最终检验程序
过程及最终检验和试验控制程序

过程及最终检验和试验控制程序一、目的保证所有产品在生产过程中都通过规定的检验后才进入下一道工序或入仓。
二、适用范围本程序适用于公司内所有正在生产的在制品、半成品、成品。
三、职责3.1 生产部负责自检工作,并同品管部一道做好首件检查。
3.2 品管部负责巡回检查、检验工序的检查、半成品、成品的检验。
四、作业程序4.1 过程检验4.1.1 首件检查a. 在规定要进行首件检查的工序,每班次开始或生产过程因换人、换料、换品种以及换工装、设备调整等改变工序条件后生产的1-3 件产品,操作者自检后,还必须送IPQC质检员做首件检查,首件检查结果于“首件检验记录表”中。
IPQC首件检查合格后送FQC检查,并将结果于“首件检验记录表”中。
b. 首件检查合格时,由质检员在首件上作首件标记并通知操作者继续作业。
首件检查不合格时,质检员向操作者指出不合格部位,要求其改进。
操作返工或重新加工首件,直到检验合格,方可继续生产。
4.1.2 自主检查生产车间作业员要在生产中进行自主检验。
有规定时,应将自主检验的结果记入“自主检验记录表”或其他相应的记录表中。
自主检查中作业员如发现产品质量时,应及时停止作业,并向领班/组长报告,寻求改善对策。
4.1.3 巡回检验a. 五金、塑料车间的QC 质检员(IPQC)按《五金产品检查作业指导书》/《塑料产品检查作业指导书》、《品管部巡检管理规定》的要求对各机台进行巡查并作好“QC 巡查记录表”。
巡查时不仅应按规定抽查产品,而且应观察作业者的作业方法及设备、工装、量具使用等方面的情况。
如发现问题应及时指导作业者或联系有关人员加以纠正。
巡查中发现的不合格品应做好标记并适当隔离。
b. 品管部IPQC在装配、插件生产线进行巡回检查,观察车间的员工是否按规定的作业方法操作,使用的生产物料是否正确,设备、工装、量具是否处于受控状态,并随时对有疑点的工位进行抽检。
IPQC应及时将发现的问题通知生产车间的组长,必要时通知车间主管,以便调整生产。
最终检验和试验控制程序

对检验不合格的产品, 按不合格品的控制程序处理;
对在生产过程中出现漏检现象的产品,不允许进行成品最终检验和试验;
返工后的成品必须按正常检验程序检验合格后,才能办理入库手续;最终检验后的合格产品与不合格产品,依据检验和试验状态控制程序作好标识;
1.目的:
为保证入库的产品满足规定的质量要求;
2.适用范围:
产品入库前的最终成品检验;
3.职责
工程部负责最终成品的质量检验,防止不合格品出货;
工程部负责制定最终检验标准;
4. 定义:无
5.工作程序
车间在产品生产完毕后,质检员按检验规范进行检验,合格产品填写合格证后入待验区;
工程部按产品最终检验规范对每批产品进行成品最终检验和试验;
入库单
批准
审核
编制
日期
日期
日期
质检员根据检验和试验结果作好最终检验记录,并将判定结果报工程部负责人审核;
对于本公司暂无能力检验和试验之项目,由工程部联系国家法定检测部门作检验和试验,并取回有关检验和试验报告;
6. 相关文件和记录
Q/BFB不合格品控制程序
Q / BFC- 006 - 2003成ቤተ መጻሕፍቲ ባይዱ检验规程
BF/QJ - 052 出厂检验报告
最终检验和试验程序
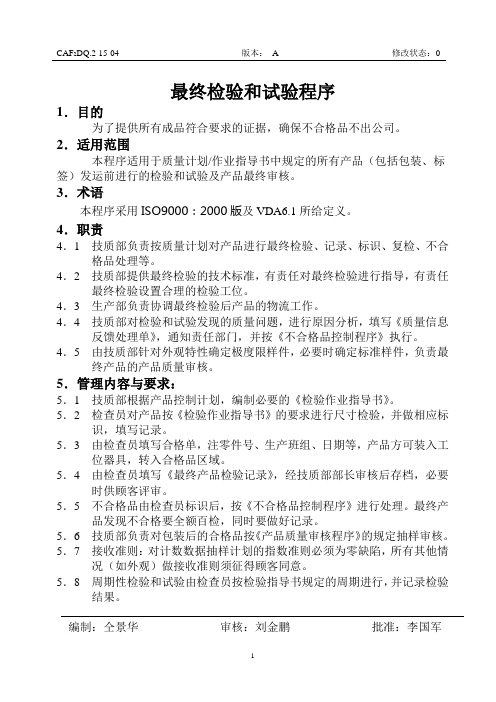
CAF2DQ.2-15-04 版本:A 修改状态:0最终检验和试验程序1.目的为了提供所有成品符合要求的证据,确保不合格品不出公司。
2.适用范围本程序适用于质量计划/作业指导书中规定的所有产品(包括包装、标签)发运前进行的检验和试验及产品最终审核。
3.术语本程序采用ISO9000:2000版及VDA6.1所给定义。
4.职责4.1 技质部负责按质量计划对产品进行最终检验、记录、标识、复检、不合格品处理等。
4.2 技质部提供最终检验的技术标准,有责任对最终检验进行指导,有责任最终检验设置合理的检验工位。
4.3 生产部负责协调最终检验后产品的物流工作。
4.4技质部对检验和试验发现的质量问题,进行原因分析,填写《质量信息反馈处理单》,通知责任部门,并按《不合格品控制程序》执行。
4.5 由技质部针对外观特性确定极度限样件,必要时确定标准样件,负责最终产品的产品质量审核。
5.管理内容与要求:5.1 技质部根据产品控制计划,编制必要的《检验作业指导书》。
