MANAGEMENT_CH18_QB
戴尔显示管理器用户指南说明书
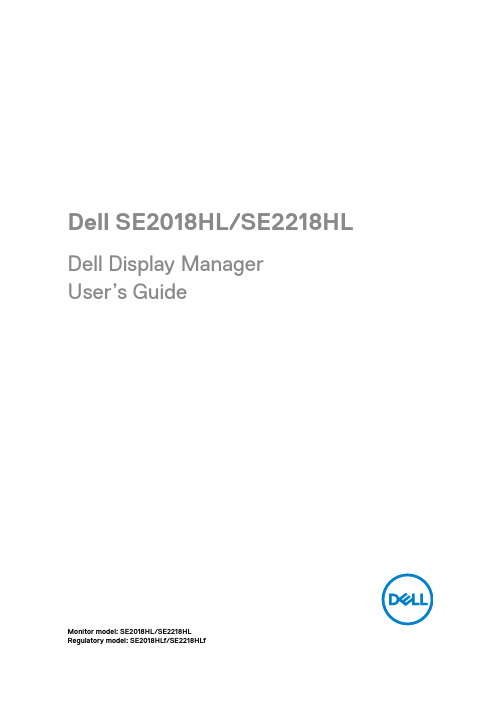
Dell SE2018HL/SE2218HL Dell Display ManagerUser’s GuideMonitor model: SE2018HL/SE2218HLRegulatory model: SE2018HLf/SE2218HLfNOTE: A NOTE indicates important information that helps you makebetter use of your computer.© 2020 Dell Inc. or its subsidiaries. All rights reserved.Dell, EMC, and other trademarks are trademarks of Dell Inc. or its subsidiaries. Other trademarks may be trademarks of their respective owners. 2020 - 01Rev. A002 │ContentsOverview (4)Using the Quick Settings Dialog (5)Setting Basic Display Functions (6)Assigning Preset Modes to Applications (7)Organizing Windows with Easy Arrange (8)Restoring Application Positions (10)Applying Energy Conservation Features (12)Troubleshooting (13)Contents │ 3OverviewDell Display Manager is a Microsoft Windows application used to manage a monitor or a group of monitors. It enables manual adjustment of the displayed image, assignment of automatic settings, energy management, window organization, image rotation, and other features on selected Dell monitors. After installation, Dell Display Manager runs each time the system starts and places its icon in the notification tray. Information about monitors connected to the system is available when hovering over the notification tray icon.NOTE: Dell Display Manager uses DDC/CI channel to communicate withyour monitor. Ensure that DDC/CI is enabled in the menu as below.4 │ OverviewUsing the Quick Settings DialogClick the Dell Display Manager’s notification tray icon to open the Quick Settings dialog box. When more than one supported Dell model is connected to the computer, a specific target monitor can be selected using the menu. The Quick Settings dialog box enables convenient adjustment of the monitor’s brightness and contrast levels. You can select Manual Mode or Auto Mode, and the screen resolution can be changed.SE2018HL/SE2218HLThe Quick Settings dialog box also provides access to Dell Display Manager's advanced user interface that is used to adjust basic functions, configure auto mode and access other features.Using the Quick Settings Dialog │ 56 │ Setting Basic Display FunctionsNOTE: When multiple Dell monitors are connected, select “Enable display matrix control” to apply brightness, contrast and color presets controls toall monitors.Setting Basic Display FunctionsYou can select Manual Mode that enables you to manually select a preset mode or select Auto Mode that applies a preset mode based on the active application. An on-screen message displays the current preset mode whenever it changes. The selected monitor's Brightness and Contrast can also be directly adjusted from the Basic tab.SE2018HL/SE2218HL SE2018HL/SE2218HLAssigning Preset Modes to Applications │ 7NOTE: Preset Mode assignments for batch files scripts, loaders, and non-executable files such as zip archives or packed files, are not supported.Assigning Preset Modes to ApplicationsThe Auto Mode tab allows you to associate a specific Preset Mode with a specific application, and apply it automatically. When Auto Mode is enabled, Dell Display Manager automatically switches to the corresponding Preset Mode whenever the associated application is activated. The Preset Mode assigned to a particular application may be the same on each connected monitor, or it can vary from one monitor to another.Dell Display Manager is pre-configured for many popular applications. To add a new application to the assignment list, simply drag the application from the desktop, Windows Start Menu or elsewhere, and drop it onto the current list.SE2018HL/SE2218HLOrganizing Windows with Easy Arrange Easy Arrange helps you to effectively organize your application windows on the desktop. You first choose a pre-defined layout pattern which suits your work, then you just need to drag the application windows into the defined zones. Press “>”or use Page Up/Page Down key to find more layouts. To create a custom layout, arrange the open windows and then click Save.SE2018HL/SE2218HLFor Windows 10, you can apply different window layouts for each of the virtual desktops.If you often use Windows snap feature, select the “Hold down the SHIFT key to enable zone positioning”. This gives Windows snap priority over Easy Arrange. You will then need to press the Shift key to use Easy Arrange positioning.8 │ Organizing Windows with Easy ArrangeSE2018HL/SE2218HLIf you are using multiple monitors in an array or matrix, Easy Arrange layout can be applied across to all the monitors as one desktop. Select “Span multiple monitors” to enable this feature. You need to align your monitors properly to use it effectively.SE2018HL/SE2218HLOrganizing Windows with Easy Arrange │ 910 │ Restoring Application Positions Restoring Application PositionsDDM can help you restore application windows into their positions when youreconnect your computer to the monitor(s). You can quickly access this feature by right-clicking on DDM icon in the notification tray.If you choose “Auto-restore window layout ”, your application windows' positions are tracked and remembered by DDM. DDM automatically puts the application windows into their original positions when you reconnect your PC to your monitor(s).If you want to go back to a favorite layout after you have moved the application windows around, you can first “Save current window layout ” and later “Restore saved window layout”.You may use monitors with different models or resolutions in your daily routine, and you may apply different window layouts on them. DDM is able to know the monitor you have reconnected and restore application positions accordingly.In case you need to replace a monitor in a monitor matrix configuration, you can save the window layout before replacement and restore the layout after a new monitor is installed.NOTE: You should keep your applications running in order to benefit fromthis feature. DDM does not launch applications.Restoring Application Positions │ 11Applying Energy Conservation Features On supported Dell models, an Options tab is available that provides PowerNap energy conservation options. You can choose to set the monitor's brightness to the minimum level, or to put the monitor to sleep when the screensaver is activated.SE2018HL/SE2218HL12 │ Applying Energy Conservation FeaturesTroubleshooting │ 13TroubleshootingIf DDM does not work with your monitor, DDM will show below icon in your notification tray.Please note that DDM only works with Dell branded monitors. If you are using monitors from other manufacturers, DDM does not support them.If DDM is unable to detect and/or communicate with a supported Dell monitor, please take below actions to troubleshoot:Make sure the video cable is properly connected between your monitor and your computer. Ensure the connectors are firmly inserted into position.Check the monitor OSD to ensure DDC/CI is enabled.Make sure you have the right graphics card driver from the vendor (Intel, AMD, NVIDIA, etc.). Graphics driver is often the cause of DDM failure.Remove any docking stations, cable extenders, and converters between the monitor and the graphics port. Some low-cost extenders, hubs or converters may not support DDC/CI properly and can fail DDM. Update the driver of such device if the latest version is available.Restart your computer.Click on the icon, DDMshows a more detailed error message.1.2.3.4.5.DDM may not work with below monitors:Dell monitor models that shipped earlier than 2013 and D-series of Dellmonitors. For more information see /support/monitors.Gaming monitors using Nvidia-based G-sync technology.Virtual and wireless displays do not support DDC/CI.Some early models of DP 1.2 monitors, it may be necessary to disableMST/DP 1.2 using the monitor OSD.If your computer is connected to the Internet, you will be prompted to upgrade to a new version of DDM when it is available. It is recommended to download and install the latest DDM application.You may also check for new version by right clicking on DDM icon while pressing and holding 'shift' key.14 │Applying Energy Conservation Features。
戴尔机箱管理控制器(CMC)版本2.0适用于戴尔PowerEdge VRTX发行说明说明书
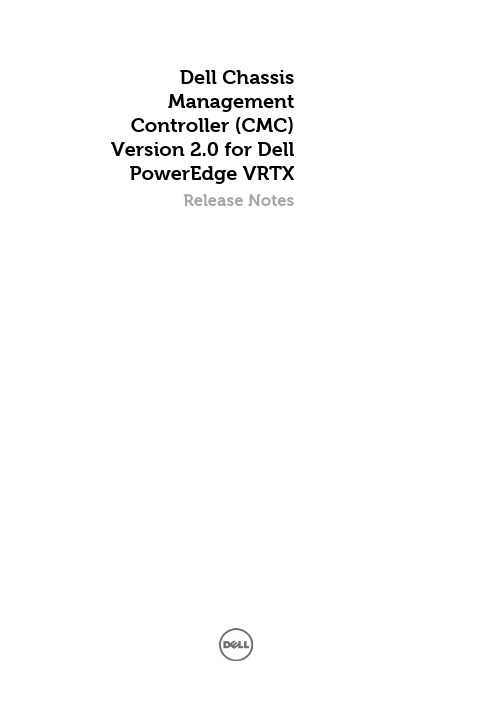
Dell ChassisManagement Controller (CMC) Version 2.0 for Dell PowerEdge VRTXRelease NotesRelease Type and DefinitionThe Dell Chassis Management Controller (CMC) Version 1.35 for Dell PowerEdge VRTX is aSystem Management hardware and software solution for managing the Dell PowerEdge VRTXchassis.Version2.0Release DateDecember 2014Previous Version1.36ImportanceRECOMMENDED: Dell recommends applying this update during your next scheduled updatecycle. The update contains feature enhancements or changes that will help keep your systemsoftware current.Platform(s) AffectedDell Chassis Management Controller (CMC) for Dell PowerEdge VRTX is supported on thefollowing system:•PowerEdge VRTXWhat is Supported?License RequirementsThe CMC supports software licensing to use advanced systems management features. For more information about the license requirements, see the Dell Chassis Management Controller for Dell VRTX User's Guide available at the support site.Supported Web Browsers for CMC for Dell PowerEdge VRTX •Microsoft Internet Explorer 9•Microsoft Internet Explorer 10•Microsoft Internet Explorer 11•Safari version 6.0•Safari version 7.0•Mozilla Firefox version 29•Mozilla Firefox version 30•Google Chrome version 33•Google Chrome version 34Supported platformsM630, M520, M620, and M820 serversSupported Server Modules•Mainboard firmware: 2.00 or later•iDRAC7 Version: 1.66.56 or later•iDRAC8 Version: 2.05.05 or later (M630 Servers)•PowerEdge M520 BIOS Version: 2.1.3 or later•PowerEdge M620 BIOS Version: 2.2.7 or later•PowerEdge M820 BIOS Version: 2.0.24 or later•PowerEdge M820 BIOS Version: 0.3.35 or laterWhat’s New?Release 2.0•13th generation M630 Blade Server enablement for VRTX Chassis.•1600W PSU support.•Broadcom 1GE quad-port NDC supported on M630 for VRTX Chassis.•Emulex ARI NDC and Mezzanine cards support on M630 for VRTX Chassis.•Intel 1G and NDC support on M630 for VRTX Chassis.•Option to use an external library (CIFS/NFS directory created by the sysadmin) for update repositories and profiles.•Option to see and use captured profiles stored on an external library.•Assign a profile in a library to a slot for Quick Deploy of Profiles.•13G COMMs card Firmware and Driver Refresh.•ARI support for COMMs Cards.•IO identity Feature support.•CMC signed image firmware update verification.FixesRelease 1.36•Fixed an issue in the CMC graphical user interface to allow editing a virtual disks policy while in Fault Tolerant (dual PERC) mode.Release 1.35•Fixed an issue in RACADM related to alert event filter configuration.•Fixed an issue in CMC web interface related to Chassis OverView-> Alerts->Chassis Events page. The Chassis Events page was not loading on the web interface due to certain alertconfiguration settings that were not working with the following filters: System-SEC-Warning,Audit-LIC-Critical, Audit-LIC-Warning and Audit-LIC-Informational. This issue has been fixed in this Release.Note: After updating to CMC 1.35 firmware version, verify the CMC alert configuration settings on the Chassis Event's page.Release 1.31•Occasional occurrences of older chassis log messages related to storage.Release 1.30•Telnet and SSH access issues with VLAN enabled.•SNMP walk when traversing certain OIDs.•PK authentication public key upload issue.•Time zone setting in CMC graphical user interface. Fixed an issue in RACADM related to alert event filter configuration.Important Notes•It is recommended not to downgrade CMC or Mainboard firmware below the supported versions mentioned in this release notes, since previous versions of CMC and Mainboard do not support SPERC disable option.•When the second SPERC is in the disabled mode, if a CMC with firmware version 1.30 or 1.31 is inserted into the chassis, then update the CMC firmware to 1.35 and run the options to disablethe PERC again.•The shared hard disk drives (HDDs) and PCIe cards are managed by the CMC and are not visible to the operating system in the server modules, until the HDDs and PCIe cards are mapped byusing the CMC web interface. For instructions about mapping PCIe cards and managing thestorage subsystem, see the Chassis Management Controller for PowerEdge VRTX User's Guideavailable at the support site.•All the server modules must be turned off before updating the firmware for chassis infrastructure and SPERC. CMC firmware can be updated while the servers are turned on.•Some advanced features require CMC enterprise license. For more information about the CMC licenses, see the Chassis Management Controller for PowerEdge VRTX Version User's Guideavailable at the support site.•Before updating the storage component using the web interface, make sure that the browser’s Cookies are enabled.•PERC storage rebuild may take more time when more number of I/O requests are processed, and could also make CMC and the TTY log to be out of sync for a short period of time.•In fault-tolerant (Redundant) mode, the controller associated with virtual disks or physical disk drives is the active controller.•When saving Server Profile under "Server Overview > Setup > Profiles", the list of characters that are not supported for the Profile Name include the characters hash(#), comma(,), and question mark(?).•You may see an impact in the performance of the Graphical User Interface with this release of CMC. The performance impact varies by configuration, GUI page, and system load.Known IssuesIssue 1:DescriptionXWKGY_Intel10G card shows Flex disabled address after racresetcfg of CMC in Network Device Page and OS.ResolutionVirtual reseat or Physical reseat of the server.Versions/Systems AffectedAll CMC versions including CMC 2.0 for Dell PowerEdge VRTX and PowerEdge servers withiDRAC7 or earlier.Issue 2:DescriptionIo-Identity values are displayed partially in the cmc getmacaddress -c all for 8F6NV(Intel).ResolutionNoneVersions/Systems AffectedCMC 2.0 for Dell PowerEdge VRTX and servers with Intel adapetrs Intel(R) 10G 2P X520-k bNDC and Intel 10GbE/FCoE Dual KR X-520.Issue 3:DescriptionRACADM displays non ISCI MAC addresses after using ISCI filter in “getmacaddress –m server-x –t iscsi” command.ResolutionNoneVersions/Systems AffectedAll CMC versions including CMC 2.0 for Dell PowerEdge VRTX.Issue 4:DescriptionVLAN settings from the leader chassis are not propagating to member chassis.ResolutionLogin to each member chassis CMC GUI and set the VLAN for iDRAC (Server Overview -> Setup -> VLAN page).Versions/Systems AffectedAll CMC versions including CMC 2.0 for Dell PowerEdge VRTX and PowerEdge servers withiDRAC7 or earlier.Issue 5:DescriptionAfter Shared PERC8 controller update, RAID related operations may take longer to report status..ResolutionWait for the operation status to report.Versions/Systems AffectedCMC version 2.0 for Dell PowerEdge VRTX.LimitationsNone for this release.InstallationPrerequisitesBefore setting up your CMC environment, download the latest version of CMC firmware forPowerEdge VRTX from the Dell Support Website at /support/. Also, make sure that you have the Dell Systems Management Tools and Documentation DVD that is included with yoursystem.Installation Procedure1.In the CMC web interface, click Chassis Overview, and then click Update.2.On the Firmware Update page, in the CMC Firmware section, select the required componentsunder the Update Targets column for the CMC or CMCs (if a standby CMC is present) you want to update, and then click Apply CMC Update.3.In the Firmware Image box, type the path to the firmware image file on the management stationor shared network, or click Browse to browse through to the file location. The default name ofthe CMC firmware image file is vrtx_cmc.bin.4.Click Begin Firmware Update, and then click Yes. The Firmware Update Progress sectiondisplays information about the firmware update status.For more information, see the Chassis Management Controller for PowerEdge VRTX User'sGuide available at the support site.VRTX Update ProcedurePrerequisites•iDRAC web interface for each server node must be accessible from management station.•Local or remote access to OS management for each server node.•VRTX chassis CMC web interface must be accessible from management station.