汽车总装领域设备故障综合处理方案
关于汽车生产线设备故障处理

邢台职业技术学院毕业论文关于汽车生产线设备故障的处理专业生产过程自动化班级过控141姓名武永鹏学号0121指导教师马军强日期2017年5月17日目录摘要 (1)第1章电频器设计存在的不足 (2)第2章焊接机器人故障处理 (3)第3章排除焊接机器人系统故障的措施3.1 排除焊接机器人人为故障和自然故障 (4)3.2焊接机器人突发故障排除 (6)第4章PLC电控设备的日常维护 (7)结论 (8)参考文献 (9)致谢 (10)摘要现阶段人们对生活的品质要求越来越高,追求生活的高质量也就造成了汽车行业的飞速发展。
为了满足人们日益迫切的需求,大量生产汽车也就势不可挡。
但是在自动化生产过程中,设备故障问题会时常发生,这就导致了生产过程受阻,本文以变频器设计上存在的不足、焊接机器人设备故障及其处理方式、PLC电控设备日常维护三个方面来讨论汽车生产线设备故障的一些处理方法,关于汽车生产线设备做一些浅显的说明。
关键词:变频器;焊接机器人;PLC电控设备;生产线设备故障维护方法。
第1章变频器设计存在的不足在某一生产车间,涂装车间挂在DEVICENET网络上的某种型号变频器,经过一定时间的使用之后,出现了连续损坏好几台的现象,出现故障时都是变频器先显示“无法通信”。
重启后仍不能正常运行,在排查故障的过程中,又同时出现了三台变频器出现相同故障的现象。
经过检查后发现电源板上的三个35V、680uf电容器容量不够,经过进一步的检测,发现所有损坏的电容器都是同一厂家生产。
在预设的情况下,这种电容器不应该失效,根据预测发现其电容的质量不合格。
经过和厂家进行调节,厂家派出技术人员对故障进行判断和检测,并对该公司所有使用了同样电容器的该系统变频器进行了逐一检测,并且更换了内部开关电源板和电容,之后问题得到解决。
第2章焊接机器人故障处理我们一般在使用焊接机器人时,会出现一下几种情况的故障:1、人为操作不当造成的故障问题,包括在装卸工件时,不当的操作导致变位机随机部件的变形,操作不当造成的焊接机器人焊枪损坏;2、周围环境不符合标准造成的系统故障,静电的强烈作用和空气湿度问题,再加上在焊接现场粉尘密度大,柜内积尘容易积压,这或许也会导致失误操作;3、插线接口的腐蚀性导致其氧化损坏,并且有时候产生接触不良的问题,这就造成了开机的困难或者设备工作不能保持一个平稳的状态;4、设计不合格导致产生故障问题,其中报括:线缆容易受损、升降平台开关出现问题,示教器工作稳定性不好,显示部分元器件质量得不到保证。
汽车零部件故障处理方法

汽车零部件故障处理方法
在汽车使用过程中,零部件出现故障是很常见的。
如果您发现了汽车零部件故障,建议您采取以下处理方法:
1.车内异响:如果您在行驶过程中听到车内产生异响,可能是由于零部件故障引起的。
此时,建议您将车辆停放在安全地带,打开车身内饰检查异响产生的地方,并尝试根据具体情况进行维修或更换。
2.引擎灯亮:如果您在行驶中发现引擎灯亮起,可能是汽车的电子控制模块(ECU)发现了故障代码。
此时,建议您将车辆停靠在安全地带,使用汽车诊断仪进行故障码读取,并对故障进行维修或更换。
3.制动不灵:如果您在制动过程中发现制动不灵,建议您首先检查刹车液是否泄漏,刹车片磨损情况是否需要更换。
如若没有发现问题,则可能是刹车片变形、刹车缸漏气等原因引起,需要及时进行维修。
4.变速箱异响:如果您在行驶中发现变速箱出现异响,可能是由于变速箱油量不足、齿轮损坏等原因引起。
此时,建议您及时添加变速箱油,并将车辆送到专业的汽车修理店进行维修。
总之,如果您发现汽车零部件故障,应立刻停车并寻求专业的汽车维修人员帮助,切勿自行操作,以免造成更大的损失。
汽车零部件故障处理方法

汽车零部件故障处理方法
汽车零部件故障处理方法可以根据具体情况而异,一般有以下步骤:
确认故障部件:通过观察、听声辨认等方式确定出现问题的零部件;
分析故障原因:找出导致零部件故障的原因,如过度磨损、老化、腐蚀等;
制定维修方案:根据故障原因制定相应的维修方案,并预估所需时间和费用;
维修操作:执行维修方案进行维修操作,如更换零部件、修复受损零件等;
检测调试:在维修结束后进行检测调试,确保零部件运转正常;
记录维护情况:对维修过程和结果进行记录,以便于今后维护管理。
需要注意的是,在进行维修操作前,需要遵循相关安全规范,确保人身安全和车辆完整性。
此外,若无经验或技能建议寻求专业人士协助。
汽车零件生产中的故障排除如何快速解决生产中的问题
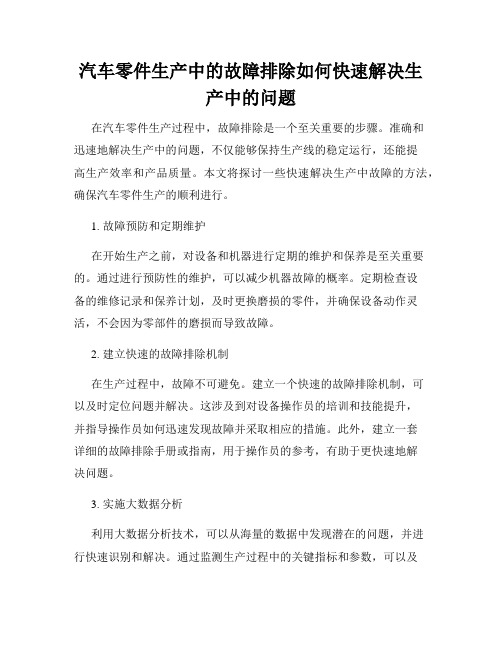
汽车零件生产中的故障排除如何快速解决生产中的问题在汽车零件生产过程中,故障排除是一个至关重要的步骤。
准确和迅速地解决生产中的问题,不仅能够保持生产线的稳定运行,还能提高生产效率和产品质量。
本文将探讨一些快速解决生产中故障的方法,确保汽车零件生产的顺利进行。
1. 故障预防和定期维护在开始生产之前,对设备和机器进行定期的维护和保养是至关重要的。
通过进行预防性的维护,可以减少机器故障的概率。
定期检查设备的维修记录和保养计划,及时更换磨损的零件,并确保设备动作灵活,不会因为零部件的磨损而导致故障。
2. 建立快速的故障排除机制在生产过程中,故障不可避免。
建立一个快速的故障排除机制,可以及时定位问题并解决。
这涉及到对设备操作员的培训和技能提升,并指导操作员如何迅速发现故障并采取相应的措施。
此外,建立一套详细的故障排除手册或指南,用于操作员的参考,有助于更快速地解决问题。
3. 实施大数据分析利用大数据分析技术,可以从海量的数据中发现潜在的问题,并进行快速识别和解决。
通过监测生产过程中的关键指标和参数,可以及时发现异常情况,并采取相应的措施。
大数据分析技术还可以帮助预测潜在故障,并提前采取预防措施,从而减少生产中的故障发生率。
4. 加强团队合作和沟通团队合作和沟通是解决生产中故障的关键。
建立一个团队合作的文化,鼓励员工之间的合作和协作,可以加快问题解决的速度。
及时的内部沟通和信息共享也是必要的,确保故障信息可以迅速传达给相关人员,并共同制定解决方案。
5. 引入自动化设备和技术自动化设备和技术的引入可以大大降低故障发生率。
自动化设备能够减少人工操作的错误和疏忽,提高生产的准确性和稳定性。
此外,自动化设备还可以通过传感器和监控系统来实时监测设备运行状态,发现异常情况并采取相应的措施,以防止故障的发生。
总结起来,在汽车零件生产中快速解决生产问题的关键在于预防和故障排除机制的建立、大数据分析的应用、团队合作和沟通的加强,以及自动化设备和技术的引入。
车辆维修故障解决方案

