固定床列管式反应器的设计 决赛国学改
固定床反应器的设计—固定床反应器特点与结构

间接换热式催化剂床层绝热操作方程
A-B 反应 x↑
B-C 换热 x不变
C-D 反应 x↑
D-E 换热 x不变
E-F 反应 x↑
F-G 换热 x不变
绝热操作线方程式: 表达温度与转化率的 关系。
反应热效应、绝热温 升、热熔、密度一定 时,反应段斜率相同
1.绝热式固定床反应器
(3)多段式催化床层温度的分布:间接换热式催化剂床层温度分布 和冷激(直接换热)式催化剂床层温度分布
1.绝热式固定床反应器
(2)多段式:有多段催化剂床层,反应和冷却间隔进行。 适应场合:反应热效应较大,反应速率慢的反应。 中间间接换热式:床层间加换热器(),调节温度。如:水煤气转换、二氧化硫的
氧化反应
1.绝热式固定床反应器
(2)多段式:有多段催化剂床层,反应和冷却间隔进行。 适应场合:反应热效应较大,反应速率慢的反应。
中间间接换热式:床层间加换热器(换热盘管),调节温度。如:环己醇脱氢制环己酮 及丁二醇脱水制丁二烯 。
换热盘管
1.绝热式固定床反应器
(2)多段式:有多段催化剂床层,反应和冷却间隔进行。适应反应 热效应较大,反应速率慢的反应。
冷激式:用冷流体直接与上一段出口气体混合来实现降温。多适应于工业上高压力操
•以高温烟道气为载体, 将反应所需热量在反应 管外通过管壁传给催化 剂层
生产实例:乙苯催化脱 氢制备苯乙烯。
2、换热式固定床反应器
(1)外换热式:以各种载热体为换热介质的对外换热式反应器多为 列管式结构。 载热体选择:
低于240℃----加压热水 250—300 ℃ -----导热油 300 ℃ -----熔盐(KNO353%,NaNO27%、NaNO340%) 600—700℃左右----烟道气
固定床反应器的设计计算

固定床反应器的设计计算
首先,确定反应器尺寸是固定床反应器设计的首要任务。
反应器的大
小取决于所需的反应物流量、反应速率以及反应物在催化剂上的接触效果等。
一般来说,如果催化剂的活性较高,可以选择较小的反应器尺寸,以
便增加接触效果和提高反应速率。
其次,确定催化剂床层数也是设计中的一个关键步骤。
催化剂床层数
的选择与反应物的转化率和选择性有关。
催化剂床层数较大时,反应物的
转化率和选择性可能会提高,但也会增加反应器的装填材料和能量损失。
因此,需要根据具体情况进行综合考虑,确定合适的床层数。
然后,确定反应条件是固定床反应器设计的重要因素之一、反应条件
包括反应温度、反应压力和反应物的进料浓度等。
这些参数的选择应根据
反应物的特性、反应速率常数以及副反应的发生情况等因素进行综合判断。
另外,反应温度还会对反应热平衡和反应速率等方面产生影响,需要通过
热力学计算和实验验证来确定。
最后,热力学参数也是固定床反应器设计中必须考虑的因素。
热力学
参数包括反应热和化学平衡等。
反应热的计算可以通过热力学数据以及反
应物的物化性质进行估算。
而化学平衡的考虑可以通过化学平衡常数和反
应物浓度的估计来确定。
综上所述,固定床反应器的设计计算涉及的内容较为复杂,需要综合
考虑反应器尺寸、催化剂床层数、反应条件和热力学参数等因素。
设计计
算的目标是确定合适的反应器尺寸和操作条件,以实现高效的反应产率和
选择性。
同时,还需要关注反应器的稳定性和运行寿命,对反应器进行适
当的改进和优化。
固定床反应器的工艺设计

固定床反应器的工艺设计1. 引言固定床反应器是一种常见的化工设备,广泛应用于化学工业中的各种反应过程中。
它由一个固定的催化剂床和一个通过床上空隙流动的气体或液体组成。
通过适当的设计和调节,固定床反应器可以实现高效的反应转化率和产出。
本文将介绍固定床反应器的工艺设计,包括反应器的结构、催化剂选择、反应条件等方面的内容。
2. 反应器的结构固定床反应器一般由反应器本体、催化剂床层、进出料口、反应气体或液体的流动通道等组成。
