JLYJ711-2008 乘用车座椅用滑轨技术条件-单行版
Q-JLY_J711168-2008汽车内外饰塑料件通用技术条件

湿箱中保温 24 h,温度为 40℃±2℃,相对温度为 95%。接着在本标准 4.1.2 规定的环境下冷却 24 h。
5.10.2.2 在本标准 4.3 规定的环境温度下,通过测力计测定其所能承受的最大拉伸力,其拉伸速度为
100mm/min,拉伸方向垂直于焊缝方向。
5.10.2.3 试验后,将评估结论及可能观察到的现象进行记录。
5.10.2.1 在待测试的产品上截取两块焊缝长度为 50 mm 的试样。把两块试样分别进行下述两种不同的老
化处理:在本标准 4.1.1 规定的环境箱中保温 100 h,温度为 90℃±2℃;在本标准 4.1.3 规定的恒温恒
共 10 页 第 5 页
GEELY
汽车内外饰塑料件通用技术条件
Q/JLY J711168-2008
要求
外饰件
1
低温抗冲击性能
经低温抗冲击性能试验后,不允许出现开裂、折断、剥离和永久变形等现象。
2
抗划伤性能
经抗划伤性能试验后,不允许出现肉眼可见的划伤。
3
燃烧性能
应符合 GB8410 中的规定。
4
耐候性能
经耐候性能试验后,应不出现龟裂、斑点或其它缺陷,灰色标度值不小于 4 级。
5
气味性能
气味性应高于 6 级。
Q/JLY J711168-2008
4.1.4 振动试验台:应能实现上下、左右、前后三个坐标轴的振动。 4.1.5 氙光曝晒试验箱: 应符合 GB/T 16422.2-1999 的规定。 4.1.6 测力计:应该能适应拉延速率(0~100)mm/min。 4.2 试验仪器 4.2.1 燃烧特性测定仪:符合 GB 8410 的规定。 4.2.2 耐磨试验仪 4.2.3 钢球:直径 60mm、质量 0.9kg 的钢球,用来做冲击试验。 4.2.4 抗划伤性试验仪:应具有下述特点的刀具组成:
中华人民共和国汽车行业标准__座椅

中华人民共和国汽车行业标准QC/T633–200×客车座椅The seats of passenger vehicles(征求意见稿)200X-XX-XX发布 200X-XX-XX实施中华人民共和国国家发展和改革委员会发布目次前言1范围2规范性引用文件3 术语和定义4 要求4.1 一般要求4.2 零部件要求4.3 装配要求4.4 调节功能4.4.1 座椅头枕4.4.2 座椅总成纵(横)向调节机构4.4.3 靠背角调节机构4.4.4 座椅扶手4.5 安全性4.5.1 座椅背面的安装件或附件4.5.2 座椅纺织面料4.5.3 座椅有机材料的燃烧特性4.5.4 座椅头枕4.5.5 安全带的安装和固定4.5.6 纵(横)向调节机构的锁止力4.5.7 座椅扶手强度4.5.8 座椅脚蹬强度4.5.9 座椅强度4.6 可靠性4.6.1 纵(横)向调节疲劳性能4.6.2 座椅扶手循环试验4.6.3 座椅脚蹬循环试验4.6.4 靠背骨架总成耐久性4.6.5 靠背调角器耐久性5 试验方法5.1 座椅面料断裂强力试验5.2 座椅面料耐摩擦色牢度试验5.3 座椅面料透气性试验5.4 座椅衬垫材料性能试验QC/T 633—200×5.5 座椅5.6 座椅总成纵(横)向调节功能试验5.7 座椅有机材料燃烧特性试验5.8 座椅头枕试验5.9 安全带安装固定点强度试验5.10 座椅扶手强度试验5.11 座椅脚蹬强度试验5.12 座椅强度试验5.13 纵(横)向调节疲劳试验5.14 座椅扶手循环试验5.15 座椅脚蹬循环试验5.16 靠背骨架总成耐久性试验5.17 靠背调角器耐久性试验6 检验规则6.1 出厂检验6.2 型式检验7 标志、包装、运输、贮存前言本标准是对QC/T 633-2000《客车座椅》的修订。
本标准代替QC/T 633-2000《客车座椅》,其主要技术差异如下:1、增加了以下要求:a)外购件、外协件的要求;b)座椅纺织面料断裂强力、缝合部位接缝强力的要求;c)座椅纺织面料的基本安全技术要求;d)座椅有机材料阻燃性能的要求;e)座椅调节装置调节功能的要求;f)纵(横)向调节疲劳性能的要求;g)座椅扶手强度和可靠性的要求;h)座椅脚蹬强度和可靠性的要求;i) 靠背骨架总成耐久性的要求;j) 靠背调角器耐久性的要求;k) 座椅总成纵(横)向调节功能的要求;2、更新了以下标准:a)GB/T 5453—1997 纺织品织物透气性的测定b)GB 8410—2006 汽车内饰材料的燃烧特性c)GB 13057—2003 客车座椅及其车辆固定件的强度d)GB l4166—2003 机动车成年乘员用安全带和约束系统e)GB 14167—2006 汽车安全带安装固定点3、修改了以下内容:a)客车座椅的名词术语;b)型式检验产品合格判定规则。
乘用车驾驶员座椅安装点静刚度分析规范

