塑胶产品设计方法及注意事项
塑胶件设计准则较全
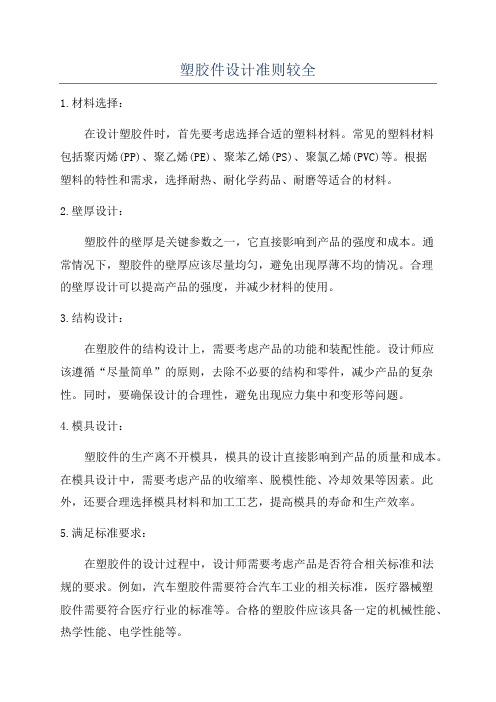
塑胶件设计准则较全1.材料选择:在设计塑胶件时,首先要考虑选择合适的塑料材料。
常见的塑料材料包括聚丙烯(PP)、聚乙烯(PE)、聚苯乙烯(PS)、聚氯乙烯(PVC)等。
根据塑料的特性和需求,选择耐热、耐化学药品、耐磨等适合的材料。
2.壁厚设计:塑胶件的壁厚是关键参数之一,它直接影响到产品的强度和成本。
通常情况下,塑胶件的壁厚应该尽量均匀,避免出现厚薄不均的情况。
合理的壁厚设计可以提高产品的强度,并减少材料的使用。
3.结构设计:在塑胶件的结构设计上,需要考虑产品的功能和装配性能。
设计师应该遵循“尽量简单”的原则,去除不必要的结构和零件,减少产品的复杂性。
同时,要确保设计的合理性,避免出现应力集中和变形等问题。
4.模具设计:塑胶件的生产离不开模具,模具的设计直接影响到产品的质量和成本。
在模具设计中,需要考虑产品的收缩率、脱模性能、冷却效果等因素。
此外,还要合理选择模具材料和加工工艺,提高模具的寿命和生产效率。
5.满足标准要求:在塑胶件的设计过程中,设计师需要考虑产品是否符合相关标准和法规的要求。
例如,汽车塑胶件需要符合汽车工业的相关标准,医疗器械塑胶件需要符合医疗行业的标准等。
合格的塑胶件应该具备一定的机械性能、热学性能、电学性能等。
6.通气设计:塑胶件在注塑过程中需要排除气体,否则会产生气泡和内部缺陷。
因此,在塑胶件的设计中,需要考虑通气的问题。
设计师可以在塑胶件的壁厚较大的地方设置气脱模系统,提高产品的质量。
7.可回收性设计:在现代社会,环保意识日益增强,可回收性成为塑胶件设计的一个重要考虑因素。
设计师应该尽量选择可回收的塑料材料,并设计可分解、可回收利用的产品。
总结起来,塑胶件设计准则涉及到材料选择、壁厚设计、结构设计、模具设计、标准要求、通气设计和可回收性设计等方面。
设计师在进行塑胶件设计时,应根据具体的产品需求和行业要求,合理应用这些准则,确保塑胶件的质量和性能,提高产品的竞争力。
塑胶产品结构设计重点

塑胶产品结构设计重点一、材料选择塑胶产品的结构设计首先要考虑材料选择。
材料的选择直接关系到产品的性能、质量和成本,因此需要根据产品的具体要求和使用环境,选择适合的塑胶材料。
常见的塑胶材料有聚乙烯(PE)、聚丙烯(PP)、聚氯乙烯(PVC)、聚苯乙烯(PS)、聚酯(PET)等。
在选择材料时需要考虑产品的机械性能、耐热性、耐化学性、耐候性、电气性能、透明度等因素。
同时还需要考虑材料的加工性能,如流动性、热稳定性、收缩率等。
材料的选择不合理会导致产品性能不达标或加工工艺困难,因此需要在产品设计之前进行充分的材料筛选和试验。
二、结构设计塑胶产品结构设计主要包括外形设计和内部结构设计。
外形设计需要考虑产品的功能、美观和人机工程学等因素。
合理的外形设计可以提升产品的市场竞争力和用户体验。
内部结构设计需要考虑产品的强度、稳定性和装配性等因素。
合理的内部结构设计可以提高产品的性能和质量,减少生产和使用过程中的故障和损坏。
此外还需要考虑产品的可制造性和生产效率。
在进行结构设计时,需要采用CAD软件进行三维建模和仿真分析,以验证设计的可行性和优化设计。
三、模具设计塑胶产品的生产需要模具进行注塑成型。
模具设计是塑胶产品结构设计中非常重要的一部分,直接影响产品的质量和生产效率。
模具设计需要考虑产品的尺寸、形状和结构特点,选择合适的注塑工艺,确定模具的结构和加工工艺。
模具的设计要求高精度、高效率、长寿命和低成本,需要充分考虑模具的结构强度、冷却系统、顶出系统、塑胶流道等因素。
合理的模具设计可以提高产品的精度和表面质量,降低生产成本和生产周期。
四、加工工艺塑胶产品的加工工艺是塑胶产品结构设计的最后一步,直接影响产品的成型质量和效率。
常见的塑胶加工工艺有注塑成型、吹塑成型、挤出成型、压缩成型等。
在选择和优化加工工艺时,需要考虑产品的形状、尺寸、材料特性和生产要求等因素。
合理的加工工艺可以提高产品的质量和生产效率,降低生产成本和能耗。
塑胶件设计规范范文
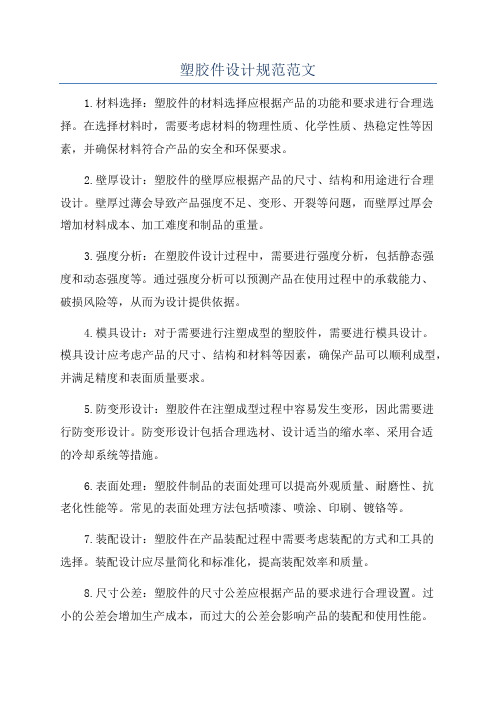
塑胶件设计规范范文1.材料选择:塑胶件的材料选择应根据产品的功能和要求进行合理选择。
在选择材料时,需要考虑材料的物理性质、化学性质、热稳定性等因素,并确保材料符合产品的安全和环保要求。
2.壁厚设计:塑胶件的壁厚应根据产品的尺寸、结构和用途进行合理设计。
壁厚过薄会导致产品强度不足、变形、开裂等问题,而壁厚过厚会增加材料成本、加工难度和制品的重量。
3.强度分析:在塑胶件设计过程中,需要进行强度分析,包括静态强度和动态强度等。
通过强度分析可以预测产品在使用过程中的承载能力、破损风险等,从而为设计提供依据。
