同工作。
-大数据分析:通过大数据分析,优化生产过程,实现精细化管理。
-云计算技术:将DCS系统迁移至云端,提高系统的灵活性和可靠性。
2. 优化系统架构-模块化设计:将DCS系统拆分成多个独立模块,便于维护和升级。
-分布式控制:采用分布式控制架构,提高系统的稳定性和响应速度。
-安全防护:增强系统的安全防护能力,防范网络攻击和数据泄露风险。
3. 智能化管理-自动化控制:引入智能控制算法,实现生产过程的自动化管理。
-预测性维护:利用机器学习算法对设备进行预测性维护,减少生产中断风险。
-远程监控:实现对生产过程的远程监控,及时发现并解决问题。
四、改造效果预期通过对DCS系统的改造,预计可以取得以下效果:-提升生产效率,降低能耗,提高产品质量。
-减少人为操作失误,提高生产安全性。
-降低运营成本,提高企业竞争力。
-增强系统的稳定性和可靠性,延长设备使用寿命。
加油站罐区整改施工方案
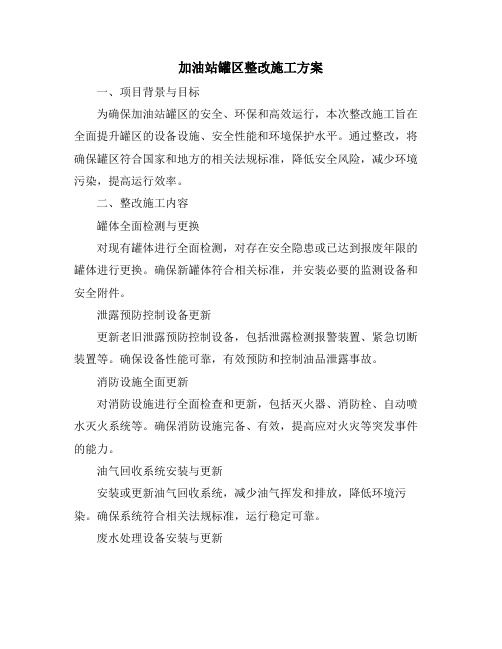
加油站罐区整改施工方案一、项目背景与目标为确保加油站罐区的安全、环保和高效运行,本次整改施工旨在全面提升罐区的设备设施、安全性能和环境保护水平。
通过整改,将确保罐区符合国家和地方的相关法规标准,降低安全风险,减少环境污染,提高运行效率。
二、整改施工内容罐体全面检测与更换对现有罐体进行全面检测,对存在安全隐患或已达到报废年限的罐体进行更换。
确保新罐体符合相关标准,并安装必要的监测设备和安全附件。
泄露预防控制设备更新更新老旧泄露预防控制设备,包括泄露检测报警装置、紧急切断装置等。
确保设备性能可靠,有效预防和控制油品泄露事故。
消防设施全面更新对消防设施进行全面检查和更新,包括灭火器、消防栓、自动喷水灭火系统等。
确保消防设施完备、有效,提高应对火灾等突发事件的能力。
油气回收系统安装与更新安装或更新油气回收系统,减少油气挥发和排放,降低环境污染。
确保系统符合相关法规标准,运行稳定可靠。
废水处理设备安装与更新安装或更新废水处理设备,确保加油站产生的废水得到有效处理,达到排放标准。
周边环境监测与保护建立周边环境监测系统,定期对加油站周边环境进行监测和评估。
发现环境问题及时采取措施,保护周边环境质量和生态安全。
排水沟渠疏通与防护对加油站内的排水沟渠进行定期疏通和清理,确保排水畅通。
同时加强沟渠的防护措施,防止油品泄露对排水系统造成污染。
物资设备防淋防湿工作对加油站内的物资设备进行防淋防湿处理,防止因天气原因造成设备损坏或性能下降。
施工过程质量控制对施工过程进行全面质量控制,确保施工质量符合设计要求和相关标准。
加强现场管理和监督,确保施工安全和质量。
施工前准备与许可在施工前做好充分的准备工作,包括施工现场布置、人员培训、设备材料采购等。
同时办理相关施工许可手续,确保施工合法合规。
三、施工进度安排本次整改施工计划分为以下几个阶段:施工前准备与许可阶段(第X周);罐体全面检测与更换阶段(第X-X周);泄露预防控制设备更新阶段(第X-X周);消防设施全面更新阶段(第X-X周);油气回收系统安装与更新阶段(第X-X 周);废水处理设备安装与更新阶段(第X-X周);周边环境监测与保护阶段(第X-X周);排水沟渠疏通与防护阶段(第X-X周);物资设备防淋防湿工作阶段(第X-X周);施工过程质量控制与验收阶段(第X-X周)。
炼油厂罐区仪表测量及报警系统的应用

孔,不动火,不损伤罐体,可不停产安装维修:不受介质的压力、密度、介电常数、腐蚀性
等因素影响测量;能够克服由于一十罐上同时安装高报、高高报、低报等各种干扰产生的误 报、冈报。综上所述,我们选用了河北球峰zKK—llI智能外贴超声液位开关。
l
2连续液位测量的技术要求为钢带内外密闭隔离,避免了油气挥发.有利于环保现场直