Q/JLY J711 -2008乘用车驾驶员座椅安装点静刚度CAE分析规范编制:校对:审核:审定:标准化:批准:浙江吉利汽车研究院有限公司二〇〇八年九月前言为了给新车型开发提供设计依据,指导新车设计,评估新车结构性能,结合本企业实际情况,制定本标准。
本规范由浙江吉利汽车研究院有限公司提出。
本规范由浙江吉利汽车研究院有限公司综合技术部负责起草。
本规范主要起草人:汤志鸿。
本规范于2008年9月5日发布并实施。
1 范围本标准规定了乘用车驾驶员座椅安装点静刚度CAE分析的软硬件设施、输入条件、输出物、分析方法、分析数据处理及分析报告。
本标准适用于乘用车驾驶员座椅安装点静刚度CAE分析。
2 软硬件设施a)软件设施:主要用于求解的软件,采用MSC/NASTRAN;b)硬件设施:高性能计算机。
3 输入条件3.1 白车身有限元模型乘用车驾驶员座椅安装点静刚度分析的输入条件主要指白车身的有限元模型,一个完整的白车身有限元模型中含内容如下:a)白车身各个零件的网格数据;b)白车身焊点数据;c)各个零件的材料数据;d)各个零件的厚度数据。
3.2 白车身3D几何模型乘用车驾驶员座椅安装点静刚度CAE分析的白车身3D几何模型,数据要求如下:a)白车身各个零件的厚度或厚度线;b)白车身几何焊点数据;c)3D CAD数据中无明显的穿透或干涉;d)白车身各个零件的明细表。
4 输出物乘用车驾驶员座椅安装点静刚度分析的输出物为PDF文档格式的分析报告,针对不同的车型统一命名为《车型驾驶员座椅安装点静刚度分析报告》(“车型”用具体车型代号替代如:车型为GC-1,则分析报告命名为《GC-1驾驶员座椅安装点静刚度分析报告》),报告内容的按7规定的内容编制。
5 分析方法5.1 分析模型分析模型包括白车身的有限元模型(不含四门两盖和前、后挡风玻璃),钣金件均采用壳单元模拟。
5.2 分析模型建立建立有限元模型,应符合下列要求:a)白车身各个零件的网格质量应符合求解器的要求;b)白车身同一总成的零件,须放在同一个“集合”里;c)白车身各个零件的材料,须与明细表规定的材料相对应;d)白车身各个零件的厚度,须与明细表规定的厚度相对应;e)焊点几何坐标须与3D焊点坐标一致,焊点连接的层数须明确,焊点单元的直径设为6mm;f)白车身有限元模型的质量应该与实车相等。
QJLY-J711----2015汽车用座椅皮革技术要求

QJLY-J711----2015汽车用座椅皮革技术要求Q/JLY J711 -2015汽车座椅皮革技术要求<秘密级>编制:付晓敏校对:杨豪审核:李莉标准化:伍永会批准:赵海澜浙江吉利汽车研究院有限公司二〇一五年四月前言为规范汽车用座椅皮革的性能,结合企业实际情况制定本标准。
本标准替代了Q/JLY J7110614A-2012《乘用车座椅皮革技术要求》,本标准与Q/JLY J7110614A-2012的主要差异为:——修改了定负荷伸长率性能要求;——增加了永久伸长率性能要求;——增加了仿皮缝合强力的要求;——增加了真皮尺寸变化率、防霉性要求;——增加了浅色皮革表面抗污性要求;——修改了真皮经向、纬向抗张力要求;——修改了真皮、仿皮(主面料)、仿皮(辅面料)断裂伸长率要求;——修改了真皮撕裂强力的要求;——修改了抗张力、断裂伸长率、撕裂强力试验方法;——修改了耐光照色牢度的试验方法;——修改了气味性要求;——修改了仿皮雾化性能要求。
本标准由浙江吉利汽车研究院有限公司提出。
本标准由浙江吉利汽车研究院有限公司NVH及环保性能开发部负责起草。
本标准主要起草人:付晓敏、杨豪。
本标准于2015年4月15日发布,2015年4月20日实施本标准历次版本更替信息如下:——Q/JLY J7110614A-2012(JLYY-JT39-08首次发布,Q/JLY J7110614A-2012第一次修改。
)I1 范围本标准规定了汽车座椅用真皮、仿皮等的技术要求及实验方法。
本标准适用于2015年4月30日之后新研发及正在研发的汽车座椅套、坐垫、头枕等皮革,2015年4月30之后的产品可参照执行。
2 规范性引用文件下列文件对于本文件的应用是必不可少的。
凡是注日期的引用文件,仅注日期的版本适用于本文件。
凡是不注日期的引用文件,其最新版本(包括所有的修改单)适用于本文件。