4.模具设计:对于需要进行注塑成型的塑胶件,需要进行模具设计。
模具设计应考虑产品的尺寸、结构和材料等因素,确保产品可以顺利成型,并满足精度和表面质量要求。
5.防变形设计:塑胶件在注塑成型过程中容易发生变形,因此需要进行防变形设计。
防变形设计包括合理选材、设计适当的缩水率、采用合适的冷却系统等措施。
6.表面处理:塑胶件制品的表面处理可以提高外观质量、耐磨性、抗老化性能等。
常见的表面处理方法包括喷漆、喷涂、印刷、镀铬等。
7.装配设计:塑胶件在产品装配过程中需要考虑装配的方式和工具的选择。
装配设计应尽量简化和标准化,提高装配效率和质量。
8.尺寸公差:塑胶件的尺寸公差应根据产品的要求进行合理设置。
过小的公差会增加生产成本,而过大的公差会影响产品的装配和使用性能。
9.耐用性设计:塑胶件在使用过程中需要具有一定的耐用性。
耐用性设计包括选择合适的材料、优化结构、进行耐久性测试等。
10.产品标识:塑胶件在制造过程中需要进行产品标识,包括产品型号、批次号、生产厂家等信息。
产品标识有助于产品追溯和质量控制。
请注意,以上只是一些常见的塑胶件设计规范,具体的设计规范还需根据具体产品和行业的要求来确定。
在进行塑胶件设计时,还需充分考虑产品的使用环境、工艺要求和成本等因素,确保产品的质量和可生产性。
塑胶产品作业指导书
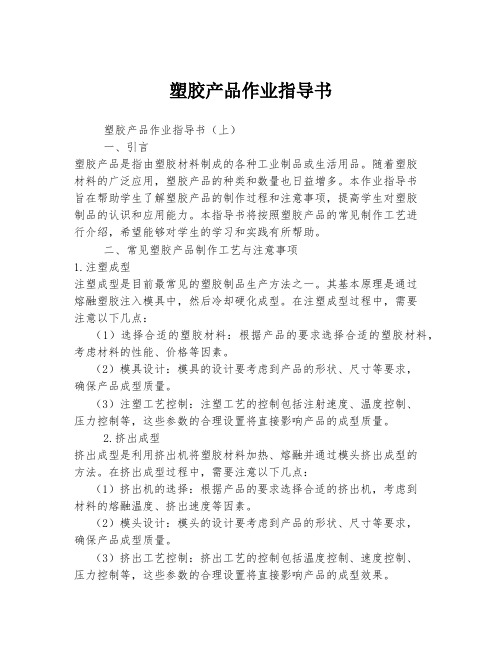
塑胶产品作业指导书塑胶产品作业指导书(上)一、引言塑胶产品是指由塑胶材料制成的各种工业制品或生活用品。
随着塑胶材料的广泛应用,塑胶产品的种类和数量也日益增多。
本作业指导书旨在帮助学生了解塑胶产品的制作过程和注意事项,提高学生对塑胶制品的认识和应用能力。
本指导书将按照塑胶产品的常见制作工艺进行介绍,希望能够对学生的学习和实践有所帮助。
二、常见塑胶产品制作工艺与注意事项1.注塑成型注塑成型是目前最常见的塑胶制品生产方法之一。
其基本原理是通过熔融塑胶注入模具中,然后冷却硬化成型。
在注塑成型过程中,需要注意以下几点:(1)选择合适的塑胶材料:根据产品的要求选择合适的塑胶材料,考虑材料的性能、价格等因素。
(2)模具设计:模具的设计要考虑到产品的形状、尺寸等要求,确保产品成型质量。
(3)注塑工艺控制:注塑工艺的控制包括注射速度、温度控制、压力控制等,这些参数的合理设置将直接影响产品的成型质量。
2.挤出成型挤出成型是利用挤出机将塑胶材料加热、熔融并通过模头挤出成型的方法。
在挤出成型过程中,需要注意以下几点:(1)挤出机的选择:根据产品的要求选择合适的挤出机,考虑到材料的熔融温度、挤出速度等因素。
(2)模头设计:模头的设计要考虑到产品的形状、尺寸等要求,确保产品成型质量。
(3)挤出工艺控制:挤出工艺的控制包括温度控制、速度控制、压力控制等,这些参数的合理设置将直接影响产品的成型效果。
3.吹塑成型吹塑成型是通过将加热的塑胶挤出成管状,并在一端封闭的空腔内注入空气,使塑胶膨胀并贴附于模具壁上,冷却后脱模而成的方法。
在吹塑成型过程中,需要注意以下几点:(1)挤出机的选择:根据产品的要求选择合适的挤出机,考虑到材料的熔融温度、挤出速度等因素。
(2)模具设计:模具的设计要考虑到产品的形状、尺寸等要求,确保产品成型质量。
(3)吹塑工艺控制:吹塑工艺的控制包括温度控制、挤出速度控制、模具压力控制等,这些参数的合理设置将直接影响产品的成型效果。
塑料产品设计注意事项
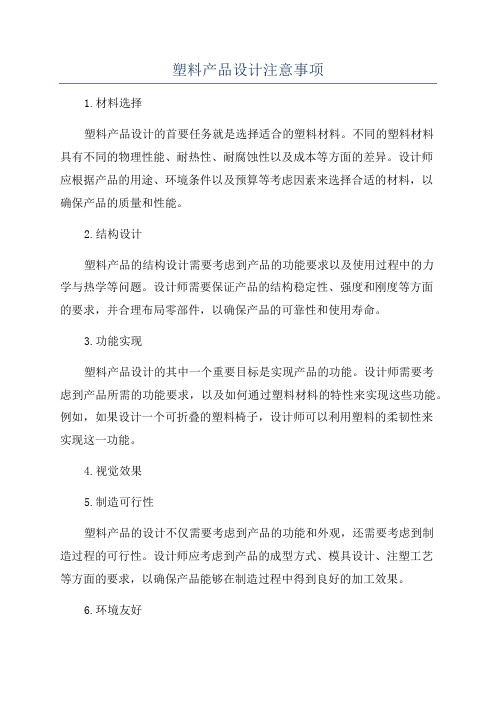
塑料产品设计注意事项
1.材料选择
塑料产品设计的首要任务就是选择适合的塑料材料。
不同的塑料材料
具有不同的物理性能、耐热性、耐腐蚀性以及成本等方面的差异。
设计师
应根据产品的用途、环境条件以及预算等考虑因素来选择合适的材料,以
确保产品的质量和性能。
2.结构设计
塑料产品的结构设计需要考虑到产品的功能要求以及使用过程中的力
学与热学等问题。
设计师需要保证产品的结构稳定性、强度和刚度等方面
的要求,并合理布局零部件,以确保产品的可靠性和使用寿命。
3.功能实现
塑料产品设计的其中一个重要目标是实现产品的功能。
设计师需要考
虑到产品所需的功能要求,以及如何通过塑料材料的特性来实现这些功能。
例如,如果设计一个可折叠的塑料椅子,设计师可以利用塑料的柔韧性来
实现这一功能。
4.视觉效果
5.制造可行性
塑料产品的设计不仅需要考虑到产品的功能和外观,还需要考虑到制
造过程的可行性。
设计师应考虑到产品的成型方式、模具设计、注塑工艺
等方面的要求,以确保产品能够在制造过程中得到良好的加工效果。
6.环境友好
在塑料产品设计过程中,设计师还应当考虑到产品的环境友好性。
选
择可回收材料、减少废弃物的产生、考虑产品的二次利用等方面的因素,
