高锰钢斗齿断裂原因分析
浅谈高锰钢铸件裂纹缺陷分析与控制

浅谈高锰钢铸件裂纹缺陷分析与控制作者:张凯李静生高菲来源:《中国科技博览》2013年第34期[摘要]由于高锰钢具有生产工艺简单、力学性能优良、生产成本低廉的特点,在制造承受冲击磨损的零部件中应用较为广泛。
在科学技术的带动下,高锰钢铸件质量也不断提升,但是高锰钢铸件裂纹缺陷尚未得到有效解决。
本文针对高锰钢铸件裂纹缺陷原因进行了探析,并提出高锰钢裂纹缺陷控制措施,以期促进高锰钢铸件质量的进一步提高。
[关键词]高锰钢铸件裂纹缺陷控制措施中图分类号:X593 文献标识码:X 文章编号:1009―914X(2013)34―0262―010、引言高锰钢(high manganese steel)是指含锰量在10%以上的合金钢,是一种典型抗冲击磨损的耐磨钢,自19世纪80年代制成以来,高锰钢技术不断发展,高锰钢的任性和耐磨性表现更为突出。
由于高锰钢具有生产工艺简单、力学性能优良、生产成本低廉的特点,在制造承受冲击磨损的零部件中应用较为广泛。
虽然在科学技术的带动下,高锰钢铸件质量也不断提升,但是高锰钢比较容易产生裂纹特性仍未得到有效改善[1]。
本文针对高锰钢铸件裂纹缺陷原因进行了探析,并提出高锰钢裂纹缺陷控制措施,以期促进高锰钢铸件质量的进一步提高。
1、高锰钢成分和性能化学成分是高锰钢组织和性能的基本要素,随着对高锰钢研究工作的不断深入,高锰钢的化学成分也逐渐清晰和明确。
作为耐磨材料的高锰钢化学成分主要分为:0.95%-1.55%的C,11%至15%的Mn,0.4%至1.0%的Si,小于0.05的S和小于0.1的P。
碳(C)是高锰钢性能的主要影响因素,在高锰钢中,C能促进单相奥氏体组织的形成,保证钢具有较高的力学性能,提高耐磨性的作用。
锰(Mn)是稳定奥氏体的主要原色,在高锰钢中,锰能够使钢的组织逐渐有珠光体型变为马氏体型并进一步转变为奥氏体型,使钢机体得到强化。
锰碳比(Mn/C)能够使高锰钢冷却时间产生珠光体转变得以避免,并使奥氏体锰钢韧性得到保证。
高锰钢铸件裂纹产生的原因及预防措施

收稿日期 :Байду номын сангаас2005 10 28; 作者简介 : 张军强 ( 1969 修订日期 : 2006 02 07 ) , 陕西渭南人 , 工程师 . 从事生产管理工作 .
因裂纹造成非正常失效, 导致产品寿命降低。因此研 究高锰钢铸件裂纹产生的原因, 从而采取有效的预防 措施, 便成为铸造工作者的重要课题。本文根据生产 实践经验 , 试图阐明高锰钢铸件产生裂纹的机理, 从而 找到有效的预防措施 , 以求推动该课题的发展。 1 高锰钢铸件裂纹产生的原因分析 1. 1 在铸造生产过程中高锰钢铸件裂纹产生的原因 分析 高锰钢铸件产生裂纹的内在 原因主要有 3 个方 面: 高锰钢线收缩值高达 2. 4% ~ 3. 0% 是碳钢线收 缩值的 2 倍, 因此当高锰钢铸件在凝固收缩过程中收
! 310 !
铸造技术 F OU N DRY T ECH NO LO GY
V ol. 27 N o. 4 A pr. 2006
高锰钢铸件裂纹产生的原因及预防措施
张军强 , 张文斌 , 王红旗
农科股份有限公司, 陕西 渭南 714100)
摘要 : 根据高锰钢生产的实践经验 , 提出了高锰钢铸 件在铸造生产过程中裂纹产生的 机理及受大 冲击载荷 高锰钢铸件 在使用 过程中裂纹产生发展的机理 。 认为铸件在使用过程中 的非正 常失效 的原因 主要是 由于铸件 内部存 在着显 微裂纹 、 碳化 物孔 洞、 晶界上的磷共晶 、 非金属夹杂物 、 缩孔 、 缩松等缺陷造成 。 从铸件的 结构设计 、 化学成分的选取 、 冶炼 、 浇注 、 造型 、 清理及热 处理各个环节中根据高锰钢的特点 , 制订出合理的工 艺并严 格执行 而获得优 质的铸 件 。 通过 采取细化 晶粒 、 强化 脱氧 、 脱磷 来预防铸件产生裂纹 。 生产实践证明 : 以上措施是消除或减小高锰钢铸件裂纹的有效手段 。 关键词 : 高锰钢 ; 裂纹 ; 预防措施
高锰钢铸件裂纹的产生机理探讨

针 对 生产 制 造 高锰 钢铸 件 的各 个 主要 环 节 ,
2 9
作者简介 : 薛福连( 98一 , 1 4 ) 高级 丁程师 , 沈阳辽 中人 , 大学 本科
po es h rv ninmes rsh v e n st ot ntefe f t cued sg rc s.T epe e t aue a eb e e r i ld o r tr e in,c e c lc mp st nc nrln o f h h i su h mia o o io o t ig i o
程中各部位的温差较大 , 造成相当大的热应力 , 这 也是产生热裂 的另一个重要原 因。如果再考虑收 缩应力累加 , 对铸件的危害就更大了。 2 铸件凝固过程 中各种因素对形成裂纹的影响 高锰钢铸件在结 晶时 , 容易形成粗 晶及柱状 晶, 在铸态晶界上存在的脆性碳化物使铸件变脆. 降低了高锰钢铸件强度, 这是铸 件形成 裂纹 的内 部条件。铸件在凝 固壳形 成时, 热节部 位应力集 中出现第 一次 开裂 , 随着凝 固壳 的 变厚 、 纹 向里 裂 扩展 。 有时裂 口被钢液充满 , 如不能被钢液充 假
Xue Fula in
Ab ta tT i at l a e cie h es no eca k rd c do ehg n a e ese l at g u n sr c :hs rceh sd s r dterao ft rc spo u e nt ih ma g n s te s i sd r g i b h h c n i
满, 在凝 固后便形成裂纹 , 也可能在被钢液充满后 第二次开裂而形成裂纹 。裂纹通常产生于铸件壁 厚 不均 匀处 、 接两 壁 的过 渡 圆角 处 及 局 部凝 固 连
高锰钢铸件裂纹缺陷分析及控制
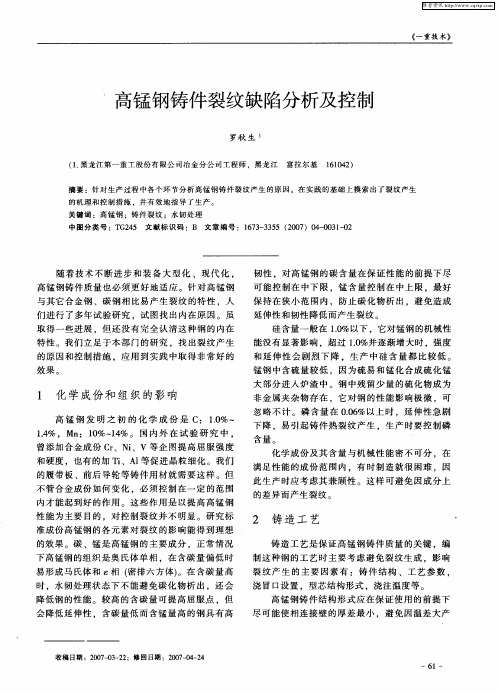
《 重技 术 》 一
高锰钢铸件裂纹缺 陷分析及 控制
