塑胶件缩水的原因及改善的方法
塑料件筋位避免缩水设计

塑料件筋位避免缩水设计在塑料制品的生产过程中,可能会出现塑料件缩水的问题。
塑料件缩水是指在射出成型过程中,塑料件的尺寸发生缩小。
这种现象会导致产品尺寸不准确,甚至无法满足设计要求,给后续加工和使用带来困扰。
因此,在设计塑料件时,需要采取一些策略来避免或减少塑料件的缩水现象。
首先,为了避免塑料件缩水,我们需要了解造成塑料件缩水的原因。
塑料件缩水主要是由于塑料在冷却过程中发生收缩。
塑料在加热过程中会膨胀,达到熔融状态后进入模具,但在冷却过程中会发生收缩,导致尺寸变小。
这种收缩现象受多个因素的影响,如塑料的种类、成型工艺、模具结构等。
一种常用的减少塑料件缩水的方法是通过调整塑料件的设计。
首先,在设计时应尽量选择收缩率较低的塑料材料,如聚丙烯、聚乙烯等。
这些材料的收缩率相对较低,可以减少塑料件的缩水现象。
其次,在设计时应尽量避免选择容易发生收缩的形状,如壁厚不均匀、尺寸过大或过小等。
其次,在塑料件的具体结构设计中,可以采用一些措施来减少收缩。
首先,可以在设计中考虑合理的圆角设计。
圆角的设置可以减少应力集中,从而减少塑料件收缩的可能性。
其次,尽量避免在塑料件中设置内部孔洞或是壁厚突变。
这些特殊结构容易引起塑料件的收缩现象,应尽量避免使用。
此外,在塑料件中设置流道或温度控制系统,可以改变塑料的流动状态和冷却速度,从而减少收缩现象。
除了在设计时采取一些策略来减少塑料件缩水,我们还可以在加工过程中进行一些控制来避免缩水现象。
首先,可以通过合理的注塑参数来控制塑料件的冷却速度。
冷却速度的控制对减少塑料件的缩水非常重要。
在注塑过程中,可以通过调整冷却时间、冷却介质和冷却方式等参数来控制塑料件的冷却速度。
其次,可以通过添加一些填充剂来改变塑料件的物理性质,从而减少塑料件的收缩。
填充剂能够改变塑料的热膨胀系数和收缩率,从而减少塑料件收缩的可能性。
综上所述,塑料件缩水是塑料制品生产中常见的问题,但通过合理的设计和加工控制,可以减少或避免塑料件缩水现象的发生。
塑胶件缩水的原因及改善的办法
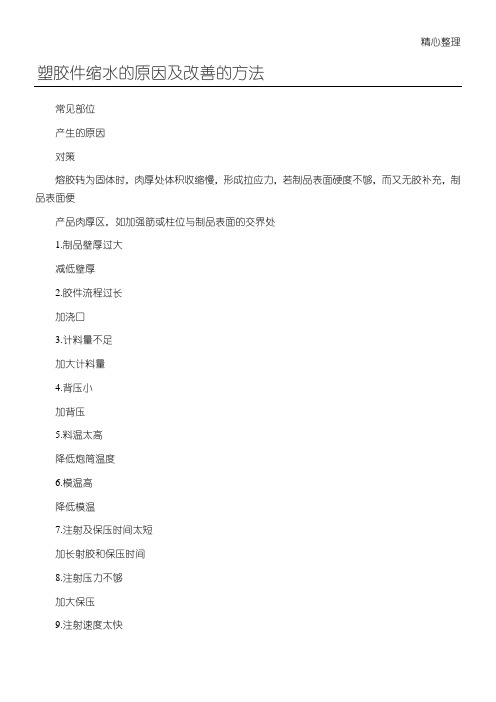
及排模不合理(如果厚壁产品在主流道的尾部,导致机注塑压力不够)。
出模斜度最小要0。5度以上,不同表面要求斜度也要求不同,如果是晒粗纹,则要求大些。
如果无特别要求当然是越大越好
主要之不良成形及其原因
?????????与成形机有关者??????????????????
(a)射出压力过高,亦且材料工给量过多
(b)加热温度过低,亦且加热温度过高
(c)加压时间(保压,开模)过长
(d)顶出机构(顶出装置)不良
???????
(a)喷嘴与型模装接不良
(b)喷嘴相应注道为过粗
(c)注道锥度过小
(d)注道衬套有疵病
(e)型模温度过高
(f)型穴内面有疵病
(g)型穴退缩倾斜不足
(h)型穴有低陷部份﹐再者角隅过份棱锐???????
(a)流动性恶
(b)润滑剂不足
气泡﹑条纹﹑斑点???????
(a)射出压力不足
(b)射出速度形成过早
(c)射出断续
(d)加压(保压,开模)时间不足
???????
(a)浇口位置不适当
(b)结合方法不良
(c)成形品厚度不均一
(d)流道过狭
(e)成形品在型模内受必要以上之冷却???????
(a)流动性恶
(b)有吸湿性
(a)有吸湿性
(b)含有挥发物质
(c)异质物混入污染
熔合线???????
(a)喷嘴温度过低
(b)射出压力不足
(c)射出压力形成过迟
???????