5.2检查员对产品按《检验作业指导书》的要求进行尺寸检验,并做相应标识,填写记录。
5.3由检查员填写合格单,注零件号、生产班组、日期等,产品方可装入工位器具,转入合格品区域。
5.4由检查员填写《最终产品检验记录》,经技质部部长审核后存档,必要时供顾客评审。
5.5不合格品由检查员标识后,按《不合格品控制程序》进行处理。
最终产品发现不合格要全额百检,同时要做好记录。
5.6技质部负责对包装后的合格品按《产品质量审核程序》的规定抽样审核。
5.7接收准则:对计数数据抽样计划的指数准则必须为零缺陷,所有其他情况(如外观)做接收准则须征得顾客同意。
5.8周期性检验和试验由检查员按检验指导书规定的周期进行,并记录检验结果。
编制:仝景华审核:刘金鹏批准:李国军6.相关支持性文件6.1不合格品控制程序6.2最终检验指导书7.质量记录7.1 最终产品检验记录7.2 试验报告7.3 废品通知单7.4 合格单7.5 返修单文件更改记录。
2. 最终成品(FQC品管)检验流程
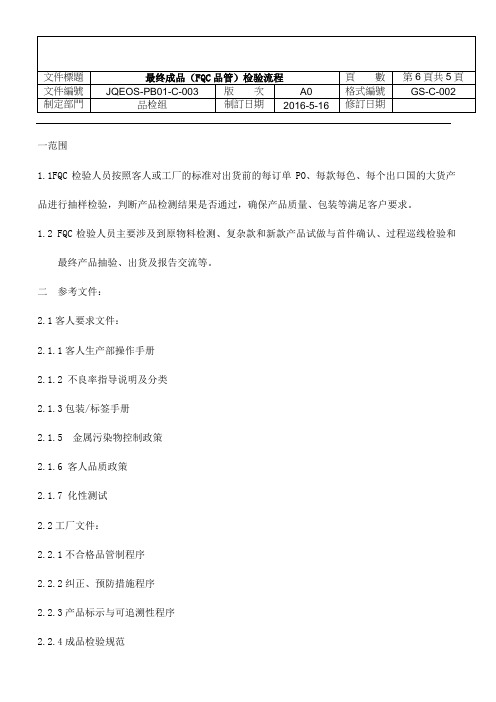
一范围
1.1FQC检验人员按照客人或工厂的标准对出货前的每订单PO、每款每色、每个出口国的大货产品进行抽样检验,判断产品检测结果是否通过,确保产品质量、包装等满足客户要求。
1.2 FQC检验人员主要涉及到原物料检测、复杂款和新款产品试做与首件确认、过程巡线检验和
最终产品抽验、出货及报告交流等。
二参考文件:
2.1客人要求文件:
2.1.1客人生产部操作手册
2.1.2 不良率指导说明及分类
2.1.3包装/标签手册
2.1.5 金属污染物控制政策
2.1.6 客人品质政策
2.1.7 化性测试
2.2工厂文件:
2.2.1不合格品管制程序
2.2.2纠正、预防措施程序
2.2.3产品标示与可追溯性程序
2.2.4成品检验规范
2.2.5计数值抽样计划使用准则
三术语和定义:
3.1检验标准:
3.1.1业务员(含)以上干部签名确认的样包或顾客提供的样品、原物料确认卡、订单通知与反馈单、顾客原始订单、工艺单、包装资料。
3.1.2生产副总签名确认的《成品检验规范》、《计数值抽样计划使用准则》。
3.1.3客人要求的验收水准和本厂的验收水准。
批准:审核:编写:。
最终检验作业指导书

东阳市鲁创红木家具有限公司最终检验作业指导书编制编号Q/LC-ZY-01核准版本 A目的:细分检验步骤,明确检验顺序及检验重点,确保产品满足客户需求范围:适用于入库检验作业指导以及质检员培资料职责:相关检验点负责严格按本规定要求对过程产品或最终产品进行检验。
作业程序一·书柜类:一·组合检验:组合后查看中间缝隙,上下缝隙是均匀,缝隙值是否达标。
1·如出现上下一头缝隙较大可确认为底脚不平。
2·出现中间分缝较大确认为边柱左右变形。
3·缝隙指数达标但边柱不在同一水平面可确认为边柱前后变形或安装不正,都需木工修理。
二.整体外观检验1·目测整体色差是否均匀。
2·光泽度是否达标。
3·黑疤·修补处是否盖色修理。
4·线条是否顺畅。
5·用手抚摸是否光滑。
6·侧板·后背板生挡等外表是否存在啃疤和不平整现象。
三·柜门检验1·拉开门查看吸住安装的外置是否准确·松紧度是否合理。
2·柜门安装整体是否到位,门与外边框是否平整。
如出现门角凹陷或突出可确认门架变形。
3·门分缝是否达标,是否均匀:3.1缝隙过大要求木条修补。
3.2缝隙上下·左右中不匀要求调节。
3.3缝隙上下一边(两天同时倾斜为不均)倾斜要求刮磨修理。
4·查看柜门花板·破损现象,花低角落胶水是否清理干净,缝隙是否修补完好线条是否顺畅。
是否存在色差。
花节等部件是否安装正确是否存在倾斜和松动现象。
四·上柜门内部检验1·打开柜门查看边槽颜色是否做到位,是否存在木工修理后油漆未修理。
打开门同时用手摸上下门边沿是否光滑,如粗糙可能存木工修理后油漆未修理。
2·查看内部色差是否均匀,光泽度是否达标,角落点白是否到位,收缩缝是否清理干净,板·面是否存在啃疤,手抚摸板·面是否存在不平整现象(变形)等。
产品出厂检验规程
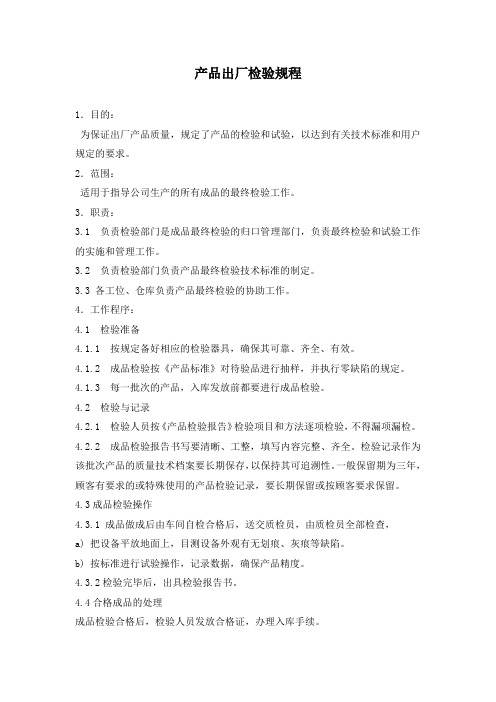
产品出厂检验规程1.目的:为保证出厂产品质量,规定了产品的检验和试验,以达到有关技术标准和用户规定的要求。
2.范围:适用于指导公司生产的所有成品的最终检验工作。
3.职责:3.1 负责检验部门是成品最终检验的归口管理部门,负责最终检验和试验工作的实施和管理工作。
