供应商品质评价流程图
质量保证流程图

出入帐本登记 Q/YQ.QP-14 生产计划部通知各部
门做好生产准备
检验方法及设备 质量记录
合同评审记录
外观:目测 尺寸:卡尺 功 能:装配 重量:电子秤
供应商审查报告
采购单
进料暂收单 进料检验报告 材料品质异常通知单 进料暂收单 领料单 电脑账 订单生产通知单 装配生产通知单 模具设备检查记录
Q/YQ.QP-14
1)资材课核对送货并通知IQC对来料检验
2)IQC根据检验基准对原材料进行检验或
验证,记录结果并进行检验壮态标识 1)物料执行先入先出的原则 2)对仓库进行定期检查,以防止变质损坏 3)收发料的凭证 1)生产设备的能力 2)模具的使用状态 3)样品是否齐备 4)检验标准是否清楚
1)对生产设备的日常检查及维修
Q/YQ.QP-12 Q/YQ.QP-13
建立设备及冶工具台帐
依作业指导书进生产
按计划对人员实施培训
及管制
实施LINE STOP制度 、生产环境5S管理
IPQC巡检、LINE QC外观、功能全检
建立作业指导书、工程图、工艺流程图
日常工程确认表 修理日报表 制程点检表
1)产品包装规格 2)包装材料
1)QA对按作业指导]执行最终检验,并对检验结果进行 记录
建立设备及模具台帐 工艺参数电脑管理 车间实施5S管理
注塑机共14台 、冲床 共17台 外观:目测 尺寸:卡尺
2小时一次巡检,出现问题及时反馈,按产品 功能:装配
编号统计当天损耗率
重量:电子秤
模具维护记录 设备维护记录
过程控制记录 过程检验记录
对生产设备及仪器进行日常检查及维护 对人员能力的培养 出现问题及时解决的能力 对生产环境的控制 过程质量控制
供应商的选择与评价流程图
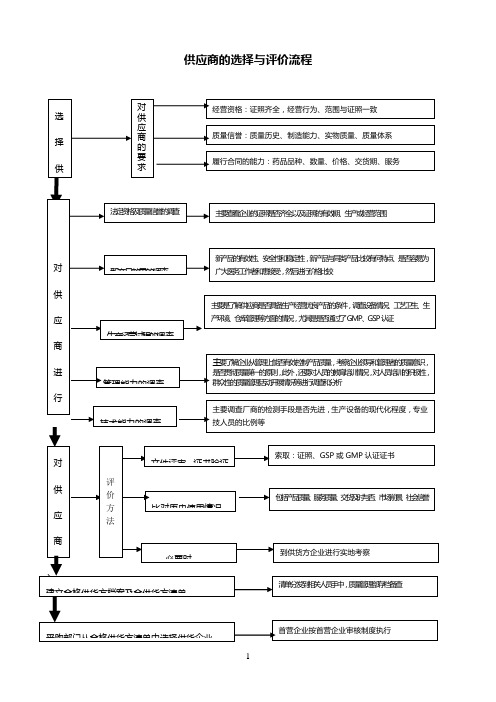
供应商的选择与评价流程编制釆购计划流程图药品购进管理药品的购进管理是药品经营企业质量过程控制的第一关。
也是确保企业经营行为合法性、保证药品经营质量关键环节。
采购员在药品的釆购过程中,承担着药品质量控制的直接责任,质量管理员必须对药品购进全过程实施有效的监督控制,按照药品的购进质量程序,严格审核供货企业的合法性和购进药品的合法性,确实把好药品购进质量关。
所以药品经营企业购进药品应严格遵循以下原则:一、购进原则1、质量第一药品是特殊商品,是人们用于预防、治疗、诊断疾病的物质,药品的质量至关重要,药品质量合格与否,直接关系到患者的生命安全。
因此,在选择药品和供货单位时,企业应该始终把质量放在首位,购进药品应当以满足人们预防、治疗、诊断疾病的需要要为目标.2、按需进货购进药品还应当以市场需要为导向.有些药品的销售也分淡季和旺季。
旺季就应该提前准备好货(例如:夏季消暑、防暑类药品藿香正气丸、清凉油、风油精等;秋冬季节,天气干燥,清肺、润肺、温肺化饮的药品.);反之,淡季则应少进货,不然就会造成药品积压,超过有效期的药品会给企业带来直接损失。
3、择优选购“货比三家”是一种普遍的心理,药品的购进当然也不例外.购进药品时在保证质量的前提下要进行价位、疗效等比较.二、药品购进的程序1、确定供货企业的法定资格及质量信誉业务购进部门负责索取并审核供货企业的合法证照,审核时应对供货方的《药品经营(生产)许可证》和“营业执照"核准的经营方式、经营范围严格把关,确保购进行为和购进药品的合法性。
业务购进部门应建立包括所有供货方资料的“合格供货方档案"。
(可对合格供货方实行企业代码识别控制管理,对在本企业已建立“合格供货方档案"或享有企业代码的供货企业,业务部门可与之正常开展业务往来;对未建立“合格供货方档案”且无企业代码的供货企业,在进货时应对供货单位按首营企业进行审核。