•All server and chassis components must be in a Healthy state with no outstanding issues or alerts. Any issues must be resolved prior to performing updates.Server Node UpdatesVisit and download the latest available Windows DUP versions of the following programmable components for the server node model (M520, M620, M630 or M820) used in the VRTX chassis to be updated:•BIOS•iDRAC7/8•CPLDAlso, download the latest available Shared PERC8 driver for the operating system installed on the server node.Note: If the OS is VMWare ESXi, the driver is part of the Dell ESXi image.Updating the Server Nodes1)Update the operating system-specific Shared PERC8 driver on all the server nodes. For Windowsoperating system, see the Shared PERC8 User’s Guide available at . For VMware, the driver is part of the Dell-customized ESXi image. For more information, see installing async drivers at .2)Update the iDRAC firmware using Windows DUP and the iDRAC web interface for each servernode or on all server nodes at once through VRTX CMC web interface if Enterprise license is in place and the Extended Storage feature is enabled. This update takes several minutes tocomplete. After the update, iDRAC web interface is inaccessible for approximately 3 minutes.3)Update the CPLD on each server node using the Windows DUP and iDRAC web interface. Makesure to select “Install and Reboot” after uploading the DUP, which forces the server nodes to reboot and perform the CPLD update. After the CPLD update completes a complete server node power cycle occurs. This action results in the iDRAC web interface being inaccessible forapproximately three minutes.4)Update the BIOS on each server node using Windows DUP and the iDRAC web interface, or onall server nodes at once through the VRTX CMC web interface (Server Overview -> Update tab) if Enterprise license is in place. Make sure to select “Install and Reboot” after uploading the DUP, which forces the server nodes to reboot and execute the BIOS update.VRTX Chassis Component UpdatesVisit and download the latest available versions of the followingprogrammable components for the VRTX chassis to be updated:•CMC Firmware•HDD Firmware (Windows DUP)•Shared PERC8 Firmware (Windows DUP)•VRTX Chassis Infrastructure Firmware•VRTX Storage Backplane Expander Firmware (Windows DUP)Updating VRTX Chassis Components1)Before updating any chassis components, the chassis must be powered on, all server nodes mustbe powered down, and remain powered down until all chassis component updates are complete.2)Update the HDD firmware for each of the installed shared storage HDD, using the Storage ->Update tab in the CMC web interface.3)Update the CMC firmware using the Chassis Overview -> Update tab in the CMC web interface.Make sure to update both CMC controllers in the same operation by selecting both the Active and Standby controller checkboxes. After the firmware upload completes, the CMC is rebooted to perform the update resulting in the CMC web interface being inaccessible for several minutes.4)Update the VRTX chassis infrastructure firmware using the Chassis Overview -> Update tab inthe CMC web interface. This update results in the chassis power cycling automatically and may result in a CMC controller reset as well. As e result, the CMC web interface becomes inaccessible for several minutes.5)Update the VRTX storage backplane expander firmware using the Storage -> Update tab in theCMC web interface.6)Verify that all installed Shared PERC8 controllers are enabled by checking the Storage ->Controllers tab in the CMC web interface. If the second Shared PERC8 controller is displayed as “Disabled PERC (Integrated 2)”, use the CMC command:‘racadm raid enableperc:RAID.ChassisIntegrated.2-1’ to enable the previously disabled controller prior to performing Step 7 below. The VRTX chassis power cycles after the SharedPERC8 enablement command is run.7)Update the Shared PERC8 controller firmware on all installed controllers using the Storage ->Update tab in the CMC web interface. Make sure to update both controllers in the HighAvailability Dual Shared PERC8 configuration in the same operation.8)If a Shared PERC8 controller was required to be enabled for update in Step 6 above, you candisable the controller again if required. Use the CMC command ‘racadm raiddisableperc:Raid.ChassisIntegrated.2-1’. This command results in a chassis power cycle. Contacting DellNote: If you do not have an active Internet connection, you can find contact information on your purchase invoice, packing slip, bill, or Dell product catalog.Dell provides several online and telephone-based support and service options. Availability varies by country and product, and some services may not be available in your area. To contact Dell for sales, technical support, or customer service issues:1.Visit /support.2.Select your support category.3.Verify your country or region in the Choose a Country/Region drop-down menu at the top ofpage.4.Select the appropriate service or support link based on your need.For information about documentation support:1.Go to /support/manuals2.In the Tell us about your Dell system section, under No, select Choose from a list of all Dellproducts and click Continue.3.In the Select your product type section, click Software & Security.4.In the Choose your Dell Software section, click the required link from the following:–Client System Management–Enterprise System Management–Remote Enterprise System Management–Serviceability Tools5.To view the document, click the required product version.Note: You can also directly access the documents using the following links:o For Client System Management documents — /OMConnectionsCliento For Enterprise System Management documents — /openmanagemanualso For Remote Enterprise System Management documents — /esmmanualso For Serviceability Tools documents — /serviceabilitytoolsAccessing Documents From Dell Support SiteTo access the documents from Dell Support site:1.Go to /support/manuals.2.In the Tell us about your Dell system section, under No, select Choose from a list of all Dell products andclick Continue.3.In the Select your product type section, click Software, Monitors, Electronics & Peripherals.4.In the Choose your Dell Software, Monitors, Electronics & Peripherals section, click Software.5.In the Choose your Dell Software section, click the required link from the following:•Client System Management•Enterprise System Management•Remote Enterprise System Management•Serviceability Tools6. To view the document, click the required product version.You can also directly access the documents using the following links:•For Client System Management documents — /OMConnectionsClient•For Enterprise System Management documents — /openmanagemanuals•For Remote Enterprise System Management documents — /esmmanualsFor Serviceability Tools documents — /serviceabilitytoolsInformation in this document is subject to change without notice.© 2014 Dell Inc. All rights reserved.Reproduction of these materials in any manner whatsoever without the written permission of Dell Inc. is strictly forbidden. Trademarks used in this text:Dell(TM), the DELL logo, PowerEdge(TM), PowerVault(TM), Compellent(TM) and OpenManage(TM) are trademarks of Dell Inc. Intel(R) is a registered trademark of Intel Corporation in the U.S. and other countries. Microsoft(R), Windows(R), Windows Server(R), Internet Explorer(R), Hyper-V(R), Active Directory(R), ActiveX(R) and Windows Vista(R) are trademarks or registered trademarks of Microsoft Corporation in the United States and/or other countries. Red Hat Enterprise Linux(R) and Enterprise Linux(R) are registered trademarks of Red Hat, Inc. in the United States and/or other countries. The term Linux(R) is a registered trademark of Linus Torvalds, the original author of the Linux kernel. SUSE(TM) is a trademark of Novell Inc. in the United States and other countries. XenServer(R) is a registered trademark of Citrix Systems, Inc. in the United States and/or other countries. Mozilla(R) and Firefox(R) are registered trademarks of Mozilla Foundation. VMware(R) and ESX(TM) are registered trademarks or trademarks of VMware, Inc. in the United States and/or other jurisdictions. Java(TM) is a registered trademark of Oracle and/or its affiliates. Google(R) and Chrome(TM) is a trademark of Google Inc. Mac(R), Macintosh(R), and Mac OS(R), Safari(R), and OS X(R) are trademarks of Apple Inc., registered in the U.S. and other countries. Matrox(R) is a registered trademark of Matrox.Other trademarks and trade names may be used in this publication to refer to either the entities claiming the marks and names or their products. Dell Inc. disclaims any proprietary interest in trademarks and trade names other than its own.。
适用于 HP-UX 的 HP Systems Insight Manager 6.0 安装与配置指南
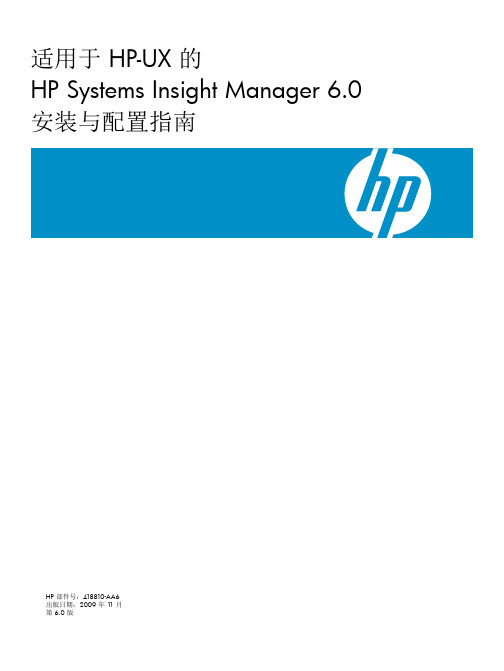
LB Management智能灯泡控制系统用户手册说明书
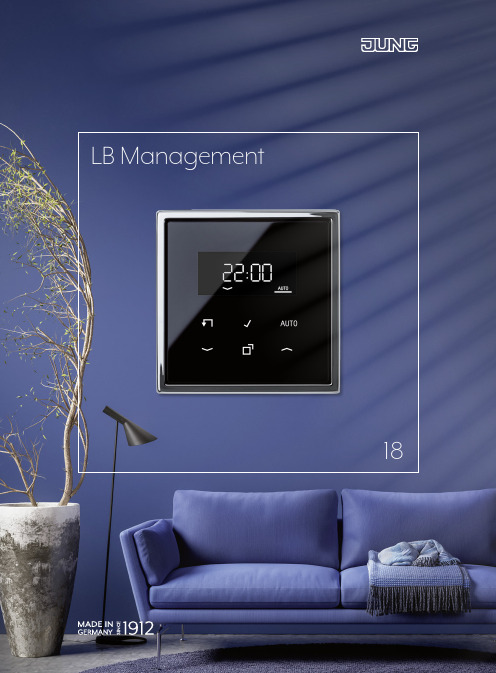
LB Management18CONTENTS The new LB Management 02Overview of the advantages 04In use: Single family house 06In use: Office building 08The controls 10The inserts 11Operation in switch design 12With the press of a button 14The Standard timer 16The Universal timer Bluetooth 20The Clever Config app 22Simply illuminating 24The automatic switches 26The motion and presence detector 28Dimming expertise 30LB Management workbook 3216 Timer with added convenience 26 Control light automatically 04An overview of all advantages22The Clever Config app 1The new LB ManagementThe installation is designed for tradespeople. For example, the small installation depth of only 24 mm (DALI insert 29 mm) creates more space for the wiring. A stable supporting plate in steel, the enclosed mounting claws and increased claw pull-out forces provide a firm hold and optimum alignment in the flush-wall box. In addition, satellites can be connected. Test operation at the site is also possible without a cover. The integrated test button, with which different operating modes can be set, shortens the installation time. The covers are simply pushed on with the help of stable retaining springs in stainless steel. During the installation, the integrated signalling by means of LED or display ensures that no unintended confusion occurs when allocating insert and cover.Out of the JUNG light and blinds management has come theLB Management. With the combination of different inserts andcovers, the modular system provides a solution for virtuallyevery desired function for light and shading control. Whenretrofitting installations, individual components (always insertplus cover) can also be exchanged for new ones from the LB Management and the others can continue to be used.Characteristics are the simple installation and commissioning, the possibility for retrofitting of existing installations andconvenient operation.Overview of the advantagesThe modular principle of the LB Management offers clearadvantages not only for tradespeople but also for ownersand modernisers.1 “Hands-free lighting” with automatic switches: practical and energy-saving 2Alarm function: blinking light for motion detection 3 Automatic light in the guest bathroom: no searching for the light switch 4 Lighting control with satellite unit: extension by operating element 5 Lock-out prevention: deactivation of the automatic shutter control at the press of a button 6 Shading complete areas: shutter control in groups by room, floor or house 7 Astro function: shade a living room with a timer and based on sun positionThe description of these scenarios, withcircuit diagrams and parts list can be foundIn use: Single familyIn private building, the LB Management provides more convenience and energy efficiency with control of light and shadingaccording to need. Daily routines are made easier with automaticfunctions. Individual settings and variable operating possibilities improve living quality.75443126666 76In use: Office buildingIn commercial construction such as office buildings, with the LB Management, the working conditions are optimised in a simple manner. Automatic functions provide more security and convenience here. With constant light regulation, the energy efficiency is increased in addition.1Daylight-linked lightingcontrol in the entrance area:safe and economical2Automatic stairwell light:automatic switches provide safety,also for retrofitting3In the meeting room: always theright light with light and shadingcontrol matched to your needs4Constant light function in the office:optimum illumination with a combinationof presence detectors and DALI push-button controls5Semi-automatic lighting with energy-saving function through appropriate delay times:ideal for small kitchens or server roomsThe description of these scenarios, withcircuit diagrams and parts list can be found532544431 2198STANDARD TIMER WITH DISPLAYThe Standard timer is a 1-channel timer for all inserts. The high-quality,real glass surface has an illuminated display and six sensor buttonsfor operation. The current time can be saved as the switching timeusing fast programming. The locking function deactivates automaticfunctions, satellites and timer programmes. Thanks to the astrofunction , switching times are adapted to the position of the sun.UNIVERSAL CENTRE PLATEThe Universal centre plate with memory and locking function is suit-able for almost all LB Management inserts. A coloured LED is assignedto each rocker half and is used for the function and status display.Opera t ion is performed manually or automatically. The cover forthe automatic shading control is available with appropriate arrow symbols.UNIVERSAL TIMER BLUETOOTHThe Universal timer Bluetooth is an attachment forall inserts for light and shading control. Operationcan be manual with the two rockers or with a smart-phone using the Clever Config app. Colour LEDs forthe display of functions and appropriate buttonprinting optimise operation.The controlsThe inserts LIGHT INSERTS BLIND INSERTS STANDARD CENTRE PLATEThe Standard centre plate is an attachment for all LB Managementinserts. Operation of light and shade is manual. The button can beactuated at the top, bottom and also full surface. The centre plateis available with or without symbols.11Operation in switch designThe controls in the LB Management are all available in the multifaceted JUNG design. As a result, they convince not only with their intuitive operating philosophy, but also with respect to form, colour and material.Without symbols for lighting control Left button without symbols for lighting control“Standard” and “Universal” centre plates, depending on the combined insert, light or shading is controlled manually with the press of a button. The universal design has additional convenience functions. For example, the upper right button (lock symbol) can activate the locking function for all automatic functions and the memory function. Alongside two switching times, a ventilation position for the shutter can also be stored. Thanks to appropriate symbols, operation is self-explanatory.With the press of a buttonThe Standard timerReal glass front in black or white with six sensor buttons forintuitive operation – these are the striking characteristics ofthe Standard timer with illuminated display. In this way, theautomatic control of light and shading becomes particularlyconvenient.SWITCHING TIMESThe Standard timer has two week blocks: fromMonday – Friday and from Saturday – Sunday.For both, time switching for light (4 times) or shade(2 times) can be programmed.ASTRO FUNCTIONThe astro function controls light and shadedepending on sunrise and sunset.SUMMER/WINTER CLOCK CHANGEThe change from summer to winter time and backis automatic. In the process, switching times arechanged accordingly.LOCK-OUT PREVENTIONProtection against being locked out: if the lockingfunction is activated, this is shown clearly on thedisplay .The display switches off automatically aftertwo minutes or a continuous display of thecurrent time is possible . The current time canbe saved as the switching time using fastprogramming . The next blind movementtime or switching time is shown on the display.The integrated Astro function, automaticsummer/winter clock change and a lockingfunction are also included.The Universal timer Bluetooth impresses above all with its operating concept. The opera t ion and parametrisation are carried out both mechanically with button presses and mobile with a smartphone with the Clever Config app. The combination with the brightness/temperature sensor allows auto m atic shade or light control based on sun position. With Bluetooth Low Energy, connecting and data transmission are parti-cularly convenient and secure.UNIVERSAL TIMER BLUETOOTHBrightness andtemperature sensorCREATING A CONNECTION Connecting the app with the LB Management device uses Bluetooth Low Energy. After a successful scan, the devices found are displayed in a clear list. The respective device configurations can then be transferred to the app.SIMPLE SET-UPThe connected devices can now be assigned to rooms and given a name, which simplifies allocation during opera t ion. In the “Parameters” menu point, the device settings can then be individualised as desired or simply copied from devices already stored.TIMER SETTINGAutomatically running timer pro-grammes: creating timer controls for the LB Management is as simple as the alarm on a smartphone. In this way, the respective device is switched on or off or switched to a different status, e. g. “Illumination dimmed 40 %”.ACCORDING TO SUN POSITION As well as programming by time, the sequences can also be set with the astro function dependent on the sun position. In the course of the year, the times for the blinds/shutters moving out and in, and the switching on and off of the light, adapt to the changing sunrise and sunset times.The Clever Config appMore information on the settings for the Clever Config app can be found in the LB Management workbook.MORE SECURITYDevice configuration and device pair-ing can be locked with a password and thus protected from unwanted access. The pairing mode can also be protected so that the device cannot be operated with the app by other people.OPERATION MADE EASYWith one finger tip, the lighting is switched on or off or the illumination is dimmed to the desired brightness. Blinds and shutters are moved out or in or into the desired position. Eventhe louvre angle can be simply set.2322Simply illuminatingLight according to your mood, light on demand – with the components of the LB Management you get more convenience and energy efficiency for your illumination control . Very easy with automatic switches, presence detectors and dimmers.The automatic switchesThe 180° detection range of the automatic switches is monitored by two PIR sensors that can be used individually or together. In the function as movement detector, they are ideal to use in corridors and passages. The 2.20 mversion can be used very well in offices or recreation rooms. The settings in the universal designs are conveniently made using the Clever Config app.Automatic LightThe automatic switches 1.10 m and 2.20 m for illumination control based on movement.Settings using Clever Config appEach of the three PIR sensors is allocated an individually activated area of 120° detection angle. By grouping up to five devices, the detec t ion area can be extended. In its role as a presence detector, the compact device auto m atically provides, for example, energy- saving lighting of the work area in an office. In corridors and hallways on the other hand, the motion detector demonstrates its strengths. The device has a 360° detection area with a radius of 20 metres – assuming an installation height of three metres. The device has a pres-ence, night light, alarm and hotel function as well as constant light control.You can rely on the detection characteristics of the motion/ presence detector. When installed at heights of up to six metres, the unit registers everything that is moving within a diameter of approx. 