3.2 负责检验部门负责产品最终检验技术标准的制定。
3.3 各工位、仓库负责产品最终检验的协助工作。
4.工作程序:4.1 检验准备4.1.1 按规定备好相应的检验器具,确保其可靠、齐全、有效。
4.1.2 成品检验按《产品标准》对待验品进行抽样,并执行零缺陷的规定。
4.1.3 每一批次的产品,入库发放前都要进行成品检验。
4.2 检验与记录4.2.1 检验人员按《产品检验报告》检验项目和方法逐项检验,不得漏项漏检。
4.2.2 成品检验报告书写要清晰、工整,填写内容完整、齐全。
检验记录作为该批次产品的质量技术档案要长期保存,以保持其可追溯性。
一般保留期为三年,顾客有要求的或特殊使用的产品检验记录,要长期保留或按顾客要求保留。
4.3成品检验操作4.3.1 成品做成后由车间自检合格后,送交质检员,由质检员全部检查,a)把设备平放地面上,目测设备外观有无划痕、灰痕等缺陷。
b)按标准进行试验操作,记录数据,确保产品精度。
4.3.2检验完毕后,出具检验报告书。
4.4合格成品的处理成品检验合格后,检验人员发放合格证,办理入库手续。
4.5 不合格成品的处理4.5.1 成品经检验判定为不合格,可以通过返工、返检达到验收要求的,由检验员做出处理。
产品经返工、返检后重新交验。
4.5.2 当成品的不合格项不可能通过返工、返检达到合格接收条件时,按《不合格品控制程序》执行。
5.相关文件:5.1 《不合格品控制程序》5.2 《纠正和预防措施控制程序》5.3 《质量记录控制程序》6.相关记录《产品检验报告》。
最终检验控制程序

最终检验控制程序一、目的:对生产完成的半成品、成品进行规定的检验,确保产品品质稳定及符合客户的要求。
二、范围适用于本公司FQC及FQC对半成品、成品的入库前的检验。
三、职责(一)生产部门:生产完成后半成品、成品的搬运及检验工作的配合,不良品的返工等。
(二)品管部:FQC负责半成品的入库前检验。
QA负责成品的入库前检验。
四、作业流程(一)检验前的准备1.生产部在半成品完成后,将半成品摆放整齐用于垫板上,并在产品上贴上标签,注明制程名称、工令单号、产品名称、数量等,将产品置于本部门“特验区”内,在低垫板上挂“待验”标志牌。
交由品管FQC进行检验。
2.组装部门将产品用装好,整齐摆放于本部门“待验区”内,在纸箱外部贴上标签,注明订单编号、产品名称、生产批号、批量等,填写《成品入库验收单》交品管QA进行检验。
(二)检验标准1.抽样计划取MIL—STD—105EII级单次正常抽样,(1)外观AQL值为:CR(严重缺陷):0 MAJ(主要缺陷):1.0MIN(次要缺陷):1.5(2)依产品《工艺指导单》的工艺标准及检验标准进行检验。
1、半成品检验(1)FQC依《生产指令单》、《产品工艺流程图》、《产品工艺指导单》、《工艺标准》、对半成品进行外观及功能检验。
(2)FQC将检验结果记录在《FQC检验记录单》内,对检验合格品贴绿色“FQC合格标签”,并注明检验日期、单号等。
2、成品检验(1)QA依《生产指令单》、客户订单及产品《工艺流程图》、《工艺指导单》、《工艺标准》、《检验标准》对成品外部包装、外观、功能进行检验。
(2)QA将检验结果填入《QA检验记录表中》,对检验合格品贴绿色“QA合格标签”,注明检验日期、验收单号等。
3、对于FQC或QA无法判定及检测设备不足无法进行检验时,应向部门主管报告,由生产、技术等部门进行会同检验。
(三)不合格品处理1.生产部门将不合格品置于“不合格”区域内。
与合格品进行隔离并标识。
品质部岗位职责及检验流程
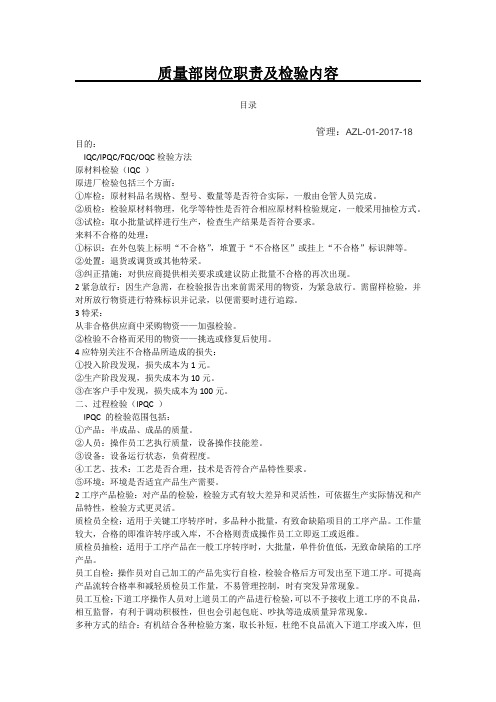
质量部岗位职责及检验内容目录管理:AZL-01-2017-18目的:IQC/IPQC/FQC/OQC检验方法原材料检验(IQC )原进厂检验包括三个方面:①库检:原材料品名规格、型号、数量等是否符合实际,一般由仓管人员完成。
②质检:检验原材料物理,化学等特性是否符合相应原材料检验规定,一般采用抽检方式。
③试检:取小批量试样进行生产,检查生产结果是否符合要求。
来料不合格的处理:①标识:在外包装上标明“不合格”,堆置于“不合格区”或挂上“不合格”标识牌等。
②处置:退货或调货或其他特采。
③纠正措施:对供应商提供相关要求或建议防止批量不合格的再次出现。
2紧急放行:因生产急需,在检验报告出来前需采用的物资,为紧急放行。