)2、审核所购入药品的合法性和质量可靠性;企业购进的药品应符合以下基本条件,以确保其合法性:●合法企业所生产的药品●具有法的质量标准,即国家药品标准●除国家未规定实施批准文号管理的中药材和中药饮片外,应有规定的批准文号和生产批号●进口药品应有符合规定的、加盖了供货单位质量管理机构原印章的《进口药品注册证》和《进口药品检验报告书》或《进品药品通关单》的复印件●包装和标识符合有关规定和储运要求●中药材应标明产地★国家药品标准:是指国家为保证药品质量所制定的质量指标(性状、熔点、吸收系数、干燥失重、炽灼残渣)(不溶性微粒、热原、重金属、砷盐)检验方法(鉴别、含量测定)以及生产工艺等技术要求,包括国家药品监督管理局颁布《中华人民和国药典》、药品注册标准和其它药品标准。
产品质量检验管理程序(含流程图)
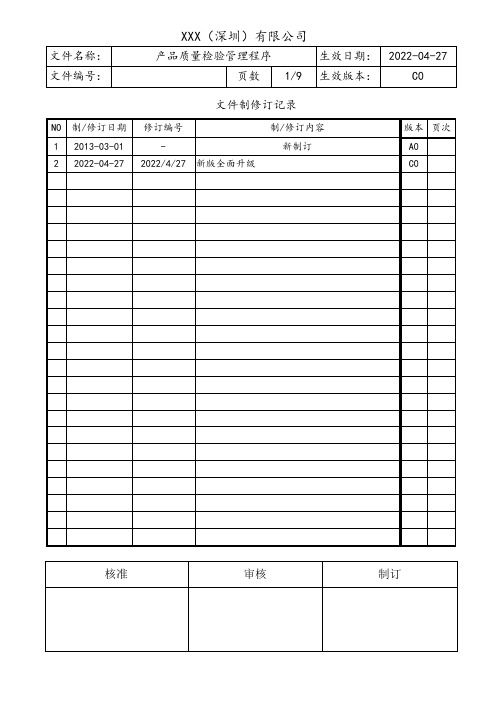
文件制修订记录1.0目的为了有效测量与监控产品从进料、制程、成品及出货各阶段检验作业能始终符合产品工程规范的各项要求。
2.0范围:适用于品管IQC、IPQC、QA过程作业。
3.0权责:3.1品管部:负责各阶段品质检验的执行、标识、追溯的管理、实际验货。
3.2工程部:产品作业标准的制定与检查。
3.3生产部:依生产计划、工程标准、验收标准执行生产作业。
3.4业务部:依订单需求验收出货数量。
3.5资材部:采购物料的外部联络。
4.0定义:无5.0作业内容:5.1进料检验5.1.1收料5.1.1.1供应商依据采购订单交货到公司仓库。
5.1.1.2仓管依据采购订单核对送货单是否一致,如若不符则退货并要求供应商重新交货,符合则点收数量并开出[进货单]。
5.1.1.3仓管将[进货单]连同要求供应商提供的相关文件(如材质报告、检验报告、测试报告等)交品管部,通知IQC进行检验。
5.1.1.4检验参照依据AQL表或依客户端需求作抽样检验。
5.1.1.5品管部IQC接到[进货单]后对供应商所提供的文件进行验证,(有法规环保类要求的产品必须依客户指定或经国家认可有检测能力机构出具的测试报告,如“SGS报告”等);品管部可以根据批量大小、价值贵重程度来对供应商所提供产品的材质进行一次确认。
5.1.1.5下列几项物料必须由品管部进料检验:a)生产性原材料。
b)外发加工产品。
c)包装材料等。
5.1.2需应用下列一种或多种方法进行验收、检验5.1.2.1接收检验及测试:a)核对材质证明(限自购原材料,样品或来料加工产品可不需要提供材质证明),核对供应商提供的相关文件。
b)依《检验标准书》逐项检验与填写[进料检验报告],无《检验标准书》时,依图面求或样板检验,检验结果可直接记录于[进料检验报告]上。
c)凡属客户提供来料进行加工,如无图面,依据客户提供的规格进行检验;如既无规格又无图面,IQC只针对其外观进行检验并记录于[进料检验报告]上。
供应商管理程序流程图

保留凭据,填写 ⑾、⑿
供应商管理程序流程图
记录 ⑴供应商调查表
⑵样件验收表
⑶检验记录单 ⑷合格供应商批量供货评审 表
⑸采购合同 ⑹合格供应商名单 ⑺供应商产品质量月汇总 表
⑻供应商月度品质评价表
⑼供应商综合评价表
⑽质量信息反馈处理单
⑾索赔单 ⑿挑选记录单
程序
总经理
供应商的选 择
供应商管理程序流程图
供应商
职能 采购部
品质部
研发部
选择、洽谈,发出⑴
填写⑴、提供资料 送样(5~10件)
验收,填写⑵
NO
重新 送样
OK
小批量供货(50 ~100套)
供应商的准 入
批准
OK通知 填写⑷
全检,记录⑶
评审
批量供货
签订⑸
批准
编制⑹
对交货产品进行 检验,进行质量
评分,填写⑺
供应商的评 价
审批
结合⑺、质量评分、 交货准时率、配合度 和产品包装等填写⑻
