DPR-2说明书(6U)new
蒂森克虏伯电梯新大陆类型并联lop在、安装手册

2 横式显示器及并联召唤盒的安装: 2.1 安装环境:
横式显示器及并联召唤盒安装环境要求见下表:
ThyssenKrupp Elevator
4
Installation Manual
编号:EC355-TS
横式显示器及并联召唤盒安装环境
项目
பைடு நூலகம்
要求
海拔
≤1000m
温度
-15~70℃
湿度
最湿月平均最高相对湿度≤90%,
1.4 横式显示器及并联召唤盒物料号、名称、型号及规格
物料号 200007590 200007591 200007592 200007593 200007594 200007595 200007579 200007580
名称 并联召唤盒 并联召唤盒 并联召唤盒 并联召唤盒 并联召唤盒 并联召唤盒 横式显示器 横式显示器
ThyssenKrupp Elevator
6
Installation Manual
编号:EC355-TS
3.2 楼层码,运行方向及特殊字符显示: a)楼层码和运行方向显示: 横式显示器应显示电梯当前所处楼层的楼层码,并电梯运行时应能显示电梯当前的运行方向 b)特殊字符显示:
电梯处于检修状态时,召唤显示器显示:“IF”字符;复位后电梯找平层时,横式显示器显示 “JU”字符;电梯出现故障时,楼层显示“——” 3.3 锁梯钥匙开关:(特殊楼层)
横式显示器技术参数:
编号:EC355-TS
信号功能
信号名称
上召唤按钮灯 上召唤按钮 下召唤按钮灯 下召唤按钮 门锁开关检测 平层传感器 消防员操作 后备输入 上/下到站信号 I < 600 mA
+24V RO
RB2电器用品用户手册说明书

USER MANUALIMPORT ANT SAFETY INSTRUCTIONSWARNING: When using electric products, basic cautions should always be followed, including the following.1. Read all safety and operating instructions before using this product2. The product should be powered by a three pin `grounded (or earthed) plug connected to a power socket with a grounded earth outlet.3. All safety and operating instructions should be retained for future reference4. Obey all cautions in the Operating instructions and on the back of the unit5. All operating instructions should be followed6. This product should not be used near water, i.e. a bathtub, sink, swimming pool, wet basement, etc.7. This product should be located so that its position does not interfere with its proper ventilation. It should not be placed flat against a wall or placed in a built up enclosure that will impede the flow of cooling air.8. This product should not be placed near a source of heat such as stove, radiator, or another heat producing amplifier.9. Connect only to a power supply of the type marker on the unit adjacent to the power supply cord.10.Never break off the ground pin on a power supply cord.11.Power supply cords should always be handled carefully. Never walk or place equipment on power supply cords. Periodically check cords for cuts or signs of stress, especially at the plug and the point where the chord exits the unit.12.The power supply cord should be unplugged when the unit is to be unused for long periods of time.13.If this product is to be mounted in an equipment rack, rear support should be provided.14.The user should allow easy access to any mains plug, mains coupler and mains switch used in conjunction with this unit thus making it readily operable.15.Metal parts can be cleaned with a damp cloth. The vinyl covering used on some units can be cleaned with a damp cloth or ammonia based household cleaner if necessary. Disconnect the unit from the power supply before cleaning.16.Care should be taken so that objects do not fall and liquids are not spilled into the unit through any ventilation holes or openings. On no account place drinks on the unit.17. A qualified service technician should check the unit if:18.The user should not attempt to service the equipment. All service work is done by a qualified service technician.19. Exposure to extremely high noise levels may cause a permanent hearing gloss. Individuals vary considerably in susceptibility to noise induced hearing loss, but nearly everyone will lose some hearing if exposed to sufficiently intense noise for a sufficient time. The U.S. Government's Occupational Safety and Health Administration (OSHA) has specified the following permissible noise level exposure. Duration Per Day In Hours Sound Level dBA, slow response8 9069249539721001 ½1021105½110¼ or less 115According to OSHA, any exposure in excess of the above permissible limits could result in some hearing loss. Ear plugs or protectors in the ear canals or over the ears must beworn when operating this amplification system in order to prevent a permanent hearing loss if exposure exceeds the limits set forth above. T o ensure against potentially dangerous exposure to high sound pressure levels it is recommended that all persons exposed to equipment capable of producing high sound pressure levels such as this amplification system be protected by hearing protectors while this unit is in operation.!The power cord has been damaged!Anything has fallen or spilled into the unit !The unit does not appear to operate correctly!The unit has been dropped or the enclosure damaged.BEFORE SWITCHING ONAfter unpacking your amplifier check that it is factory fitted with a three pin 'grounded' (or earthed) plug. Before plugging into the power supply ensure you are connecting to a grounded earth outlet.If you should wish to change the factory fitted plug yourself, ensure that the wiring convention applicable to the country where the amplifier is to be used is strictly conformed to. A s an example in the United Kingdom the cable colour code for connections are as follows.NOTEThis manual has been written for easy access of information. The front and rear panels are graphically illustrated, with each control and feature numbered. For a description of the function of each control feature, simply check the number with the explanations adjacent to each panel.Y our Laney amplifier has undergone a thorough two stage, pre-delivery inspection, involving actual play testing.When you first receive your Laney Bass amp, follow these simple procedures:(i) Ensure that the amplifier is the correct voltage for the country it is to be used in.(ii) Connect your instrument with a high quality shielded instrument cable. Y ou have probably spent con siderable money on your amplifier and guitar - don’t use poor quality cable it won’t do your gear justice.Please retain your original carton and packaging so in the unlikely event that some time in the future your amplifier should require servicing you will be able to return it to your dealer securely packed.Care of your Laney amplifier will prolong it's life.....and yours!EARTH OR GROUND - GREEN/YELLOW NEUTRAL - BLUELIVE - BROWNINTRODUCTIONThe RB2 is a 30W bass combo with a 10 inch loudspeaker in a sturdy wooden cabinet. Its features include; two ¼” jack inputs for Normal / Hi level signals, a gain control and a switchable compressor, a flexible EQ system with Bass, swept Mid and T reble control followed by an overall Volume. Should you need to play along to CDs/MP3s you can plug the output of your player into the CD/line in socket. A headphone socket is also provided for private practice, and an external speaker socket for connecting additional cabinets. A Direct out allows you to connect to a PA or recording device. An explanation of these features follows on pages 6-8.Dear Player,Thank you very much for purchasing your new Laney product and becoming part of the worldwide Laney family. Each and every Laney unit is designed and built with the utmost attention to care and detail, so I trust yours will give you many years of ney products have a heritage which stretches back to 1967 when I first began building valve amplifiers in my parent’s garage. Since then we have moved on from strength to strength developing an extensive range of guitar, bass, public address and keyboard amplification products along with a list of Laney endorsees that includes some of the world’s most famous and respected musicians. At the same time we believe we have not lost sight of the reason Laney was founded in the first place - a dedication to building great sounding amplification for working musicians. Warm Regards,Lyndon Laney CEONormal and High inputs are provided for connection of bass guitars. High output basses, either Active or Passive should be connected via the High socket. Low output basses should be connected using the normal input. High output basses may also be placed in the Normal input if pre-amp overloading is desired.This control is used to set the level of gain present in the pre-amp. producing distortion. The Gain control should be used in conjunction with the signal characteristics.Engages and disengages the on-board compressor, this compresses the input-signal giving a punchier sound. In association with the compressor is an LED indicating that the compressor is active. The amount of compression is controlled by the Gain control. The higher the setting the more compression. With most guitars compression will begin at about 5-6 on the control. It is possible to have the compressor engaged but it only be active during certain periods of playing - typically the most dynamic sections.Controls the boost and cut of the low-frequency response of the pre-amplifier.FRONT P ANEL CONTROLST o access low mid-frequencies turn the frequency control anticlockwise, to access higher mid frequencies turn the frequency control clockwise.Controls the boost and cut of the high-frequency response of the pre-amplifier.Sets the overall listening level of the amplifier.RCA/Phono connections provided for connecting an external sound source such as; CD players, MP3 players, Minidisc etc.This socket provides a balanced low-impedance output-signal from the pre-amplifier taken before the Master Volume but after any tone correction, used for direct-injection of the amplifier signal to a mixing-desk or additional power-amplifier.This socket(s) should be used to connect an external cabinet. The impedance of the extension-cabinet must not be less than 4 Ohms. Connecting cabinets that have a lower impedance than 4 Ohms will result in the amplifier overheating. Continual use in this manner may cause permanent damage. Connecting a cabinet with an impedance of greater than 4 Ohms will cause no damage to the amplifier but will result in a reduced output level. (When using an external cabinet the internal speaker is automatically disconnected)Socket for connecting headphones. With headphones connected, the internal and any externally connected loudspeakers are automatically switched off.Indicates power is connected and the amplifier is switched on.(Always switch off and disconnect power cord when not in use)Main power on/off switch.Power inlet socket. Connect to your power source. Make sure the specified voltage is correct for your country!The mains safety fuse for the unit is contained within this drawer.USE ONLY THE CORRECT SIZE AND RATING OF FUSE AS SPECIFIED ON THE PANEL.The mains fuse ratings are detailed in the specs section at the rear of this manual.Serial Number and model of your unit.REAR P ANEL CONTROLSu d s p e a k e r C a b l eHIUSER SETTINGSFound some cool settings you want to keep? Make a note of them here:General NotesAmplifier connection: In order to avoid damage, it is advisable to establish and follow a pattern for turning on and off your equipment. With all system parts connected, turn on source equipment, tape decks, cd players, mixers, effects processors etc. BEFORE turning on your Bass Amplifier. Many products have large transient surges at turn on and off which can cause damage to your speakers. By turning on your Bass Amplifier LAST and making sure its Volume control is set to minimum any transients from other equipment will not reach your loudspeakers. Wait until all system parts have stabilised; usually a couple of seconds. Similarly when turning off your system always turn down the Volume control on your Bass Amplifier and then turn off its power before turning off other equipment.Cables: Never use shielded or microphone cable for any speaker connections as this will not be substantial enough to handle the amplifier load and could cause damage to your amplifier system.Caution:These professional loudspeaker systems are capable of generating very high sound pressure levels. Use care with placement and operation to avoid exposure to excessive levels that can cause permanent hearing damage. (Refer to guidelines on page 2)Servicing: The user should not attempt to service these products. Refer all servicing to qualified service personnel.SPECIFICA TIONSSupply Voltage~100V , ~120V , ~220V , ~230V , ~240V 50/60Hz Factory Option Mains Fuse ~220V>~240V = T250mA L. ~100>~120V = T500mA L (Time delay)Power Consumption 50WOutput Power Rating 30WLoudspeaker 10” Custom Designed DriverFeatures Normal + Hi InputsSwitchable Compressor with Activity light.Clip distortion limiter.EQ Bass (Shelving)Paramid (KHz Peaking)D.I.Y es, Balanced Jack. (Can be used for T uner)Extension Loudspeaker Socket (4 Ohms minimum, disconnects internal speaker)Input Impedance 1M Ohm/100pFRecommended Min Extension Speaker Power 80WRecommended Richter Extension Cab RB410 / RB115Size 440*390*257(H*W*D)Unit Weight 11.75 KgPacking Weight 13 Kg±12dB at 65Hz,±12dB at 200Hz > 2T reble (±15dB at 3.5KHz, Shelving)This product conforms to:European EMC directive(2004/108/EC), Low Voltage Directive (72/23/EEC) and CE mark Directive (93/68/EEC)Page 11 /12LaneyOPERATING INSTRUCTIONSIn the interest of continued product development, Laney reserves the right to amend product specification without prior notification.POWER TO THE MUSIC Laney@。
Dell PowerEdge M620 Systems 用户手册说明书