以减少对环境的负面影响。
7.人机工程学
8.安全性
总之,塑料产品设计需要综合考虑到材料选择、结构设计、功能实现、视觉效果、制造可行性、环境友好、人机工程学和安全性等方面的要求。
只有在综合考虑这些因素的基础上,设计师才能设计出具有良好品质和用
户体验的塑料产品。
塑胶件设计准则(一)
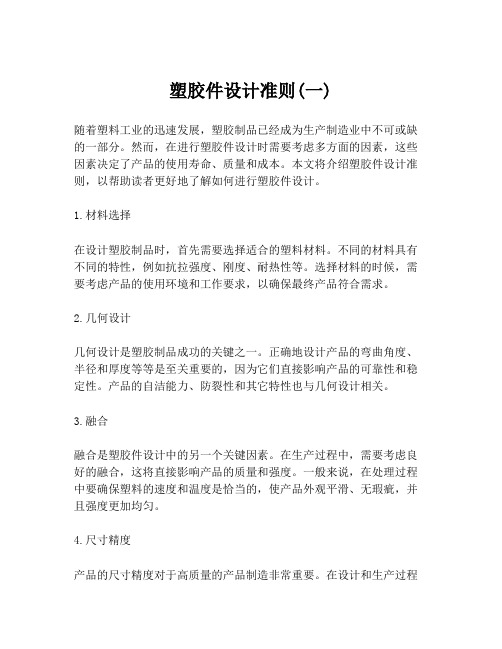
塑胶件设计准则(一)随着塑料工业的迅速发展,塑胶制品已经成为生产制造业中不可或缺的一部分。
然而,在进行塑胶件设计时需要考虑多方面的因素,这些因素决定了产品的使用寿命、质量和成本。
本文将介绍塑胶件设计准则,以帮助读者更好地了解如何进行塑胶件设计。
1.材料选择在设计塑胶制品时,首先需要选择适合的塑料材料。
不同的材料具有不同的特性,例如抗拉强度、刚度、耐热性等。
选择材料的时候,需要考虑产品的使用环境和工作要求,以确保最终产品符合需求。
2.几何设计几何设计是塑胶制品成功的关键之一。
正确地设计产品的弯曲角度、半径和厚度等等是至关重要的,因为它们直接影响产品的可靠性和稳定性。
产品的自洁能力、防裂性和其它特性也与几何设计相关。
3.融合融合是塑胶件设计中的另一个关键因素。
在生产过程中,需要考虑良好的融合,这将直接影响产品的质量和强度。
一般来说,在处理过程中要确保塑料的速度和温度是恰当的,使产品外观平滑、无瑕疵,并且强度更加均匀。
4.尺寸精度产品的尺寸精度对于高质量的产品制造非常重要。
在设计和生产过程中,必须严格控制尺寸精度。
如果精度过低,往往会影响产品的可靠性和性能。
5.模具设计加工模具的质量将直接影响成品的质量。
因此,在设计模具时,需要充分考虑产品的要求,并尽可能减少缺陷的可能性。
从模具材料的选择到处理方法的选定,都必须被考虑到。
综上所述,塑胶件设计准则是非常重要的,可以确保产品质量和性能。
设计师需要仔细考虑产品使用的工作条件,选择适合的材料,并采取正确的几何设计方法。
保证良好的融合、尺寸精度和模具设计,可以使塑料制品达到最高质量标准,从而满足用户的需求。
塑胶产品结构设计

塑胶产品结构设计要点1.胶厚(胶位):塑胶产品的胶厚(整体外壳)通常在0.80-3.00左右,太厚容易缩水和产生汽泡,太薄难走满胶,大型的产品胶厚取厚一点,小的产品取薄一点,一般产品取1.0-2.0为多。
而且胶位要尽可能的均匀,在不得已的情况下,局部地方可适当的厚一点或薄一点,但需渐变不可突变,要以不缩水和能走满胶为原则,一般塑料胶厚小于0.3时就很难走胶,但软胶类和橡胶在0.2-0.3的胶厚时也能走满胶。
2.加强筋(骨位):塑胶产品大部分都有加强筋,因加强筋在不增加产品整体胶厚的情况下可以大大增加其整体强度,对大型和受力的产品尤其有用,同时还能防止产品变形。
加强筋的厚度通常取整体胶厚的0.5-0.7倍,如大于0.7倍则容易缩水。
加强筋的高度较大时则要做0.5-1的斜度(因其出模阻力大),高度较矮时可不做斜度。
3.脱模斜度:塑料产品都要做脱模斜度,但高度较浅的(如一块平板)和有特殊要求的除外(但当侧壁较大而又没出模斜度时需做行位)。
出模斜度通常为1-5度,常取2度左右,具体要根据产品大小、高度、形状而定,以能顺利脱模和不影响使用功能为原则。
产品的前模斜度通常要比后模的斜度大0.5度为宜,以便产品开模事时能留在后模。
通常枕位、插穿、碰穿等地方均需做斜度,其上下断差(即大端尺寸与小端尺寸之差)单边要大于0.1以上。
4.圆角(R角):塑胶产品除特殊要求指定要锐边的地方外,在棱边处通常都要做圆角,以便减小应力集中、利于塑胶的流动和容易脱模。
最小R通常大于0.3,因太小的R模具上很难做到。
5.孔:从利于模具加工方面的角度考虑,孔最好做成形状规则简单的圆孔,尽可能不要做成复杂的异型孔,孔径不宜太小,孔深与孔径比不宜太大,因细而长的模具型心容易断、变形。
孔与产品外边缘的距离最好要大于1.5倍孔径,孔与孔之间的距离最好要大于2倍的孔径,以便产品有必要的强度。
与模具开模方向平行的孔在模具上通常上是用型心(可镶、可延伸留)或碰穿、插穿成型,与模具开模方向不平行的孔通常要做行位或斜顶,在不影响产品使用和装配的前提下,产品侧壁的孔在可能的情况下也应尽量做成能用碰穿、插穿成型的孔。
塑胶产品结构设计要点

塑胶产品结构设计要点塑胶产品的结构设计是指根据产品功能和使用要求,通过合理的结构布局和构造设计,使产品能够满足使用功能和质量要求,以及具备良好的外观和实用性。
在进行塑胶产品结构设计时,应注意以下要点:1.确定产品功能和使用要求:了解产品的使用功能和要求,包括产品的使用环境、使用寿命、承载能力、阻燃性能、耐磨性等方面的要求。
根据这些要求来确定产品的结构设计目标。
2.材料选择:根据产品的使用要求,选择适合的塑胶材料。