GB/T 250-2008 纺织品色牢度试验评定变色用灰色样卡GB/T 251-2008 纺织品色牢度试验评定沾色用灰色样卡GB/T 3920-2008 纺织品色牢度试验耐摩擦色牢度GB/T 8808-1988 软质复合塑料材料剥离试验方法GB/T 11547-2008 塑料耐液体化学试剂性能的测定GB/T 13773.1-2008 纺织品织物及其制品的接缝拉伸性能第1部分:条样法接缝强力的测定GB/T 16578.1-2008 塑料薄膜和薄片耐撕裂性能的测定第1部分:裤形撕裂法GB/T 17928-1999 皮革针孔撕裂强度测定方法QB/T 2537-2001 皮革色牢度试验往复式摩擦色牢度QB/T 2707-2005 皮革物理和机械试验样件的准备和调节QB/T 2709-2005 皮革物理和机械试验厚度的测定QB/T 2710-2005 皮革物理和机械试验抗张强度和延长率的测定QB/T 2714-2005 皮革物理和机械性能耐折牢度的测定QB/T 2726-2005 皮革物理和机械性能耐磨性的测定Q/JLY J711034B-2012 车内非金属材料雾化性限值要求及试验方法Q/JLY J711291-2008 汽车内饰材料挥发性有机物限值要求Q/JLY J7110279B-2014 汽车内外饰非金属件耐光老化试验规范Q/JLY J7110335A-2011 汽车非金属材料阻燃性限值要求及试验方法Q/JLY J7110538A-2012 车内非金属材料气味性试验方法Q/JLY J7110738A-2012 乘用车非金属零部件耐光老化性能技术要求3 术语和定义3.1真皮指动物原皮,经过物理或者化学处理后的天然产品。
QJLY J7110543A-2012-汽车行李舱内饰件技术条件(4)

表面应无破损、裂缝,不允许有直 径大于 3mm 的对穿孔和气孔。
经耐高温、低温和冷热交变试验后不允许出现扭曲、变形、起泡、凹陷、
变色、龟裂以及可见色调和光泽的变化等异常现象。
测试布上不允许有颜色痕迹,产品表面不允许有软化、发粘、斑点、颜
色等显著变化,允许轻微失光。
≥3 级
≤80mm/min
试样分组编号
1
2
3
4
5
6
7
8
9
10
√
√
√
√
√
√
√
√
√
√
√
-
-
-
-
-
-
-
-
-
-
√
-
-
-
-
-
-
-
-
-
-
√
-
-
-
---来自---
-
√
-
-
-
-
-
-
-
-
-
-
√
-
-
-
-
-
-
-
-
-
-
√
-
-
-
-
-
-
-
-
-
-
√
-
-
-
共 5 页 第 4页
GEELY
汽车行李舱内饰件技术条件
Q/JLY J7110543A-2012
表 3 (续)
将行李舱内饰件按实车装配状态安装在夹具上,在(-40±3)℃的恒温箱中保持 24h 以上,取出后在 常温(15℃~35℃)下放置 0.5h,目视应无扭曲、变形、起泡、凹陷、变色、龟裂及可见色调和光泽的变 化等异常现象。 5.1.3 冷热交变试验
乘用车座椅滑轨试验项目

座椅检测知多少
2.性能要求 2.1滑轨行程
标准要求
滑轨行程按产品图样的要求。
测试方法
调整上滑轨锁止在最前位置,测量上滑轨前端伸出下滑轨 前端的距离;再调整上滑轨锁止在最后位置,测量上滑轨 前端退入下滑轨前端的距离,两个距离之和为滑轨的行程
前端伸出距离
前端退入距离
座椅检测知多少
2.2前后调节手柄操作力 标准要求
座椅检测知多少
2.12滑轨耐久性 标准要求
QCT805-2008 4.2.12标准要求: 滑轨总成(或单只滑轨)经15000次 往复耐久试验后,工作正常,且不应 出现零件明显变形和异常响声。
测试方法
将滑轨安装在座椅上(或模拟实际座椅的安装夹具),固 定滑轨下安装孔,在座椅上(或模拟实际座椅的安装夹具) 加载P=80kg,然后调整滑轨至最后位置,以频率5次/分 钟~10次/分钟,按以下程序往复运动15000次循环: a) 在最后位置将滑轨解锁; b) 向前滑动至最前位置锁止; c) 在最前位置解锁; d) 由最前位置滑动至最后位置锁止。 此程序为一个循环。 备注:单支滑轨不加载。
45
75
90
130 130
座椅检测知多少
2.11静载荷强度 标准要求
QCT805-2008 4.2.11标准要求: 单只滑轨分离强度满足下表。 试验后滑轨无损坏,且功能正常。
单只滑轨 滑轨总成
载荷(N·m) 731 1350
测试方法
将单支滑轨或滑轨总成固定在夹具上,上部安装一模拟刚性靠 背骨架。在靠背上施加一相对H点的向后力矩(单支滑轨 T=731 N·m,滑轨总成T=1350 N·m),施加的力在5s内达到规定 值。同时保持0.3s以上,试验完成后滑轨总成不得有开裂,影 响安全的过度变形发生。滑轨(或滑轨总成)在测试时位于最 不利位置
座椅调角器_滑轨检测范围

汽车安全带
2
汽车安全带 安装固定点
2.1
安装固定点 强度
0324
GB14167-2006 《汽车安全带 安装固定点》
只做静态试验
3.1 滑轨行程
滑轨调节手
3.2
柄
操作力
滑轨滑动阻
3
乘用车座椅 用滑轨
3.3
力 滑轨松动间
0324
Q/HQNS001-2006《乘用车座椅 用滑轨通用技术条件》
3.4
隙
滑轨调节手
验
只做靠背骨 架总成及扶
手项目
靠背骨架总
5.3
成
耐久性试验
No. CNAS L2704
第4页共5页
序
产品/
项目/参数
号 产品类别 序号
名称
领域 代码
