液压压下AGC控制介绍
AGC液压系统的组成及维护

Vo1.45 NO.3 June 2016
AGC液 压 系统 的 组成 及 维 护
罗 超
(中色科技股份有限公司 ,河南 洛阳 471039)
摘 要 :文章简要介绍了铝板带轧机 AGC液压 系统 的组 成及其基本工作 原理 ,结 合生产过 程中经常 出现的故障进 行 了
AGC液压系统发生故障除 了元器件质量和使用 不 当外 ,最 主要还 是液 压油 受 到污 染 。AGC液 压 系统 要求油液的清洁度为 NAS 6级 ,即便是很小的污染物 都可能导致液压元器件的卡阻或者相对运动面 的磨 损 ,从而导致液压系统频繁 出现故 障 ,因此保证液压 系统 的清 洁至关 重要 。在 液压 系 统安 装 时 ,需 用 面粉 团清 理油 箱 的每一 个角 落 ,尽 量 清理 掉 制造 和 运 输 过 程 中产生 的所 有异 物 ;液压 管 路需 采 用 不锈 钢 氩 弧 焊 焊 接 ,焊 接后 的不 锈 钢 管 必 须 进 行 认 真 清 理 ,尽 可 能 完 全去 除钢 管 内部 的 附着 物 。通 过 加 油 车 往 油 箱 中 加 油 时一定要 通 过过 滤 滤芯 ,要 摈 弃新 油 或 者看 起 来 没 有杂 质 的油液 就是 干 净 的错 误 观念 。加注 完 成 后 , 最好 用过滤 车连 续循 环 过滤 油 箱 内 的油 液 一段 时 间 , 之后 才能用 泵 站连接 阀台进 行 系 统 内 的循 环 冲洗 ,直 至从 油 箱 中取 出 的油 液 经化 验 后 达 到 NAS 6级 。在 生产过程 中也要避免无谓的加油次数 ,避免新油污染 液压 系统 。在 正 常使 用 过 程 中 ,由于 密 封 件 损 坏 、液 压元 器件 磨损 以及 外来 物 污 染 ,油液 的清 洁度 是 不 断 变 化 的 ,除 了按 要 求更换 滤芯 外 还需 定 期按 液 压 油 指 标 (SH/T0599~1994)的 要 求 对 油 箱 内 油 液 进 行 化 验,不满足要求时需及时进行更换 。
AGC控制

液压AGC控制技术的分析与应用摘要:综述板带轧钢厚度控制技术的发展和产生厚差的原因(主要有:温度、轧制力等)。
着重介绍了液压厚度自动控制的概念、原理、应用等。
关键词:液压AGC;原理;应用第一章液压AGC概念与原理1.1 液压AGC的概念厚度自动控制是通过测厚仪或传感器(如辊缝仪和压头等)对带钢实际轧出厚度进行连续地测量(或估算),并根据实测值与给定值相比较后的偏差信号,借助于控制回路和装置或计算机的功能程序,改变压下位置、轧制压力、张力、轧制速度等,把厚度控制在允许偏差范围之内的方法。
特制品的厚度自动控制在一定尺寸范围内的系统称为厚度自动控制系统,简称为AGC。
液压AGC就是借助于轧机的液压系统,通过液压伺服阀调节液压缸的油量和压力来控制轧辊的位置,对带钢进行厚度自动控制的系统。
1.2板带轧钢产生厚差的原因带钢厚度精度可分为一批同规格带钢的厚度异板差和每一条带钢的厚度同板差。
为此可将厚度精度分解为带钢头部厚度命中率和带钢全长厚度偏差。
从厚差分布特征来看,产生厚差的原因有以下几种: (1)头尾温差,这主要是由于粗轧末出口速度一般比精轧机入口速度要高,因而造成了带钢头部和尾部在空气中停留时间的不同。
( 2)加热炉内导轨在钢胚表面造成的低温段称为水印,由于此段温度变化率大,厚度变动比较“陡”。
(3)活套起套过猛,对带钢产生冲击,使颈部厚度变薄。
( 4 )咬钢时,由于速度设定不协调加上动态速降造成钢套过大,起套并投入高速控制后由于纠偏过快造成带钢拉钢,这一松一紧使厚度减薄,宽度拉窄。
(5)温度波动造成轧制力以及厚度波动。
(6)油膜轴承的油膜厚度发生变化使实际辊缝变化,从而影响轧件厚度。
(7)轧辊偏心将直接使实际辊缝产生高频周期变化。
为了克服或减轻这些干扰因素对成品厚度的影响,除了改进AGC 系统的结构外,还可以将它与各种先进的智能算法相结合,以提高其精度。
1.3液压AGC基本原理1.3.1液压AGC 的设备及其与工作液压AGC技术是将机械、液压、自动控制以及轧制工艺等专业紧密联系在一起的综合先进技术。
AGC液压系统的功能描述

AGC液压系统的功能描述BISRA AGC仅对主要扰动—轧制力的变化及影响进行补偿,并提出了头部锁定(相对值)AGC技术。
为使板厚精度达到高标准(例如,冷轧薄板的同板差≤±0.003mm,热轧薄板的同板差≤±0.02mm)必须对其他扰动也进行补偿,完善的液压AGC系统如有右图所示,它包括:1液压APC(Automatic Position Control)即液压位置自动控制系统,它是液压AGC的内环系统,是一个高精度、高响应的电液位置闭环伺服系统,它决定着液压AGC系统的基本性能。
它的任务是接受厚控AGC系统的指令,进行压下缸的位置闭环控制,使压下缸实时准确地定位在指令所要求的位置。
也就是说,液压APC是液压AGC的执行系统2轧机弹跳补偿MSC(Mill Stretch Compensation),其任务是检测轧制力,补偿轧机弹跳造成的厚度偏差。