(a)浇口﹐流道过小
(b)浇口位置不适当
(c)型模温度过低
塑胶件缩水的原因及改善的方法完整版

塑胶件缩水的原因及改善的方法完整版塑胶件缩水是塑料加工过程中常见的一个问题。
塑胶件缩水通常是由于材料热收缩率高和制造过程中的一些其他因素导致的。
在一些特定的应用中,塑胶件缩水可能会对产品的性能和质量产生负面影响。
因此,了解塑胶件缩水的原因以及如何改善是至关重要的。
1.材料热收缩率高:不同类型的塑料具有不同的热收缩率。
热收缩率高的塑料在加工过程中容易出现缩水现象。
热收缩率高主要是由于塑料分子结构中的高分子链较容易受热而产生收缩。
2.制造过程中的温度梯度:塑胶件在冷却过程中,内部和表面的温度梯度可能不均匀,导致不同部位收缩程度不一致,从而引起塑胶件整体或局部的缩水现象。
3.模具结构设计不合理:模具结构的设计不仅会影响逐次填充的均匀性,还会影响模具内部的温度分布。
如果模具结构设计不合理,可能会导致塑胶件缩水。
针对塑胶件缩水问题,可以采取一些改善措施来解决:1.选择合适的塑料材料:在产品设计初期,应仔细选择合适的塑料材料。
低热收缩率的塑料可以减少缩水现象的发生。
此外,还可以添加填充材料来改变塑料的热收缩性能。
2.合理控制加工温度:加工温度是影响塑胶件缩水的重要因素之一、通过调整加工温度,可以减少热应力,从而减轻塑胶件的收缩现象。
3.优化模具结构设计:合理的模具结构设计可以改善塑料的填充均匀性,减少温度梯度的差异。
通过优化模具结构,可以减少塑胶件的收缩现象。
4.增加冷却时间:适当延长冷却时间可以减少塑胶件的收缩现象。
冷却时间的延长可以保持材料在模具中的时间更长,使塑胶更加均匀地收缩,减少缩水的发生。
5.使用模具温度控制系统:在模具中增加温度控制系统可以提高塑胶件的熔体温度均匀性,减少缩水的发生。
通过控制模具表面的温度,可以减轻塑胶件的热应力,并减少收缩现象。
总之,塑胶件的缩水问题可以通过选择合适的塑料材料、优化加工参数以及合理设计模具结构来解决。
通过以上的改善方法,可以减少塑胶件的收缩现象,提高产品的质量和性能。
注塑件缩水产生的原因

注塑件缩水产生的原因注塑件缩水是指在注塑过程中,塑料制品在冷却后体积缩小的现象。
缩水是注塑过程中常见的问题之一,其产生的原因多种多样。
本文将从塑料材料、模具设计、注塑工艺等方面探讨注塑件缩水产生的原因。
一、塑料材料的影响1. 热收缩率:热收缩率是指塑料在固化过程中由高温状态向室温状态过渡时体积缩小的程度。
不同种类的塑料具有不同的热收缩率,这是导致注塑件缩水的主要原因之一。
例如,聚丙烯的热收缩率较大,容易产生缩水现象。
2. 结晶度:塑料材料的结晶度也会影响注塑件的缩水程度。
结晶度越高,塑料分子排列越紧密,导致注塑件的收缩率增加。
因此,在注塑件缩水问题较为严重的情况下,可以考虑调整塑料材料的结晶度来解决。
二、模具设计的影响1. 缩水率考虑不足:在注塑件的模具设计过程中,如果没有充分考虑到塑料材料的收缩率,就会导致注塑件在冷却后出现缩水现象。
因此,在模具设计中,需要根据塑料材料的收缩率合理设置模具尺寸,以减少注塑件的缩水问题。
2. 浇口位置:浇口的位置对注塑件的缩水问题也有一定影响。
如果浇口位置选择不当,注塑件在冷却过程中可能出现不均匀的收缩,导致缩水现象。
因此,在模具设计中,需要综合考虑注塑件的形状和材料特性,选择合适的浇口位置。
三、注塑工艺的影响1. 注塑温度:注塑温度是影响注塑件缩水的重要因素之一。
如果注塑温度过高,塑料在冷却过程中收缩过大,容易导致注塑件缩水现象的发生。
因此,在注塑过程中,需要根据具体的塑料材料和注塑件的要求,合理调整注塑温度。
2. 冷却时间:冷却时间是指注塑件在模具中冷却至一定温度的时间。
如果冷却时间过短,注塑件内部温度无法充分降低,容易导致缩水现象的发生。
因此,在注塑工艺中,需要合理设置冷却时间,确保注塑件能够充分冷却。
注塑件缩水是由多种因素共同作用导致的。
塑料材料的热收缩率和结晶度、模具设计中的缩水率考虑和浇口位置选择、注塑工艺中的注塑温度和冷却时间等因素都会对注塑件的缩水产生影响。
塑胶件缩水的原因及改善的方法

塑胶件缩水的原因及改善的方法
1.材料因子:塑胶材料的收缩率、热变形温度和熔融温度会影响缩水
的程度。
2.注塑工艺因子:如注射温度、注射压力、注射速度和模具温度等参
数的设置不合理,会导致过热或过冷,进而引起缩水。
3.模具设计因子:模具的工艺设计不合理,如射嘴冷却不均匀、壁厚
不均匀、出线方向不合理等,都会导致缩水。
为了改善塑胶件的缩水问题,可以采取以下方法:
1.选择合适的塑胶材料:选用热稳定性好、收缩率低的材料,可以降
低缩水的程度。
2.调整注射工艺参数:合理设置注射温度、注射压力和注射速度等参数,减小温度差异和流动速度差异,有利于减少缩水现象。
3.优化模具设计:合理设计模具的型腔结构、冷却系统和出线方向等,使塑胶材料的冷却均匀,减少缩水的可能性。
4.储存与处理:将塑胶件储存在适宜的温度和湿度条件下,避免长时