需留样检验,并对所放行物资进行特殊标识并记录,以便需要时进行追踪。
3特采:从非合格供应商中采购物资——加强检验。
②检验不合格而采用的物资——挑选或修复后使用。
4应特别关注不合格品所造成的损失:①投入阶段发现,损失成本为1元。
②生产阶段发现,损失成本为10元。
③在客户手中发现,损失成本为100元。
二、过程检验(IPQC )lPQC 的检验范围包括:①产品:半成品、成品的质量。
②人员:操作员工艺执行质量,设备操作技能差。
③设备:设备运行状态,负荷程度。
④工艺、技术:工艺是否合理,技术是否符合产品特性要求。
⑤环境:环境是否适宜产品生产需要。
2工序产品检验:对产品的检验,检验方式有较大差异和灵活性,可依据生产实际情况和产品特性,检验方式更灵活。
质检员全检:适用于关键工序转序时,多品种小批量,有致命缺陷项目的工序产品。
工作量较大,合格的即准许转序或入库,不合格则责成操作员工立即返工或返维。
质检员抽检:适用于工序产品在一般工序转序时,大批量,单件价值低,无致命缺陷的工序产品。
员工自检:操作员对自己加工的产品先实行自检,检验合格后方可发出至下道工序。
可提高产品流转合格率和减轻质检员工作量,不易管理控制,时有突发异常现象。
CCC最终检验和试验控制程序

德信诚培训网
更多免费资料下载请进: 好好学习社区 CCC 最终检验和试验控制程序
1.目 的
为保证最终产品质量,避免不良品流出造成不良影响和损失,特制定本
程序。
2. 适 用 范 围
本程序适用于最终产品的检验和试验。
3.引 用 文 件
3.1 DXC-10 《检验和试验状态控制程序》
3.2 DXC-19 《不合格品控制程序》
3.3 DXC-24 《纠正与预防措施控制程序》
3.5 DXC-27 《质量记录控制程序》
4.职 责
4.1 品质部出货检验员(ODXC)负责最终产品的检验和试验。
4.2 相关部门和人员协助本程序的实施。
4.3 品质主管监督本程序的执行。
5.程 序
5.1 检验前准备
5.1.1品质部依据产品标准、客户要求及产品质量特性制定《产品最终检。
最终检验控制程序
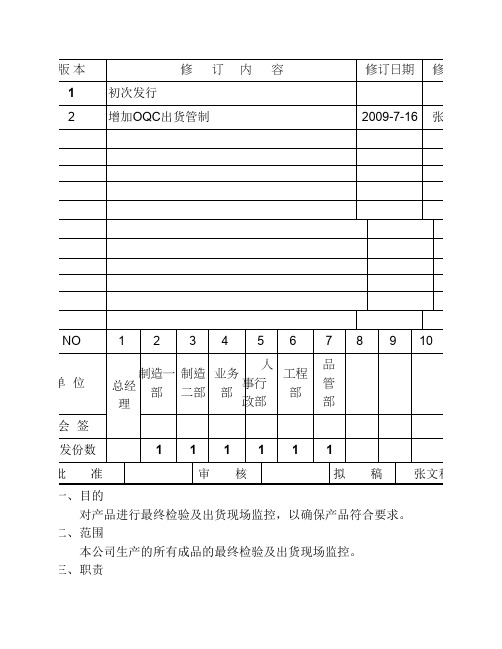
位应及时分析原因采取纠正措施,并在二个工作日内将纠正/预防措施 回交品管部。品管部 负责跟踪改善结果,对在规定时间内未能改善的,品管部再次跟进,直 到改善为止。 5.5.经检验合格的成品入库后,由仓库员负责按《仓储管理程序》进行作业。 5.6. 对于客户退货,品管部先进行判定和分析确认后,由业务部和品管部协同办 理相应退货手续。 5.7. 成品复检:本公司库存成品保存时间如超过期限,在出货前由物控中心负责 填写内部联络单 交于品管部,品管部安排检验员按照相关文件执行复检工作及OQC出货 现场监控。 5.8. 本公司一般不存在紧急放行的情况,如有应经过副总经理及以上人员批准, 并经客户同意后方可放行,否则需按文件化要求完成所有的检验项目才能出 货。 5.9.确认检验
二、范围 本公司生产的所有成品的最终检验及出货现场监控。
三、职责
3.1.制造部包装组:负责将成品包装完毕后,整齐摆放在“待检区”并填 写《成品/半成品送
验单》,经判定合格后入库。 .2.品管部:FQC负责按《MIL-STD-105E计数抽样计划》及检验规范和作业指导书等进行最
终 检验,并对产品进行判定;OQC负责出货现场监控。
3.3.仓库:负责协同制造部将最终检验后之合格品入库和出货作业。 四、定义:
4.1 送检:包装组将成品送至成品待检区,送检成立。 4.2 一批:制造单位一次送检的每一种型号称为一批。 4.3 FQC:品管部最终检验。 4.4 OQC:品管出货现场监控。 五、作业内容: 5.1. 制造部将完成的产品送至“待检区”,通知品管部成品检验员FQC进行 检验。 5.2 .品管部成品检验员依据《抽样检验计划表》及相应检验规范等对送检 成品实施检验和判定。 5.3. 品管人员依据产品类型分别将检验情况及结果记录于《FQC检验报告》、 《FQC检验日报
过程及最终检验控制程序【范本模板】
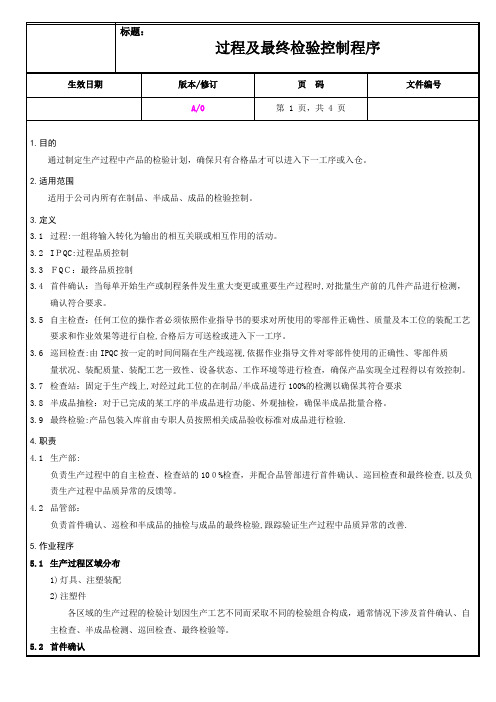
5.6.3成品致命缺陷不良为O ,检查发现有1个致命缺陷,经核检确认,则全部返工重检;重要缺陷不良大于或等于2%时与轻缺陷大于或等于2。5%之数量,经核查确认属实退由生产部全部返工重检。