其中,反应器本体一般采用合适的材料制成,以承受反应过程中的温度和压力。
催化剂床层通常由多层的填料或颗粒催化剂组成,以提供反应活性面积和流动通道。
为了实现高效的反应,固定床反应器通常还配备有预热器、冷却器、再生器等附属设备,以控制反应温度、催化剂活性和产物的分离等。
3. 催化剂的选择催化剂是固定床反应器中实现化学反应的关键组件。
在选择催化剂时,需要考虑反应的性质、反应温度和压力、催化剂的稳定性和活性等因素。
常见的催化剂包括金属催化剂、氧化物催化剂、酸碱催化剂等。
选择合适的催化剂可以提高反应的转化率和选择性,降低反应温度和压力,减少副反应和催化剂失活等问题。
4. 反应条件的确定反应条件的确定是固定床反应器工艺设计的重要环节。
反应条件包括温度、压力、反应物浓度、催化剂负荷量等因素。
在确定反应温度时,需要考虑反应的热力学平衡和动力学要求。
过高的温度可能导致副反应的发生和催化剂失活,而过低的温度则可能使反应速率过慢。
压力的选择取决于反应物的状态和反应的热力学平衡。
在固定床反应器中,通常会通过控制进料流量和床层压降来维持适当的压力。
反应物浓度对反应速率和选择性有直接影响。
合理选择反应物浓度可以提高反应转化率和产物选择性。
催化剂负荷量的确定需要考虑催化剂的活性和催化剂床层的透气性。
过高的催化剂负荷量可能导致流动阻力加大,而过低的负荷量则可能使反应活性降低。
5. 反应器的优化和改进固定床反应器的工艺设计是一个复杂的过程,通常需要通过试验和模拟来进行优化和改进。
列管式固定床反应器壳程结构的设计

维普资讯
石 油 化 工 设 备 技 术
2002年
分 配板 孔进 入壳程 .环槽 内的流体 流量 逐渐 减小 , 这 一过 程 为典型 的“变 质量 流”。若 环槽 截 面积不 变 .伴 随流 量逐渐 减小 ,槽 内流体 静压 能 上升 。当 流 体从 h 流 到 ^ 处 ,若 静 压 能 增 量 大 于 该 段 流 动 压力 降损 失 ,则 从 h:处 进^ 的流体 的推 动 力 大 于 h 处 的 推 动 力 ,所 以 h!的 开 孔 面 积 应 小 于 h 的 开 孔 面 积 。依 此 类 推 .分 配 板 上 开 L面 积 应 递 减 , 使 流 量 均 匀 分 配 。
从 流体 力学 上 分 析 ,造成 上述 流 体流 动形 式 的环槽 通道 总称 为集合 管 。又可将 人 口的通 道称 为分流 管 ,出 口通 道 为集 流 管 。换 热 介质 由人 口 进 入 环 槽 即 分 为 两 路 .其 中 一 路 由 h.,h … … h
收 稿 日期 :2001 li—i6 作者 筒 彳r:赵 增 慧 (1952一 ).女 ,北 京 人 ,l984年 毕 业 于 北 京 石油 化 工 学 院化 工 设 备 与 机 械 专 业 ,获 学 士 学 位 ,讲 师 , 现 从事 固定 床 反 应 器 工 艺 及 设 备 设 计 研 究 和计 算 机 辅 助 设 计 工作 ,已发 表 论 文 5篇 。
Hale Waihona Puke 其 所 在 位 置 与 环 槽 总 人 口 的 距 离 而 递 减 (出 口 处 为 递 增 ),人 (出 )口 两 分 流 通 道 的 开 孔 对 称 分 布 。 这种 结构 的 目的是想 使换 热介质 均 匀地 流人 (出) 壳 程 。
图 1 某苯 酐 反 应 器 壳 体人 口结 构示 意 图
基于列管式固定床反应器的换热结构设计进展

器(丙烯酸反应器及煤制乙醇反应器等' 化工装置生产规模不断放大已经成为当前发
展的趋势! 核心反应装备的大型化也成为国内外 争 相 研 究 的 课 题 )!:)*' 甲 醇 制 烯 烃 (煤 制 乙 二 醇 (煤 制乙醇等新兴煤化工技术不断取得突破! 开始进 入化工大宗品市场! 对单台反应器的产能扩大的
分管束式反应器
一种内置分管束式的径向流反应器结构示意
. A见l图l &Rights Reserved.