间接触阳光和高温环境,以防塑胶件因受热再次发生收缩。
5.合理设计产品结构:考虑产品结构设计,避免大面积的平均壁厚的
设计,以减少缩水。
另外,还可以通过使用模流分析软件来模拟注塑过程,验证和优化塑
胶件的工艺参数和模具设计,以实现更好的缩水控制。
此外,加强对塑胶
件的质量检验和控制,以及选择有经验的塑胶制品加工厂商,也能有效降
低塑胶件缩水的发生。
总之,正确选择材料、合理调整注射工艺参数、优化模具设计和合理产品结构设计等措施是改善塑胶件缩水问题的关键。
同时,强化质量控制和使用模流分析软件等也是必要的手段,以提高塑胶件的加工质量和产品性能。
塑胶缩水原因及解决措施

塑胶缩水原因及解决措施
塑胶缩水是指在加工过程中,塑料制品出现尺寸缩小的现象。
其原因主要有以下几点:
1.材料选择不当。
塑料原料的选择过于经济,添加剂浓度过低,或者配方不当,都会导致制品缩水。
2.模具设计不合理。
模具结构、尺寸、冷却方式等都会影响产品缩水情况。
模具温度不均匀或者冷却不充分等,都会导致制品缩水。
3.加工工艺不当。
注塑过程中,料筒温度、模具温度、注入速度、压力等参数的控制不当,都会导致产品缩水。
那么,如何解决塑胶缩水问题呢?以下是几种常用的解决措施: 1.优化材料选择。
选择质量更好的原材料,加入适量的添加剂,合理设计配方,可以有效降低产品缩水率。
2.改进模具设计。
优化模具结构,增加冷却管道,控制模具温度,有助于改善缩水问题。
3.调整加工工艺。
合理控制料筒温度、模具温度、注入速度、压力等参数,可以有效降低产品缩水率。
4.加入缩水率调节剂。
在塑料制品中加入缩水率调节剂,可以调节缩水率,降低产品缩水率。
总之,针对不同的塑胶缩水问题,需要综合考虑材料、模具、工艺等因素,进行有针对性的解决措施,以达到更好的制品效果。
- 1 -。
零件缩水改善方法

零件缩水改善方法
零件缩水是指在塑胶件成型过程中,由于冷却速度和塑料收缩率的差异,导致塑胶件尺寸变小或内部产生空洞的现象。
下面是一些改善零件缩水的方法:
1. 调整模具温度:通过适当提高模具的温度,可以增加塑料的流动性,减少冷却速度,从而减少缩水问题。
2. 增加注塑压力和时间:增加注塑压力和时间可以促使塑料更充分地填充模具,减少内部空洞和收缩。
3. 优化塑料配方:通过调整塑料的配方,加入适量的填充剂或增强剂,可以改变塑料的收缩率,从而减少缩水问题。
4. 调整浇口位置和大小:浇口的位置和大小对塑料的填充和冷却有重要影响。
通过调整浇口的位置和大小,可以改变塑料的流动方向和冷却速度,从而减少缩水问题。
5. 增加后处理工序:在零件成型后进行后处理,如热处理、退火处理等,可以减小塑料的收缩率,提高零件尺寸的稳定性。
6. 使用气辅成型技术:气辅成型技术通过在注射过程中将气体注入模具中,形成气垫,使塑料在冷却过程中保持更好的形状,从而减少缩水问题。
以上方法仅供参考,建议根据具体情况进行选择和应用。
同时,也可以寻求专业人士的帮助,对模具和工艺进行更为精确的调整和优化。
塑料产品缩水的原因及处理方法

塑料产品缩水的原因及处理方法塑料产品是现代工业中广泛使用的一类产品,它具有重量轻、耐久、易加工等特点,因此被广泛应用于各个领域。
然而,在使用过程中,我们有时会发现塑料产品出现缩水的现象,这给产品的使用和生产带来了一定的困扰。
本文将从塑料产品缩水的原因和处理方法两个方面进行探讨。
我们来分析塑料产品缩水的原因。
塑料产品缩水是由于塑料材料在制作过程中或使用过程中发生了物理或化学变化导致的。
具体原因如下:1.热收缩:塑料材料在加工过程中需要进行热处理,但由于塑料的热膨胀系数较大,加热后容易发生热收缩现象。
特别是在注塑成型过程中,塑料材料经过高温熔化后,冷却后会发生收缩,导致产品尺寸缩小。
2.材料选择不当:不同类型的塑料材料具有不同的热膨胀系数和收缩率,选择不当的材料会导致产品缩水。
例如,一些低温热塑性塑料的收缩率较大,容易出现缩水现象。
3.制作工艺不当:塑料制品的缩水问题与制作工艺密切相关。
在注塑成型过程中,如果模具温度、注射压力、注射速度等参数控制不当,都可能导致产品缩水。
那么,针对塑料产品缩水问题,我们应该采取哪些处理方法呢?下面将从材料选择、工艺改进和质量控制三个方面进行详细介绍。
1.材料选择:合理选择塑料材料对于避免产品缩水问题至关重要。
在选择材料时,应考虑其热膨胀系数和收缩率等因素。
对于需要高精度的产品,可以选择热膨胀系数较小的塑料材料,从而减少产品的缩水程度。
2.工艺改进:改进制作工艺也是解决塑料产品缩水问题的重要方法之一。
首先,合理调整模具的温度,保持模具温度稳定,避免温度过高或过低导致产品缩水。
其次,合理控制注射压力和速度,避免过高的压力和过快的速度导致产品缩水。
此外,还可以采用预热模具的方式,使模具温度均匀分布,减少产品缩水的可能性。
3.质量控制:加强质量控制是预防和解决产品缩水问题的关键。
在生产过程中,应建立严格的质量控制体系,包括原材料的检验和筛选、生产工艺的监控和调整、产品的检测和测试等。