Dell PowerEdge M620 Systems(适用于 Dell PowerEdge VRTX 机柜)用户手册管制型号: HHB管制类型: HHB003注、小心和警告注: “注”表示可以帮助您更好地使用计算机的重要信息。
小心: “小心”表示可能会损坏硬件或导致数据丢失,并说明如何避免此类问题。
警告: “警告”表示可能会造成财产损失、人身伤害甚至死亡。
版权所有© 2014 Dell Inc. 保留所有权利。
本产品受美国、国际版权和知识产权法律保护。
Dell™和 Dell 徽标是 Dell Inc. 在美国和 / 或其他管辖区域的商标。
所有此处提及的其他商标和产品名称可能是其各自所属公司的商标。
2014–10Rev. A01目录1 关于系统 (7)简介 (7)前面板部件和指示灯 (8)使用 USB 软盘或 USB DVD/CD 驱动器 (8)硬盘驱动器功能部件 (8)您可能需要的其他信息 (9)2 使用系统设置程序和引导管理器 (11)选择系统引导模式 (12)进入系统设置 (12)响应错误消息 (12)使用系统设置程序导航键 (12)系统设置选项 (12)系统设置程序主屏幕 (13)系统 BIOS 屏幕 (13)System Information(系统信息)屏幕 (14)Memory Settings(内存设置)屏幕 (14)Processor Settings(处理器设置)屏幕 (15)SATA Settings(SATA 设置)屏幕 (16)Boot Settings(引导设置)屏幕 (16)Integrated Devices(集成设备)屏幕 (17)Serial Communications(串行通信)屏幕 (18)系统配置文件设置屏幕 (18)System Security(系统安全)屏幕 (19)Miscellaneous Settings(其它设置) (20)系统和设置密码功能 (21)分配系统密码和/或设置密码 (21)使用系统密码保护系统安全 (22)删除或更改现有系统密码和/或设置密码 (22)在已启用设置密码的情况下进行操作 (22)进入 UEFI 引导管理器 (23)使用引导管理器导航键 (23)Boot Manager(引导管理器)屏幕 (23)UEFI Boot(UEFI 引导)菜单 (24)嵌入式系统管理 (24)iDRAC 设置公用程序 (24)进入 iDRAC 设置公用程序 (25)3 安装服务器模块组件 (26)建议工具 (26)安装和卸下服务器模块 (26)卸下服务器模块 (26)安装服务器模块 (28)打开与合上服务器模块 (28)打开服务器模块 (28)合上服务器模块 (29)服务器模块内部 (30)冷却导流罩 (30)卸下冷却导流罩 (30)安装冷却导流罩 (31)系统内存 (31)一般内存模块安装原则 (33)模式特定原则 (34)内存配置示例 (35)卸下内存模块 (38)安装内存模块 (39)PCIe 夹层卡 (40)卸下 PCIe 夹层卡 (40)安装 PCIe 夹层卡 (41)管理提升卡 (42)更换 SD 卡 (42)内部 USB 盘 (43)SD vFlash 卡 (43)装回 SD vFlash 卡 (43)网络子卡/LOM 提升卡 (44)卸下网络子卡/LOM 提升卡 (44)安装网络子卡/LOM 提升卡 (45)处理器 (45)卸下处理器 (46)安装处理器 (48)硬盘驱动器 (49)硬盘驱动器/SSD 安装原则 (50)卸下硬盘驱动器/SSD (50)安装硬盘驱动器/SSD (50)进行硬盘驱动器维修前的关机程序 (51)配置引导驱动器 (51)从硬盘驱动器/SSD 托盘中卸下硬盘驱动器/SSD (51)将硬盘驱动器/SSD 安装到硬盘驱动器/SSD 托盘中 (52)硬盘驱动器/SSD 背板 (52)卸下硬盘驱动器/SSD 背板 (52)安装硬盘驱动器/SSD 背板 (53)系统板 (54)卸下系统板 (54)安装系统板 (55)NVRAM 备用电池 (56)更换 NVRAM 备用电池 (56)存储控制器卡 (57)卸下存储控制器卡 (57)安装存储控制器卡 (58)4 系统故障排除 (59)安全第一—为您和您的系统着想 (59)系统内存故障排除 (59)硬盘驱动器故障排除 (59)USB 设备故障排除 (60)内部 SD 卡故障排除 (60)处理器故障排除 (61)系统板故障排除 (61)NVRAM 备用电池故障排除 (61)5 使用系统诊断程序 (63)Dell Online Diagnostics (63)Dell 嵌入式系统诊断程序 (63)何时使用 Embedded System Diagnostics(嵌入式系统诊断程序) (63)运行嵌入式系统诊断程序 (63)从外部介质运行嵌入式系统诊断程序 (64)系统诊断程序控件 (64)6 跳线和连接器 (65)系统板跳线设置 (65)系统板连接器 (66)禁用已忘记的密码 (67)7 技术规格 (68)8 系统消息 (71)LCD 状态信息 (71)查看 LCD 信息 (71)删除 LCD 消息 (71)系统错误消息 (71)警告信息 (141)诊断消息 (142)警报消息 (142)9 获得帮助 (143)联系 Dell (143)1关于系统简介本说明文件提供了有关 Dell PowerEdge M620 服务器模块的信息,该模块专为 PowerEdge VRTX 机柜配置,并且可以通过服务器模块上的标记为PCIe的标签来进行识别。
301 DPU II 用户手册

EDPF-NT分散控制系统DPU II用户手册(VER:5.2版)北京国电智深控制技术有限公司2007.7目录1.概述 (1)2.技术特点和技术参数 (2)2.1.技术特点 (2)2.2.技术参数 (3)3.硬件说明 (6)3.1.装置外形和结构: (6)3.2.指示灯及按钮: (8)3.3.底座端子定义: (9)3.4.DPU模块的硬件设置和跳线 (11)3.5.底座的硬件设置 (14)4.软件配置 (15)4.1.直接在DPU站设置 (15)4.2.在工程师站设置 (16)5.装配图 (18)1.概述EDPF-NT II型DPU 是我公司最新研制的DPU控制器,具有体积小,性能高,维护方便,可靠性高等特点。
第 1 页2.技术特点和技术参数2.1. 技术特点2.1.1.体积小,性能高在DPU模块内集成了主CPU、I/O通讯控制器和双网卡,使得DPU 控制器与I/O模块具有同样的大小。
采用PENTIUN级低功耗CPU,性能卓越,可满足各种工程需要。
2.1.2.多重冗余,安全可靠采用双机,双网,双电源,大大提高了系统的可靠性2.1.3.模块式结构维护方便采用模块化设计,由DPU单元和底板组成,DPU模块带有标准欧式插座,主副站可独立插拔,安装、更换十分方便、安全。
2.1.4.可靠的直流冗余宽范围供电接受两路宽范围DC18-72V电源输入,内部实现冗余切换,保证了电源的可靠性。
2.1.5.全隔离高抗干扰设计确保运行可靠内部采用DC/DC与电源以及I/O通讯网络进行隔离,硬件和软件都具有多重抗干扰和容错纠错能力。
第 2 页2.1.6.安全可靠的数据存储。
采用CF卡保存组态数据,确保数据的长期保存。
2.1.7.方便的I/O模块联结方式。
模块底座除了提供端子式I/O出线外,还提供两个DB25 I/O标准接口,可直接与模块底座拼接,方便组屏安装。
2.2. 技术参数2.2.1.电源y电压:冗余宽范围 DC18~72V,额定24V/48Vy功耗:小于10Wy纹波:不大于5%2.2.2.配置y CPU: 300MHz奔腾级低功耗CPUy RAM:64My电子盘:>=32M Compact Flashy以太网口:2个冗余,10M/100M自适应,RJ45双绞线接口。
自由挂载型轮廓电机56-C(D)RBU2-Z系列II 3 G说明书

Instruction ManualFree Mount Type Rotary ActuatorMarking Description:II3GEx hThe intended use of this Free Mount Type Rotary Actuator is to convert potential energy provided by compressed air into a force which causes Note 1: The X at the end of the certificate number represents that this product is subject to “Special Conditions of Use”, please see Section 2.3.1 Safety InstructionsThese safety instructions are intended to prevent hazardous situations and/or equipment damage. These instructions indicate the level of potential hazard with the labels of “Caution,” “Warning” or “Danger.”They are all important notes for safety and must be followed in additionto International Standards (ISO/IEC) *1), and other safety regulations.*1) ISO 4414: Pneumatic fluid power - General rules relating to systems.ISO 4413: Hydraulic fluid power - General rules relating to systems.IEC 60204-1: Safety of machinery - Electrical equipment of machines. (Part 1: General requirements)ISO 10218-1: Robots and robotic devices - Safety requirements for industrial robots - Part 1: Robots.Refer to product catalogue, Operation Manual and Handling Precautions for SMC Products for additional information.Keep this manual in a safe place for future reference.WarningAlways ensure compliance with relevant safety laws and standards.All work must be carried out in a safe manner by a qualified person in compliance with applicable national regulations. 2 SpecificationsThis product is suitable for use in Zone 2 only.2.1 Product Specifications:Refer to the operation manual for this product;2.1.3 Energy and Speed Specification:WarningEnsure a speed is selected that is within the products allowable kineticenergy limit.In the case that the kinetic energy value exceeds the specification usean external method of absorbing the energy e.g. a shock absorber, ifthere are still concerns, please contact SMC.Do not stop or hold the product at the midpoint by keeping air pressurein the product, this is not an acceptable use of the product.If the product is used at low speed below the specified speedadjustment range, it can introduce problems such as the stick-slip2.2 Production Batch Code:The batch code printed on the label indicates the month and the year ofproduction as per the following table;2.3 Special Conditions of Use:Products are suitable for sub-divisions IIC.Products are suitable for Zones 1 and 2 only.2.3.1 Temperature Marking:2.3.1.1 Standard Product:In the normal ambient temperature range (+5°C to +40°C) the productis rated to temperature class T5.In the special ambient temperature range (+40°C to +60°C) the productis rated to temperature class T4.3 Installation3.1 InstallationWarningDo not install the product unless the safety instructions have been readand understood.Do not twist or bend the cylinder or mount the product when subject totension.Do not use in an application where the product is stopped mid-stroke,via an external stop.Do not use where cylinders are being synchronised to move a singleload.For direct mounting, use standard hexagon socket head cap screws3.1.1 Direct Loading to the ShaftAlthough applying static loads as shown in the table below areallowable, it is recommended that they are not applied directly to theIn order to improve operating conditions, it is recommended that aflexible couple shall be used to avoid the direct loading on the shaft.3.1.2 Axis Alignment on Extended ShaftsWhen the rotary actuator is used with an extended shaft, ensure thatthe axis centres of the rotary actuator and its counterpart are aligned.If they are off-centred, the load factor becomes large and an excessivebending moment may be applied to the shaft. In such a condition, theassembly may not perform a stable operation and the shaft may bedamaged, in which case it is recommended to use a flexible fitting.3.2 EnvironmentWarningDo not use in an environment where corrosive gases, chemicals, saltwater or steam are present.Do not use in an explosive atmosphere except within the specifiedrating.Do not expose to direct sunlight. Use a suitable protective cover.Do not install in a location subject to vibration or impact in excess ofthe product’s specifications.Do not mount in a location exposed to radiant heat that would result intemperatures in excess of the product’s specifications.Do not use in a place subject to heavy vibration and/or shock.Do not use in wet environments, where water can remove the presenceof the lubrication.Do not use in case of heavy dusty environments where dust canpenetrate into the cylinder and dry the grease.Do not allow dust layers to build up on the cylinder surface and insulatethe product.3.3 PipingCautionBefore connecting piping make sure to clean up chips, cutting oil, dustetc.When installing piping or fittings, ensure sealant material does notenter inside the port. When using seal tape, leave 1 thread exposedon the end of the pipe/fitting.Tighten fittings to the specified tightening torque.Model Port Size Model Port SizeSize 10 & 15 M3 x 0.5Size20,30&40M5 x 0.8The axis rotates clockwise when Port A is pressurised.The rotary actuator port is equipped with a fixed size orifice. Do notenlarge the hole. Enlarging the hole will increase the operation speedof the actuator and the consequent impact at the end of each strokecould lead to the actuator failure.ORIGINAL INSTRUCTIONSBody Axial3.4 LubricationCautionSMC products have been lubricated for life at manufacture, and do not require lubrication in service.If a lubricant is used in the system, refer to catalogue for details.3.5 Basic CircuitPlugging one of the ports on the actuator is considered a non-intended use, and could relate to an increase in maximum surface temperature above what the product specification declares.3.6 Electrical ConnectionThe product should be grounded by the piston rod and the body in order to create an electrically conductive path to the system/application. Ground the product in accordance with applicable regulations. Do not pass an electrical current through the product.4 SettingsRefer to the standard product catalogue for general setup precautions.5 How to OrderRefer to catalogue for ‘How to Order’.6 Outline DimensionsRefer to catalogue for outline dimensions. 7 Maintenance7.1 General maintenanceCautionNot following proper maintenance procedures could cause the product to malfunction and lead to equipment damage.If handled improperly, compressed air can be dangerous.Maintenance of pneumatic systems should be performed only by qualified personnel.Before performing maintenance, turn off the power supply and be sure to cut off the supply pressure. Confirm that the air is released to atmosphere.After installation and maintenance, apply operating pressure and power to the equipment and perform appropriate functional and leakage tests to make sure the equipment is installed correctly.If any electrical connections are disturbed during maintenance, ensure they are reconnected correctly and safety checks are carried out as required to ensure continued compliance with applicable national regulations.Do not make any modification to the product.Do not disassemble the product, unless required by installation or maintenance instructions.Do not use a product which looks or contains damage, this will invalidate the certification. If damage is seen, please replace the product immediately.Periodically check the product for any damage or rust appearing. This could result in an increase in friction and lead to dangerous conditions. Replace the whole actuator if any of these conditions appear.8.1 Limited warranty and disclaimer/compliance requirements Refer to Handling Precautions for SMC Products.8.2 Obligations of the end-userEnsure the product is used within the specification outlined.Ensure that the maintenance periods are suitable for the application. Ensure any cleaning processes to remove dust layers are made with the atmosphere in mind (e.g. using a damp cloth to avoid static build up).Ensure that the application does not introduce additional hazards by mounting, loading, impacts or other methods.Ensure that there is sufficient ventilation and air circulation around the product.If the product is subject to direct heat sources in the application, they should be shielded so that the actuator temperature stays within the stated operating range.DangerDo not exceed any of the specifications listed in Section 2 of this document as this will be deemed improper use.Air equipment has an air leakage during operation within certain limits. Do not use this equipment when the air itself introduces additional hazards and could lead to an explosion.Use only Ex certified auto switches. These should be ordered separately.Do not use this product in the presence of strong magnetic fields that could generate a surface temperature higher than the product specification.Avoid applications where the shaft and the adjoining part in the application can create a possible ignition source.Do not install or use these actuators where there is the possibility for the shaft and adjoining parts to impact foreign objects.In the event of damage or failure of any parts located in the vicinity where this product has been installed, it is the responsibility of the user to determine whether or not this has compromised the safety and condition of this product and/or the application.External impact on the cylinder body could result in a spark and/or cylinder damage. Avoid any application where foreign objects can hit or impact the cylinder. In such situations the application should install a suitable guard to prevent this occurrence.Do not use this equipment where vibration could lead to failure.9 Product DisposalThis product shall not be disposed of as municipal waste. Check your local regulations and guidelines to dispose this product correctly, in order to reduce the impact on human health and the environment.10 ContactsRefer to or www.smc.eu for your local distributor/importer.URL : https:// (Global) https:// www.smc.eu (Europe) SMC Corporation, 4-14-1, Sotokanda, Chiyoda-ku, Tokyo 101-0021, JapanSpecifications are subject to change without prior notice from the manufacturer. © 2022 SMC Corporation All Rights Reserved. Template DKP50047-F-085M。
纳普尔顿冷暖机系列产品说明书