靠背骨架 5.4 总成间隙试
验
检测标准(方法)名称及 编号(含年号)
限制
说
范围
明
座椅扶手强
5.5
度
和刚度试验
扶手循环试
5.6
验
6.1 锁止强度
6.2
锁止力
调角器 4.7 锁止性能
涡卷弹簧 4.8 耐静力特性
定位偏差性
4.9
能
调角器交变 4.10 载荷耐久性
调角器工作
4.11
耐久性
调角器冲击
4.12
耐久性
靠背骨架 5.1 总成强度试
验
检测标准(方法)名称及 编号(含年号)
限制
说
范围
明
5
靠背骨架 总成
5.2
靠背骨架 总成刚度试 0324
QC/T740-2005《乘用车座椅 总成》
乘用车座椅总成标准

本标准规定了乘用车座椅总成的技术要求、试验方法、检验规则及标志、包装、运输和储存。
本标准适用于M1 类车辆的前排座椅总成。
本标准不适用于折叠式的附加座椅、侧向座椅。
下列文件中的条款通过本标准的引用而成为本标准的条款。
凡是注日期的引用文件,其随后所有的修改单(不包括勘误的内容)或修订版均不适用于本标准,然而,鼓励根据本标准达成协议的各方研究是否可使用这些文件的最新版本。
凡是不注日期的引用文件,其最新版本适用于本标准。
GB 8410 汽车内饰材料的燃烧特性GB ll550 汽车座椅头枕性能要求和试验方法GB 11552—1999 轿车内部凸出物GB/T 11563—1995 汽车 H 点确定程序GB l4167 汽车安全带安装固定点GB l5083 汽车座椅系统强度要求及试验方法QC/T 55—1993 汽车座椅动态舒适性试验方法SAE J826--2002 H 点测量仪和设计模型步骤和规范SAE Jl351—1993 绝缘材料的气味试验SAE Jl756—1994 汽车内饰材料确定成雾特性的试验下列术语和定义适用于本标准。
零部件装配完整的座椅。
汽车内最前排的座椅总成,也分为驾驶座总成和副驾驶座总成。
3.3在前排座椅总成中用于支持乘员坐骨和大腿的那一部分,可以通过联接方式与前靠背装配在一起。
前座垫总成可以有一个前后可调的或高度可调的调节机构。
在前排座椅总成中用于支持乘员背部的那一部分,前靠背总成可以用调角器来调节靠背的角度。
4.1 一般要求4.1.1 座椅总成应符合本标准的要求,并按经规定程序批准的产品图样和技术文件制造。
4.1.2 座椅表面不得有任何可能危及乘员安全的粗糙面或尖棱,应符合 GB ll552—1999 的要求。
4.1.3 所有面套应符合其对应图样的缝制及外观要求。
4.1.4 座椅表面应无污染、破损、开裂等缺陷以及客户不能接受的褶皱。
4.1.5 座椅 H 点的测量按 GB/T 11563—1995 ,应满足设计要求,允许误差为±15mm。
Q JLY J7110738A-2012

Q/JLY J7110738A-2012乘用车非金属零部件耐光老化性能技术要求<秘密级>编 制: 李慧连校 对: 王文涛审 核: 李 莉审 定: 刘 强会 签: 戴开红、高冬仙、张加聪梁文伟、祝贺、吴刚、何后裔标准化: 伍永会批 准: 杨安志浙江吉利汽车研究院有限公司前 言乘用车非金属零部件受太阳光、温度、湿度等环境因素的影响,易产生光老化现象,影响其观感和使用舒适性,严重时可使乘用车功能失效。
为了保证乘用车非金属零部件耐光老化性能达到使用要求,参考相关资料,结合本企业的具体情况特编制本标准。
本标准由浙江吉利汽车研究院有限公司提出。
本标准由浙江吉利汽车研究院有限公司NVH及材料工程部负责起草。
本标准起草人: 李慧连、王文涛、李莉。
本标准于2012年12月1日发布,2012年12月10日实施。
1 范围本标准规定了乘用车非金属零部件耐光老化性能的技术要求和试验方法。
本标准适用于2012年12月1日之后新研发及正在研发的乘用车非金属零部件,2012年12月1日之前已量产的产品可参照执行。
2 规范性引用文件下列文件对于本文件的应用是必不可少的。
凡是注日期的引用文件,仅注日期的版本适用于本文件。
凡是不注日期的引用文件,其最新版本(包括所有的修改单)适用于本文件。
GB/T 250-2008 纺织品色牢度试验评定变色用灰色样卡Q/JLY J7110279A-2011汽车内外饰非金属件耐光老化试验规范3 技术要求3.1 乘用车车内零部件依据所处环境受阳光影响强烈程度不同,其耐光老化试验的试验周期要求见表1,乘用车车外零部件依据所处水平面和垂直面的位置不同,其耐光老化试验的试验周期要求见表2。
3.2 乘用车非金属零部件测试样件按试验周期要求完成试验后,试样应满足以下要求:a) 灰度等级≥4;b) 试样表面无龟裂、粉化、变形、斑点、发白等影响产品外观质量的缺陷;c) 如需测试除表观性能外的其他性能(如机械性能等),其技术要求另行规定。
乘用车座椅用滑轨技术条件

乘用车座椅用滑轨技术条件
在乘用车座椅的设计中,滑轨技术是至关重要的。