塑料缩水是什么问题?塑料缩水的最强解决方法

塑料缩水是什么问题?塑料缩水的最强解决方法塑料缩水就是塑料收缩的问题01塑料收缩有四种情况热收缩、相变收缩、取向收缩、压缩收缩与弹性恢复。
收缩过程有三部分组成:浇口凝固前的收缩、冷却收缩和脱模后收缩。
021缩水的主要原因①注射量不够;②熔体温度过高;③注射压力和保压压力过小;④注射时间和保压时间过少;⑤注射速度过大;⑥模具温度不当。
031缩孔的主要原因①注射量不够;②注射压力太低;③注射速度不当;④模具温度过低。
041注塑件缺胶、不饱模原因分析:①塑胶熔体未完全充满型腔。
②塑胶材料流动性不好。
对策:1)制品与注塑机匹配不当,注塑机塑化能力或注射量不足。
2)料温、模温太低,塑胶在当前压力下流动困难,射胶速度太慢、保压或保压压力过低。
3)塑料熔化不充分,流动性不好,导致注射压力损失大。
4)增加浇口数,浇口位置布置要合理、多腔不平衡排布充填.流道中冷料井预留不足或不当,冷料头进入型腔而阻碍塑胶之正常流动,增加冷料穴。
5)喷嘴、流道和浇口太小,流程太长,塑胶填充阻力过大。
6)模具排气不良时,空气无法排除。
051披峰(毛边)原因分析:①塑胶熔体流入分模面或镶件配合面将发生。
②锁模力足够,但在主浇道与分流道会合处产生薄膜状多余胶料。
对策:1)锁模力不足,射入型腔的高压塑胶使分模面或镶件配合面产生间隙,塑胶熔体溢进此间隙。
2)模具(固定侧)未充分接触机台喷嘴,公母模产生间隙。
3)(没装紧)模温对曲轴式锁模系统的影响。
4)提高模板的强度和平行度。
5)模具导柱套摩损/模具安装板受损/拉杆强度不足发生弯曲,导致分模面偏移。
6)异物附着分模面。
7)排气槽太深。
8)型腔投影面过大/塑胶温度太高/过保压。
061表面缩水、缩孔(真空泡)原因分析:①制品表面产生凹陷的现象。
②由塑胶体积收缩产生,常见于局部肉厚区域,如加强筋或柱位与面交接区域。
制品局部肉厚处在冷却过程中由于体积收缩所产生的真空泡,叫缩孔(Void)。
③塑胶熔体含有空气、水分及挥发性气体时,在注塑成型过程空气、水分及挥发性气体进入制品内部而残留的空洞叫气泡(Bubble)。
塑料产品缩水的原因及处理方法

塑料产品缩水的原因及处理方法
塑料产品缩水的原因有很多,主要有以下几个方面:
1. 材料选择不当:塑料产品的缩水可能是由于材料选择不当引起的。
某些塑料材料在高温下容易产生缩水现象,因此选择适合的塑料材料对于产品的缩水是至关重要的。
2. 加工温度不合适:塑料产品在加工过程中的温度控制也会对产品的尺寸稳定性产生影响。
如果加工温度过高或过低,都有可能导致产品缩水。
3. 龙头班加工:龙头班加工是指在塑料产品加工过程中,因为一些原因导致产品的某些区域受热或受力不均匀,从而引起缩水现象。
针对塑料产品缩水问题的处理方法包括:
1. 选择合适的塑料材料:根据产品的使用环境和要求,选择适合的塑料材料,可以在一定程度上避免产品缩水问题。
2. 控制加工温度:在塑料产品的加工过程中,严格控制加工温度,避免温度过高或过低引起产品缩水。
可以通过调整加工设备、加工参数等方式实现。
3. 均匀受力和加热:在塑料产品的加工过程中,要尽量保证产品受力和加热的均匀性,避免龙头班加工现象的发生。
可以通过改进模具结构、调整加热设备等方式实现。
以上是一些常见的处理方法,具体的处理方法还需根据具体情况进行调整和改进。
在实际生产中,可以结合产品的特点和工艺要求,采取适当的措施来解决塑料产品缩水问题。
塑胶件缩水的原因及改善的方法

塑胶件缩水的原因及改善的方法塑胶件缩水是塑料加工过程中常见的一个问题,指的是注塑成型后的塑胶件尺寸变小的现象。
在注塑成型过程中,塑胶件材料会遇到高温、高压和急速冷却等条件,导致塑胶件内部的温度变化、流动速度差异等因素引起尺寸缩水。
本文将探讨塑胶件缩水的原因及改善的方法。
一、塑胶件缩水的原因1.材料因素:塑胶材料的热收缩率是造成缩水的主要原因之一、不同类型的塑胶材料具有不同的热收缩率,部分塑胶材料热收缩率较高,容易引起较大的缩水问题。
2.压力因素:注塑过程中的注塑压力对塑胶件缩水也有影响。
如果注塑压力设置过高,会使塑胶材料在注塑过程中过度流动,造成塑胶件内部的紧凑性降低,从而导致尺寸缩水。
3.温度因素:注塑过程中的温度控制对塑胶件缩水也有很大的影响。
如果注塑过程中的温度设置过高或过低,都会导致塑胶件的收缩率增大,从而引起尺寸缩水。
4.冷却因素:注塑过程中的冷却速度也是塑胶件缩水的重要原因。
如果注塑件在冷却过程中冷却速度过快,会使得塑胶件内部的温度梯度较大,从而引起尺寸缩水。
5.模具结构:模具的开口结构以及模具背压设计等因素也会对塑胶件的缩水问题产生一定的影响。
二、改善塑胶件缩水的方法1.选择低收缩率的塑胶材料:在项目设计和材料选择过程中,可以优先选择具有低热收缩率的塑胶材料,减少后续成型过程中的尺寸变化。
2.优化注塑工艺参数:合理调整注塑过程中的温度、压力和冷却速度等工艺参数,以减少塑胶件的热收缩率。