5.6.4检验发现的不合格品要及时区分隔离标识,防止不良品与良品混淆.
5.2.1首件确认的时机;
a.每单灯具、注塑产品装配或注塑件生产前;
b.产品批量生产前;
c.生产条件发生重大变化,如生产设备变更、原材料变更、变更生产工艺等。
5.2.2首检确认依据:详细规定见《IPQC作业指导书》。
5.2.3首件确认由生产组长负责送检,IPQC负责检测,首件确认合格之后由生产和IPQC签字确认。
5.4自ห้องสมุดไป่ตู้检查
作业员都应对自己加工的产品进行检查以便及时发现错误,避免不良品流入下一工序,自主检查不需要做记录.
5.5检查站
5.5.1检查站通常包括:检查产品外观、结构性(装配零件组成结构)
5.5.2检查站由作业员负责,根据订单及检验标准的作业要求,在某一特定工序对经过此工位的在制品/半成品进行100%检测
4.2品管部:
负责首件确认、巡检和半成品的抽检与成品的最终检验,跟踪验证生产过程中品质异常的改善.
5.作业程序
5.1生产过程区域分布
1)灯具、注塑装配
2)注塑件
各区域的生产过程的检验计划因生产工艺不同而采取不同的检验组合构成,通常情况下涉及首件确认、自主检查、半成品检测、巡回检查、最终检验等。
5.2首件确认
3.7检查站:固定于生产线上,对经过此工位的在制品/半成品进行100%的检测以确保其符合要求
FQC检验规范流程
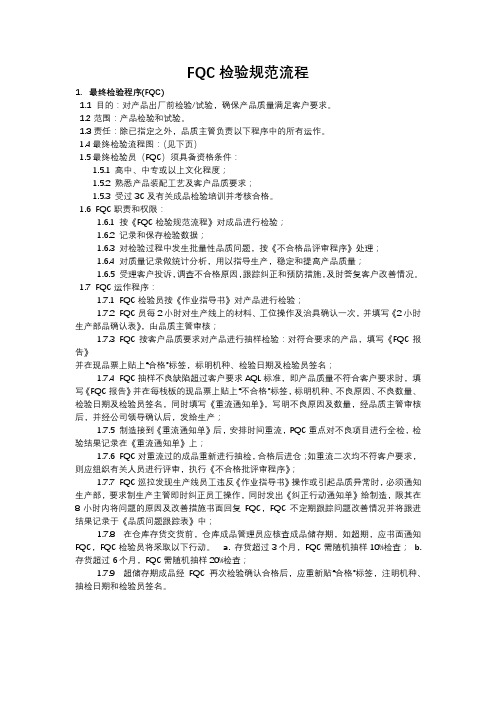
FQC检验规范流程1. 最终检验程序(FQC)1.1 目的:对产品出厂前检验/试验,确保产品质量满足客户要求。
1.2范围:产品检验和试验。
1.3责任:除已指定之外,品质主管负责以下程序中的所有运作。
1.4最终检验流程图:(见下页)1.5最终检验员(FQC)须具备资格条件:1.5.1 高中、中专或以上文化程度;1.5.2 熟悉产品装配工艺及客户品质要求;1.5.3 受过3C及有关成品检验培训并考核合格。
1.6 FQC职责和权限:1.6.1 按《FQC检验规范流程》对成品进行检验;1.6.2 记录和保存检验数据;1.6.3 对检验过程中发生批量性品质问题,按《不合格品评审程序》处理;1.6.4 对质量记录做统计分析,用以指导生产,稳定和提高产品质量;1.6.5 受理客户投诉,调查不合格原因,跟踪纠正和预防措施,及时答复客户改善情况。
1.7 FQC运作程序:1.7.1 FQC检验员按《作业指导书》对产品进行检验;1.7.2 FQC员每2小时对生产线上的材料、工位操作及治具确认一次,并填写《2小时生产部品确认表》,由品质主管审核;1.7.3 FQC按客户品质要求对产品进行抽样检验:对符合要求的产品,填写《FQC报告》并在现品票上贴上“合格”标签,标明机种、检验日期及检验员签名;1.7.4 FQC抽样不良缺陷超过客户要求AQL标准,即产品质量不符合客户要求时,填写《FQC报告》并在每栈板的现品票上贴上“不合格”标签,标明机种、不良原因、不良数量、检验日期及检验员签名,同时填写《重流通知单》,写明不良原因及数量,经品质主管审核后,并经公司领导确认后,发给生产;1.7.5 制造接到《重流通知单》后,安排时间重流,PQC重点对不良项目进行全检,检验结果记录在《重流通知单》上;1.7.6 FQC对重流过的成品重新进行抽检,合格后进仓;如重流二次均不符客户要求,则应组织有关人员进行评审,执行《不合格批评审程序》;1.7.7 FQC巡拉发现生产线员工违反《作业指导书》操作或引起品质异常时,必须通知生产部,要求制生产主管即时纠正员工操作,同时发出《纠正行动通知单》给制造,限其在8小时内将问题的原因及改善措施书面回复FQC,FQC不定期跟踪问题改善情况并将跟进结果记录于《品质问题跟踪表》中;1.7.8 在仓库存货交货前,仓库成品管理员应核查成品储存期,如超期,应书面通知FQC,FQC检验员将采取以下行动。
最终检验控制程序

更改记录1.目的:通过对将要进入成品库的成品进行抽样检验,确保符合品质要求的成品才能进入成品库。
2.范围:本公司生产的各种产品。
3.定义:无4.职责:4.1生产部负责生产4.2资材部负责仓储4.3品保部负责检验。
5.内容5.1生产成品检验5.1.1 最终检验组在接到生产组通知后,即安排人员到成品待检区,依据《助焊剂检验办法》、《锡膏检验办法》或《稀释剂,清洗剂检验办法》抽取样品。