根据材料的物理性质、化学性能、加工性能以及市场价格等因素进行综合考虑,选择最合适的材料。
3.结构布局:根据产品的功能要求和外观要求,设计出合理的结构布局。
合理的结构布局可以提高产品的使用效果和降低生产成本。
在进行结构布局时,要考虑产品的各个功能部件的位置、载荷传递路径、连接方式等因素。
4.强度设计:对于承载载荷的部件,需要进行强度设计。
通过选用合适的截面形状、增加加强筋和加大材料厚度等手段,确保产品在使用过程中不会发生断裂、变形和塑胶疲劳等现象。
5.组装和拆卸设计:对于复杂的塑胶产品,需要考虑组装和拆卸的方便性。
通过设计合理的连接方式、采用模块化结构等手段,简化组装和拆卸过程,提高产品的维修和更换部件的便利性。
6.注塑成型设计:在进行塑胶产品结构设计时,需要考虑塑胶材料的注塑成型工艺。
通过优化产品的结构设计,减少成型缺陷和变形,提高产品的成型质量。
7.外观设计:塑胶产品通常需要具备良好的外观。
在进行结构设计时,应注意产品的外观效果,设计合理的形状和曲线,避免尖锐边缘和毛刺等缺陷。
8.安全设计:塑胶产品在使用过程中,需要考虑安全性。
对于与人体直接接触的部件,应采用无毒、无害的材料,并设计合理的圆角和平滑表面,避免刺伤和损伤。
9.可维修性设计:对于长期使用的塑胶产品,需要考虑其可维修性。
合理的结构设计可以方便产品的维护和更换损坏部件,延长产品的使用寿命。
总之,塑胶产品的结构设计是一个复杂而综合的过程,需要综合考虑产品的功能要求、材料性能、工艺要求、外观要求和安全要求等因素。
塑胶件的设计要点
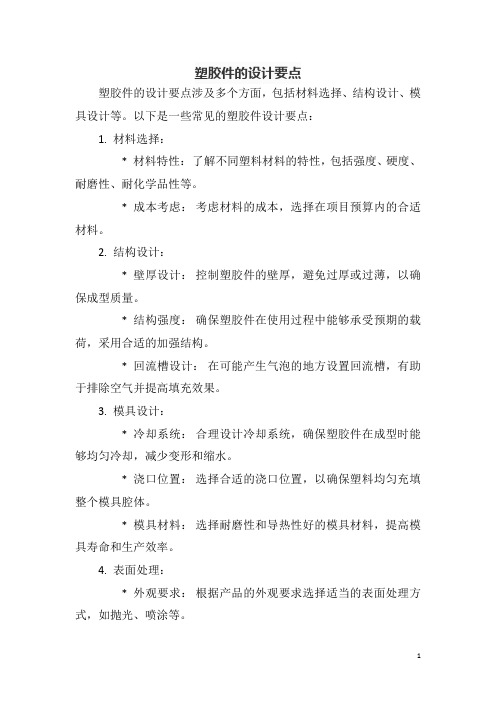
塑胶件的设计要点塑胶件的设计要点涉及多个方面,包括材料选择、结构设计、模具设计等。
以下是一些常见的塑胶件设计要点:1. 材料选择:* 材料特性:了解不同塑料材料的特性,包括强度、硬度、耐磨性、耐化学品性等。
* 成本考虑:考虑材料的成本,选择在项目预算内的合适材料。
2. 结构设计:* 壁厚设计:控制塑胶件的壁厚,避免过厚或过薄,以确保成型质量。
* 结构强度:确保塑胶件在使用过程中能够承受预期的载荷,采用合适的加强结构。
* 回流槽设计:在可能产生气泡的地方设置回流槽,有助于排除空气并提高填充效果。
3. 模具设计:* 冷却系统:合理设计冷却系统,确保塑胶件在成型时能够均匀冷却,减少变形和缩水。
* 浇口位置:选择合适的浇口位置,以确保塑料均匀充填整个模具腔体。
* 模具材料:选择耐磨性和导热性好的模具材料,提高模具寿命和生产效率。
4. 表面处理:* 外观要求:根据产品的外观要求选择适当的表面处理方式,如抛光、喷涂等。
* 纹理设计:如果需要特定的表面纹理,要在模具设计中考虑进去。
5. 可回收性:* 材料选择:尽量选择可回收的塑料材料,有助于减少环境影响。
6. 装配考虑:* 装配设计:如果塑胶件需要与其他零部件进行装配,确保设计中考虑到装配的便捷性。
7. 模拟和测试:* 流动性模拟:使用模流分析工具模拟塑胶熔体在模具中的流动,优化充填效果。
* 强度模拟:进行有限元分析等强度模拟,确保塑胶件在使用条件下具有足够的强度。
这些是一般塑胶件设计的要点,具体的设计要根据具体项目的要求、材料特性和生产工艺来进行调整。
最好在设计过程中进行充分的沟通和合作,确保设计能够满足产品的功能、外观和生产要求。
塑胶产品设计方法及注意事项

第六章塑料件设计工艺塑胶件设计一般步骤塑料件是在工业造型的基础上进行的结构设计,首先看有无相似的产品借鉴,再对产品及零件进行详尽的功能分解,确定零件的折分、壁厚、脱模斜度、零件间的过渡处理、连接处理、零件的强度处理等主要工艺问题。
1)相似借鉴在设计前,首先应查找公司和同行类似的产品,原有的产品发生过那些问题,有那些不足,参考现有的成熟结构,避免有问题的结构形式。
2)确定零件折分、零件间的过渡、连接、间隙处理从造型图和效果图理解造型风格,配合产品的功能分解,确定零件折分的数目(不同的表面状态要么分为不同的零件,要么在不同的表面之间须有过度处理),确定零件表面间的过度处理,决定零件之间的连接方式,零件之间的配合间隙。
3)零件强度与连接强度的确定根据产品大小,确定零件主体壁厚。
零件本身的强度,由壁厚塑料件、结构形式(平板形状的的塑料件强度最差)、加强筋与加强骨共同决定。
在决定零件的单个强度的同时,须确定零件之间的连接强度,改变连接强度的方法有,加螺钉柱,加止口,加扣位,加上下顶住的加强骨。
4)脱模斜度的确定脱模斜度要根据材料(PP,PE硅胶,橡胶能强行脱模)、表面状态(饰纹的斜度要比光面的大,蚀纹面的斜度尽可能比样板要求的大0.5度,保证蚀纹表面不被损伤,提高产品的良品率)、透明与否决定零件应有的脱模斜度(透明的斜度要大)等因素综合确定。
公司不同的产品系列推荐的材料种类。