3
2主要技术指标
1
3 2
zYG—B301电子智能液位仪的精度为±2mm,在实际生产运行过程中误差小于±2m。 7A'G—B301电子智能液位仪的分辨翠为l硼,对于万方储罐每1胁就有几吨的偏差,在
3
2 2
实际生产运行过程中通过人工检尺和榆查仪表对照完仝满主技术要求。
3 2 3 ZWCK
IlI型液位开关精度为±2皿,在实际生产远行过程中通过人工检R实际报警谍差
4.1
ZYG一101型钢带仪表液位计,因大部分仪表使用年限均超过10年以上(其中有18台仪
表在1994年投用、34台仪表在1995年投用、两台仪表在2004年投用),故障率逐年上升, 严重影响了液位测量精度和罐区生产安全,在日常维护过程中油罐码带表经常卡瑟,新型 ZYG—B301电子智能液位仪表使用后仪表的月故障次数大幅度下降。
12000
1l 000 11000 15000 j 5500
4500
建北42 建J匕
70
止常 正常 正常 正常
建北85
12500 12500
10建北89
ZYG—B301智能液位仪具有4、20mA电流传输功能,所有罐区测量信号全部引入DCS控制 系统,进行集中显示控制,并且具备RS一485接口可以和计算机通讯,测量范围提高到o、32m, 通讯方式兼容MODUBS协议。 4.总结分析
石油化工罐区自动化系统设计规范 SH-T 3184-2017(6,8)
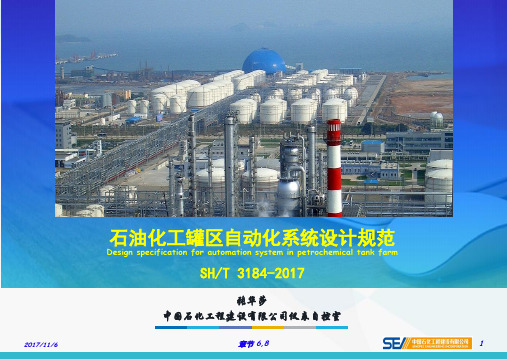
机柜室 现场
一级接线箱 JB-XXX
SI0SIOSIOSIOSIOSIOSIOSIOSIOSIO 1 2 3 4 5 6 7 8 9 10 11 12 13 14 15 16 17 18 19 20 21 22 23 24 25 26 27 28 29 30
CC-JB-XXXA
CC-JB-XXXB
······
号通信单元连接仪表的总数量不应超过通信单元能力的70%。 6.3.2 信号连接方案
6.3.2.1 雷达液位计、伺服液位计、磁致伸缩液位计与配套的储罐信号通信单元的连接路径可根据情况 选择环形、树形、混合等。 ∆ 说明:连接路径指电缆敷设经过的路线,信号电路连接方式指电路的串联、并联接线方式。串行通 信方式信号电路接线为并联。冗余的储罐信号通信单元双线环路接连原理见图 4。
石油化工罐区自动化系统设计规范
Design specification for automation system in petrochemical tank farm
SH/T 3184-2017
张华莎 中国石化工程建设有限公司仪表自控室
2017/11/6
章节 6,8
1
石油化工罐区自动化系统设计规范 —— 6 罐区自动控制系统
计量分类
计量级、非计量级
介质特性
原料油、中间产品、 产品、液化石油气 ……
计量方法
混合法、体积法、 静压法
2017/11/6
储罐计量 罐区库存统计
自动控制系统(DCS)
罐区生产管理系统(TMES)
企业资源计划系统(ERP)
章节图61,8
3
石油化工罐区自动化系统设计规范 —— 6 罐区自动控制系统
6.1 自动控制系统 6.1.1 罐区自动控制系统应具备罐区运行的过程控制、信号检测、数据处理、记录存储、人机接口、生产 操作、报表、数据服务等功能。 6.1.2 罐区自动控制系统应采用DCS、SCADA、PLC等控制系统,小型罐区、分散的、远距离的罐区也 可以采用小型控制系统。 6.1.3 计量级储罐的雷达液位计、伺服液位计、磁致伸缩液位计的信号可接入专用的储罐数据管理单元 TMU进行罐容计算和管理,也可接入自动控制系统,在DCS中通过组态实现。
石油化工罐区自动化系统设计规范 SH-T 3184-2017(9)