5.1.2 对所抽取样品按照《助焊剂检验办法》、《稀释剂、清洗剂检验办法》或《锡膏检验办法》进行检验,依据《现有产品一览表》进行判断,并将检验结果作记录,填入《QA检验报告》。
5.1.3检验合格之成品,还须对产品的型号、批号、日期、数量、包装方式等与《生产命令》核对是否相符。
核对无误后,由QA在每批成品外包装上标识“合格”标签,通知仓储组按《货仓管理办法》办理入库手续。
5.1.4核对有误之产品,立即凭《生产命令》通知生产组更正后再按5.1.3执行,直至合格。
5.1.5检验不合格之产品,按照《产品标识和可追溯性程序》,贴上“不合格”标签后,按照《不合格品控制程序》予以处理。
5.1.6最终检验组将每次检验结果填入《生产成品月合格率统计表》,并保存二年,作为制程能力评估的依据。
5.2销货退回的检验5.2.1对于客户因各种原因退回的成品,由业务人员填写《退货申请表》,退回成品由仓储组归入退货区并标识,并凭《退货申请表》通知QA进行检验。
5.2.2 QA对退回未使用的成品进行全检。
对于客户已使用过的产品,由于无法验证环境禁用物质含量,按直接报废处理。
5.2.3 QA依据《助焊剂检验办法》、《稀释剂、清洗剂检验办法》或《锡膏检验办法》对退回成品进行检验,并依据《现有产品一览表》进行判断,最后将检验结果填入《QA检验报告》中。
5.2.4 检验合格的成品,由QA在每个外包装上加贴“合格”标签,通知仓储组办理入库。
5.2.5 检验不合格的成品,由QA在每个外包装上加贴“不合格”标签,通知仓储组将此成品转入不合格品区,按《不合格品控制程序》处理。
最终检验控制程序

受控状态受控页码1/4发布日期2023年03月10日实施日期2023年03月13日文件发行栏☑行政部☑采购部☑生产部☑工程部☑业务部☑品质部☑仓库修订履历表版本日期修改原因及内容提要修改人审核人批准人A02023/03/06新版发行受控状态受控页码2/4发布日期2023年03月10日实施日期2023年03月13日一、目的为确保成品品质符合顾客需要,同时为找出潜在品质问题,作为改善制程之依据,特制定本程序。
二、适用范围凡本公司所承制之产品于入库或出货前之最终检验均适用之。
三、术语及定义无四、职责和权限4.1品质部:负责成品的最终检验。
4.2品质部主管:负责检验工作之协调及记录之审核。
五、流程图5.1最终检验作业流程图(附件1)六、作业内容6.1检验前的准备6.1.1待检验品须放置在待验区,申请部门填写《请检单》发至品质部。
6.1.2检验前须核对检验设备(仪器)是否仍在有效校验周期内。
6.1.3检验前准备好相关的检验规范、出货单、仪器设备等。
6.2检验作业6.2.1成品检验依据检验标准(如控制计划、BOM表、工程图纸、生产通知单、样品以及检验规范等)来实施检验,若客户有特殊状况或要求时品质部主管可予追加项目或依客户之要求施行检验。
6.2.2检查批以同生产批次同型号、同规格、同测试条件产品为一检查批量。
6.2.3检验人员须接受过专业训练,参照《人力资源控制程序》。
6.2.4检验结果需分别登录于《成品(出货)检验记录表》,检验合格者经检验人员签字核准可转成品包装,检验结果若不合格依《不合格品控制程序》执行。
其相关生产、检验记录表由品质部保存归档以便追溯。
6.2.5出货检查6.2.5.1成品仓在打好外箱包装后,须按区域对不同客户、不同订单号码之产品进行摆放整齐。
6.2.5.2业务单位最迟于出货前四小时开具《出货单》给品质及仓库,仓库依据《出货单》通知品质人员一起进行备货作业。
受控状态受控页码3/4发布日期2023年03月10日实施日期2023年03月13日6.2.5.3备货完成后OQC人员需100%确认以下项目:a.标签及条码上所有内容填写一定要完整。
最终检验和试验控制程序

1.目的为验证产品最后是否符合顾客要求,并提供证据,确保所有的检验和试验均已完成,确保不合格产品不出厂。
2.范围适用于本公司生产的所有产品的最终检验和最终审核的控制。
3.职责3.1技术部负责提供《机械加工作业指导书》。
3.2理化分析室负责对产品材料成份进行分析,清洁度的检验并作好记录。
3.3品管部检验员负责对加工完毕的产品进行检验并保存其检验记录;部门主管负责对产品最终检验和试验的所有报告进行审核。
3.4营销部检验员负责对即将出库的产品进行抽查。
4.流程图5.工作程序5.1成品的分类成品按其性质分为主机产品和维修产品两大类。