车辆维修故障解决方案车辆是人们日常生活中使用最频繁的交通工具之一,但是在长时间使用中,车辆难免出现一些故障。
这些故障给人们的生活带来了不少不便,甚至会影响到人们的安全。
因此,解决车辆故障问题及时地成为了一个重要的问题。
本文将为大家介绍车辆维修故障的解决方案。
车辆维修故障分类车辆维修故障可以分为两大类:机械故障和电子故障。
机械故障机械故障包括:发动机故障、转向故障、制动系统故障、悬挂系统故障等。
发动机故障是指发动机无法正常启动、启动后无法保持正常运转、发动机冒黑烟等。
通常可以通过更换或修理发动机零部件来解决。
转向故障是指车辆转向困难、转向不灵活等问题。
常见的解决方案是更换转向系统的零部件。
制动系统故障是指刹车系统无法正常工作。
常见问题包括制动距离过长、制动器噪音大、制动失灵等。
针对不同的情况可以采取不同的解决方案,如更换刹车片、刹车盘等。
悬挂系统故障是指车辆悬挂系统出现问题,如车辆行驶时出现颠簸、悬挂系统异响等问题。
解决方案一般是更换悬挂系统的零部件。
电子故障电子故障包括:电气系统故障、电子控制单元故障、仪表板故障、音响系统故障等。
电气系统故障通常是因为电路中断或腐蚀导致的。
解决方案可以是更换电路连接器或线路维修。
电子控制单元故障是指车辆的电子控制单元出现问题,如发动机控制模块失灵、车速传感器故障等。
解决方案通常是更换故障的控制单元。
仪表板故障指的是仪器表盘显示不正确,例如转速表指针跳动、油量表不准等。
一般的解决方案是更换仪表盘的整个模块。
音响系统故障通常是由于音响系统的线路出现故障导致。
可以通过更换线路或连接器来解决这种故障。
解决车辆故障的方法在遇到车辆故障的情况下,我们应该采取适当的方法来解决问题,以确保车辆可以正常运行。
定期维护保养定期维护保养是解决车辆故障的一个重要方法。
通过定期维护保养可以及时发现和解决车辆中出现的问题,比如更换机油滤芯、更换制动器等。
学会简单的维修方法对于一些简单的车辆故障,比如更换车轮胎、更换汽车雨刮片等,我们可以自己学会维修的方法,这样可以省去不必要的维修费用。
汽车电子设备故障排除方法
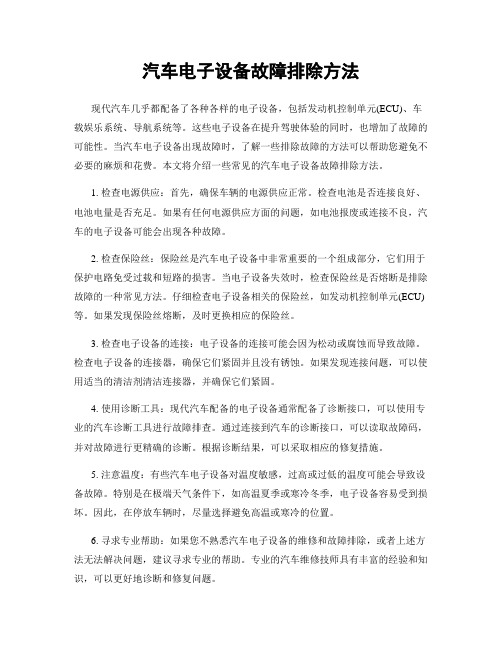
汽车电子设备故障排除方法现代汽车几乎都配备了各种各样的电子设备,包括发动机控制单元(ECU)、车载娱乐系统、导航系统等。
这些电子设备在提升驾驶体验的同时,也增加了故障的可能性。
当汽车电子设备出现故障时,了解一些排除故障的方法可以帮助您避免不必要的麻烦和花费。
本文将介绍一些常见的汽车电子设备故障排除方法。
1. 检查电源供应:首先,确保车辆的电源供应正常。
检查电池是否连接良好、电池电量是否充足。
如果有任何电源供应方面的问题,如电池报废或连接不良,汽车的电子设备可能会出现各种故障。
2. 检查保险丝:保险丝是汽车电子设备中非常重要的一个组成部分,它们用于保护电路免受过载和短路的损害。
当电子设备失效时,检查保险丝是否熔断是排除故障的一种常见方法。
仔细检查电子设备相关的保险丝,如发动机控制单元(ECU)等。
如果发现保险丝熔断,及时更换相应的保险丝。
3. 检查电子设备的连接:电子设备的连接可能会因为松动或腐蚀而导致故障。
检查电子设备的连接器,确保它们紧固并且没有锈蚀。
如果发现连接问题,可以使用适当的清洁剂清洁连接器,并确保它们紧固。
4. 使用诊断工具:现代汽车配备的电子设备通常配备了诊断接口,可以使用专业的汽车诊断工具进行故障排查。
通过连接到汽车的诊断接口,可以读取故障码,并对故障进行更精确的诊断。
根据诊断结果,可以采取相应的修复措施。
5. 注意温度:有些汽车电子设备对温度敏感,过高或过低的温度可能会导致设备故障。
特别是在极端天气条件下,如高温夏季或寒冷冬季,电子设备容易受到损坏。
因此,在停放车辆时,尽量选择避免高温或寒冷的位置。
6. 寻求专业帮助:如果您不熟悉汽车电子设备的维修和故障排除,或者上述方法无法解决问题,建议寻求专业的帮助。
专业的汽车维修技师具有丰富的经验和知识,可以更好地诊断和修复问题。
综上所述,汽车电子设备故障排除需要综合考虑电源供应、保险丝、连接情况、温度等因素,同时可以使用诊断工具进行更精确的排查。
设备故障时的紧急应对策略和行动