滑轨技术用于调节座椅的前
后位置,以满足乘客的舒适需求。
根据乘用车座椅用滑轨技术条件的要求,以下是相关的内容需求:
1. 必须具备稳定性:乘用车座椅滑轨技术在设计时必须确保座椅的稳定性,避
免在行驶过程中产生晃动或噪音。
这有助于保障乘客的安全和舒适感。
2. 滑动顺畅:滑轨技术应确保座椅可以平稳、顺畅地在滑轨上前后调节。
这样,乘客便能够方便地调整座位位置,以获得舒适的驾乘体验。
3. 耐久性要求:座椅滑轨技术应具备足够的耐久性,能承受长时间的使用和重
复移动,而不会出现损坏或失效的情况。
这有助于提高乘用车座椅的可靠性和使用寿命。
4. 安全性要求:座椅滑轨技术必须具备良好的安全性能,确保座椅在发生碰撞
或急刹车等情况下不易滑动或打开。
这是为了保护乘客免受潜在伤害。
5. 调节范围广:滑轨技术应满足乘客不同身材和个人喜好的需求,能够提供足
够的调节范围和选项,以便每个乘客都能找到最舒适的座椅位置。
综上所述,乘用车座椅的滑轨技术条件需要确保座位的稳定性、滑动顺畅、耐
久性、安全性以及调节范围广。
这些要求能够为乘客提供舒适、安全的驾乘体验,并进一步提高乘用车座椅的品质和性能。
对JT 711-2008标准的实践与建议
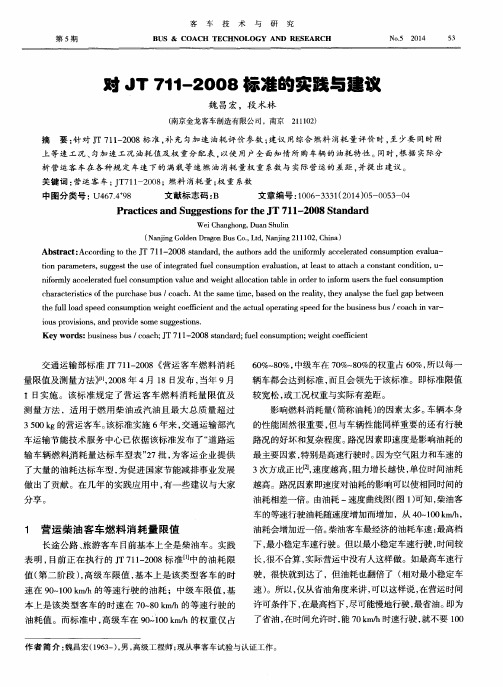
文献标志码 : B
文章编号 : 1 0 0 6 — 3 3 3 1 ( 2 0 1 4 ) 0 5 - 0 0 5 3 — 0 4
Pr a c t i c e s a n d S u g g e s t i o n s f o r t h e J T 7 1 1 — 2 O 0 8 S t a n d a r d
影 响燃料消耗量 ( 简称油耗 ) 的因素太多。 车辆本 身 的性 能固然 很重要 , 但与车辆性能 同样重要 的还 有行驶 路况 的好坏 和复杂程度 。 路况 因素 即速度是影响油耗的 最主要 因素 , 特别是高速行驶时。 因为空气阻力和车速 的 3 次方成正 比囝 , 速度越 高 , 阻力增长越快 , 单位时间油耗 越高。路况因素即速度对油耗 的影响可 以使相同时间的
交通运输部标 准 J T 7 1 1 - 2 0 0 8《 营运客 车燃 料消耗
6 0 %~ 8 0 %, 中级车在 7 0 %~ 8 0 %的权重 占 6 0 %, 所 以每一
量限值及测量方法》 【 l 】 , 2 0 0 8 年 4月 1 8日发布 , 当年 9月
1日实施 。该 标准 规定 了营运 客车 燃料 消耗 量 限值及
客 第5 期
车
技
术
与
研
究
BUS & C0ACH TECH N0Lo GY AND RES EARCH
对J T 7 1 1 — 2 0 0 8标准的实践与建议
魏 昌宏 ,段 术林
( 南 京 金龙 客车 制造 有 限公 司 ,南 京 2 1 1 1 0 2 )
摘 要 : 针对 J T 7 1 1 - 2 0 0 8标准 , 补 充匀加 速油耗 评价参数 ; 建议 用综合 燃料 消耗量评价 时 , 至 少要 同时 附 上等速 工况、 匀加速 工况油耗值及权 重分配表 , 以使 用户全 面知情所购车辆的油耗特性。同时, 根据 实际分
座椅滑轨

《乘用车座椅用滑轨技术条件》编制说明一、任务来源根据全国汽车标准化技术委员会“汽标秘字(2007)33号”《关于转发二○○七年汽车行业标准制订项目计划的通知》,汽车行业标准《乘用车座椅用滑轨技术条件》已列入了该计划中,项目号200709。
《乘用车座椅用滑轨技术条件》是根据目前国内座椅用滑轨无相应技术标准的现状,且各制造厂、座椅厂和主机厂之间的标准又不统一。
杭州市汽车内饰件有限公司为统一和规范国内乘用车座椅用滑轨设计、制造和试验要求而提出制订的。
二、标准制订的目的和意义随着中国汽车业的迅猛发展,我国的汽车配件行业已经融入了国际市场,越来越多的跨国公司把中国作为一个世界性的汽车配件生产制造中心。
而国内乘用车座椅滑轨的技术含量、产品质量良莠不齐,在一定程度上制约了市场的发展。
乘用车座椅用滑轨是乘用车座椅的主要功能件之一,由于近几年乘用车座椅的快速发展,对乘用车座椅功能件的要求也愈趋提高。
但至今还无国家标准或行业标准对乘用车座椅用滑轨的设计、制造及试验规定作相应的要求和方法。
目前乘用车座椅用滑轨基本上是按照整椅厂的要求、或参照国外汽车厂商的类似标准设计和制造,不同的车型、不同的厂家(生产厂家、座椅厂和主机厂)分别制定有不同的产品标准,有些合资、外资企业沿用了不同国家不同汽车主机厂的现有标准,致使企业的产品标准过多、基本性能、技术要求、试验方法不统一,极易在试验和判定时产生很大误差,引起各厂商间的争执。
部分国外标准也不尽适应中国的汽车行业现状。
少量制造商利用国家现无标准的现状,粗制滥造使得产品质量低下,不安全因素上升。