20 m. For this, the device has three PIR sensors operating independently of each other. All settings are made conveniently using the Clever Config app.Settings usingClever Config app29ROTARY DIMMER/POWER DALI POTENTIOMETER The Standard and Universal rotary dimmers work according to the leading edge phase control or trailing edge phase control principle. Setting the device to the dimming principle that matches the respective consumer is done automatically or also manually for the universal design. A coloured LED indicates the selected operating mode. The Power DALI potentio m eter insert operates lamps with DALI interface, including colour temperature control (tunable white).UNIVERSAL DIMMER FOR RAIL MOUNTING LED/ POWER AMPLIFIERThe dimmer version for the distribution also works according to the leading edge phase control or trailing edge phase control principle. The dimmer for rail mounting is operated via a 2-wire or 3-wire satellite unit or with a button with make contact. The power amplifier LED is used as a capacity expan s ion for spreading larger loads for the LB Management dimmers.MINI UNIVERSAL DIMMER LEDThe compact dimmer is suitable for installation in standard flush-mounting boxes. The operation of all common lamps is then carried out via a 2-wire satellite unit, rotary satellite unit or a button with make contact. The dimmer mini also uses the leading edge phase control or trailing edge phase control principle.LB Management workbookCONTROL VERSIONSThe various possibilities for controlling light and shade described in detail and clearly presented. Including use cases, concrete advantages and notes on connection versions.WIRING DIAGRAMSFrom simple installation of the individual components to complex installations with multiple satellite units or group switching, the descriptions in the work-book are always provided with concrete wiring diagrams.COMMISSIONINGCommissioning and parametrisation of the individual LB Management devices are also explained and illustrated. In this way, the installer can become familiar with the work in advance or also refer to specific areas on location at the site.The handbook for the electrical installer: With the LB Management workbook, the professional has all the information on the modular system in the hand. From the individual building blocks to functions and application examples to concrete wiring diagrams – all the valuable information in an overview.1710 DEStandard touch dimmer insert LED1711 DEUniversal touch dimmer insert LED1708 IEPulse insert1713 DSTEPower DALI push-buttoncontroller TW1704 ESEElectronic switch insert 1-channel1733 DNERotary satellite insert 3-wireULZ 1755 REGAmplifier LEDUD 1755 REGUniversal dimmer LED1720 NESatellite insert 2-wireLi ght1701 SERelay switch insert 1-channel1723 NESatellite insert 3-wire Light ManagementLight ManagementLB ManagementLB ManagementOverview reference numbers1730 DDStandard rotary dimmer LED 1731 DDUniversal rotary dimmer LEDL it1240 STEPush-button controller1202 URERelay switch insert 2-channel 1224 LEDUDELED universal touch dimmer insert 1225 SDEStandard touch dimmer insert 1208 UI Pulse unit1254 TSETRONIC switch insert 1201-1 URERelay switch insert with floating contact 1252 UDEUniversal 2-gang dimmer insert 1244 NVSELV triac switch insert1220 NESatellite insert “2-wire”1201 URERelay switch insert 1-channel 201 TETimer switch insert1223 NESatellite insert “3-wire”254 NIE1Satellite rotary dimmer insert1730 JEStandard blinds insert 1731 JEUniversal blinds insert B l i n d Blinds ManagementLB Management230 MEMotor control insert 232 MEMotor control insert 32 SDSunlight/dawn sensorULZ 1215 REGUniversal amplifier for rail mountingUD 1255 REGUniversal dimmer for rail mounting225 NVDERotary dimmer insert 225 TDETRONIC rotary dimmer 266 GDERotary dimmer insert 254 UDIE1Universal rotary dimmer insertBlind Blinds ManagementAS rangeBlinds ManagementA rangeCD rangeLB Management LB ManagementA 5232 S..Centre plate with sensor connectionA 5232 T3..Centre plate with timer functionuniversalA 5232 TS3..Centre plate with timer functionuniversalA 5232..Centre plate standardAS 5232 MS..Centre plate with memory functionAS 5232 MS..Centre plate with memory functionAS 5232..Centre plate standardA 5232 BF..Centre plate standardA 5232 BFMS..Centre plate with memory functionA 5232 MS..Centre plate with memory functionA 5232 MS..Centre plate with memory functionBliA 5232 T3..Centre plate with timer functionuniversalA 5232 TS3..Centre plate with timer functionuniversalA 5232 ST..Centre plate with timer functionstandardCD 5232 ST..Centre plate with timer functionstandardCD 5232 TS3..Centre plate with timer functionuniversal and sensor connectionCD 5232..Centre plate standardCD 5232 MS..Centre plate with memory functionCD 5232 MS..Centre plate with memory functionCD 5232 S..Centre plate with sensor connectionCD 5232 T3..Centre plate with timer functionuniversalA 5232 BFMS..Centre plate with memory functionA 5232 BFS..Centre plate with sensor connectionL i g h tLight ManagementLB Management..5201 DTST..Standard timer switch..5201 DTU..Universal timer switch A 1561.07 BF..Standard centre plate..1561.07..Standard centre plate ..1561.07 U..Universal centre plate A 5201 DTST..Standard timer switchCD 5201 DTST..Standard timer switchCD 5201 DTU..Universal timer switch CD 1561.07..Standard centre plate CD 1561.07U..Universal centre plateA 1561.07U..Universal centre plate A 1561.07U BF..Universal centre plate A 5201 DTU..Universal timer switch L i tB l i Blinds Management Light Management LB Management LB ManagementLS rangeAS rangeA rangeA 1561.07..Standard centre plateAS 1561.07..Standard centre plate AS 1561.07U..Universal centre plate.. 5232 ST..Centre plate with timer function standard.. 5232 T3..Centre plate with timer function universal.. 5232 TS3..Centre plate with timer function universal and sensor connection .. 5232..Centre plate standard.. 5232 MS..Centre plate with memory function .. 5232 MS..Centre plate with memory function .. 5232 S..Centre plate with sensor connectionCD rangeLS rangeLight ManagementAu t o m a t i c s w i t c hLight ManagementLight Management LB ManagementLB ManagementLS range.. 1280-1..Universal automatic switch 2.2 mDAW 360..Ceiling automatic switch PMU 360..Universal presence detector.. 1280..Standard automatic switch 2.2 m .. 1180..Standard automatic switch 1.1 m .. 1180-1..Universal automatic switch 1.1 m .. 1180 WU..Standard automatic switch 1.1 m IP44.. 1180-1 WU..Universal automatic switch 1.1 m IP44t t i c s i t c CD rangeAS/A rangeLB Management CD 1280..Standard automatic switch 2.2 m CD 1180-1 WU.. Universal automatic switch 1.1 m IP44A 1180-1 WU..Universal automatic switch 1.1 m IP44A 1280..Standard automatic switch 2.2 mA 1280-1..Universal automatic switch 2.2 mCD 1180..Standard automatic switch 1.1 m CD 1180-1..Universal automatic switch 1.1 m CD 1180 WU..Standard automatic switch 1.1 m IP44A 1180..Standard automatic switch 1.1 m A 1180-1..Universal automatic switch 1.1 m A 1180 WU..Standard automatic switch 1.1 m IP44CD 1280-1..Universal automatic switch 2.2 mALBRECHT JUNG GMBH & CO. KGP.O. Box 132058569 SchalksmuhleGermanyPhone +49 2355 806-553Fax +49 2355 806-254*********************For sales contacts in your country see:/contactBL-BG-P。
戴尔 可管理性技术指南说明书

Intel Active Management Technology v7.0管理员指南概览产品概览开箱即用体验操作模式设置和配置概览菜单及默认设置MEBx 设置概览ME 常规设置AMT 配置Intel 快速呼叫帮助MEBx 默认设置ME 常规设置AMT 配置设置和配置方法概览配置服务 - 使用 USB 设备配置服务 - USB 设备步骤系统部署操作系统驱动程序管理Intel AMT Web GUIAMT 重定向 (SOL/IDE-R)AMT 重定向概览Intel Management and Security Status 应用程序Intel Management and Security Status 应用程序故障排除故障排除如果您购买的是 Dell™ n 系列计算机,则本说明文件中关于 Microsoft® Windows®操作系统的任何参考内容均不适用。
本说明文件中的信息如有更改,恕不另行通知。
© 2011 Dell Inc. 版权所有,翻印必究。
未经 Dell Inc. 书面许可,严禁以任何形式复制这些材料。
本文中使用的商标:Dell™、DELL 徽标、Dell Precision™、Precision ON™、ExpressCharge™、Latitude™、Latitude ON™、OptiPlex™、Vostro™和 Wi-Fi Catcher™是 Dell Inc. 的商标。
Intel®、Pentium®、Xeon®、Core™、Atom™、Centrino®和 Celeron®是 Intel Corporation 在美国和其他国家和地区的注册商标或商标。
AMD®是 Advanced Micro Devices, Inc. 的注册商标,AMD Opteron™、AMD Phenom™、AMD Sempron™、AMD Athlon™、ATI Radeon™和 ATI FirePro™是 Advanced Micro Devices, Inc. 的商标;Microsoft®、Windows®、MS-DOS®、Windows Vista®、Windows Vista 开始按钮和 Office Outlook®是Microsoft Corporation 在美国和/或其他国家和地区的商标或注册商标。
AM18X5系列系统电源管理应用说明书

1.IntroductionIn addition to fundamentally low power RTC operation, the Ambiq AM18X5 includes the capability to effectively manage the power of other devices in a system. This allows the creation of extremely power efficient systems with minimal additional components. This Application Note describes how the AM18X5 may be used in various applications.2.System Power Control ApplicationsThe AM18X5 enables a variety of system implementations in which the AM18X5 can control the power used by other elements in the system. This configuration is typically used when the entire system is powered from a battery and minimizing total power usage is critical.2.1VSS Power SwitchedFigure 1 shows the recommended implementation, in which the internal power switch of the AM18X5 is used to completely turn off the MCU and/or other system elements. In this case the PSW/nIRQ2 output is configured to generate the SLEEP function, and the PWR2 bit is asserted. Under normal circumstances, the PSW/nIRQ2 pin is pulled to VSS with ~1 ohm of resistance, so that the MCU receives full power. The MCU initiates a SLP operation, and when the AM18X5 enters the SLEEP state the PSW/nIRQ2 pin is opened and power is completely removed from the MCU. This results in significant additional power savings relative to the other alternatives because even very low power MCUs require more current in their lowest power state than the AM18X5.The AM18X5 normally powers up selecting the OUTB register bit to drive the PSW/nIRQ2 pin, and the default value of the OUTB bit is zero. This ensures that the power switch is enabled at power up. If the power switch function is used, software should only change the PSW/nIRQ2 selection between OUTB (0b111) and SLEEP(0b110) to ensure no glitches occur in the power switching function.Figure 1 – Switched VSS Power Control2.2 VCC Power SwitchedFigure 2 shows the application in which an external transistor switch T is used to turn off power to the MCU. The SLP function operates identically to the VSS switched case above, but this implementation allows switchinghigher current and maintains a common ground. R can be on the order of megohms, so that negligible current is drawn when the circuit is active and PSW/nIRQ2 is low.Figure 2 – Switched VCC Power Control2.3 Reset DrivenFigure 3 shows the application in which the AM18X5 communicates with the system MCU using the reset function. In this case the MCU initiates a SLP operation, and sets the SLRES bit so that when the AM18X5enters the SLEEP state, it brings nRST low to reset the MCU. When the trigger occurs, the AM18X5 releases the MCU from reset, and may also generate an interrupt which the MCU can query to determine how reset wasexited. Since many MCUs use much less power when reset, this implementation can save some system power.Figure 3 – Reset Driven Power ControlOne potential issue with this approach is that many MCUs include internal pullup resistors on their reset inputs, and the current drawn through that resistor when the reset input is held low is generally much higher than theMCU would draw in its inactive state. Any pullup resistor should be disabled and the nRST output of the AM18X5 should be configured as a push-pull output.2.4Interrupt DrivenFigure 4 shows the simplest application, in which the AM18X5 communicates with the system MCU using an interrupt. The MCU can go into standby mode, reducing power somewhat, until the AM18X5 generates an interrupt based on an alarm or a timer function. This produces smaller power savings than other alternatives, but allows the MCU to wake in the shortest time.Figure 4 – Interrupt Driven Power Control3.Sleep RegisterThe register which controls the Sleep function of the Power Management system in the AM18X5 is the Sleep Register, accessed at register offset 0x17. The bits of the Sleep Register are defined below.SLP [7] - when 1, the Power Control State Machine (SM) described in Section 4will transition to theSWAIT state. This bit will be cleared when the SM returns to the RUN state. If either STOP is 1 or no interrupt is enabled, SLP will remain at 0 even after an attempt to set it to 1.SLRES [6] - when 1, assert nRST low when the Power Control SM is in the SLEEP state.EX2P [5] - when 1, the external interrupt XT2 will trigger on a rising edge of the WDI pin. When 0, the external interrupt XT2 will trigger on a falling edge of the WDI pin.EX1P [4] - when 1, the external interrupt XT1 will trigger on a rising edge of the EXTI pin. When 0, the external interrupt XT1 will trigger on a falling edge of the EXTI pin.SLST [3] - set when the AM18X5 enters Sleep Mode. This allows software to determine if a SLEEP has occurred since the last time this bit was read.SLTO [2:0] - the number of 7.8 ms periods after SLP is set until the Power Control SM goes into theSLEEP state. If SLTO is not 0, the actual delay is guaranteed to be between SLTO and (SLTO - 1)periods. If SLTO is 0, the transition will occur with no delay.4.Sleep Control State MachineThe AM18X5 includes a sophisticated Sleep Control system that allows the AM18X5 to manage power for other chips in a system. The Sleep Control system provides two outputs which may be used for system power control:1) A reset (nRST) using the nRST output pin may be generated to put any host controller into a minimumpower mode and to control sequencing during power up and power down operations.2) A power switch signal may be generated (PWR), which allows the AM18X5 to completely power downother chips in a system by allowing the PSW/nIRQ2 pin to float. The OUT2S field must be set to a value of 6 to select the SLEEP output. When using the PWR output, PSW/nIRQ2 is configured as an opendrain pin with 1 ohm resistance. This allows the AM18X5 to directly switch up to 50 mA of current with no external components or to control a single external transistor for higher current switching. The lowresistance power switch is enabled by setting the PWR2 bit. If the I2C or SPI master (i.e., the hostcontroller) is powered down by the power switch, the PWGT bit should be set to ensure that a floating bus does not corrupt the AM18X5.3) If OUT2S is 6, but the PWR2 bit is not set, PSW/nIRQ2 will be configured as a high true Sleep outputwhich may be used as an interrupt.The Sleep state machine in Figure 5 receives several inputs which it uses to determine the current Sleep State:1) POR – the indicator that power is valid, i.e. either VCC or VBAT is above the minimum voltage.2) SLP - the Sleep Request signal which is generated by a software access to the Sleep Register.3) TRIG - the OR of the enabled interrupt request from the Alarm comparison in the RTC, the interrupt signalfrom the Countdown Timer in the RTC, the interrupt signal from the Watchdog Timer in the RTC, theExternal Interrupt 1 or 2 pins, the Battery Low detection interrupt, the Autocalibration Fail interrupt, or the Oscillator Fail interrupt.4) TO - the timeout signal from the SL Timeout counter.4.1RUNRUN is the normal operating state of the AM18X5. PWR and nRST are not asserted, SLP is 0, and SLST holds the state of the previous Sleep. SLST should be cleared by software before entering the SWAIT state.4.2SWAITSoftware can put the chip to sleep by setting the SLP bit in the Sleep Register, as long as a valid interrupt is enabled (see Section 4.4) indicated by VAL being asserted. The SM moves to the SWAIT state and waits for a programmable number of seconds (0 to 7) selected by the SLTO field in the Sleep Register. This allows software to perform additional cleanup functions after setting SLP before the MCU is shut down. Operation is the same in SWAIT as it is in RUN, and if an enabled interrupt occurs (TRIG) the SM returns to the RUN state and clears the SLP bit. PWR and nRST are not asserted, SLP is 1, and SLST is 0.4.3SLEEPOnce the programmed number of seconds has elapsed in the SWAIT state, the TO signal is asserted and the machine moves to the SLEEP state, putting the AM18X5 into Sleep Mode. In this case the PWR signal is removed, and nRST is asserted if SLRES is set. Once an enabled operational interrupt occurs (TRIG), the SM returns to the RUN state, reactivates power and removes reset as appropriate. The SLST register bit in the Sleep Register is set when the SLEEP state is entered, allowing software to determine if a SLEEP has occurred.!POR!TO * !TRIG!SLP + !VAL!TRIGFigure 5 – Sleep State Machine4.4 SLP ProtectionSince going into Sleep Mode may prevent an MCU from accessing the AM18X5, it is critical to ensure that the AM18X5 will receive a TRIG signal. To guarantee this, the SLP signal cannot be set unless the STOP bit is 0 and at least one of the following conditions exists:1) The AIE bit is 1, enabling an Alarm interrupt.2) The TIE and the TE bits are 1, enabling a Countdown Timer interrupt. 