表6-1 不同塑料零件的推荐材料塑胶件的表面处理表6-2 塑料表面处理的选择塑胶件的工艺技术要求.塑胶件零件的壁厚选择塑胶件,对壁厚均匀性有要求,壁厚不均匀工件将有缩水痕迹,要求加强筋与主体壁厚的比值最好为0.4以下,最大比值不超过0.6.塑胶零件的脱模斜度在立体图的构建中,凡影响外观,影响装配的地方需要画出斜度,加强筋一般不画斜度。
塑胶零件的脱模斜度由材料,表面饰纹状态,零件透明与否决定。
硬质塑料比软质塑料的脱模斜度大,零件越高,孔越深,斜度越小。
塑胶产品结构设计要点

塑胶产品结构设计要点1.产品功能要求:首先要明确产品的功能要求,确定产品的用途和目标市场,以便能够合理的确定产品的结构。
产品功能要求包括产品的使用寿命、耐磨性、承载能力、耐高温、防水等。
2.材料选择:塑胶产品的材料选择是非常重要的。
在选择材料时要考虑到产品的用途、强度要求、耐用性、环保性等因素。
常见的塑胶材料有聚乙烯、聚氯乙烯、聚丙烯、聚苯乙烯等。
在选择材料时要注意材料的可塑性、流动性、热稳定性等。
3.结构设计:塑胶产品的结构设计是塑胶产品设计中的重要环节。
结构设计包括形状设计、尺寸设计、壁厚设计等。
形状设计要符合人体工程学原理,使产品使用起来更加方便舒适。
尺寸设计要考虑到产品的装配性能和使用性能。
壁厚设计要兼顾产品的强度和成本。
4.模具设计:塑胶产品需要通过模具加工成型,所以模具设计也是塑胶产品结构设计的一部分。
模具设计要根据产品的结构特点和装配要求,确定模具的型腔结构和尺寸。
同时要考虑到模具的制造工艺和经济效益。
5.工艺选择:塑胶产品的工艺选择与产品的结构密切相关。
工艺选择包括注塑成型、吹塑成型、挤出成型等。
在选择工艺时要考虑到产品的结构形状、尺寸要求、生产效率、成本等因素。
6.结构强度和稳定性:塑胶产品在使用过程中要能够承受一定的载荷和挤压力,并保持稳定性。
在结构设计中要考虑到产品受力情况,合理设计产品的强度和稳定性结构,以保证产品的使用寿命和安全性。
7.防水设计:塑胶产品往往需要具备防水功能,尤其是在户外环境中使用的产品。
在结构设计中要考虑到产品的密封性和防水性,采取相应的设计措施,如增加密封条、防水胶等。
8.美观性设计:塑胶产品的美观性设计是非常重要的,直接影响到产品的销售和市场竞争力。
在结构设计中要考虑到产品的外观造型、颜色选择等,使产品具备良好的外观质感和市场竞争力。
9.成本控制:塑胶产品的结构设计还需要考虑到成本控制。
在设计中要尽量减少材料的使用量、降低模具和加工成本,从而提高产品的经济效益。
塑胶产品结构设计规范
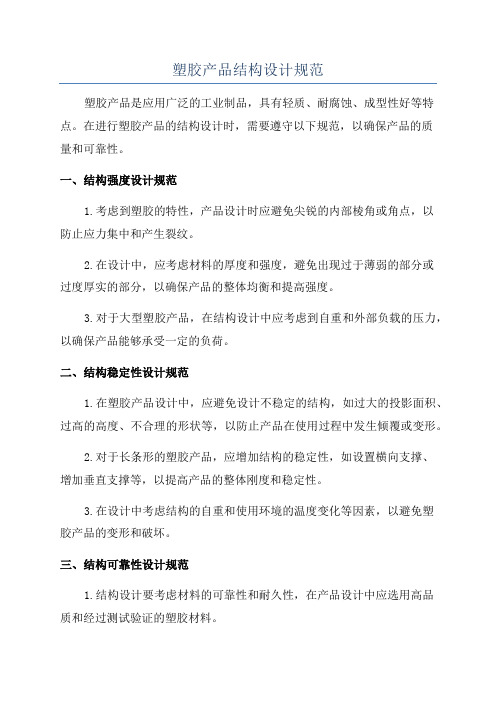
塑胶产品结构设计规范塑胶产品是应用广泛的工业制品,具有轻质、耐腐蚀、成型性好等特点。
在进行塑胶产品的结构设计时,需要遵守以下规范,以确保产品的质量和可靠性。
一、结构强度设计规范1.考虑到塑胶的特性,产品设计时应避免尖锐的内部棱角或角点,以防止应力集中和产生裂纹。
2.在设计中,应考虑材料的厚度和强度,避免出现过于薄弱的部分或过度厚实的部分,以确保产品的整体均衡和提高强度。
3.对于大型塑胶产品,在结构设计中应考虑到自重和外部负载的压力,以确保产品能够承受一定的负荷。
二、结构稳定性设计规范1.在塑胶产品设计中,应避免设计不稳定的结构,如过大的投影面积、过高的高度、不合理的形状等,以防止产品在使用过程中发生倾覆或变形。
2.对于长条形的塑胶产品,应增加结构的稳定性,如设置横向支撑、增加垂直支撑等,以提高产品的整体刚度和稳定性。
3.在设计中考虑结构的自重和使用环境的温度变化等因素,以避免塑胶产品的变形和破坏。
三、结构可靠性设计规范1.结构设计要考虑材料的可靠性和耐久性,在产品设计中应选用高品质和经过测试验证的塑胶材料。
2.考虑到使用环境的特殊性,如高温、低温、湿度等,结构设计时应选用相应的材料,以确保产品能在各种环境下正常使用。
3.在设计中应考虑到塑胶制品的组装和连接方式,确保结构的稳定和牢固。
四、结构尺寸设计规范1.结构设计时应根据产品的功能和使用要求,选择合适的尺寸和比例。
2.对于塑胶制品的配合尺寸,应预留适当的间隙,以确保组装和操作的方便性。
3.结构设计时应考虑到材料的收缩率和变形率,合理控制尺寸和形状,以确保制品的精度和几何形状的一致性。
五、智能化设计规范1.随着信息技术的发展,越来越多的塑胶产品应用于智能化领域,结构设计时应考虑到智能模块的安装和集成。
2.在设计中应考虑到电子元器件的嵌入和连接方式,以便实现产品的智能化功能。
3.考虑到智能化产品的使用便利性和系统的稳定性,结构设计中应充分考虑维修和维护的便利性,合理设置操作和维护接口。
塑胶模具制作流程和注意事项

塑胶模具制作流程和注意事项
嘿呀!今天咱们来聊聊塑胶模具制作流程和注意事项呢!