路径短解决了轴向流床层压降大的问题循环能 耗较低'( 目前该方案在大型甲醇装置中广泛应 用单台反应器的最大产能可达到 ))* 万 +,-
该径向流反应器在管外装填催化剂作为反应 空间换热介质在管内流动换热管两端通过弯曲汇 总连接到管箱分别连接换热介质的进出口 !&$!. 换热管直管段位置从内向外依次设置有中心进料 分 布 器 催 化 剂 筐 管 束 和 外 收 集 器 #*
传统列管式固定床反应器在管内装填催化剂 时受到反应管布管最小间距的限制其整体催化 剂装填率较低 只能通过扩大反应器直径来满足 装置大型化的需求 为了进一步提高催化剂装填 率将反应介质空间和换热介质空间调换催化剂
图 刺刀管式夹套管式反应器结构示图
自冷式反应器 对于放热强度小的反应工况 可通过反应器
. All %Ri&'g#h()ts*+R"e(+s&e'r' v"e, d-.&./ 0123.)(& 4/+52/5+& 6.'&7 ") 8595:.+ ;#1&7 6&7 <&.2/"+
列管反应器设计
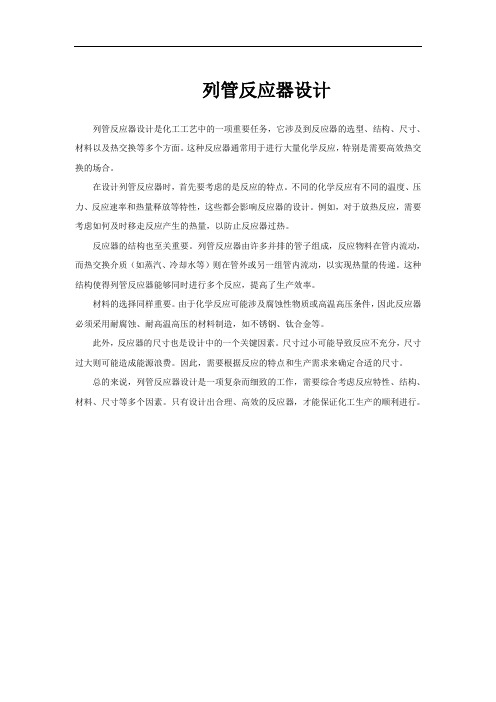
列管反应器设计
列管反应器设计是化工工艺中的一项重要任务,它涉及到反应器的选型、结构、尺寸、材料以及热交换等多个方面。
这种反应器通常用于进行大量化学反应,特别是需要高效热交换的场合。
在设计列管反应器时,首先要考虑的是反应的特点。
不同的化学反应有不同的温度、压力、反应速率和热量释放等特性,这些都会影响反应器的设计。
例如,对于放热反应,需要考虑如何及时移走反应产生的热量,以防止反应器过热。
反应器的结构也至关重要。
列管反应器由许多并排的管子组成,反应物料在管内流动,而热交换介质(如蒸汽、冷却水等)则在管外或另一组管内流动,以实现热量的传递。
这种结构使得列管反应器能够同时进行多个反应,提高了生产效率。
材料的选择同样重要。
由于化学反应可能涉及腐蚀性物质或高温高压条件,因此反应器必须采用耐腐蚀、耐高温高压的材料制造,如不锈钢、钛合金等。
此外,反应器的尺寸也是设计中的一个关键因素。
尺寸过小可能导致反应不充分,尺寸过大则可能造成能源浪费。
因此,需要根据反应的特点和生产需求来确定合适的尺寸。
总的来说,列管反应器设计是一项复杂而细致的工作,需要综合考虑反应特性、结构、材料、尺寸等多个因素。
只有设计出合理、高效的反应器,才能保证化工生产的顺利进行。
固定床列管式反应器的设计 决赛国学改

目录固定床列管式反应器1的设计:一、反应器选择及操作条件说明 (3)二工艺计算 (5)2.1 催化剂用量 (5) (6)2.2 反应器列管数 (6)2.3换热面积三设备尺寸计算 (7)3.1反应器筒体直径 (7)3.2反应器高度 (8)3.3筒体和封头厚度 (8)四接管零部件尺寸计算 (9)4.1进料管 (9)4.2 出料管 (10)4.3 熔盐进出口 (10)4.4安全阀 (10)4.5 温度计接管 (11)4.6孔 (11)五设计结果汇总 (12)1六参考文献: (13)固定床列管式反应器1的设计:一、反应器选择及操作条件说明 (14)二工艺计算 (16)2.1 催化剂用量 (16) (17)2.2 反应器列管数 (17)2.3换热面积三设备尺寸计算 (18)3.1反应器筒体直径 (18)3.2反应器高度 (19)3.3筒体和封头厚度 (19)四接管零部件尺寸计算 (20)4.1进料管 (20)4.2 出料 (21)4.3 熔盐进出口 (21)4.4安全阀 (22)4.5 温度计接管 (22)4.6孔 (22)五设计结果汇总 (23)六参考文献: (24)2固定床列管式反应器1的设计一、反应器选择及操作条件说明A反应器选择:本工艺反应为气固相反应,返混程度不高,为了很好的控制温度,使传热的面积更大,我们选择了列管式固定床形式。