3) Either the EX1E or EX2E bit is a 1, enabling an External interrupt.4) The BMB field is not zero and the WDS bit is zero, enabling a Watchdog InterruptIn addition, SLP cannot be set if there is an interrupt pending. Software should read the SLP bit after attempting to set it. If SLP is not asserted, the attempt to set SLP was unsuccessful either because a correct trigger was not enabled or because an interrupt was already pending. Software must correct the situation before attempting to enter Sleep Mode again.5.Typical System ImplementationFigure 6 is a more detailed view of a typical system using the VSS Power Switched approach. The VSS pin of the MCU, and potentially other system components, is switched using the PSW pin of the AM18X5. The nIRQ pin of the AM18X5 is connected to an interrupt input of the MCU, allowing the MCU to utilize the RTC interrupt functions of the AM18X5 when it is awake. The nRST output of the AM18X5 is connected to the reset input of the MCU, enabling the AM18X5 to control power on reset and integrate an external MCU reset button RESET. The MCU controls the AM18X5 over a SPI or I2C I/O channel.Figure 6 – System ExampleThe key value of the AM18X5 in this type of system is the ability to put the MCU into an off state, and providing a very rich variety of triggers which can cause the AM18X5 to wake the MCU from the off state. There are a number of different triggers which may be useful.5.1AlarmsThe system may require the MCU to wake up at particular times, which is accomplished by configuring the Alarm Interrupt function of the AM18X5.5.2Countdown TimerThe system may require the MCU to wake up at periodic intervals which do not necessarily correspond to specific calendar times. The Countdown Timer of the AM18X5 provides highly flexible time interval configuration to support this function.5.3WAKE Button/SwitchA very common requirement is the capability to wake the system with a manual input such as a pushbutton or switch, typified by the WAKE button in Figure 6. One of the external interrupt inputs such as EXTI may be simply connected to the button. All AM18X5 inputs include Schmitt trigger circuitry to enable clean interrupts. If additional debouncing of the input is required, the AM18X5 provides direct access to the interrupt input pins to facilitate software implementations.5.4External Device InputsIn some systems an external device such as a wakeup radio may provide a signal which must wake the MCU. An AM18X5 external interrupt such as the WDI pin provides this capability.5.5Analog InputsSome systems include analog signals, such as light sensors or detectors on radio antennas, which must wake the MCU. The Analog Comparator function, which allows the voltage on the VBAT input of the AM18X5 to be compared with a configurable voltage threshold and generate an interrupt, can easily be used in this application, and it allows flexible configuration, both in voltage levels and in transition direction to support different environments. The Analog Comparator may also be used to provide a third external digital interrupt if necessary by selecting the proper digital threshold.5.6Battery Low DetectionThe Analog Comparator can provide a battery low detection function. In this case, the VCC pin would be tied to the VBAT pin, and the thresholds would be adjusted to ensure that the Battery Low interrupt occurs prior to any Brownout Detection on the VCC input. This allows software to prepare for a potential battery failure in advance without having to poll the battery level.5.7ErrorsAny failure interrupt in the AM18X5 may also be configured to wake the MCU. This can be particularly valuable for Oscillator Failure detection, when software may need to respond to the error in order to report the problem quickly.6.Saving ParametersIf the MCU is powered down in Sleep Mode, there is often some data which must be preserved until the next power up. The internal RAM of the AM18X5 is always available, so software can easily save any necessary parameters prior to entering Sleep Mode and retrieve them when the MCU wakes up.7.Power Switch Electrical CharacteristicsThe power switch on the AM18X5 PSW pin has a typical on resistance of 1 ohm over the full temperature range so that currents up to 50 mA may be handled without appreciable voltage drop. This allows the AM18X5 to switch power to multiple devices in most systems, which can be particularly important for components without internal Sleep functions. If the PSW pin is not used as a power switch, the maximum leakage current of the ~1 Ω switch is less than 250 pA at 25 °C.8.Avoiding Unexpected Leakage PathsOne potential problem which can occur when the AM18X5 powers other devices down is that unexpected leakage paths can be created between the powered AM18X5 and the unpowered device. The AM18X5 can be configured to disable inputs and outputs in Sleep Mode to prevent leakage. In general, any input or output pin connected to a device which is powered down should be disabled. Any pins which remain powered in Sleep Mode, such as pushbutton inputs used to wake the system, must not be disabled.1) nRST is disabled in Sleep Mode by clearing the RSEN bit in the Output Control Register.2) FOUT/nIRQ is disabled in Sleep Mode by clearing the O1EN bit in the Output Control Register.3) CLKOUT/nIRQ3 is disabled in Sleep Mode by clearing the O4EN bit in the Output Control Register.4) nTIRQ (I2C devices only) is disabled in Sleep Mode by clearing the O3EN bit in the Output ControlRegister.5) EXTI is disabled in Sleep Mode by setting the EXDS bit in the Output Control Register.6) WDI is disabled in Sleep Mode by setting the WDDS bit in the Output Control Register.7) The I2C or SPI interface pins are disabled in Sleep Mode by setting the PWGT bit in the Oscillator ControlRegister. This is a particularly important function because there are multiple leakage paths in the I/Ointerfaces.9.System Power AnalysisThe AM18X5 can significantly improve the power characteristics of many different types of systems. A specific example will be presented, and several other generalizations can be made from this. The fundamental advantage provided by the AM18X5 is that it allows the system designer to essentially ignore the sleep current of other system components, which allows the utilization of components which have be optimized for other parameters, such as active power, cost or functionality.9.1Using an External RTC with Power ManagementThe key element in any system power analysis is the usage profile, and for this example we assume the system is active for T act and inactive for T inact. I act is the current drawn when the system is active, and I inact is the current drawn when the system is inactive. The average current I avg is therefore:I avg = (T act * I act + T inact * I inact )/(T act + T inact)An example will use a PIC16LF1947 MCU, which is highly optimized for low power operation. This MCU draws 80 nA in Sleep Mode, 1.8 uA in Sleep Mode with the internal oscillator and RTC active, and 120 uA in 500 KHz active mode. Assume a usage profile where the system in active for 1 second every 30 minutes, so that T act is 1 and T inact is 1799. If this MCU is used alone and supplies the RTC functions, the average current for theusage profile is:I avg = (1 * 120 uA + 1799* 1.8 uA)/1800 = 1.865 uAIf the AM18X5 is used to provide the RTC functionality in Autocalibrated RC Mode (<20 nA continuous current) and the PIC is placed into Sleep Mode, the average current for the usage profile is dramatically lower:I avg = (1 * 120 uA + 1799* 80 nA)/1800 + 20 nA = 166 nAThis is a significant improvement, but the current can be further reduced by having the AM18X5 switch power to the MCU. The resulting average current is ~50% lower:I avg = (1 * 120 uA + 1799* 0 nA)/1800 + 20 nA = 86 nA9.2Managing MCU Active PowerIn many cases, the duration of the active time is a function of how much processing must be accomplished, and can therefore be assumed to be a linear function of the MCU clock frequency in active mode. The examples in the previous section assumed that the MCU ran for 1 second at 500 KHz, so 500,000 cycles of an 8-bit processor were required. Like most MCUs, the PIC has a relatively constant active current as a function of clock frequency, so using a higher internal frequency in the same MCU would have little effect on the overall power. However, there may be other MCUs (such as those with 32-bit processors) which have better active power efficiency but poor sleep power, and power switching with the AM18X5 eliminates any sleep power considerations.9.3Lower Cost MCUsLower cost MCUs often have poor sleep power characteristics relative to sleep optimized parts. Since theAM18X5 eliminates sleep power considerations, these lower cost processors may provide equivalent overall average power at significant cost savings.9.4High Performance ProcessorsIn some applications very high performance processors such as DSPs must be used due to real time processing requirements. These processors are generally not optimized for sleep performance, but they may be used in applications with low duty cycles. One example of this is fingerprint recognition, which is rarely accessed but must provide very fast response with complex processing. The AM18X5 power management functions enable a system design where the processor is powered down the vast majority of the time, providing low average power combined with very high instantaneous performance.Document Revision HistoryRev # Description0.01 Initial version0.02 Add leakage management0.03 Corrected calculations in section 9.10.04 Updated doc to only reflect the AM18X5 part numbersAddress:Ambiq Micro, Inc.11305 Four Points Drive, Building 2, Suite 250Austin, TX 78726+1-512-879-2850Website:General Information:*******************Sales:********************Technical Support:**********************。
Intel Active Management Technology v4.0 管理员指南说明书
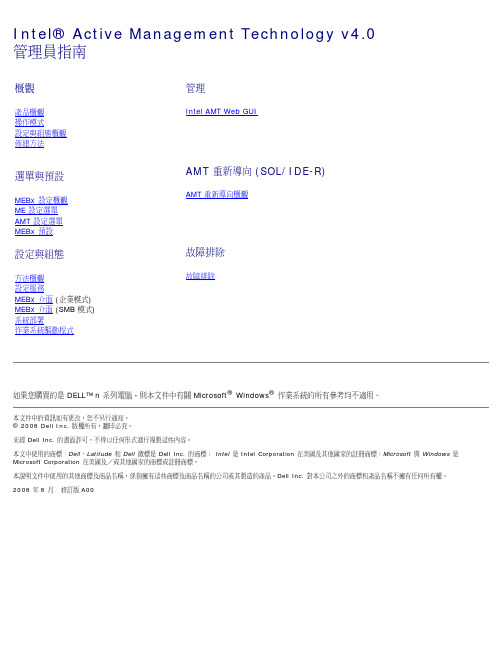
Intel® Active Management Technology v4.0管理員指南概觀產品概觀操作模式設定與組態概觀佈建方法選單與預設MEBx 設定概觀ME 設定選單AMT 設定選單MEBx 預設設定與組態方法概觀設定服務MEBx 介面 (企業模式) MEBx 介面 (SMB 模式)系統部署作業系統驅動程式管理Intel AMT Web GUIAMT 重新導向 (SOL/IDE-R) AMT 重新導向概觀故障排除故障排除如果您購買的是 DELL™ n 系列電腦,則本文件中有關 Microsoft® Windows®作業系統的所有參考均不適用。
本文件中的資訊如有更改,恕不另行通知。
© 2008 Dell Inc. 版權所有,翻印必究。
未經 Dell Inc. 的書面許可,不得以任何形式進行複製這些內容。
本文中使用的商標:Dell、Latitude和 Dell 徽標是 Dell Inc. 的商標;Intel是 Intel Corporation 在美國及其他國家的註冊商標;Microsoft與Windows是Microsoft Corporation 在美國及/或其他國家的商標或註冊商標。
本說明文件中使用的其他商標及商品名稱,係指擁有這些商標及商品名稱的公司或其製造的產品。
Dell Inc. 對本公司之外的商標和產品名稱不擁有任何所有權。
2008 年 8 月修訂版 A00概觀Intel® Active Management Technology (Intel AMT) 可讓企業使用以下方法,輕鬆管理透過網路連接的電腦。
無論電腦開機或關機,皆可探索網路上的運算資產 – Intel AMT 使用儲存於非揮發性系統記憶體中的資訊存取電腦。
電腦即使關機也可存取資料 (亦稱為 Out-of-Band 或 OOB 存取)。
即使作業系統故障,仍可自遠端修復系統 — 軟體或作業系統故障時,Intel AMT 可用於自遠端存取電腦,並進行修復。
BidManager 发布公告-新特性和改进 2022年11月说明书
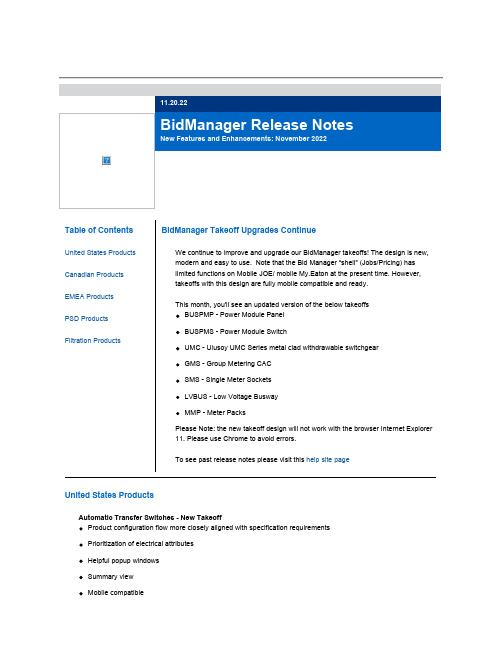
Products options added Service entrance rated Bypass Isolation Contactor ATS NEMA 3RX rating for free-standing enclosures – 304 or 316 stainless steel
Uncertainty and Liquidity Crises
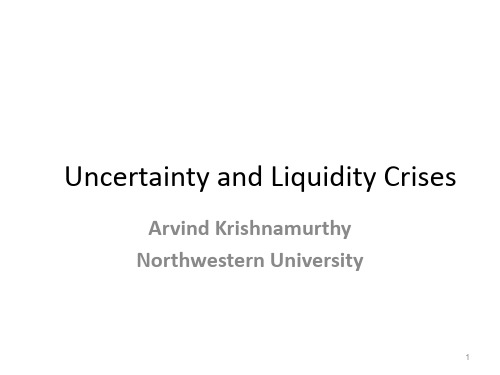
• What are appropriate policy responses?
– Why intervene? – Channels for policies. Optimal policy.
3
Outline
• Liquidation model
– Bank runs – Financial markets/capital constraints
– P0 = 1 – (1 – L/2) qA qB – Liquidity premium = (1 – L/2) qA qB
6
Bank run a la Diamond-Dybvig
• Bank imposes sequential service constraint:
– If all agents liquidate, first liquidators get 1, until all of L is used up – Agents after L get 0 if liquidate, or P<1 if they hold on past date 1
– Choose either urn A or urn B, and choose a color to bet on.
• If subjective prob(red, B) < ½ , then subject should choose B and green. Or, vice-versa
16
Recap
• So far, liquidation model
• Next, Uncertainty and Crises
17
Uncertainty
• Subprime crisis:
cas-management 配置说明-概述说明以及解释

cas-management 配置说明-概述说明以及解释1.引言1.1 概述CAS-Management是一种用于统一身份认证和授权管理的开源软件,旨在提供安全、可扩展和灵活的身份认证解决方案。
它基于CAS(Central Authentication Service)协议,可以帮助组织轻松地集成各种应用程序和服务,实现单点登录和安全身份验证。
本文旨在介绍CAS-Management的配置及使用方法,帮助读者了解如何快速搭建和部署CAS-Management,并解决在配置过程中可能遇到的常见问题。
通过学习本文,读者将能够更好地使用CAS-Management 来管理用户身份验证和授权,提升系统的安全性和用户体验。
1.2 文章结构文章结构部分应该包括本篇文章的整体框架和组织结构。
在文章结构部分,通常会描述文章的分章节内容和主要议题。
具体来说,在CAS-Management 配置说明这篇文章中,文章结构部分可以简要概括为以下几个方面:1. 引言部分:介绍CAS-Management的背景和重要性,概括本文的内容以及解决问题的目的。
2. 正文部分:主要分为CAS-Management简介、配置步骤和常见问题解决方法三大部分,详细介绍CAS-Management系统的相关知识和配置方法。
3. 结论部分:总结文章内容,展望未来CAS-Management的发展,并结束整篇文章的结尾。
在文章结构中,以上各个部分应该清晰明了,使读者能够快速了解文章的整体结构和主要内容。
1.3 目的CAS-Management 配置说明的主要目的是帮助读者了解如何配置和使用CAS-Management,提供详细的配置步骤和常见问题的解决方法。
通过本文,读者将能够快速上手CAS-Management,并且能够避免一些常见的配置错误。
此外,本文还旨在介绍CAS-Management 的基本概念,并展望其在未来的发展方向,帮助读者更好地理解和使用这一工具。
NVIDIA Quadro P400 专业图形卡商品说明书
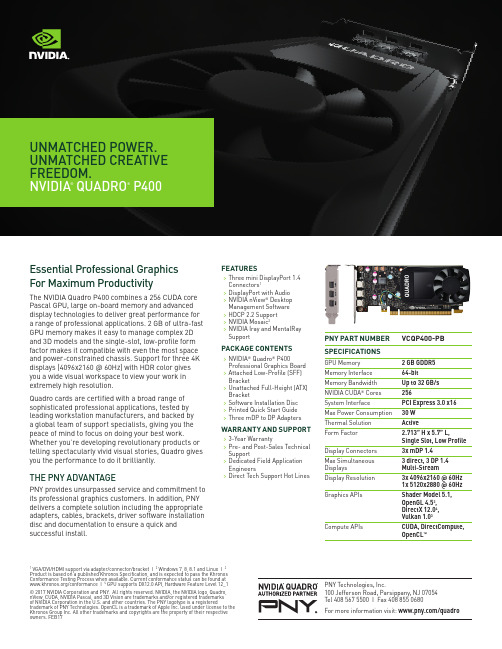
Essential Professional Graphics For Maximum ProductivityThe NVIDIA Quadro P400 combines a 256 CUDA core Pascal GPU, large on-board memory and advanced display technologies to deliver great performance for a range of professional applications. 2 GB of ultra-fast GPU memory makes it easy to manage complex 2D and 3D models and the single-slot, low-profile form factor makes it compatible with even the most space and power-constrained chassis. Support for three 4K displays (4096x2160 @ 60Hz) with HDR color gives you a wide visual workspace to view your work in extremely high resolution.Quadro cards are certified with a broad range of sophisticated professional applications, tested by leading workstation manufacturers, and backed by a global team of support specialists, giving you the peace of mind to focus on doing your best work. Whether you’re developing revolutionary products or telling spectacularly vivid visual stories, Quadro gives you the performance to do it brilliantly. THE PNY ADVANTAGE PNY provides unsurpassed service and commitment to its professional graphics customers. In addition, PNY delivers a complete solution including the appropriate adapters, cables, brackets, driver software installation disc and documentation to ensure a quick and successful install.FEATURES >Three mini DisplayPort 1.4 Connectors 1 >DisplayPort with Audio >NVIDIA nView ® Desktop Management Software >HDCP 2.2 Support >NVIDIA Mosaic 2 >NVIDIA Iray and MentalRay Support PACKAGE CONTENTS >NVIDIA ® Quadro ® P400 Professional Graphics Board >Attached Low-Profile (SFF) Bracket >Unattached Full-Height (ATX) Bracket >Software Installation Disc >Printed Quick Start Guide >Three mDP to DP Adapters WARRANTY AND SUPPORT >3-Year Warranty >Pre- and Post-Sales Technical Support >Dedicated Field Application Engineers >Direct Tech Support Hot Lines PNY PART NUMBER VCQP400-PB SPECIFICATIONS GPU Memory 2 GB GDDR5 Memory Interface 64-bit Memory Bandwidth Up to 32 GB/s NVIDIA CUDA ® Cores 256 System Interface PCI Express 3.0 x16 Max Power Consumption 30 W Thermal Solution Active Form Factor 2.713” H x 5.7” L, Single Slot, Low Profile Display Connectors3x mDP 1.4 Max Simultaneous Displays3 direct, 3 DP 1.4 Multi-Stream Display Resolution3x 4096x2160 @ 60Hz 1x 5120x2880 @ 60Hz Graphics APIs Shader Model 5.1, OpenGL 4.53, DirectX 12.04, Vulkan 1.03Compute APIsCUDA, DirectCompute, OpenCL ™ UNMATCHED POWER.UNMATCHED CREATIVE FREEDOM. NVIDIA ® QUADRO ®P4001 VGA/DVI/HDMI support via adapter/connector/bracket | 2 Windows 7, 8, 8.1 and Linux | 3 Product is based on a published Khronos Specification, and is expected to pass the Khronos Conformance Testing Process when available. Current conformance status can be found at /conformance | 4 GPU supports DX12.0 API, Hardware Feature Level 12_1© 2017 NVIDIA Corporation and PNY. All rights reserved. NVIDIA, the NVIDIA logo, Quadro, nView, CUDA, NVIDIA Pascal, and 3D Vision are trademarks and/or registered trademarks of NVIDIA Corporation in the U.S. and other countries. The PNY logotype is a registered trademark of PNY Technologies. OpenCL is a trademark of Apple Inc. used under license to the Khronos Group Inc. All other trademarks and copyrights are the property of their respective owners. FEB17PNY Technologies, Inc. 100 Jefferson Road, Parsippany, NJ 07054 Tel 408 567 5500 | Fax 408 855 0680For more information visit: /quadro。