5.2成品检验和试验备件5.2.1成品检验和试验所用的检验、测量和试验设备要适用且满足规定的准确度和精度,并与要求的测量能力一致。
参见“检验、测量和试验设备控制程序”。
5.2.2成品的检验和试验工作须由熟悉本岗位职责的接受专业培训,考核合格,具备资格后的人员,经品管部主管批准,才能上岗检验。
参见“培训控制程序”。
5.3检验和试验依据5.3.1成品尺寸检验作业指导书、成品外观检验作业指导书、成品包装检验作业指导书。
5.3.2产品验收标准5.3.3顾客的要求5.3.4控制计划5.4检验和试验的实施产品最终检验和试验包括成品尺寸检验、成品外观检验、成品包装检验。
5.4.1检验员须按照《机械加工作业指导书》上要求的频次、项目、方法对成品进行尺寸抽检,并将检测结果记录于“成品尺寸检验记录上”。
若客户对最终检验和试验另有要求,按照客户要求进行检查。
5.4.2成品尺寸经抽检合格后,才能进行外观检验。
检验员必须按照“产品图”及《机械加工作业指导书》对产品外观质量进行普检,并将检验结果记录在“成品外观检验记录”上。
5.4.3经外观检验合格的产品,检验员须在“分箱单”上记录检验状态,签字后才能包装。
5.4.4包装工按照《机械加工作业指导书》对包装进行自检,检验合格后放入合格证,并将检验结果登录在包装检验记录中。
出货检验有哪些程序

出货检验有哪些程序出货检验也叫最终检验是指产品在出货之前为保证出货产品满足客户品质要求所进行的检验。
经检验合格的产品才能予以放行出货。
出货检验一般实行抽检,出货检验结果记录有时根据客户要求提供给客户。
出货检验是验证产品完全符合客户要求的最后保障。
当产品复杂时,把各种零部件组装成半成品时,有必要把半成品作为最终产品来对待,因为有时候检验活动会被策划成与生产同步进行,这样有助于最终检验的迅速完成。
因此,当它们在装配后往往不能再进行单独的检验。
出货检验需履行的程序如下:1.检验准备(1)营销部根据出货日期提前2天通知品管部安排检验人员对成品进行检验。
(2)品控部在进行检验前2小时,通知仓库进行检验的协作准备。
(3)根据出货通知内容和品控部通知时间,仓库把需要检验的待出货成品搬运至验货区,并挂上“待检”牌。
2.出货检验(1)出货检验员按照抽样标准抽样,必要时,按顾客要求执行抽样。
(2)出货检验员依产品样板、工艺标准、客户相关要求资料及《最终检验指导书》对产品进行全面检验。
3.检验项目(1)外观检查。
检查产品的外表是否有刮花、伤痕、污渍、水渍,产品是否变形、受损、配件、组件、零件是否有松动脱落、数量不符及配置错误等。
外观评判必须参照《成品检验标准》及相关样品,评判人员的能力和资格由品控部主管验证。
(2)尺寸检验。
检查产品是否符合规格,零配件尺寸是否符合要求,包装材料尺寸是否符合标准。
(3)功能特性试验。
检查产品的物理、化学特性是否产生变化和环境对产品的影响程度以及是否有漏水等功能性问题。
(4)使用寿命试验。
在模拟状态下或破坏性试验状态下,检测产品的使用寿命参数。
(5)产品包装和标识检查。
产品包装方式、数量、包装材料使用,以及标签的位置和书写内容等是否正确。
4.不合格判定根据抽样计划及执行抽样的结果,出货检验员判定不合格的数量,若无法判定时上报品控部主管进行判定,确定不合格品的数量及处理意见;必要时,依实际抽样情况决定是否需要全检。
最终检验程序
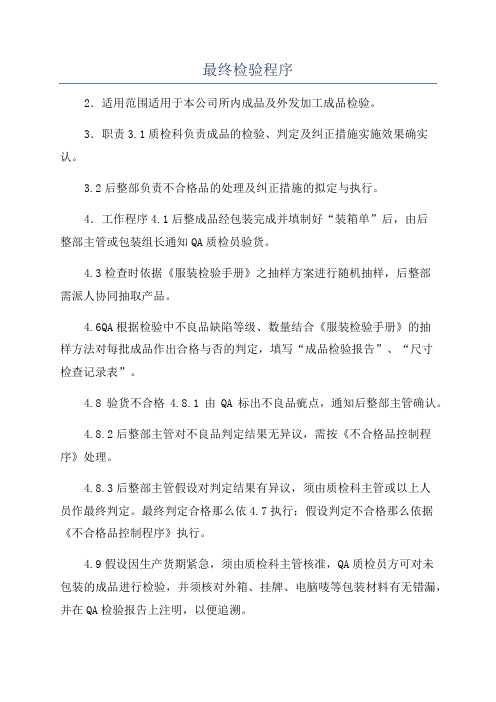
最终检验程序
2.适用范围适用于本公司所内成品及外发加工成品检验。
3.职责3.1质检科负责成品的检验、判定及纠正措施实施效果确实认。
3.2后整部负责不合格品的处理及纠正措施的拟定与执行。
4.工作程序4.1后整成品经包装完成并填制好“装箱单”后,由后
整部主管或包装组长通知QA质检员验货。
4.3检查时依据《服装检验手册》之抽样方案进行随机抽样,后整部
需派人协同抽取产品。
4.6QA根据检验中不良品缺陷等级、数量结合《服装检验手册》的抽
样方法对每批成品作出合格与否的判定,填写“成品检验报告”、“尺寸
检查记录表”。
4.8验货不合格4.8.1由QA标出不良品疵点,通知后整部主管确认。
4.8.2后整部主管对不良品判定结果无异议,需按《不合格品控制程序》处理。
4.8.3后整部主管假设对判定结果有异议,须由质检科主管或以上人
员作最终判定。
最终判定合格那么依4.7执行;假设判定不合格那么依据《不合格品控制程序》执行。