它的优点有:①返混小,流体同催化剂可进行有效接触,当反应伴有串联副反应时可得较高选择性;②催化剂机械损耗小;③结构简单。
它的投资和操作费用介于绝热固定床和流化床之间,气相两步氧化法生产丙烯酸比较理想的反应设备。
B操作条件说明:1.反应方程式:CH2CHCH3+O2→CH2CHCHO该步骤中会有副反应发生,副反应产物为乙酸和丙酸等。
进料状态:丙烯是液态进料,经过丙烯蒸发器后变为气体进入预混合器,空气经过空气压缩机进入预混合器,水直接以液态水形式进入预混合器。
2.工艺条件确定:使用Mo-Bi系列催化剂。
列管式固定床反应器的模拟与设计 毕业设计

列管式固定床反应器的模拟与设计摘要:列管式固定床反应器是化工行业和石化行业中一种非常重要的反应器,对一些强放热反应优势明显。
传统的模拟和设计列管式反应器的方法是基于单管实验,假定工业反应器内各反应管的操作条件与单管实验条件相同,也就是说忽视了工业反应器内冷却条件和流动的不均匀性,这个假定会引起很大的误差。
邻二甲苯氧化制苯配是工业生产苯配的主要工艺,其工业生产主要在列管式固定床反应器内进行。
要设计合理的列管式反应器,最重要的就是确定壳程空间的最优解。
本文提出了一个关于壳程的二维小池模型,将壳程空间分成若干个二维小池,在所有小池内,冷却剂的流动只有平行于管束和垂直于管束两个分量。
关键词:列管式反应器,固定床,结构设计目录列管式固定床反应器的模拟与设计 (1)第1章前言 (3)第2章文献综述 (4)2.1苯配生产 (4)2.2列管式固定床反应器的结构 (5)2.3列管式固定床反应器的设计进展 (7)2.4反应器的分析方法 (18)2.5反应器结构的优化 (19)第3章列管式固定床反应器中邻二甲苯氧化反应的研究 (20)3.1邻二甲苯氧化制苯配工艺 (20)3.2一维拟均相模型求解管侧 (22)3.3二维拟均相模型求解管侧 (24)3.4操作参数对邻二甲苯氧化反应的影响 (26)3.5结果与讨论 (28)第6章全文总结 (29)参考文献 (31)第1章前言固定床催化反应器是化学工业和石油化学工业中应用多、用面广泛的反应设备,根据其换热方式可分为绝热和非绝热(列管式)两种。
对于反应热效应很大,收率对温度敏感而又要求高转化率和高选择性的反应,为维持适宜的温度,必须用换热介质来移走或供给热量,采用列管式固定床反应器是非常合适的。
如丙烯胺氧化制备丙烯睛、蔡或邻二甲苯氧化制备苯配、乙烯氧化制环氧乙烷、苯或正丁烷氧化制顺配、异丁烯氧化制备甲基丙烯酸等[1][5]。
如今,相当一部分气固相催化反应在列管式固定床反应器中进行,而该反应器的设计开发技术大都是从国外引进,国内的装置普遍存在温差较大的问题,主要是壳程冷却剂流动分布不均的问题。
列管式固定床反应器设计的限制条件

本工作的目的是导出列管式固定床反应器热稳 定性 、热灵敏性及床层压降的限制条件 , 并通过便于 反应器设计的一些易测变量(如管径 、管长 、物料流 量等)将其表达为简单实用的判据 。
剂颗粒间只存在点接触 , 导热面积极小 , 故其传热主
要依靠气体经催化剂颗粒间空隙时的分流与汇合作
用 , 因此对 λe 的静态贡献可以忽略不计 。 如果只考
虑对 λe 的动态贡献 , 则传热 Peclet 准数可 用传质 Peclet 准数近 似[ 5] 。 在工业反应器的高流 速下 , 传 质 Peclet 准数约为 10[ 7, 8] 。 按照文献[ 5] 对 Peclet 准
便 。为便于实际应用 , 以冷却介质温度 T c 代替式