每年年底组织综合评 价(产品质量状况、 顾客反馈、交货履约 、配合度和产品包装
等,填写⑼
供应商质量 问题的处理
供应商质量 问题的处理
对供应商的 索赔
批准
被索赔(扣货款)
产品质量问题(进 货检验、生产过程 、顾客反馈),发 出⑽,限期回复及
供应商质量管理流程图:步骤详解

• 提高供应商评审和评估的准确性和有效性
降低供应链质量风险
• 建立供应商风险管理机制
• 及时发现和应对供应商质量问题
• 提高供应链的可靠性和稳定性
供应商质量管理对企业竞争力的影响
提高产品质量
降低生产成本
增强企业竞争力
• 增强产品性能和客户满意度
• 优化供应链管理,提高生产效率
⌛️
质量控制与改进
• 建立供应商的质量控制体系
• 制定供应商的质量检验标准和程序
• 促进供应商持续改进质量管理体系和产品质量
供应商质量管理体系的建立与实施
制定供应商质量管理手册
• 明确供应商质量管理的基本要求和程序
• 制定供应商质量管理的操作指南和实施细则
• 确保供应商质量管理手册符合标准和法规要求
• 流程连接:表示流程步骤之间的关联和依赖关系
供应商质量管理流程图的绘制步骤与方法
确定流程图的绘制目标
绘制流程图的框架
• 明确供应商质量管理的关键环节和流程
• 绘制顶层流程图,展示供应商质量管理的
• 确定流程图的层次结构和详细程度
整体流程
• 确定子流程图的布局和顺序
绘制流程图的细节
检查和优化流程图
• 建立良好的供应商合作关系
• 提高市场竞争力和品牌价值
• 降低不良品返工和维修费用
• 提高市场份额和品牌价值
• 降低客户投诉和退换货率
• 提高企业盈利能力
• 降低供应链风险
02
供应商的选择与评估
供应商选择的标准与依据
质量标准
• 供应商的产品质量水平
• 供应商的质量管理体系和认证
供应商评审流程图

结序束
供应商评审流程图
流程名称
供应商评审流程
编号
内容
供应商质量评价
执行部门
质检部
部门
管代
质检科
采储科
相关供应商
审核 是 是否合
格
工 作 程 序
组织现场审核小 组
现场审核
现场审核报告
通知供应商
准备 现场审核接
待
未通过
跟踪验 证
列入合格供应商 样件名检录验评定
结束
放弃 否
限期整改
不合格
相关制度 流程名称
委外产品检验流程
编号
内容
委外产品质量管理
执行部门
质检部
部门 技术科
质检科
质检员
外协
相关供应商
工 作 程 序
相关制 度
首件评审
是否合
格
否
制定纠正措施
开始 执行首件检
验 填写首检记 合格录
跟踪验证 合格
送样
通知供应 商
制定整改计
划 实施
批量生产
收到检验通知 单
执行检验
报检
生产完工
填写“外协产
品检验卡” 是否合
否 通知供应
质量检验控制流程图

10
提料
过程检验
N
技术分析
1.IPQC(制程检验员)对半成品工艺材质和作业手法进 行。2.有品质异常时技术部进行技术分析出矫正方案
1.装配组按照配置清单领料。2.对物料进行自检合格才
11
成品装配
可装配。3.现场加工部位要通知检验员确认。4.严格按
照作业指导书的工艺作业。
N产品损坏或其他异常
4.检验不合格请生产部重工后再送检。
15
装柜发货
1.样品确认后根据订单可进行外购件的批量采购普和半 成品加工; 2.自检物料合格才可生产,严格按规范操作; 3.过程不良时要按技术部的方案进行重工处理,并通知 质检员确认。 1.对供应商物料核对数量及规格查看包装完整性必须标 识有送货单,2.报检给IQC(进料检验)。3.实物不符 或检验不合格时请通知采购与供应商联络办理退货手续 。 1.核对确认样品以及技术图纸。2.按检验规范和技术参 数的要求进行检验。3.合格后在实物包装上贴上“合格 ”标签并通知仓库入库。4.有不合格品超出允收水准, 通知仓库要求退货。5.将不合格事件知会采购,通知供 应商改善。
