回焊炉掉板问题
回流焊炉的工作原理

回流焊炉的工作原理
回流焊炉是一种常见的电子元器件焊接设备,其工作原理是利用热风循环加热和冷却,将电子元器件焊接在印刷电路板上。
回流焊炉的工作原理可以分为以下几个步骤:
第一步,预热区加热。
在回流焊炉的预热区,通过加热器将热风加热到一定温度,然后将热风喷射到印刷电路板上,使其达到预定的温度。
这个温度通常在100℃左右,目的是将印刷电路板中的水分蒸发掉,避免在焊接过程中产生气泡。
第二步,焊接区加热。
在回流焊炉的焊接区,通过加热器将热风加热到一定温度,然后将热风喷射到印刷电路板上,使其达到焊接温度。
这个温度通常在200℃左右,目的是将焊料熔化,将电子元器件与印刷电路板焊接在一起。
第三步,冷却区冷却。
在回流焊炉的冷却区,通过加热器将热风加热到一定温度,然后将热风喷射到印刷电路板上,使其达到冷却温度。
这个温度通常在100℃左右,目的是将焊接完成的电子元器件和印刷电路板冷却,避免在移动过程中产生变形或损坏。
回流焊炉的工作原理是通过热风循环加热和冷却,将电子元器件焊接在印刷电路板上。
在整个焊接过程中,需要控制好温度和时间,以确保焊接质量和稳定性。
同时,还需要注意焊接过程中的安全问题,避免发生火灾或爆炸等意外情况。
SMT二次回流焊时避免第一面零件掉落的解决方法

SMT⼆次回流焊时避免第⼀⾯零件掉落的解决⽅法近⼏年,随着⼿机技术的快速发展,国内EMS不时传出严重的缺⼯问题,其次就是⼯业4.0让EMS⼚追求⾃动化的需求⽇益⾼涨,所以现在很多原本还不⼀定可以过SMT制程的零件,它们也都被要求零件要符合⾛PIH的制程。
1、在零件的底下或是旁边点红胶其实在早期的⼴州SMT贴⽚加⼯⼚,点胶机是必备的设备,因为点过胶的SMD零件可以拿去过波峰焊,不过现在⼤部分的SMT⽣产线⼏乎都沒有这个设备了。
如果沒有点胶机,就必须使⽤⼈⼯⼿动来点胶,个⼈不太建议⼈⼯,因为⼈⼯作业除了耗费⼈⼒及⼯时外,品质也较难管控,因为⼀不⼩⼼就会碰到其他已经贴⽚好的零件,如果有机器点胶机品质当然⽐较好管控。
点红胶的⽬的是要将零件粘着在电路板上,所以红胶⼀定要点在电路板上⾯,并且沾粘住零件,然后过回焊炉,利⽤回焊炉的⾼温将红胶固化,这种红胶属于不可逆胶,⽆法再经由加热软化。
如果红胶要点在零件的下⽅,点胶作业必须在电路板印完锡膏后马上点上去,然后再将⽐较重的零件覆盖在其上⾯。
要注意的是,红胶点在零件下⽅会有撑起零件的风险,所以⼀般都是⽐较重且⼤的零件才会这样作业。
另⼀种点胶作业会点在零件的侧边,这个必须等锡膏印刷完毕及零件放到固定位置以后才能作业,如果不⼩⼼会有碰掉零件的风险,所以⼀般会使⽤于PIH的零件。
如果使⽤机器点胶于侧边的话,必须精准控制胶量及点胶位置,将胶点于零件的边缘,然后⽤贴⽚机的吸嘴轻压零件⾄固定深度,以确保零件沒有浮⾼的风险。
现在因为机器⼈技术的进步,很多早期点胶不易控制的项⽬都可以有解決⽅案,众焱电⼦⼩编就看过使⽤简单的机器⼿臂来架在SMT流线上做点胶的解決⽅案,费⽤也不会很贵,提供有需要做点胶制程的朋友,当然,这个只适合少量的点胶作业。
2、使⽤过炉载具/托盘过炉载具可以设计成肋条刚好⽀撑住较重的零件位置,这样⽐较重的零件在过⼆次回流焊时就不易掉落。
但是过炉载具的费⽤不便宜,⽽且载具全部数量排起来要⼤于回焊炉 (reflow oven)的长度,也就是要计算回焊炉内同时有多少⽚板⼦⾏⾛其间,还要加上缓冲及备品,全部加起来沒有三⼗个也有⼆⼗个,可能还要更多,所费不眥。
回流焊常见问题及改善措施

回流焊常见问题及改善措施
一、焊接不良
1.问题描述:焊接点不牢固,容易脱落或产生气泡。
2.改善措施:
3.(1)检查焊盘是否清洁,去除表面的杂质和氧化层。
4.(2)检查锡膏是否正确印刷,确保焊盘上锡膏量充足且均匀。
5.(3)合理设置工艺参数,提高预热或焊接温度,保证足够的焊接时间。
6.(4)使用氮气保护环境,改善润湿行为。
二、焊点缺失
1.问题描述:在回流焊过程中,出现焊点不完整或缺失的情况。
2.改善措施:
3.(1)检查锡膏印刷是否均匀,确保每个焊盘上都有适量的锡膏。
4.(2)调整工艺参数,提高焊接温度和时间,确保焊点充分熔合。
5.(3)检查零件放置是否正确,确保零件与焊盘对齐。
6.(4)使用X光或超声波检测设备检查焊点内部质量,确认是否存在气孔或
裂纹等缺陷。
三、冷焊
1.问题描述:焊接点表面粗糙、不光滑,呈现冷焊现象。
2.改善措施:
3.(1)调整工艺参数,降低冷却速度,延长焊接时间。
4.(2)使用合适的助焊剂,提高焊接润湿性。
5.(3)确保零件和焊盘表面清洁,去除氧化层和杂质。
四、桥连
1.问题描述:两个焊接点之间出现多余的焊接材料,形成桥连现象。
2.改善措施:
3.(1)调整锡膏印刷量,减少多余的锡膏。
4.(2)合理设置工艺参数,控制焊接时间,避免过长或过短的焊接时间。
5.(3)使用合适的助焊剂,提高焊接润湿性,减少桥连现象。
回流焊炉安全事故案例

回流焊炉安全事故案例回流焊炉是电子制造业中常用的设备,用于焊接电路板上的表面贴装元件。
然而,由于操作不当或设备故障,会导致回流焊炉发生安全事故。
下面列举了十个回流焊炉安全事故案例:1. 操作员疏忽大意,未按规定的程序关闭回流焊炉,导致炉内温度过高,引发火灾,造成严重的财产损失。
2. 操作员没有佩戴足够的防护设备,接触到高温的焊接区域,导致皮肤烧伤。
3. 回流焊炉内部温度传感器失灵,未能及时发现温度异常,导致焊接过程中电路板过热,引发短路,造成产品损坏和生产线停产。
4. 回流焊炉设备维护不及时,导致部分电路元件老化、脱落,使得焊接质量下降,影响产品稳定性和可靠性。