Dell Wyse Management Suite 版本 1.1 管理员指南说明书
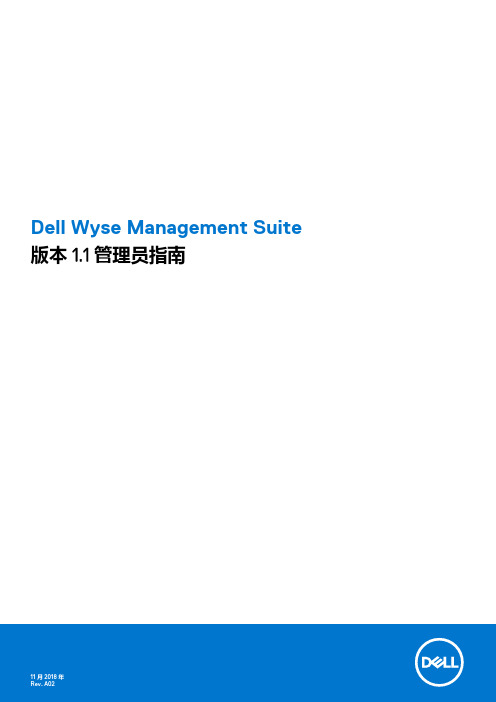
Dell Wyse Management Suite 版本 1.1 管理员指南11 2018注意、小心和警告:“注意”表示帮助您更好地使用该产品的重要信息。
:“小心”表示可能会损坏硬件或导致数据丢失,并告诉您如何避免此类问题。
:“警告”表示可能会导致财产损失、人身伤害甚至死亡。
© 2018 Dell Inc. 或其子公司。
保留所有权利Dell、EMC 和其他商标为 Dell Inc. 或其子公司的商标。
其他商标均为其各自所有者的商标。
章 1: Wyse Management Suite 简介 (7)章 2: 此版本有哪些新功能? (8)章 3: Wyse Management Suite 使用入门 (9)公共云上的 Wyse Management Suite 登录 (9)在私有云上部署 Wyse Management Suite 的前提条件 (10)管理控制台的功能区域 (10)配置和管理 Thin Client (11)章 4: Wyse Management Suite 仪表板 (12)章 5: 管理组和配置 (13)配置全局级别策略 (14)配置组级别策略 (14)配置设备级别策略 (14)组树层次结构 (15)添加组 (15)编辑组 (15)移除组 (15)未托管组 (16)配置 ThinOS 策略设置 (16)ThinOS - 向导模式 (16)ThinOS - 高级模式 (20)配置 Windows Embedded Standard 策略设置 (44)配置系统个性化 (45)配置桌面体验 (47)配置网络设置 (48)配置安全性和锁定设置 (48)配置其他设置 (48)配置远程连接设置 - Citrix (49)配置远程连接设置 - VMware (51)配置远程连接设置 - RDP (52)配置远程连接设置 - 浏览器 (54)配置 Latitude 移动 Thin Client BIOS 设置 (55)配置 Wyse 7040 Thin Client BIOS 设置 (56)配置设备信息 (57)配置 Wyse Easy Setup 设置 (58)配置 VNC 设置 (59)配置域设置 (59)配置 Linux 策略设置 (59)配置系统个性化 (60)配置桌面体验 (61)目录3配置安全设置 (63)配置集中配置设置 (63)配置其他设置 (64)配置 VDI 全局设置 (64)配置远程连接设置 - Citrix (66)配置远程连接设置 - VMware (67)配置远程连接设置 - RDP (68)配置远程连接设置 - 浏览器 (69)配置高级设置 (70)配置 ThinLinux 策略设置 (70)配置系统个性化 (71)配置桌面体验 (72)配置登录体验 (73)配置网络设置 (73)配置安全设置 (73)配置集中配置设置 (74)配置其他设置 (75)VDI 全局设置 (75)配置远程连接设置 - Citrix (76)配置远程连接设置 - VMware (78)配置远程连接设置 - RDP (79)配置远程连接设置 - 浏览器 (80)配置高级设置 (80)配置设备信息 (81)配置 Wyse 3040 Thin Client BIOS 设置 (81)配置 Wyse Software Thin Client 策略设置 (82)配置系统个性化 (83)配置桌面体验 (85)配置网络设置 (86)配置安全性和锁定设置 (86)配置其他设置 (86)配置远程连接设置 - Citrix (88)配置远程连接设置 - VMware (90)配置远程连接设置 - RDP (90)配置远程连接设置 - 浏览器 (93)配置设备信息 (94)配置 VNC 设置 (94)配置域设置 (94)章 6: 管理设备 (95)使用筛选器 (95)保存当前筛选器 (96)将设备注册到 Wyse Management Suite 中 (96)通过 WDA 用户界面注册 ThinOS 瘦客户端 (97)通过 Wyse 设备代理用户界面注册 Windows Embedded Standard Thin Client (99)通过 Wyse 设备代理用户界面注册 Linux Thin Client (100)使用 DHCP 选项标签注册设备 (100)4目录拉取 Windows Embedded Standard 或 ThinLinux 映像 (104)拉动日志文件 (106)重命名 Thin Client (106)配置远程阴影连接 (107)章 7: 应用和数据 (109)配置应用库存清单 (110)移动应用库存清单 (110)配置 Thin Client 和 Wyse Software Thin Client 应用库存清单 (110)向 Thin Client 部署应用程序 (111)创建并部署高级应用程序策略到 Thin Client (111)将 Windows Embedded Standard 操作系统和 ThinLinux 映像添加到资源清册 (113)管理 ThinOS 固件库存清单 (113)管理 Windows Embedded Standard 和 ThinLinux 映像策略 (113)管理文件库 (114)更改所有属于营销组的设备的壁纸 (114)章 8: 管理规则 (116)注册未托管设备 (116)创建未托管设备自动分配规则 (117)警报通知 (118)章 9: 管理作业 (120)同步 BIOS 管理员密码 (121)计划映像策略 (121)计划应用程序策略 (121)计划设备命令作业 (122)章 10: 事件 (123)查看事件摘要 (123)查看审计日志 (124)章 11: 管理用户 (125)添加新管理员用户 (126)编辑管理员用户 (126)停用管理员帐户 (127)删除管理员 (127)章 12: 门户管理 (128)配置控制台设置 (128)Active Directory (128)警报分类 (130)外部应用程序服务 (130)文件库 (130)其他设置 (131)Thin Client (131)目录5双重验证 (131)生成报告 (132)多租户 (133)配置帐户设置 (133)自定义品牌 (133)许可证订阅 (133)系统设置程序 (134)附录 A: 安装或升级 Wyse 设备代理 (135)使用 Wyse Management Suite 应用程序策略升级 Wyse 设备代理 (135)手动安装 Wyse 设备代理程序 (135)在 ThinLinux 和 Linux 客户端上安装或升级 Wyse 设备代理 (136)附录 B: Wyse Management Suite 功能矩阵 (137)附录 C: Wyse Management Suite 上支持的 Thin Client (139)附录 D: 无线配置文件密码编辑器 (141)配置无线配置文件密码编辑器 (141)无线配置文件密码编辑器的限制 (142)附录 E: 创建和配置 DHCP 选项标签 (143)附录 F: 创建和配置 DNS SRV 记录 (149)6目录Wyse Management Suite 简介Wyse Management Suite 是下一代管理解决方案,使您能够集中配置、监控、管理和优化您的 Dell Wyse Thin Client。
Dell Wyse Management Suite 版本 1.4 高可用性指南说明书
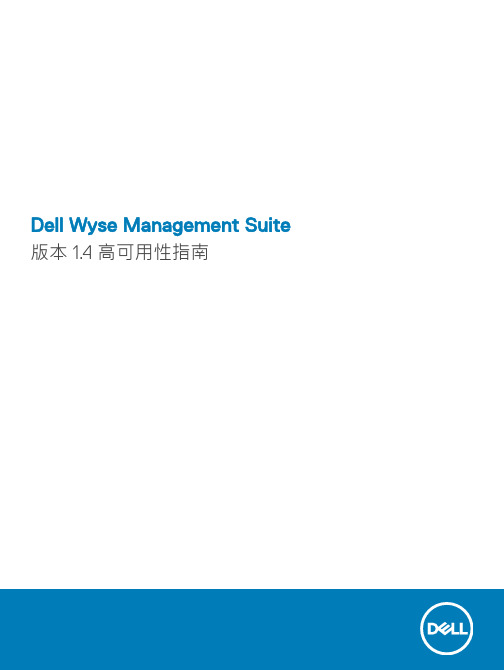
Dell Wyse Management Suite 版本 1.4 高可用性指南註、警示與警告註:「註」表示可以幫助您更有效地使用產品的重要資訊。
警示:「警示」表示有可能會損壞硬體或導致資料遺失,並告訴您如何避免發生此類問題。
警告:「警告」表示有可能會導致財產損失、人身傷害甚至死亡。
© 2019 Dell Inc. 或其子公司。
版權所有,翻印必究。
Dell、EMC 與其他商標均為 Dell Inc.或其子公司的商標。
其他商標可能為其各自擁有者的商標。
2019 - 05修正版 A001 簡介 (5)高可用性概觀 (5)2 高可用性架構 (6)高可用性的系統需求 (6)3 Windows Server 2012/2016 的高可用性 (8)建立叢集角色 (8)4 在 Windows Server 2012/2016 上達到高可用性 (12)在 Windows Server 2012/2016 上新增容錯移轉叢集功能 (12)建立檔案共用見證 (18)設定叢集仲裁設定 (19)建立叢集角色 (21)5 達到 MySQL InnoDB 的高可用性 (25)使用 MySQL InnoDB 達到高可用性 (25)安裝 MySQL InnoDB 資料庫 (25)檢查 MySQL InnoDB 伺服器執行個體 (43)建立 MySQL InnoDB 的叢集執行個體 (44)將伺服器執行個體新增至 MySQL InnoDB 叢集 (45)設定 MySQL 路由器 (46)在 MySQL InnoDB 伺服器上建立資料庫和使用者 (59)6 在 MongoDB 上達到高可用性 (60)安裝 MongoDB (60)建立 MongoDB 資料庫的複本伺服器 (61)建立資料庫使用者 (61)建立 MongoDB 的 DBadmin 使用者 (62)編輯 mongod.cfg 檔案 (62)啟動伺服器複寫 (62)7 達到 T eradici 裝置的高可用性 (66)安裝和設定 HAProxy (66)安裝 Wyse Management Suite 伺服器 (68)8 在 Windows Server 2012/2016 上安裝 Wyse Management Suite (69)9 將 Wyse Management Suite 1.3 版升級至 1.4 版 (70)10 安裝後檢查 (78)目錄311 疑難排解 (79)4目錄簡介Wyse Management Suite version 1.4 為下一代的管理解決方案,可讓您設定、監控、管理及最佳化 Dell Wyse 精簡型用戶端。
Intel 主动管理技术(主动式管理技术) v4.0 管理员指南说明书
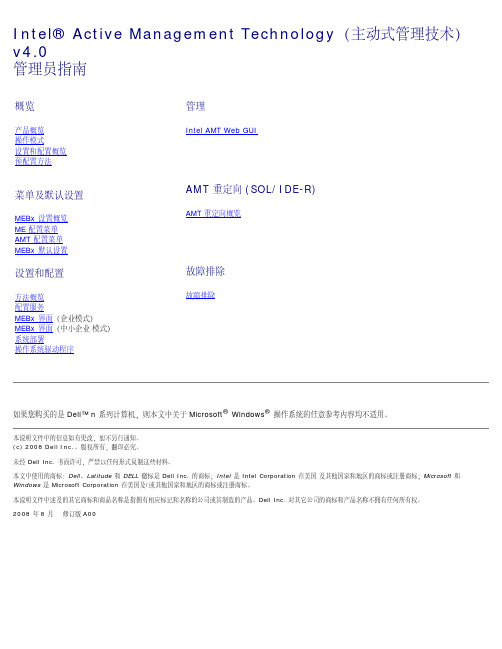
Intel® Active Management Technology(主动式管理技术)v4.0管理员指南概览产品概览操作模式设置和配置概览预配置方法菜单及默认设置MEBx 设置概览ME 配置菜单AMT 配置菜单MEBx 默认设置设置和配置方法概览配置服务MEBx 界面(企业模式)MEBx 界面(中小企业模式)系统部署操作系统驱动程序管理Intel AMT Web GUIAMT 重定向 (SOL/IDE-R) AMT 重定向概览故障排除故障排除如果您购买的是 Dell™ n 系列计算机,则本文中关于 Microsoft® Windows®操作系统的任意参考内容均不适用。
本说明文件中的信息如有更改,恕不另行通知。
(c) 2008 Dell Inc.。
版权所有,翻印必究。
未经 Dell Inc. 书面许可,严禁以任何形式复制这些材料。
本文中使用的商标:Dell、Latitude和DELL徽标是 Dell Inc. 的商标;Intel 是 Intel Corporation 在美国及其他国家和地区的商标或注册商标;Microsoft和Windows是 Microsoft Corporation 在美国及/或其他国家和地区的商标或注册商标。
本说明文件中述及的其它商标和商品名称是指拥有相应标记和名称的公司或其制造的产品。
Dell Inc. 对其它公司的商标和产品名称不拥有任何所有权。
2008 年 8 月修订版 A00概览Intel® 主动管理技术 (Intel AMT) 使公司可通过以下方法轻松实现对其联网计算机的管理:搜索网络上的计算机资产(无论计算机处于打开或关闭状态)– Intel AMT 使用存储在非易失性系统内存中的信息来访问计算机。
即使计算机处于关闭状态,也能对其进行访问(也称为带外访问或 OOB 访问)。
假如操作系统发生故障,也可远程修复系统 — 在软件或操作系统发生故障的情况下,可使用 Intel AMT 远程访问计算机以完成修复。
Lab-T, Inc. T300 User Manual
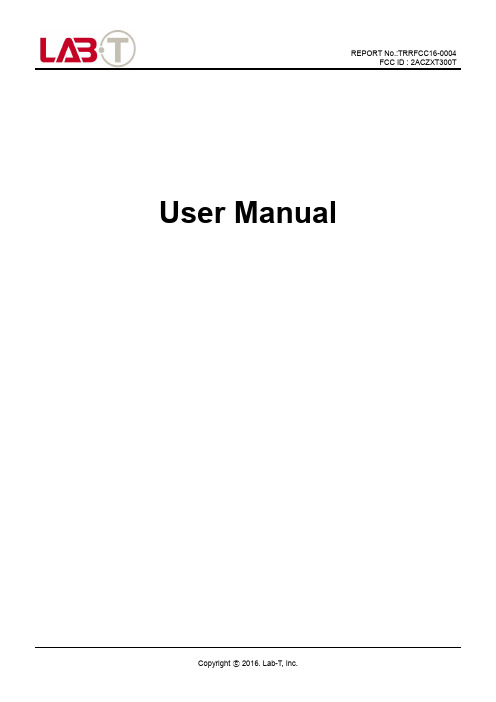
REPORT No.:TRRFCC16-0004FCC ID : 2ACZXT300T User ManualCopyright ⓒ 2016. Lab-T, Inc.4. Press and release the CH UP key to5.enter the automatic code search mode.The remote will transmit the TV power code every 1.5 seconds and the LED will blink at the same time.off, the remote has found a candidate group device code.the code and to exit the search mode.Time Warner Cable Enterprises LLC.assumes no responsibility for errors or omissions that may appear in this guide. We reserve the right to change this guide at any time without notice.Time Warner Cable Enterprises and the Time Warner Cable logo aretrademarks or registered trademarks of Time Warner Cable Enterprises in the U.S. and other countries.Third-party trademarks mentioned are the property of their respective owners.The use of the word partner does not Time Warner Cable Enterprises and any other company.2015 Time Warner Cable Enterprises LLC. All rights reserved.Last Updated: December 2015Printed in ChinaDisclaimerAll TV Setup CodesMost Common TV Codes1. Universal Power:2. TV:The universal power button simply sends the power code for all mapped with the DTA.4. MENU:application if available.5. GUIDE:The Guide button will launch the onscreen Guide UI.6. EXIT:The Exit button will dismiss all on screen UI.7. INFO:or a channel banner if available devices.code to any TV that is programmed.states are out of sync.3. PROG:Press and hold PROG with another button on the remote to RF4CE pair This is intended to allow the user to correct when the TV and DTA power 8. Directional Pad:Up, Down, Right, Left and OK keys 11.Volume:Increases or decreases the volume of the currently programmed TV.9. Last:Quick access to the most recently watched channels.10.Mute:on the currently programmed TV.12.Channel::This button toggles on/off the closed 15.INPUT:on the currently programmed TV.13.Number Keys:Understanding Your Remote Control KeysThe unified DTA Remote controls your Cisco, Arris and Technicolor DTA and the Volume, Mute, Power,Input on many connected TVs. Use the instructions in this guide to set up and use your unified DTA remote.WelcomeUse two AAA batteries.Check the diagram inside the battery compartment to ensure the batteries are inserted in the correct direction.BatteriesThis device complies with Part 15 of the FCC Rules.Operation is subject to the following two conditions:(1) This device may not cause harmful interference, and(2) This device must accept any interference received, including interference that may cause undesired operation.NOTE:tested and found to comply with the limits for a Class B digital FCC Rules.FCC Notice- Insert batteries correctly.There may be a risk of explosion if the batteries are incorrectly inserted.- Do not attempt to recharge ‘disposable’ or ‘non-reusable’batteries.- Please follow instructions provided for charging ‘rechargeable’ batteries.- Replace batteries with the same or equivalent type that we recommend.- Do not expose batteries to excessive heat (such as sunlight of fire).- Do not expose batteries to temperatures above 100(212).The batteries may containperchlorate, a known hazardous substance, so special handling and disposal of this product might be necessary. For more informaion about perchlorate and best management practices for perchlorate-containingsubstance, see /hazardouswaste/perchlorateThese limits are designed to provide reasonable protection against harmful interference in a residential installation.This equipment generates, uses and can radiate radio frequency energy and if not installed and used in accordance with the instructions, may cause harmful interference to radio communications.However, there is no guarantee that interference will not occur in a particular installation.If this equipment does cause harmful interference to radio or television reception, which can be determined by turning the equipment off and on, the user is encouraged to try to correct the interference by one or more of the following measures:- Reorient or relocate the receiving antenna.-the equipment and receiver.- Connect the equipment into an outlet on a circuit different from that to which the receiver is connected.- Consult the dealer or anexperienced radio/TV technician for help.The changes or modifications not expressly approved by the party responsible for compliance could void the user's authority to operate the equipment.CAUTION:Exposure to RadioFrequency Radiation.Antenna shall be mounted in such a manner to minimize the potential for human contact during normal operation.The antenna should not be contacted during operation exceeding the FCC radio frequency exposure limit.Battery SafetyThe batteries may contain substances that could be harmful to the environment.Recycle or dispose of batteries in accordance with the battery manufacturer’s instructions and local/national disposal and recycling regulations.Battery DisposalThis product may contain disposable batteries. Heed the following warning and follow the Battery Safety and Battery Disposal instructions below.BatteriesHandling Disposable Automatic Code Search begins with the through all device in the brand list.If the device code for your TV brand can’t be found in the list, please try to search the device code database using the following steps:1. Turn on your TV.3. Release the PROG key and make sure the RED LED stays on.Automatic Code SearchThis remote control is initiallyprogrammed for the Cisco DTA. Use to use the remote to control Arris,Technicolor DTA and your TV.Important Information about Your RemoteYour remote control can be paired with 1. Turn on the target (DTA) device.2. Press the PROG key for three seconds or until the RED LED turns on and then press "INFO" key.3. The LED on the remote control blinks mode.4. The DTA will prompt the user, via a message on the TV to enter a unique three (3) digit number.5. If the three digits entered are correct,the target (DTA) will prompt the user that pairing is successful.the DTA, allowing you to place the DTA out of the line of sight(behind your TV, for example)RF Pairing between Remote Control and DTA6. If the three digits entered are incorrect,the target (DTA) will prompt the user that pairing fails and to try again until the correct code is entered.Long Key Press Limit1.2.If you want to restore all settings to a default status or unpair the RCU,follow the steps below:Factory Reset(including RF unpairing)Technicolor, and Cisco box.Default state: the remote is initially Follow the steps below to program the remote to match DTA vendor:1. Check the brand of DTA box you have3. If your DTA box is Cisco, press the [101] keyIf your DTA box is Arris, press the [102] keyIf your DTA box is Technicolor, press the [103] keyassigned to control DTA VOLUME and MUTE.Your remote control can be used to control three DTAs which are Arris,Programming the remote to match DTA vendor1. Press and hold the PROG key for three seconds or until the RED LED turns on.2. Press [VOL+] key.If you want to lock Volume and Mute to your TV, follow the steps below:Locking Volume/Mute Controls to your TVProgram the remote control for TV following these steps:1. Turn on your TV.5. Find the four (4) digit device code for your TV brand.keys in order.code will be retained.If the device code is invalid, the REDWhile in programming mode, if a key is not pressed within 15 seconds, the remote exits the programming mode and doesn't make any changes.Program the Remote to Control Your TVWarning: There is danger of explosion if the battery is mishandled or incorrectly replaced. Replace only with the same type of battery.Do not crush, puncture,dispose of in fire, short the external contacts, or expose to water or other liquids.Dispose of the battery in accordance with localregulations and instructions from your service provider.User Manual for TWC, Unified DTA Remote Control1. Press and hold the PROG key for three seconds or until the RED LED turns on.If you want to lock Volume and Mute to your DTA, follow the steps below:Locking Volume/Mute Controls to your DTA2. Press [VOL ] key.Caution: This remote control should be kept out of reach of the children under the age of 6.124691114571012831315。
有症状颈动脉狭窄的治疗策略
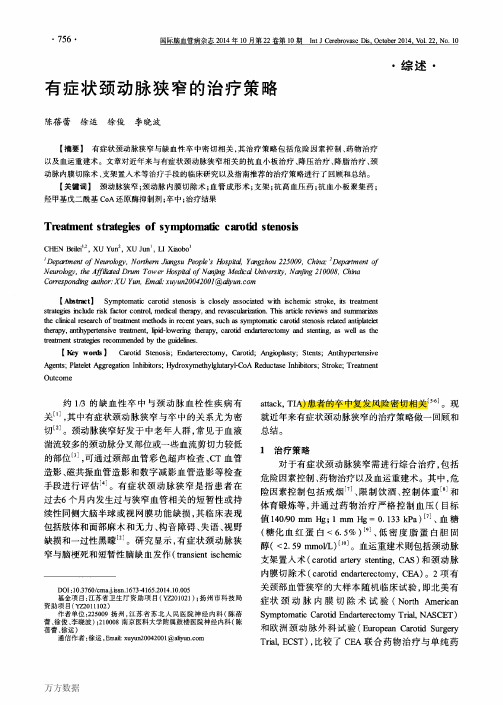
・756・垦匾堕鱼篮痘盘蠢!!!!生!!旦筮丝鲞筮!!翅!堕』£笪堂!坚箜!旦堡:Q£!Qb笪2Q!垒,№!:22,丛!:!Q有症状颈动脉狭窄的治疗策略陈蓓蕾徐运徐俊李晓波【摘要】有症状颈动脉狭窄与缺血件卒中密切相关,其治疗策略包括危险因素摔制、药物治疗以及血运重建术。
文章对近年来与有症状颈动脉狭窄相关的抗血小板治疗、降压治疗、降脂治疗、颈动脉内膜切除术、支架置入术等治疗手段的临床研究以及指南推荐的治疗策略进行了回顾和总结。
【关键词】颈动脉狭窄;颈动脉内膜切除术;血管成形术;支架;抗高血压药;抗血小板聚集药;羟甲基戊二酰基CoA还原酶抑制剂;卒中;治疗结果TreatmentstrategiesofsymptomaticcarotidstenosisCI-IENBeilei”,XUYun2,XUJunl,LIXiaob01。
DepartmentofNeurology,NorthernJia孵gsuPeople'sHospital,Yangzhou225009,China;2DepartmentofNeurology,theAffHiatedDrumTowerHospitalofNc矾jmgMedicdUniversity,Nanj新g210008,Ch自aaCorrespond#agauthor:XUYun,EmaiL"xuyun20042001@aliyun.com【Abstract】Symptomaticcarotidstenosisiscloselyassociatedwithischemicstroke,itstreatmentstrategiesincluderiskfactorcontrolmedicaltherapy,andrevascularization.Thisarticlereviewsandsummarizestheclinicalresearchoftreatmentmethodsinrecentyears,suchaSsymptomaticcarotidstenosisrelatedantiplatelettherapy,onflaypertensivetreatment,肇id—loweringtherapy,carotidendartereetomyandstenting,llSwellasthetreatments订al昭iesrecommendedbytheguidehes.【Keywords】CarotidStenosis;Endarterectomy,Carotid;Angioplasty;Stents;AntihypertensiveAgents;PlateletAggregationInh日0itors;Hydroxymethylglutaryl-CoAReductaseInhmitors;Stroke;TreatmentOutcome约1/3的缺血性卒中与颈动脉血栓性疾病有关¨。
HP Device Manager 4.7 管理员指南
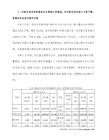
HP Device Manager 4.7©Copyright 2015–2017 HP Development Company, L.P.ARM 是 ARM Limited 的注册商标。
Java 是 Oracle 和/或其子公司的注册商标。
Linux® 是 Linus Torvalds 在美国和其他国家/地区的注册商标。
Microsoft、Windows 和 Windows Server 是 Microsoft Corporation 在美国和/或其他国家/地区的注册商标或商标。
Pentium 是 Intel Corporation 在美国和其他国家/地区的商标。
保密的计算机软件。
需要有 HP 颁发的有效许可证才能拥有、使用或复制。
与 FAR 12.211 和 12.212 相一致,依据供应商的标准商业许可将“商业计算机软件、计算机软件文档和用于商业单位的技术数据”许可给美国政府使用。
本文档中包含的信息如有更改,恕不另行通知。
随 HP 产品和服务附带的明确有限保修声明中阐明了此类产品和服务的全部保修服务。
本文档中的任何内容均不应理解为构成任何额外保证。
HP 对本文档中出现的技术错误、编辑错误或遗漏之处不承担责任。
第四版: 2017 年 7 月第一版:2015 年 8 月文档部件号: 834476-AA4用户输入语法项您必须输入用户界面的文本以等宽字体表示。