Maximum Elevation (ft/m)
Refrigeration Pipe Diameter (Liquid side / Gas Side) (in)
INDOOR DIMENSIONS Width (in)
33ft./10m 66ft./20m 66ft./20m 1/4 / 1/2 1/4 / 1/2 3/8 / 5/8 NHAS-12 NHAS-18 NHAS-24
17 9.5 9.5
HIGHLIGHTS • Up to 19 SEER, 10 HSPF • Remote controlled • LED light display • Auto-Restart for power outages • Self diagnostic controls
HSPF5
-
LIMIT-ED WARRANTY-
Standard Remote Self Diagnostic Controls
•
10•
YEAR
•
•
20 HELAIMTIT•EEDXWCAHRARANNGTY•ER
YEAR YEAR
YEAR
YEAR YEAR
Ductless - 23 SEER only
PROFIBUS DP 从机通信模块 DVPPF02-SL 操作手册说明书

DVPPF02-SLPROFIBUS DP Slave Communication Module Operation ManualDVP-0155320-01Warning3 This operation manual provides introduction on the functions, specifications, installation, basic operation,settings and network protocol for DVPPF02-SL.3 This is an OPEN TYPE device and therefore should be installed in an enclosure free of airborne dust,humidity, electric shock and vibration. The enclosure should prevent non-maintenance staff fromoperating the device (e.g. key or specific tools are required to open the enclosure) in case danger and damage on the device may occur. DO NOT touch any terminal when the power is switched on.3 Please read this operation manual thoroughly and follow the instructions in case damages on the device or injuries on the operation staff occur.Table of Content1Introduction to DVPPF02-SL (2)1.1Features (2)2Product Profile and Outline (2)3Installation (4)3.1Dimensions (4)3.2Connecting DVPPF02-SL to PLC MPU (4)3.3Installing DVPPF02-SL and PLC MPU on DIN Rail (4)3.4PIN Definition for PROFIBUS DP Port (5)3.5Connecting to PROFIBUS DP Port (5)3.6Address Switch (5)4Establishing PROFIBUS DP Network by DVPPF02-SL (6)5Transmission Distance and Baudrate (6)6GSD File (7)7Mapping Areas and Status Registers (7)8Configuring DVPPF02-SL (8)8.1Configuring DVPPF02-SL (8)8.2I/O Configuration for DVPPF02-SL (8)9LED Indicators and Trouble-shooting (9)10Application Example (10)1 Introduction to DVPPF02-SL1. Thank you for choosing Delta DVPPF02-SL PROFIBUS DP slave communication module. To ensurecorrect installation and operation of the product, please read this operation manual carefully before using it.2. This operation manual only provides introductory information on DVPPF02-SL. For more detailedinformation on the PROFIBUS DP protocol, please refer to relevant references or literatures.3. DVPPF02-SL is a PROFIBUS DP slave communication module, used for connecting the DeltaDVP-SV and DVP-SX2 series PLC to the PROFIBUS DP network. DVPPF02-SL is a left-sideextension module, and no external power supply is required when using it. The power is supplied by the PLC MPU (main processing unit).1.1 Featuresz Supports the loop data transmission between the PROFIBUS DP master and many slaves.z Auto-detects baudrate; supports max. 12M bps.z Self-diagnosisz A PLC MPU is extendable to max. 8 modules on its left hand side.z Supports max. 100 words of I/O output and 100 words of I/O input.2 Product Profile and Outline2.1 Product Profiles1 Interface for left-side I/O module2 I/O module fastening clip3 I/O module positioning hole4 POWER indicator5 NET indicator6 PROFIBUS DP port7 DIN rail clip 8 Digital display 9 Address switch10 Positioning clip 11 Nameplate 12I/O module interface(35mm)railDIN13DVP-PLC Operation Manual 22.2 SpecificationsPROFIBUS DP PortInterface DB9connector Transmission method High-speed RS-485Transmission cable Shielded twisted pair cableElectrical isolation 500 VDCCommunicationData type Cyclic data exchangeModule name DVPPF02-SLGSD document DELA0AFE.GSDProduct ID 0AFESerial baudrate supported (auto-detection) 9.6k, 19.2k, 93.75k, 187.5k, 500k, 1.5M, 3M, 6M, 12M bps (bits/second)Electrical SpecificationPower supply voltage 24 VDCInsulation voltage 500 VDCPower consumption 2 WWeight 115g EnvironmentInterference immunity ESD (IEC 61800-5-1, IEC 6100-4-2)EFT (IEC 61800-5-1, IEC 6100-4-4)Surge Teat (IEC 61800-5-1, IEC 6100-4-5)Conducted Susceptibility Test (IEC 61800-5-1, IEC 6100-4-6)Storage/operation Operation: -10 to 50°C (temperature), 90% (humidity) Storage: -25 to 70°C (temperature), 95% (humidity)Shock/vibration immunity International standards: IEC 61800-5-1, IEC 60068-2-6/IEC 61800-5-1, IEC 60068-2-273 Installation3.1 DimensionsUnit: mm3.2 Connecting DVPPF02-SL to PLC MPUz Open the fastening ports for the I/O module on the left hand side of the PLC MPU and insert the DVPPF02-SL alongside the fastening clips, as c.z Press the clips to make sure the connection is tight, as d.3.3 Installing DVPPF02-SL and PLC MPU on DIN Railz Use 35mm DIN rail.z Open the DIN rail clips on DVPPF02-SL and the PLC MPU. Insert DVPPF02-SL and the PLC MPU onto the DIN rail.z Clip up the DIN rail clip on DVPPF02-SL and the PLC MPU to fix them on the DIN rail.DVP-PLC Operation Manual 43.4 PIN Definition for PROFIBUS DP PortPINNameDefinition1 -- N/C2 -- N/C3 RxD/TxD-P Sending/receiving data P (B)4 --N/C5 DGND Data reference potential (C)6 VP Power voltage - positive7 -- N/C8RxD/TxD-NSending/receiving data N (A) 9 --N/C3.5 Connecting to PROFIBUS DP PortInsert the PROFIBUS DP bus connector into the PROFIBUS DP port on DVPF02-SL. Screw it tight to ensure DVPF02-SL and the PROFIBUS DP bus are properly connected.3.6 Address SwitchThe address switches on DVPPF02-SL are used for setting up the node address of DVPPF02-SL on the PROFIBUS DP network. The switches are two rotary switches x160 and x161. Range for each switch: 0 ~ F. See the table below for the setup range for the switches.DVP-PLC Operation Manual6Address DefinitionH’1 ~ H’7D Valid PROFIBUS address H’0 or H’7E ~ H’FFInvalid PROFIBUS addressExample: If you are to set the node address of DVPPF02-SL to 26 (decimal), simply switch x161 to 1 and x160to A. 26 (decimal) = 1A (hex) = 1×161 + A×160. Notes:z Set up the address of DVPPF02-SL when the power is off. Re-power the module after youfinish setting up the address.z Changing the setting of address when DVPPF02-SL is operating is regarded invalid. zUse slotted screwdriver carefully to adjust the address in case you scrape the module.4Establishing PROFIBUS DP Network by DVPPF02-SLDVPPF02-SL is used for connecting the DVP-SV and DVP-SX2 series PLC to the PROFIBUS DP network.5 Transmission Distance and BaudrateThe baudrate for PROFIBUS DP communication ranges from 9.6k to12M bits per second (bps). The length of cable is determined by the transmission speed. The transmission distance can be from 100 to 1,200 meters. See the table below for the baudrates DVPPF02-SL support and their corresponding transmission distance.Baudrate (bps) 9.6k 19.2k 93.75k187.5k500k 1.5M 3M 6M 12MDistance (m) 1,200 1,200 1,2001,000400 200 100 100 100 6 GSDFileGSD file is a text file, used for identify the PROFIBUS DP device (master or slave). A GSD file includes data required for configuring a slave on the PROFIBUS DP master, information on the supplier,baudrates supported and applicable I/O. When using DVPPF02-SL, first import the GSD file to thesoftware for configuring the PROFIBUS DP master, then DVPPF02-SL and items to be configured will be displayed in the software. You can download the GSD file for DVPPF02-SL from Delta’s website: /7 Mapping Areas and Status RegistersThe PLC MPU is extendable to 8 DVPPF02-SL modules on its left hand side. The first module is atlocation 1. See the table below for the I/O mapping and status registers of DVPPF02-SL at different locations.Explanations on status registers for DVPPF02-SL:High byte Low byteCode Definition Code Definition0 Normal status 0 No error1 Initializing F1 DVPPF02-SL is initializing.F0 The node address of DVPPF02-SL is out of range.F2 Error in low voltage detectionF3 DVPPF02-SL enters factory test mode.F4 DVPPF02-SL is disconnected from the master.2 ErrorF5 Error in parameterDVP-PLC Operation Manual8High byteLow byteCodeDefinitionCodeDefinitionF7 Hardware error2 ErrorF9 Configuration error8 Configuring DVPPF02-SL8.1 Configuring DVPPF02-SLWhen you configure DVPPF02-SL in the software for PROFIBUS DP master and DVPPF02-SL is offline from the PROFIBUS DP master, you can select to “clear I/O data” or “hold I/O data”, as shown below.Figure 8.1-1ParameterValue DefinitionHold I/O dataAfter DVPPF02-SL goes offline from the master, the I/O data will remain the same as they were before being offline.Los comm. with masterClear I/O dataAfter DVPPF02-SL goes offline from the master, the output data will be reset to 0 and input data remain the same.8.2 I/O Configuration for DVPPF02-SLWhen DVPPF02-SL is configured in the software for the PROFIBUS DP master, it offers many choices for configuration, satisfying all kinds of data length demands. See the table below. The output configuration means the data is sent from the master to the salve; the input configuration means from the salve to the master.Output configuration Input configuration I/O configuration1 word out 1 word out 1 word out 1 word in2 words out 2 words out 2 words out 1 word in4 words out 4 words out 4 words out 1 word in8 words out 8 words out 8 words out 1 word in16 words out 16 words out 16 words out 1 word in32 words out 32 words out 32 words out 1 word in64 words out 64 words out 64 words out 1 word in 9 LED Indicators and Trouble-shootingz POWER LEDThe POWER LED displays the status of the power supply for DVPPF02-SL.LED status Indication How to correctGreen light on The power supply is normal.--Off No power supply 1. Check if the connection between DVPPF02-SLand the PLC MPU is normal.2. Check if the power supply from the PLC MPUis normal.z NET LEDThe NET LED displays the communication status between DVPPF02-SL and the PROFIBU DP master.LED status Indication How to correctGreen light on A connection is established betweenthe master and slave.--Red light on DVPPF02-SL has notestablished aconnection with themaster.1. Check if DVPPF02-SL is connected with thePROFIBUS DP bus.2. Check if the communication cable betweenDVPPF02-SL and the PROFIBUS DP master iswell connected.3. Check if the actual address of DVPPF02-SL isconsistent with the address configured in thesoftware.4. Check if the GSD file is used correctly.z Digital DisplayThe digital display shows the status of DVPPF02-SL.Code Indication How to correct1 ~ 7D The node address ofDVPPF02-SL when it is operating normally.--F0 The node address ofDVPPF02-SL is out ofrange.Set the node address of DVPPF02-SL to be 1 to125.Code Indication How to correct F1 DVPPF02-SL is initializing. --F2 Error in low voltagedetection1. Check if the connection between DVPPF02-SLand the PLC MPU is normal.2. Check if the power supply from the PLC MPU isnormal.F3 DVPPF02-SL enters factorytest mode.Write 0 into D6350 in the PLC MPU.F4 DVPPF02-SL isdisconnected from themaster.Check if the communication cable betweenDVPPF02-SL and the PROFIBUS DP master iswell connected.F5 Error in parameter Check if the GSD file is used correctly.F7 Hardware error Send the module back to factory for repair. F9 Configuration error Check if the GSD file is used correctly.80 The PLC MPU connectedto DVPPF02-SL is in STOPstatus.Switch the PLC MPU to RUN.Operation of Digital Display1. When DVPPF02-SL is in normal operation status and the PLC MPU is in RUN status, the digitaldisplay will only show its node address.2. When DVPPF02-SL is in normal operation status and the PLC MPU is in STOP status, the digitaldisplay will how its node address and the STOP status code alternately.3. When DVPPF02-SL is initializing or in error status and the PLC MPU is in RUN status, the digitaldisplay will show its node address, initialization code or error code alternately.4. When DVPPF02-SL is initializing or in error status and the PLC MPU is in STOP status, the digitaldisplay will show its node address, initialization or error code and STOP status code alternately.10 Application ExampleApplication:A data exchange between Siemens S7-300 PLC and DVPPF02-SL through the PROFIBUS DP network Connecting DVPPF02-SL to the PROFIBUS DP Network:1. The Siemens S7-300 PLC is the PROFIBUS DP master and DVPPF02-SL the slave. See Figure10-1 for the network structure.DVP-PLC Operation Manual 10Figure 10-12. Set the PROFIBUS address of DVPPF02-SL to “1”.3. Connect a DVP-SV PLC on the right side of DVPPF02-SL and check if the connection is proper. Configuring DVPPF02-SL on the PROFIBUS DP Network by Software:z Creating a new project using the software wizard1. Open the software SIMATIC Manager, as Figure 10-2.Figure 10-22. Select “File” => “New Project Wizard”, as Figure 10-3.DVP-PLC Operation Manual12Figure 10-33.Click “Next” in the wizard, as Figure 10-4.Figure 10-44. Select a CPU type for the S7-300 model we are using and click “Next”, as Figure 10-5.5. Select a language for selected blocks and click “Next”, as Figure 10-6.6. Enter the project name and click “Finish”, as Figure 10-7.DVP-PLC Operation Manual14Figure 10-77.A new window for the newly created project then appears, as Figure 10-8.Figure 10-8z Adding PROFIBUS DP bus1. Select “SIMATIC 300 Station” in the new project window and double click “Hardware” in theright-hand side window. A new window “HW-Config” will then appear.Figure 10-92. In the HW Config window, double click “DP” in the (0)UR window, as Figure 10-10, and a new dialogbox will appear.Figure 10-103. In the new dialog box, click “Properties” to open another dialog box, as Figure 10-11.DVP-PLC Operation Manual16Figure 10-114. In this dialog box, select an address for the master and click “New” to open another dialog box, asFigure 10-12.Figure 10-125. In this dialog box, select transmission rate and profile for the bus and click “OK”, as Figure 10-13.Figure 10-136. In this successive dialog box, confirm the address and transmission rate of the PROFIBUS DP busand click “OK”.Figure 10-147. In this successive dialog box, confirm all information for the DP bus and click “OK”, as Figure 10-15.DVP-PLC Operation Manual18Figure 10-158. After all the parameters are set, a PROFIBUS DP bus will be created after the UR window, as Figure10-16.Figure 10-16z Adding GSD file1. In the HW Config window, select “Options” => “Install GSD File”, as Figure 10-17.10-17Figure2. Find the location to save the GSD file, select the GSD file to be installed and click “Install”, as Figure10-18.Figure 10-183. After the GSD file is added, we can find DVPPF02-SL in the right-hand side window, as Figure 10-19.DVPPF02-SL is the new module created.DVP-PLC Operation Manual20Figure 10-19z Adding the slave DVPPF02-SL and setting up parameters1. Select the PROFIBUS DP bus and double click the DVPPF02-SL in the right-hand side, as Figure10-20, to open a dialog box.Figure 10-202. In this dialog box, select an address for DVPPF00-SL, as Figure 10-21. The address has to beconsistent with the address set by the address switch on DVPPF02-SL. Next, click “OK”.Figure 10-213. DVPPF02-SL is now added to the PROFIBUS DP bus, as Figure 10-22.Figure 10-224. Select Slot 0 and double click “1 Word Out” on the right-hand side window, as Figure 10-23.DVP-PLC Operation Manual22Figure 10-235.Configure “1 Word Out” to Slot 0, as Figure 10-24.Figure 10-246. Configure other slots as the way Slot 0 is configured, as Figure 10-25. Finish configuring Slot 0 toSlot 2.Figure 10-257. After DVPPF02-SL is configured, double click the slave DVPPF02-SL on the PROFIBUS DP bus inFigure 10-25, and a dialog box will appear, as Figure 10-26. See 8.1 for definitions of the parameters in the dialog box.Figure 10-268. Download the configured parameters. After the master establishes a connection with DVPPF02-SL,the NET LED on DVPPF02-SL will be constantly on in green color.Data Mapping:DVP-PLC Operation Manual24Figure 10-30The data mapping for the parameters shown in Figure 10-30 is illustrated in Table 10-1.Table 10-1Program Example:The program for masterz Write the program for master in OB1.z When M0.0 is ON, write 1000 into PQW256 and 2000 into PQW258. The master will then send thedata in PQW256 and PQW258 to D6000 and D6001 in the slave through the PROFIBUS DP bus.z When M0.0 is ON, write the data in PIW256 to MW10 and data in PIW258 to MW12. The data inPIW256 and PIW258 are sent from D6250 and D6251 in the slave to the master through thePROFIBUS DP bus.The program for slavez Compile the program by Delta WPLSoft software. See the software help document for details.z When M0 is ON, write 3000 into D6250 and 4000 into D6251. DVPPF02-SL will send the data in D6250 and D6251 to PIW256 and PIW258 in the master through the PROFIBUS DP bus.z When M1 is ON, write the value in D6000 to D10 and the value in D6001 to D11. The data in D6000 and D6001 are sent from the master to DVPPF02-SL through the PROFIBUS DP bus.MEMODVP-PLC Operation Manual 26。
FDR-2说明书(新板)
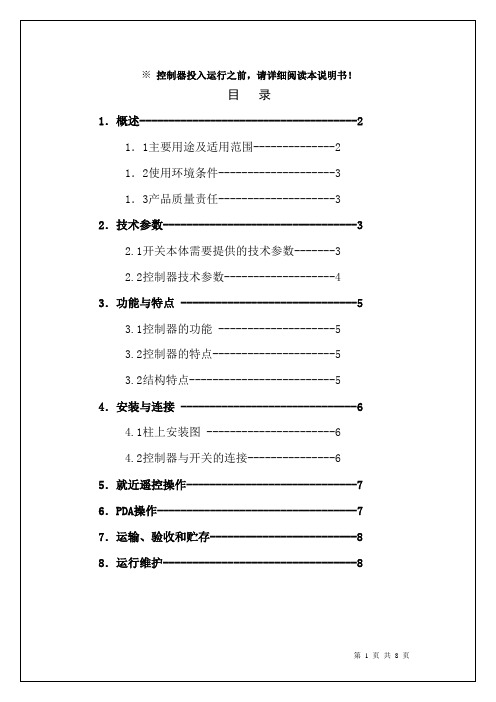
图1:用户分界开关控制器外形图
说明:CTA为A相CT;CTC为C相CT;CTZ为零序CT;
TA航空插头接线图;FXQ为分闸线圈;HXQ为合闸线圈
.就近遥控操作方法:
键:解锁键;A键:分闸键;D键:合闸键;
遥控操作时,先按B键1秒,3秒内再按功能键;
如:分闸操作时,先按下B键1秒后,3秒内再按A键;
合闸操作时,先按下B键1秒后,3秒内再按D键;
智能掌上机功能描述
搜索设备
选择‘搜索设备’选项,PDA会搜索处于通信范围内(空旷距离小于150米)控制器,如搜索范围内有控制器,选择对应控制器的设备号,进入显示有选中的设备号的主界
面窗口。
查询状态
选择‘查询状态’,显示结果为当前控制器的实时状态值。
.查询记录
选择‘查询记录’,显示过去发生过的最近发生的30条故障记录;。
ASB680的DP2 Profibus 说明书