设备故障时的紧急应对策略和行动策略概述设备故障是任何企业运作过程中可能面临的常见问题之一。
为了确保业务的连续性和最小化生产中断,制定紧急应对策略至关重要。
本文档旨在提供一些简单且没有法律复杂性的策略,以帮助企业在设备故障时做出适当的应对行动。
策略和行动1. 设备故障预防措施- 定期维护和保养设备,包括清洁、润滑和校准操作。
- 实施定期的设备检查和测试,以及记录设备状况和维修历史。
- 培训员工正确操作设备,遵循使用手册和操作规程。
2. 事前准备- 建立紧急联系人清单,包括设备供应商、维修服务提供商和其他相关部门的联系方式。
- 创建紧急应对计划,明确各个部门的责任和行动步骤。
- 贮备常用备件和关键零部件,以便在需要时进行更换。
3. 紧急应对行动- 立即通知相关人员,包括设备操作人员、维修人员和管理层。
- 根据紧急应对计划执行相应的行动步骤。
- 尽快评估设备故障的性质和严重程度,并采取适当的应对措施。
- 如果可能,尝试修复设备故障,或者联系维修服务提供商进行维修或替换设备。
- 在设备维修期间,尽量调配其他设备或资源,以确保生产持续进行。
4. 记录和评估- 记录设备故障的详细信息,包括故障原因、修复过程和所需时间。
- 定期评估设备故障的频率和模式,以识别潜在的长期解决方案。
- 分析设备故障对业务的影响,以及采取的应对措施的有效性。
- 根据评估结果,更新和改进紧急应对策略和行动计划。
总结设备故障时的紧急应对策略和行动是确保企业连续运营的关键要素。
通过预防措施、事前准备和快速应对行动,企业可以最小化设备故障带来的生产中断和损失。
同时,持续记录和评估设备故障情况,有助于改进和优化紧急应对策略,提高业务的稳定性和可靠性。
汽修中的车辆电子设备故障排障与更换
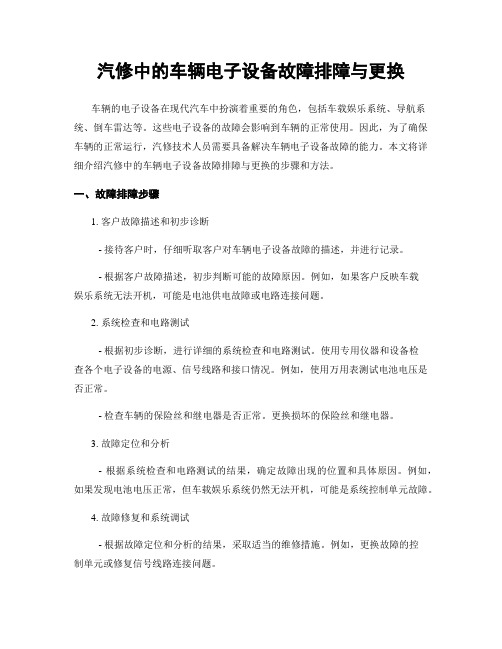
汽修中的车辆电子设备故障排障与更换车辆的电子设备在现代汽车中扮演着重要的角色,包括车载娱乐系统、导航系统、倒车雷达等。
这些电子设备的故障会影响到车辆的正常使用。
因此,为了确保车辆的正常运行,汽修技术人员需要具备解决车辆电子设备故障的能力。
本文将详细介绍汽修中的车辆电子设备故障排障与更换的步骤和方法。
一、故障排障步骤1. 客户故障描述和初步诊断- 接待客户时,仔细听取客户对车辆电子设备故障的描述,并进行记录。
- 根据客户故障描述,初步判断可能的故障原因。
例如,如果客户反映车载娱乐系统无法开机,可能是电池供电故障或电路连接问题。
2. 系统检查和电路测试- 根据初步诊断,进行详细的系统检查和电路测试。
使用专用仪器和设备检查各个电子设备的电源、信号线路和接口情况。
例如,使用万用表测试电池电压是否正常。
- 检查车辆的保险丝和继电器是否正常。
更换损坏的保险丝和继电器。
3. 故障定位和分析- 根据系统检查和电路测试的结果,确定故障出现的位置和具体原因。
例如,如果发现电池电压正常,但车载娱乐系统仍然无法开机,可能是系统控制单元故障。
4. 故障修复和系统调试- 根据故障定位和分析的结果,采取适当的维修措施。
例如,更换故障的控制单元或修复信号线路连接问题。
- 完成修复后,进行系统调试和功能测试,确保车辆电子设备恢复正常工作。
二、故障更换步骤1. 设备拆卸和安装- 根据故障的具体情况,拆卸需要更换的电子设备。
例如,拆卸损坏的车载娱乐系统。
- 安装新的电子设备。
确保设备安装牢固,接口连接正常。
2. 系统编程和配置- 部分电子设备更换后,需要进行系统编程和配置。
根据车辆制造商提供的信息,使用特定的设备和软件进行编程和配置操作。
例如,更换新的导航系统后,需要对系统进行编程,以适应特定车型的要求。
3. 功能测试和调试- 安装和配置完成后,进行功能测试和调试,确保新电子设备能够正常工作。
例如,测试车载娱乐系统的音频输出和触摸屏功能是否正常。
汽车电子设备故障排查与修复

汽车电子设备故障排查与修复在汽车维修领域中,电子设备故障排查与修复是一项非常重要且复杂的任务。
随着汽车技术的不断发展,车辆上的电子设备数量也越来越多,因此,了解如何准确检测和解决电子设备故障是汽车维修人员必备的技能之一。
本文将介绍汽车电子设备故障排查与修复的方法和步骤。
一、故障排查前的准备工作在开始排查汽车电子设备故障之前,我们需要做一些准备工作。
首先,我们需要了解车辆的电子系统,并熟悉相关的技术手册和电路图。
其次,我们需要使用适当的工具和设备,如多用途测试仪、示波器、故障代码扫描仪等。
最后,我们还需要确保自己具备一定的电子设备知识和经验,以便能够正确地解读故障代码和故障现象。
二、故障排查的步骤1. 收集故障信息在开始排查故障之前,我们需要与车主充分沟通,了解故障发生的具体情况。
车主通常会描述一些故障现象,如发动机启动困难、仪表盘异常显示等。
这些信息对我们进行故障排查非常重要,可以帮助我们缩小故障范围。
2. 进行系统诊断根据故障信息,我们可以根据经验判断可能出现故障的电子系统,并优先检查这些系统。
使用故障代码扫描仪可以帮助我们获取更多的故障信息。
扫描仪通常能够读取车辆电子控制单元中存储的故障代码,并提供相应的解决方案。
同时,使用示波器可以帮助我们检测电压和信号的波形,从而更准确地判断故障原因。
3. 检查相关元件和线路在诊断系统之后,我们需要进一步检查相关的元件和线路。
这包括检查传感器、执行器、继电器、电磁阀等元件的工作情况,以及检查线路是否存在断路、短路等问题。
使用多用途测试仪可以帮助我们对元件和线路进行测试,确保其正常工作。
4. 修复故障当确定了故障的具体原因后,我们可以进行修复工作。
修复的方法包括更换故障元件、修复断路和短路等问题,或者根据故障代码进行调整和设置。
根据故障的复杂程度,修复工作可能需要较长的时间和专业的知识。
5. 验证修复效果修复完成后,我们需要使用故障代码扫描仪和示波器再次测试系统,确保故障已经被彻底排除。
车身车间设备故障应急预案