项目说明无括号或大括号的文本您必须完全依原样键入的项目<尖括号内的文本>您必须提供的值的占位符; 省略括号[方括号内的文本]可选项; 省略括号{大括号内的文本}您只能从其中选择一项的一组项目; 省略大括号|项目分隔符,用于分隔您只能从其中选一项的项目; 省略竖线...可以或必须重复的项目; 省略省略号iiiiv 用户输入语法项目录1 入门 (1)术语与定义 (1)存储库协议 (2)部署示例 (3)2HPDM Console 概述 (4)登录 HPDM Console (4)设备选项卡 (5)HPDM Gateway 选项卡 (6)显示设备属性 (7)基本资产信息 (7)收集完整的资产信息 (8)显示完整的设备资产信息 (8)3 设备发现 (9)自动注册(常规瘦客户机) (9)DNS 服务记录 (9)创建 DNS 服务记录 (9)故障排除 (10)设置静态域名(仅适用于 Windows) (10)自动注册(CoIP 零客户机) (10)使用 DNS 服务记录 (10)使用 DHCP 供应商类别选项 (11)搜索设备 (12)使用 Walking With IP Range(用 IP 范围扫描)的方法 (12)配置 IP 范围 (12)使用 Walking With IP List(用 IP 列表扫描)方法 (12)手动注册设备 (13)手动注册多个设备 (13)4 任务和任务模板 (14)任务模板 (14)创建任务模板 (14)将任务模板添加到“收藏夹”列表 (15)v导出任务模板 (15)导入任务模板 (15)从负载中生成模板 (15)复制 Deploy Image 模板以用于不同的 OS 类型 (16)模板序列 (16)基本模板序列 (16)高级模板序列 (16)任务 (17)执行任务 (17)任务状态图标 (18)任务参数 (18)任务延迟 (19)显示任务属性 (19)暂停任务 (19)继续任务 (20)重新发送任务 (20)取消任务 (20)删除任务 (20)显示任务日志 (20)显示任务的成功率 (21)打开用于远程控制的 VNC 查看器 (21)打开结果模板 (21)查看所有用户的任务 (21)任务规则 (21)添加新规则 (21)5 设备管理 (23)查看设备 (23)删除设备 (23)分组设备 (24)使用 DHCP 标签设置分组信息 (24)切换到手动分组 (24)添加新手动分组 (24)动态分组 (24)创建新动态分组方案 (25)切换到动态分组 (25)快速搜索 (25)过滤设备 (25)创建新的设备过滤器 (25)vi编辑设备过滤器 (25)安全过滤器 (26)检查网络连接状态 (26)远程控制设备 (27)电源管理 (27)管理常规瘦客户机 (27)更改设备的主机名 (27)捕获和部署连接 (27)克隆和部署设置 (28)应用自定义设置 (28)管理文件和注册表设置 (29)捕获文件 (30)部署文件 (30)删除文件 (31)管理设备注册表设置 (31)克隆注册表设置 (31)添加、编辑和删除注册表设置 (31)远程执行命令 (32)远程执行 Windows 脚本 (33)暂停 _File and Registry 任务 (33)添加或删除程序记录 (33)运行脚本 (33)使用 SCEP 注册证书 (34)管理 PCoIP 零客户机 (34)捕获连接 (34)部署连接 (35)更新固件 (35)6 映像操作 (36)不使用 PXE 的映像 (36)捕获不使用 PXE 的映像 (36)不使用 PXE 的映像捕获期间保留的设置 (37)部署不使用 PXE 的映像 (37)不使用 PXE 的映像部署期间保留的设置 (38)使用 PXE 的映像 (38)创建 PXE Deploy 模板 (39)导入映像文件 (39)将 Deploy Image 模板转换为 PXE Deploy 模板 (39)复制现有 PXE Deploy 模板,以用于不同的 OS (39)vii将设备配置为从 PXE 引导 (40)本地更改引导顺序 (40)远程更改引导顺序 (40)为 PXE 映像配置 DHCP 服务器 (42)DHCP 服务器与 HPDM Server 安装在不同的物理服务器上 (42)DHCP 服务器与 HPDM Server 安装在同一物理服务器上 (42)为 PXE 映像配置 Linux DHCP 服务器 (43)为 PXE 映像配置路由器 (43)为 PXE 映像在传统 Neoware 设备上配置 BIOS 设置 (44)部署映像 (44)故障排除 (44)7 存储库管理 (46)配置 HPDM Master Repository (46)配置 HPDM Child Repository (46)删除 HPDM Child Repository (46)导出库 (47)导入库 (47)同步库 (47)内容管理 (47)查看详细的相关文件信息 (48)从 HPDM Master Repository 删除内容 (48)从 Files Captured(已捕获文件)类别下载内容 (48)库映射 (48)批处理映射 (48)每个设备映射 (48)8 安全性管理 (49)用户管理 (49)添加用户 (49)删除用户 (49)向组分配用户 (49)更改用户的密码 (49)为用户分配安全过滤器 (50)添加组 (50)向组分配权限 (50)向组分配用户 (50)viii使用 LDAP 和 Active Directory 进行用户身份验证 (51)配置 (51)导入用户和组 (52)身份验证管理 (53)密钥管理 (54)HPDM Gateway 访问控制 (55)9 报告管理 (56)添加报告 (56)编辑报告 (56)删除报告 (56)生成报告预览 (57)10HP Update Center (58)生成任务模板 (58)配置 HP Update Center 代理设置 (58)11HPDM Server Backup and Restore Tool (60)备份 HPDM Server (61)恢复 HPDM Server (62)12HPDM Port Check Tool (63)13HPDM Archive Tool (64)14 分组工具 (65)在自定义脚本中使用 groupingtoolex 命令 (65)示例命令 (65)定期调用自定义脚本 (65)示例程序 (66)15HPDM Agent 轮询和错误日志记录 (67)HPDM Agent 轮询 (67)错误日志记录 (67)HPDM Agent 日志记录 (67)HPDM Gateway 日志记录 (67)ixHPDM Server 和 HPDM Console 日志记录 (68)HPDM Master Repository Controller 日志记录 (68)附录 A 任务模板参考 (69)文件和注册表 (69)Agent (69)连接 (69)映像 (70)操作 (70)设置 (70)模板序列 (71)附录 B 端口参考 (72)HPDM Console 端口(入站) (72)HPDM Console 端口(出站) (72)HPDM Server 端口(入站) (73)HPDM Server 端口(出站) (73)HPDM Gateway 端口(入站) (74)HPDM Gateway 端口(出站) (74)HPDM Agent 端口(入站) (75)HPDM Agent 端口(出站) (76)存储库端口(入站) (77)存储库端口(出站) (78)索引 (80)x1入门要查找最新的 HPDM 软件、管理员指南(本文档)、白皮书和版本说明:访问 ftp:///pub/hpdm。
Dell Wyse Management Suite 1.4 部署指南说明书
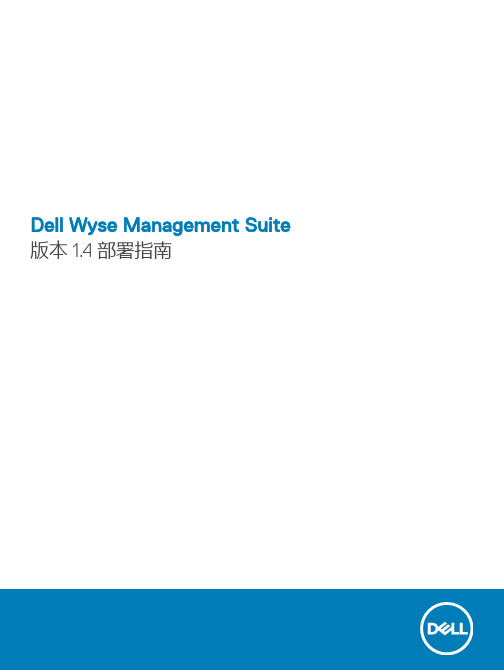
Dell Wyse Management Suite 版本 1.4 部署指南注、小心和警告注: “注”表示帮助您更好地使用该产品的重要信息。
小心: “小心”表示可能会损坏硬件或导致数据丢失,并说明如何避免此类问题。
警告: “警告”表示可能会造成财产损失、人身伤害甚至死亡。
© 2019 Dell Inc. 或其子公司。
保留所有权利。
Dell、EMC 和其他商标是 Dell Inc. 或其附属机构的商标。
其他商标可能是其各自所有者的商标。
2019 - 05Rev. A001 简介 (4)2 硬件要求 (5)3 Wyse Management Suite 部署架构 (6)4 部署详细信息 (7)在单个服务器上部署以支持 50,000 个瘦客户端设备 (7)在单个服务器上部署以支持 120,000 个瘦客户端设备 (7)支持 T eradici 设备的部署详细信息在单个服务器上部署以支持 5000 个 Teradici 设备部署以支持 5000多个 T eradici 设备 (8)单独数据库服务器上的 Wyse Management Suite (11)5 自定义端口配置 (13)更改 T omcat 服务端口 (13)更改 MQTT 端口 (14)更改 MariaDB 端口 (14)更改 MongoDB 数据库端口 (14)远程存储库 (15)管理 Wyse Management Suite 存储库服务 (21)6 将 Wyse Management Suite 版本 1.3 升级到 1.4 (22)7 维护 (26)数据库备份 (26)数据库还原 (26)目录3简介Dell Wyse Management Suite 是新一代管理解决方案,允许您集中配置、监控、管理和优化 Dell Wyse Thin Client。
新版 Suite 提供出色的功能、性能以及易用性,让您可以更轻松地部署和管理 Thin Client。
AllFusion Model Manager Release Summary r7 用户说明说明
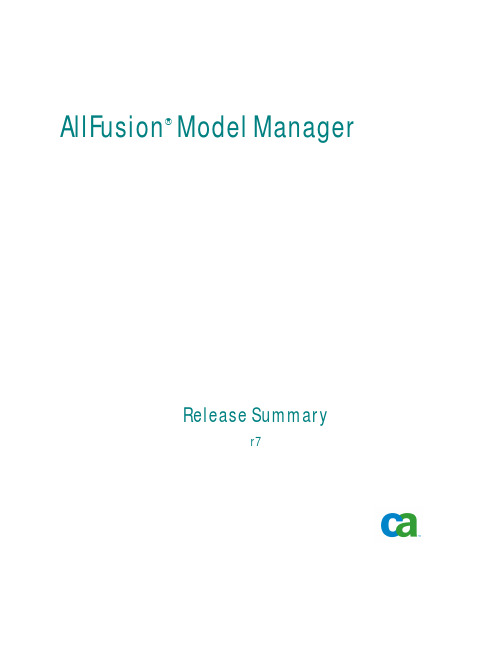
AllFusion® Model ManagerRelease Summaryr7This documentation and related computer software program (hereinafter referred to as the “Documentation”) is for the end user’s informational purposes only and is subject to change or withdrawal by Computer Associates International, Inc. (“CA”) at any time.This documentation may not be copied, transferred, reproduced, disclosed or duplicated, in whole or in part, without the prior written consent of CA. This documentation is proprietary information of CA and protected by the copyright laws of the United States and international treaties.Notwithstanding the foregoing, licensed users may print a reasonable number of copies of this documentation for their own internal use, provided that all CA copyright notices and legends are affixed to each reproduced copy. Only authorized employees, consultants, or agents of the user who are bound by the confidentiality provisions of the license for the software are permitted to have access to such copies.This right to print copies is limited to the period during which the license for the product remains in full force and effect. Should the license terminate for any reason, it shall be the user’s responsibility to return to CA the reproduced copies or to certify to CA that same have been destroyed.To the extent permitted by applicable law, CA provides this documentation “as is” without warranty of any kind, including without limitation, any implied warranties of merchantability, fitness for a particular purpose or noninfringement. In no event will CA be liable to the end user or any third party for any loss or damage, direct or indirect, from the use of this documentation, including without limitation, lost profits, business interruption, goodwill, or lost data, even if CA is expressly advised of such loss or damage.The use of any product referenced in this documentation and this documentation is governed by the end user’s applicable license agreement.The manufacturer of this documentation is Computer Associates International, Inc.Provided with “Restricted Rights” as set forth in 48 C.F.R. Section 12.212, 48 C.F.R. Sections 52.227-19(c)(1) and (2) or DFARS Section 252.227-7013(c)(1)(ii) or applicable successor provisions.Copyright © 2006 CA. All rights reserved.All trademarks, trade names, service marks, and logos referenced herein belong to their respective companies.ContentsChapter 1: Changes to Existing FeaturesDatabase and Model Conversion Management..................................................1-1 Services Menu Replaces ModelMart Menu......................................................1-2 Change Management Functionality Changed....................................................1-2 Review Changes uses the Complete Compare Functionality......................................1-2 Refresh uses the Complete Compare Functionality...............................................1-2 Version Manager uses the Complete Compare Functionality......................................1-3 Renamed Subject Areas to Submodels..........................................................1-3 Complete Compare Functionality Replaces the (ModelMart) Merge Manager.......................1-3 Version Dependency Removed.................................................................1-4 ModelMart Synchronizer Removed.............................................................1-4 Change in Database Support Policy.............................................................1-4 Additional Database Version Support.......................................................1-4 Databases No Longer Supported...........................................................1-4 Dropped Support for Database Versions....................................................1-41 Changes to Existing FeaturesThis chapter documents changes made to existing features and includes a list offeatures removed from the product for r7. A number of changes have been madeto the user interface to improve functionality and consistency. The changes areoutlined as follows:Database and Model Conversion ManagementServices menu replaces the ModelMart menuChange Management Functionality ChangedReview Changes uses the Complete Compare functionalityRefresh uses the Complete Compare functionalityVersion Manager uses the Complete Compare functionalityRenamed Subject Areas to SubmodelsComplete Compare functionality replaces the (ModelMart) Merge ManagerVersion Dependency RemovedModelMart Synchronizer RemovedChange in Database Support PolicyDatabase and Model Conversion ManagementIf you previously worked with AllFusion Model Manager (ModelMart), probablythe most important task is preserving the database structure and the contents ofyour ModelMart 4.1.4 database. AllFusion MM r7 includes a built-in conversionutility that the administrator uses to perform the conversion. The conversionutility does all the work of transforming the old into the new database and itconverts the AllFusion ERwin DM and AllFusion Process Modeler models to thenewest version as well. More information about using the conversion utility isincluded in the AllFusion Model Manager r7 Administrator Guide.Services Menu Replaces ModelMart MenuServices Menu Replaces ModelMart MenuThe client-server functionality available in the AllFusion Modeling Suite nowuses the broader term "Services." Features that formerly appeared under the"ModelMart'" menu item now appear under a "Services" menu.Change Management Functionality ChangedThe addition of the Action Log feature, and implementation of CompleteCompare have replaced the Change Control Manager user interface forAllFusion ERwin DM clients.Note: The Change Control Manager is still available for AllFusion ProcessModeler clients.If you make changes to a model checked out of AllFusion MM, and then try tosave the model to the mart, you are reminded to first use the Action Log toreview your changes. If no changes conflict with the version in the mart, yourmodel is saved. In earlier versions you were prompted to review changes usingthe Change Control Manager.If conflicts between your local model and the one in the mart are detected duringthe save process, the Complete Compare - Difference Reconciliation dialog isdisplayed to help you resolve the differences before committing the changes tothe mart.Review Changes uses the Complete Compare Functionality When you choose the Review Changes from the Services menu and changes aredetected, the Right Model Pane of Complete Compare is displayed. In earlierversions you were prompted to review changes using the Change ControlManager.Refresh uses the Complete Compare FunctionalityWhen you choose Refresh from the Services menu and changes are detected, theComplete Compare interface is used to display and reconcile the changes. Inearlier versions you were prompted to review changes using the Change ControlManager.Version Manager uses the Complete Compare FunctionalityVersion Manager uses the Complete Compare Functionality When you choose Diff to compare two model versions in the AllFusion VersionManager, the Right Model Pane of the Complete Compare interface is used todisplay and reconcile the differences. In earlier versions you were prompted toreview changes using the Change Control Manager.Renamed Subject Areas to SubmodelsAllFusion MM is now using the term Submodel instead of the ERwin termSubject Area. The corresponding item on the Services menu has been changed,and the dialog has been renamed to highlight the distinction between subjectareas and submodels. This is meant to highlight the distinction that opening aSubmodel from the AllFusion MM Open dialog just gives you access to thatsubmodel, and restricts access to other subject areas of that model in the ERwinediting session. There is no real inherent difference between subject areas andsubmodels, so whether you used the ERwin dialog to edit subject areas, or theAllFusion MM dialog on the Services menu to edit Stored Displays, the results ofeach do show up in the other.As we move into future releases, we expect submodels to become betterdifferentiated from Subject Areas by having more capabilities that are unique tothem.Complete Compare Functionality Replaces the (ModelMart) Merge ManagerIn previous versions, the Merge Manager presented a series of dialogs that letyou merge the current model with another model from the mart, or with a localmodel. New functionality in the Complete Compare wizard expands on thisfunctionality. The Complete Compare Wizard does the following:Load models from a variety of sources.Merge into an empty model.Merge into an existing model and use the Save As feature to create a newmodel.Lets you skip pages of the wizard, for instance, if you want to set up filters,you can.Lets you compare any combination of logical/physical, logical-only, andphysical-only models.Version Dependency RemovedVersion Dependency RemovedIn earlier releases of the AllFusion Modeling Suite, the release version ofAllFusion ERwin Data Modeler and AllFusion Model Manager had to beidentical. With r7, this dependency has been removed. Although we recommendthat you install the latest service pack for all products, the requirement of havingall products installed to the same service pack level no longer exists.ModelMart Synchronizer RemovedThe ModelMart Synchronizer feature has been removed from AllFusion MM.Previously it synchronized AllFusion ERwin DM and AllFusion PM modelswhile these models were stored in AllFusion MM. There is no longer adependency on AllFusion Model Manager in order to accomplishsynchronization. Synchronization is now done within AllFusion ERwin DM andAllFusion PM. For more information, see the AllFusion ERwin DM ReleaseSummary or the AllFusion PM Release Summary.Change in Database Support PolicyThe following are the changes in the database support policy for AllFusionModel Manager r7:Additional database version supportDatabases no longer supportedAdditional Database Version SupportAllFusion Model Manager has added support for additional databases. TheAllFusion MM Connection Manager dialog now supports the followingadditional database:Microsoft SQL Server 2005Databases No Longer SupportedThe AllFusion Model Manager has dropped support for some databases. TheAllFusion MM Connection Manager dialog no longer displays the followingdatabase:Informix。
MBN_10447_2010-05_EN_Quality Management Standard-Elektrics-Elektronics for Mercedes-Benz Cars_nng
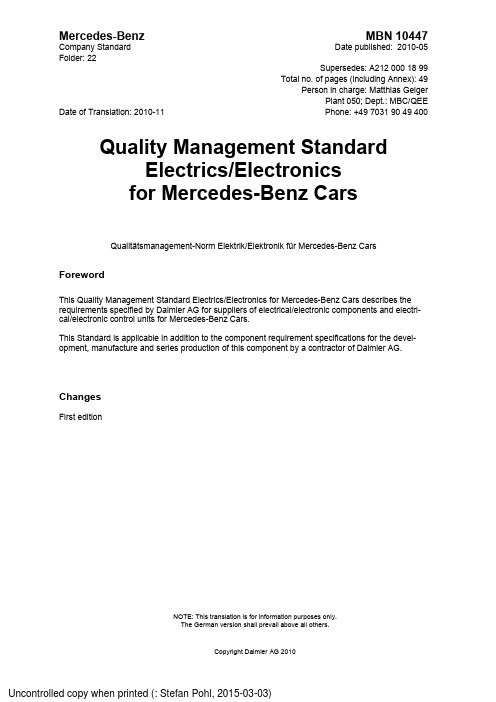
10447 Mercedes-Benz MBN Company Standard Date published: 2010-05Folder: 22Supersedes: A212 000 18 99Total no. of pages (including Annex): 49Person in charge: Matthias GeigerPlant 050; Dept.: MBC/QEEDate of Translation: 2010-11 Phone: +49 7031 90 49 400Quality Management StandardElectrics/Electronicsfor Mercedes-Benz CarsQualitätsmanagement-Norm Elektrik/Elektronik für Mercedes-Benz CarsForewordThis Quality Management Standard Electrics/Electronics for Mercedes-Benz Cars describes therequirements specified by Daimler AG for suppliers of electrical/electronic components and electri-cal/electronic control units for Mercedes-Benz Cars.This Standard is applicable in addition to the component requirement specifications for the devel-opment, manufacture and series production of this component by a contractor of Daimler AG.ChangesFirst editionNOTE: This translation is for information purposes only.The German version shall prevail above all others.Copyright Daimler AG 2010Contents1Scope (5)2Normative references (6)3Terms and definitions (7)3.1List of abbreviations (7)3.2Nomenclature (8)4General requirements (9)4.1Contacts at Daimler AG (9)4.2Contacts at the supplier and its sub-suppliers (10)4.3Key processes (10)5Preventive maturity level management (11)5.1Start of preventive maturity level management (11)5.2Scope (11)5.3Tracking of sub-supplier maturity level (12)5.4Changes following start of production (12)5.4.1Process and sub-process relocation (12)5.4.2Replacement or exchange of machines or equipment (12)5.4.3Change of a sub-supplier (13)6Detection of anomalies (14)7Process capability and product reliability (15)7.1Proof of machine and process capability for SMT processes (15)7.1.1Machine and process capability of paste printer (15)7.1.2Machine capability placement machines (15)7.1.3Verification of solder profile (16)7.2Proof of reliability of the assembly and connection technology (16)7.3Proof of reliability of the devices used (16)7.4Board bending test (17)7.5Requalification (18)7.5.1Complete repeat of the environmental and life tests (18)7.5.2Q-Review Environment E/E (18)8Manufacturing processes for electronic components (20)8.1Storage (20)8.1.1Moisture sensitive devices (20)8.2Printed circuit board magazines (21)8.3Transportation of devices and components (21)8.4Soldering paste printing (21)8.4.1Initial part approval during series production (21)8.4.2Soldering paste (21)8.4.3Paste printer (22)8.4.4Cleaning of the stencil (22)8.4.5Cleaning of circuit boards following soldering paste printing (22)8.4.6Mechanical stress in double-sided PCB assembly (23)8.5PCB assembly (23)8.5.1Initial part approval (23)8.5.2Reel change (23)8.5.3Mechanical stress (23)8.5.4Process control (23)8.5.5Maintenance (23)8.6Assembly and connection technology (24)8.6.1Reflow soldering (24)8.6.1.1Machine malfunctions (25)8.6.1.2Temperature profile (25)8.6.2Press-fit technology (25)8.6.3Selective soldering with mini-wave (26)8.6.3.1Flux (26)8.6.3.2Temperature pretreatment and temperature gradient (26)8.6.3.3Temperature monitoring (27)8.6.3.4Machine malfunctions (27)8.6.3.5Solder residue (27)8.6.3.6Solder bath (27)8.6.3.7Solder filling level (27)9Rework (28)10Test technology in series production (29)10.1Inspection of soldered joints (29)10.1.1Inspection of paste printing (29)10.1.2Inspections after reflow soldering (29)10.1.3Inspections after selective soldering (30)10.1.4Manual visual inspections (30)10.2In-circuit test (30)10.3Contacting of components (31)10.4End-of-line