5. 操作员没有经过专业培训,不熟悉回流焊炉的操作规程,误触操作面板上的控制按钮,导致焊接参数错误,引发电路板焊接不良,影响产品质量。
6. 回流焊炉设备故障引发电路板短路,导致电路板起火,造成厂房火灾,严重威胁到工人的生命安全。
7. 操作员在操作过程中没有切断电源,导致回流焊炉内的电路仍然通电,一旦操作不当,可能触电导致伤亡事故。
8. 回流焊炉设备运行时发生故障,导致焊接区域的温度异常升高,引发电路板熔化,可能造成设备短路、火灾等严重后果。
9. 操作员在打开回流焊炉门时没有等待足够的冷却时间,导致热气涌出,引起烫伤。
10. 回流焊炉设备没有进行定期维护和保养,导致设备运行不稳定,可能出现温度偏差、电路板焊接不良等问题,影响产品质量。
这些案例表明,回流焊炉的安全事故多数是由于操作不当、设备故障或维护不到位等原因引起的。
为了避免这些安全事故的发生,需要严格按照操作规程操作设备,定期进行设备维护和保养,并确保操作员接受专业培训,提高安全意识。
只有这样,才能保障回流焊炉的安全运行,确保产品质量和工人的生命安全。
如何评估SMT二次回焊时第一面零件不掉件风险与机率

如何评估SMT二次回焊时第一面零件不掉件风险与机率电路板组装(PCBA)走SMT双面回流焊已经是现代电子制造的主流,不过偶尔还是有许多朋友会询问:「是否有方法可以提前知道、或有什么计算公式可以预测哪些在第一面的电子零件过二次回焊时可能有掉件的风险或掉件率?」电路板组装全双面回流焊接的工艺与制程基本如下:制程:第一面印锡膏打SMD零件》第一次回焊炉(1st reflow) 》翻面》第二面印锡膏打SMD零件》第二次回焊炉(2nd reflow)所以,在进行第二面贴片回焊时,已经贴焊在板子第一面的零件将会背面进回焊炉,当板子来到回焊区时高温将会重新熔融原第一面已经固化的焊锡,这时再加上电子零件本身的重量,就很有可能让比较重的零件发生掉落问题。
那么有哪些因素可能影响到二次回焊时第一面贴片零件掉落呢?如果你有仔细观察过那些在回焊炉中容易掉落的零件,你会发现它们有些共同的特征,比如说焊点比较少、零件本身较重或较高,例如SMD型号的网络变压器(lan transformer)、线圈变压器(coil transformer)、线圈滤波器(coil filter)、比较大颗的电解电容器(Electrolytic capacitor)、同轴连接器(coaxial connector)、LGA、MCM…等。
●贴片零件的质量由于地球本身重力的关系,质量越大的零件受到来自地球的引力就越大,也就越容易从电路板上吊落。
●锡膏的合金成份目前业界使用锡膏的最大宗分别为无铅(lead-free)及含铅/有铅(Tin-lead)两种。
而无铅锡膏的成份又以SAC305最多人使用,SAC305的主要成份为锡(Sn)占了96.5%、银(Ag)占了3%、铜(Cu)占了0.5%比率的锡膏,而其熔点约为217°C。
含铅锡膏最主要为Sn61.9%/Pb38.1%,其熔点只有183°C。
所以无铅及有铅锡膏的熔点差了大约34°C。
点焊机虚焊、掉焊原因[修改版]
![点焊机虚焊、掉焊原因[修改版]](https://img.taocdn.com/s3/m/134a44d7482fb4daa48d4b00.png)
第一篇:点焊机虚焊、掉焊原因产生虚焊掉焊的原因及解决办法由于长期以来点焊出现虚焊、掉焊的问题,此类问题严重影响产品的安全性,属致命缺陷。
产生虚焊掉焊的问题分析:点焊机主要电源、机器设备、操作员工三个方面因素影响。
一、电源自2010年11月份已从原线上分线接换从主电线拉线接电源。
保证了电源电压的稳定。
二、1、机器设备点焊数调节。
一般按点焊工作的上下材料厚度按规定正常点焊参数:2、现车间工装夹具因年久磨损还有制作人不一,规格参差不齐,铜棒与主杆连接孔大小不一,配合不良或本身生锈未擦试干净,导电性能不好。
3、点焊机使用时间过长,维修过程中,一些配件可能与原机器组件不匹配。
造成放电不稳定。
4、现车间点焊机调的预压时间多为0.4-0.6秒,预压时间为上电极下行压紧工件时间;预压时间根据行程高度来设定,一般设定为0.6—1秒,如果预压时间不够容易产生火花,工件表面有毛刺不光滑影响工件质量,操作工在生产过程中不能随便调整参数。
三、1、操作员工自检频率不够。
2、操作员工图快随意调整点焊机参数。
3、由于点焊方式为电阻焊,刚开机点焊时,因点焊机处于常温状态,电阻稳定。
点了一会后点焊机各接触部位发热,导致电阻加大,此时应增大电流。
解决方案1.将组织装配车间技工调试好了再让员工上机点焊,并告知点焊机电阻因导体受热影响点焊质量的原理。
2.焊机的预压时间应调至6-10以上,严禁调至6以下,班组长每小时要求检查一次。
发现一次对操作员工50元一次的罚款。
3.作员工应以点焊20件为单位自检一次,车间班组长应每小时对点焊效果检查一次,看点焊工作有无掉焊现象,如有应立即停机调整。
4.员工学点焊时,老员工应教会其点焊相关技巧注意事项。
保证点焊质量。
5.将装配车间工装夹具清理并维修,尽可能标准化。
此项将列入本人今后工作重点,在四月份前完成工装夹具的检修,五月份完成不良模具的更新。
6.车间调模技工应该测试工装夹具是否配合良好,并将有锈的铜棒处理干净后再组装模具,保证导电性能。
回流焊炉温板使用寿命
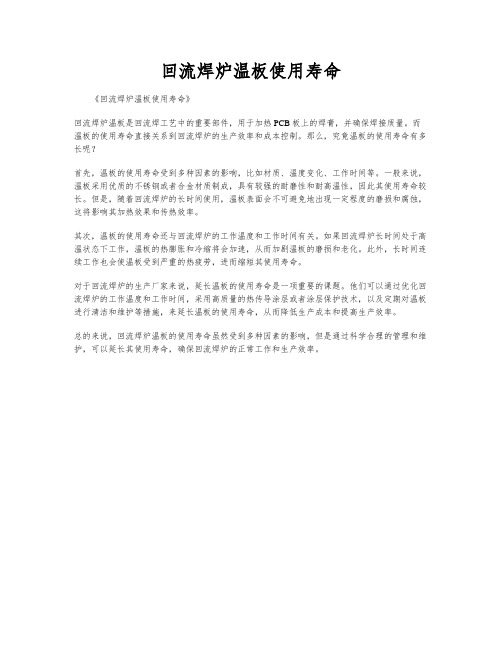
回流焊炉温板使用寿命
《回流焊炉温板使用寿命》
回流焊炉温板是回流焊工艺中的重要部件,用于加热PCB板上的焊膏,并确保焊接质量。
而温板的使用寿命直接关系到回流焊炉的生产效率和成本控制。
那么,究竟温板的使用寿命有多长呢?