一、编制目的为保障车身车间生产秩序的稳定,提高设备故障应急处理能力,降低设备故障带来的经济损失,确保员工生命财产安全,特制定本预案。
二、适用范围本预案适用于车身车间内各类设备发生的故障,包括但不限于生产线设备、检测设备、辅助设备等。
三、应急职责1. 车间主任(1)负责组织、协调、指挥设备故障应急处理工作;(2)向公司领导汇报故障情况及处理进展;(3)监督、检查应急处理措施的落实情况。
2. 设备主管(1)负责设备故障的初步判断和应急处理方案的制定;(2)组织抢修人员就位,确保应急工作的顺利开展;(3)对抢修后的设备进行检查,确保设备恢复正常运行。
3. 抢修人员(1)按照应急处理方案进行设备故障抢修;(2)严格遵守操作规程,确保自身及他人安全;(3)及时向上级汇报抢修进度。
4. 班组长(1)负责组织本班组人员参与设备故障应急处理;(2)加强班组安全教育培训,提高员工安全意识;(3)督促员工做好个人防护,确保安全作业。
四、应急处理流程1. 故障报警(1)设备发生故障时,操作人员应立即向班组长报告;(2)班组长接到报告后,立即向车间主任和设备主管报告。
2. 应急响应(1)设备主管根据故障情况,制定应急处理方案;(2)车间主任组织抢修人员就位,开展抢修工作。
3. 抢修实施(1)抢修人员按照应急处理方案进行设备故障抢修;(2)设备主管对抢修过程进行监督、检查,确保抢修质量。
4. 故障排除(1)设备故障排除后,进行试运行,确认设备恢复正常运行;(2)设备主管对抢修后的设备进行检查,确保设备安全可靠。
5. 信息报告(1)车间主任向公司领导汇报故障处理情况;(2)设备主管对故障原因进行分析,总结经验教训。
五、应急保障措施1. 建立设备故障应急处理队伍,定期进行培训,提高抢修人员的技术水平;2. 配备必要的抢修工具、备品备件,确保抢修工作的顺利进行;3. 加强设备维护保养,降低设备故障发生率;4. 完善应急预案,定期组织演练,提高员工应急处理能力。
整车总装不合格处理流程

整车总装不合格处理流程英文回答:The process for handling the non-conformance of the vehicle assembly involves several steps to ensure that the issue is addressed and resolved effectively.Firstly, when a non-conformance is identified during the vehicle assembly process, it is important to document the issue and notify the relevant personnel, such as the quality control team or the production manager. This can be done through a non-conformance report, which outlines the details of the issue, including the specific problem, the location of the non-conformance, and any relevant supporting documentation or evidence.Once the non-conformance report is submitted, the next step is to investigate the root cause of the issue. This involves analyzing the production process, examining the materials used, and reviewing any relevant procedures orwork instructions. The goal is to determine why the non-conformance occurred and identify any contributing factors. For example, if the non-conformance is related to a faulty part, the investigation may reveal that there was a problem with the supplier or the quality control measures for incoming materials.Based on the findings of the investigation, appropriate corrective actions can be developed and implemented. These actions may include rework or repair of the non-conforming vehicle, replacement of defective parts, or changes to the assembly process to prevent similar issues in the future. The corrective actions should be documented and communicated to the relevant personnel to ensure that everyone is aware of the steps to be taken.After the corrective actions have been completed, it is important to verify their effectiveness. This can be done through inspections, testing, or other quality control measures to ensure that the non-conformance has been resolved and that the vehicle now meets the required standards. The verification process should also bedocumented to provide evidence of compliance.In some cases, if the non-conformance is severe or cannot be resolved through corrective actions, the vehicle may need to be scrapped or reworked extensively. This decision should be made by the appropriate personnel, such as the production manager or the quality control team, based on the severity of the non-conformance and the feasibility of resolving the issue.Overall, the process for handling non-conformance in vehicle assembly involves documenting the issue, investigating the root cause, implementing corrective actions, verifying their effectiveness, and making decisions on further actions if necessary. This ensuresthat any non-conforming vehicles are addressed promptly and that the assembly process is improved to prevent similar issues in the future.中文回答:整车总装不合格的处理流程包括多个步骤,以确保问题能够得到有效解决。
车辆机械故障修补方案

车辆机械故障修补方案引言车辆在使用过程中可能会出现各种机械故障,这些故障会影响车辆的正常运行和安全性。
为了确保车辆能够及时修复并恢复正常运行,制定一份车辆机械故障修补方案是非常必要的。
目标本方案的目标是提供一套简单而有效的车辆机械故障修补策略,以保证车辆故障的及时修复和恢复。
修补流程1. 检查故障现象:当车辆出现故障时,驾驶员应立即停车,并仔细观察故障现象。
2. 诊断故障原因:根据故障现象进行初步判断,并采取相应的诊断方法,以确定故障原因。
3. 寻找修补方案:在确定故障原因后,查找车辆操作手册或咨询专业人士,找到适当的修补方案。
4. 修补车辆:根据修补方案,采取相应的修补措施,修复车辆故障。
5. 测试修补效果:修补完成后,进行相关测试,确保车辆故障得到彻底解决。
6. 定期保养维护:定期进行车辆保养维护,以降低故障发生的概率。
故障分类常见的车辆机械故障可以分为以下几类:1. 发动机故障- 熄火- 抖动- 转速不稳2. 传动系统故障- 换挡困难- 噪音异常- 齿轮滑动3. 制动系统故障- 刹车失灵- 刹车不灵敏- 刹车异响4. 电气系统故障- 灯光闪烁- 电瓶电压低- 电路短路修补机制根据车辆故障的不同,采取相应的修补机制,常用的修补方式有:1. 更换故障零部件:对于一些机械故障,需要更换受损的零部件,以恢复车辆的正常运行。
2. 修理故障零部件:对于一些可以修理的故障零部件,可以进行修理,以降低维修成本。
3. 调整机械部件:对于一些调整不当或松动的机械部件,可以调整其紧固度或位置,以消除故障现象。
总结车辆机械故障修补方案是确保车辆正常运行和安全性的重要措施。
通过制定明确的修补流程和修补机制,可以有效提高故障修复的效率和准确性,保障车辆用户的出行安全。
汽车维修过程设备安装检修的问题及解决对策