罗 秋 生
( . 龙 江 第 一 重 工 股 份 有 限公 司冶 金 分 公 司 工 程 师 ,黑龙 江 1黑
富拉 尔 基 1 14 ) 6 0 2
摘 要 :针 对 生产 过 程 中各 个 环 节 分 析 高锰 钢 铸 件 裂 纹 产 生 的 原 因 。 在 实 践 的基 础 上 摸 索 出 了裂 纹 产 生 的机 理 和 控制 措 施 ,并 有 效 地 指 导 了 生产 。 关 键 词 :高锰 钢 ;铸 件 裂 纹 ;水 韧处 理 中图 分 类 号 :T 2 5 文 献 标 识 码 :B 文 章 编 号 :17 — 3 5 (0 7 4 — 0 10 G 4 6 3 3 5 2 0 )0 0 3 — 2
降低钢 的性能 。较 高 的含 碳 量可 提 高屈 服 点 ,但 会 降低 延 伸性 .含 碳 量低 而 含锰 量 高 的钢 具有 高
收 稿 日期 :20 — 3 2 :修 回 日期 :20 — 4 2 070 —2 07 0—4
一
6 1—
维普资讯
效果 。
韧性 ,对 高锰 钢 的碳 含 量 在保 证 性能 的前提 下尽
可能 控制 在 中下 限 。锰 含量 控 制 在 中上 限 。最好
保 持 在狭 小 范 围 内 ,防止碳 化 物 析 出 ,避 免 造成
延 伸性 和 韧性 降低 而产生 裂纹 。
硅 含量 一般 在 1 %以下 ,它 对锰钢 的机 械性 . O
制 这 种钢 的工 艺 时 主要 考 虑避 免裂 纹 生成 .影 响
准成 份高 锰钢 的各 元 素对 裂 纹 的影 响 能得 到理 想 的效 果 。碳 、锰是 高锰钢 的主 要成 分 ,正 常情 况 下高锰 钢 的组 织是 奥 氏体 单 相 。在 含碳 量 偏低 时 易形成 马 氏体 和 8相 ( 密排 六方 体) 。在 含碳 量 高
浅谈钢材韧性及断裂的原因分析
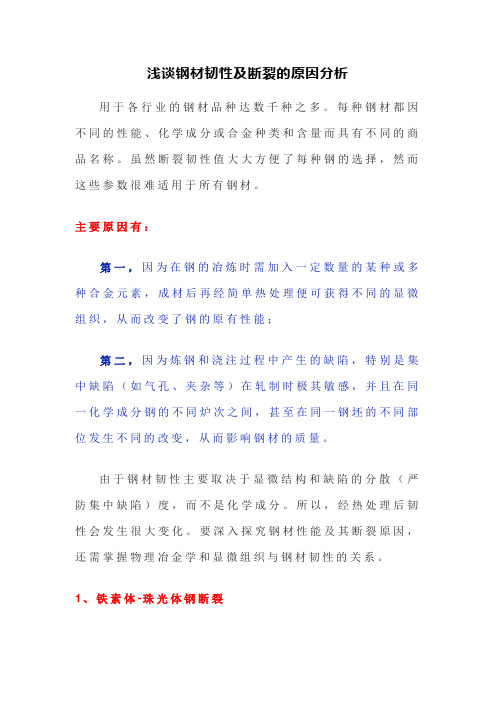
浅谈钢材韧性及断裂的原因分析用于各行业的钢材品种达数千种之多。
每种钢材都因不同的性能、化学成分或合金种类和含量而具有不同的商品名称。
虽然断裂韧性值大大方便了每种钢的选择,然而这些参数很难适用于所有钢材。
主要原因有:第一,因为在钢的冶炼时需加入一定数量的某种或多种合金元素,成材后再经简单热处理便可获得不同的显微组织,从而改变了钢的原有性能;第二,因为炼钢和浇注过程中产生的缺陷,特别是集中缺陷(如气孔、夹杂等)在轧制时极其敏感,并且在同一化学成分钢的不同炉次之间,甚至在同一钢坯的不同部位发生不同的改变,从而影响钢材的质量。
由于钢材韧性主要取决于显微结构和缺陷的分散(严防集中缺陷)度,而不是化学成分。
所以,经热处理后韧性会发生很大变化。
要深入探究钢材性能及其断裂原因,还需掌握物理冶金学和显微组织与钢材韧性的关系。
1、铁素体-珠光体钢断裂铁素体-珠光体钢占钢总产量的绝大多数。
它们通常是含碳量在0.05%~0.20%之间的铁-碳和为提高屈服强度及韧性而加入的其它少量合金元素的合金。
铁素体-珠光体的显微组织由BBC铁(铁素体)、0.01%C、可溶合金和Fe3C组成。
在碳含量很低的碳钢中,渗碳体颗粒(碳化物)停留在铁素体晶粒边界和晶粒之中。
但当碳含量高于0.02%时,绝大多数的Fe3C形成具有某些铁素体的片状结构,而称为珠光体,同时趋向于作为“晶粒”和球结(晶界析出物)分散在铁素体基体中。
含碳量在0.10%~0.20%的低碳钢显微组织中,珠光体含量占10%~25%。
尽管珠光体颗粒很坚硬,但却能非常广泛地分散在铁素体基体上,并且围绕铁素体轻松地变形。
通常,铁素体的晶粒尺寸会随着珠光体含量的增加而减小。
因为珠光体球结的形成和转化会妨碍铁素体晶粒长大。
因此,珠光体会通过升高d-1/2(d为晶粒平均直径)而间接升高拉伸屈服应力δy。
从断裂分析的观点看,在低碳钢中有两种含碳量范围的钢,其性能令人关注。
一是含碳量在0.03%以下,碳以珠光体球结的形式存在,对钢的韧性影响较小;二是含碳量较高时,以球光体形式直接影响韧性和夏比曲线。
大型矿山挖掘机斗齿磨损失效分析与抗磨措施
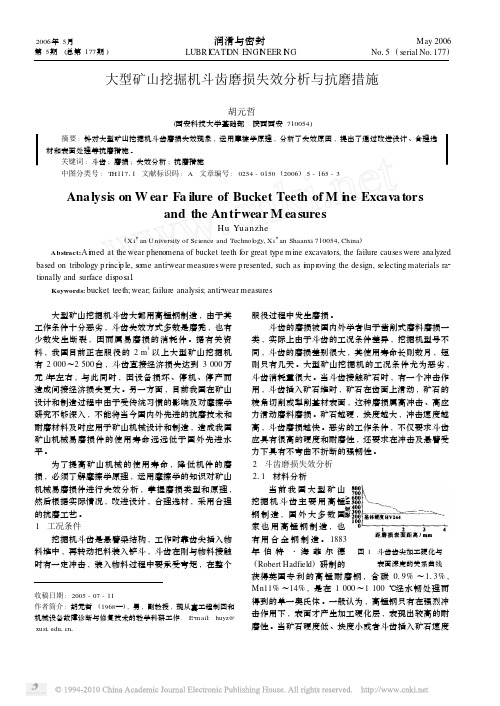
收稿日期:2005-07-11作者简介:胡元哲(1968—),男,副教授,现从事工程制图和机械设备故障诊断与修复技术的教学科研工作.E 2mail:huyz@xust 1edu 1cn 1大型矿山挖掘机斗齿磨损失效分析与抗磨措施胡元哲(西安科技大学基础部 陕西西安710054)摘要:针对大型矿山挖掘机斗齿磨损失效现象,运用摩擦学原理,分析了失效原因,提出了通过改进设计、合理选材和表面处理等抗磨措施。
关键词:斗齿;磨损;失效分析;抗磨措施中图分类号:T H11711 文献标识码:A 文章编号:0254-0150(2006)5-165-3Ana lysis on W ear Fa ilure of Bucket Teeth of M i n e Excava tors and the Anti 2wear M ea suresHu Yua nzhe(Xi ’an University of Science and Technol ogy,Xi ’an Shaanxi 710054,China )Abstract:A i m ed at the wear phenomena of bucket teeth for great type m ine excavat ors,the failure causes were analyzedbased on tribology p rincip le,s ome anti 2wear measures were p resented,such as i m p r oving the design,selecting materials ra 2tionally and surface dis posal .Keywords:bucket teeth;wear;failure analysis;anti 2wear measures 大型矿山挖掘机斗齿大都用高锰钢制造,由于其工作条件十分恶劣,斗齿失效方式多数是磨秃,也有少数发生断裂,因而属易磨损的消耗件。