首先,温板的使用寿命受到多种因素的影响,比如材质、温度变化、工作时间等。
一般来说,温板采用优质的不锈钢或者合金材质制成,具有较强的耐磨性和耐高温性,因此其使用寿命较长。
但是,随着回流焊炉的长时间使用,温板表面会不可避免地出现一定程度的磨损和腐蚀,这将影响其加热效果和传热效率。
其次,温板的使用寿命还与回流焊炉的工作温度和工作时间有关。
如果回流焊炉长时间处于高温状态下工作,温板的热膨胀和冷缩将会加速,从而加剧温板的磨损和老化。
此外,长时间连续工作也会使温板受到严重的热疲劳,进而缩短其使用寿命。
对于回流焊炉的生产厂家来说,延长温板的使用寿命是一项重要的课题。
他们可以通过优化回流焊炉的工作温度和工作时间,采用高质量的热传导涂层或者涂层保护技术,以及定期对温板进行清洁和维护等措施,来延长温板的使用寿命,从而降低生产成本和提高生产效率。
总的来说,回流焊炉温板的使用寿命虽然受到多种因素的影响,但是通过科学合理的管理和维护,可以延长其使用寿命,确保回流焊炉的正常工作和生产效率。
真空回流焊炉原理

真空回流焊炉原理今天咱们来唠唠那个听起来就很厉害的真空回流焊炉的原理。
咱先想象一下啊,这回流焊炉就像是一个超级大厨的魔法厨房。
普通的焊接呢,就像是在露天的烧烤摊烤串儿,周围啥环境都有。
但是真空回流焊炉呢,就像是在一个超级密封、干净又高级的厨房里面做菜。
这个真空回流焊炉啊,它主要是用来焊接那些小小的电子元件的。
你看啊,那些电子元件就像一群小小的精灵,它们得按照一定的规则组合在一起才能发挥作用呢。
这时候就轮到真空回流焊炉出场啦。
它有一个很重要的特点,就是真空环境。
为啥要有真空环境呢?你想啊,要是在普通的环境里焊接,就像是在一个满是灰尘和小杂质的地方做精细活儿。
那些灰尘啊杂质啊就会像调皮捣蛋的小鬼一样,偷偷地钻进焊接的地方,把焊接效果搞得乱七八糟的。
可是在真空环境里就不一样啦,就像是给这些电子元件精灵们创造了一个纯净的世界,没有那些捣乱的灰尘和杂质。
那它是怎么把那些小元件焊接在一起的呢?这就涉及到回流焊的原理啦。
在这个真空回流焊炉里,有一块特殊的板子,上面放着那些要焊接的电子元件。
然后呢,会有焊锡膏涂在需要焊接的地方。
这个焊锡膏啊,就像是胶水一样,不过它是能在加热的时候变成液态,把元件和电路板紧紧粘在一起的神奇“胶水”。
接着啊,这个炉子就开始加热啦。
这加热就像是给这个小世界开了暖气一样。
随着温度慢慢升高,焊锡膏就开始发生变化啦。
它从一开始有点干干的状态,慢慢变成了液态。
这个时候,那些液态的焊锡就会像一个个听话的小士兵,按照预定的位置,把电子元件和电路板连接起来。
在真空的环境下,这个过程就进行得特别顺利,不会有气泡之类的坏家伙捣乱。
而且啊,这个真空回流焊炉的温度控制可是相当精准的呢。
它就像一个特别有经验的老中医,知道每个阶段该用多少温度。
如果温度太高了,就像火太大了,那些焊锡可能就会变得太稀,流得到处都是,把不该连接的地方也连接起来了,这可就乱套了。
如果温度太低呢,焊锡又不能很好地融化,焊接就不牢固。
再说说这个真空的好处吧。
焊把线脱落整改措施

焊把线脱落整改措施
焊把线脱落整改措施
焊把线脱落整改措施
1、在焊接时焊盘脱落多是因为焊接时间过长或反复焊接造成温度过高,焊盘铜片反复膨胀才会脱落,在焊接的时候要多加注意这点防止更多的脱落。
2、将脱落的焊盘用刀切掉切到未脱落处,防止电路顺着脱落处扩大,如果你的元件引脚够长,可以将切断后的电路接头处的绝缘漆刮掉,上好焊锡将远见的引脚焊接在此处。
3、如果你的元件引脚不够长,你可以使用一段细导线上好焊锡顺着焊盘孔穿过后焊接在元件引脚,另一头焊接在焊盘接头处并使用热熔胶固定防止再次开焊脱落。
4、如果你的焊盘出脱落十分严重不合适上面的方法,你还可以选择飞线的方式,将导线一头焊接在脱焊的元件引脚上,另一端焊接在和脱焊的焊盘相连的任意焊点上。
5、还有一种方式,搭桥,要是脱焊的焊盘元件引脚周围有同一线路上的元件,你可以直接将元件引脚焊接在那个元件的引脚上,废弃原焊盘,当然,焊接的时候一定看清不能焊串位防止烧坏元件。
6、脱焊应该将原焊口用锉刀或砂纸清理干净之后,再进行焊接处理。
7、脱焊就是焊接金属时焊接电极触手接触点移位,造成电流疏导障碍,不能继续操作焊接机器及脱焊。
重新调整电极触手与焊接体的接触位置,以便能继续焊接操作。
回焊炉掉板问题
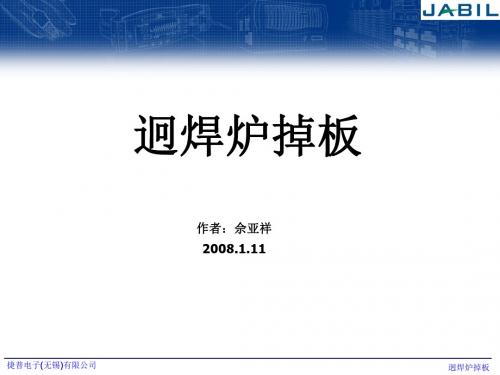
1.5 用空的PCB或治具进行传输测试(为了节省时间请调整轨道整速度至1.5m/分)