首先,咱来说说塑胶模具制作流程。
第一步,产品设计,哇!这可太重要啦!得把产品的形状、尺寸、功能啥的都想得明明白白,不然后面可就麻烦啦!
第二步,模具设计,哎呀呀!这得考虑模具的结构、分型面、浇口位置等等,要精心设计才能保证模具好用呀!
第三步,材料选择,哇塞!这可不能马虎,得根据产品需求选对材料,质量不好的材料可不行呢!
第四步,加工制造,这可是个细致活儿,什么铣削、磨削、电火花加工等等,都得认真对待呀!
第五步,装配调试,嘿!把各个部件组装起来,然后调试,看看有没有问题,这一步也不能粗心大意哟!
接下来,咱们讲讲注意事项。
第一,设计要合理,哎呀呀!不合理的设计会导致模具制造困难,甚至影响产品质量呢!
第二,加工精度要保证,哇!精度不够,模具就不好用啦!
第三,材料质量要过关,不然模具容易损坏,这可不得了呀!
第四,装配要精准,错一点都不行呢!
第五,调试要仔细,每个环节都得检查到位,可不能有疏漏哇!
第六,注意安全,加工过程中可别受伤啦!
第七,成本控制要做好,不能浪费材料和时间呀!
第八,跟客户沟通要及时,了解他们的需求变化,免得做出来不符合要求,那可就惨啦!
第九,模具的维护保养也很重要,定期检查,延长使用寿命呢!
第十,不断学习新技术,跟上时代步伐,这样才能做出更好的模具呀!
哎呀呀!总之,塑胶模具制作可不是一件简单的事儿,每个环节都得认真对待,注意这些流程和事项,才能做出高质量的塑胶模具呢!。
塑胶模具成型注意事项

塑胶模具成型注意事项塑胶模具成型是一种广泛应用于塑胶制品生产的技术,以下是一些注意事项:1. 材料选择:在进行塑胶模具成型之前,需要选择适合的塑料材料。
不同的塑料材料具有不同的特点和性能,如耐高温、抗冲击等。
因此,根据产品的要求和使用环境,选择合适的塑料材料是十分重要的。
2. 模具设计:模具的设计是塑胶模具成型的关键。
在设计过程中,需要考虑产品的形状、尺寸、壁厚等因素。
同时,还需要确保模具的可靠性和稳定性,以提高产品的质量和产量。
3. 模具加工:模具的加工过程包括数控加工、电火花加工等。
在加工过程中,需要保证模具的精度和表面质量,以确保模具的寿命和成型产品的质量。
4. 模具材料:模具材料的选择也是十分重要的。
常用的模具材料有工具钢、合金钢等。
这些材料需要具备良好的耐磨性、热导率和强度,以应对长时间高温和高压下的工作环境。
5. 模具温度控制:模具温度的控制是塑胶模具成型的关键,它直接影响着成型产品的质量和生产效率。
在成型过程中,需要控制模具的温度,使得熔融的塑料能够均匀地充填模具腔道,并在适当的时间内冷却固化。
6. 系统压力控制:系统压力的控制也是塑胶模具成型的关键之一。
过高或过低的压力都会影响产品的质量和产量。
因此,需要根据塑胶材料的特性和模具的设计要求,合理地控制系统的压力。
7. 成型条件调整:在进行塑胶模具成型时,需要根据实际情况进行成型条件的调整。
这包括温度、压力、速度等方面的调整。
通过不断试验和调整,以达到最佳的成型效果。
8. 模具维护和保养:模具的维护和保养是确保模具长时间稳定工作的重要措施。
需要定期对模具进行清洁、润滑和检查,及时修复和更换损坏的零部件,以确保模具的正常运行和延长使用寿命。
总结起来,塑胶模具成型是一项技术性较高的工作,需要在材料选择、模具设计、模具加工、模具温度控制、系统压力控制、成型条件调整以及模具的维护和保养等方面注意细节。
只有全面考虑这些因素,才能确保成型过程的顺利进行,提高产品的质量和产量。
(完整版)塑胶产品结构设计注意事项

塑胶产品结构设计注意事项目录第一章塑胶结构设计规范1、材料及厚度1.1、材料选择1.2、壳体厚度1.3、零件厚度设计实例2、脱模斜度2.1、脱模斜度要点3、加强筋3.1、加强筋与壁厚的关系3.2、加强筋设计实例4、柱和孔的问题4.1、柱子的问题4.2、孔的问题4.3、“减胶”的问题5、螺丝柱的设计6、止口的设计6.1、止口的作用6.2、壳体止口的设计需要注意的事项6.3、面壳与底壳断差的要求7、卡扣的设计7.1、卡扣设计的关键点7.2、常见卡扣设计7.3、第一章塑胶结构设计规范1、材料及厚度1.1、材料的选取a. ABS:高流动性,便宜,适用于对强度要求不太高的部件(不直接受冲击,不承受可靠性测试中结构耐久性的部件),如内部支撑架(键板支架、LCD支架)等。
还有就是普遍用在电镀的部件上(如按钮、侧键、导航键、电镀装饰件等)。
目前常用奇美PA-757、PA-777D等。
b. PC+ABS:流动性好,强度不错,价格适中。
适用于作高刚性、高冲击韧性的制件,如框架、壳体等。
常用材料代号:拜尔T85、T65。
c. PC:高强度,价格贵,流动性不好。
适用于对强度要求较高的外壳、按键、传动机架、镜片等。
常用材料代号如:帝人L1250Y、PC2405、PC2605。
d. POM具有高的刚度和硬度、极佳的耐疲劳性和耐磨性、较小的蠕变性和吸水性、较好的尺寸稳定性和化学稳定性、良好的绝缘性等。
常用于滑轮、传动齿轮、蜗轮、蜗杆、传动机构件等,常用材料代号如:M90-44。
e. PA坚韧、吸水、但当水份完全挥发后会变得脆弱。