(1)中的壁温 T W , 则温度灵敏性判据应当满足 :
T1.37
Tθc <1
(13)
对气固相反应 , 由于气体热容很小 , 气体沿轴向 的载热作用相对于径向传热可以忽略 ;又因列管式
反应器长径比很大 , 轴向传热的热阻很大 , 轴向传热
相对于径向传热也可以忽略 。 因此 , 列管式反应器
在选择列管 管径 d 和长度 L 时 , 常常需要 对 一些数值进行权衡 。 由式(24)、式(25)可见 , 列管 管径越小 , 则床层有更好的热稳定性 , 但管径越小 , 设备费用越高 。对管长 L 的限制首先是压降的考 虑 。 此外 , 反应器内反应管束的物理支撑问题也对 L 有所限制 。在满足限制条件的范围内 , 列管选择 长一些 , 可以使允 许的管径大一些 , 从经济的 角度 考虑是有利的 。在列管式反应器操作过程中 , 有时 反应物料的流量可能发生变化 , 这种情况下要考虑 流量变化对上述限制 条件的影响 。 如果反应 不受 传质的控制 , 则反 应速率与流量无关 , 只取决 于进 料组成和反应温度 。 但流量的 改变不仅要影 响式 (24)、式(25)中的总 传热系数 U , 同时对 式(4)中 的 G 也有 影响 。 这 种情况下 , 温度灵 敏性会因 流 量的增大而减小 , 因此应该以反应器物料流量的下 限来计算判据 。
固定床反应器的设计与分析

重点掌握
※固定床压力降的计算方法。 ※固定床催化反应器拟均相活塞流模型 的建立与应用,包括考虑内扩散的情况。 ※绝热式固定床催化反应器催化剂用量 的计算方法。
深入理解
▼固定床催化反应器的主要类型及其结 构特点。 ▼换热式固定床催化反应器的设计优化 问题、参数敏感性问题以及飞温和失控 的现象。
22:46
压力降的计算
流体在固定床中的流动,与空管中的流体流动相似, 只是流道不规则而已。故此可将空管中流体流动的压力 降计算公式修正后用于固定床。
固定床压力降计算公式:
Lu (1 ) P f 3 dS
2 0
22:46
(6.2-2)
式中:ρ——流体密度
f —— 摩擦系数 u0——空管流速
当Re>10时,(Pea)m=2.有
Da Da d p 1 d p 1 Pea uLr ud p Lr 2 Lr
0.005
所以,当床层高度Lr>100dp时,可以忽略 床层内轴向混合扩散,即将流体在床层内 的轴向流动似为平推流流动。在实际反应 器,能够满足该前提条件,而实验反应器 往往不能达到,希注意。
22:46
① 一维模型
在一维模型中,床层径向温度被认为是相同 的。床层热阻和壁膜热阻合并作为一个热阻来考 虑,用床层与器壁间的给热系数h0来表示,给热 速率式以床层平均温度tm与壁温tW之差来定义:
q ht A(tm t ht 值大致为 61.2~320kJ/(m2· h· K)。下面推荐两个计算ht的关 联式,
T0
TC Tf
Tf
T0
逆流
并流
图6.1-3 自热式反应器示意图
列管式固定床反应器模拟与设计进展

列管式固定床反应器模拟与设计进展
Stank.,A;薛冠申
【期刊名称】《化学工程》
【年(卷),期】1990(18)6
【摘要】一、前言传统的固定床设计一般假定工业多管反应器的实际操作条件与单管实验反应器的操作条件相同,这个假定只对热载体完全均匀分布的并流反应器适用。
但在实际的操作系统中,管与管之间的相互作用对过程的总效率以及冷却剂经壳程的泵送成本有很大的影响,而且。
【总页数】11页(P62-72)
【作者】Stank.,A;薛冠申
【作者单位】不详;不详
【正文语种】中文
【中图分类】TQ051.14
【相关文献】
1.列管式固定床反应器的设计探讨 [J], 赵增慧;夏丽