MSC是HAGC系统的主要补偿环3热凸度补偿TEC(Thermal Crown Compensation):轧辊受热膨胀时,实际辊缝减小,轧制力增加,轧件出口厚度减小;此时如用弹跳方程式计算轧件出口厚度,由于轧制力增大,计算出的厚度反而变大了。
如果不对此进行处理,AGC就会减小辊缝,使实现出口轧件厚度更薄,即轧辊热膨胀的影响反而被轧机弹跳补偿放大了。
TEC的作用便是消除这种不良影响。
此外,TEC中还要考虑轧辊磨损的影响4油膜轴承厚度补偿BEC(Beering Oil Compensation):大型轧机支承辊轴承一般采用能适应高速重载的油膜轴承。
油膜厚度取决于轧制力和支承辊速度:轧制力增加,辊缝增加;速度增加、辊缝减小。
通过检测轧制力和支撑辊速度可进行BEC补偿5支承辊偏心补偿ECC(Eccentricity Compensation):支承辊偏心将使辊缝和轧制压力发生周期性变化,偏心使辊缝减小的同时,将使轧制压力增大,如果将偏心量引起的轧制压力进行力补偿,必将使辊缝进一步减小,因为力补偿会使压下缸活塞朝着使辊缝减小的方向调节。
北京科技大学科技成果——轧机液压AGC控制系统

北京科技大学科技成果——轧机液压AGC控制系统项目简介液压AGC具有响应速度快、控制精度高的优点,正在取代电动AGC成为当今新建轧机和欲改造轧机的首选技术。
北京科技大学高效轧制国家工程研究中心长期致力于液压AGC在大型工业轧机应用的研究,并在多条带钢连轧机组中取得成功应用,为轧钢技术国产化作出较大贡献。
AGC控制系统由L2过程控制系统和L1基础自动化控制体统组成。
L2级系统主要通过模型自学习完成对液压控制系统参数的缓慢变化造成的厚度偏差进行补偿;L1级系统则完成对实时参数变化造成的厚度偏差进行补偿,同时完成液压APC和液压AFC控制功能。
L2级完成的主要功能包括:轧制负荷分配及优化、辊缝位置基准计算和设定、轧制力预报、温度预报、模型自学习等。
涉及的计算模型包括:轧制力模型、变形抗力模型、残余应变模型、轧制弹跳模型(辊系弹性变形分析、轧机牌坊弹性变形)、板坯温度模型(辐射和对流、高压水、与轧辊接触产生的热传导、塑性功转变为热量引起的温升、摩擦热)、轧辊磨损模型、轧辊热膨胀模型、力矩模型、宽展模型、前滑模型、轧件尺寸计算模型、板形和板凸度模型、板厚控制与板形控制之间的关系、平面形状预测和控制模型等。
由L1级完成的液压AGC主要控制功能包括:液压缸位置控制(HAPC)、电动压下螺丝控制(EAPC)、自动厚度控制(HAGC,根据不同应用场合可以选择:压力AGC、硬度前馈AGC、测厚仪监控AGC、穿带自适应、快速监控AGC、流量AGC和张力AGC等的一种或几种)、补偿AGC(包括轧件宽度补偿、油膜轴承油膜厚度补偿、轧辊热膨胀与磨损补偿、尾部失张补偿、偏心滤波及补偿、伺服阀偏移补偿、穿带冲击补偿、卷取冲击补偿等)、轧辊平行控制(ALC)、自动纠偏、、轧机调零、轧机刚度测量、手动倾斜、事故锁定和卸荷等。
AGC工作方式包括相对AGC控制和绝对AGC控制两种。
该液压AGC系统和板形控制系统一起被评为“九五”国家重点科技攻关计划(重大技术装配)优秀科技成果,并已成功应用于多条轧线,取得了极高的控制精度。
液压AGC自动厚度控制系统介绍

一、液压AGC自动厚度控制系统简介液压AGC自动厚度控制系统是现代化轧机提高轧制精度必不可少的技术装备,是生产厂家在未来激烈市场竞争中取得优势的重要保证。
公司致力于液压AGC成套技术与装备的研发、推广。
公司建立了多学科相配套的AGC专业体系,可以集液压AGC自动厚度控制系统的设计、开发、制造、安装、调试于一体,为用户提供优质服务。
目前为止,本公司所推出的液压AGC自动厚度控制系统已经应用在国内外上百条冷轧、热轧带钢生产线上,完全可以满足带钢产品厚度的精确控制。
为了保证带钢产品的厚度精度和良好板型,本系统具有液压压下辊缝控制(AGC)、恒轧制压力控制(AFC)、测厚仪监控,对薄规格产品还可采用张力厚度控制等功能。
本系统工作可靠、操作方便、自我保护功能完备,并具有轧制工艺数据库,在轧制不同规格的带材时,只需要调出相应的轧制工艺即可在每次开始轧制以前设置轧制状态。
应用该系统后,冷轧带钢的厚控精度可以达到:0.15±0.003mm、0.3±0.006mm(纵向厚度偏差)二、系统主要控制功能1、辊缝位置闭环控制(APC);2、带钢厚度闭环控制(监控AGC、张力AGC、秒流量AGC、予控AGC);3、辊缝压靠压力设定及辊缝拨零操作;4、轧辊两侧压/抬同步控制;5、辊缝差设定与钢带纠偏控制;6、轧制力设定与报警;7、各项轧制工艺参数的采集、记录、显示和打印为轧制规程的优化提供参数。
三、主要技术性能指标1、辊缝(厚度)设定精度优于0.001mm2、带材厚度控制精度:±1.5~3%h(带钢厚度)本指标与测厚仪以及来料和轧机精度水平有关。
3、系统响应时间: 30-50 ms四、主要设备介绍1、液压泵站液压泵站主要由主液压泵、蓄能器、油箱,司服阀组,减压稳压阀组、循环过滤机构等组成。
2、压下油缸压下油缸采用优质锻造合金钢制作,经过三次无损探伤,以保证缸体的质量;结构采用特殊设计,油封采用进口产品;装有高分辨率的位移传感器以检测油缸的位移。