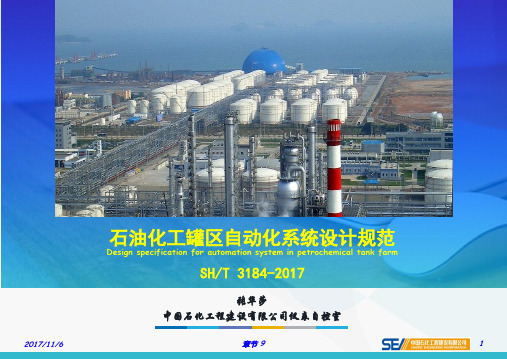
石油化工罐区自动化系统设计规范Design specification for automation system in petrochemical tank farmSH/T 3184-2017张华莎中国石化工程建设有限公司仪表自控室9 液化烃装车发运系统9.1 火车装车设施◆9.1.1 火车装车站设施●9.1.1.1 根据液化烃种类不同可采用顶部装车或顶部密闭装车方式。
●9.1.1.2 火车装车站应设置操作室,室内应设装车操作站、装车业务管理站,应按照规定的流程对装车作业全过程进行监控管理。
●9.1.1.3 装车操作站应实现装车作业的自动控制、报警、计量、记录,作业记录不能修改。
●9.1.1.4 装车业务管理站应设置与客户的销售接口,所有装车内容、收发数据、销售信息均应在业务管理站自动记录,作业记录不能修改。
●9.1.1.5 火车装车可采用批量控制器,也可采用自动控制系统直接控制。
●9.1.1.6 火车装车应设有防溢液位开关、静电接地等安全作业检测功能,并应在控制设备中设置允许操作及联锁停止的功能。
●9.1.1.7 火车装车计量可采用高精度电子动态轨道衡,也可采用流量计累积计量。
◆9.1.2 火车装车控制管理系统●9.1.2.1 火车装车控制管理系统应由现场自动化仪表、批量控制器、轨道衡和操作室内的自动控制系统和装车管理站等组成,典型的火车装车控制管理系统基本结构见图9.1.2。
●9.1.2.2 火车装车过程应通过自动控制系统操作站监控并记录,记录数据应存入历史数据库,并不得修改。
通信接口DCS/PLC 机柜……轨道衡计算机中心控制室………轨道衡………批量控制器批量控制器装车鹤位1现场装车鹤位N装车操作室装车操作站OPC 服务器DCS/PLC 操作站装车业务管理站罐区生产管理系统(TMES )和企业资源计划系统(ERP )数据服务器数据转换MODBUS RS485MODBUS RS485TCP/IP◆9.1.3 带油气回收的火车密闭装车方案●9.1.3.1 常压下易挥发的液化烃,火车密闭装车应设置油气回收装置。
DCS改造实施方案

DCS改造实施方案一、背景随着信息技术的不断发展,数字化控制系统(DCS)在工业自动化领域的应用越来越广泛。
然而,随着设备老化和生产需求的变化,许多企业的原有DCS系统已经不能满足现代生产的要求,因此需要对DCS系统进行改造升级。
二、改造目标1. 提高系统稳定性和可靠性:通过对硬件和软件的升级,提高系统的稳定性和可靠性,降低故障率,减少生产停机时间。
2. 提升系统性能:通过更新控制算法和优化系统结构,提升系统的响应速度和控制精度,提高生产效率和产品质量。
3. 拓展系统功能:根据生产需求,增加新的功能模块,满足生产工艺的变化和扩展。
4. 降低系统维护成本:通过改造,降低系统的维护成本,减少对专业技术人员的依赖,提高系统的可维护性。
三、改造方案1. 系统评估:对原有DCS系统进行全面评估,包括硬件设备的状况、软件版本和功能模块的使用情况,以及系统存在的问题和不足之处。
2. 技术方案设计:根据评估结果,制定改造的技术方案,包括硬件设备的更新、软件系统的升级、功能模块的添加和系统结构的优化等内容。
3. 设备采购和更新:根据技术方案,采购新的硬件设备,包括控制器、输入输出模块、通讯设备等,并进行设备更新和替换。
4. 软件升级和优化:对DCS系统的软件进行升级,并对控制算法和系统结构进行优化,以提升系统的性能和稳定性。
5. 功能模块添加:根据生产需求,添加新的功能模块,如数据采集与分析模块、智能控制模块等,以满足生产工艺的变化和扩展。
6. 系统集成与调试:对改造后的硬件设备和软件系统进行集成和调试,确保系统的稳定性和可靠性。
