PLC传送带控制系统
传送带PLC控制系统设计

参考内容
一、引言
可编程逻辑控制器(PLC)是一种广泛应用于工业自动化控制的装置,具有 高可靠性、抗干扰能力强、编程简单等特点。在物料分拣传送带系统中,PLC通 常作为主控单元,对传送带运行进行实时监控和控制。物料分拣传送带主要负责 将不同种类的物料按照要求分拣到指定位置,变频调速控制系统则可以调节传送 带的运行速度,提高分拣效率。本次演示将详细介绍基于PLC的物料分拣传送带 变频调速控制系统的设计。
传送带PLC控制系统设计
ห้องสมุดไป่ตู้ 目录
01 一、理解传送带PLC 控制系统的重要性
03 参考内容
02
二、传送带PLC控制 系统设计详解
随着工业生产的不断发展,PLC控制系统在各种生产设备中的应用越来越广 泛。其中,传送带PLC控制系统设计对于提高生产效率和降低成本具有重要意义。 本次演示将详细介绍传送带PLC控制系统设计的相关内容。
三、系统设计
1、硬件设计
(1)电气控制系统:包括电源模块、输入模块、输出模块和通信模块。电 源模块为整个系统提供稳定的电源;输入模块接收操作人员输入的信号和传感器 采集的信号;输出模块根据PLC的处理结果控制变频器和执行机构;通信模块则 实现PLC与其他设备的数据交换。
(2)传感器选择:根据分拣要求选择相应的传感器,如重量传感器、颜色 传感器、尺寸传感器等,对物料进行检测和识别。
感谢观看
(3)仪表安装:选择合适的仪表对系统进行实时监控,如电流表、电压表、 转速表等。
2、软件设计
(1)PLC程序设计:根据分拣要求编写PLC程序,实现系统的逻辑控制和实 时监控。程序包括输入处理、输出处理、通信处理、数据处理等功能。
(2)变频器调试:根据传送带的负载和电动机的参数,调试变频器参数, 实现稳定的调速控制。
基于PLC的传送带控制系统设计
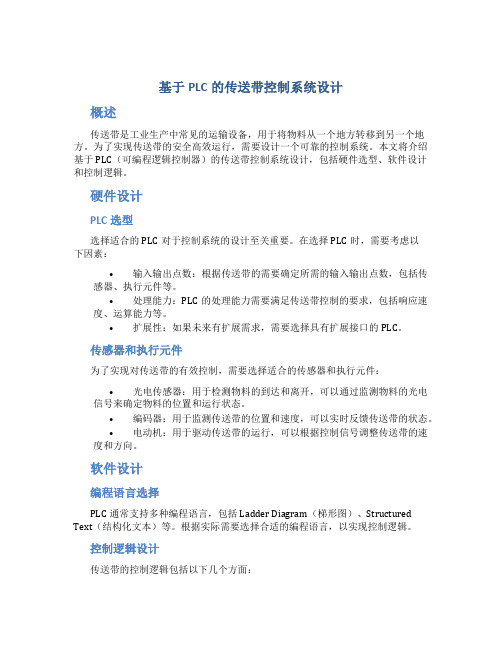
基于PLC的传送带控制系统设计概述传送带是工业生产中常见的运输设备,用于将物料从一个地方转移到另一个地方。
为了实现传送带的安全高效运行,需要设计一个可靠的控制系统。
本文将介绍基于PLC(可编程逻辑控制器)的传送带控制系统设计,包括硬件选型、软件设计和控制逻辑。
硬件设计PLC选型选择适合的PLC对于控制系统的设计至关重要。
在选择PLC时,需要考虑以下因素:•输入输出点数:根据传送带的需要确定所需的输入输出点数,包括传感器、执行元件等。
•处理能力:PLC的处理能力需要满足传送带控制的要求,包括响应速度、运算能力等。
•扩展性:如果未来有扩展需求,需要选择具有扩展接口的PLC。
传感器和执行元件为了实现对传送带的有效控制,需要选择适合的传感器和执行元件:•光电传感器:用于检测物料的到达和离开,可以通过监测物料的光电信号来确定物料的位置和运行状态。
•编码器:用于监测传送带的位置和速度,可以实时反馈传送带的状态。
•电动机:用于驱动传送带的运行,可以根据控制信号调整传送带的速度和方向。
软件设计编程语言选择PLC通常支持多种编程语言,包括Ladder Diagram(梯形图)、Structured Text(结构化文本)等。
根据实际需要选择合适的编程语言,以实现控制逻辑。
控制逻辑设计传送带的控制逻辑包括以下几个方面:•启动和停止控制:根据输入信号判断传送带是否需要启动或停止,同时控制电动机的开启和关闭。
•速度和方向控制:根据设置的速度和方向信号,调整电动机的转速和传送带的运行方向。
•故障检测和保护:监测传感器和执行元件的状态,及时发现故障并采取保护措施,例如停止传送带或报警。
控制系统实现硬件连接根据PLC和传感器、执行元件的接口要求,进行硬件连接。