2.列管式固定床反应器设计的限制条件 [J], 陈尚伟
3.列管式固定床反应器壳程结构的设计 [J], 赵增慧
4.列管式固定床反应器催化剂支托结构的设计 [J], 赵增慧;夏丽
5.基于列管式固定床反应器的换热结构设计进展 [J], 何鹏;吕靖;刘应春;杨培志因版权原因,仅展示原文概要,查看原文内容请购买。
- 1、下载文档前请自行甄别文档内容的完整性,平台不提供额外的编辑、内容补充、找答案等附加服务。
- 2、"仅部分预览"的文档,不可在线预览部分如存在完整性等问题,可反馈申请退款(可完整预览的文档不适用该条件!)。
- 3、如文档侵犯您的权益,请联系客服反馈,我们会尽快为您处理(人工客服工作时间:9:00-18:30)。
目录固定床列管式反应器1的设计:一、反应器选择及操作条件说明 (3)二工艺计算 (5)2.1 催化剂用量 (5) (6)2.2 反应器列管数 (6)2.3换热面积三设备尺寸计算 (7)3.1反应器筒体直径 (7)3.2反应器高度 (8)3.3筒体和封头厚度 (8)四接管零部件尺寸计算 (9)4.1进料管 (9)4.2 出料管 (10)4.3 熔盐进出口 (10)4.4安全阀 (10)4.5 温度计接管 (11)4.6孔 (11)五设计结果汇总 (12)1六参考文献: (13)固定床列管式反应器1的设计:一、反应器选择及操作条件说明 (14)二工艺计算 (16)2.1 催化剂用量 (16) (17)2.2 反应器列管数 (17)2.3换热面积三设备尺寸计算 (18)3.1反应器筒体直径 (18)3.2反应器高度 (19)3.3筒体和封头厚度 (19)四接管零部件尺寸计算 (20)4.1进料管 (20)4.2 出料 (21)4.3 熔盐进出口 (21)4.4安全阀 (22)4.5 温度计接管 (22)4.6孔 (22)五设计结果汇总 (23)六参考文献: (24)2固定床列管式反应器1的设计一、反应器选择及操作条件说明A反应器选择:本工艺反应为气固相反应,返混程度不高,为了很好的控制温度,使传热的面积更大,我们选择了列管式固定床形式。
它的优点有:①返混小,流体同催化剂可进行有效接触,当反应伴有串联副反应时可得较高选择性;②催化剂机械损耗小;③结构简单。
它的投资和操作费用介于绝热固定床和流化床之间,气相两步氧化法生产丙烯酸比较理想的反应设备。
B操作条件说明:1.反应方程式:CH2CHCH3+O2→CH2CHCHO该步骤中会有副反应发生,副反应产物为乙酸和丙酸等。
进料状态:丙烯是液态进料,经过丙烯蒸发器后变为气体进入预混合器,空气经过空气压缩机进入预混合器,水直接以液态水形式进入预混合器。
2.工艺条件确定:使用Mo-Bi系列催化剂。
在温度为325℃时候单程的丙烯醛收率为90.2%,丙烯酸的收率为6.0%,总收率为96.2%。
原料组成反应器一的物料衡算表格可以确定。
反应温度控制在320℃左右,出料温度为250℃,该反应是放热反应,反应产生的热量要及时通过熔盐经熔盐换热器带走。
反应温度反应温度对选择性、空时收率及出口气中各组分气体含量有一定关系。
当选择操作温度比较低时,反应的选择性较好,但空时收率较低;随着温度的升高,反应选择性略有下降,与此同时空时收率在逐渐提高。
温度继续升高,由于完全氧化副反应的加剧,使得反应选择性明显下降,而且因为大量的氧气被消耗在完全氧化副反应上,使得反应器出口气中氧气的含量大幅度地减少,并有一定量的一氧化碳生成,而一氧化碳的存在可使催化剂3的活性减退,这样必然使得空时收率产生明显下降。
因此,丙烯酸合成过程存在着一个最适宜的操作温度范围,并且随着使用催化剂活性的不断下降,需要相应地将操作温度逐渐提高。