熟练掌握新系统的使用方法和维护技能。
8. 系统验收和投入运行:进行系统的验收测试,确保系统达到设计要求,并顺利投入生产运行。
四、实施步骤1. 制定改造计划:根据改造方案,制定详细的改造计划,包括时间节点、责任人和具体任务。
2. 设备采购和更新:按照计划,进行硬件设备的采购和更新工作。
3. 软件升级和优化:对软件系统进行升级和优化,确保系统的稳定性和性能。
石油化工行业生产自动化系统改造方案

石油化工行业生产自动化系统改造方案第1章项目背景与目标 (4)1.1 行业现状分析 (4)1.2 改造目标与意义 (4)1.3 改造范围与预期效果 (5)第2章自动化系统需求分析 (5)2.1 生产流程分析 (6)2.1.1 原料预处理 (6)2.1.2 化学反应 (6)2.1.3 产品分离和精制 (6)2.2 自动化系统功能需求 (6)2.2.1 数据采集与监控 (6)2.2.2 设备控制 (6)2.2.3 故障诊断与报警 (6)2.2.4 生产过程优化 (6)2.2.5 信息集成与共享 (7)2.3 自动化系统功能需求 (7)2.3.1 实时性 (7)2.3.2 可靠性 (7)2.3.3 可扩展性 (7)2.3.4 安全性 (7)2.3.5 易用性 (7)第3章自动化系统设计原则与标准 (7)3.1 设计原则 (7)3.1.1 安全性原则 (7)3.1.2 可靠性原则 (7)3.1.3 先进性原则 (7)3.1.4 可扩展性原则 (8)3.1.5 易维护性原则 (8)3.1.6 经济性原则 (8)3.2 设计标准与规范 (8)3.2.1 国家及行业标准 (8)3.2.2 企业内部标准 (8)3.2.3 国际标准 (8)3.3 技术路线选择 (8)3.3.1 控制系统选型 (8)3.3.2 传感器与执行器 (8)3.3.3 网络通信技术 (8)3.3.4 数据采集与处理 (9)3.3.5 信息化管理 (9)第4章系统架构设计 (9)4.1 总体架构 (9)4.1.2 数据处理与分析层 (9)4.1.3 生产管理层 (9)4.1.4 决策支持层 (9)4.2 网络架构 (9)4.2.1 层次结构 (10)4.2.2 分域设计 (10)4.3 硬件架构 (10)4.3.1 数据采集设备 (10)4.3.2 控制设备 (10)4.3.3 服务器 (10)4.3.4 网络设备 (10)4.4 软件架构 (10)4.4.1 数据采集与控制软件 (10)4.4.2 数据处理与分析软件 (10)4.4.3 生产管理软件 (11)4.4.4 决策支持软件 (11)第5章关键技术与设备选型 (11)5.1 控制系统 (11)5.1.1 系统架构 (11)5.1.2 控制策略 (11)5.1.3 控制器选型 (11)5.2 传感器与执行器 (11)5.2.1 传感器选型 (11)5.2.2 执行器选型 (11)5.3 数据采集与传输 (12)5.3.1 数据采集 (12)5.3.2 数据传输 (12)5.4 人工智能技术应用 (12)5.4.1 智能优化算法 (12)5.4.2 故障诊断与预测 (12)5.4.3 智能调度与优化 (12)第6章自动化控制系统实现 (12)6.1 控制策略与算法 (12)6.1.1 确定控制目标 (12)6.1.2 选择控制策略 (12)6.1.3 算法实现 (12)6.2 控制逻辑设计 (13)6.2.1 控制逻辑结构 (13)6.2.2 控制逻辑编程 (13)6.2.3 控制逻辑验证 (13)6.3 控制模块配置与调试 (13)6.3.1 控制模块选型 (13)6.3.2 控制模块配置 (13)6.4 人机界面设计 (13)6.4.1 界面需求分析 (13)6.4.2 界面布局设计 (13)6.4.3 界面开发与测试 (13)第7章数据采集与处理 (14)7.1 数据采集方案 (14)7.1.1 采集原则 (14)7.1.2 采集内容 (14)7.1.3 采集方式 (14)7.1.4 采集设备选型 (14)7.2 数据处理与分析 (14)7.2.1 数据预处理 (14)7.2.2 数据分析 (14)7.2.3 数据可视化 (14)7.3 数据存储与备份 (14)7.3.1 存储方案 (14)7.3.2 备份策略 (15)7.4 数据安全与隐私保护 (15)7.4.1 数据安全 (15)7.4.2 隐私保护 (15)7.4.3 安全审计 (15)第8章系统集成与调试 (15)8.1 系统集成策略 (15)8.1.1 集成目标 (15)8.1.2 集成原则 (15)8.1.3 集成步骤 (15)8.2 系统调试与验证 (16)8.2.1 调试目标 (16)8.2.2 调试方法 (16)8.2.3 调试过程 (16)8.3 系统优化与调整 (16)8.3.1 优化目标 (16)8.3.2 优化方法 (16)8.3.3 调整过程 (17)8.4 系统交付与验收 (17)8.4.1 交付标准 (17)8.4.2 验收流程 (17)8.4.3 验收后服务 (17)第9章运维管理与服务 (17)9.1 运维管理体系 (17)9.1.1 运维组织架构 (17)9.1.2 运维管理制度 (17)9.1.3 运维监控与评估 (17)9.2.1 故障诊断方法 (18)9.2.2 故障排除流程 (18)9.2.3 应急预案与演练 (18)9.3 维护与保养策略 (18)9.3.1 定期维护计划 (18)9.3.2 预防性维护 (18)9.3.3 动态保养策略 (18)9.4 技术支持与服务 (18)9.4.1 技术支持 (18)9.4.2 服务承诺 (18)9.4.3 售后服务网络 (18)第10章项目实施与效益评估 (19)10.1 项目实施计划 (19)10.1.1 实施目标 (19)10.1.2 实施步骤 (19)10.1.3 实施时间表 (19)10.2 项目风险与应对措施 (19)10.2.1 技术风险 (19)10.2.2 人员风险 (19)10.2.3 投资风险 (19)10.3 项目投资与成本分析 (20)10.3.1 投资估算 (20)10.3.2 成本分析 (20)10.4 效益评估与持续改进 (20)10.4.1 效益评估 (20)10.4.2 持续改进 (20)第1章项目背景与目标1.1 行业现状分析石油化工行业作为我国经济发展的重要支柱产业,近年来取得了显著的发展成果。
5化工仿真DCS罐区单元仿真操作

5化工仿真DCS罐区单元仿真操作化工仿真DCS(分散控制系统)罐区单元仿真操作是一种通过模拟和模型技术来模拟化工罐区单元操作的虚拟环境。
它通过DCS系统来监控和控制各种化工流程,提供了一个安全、可靠和高效的控制环境。
以下将介绍化工仿真DCS罐区单元仿真操作的基本流程和注意事项。
首先,进行化工仿真DCS罐区单元仿真操作前需要准备相应的硬件设备和软件平台。
硬件设备包括计算机、DCS系统、传感器、执行器等。
软件平台则包括仿真软件、模型建立软件等。
这些设备和软件的选择应根据实际场景和要求来确定。
其次,进行仿真操作前需要建立相应的模型。
模型的建立需要对罐区单元的流程、设备、传感器和执行器等进行建模和参数设置。
在建立模型时,应考虑对每个设备和传感器进行适当的标定和调整,以确保模型的准确性和可靠性。
模型的建立可以使用专业建模软件或者DCS系统自带的模型库。
接下来,进行仿真操作时,首先需要进行系统的初始化和校准。
系统的初始化包括对系统进行各种设定和参数调整,以及对传感器和执行器进行校准和调整。
校准和调整的目的是为了确保系统的准确性和稳定性。