汽车维修过程设备安装检修的问题及解决对策汽车维修过程中设备安装检修的问题非常重要,因为设备的正确安装和定期检修对于汽车维修的质量和安全至关重要。
以下是一些常见的问题以及相应的解决对策:问题1:设备安装不正确解决对策:确保设备的正确安装非常重要。
对于每一种设备,必须按照制造商的指南来进行安装。
使用专业的工具和设备来完成安装过程,确保每个零件都安装到正确的位置并牢固固定。
在安装完成后,进行一次全面测试,确保设备的功能正常。
问题2:设备安装后不起作用解决对策:如果设备安装完成后没有正常工作,可能是由于多种原因引起的。
检查电源连接是否正确。
然后,检查设备的控制面板和开关是否处于正确的位置。
如果这些都没有问题,可能是设备自身出现故障。
在这种情况下,需要进行更详细的故障排除,并根据设备制造商的指南进行修理或更换。
问题3:设备定期检修不及时解决对策:设备的定期检修非常重要,可以帮助发现潜在的故障并及时修理,从而避免由于设备故障引起的问题。
解决这个问题的最佳方法是建立一个定期检修计划,并确保严格按照计划进行检修。
在检修过程中,对设备进行全面的检查,包括清洁、润滑、更换磨损部件等。
如果发现任何问题,立即采取措施进行修理或更换。
问题4:设备维修困难解决对策:有时候,由于设备的复杂性或特殊性,可能会导致设备维修变得困难。
解决这个问题的关键是培训和提供合适的工具和设备。
确保维修人员接受了专业的培训,并了解设备的使用和维修方法。
提供适当的维修工具和设备,以便维修人员能够更方便地进行维修工作。
与设备制造商建立良好的合作关系,并及时获得技术支持和备件供应。
探究汽车行业生产线设备故障处理手段

探究汽车行业生产线设备故障处理手段摘要:现阶段人们对生活的品质要求越来越高,追求生活的高质量也就造成了汽车行业的飞速发展。
为了满足人们日益迫切的需求,大量生产汽车也就势不可挡。
但是在自动化生产过程中,设备故障问题会时长发生,这就导致了生产过程受阻,本文以变频器设计上存在的不足、焊接机器人设备故障及其处理方式、玻璃涂胶机器人的改进三个方面来讨论汽车生产线设备故障的一些处理方法,关于汽车生产线设备做一些浅显的说明。
关键词:汽车行业;生产线;故障;处理手段引言随着时间的推移汽车生产线上的设备故障发生的几率逐渐增大,这样的现象对汽车的生产效率产生了一定的影响。
故障产生的原因有人为故障和自然故障两种,而这两种故障只是产生的主体不同,其都是由于操作不当导致的问题。
人为操作不当导致的故障问题容易解决,自然故障的处理就会显得错综复杂。
一、生产线上的变频器故障类型及处理对策的设计存在着一定的问题在汽车有关构件的生产车间中,对于涂装车间来讲,其主要是挂在某一个特定网络上的变频器,在涂装车间移动辊床均使用变频器驱动电机传动,在实际设备维修中,遇到最多的是进口变频器。
如三星、ABB、AB、西门子等厂家,故障类型一种为自动运行过程中频繁出现的自动停机现象,并伴随着一定的故障显示代码,这类故障一般是由于变频器运行参数设定不合适或外部环境造成,可现场修复;另一类是由于使用环境恶劣,导电粉尘引起的路,这类故障发生后,变频器内部元器件多为发生短路或者烧坏,其处理方法是先对变频器解体检查,重点查找损坏件,进行清理、测量、更换,然后全面测试,空载试运行,观察运行状况,再进行加载试运行。
在本次探讨实际生产过程中遇到的西门子 G120 系列变频器为例,这种变频器在使用一段时间之内会出现损坏的现象,有时会有几台变频器出现故障的现象,西门子变频器 SINAMICS G120 在出现报警或者故障时会显示到操作面板上。
如在实际生产过程中遇到的F30021 接地报警,电机出现蜂鸣声,无法运转,首先检查变频器参数是否有人改动,使用交换法测试,是否为机械原因造成变频器故障,电机抱闸是否打开、电缆是否破损,检查均未发现异常,经初步断定为变频器功率器件故障。
汽车生产总装车间设备管理流程缺陷与解决办法
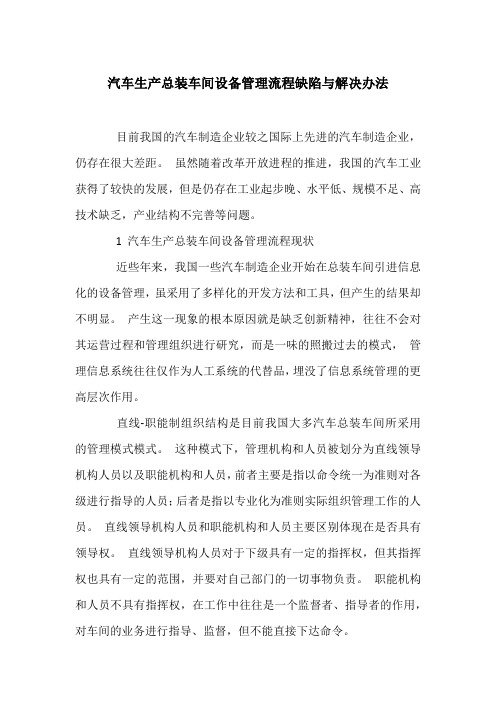
汽车生产总装车间设备管理流程缺陷与解决办法目前我国的汽车制造企业较之国际上先进的汽车制造企业,仍存在很大差距。
虽然随着改革开放进程的推进,我国的汽车工业获得了较快的发展,但是仍存在工业起步晚、水平低、规模不足、高技术缺乏,产业结构不完善等问题。
1 汽车生产总装车间设备管理流程现状近些年来,我国一些汽车制造企业开始在总装车间引进信息化的设备管理,虽采用了多样化的开发方法和工具,但产生的结果却不明显。
产生这一现象的根本原因就是缺乏创新精神,往往不会对其运营过程和管理组织进行研究,而是一味的照搬过去的模式,管理信息系统往往仅作为人工系统的代替品,埋没了信息系统管理的更高层次作用。
直线-职能制组织结构是目前我国大多汽车总装车间所采用的管理模式模式。
这种模式下,管理机构和人员被划分为直线领导机构人员以及职能机构和人员,前者主要是指以命令统一为准则对各级进行指导的人员;后者是指以专业化为准则实际组织管理工作的人员。
直线领导机构人员和职能机构和人员主要区别体现在是否具有领导权。
直线领导机构人员对于下级具有一定的指挥权,但其指挥权也具有一定的范围,并要对自己部门的一切事物负责。
职能机构和人员不具有指挥权,在工作中往往是一个监督者、指导者的作用,对车间的业务进行指导、监督,但不能直接下达命令。
这种直线-职能组织机构是一种金字塔结构,从本质上讲是一种分散维修。
董事会或厂长处于金字塔的最顶端,其隶属部门主要就是设备动力处也称机动处,对企业设备进行宏观的综合管理,采取监督下级单位工作的方式来替代直接管理的方式。
下级部门并不对设备动力部负责,而是接受其直属领导的命令,并对其负责,而设备动力部在这一过程仅仅发挥监督指导作用。
工作组,负责各项工作的实际开展,位于金字塔的最底层。
2 这种组织结构存在的主要弊端(1)纵向层级设置过多,反应速度慢,信息的真实性很难保证。
如设备出现故障需要处理,就会经过一个冗杂的处理程序。
首先由车间的维修工人进行最初步的判断,若能维修就可以直接内部解决,但是维修工若处理不了就需要技术维修人员,技术维修人员首先要确定设备是否在保修期内,若在保修期内则直接联系厂家进行维修,若保修期已过就要判断维修等级,即是需要大修还是局部处理。
车身车间设备故障应急预案