液压agc的原理

液压agc的原理液压AGC(Hydraulic Automatic Gauge Control)是一种广泛应用于轧钢生产过程中的自动测厚和控制系统。
它通过调整轧机辊缝来实时控制钢材的厚度,以确保产品达到预期的厚度要求。
液压AGC系统的工作原理可以简单地分为测量和调节两个过程。
1. 测量过程:液压AGC系统首先使用高精度的测厚仪器对钢材进行测量,实时获取当前的厚度数据。
这些数据可以通过厚度传感器或激光测距仪等设备获得。
测厚仪器通常会安装在轧机出口或入口的适当位置,能够准确快速地测量通过的钢材厚度。
2. 调节过程:在测量到当前厚度数据后,液压AGC系统会将这些数据与预定的目标厚度进行比较。
如果当前厚度与目标厚度相差较大,则需要对轧机辊缝进行调节,使厚度逐渐趋近于目标厚度。
调节过程通过液压系统来实现,包括液压缸和油源系统。
具体而言,液压AGC系统将通过控制非工作侧辊缝和工作侧辊缝的间隙来调节钢材的厚度。
当当前厚度小于目标厚度时,系统会通过增大非工作侧辊缝的间隙,使得钢材矫直或压扁。
这将在下一工作循环中导致钢材变薄。
相反,当当前厚度大于目标厚度时,系统会通过增大工作侧辊缝的间隙,使钢材伸长或胀厚,即下一工作循环中导致钢材变厚。
液压AGC系统通过调节液压缸来实现轧机辊缝的调整,使其达到预期的值。
液压缸通常由一个或多个活塞、液压油口和控制阀组成。
液压油通过液压油口进入油缸,推动活塞运动。
控制阀用来控制液压系统的入口和出口,以调整液压缸的位移和速度。
液压AGC系统还会根据测得的厚度数据进行统计和分析。
通过对历史数据的分析,系统可以根据产生的变化模式对轧机辊缝进行智能地调整,在长时间内保持稳定的厚度控制,并避免由于材料、温度和速度等因素引起的厚度波动。
总之,液压AGC系统通过测量钢材厚度,并使用液压系统调整轧机辊缝来控制钢材的厚度。
它提供了高精度和实时的厚度控制,确保生产出符合要求的钢材。
在钢铁工业中,液压AGC系统已经得到了广泛的应用,为钢材生产过程带来了巨大的效益和质量改进。
液压AGC系统
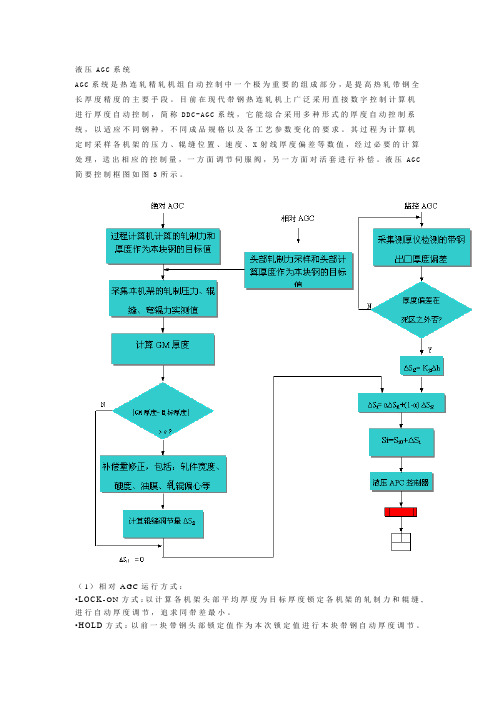
液压A G C系统A G C系统是热连轧精轧机组自动控制中一个极为重要的组成部分,是提高热轧带钢全长厚度精度的主要手段。
目前在现代带钢热连轧机上广泛采用直接数字控制计算机进行厚度自动控制,简称D D C-A G C系统,它能综合采用多种形式的厚度自动控制系统,以适应不同钢种,不同成品规格以及各工艺参数变化的要求。
其过程为计算机定时采样各机架的压力、辊缝位置、速度、X射线厚度偏差等数值,经过必要的计算处理,送出相应的控制量,一方面调节伺服阀,另一方面对活套进行补偿。
液压A G C 简要控制框图如图3所示。
(1)相对A GC运行方式:•L O C K-O N方式:以计算各机架头部平均厚度为目标厚度锁定各机架的轧制力和辊缝,进行自动厚度调节,追求同带差最小。
•H O L D方式:以前一块带钢头部锁定值作为本次锁定值进行本块带钢自动厚度调节。
当实测带钢出口厚度与给定的目标厚度之差超过某极限值时,将以各机架实测值作为本块钢的给定目标厚度。
(2)绝对A GC运行方式:以过程计算机计算的目标厚度和预报轧制力作为目标厚度和锁定各机架轧制力进行自动厚度调节,追求与要求的成品厚度差最小。
当实测带钢出口厚度与给定的目标厚度之差超过某极限值时,将以实测值作为本块钢的给定目标厚度。
(3)控制方式:A GC系统中基本的控制功能是根据基本弹跳方程实现的:上式中,——弯辊力造成的厚度变化——油膜轴承的油膜厚度变化——辊缝零位(热膨胀及磨损)——轧机的刚性系数,牛顿/毫米——轧辊辊缝值,毫米但为了进一步提高厚调精度,需采取各种补偿措施,主要是弯辊力造成的厚度变化补偿,油膜厚度补偿以及辊缝零位补偿。
同时利用测厚仪直接测得的成品带钢厚度值为基准对A GC系统进行监视,另外为了克服以弹跳方程为基础的反馈式A GC系统的滞后现象,在A GC系统中增加前馈控制功能。
4结束语本控制系统根据图4所规定的精度要求编写控制程序,对每块带材的厚度精度进行命中率统计(见表1),也就是该带材的厚控精度是否在图4所规定的范围内。
AGC

新型轧机系统是机、电、液、气、仪一体化的大型复杂系统,其结构与功能的复杂性决定了故障机理的复杂性以及故障诊断的困难度。轧机系统高精度与高可靠性要求使故障诊断任务更加艰巨。
这一章根据作者在轧机液压系统设计分析、故障诊断与维修领域的长期实践与积累,对现代新型轧机液压故障的症状、原因,以及故障分析的过程和方法等进行总结与提炼。主要是概括轧机控制系统(AGC系统、CVC系统、弯辊系统、活套系统)的常见故障,整理故障分析的基本思路与程序、列出故障树,并总结出故障症状与原因的关系。同时,也对轧机液压控制故障与产品质量的关系进行分析。上述内容是轧机智能诊断与监测系统的主要专家知识。
4、油缸卡死,驱动电流不为零
5、电气断线,驱动电流为零
3.2 CVC液压故障与分析