1.根据技术参数要求外购件样品购买; 2.购买的样品要有说明书,出厂检验报告,安全器件要 有注册检验报告或者认证证书,特殊要求材料要有第三 方检验材料成份报告; 3.进行制样或者小批量生产。
1.技术员对样品进行全面的试验; 2.符合技术要求的要贴合格标签并签名; 3.样品不符合返回图纸设计到制样重新跟踪解决。
质量检验控制流程图
步 骤 采购
仓库
部门 质量
生产
技术
说明
1
图纸设计 1.根据订单要求设计产品
2
供应商质量管理流程图
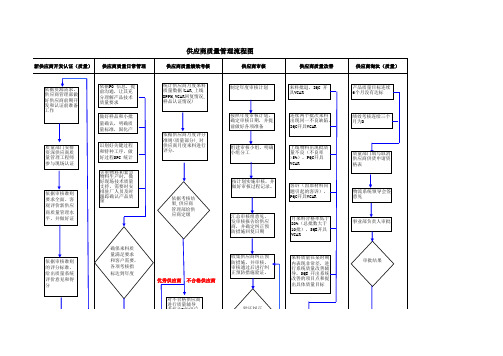
同意 不同意
信息反馈供应商管 部,从系统中注销 供应商资格。
进行高层沟通,组 建辅导团队,再次 进行质量辅导
SQE 审核报 告并验证改 善措施效果
OK
NG
验证合格后,此 项改善结束,问 题关闭
直接取消备选 供应商资格
月来料合格率低于 80%(总批数大于 10批),SQE开具 VCAR
优秀供应商 不合格供应商
收集供应商纠正预 防措施,并审核, 审核通过后进行纠 正预防措施验证。
对不合格供应商 进行质量辅导, 考核为D的供应
验证纠正
来料质量在某时期 内表现非常差,进 行系统质量改善辅 导,SQE 开出系统 改善的项目点和提 出具体质量目标
新供应商开发认证(质量) 供应商质量日常管理
供应商质量管理流程图
供应商质量绩效考核
供应商审核
供应商质量改善
依据资源需求, 供应商管理部做 好供应商前期开 发和认证前准备 工作
质量部门安排 资深供应商质 量管理工程师 参与现场认证
依据审核准则 要求全面、客 观评价新供应评价意见和得 分
依据PO 信息,提 前沟通,让其充 分理解产品技术 质量要求
做好样品和小批 量确认,明确质 量标准,固化产
识别好关键过程 和特种工序,做 好过程SPC 统计
关重物料和紧急 物料生产时,做 好现场技术质量 支持,需要时安 排驻厂人员及时 跟踪确认产品质 量
确保来料质 量满足要求 和客户需要, 各项考核指 标达到年度
统计供应商月度来料 质量数据(LAR,上线 DPPM,VCAR回复情况, 样品认证情况)
依据供应商月度评分 准则(质量部分),对 供应商月度来料进行 评分.
检测方式及不合格品处理流程图

供应商来料 仓库收料 仓库清点数量 IQC抽检
合格品 报表记录
IQC作业流程
不合格品 特采/挑选 良品入库
采购退货 不良区 拒收 异常反馈单
IPQC作业流程
OK 首样制作/自检
NG
NG 品质异常单
OK IPQC确认
批量生产
判定 OK
OK IPQC巡回检验
生产实施纠正
NG
OK
IPQC确认
成品检验 OK
不合格品控制程序
1.目的:
为了对不合格品进行标识、记录、评价、隔离 (可行时)和处置的控制,以防止不合格品的非 预期使用和交付。可疑品将作为不合格品予以 控制直到最终状态被确认。
为了降低不合格品的数量过多的流入生产,因 此检测的方式及作业流程如下:
①减量抽检 ②正常抽检 ③加严抽检 ④IQC作业流程
AQL减量抽检表
当来料及成品检测连 续5-10批合格后,可 以作为减量抽检,但 若有出现1批不良时, 立即改为正常抽检
AQL正常抽检表
一般情况下,不管是 来料还是成品检测中, 都以单次二级正常抽 检表为主
AQL加严抽检表
当来料或者成品正 常抽检当中,连续3 批出现不良状况时, 应当以加严抽检为 主,直到检测合格 批次连续为3批后, 方能回到正常抽检
生产成品
成品检验
库存三个月成品
合格
成品检验
不合格
报废
老化
包装
出货
此课件下载可自行编辑修改,供参考! 部分内容来源于网络,如有侵权请与我联系删除!