高锰钢铸件裂纹的分析与预防
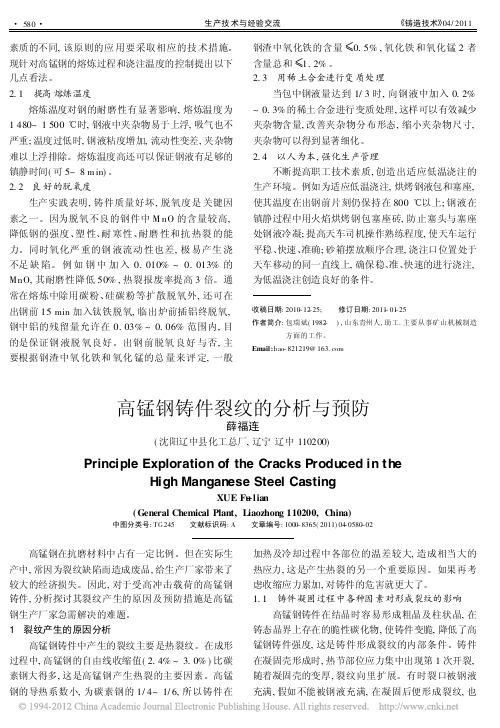
生产技术与经验交流5铸造技术604/2011素质的不同,该原则的应用要采取相应的技术措施。
现针对高锰钢的熔炼过程和浇注温度的控制提出以下几点看法。
2.1 提高熔炼温度熔炼温度对钢的耐磨性有显著影响,熔炼温度为1480~1500e 时,钢液中夹杂物易于上浮,吸气也不严重;温度过低时,钢液粘度增加,流动性变差,夹杂物难以上浮排除。
熔炼温度高还可以保证钢液有足够的镇静时间(可5~8m in)。
2.2 良好的脱氧度生产实践表明,铸件质量好坏,脱氧度是关键因素之一。
因为脱氧不良的钢件中M nO 的含量较高,降低钢的强度、塑性、耐寒性、耐磨性和抗热裂的能力。
同时氧化严重的钢液流动性也差,极易产生浇不足缺陷。
例如钢中加入0.010%~0.013%的MnO,其耐磨性降低50%,热裂报废率提高3倍。
通常在熔炼中除用碳粉、硅碳粉等扩散脱氧外,还可在出钢前15min 加入钛铁脱氧,临出炉前插铝终脱氧,钢中铝的残留量允许在0.03%~0.06%范围内,目的是保证钢液脱氧良好。
出钢前脱氧良好与否,主要根据钢渣中氧化铁和氧化锰的总量来评定,一般钢渣中氧化铁的含量[0.5%,氧化铁和氧化锰2者含量总和[1.2%。
2.3 用稀土合金进行变质处理当包中钢液量达到1/3时,向钢液中加入0.2%~0.3%的稀土合金进行变质处理,这样可以有效减少夹杂物含量,改善夹杂物分布形态,缩小夹杂物尺寸,夹杂物可以得到显著细化。
2.4 以人为本,强化生产管理不断提高职工技术素质,创造出适应低温浇注的生产环境。
例如为适应低温浇注,烘烤钢液包和塞座,使其温度在出钢前片刻仍保持在800e 以上;钢液在镇静过程中用火焰烘烤钢包塞座砖,防止塞头与塞座处钢液冷凝;提高天车司机操作熟练程度,使天车运行平稳、快速、准确;砂箱摆放顺序合理,浇注口位置处于天车移动的同一直线上,确保稳、准、快速的进行浇注,为低温浇注创造良好的条件。
收稿日期:2010-12-25; 修订日期:2011-01-25作者简介:包瑞斌(1982- ),山东青州人,助工.主要从事矿山机械制造方面的工作。
针对生产过程中各个环节分析高锰钢铸件裂纹产生的原因
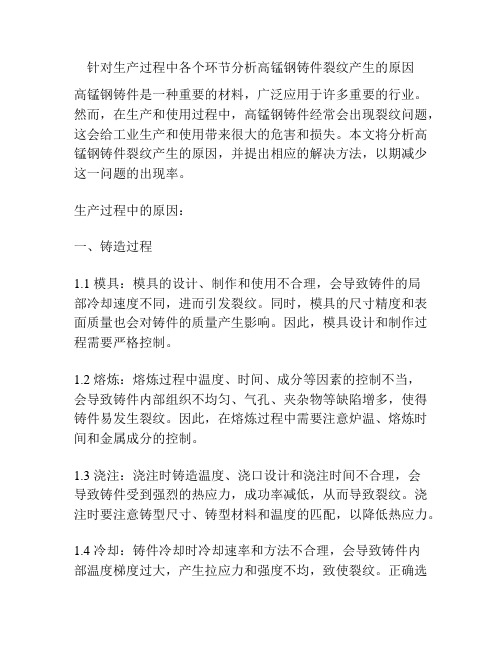
针对生产过程中各个环节分析高锰钢铸件裂纹产生的原因高锰钢铸件是一种重要的材料,广泛应用于许多重要的行业。
然而,在生产和使用过程中,高锰钢铸件经常会出现裂纹问题,这会给工业生产和使用带来很大的危害和损失。
本文将分析高锰钢铸件裂纹产生的原因,并提出相应的解决方法,以期减少这一问题的出现率。
生产过程中的原因:一、铸造过程1.1 模具:模具的设计、制作和使用不合理,会导致铸件的局部冷却速度不同,进而引发裂纹。
同时,模具的尺寸精度和表面质量也会对铸件的质量产生影响。
因此,模具设计和制作过程需要严格控制。
1.2 熔炼:熔炼过程中温度、时间、成分等因素的控制不当,会导致铸件内部组织不均匀、气孔、夹杂物等缺陷增多,使得铸件易发生裂纹。
因此,在熔炼过程中需要注意炉温、熔炼时间和金属成分的控制。
1.3 浇注:浇注时铸造温度、浇口设计和浇注时间不合理,会导致铸件受到强烈的热应力,成功率减低,从而导致裂纹。
浇注时要注意铸型尺寸、铸型材料和温度的匹配,以降低热应力。
1.4 冷却:铸件冷却时冷却速率和方法不合理,会导致铸件内部温度梯度过大,产生拉应力和强度不均,致使裂纹。
正确选择冷却方法、冷却时间和冷却速率,控制温度梯度,能够有效减少铸件的热应力。
二、热处理过程高锰钢铸件在使用前通常需要进行热处理,如退火、正火、淬火等,以获得更好的性能、组织和硬度。
但热处理过程本身也可能成为产生裂纹的原因。
2.1 温度:热处理中温度过高或温度不均匀,会导致铸件内部产生应力不均,易发生裂纹。
2.2 时长:热处理时间过长或过短,也可能导致铸件内部应力过大而产生裂纹。
2.3 冷却速度和方法:热处理后的铸件需要进行冷却,若冷却过程不恰当,也会使铸件产生裂纹。
三、机械加工过程机械加工过程中裂纹通常是由过大的切削力引起的。
多余的应力作用于铸件的表面,产生一些小裂纹,其在后续加工过程中会扩大。
这是一种慢性损伤,会减少高锰钢铸件的使用寿命。
解决方法1. 完善的工艺控制:通过合理的模具、熔炼和浇注工艺及合适的冷却方式,可以减少高锰钢铸件的热应力和应力过大的问题,从而避免裂纹的产生。
钢材断裂基本原因分析大全

钢材断裂基本原因分析大全用于各行业的钢材品种达数千种之多。
每种钢材都因不同的性能、化学成分或合金种类和含量而具有不同的商品名称。
虽然断裂韧性值大大方便了每种钢的选择,然而这些参数很难适用于所有钢材。
主要原因有:第一,因为在钢的冶炼时需加入一定数量的某种或多种合金元素,成材后再经简单热处理便可获得不同的显微组织,从而改变了钢的原有性能;第二,因为炼钢和浇注过程中产生的缺陷,特别是集中缺陷(如气孔、夹杂等)在轧制时极其敏感,并且在同一化学成分钢的不同炉次之间,甚至在同一钢坯的不同部位发生不同的改变,从而影响钢材的质量。
由于钢材韧性主要取决于显微结构和缺陷的分散(严防集中缺陷)度,而不是化学成分。
所以,经热处理后韧性会发生很大变化。
要深入探究钢材性能及其断裂原因,还需掌握物理冶金学和显微组织与钢材韧性的关系。
1. 铁素体-珠光体钢断裂铁素体-珠光体钢占钢总产量的绝大多数。
它们通常是含碳量在0.05%~0.20%之间的铁-碳和为提高屈服强度及韧性而加入的其它少量合金元素的合金。
铁素体-珠光体的显微组织由BBC铁(铁素体)、0.01%C、可溶合金和Fe3C 组成。
在碳含量很低的碳钢中,渗碳体颗粒(碳化物)停留在铁素体晶粒边界和晶粒之中。
但当碳含量高于0.02%时,绝大多数的Fe3C形成具有某些铁素体的片状结构,而称为珠光体,同时趋向于作为“晶粒”和球结(晶界析出物)分散在铁素体基体中。