3.2.1 CVC液压故障概述
CVC主要故障有:
1) 位置传感器故障。BA给定位置设定信号,CVC油缸位移不到位,主要有:单个位置传感器测量值>极限位,或控制过程中位置传感器输出信号不变,即可能位置传感器故障;同一个辊两个位置传感器位置差|E-A|>5mm,报警;上、下两辊||UP|-|DOWN||>2mm,封锁。可能故障:液压伺服系统零点漂移、油缸卡滞等。分析位移偏差量的变化趋势。
伺服阀寿命性故障 伺服阀零偏电流趋势增大,对零偏电流I趋势分析
伺服阀突发性故障 油缸位置无法控制或偏向某一端,零偏电流突然增大
溢流阀调压力过高 当伺服系统发生故障时,可能引起油缸压力过高
溢流阀调压力过低 当伺服系统发生故障时,可能引起油缸压力过低
溢流阀损坏 压力建立不起,或起不到溢流作用
机械与电气零点不一致 伺服系统驱动零偏电流增大
6) 调节器封锁:系统应符合CVC功能投入条件,如:硬件好,传感器没有故障;开关自动状态;BA硬件好(油库准备好)等。否则调节器封锁。
关于轧机液压AGC系统内模控制的分析探索
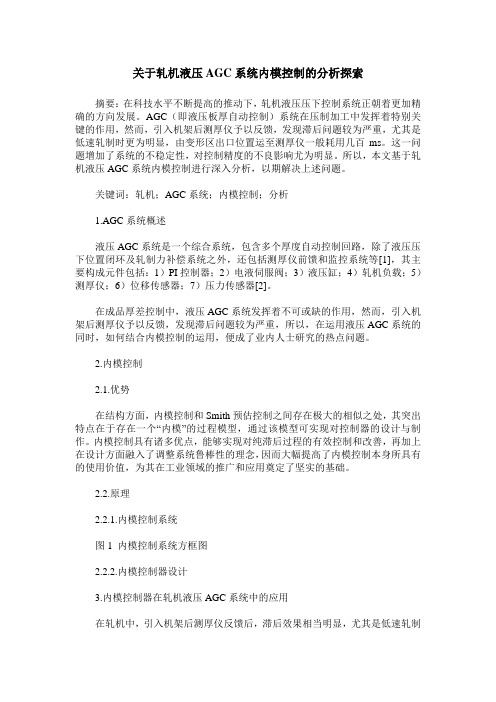
关于轧机液压AGC系统内模控制的分析探索摘要:在科技水平不断提高的推动下,轧机液压压下控制系统正朝着更加精确的方向发展。
AGC(即液压板厚自动控制)系统在压制加工中发挥着特别关键的作用,然而,引入机架后测厚仪予以反馈,发现滞后问题较为严重,尤其是低速轧制时更为明显,由变形区出口位置运至测厚仪一般耗用几百ms。
这一问题增加了系统的不稳定性,对控制精度的不良影响尤为明显。
所以,本文基于轧机液压AGC系统内模控制进行深入分析,以期解决上述问题。
关键词:轧机;AGC系统;内模控制;分析1.AGC系统概述液压AGC系统是一个综合系统,包含多个厚度自动控制回路,除了液压压下位置闭环及轧制力补偿系统之外,还包括测厚仪前馈和监控系统等[1],其主要构成元件包括:1)PI控制器;2)电液伺服阀;3)液压缸;4)轧机负载;5)测厚仪;6)位移传感器;7)压力传感器[2]。
在成品厚差控制中,液压AGC系统发挥着不可或缺的作用,然而,引入机架后测厚仪予以反馈,发现滞后问题较为严重,所以,在运用液压AGC系统的同时,如何结合内模控制的运用,便成了业内人士研究的热点问题。
2.内模控制2.1.优势在结构方面,内模控制和Smith预估控制之间存在极大的相似之处,其突出特点在于存在一个“内模”的过程模型,通过该模型可实现对控制器的设计与制作。
内模控制具有诸多优点,能够实现对纯滞后过程的有效控制和改善,再加上在设计方面融入了调整系统鲁棒性的理念,因而大幅提高了内模控制本身所具有的使用价值,为其在工业领域的推广和应用奠定了坚实的基础。
2.2.原理2.2.1.内模控制系统图1 内模控制系统方框图2.2.2.内模控制器设计3.内模控制器在轧机液压AGC系统中的应用在轧机中,引入机架后测厚仪反馈后,滞后效果相当明显,尤其是低速轧制时更为明显,由变形区出口位置运至测厚仪一般耗用几百ms。
这一问题增加了系统的不稳定性,对控制精度的不良影响尤为明显。
1450热轧板厂AGC液压系统浅析

1450热轧板厂AGC液压系统浅析陈好庆1450热轧板厂AGC液压系统浅析陈好庆摘要:本文介绍了热轧板厂精轧区AGC(厚度自动控制)液压系统的基本工作原理以及结构性能,对实际生产应用情况中存在的问题进行分析浅析,针对问题提出了处理措施和方法,较好的解决了液压压下系统的工作稳定性,满足生产要求,为相似设备运行管理提供经验以及系统日常维护的要点。
对于设备使用和维护管理具有重要的实际意义。
[关键词]:AGC 液压压下系统HAGC系统改造一引言攀钢1450热轧板厂AGC液压压下系统主要服务于精轧F1-F6轧机液压压下控制,AGC英文是Automatic Gain Control(自动厚度控制)的缩写,该系统是厦门海德科液压机械设备有限公司的一套先进自动化设备,安装于精轧机的F1-F6轧机之上)其主要作用是:在轧钢过程中,对轧辊进行精确定位,控制板材的轧制厚度,提高板形质量。
AGC液压系统的主要功能是为精轧F1-F6轧机动作提供动力源。
二 AGC系统工作原理及主要设备介绍1,AGC系统的工作原理AGC液压系统主要由动力元件、控制元件、执行元件、辅助元件、工作介质五部分组成。
动力元件的功用是将原动机输出的机械能转化为液体的压力能,其主要设备为三台(两用一备)通轴斜盘式恒压变量柱塞泵;控制元件的功用是控制和调节系统中油液的压力大小、流量大小和液流方向,其主要为伺服液压缸;辅助元件的功用是输油、集油、辅助改善系统性能, 其主要元件有油箱、滤油器、蓄能器等设备;工作介质的功用是传递动力和信号,同时还起到润滑、冷却、防锈的作用,其主要由液压油液组成。
AGC液压系统工作原理:系统正常工作时,主泵(两台工作,一台备用)打出的压力油,通过泵出口控制阀架分为两路:一路为主油路,一路为蓄能器储存及泄压油路。
轧机正常工作时,主油路的压力油经过伺服阀控制伺服液压缸工作,以达到轧机轧辊定位和控制板坯轧制厚度的目的。
AGC系统液压站由油箱装置、主泵供油系统、蓄能器装置、循环过滤冷却系统和回油过滤装置组成。