iqc作业流程aql减量抽检表当来料及成品检测连续510批合格后可以作为减量抽检但若有出现1批不良时立即改为正常抽检aql正常抽检表一般情况下不管是来料还是成品检测中都以单次二级正常抽检表为主aql加严抽检表当来料或者成品正常抽检当中连续3批出现不良状况时应当以加严抽检为主直到检测合格批次连续为3批后方能回到正常抽检iqc作业流程供应商来料仓库收料仓库清点数量iqc抽检不合格品合格品报表记录良品入库拒收异常反馈单不良区采购退货特采挑选ipqc作业流程首样制作自检ipqc确认批量生产ipqc巡回检验判定品质异常单生产实施纠正ipqc确认成品检验okokokokokokokokngngokokngngngngokok成品检验库存三个月成品生产成品成品检验合格不合格报废老化产品返工特许放行fqcoqc包装出货此课件下载可自行编辑修改供参考
供应商品质问题控制管理流程图

版本拟制A/0mwiyingwu 权责参考文件作业依据《供应商回复的改善报
告》
《来料检验报告》
《供应商回复的改善报
告》
《来料检验报告》
IQC检验中发现的来料异常
生产中发现的来料异常
试产中发现的来料异常
品质异常联络单通知采购联系供应商
采购、品质跟进供应商回复改善方案
品质跟进供应商改
善结果
结案
提出改善对策
知会采购部
继续跟进供应商回
复改善结果《来料检验报告》《巡检报告》《品质异常处理单》
《试产报告》
《品质异常处理单》
采购部《来料检验规范》《制程巡检作业规
范》
《生产管理作业规
范》
《试产作业规范》
《供应商品质控制管理流程》《来料检验规范》
《供应商品质控制管理流程》《来料检验规范》
供应商
采购部
品质部
品质部
采购部
品质部
采购部供应商
IQC IPQC 生产
工程部OK
NG
OK
NG
文件编号文件名
MX/WI006-2020
供应商品质问题控制管理流程图
xxxxxx有限公司供应商品质问题控制管理流程图。
品质部检验流程图总表

[品质部管理流程图]1:品质管控流程图2:QA成品检验流程图3:IPQC巡检流程图4:IQC来料检验流程图品质管控流程图 厂商交货IQC 检验生产计划IPQC 首件检IPQC 巡回检生产安排 发现不合格品QC 测试发现不 合格品发现不 合格品QA 检验joK 品贴绿色标标 识预防改善______________. _____处置1 T异常开案1 r隔离发现不 合格品QA成品检验流程图流程说明1:生产线把做好的成品送检至QA o2:QA根据《产品规格书、图纸》《样品》《生产指令单》《AQL抽样计划》对送检成品进行外观和功能性检验,有必要时需进行可靠性试验。
3:检验完成时填写《QA检验报告》记录存档。
4:产品合格后贴绿色合格标识并通知入库,产品不合格则贴红色标识,注明不良原因,并开出《QA检验不良报告》。
5:由品质部,研发中心,业务部,生产部门,计划部共同确认不良产品处理方式。
6:处理方法确认后对不良产品进行处理,并跟进。
流程说明1:生产线领料后按《作业指导 书》进行首件制作。
2:生产线制作首件交于IPQC 进行首件确认。
3:IPQC 根据《作业指导书》 《产品规格图纸》《产品规格 书》《样品》对首件的性能, 外观,尺寸进行确认,并填写 《首件确认表》。
4:首件合格后交由生产并开 始生产作业,首件不合格则要 求生产分析并作出改善措施, 重做首件进行确认。
5:正常生产开始后IPQC 进行 巡回检验,作业员需按照《生 产SOP 》进行作业,注意电 子产品的防护。
6:巡检未发现异常,生产持续 作业至产品完工,如巡检过程 发现异常,开出《生产异常报 告》通知生产,品质部,研发 中心。
7:生产,品质部,研发中心分 析不良原因,给出改善措施。
确定是否需要停止生产。
8:确定改善措施后,IPQC 进 行监督性检验,跟进措施实行 效果。
9:产品生产完工,生产移交产 品或入库。
10:IPQC 填写《每日巡检报 告》IPQC 巡检流程----首件检验kt !1!重做首样不合格 合格生产移交或入库供应商/外协厂送货至仓库仓库收料打单送检IQCIQC检验流程图IQC进行物料检验(根据承认书.样板.规格书等)填写?IQC检验报告?流程说明1:供应商/外协厂送货至仓库,仓库确认数量,型号,合格放置待检区并打单送至IQC,不合格退货至供应商。
供方选择与评价控制程序(带流程图)