4.9假设因生产货期紧急,须由质检科主管核准,QA质检员方可对未
包装的成品进行检验,并须核对外箱、挂牌、电脑唛等包装材料有无错漏,并在QA检验报告上注明,以便追溯。
4.10本厂外发加工之成品由QA按4.2~4.9步骤执行检验,并填写“外发品验货报告”。
4.11成品检验中发现重大质量问题,按《纠正及预防措施管理程序》处理。
5.相关文件5.1《服装检验手册》5.2《不合格品控制程序》5.3《纠
正及预防措施管理程序》6.记录6.1《成品检验报告》6.2《尺寸检查记
录表》6.3《装箱单》6.4《外发品验货报告》。
QW7066-最终检验管理办法

NO
YES
6.8产品质量审核
6.8.1质量部定期对已入库的产品进行产品审核,具体按《产品审核管理办法》和《不合格品控制程序》执行;
6.8.2质量部保存所有最终检验记录和审核记录,按产品正常检验的流程检须在进行进货检验和试验、过程检验和试验均已经检验合格后进行;
6.4.2在检验员进行成品最终检验前,生产班组必须对将要送检的所有成品进行100%检验,确保送检的成品全部合格;
6.4.3生产班组在自检完成后,填写好产品质量流转卡,通知质量部检验员进行终检;
NO
YES
最终检验管理程序
1.目的
为防止不合格品流到顾客手中,特制定本程序。
2.范围
本程序适用于进货检验、过程检验均已完成,且结果满足规定要求的产品入库前的最终检验。
3.引用文件
QP/QF2804《不合格品控制程序》
QP/QF2805《纠正与预防措施管理程序》
QP/QF2403《记录管理程序》
4.术语和定义
不合格品:不符合顾客要求和规范的产品或材料。
NO
YES
6.3检验规程的审批
6.3.1编制完成的《总成检验作业指导书》,应由编制人署名,交其他质量部成员校对,审核,,然后由质量部经理批准生效;
6.3.2经质量部经理批准生效的《总成检验作业指导书》由质量部负责统一复印,加盖受控标识,下发给检验员,并存档;
6.3.3检验员将接收的《总成检验作业指导书》妥善保管,在总成检验中使用;及时指正错误或与实际不符合项目,反映给文件编制人员,以便更正;
- 1、下载文档前请自行甄别文档内容的完整性,平台不提供额外的编辑、内容补充、找答案等附加服务。
- 2、"仅部分预览"的文档,不可在线预览部分如存在完整性等问题,可反馈申请退款(可完整预览的文档不适用该条件!)。
- 3、如文档侵犯您的权益,请联系客服反馈,我们会尽快为您处理(人工客服工作时间:9:00-18:30)。
4·1检验准备
4·1·1成品检按《成品检验标准》准备好相应的标准件、检查仪器仪表,确保其可靠、齐全、有效。
4·1·2成品检按《产品检验抽样规程》对报验产品进行抽样,准备检验样本,并执行零缺陷的规定。
4·1·3每一批次的产品,入库发放前都要进行成品检定。
4·2检验与记录
4·2·1检验人员按照《成品检验标5·2 QS/TSB21301—2002《不合格品控制程序》
5·3 QS/TSB21401—2002《纠正和预防措施控制程序》
5·4 QS/TSB21601—2002《质量记录控制程序》
⒍质量记录
见清单。
4·4不合格成品的处理
4·4·1成品经检验判定为不合格,可以通过返工、返检达到验收要求的,由检验组做出处理。产品经返工、返检后重新交验。
4·4·2当成品的不合格项不可能通过返工、返检达到合格接收条件时,按《不合格品控制程序》执行。
⒌相关文件:
5·1 QS/TSB21101—2002《检验、测量和试验设备控制程序》
⒈目的:
保证出厂产品进行了规定的检验和试验,达到有关技术标准和用户规定的要求。
⒉范围:
适用于指导公司生产的所有成品的最终检验和试验工作。
⒊职责:
3·1检验组是成品最终检验的归口管理部门,负责最终检验和试验工作的实施和管理工作。
3·2技术部负责产品最终检验技术标准的制定。
3·3装配工段、成品仓库负责产品最终检验的协助工作。
4·2·2成品检验记录书写要清晰、工整,填写内容完整、齐全。检验记录作为该批次产品的质量技术档案要长期保存,以保持其可追溯性。一般产品的保留期为五年,顾客有要求的或特殊使用的产品检验记录,要长期保留或按顾客要求保留。
4·3合格成品的处理
4·3·1内销成品检验合格后,检验人员发放绿色PASS合格证。
4·3·2出口产品最终检验合格后除按4·3·1办理完毕后,由生产部按外贸商检报验程序与商检局办理报验和检验的有关手续。