同时,优化保压时间和保压力度的设置,以提高塑胶件内部的紧凑性,减少缩水问题。
3.加强模具设计和制造:合理优化模具结构,并采用合适的模具开口方式,可以减少塑胶件的内部应力,降低缩水问题的发生。
此外,选择高品质的模具材料和制造工艺,确保模内温度均匀分布以及良好的冷却效果,有助于减少塑胶件的缩水现象。
4.控制注塑过程中的冷却速度:通过合理的冷却系统设计和冷却介质的选择,以及控制冷却时间和冷却速度的参数,可以减少注塑件过快冷却引起的尺寸缩水。
塑胶件缩水的原因与改善的方法
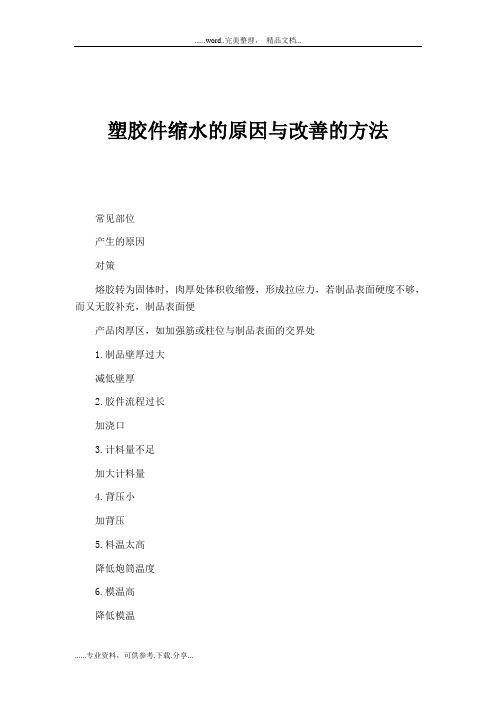
塑胶件缩水的原因与改善的方法常见部位产生的原因对策熔胶转为固体时,肉厚处体积收缩慢,形成拉应力,若制品表面硬度不够,而又无胶补充,制品表面便产品肉厚区,如加强筋或柱位与制品表面的交界处1.制品壁厚过大减低壁厚2.胶件流程过长加浇口3.计料量不足加大计料量4.背压小加背压5.料温太高降低炮筒温度6.模温高降低模温7.注射及保压时间太短加长射胶和保压时间8.注射压力不够加大保压9.注射速度太快减慢射速10.保压切换位置不当调好位置11.运水不足增加运水组数12.浇口位置不当改浇口位置至肉厚部分13.过胶圈磨损更换过胶圈14.射嘴堵塞清理射嘴15.液压油温高清理液压油热交换器缩水除了注塑工艺外,一是设计壁厚及骨位厚薄不合理,骨位厚度一般不过超过壁厚的2/3,二是从模具上来说入水设计不合理(如果长方形产品从一边入水就有机会在对面有骨位处产生缩水)及排模不合理(如果厚壁产品在主流道的尾部,导致机注塑压力不够)。
出模斜度最小要0。
5度以上,不同表面要求斜度也要求不同,如果是晒粗纹,则要求大些。
如果无特别要求当然是越大越好主要之不良成形及其原因与成形机有關者充填不良(a)射出壓力過低(b)壓出缸中溫度過低(c)壓出缸及噴嘴堵阻(d)噴嘴過小(e)材料供給過少(f)儲料斗堵阻(g)射出速度形成過遲(a)澆口位置不适當(b)結合方法不良(c)流道過狹(d)型模溫度過低(e)冷卻殘渣對流道及澆口堵阻(f)成形品有肉厚特薄之處(a)流動性惡(b)潤滑劑不足气泡﹑條紋﹑斑點(a)射出壓力不足(b)射出速度形成過早(c)射出斷續(d)加壓(保壓,開模)時間不足(a)澆口位置不适當(b)結合方法不良(c)成形品厚度不均一(d)流道過狹(e)成形品在型模內受必要以上之冷卻(a)流動性惡(b)有吸濕性(c)含有揮發性物質表面光澤不良(a)壓力缸中加熱不均一(b)噴嘴一部分堵阻(c)噴嘴徑過大(d)成形品超過成形機之能量(e)壓力缸中壓力過低(f)材料供應量不足(a)電鍍不良(b)澆口及流道過狹(c)冷卻殘渣儲穴欠缺(d)型模表面為水及油污染(e)型模溫度過低(f)結合方法不良(a)有吸濕性(b)含有揮發物質(c)异質物混入污染熔合線(a)噴嘴溫度過低(b)射出壓力不足(c)射出壓力形成過遲(a)澆口﹐流道過小(b)澆口位置不适當(c)型模溫度過低(d)結合方法不良a)材料固化過速(b)有吸濕性(c)潤滑不良磨邊生成(a)射出壓力過高(b)開模壓力不足(c)成形材料供給量過多(d)加壓時間(保壓,開模)過長(a)型模未能緊密密合(b)型模中有异物及毛刺等附著﹐不能完全關合(c)型穴設計不良﹐邊緣部份材料容易擠出(d)投影面積相應机械為過大(a)材料流動性過大缺凹(a)射出壓力不足(b)加熱溫度過高(c)射出速度形成過遲(d)材料供應兩量不足(e)成形品超過成形機之能量(f)加壓時間過短(a)型模溫度過高﹐并且不均一(b)澆口過狹(c)流道過狹(d)成形品厚度不均一(e)噴嘴過細(f)作業循環過速(g)保壓時間不足(a)材料過軟注道及成形品對型模黏著(a)射出壓力過高,亦且材料工給量過多(b)加熱溫度過低,亦且加熱溫度過高(c)加壓時間(保壓,開模)過長(d)頂出機構(頂出裝置)不良(a)噴嘴与型模裝接不良(b)噴嘴相應注道為過粗(c)注道錐度過小(d)注道襯套有疵病(e)型模溫度過高(f)型穴內面有疵病(g)型穴退縮傾斜不足(h)型穴有低陷部份﹐再者角隅過份棱銳(a)潤滑劑不足怎样避免产品凹痕和气孔产品凹痕通常由于制品上受力不足、物料充模不足以及制品设计不合理,凹痕常出现在与薄壁相近的厚壁部分。
塑胶件缩水的原因与改善的方法

塑胶件缩水的原因与改善的方法一、塑胶件缩水的原因:1.材料选择不当:塑胶件缩水可能是由于材料中含有溶剂、水分或其他挥发性物质,这些物质在注射过程中挥发,导致塑胶件体积缩小。
2.注射温度不适宜:注射过程中,温度过高或过低都可能导致塑胶件缩水。
温度过高会使塑胶熔化过度,造成缩水;温度过低则可能导致不充分的熔融,也会引起缩水。
3.注射压力不稳定:注射过程中,压力过高或过低都可能导致塑胶件缩水。
过高的注射压力可能使塑胶件内部气泡增多,导致缩水;过低的注射压力则可能导致塑胶无法填充模具中的细小空间,也会引起缩水。
4.注射时间控制不准确:注射时间过短或过长都可能造成塑胶件缩水。
时间过短可能导致塑胶未能充分流动,时间过长则可能导致塑胶过度熔化,都有可能引起缩水。