这样的现状已远不能满足国内汽车行业座椅滑轨的生产和产品档次提升,也影响到座椅安全性和舒适性的要求。
为规范国内各类乘用车座椅用滑轨的基本性能、技术要求和试验方法,制订乘用车座椅用滑轨技术条件显得十分迫切。
我公司在行业内技术力量雄厚,产品质量上乘,在技术上有所突破,填补了一些国内空白,并建有国家认可的检测实验室。
QJLY J711147-2008乘用车座椅技术条件
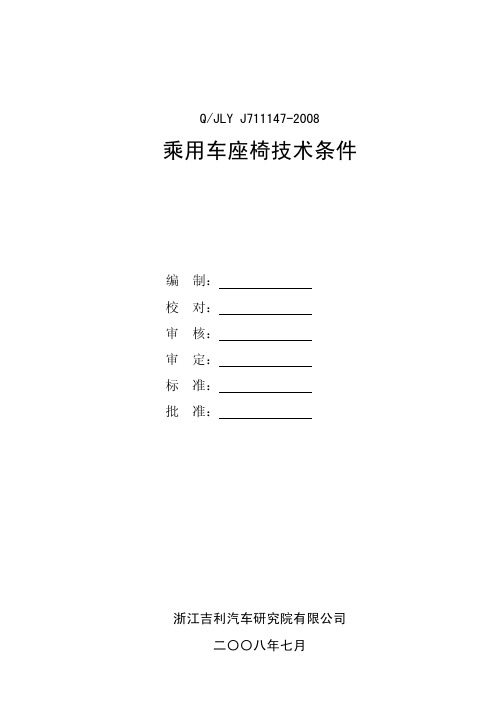
Q/JLY J711147-2008乘用车座椅技术条件编 制:校 对:审 核:审 定:标 准:批 准:浙江吉利汽车研究院有限公司二〇〇八年七月前 言在综合分析同类产品的国内外标准的基础上,结合本企业实际情况,制定本标准。
本标准由浙江吉利汽车研究院有限公司提出。
本标准由浙江吉利汽车研究院有限公司车身内外饰部附件科负责起草。
本标准起草人:杜光圣。
本标准于2008年7月25日发布并实施。
Ⅰ1 范围本技术条件规定了汽车座椅的技术要求、试验方法、检验规则、标志、包装、运输贮存等。
本技术条件适用于乘用车座椅。
2 引用标准下列文件中的条款通过本标准的引用而成为本标准的条款。
凡是注日期的引用文件,其随后所有的修改单(不包括勘误的内容)或修订版均不适用于本标准,然而,鼓励根据本标准达成协议的各方研究是否可使用这些文件的最新版本。
凡是不注日期的引用文件,其最新版本适用于本标准。
GB/T 5453-1997 纺织品 织物透气性的测定GB 8410 汽车内饰材料燃烧特性GB/T 10125-1997 人造气氛腐蚀试验 盐雾试验GB/T 10802-2006 通用软质聚醚型聚氨酯泡沫塑料GB 14167 汽车安全带安装固定点GB 15083 汽车座椅、座椅固定装置及头枕强度要求和试验方法JB/T 5943-1991 工程机械焊接件通用技术条件QC/T 55-1993 汽车座椅动态舒适性试验方法QC/T 56-1993 汽车座椅衬垫材料性能试验方法QC/T 484-1999 汽车油漆涂层QC/T 625-1999 汽车用涂镀层和化学处理层QC/T 740-2005 乘用车座椅总成ECE R44 儿童约束系统SAE J826-1995 H点测量仪和设计步骤和规范SAE J1756-2006 汽车内饰材料确定成雾特性的试验JLYY-JT1-08 车用纬编座椅面料性能要求JLYY-JT39-08 车用皮革技术要求JLYY-JT52-08 车用机织座椅面料性能要求JLYY-JT146-04 汽车内饰材料气味性试验方法JLYY-JT191-06 汽车内外饰塑料件通用技术条件JLYY-JT296-08 车用经编座椅面料性能要求JL 100003-2007 汽车零部件永久性标识规定3 术语定义下列术语和定义适用于本标准。
《乘用车座椅用滑轨》浙江制造标准编制说明

《乘用车座椅用滑轨》“浙江制造”标准编制说明1 项目背景本项目标准相应的产品属于:中国标准分类T21,行业标准分类“C制造业”大类下的“汽车制造业”中的“汽车零部件及配件制造”小类(行业代码C3670)。
根据科学技术部、财政部、国家税务总局发布的《国家重点支持的高新技术领域(2017 年)》,公司产品涉及 “八、先进制造与自动化”之“(七)汽车及轨道车辆相关技术”之 “2、汽车关键零部件技术”。
汽车行业是国民经济重要的支柱产业,汽车产品是重要的交通运输工具,汽车市场的发展自有其与国计民生密不可分的内在规律。
近十年来,作为我国的支柱产业之一,汽车业也得到迅速的发展,汽车产量、销量快速增加。
据中汽协预测,未来几年不会出现大幅波动,座椅市场规模增速将与汽车产量增速保持一致,新能源汽车将是下一个快速增长的新市场;预计未来三年内,新能源车销量复合增长速度将在五成以上。
2020年将有突破性发展;新能源汽车保有量2025年很可能大幅增长。
对于汽车零部件生产企业是一个很好的机遇。
根据我国汽车市场自主品牌乘用车和10万元以下的乘用车未来几年的销量增速预测,至2020年,自主品牌乘用车座椅规模有望突破360亿元,其中10万元以下乘用车(自主品牌+合资品牌+外资品牌)座椅市场规模有望达突破330亿元,随着中国经济的发展,城镇化水平的提升,居民收入的增长,消费能力的提升,以及道路基础设施的改善,将持续为中国汽车市场增长提供动力,因此,从中长期看,为汽车工业发展相配套的本行业还有较稳定的发展空间。
乘用车座椅用滑轨是汽车座椅总成中最为重要的一个零部件,它安装在汽车座椅的底部,以便根据需要调节座椅的前后位置,具有非常高的技术含量和专利保护,属于汽车安全件之一。
国务院发布《中国制造2025》指出核心基础零部件(元器件)、先进基础工艺、关键基础材料和产业技术基础(以下统称“四基”)等工业基础能力薄弱,是制约我国制造业创新发展和质量提升的症结所在。