1.6 如果不能通过测试,请将调用冷却程序或建一个所有温区为室温的冷却程序冷却炉膛 1.7 炉温降到60摄氏度以下时请慢慢开启炉膛到最大 1.8 用合适的PCB或治具检查整个机器轨道的宽度是否一致,通常要求误差极限为1mm 1.9 将轨道宽度调整到最大及最小再重复测试轨道宽度,确定轨道宽度在要求的范围内 1.10 正常情况经过以上的确认能够完全排除掉板问题(前后传送轨道需优先确认,炉膛异物需要注意) 2. 生产中不确定的时间的掉板(不确定的频率,不确定的时间) 2.1 请优先检查前后传送轨道是否对齐,宽度调整是否合适,以及机器轨道的设定及前后差异是否合适 2.2 检查你的PCB或治具是否在进炉以前已经严重变形,治具是否损坏,方向是否正确 2.3 检查PCB掉入机器的PCB及治具的宽度是否与机器的轨道宽度设定符合 2.4 检查机器防跌落机构或中心支撑机构是否设定正确(公司目前尚未配备CBS) 2.5 经过以上仔细的检查和确认,这种问题通常是能够很快解决的
捷普电子(无锡)有限公司
迥焊炉掉板
基本检测调整
检测机器轨道宽度(进板位置和出板位置)
调整进板导向模块(固定和移动轨道各一片,松开两颗固定螺丝调整位置即可)
捷普电子(无锡)有限公司
迥焊炉掉板
基本检测调整
检测传送轨道对位(使用直尺或PCB均可)
捷普电子(无锡)有限公司
迥焊炉掉板
基本检测调整
检查轨道宽度设定值和实际值
捷普电子(无锡)有限公司 迥焊炉掉板
常见故障处理
3. 试产中总是不定期及不定期的掉板 3.1 请首先检查产品进入机器长度方向大于宽度方向(有V-Cut或较大空洞时应特别考虑) 3.2 检查进板及出板处的轨道宽度与实际产品的轨道宽度,通常轨道寬度不能大于产品宽度2mm 3.3 检查治具及PCB板上是否有较高的元器件及突出物,超出炉膛内部高度 3.4 检查PCB厚度是否适合于PCB直接进行迥流焊接,小于1.0mm的板不太适合 3.5 对于PCB宽度大于300mm且厚度在1.0~1.6mm之间的PCB需要进行评估 3.6 对于使用沉重治具的PCB要检测重量,建议不大于1.5公斤 3.7 机器内有异物,运行中的链网及链条不定期的受到阻挡也会导致这种问题 4. 生产中突然发生跌板之后一切恢复正常(出现的概率非常小) 4.1 有时候会在某些迥流焊炉发生,生产中轨道突然变宽致掉板的情形 4.2 针对于这种情形,请注意监视器上显示的实际轨道宽度值是否有异变 4.3 部分使用拉绳式宽度测量的机器,有异物跌下压在拉绳上导致检测的轨道宽度变宽 4.4 使用编码器测量机器宽度的设备,请记录发生的状况,重复发生需要更换编码器 4.5 机器配置设定的编码器的类型也有机会导致这个问题的发生(模拟和数码两种) 4.6 机器的链条传动与机器的轨道宽度调共同使用一片控制卡,控制卡故障时也会有机会
平吊顶窑炉吊板掉落原因分析
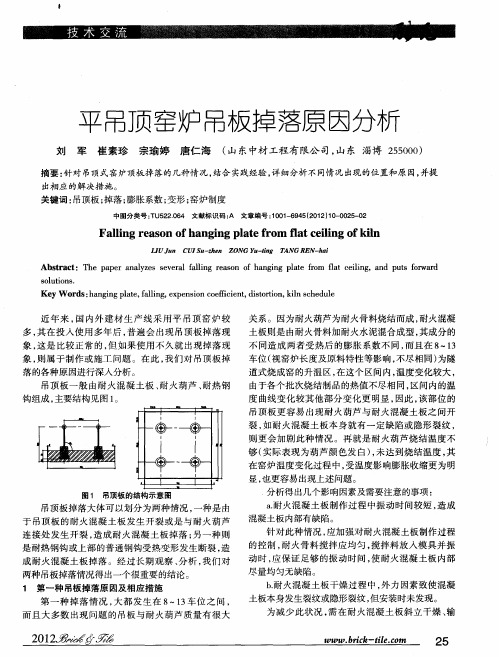
土板则是 由耐火骨料加耐火水泥混合成型 , 其成分 的 不 同造 成 两 者 受 热 后 的膨 胀 系 数 不 同 , 而且 在 8 3 一l 车位( 视窑炉长度及原料特性等影响 , 不尽相同) 为隧 道式烧成窑的升温区 , 在这个 区间内, 温度变化较大 , 由于各 个 批次 烧 结 制 品 的热值 不 尽 相 同 , 区间 内 的温 度 曲线 变 化 较 其 他 部分 变 化 更 明显 , 因此 , 部 位 的 该
吊顶 板 更 容 易 出 现 耐 火 葫芦 与 耐火 混 凝 土 板 之 间开
裂, 如耐火混凝土板本身就有一定缺陷或隐形裂纹 , 则更会加剧此种情况 。再就是 耐火葫芦烧结温度不 够( 实际表现为葫芦颜色发 白)未达到烧结 温度 , , 其
在 窑炉 温 度变 化 过 程 中 , 受温 度影 响膨胀 收缩 更 为 明
显 , 更容 易 出现上 述 问题 。 也
图 1 吊顶 板 的 结构 示 意 图
分析 得 出几个影 响因素 及需要 注意 的事项 : a耐火 混 凝 土 板 制 作 过程 中振 动 时 间 较 短 , 成 . 造 混凝 土板 内部 有缺 陷 。 针对 此 种 情况 , 应加 强 对 耐火 混 凝 土板 制作 过 程
ห้องสมุดไป่ตู้
关 系 。 因为 耐火 葫 芦 为耐 火 骨料 烧 结 而成 , 火混 凝 耐
多, 其在投入使用多年后 , 普遍会 出现 吊顶板掉落 现 象, 这是 比较正常 的 , 但如果使用 不久就出现掉落现 象, 则属 于制作或施工 问题 。在此 , 我们对 吊顶板 掉 落的各种原因进行深入分析。 吊顶 板 一 般 由 耐 火 混凝 土板 、 耐火 葫芦 、 热 钢 耐 钩 组成 , 主要结 构见 图 1 。
【常见问题解答】红胶厚网工艺,波峰焊掉件问题