初始化和校准完成后,系统即可进入正常的操作状态。
在进行正常的操作时,可以通过DCS系统监测和控制各个设备和流程。
DCS系统可以实时显示罐区单元的各种参数和状态,并可以通过控制指令来调整和控制各个设备的运行。
在操作过程中,需要密切关注系统的各种指标和报警信息,并及时采取相应的措施来保证系统的稳定和安全。
此外,进行仿真操作时还需要注意一些事项。
首先,操作人员应具备一定的化工流程和DCS系统的知识和技能,以便能够正确操作和处理各种情况。
其次,操作人员应熟悉罐区单元的操作规程和安全操作规范,确保操作过程的安全和可靠。
最后,操作人员应随时保持警惕,及时响应和处理各种异常情况,确保操作过程的顺利进行。
总结起来,化工仿真DCS罐区单元仿真操作是一种通过模拟和模型技术来模拟化工罐区单元操作的虚拟环境。
罐区计算机控制系统设计与开发

罐区计算机控制系统设计与开发陈再良(湖南长岭炼油化工总厂计算机应用研究所,414012) 摘要:简述了一套由GE FANUC 的System90230与PC 机组成的分散型控制系统。
并且从系统的设计思想、所实现的功能以及系统在油罐区应用的特点进行了较详细的叙述。
关键词:操作站 控制站 罐量计算 事件驱动 网络 随着电子信息技术应用的迅猛发展和工业水平的提高,工业控制对象也变得大型化和复杂化,工业控制规模由局部控制发展到整个生产装置的全过程控制、优化和调度,乃至整个工厂的控制和管理一体化。
本文介绍的罐区计算机控制系统就是为了适应我厂电子信息技术应用发展的要求设计并开发出来的。
1 原系统存在的问题1.1 我厂原罐区计算机控制系统存在的问题1)原系统为国内一家公司首次开发的非标准化I/O 模件,不便于维护。
2)系统只有一级控制,可靠性、安全性都很差,再加之手动也是通过计算机I/O 起作用,计算机万一出故障,手操也起不了作用。
3)系统不具有网络功能,数据不能共享,各个数据采集站各采一部份数据,相互之间没有信息连通,因而罐区实时报表难以实现,各个操作站之间不能互为热备份。
4)系统没有高级语言接口,不便于开发先进控制和复杂控制。
5)系统不易于扩展。
112 新系统开发的原则针对原系统存在的问题及我厂电子信息技术的发展规划,我们在对原系统进行改造时,提出了如下原则:1)改造后的新系统必须满足长远发展的要求,从规模上讲,要能够达到75个罐的控制和管理,因此系统必须便于扩展,软件上必须便于重新组态、开发。
2)系统必须采用局域网结构,同时必须具有与全厂主干网联网的接口。
3)系统必须是二级控制,以保证系统的安全性和可靠性。
4)系统应用软件必须具有高级语言接口功能,便于优化控制程序的开发。
5)人2机界面友好,画面直观,操作简单。
2 系统组成根据上述的原则和罐区使用现场的实际,我们设计并建立了1套如图1所示的油罐区计算机测控管理系统。
中控ECS-700DCS系统在新罐区的应用

周龙生. 中控 E C S一 7 0 0 D C S系统在新 罐区的应 用
3 9
中控 E C S一 7 0 0 D CS 系统 在 新 罐 区的应 用
周 龙生
( 内蒙古 双欣 环保材 料股份 有 限公 司, 内蒙古鄂 尔多斯 0 1 6 0 1 4 )
3 D C S 系统 接 地 要 求
D C S系统 的可靠接 地 是保 证 系统 安全 稳定 运 行 的首 要条 件 , 系统 接地 网络如 图 1 所示。
2 5 mm, 长度根 据 实 际情 况 确 定 , 为 确保 接 地 引 线 连接 可靠牢 固 , 接 地 铜 排 应 直 接 攻 丝 或 连 接螺 丝 相连 , 接地 系统 的接地 应设 置 铜质 接地 片 , 并 采用 铜 质 紧 固件 。 ( 4 ) 现场 仪表 的工 作地 一般 只一侧 接地 , 如个 别 仪表 要求 控 制 室 及 现 场 侧 均 要 求 接地 , 则 必须 采 用 隔离器将 两侧 的接地 隔离 。 ( 5 ) D C S机 柜 、 辅 助 柜 内含有保 护接地 铜排及 工 作接 地铜 排 , 带 有 E标 识 的铜排 为工作 接 地 , 带 有P E标识 的铜 排 为保 护接 地 , 操 作站一 般 只有保