5.模具设计不合理:模具的设计和制造也可能对塑胶件缩水产生影响。
例如,模具中的冷却系统不畅通或不均匀,可能导致部分区域塑胶冷却不充分,引起缩水。
二、塑胶件缩水的改善方法:1.优化材料选择:选择合适的塑胶材料,避免含有溶剂、水分或其他挥发性物质,减少挥发物对塑胶件的影响。
2.控制注射温度:根据材料的熔点和注射工艺要求,控制注射温度在合适的范围内。
可以通过调整加热器的温度、防止温度波动等方法来控制注射温度。
3.稳定注射压力:根据塑胶件的形状和尺寸,调整注射压力,保持稳定的注射压力。
可以通过更换适合的注射机、调整压力传感器等方法来实现。
4.控制注射时间:根据塑胶件的形状和尺寸,合理控制注射时间。
可以通过调整注射机的时间控制装置、优化注射工艺参数等方法来控制注射时间。
5.优化模具设计:改进模具的冷却系统,保证冷却水的流动畅通,并合理分布在模具的各个部位。
可以通过提高冷却水的流量、增加冷却水的喷嘴等方法来优化模具设计。
6.限制模具开启时间:在注射过程中,控制模具开启时间,使塑胶件冷却时间更长,以减小塑胶件的缩水程度。
7.加入增容剂:适量加入增容剂,可以增加塑胶件的体积,减少缩水。
塑胶件缩水的原因与改善的方法

塑胶件缩水的原因与改善的方法塑胶件缩水是指在塑胶制品加工过程中,塑胶材料在冷却过程中出现体积变小的现象。
这种现象通常是由于塑胶件内部存在残余应力或塑胶分子结构的变化而引起的。
塑胶件缩水会导致尺寸不准确、外观变形,影响产品的质量和性能。
为了解决这个问题,有必要了解塑胶件缩水的原因以及改善的方法。
一、原因分析:1.内部残余应力:塑胶件在注射成型或挤出过程中,由于塑胶材料的熔融和冷却速度较快,使得塑胶分子排列不齐,形成内部残余应力。
当塑胶件冷却到一定程度时,内部残余应力会导致塑胶分子结构的变化,从而引起塑胶件缩水。
2.材料收缩率:塑胶材料在冷却过程中会出现体积收缩现象,这是由于塑胶分子在熔融状态下存在空隙和热膨胀,当冷却时这些空隙缩小,导致材料体积减小。
材料的收缩率取决于塑胶材料的种类和配方以及加工条件。
3.温度变化:塑胶件在注射成型或挤出过程中,由于熔融温度和冷却温度的变化,会引起塑胶分子的热胀冷缩现象,从而使塑胶件出现缩水。
4.成型周期:塑胶件在注射成型或挤出过程中,成型周期的长短也会影响塑胶件的缩水。
成型周期过长可以使塑胶件充分冷却,从而减少缩水现象。
二、改善方法:1.优化材料选择:选择低收缩率的塑胶材料,可以减少塑胶件的缩水现象。
此外,合理调整塑胶材料的配方,添加适当的增塑剂或稳定剂,能够优化塑胶件的结构和性能,减轻缩水现象。
2.控制成型温度:合理控制塑胶件的成型温度,避免温度过高或过低。
高温会导致塑胶材料的热胀冷缩现象增加,而低温则容易引起塑胶件内部残余应力,从而增加缩水现象。
3.调整注射成型参数:在注射成型过程中,应控制好注射速度、冷却时间和充模时间等参数。
合理的注射速度和充模时间可以使塑胶材料充分填充模具,避免空隙的形成,减轻缩水现象。
同时,适当延长冷却时间,允许塑胶材料充分冷却,有利于缩减塑胶件变形。
4.优化模具设计:优化模具结构和冷却系统,有助于加快塑胶件的冷却速度,减少残余应力和缩水现象。
塑胶件缩水的原因及改善的方法
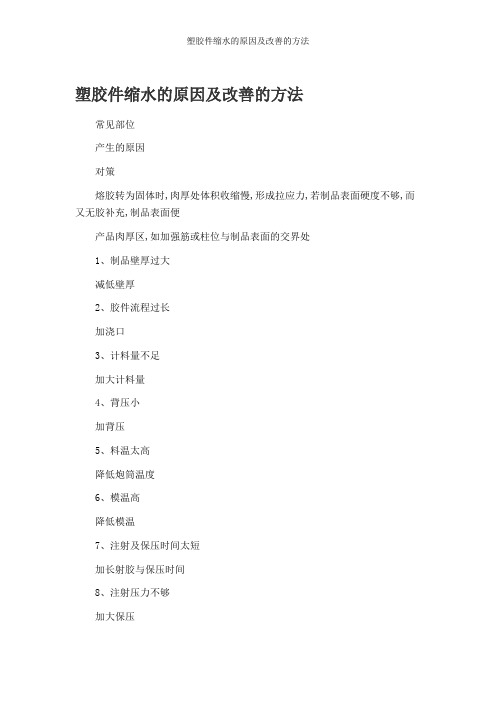
注道及成形品對型模黏著
(a)射出壓力過高,亦且材料工給量過多
(b)加熱溫度過低,亦且加熱溫度過高
(c)加壓時間(保壓,開模)過長
(d)頂出機構(頂出裝置)不良
(a)噴嘴与型模裝接不良
(b)噴嘴相應注道為過粗
(c)注道錐度過小
(d)注道襯套有疵病
(e)型模溫度過高
(f)型穴內面有疵病
(g)型穴退縮傾斜不足
②使注射周期正常;
(6)冷却条件问题:
①部件在模内冷却过长,避免由外往里收缩,缩短模子冷却时间;
②将制件在热水中冷却。
(1)物料问题:
①干燥物料
②加润滑剂
③降低物料中挥发物
(2)注塑条件问题
①注射量不足;
②提高注射压力;
③增加注射时间;
④增加全压时间;
⑤提高注射速度;
⑥增加注射周期;
⑦操作原因造成的注射周期反常。
(3)温度问题
①物料太热造成过量收缩;
②物料太冷造成充料压实不足;
③模温太高造成模壁处物料不能很快固化;
充填不良
(a)射出壓力過低
(b)壓出缸中溫度過低
(c)壓出缸及噴嘴堵阻
(d)噴嘴過小
(e)材料供給過少
(f)儲料斗堵阻
(g)射出速度形成過遲
(a)澆口位置不适當
(b)結合方法不良
(c)流道過狹
(d)型模溫度過低
(e)冷卻殘渣對流道及澆口堵阻
(f)成形品有肉厚特薄之處
(a)流動性惡
(b)潤滑劑不足
气泡﹑條紋﹑斑點
降低模温
7、注射及保压时间太短
加长射胶与保压时间
8、注射压力不够
加大保压
9、注射速度太快
塑胶制品出现凹痕缩水是什么原因
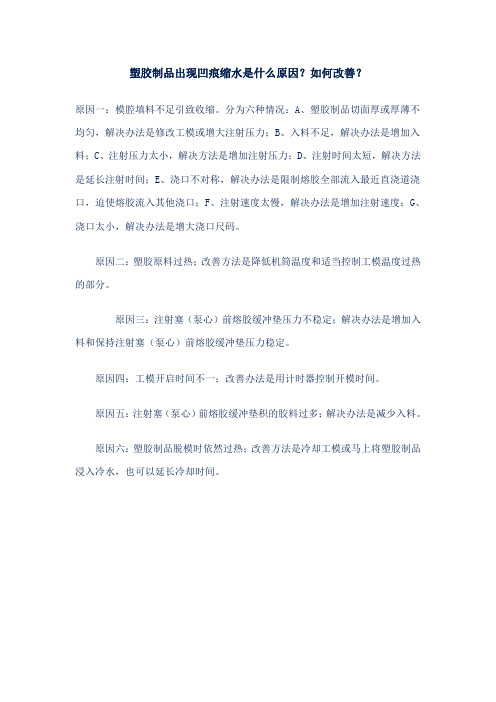
塑胶制品出现凹痕缩水是什么原因?如何改善?