反应压力在丙烯酸地合成过程中,由于原料的单程转化率较低,丙烯的单程转化率一般较低。
因此,需要有大量的气体物料在系统内循环。
丙烯酸合成反应属于分子数减少的反应,增加压力有利于反应向生成丙烯醛和丙烯酸方向进行,同时加压使反应物的浓度提高,有助于反应速度的加快,这样就使得反应的空时收率能有所提高。
因此,提高压力不仅可使空时收率提高,而且有利于反应选择性的改善。
但是,当压力过大时容易有二聚体的出现,不利于得到所需产品。
当然压力的提高要受到设备条件的约束,设备的投资费用随着压力的升高而提高。
3.已知物性参数由物料衡算得到如下表格:45其中进料的总质量流量为25617.8 kg/h ,摩尔流量为887.732kmol/h.出料的总质量流量为25617.8 kg/h ,摩尔流量为88,2.834kmol/h.二 工艺计算2.1 催化剂用量此工艺采用列管式固定床反应器,催化剂填充于反应器的列管当中。
催化剂为钼-铋催化剂,圆形,粒度为Φ5.2mm ,催化剂的空速为95h -1。
下面是反应方程式:CH 2CHCH 3+O2→CH 2CHCHO由《物料衡算》中可得,原料进料总的质量流量为25617.8kg/h,在该条件下进料的平均密度为6.25kg/m 3由公式:vV V f R上式中:R V 为催化剂床层体积,单位为m 3;6fV 为原料气体体积流量,单位为m 3/h ;v 为催化剂空速,单位为h -1。
故得:)(15.4325.6958.256173m V R =⨯= 2.2 反应器列管数给定管子为Φ30mm ×2.5mm ,故内径d t 为0.02m ,催化剂填充高度为3.5m 。
故列管数)(251285.3)025.0(415.43422根=⨯⨯==ππLd V n t R 列管采用正三角形排列,实际取的管数为25200根。
2.3换热面积2.3.1热量衡算:由aspen 模拟可得:对于该反应,反应吸收的总热量为:10993817KJ/h;反应放出的总热量为:17299022KJ/h. 因此对于该反应实际放热量为:17299022-10993817=6305205KJ/h 反应的传热系数为K=130.5 2.3.2核算换热面积熔盐进口温度325℃出口温度为250℃,整个床层近似地看成等温为330℃, 故传热推动力为:C t m 5.422)325330()250330(=-+-=∆7需要传热面积为:285.11365.425.1306305205m t K Q A m =⨯=∆=需实际传热面积为:270.6923252005.3025.014.3m Ln d A t =⨯⨯⨯==π实A 实>A 需,能满足传热要求。
三 设备尺寸计算3.1反应器筒体直径列管式反应器壳体直径用下式计算:D =t(b-1)+2e上式中:t ——列管管间距,对于正三角形排列t=1.368d 0,d 0为列管外径; b ――最外层六边形对角线上的管数,b=2a+1,a 为六边形层数,21)312(6121--=n a , n 为列管数;e ――最外层列管到壳体距离,e=(1~1.5)d 0。
列管为Φ30mm ×2.5mm ,共25200根。
所以t=1.368×0.025=0.0342(m))(9121)32520012(6121层=--⨯⨯=ab=2×91+1=183(根)8e=1.5×0.025=0.0375(m)D =0.0342(183-1)+2×0.0375=6.299(m) 取反应器壳体直径 D =6.3m3.2反应器高度列管长度:由工艺计算中可知,列管长度L =4.55m ; 筒体顶部空间:根据《压力容器手册》,H a =1m ; 筒体底部空间:根据《压力容器手册》,H b =2m ;封头高度:采用EHA 椭圆形封头,根据JB/T 4746—2002可得,曲面高度H 1=1000mm ,直边高度H 2=50mm ,则封头高度 H c =2×(1.0+0.05)=2.1m 。