收稿 日期 : 2 0 1 6— 0 7— 2 8 , , 作者简介 : 周龙生 ( 1 9 8 8一) 。 男, 助 理工 程师 , 2 0 1 0年毕 业于
兰州城市学 院。现 任内蒙 古双欣 环保材 料股 份有 限公 司动 力厂 电仪 车间技术员。
《 维纶通讯》
2 0 1 7年 O 6月
人机 界 面性 价 比也较 高 。
2 D CS配置
石油化工罐区自动控制系统和生产管理系统

石油化工罐区自动控制系统和生产管理系统摘要:近年来国内新建的石油化工厂储运罐区的自动化水平已经不仅局限于采用仪表测量加分散型控制系统(DCS),有些厂家还配有罐区生产管理系统。
将罐区的自动控制系统、生产管理系统与工厂信息管理系统结合起来,卓有成效地提高了储运系统的整体自动化水平和管理水平,实现了控制和管理的系统集成、数据共享、功能集成。
关键词:石油化工罐区;罐区自动控制系统;罐区生产管理系统1前言储罐是石油化工企业重要的组成部分,是企业生产、储存和运输过程中基本且重要的环节。
一般具有占地面积广、储存量大和布置密集的特点。
储罐储存的物质通常有易燃易爆、易挥发和有毒等特性,一旦发生泄漏,挥发出的易燃易爆介质遇明火或高温物体,就有可能引发火灾或爆炸事故,故石油化工的罐区大多被划为高危险区域。
作为石油化工储罐实时变化的动态参数,液位连续精确测量是罐区最重要的监控仪表,也是成品计量管理的重要参数。
本文通过对罐区中常用的液位仪表测量方案进行对比分析,从工程设计的角度叙述雷达液位计在罐区储罐液位测量中的设计选型和安装方案。
2储罐类型的选择储罐类型的选择要充分考虑物料特性(火灾危险性、挥发性、毒性、化学稳定性等)、存储温度等各种因素。
储存甲、乙类的液体(该类化学品挥发性通常较大)通常优先选用内浮顶罐。
由于内浮顶罐罐内气体空间较小,可大大降低化工挥发性气体损耗和对大气的污染,并减少储罐着火几率,目前设计上通常采用金属浮舱式浮盘。
对于有特殊要求的甲、乙类液体物料,如甲醛、酯类等易聚合或易氧化的液体物料,选用固定顶储罐加氮封储存;对于沸点低的化学品,可以采用固定顶储罐,并增加外循环降温的措施存储。
或采用外盘管冷却形式,外盘管内通入冷却水或冷冻水。
外循环降温通常利用罐区内送料泵,将送料泵的旁路通过冷却器后再打回到储罐内,这类储罐和管道外部均按保冷设计。
当储罐内存储的介质为甲类液体介质时,要考虑太阳直接照射产生的热量,太阳直接照射会造成储罐顶部局部温度过高,增加了储罐内部挥发性气体挥发量。
- 1、下载文档前请自行甄别文档内容的完整性,平台不提供额外的编辑、内容补充、找答案等附加服务。
- 2、"仅部分预览"的文档,不可在线预览部分如存在完整性等问题,可反馈申请退款(可完整预览的文档不适用该条件!)。
- 3、如文档侵犯您的权益,请联系客服反馈,我们会尽快为您处理(人工客服工作时间:9:00-18:30)。
油品罐区DCS系统改造
一、油品罐区改造前的概况:
西安石化油品罐区共有储罐83台,共设置1#原油罐区、2#原油罐区、3#原油及成品油罐区、中间罐区、零位罐及铁路装卸车、沥青罐区等6个控制室。
现场仪表普遍存在储罐测量、安全仪表不齐全、仪表档次低、部分仪表损坏、故障率高、维护工作量大等问题,存在较大的安全隐患,加上控制室多且分散,浪费人力资源,现场工人的劳动强度很大,给生产和管理带来众多不便,不符合安全生产的要求。
二、改造方案:
针对以上问题,我们对公司油品罐区进行统一规划,将6个分散的小控制室进行整合,设置罐区中心控制室,采用一套国产DCS,设置3个远程现场控制站,1个现场操作站,4个中控室操作站,各远程站、各区域与中控室之间采用光缆连接,光缆敷设沿ERP骨架网敷设,实现对所有储罐的监控。
同时,对现场测量仪表进行部分更新和完善,按照规范要求配全储罐必需有的液位、温度、高低液位报警、可燃气体和有毒气体检测报警器等仪表。
以达到提高劳动生产率、节约人力资源、降低职工劳动强度、消除安全隐患的目标,避免各种生产、安全事故的发生,实现安全生产。
在实施过程中,可以分步实施,根据各个罐区情况,先逐步把各个罐区监控仪表由目前的常规仪表改为DCS远程节点,利用操作站进行监控待罐区中心控制室建好后,在将各罐区仪表信号通过冗余光缆连接到中心控制室DCS上,并将操作站移到中心控制室,实现对所有储罐的集中监控,系统构成详见系统网络配置图。
三、仪表选型:
对沥青罐和零位罐选用雷达液位计,主要考虑雷达液位计:a.非接触式仪表、容易安装、无移动部件、维修量小。
b.精度高、可靠性最高。
c.可适应沥青高粘度、易凝固、温度高,容易挂料的苛刻工艺条件。
d.输出为叠加于HART的4~20mA信号,可将温度信号引入传输。
控制系统选用DCS,主要考虑DCS技术先进成熟,性能可靠,具有冗余功能,操作界面清晰,组态简单,性价比高。
经过设计院推荐、自控专业技术人员讨论、外出考察,并结合分公司实际情况,确定主要仪表选型如下:
1、沥青罐区:液位测量选用SAAB抛物面天线雷达液位计,温度选用铂电阻信号引入雷达液位计;
2、1#、2#原油罐12台罐液位测量选用智能光导液位计,温度选用一体化温度变送器信号引入智能光导液位计;
3、6台零位罐罐液位测量选用SAAB喇叭口天线雷达液位计,温度选用铂电阻信号引入雷达液位计;
4、控制系统选用先进可靠国产的浙大中JX-300XP DCS控制系统;
5、可燃气体报警仪选用深圳特安公司可燃(毒性)气体报警仪。
四、现场施工:
现场施工2008年4月20日开始,由于施工区域太大、现场情况特别复杂,加上储罐内有油,不能影响正常生产,不能在罐区内动火,给施工带来了很大大的困难,根据现场复杂的情况,光缆沿ERP骨架网敷设,罐体上充分利用旧仪表的固定支架,罐区内穿线管采取制作地面支架和制作管卡与管道钢结构连接等固定方式;电缆敷设上充分合理利用原有电缆,减少电缆敷设;罐体上仪表安装,采用倒罐的方式,分部安装;现场施工于2008年6月25日基本结束,经过1个月的调试和试运行,于2008年7月23日正式投用。
五、实施效果:
经过1年多的运行,控制系统和现场仪表运行正常,达到了改造目的。
油品罐区DCS系统改造,将6个分散的小控制室进行整合,设置罐区中心控制室,对分公司所有储罐实现集中监控,降低职工劳动强度,提高了工作效率,全面提高罐区自动化管理水平,为罐区数据信息化打下坚实的基础。
同时,按照规范要求对储罐的液位、温度、高低液位报警、可燃气体和有毒气体检测报警器等仪表进行更新和完善,彻底消除了罐区存在的安全隐患,达到了预期目的。
六、经验和教训
1、要做好统筹和规划。
对于改造项目,应当对现场进行的调研,明确改造后要达到的目标,根据企业实际情况,从长远考虑,制定全面科学合理的规划。
2、根据规划从实用性、可实施性、投资费用等方面,制定实施方案。
3、要对现场情况进行详细的调查,包括在用设备运行情况、区域环境、那些可利旧、设备的规格型号、信号、通讯协议等,做到心中有数,以免信号不匹配及无法施工的问题。
4、在设备选型时,要根据工艺条件,选择有实际使用业绩的测量和控制仪表,以保证所选设备能正常投用。
5、在实施中,要认真组织施工,根据不同的现场情况,制定相应的施工方案,保证施工质量和施工进度。
陈化民
2009.10.3。