液压AGC在宁波建龙热连轧上的应用

液压AGC在宁波建龙热连轧上的应用宁波建龙热连轧厂作为中国最大的不锈钢生产基地之一,为了提高产品质量和生产效率,不断引进先进的技术和设备,其中液压AGC(自动轧制控制系统)在该厂的应用发挥了重要作用。
液压AGC是一种采用液压控制技术的自动轧制控制系统,主要用于热轧生产线中的轧机控制。
它通过实时监测轧机的工作状态,自动调整轧制参数,以实现产品尺寸、形状和表面质量的精确控制。
在宁波建龙热连轧厂的实际应用中,液压AGC发挥了以下几个方面的重要作用:首先,液压AGC能够实现轧机的自动控制。
传统的轧机控制需要人工干预和调整,容易受到人为因素和环境变化的影响,而液压AGC能够自动根据预设的轧制参数进行调整,减少人为误差,提高轧机的控制精度。
其次,液压AGC能够实现快速换轧。
热连轧生产线需要频繁地进行轧辊更换,传统的手动调整方式耗时且易出错。
而液压AGC能够通过自动调整轧机的参数,实现快速换轧,大大提高了生产效率。
再次,液压AGC能够实现轧机负载的精确控制。
在轧制过程中,轧机的负载会随着材料的变化而变化,传统的控制方式往往无法精确控制负载。
而液压AGC通过实时监测轧机的负载情况,自动调整轧制参数,使轧机负载保持在一个合理的范围内,避免了负载过大或过小对轧机和产品质量的影响。
最后,液压AGC能够实现轧机的自适应控制。
在轧制过程中,轧机工作状态和材料特性会发生变化,传统的控制方式往往无法适应这些变化。
而液压AGC能够根据实时监测到的工作状态和材料特性,自动调整轧制参数,实现自适应控制,提高了轧机的适应性和稳定性。
总之,液压AGC在宁波建龙热连轧厂的应用为提高产品质量和生产效率做出了重要贡献。
随着科技的不断发展,液压AGC 将会进一步完善和应用于更多的生产领域,为中国制造业的发展做出更大的贡献。
板带轧机AGC控制技术
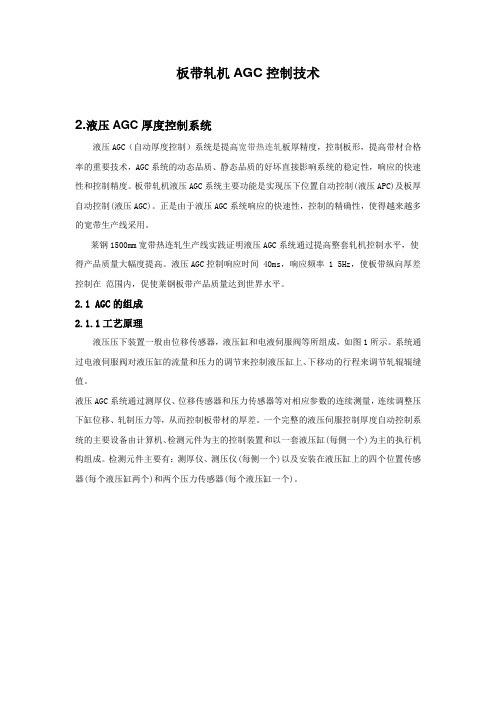
板带轧机AGC控制技术2.液压AGC厚度控制系统液压AGC(自动厚度控制)系统是提高宽带热连轧板厚精度,控制板形,提高带材合格率的重要技术,AGC系统的动态品质、静态品质的好坏直接影响系统的稳定性,响应的快速性和控制精度。
板带轧机液压AGC系统主要功能是实现压下位置自动控制(液压APC)及板厚自动控制(液压AGC)。
正是由于液压AGC系统响应的快速性,控制的精确性,使得越来越多的宽带生产线采用。
莱钢1500mm宽带热连轧生产线实践证明液压AGC系统通过提高整套轧机控制水平,使得产品质量大幅度提高。
液压AGC控制响应时间40ms,响应频率1 5Hz,使板带纵向厚差控制在范围内,促使莱钢板带产品质量达到世界水平。
2.1 AGC的组成2.1.1工艺原理液压压下装置一般由位移传感器,液压缸和电液伺服阀等所组成,如图1所示。
系统通过电液伺服阀对液压缸的流量和压力的调节来控制液压缸上、下移动的行程来调节轧辊辊缝值。
液压AGC系统通过测厚仪、位移传感器和压力传感器等对相应参数的连续测量,连续调整压下缸位移、轧制压力等,从而控制板带材的厚差。
一个完整的液压伺服控制厚度自动控制系统的主要设备由计算机、检测元件为主的控制装置和以一套液压缸(每侧一个)为主的执行机构组成。
检测元件主要有:测厚仪、测压仪(每侧一个)以及安装在液压缸上的四个位置传感器(每个液压缸两个)和两个压力传感器(每个液压缸一个)。
2.1.2液压AGC阀台图2 液压AGC阀台示意液压AGC阀台原理示意如图2所示。
(1)阀站下方P口连通液压站的系统供油油路,用于为液压AGC系统提供液压动力,T口连通液压站油箱,用于回油。
(2)阀站右方的P口,T口,X口用于检修或排查故障时检测阀站内系统供油压力P 以及伺服阀控制油路X是否正常。
(3)阀站上方A口连通液压AGC液压缸无杆腔,B口连通液压AGC液压缸的有杆腔。
(4)过滤器对阀站内的P油路和X油路中的杂质进行过滤,如果过滤器DPS1堵塞,将发出故障信号,应及时更换。
浅析热轧厂精轧液压AGC控制系统

2 液压AGC系统的组成及控制原理
2 . 1 系 统 组成
好的轧件板形 ,要在最后 的精轧机上采用恒 轧制力控制 。 而其他精 轧机 的AP C 系统 则可 由操 作人员选择恒 辊缝控制 或恒轧制力控制。液压 A P C 的控制原理图如图1 所示 :
p啦 譬僚锺 I 嚣 O S t 赶 鬣传爆 潞
表1 T DC的 硬 件 配 置 及 其 用途 说 明
1 概述
精轧机控 制作为轧线 上的 主要 控制 内容 ,它包括 了板
型 、厚度 、活套 和 主速 度 四个 方面 的控 制 。厚 度 控制 又
是其重点 控制 内容 ,厚度控制好 坏将直接关 系到产 品质量 的好坏 ,它主要包括 了监 控 、偏 心补偿 、反 馈和前馈 的 自
关键 词 :精 轧机 ;液Y  ̄ . A GC;厚 度控 制 ;热轧 厂 中图分类号 :T G3 3 3 文 献标识码 :A 文章 编号 :1 0 0 9 - 2 3 7 4( 2 0 1 3 )1 4 — 0 0 3 7 — 0 3 数 据交换快 速响应 、数 量庞大 的要 求 ,在各精 轧机 的T DC 之间使用了光纤 网 ( 1 0 0 M) 进行 连接 。T D C 的硬件配置及 其用途 如表1 所示 :