由于反应器下部用于对反应出料的降温,根据西安华威公司提供的相关材料可知气用于降温部分的长度为2.2m 。
由以上可得:反应器高度H=L+H a +H b +H c +H T=4.5+1.0+2.0+2.1+2.2 =11.8m3.3筒体和封头厚度化工生产中的容器壁厚可根据下式计算:ppD S i-=ϕσ][2式中:S——容器计算厚度,mm;P——设计压力,MPa;Di——筒体内直径,mm;[σ]——材料的许用压力,MPa;ϕ——焊缝系数。
本反应器材质选择不锈钢0Cr18Ni9,查GB150可知,材料的许用压力为82.6MPa;采用双面焊对接焊缝,焊缝系数取0.85;由工艺计算中可知,反应器设计压力为0.4MPa,筒体内直径为6300mm。
所以筒体的计算厚度mm S48.133.085.06.82263003.0=-⨯⨯⨯=查GB708可知,厚度负偏差C1=0.22mm,腐蚀裕量C2=2mm,故筒体的名义厚度δ=S+C1+C2=13.48+0.22+2=15.7mm 取圆整后,则筒体的名义厚度为16mm。
封头厚度与筒体厚度等同。
四接管零部件尺寸计算4.1进料管由《物料衡算》中可知,进料流量smVf/685.33=;根据《常用化工单元设计》书中P81,常压操作时,可取12~20m/s;绝对压力为6000~14000pa时,可取30~50m/s;绝对压小于6000pa时,可取50~70m/s。
由于进料部位的气体密度较小设进料流速为30m/s。
910则进料管直径m u V d ff396.03014.3685.344=⨯⨯==π由以上计算,选取公称直径400mm ,Φ426mm ×8mm 的进料管。
管法兰选用PL400(B)-0.25RF ,外加补强圈,型号为DN200-Q235-B JB/T4736。
4.2 出料管由《物料衡算》中可知,出料流量s m V f /775.63=,管流速fu 同样取30m/s,则出料管直径m u V d ff536.03014.3775.644=⨯⨯==π由以上计算,选取公称直径550mm ,Φ569mm ×9.5mm 的出料管。
管法兰选用PL400(B )-0.25RF ,外加补强圈,型号为DN200×6-B-Q235-B JB/T4736。
4.3 熔盐进出口最大撤热量为:27.22MW同4.1、4.2,熔盐流量s m V f/23.03=,管流速s m u f /2=,熔盐进出口直径 mu V d ff383.00.214.323.044=⨯⨯==π由以上计算,选取公称直径400mm,Φ426mm ×8mm 的接管。
管法兰选用PL400(B)-0.25RF ,外加补强圈,型号为DN200×6-B-Q235-B JB/T4736。
4.4安全阀由本设计设计压力为180Kpa,额定排放压力为180KPa ,参考化工设计手册,选公称11直径为100mm ,Φ108mm ×4mm 的接管,接管距轴500mm 。
管法兰选用PL100(B )-0.25RF 。
查法兰标准:D=210mm ,C=18mm 。
故mm l 46.14518500)41000(5.020006545.0395)410020009045.0(2222=+-+⨯-⨯--++⨯=取管长L 为150mm 。
4.5 温度计接管采用外用接管,内用无缝钢管,参照化工设计手册,外接管为Φ45mm ×3.5mm ,L=137mm ,无缝钢管为Φ32mm ×3.5mm ,长度L=1630mm 。