DP2 Profibus说明书DP2 Profibus说明书目 录前言 (2)第一章 安装与接线 (3)1.1扩展卡硬件布局 (3)1.2 拨码开关说明 (4)1.3接口说明 (5)第二章 通讯参数 (7)3.1 变频器通讯卡类型设置 (7)3.2 通讯控制相关参数 (7)3.3 通讯监控相关参数 (8)第三章 通讯实例 (10)3.1 DP卡与Profibus的接线 (10)3.2 DP卡与Profibus主站通讯配置说明 (11)3.2.1 数据传送格式 (11)3.2.2 PKW数据描述 (12)3.2.3 PZD区数据描述 (14)3.3 在STEP7 V5.4中用S7-300主站配置从站 (16)3.4 在TIA Portal V13中用S7-1200配置从站 (21)3.5 操作变频器从站的周期读写 (30)3.6 操作变频器从站的非周期读写 (31)3.7 诊断 (33)第四章 故障描述和处理 (35)4.1 DP卡灯状态和处理 (35)4.2 GSD安装失败的处理方法 (36)4.3 常见故障处理方法 (38)版本变更记录 (40)DP2 Profibus 说明书前言前言本DP2卡是Profibus-DP现场总线适配卡,符合国际通用的Profibus现场总线标准,可提高变频器上通讯效率,实现组网功能,使变频器成为现场总线的从站,接受现场总线主站控制。
该卡不仅可以实现Profibus-DP通讯,还提供了CANlink通讯接口,实现CANlink通讯功能。
本手册所述内容适用的DP2卡软件为1.09或以上版本(卡安装好并上电后,可通过参数查询,对应的查询参数为U0-67)。
本DP2卡可以通过设置拨码切换为DP1,与原变频器进行通讯,使用DP1时还需使用原GSD文件(PFS2.GSD)和设置方法。
本手册以DP2为主进行介绍,如使用DP1功能,除了拨码定义和变频器Fd-00设置外(详见本手册“拨码开关说明”),其它请参考《Profibus说明书》。
RC-2SPDT-A26 双频带电子切换开关说明书

REV. CPRODUCT OVERVIEWMini-Circuits’ RC-2SPDT-A26 comprises of two independently controlled, electro-mechanical SPDT switches. Each switch operates over an extremely wide bandwidth, from DC to 26.5 GHz with high isolation and low insertion loss. The absorptive switches are of a failsafe and break-before-make-configuration, with a lifetime of 2 million switching cycles per switch when used within the noted specifications.The switch box is constructed in a compact, rugged metal case (4.5 x 6.0 x 2.25”) with all SMA (f) RF connectors on the front panel. The switches are controlled via USB or Ethernet, allowing control directly from a PC, or remotely over a network. Full software support is provided, including our user-friendly GUI application for Windows and a full API with programming instructions for Windows and Linux environments (both 32-bit and 64-bit systems).THE BIG DEALy Dual independent mechanical SPDT switchesy Excellent performance to 26.5 GHz y 30W power rating (cold switching)APPLICATIONSy 5G node / device testing y Automated test equipmentyFail-safe / redundancy switchingCASE STYLE: LM1849SOFTWARE PACKAGESee our website for RoHS Compliance methodologies and qualificationsOUTLINE DRAWING (LM1849)A B C D E F G H J K L wt 6.00 4.50 2.250.440 1.285 1.500.28 1.6700.375 6.75 3.500grams 152.4114.357.211.1832.6438.17.142.429.53171.588.9960SWITCHING CONFIGURATION (PER SWITCH): y Fail-SafeyAbsorptive (internal terminations on ports J1-J2)STATE 1STATE 2OUTLINE DIMENSIONS (Inches )mmTYPICAL PERFORMANCE DATA / CURVESSOFTWARE SPECIFICATIONSSOFTWARE & DOCUMENTATION DOWNLOAD:y Mini-Circuits’ full software and support package including user guide, Windows GUI, DLL files, programming manual and examples can be downloaded free of charge from: https:///softwaredownload/rfswitchcontroller.html y Please contact ******************************for supportETHERNET SUPPORT:y Simple ASCII / SCPI command set for attenuator controly Communication via HTTP or T elnety Supported by most common programming environmentsUSB SUPPORT (WINDOWS):y ActiveX COM DLL file for creation of 32-bit programs library DLL file for creation of 32 / 64-bit programsy Supported by most common programming environments (refer to application note AN-49-001 for summary of suported environments)USB SUPPORT (LINUX):y Direct USB programming using a series of USB interrupt codesFull programming instructions and examples available for a wide range of programming environments / languages.y View and set switch states at the click of a buttony Configure and run timed switching sequences y Set start-up switch statey Configure Ethernet IP settingsGRAPHICAL USER INTERFACE (GUI) FOR WINDOWS - KEY FEATURES y Connect via USB or Ethernety Run GUI in “demo mode” to evaluate software without a hardware connectionNOTESA.Performance and quality attributes and conditions not expressly stated in this specification document are intended to be excluded and do not form a part of this specification document.B.Electrical specifications and performance data contained in this specification document are based on Mini-Circuit’s applicable established test performance criteria and measurement instructions.C.The parts covered by this specification document are subject to Mini-Circuits standard limited warranty and terms and conditions (collectively, “Standard T erms”); Purchasers of this part are entitled to the rightsand benefits contained therein. For a full statement of the standard. T erms and the exclusive rights and remedies thereunder, please visit Mini-Circuits’ website at /MCLStore/terms.jspORDERING INFORMATIONRefer to Mini-Circuits’ website for pricing and availability information:https:///WebStore/dashboard.html?model=RC-2SPDT-A265. If you need a Power cord for a country not listed please contactUSB-CBL-AB-3+ 2.7 ft (0.8 m) USB Cable: USB type A(Male) to USB type B(Male)USB-CBL-AB-7+ 6.8 ft (2.1 m) USB Cable: USB type A(Male) to USB type B(Male) USB-CBL-AB-11+11 ft (3.4 m) USB Cable: USB type A(Male) to USB type B(Male)CBL-RJ45-MM-5+ 5 ft (1.5 m) Ethernet cable: RJ45(Male) to RJ45(Male) Cat 5E cable BKT-272-08+Bracket (One set of 2 each)OPTIONAL ACCESSORIES。
德尔堡 2 型标准通气器 使用说明书