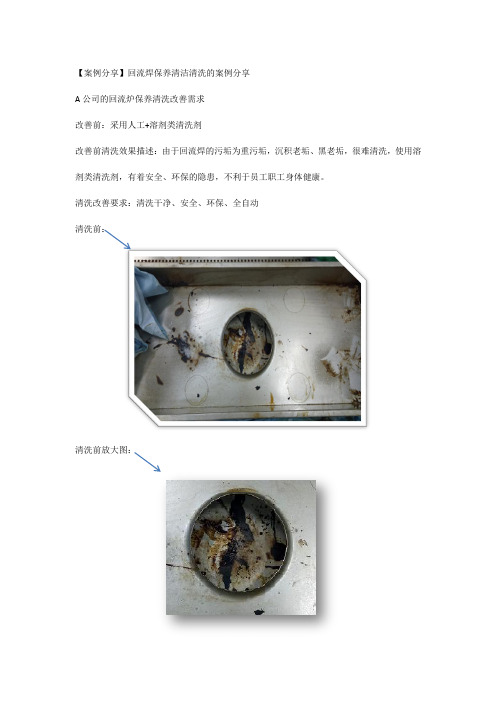
【案例分享】回流焊保养清洁清洗的案例分享
A公司的回流炉保养清洗改善需求
改善前:采用人工+溶剂类清洗剂
改善前清洗效果描述:由于回流焊的污垢为重污垢,沉积老垢、黑老垢,很难清洗,使用溶剂类清洗剂,有着安全、环保的隐患,不利于员工职工身体健康。
清洗改善要求:清洗干净、安全、环保、全自动
清洗前:
清洗前放大图:
回流炉清洗【解决方案】
1:使用合明科技水基清洗剂W4000H
2:超声波清洗机
3.将此清洗部件需要放置在超声机里,水平放置,清洗约10分钟,效果如下图
回流炉经过超声波水基W4000H清洗后放大图:
合明科技提供回流焊清洗解决方案:
全自动、安全、环保、干净、高效率、低成本。
回焊炉卡板经验分享和回焊炉链条保养方法

回焊炉卡板原因:
遇到过几次回焊炉卡板的故障,与大家分享一下,
1.轨道喇叭口,这个不用说了,大家都知道,需要调节轨道宽度。
2.马达碳刷短了,时而接触不良,链条时而停转,所以卡板。
3.链条运动中被挂住,有异物。
4.链条太久没有清理,硬化。
翘起卡板。
5.链条失效坏掉,在导槽中卡住,造成卡板。
6.马达驱动卡有问题,接触不良,造成链条停转卡板。
怎样清洗回焊炉链条:因为我们使用的高温链条油99%都是合成润滑油,主要成分
还是C H 化合物,所以每
隔一定时间。
链条就会脏,上面的碳的渣子,有时会在链节的缝隙里,造成链条不柔顺,运动不顺畅,卡板,甚至不能转动等问题。
链条的清洗对很多工厂是个难题,超声波,油,酒精,用火烧18般武艺都用上了,还是不理想,那么应该怎么样清洗链条呢,本人多年来的经验如下:最好能备用一根链条,几个接头,还有链条卸分器。
这样有充足时间工作,洗的干净彻底,而且拆卸
过程中如果有损坏也可以及时更换。
将换下的链条泡在溶剂中,哪种溶剂好呢?很多种都比较好,碱性加活性剂的水基溶剂比较好用,要浸没过链条,泡上一天左右后,用刷子刷,浸泡其间不间断翻动比较好些,然后清水冲洗,然后涂高温链条油盘起后保管。
清洗过程要注意每个链节缝隙间的杂质要洗干净,链节不要太松动也不能太紧,如果有损坏,立刻更换。
最后链
条盘好涂油保存。
回流焊炉安全事故案例
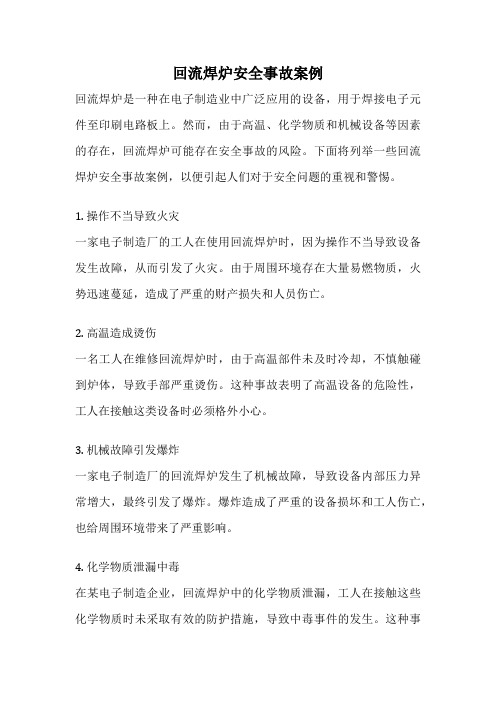
回流焊炉安全事故案例回流焊炉是一种在电子制造业中广泛应用的设备,用于焊接电子元件至印刷电路板上。
然而,由于高温、化学物质和机械设备等因素的存在,回流焊炉可能存在安全事故的风险。
下面将列举一些回流焊炉安全事故案例,以便引起人们对于安全问题的重视和警惕。
1. 操作不当导致火灾一家电子制造厂的工人在使用回流焊炉时,因为操作不当导致设备发生故障,从而引发了火灾。
由于周围环境存在大量易燃物质,火势迅速蔓延,造成了严重的财产损失和人员伤亡。
2. 高温造成烫伤一名工人在维修回流焊炉时,由于高温部件未及时冷却,不慎触碰到炉体,导致手部严重烫伤。
这种事故表明了高温设备的危险性,工人在接触这类设备时必须格外小心。
3. 机械故障引发爆炸一家电子制造厂的回流焊炉发生了机械故障,导致设备内部压力异常增大,最终引发了爆炸。
爆炸造成了严重的设备损坏和工人伤亡,也给周围环境带来了严重影响。
4. 化学物质泄漏中毒在某电子制造企业,回流焊炉中的化学物质泄漏,工人在接触这些化学物质时未采取有效的防护措施,导致中毒事件的发生。
这种事故提醒人们在操作化学品时必须注意安全防护。
5. 设备维护不及时导致故障一家电子制造企业因为长期忽视回流焊炉的维护保养,导致设备老化严重,最终在生产过程中出现故障。
故障不仅影响了生产进度,也给工人的安全带来了隐患。
6. 电气故障引发火灾某工厂的回流焊炉由于电气线路老化,发生了短路引发火灾的事故。
电气设备的安全性对于回流焊炉的正常运行至关重要,一旦发生问题,后果不堪设想。
7. 操作人员疲劳导致操作失误长时间连续操作回流焊炉的工人,由于疲劳过度,容易出现操作失误,导致安全事故的发生。
为了避免这种情况,企业应当合理安排工作时间,保证操作人员的状态良好。
8. 缺乏应急预案导致事故扩大一家电子制造企业在回流焊炉发生故障时,由于缺乏有效的应急预案,导致事故扩大,影响了整个生产线的正常运转。
及时有效的应急预案对于避免事故造成的损失至关重要。
回流焊后电阻焊盘脱落的原因
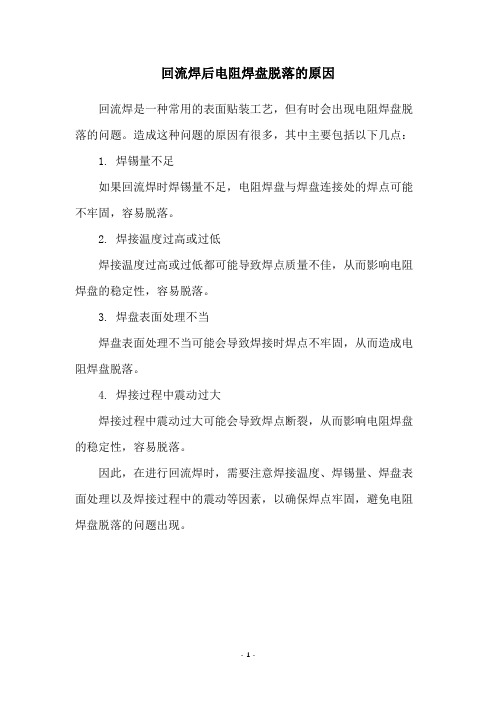
回流焊后电阻焊盘脱落的原因
回流焊是一种常用的表面贴装工艺,但有时会出现电阻焊盘脱落的问题。
造成这种问题的原因有很多,其中主要包括以下几点: 1. 焊锡量不足
如果回流焊时焊锡量不足,电阻焊盘与焊盘连接处的焊点可能不牢固,容易脱落。