- 1、下载文档前请自行甄别文档内容的完整性,平台不提供额外的编辑、内容补充、找答案等附加服务。
- 2、"仅部分预览"的文档,不可在线预览部分如存在完整性等问题,可反馈申请退款(可完整预览的文档不适用该条件!)。
- 3、如文档侵犯您的权益,请联系客服反馈,我们会尽快为您处理(人工客服工作时间:9:00-18:30)。
4.1 基本要求 4.1.1 滑轨总成应符合本标准的要求,并按经规定程序批准的产品图样和技术文件制造。 4.1.2 零件外表面应光洁、无伤痕、无裂纹,以及毛刺等缺陷。
共 10 页 第 1 页
GEELY
乘用车座椅用滑轨技术条件
Q/JLY J711 -2008
4.1.3 铆接和焊接部位应牢固可靠,无松动现象,焊接部位应光滑。
单支滑轨的分离强度按图 5所示方法试验。上滑轨调整至设计位置(无设计位可处于中间位)并在正 上方逐渐加载至规定值,其结果应符合 4.2.7 的要求。
图 5 分离强度 5.8 锁止强度试验
单支滑轨的锁止强度按图 6 所示方法试验。 滑轨锁止在任意位置, 在上滑轨上逐渐加载至规定值, 其
共 10 页 第 5 页
a) 向前加载至规定值,然后卸载至零; b) 再向后加载至规定值,然后卸载至零。 此程序为一个循环,试验后其结果应满足 4.2.13 的要求。
图8 交变载荷承受强度试验 5.14 滑轨异响的试验
在安静的环境内,对滑轨进行全行程滑动,其结果应满足 4.2.14 的要求。 5.15 升降机构性能测试
a) 将68kg载荷加载在升降机构上,操作手轮在高度调节时测量运动过程中最大的扭矩;操作手柄在 离末端 10mm处高度调节时测量运动过程中最大的操作力,其结果应满足 4.2.15-a) 的要求。
GEELY
乘用车座椅用滑轨技术条件
结果应符合 4.2.8 的要求。
Q/JLY J711 -2008
图6 滑轨强度试验
5.9 限位档点强度试验
单支滑轨限位档点强度按图 6 所示方法试验。在解锁的状态下将上滑轨推至一端,并在上滑轨上逐
渐加载至规定值,其结果应符合 4.2.9 的要求。
5.10 螺母焊接强度试验
此程序为一个循环,试验后其结果应满足 4.2.12 的要求(单支滑轨不加载) 。
5.13 滑轨交变载荷承受强度耐久试验
共 10 页 第 6 页
GEELY
乘用车座椅用滑轨技术条件
Q/JLY J711 -2008
滑轨交变载荷承受强度耐久试验按图 8所示方法进行。以频率 15次/ 分钟~ 30次/ 分钟,按以下程序往 复运动 15000次:
共 10 页 第 4 页
GEELY
足4.2.4 的要求。
乘用车座椅用滑轨技术条件
Q/JLY J711 -2008
图 3 松动间隙 5.5 手柄套拔出力试验
解锁手柄套拔出力按图 4 所示方法试验,其结果应满足 4.2.5 的要求。
图 4 手柄套拔出力 5.6 解锁手柄强度试验
解锁手柄强度按图 1所示方法试验,其结果应满足 4.2.6 的要求。 5.7 分离强度试验
c) 锁止强度按图 9所示方法进行,滑轨锁定在中间位置,升降机构锁定在最高位上。在机构上端中心
位置施加载荷 G=4000N,其结果应满足 4.2.15-c) 的要求。
d) 垂直冲击强度试验:滑轨锁定在中间位置,升降机构分别调节至最高、中间和最低位,从距
H点
200mm的高度自由落体 64kg的重物进行冲击测试, 每种状态重复 2次, 试验后其结果应满足 4.2.15-d)
图1 调节手柄操作力 5.3 滑动阻力的试验
滑动阻力试验方法如图 2所示。在滑轨总成上部施加 P=68kg 的载荷,先滑动 5个循环,再用测力计 试验其滑动阻力,其结果应满足 4.2.3 的要求(单支滑轨不加载) 。
图 2 滑动阻力 5.4 松动间隙试验
松动间隙的试验方法如图 3所示。将滑轨固定在测试台上,并在最后或最前位置锁定滑轨。先从一个 方向施加规定的作用力,调百分表至零位,再反方向施加规定的作用力,读取表中的位移量。其结果应满
物进行冲击测试,每种状态各测试 2次,功能及其它调节装置应无失效现象 ;
共 10 页 第 3 页
GEELY
乘用车座椅用滑轨技术条件
Q/JLY J711 -2008
e) 耐久性能,经 15000次耐久试验,升降机构零部件不得破坏,机构不得失效。 4.2.16 滑轨汽车安全带安装固定点强度
单支滑轨:施加拉力至 14700N时,固定点的变形量不大于 60mm,零件连接无脱落或拉裂现象。 滑轨总成:应符合 GB14167标准中的要求。 4.2.17 电动滑轨调节功能要求 电动滑轨的调节功能应符合相关图样的要求。
单支滑轨
731N·m
滑轨总成
1350N·m
4.2.12 滑轨耐久性 滑轨总成 (或单支滑轨) 经15000次往复耐久试验后, 工作正常 , 且不应出现零件明显变形和异常响声。