• Start ventilation by height • NIV therapy• Resuscitation (CPR) with IPPV • Resuscitation (CPR) with CCSV • Anesthesia induction (RSI)MEDUMAT Standard2Step-by-step instructionsImportant: This document does not replace the instructions for use. Complete information can be found in the instructionsfor use.Operating steps12Switch on ventilator Select “New patient”34Select patient height and gender Select “next”56Start ventilation Select the ventilation mode and checkthe displayed ventilation parametersUse presets and work according to guidelinesBy using the setting option of the Vt/kg body weight (BW) 4-10 ml/kg BW to be applied, you will be working according to guidelines and determining the calculated tidal volume for volume-controlled ventilation.The ideal body weight and thus also the tidal volume to be applied are calculated differently for male and female patients. The following formulas are used for this purpose:iGajic, O. et al. Ventilator-associated lung injury in patients without acute lung injury at the onsetof mechanical ventilation. Critical care medicine, 2004, no. 32, p. 1817-1824.iiDeakin, C. D. et al. Advanced life support Section 4 of the European Resuscitation Council Guidelines on Resuscitation 2010. Emergency + Rescue Medicine, 2010, No. 7, p. 578.iiiDevine, Ben J. Gentamicin therapy. The Annals of Pharmacotherapy.1974, 8. year, no. 11, p. 650-655With a male patient 185 cm tall and a setting of 6 ml/kg BW, this results in thefollowing tidal volume:The tidal volume results accordingly: Vt = 80 kg x 6 ml/kg KG = 480 ml= 79.51 kg ~ 80 kgIBW (in kg) = 50 + 2.3 x1852.54- 60IBW female (in kg) = 45 + 2.3 x Height in cm2.54iii-60IBW male (in kg) = 50 + 2.3 xHeight in cm2.54iii-60Start faster and ventilate more preciselyFrom now on you don't have to think long about which tidal volume (Vt) is best for your patient. With MEDUMAT Standard 2, you can now initiate ventilation even more precisely and quickly. By entering the patient’s height and gender, your ventilator automatically calculates all ventilation parameters for the ideal body weight (IBW). The IBW serves as an important indicator for setting the ventilation parameters i . MEDUMAT Standard 2 enables you to start ventilation more quickly and far more precisely – giving you more time for all the other important tasks.Start ventilation by heightNIV therapy1Select “New patient” in the start menu.2Set the patient’s height and gender or select the appropriate patient group: Adult, Child, Infant.3Select the desired CPAP therapy using the navigation button: PEEP , pMax, ΔpASB. After adjusting the values, begin the ventilation via “start”.5Now connect the patient to MEDUMAT Standard². It is possible to adjust the values using the navigation button while the ventilation is running. You can find other ventilation parameters in the user menu on the right navigation button. If it is necessary to switch the ventilation mode, this is done using the “user menu” function button on the right side.6Select one of the following ventilation modes: CPAP* or CPAP + ASB (if available).*pure CPAP is the ventilation form CPAP + ASB with a ΔpASB of 0 mbar4Modified by Prof. Dr. med. Thoralf KernerLogistical requirementsOxygen supply: at least a 2-l bottle, filled .......................................................Check Emergency medical team familiar with NIV .....................................................CheckClinical requirementsAlert, cooperative (GCS > 12) ........................................................................Check breathing spontaneously ................................................................................Check If applicable, light sedation of agitated patients e.g. morphine (5-10 mg i.v. titrated) or a short-acting benzodiazepineIndicationsDyspnea .........................................................................................................Check Respiratory rate > 25/min (count!) .................................................................Check SpO 2 < 90 % despite O 2 administration ..........................................................CheckContraindicationsAbsolute contraindications: ............................................................................Check Absence of spontaneous respiration, gasping, airway obstruction, gastrointestinal bleeding or ileusRelative contraindications: ..............................................................................Check Coma, massive agitation, hemodynamic instability, severe hypoxemia(SpO 2 < 75% despite O 2), problems with airway access, status post gastrointestinal surgeryPulmonary edemaPrimary device settingsVentilation mode: ............................................................................................CPAP PEEP (according to comfort and oxygenation): ..............................5 / 10 / (12) mbar FiO 2: .............................................................Initial 100 %, then AirMix if necessary Target and success criteriaTarget SpO 2: > 90 % ......................................................................................Check Decrease in dyspnea ......................................................................................Check Falling respiratory and heart rate ....................................................................Check If applicable, improved vigilance .....................................................................CheckNIV sequence: Adjust device, place mask on patient's face (explain measure!), connect mask to breathing circuit while device is running. Aim: Synchronization of patient and deviceSOP(Standard Operating Procedure)Non-invasive ventilation (NIV) by the EMSEscalation levelsIn the event of imminent respiratory muscle fatigue, set pressure support (ASB). Immediate intubation in the absence of clinical improvement or the occurrence of contraindications!Caution• Continuous clinical observation and close patient contact• No delay in pharmacological therapy or necessary intubation• Prepared for intubation at any time• Timely advance information to the receiving hospitalExacerbated COPDPrimary device settingsVentilation mode: .................................................................................CPAP + ASB PEEP: .........................................................................................................3/6 mbar ∆pASB (according to comfort and oxygenation): increase slowly, peak pressure max. 25 mbarInspiration trigger: as low as ........................................................................possible Pressure ramp: .................................................................................................steep : .......................................................................................................as required FiO2Target and success criteria: > 85 % ......................................................................................Check Target SpO2Decrease in dyspnea ......................................................................................Check Decrease respiratory and heart rate ................................................................Check If applicable, improved vigilance .....................................................................CheckEscalation levelsIn the event of imminent respiratory muscle fatigue, if available, set ventilation mode BiLevel + ASB (e.g. PEEP: 5 mbar, pInsp: 20 mbar).Immediate intubation in the absence of clinical improvement or the occurrence of contraindications!Caution• Continuous clinical observation and close patient contact• No delay in pharmacological therapy or necessary intubation• Prepared for intubation at any time• Timely advance information to the receiving hospitalInspiratory triggerThe inspiratory trigger triggers a pressure support or a mechanical breath as soonas inhalation effort is detected.Trigger level Corresponding unit value Level 1 (sensitive)Approx. 3 l/min Level 2 (medium)Approx. 6 l/min Level 3 (insensitive)Approx. 10 l/minSetting the levels of the inspiration trigger:(If “3 levels” has been chosen as the trigger setting in the operator menu)1 l/min Very sensitive 5 l/min sensitive 10 l/min insensitive 15 l/min Very insensitiveTrigger sensitivity:1 l/min-15 l/minPressuresupport and the expiration triggerPressure support ΔpASBThe pressure support is always given as a value above PEEP . In addition to the set PEEP , a patient receives this as soon as the inspiration trigger has been detected.Example calculation:PEEP = 5 mbar, ΔpASB = 10 mbar inspiration pressure in the inhalation phase = 15 mbarTrigger level Corresponding unit value Level 1 (long)Approx. 10% Flow max Level 2 (medium)Approx. 35 % Flow max Level 3 (Short)Approx. 70 % Flow maxExpiratory triggerInitiate expiration as soon as the flow to the patient is only the set value (in %) with respect to the maximum flow. The length of the pressure support is set with the expiratory trigger.Trigger sensitivity: 5-80% of max. flow. In principle, the following applies: the smaller the % value, the longer the pressure support lasts.max Setting the levels of the expiration trigger:(If “3 levels” has been chosen as the trigger setting in the operator menu)Pressure ramp (pressure increase time)A pressure ramp (or the pressure increase time) defines the time in which the pressure increases from the PEEP to the inspiration pressure. This pressure increase time can be set by the shape of the ramp: flat, medium and steep.< 0.2 seconds:steepApprox. 0.2 seconds:mediumApprox. 0.4 seconds:flat Pressure ramps using the example of a BiLevel + ASB curvePmaxPinspResuscitation (CPR) with IPPV Press the CPR button and select the patient group.Check the ventilation parameters. In the ventilation phase of 30:2 or 15:2resuscitation, press the mask with the “Double C grip” over the patient’smouth and nose.Then hold down the MEDUtrigger keyuntil two mechanical breaths have been administered.123Following successful intubation, switch to continuous ventilation “CPR IPPV”. Check the ventilation parameters.During the cardiac rhythm analysis or defibrillation, select “pause” to pause the ventilation. • No movement artifacts • Reduction of thoracic impedance • No oxygen enrichment of ambient air Following successful defibrillation, if applicable, press “pause” again to restart the ventilation. The ventilation will start automatically after at most 50 seconds.Once ROSC is achieved, press the CPRkey again to exit the CPR mode. Thencheck the ventilation parameters andselect, if applicable, the Air Mix key tolower the FiO 2 to < 1.0. 456R esuscitationw ith C CSV Press the CPR button and select the patient groupCheck the ventilation parameters. In the ventilation phase of 30:2 or 15:2 resuscitation, press the mask with the “Double C grip” over the patient’s mouth and nose.Then hold down the MEDUtrigger key until two mechanical breaths have been administered.1 2 34Following successful intubation, switchto continuous ventilation “CPR CCSV”.5Perform chest compressions continu-ously. MEDUMAT Standard² will delivera mechanical breath synchronously toeach compression.You can use the frequency tachometershown above to determine the frequen-cy of the compressions.6If a chest compression device is broughtto the patient, this must be indicated viathe middle navigation button.With machine compressions the com-pression frequency alarm is deactivatedand the frequency tachometer turnsgray.The triggers are optimized by the deviceand the trigger level is automatically setto "3".In the absence of chest compressions, the hands-off time is displayed. When the alarm limit is reached, the device outputs a hands-off time alarm. If this is not answered with compressions, the device automatically switches to "CPRIPPV” ventilation.If chest compressions are detected again by MEDUMAT Standard² during "CPR IPPV”apnea ventilation, the de-vice automatically switches back to"CPR CCSV".If these two measures do not lead to success, CCSV is not applicable to this patient. Please switch to "CPR IPPV" via the right navigation button.78910If less or no compressions are detected by MEDUMAT Standard² despite cor-rectly performed compressions, please perform the following escalation steps:• Reduce the set trigger• Increase the set PEEPAdvanced Life Supporthttps://cprguidelines.eu/European Resuscitation Council Guidelines for Resuscitation 2015Monsieurs, Koenraad G.Khalifa, Gamal Eldin Abbas et al. Resuscitation , Volume 95 , 1 - 80 Copyright: © 2015 European Resuscitation Council. Published by Elsevier Ireland Ltd. All rights reserved.Interactive Simulation Operate MEDUMAT Standard² live on your computer with our free simulation software.You can find more information at:Anesthesia induction (RSI*)Switch on the deviceSelect “New patient” on the homescreen and set the patient’s heightand gender. Or select the appropriatepatient group: Adult, Child, InfantSelect “RSI” in the “mode” submenuMEDUMAT Standard² begins thetherapy in demand mode. In this mode,the spontaneously breathing patient ispre-oxygenated. The total RSI time andthe time since the last spontaneous breath are shown on the display.2134To check the tube position followingsuccessful intubation or as a fallbackposition for a difficult airway, switch tothe Manual mode.Check the ventilation parameters. Con-nect the patient hose system to thetube or press the mask with the “Dou-ble C grip” over the patient’s mouthand nose and trigger the mechanicalbreath with the MEDUtrigger.Following successful intubation, switchto continuous ventilation to ventilatethe patient in a controlled manner.The device switches to controlled IPPVor BiLevel + ASB ventilation dependingon availability and setting. Please checkthe ventilation parameters and adjust them if necessary.5678Excerpt from the S1 guideline "Prehospital Emergency Anaesthesia in Adults" of the DGAI Indications for prehospital emergency anaesthesia• Acute respiratory insufficiency (hypoxia and/or respiratory rate*< 6 or > 29/min) and contraindications for or failure of non-invasive ventilation • Loss of consciousness/neurological deficit with risk of aspirationMultiple trauma/severe trauma withi) hemodynamic instability, systolic BP < 90 mmHg orii) hypoxia with SpO2 < 90% despite = 2 l/min O2administration oriii) traumatic brain injury with GCS < 9* in the presence of not rapidly reversible causes2Rapid Sequence Induction (RSI)• If applicable, remove the cervical spine immobilization and beginmanual in-line stabilization• Announcement of the Anaesthesia medication with activesubstance and dosage, step-by-step application• Wait for loss of consciousness and relaxation effect• Airway management without intermediate ventilation in normoxic patients*• Tube position check (capnography, auscultation, insertion depth)• If applicable, stop manual in-line stabilization and close thecervical spine immobilization brace again* In individual cases, despite the increased risk of aspiration, intermediate ventilation may benecessary in order to maintain oxygenation.Please note that these are excerpts from the S1 guideline“Pre-hospital emergency anesthesia in adults”.Source: Anästh Intensivmed 2015;56:317-335 Aktiv Druck & Verlag GmbHHeadquarter WEINMANN Emergency Medical Technology GmbH + Co. KG Frohbösestraße 12 22525 Hamburg Germany T: +49 40 88 18 96-0 F: +49 40 88 18 96-480 T: +49 40 88 18 96-120 Customer Service T: +49 40 88 18 96-122 After-Sales Service E:******************** Center for Production, Logistics, Service WEINMANN Emergency Medical Technology GmbH + Co. KG Siebenstücken 14 24558 Henstedt-Ulzburg Germany China Weinmann (Shanghai) Medical Device Trading Co. Ltd. T: +862152302225•******************** U.A.E. WEINMANN Emergency Medical Technology GmbH + Co.KG (Branch) T:+97143210031•*************************** France WEINMANN Emergency France SARL – Paris – Les Ulis T: +33169415120•******************** Russia Weinmann SPb GmbH – St. Petersburg T: +78126333082•******************** Singapore Weinmann Singapur PTE, Ltd. T: +6565094430•****************************** Spain WEINMANN Emergency Medical Technology GmbH + Co. KG T: +34917901137•**************************83445-EN-02-2020 © C o p y r i g h t W E I N M A N N E m e r g e n c y , H a m b u r g . D u p l i c a t i o n o f a n y k i n d o n l y w i t h t h e e x p r e s s p e r m i s s i o n o f W E I N M A N N E m e r g e n c y . A l l r i g h t s t o d e s i g n a n d s p e c i fi c a t i o n m o d i fi c a t i o n s r e s e r v e d 。
Siemens DP1 DP2控制器用户手册说明书