车身车间设备故障应急预案一、引言车身车间是汽车制造企业中的关键生产环节,其中的设备故障对生产效率和产品质量有着直接的影响。
为应对设备故障对生产造成的影响,制定并实施一套有效的应急预案非常重要。
本文档旨在提供车身车间设备故障应急预案,以应对突发情况并最大限度地减少生产中断。
二、预案制定的目的1.有效减少设备故障对生产造成的影响。
2.提高应急响应的效率,尽快恢复生产。
3.确保生产过程中的安全。
三、预案内容3.1 设备故障的分类设备故障可分为以下几种类型:1.机械故障:包括设备损坏、磨损、断裂等;2.电气故障:包括电路短路、电源故障、电机故障等;3.传感器故障:包括传感器失效、读取错误等;4.控制系统故障:包括程序错误、通信故障等。
3.2 应急预案的实施步骤在设备故障发生时,按下述步骤进行应急预案的实施:步骤一:报警与人员安全1.设备故障发生后,首先需立即按设备报警系统进行警示,并将故障信息反馈给工作人员。
2.在确保人员安全后,尽快停止相关设备的运行,防止二次事故的发生。
步骤二:故障定位与分析1.快速定位故障点,并评估故障的影响范围。
2.利用故障诊断设备进行故障分析,找出故障原因和可能的解决方案。
步骤三:紧急维修与备件更换1.根据故障的严重程度,及时启动紧急维修计划,派遣专业人员进行维修。
2.准备常用备件,并在需要时进行更换,以最快速度恢复设备运行。
步骤四:恢复生产1.维修工作完成后,进行必要的测试与验证。
2.根据生产计划,逐步恢复设备的正常运行,并确保产品质量。
3.3 预案的组织与协调为有效实施预案,需要明确预案的组织与协调机构:1.预案组织机构:设立应急预案组织领导小组,并明确各组成员的职责和权限。
2.预案协调机构:成立由相关部门负责人组成的预案协调小组,负责协调预案的执行和推广。
3.4 预案的演练与修订为确保预案的可行性与有效性,应定期进行演练和修订:1.演练计划:制定年度演练计划,包括演练时间、内容和参与人员等。
汽车维修过程设备安装检修的问题及解决对策

汽车维修过程设备安装检修的问题及解决对策1. 设备安装不准确设备安装不准确是汽车维修过程中常见的问题之一。
可能是由于操作人员对设备的使用方法不熟悉,或者是设备本身存在缺陷造成的。
解决对策:- 培训提升:加强对操作人员的培训,提高其对设备的使用方法和安装要求的理解。
包括提供设备操作手册、培训课程等。
- 设备校准:定期对设备进行校准,确保其安装的准确性。
同时设备使用前应进行检查,确保设备没有缺陷。
2. 设备维护不及时设备的维护保养对于保证设备正常运行至关重要。
然而在汽车维修过程中,由于工作繁忙、维护意识不足等原因,可能导致设备的维护保养不及时。
解决对策:- 维护计划:制定设备维护计划,明确设备维护的时间、内容和责任人。
根据设备的使用频率和工作环境,制定相应的维护频率和维护内容。
- 定期检查:定期对设备进行检查,及时发现设备的故障和问题。
确定维修方案,保证设备的及时修复。
- 设备保养记录:建立设备的保养记录,对设备的维护情况进行记录和跟踪。
可以通过这些记录来评估设备的维护情况,并及时调整维护计划。
3. 设备检修能力不足对于一些复杂设备的检修,操作人员可能存在技术能力不足的问题。
这会影响设备的正常使用,并增加维修过程中潜在的风险。
解决对策:- 技术培训:加强对操作人员的技术培训,提升其设备检修的专业技术能力。
可以通过请专业教师进行培训、组织内部技术培训班等方式来提高操作人员的技术能力。
- 多人合作:对于一些复杂设备的检修,可以采取多人合作的方式,充分发挥各个人员的专业能力。
可以避免因为个人能力不足导致的问题。
汽车维修过程中设备安装检修的问题及解决对策主要涉及设备安装不准确、设备维护不及时和设备检修能力不足等方面。
通过加强培训提升、设备校准、制定维护计划、定期检查、设备保养记录、技术培训和多人合作等措施,可以解决这些问题,提高汽车维修过程中设备的安装检修质量。
车辆总成修理方案

车辆总成修理方案车辆总成是汽车的核心部件,包含发动机、变速器、传动系统等多个部件。
随着汽车车龄的不断增加和使用频率的提高,车辆总成出现故障的情况也越来越普遍。
在这种情况下,为了保证车辆的正常运转和安全性,及时进行修理就显得尤为重要。
检修前的预备工作在进行车辆总成修理之前,需要进行一些必要的预备工作,以免造成不必要的损失和延误。
以下是一些必要的预备工作:1. 确定修理方案在进行检修之前需要确定车辆总成的具体故障原因,并设计出一套系统的修理方案,包括选择使用的备件类型、需要进行的维修步骤以及时间和费用的估算等。
2. 准备检测工具必要的检测工具包括万用表、引擎转速表、压缩计、燃油压力计等,这些工具的使用需要熟练掌握,以保证检测结果的准确性。
3. 确认备件库存在进行车辆总成的修理时,需要使用到多种备件,事先确认备件库存,以免发生备件短缺的情况。
车辆总成常见故障及修理方案1. 发动机无法启动当车辆发动机无法启动时,可能出现的原因包括电路故障、点火系统故障、供油系统故障等。
对于这种情况,可以采取如下的修理方案:•检查电路,确认无故障;•检查点火系统,包括点火塞、线圈、点火开关等,以确定是否有故障;•检查供油系统,包括燃油泵、油路、喷油嘴等,以确定是否存在故障。
2. 发动机抖动或噪音过大当发动机出现抖动或者噪音过大的情况时,通常是由于气缸、曲轴、连杆等发动机部件出现故障所导致的。
在这种情况下,可以采取如下的修理方案:•对发动机进行检测以确认出现故障的具体部件;•更换有问题的部件或者整块更换发动机;•在更换之前,需要先进行大量测试,以确保故障已经得到有效解决。
3. 变速器顿挫或异响当车辆在行驶途中出现顿挫或异响时,通常是由于变速器的摩擦材料磨损或者液压系统故障所导致的。
对于这种情况,可以采取如下的修理方案:•更换变速器摩擦片;•更换变速器内部的O形密封圈等液压元件;•更换变速器油,确保选用正确类型的变速器油。
4. 制动失灵当车辆制动失灵时,可能是由于制动系统出现故障所导致的。
汽车制造工厂装配线故障演练方案