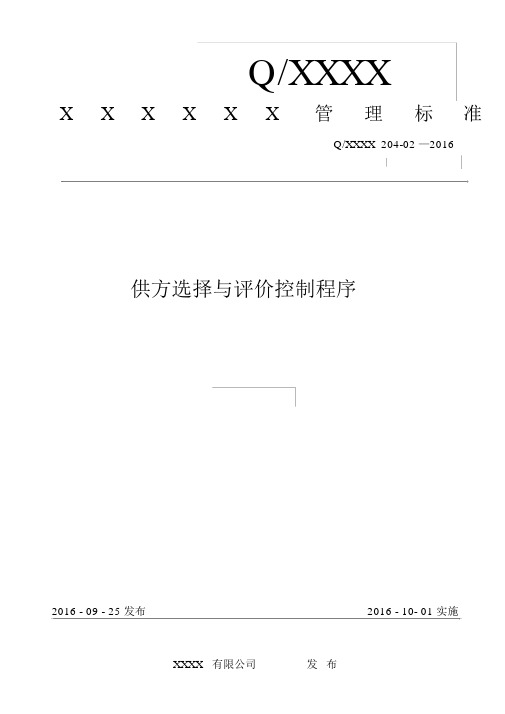
Q/XXXXX X X X X X管理标准Q/XXXX 204-02 —2016供方选择与评价控制程序2016 - 09 - 25 发布2016 - 10- 01 实施供方选择与评价控制程序1范围本办法适用于公司采购部对供方选择与评价管理。
本办法确定了对供方选择与评价管理流程及方法。
2规范性引用文件Q/XXXX 201-01-2016 《质量、环境、职业健康安全管理手册》Q/XXXX 204-04-2012 《零部件委外加工管理办法》Q/XXXX 204-05-2011《采购价格审批监管制度》3术语3.1供方提供产品的组织或个人。
3.2合格供方临时供方通过小批量供货验证,某种规格物料的产品质量、供货能力、服务及价格评价合格,可以为公司批量提供该种物料的供方。
3.3优秀供方经过对合格供方评价,合格供方评价分数在规定分数以上的合格供方确认为优秀供方。
4职责与权限本程序涉及相关部门及岗位人员职责权限如下:a)资材采购部负责本制度修订、宣贯和实施,对本制度符合性、适宜性与有效性负责;同时负责供方信息收集、沟通;负责组织对供方开发、调查、筛选、评价、选定和考核;负责供方档案的资料齐套、更新等归档的管理。
b)技术部负责参与供方的开发、选择和评价;负责《采购物料样品确认单》及《小批量物料试用报告单》的确认。
c)品保部负责供方来料的检验,参与供方的评价、考核和评比;负责各供方月进货质量统计上报。
d)生产部负责对供方物料《小批量试用报告单》试用结果的填写;参与供方评价。
e)管理者代表负责来料质量事故最终处理和《供方评价表》的审核。
f)总裁负责《合格供方名册》审批意见签署。
5管理内容、方法与要求5.1开发供方时机5.1.1新开发产品供方选择当配套客户指定的材料生产厂家或技术部开发产品寻找新材料而现有供方不能提供时,任何部门提供可靠讯息,采购部发出多家《供方调查表》,必要时组织相关部门现场调查,对多家调查结果进行评估,样品合格后,择优取用。
供应商审核流程图

供应商审核流程图供应商审核是企业采购管理中的重要环节,通过审核能够确保供应商的合法性、可靠性和合作能力,为企业的采购决策提供参考依据。
以下是一个供应商审核的流程图示例,简洁明了地展示了整个审核过程。
第一步:确定审核对象企业确定需要审核的供应商对象,这可以是新的潜在供应商,或者是对现有供应商的再次审核。
第二步:搜集供应商信息企业收集供应商的相关信息,包括但不限于企业注册信息、营业执照、税务登记证、生产能力、产品质量认证、经验和声誉等。
第三步:初步筛选根据收集到的供应商信息,初步筛选出满足企业要求的供应商。
筛选的标准可以包括供应商的合法性、质量管理体系认证情况、资金实力等。
第四步:面谈和考察对通过初步筛选的供应商进行面谈和考察,了解其实际情况和经营状况。
面谈可以包括与供应商代表的会议、电话沟通等形式,考察可以包括参观供应商的生产基地、调研其产品质量等。
第五步:风险评估对供应商的风险进行评估,包括但不限于供应商的信用状况、稳定性、合规性等。
根据评估结果,确定供应商是否符合企业的合作要求。
第六步:合同签订符合企业要求的供应商会进入合同签订阶段。
在签订合同前,企业应与供应商协商并明确双方的合作条件、付款方式、配送方式等。
第七步:持续审核审核并选择供应商不是一次性的工作,企业需要建立持续的供应商审核机制。
通过定期或不定期的审核,确保供应商仍然符合企业的合作要求。
这些审核可以包括对供应商的质量管理体系、交付绩效、售后服务等进行评估。
通过以上流程图,企业可以清晰地了解供应商审核的全过程,并根据实际情况进行调整和优化。
建立一个科学有效的供应商审核机制,能够确保企业与合适的供应商进行长期稳定的合作,提升采购管理的效率和效果。
以上是供应商审核流程图的内容,希望能够对您有所帮助。
如有任何问题,请随时与我联系。
品质体系