display
ConF ------
meaning
Konfigurationsmenü The parameter menu leads to the configuration menu (‚CONF.‘). To start the configuration menu, the password has to be entered. Consider that the digits of the password have to be entered starting right (!) by pressing key A1 or B1. Enter by pressing key F.
D Fault report ”Pol. TH 2”
Polarity error at thermocouple of zone 1 or 3
Polarity error at ther- Correct the polarity mocouple
E Significant fluctuation of temperature (+/- 100 °C )
softstart By entering the menu “SOFT” the softstart function for 230V nozzles is selected. Within this parameter it is possible to enable or disable the softstart function.
Please check the wiring of your thermocouple!
Note
Err. tH.1
After confirming the fault report “thermocouple failure” or “polarity error at thermocouple connection” with key F, the DP1/DP2 switches into percentage control mode automatically. If the user solves the problem before confirming with key F, the controller remains in thermocouple control mode..
ProBER 2 2 Mb s 手持测试设备说明书

Testing at 2 Mb/s?Now, probe deeper . . .ProBER 2 setsnew standards forhandheld test powerand ease-of-useSingle transmit/receive setup display . . and graphicalClear results presentation, both tabular . .Local language on-line helpThe handheld that takes 2 Mb/s testing beyond conventionCompact and rugged design withstands rough handling; ergonomic shape makes the ProBER 2a favorite with seasoned professionals and newtechnicians alike.For comprehensive 2 Mb/s circuit testing, in- or out-of-service, use the high-performance ProBER 2handheld test set.It has all the error and alarm measurements you’ll need to verify quality-of-service in your network. Plus, a complete range of signal quality measurements including pulse mask and jitter.This unique combination means you won’t waste valuable time switching to other moreexpensive instruments tocomplete your network testing.What’s more, useability isenhanced with a graphical user interface that’s so simple, even inexperienced technicians will find the tester easy to operate.If you want a robust, go-anywhere handheld that extends to more than routine measurements, the ProBER 2 is the perfect choice.A range of signal quality measurements forfaster problem resolutionSave time by quickly identifying signalquality problems before running long-termerror measurements and during trouble-shooting.With a single keystroke, the ProBER 2rapidly identifies any frequency, level, pulse shape or jitter problem on a 2 Mb/s signal. Measurement summary•2 Mb/s, n × 64 kb/s and 64 kb/sco-directional testing•Extensive error and alarm generationand measurement•I TU-T G.821, G.826performance analysis•Frequency and level measurements•– pulse, pulse width ratio, pulseamplitude ratio)•standard O.172 (supports pointer jittertests)•Delay measurement•VF tone generation and measurement •Timeslot activity monitor•Line rate offset•Frame data control and monitoring •Synchronization status messages•Built-in talk/listen capability•Thru-mode test capabilityRelated p roductsThe OmniBER 718 communications performance analyzer is a rugged, portable one-box solution for installation, maintenance and manufacturing of SDH/SONET networks and network elements.It provides full PDH/T-carrier and SDH/SONET capability up to2.5 Gb/s, including STM-16c/OC-48c payloads and jitter.Agilent Technologies manufactures the ProBER 2 2 Mb/s handheld test set under a quality system approved to the international standard ISO 9001 plus TickIT (BSI Registration Certificate No FM 10987).Performance summary •Comprehensive error and alarm testing plus unique set of signal quality measurements (pulse mask, jitter, level and frequency)•Easy-to-learn, easy-to-use graphical user interface•Auto setup mode•120 ohm balanced and 75 ohm unbalanced input/output ports•2 MHz external clock input(75 ohm unbalanced)•Result logging to external printer •Save/recall of up to four user-defined setups and up to 10 sets of graphical results•More than 8 hours measurement operation from a single battery charge•Weight: 1 kg•EMC/EMI compliant•Impact resistant case•Agilent quality and reliability •Agilent service and support Ordering informationProBER 2 (E7580A)2 Mb/s handheld test setincludes ac adaptor, operating manual and BNC loopback cable. Option 001: Advanced signal quality measurements (adds 2 Mb/s pulse mask, jitter, level and frequency measurements).Option 002: 64 kb/s co-directional interface.Option 003: M.2100 performance analysis (including M.2110 andM.2120).Option 020: Soft carrying case. Option 031: Latin American Spanish localization.Option 032: Brazilian Portuguese localization.Option AB2: Chinese localization. Accessories15730B: Lightweight, battery-operated thermal printer (40 column) with 230V power supply. Specify Option 100 for 100V power supply and Option 120 for 120V. 15736A: RS-232-C printer cable(9-pin male to 9-pin female).Agilent Technologies’ Test and Measurement Support, Services, and AssistanceAgilent Technologies aims to maximize the value you receive, while minimizing your risk and problems. We strive to ensure that you get the test and measurement capabilities you paid for and obtain the support you need. Our extensive support resources and services can help you choose the right Agilent products for your applications and apply them successfully. Every instrument and system we sell has a global warranty. Support is available for at least five years beyond the production life of the product. Two concepts underlie Agilent’s overall support policy: “Our Promise” and “Your Advantage.”Our PromiseOur Promise means your Agilent test and measurement equipment will meet its advertised performance and functionality. When you are choosing new equipment, we will help you with product information, including realistic performance specifications and practical recommendations from experienced test engineers. When you use Agilent equipment, we can verify that it works properly, help with product operation, and provide basic measurement assistance for the use of specified capabilities, at no extra cost upon request. Many self-help tools are available.Your AdvantageYour Advantage means that Agilent offers a wide range of additional expert test and measurement services, which you can purchase according to your unique technical and business needs. Solve problems efficiently and gain a competitive edge by contracting with us for calibration, extra-cost upgrades, out-of-warranty repairs, and on-site education and training, as well as design, system integration, project management, and other professional engineering services. Experienced Agilent engineers and technicians worldwide can help you maximize your productivity, optimize the return on investment of your Agilent instruments and systems, and obtain dependable measurement accuracy for the life of those products.By internet, phone, or fax, get assistance with all your test & measurement needsOnline a ssistance:/find/assistPhone or Fax United States: (tel)180****4844 Canada:(tel)187****4414 (fax) (905) 282 6495 China:(tel) 800 810 0189 (fax) 1 0800 650 0121 Europe:(tel) (31 20) 547 2323 (fax) (31 20) 547 2390Japan:(tel) (81) 426 56 7832(fax) (81) 426 56 7840Korea:(tel) (82 2) 2004 5004(fax) (82 2) 2004 5115Latin A merica:(tel) (305) 269 7500(fax) (305) 269 7599Taiwan:(tel) 080 004 7866(fax) (886 2) 2545 6723Other Asia Pacific Countries:(tel) (65) 375 8100(fax) (65) 836 0252Email: t******************Product specifications and descriptionsin this document subject to changewithout notice.© Agilent Technologies UK LTD. 2001Printed in UK August 7, 20015988-3772EN。
爱特顿PDG62P2500E2ZM电源防御型电路保护器说明书

Eaton PDG62P2500E2ZMEaton Power Defense molded case circuit breaker, Globally Rated, Frame 6, Two Pole, 2500A, 100kA/480V, PXR20 LSI w/ ZSI and Relays, No Terminals (Metric Tapped Conductors)Eaton Power Defense molded case circuit breakerPDG62P2500E2ZM 786679939932247.7 mm 406.4 mm 393.7 mm 61.23 kg Eaton Selling Policy 25-000, one (1) year from the date of installation of theProduct or eighteen (18) months from thedate of shipment of the Product,whichever occurs first.RoHS Compliant UL 489CSAIEC 60947-2CCC MarkedProduct NameCatalog Number UPCProduct Length/Depth Product Height Product Width Product Weight WarrantyCompliancesCertifications2500 AComplete breaker 6Two-polePD6 Global Class A PXR 20 LSI600 Vac600 VNo Terminals100 kAIC at 480 Vac 40 kAIC Icu/ 25 kAIC Ics/ 84 kAIC Icm @525V South Africa (IEC)100 kAIC Icu/ 50 kAIC Ics/ 220 kAIC Icm @380-415V (IEC) 200 kAIC @240V (UL) 100 kAIC @480/277V (UL) 65 kAIC @600/347V (UL)100 kAIC Icu/ 50 kAIC Ics/ 220 kAIC Icm @440V (IEC) 35 kAIC Icu/ 18 kAIC Ics/ 73.5 kAIC Icm @690V (IEC) 85 kAIC Icu/ 40 kAIC Ics/ 187 kAIC Icm @480V Brazil (IEC) 200 kAIC Icu/ 100 kAIC Ics/ 440 kAIC Icm @240V (IEC)2500 AEaton Power Defense PDG62P2500E2ZM 3D drawing Power Xpert Protection Manager x32Amperage Rating Circuit breaker frame type Frame Number of poles Circuit breaker type Class Trip Type Voltage rating Voltage rating - max Terminals Interrupt rating Interrupt rating rangeTrip rating 3D CAD drawing packageApplication notesPower Xpert Protection Manager x64Consulting application guide - molded case circuit breakersBrochuresPower Defense technical selling bookletPower Defense molded case circuit breaker selection posterPower Defense brochureCatalogsPower Defense molded case circuit breakers - Frame 6 product aid Molded case circuit breakers catalogPower Xpert Release trip units for Power Defense molded case circuit breakersCertification reportsPDG5 CCC certificationPDG6 CCC certificateEU Declaration of Conformity - Power Defense molded case circuit breakersPDG6 CB reportPDG6 UL AuthorizationPower Defense Declaration concerning California’s Proposition 65PDG6 CSA certificationInstallation instructionsPower Defense Frame 6 aux, alarm, shunt trip and uvr instructions -IL012202ENPower Defense Frame 2/3/4/5/6 voltage neutral sensor module wiring instructions – IL012316ENPower Defense Frame 6 flex shaft handle mech assembly instructions - IL012285ENPower Defense Frame 6 key interlock installation instructions -IL012282ENPower Defense Frame 6 bar rear connectors (copper), 2000A - 5000A instructions - IL012256EN H01Power Defense Frame 6 walking beam interlock installation instructions - IL012286ENPower Defense Frame 6 modbus and relay board installation -IL012306ENPower Defense Frame 6 handle lock hasp installation instructions -IL012292ENInstallation videosPower Defense Frame 6 Shunt Trip How-To VideoPower Defense Frame 6 Aux, Alarm, ST and UVR Animated Instructions.rhEaton Corporation plc Eaton House30 Pembroke Road Dublin 4, Ireland © 2023 Eaton. All Rights Reserved. Eaton is a registered trademark.All other trademarks areproperty of their respectiveowners./socialmediaPower Defense Frame 6 Trip Unit Replacement Animated Instructions Power Defense Frame 6 Aux and Alarm Trip How-To Video Power Defense Frame 6 UVR Trip How-To Video Power Defense Frame 3 Variable Depth Rotary Handle Mechanism Installation How-To VideoEaton Power Defense for superior arc flash safety Power Defense Frame 6 Trip Unit How-To Video Power Defense Frame 5 Trip Unit How-To Video Power Defense molded case circuit breakersPower Defense Frame 2 Variable Depth Rotary Handle Mechanism Installation How-To Video Power Defense Breakers Eaton Specification Sheet - PDG62P2500E2ZM Power Defense time current curve Frame 6 - PD6Intelligent circuit protection yields space savings Single and double break MCCB performance revisitedImplementation of arc flash mitigating solutions at industrial manufacturing facilitiesMaking a better machineIntelligent power starts with accurate, actionable data Molded case and low-voltage power circuit breaker health Molded case and low-voltage breaker health Safer by design: arc energy reduction techniquesMultimediaSpecifications and datasheetsTime/current curvesWhite papers。
DVP02TUN-S系列温控器说明书