2. 焊接温度过高或过低
焊接温度过高或过低都可能导致焊点质量不佳,从而影响电阻焊盘的稳定性,容易脱落。
3. 焊盘表面处理不当
焊盘表面处理不当可能会导致焊接时焊点不牢固,从而造成电阻焊盘脱落。
4. 焊接过程中震动过大
焊接过程中震动过大可能会导致焊点断裂,从而影响电阻焊盘的稳定性,容易脱落。
因此,在进行回流焊时,需要注意焊接温度、焊锡量、焊盘表面处理以及焊接过程中的震动等因素,以确保焊点牢固,避免电阻焊盘脱落的问题出现。
- 1 -。
回流焊常见焊接不良及应对

回流焊常见焊接不良及应对随着表面组装技术的广泛应用,SMT焊接质量问题引起了人们的高度重视。
为了减少或避免回流焊接中各种缺陷的出现,不仅要注重提高工艺人员分析、判断和解决这些问题的能力,而且还要完善工艺管理,提高工艺质量控制技术,这样才能更好的提高SMT焊接质量,保证电子产品的最终质量。
1、桥连桥连产生原因及解决办法:(1)温度升速过快。
回流焊时,如果温度上升过快,焊膏内部的溶剂就会挥发出来,引起溶剂的沸腾飞溅,测出焊料颗,形成桥连。
其解决办法是:设置适当的焊接温度曲线。
(2)焊膏过量。
由于模板厚度及开孔尺寸偏大,造成焊膏过量,回流焊后必然会形成桥连。
其解决办法是:选用模板厚度较薄的模板,缩小模板开孔尺寸。
(3)模板孔壁粗糙不平,不利于焊膏脱膜,印制出的焊膏也容易坍塌,从而产生桥连。
其解决办法是:采用激光切割的模板。
(4)贴装偏移,或贴片压力过大,使印制出的焊膏发生坍塌,从而产生桥连。
应减小贴装误差,适当降低贴片头的放置压力。
(5)焊膏的黏度较低,印制后容易坍塌,回流焊后必然会产生桥连。
其解决的办法是,选用黏度较高的焊膏。
(6)电路板布线设计与焊盘间距不规范,焊盘间距过窄,导致桥连。
需要改进电路板的设计。
(7)锡膏印制错位,也会导致产生桥连。
应提高锡膏印刷的对准精度。
(8)过大的刮刀压力,使印制出的焊膏发生坍塌,从而产生桥连。
其解决办法是,降低刮刀压力。
2、立碑立碑是指两个焊端的表面组装元件,经过回流焊后其中一个端头离开焊盘表面,整个元件呈斜立或直立,如石碑状,又称吊桥、曼哈顿现象.产生原因及解决办法:(1)贴装精度不够:一般情况下,贴装时产生的组件偏移,在回流焊接时由于焊膏熔化产生表面张力,拉动组件进行定位,即自动定位。
但如果偏移严重,拉动反而会使组件竖起,产生立碑现象。
别外,组件两端与焊膏的黏度不同,也是产生产碑现象的原因之一。
其解决办法是:调整贴片机的贴片精度,避免产生较大的贴片偏差。
(2)焊盘尺寸设计不合理:若片式组件是一对焊盘不对称,会引起漏印焊膏量不一致,小焊盘对温度响应快,焊盘上的焊膏易熔化,大焊盘则相反。
煤锅炉炉膛炉墙掉落检修氮气置换方案
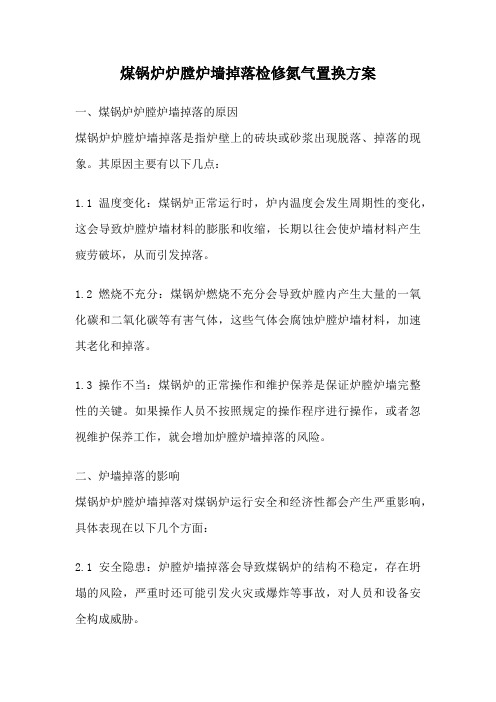
煤锅炉炉膛炉墙掉落检修氮气置换方案一、煤锅炉炉膛炉墙掉落的原因煤锅炉炉膛炉墙掉落是指炉壁上的砖块或砂浆出现脱落、掉落的现象。
其原因主要有以下几点:1.1 温度变化:煤锅炉正常运行时,炉内温度会发生周期性的变化,这会导致炉膛炉墙材料的膨胀和收缩,长期以往会使炉墙材料产生疲劳破坏,从而引发掉落。
1.2 燃烧不充分:煤锅炉燃烧不充分会导致炉膛内产生大量的一氧化碳和二氧化碳等有害气体,这些气体会腐蚀炉膛炉墙材料,加速其老化和掉落。
1.3 操作不当:煤锅炉的正常操作和维护保养是保证炉膛炉墙完整性的关键。
如果操作人员不按照规定的操作程序进行操作,或者忽视维护保养工作,就会增加炉膛炉墙掉落的风险。
二、炉墙掉落的影响煤锅炉炉膛炉墙掉落对煤锅炉运行安全和经济性都会产生严重影响,具体表现在以下几个方面:2.1 安全隐患:炉膛炉墙掉落会导致煤锅炉的结构不稳定,存在坍塌的风险,严重时还可能引发火灾或爆炸等事故,对人员和设备安全构成威胁。
2.2 燃烧效率下降:炉膛炉墙掉落会导致煤锅炉的燃烧室形状不规则,燃烧空间变小,燃烧效率下降,造成能源浪费。
2.3 维修成本增加:炉膛炉墙掉落后,需要进行维修和更换炉墙材料,这将增加维修成本和停机时间,对生产造成一定的影响。
三、氮气置换方案为了解决煤锅炉炉膛炉墙掉落问题,可以采用氮气置换的方法。
具体操作步骤如下:3.1 准备工作在进行氮气置换之前,需要做好以下准备工作:- 确定炉膛炉墙掉落的具体位置和范围;- 准备好氮气供应设备和氮气储存容器;- 确保操作人员具备相关的安全知识和操作技能。
3.2 置换操作具体的氮气置换操作步骤如下:- 关闭煤锅炉的供气和供热系统;- 将氮气供应设备连接到煤锅炉炉膛;- 开始向炉膛内注入氮气,注入的速度和压力要适当,以避免对炉膛造成额外的损伤;- 注入氮气的同时,通过炉膛的通风系统排除炉内的有害气体,确保炉膛内的气氛达到安全标准。