于9 9 %。
式中 :
通过调整板 厚偏差 以获得 标准板厚是AG C 控制的最终 目的 。液压 A P C 是液压 A G C 系统 的执 行机构 ,它主要用于 辊缝调节量 的确定 。然后 在轧钢过程 中 ,利用液压AG C 对
因为A G C 系统 在液 压压 下具 有 调节 精 度高 、抗 干扰性 能
好 、截 止频率高 、反应快 、惯 性小 的优 点 ,它是提 高带钢
AGC液压系统的功能描述
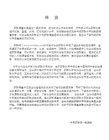
BISRA AGC仅对主要扰动—轧制力的变化及影响进行补偿,并提出了头部锁定(相对值)AGC技术。为使板厚精度达到高标准(例如,冷轧薄板的同板差≤±0.003mm,热轧薄板的同板差≤±0.02mm)必须对其他扰动也进行补偿,完善的液压AGC系统如有右图所示,它包括:
1液压APC(Automatic Position Control)即液压位置自动控制系统,它是液压AGC的内环系统,是一个高精度、高响应的电液位置闭环伺服系统,它决定着液压AGC系统的基本性能。它的任务是接受厚控AGC系统的指令,进行压下缸的位置闭环控制,使压下缸实时准确地定位在指令所要求的位置。也就是说,液压APC是液压AGC的执行系统
4油膜轴承厚度补偿BEC(Beering Oil Compensation):大型轧机支承辊轴承一般采用能适应高速重载的油膜轴承。油膜厚度取决于轧制力和支承辊速度:轧制力增加,辊缝增加;速度增加、辊缝减小。通过检测轧制力和支撑辊速度可进行BEC补偿
5支承辊偏心补偿ECC(Eccentricity Compensation):支承辊偏心将使辊缝和轧制压力发生周期性变化,偏心使辊缝减小的同时,将使轧制压力增大,如果将偏心量引起的轧制压力进行力补偿,必将使辊缝进一步减小,因为力补偿会使压下缸活塞朝着使辊缝减小的方向调节。为解决这一问题,拟在力补偿系数C环节之前加一死区环节,死区值等于或略大于最大偏心量,为了让小于死区值的其它缓变信号能够通过,死区环节旁并联一个时间常数较大的滤波器,滤波器不允许快速周期变化的偏心信号通过
以上补偿措施并非每台轧机都全部采用,需要根据轧机的类型、精度要求和工程经验采用其中的一些主要补偿措施
11恒压力AGC
上述AGC系统,难以补偿支承辊偏心造成的微小厚差。通常,轧制最后一个道次时,采用恒压轧制来减缓偏心造成的厚差。所谓恒压轧制,是断开位置闭环,将力补偿变成力闭环,实现恒压力闭环控制。平整机中一般都采用恒压力AGC
液压AGC原理及其液压缸.docx
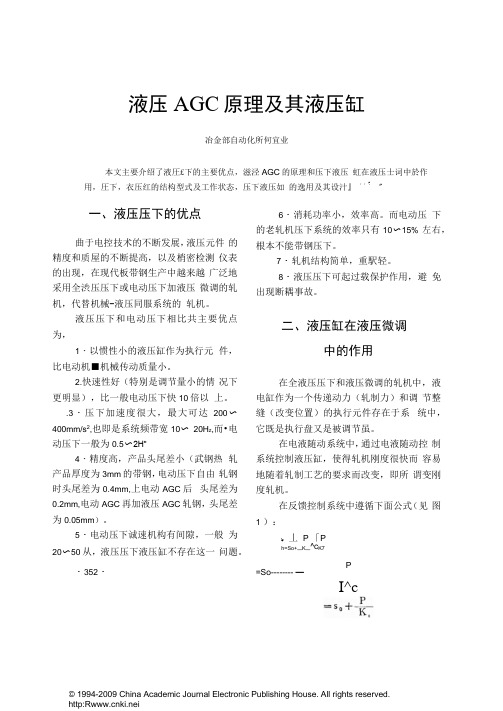
© 1994-2009 China Academic Journal Electronic Publishing House. All rights reserved. http:ki.nei液压AGC 原理及其液压缸冶金部自动化所何宜业本文主要介绍了液圧£下的主要优点,滋泾AGC 的原理和压下液压 虹在液压士词中於作用,圧下,衣压红的结构型式及工作状态,压下液压如 的逸用及其设汁』 ::7 "一、液压压下的优点曲于电控技术的不断发展,液压元件 的精度和质屋的不断提高,以及梢密检测 仪表的出现,在现代板带钢生产中越来越 广泛地采用全渋压压下或电动压下加液压 微调的轧机,代替机械-液压同服系统的 轧机。
液压压下和电动压下相比共主要优点 为,1・以惯性小的液压缸作为执行元 件,比电动机■机械传动质量小。
2.快速性好(特别是调节量小的情 况下更明显),比一般电动压下快10倍以 上。
.3・压下加速度很大,最大可达200〜 400mm/s 2,也即是系统频带宽10〜 20H z ,而•电动压下一般为0.5〜2H“4・精度高,产品头尾差小(武钢热 轧产品厚度为3mm 的带钢,电动压下自由 轧钢时头尾差为0.4mm,上电动AGC 后 头尾差为0.2mm,电动AGC 再加液压AGC 轧钢,头尾差为0.05mm )。
5・电动压下诚速机构有间隙,一般 为20〜50从,液压压下液压缸不存在这一 问题。
・352・6・消耗功率小,效率高。
而电动压 下的老轧机压下系统的效率只有10〜15% 左右,根本不能带钢压下。
7・轧机结构简单,重駅轻。
8・液压压下可起过载保护作用,避 免出现断耦事故。
二、液压缸在液压微调中的作用在全液压压下和液压微调的轧机中, 液电缸作为一个传递动力(轧制力)和调 节整缝(改变位置)的执行元件存在于系 统中,它既是执行盘又是被调节虽。
在电液随动系统中,通过电液随动控 制系统控制液压缸,使得轧机刚度很快而 容易地随着轧制工艺的要求而改变,即所 谓变刚度轧机。
AGC操作规范
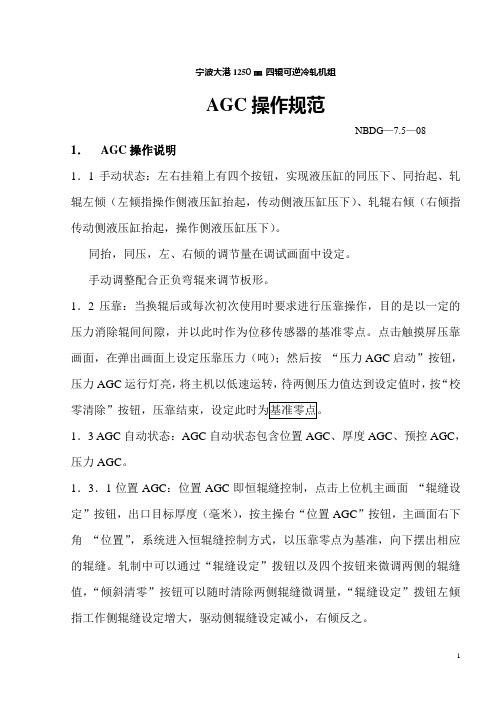