DVP02TUN-S50140317022022-05-16EN Instruction Sheet TR Bilgi DökümaniTW 薄型溫度量測模組簡易版說明 CN薄型温度量测模块简易版说明ENThis is an OPEN TYPE module and therefore should be installed in an enclosure free of airborne dust, humidity, electric shock andvibration. The enclosure should prevent non-maintenance staff from operating the device (e.g. key or specific tools are required for operating the enclosure) in case danger and damage on the device may occur.FRCeci est un module ouvert et il doit donc être installé dans un coffret à l’abri des poussières, des vibrations et ne pas être exposé auxchocs électriques. Le boitier ou l’armoire doit éviter toute action d’un personnel autre que celui affecté à la maintenance de l’appareil (par exemple, clefs, outils spécifiques pour l’ouverture du coffret), ceci afin d’éviter tout accident corporel ou endommagement du produit).TR Bu ürün AÇIK TİP bir modül olup toz, rutubet, elektrik şoku ve titreşimden uzak kapalı yerlerde muhafaza edilmelidir. Yanlış kullanımsonucu ürünün zarar görmesini önlemek için yetkili olmayan kişiler tarafından ürüne müdahale edilmesini önleyecek koruyucu önlemler alınmalıdır. (Ürünün bulunduğu panoya kilit konulması gibi).TW 本機為開放型(OPEN TYPE )機種,因此使用者使用本機時,必須將之安裝於具防塵、防潮及免於電擊∕衝擊意外之外殼配線箱內。
SM-DPN系列2口显示端口KVM开关用户手册说明书

USER MANUALDesigned and Manufactured in the USA1-800-284-2131SM-DPN-2S 2-Port Single-Head DisplayPort KVM Switch SM-DPN-2D2-Port Dual-Head DisplayPort KVM SwitchOVERVIEWTECHNICAL SPECIFICATIONS_________________________________________________________________ WHAT’S IN THE BOX?_________________________________________________________________________ FRONT AND BACK___________________________________________________________________________ INSTALLATION_______________________________________________________________________________ SYSTEM OPERATION_________________________________________________________________________ FRONT PANEL CONTROL_____________________________________________________________________ HOTKEY AND RS232 SERIAL CONTROL_______________________________________________________ CUSTOM HOTKEY TRIGGERS_________________________________________________________________ LED’S BEHAVIOUR___________________________________________________________________________ TROUBLESHOOTING_________________________________________________________________________ TECHNICAL SUPPORT________________________________________________________________________ LIMITED WARRANTY STATEMENT____________________________________________________________3 4 4 5-6 7 7 7 8 9 10 10 11Technical SpecificationsWhat’s in the box?FRONT AND BACKSM-DPN-2S Back SM-DPN-2D BackSM-DPN-2S FrontSM-DPN-2D FrontINSTALLATION1. Ensure that power is turned off or disconnected from the unit and the computers.2. Use a DisplayPort cable to connect the DisplayPort output port from each computer to thecorresponding DP IN ports of the unit.3. Use a USB cable (Type-A to Type-B) to connect a USB port on each computer to the respectiveUSB ports of the unit.4. Optionally connect a stereo audio cable (3.5mm to 3.5mm) to connect the audio output of thecomputers to the AUDIO IN ports of the unit.5. Connect a monitor to the DP OUT console port of the unit using a DisplayPort cable.6. Connect a USB keyboard and mouse in the two USB console ports.7. Optionally connect stereo speakers to the AUDIO OUT port of the unit.8. Finally, power on the KVM by connecting a 12VDC power supply to the power connector, and thenturn on all the computers.Note: You can connect up to 2 computers to the 2 port KVM.Installation (continued)EDID LEARNThe KVM is designed to learn the connected monitor’s EDID upon power up. In the event of connecting a new monitor to the KVM, a power recycle is required.The KVM will indicate to the user the EDID learn process by flashing the front panel’s LEDs. Port one green and push button blue LEDs will both begin to flash for about 10 seconds. When the LEDs stop flashing, the EDID learn process is done.If the KVM has more than one video board (such as dual-head and quad-head models), then the unit will continue to learn the EDIDs of the connected monitors and indicate the progress of the process by flashing the next port selection green and push button blue LEDs respectively.The monitor must be connected to the video output connector located in the console space at the back of the KVM during the EDID learn process.If the read EDID from the connected monitor is identical to the current stored EDID in the KVM then the EDID learn function will be skipped.System operationhotkey and rs232 serial controlThere are three ways to control the SM-DPN: Keyboard Hotkeys, RS-232 Serial Commands, and Front Panel Buttons. All modes of control will allow the user the set their desired configurations.The SM-DPN may also be controlled via RS-232 commands. T o use these commands, you must use HyperT erminal or an alternate terminal application. The settings for the connection are as follows:Baudrate 115200; Data Bits 8; Parity None ; Stop Bits 1; Flow Control None .Once you have connected to the SM-DPN via Serial, you will see the SM-DPN information when the device starts up.The following commands can be used for RS-232 with available keyboard hotkeys:front panel controlT o switch to an input port, simply push the button on the front-panel of the KVM. If an input port is selected, the LED of that port will turn on.Hold down the button of Front Panel for 3 seconds to force learn EDID.Custom hotkey triggersUsers are able to customize the keys that trigger Hotkeys. The default trigger for hot key function on the keyboard is Ctrl + Ctrl. The trigger function can be used to change to the following keys:Ctrl (Left / Right), Alt, Shift (Left / Right), Caps Lock, Scroll Lock, F1-F12TO VIEW HOTKEY TRIGGER SETTINGUse the RS-232 command: / + / + ? + ? + Enter to view the current HotKey Trigger T o reset the Hotkey Trigger use the “Factory Defaults” command.TO CHANGE THE HOTKEY TRIGGER SETTINGHotKey + HotKey + x + [desired hotkey]Example: If users current Hotkey trigger is Shift and want to change to Scroll Lock, user would type Shift + Shift + x + Scroll LockLed’s behaviorUser Console Interface – Display LED:Front Panel – Port Selection LED’s:EDID Learn - Front Panel LED’s:All LED’s are turned on for 1 second. Then:• Port 1 LED’s will flash until the end of the process.• Port 2 LED’s will flash until the end of the process if a second video board exists (Dual-head KVM)IMPORTANT!If all Front Panel LED’s are on and not flashing , the POWER UP SELF TEST has failed and all functions are disabled. Check if any of the front panel port selection buttons are jammed. In this case, release thejammed button and recycle the power. If power up self test is still failing, please contact SmartAVI technical support at ********************.TroubleshootingTechnical supportNo Power• Make sure that the power adapter is securely connected to the power connector of the unit.• Check the output voltage of the power supply and make sure that the voltage value is around 12VDC.• Replace the power supply. No Video• Check if all the video cables are connected properly.• Connect the computer directly to the monitor to verify that your monitor and computer are functioning properly.• Restart the computers. Keyboard is not working• Check if the keyboard is properly connected to the unit.• Check if the USB cables connecting the unit and the computers are properly connected.• Try connecting the USB on the computer to a different port.• Make sure that the keyboard works when directly connected to the computer.• Replace the keyboard. Mouse is not working• Check if the mouse is properly connected to the unit.• Try connecting the USB on the computer to a different port.• Make sure that the mouse works when directly connected to the computer.• Replace the mouse.No Audio• Check if all the audio cables are connected properly.• Connect the speakers directly to the computer to verify that the speakers and the computer audio are functioning properly.• Check the audio settings of the computer and verify that the audio output is through the speakers.For product inquiries, warranty questions, or technical questions, please contact *****************.Limited warranty statementA. Extent of limited warrantySmartAVI, Inc. warrants to the end-user customers that the SmartAVI product specified above willbe free from defects in materials and workmanship for the duration of 1 year, which duration begins on the date of purchase by the customer. Customer is responsible for maintaining proof of date of purchase.SmartAVI limited warranty covers only those defects which arise as a result of normal use of the product, and do not apply to any:a. Improper or inadequate maintenance or modificationsb. Operations outside product specificationsc. Mechanical abuse and exposure to severe conditionsIf SmartAVI receives, during applicable warranty period, a notice of defect, SmartAVI will at its discretion replace or repair defective product. If SmartAVI is unable to replace or repair defective product covered by the SmartAVI warranty within reasonable period of time, SmartAVI shall refund the cost of the product.SmartAVI shall have no obligation to repair, replace or refund unit until customer returns defective product to SmartAVI.Any replacement product could be new or like new, provided that it has functionality at least equal to that of the product being replaced.SmartAVI limited warranty is valid in any country where the covered product is distributed by SmartAVI.B. Limitations of warrantyT o the extant allowed by local law, neither SmartAVI nor its third party suppliers make any other warranty or condition of any kind whether expressed or implied with respect to the SmartAVI product, and specifically disclaim implied warranties or conditions of merchantability, satisfactory quality, and fitness for a particular purpose.C. Limitations of liabilityT o the extent allowed by local law the remedies provided in this warranty statement are the customers sole and exclusive remedies.T o the extant allowed by local law, except for the obligations specifically set forth in this warranty statement, in no event will SmartAVI or its third party suppliers be liable for direct, indirect, special, incidental, or consequential damages whether based on contract, tort or any other legal theory and whether advised of the possibility of such damages.D. Local lawT o the extent that this warranty statement is inconsistent with local law, this warranty statement shall be considered modified to be consistent with such law.NOTICEThe information contained in this document is subject to change without notice. SmartAVI makes no warranty of any kind with regard to this material, including but not limited to, implied warranties of merchantability and fitness for particular purpose. SmartAVI will not be liable for errors contained herein or for incidental or consequential damages in connection with the furnishing, performance or use of this material. No part of this document may be photocopied, reproduced, or translated into another language without prior written consent from SmartAVI, Inc.20180109Designed and Manufactured in the USAT el: (800) AVI-2131 • (702) 800-00052455 W Cheyenne Ave, Suite 112North Las Vegas, NV 89032。
Power-PRO 2 电动救护车床说明书