含碳量在0.10%~0.20%的低碳钢显微组织中,珠光体含量占10%~25%。
尽管珠光体颗粒很坚硬,但却能非常广泛地分散在铁素体基体上,并且围绕铁素体轻松地变形。
通常,铁素体的晶粒尺寸会随着珠光体含量的增加而减小。
因为珠光体球结的形成和转化会妨碍铁素体晶粒长大。
因此,珠光体会通过升高d-1/2(d为晶粒平均直径)而间接升高拉伸屈服应力δy。
从断裂分析的观点看,在低碳钢中有两种含碳量范围的钢,其性能令人关注。
一是,含碳量在0.03%以下,碳以珠光体球结的形式存在,对钢的韧性影响较小;二是,含碳量较高时,以球光体形式直接影响韧性和夏比曲线。
高锰钢铸件生产过程中常见缺陷分析及相关预防措施探讨
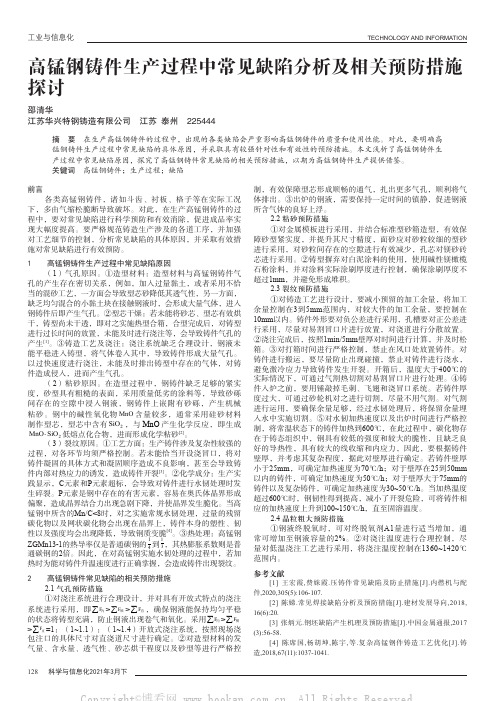
包注口的具体尺寸对直浇道尺寸进行确定。②对造型材料的发 气量、含水量、透气性、砂芯烘干程度以及砂型等进行严格控
(2)粘砂原因。在造型过程中,钢铸件缺乏足够的紧实 度,砂型具有粗糙的表面,采用质量低劣的涂料等,导致砂砾 间存在的空隙中浸入钢液,钢铸件上嵌附有砂砾,产生机械 粘砂。钢中的碱性氧化物 MnO 含量较多,通常采用硅砂材料 制作型芯,型芯中含有 SiO2 ,与 MnO 产生化学反应,即生成 MnO ⋅ SiO2 低熔点化合物,进而形成化 AND INFORMATION
高锰钢铸件生产过程中常见缺陷分析及相关预防措施 探讨
邵清华 江苏华兴特钢铸造有限公司 江苏 泰州 225444
摘 要 在生产高锰钢铸件的过程中,出现的各类缺陷会严重影响高锰钢铸件的质量和使用性能。对此,要明确高 锰钢铸件生产过程中常见缺陷的具体原因,并采取具有较强针对性和有效性的预防措施。本文浅析了高锰钢铸件生 产过程中常见缺陷原因,探究了高锰钢铸件常见缺陷的相关预防措施,以期为高锰钢铸件生产提供借鉴。 关键词 高锰钢铸件;生产过程;缺陷
前言
各类高锰钢铸件,诸如斗齿、衬板、格子等在实际工况 下,多由气缩松脆断导致破坏。对此,在生产高锰钢铸件的过 程中,要对常见缺陷进行科学预防和有效消除,促进成品率实 现大幅度提高。要严格规范铸造生产涉及的各道工序,并加强 对工艺细节的控制,分析常见缺陷的具体原因,并采取有效措 施对常见缺陷进行有效预防。
11
ZGMn13-1的热导率仅是普通碳钢的 4 到 3 ,其热膨胀系数则是普 通碳钢的2倍。因此,在对高锰钢实施水韧处理的过程中,若加 热时为能对铸件升温速度进行正确掌握,会造成铸件出现裂纹。
研究采煤机行走轮齿的断齿原因与改进措施

研究采煤机行走轮齿的断齿原因与改进措施
采煤机是煤矿生产中不可或缺的设备,其行走轮齿的断裂问题一直是采煤机运行中存在的难题。
本文通过实地研究与实验分析,总结了采煤机行走轮齿的断齿原因及改进措施。
1.工作环境:采煤机在煤矿矿井中长时间工作,容易受到尘土、潮气和水质等环境因素的影响,导致轮齿内部腐蚀,断裂概率增加。
2.材质问题:采煤机行走轮齿多采用的是高锰钢、低碳合金钢等材料,这些材料的硬度高、韧性差,可能因质量问题或淬火不当等原因导致轮齿裂纹产生,影响使用寿命。
3.过载操作:采煤机在工作过程中可能会遇到较大的阻力,从而导致行走轮齿产生超载操作,造成轮齿损伤、断裂。
4.排煤板堆积:采煤机在排放煤炭时,容易出现排煤板堆积的情况,影响行走轮齿的使用,从而造成轮齿脱落、断裂等情况。
1.升级材料:在行走轮齿的材料选择上,可改用合金钢、高硬度不锈钢等材料,提高行走轮齿的强度和韧性,减少轮齿断裂、龟裂等问题。
2.定期检查:定期对采煤机进行维护保养和检查,发现行走轮齿损坏、老化或磨损严重等情况,及时更换或修复。
3.防止超载操作:避免采煤机发生超载操作,即避免采煤机在超过其最大承受力时工作,可通过减少阻力等方式来避免超载操作,保护行走轮齿不受损害。
5.行走轮齿的加强与轮边缘平滑处理:可通过行走轮齿的加强设计和轮边缘平滑处理等措施,减少行走轮齿受到外力冲击和支撑力的损伤,进一步提高行走轮齿的寿命。
综上所述,采煤机行走轮齿的断齿原因复杂,但针对问题采取相应的改进措施可有效延长行走轮齿的使用寿命,减少采煤机的故障率,更好地维护采煤机的正常工作。
断裂的原因及使用寿命

那么如何在正常使用情况下延长刀具的使用寿命?且往下看。
刀具的磨损与刀具的几何角度,切削力,切削热及切削用量等因素有关,刀具的使用寿命是可以通过人的操作去延长的。
(1) 先选择合适的刀具材料:加工不同的材料,要知道选择什么样的刀具适合,这样才能更好的加工工件。如HRC45以下的软材料工件选择硬质合金刀具,HRC45—HRC55之间的精加工工序选择陶瓷刀具,HRC45以上的高硬度工件选择CBN刀具。
在生产制造过程中,常会出现刀具断裂或崩刃等现象,其中原因有很多,在客户实际操作中得出以下结论:
1、刀具自身的原因:如刀片底部不平,刀垫磨损严重不平整,刀片在制造中有裂纹等。
2、切削过程的原因:如在加工高铬,高镍等合金铸铁材料时,工作层有大量的高硬度碳化物,切削过程中对刀刃有划伤作用,从而产生刃口的豁口,并且在长期的切削中不断遭受冲击,导致刀片承受不了而造成断裂。
(2)改进刀具的几何角度:如前角度增大时,切屑变形小,切削轻快、切削力及切削热下降。在保证刀具有足够强度的前提下,应尽量取较大前角,主偏角缩小时,刀刃参加切削的长度增加,使切削热相对分散,且刀尖角增大,可使切削温度下降。
(3)选择合适的切削用量:切削用量包括切削速度,切削深度,进给量,调整合理的切削参数,可以延长刀具的使用寿命。
铸造高锰钢辙叉产生裂纹的原因分析
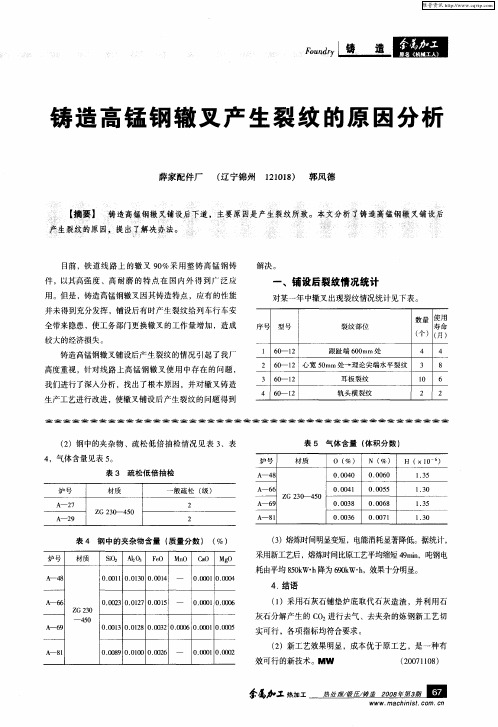
材质
s 2 A2 i 】 0
F0 Mn C0 Mg O a 0
0.0 . O 0l 0 O
耗由平均 8 k h 5 W・ 降为 6 k h 效果十分明显。 0 9 W・, 0
0. o 1 0 l 0. 1 0 0. ol 03 0 4
维普资讯
二 、理论分析