test (31)10.5Test parameters (32)10.6Mechanical interfaces (32)10.7Product audit (32)10.7.1Temperature cycle test (33)10.7.2Additional component-specific tests (33)10.7.3Changes (34)10.8Early defect detection (34)10.8.1Realization of early defect detection (34)10.8.2Active run-in (34)10.9Test coverage analysis (35)10.10Evaluation and reporting of internal test results (36)10.11Haptic measurements (36)10.12Testing of function, switch and controls illumination (37)10.13Noise testing (37)10.14Process documentation and process records (38)10.14.1Soldering paste printing (38)10.14.2Placement machines (38)10.14.3Reflow soldering (38)10.14.4Selective soldering with mini-wave (38)10.14.5Rework (39)10.14.6Test parameters (39)11Mechanical manufacturing processes (40)11.1Circuit board separation (40)11.1.1Milling (40)11.1.2Punching (V-cutting) (40)11.1.3Sawing (40)11.1.4Laser cutting (41)11.2Assembly and screw-fastening processes (41)11.3Zero Insertion Force (ZIF) connectors (41)11.3.1Manual joining of zero insertion force connectors (42)11.3.2Semi or fully automatic joining of zero insertion force connectors (42)11.3.3Testing of the connection of zero insertion force connectors (42)11.3.4Opening of the plug connection of zero insertion force connectors (42)12Traceabilty of devices and components (43)12.1Incoming goods (43)12.2PCB assembly (43)12.3Tests (44)12.4End-of-line test (44)12.5Outgoing goods (44)12.6Rework (44)13ESD (45)13.1ESD protection measures in electronics production (45)13.2Personnel grounding (45)13.3Rework (45)14Flashing of components (46)14.1Handling (46)14.2Contacting and flashing (46)14.3Testing and traceability of flashed components (46)14.4Capacity of the flashing process (47)15Failure analysis (48)15.1Analysis reports (48)15.2Priority failures (48)15.3NTF failures (complaints) (48)15.4Failure analysis on site (48)16On-site support (49)16.1Professional requirements for staff (49)16.2Time-related requirements (49)16.3Other requirements (49)1 ScopeThis Quality Management Standard Electrics/Electronics applies irrespective of the model to all electri-cal/electronic components in general.2 Normative referencesMB Special Terms Mercedes Benz Special Termsof Electronic AssembliesANSI/IPC-A-610D AcceptabilityIPC/JEDEC J-STD-033B.1 Handling, Packing, Shipping and Use of Moisture/ReflowSensitive Surface Mount DevicesDIN EN ISO 9453 Soft Solder Alloys – Chemical Compositions and FormsA2110039899 Design Rules for E/E ComponentsDIN EN 61340-5-1 Protection of Electronic Devices from Electrostatic Phenom-ena — General RequirementsIEC/TR 61340-5-2 Protection of Electronic Devices from Electrostatic Phenom-ena – User GuideDIN EN 61340-4-5 Standard Test Methods for Specific Applications – Methodsfor Characterising the Electrostatic Protection of Footwearand Flooring in Combination with a PersonDIN EN 61340-4-3 Standard Test Methods for Specific Applications – Footwear AEC-Q100 Stress Qualification for Integrated CircuitsAEC-Q101 Stress Test Qualification for Discrete SemiconductorsAEC-Q200 Stress Test Qualification for Passive ComponentsAEC-Q004 Zero Defects Guideline (Draft version)ANSI/IPC J-STD-001D Requirements for Soldered Electrical and Electronic Assem-bliesMBN 10448 Field Failure Analysis3 Terms and definitions3.1 List of abbreviationsTwo-dimensional2DThree-dimensional3DAEC Automotive Electronic Council (body for quality standards in the automotive indus-try)InspectionOpticalAutomatedAOI(Ausführungsvorschrift)regulationAVImplementationBGA Ball Grid Array componentsBR Vehicle model series (Baureihe)cmk Short-term process capabilitycapabilityprocessLong-termcpksupplyspecification (Liefervorschrift)Daimler-BenzDBLDS Identification and documentation of safety relevancedocumentation of certification relevanceandIdentificationDZE/E component Electrical/electronic componentProgrammable Read-Only MemoryEEPROM ElectricallyErasableX-rayspectroscopyEnergy-dispersiveEDXEOL End Of Line testOverStressEOSElectricalDischargeElectroStaticESDFMEA Failure Mode and Effects AnalysisLevelingAirHotHALHIL Hardware In the LoopHardWareHWStandardizationISOforOrganisationInternationalCircuitsIC IntegratedIn-Circuit-TestICTspecifications (Komponentenlastenheft)requirementComponentKLHMBN Mercedes-Benz standard (Mercedes-Benz Norm)SystemDevelopmentMercedes-BenzMDSInterfaceMan-MachineMMIMSD Moisture Sensitive DeviceLevelSensitiveMSLMoistureSystemProductionMercedes-BenzMPSMTTF Mean Time To FailureNTF No Trouble Foundprocess and product approvalPPAProductioncapabilityprocessPreliminaryppkPRG Product maturity level (Produkt-Reifegrad)GateQGQualityQualityManagementQMStatusQ-Status QualityMemoryAccessRandomRAMMemoryOnlyReadROMTemperatureRoomRTUnitControlCUMountedTechnologySurfaceSMTSOP Start of ProductionSoftWareSWTechnologyHoleThroughTHT3.2 NomenclatureBelow, electrical/electronic components and electrical/electronic control units are termed "components" for the reader’s convenience.Below, the contractor of Daimler AG is termed "supplier".Below, the sub-components of components such as circuit boards, electronic devices (e.g. controllers, transceivers, micromechanical semiconductors) and mechanical units (e.g. housings) are termed "de-vices" for the reader’s convenience.Below, requirements for documentation and the recording of data are specified. In this context, "docu-ment" refers to instructions and specifications (e.g. work instructions, process descriptions, etc). The term "record" refers to evidential data (e.g. completed checklists, audit evidence, etc).4 GeneralrequirementsFor safety requirements, homologation and quality, the existing statutory requirements and laws shall be complied with. In addition, the relevant requirements of Daimler AG apply.All materials, procedures, processes, components, and systems shall conform to the current regulatory (governmental) requirements regarding regulated substances and recyclability.This Quality Management Standard Electrics/Electronics makes reference to applicable laws, standards and regulations etc. The supplier shall be responsible for compliance with all laws, standards and regula-tions and for the development and production of the component in line with the state of the art. In this con-text, due consideration shall be given to the fact that the vehicles of Daimler AG containing this compo-nent are sold worldwide.This Quality Management Standard Electrics/Electronics makes reference to other applicable documents of the component requirement specifications (KLH) (specifications, test methods, implementation regula-tions, instructions of Daimler AG). Where this Quality Management Standard Electrics/Electronics contains deviating or contradictory information compared with other standards, specifications or implementation regulations, the more severe specification shall apply. In case of doubt, clarifying agreements following discussions with Daimler AG Quality Management shall be set down in writing.The supplier shall supply conforming products to Daimler AG, and the supplier shall maintain the zero-defect target.If the supplier is aware of measures or alternatives serving to increase quality or reliability, the supplier shall notify these to Daimler AG Quality Management.All information and documents associated with the development, manufacture and production of the com-ponent shall be treated confidentially.4.1 Contacts at Daimler AGThe responsible component developer and other contacts at Daimler AG are listed in the component re-quirement specifications (KLH).Mercedes-Benz Cars Quality Management is divided into two units:- Preventive Quality Management (Prevention) and- Quality Management Production in the worldwide Daimler assembly, body, paintwork and stamp-ing plants (e.g. Sindelfingen, Bremen, Tuscaloosa, South Africa etc.).During the development phase (requirement specification phase up to the launch of the component in production), a staff member from Prevention is the responsible quality contact for the supplier. Together with the responsible staff member from Prevention, the supplier shall hold coordination discussions re-garding quality management requirements. The supplier shall seek approval from the responsible staff member from Prevention for any deviations from these quality management requirements.During the production phase (launch of component in production up to discontinuation of production), a Quality Management staff member from each assembly, body, paintwork and stamping plant is the re-sponsible quality contact for the supplier. The supplier shall seek approval for all changes to the compo-nent or production process during the production phase from the responsible Quality Management staff member from the assembly, body, paintwork and stamping plants. In the event of deviations from the re-lease status of the component, the supplier shall present appropriate measures and samples and have any changes approved.Any deviation from the requirements of this Quality Management Standard Electrics/Electronics are sub-ject to the written approval of Daimler AG Quality Management.4.2 Contacts at the supplier and its sub-suppliersThe supplier shall submit an organizational diagram to Daimler AG Quality Management showing all per-sons responsible for the project and their functions.The supplier shall reveal the complete supply chain of devices for the project to Daimler AG Quality Man-agement. In this process, the supplier shall document the scope of supply and supplier name of each de-vice.4.3 Key processesTo facilitate the successful implementation of the project, the supplier shall provide evidence of docu-mented process structures for the following key processes during the concept presentation:1. Requirements analysis process2. Test strategy process3. Configuration and change management process4. Problem analysis process5. Project management5 Preventive maturity level managementThe objective of preventive maturity level management is to recognize quality-related problems and defi-cits concerning the product and/or production process as early as during the development phase of the component and to be able to initiate countermeasures. Timely completion of the project and defect-free implementation of all specified functions are the top priorities for Daimler AG.The supplier shall document and maintain a preventive maturity level management system. As part of this system, the supplier shall determine and record characteristic data (metrics, process capability indices, inspections, etc.).In this context, all company units of the supplier involved with the product creation process shall be sub-ject to the maturity level management system.Assessment of the maturity level shall be based on the specified quality targets and quality criteria throughout the product and process development process.The supplier shall document compliance with and fulfillment of all requirements from the component re-quirement specifications (KLH) and this Standard.To track all activities during development, the supplier shall maintain a list of open issues, and grant Daim-ler AG Quality Management access to this list on request.The supplier shall submit regular reports to Daimler AG Quality Management regarding maturity level pro-gress. The supplier shall document maturity level reports in writing. The supplier shall record the maturity level reports for the Quality Gates (according to MDS) and submission of A, B, C, D and PPF samples in writing.5.1 Start of preventive maturity level managementThe supplier shall initiate preventive maturity level management at the time of project start - immediately following the commencement of hardware and software development and the start of the production proc-ess.5.2 ScopeThe supplier shall coordinate and document the scope of preventive maturity level management with Daimler AG Quality Management.The preventive maturity level tracking during the product creation process includes the monitoring of the degree of fulfillment of all requirements. In this context, the supplier shall document and record the (func-tional and non-functional) requirements for the component and the production process during the devel-opment phase of the component.The supplier shall carry out an assessment on the basis of the degree of implementation of the require-ments at the relevant project date. The maturity level is divided into four stages:- Requirement not implemented by the deadline- Requirement is in the process of being implemented- Requirement has been implemented by the deadline- Requirement has been implemented and tested successfully by the deadline5.3 Tracking of sub-supplier maturity levelThe supplier shall document and implement a preventive maturity level management system at all sub-supplier companies involved in the project (Tier 2, Tier 3, …).The supplier shall inform Daimler AG Quality Management of the status of the preventive maturity level management if there is a risk of the sub-suppliers involved in the project failing to reach the project objec-tive.On request, the supplier shall grant Daimler AG Quality Management access to records concerning the maturity level management of the sub-suppliers involved in the project.5.4 Changes following start of productionAny changes to the component or an existing manufacturing process shall be subject to the approval of Daimler AG Quality Management and be approved using a PPA process.The supplier shall qualify any change, e.g. in the event of changes to devices (material or manufacturing process of the device) or in the manufacturing process of the component. The supplier shall provide evi-dence of and document qualification in accordance with the component requirement specifications.Deviations from a complete qualification by the supplier shall be subject to the approval of Daimler AG Quality Management.Qualification shall be carried out using components manufactured on the production equipment at the se-rial production location.The documentation of changes shall be coordinated with Daimler AG Quality Management.The supplier shall adhere to a previously defined time frame for pre-advice to Daimler AG Quality Man-agement.In the cases indicated below, the supplier shall inform the following Daimler AG units: Quality Manage-ment, Development, Purchasing and Logistics.5.4.1 Process and sub-process relocationIn the case of any type of process and sub-process relocation, the supplier shall inform Daimler AG Qual-ity Management no later than 9 months before the intended implementation of the change. The supplier shall submit a relocation scenario and seek the approval of Daimler AG Quality Management for such scenario.This time frame also applies to the outsourcing of processes or sub-processes to sub-suppliers.5.4.2 Replacement or exchange of machines or equipmentIn the case of the replacement or exchange of machines or equipment or other systems, the supplier shall inform Daimler AG Quality Management no later than 3 months before the intended implementation of the change.5.4.3 Change of a sub-supplierIn the case of a change of a sub-supplier or manufacturer of a device of the component, the supplier shall submit a change scenario to Daimler AG Quality Management and seek the approval of Daimler AG Qual-ity Management for such scenario. The supplier should inform Daimler AG Quality Management no later than 6 months before the intended implementation of the change.6 Detection of anomaliesThe statistical detection of anomalies is intended for the detection of unusual features in the functionality or measurement parameters. These may be anomalies which lie within the specification limits provided, but are unusual compared to other components. The anomalies may point towards pre-damage to the component.In order to ensure the process capability and product reliability, the supplier shall document and use a method for the detection of anomalies, and provide evidence by means of records.To verify the process capability and product reliability, the supplier shall use this method, starting with the manufacture of initial samples, and create records. Evidence shall be provided no later than at the time of submission of the initial sample documentation.7 Process capability and product reliabilityIn accordance with VDA 2, the supplier shall provide evidence of the process capabilities for its production processes.For the deadline and the required values for the process capabilities, refer to MBST.At the time of submission of the initial samples, the supplier shall document the final evidence of the proc-ess capabilities and product reliabilities required.The initial samples shall be manufactured on production equipment and selected randomly.The supplier shall have any deviations from these specifications approved by Daimler AG Quality Man-agement.7.1 Proof of machine and process capability for SMT processesWithin the framework of the zero-defects strategy in relation to the customer, the supplier shall make every effort to prevent and detect nonconformances. From the point of view of customer satisfaction and with a view to ensuring the quality of the components, it is essential that nonconformances are detected as early as possible