Power-PRO™ 2 powered ambulance cotResponse inspiredNobody knows what works in the field better than you. That’s why we reimagined our proven design to redefine your partner on scene—focusing on what matters most to help you get the job done.Y ou live it. We built it.Respond safely• Perform a true, unassisted lift and reachoptimal loading height using smarter hydraulic assembly with load-sensing capabilities • See and be seen in low light environments with powerful lights and reflectors • Reduce the chance of cot damage and medic or patient injury with new bumper detection technology 2Respond ready• Remotely track your fleet with Smart Equipment Management (SEM) and pinpoint your cot with its last-known location 3 • Improve battery life and management with a new lithium-ion battery and charge indicator • Limit cot downtime, reduce unexpected costs and ready your ambulancesRespond confidently• Reach optimal transport height 1 with a single button and increase maneuverability using an extended transport handle • Navigate through tighter spaces with a new retractable foot section (extends and retracts an extra 7.62 centimeters each) • Help decrease body fatigue with enhanced ergonomics during manualloading and unloading3. Receive location updates when connected to an active Wi-Fi ® network and inductive charger from Power-LOAD or Performance-LOAD. Hot spot required for off-network use (not provided by Stryker). Frequency of updates depends on your connection.2. When unloading with manual fastener1. The optimal transport height is predefined to a low transport position to reduce the risk of patient falls without disturbing caregivers access to the patient.Maximize your investment• Extend the life of your equipment byevaluating cot usage and rotating your fleet • Identify training opportunities usingdetailed analytics to help improve patient and medic safety • Take the guesswork out of batteryreplacement by monitoring use over timeAutomatically track cot health and remotely manage your fleet through one convenient, interactive dashboard.Minimize downtime• Keep your fleet ready to respond by identifying which cots need attention • Save time and budget by troubleshooting the issue before on-site repair • Quickly get your equipment back in the field with direct access to ProCare ServicesMaintain your service• Start your shift right with battery status updates and other critical cot insights • Pinpoint your fleet in near real-time with last-known location 3• Streamline reporting and planningrequirements with instant access to vital equipment metrics3. Receive location updates when connected to an active Wi-Fi ®network and inductive charger from Power-LOAD or Performance-LOAD. Hot spot required for off-network use (not provided by Stryker). Frequency of updates depends on your connection.Last-known location88% total stateof battery healthTroubleshootthe issueA legacy of trustContact your local sales representative or visit Emergency CareThis document is intended solely for the use of healthcare professionals. A healthcare professional must always rely on his or her own professional clinical judgment when deciding whether to use a particular product when treating a particular patient. Stryker does not dispense medical advice and recommends that healthcare professionals be trained in the use of any particular product before using it. The information presented is intended to demonstrate the breadth of Stryker product offerings. A healthcare professional must always refer to the package insert, product label and/or instructions for use before using any Stryker product.Products may not be available in all markets because product availability is subject to the regulatory and/or medical practices in individual markets. Please contact your Stryker representative if you have questions about the availability of Stryker products in your area.Stryker Corporation or its divisions or the corporate affiliated entities own, use or have applied for the following trademarks or service marks: Power-LOAD, Power-PRO, Power-PRO 2. All other trademarks are trademarks of their respective owners or holders. The products depicted are CE marked in accordance with applicable EU Regulations and Directives: Class I, Stryker.10/2021Copyright © 2021Stryker2021-313563800 E. Centre Avenue Portage, MI 49002 USAWorking in partnership with our customers, Stryker develops technologies and devices to give first responders and hospitals more control during a critical event. Our uncompromising commitment to quality means product performance you can count on, so that in critical situations you can focus on what you do best: save lives.。
- 1、下载文档前请自行甄别文档内容的完整性,平台不提供额外的编辑、内容补充、找答案等附加服务。
- 2、"仅部分预览"的文档,不可在线预览部分如存在完整性等问题,可反馈申请退款(可完整预览的文档不适用该条件!)。
- 3、如文档侵犯您的权益,请联系客服反馈,我们会尽快为您处理(人工客服工作时间:9:00-18:30)。
DPR-2分布式微机母联备投及过流保护装置_________________________________________技术和使用说明书南京恒星自动化设备有限公司SUN NANJING AUTOMA TION EQUIPMENT CO.,L TD南京恒星自动化设备有限公司版权所有2006.12(V1.2)本说明书适用于DPR-2保护装置,V2.00版本本说明书和产品今后可能会有小的改动,请核对实际产品与说明书的版本是否相符。
目录1.概述 (4)1.1 DP系列产品概述 (4)1.2 应用范围 (4)1.3 保护配置 (4)1.4性能特征 (4)1.5规范性引用文件 (5)2.技术条件 (6)2.1环境条件 (6)2.2电源 (7)2.3 交流回路 (7)2.4过载能力 (7)2.5装置的主要功能 (8)2.6主要技术性能指标 (8)2.7测量元件 (9)3.工作原理 (9)3.1. 定时限过流保护 (9)3.2. 母联备自投 (9)3.3 电压回路断线监视回路 (10)3.4 定值组切换 (10)4.辅助功能 (11)4.1定值组切换 (11)4.2 测量 (11)4.3 对开关的控制 (11)4.4 事故记录 (11)4.5 故障录波 (12)4.6 事件记录 (12)5.面板及操作 (12)5.1面板说明 (12)5.1.1面板图 (12)5.1.2面板按键说明 (13)5.1.3指示灯说明 (13)5.1.4操作箱的使用 (13)5.2键盘操作 (13)5.3界面内容 (14)5.3.1默认界面 (14)5.3.2目录界面 (14)5.3.3监测界面 (14)5.3.4系统界面 (14)5.3.5控制界面 (14)5.3.6整定界面 (15)5.3.7设置界面 (15)5.3.8记录界面 (15)5.3.9校准界面及调试界面 (15)5.3.10重要数据浏览界面 (15)6.安装与对外接线 (16)6.1 开箱与安装 (16)6.1.1 开箱和包装 (16)6.1.2 安装现场要求 (16)6.1.3 安装尺寸 (16)6.1.4 保护和系统接地 (17)6.2 连接 (19)6.2.1 连接测量和辅助回路 (19)6.2.2 连接电源 (19)6.2.3 连接开关量输入 (19)6.2.4 连接通讯口1 (19)6.2.5 连接亮屏控制 (19)6.2.6 面板LED平面发光管的使用 (20)6.2.7 电源模块脉冲输入设置说明 (20)附录一.信息表 (21)附录二.DPR-2保护装置逻辑框图 (31)附录三.DPR-2保护装置开出原理图 (31)附录四.DPR-2保护装置对外接线原理图 (31)DPR-2型分布式微机母联备投及过流保护装置1.概述1.1 DP系列产品概述DP系列的保护在开发时借鉴了当前国内外同类产品的成熟经验,并根据我国电力系统运行的实际要求,以及数字式保护今后的发展趋势,在制定设计方案时要求做到:●满足变电站综合自动化的要求,有按标准规约制定的网络接口,所有保护的运行数据能够在数据总线上交流,配合监控软件可以组成变电站自动化系统。
●保护原理先进,配置合理、完善,既能满足大网的运行要求,也能适应小网特别是小水电网的要求。
●结构可靠密封好,具有良好的抗干扰和防尘能力。
●减小安装尺寸,分布式安装时可直接装于开关柜上,集中组屏时可减少屏数,降低造价。
使用与操作简单,适应低电压等级运行人员的技术水平。
●装置的核心部件(CPU)采用了处理能力强的32位系统,替代了以往2~3个CPU才能实现的功能,大大提高装置的可靠性。
●对于交流信号处理电路,转换精度为16位,最高采样速度可达250KHz/s,大大提高了系统数据的采集精度和加速了数据采集。
●整个系统基于嵌入式系统的技术,采用C语言和汇编语言混合编程,以由硬件驱动程序实时多任务操作系统,数据服务三部分组成的实时软件平台技术为基础,保证了产品功能的高可靠性、灵活配置、可移植性。
●采用新的交流采样快速算法,不仅计算简单、速度快、精度高,同时可完全滤清暂态超越时产生的衰减非周期分量及奇次谐波分量,极大地提高了滤波能力,特别适合于需要快速动作的继电保护。
1.2 应用范围DPR-2型分布式微机母联备投及过流保护装置是DP系列数字式保护中的一种,可独立构成供电系统中母联的完整保护及备自投功能。
1.3 保护配置●复合电压过流保护●母联备自投功能●电压回路断线监视回路1.4性能特征●动作速度快,速断故障跳闸时间<35ms。
●交流采样算法速度快,精度高并可完全滤除非周期分量。
●硬件上采取了全封闭机箱,结构可靠密封好,具有良好的抗干扰和防尘能力。
●事故报文,可保存最新的16条故障数据,7次故障录波报文,以及1024次最新的装置操作记录。
●此保护可采用分布式安装,简化接线。
具有良好的中文人机交互界面,可通过面板整定定值。
●具备遥测功能,正常运行时能够上报各种运行参数,故障时能够记录并上报所有故障数据。
●可以接入脉冲电度表的计数脉冲。
●对开关有就地和远方的控制功能。
●对跳、合闸回路接线的状态有在线监视功能。
●灵活的通信方式,配有RS-485和以太网接口。
1.5规范性引用文件下列文件中的条款通过在本标准的引用而成为本标准的条款。
凡是注日期的引用文件,其随后所有的修改单(不包括勘误的内容)或修订版均不适用于本标准,然而,鼓励根据本标准达成协议的各方研究是否可使用这些文件的最新版本。
凡是不注日期的引用文件,其最新版本适用于本标准。
GB 9361-1988 计算站场地安全要求GB 16836-1997 量度继电器和保护装置安全设计的一般要求GB/T 191-2000 包装储运图示标志(eqv ISO 780:1997)GB/T2887-2000 电子计算机场地通用规范GB/T3047.4-1986 高度进制为44.45mm的面板、架和柜的基本尺寸系列GB 4208-1993 外壳防护等级(IP代码)(eqv IEC 529:1989)GB/T7261-2000 继电器及装置基本试验方法GB/T8367-1987 量度继电器直流辅助激励量的中断与交流分量(纹波)(eqv IEC60255-11:1979)GB/T11287-2000 电器继电器第21部分:量度继电器和保护装置的振动、冲击与碰撞和地震试验第1篇:振动试验(正玄)(idt IEC60255-21-1:1988)GB/T14537-1993 量度继电器和保护装置的冲击与碰撞试验(eqv IEC 60255-21-2:1988)GB/T14598.3-1993 电气继电器第5部分:电气继电器的绝缘试验(eqv IEC 60255-5:1977)GB/T14598.9-2002 电器继电器第22部分:量度继电器和保护装置的电气干扰试验第三篇:辐射电磁场干扰试验(Idt IEC 60255-22-3:1989)GB/T14598.10-1996 电器继电器第22部分:量度继电器和保护装置的电气干扰试验第4篇:快速瞬变干扰试验(Idt IEC 60255-22-4:1992)GB/T14598.13-1998 电器继电器第22部分:量度继电器和保护装置的电气干扰试验第1篇:1MHz脉冲干扰试验(eqv IEC 60255-22-1:1988)GB/T14598.14-1998 电器继电器第22部分:量度继电器和保护装置的电气干扰试验第2篇:静电放电试验(Idt IEC 60255-22-2:1996)GB/T 17626.5-1999 电磁兼容试验和测量技术浪涌(冲击)抗扰度试验(idt IEC61000-4-5:1995)JB/T7828-1995 继电器及装置包装储运技术条件GB/T13729-2002 远动终端设备DL/T630-1997 交流采样远动终端技术条件GB/T 17626.8-1998 电磁兼容试验和测量技术工频磁场抗扰度试验(idtIEC61000-4-8:1993)DL/T478-2001 静态继电保护及安全自动装置通用技术条件GB/T2900.49-1994 电工术语电力系统保护(eqv IEC60010(448):1987)GB/T17742-1999 中国地震烈度表GB/T14598.16-2002 电气继电器第25部分:量度继电器和保护装置的电磁发射试验(IEC 60255-25:2000,IDT)GB/T 17626.6-1998 电磁兼容试验和测量技术射频场的传导骚扰抗扰度试验GB/T 17626.9-1998 电磁兼容试验和测量技术脉冲磁场抗扰度试验(idt IEC61000-4-9:1993)GB/T17626.10-1998 电磁兼容试验和测量技术阻尼振荡磁场抗扰度试验(idtIEC61000-4-10:1993)GB/T17626.11-1999 电磁兼容试验和测量技术电压暂降、短时中断和电压变化抗扰度试验IEC60255-22-7:2003 电气继电器第22-7部分:量度继电器和保护装置的电气骚扰试验—工频抗扰度试验IEC 60255-5:2000 电气继电器第5部分:量度继电器和保护装置的绝缘配合要求和试验.2.技术条件2.1环境条件2.1.1 正常工作的大气条件a)环境温度:-20℃~+55℃;b)相对湿度:≤90%(相对湿度为90%时,环境温度不低于25℃,继电器内无凝结及冰形成);c)大气压力 86kPa~106kPa2.1.2 试验的标准大气条件a)环境温度:+15℃~35℃;b)相对湿度:45%~75%;c)大气压力:86kPa~106kPa.2.1.3 仲裁试验的标准大气条件:a)环境温度:+20℃±2℃。
b)相对湿度:45%~75%。
c)大气压力:86kPa~106kPa.2.1.4 储存、运输极限环境温度:-25℃~+70℃2.1.5 周围环境a)不允许有超过2.11规定的电磁干扰存在.b)场地应符合GB 9361-1988中B类安全要求的规定.c)使用地点不出现超过GB/T11287-2000规定的严酷等级为1级的振动;不发生超过GB/T17742-1999规定的烈度为ⅤⅡ度的地震。
d ) 装置的使用地点应无爆炸危险的物质,周围介质中不应含有能腐蚀金属、破坏绝缘和表面涂覆层的介质及导电介质,不允许有明显的水气,不允许有严重的霉菌存在, e ) 应具有防御雨、雪、风、沙、尘埃的措施.f ) 接地电阻应符合GB/T2887中2.4的规定.2.1.6 特殊使用条件当超出2.1.1~2.1.5规定的正常工作条件时,由用户与本公司商定.2.2电源2.2.1交流(直流)电源:a ) 额定电压: 220V(也可根据用户要求改为110V);交流时频率为50Hz(或60Hz)b ) 电压允许偏差:-20%~+15%;频率误差:±1Hzc ) 纹波系数:≤5%2.3 交流回路a)额定电流:In=5A 。