汽车制造工厂装配线故障演练方案近年来,汽车行业快速发展,汽车制造工厂扮演着至关重要的角色。
然而,装配线故障常常会导致生产延误和经济损失。
为了提高工厂的效率和应对装配线故障,制定一个有效可行的演练方案至关重要。
本文将介绍一个综合的汽车制造工厂装配线故障演练方案,旨在提高工厂的应急响应能力和故障排除能力。
一.方案目标本方案的目标是通过演练提高装配线故障的应急响应能力和故障排除能力,减少生产中断时间,降低经济损失,并确保汽车的生产质量和生产效率。
二.方案内容1.制定演练计划演练前,需要制定详细的演练计划,包括演练时间、参与人员、演练内容、演练目标等。
演练计划需要事先与各部门协商,确保各方的积极配合和支持。
2.明确演练场景根据实际情况制定不同的演练场景,包括装配线故障类型、故障严重程度以及发生故障的位置等。
演练场景应真实反映可能出现的故障情况,并结合历史故障案例进行分析。
3.演练参与人员培训在演练开始前,需要对参与人员进行相关培训,提高其对装配线故障的认知和应急响应能力。
培训内容可以包括故障排除流程、操作规范以及紧急情况下的安全措施等。
4.模拟故障发生在演练中,需要模拟装配线故障的发生,例如断电、电路短路、机械故障等,并设置不同的故障严重程度和发生频率。
通过模拟故障的方式,可以检验工厂的应急响应能力以及故障排除流程的有效性。
5.实时监控和记录在演练过程中,需要对各种操作和故障排除情况进行实时监控和记录,包括人员反应时间、故障排除时间以及操作规范的执行情况等。
这样可以对演练效果进行评估,并为后续改进提供参考依据。
6.总结和改进演练结束后,需要对演练中发现的问题进行总结和分析,并提出改进措施。
这些改进措施可以包括流程优化、设备升级以及人员培训等,旨在提升工厂的装配线故障应对能力。
三.方案意义1.提高装配线故障应急响应能力通过演练,工厂的员工可以更加熟悉装配线故障的应急响应流程,提高其应对紧急情况的能力和效率。
- 1、下载文档前请自行甄别文档内容的完整性,平台不提供额外的编辑、内容补充、找答案等附加服务。
- 2、"仅部分预览"的文档,不可在线预览部分如存在完整性等问题,可反馈申请退款(可完整预览的文档不适用该条件!)。
- 3、如文档侵犯您的权益,请联系客服反馈,我们会尽快为您处理(人工客服工作时间:9:00-18:30)。
摘要:在一条德系一分钟节拍汽车装配流水线上,大约分布着四十余台工艺设备,标准工况下的统计数据表明,由这些工艺设备的故障造成的停产维修工时约占整体停产工时的35%。
采用一种设备故障综合处理方案,通过工艺设备镜像化,故障信息参数代码化,维修方案算法化,执行过程标准化等技术改造,大幅提升设备故障处理效率,显著降低故障停产工时。
关键词:工艺设备镜像化故障分析中图分类号:TP277文献标识码:BDOI :10.19710/ki.1003-8817.20180206汽车总装领域设备故障综合处理方案陈恪毅(一汽-大众汽车有限公司,长春130011)作者简介:陈恪毅(1987—),男,工程师,研究生学历,从事总装工艺规划工作。
1前言自动化是汽车制造工业4.0的必然途径,伴随自动化水平的提升,工厂内会出现越来越复杂的工艺设备。
如何让这些工艺设备最优效率的运转,发挥出最大的价值,非常考验维修体系的运转效能。
在现有工作模式下,维修工的经验和技能熟练度,决定了一个工厂维修水平的高低。
如何能够减少这种依赖,如何能够让复杂的维修工作变得简化,从根本上提高维修效率,这就要依赖于大量的计算机介入以及信息化植入,将维修工作合理分解。
以下提出了故障综合处理的详细方案。
2总体信息流方案设备发生故障之后,首先要快速确定故障原因,系统才可以高效率的处理及反馈故障。
依靠工业以太网和无线网络建立的信息采集、处理、分析、反馈、控制模块,共同形成了故障处理方案的综合通讯架构。
设备故障发生后的信息流与处理系统的通讯架构示意如图1所示。
2.1Server 端信息流并网的工艺设备,将采集或监控的参数信息,以实时数据的形式存入到通用读写模块中,一旦图1总体信息流向图设备故障智能处理系统机构图及信息流向图ServerPC共享维修自行车模式结合GPSPLC1PLC2PLCn VD1VD2VDn内置算法:1.技能等级选择2.工具包选择3.耗材4.耗时选择RE1RE2REn VR1VR2VRn通用读写模块且地址连续1.提示维修步骤(声音结合图像)2.远程连线指导操作发生参数异常,异常发生时点的参数信息将被记录下来,并存入到单独的栈中,Server将每20s访问一次通用读写模块,并优先访问异常参数的栈,Server将异常参数与故障清单中编译好的参数比对,以此确认故障信息,同时Server将调用视频监控信号,进一步确认故障状态,当故障信息确认之后,Server将故障代码发送给PC。
2.2PC端信息流PC获得Server发出的故障信息后,就要根据维修工位置,维修工当前任务状态,耗材位置,路径耗时等信息,按照算法得出的结果来分配维修任务以及制定行动路径,并将以上信息发送给到维修工佩戴的手环上,并将具体的维修步骤下载到维修工的AR眼镜中,同时处理VR远程连线指导的请求,当PC获得手环反馈的维修任务完成信号时,PC将此请求发送给Server,由Server根据设备参数信息及视频监控信息给予确认。
如确认,则将故障消除,并直接发送确认信息给该维修工手环;如故障未消除,则通过现场的监控摄像头发出声音提示。
3总体硬件方案3.1Server端组件a.制作并维护每台并网工艺设备的故障清单,故障清单的要求是所有特征信号与故障一一对应,故障清单的形式如表1。
对于新出现的故障,在处理完成之后,协助维修将故障更新到故障清单中,并固化处理步骤。
b.针对每台并网工艺设备提供两套(一用一备)故障信息读取模块,并配合各个工艺设备供应商完成相关的通讯设置,供应商须保证一次读取的时间为20s以内,并将读取到的信息反馈给Server。
c.在每个工艺设备区域标高以上位置(3M)配备高清摄像头,可以旋转,并可以接受语音传输,要求能够覆盖整个设备区域,且直接观察没有死角,即至少每台设备需配备两个摄像头,具体数量以全覆盖为准,该摄像头可选有线或无线,但必须可以支持2.4/5G两种通信网络。
d.在Server端完成与维修PC的通讯设置,并提供Server的热备份硬件。
3.2PC端组件a.制作维修技能等级列表,标准工具包列表,耗材列表,为后续算法实现提供源数据。
b.在维修覆盖的工艺设备空间范围内,配备相应的硬件,要求能够实时反馈佩戴信号发生终端的载体(维修工,维修用自行车)的具体位置,并且能够将位置信息反馈到PC。