辙又是细 长形铸件 ,以型号 为 6 一1 的全加辙叉为 o 2 例, 长、宽 、高分 别 为 5 m 、40 m 7m ,壁 厚  ̄T m 4m 、19 m
2 m ,铸件从一端浇 注,轨面全部 下冷铁 ,浇注 温度为 2m 18 ~l1℃,水韧处理温度为 12 ~18℃,保温 2 。 40 50 00 00 h 理论上认 为 ,辙叉裂纹 主要是产 生弱断 面引起 ,如
A 4 一 8 A 6 一 6 ZG 2 o 一4 0 3 _ 5 A 6 一 9 0. 0 0 38 0. 0 6 0 3 0. 0 8 0 6 0. 0 0 7l 13 .5 1. 0 3
材 质
Of ) %
0. o 0 o 4 0. o o 4l
N( ) %
细化,过热还会使晶粒进一步 长大 ,因此解决该裂纹最
好的办法是降低浇注温度 。实际生产 中,将浇注温度 由
生产工艺进行改进 ,使辙叉铺设后 产生 裂纹 的问题得 到
坐 妇 逝 } 妇 坐
2 6_ 2 心宽 5 rm处 一 理 论 尖 端 水 平 裂纹 o一l 0 a 3 6一 l 0 2 耳 板 裂 纹
4 6_ 2 o一I
轨头横裂纹
2
2
妇
坐
妇
妇
【精品文档】高锰钢铸件裂纹-范文模板 (9页)

本文部分内容来自网络整理,本司不为其真实性负责,如有异议或侵权请及时联系,本司将立即删除!== 本文为word格式,下载后可方便编辑和修改! ==高锰钢铸件裂纹篇一:高锰钢铸件裂纹产生的机理和控制措施高锰钢铸件裂纹产生的机理和控制措施关键词:高锰钢;铸件裂纹;水韧处理随着技术不断进步和装备大型化、现代化,高锰钢铸件质量也必须更好地适应。
针对高锰钢与其它合金钢、碳钢相比易产生裂纹的特性,人们进行了多年试验研究,试图找出内在原因。
虽取得一些进展.但还没有完全认清这种钢的内在特性。
我们立足于本部门的研究,找出裂纹产生的原因和控制措施。
应用到实践中取得非常好的效果。
1 化学成份和组织的影响高锰钢发明之初的化学成份是C:1.0%~1.4%,Mn:10%~14%。
国内外在试验研究中曾添加合金成份 Cr、Ni、V等企图提高屈服强度和硬度,也有的加Ti、Al等促进晶粒细化。
我们的履带板、前后导轮等铸件用材就需要这样。
但不管合金成份如何变化,必须控制在一定的范围内才能起到好的作用。
这些作用是以提高高锰钢性能为主要目的,对控制裂纹并不明显。
研究标准成份高锰钢的各元素对裂纹的影响能得到理想的效果。
碳、锰是高锰钢的主要成分,正常情况下高锰钢的组织是奥氏体单相。
在含碳量偏低时易形成马氏体和8相 (密排六方体)。
在含碳量高时。
水韧处理状态下不能避免碳化物析出,还会降低钢的性能。
较高的含碳量可提高屈服点,但会降低延伸性.含碳量低而含锰量高的钢具有高韧性,对高锰钢的碳含量在保证性能的前提下尽可能控制在中下限。
锰含量控制在中上限。
最好保持在狭小范围内,防止碳化物析出,避免造成延伸性和韧性降低而产生裂纹。
硅含量一般在 1.0%以下,它对锰钢的机械性能没有显著影响,超过1.0%并逐渐增大时,强度和延伸性会剧烈下降。
生产中硅含量都比较低。
锰钢中含硫量较低,因为硫易和锰化合成硫化锰大部分进入炉渣中。
钢中残留少量的硫化物成为非金属夹杂物存在,它对钢的性能影响极微,可忽略不计。
高锰钢使用后开裂原因

高锰钢使用后开裂原因高锰钢在很多地方都有用武之地呢,像那些需要耐磨的机械部件之类的。
可有时候啊,这高锰钢使用后就开裂了,这是为啥呢?咱得先知道高锰钢的脾气。
高锰钢啊,就像一个特别有个性的人。
它里面锰的含量高,这就使得它的性能很独特。
要是在加工或者使用过程中没照顾好它的小脾气,就容易出问题。
比如说,它的加工工艺要是不合适,就好比给一个性格倔强的人穿了不合身的衣服,怎么着都别扭。
加工的时候温度没控制好,忽冷忽热的,这高锰钢内部的结构就被折腾得乱七八糟,就像咱们的心情一样,被搅得心烦意乱,那可不就容易出毛病,产生裂纹嘛。
再说说使用环境这事儿。
高锰钢如果处在一个特别恶劣的环境里,那简直就是把一个娇弱的人扔到了狂风暴雨里。
要是在高应力的环境下,就像一个人一直承受着巨大的压力,它能不崩溃吗?它可能会超出自己所能承受的极限,然后就开裂了。
而且啊,如果周围的介质对它有腐蚀性,那就像是一群小虫子在不停地啃咬它,时间一长,结构被破坏,开裂也就不奇怪了。
还有一个很容易被忽视的点,就是高锰钢本身的质量问题。
你想啊,如果是从一开始它就像一个先天不足的孩子,内部有缺陷,那在使用的时候就像带着病去干活。
这缺陷就像一颗定时炸弹,说不定什么时候就炸了,表现出来就是开裂呗。
就好比我们买东西,要是买了个质量不好的碗,用着用着突然裂了,你说是不是很气人?这高锰钢也是一样的道理啊。
另外呢,在高锰钢的安装或者装配过程中也可能埋下隐患。
如果装配的时候就像是给它穿了一双不合适的鞋子,各个部件之间的配合不协调,那在使用的时候就会产生额外的应力。
这就好比两个人在合作的时候总是互相使绊子,这样肯定干不好事儿啊。
这额外的应力就会不断地拉扯高锰钢,就像在拉扯一块有韧性但也有限度的橡皮筋,拉过头了,可不就断了,也就是开裂了。
从这些方面看啊,高锰钢使用后开裂不是一个简单的事儿,是很多因素综合起来的结果。
这就像我们生活中的很多事情一样,不是单一原因造成的。
可能是加工的时候没用心,可能是使用环境太恶劣,可能是本身质量就不过关,还可能是装配的时候就没弄好。
高锰钢裂纹防治与的热处理工艺

一、高镒钢铸件防止裂纹的产生1、铸件的结构设计铸件的壁厚相差太大、壁厚过渡不当、铸件圆角过渡太小等结构问题均容易产生裂纹。
因此,铸件设计应密切与铸造工艺相结合,尽量避免铸件设计不合理。
例如可以将字断面改为形断面等。
2、铸造工艺设计(包括各种工艺因素及浇注系统)在铸造工艺各因素中最重要的是铸型的退让性,其次是砂箱设计不合理。
例如箱筋阻碍收缩可以产生裂纹,因此,箱筋距铸件及冒口要有一定的距离。
浇注系统设计不当,分散导人的多条内浇道往往因阻碍铸件收缩,而在与内浇道联结处开裂。
应该特别指出,在铸件内浇道导入处,局部温度高而最后凝固,由于得不到足够的补缩,收缩应力使铸件开裂,所以一般在内浇道处要设置冒口补缩。