原因一:模腔填料不足引致收缩。
分为六种情况:A、塑胶制品切面厚或厚薄不均匀,解决办法是修改工模或增大注射压力;B、入料不足,解决办法是增加入料;C、注射压力太小,解决方法是增加注射压力;D、注射时间太短,解决方法是延长注射时间;E、浇口不对称,解决办法是限制熔胶全部流入最近直浇道浇口,迫使熔胶流入其他浇口;F、注射速度太慢,解决办法是增加注射速度;G、浇口太小,解决办法是增大浇口尺码。
原因二:塑胶原料过热;改善方法是降低机筒温度和适当控制工模温度过热的部分。
原因三:注射塞(泵心)前熔胶缓冲垫压力不稳定;解决办法是增加入料和保持注射塞(泵心)前熔胶缓冲垫压力稳定。
原因四:工模开启时间不一;改善办法是用计时器控制开模时间。
原因五:注射塞(泵心)前熔胶缓冲垫积的胶料过多;解决办法是减少入料。
原因六:塑胶制品脱模时依然过热;改善方法是冷却工模或马上将塑胶制品浸入冷水,也可以延长冷却时间。
塑胶件缩水的原因及改善的方法
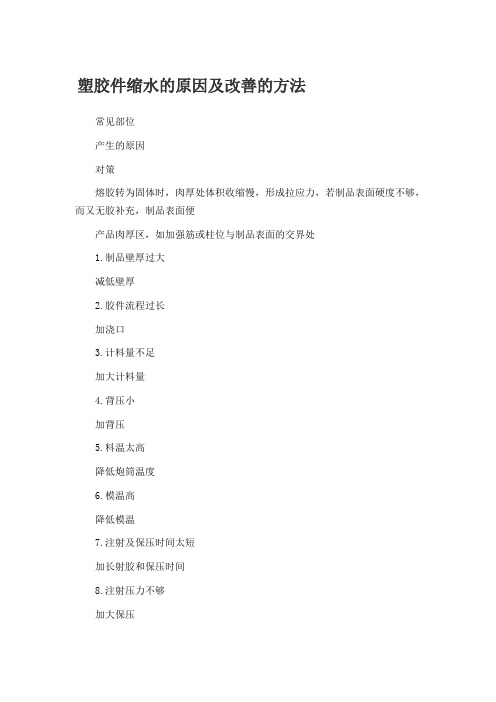
塑胶件缩水的原因及改善的方法常见部位产生的原因对策熔胶转为固体时,肉厚处体积收缩慢,形成拉应力,若制品表面硬度不够,而又无胶补充,制品表面便产品肉厚区,如加强筋或柱位与制品表面的交界处1.制品壁厚过大减低壁厚2.胶件流程过长加浇口3.计料量不足加大计料量4.背压小加背压5.料温太高降低炮筒温度6.模温高降低模温7.注射及保压时间太短加长射胶和保压时间8.注射压力不够加大保压9.注射速度太快减慢射速10.保压切换位置不当调好位置11.运水不足增加运水组数12.浇口位置不当改浇口位置至肉厚部分13.过胶圈磨损更换过胶圈14.射嘴堵塞清理射嘴15.液压油温高清理液压油热交换器缩水除了注塑工艺外,一是设计壁厚及骨位厚薄不合理,骨位厚度一般不过超过壁厚的2/3,二是从模具上来说入水设计不合理(如果长方形产品从一边入水就有机会在对面有骨位处产生缩水)及排模不合理(如果厚壁产品在主流道的尾部,导致机注塑压力不够)。
出模斜度最小要0。
5度以上,不同表面要求斜度也要求不同,如果是晒粗纹,则要求大些。
如果无特别要求当然是越大越好主要之不良成形及其原因?????????与成形机有关者??????????????????充填不良???????(a)射出压力过低(b)压出缸中温度过低(c)压出缸及喷嘴堵阻(d)喷嘴过小(e)材料供给过少(f)储料斗堵阻(g)射出速度形成过迟???????(a)浇口位置不适当(b)结合方法不良(c)流道过狭(d)型模温度过低(e)冷却残渣对流道及浇口堵阻(f)成形品有肉厚特薄之处???????(a)流动性恶(b)润滑剂不足气泡﹑条纹﹑斑点???????(a)射出压力不足(b)射出速度形成过早(c)射出断续(d)加压(保压,开模)时间不足???????(a)浇口位置不适当(b)结合方法不良(c)成形品厚度不均一(d)流道过狭(e)成形品在型模内受必要以上之冷却???????(a)流动性恶(b)有吸湿性(c)含有挥发性物质表面光泽不良???????(a)压力缸中加热不均一(b)喷嘴一部分堵阻(c)喷嘴径过大(d)成形品超过成形机之能量(e)压力缸中压力过低(f)材料供应量不足???????(a)电镀不良(b)浇口及流道过狭(c)冷却残渣储穴欠缺(d)型模表面为水及油污染(e)型模温度过低(f)结合方法不良???????(a)有吸湿性(b)含有挥发物质(c)异质物混入污染熔合线???????(a)喷嘴温度过低(b)射出压力不足(c)射出压力形成过迟???????(a)浇口﹐流道过小(b)浇口位置不适当(c)型模温度过低(d)结合方法不良???????a)材料固化过速(b)有吸湿性(c)润滑不良磨边生成???????(a)射出压力过高(b)开模压力不足(c)成形材料供给量过多(d)加压时间(保压,开模)过长???????(a)型模未能紧密密合(b)型模中有异物及毛刺等附着﹐不能完全关合(c)型穴设计不良﹐边缘部份材料容易挤出(d)投影面积相应机械为过大??????? (a)材料流动性过大缺凹???????(a)射出压力不足(b)加热温度过高(c)射出速度形成过迟(d)材料供应两量不足(e)成形品超过成形机之能量(f)加压时间过短???????(a)型模温度过高﹐并且不均一(b)浇口过狭(c)流道过狭(d)成形品厚度不均一(e)喷嘴过细(f)作业循环过速(g)保压时间不足???????(a)材料过软注道及成形品对型模黏着???????(a)射出压力过高,亦且材料工给量过多(b)加热温度过低,亦且加热温度过高(c)加压时间(保压,开模)过长(d)顶出机构(顶出装置)不良???????(a)喷嘴与型模装接不良(b)喷嘴相应注道为过粗(c)注道锥度过小(d)注道衬套有疵病(e)型模温度过高(f)型穴内面有疵病(g)型穴退缩倾斜不足(h)型穴有低陷部份﹐再者角隅过份棱锐???????(a)润滑剂不足怎样避免产品凹痕和气孔产品凹痕通常由于制品上受力不足、物料充模不足以及制品设计不合理,凹痕常出现在与薄壁相近的厚壁部分。
- 1、下载文档前请自行甄别文档内容的完整性,平台不提供额外的编辑、内容补充、找答案等附加服务。
- 2、"仅部分预览"的文档,不可在线预览部分如存在完整性等问题,可反馈申请退款(可完整预览的文档不适用该条件!)。