常用于齿轮、滑轮等。
受冲击力较大的关键齿轮,需添加填充物。
材料代号如:CM3003G-30。
f. PMMA有极好的透光性,在光的加速老化240小时后仍可透过92%的太阳光,室外十年仍有89%,紫外线达78.5% 。
机械强度较高,有一定的耐寒性、耐腐蚀,绝缘性能良好,尺寸稳定,易于成型,质较脆,常用于有一定强度要求的透明结构件,如镜片、遥控窗、导光件等。
塑胶件设计注意事项
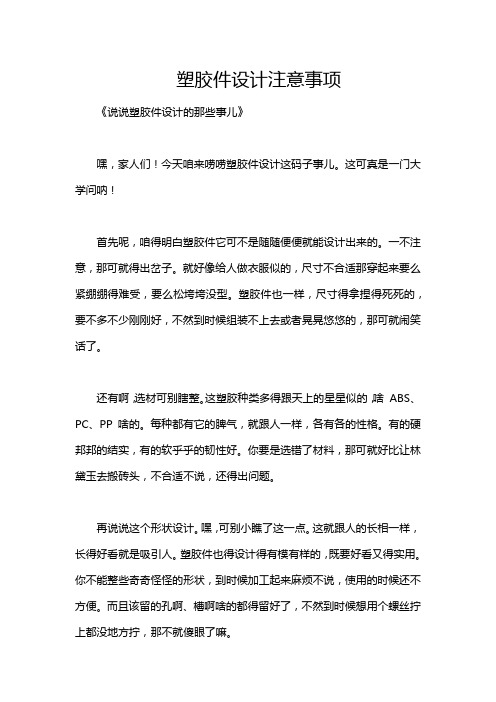
塑胶件设计注意事项《说说塑胶件设计的那些事儿》嘿,家人们!今天咱来唠唠塑胶件设计这码子事儿。
这可真是一门大学问呐!首先呢,咱得明白塑胶件它可不是随随便便就能设计出来的。
一不注意,那可就得出岔子。
就好像给人做衣服似的,尺寸不合适那穿起来要么紧绷绷得难受,要么松垮垮没型。
塑胶件也一样,尺寸得拿捏得死死的,要不多不少刚刚好,不然到时候组装不上去或者晃晃悠悠的,那可就闹笑话了。
还有啊,选材可别瞎整。
这塑胶种类多得跟天上的星星似的,啥ABS、PC、PP 啥的。
每种都有它的脾气,就跟人一样,各有各的性格。
有的硬邦邦的结实,有的软乎乎的韧性好。
你要是选错了材料,那可就好比让林黛玉去搬砖头,不合适不说,还得出问题。
再说说这个形状设计。
嘿,可别小瞧了这一点。
这就跟人的长相一样,长得好看就是吸引人。
塑胶件也得设计得有模有样的,既要好看又得实用。
你不能整些奇奇怪怪的形状,到时候加工起来麻烦不说,使用的时候还不方便。
而且该留的孔啊、槽啊啥的都得留好了,不然到时候想用个螺丝拧上都没地方拧,那不就傻眼了嘛。
另外,咱还得考虑到成本问题。
咱不能光顾着设计得高大上,结果成本高得吓人,老板不得跟咱急眼啊。
所以啊,能简化的结构就简化,能省的材料就省点,毕竟钱不是大风刮来的。
我就记得有一次啊,我设计一个塑胶件,那是信心满满,觉得自己设计得可完美了。
结果拿去加工的时候,人家师傅瞅了一眼就乐了,说我这设计根本没法加工,尺寸太小了刀具都进不去。
哎呀妈呀,当时我那个脸通红通红的,恨不得找个地缝钻进去。
从那以后啊,我每次设计之前都得好好琢磨琢磨加工的事儿,可不能再犯这种低级错误了。
总的来说呢,塑胶件设计就是要细心、耐心,还得有点创意。
要把各种因素都考虑进去,不能马虎大意。
家人们,咱可别小瞧了这小小的塑胶件,这里面的学问大着呢!只有咱把这些都整明白了,才能设计出好用又好看的塑胶件来。
让我们一起加油,在塑胶件设计的道路上越走越远,越走越好!。
塑料产品结构设计注意事项
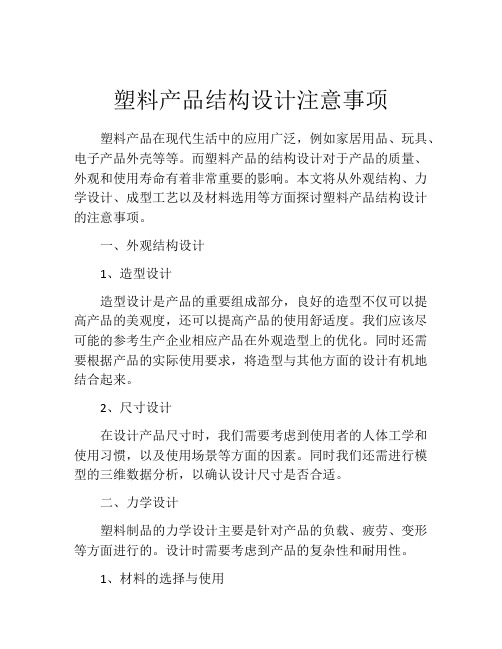
塑料产品结构设计注意事项塑料产品在现代生活中的应用广泛,例如家居用品、玩具、电子产品外壳等等。
而塑料产品的结构设计对于产品的质量、外观和使用寿命有着非常重要的影响。
本文将从外观结构、力学设计、成型工艺以及材料选用等方面探讨塑料产品结构设计的注意事项。
一、外观结构设计1、造型设计造型设计是产品的重要组成部分,良好的造型不仅可以提高产品的美观度,还可以提高产品的使用舒适度。
我们应该尽可能的参考生产企业相应产品在外观造型上的优化。
同时还需要根据产品的实际使用要求,将造型与其他方面的设计有机地结合起来。
2、尺寸设计在设计产品尺寸时,我们需要考虑到使用者的人体工学和使用习惯,以及使用场景等方面的因素。
同时我们还需进行模型的三维数据分析,以确认设计尺寸是否合适。
二、力学设计塑料制品的力学设计主要是针对产品的负载、疲劳、变形等方面进行的。
设计时需要考虑到产品的复杂性和耐用性。
1、材料的选择与使用不同的塑料材料有着不同的物理和化学性质,对于不同类型的塑料产品,我们需要根据其使用要求进行材料选择和使用,而且,我们需要综合考虑材料的成本、可回收性、抗氧化性、耐久性等因素。
2、设计承载力设计产品时我们需要考虑到产品的承载力,以保证产品在使用时不会出现断裂、变形等安全问题。
一般来说,塑料制品往往具有大型面板或外壳,因此在考虑承载力时应注意加强框架约束,以消除塑料制品的变形或脆性断裂。
3、环境适应性设计塑料制品在不同环境下都会有不同的表现,在设计时需要考虑到产品的使用场景和用途等因素。
例如,某些塑料制品的要求比较高,需要符合精度要求;而另一些型号的产品需要涉及强化和额外验收等工艺,以防水或防腐等方面进行特殊处理。
三、成型工艺1、成型材料选择在选择成型材料时需要考虑到其强度、可加工性等。
常见的塑料成型方法有吹塑、注塑、压缩成型和挤出成型等,而不同的方法可以满足不同的需求。
2、模具结构设计模具对于塑料成型过程至关重要,因此,模具的设计需要考虑到复杂性、成本、加工时间等因素。
- 1、下载文档前请自行甄别文档内容的完整性,平台不提供额外的编辑、内容补充、找答案等附加服务。
- 2、"仅部分预览"的文档,不可在线预览部分如存在完整性等问题,可反馈申请退款(可完整预览的文档不适用该条件!)。
- 3、如文档侵犯您的权益,请联系客服反馈,我们会尽快为您处理(人工客服工作时间:9:00-18:30)。
第六章塑料件设计工艺
塑胶件设计一般步骤