3.3 安全措施在进行氮气置换操作时,需要注意以下安全措施:- 操作人员必须佩戴防护装备,如防毒面具、防护服等;- 操作人员要经过专门的培训,了解氮气操作的注意事项和应急处理方法;- 确保操作现场通风良好,避免氮气积聚导致安全事故。
回焊炉降温斜率

回焊炉降温斜率是指在电子元器件制造中,回焊炉升温完成后,从高温到低温过程中的温度下降速率。
回焊炉降温斜率对于电子元器件的焊接质量和可靠性有着重要的影响。
降温斜率的大小直接影响到焊接过程中的温度梯度和热应力,如果降温斜率过大,会导致电子元器件的热应力增大,从而造成焊接点的裂纹和焊盘的脱落等问题;反之,如果降温斜率过小,会导致焊接点之间的互连良好性变差,甚至引发焊接品质不良。
要控制回焊炉降温斜率,一般需要考虑以下几个方面:1.回焊炉的设计和控制:回焊炉的设计和控制是影响降温斜率的关键因素。
合理的回焊炉设计可以保证热量的均匀输送,从而降低焊点之间的温度梯度,减小焊接点的热应力。
在控制回焊炉降温斜率时,需要根据焊接工艺的要求,设置合适的升温速度和降温速度。
2.PCB板的设计和材料选择:PCB板的设计和材料的选择也会对回焊炉降温斜率产生影响。
在设计PCB板时,应合理布局焊接点,减小热损失和热阻;在选择材料时,应选择导热性能较好的材料,加快热量的传导,减小温度梯度。
3.焊料的选择:焊料的选择也会对回焊炉降温斜率产生影响。
不同类型的焊料在加热和冷却过程中具有不同的热学特性,选用合适的焊料可以降低焊接点的热应力,提高焊接质量。
4.工艺参数的优化:在实际生产中,还可以通过优化工艺参数来控制回焊炉降温斜率。
例如,调整加热和冷却区域的温度分布,改变传送带的速度等,都能对降温斜率产生影响。
总之,控制回焊炉降温斜率对于确保焊接质量和提高电子元器件的可靠性非常重要。
在实际生产中,需要综合考虑回焊炉的设计和控制、PCB板的设计和材料选择、焊料的选择以及工艺参数的优化等因素,以达到合理控制降温斜率的目的。
这样才能保证电子产品的质量,提高生产效率。
煤锅炉炉膛炉墙掉落检修氮气置换方案

煤锅炉炉膛炉墙掉落检修氮气置换方案煤锅炉作为一种常见的供热设备,其正常运行对于保障供暖质量至关重要。
然而,在煤锅炉的使用过程中,由于炉膛炉墙的老化或其他原因,可能会出现炉膛炉墙掉落的情况。
为了及时修复煤锅炉炉膛炉墙的问题,确保其正常运行,采用氮气置换的检修方案是一种有效的解决方法。
煤锅炉炉膛炉墙掉落的问题,一般是由于长时间的使用或不当的维护导致的。
炉膛炉墙掉落不仅会影响煤锅炉的热效率,还会造成设备的安全隐患。
因此,在检修过程中,采用氮气置换方案可以有效地解决这一问题。
在进行煤锅炉炉膛炉墙掉落检修之前,需要进行严格的安全评估。
确保检修过程中的安全性和稳定性。
在检修过程中,需要将煤锅炉停机,并切断所有与煤锅炉相关的电源和燃气供应。
同时,需要提前准备好足够的氮气。
接下来,开始进行煤锅炉炉膛炉墙掉落的检修工作。
首先,需要将炉膛炉墙上的残留煤渣和积灰清理干净,确保炉膛炉墙的表面干净无尘。
然后,使用专业的检修工具进行炉膛炉墙的检查,查找可能存在的裂缝、破损或掉落的部位。
在确定了炉膛炉墙掉落的具体位置后,可以开始进行氮气置换。
氮气置换是指利用氮气将煤锅炉炉膛炉墙内的空气排出,以防止氧气对煤锅炉产生腐蚀作用。
首先,将氮气通过专用的管道引入炉膛炉墙内部,逐渐将炉膛炉墙内的空气排出。
待炉膛炉墙内的空气完全被氮气置换后,可以进行下一步的修复工作。
修复炉膛炉墙的方法可以根据具体情况来选择。
一种常见的修复方法是使用耐火材料进行补焊或补贴。
将耐火材料涂抹在炉膛炉墙的破损处,经过一定时间的干燥和固化,可以有效地修复炉膛炉墙的问题。
在修复过程中,需要确保使用的耐火材料具有良好的耐高温性能和粘接性能。
修复完成后,需要进行严格的检测和测试,确保修复的炉膛炉墙能够满足正常运行的要求。
同时,还需要对煤锅炉的其他部位进行检查,确保没有其他潜在的安全隐患。
将煤锅炉重新启动,并进行试运行。
在试运行过程中,需要监测煤锅炉的运行情况,确保其正常工作。
- 1、下载文档前请自行甄别文档内容的完整性,平台不提供额外的编辑、内容补充、找答案等附加服务。
- 2、"仅部分预览"的文档,不可在线预览部分如存在完整性等问题,可反馈申请退款(可完整预览的文档不适用该条件!)。
- 3、如文档侵犯您的权益,请联系客服反馈,我们会尽快为您处理(人工客服工作时间:9:00-18:30)。
常见故障处理