and eliminated. The focus shall therefore be on the process capability of the supplier's manufacturing process. This includes the determination of the ongoing process capability, the control of the production process and continuous process improvement.The supplier shall supply regular evidence of the process capabilities of production as a whole and each production process and maintain the appropriate records.7.1.1 Machine and process capability of paste printerThe supplier shall check the machine capability once every year and maintain the pertinent records.Evidence of the machine capability of the paste printer can be provided by means of a reference stencil. The relevant parameters for this purpose are the positioning accuracy in the x and y direction of the solder deposit.The supplier shall check the process capability of the paste printer with the product-specific original stencil and maintain appropriate records. During this process, the supplier shall document reference points and determine their positioning accuracies in x and y position as well as the volume. To do so, the supplier may use the paste AOI provided that the AOI measuring data can be analyzed.7.1.2 Machine capability placement machinesThe supplier shall check the machine capability every other year and maintain the pertinent records.The supplier shall check the machine capability using a glass board and glass devices or ceramic pads and maintain appropriate records. To prove capability, the supplier shall document the critical SMD shapes and test these.7.1.3 Verification of solder profileThe supplier shall verify that the solder profile determined allows each solder joint to reach the required soldering temperature and the required temperature profile. The supplier shall maintain appropriate re-cords.The supplier shall verify that "thermally critical" devices on the circuit board are not overheated. The sup-plier shall maintain appropriate records.The supplier shall observe the specifications of the board, device and soldering paste manufacturers, and provide evidence of compliance. The temperature profile shall therefore be recorded with the printed com-ponent circuit board.7.2 Proof of reliability of the assembly and connection technologyThe supplier shall document the development progress at the time of each delivery of sample parts.At the time of submission of the initial samples, the supplier shall perform a full qualification on the basis of the requirements of the KLH and provide the appropriate evidence.The supplier shall coordinate the number and scope of the tests with Development and Daimler AG Qual-ity Management and document the results.In order to allow the impact of changes on the component to be assessed, the supplier shall document a comparison of measuring results before and after the intended change.Qualification shall be carried out using components manufactured on the series production equipment. 7.3 Proof of reliability of the devices usedOn delivery, the supplier shall provide evidence of device qualification.For ICs, the supplier shall provide evidence of the device qualification in accordance with AEC-Q100, for discrete components in accordance with AEC-Q101, and for passive components in accordance with AEC-Q200.To achieve the zero-defects strategy, the supplier shall document the methods as per AEC-Q004 and provide evidence of the records to Daimler AG Quality Management.The supplier shall have any deviations from these specifications approved by Daimler AG Quality Man-agement.7.4 Board bending testThe supplier shall ensure that soldered circuit boards or devices cannot be damaged as a result of me-chanical stresses. Excessive mechanical stresses result in the danger of the board or devices becoming pre-damaged due to microcracks. The supplier shall support the PCB boards using an appropriate fixture.By means of a board bending test, the mechanical stress to which a soldered circuit board is exposed during the production process can be determined.The supplier shall perform a bending test for the following production steps on the component-specific board and maintain the relevant records:- Paste printer (only for double-sided boards)- SMD placement machines- ICTseparatorboard- Circuit- Press-fit process for contacts- Press-fit and assembly fixtures and jigs for installing boards in a housing- Transport systems, including gripping devices.The supplier shall repeat the board bending test at regular time intervals and record the relevant results.The supplier shall use the bending test for fault finding in the event of failures of devices (e.g. damage, microcracks on ceramic capacitors). The supplier shall record the results and submit them to Daimler AG Quality Management on request.The supplier shall use an appropriate measurement procedure for carrying out the board bending test.The maximum critical bending of boards depends on the individual circuit board or the devices used. The supplier shall take care to ensure that the sensors are positioned on the board at the point of maximum bending.The supplier shall take care to ensure that circuit board is assembled and soldered in line with the relevant process step to be examined.During the processing of ceramic capacitors, the supplier shall ensure that the specifications ofAV A2110039899 "Design Rules for E/E Components“ are complied with for all manufactured compo-nents.7.5 RequalificationThe supplier shall check at least once every year whether its deliveries conform to the specifications of Daimler AG.As a minimum requirement, the test scope shall include evidence that the specifications with regard to dimensional, material, reliability, environmental, process and statutory rules have been complied with.The supplier shall coordinate and document the test scopes with Daimler AG Quality Management. This coordination shall be based on the environmental and lifetime tests specified in the component require-ment specifications (KLH) as well as other specifications such as DBL, MBN, AV, etc.The supplier can choose between the following methods to prove compliance with the specifications of the environmental and life tests required in KLH:- complete annual repeat of the of the environmental and life tests specified in KLH- annual execution of a so-called "Q-Review Environment E/E“.7.5.1 Complete repeat of the environmental and life testsThe supplier shall record the results of the repeat and submit them to Daimler AG Quality Management on request.The supplier shall notify Daimler AG Quality Management of any deviations from the specification without delay.The supplier shall supply regular evidence of the process capabilities of production as a whole and each production process and maintain the appropriate records.If the tests show that the required cp or cpk values are not achieved and that the equipment requires read-justment, the supplier shall shorten the test interval.7.5.2 Q-Review Environment E/ETo perform a "Q-Review Environment E/E“, the supplier is required to comply with the following conditions: The environmental and life tests specified in the KLH have been performed once successfully, and the relevant results recorded.Another condition for the execution of a "Q-Review Environment E/E“ is that the following requirements have been fulfilled during the previous 12 months:- The supplier has used a statistical method for the early detection of faults in production. This method has ensured that 100% of the manufactured parts have been covered, the results recorded and evaluated regularly. All measures defined as part of the early fault detection system during the previous 12 months must have been effectively implemented.- The required qualification tests shall have been passed successfully with regard to any changes to the component or the production process.- All failures during the tests in production have been determined, and the relevant results recorded and regularly evaluated. All measures defined during the previous 12 months shall have been effectively im-plemented.- All measures defined during internal and external audits during the previous 12 months shall have been effectively implemented.- All 0-km failures and field failures during the previous 12 months shall have been analyzed and evalu-ated. Any resulting measures shall have been implemented effectively.。
- 1、下载文档前请自行甄别文档内容的完整性,平台不提供额外的编辑、内容补充、找答案等附加服务。
- 2、"仅部分预览"的文档,不可在线预览部分如存在完整性等问题,可反馈申请退款(可完整预览的文档不适用该条件!)。
- 3、如文档侵犯您的权益,请联系客服反馈,我们会尽快为您处理(人工客服工作时间:9:00-18:30)。
CHAPTER 18THE SYSTEM AND PROCESS OF CONTROLLING MULTIPLE CHOICE QUESTIONS. Choose the best answer.1. Which of the following is not a term in the controlling process?A.Staffing the position of a controller.B.Establishing standards.C.Measuring performance against standards.D.Correcting variations from standards and plans.Answer: A2. Managers may correct deviations by all except one of the following actions:A.Exercising their organizing function through reassignment orclassification of duties.B.Re-drawing their plans or modifying their goals.C.Exercising their staffing functions through additional staffing or theultimate re-staffing measure of firing.D.Exercising their leadership function through switching to autocratic stylesof leadership.Answer: D3. The way control is exercised differs between countries. In which of thefollowing countries is pinpointing responsibility for deviations from standards commonly attempted?A.United States.B.Japan.C.China.D.None of the above.Answer: A4. Which one of the following types of standards is for non-monetarymeasurements that are common at the operating levels, where materials are used, labor is employed, services are rendered, and goods are produced?A.Program standards.B.Physical standards.C.Cost standards.D.Intangible standards.Answer: B5. Which one of the following types of standards is for monetary measurementsthat are common at the operating level, which attach monetary values to specific aspects of operation?A.Program standards.B.Physical standards.C.Cost standards.D.Intangible standards.Answer: C6. Which one of the following types of standards is for those performancesarising from the application of monetary measurements to physical items?A.Program standards.B.Physical standards.C.Capital standards.D.Intangible standards.Answer: C7. Which one of the following types of standards is for those performancesarising from monetary values to sales?A.Physical standards.B.Cost standards.C.Capital standards.D.Revenue standards.Answer: D8. Which one of the following types of standards is for determining thecompetence of the divisional purchasing agent or the personnel director?A.Program standards.B.Intangible standards.C.Goals as standards.D.Strategic control.Answer: B9. Which of the following statement is not true?A.Strategic plans require strategic control.B.Strategic control provides opportunities for learning which in turn is thebasis for organizational change.C.Strategic control enables one to gain insights not only aboutorganizational performance but also about the ever-changingenvironment.D.Planning and control are independent of each other.Answer: D10. _______________ compares various strategies and identifies the key strategicelements of success.A.Strategic benchmarking.B.Operational benchmarking.C.Management benchmarking.11. Management control is usually perceived as a _______________ systemsimilar to the common household thermostat.A.Feedforward.B.Feedbackward.C.Feedback.D.None of the above.Answer: C12. Which of the following actions is not a step in the management controlprocess?A.Measurement of actual performance.parison of actual performance against standards.C.Identification of deviations.D.Analysis of causes of miscommunication.Answer: D13. ______________________ is information about what is happening while it ishappening.A.On-line information.B.Real-time information.C.Off-air information.D.None of the above.Answer: B14. Efficient control requires that managers look for _______________, whileeffective controls require that managers pay primary attention to things that are most _______________.A.Mistakes; damaging.B.Results; profitable.C.Exceptions; important.D.None of the above.Answer: C15. If controls are to remain effective despite failures or unexpected changes ofplans, they must be _______________.A.Adjustable.B.Flexible.C.Controllable.D.None of the above.Answer: B16. According to the case “Wal-Mart in America and around the Globe,” successdid not come to Wal-Mart by accident. Which of the following factor is not true about the Wal-Mart success story?A. A 280,000 strong organization structure.B.An effective human resource policy.C.An inspiring leadership style.D. A clever use of IT to manage its inventory.Answer: A17. According to the case “Wal-Mart in America and around the Globe,” a_______________ orientation is reflected in Wal-Mart’s values, which emphasizes maintaining good relationships with staff as well as suppliers.A.Big town.B.Small town.C.Small city.D.None of the above.Answer: B18 According to the case “Wal-Mart in America and around the Globe,” Wal-Mart is known for its national brand strategies, which allows consumers to compare prices. The focus on cost savings enables the company to offer “_______________________” which has become the familiar company slogan.A.Everyday low prices.B.Every week low prices.C.Lowest prices in town.D.Lowest prices nationwide.Answer: A19. According to the case “Wal-Mart in America and around the Globe,” one ofthe key factors for Wal-Mart’s success is the ____________________ that uses modern technology, a system that is considered one of the largest in America.A.Human resource system.B.Consumable goods price index system.C.Inventory system.D.Feedforward control system.Answer: CTRUE or FALSE.Mark each statement as true (T) or false (F). If the statement is false, or partly false, mark (F), write the correct version of the statement and discuss it.20. Performance is measured at selected points in an entire program so thatmanagers may receive signals about how things are going without having to watch every step in the execution of plans.Answer: T21. Alert managers need only measure performance as and when tasks areexecuted.Answer: FT Measurement of performance against standards should ideally be done on a forward-looking basis although such measurement is not always practical.Alert and forward-looking managers can sometimes predict probably departure from standards. In any case, deviations should always be detected and disclosed as early as possible so that they may be avoided by appropriate actions.22. For Wal-Mart, which has operations around the globe, the same measurementcriteria is applied to all stores.Answer: FT For Wal-Mart, which has operations around the globe, the same measurement criteria can hardly be applied to all stores. Control standards have to be adjusted to the local environment. Productivity in countries with low labor costs may lag behind that of other countries. Transfer pricing between the headquarters and the subsidiaries or between subsidiaries may distort the profitability and return-on-investment pictures.23. Effective control requires attention to those factors critical to evaluatingperformance against plans.Answer: T24. It is not possible to establish verifiable qualitative or quantitative goals toreplace the use of intangible standards.Answer: FT Modern managers are finding that through research and thinking it is possible to define goals that can be used as performance standards. While the quantitative goals are likely to take the form of variable tangible standards, the definition of qualitative goals represents an important development in the area of standards.25. Benchmarking developed out of the need to have data against whichperformance can be measured.Answer: T26. With real-time data, management control may be used to correct deviationsfrom standards instantly.Answer: FT Real-time data do not, except in the simplest and most unusual cases, make possible real-time control. It might be possible to compare these data with standards and even identify deviations very quickly, but the analysis of causes of deviations, the development of programs of correction, and the implementation of these programs are likely to be time-consuming tasks.27. Feedback from the output of a system is perfect for management control. Answer: FT What managers need for effective control is a system that will tell them to take corrective actions, that certain problems will occur if they do not do something now. Feedback from the output of a system is not good enough for control. It is little more than a postmortem, and no one has found a way to change the past. The time lag in the management control process shows that control must be directed toward the future if it is to be effective.28. Feedforward systems monitor inputs into a process to ascertain if the inputsare as planned. If they are not, the inputs or the process is changed in order to obtain the desired results.Answer: T29. Disturbances are factors which have not been taken into account in the inputmodel but which may have an impact on the system and the desired end result.Answer: T。