塑料件是在工业造型的基础上进行的结构设计,首先看有无相似的产品借鉴,再对产品及零件进行详尽的功能分解,确定零件的折分、壁厚、脱模斜度、零件间的过渡处理、连接处理、零件的强度处理等主要工艺问题。
1)相似借鉴
在设计前,首先应查找公司和同行类似的产品,原有的产品发生过那些问题,有那些不足,参考现有的成熟结构,避免有问题的结构形式。
2)确定零件折分、零件间的过渡、连接、间隙处理
从造型图和效果图理解造型风格,配合产品的功能分解,确定零件折分的数目(不同的表面状态要么分为不同的零件,要么在不同的表面之间须有过度处理),确定零件表面间的过度处理,决定零件之间的连接方式,零件之间的配合间隙。
3)零件强度与连接强度的确定
根据产品大小,确定零件主体壁厚。
零件本身的强度,由壁厚塑料件、结构形式(平板形状的的塑料件强度最差)、加强筋与加强骨共同决定。
在决定零件的单个强度的同时,须确定零件之间的连接强度,改变连接强度的方法有,加螺钉柱,加止口,加扣位,加上下顶住的加强骨。
4)脱模斜度的确定
脱模斜度要根据材料(PP , PE硅胶,橡胶能强行脱模)、表面状态(饰纹的斜度要比光面的大,蚀纹面的斜度尽可能比样板要求的大0.5度,保证蚀纹表面不被损伤,
提高产品的良品率)、透明与否决定零件应有的脱模斜度(透明的斜度要大)等因素综合确定。
公司不同的产品系列推荐的材料种类。
塑胶件的表面处理
塑胶件的工艺技术要求
塑胶件零件的壁厚选择
塑胶件,对壁厚均匀性有要求,壁厚不均匀工件将有缩水痕迹,要求加强筋与主体壁厚的
比值最好为0.4以下,最大比值不超过06
塑胶零件的脱模斜度
在立体图的构建中,凡影响外观,影响装配的地方需要画出斜度,加强筋一般不画斜度。
塑胶零件的脱模斜度由材料,表面饰纹状态,零件透明与否决定。
硬质塑料比软质塑料的脱模斜度大,零件越高,孔越深,斜度越小。
塑胶零件的尺寸精度
塑胶零件一般精度不高,
在实际使用中,我们主要检验装配尺寸,在平面图上主要标注总体尺寸,装配尺寸,及其它需要控制的尺寸。
我们在实际中主要考虑尺寸的一致性,如上下盖的边需对齐,
塑胶的表面粗糙度
1)蚀纹表面不能标注的粗糙度。
在塑胶表面光洁度特别高的地方,将此范围圈出标注表面状态为镜面。
2 )塑胶零件的表面一般平滑,光亮,表面粗糙度一般为Ra2.5〜0.2um..
3 )塑胶的表面粗糙度,主要取决于模具型腔表面的粗糙度,模具表面的粗糙度要
求比塑胶零件的表面粗糙度高一到二级。
用超声波、电解抛光模具表面能达到
Ra0.05 。
圆角
注塑圆角值由相邻的壁厚决定,一般取壁厚的0.5〜1.5倍,但不小于0.5mm
分型面的位置要郑重选择圆角,在分型面有圆角,圆角部分需出在模具另外一
边,制作有一定难度,在圆角处有细微的痕迹线。
但需要防割手时需要圆角。
加强筋的问题
注塑工艺与铸造工艺类似,壁厚的不均匀性将产生缩水缺陷,一般筋的壁厚为
主体厚的0.4倍,最大不超过0.6倍。
筋之间的间距大于 4t ,筋的高度低于3t ,如 图6-1 o 在提高零件强度的方法中,一般加筋,不增加壁厚,如图 6-1所示。
螺钉柱子的筋取至少低于柱子端面
1.0mm ,筋至少需要低于零件表面,或分型
面 1.0mm o
多条筋相交,要注意相交带来的壁厚不均匀性问题。
支承面
塑胶易变形,在定位上应当归为毛胚的定位一类,
在定位面积上要小,如平面的支承,应
当改为小凸点,凸环。
斜顶与行位问题
斜顶与行位,在分模方向,垂直于分模方向均有运动。
斜顶与行位在垂直于分模的方向不
能有胶位阻挡运动,要有足够的运动空间,如下图
6-2
I :
>4t
<0.6t
图6-1塑料件加强筋设计
图6-2斜顶与行位问题
塑胶的极限工艺问题的处理方法
1)壁厚的特殊处理方法
特别大的工件,如玩具汽车外壳,采用多点进胶的方法,能将壁厚取的相对薄些。
柱子的局部胶位
厚,用如下图6-3的方法处理。
加长芯子内壁减胶外壁减胶
图6-3 壁厚的特殊处理
2)小斜度与垂直面的处理。
模具表面尺寸精度高,表面光洁度高,脱模阻力小,脱模斜度能取小。
为达到此目的将工件小斜度的地方单独镶,镶件用线割,用磨的方法加工,如图6-4。
般将接线放在圆角与大面的交接处,如图6-5。
图6-5 小斜度与垂直面的处理
塑胶零件常须解决的问题
1 )过渡处理问题:
塑胶零件的精度一般不高,在相邻零件之间,同一零件的不同表面之间须有过渡处理。
同一零件的不同表面之间一般用小槽过渡,不同零件之间可用小槽,高低错面处理,如图6-6所示。
图6-6 表面过度处理
2 )塑胶零件的间隙取值:
零件间直接装配,相互间无运动一般取0.1mm ;
止口一般取0.15mm ;
零件间不需接触的最小间隙为0.3mm,—般取0.5mm
3 )塑胶零件止口的常见形式及间隙取法如图6-7所示。
图6-7塑胶零件止口的常见形式及间隙取法
自攻螺钉对应的塑料件孔径
塑胶件正在进入的领域
1. 用塑胶机箱盖替代钣金机箱盖;
2. 用双色注塑的标牌代替电铸标牌;
3. 公司正在用防静电的塑胶小面板代替金属防静电小面板;
4. 公司正在用塑胶屏蔽面板代替金属屏蔽小面板;。