3、高镒钢铸件的冒口及冷铁设置高镒钢铸件的冒口设置以不用普通顶冒口为原则,因为用乙烘焰切割冒口时容易造成裂纹。
所以最好采用侧冒口及易割冒口,冒□一般用锤打掉。
铸件设置冒口对热节进行补缩,使铸件不产生缩孔及缩松,是防止内裂的有效措施,但冒口设置又产生了接触热节,其它工艺措施要与其配合得当。
如合理地使用冷铁,就可做到既防止内裂又不会产生外裂。
冷铁可以调节铸件各部分凝固速度,可以使铸件的缺陷发生位置迁移,同冒口配合可以扩大冒口的补缩范围。
但是冷铁使用不当,例如使用弯曲变形的冷铁时往往会在不适当的冷铁长度范围内因铸件凝固速度不均衡而造成裂纹。
冷铁之间间隔大也可造成裂纹,高镒钢铸件对此很敏感,所以工艺设计时应特别注意。
4、化学成分及熔炼工艺在高镒钢中,碳和磷对裂纹的产生影响最大。
含碳量越高,铸件越容易产生裂纹。
钢液的还原精炼对高镒钢铸件裂纹的影响也要引起重视。
在高镒钢的冶炼过程中应严格控制炉渣中FeO+MnO之和不大于1.2%,因为随着渣中FeO+MnO之和的提高,钢液中FeO+MnO也必升高,凝固后在晶界上析出,会使钢变脆。
控制浇注温度及开箱温度也是防止高镒钢铸件产生裂纹的有效措施。
随着浇注温度的升高,铸件收缩应力增大,更重要的是晶粒粗大,柱状晶严重,大大削弱了钢的强度。
矿山高锰钢铲齿断裂原因分析
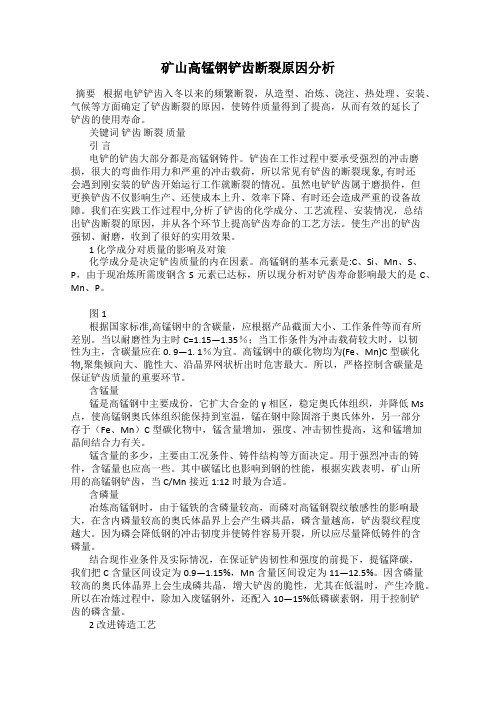
矿山高锰钢铲齿断裂原因分析摘要根据电铲铲齿入冬以来的频繁断裂,从造型、冶炼、浇注、热处理、安装、气候等方面确定了铲齿断裂的原因,使铸件质量得到了提高,从而有效的延长了铲齿的使用寿命。
关键词铲齿断裂质量引言电铲的铲齿大部分都是高锰钢铸件。
铲齿在工作过程中要承受强烈的冲击磨损,很大的弯曲作用力和严重的冲击载荷,所以常见有铲齿的断裂现象, 有时还会遇到刚安装的铲齿开始运行工作就断裂的情况。
虽然电铲铲齿属于磨损件,但更换铲齿不仅影响生产、还使成本上升、效率下降、有时还会造成严重的设备故障。
我们在实践工作过程中,分析了铲齿的化学成分、工艺流程、安装情况,总结出铲齿断裂的原因,并从各个环节上提高铲齿寿命的工艺方法。
使生产出的铲齿强韧、耐磨,收到了很好的实用效果。
1 化学成分对质量的影响及对策化学成分是决定铲齿质量的内在因素。
高锰钢的基本元素是:C、Si、Mn、S、P,由于现冶炼所需废钢含S元素已达标,所以现分析对铲齿寿命影响最大的是C、Mn、P。
图1根据国家标准,高锰钢中的含碳量,应根据产品截面大小、工作条件等而有所差别。
当以耐磨性为主时C=1.15—1.35%;当工作条件为冲击载荷较大时,以韧性为主,含碳量应在0. 9—1. 1%为宜。
高锰钢中的碳化物均为(Fe、Mn)C型碳化物,聚集倾向大、脆性大、沿晶界网状析出时危害最大。
所以,严格控制含碳量是保证铲齿质量的重要环节。
含锰量锰是高锰钢中主要成份,它扩大合金的γ相区,稳定奥氏体组织,并降低Ms 点,使高锰钢奥氏体组织能保持到室温,锰在钢中除固溶于奥氏体外,另一部分存于(Fe、Mn)C型碳化物中,锰含量增加,强度、冲击韧性提高,这和锰增加晶间结合力有关。
锰含量的多少,主要由工况条件、铸件结构等方面决定。
用于强烈冲击的铸件,含锰量也应高一些。
其中碳锰比也影响到钢的性能,根据实践表明,矿山所用的高锰钢铲齿,当C/Mn接近1:12时最为合适。
含磷量冶炼高锰钢时,由于锰铁的含磷量较高,而磷对高锰钢裂纹敏感性的影响最大,在含内磷量较高的奥氏体晶界上会产生磷共晶,磷含量越高,铲齿裂纹程度越大。
高锰钢斗齿断裂原因分析
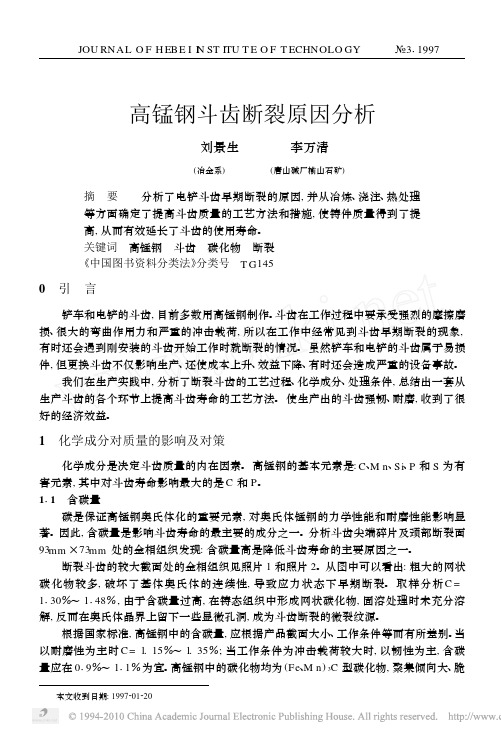
JOU RNAL O F H EB E I I N ST ITU T E O F T ECHNOLO GY 311997 高锰钢斗齿断裂原因分析 刘景生 李万清 (冶金系) (唐山碱厂榆山石矿)摘 要 分析了电铲斗齿早期断裂的原因,并从冶炼、浇注、热处理等方面确定了提高斗齿质量的工艺方法和措施,使铸件质量得到了提高,从而有效延长了斗齿的使用寿命。
关键词 高锰钢 斗齿 碳化物 断裂《中国图书资料分类法》分类号 T G1450 引 言铲车和电铲的斗齿,目前多数用高锰钢制作。
斗齿在工作过程中要承受强烈的摩擦磨损、很大的弯曲作用力和严重的冲击载荷,所以在工作中经常见到斗齿早期断裂的现象,有时还会遇到刚安装的斗齿开始工作时就断裂的情况。
虽然铲车和电铲的斗齿属于易损件,但更换斗齿不仅影响生产、还使成本上升、效益下降、有时还会造成严重的设备事故。
我们在生产实践中,分析了断裂斗齿的工艺过程、化学成分、处理条件,总结出一套从生产斗齿的各个环节上提高斗齿寿命的工艺方法。
使生产出的斗齿强韧、耐磨,收到了很好的经济效益。
1 化学成分对质量的影响及对策化学成分是决定斗齿质量的内在因素。
高锰钢的基本元素是:C、M n、Si、P和S为有害元素,其中对斗齿寿命影响最大的是C和P。
111 含碳量碳是保证高锰钢奥氏体化的重要元素,对奥氏体锰钢的力学性能和耐磨性能影响显著。
因此,含碳量是影响斗齿寿命的最主要的成分之一。
分析斗齿尖端碎片及颈部断裂面93mm×73mm处的金相组织发现:含碳量高是降低斗齿寿命的主要原因之一。
断裂斗齿的较大截面处的金相组织见照片1和照片2。
从图中可以看出:粗大的网状碳化物较多,破坏了基体奥氏体的连续性,导致应力状态下早期断裂。
取样分析C= 1130◊~1148◊,由于含碳量过高,在铸态组织中形成网状碳化物,固溶处理时未充分溶解,反而在奥氏体晶界上留下一些显微孔洞,成为斗齿断裂的微裂纹源。
根据国家标准,高锰钢中的含碳量,应根据产品截面大小、工作条件等而有所差别。
大型挖掘机高锰钢履带板断裂机理及控制措施

大型挖掘机高锰钢履带板断裂机理及控制措施大型挖掘机是一种重型工程机械,常用于土石方工程、矿山开采等领域。
其履带板作为挖掘机的重要部件,承受着巨大的负荷和冲击力。
然而,履带板在工作过程中可能会出现断裂现象,给挖掘机的正常运行带来困扰。