- 3、如文档侵犯您的权益,请联系客服反馈,我们会尽快为您处理(人工客服工作时间:9:00-18:30)。
(a)潤滑劑不足
怎样避免产品凹痕和气孔
产品凹痕通常由于制品上受力不足、物料充模不足以及制品设计不合理,凹痕常出现在与薄壁相近的厚壁部分。气孔的造成是由于模腔塑料不足,外圈塑料冷却固化,部塑料产生收缩形成真空。多半由于吸湿性物料未干燥好,以及物料中残留单体及其他化合物而造成的。判断气孔造成的原因,只要观察塑料制品的气泡在开模时瞬时出现还是冷却后出现。如果当开模时瞬时出现,多半是物料问题,如果是冷却后出现的则属于模子或注塑条件问题。
(d)投影面積相應机械為過大
(a)材料流動性過大
缺凹
(a)射出壓力不足
(b)加熱溫度過高
(c)射出速度形成過遲
(d)材料供應兩量不足
(e)成形品超過成形機之能量
(f)加壓時間過短
(a)型模溫度過高﹐并且不均一
(b)澆口過狹
(c)流道過狹
(d)成形品厚度不均一
(e)噴嘴過細
(f)作業循環過速
(g)保壓時間不足
(a)澆口﹐流道過小
(b)澆口位置不适當
(c)型模溫度過低
(d)結合方法不良
a)材料固化過速
(b)有吸濕性
(c)潤滑不良
磨邊生成
(a)射出壓力過高
(b)開模壓力Hale Waihona Puke 足(c)成形材料供給量過多
(d)加壓時間(保壓,開模)過長
(a)型模未能緊密密合
(b)型模中有异物及毛刺等附著﹐不能完全關合
(c)型穴設計不良﹐邊緣部份材料容易擠出
二是从模具上来说入水设计不合理(如果长方形产品从一边入水就有机会在对面有骨位处产生缩水)
及排模不合理(如果厚壁产品在主流道的尾部,导致机注塑压力不够)。
出模斜度最小要0。5度以上,不同表面要求斜度也要求不同,如果是晒粗纹,则要求大些。
如果无特别要求当然是越大越好
主要之不良成形及其原因
与成形机有關者
充填不良
(c)噴嘴徑過大
(d)成形品超過成形機之能量
(e)壓力缸中壓力過低
(f)材料供應量不足
(a)電鍍不良
(b)澆口及流道過狹
(c)冷卻殘渣儲穴欠缺
(d)型模表面為水及油污染
(e)型模溫度過低
(f)結合方法不良
(a)有吸濕性
(b)含有揮發物質
(c)异質物混入污染
熔合線
(a)噴嘴溫度過低
(b)射出壓力不足
(c)射出壓力形成過遲
(a)射出壓力過低
(b)壓出缸中溫度過低
(c)壓出缸及噴嘴堵阻
(d)噴嘴過小
(e)材料供給過少
(f)儲料斗堵阻
(g)射出速度形成過遲
(a)澆口位置不适當
(b)結合方法不良
(c)流道過狹
(d)型模溫度過低
(e)冷卻殘渣對流道及澆口堵阻
(f)成形品有肉厚特薄之處
(a)流動性惡
(b)潤滑劑不足
气泡﹑條紋﹑斑點
(a)材料過軟
注道及成形品對型模黏著
(a)射出壓力過高,亦且材料工給量過多
(b)加熱溫度過低,亦且加熱溫度過高
(c)加壓時間(保壓,開模)過長
(d)頂出機構(頂出裝置)不良
(a)噴嘴与型模裝接不良
(b)噴嘴相應注道為過粗
(c)注道錐度過小
(d)注道襯套有疵病
(e)型模溫度過高
(f)型穴內面有疵病
(g)型穴退縮傾斜不足
(a)射出壓力不足
(b)射出速度形成過早
(c)射出斷續
(d)加壓(保壓,開模)時間不足
(a)澆口位置不适當
(b)結合方法不良
(c)成形品厚度不均一
(d)流道過狹
(e)成形品在型模內受必要以上之冷卻
(a)流動性惡
(b)有吸濕性
(c)含有揮發性物質
表面光澤不良
(a)壓力缸中加熱不均一
(b)噴嘴一部分堵阻
(1)物料问题:
①干燥物料
②加润滑剂
③降低物料中挥发物
(2)注塑条件问题
①注射量不足;
②提高注射压力;
③增加注射时间;
④增加全压时间;
⑤提高注射速度;
⑥增加注射周期;
⑦操作原因造成的注射周期反常。
(3)温度问题
①物料太热造成过量收缩;
②物料太冷造成充料压实不足;
③模温太高造成模壁处物料不能很快固化;
降低模温
7.注射及保压时间太短
加长射胶和保压时间
8.注射压力不够
加大保压
9.注射速度太快
减慢射速
10.保压切换位置不当
调好位置
11.运水不足
增加运水组数
12.浇口位置不当
改浇口位置至肉厚部分
13.过胶圈磨损
更换过胶圈
14.射嘴堵塞
清理射嘴
15.液压油温高
清理液压油热交换器
缩水除了注塑工艺外,一是设计壁厚及骨位厚薄不合理,骨位厚度一般不过超过壁厚的2/3,
②使注射周期正常;
(6)冷却条件问题:
①部件在模冷却过长,避免由外往里收缩,缩短模子冷却时间;
②将制件在热水中冷却。
塑胶件缩水的原因及改善的方法
常见部位
产生的原因
对策
熔胶转为固体时,肉厚处体积收缩慢,形成拉应力,若制品表面硬度不够,而又无胶补充,制品表面便
产品肉厚区,如加强筋或柱位与制品表面的交界处
1.制品壁厚过大
减低壁厚
2.胶件流程过长
加浇口
3.计料量不足
加大计料量
4.背压小
加背压
5.料温太高
降低炮筒温度
6.模温高
④模温太低造成充模不足;
⑤模子有局部过热点;
⑥改变冷却方案。
(4)模具问题;
①增大浇口;
②增大分流道;
③增大主流道;
④增大喷嘴孔;
⑤改进模子排气;
⑥平衡充模速率;
⑦避免充模料流中断;
⑧浇口进料安排在制品厚壁部位;
⑨如果有可能,减少制品壁厚差异;
⑩模子造成的注射周期反常。
(5)设备问题:
①增大注压机的塑化容量;