宁波大港1250㎜四辊可逆冷轧机组AGC操作规范NBDG—7.5—08 1.AGC操作说明1.1手动状态:左右挂箱上有四个按钮,实现液压缸的同压下、同抬起、轧辊左倾(左倾指操作侧液压缸抬起,传动侧液压缸压下)、轧辊右倾(右倾指传动侧液压缸抬起,操作侧液压缸压下)。
同抬,同压,左、右倾的调节量在调试画面中设定。
手动调整配合正负弯辊来调节板形。
1.2压靠:当换辊后或每次初次使用时要求进行压靠操作,目的是以一定的压力消除辊间间隙,并以此时作为位移传感器的基准零点。
点击触摸屏压靠画面,在弹出画面上设定压靠压力(吨);然后按“压力AGC启动”按钮,压力AGC运行灯亮,将主机以低速运转,待两侧压力值达到设定值时,按“校1.3 AGC自动状态:AGC自动状态包含位置AGC、厚度AGC、预控AGC,压力AGC。
1.3.1位置AGC:位置AGC即恒辊缝控制,点击上位机主画面“辊缝设定”按钮,出口目标厚度(毫米),按主操台“位置AGC”按钮,主画面右下角“位置”,系统进入恒辊缝控制方式,以压靠零点为基准,向下摆出相应的辊缝。
轧制中可以通过“辊缝设定”拨钮以及四个按钮来微调两侧的辊缝值,“倾斜清零”按钮可以随时清除两侧辊缝微调量,“辊缝设定”拨钮左倾指工作侧辊缝设定增大,驱动侧辊缝设定减小,右倾反之。
1.3.2厚度AGC:厚度AGC是自动厚度控制,以出口测厚仪的厚度为反馈值,设定出口厚度为目标厚度值,出现偏差时去修正辊缝设定值,最终使出口板厚达到设定厚度。
厚度AGC在位置AGC投入后才会有效,在位置AGC 退出后自动退出。
按“厚度AGC”按钮,绿灯亮,主机速度高于0.5 m/s后厚度AGC自动投入,低于0.3m/s则自动切除到位置AGC。
若“厚度AGC”按钮绿灯不亮,厚度AGC不随主机速度自动投入。
厚度AGC要在手动压到位时(±0.01mm出口设定厚度)投入效果更好,若没压到位就投,容易引起超调,影响精度。
AGC介绍
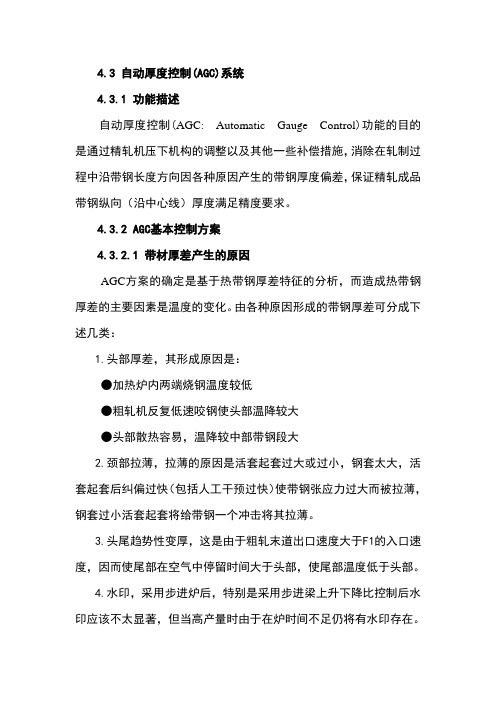
4.3 自动厚度控制(AGC)系统4.3.1 功能描述自动厚度控制(AGC: Automatic Gauge Control)功能的目的是通过精轧机压下机构的调整以及其他一些补偿措施,消除在轧制过程中沿带钢长度方向因各种原因产生的带钢厚度偏差,保证精轧成品带钢纵向(沿中心线)厚度满足精度要求。
4.3.2 AGC基本控制方案4.3.2.1 带材厚差产生的原因AGC方案的确定是基于热带钢厚差特征的分析,而造成热带钢厚差的主要因素是温度的变化。
由各种原因形成的带钢厚差可分成下述几类:1.头部厚差,其形成原因是:●加热炉内两端烧钢温度较低●粗轧机反复低速咬钢使头部温降较大●头部散热容易,温降较中部带钢段大2.颈部拉薄,拉薄的原因是活套起套过大或过小,钢套太大,活套起套后纠偏过快(包括人工干预过快)使带钢张应力过大而被拉薄,钢套过小活套起套将给带钢一个冲击将其拉薄。
3.头尾趋势性变厚,这是由于粗轧末道出口速度大于F1的入口速度,因而使尾部在空气中停留时间大于头部,使尾部温度低于头部。
4.水印,采用步进炉后,特别是采用步进梁上升下降比控制后水印应该不太显著,但当高产量时由于在炉时间不足仍将有水印存在。
5.随机温度波动造成的厚度波动。
6.轧辊偏心造成的厚度周期变动。
7.尾部厚差,一方面由和头部相同的原因造成,即温度较低,另一方面也由于带尾离开i F 机架时在i F 及1+i F 机架间带钢失张而使1+i F 机架轧制力升高所造成。
8.除此之外,设定模型精度不够也将造成头部厚度偏离设定值。
针对产生厚差的原因不同,应采取不同的厚度控制方式和补偿措施。
长期来AGC 系统主要承担消除(3)(4)(5)项,而对(6)一般采取回避,对(1)(7)不进行考核,而(2)只能靠改进活套控制来减少,而(8)则需要靠提高模型精度来解决。
近年来为了进一步提高进入厚度精度的带钢长度百分比,对(1),(2)及(7)采取了专门的措施,对(8)除了提高模型精度外,增加了穿带自适应功能。
AGC系统
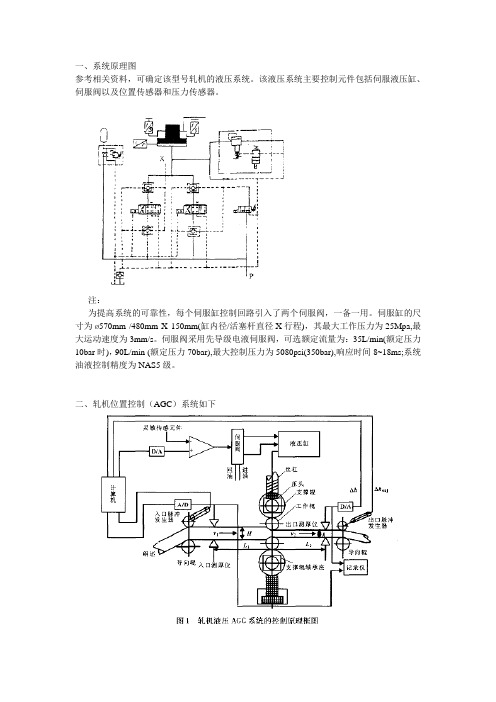
一、系统原理图参考相关资料,可确定该型号轧机的液压系统。
该液压系统主要控制元件包括伺服液压缸、伺服阀以及位置传感器和压力传感器。
注:为提高系统的可靠性,每个伺服缸控制回路引入了两个伺服阀,一备一用。
伺服缸的尺寸为ø570mm /480mm X 150mm(缸内径/活塞杆直径X行程),其最大工作压力为25Mpa,最大运动速度为3mm/s。
伺服阀采用先导级电液伺服阀,可选额定流量为:35L/min(额定压力10bar时),90L/min (额定压力70bar),最大控制压力为5080psi(350bar),响应时间8~18ms;系统油液控制精度为NAS5级。
二、轧机位置控制(AGC)系统如下该轧机液压压力系统主要由TCS系统、液压控制器、伺服阀控制器、伺服阀、液压油缸、位移传感器等6部分组成。
以下是液压压力伺服系统的控制图:液压AGC位置控制方式控制框图三、AGC系统的控制原理与计算方法1.模型调节原理AGC的调节过程,实际上是解决外界扰动(坯料厚度和硬度差等)、调节量(辊缝)和目标量(厚度)等之间的相互影响关系的过程。