品质体系的一般架构图中各缩写词含义如下:QC:Quality Control 品质控制QA:Quality Assurance 品质保证QE:Quality Engineering 品质工程IQC:Incoming Quality Control 来料品质控制LQC:Line Quality Control 生产线品质控制IPQC:In Process Quality Control 制程品质控制FQC:Final Quality Control 最终品质控制SQA:Source (Supplier) Quality Assurance 供应商品质控制DCC:Document Control Center 文控中心PQA:Process Quality Assurance 制程品质保证FQA:Final Quality Assurance 最终品质保证DAS:Defects Analysis System 缺陷分析系统FA:Failure Analysis 坏品分析CPI:Continuous Process Improvement 连续工序改善CS: Customer Service 客户服务TRAINNING:培训一供应商品质保证(SQA)1.SQA概念SQA即供应商品质保证,识通过在供应商处设立专人进行抽样检验,并定期对供应商进行审核、评价而从最源头实施品质保证的一种方法。
是以预防为主思想的体现。
2.SQA组织结构3.主要职责1)对从来料品质控制(IQC)/生产及其他渠道所获取的信息进行分析、综合,把结果反馈给供应商,并要求改善。
2)耕具派驻检验远提供的品质情报对供应商品质进行跟踪。
3)定期对供应商进行审核,及时发现品质隐患。
4)根据实际不定期给供应商导入先进的品质管理手法及检验手段,推动其品质保证能力的提升。
5)根据公司的生产反馈情况、派驻人员检验结果、对投宿反应速度及态度对供应商进行排序,为公司对供应商的取舍提供依据。
供应商评价流程图

金额范围 大于 5 万
质量管理审核 质量管理审核
质量管理部门审核
质量主管及 相关工作人 员
供应商评价 表
N
通 过 财务部评价 财务部评价 财务部负责 人 供应商评价 表
Y
财务部门评价
N
同意
Y
确认评价过程 质量管理确认 评价过程有效 有效 总经办质量管理评 价 质量主管 供应商评价 表
管理者代表或 管理者代表或总经理批准 总经理批准 注:采购额在 同意 100 万 / 年 以 上 由总经理审批。
管理者代表或总经 理批准
管理者代表 或总经理
供应商评价 表
N
Y
申请部门及质量管理归档
供应商评价流程图
流程
供应商评价流程 节点名称 节点解释 节点执门评价后提 交部门负责人及其 它相关部门进行评 价 采购部门领导 采购部门评价 大于等于 1 万小于等于 5 万 评价 采购部门领导评价 采购部门负 责人 供应商评价 表 采购申请人 及申请部门 供应商评价 表
品质保证体系流程图
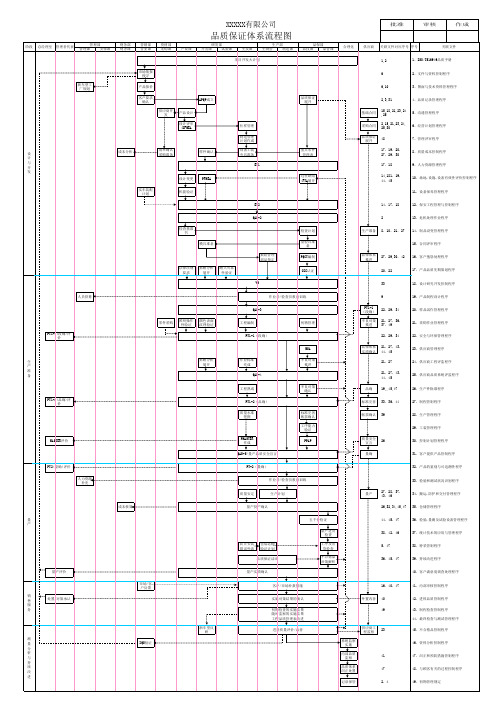
生产准备 8,10,21,27 14、制品设变管理程序
15、合同评审程序
品保体系 推进
27,29,30,42
16、客户抱怨处理程序
20,22
17、产品品质先期策划程序
33
18、设计研究开发控制程序
人员招募
PT1-1(段确)评 价
生 产 准 备
PT1-2(品确)评 价
MASTER评价
零件采购
照明操作 性验证
阶段
总经理室 管理者代表
管理部
管理课
安保课
财务部 财务课
营销部 营业课
资材部 采购课
产设课
XXXXX有限公司
品质保证体系流程图
研发部
开发课
试验课
生技课
生产部
生物管
制造课
品保部
品技课
品管课
项目开发大计划
市场情报 搜寻
新车型工 厂规划
产品报价
客户要求 确认
APQP成立
品质保证 展开
供应商开 发
产品设计
设计评审 /DFMEA
22,29,34
不良对策 21,27,36, 推进 37,49
22,29,34
品保体系 21,27,43, 实绩确认 44,45
21,27
21,27,43, 44,45
品确 19,,45,47
19、产品制程设计程序 20、样品试作管理程序 21、采购作业管理程序 22、安全与环保管理程序 23、供应商管理程序 24、供应商工程评监程序 25、供应商品质系统评监程序 26、生产件批准程序
内部品质 监察
41
品质体系 纠正处置
47
记录保管
2,4
产品品质管理系统流程图

标
零件
标准,
来料
置待 检区
IQC 检验
NG
OK
入合 格区
入原 料仓
作业 过程
装配 (关键
成品测
IPQ C过OK 试(关 来自K 键质控OKFQC质控点)
点)
NG
NG
不合格标
不合格标
记录、隔离