本文将就大型挖掘机高锰钢履带板断裂的机理和控制措施展开探讨。
我们来分析大型挖掘机高锰钢履带板断裂的机理。
履带板断裂的原因主要包括材料问题、设计问题和使用问题。
首先是材料问题。
由于大型挖掘机在工作过程中需要承受巨大的冲击力和磨损,因此需要选用具有较高强度和耐磨性的材料。
高锰钢作为一种优质材料,具有良好的强度和耐磨性,常被用于制造履带板。
然而,高锰钢也存在着一定的脆性,容易发生断裂。
其次是设计问题。
履带板的设计不合理也会导致断裂。
例如,设计上存在应力集中、结构不均匀等问题,都可能导致履带板出现断裂。
最后是使用问题。
挖掘机在使用过程中,如果超负荷工作、频繁冲击等操作不当,都会加剧履带板的磨损和断裂风险。
为了有效控制大型挖掘机高锰钢履带板的断裂,可以从以下几个方面进行措施。
首先是材料的选择。
应选用质量可靠、强度高、耐磨性好的高锰钢材料,以提高履带板的抗冲击和抗磨损能力,降低断裂风险。
其次是优化设计。
履带板的设计应考虑到力学原理,避免应力集中,增加板材的均匀性,提高其承载能力。
此外,还可以采用适当的加固措施,如增加履带板的厚度或采用加强筋等,来提高其抗断裂能力。
第三是加强使用管理。
操作人员应严格按照使用说明进行操作,避免超负荷工作和频繁冲击,合理控制挖掘机的工作负荷,以延长履带板的使用寿命。
此外,还应定期检查、维护和更换履带板,及时发现和处理存在的问题,防止断裂事故的发生。
大型挖掘机高锰钢履带板断裂是由材料问题、设计问题和使用问题共同引起的。
为了有效控制履带板的断裂,需要选择合适的材料,优化设计,加强使用管理。
只有从多个方面综合考虑和控制,才能降低履带板的断裂风险,确保挖掘机的正常运行。
- 1、下载文档前请自行甄别文档内容的完整性,平台不提供额外的编辑、内容补充、找答案等附加服务。
- 2、"仅部分预览"的文档,不可在线预览部分如存在完整性等问题,可反馈申请退款(可完整预览的文档不适用该条件!)。
- 3、如文档侵犯您的权益,请联系客服反馈,我们会尽快为您处理(人工客服工作时间:9:00-18:30)。
JOU RNAL O F H EB E I I N ST ITU T E O F T ECHNOLO GY 311997 高锰钢斗齿断裂原因分析 刘景生 李万清 (冶金系) (唐山碱厂榆山石矿)摘 要 分析了电铲斗齿早期断裂的原因,并从冶炼、浇注、热处理等方面确定了提高斗齿质量的工艺方法和措施,使铸件质量得到了提高,从而有效延长了斗齿的使用寿命。
关键词 高锰钢 斗齿 碳化物 断裂《中国图书资料分类法》分类号 T G1450 引 言铲车和电铲的斗齿,目前多数用高锰钢制作。
斗齿在工作过程中要承受强烈的摩擦磨损、很大的弯曲作用力和严重的冲击载荷,所以在工作中经常见到斗齿早期断裂的现象,有时还会遇到刚安装的斗齿开始工作时就断裂的情况。
虽然铲车和电铲的斗齿属于易损件,但更换斗齿不仅影响生产、还使成本上升、效益下降、有时还会造成严重的设备事故。
我们在生产实践中,分析了断裂斗齿的工艺过程、化学成分、处理条件,总结出一套从生产斗齿的各个环节上提高斗齿寿命的工艺方法。
使生产出的斗齿强韧、耐磨,收到了很好的经济效益。
1 化学成分对质量的影响及对策化学成分是决定斗齿质量的内在因素。
高锰钢的基本元素是:C、M n、Si、P和S为有害元素,其中对斗齿寿命影响最大的是C和P。
111 含碳量碳是保证高锰钢奥氏体化的重要元素,对奥氏体锰钢的力学性能和耐磨性能影响显著。
因此,含碳量是影响斗齿寿命的最主要的成分之一。
分析斗齿尖端碎片及颈部断裂面93mm×73mm处的金相组织发现:含碳量高是降低斗齿寿命的主要原因之一。
断裂斗齿的较大截面处的金相组织见照片1和照片2。
从图中可以看出:粗大的网状碳化物较多,破坏了基体奥氏体的连续性,导致应力状态下早期断裂。
取样分析C= 1130◊~1148◊,由于含碳量过高,在铸态组织中形成网状碳化物,固溶处理时未充分溶解,反而在奥氏体晶界上留下一些显微孔洞,成为斗齿断裂的微裂纹源。
根据国家标准,高锰钢中的含碳量,应根据产品截面大小、工作条件等而有所差别。
当以耐磨性为主时C=1.15◊~1.35◊;当工作条件为冲击载荷较大时,以韧性为主,含碳量应在019◊~111◊为宜。
高锰钢中的碳化物均为(Fe、M n)3C型碳化物,聚集倾向大、脆本文收到日期:1997201220照片1 斗齿93mm ×73mm 处 碳化物形态×100照片2 网状碳化物×400性大、沿晶界网状析出时危害最大。
所以,严格控制含碳量是保证斗齿质量的重要环节。
112 含磷量磷在高锰钢中的溶解度不大,且随碳含量的提高而降低。
磷主要以磷共晶的形式存在,当磷共晶以细小、弥散分布时,对高锰钢的耐磨性有贡献;但当磷含量过高,形成粗大、沿晶界分布的磷共晶时,会严重地降低基体强度,导致构件早期断裂。
早期断裂的斗齿化学成分中磷含量高达0108◊~011◊。
当碳和磷同时达到标准含量上限时,也会使碳化物数量明显增多,增加固溶处理的难度,甚至影响到产品的质量和寿命。
因此,在冶炼中按国家标准控制成分是生产高质量产品的关键,其中严格控制碳和磷,较之其它元素含量的控制更为重要。
2 改进铸造工艺高锰钢的机械性能与铸态组织中的晶粒大小密切相关,铸件中粗大的奥氏体晶粒不能通过热处理方法加以细化,所以要获得细小的晶粒应该主要从优化铸造工艺入手。
211 严格控制浇注温度适当降低浇注温度,可获得细小的晶粒。
由于生产的实际条件所限,低温浇注操作有一定难度。
若有快速热电偶,采用包内测温,可将浇注温度控制在1420~1450℃;或者,可采用样勺结膜25~30秒的时间控制法。
出钢温度较高时,根据造型箱的多少,静置适当的时间,原则是浇完最后一箱时钢包内剩余钢水呈半凝固状态为准。
212 采用金属型或内外冷铁采用金属型或内外冷铁的主要目的是加速结晶过程。
一方面快速结晶时,已经形成的晶粒来不及长大,可细化晶粒;另一方面通过冷铁使铸件不同厚度的截面达到同时凝固,以减少应力、变形和开裂。
金属型铸造是常用的方法,虽然金属型的一次投资大,但在产品质量和尺寸精确度方面的优越性是显而易见的。