4.2.13 滑轨交变载荷承受强度耐久性 滑轨总成在向前施加 98N·m ,向后施加 245N·m载荷下,经 15000次往复试验后,滑轨应工作正常,
GB 14167 汽车安全带安装固定点
3 术语和定义
下列术语和定义适用于本标准。 3.1
单支滑轨 every slider 指座椅单侧滑轨。 3.2 滑轨总成 slider assembly 指左右滑轨按座椅安装尺寸装配后总成状态。 3.3 升降机构 height adjuster 改变座椅高度的机构也称座椅高度调节器。 3.4 座椅 seat 汽车内有靠背的座具。
4.1.4 零件表面应进行防腐处理或采用耐腐材料。 4.1.5 各滑动摩擦表面应涂有适量的润滑脂。
4.2 性能要求
4.2.1 滑轨行程 滑轨行程按供需双方商定的要求。
4.2.2 调节手柄操作力 按5.2 测试,滑轨总成调节手柄的操作力 F1为10N~98N,F2为10N~68N。
4.2.3 滑动阻力 单支滑轨的滑动阻力为 15N~58N,总成状态为 30N~166N。
5 试验方法
5.1 行程试验
调整上滑轨锁止在最前位置, 测量上滑轨前端伸出下滑轨前端的距离; 再调整上滑轨锁止在最后位置,
测量上滑轨前端退入下滑轨前端的距离,两个距离之和为滑轨的行程,其结果应满足
4.2.1 的要求。
5.2 调节手柄操作力的试验
滑轨总成调节手柄操作力按图 1 所示方法用测力计试验,其结果应满足 4.2.2 的要求 。
4000N
4000N
共 10 页 第 2 页
GEELY
乘用车座椅用滑轨技术条件
Q/JLY J711 -2008
4.2.8 锁止强度 单支滑轨锁止强度应符合表 2的规定,试验后滑轨无损坏,且上下滑轨没有相对位移。
4.2.9 限位档点强度
单支滑轨限位档点强度应符合表 2的规定,试验后限位档点无损坏,且上下滑轨没有相对位移。
本标准由浙江吉利汽车研究院有限公司提出。 本标准由浙江吉利汽车研究院有限公司附件科负责起草。 本标准主要起草人:杜光圣。 本标准于 2008年7月30日首次发布并实施。
Ⅰ
GEELY
乘用车座椅用滑轨技术条件
Q/JLY J711 -2008
1 范围
本标准规定了乘用车座椅用滑轨的术语和定义、技术要求、试验方法、检验规则、标志、包装、运输 及储存。
图7 静载荷试验强度
5.12 滑轨耐久性试验
滑轨耐久性试验按图 2 所示方法进行。固定滑轨并加载 P=80kg,然后调整滑轨至最后位置,以频率 5
次/ 分钟~ 10次/ 分钟,按以下程序往复运动 15000次:
a) 在最后位置将滑轨解锁;
b) 向前滑动至最前位置锁止;
c) 在最前位置解锁;
d) 由最前位置滑动至最后位置锁止。
本技术条件适用于乘用车座椅滑轨。
2 规范性引用文件
下列文件中的条款通过本标准的引用而成为本标准的条款 . 凡是注日期的引用文件,其随后所有的修 改单 ( 不包括堪误的内容 ) 或修订版均不适用于本标准,然而,鼓励根据本标准达成协议的各方研究是否可 使用这些文件的最新版本 . 凡是不注日期的引用文件,其最新版本适用于本标准。
b) 带自动回复功能的升降力测试按图 9所示方法进行将升降机构锁止在最高状态,在上端中心位置施 加作用力 G=500N,打开锁止机构,升降器应下降。 将升降机构锁止在最低位置,在上端中心位置 施加作用力 G=220N,打开锁止机构,升降器应上升。 其结果都应满足 4.2.15-b) 的要求。
图 9 升降机构性能测试
4.2.4 松动间隙 单支滑轨的松动间隙应符合表 1的规定。
表 1 单支滑轨松动间隙
项
目
位置
载荷( N)
松动间隙( mm)
前后
100
≤0.35
左右
50
≤0.50
上下
50
≤0.50
4.2.5 手柄套拨出力 解锁手柄套拔出力应大于 196N。
4.2.6 解锁手柄强度 解锁手柄强度在施加 294N的力后,应无影响其功能的变形和损坏。
4.2.7 分离强度
单支滑轨的分离强度应符合表 2的规定,试验后滑轨无损坏,且功能正常。
表 2 分离强度、锁止强度和限位档点强度
分离强度
锁止强度
前向
后向
限位档点强度
前向
后向
带安全带固定点
5900N
13500N
5900N
5900N
4000N
无安全带固定点
4000N
5900N
5900N
个循环。 3) 升降器后端全程升降试验:将升降机构后端调整到最高位置和最低位置为一循环,往复升降 5000个循环。 经15000个耐久试验后, 其结果应满足 4.2.15-e) 条的要求。 (如前后只一端有升降机 构,试验为 10000个循环) 5.16 滑轨汽车安全带安装固定点强度试验 单支滑轨按图 10 所示方法进行,施加力沿滑轨水平向上 50 °方向,并检测固定点的变形量,试验 需在最前、中间、最后状态各一次,其结果应满足 4.2.16 的要求。 滑轨总成汽车安全带安装固定点强度的试验方法按 GB14167 标准中的要求进行。