3. 试产中总是不定期及不定期的掉板 3.1 请首先检查产品进入机器长度方向大于宽度方向(有V-Cut或较大空洞时应特别考虑) 3.2 检查进板及出板处的轨道宽度与实际产品的轨道宽度,通常轨道寬度不能大于产品宽度2mm 3.3 检查治具及PCB板上是否有较高的元器件及突出物,超出炉膛内部高度 3.4 检查PCB厚度是否适合于PCB直接进行迥流焊接,小于1.0mm的板不太适合 3.5 对于PCB宽度大于300mm且厚度在1.0~1.6mm之间的PCB需要进行评估 3.6 对于使用沉重治具的PCB要检测重量,建议不大于1.5公斤 3.7 机器内有异物,运行中的链网及链条不定期的受到阻挡也会导致这种问题 4. 生产中突然发生跌板之后一切恢复正常(出现的概率非常小) 4.1 有时候会在某些迥流焊炉发生,生产中轨道突然变宽致掉板的情形 4.2 针对于这种情形,请注意监视器上显示的实际轨道宽度值是否有异变 4.3 部分使用拉绳式宽度测量的机器,有异物跌下压在拉绳上导致检测的轨道宽度变宽 4.4 使用编码器测量机器宽度的设备,请记录发生的状况,重复发生需要更换编码器 4.5 机器配置设定的编码器的类型也有机会导致这个问题的发生(模拟和数码两种) 4.6 机器的链条传动与机器的轨道宽度调共同使用一片控制卡,控制卡故障时也会有机会
迥焊炉掉板
MPM操作培训课程
作者:佘亚祥 2008.1.11
捷普电子(无锡)有限公司
迥焊炉掉板
问题及现象
PCB或治具掉入机器
捷普电子(无锡)有限公司
迥焊炉掉板
基本原因分析
1. 不正确的轨道宽度 由于迥焊炉内有加热器,会产生一定的热胀冷缩的误差,设定的轨道宽度误差范围过大 2. 轨道变形,各位置的宽度不一致 进板处和炉内及出板处的轨道宽度差异大,前中后不能兼顾导致。或是轨道变形某个部位宽度大 3. 轨道宽度不稳定致调整宽度时不准确 轨道悬挂机构过于松动或调整宽度的丝杆固定机构损坏及固定螺丝松动,固定或移动轨道位置变化 4. 冷机时轨道正常,加热时轨道变形 轨道悬持机构不正确锁定,致加热时轨道不能促缩。所以轨道各个位置的宽度差异大 5. PCB或治具运行到链条上,因为振动导致运输过程中迭落 没有预防产品运行超出正常链条位置的机构或机构设定不正确;前后的传送轨道与机器不对应 6. 不正确的取付导致PCB运行到链条上 炉子前的传送轨道速度过快,将产品推入炉膛;炉子后的传送轨道速度过慢,不能及时传送产品 7. 不正确的制程设定 产品进炉时宽度方向远大于长度方向或硬度太小,受热后纤维材料软化变形致PCB跌入炉膛 8. 有异物阻塞机器轨道 在传送过程中有异物阻塞轨道,致产品在传送过程中跌入炉膛
捷普电子(无锡)有限公司
迥焊炉掉板
基本检测调整
检测机器轨道宽度(进板位置和出板位置)
调整进板导向模块(固定和移动轨道各一片,松开两颗固定螺丝调整位置即可)
捷普电子(无锡)有限公司
迥焊炉掉板
基本Байду номын сангаас测调整
检测传送轨道对位(使用直尺或PCB均可)
捷普电子(无锡)有限公司
迥焊炉掉板
基本检测调整
检查轨道宽度设定值和实际值
检查PCB或治具实际宽度 (掉入机器的)
捷普电子(无锡)有限公司
迥焊炉掉板
完成
捷普电子(无锡)有限公司
迥焊炉掉板
捷普电子(无锡)有限公司
迥焊炉掉板
常见故障处理
1. 生产中总是掉板,没法进行生产的情况(产品已经生产很长时间) 1.1 请停止PCB进入机器,且清除炉膛内所有的产品及治具 1.2 检查进板及出板处的轨道宽度与实际产品的轨道宽度,通常轨道寬度不能大于产品宽度2mm 1.3 检查轨道前后的悬挂支撑及固定螺丝,摇晃固定及移动轨道确定轨道没有松动现象,否则维修它 1.4 松动前后的轨道固定螺丝,之后用手拧紧即可且确认轨道不松动
1.5 用空的PCB或治具进行传输测试(为了节省时间请调整轨道整速度至1.5m/分)
1.6 如果不能通过测试,请将调用冷却程序或建一个所有温区为室温的冷却程序冷却炉膛 1.7 炉温降到60摄氏度以下时请慢慢开启炉膛到最大 1.8 用合适的PCB或治具检查整个机器轨道的宽度是否一致,通常要求误差极限为1mm 1.9 将轨道宽度调整到最大及最小再重复测试轨道宽度,确定轨道宽度在要求的范围内 1.10 正常情况经过以上的确认能够完全排除掉板问题(前后传送轨道需优先确认,炉膛异物需要注意) 2. 生产中不确定的时间的掉板(不确定的频率,不确定的时间) 2.1 请优先检查前后传送轨道是否对齐,宽度调整是否合适,以及机器轨道的设定及前后差异是否合适 2.2 检查你的PCB或治具是否在进炉以前已经严重变形,治具是否损坏,方向是否正确 2.3 检查PCB掉入机器的PCB及治具的宽度是否与机器的轨道宽度设定符合 2.4 检查机器防跌落机构或中心支撑机构是否设定正确(公司目前尚未配备CBS) 2.5 经过以上仔细的检查和确认,这种问题通常是能够很快解决的