c.提供专用的维修用自行车,并安装定位组件及智能锁。
d.以整个维修过程耗时最短为优化目标,根据维修工的技能等级、维修工的位置、故障设备位置、行动路线、工具包位置、耗材位置、现行任务情况等信息综合计算,给出最符合目标的维修工和维修路径,并应用组态软件或Labwindows(Lab⁃view)开发相对应的管理界面。
e.提供适合维修用的AR眼镜和手环,其中VR 眼镜将获得的设备状态反馈给PC,PC端发送故障信息和处理步骤,以声音和图像配合的方式辅助维修工完成操作过程;当出现复杂问题时,VR眼镜也可以与PC直接连线,获得PC端的远程指导;其中手环的作用是提醒维修工当前维修任务状态以及当故障处理完成时,以手环为发送载体,反馈处理信息给PC,故障处理过程闭环。
f.在PC端完成与Server的通讯设置,并提供PC的热备份硬件。
3.3通讯a.Server与PLC的通讯这部分通讯是由Server访问固定IP地址下的各PLC专用读取模块来实现的,其中通讯协议可采用TCP或Profinet,通讯类型为工业以太网,专用读取模块与PLC主单元的通讯可采用串口或并处理步骤口,根据各个工艺设备的实际情况确定。
对每个并网设备,Server每20s读取一次读取模块中的数据,专用读取模块应满足记录异常参数,实时获得参数的要求,要求使用西门子PLC专用的数据采集读取模块,且地址连续。
b.Server与Video的通讯根据Video的具体品牌和类型,赋予其固定IP,同时在Server端配置相应的监控界面,这个监控界面应作为人机界面的一个插件存在,即不实时显示和获取数据,一旦获得Video需求信号,则访问该IP,同时以插件界面的形式显示在人机界面中。
此外,该通讯应支持双向的语音传输,在Server和Video端都应配置相关的硬件。
4PC内置最优化算法4.1算法前提a.工具包不允许在维修工之间直接交换;b.一旦确定维修工行动路径后,所需元素会通过系统来准备;c.维修工行动路径不允许穿越生产线线体;d.如果任务中的维修工通过手环反馈无法在标准耗时内完成当前任务,则反馈给PC重新计算任务安排;e.如果发生突发情况,如网络传输问题,人员生理状况等导致任务无法发送或任务中断,或根据预计时间维修工没有到达指定故障位置,则由PC重新计算并安排维修工。
4.2算法要求在该算法下,要求考虑维修工位置(手环)、工具包类型、工具包位置、耗材类型、耗材位置、故障标准耗时,维修专用自行车位置这些影响因子,来求解从故障发生直到故障解除的最短反应时间,制定出详细的行动路径供维修工使用,对于40名维修工,50台设备的预设需求,须满足不超过10s 的计算时间。
4.3平面布局在图2的平面布局示例中,展示了维修基地,材料库,不同工艺设备以及操作工的位置信息,以此为例,综合上述信息详细说明维修方案的形成过程。
在故障清单中,对每一种故障的处理都有针对性的耗材说明,耗材存放在材料库中,当维修任务下达到维修工后,相关耗材的准备任务也下达到材料库,如因耗材缺少导致维修任务无法完成时,材料库将相关信息反馈给Server。
a.标准耗时根据统计数据和实测数据,将所有故障的处理过程细化并赋时,形成标准耗时。
b.工具包根据故障处理的不同类型,供应商将维修工具包编成若干种标准工具包,在每个工具包上应做好二维码标记,每次取用时使用手环扫码,从而确定临时监管人,并根据使用频次来确定每种工具包的储备数量,工具包中的具体工具类型应满足维修提出的具体要求,且能够保持合理的尺寸和重量,便于随身携带,其功能应至少涵盖电气测试,一般性修理,通用更换等。
c.维修专用自行车该自行车应具备GPS定位组件、智能锁、多用途外接充电接口,其中GPS定位组件作为信号发射端,向处理器实时发送自身所处的位置(精确到工位5.6m);智能锁的作用是只接受PC发送的任务安排及对应的手环扫码才可以解锁;自行车应在可靠位置放置一块10A·h以下的电瓶,平时用来向GPS组件、智能锁提供电能,必要时可以通过外接口对外充电,如向大型测量工具,调试用直流电等。
整车重量不超过45Kg,载荷不低于图2平面布局示例维修基地BA1BA2BA3BA4材料库100Kg。
d.手环手环由维修工工作期间佩戴,开始工作前由维修主管分配手环并扫描个人二维码绑定,结束工作后再次扫码解除绑定。
手环应可接收PC发出的任务信息,也可以向PC发出接收任务或任务中断或无法执行任务等信息,同时作为与维修工的绑定体,手环应实时向PC反馈位置信号,同时手环也是记录维修处理过程的计时器。
手环应具备以下特性,防水、绝缘、轻便(不超过40g)防磨的显示屏,体温充电,支持2.4/5G 网络。
e.AR眼镜AR眼镜由维修工在进行相对复杂的维修工作时佩戴,非工作状态下存放在维修基地,处理故障表内的故障时,维修工在固定位置佩戴AR 眼镜后,会出现每一步的维修步骤及对应位置,同步带有语音提示,这就要求AR眼镜内,要提前下载好最新状态的设备形态和状态,每一步的维修步骤结束后,都会有相应的变化提示和语音提醒。
当处理故障表外的故障时,AR眼镜可以起到记录维修过程影像的作用,同时AR影像同步投放到PC显示屏上,接受远程连线维修指导,此时AR眼镜应具备双向的语音传输功能。
当维修步骤结束,但AR没有响应时,应允许手动处理,进入到下一步。
AR眼镜的内存不低于16GB,语音图像信号传输效率不低于500kb/s,整体重量不高于1Kg。
4.4算法结构算法由图3的主结构算法和图4的耗时计算算法组成,其输出结果即为某一故障在某一时段内的最佳维修方案。
5对工厂智能化的影响本文所述的设备故障处理系统,以汽车装配车间为应用样例,面向的是广阔的工业市场,自动化程度越高的工厂,越能体现出这一系统的价值。
以自动化为基础,以物联网和信息化为媒介,结合自身的算法机构,将工厂中的维修工作充分智能化,并且与库房管理、生产线紧密协作,大大降低总装车间的运行成本,提高了维修效率。
图3主机构算法图4耗时计算算法耗时计算模块表外故障故障发生故障类型主结构表内故障维修工状态空闲维修工任务中维修工是否有耗材是否有耗材是否用工具是否用工具耗时计算模块1耗时计算模块2下发维修任务NYYYYNN N耗时计算模块获得各维修工位置获得故障设备位置获得各自行车位置维修工状态表内故障表外故障空闲维修工空闲维修工任务中维修工计入当前任务剩余耗时并额外计入当前任务标准耗时的30%计算所有可行方式和路径求取总耗时最少的两个维修工和路径计算所有可行方式和路径求取总耗时最少的维修工和路径。