外界扰动影响压制力,调节辊缝也引起轧制力的变化。
因此,当轧件头部锁定之后,第一次测得的轧制力差⊿p肯定是由外界扰动引起的,就可用⊿p1=⊿pd计算出当时的辊缝调节量⊿s;第二次,第三次…,第n次的压力测量值,不仅包含了外界扰动因素的影响(⊿pd),而且包含辊缝调节引起的轧制力变化量(⊿p1)。
它们之间的关系如图所示。
2. 工作原理:利用液压缸实现轧辊辊缝调整,轧机压下厚度自动控制,液压AGC的控制原理如下图所示1——位置控制放大器,2——功率放大器,3——油源,4——伺服阀,5——压力传感器,6——位置传感器,7——伺服压下缸,8——测厚仪,9——负载传感器(压头);10——比例放大器,11——压力脉冲器,12——积分器给定初值辊缝值调整信号经1→2→3→4→相应流量输出→伺服缸下缸7移动→轧辊移动。
- 1、下载文档前请自行甄别文档内容的完整性,平台不提供额外的编辑、内容补充、找答案等附加服务。
- 2、"仅部分预览"的文档,不可在线预览部分如存在完整性等问题,可反馈申请退款(可完整预览的文档不适用该条件!)。
- 3、如文档侵犯您的权益,请联系客服反馈,我们会尽快为您处理(人工客服工作时间:9:00-18:30)。
张力调节量
十一、 PLC配置(1型)
十二、 PLC配置(2型高速)
十三、 PLC系统(1型)
电控箱
操作台
十四、 PLC系统(2型)
电控箱
操作台
个位置传感器
十五、简明实用的人机界面--1
成品厚度精度统计表
102 100
100*%
98 96 94 92 高精度 较高精度 精度等级 普通精度 95 98 100
- 0 .0 0 3 m m
十八、
• • • • • • • •
产品适用范围
各类有色黑色轧机设备: 各类冷、热轧四辊轧机 各类连轧机组 HC轧机 各类多辊液压压下轧机 平整机 各类旧轧机液压微调技术改造 (含弯辊控制)
系统介绍
——一个集机、电、液、测量 技术为一体的高性能数字式电液伺服
自动控制系统
一、系统的组成;
•
系统有压下油缸,測量 传感器(位置,压力传感 器),电液伺服阀,泵站, 测厚仪及快速高性能P.L.C. 组成数字式自动控制系统。
一、系统的组成; (压下电液原理)
F轧 制 力 + F平 衡 力
+ F弯 辊 力 + F磨 擦 力
编码器 编码器
系统
位置实际值 位置调节值 轧制力 调节量
辊缝设定
入口厚度设定
预控
监控
出口厚度设定
轧制方向
十、张力、速度AGC
压下油缸
轧制方向 测厚仪
轧制力给定
编码器
轧制力际值
轧制力调节值
控制系统
轧 制 力 FW 速度装置
辊缝实际值 轧制力附加给定 出口厚度设定 入口厚度设定
开卷张力装置
速度调节量
二号伺服阀流量特性
四、测量传感器;
• 位置传感器: • 德国BLLUFF微脉冲位置传感器, • 分辨率:1um, 精度:±3um。 • 或日本SONY磁尺, • 分辨率:1um, 精度:±2um。 • 压力传感器: • 根据液压系统选定。
五、位置闭环系统A.P.C.;
位置反馈1
位置给定 压下 抬起
二、双伺服阀控制;
• • • • • • 采用德国西马克双伺服阀控制方案; 配有单阀,双阀工作选择环节; 提高了系统快速反应及稳定性; 提高了伺服阀使用寿命; 方便系统维护; 减少了设备停机时机;
三、 2个伺服阀工作状况
流量 电流
号伺服阀流量特性
流量
电流
• 当第1个伺服阀流量 输出饱和后, • 第2个伺服阀流量才 开始输出; • 总流量为2个伺服阀 输出流量的和; • 微调时仅1个伺服阀 工作。
位置反馈2
位置传感器 伺服阀1 压下油缸
倾斜给定 左倾 右倾 油源 回油 平衡油源 伺服阀2
六、压力闭环系统A.F.C.
背压 压力反馈 压力给定 压下 抬起 伺服阀1 压下油缸
倾斜给定 左倾 右倾
油源 回油
压力传感器 伺服阀2 平衡油源
七、压下主要功能介绍;
• 位置传感器自动机械 定位; • 位置传感器压靠校零; • 二油缸同步调节; • 辊缝或压力给定; • 倾斜给定; • APC,AFC自动切换; • 平稳光滑切换; • 二侧辊缝数字显示, 分辨率〈5um。 • 辊缝倾斜数字显示; • 操作侧传动侧轧制力, 总轧制力数字显示; • 信号及报警系统; • 紧急卸压。 • 根据需要可配远程故 障诊断。
十五、简明实用的人机界面--2
操作侧 轧制力 辊 缝 传动侧 轧制力 辊 缝
入口厚 速 度
出口厚
十六、远程故障诊断
根据用户需要可增加硬件和软化,实现远程故障诊断。
上海
用户地
十 七 、 A .G .C .效 果
3 σ = ± 3 um A. G . C . 投 入 A. G . C . 退 出
+ 0 .0 0 3 m m
八、厚度自动控制AGC
• 液压压下装置根据 • 需要,配以测厚仪 在APC,AFC外组 • 成厚度闭环,实现 • 厚度自动控制。即 • A.G.C系统。
予控; 监控; 张力AGC; • 张力优先AGC; • 速度优先AGC。
根据需要A.G.C系 统有多种控制形式:
九、予控、监控AGC
压下油缸
测厚仪 测厚仪 位置给定