record,insulat e
记录、隔离
record,insulat e
包装 过程
退供 应商
NG 验证改善 结果
YES 关闭
OQOCK
入成 品仓
停产
此品质管理 系统流程图 目的:(1)
运输
交付
客户服务
确认投诉信息,系统收 集客户投诉信息并与 相关部门沟通
针对客户所反映问题,确定临时纠 正措施,及后续预防改善措施
采取与落实临 时措施
现场查证问题 的根本原因
评审措施可 行性,效果确
认
整理CAR报告
拒收
置不合格区
nonconformity area
特别采用
挑选/返工使用 (供应商或生产挑选)
NG
OK
正常流程 frequent flow
异常 处no理nco流fo程r mity
发出公司内 部质量纠正 预防行动报
告单
YES 质量管理部/生
是否要停产改
产制造部经理
NG
分析原因并 制订改善措
确认原因与措施
- 1、下载文档前请自行甄别文档内容的完整性,平台不提供额外的编辑、内容补充、找答案等附加服务。
- 2、"仅部分预览"的文档,不可在线预览部分如存在完整性等问题,可反馈申请退款(可完整预览的文档不适用该条件!)。
- 3、如文档侵犯您的权益,请联系客服反馈,我们会尽快为您处理(人工客服工作时间:9:00-18:30)。
C级:≥70分 级 分
定期检讨会议 开展改善活动 3个月事后监管
前端管理
年度供应商管理方案 供应商辅导/培训 SQE驻在管理 定期工厂审查 质量保证协议书 供应商Benchmarking活动 D级:≥60分 级 分 驻在管理/现场验收 树立品质改善计划 临时工厂审查
来料检查
部品来料检查 部品工程品质监视/检讨 部品品质异常检讨 树立部品问题点对策 对策效果验证管理 CTQ部品的Cpk管理
-. Business review meeting -. Corrective actions -. Effect monitoring On-. On-site support On-. On-site check and accept -. Corrective actions -. Audit -. PO cancel Re-. Re-evaluate -. Supplier cancel
EVE Energy
供应商 品质管理 流程
新供应商导入评审
供应商品质实绩管理
A级:≥90分 级 分 B级讨会议运营 内部客户部品满意度调查 订单配额管理会议 供应商自主改善课题展开
供方资信/交付能力--采购 工厂体系/品质水准--品管 新品认可/技术评估--研发
IQC
Sampling/Inspection Monitoring parts in process Defect analysis Sending NCR Improvement effect confirming CTQ parts control
E Rank:<60
Version Jan. 2010
Supplier Performance Management
A Rank:≥90
Supplier Chains Analysis
Monthly performance review Business review meeting Internal VOC survey Cutting the PO Improvement project
Supplier Quality Management Process
New Supplier Development Review
Capital Credit/ Production capacity Quality system/Quality level New parts certification/ SPEC review
E级:<60分 级 分
交货中止 重新评定供应商资格 订单终止
Version Jan. 2010
EVE Energy
B Rank:≥80
C Rank:≥70
Front-end Management
Annual SQM project/plan Training the Supplier SQE on-site management Regularity Q-system audit Quality assurance agreement Supplier benchmarking D Rank:≥60