金属型导热能力强、吸热量大,因此能增大结晶过程中的成核率而使晶粒细化,在采用顺序凝固方案时金属型的优越性显著。
使金属型同时凝固有两种方法:一是在斗齿大截面处中心加内冷铁。
例如,在1m 3电铲斗齿93mm ×73mm 截面处7高锰钢斗齿断裂原因分析——刘景生 李万清8 河北理工学院学报 1997年 第19卷第3期加 20mm×180mm的内冷铁,使内冷铁的外表面与钢水相遇,结晶时形成细小的等轴晶,可避免通常金属型铸造时出现的“穿透”柱状晶的出现,从而显著地改善了斗齿力学性能上的各向异性,提高了使用寿命;二是在斗齿两端薄截面处金属型内加沙套。
这样在浇注后,薄截面处钢水少,可得到较温和的冷却速度,厚截面处钢水多,可得到较激烈的冷却速度。
从而使整个铸件得到基本相同的凝固条件,避免了同一铸件因在不同截面处先后凝固而产生的热应力和相变应力。
因高锰钢导热性差、膨胀系数大,在铸件中产生热应力较大时,会使铸件热节处产生裂纹。
213 浇冒口及处理高锰钢件一般少用冒口。
其理由是含碳量、含锰量高,熔点低,在浇注时对钢水的过热度要求较小,流动性好不易产生缩孔,采用易割冒口及压边冒口都能收到较好的效果。
小型铸件的冒口在水韧处理前打掉;大型铸件的冒口在水韧处理后用气割割掉。
在割冒口时,为防止冒口根部与铸件接触处的局部过热而产生裂纹,常将铸件的2 3浸入循环冷水中(水温低于45℃)。
在切割斗齿的皮缝时,也将斗齿置于预制的水箱内,使之2 3浸入水中,这样就防止了因局部过热而产生的小裂纹。
3 优化热处理工艺311 加热速度的选择因高锰钢导热性差、线收缩较大,在加热过程中产生内应力较大;同时由于铸态组织中碳化物的存在降低了钢的塑性,易使铸件开裂,所以,加热速度不宜太快,特别是从常温加热到600℃的一段时间内,钢的塑性低更易使铸件开裂,加热速度应适当控制。
加热速度按铸件的厚度及结构考虑,见表1。
温度达600℃以后,对全部铸件均采用120~150℃ h,升温到1100℃。
表1 不同壁厚铸件加热速度的选择壁厚(mm)<3030~60>60加热速度(℃ h)70~8050~6030~50312 加热温度和保温时间选择加热温度和保温时间的原则是应保证钢中碳化物充分固溶到奥氏体中,同时保持细小的奥氏体晶粒。
因此必须加热到状态图A c m线以上,并保温足够的时间。
当C=0. 9◊~1.1◊时,固溶处理温度为1050~1100℃。
在加热时应注意以下两个问题。
31211 防止欠热当欠热时,碳化物不能充分溶解到奥氏体中,易分布于晶界,使铸件脆断。
铸态组织见图3。
31212 防止过热过热时奥氏体晶粒粗大,表层氧化脱碳,使耐磨度下降。
313 水韧处理开启炉门后迅速将铸件投入循环水中,铸件在空气中停留时间应小于20~30s。
铸件入水前,水温应低于30℃,入水后水温应低于60℃,否则碳化物重新以网状形式析出会影响质量。
水韧处理后其组织为单一奥氏体,见图4。
图3 铸态组织×100图4 水韧处理后组织×100图5 1m 3电铲斗齿热处理工艺314 热处理工艺曲线为使斗齿受热均匀,防止热裂,采取了分段保温热处理方案。
工艺曲线见图5。
按此工艺处理的斗齿,多年来没有发生表面断裂及过烧脱碳现象。
现场使用情况很好。
4 结束语通过分析电铲斗齿早期断裂的原因,总结出了一套提高其质量的方法和措施。
即在产品中,应从冶炼、浇注、热处理工艺等方面严把质量关,以提高铸件的成品率和生产质量。
参考文献1 陈希杰1高锰钢1北京:机械工业出版社1989,212 张清1金属磨损和金属耐磨材料手册1北京:冶金工业出版社 1991,113 赵沛1合金钢冶炼1北京:冶金工业出版社,1992,1019高锰钢斗齿断裂原因分析——刘景生 李万清01 河北理工学院学报 1997年 第19卷第3期ANALY SIS ON REAS ONS OF H IGH-M ANGANESESTEEL B OOT-TEETH′S BREAK DOW NL iu J ingsheng(D ep artm en t of M etallu rgy)L iW angqing(Yu shan O re Stati on T angshan A lkatine facto ry)Abstract T h is paper has analyzed the reason s of pow er shovel boo t-teeth′s early p eri od b reakdow n,the m ethods and w ays are given from m elting,pou ring,heat-treating and so on,the casting quality is then i m p roved,and they greatly p ro long the du rab ility of boo t-teeth.Key words H igh-m anganese-steel Boo t-teeth Carb ide B reakdow n可以不退火进行冷锻的表面硬化钢据报道日本大同钢铁有限公司开发了一种可不经球化退火处理进行冷锻的表面硬化钢。
标准的表面硬化钢含有C、Si、M n、C r,有时还含有M o或N i。
然而,这些元素在正火和球化这样的软化处理后,可能引起硬度的提高。
合金化元素与硬度的关系研究得到的结论是:添加B同时降低Si、M n和C r的含量,对于使轧制棒材变软而不降低表面硬化性是有利的。
而且,通过控制晶界上磷的偏析,B 改进了钢的韧性和疲劳强度。
该钢的组成为:Fe20120C20107Si20.5M n20.015P20.015S21.00C r和010015B (m ass%)。
此外,添加少量的T i和N b可减少氮化硼夹杂和控制晶粒长大。
该钢在热轧后具有75HRB的硬度,相当于通常的球化处理钢Scr420。
渗碳处理以后,该钢具有良好的冷变形性和机加工性。
在正火状态下具有比通常钢更好的机加工性。
这种最新开发的钢,目前被试用于差动齿轮和变速齿轮。