确保输入信号和输出信号正确连接到PLC的相应接口。
软件编程根据控制逻辑设计,使用选择的编程语言编写PLC程序。
在编程过程中,需要充分考虑系统的实时性和稳定性,确保程序的可靠性。
plc第七章传送带(电子书)

第7章传送带控制系统本章以制作传送带控制系统为目的,首先从简单的单传送带、多传送带控制入手,逐步学会传送带控制的多种设计方法,最终完成四节传送带控制系统设计,使学生对传送带可编程控制系统有一个直观、感性的认识,锻炼读者应用PLC解决问题的能力。
教学导航教知识重点(1)基本触点指令,置位、复位、RS触发器。
(2)掌握顺序控制程序设计方法。
(3)掌握程序控制类指令、子程序设计。
(4)熟练掌握PLC程序设计、调试流程。
知识难点(1)S7-200的I/O地址分配规律。
(2)程序控制类指令设计方法。
推荐教学方法本章的知识链接部分用讲授法和引导文法;初步训练部分使用案例教学法;强化训练、拓展训练部分使用项目教学法。
学推荐学习方法动手完成小车传送带控制系统的实现,实施过程中逐步理解S7-200的编程指令真正含义。
必须掌握的理论知识(1)基本触点指令,置位、复位、RS触发器。
(2)程序控制类指令使用方法。
必须掌握的技能(1)S7-200指令编写和外部接线连接。
(2)电动机传送带控制设计方法。
(3)传送带触摸屏控制设计方法。
7.1 知识链接7.1.1 程序控制类指令程序控制类指令用于程序运行状态的控制,主要包括系统控制、跳转、循环、子程序调用、顺序控制等指令,系统控制类指令主要包括暂停、结束、看门狗等指令。
1、条件结束(END/MEND) 指令所谓有条件结束(END)指令,就是执行条件成立时结束主程序,返回主程序起点,终止用户程序的执行返回主程序的第一条指令指行(循环扫描工作方式)。
梯形图结束指令不连在左侧母线时,为条件结束指令(END)。
条件结束指令用在无条件结束(MEND)指令之前,用户必须以无条件结束指令结束主程序。
条件结束指令执行时(指令直接连在左侧母线,无使能输入),梯形图结束指令直接连在左侧电源母线时,为无条件结束指令(MEND)。
注意:结束指令只能在主程序中使用,不能在子程序和中断服务程序中使用。
STEP7-Micro/WIN编程软件在主程序的结尾自动生成无条件结束(MEND)指令,用户不得输入无条件结束指令,否则编译出错。
PLC传送带控制系统
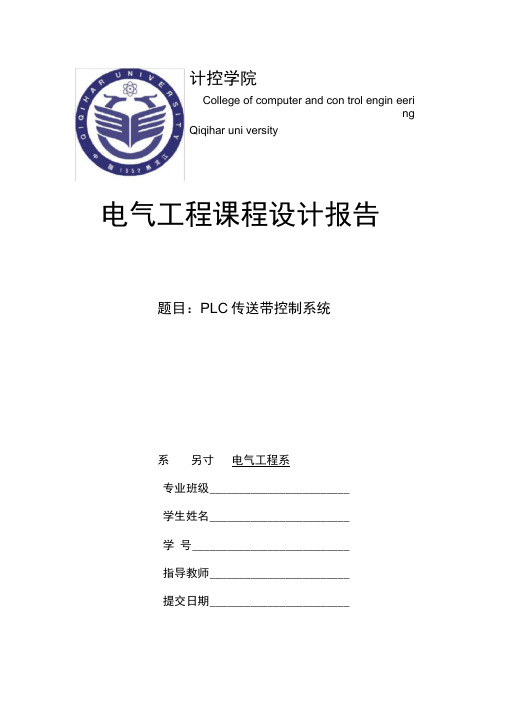
计控学院College of computer and con trol engin eeringQiqihar uni versity电气工程课程设计报告题目:PLC传送带控制系统系另寸电气工程系专业班级________________________学生姓名________________________学号___________________________指导教师________________________提交日期________________________成绩___________________________传送带是一种广泛应用于工业的传输设备,对其进行自动化的改造无疑将提高工业生产的效率和安全性并且将大大的节约人力资源。
因其意义重大,对传送带的改造是多方面的而本文将主要介绍的是:基于PLC的传送带多速度控制系统的设计。
该系统的设计包括硬件设计和软件设计。
其中硬件设计包括PLC、变频器、异步电动机的外部电路的设计与安装;软件部分包括程序的设计与调试。
所设计系统最终能够通过PLC与变频器实现以下功能:(1)能对物品进行运送,速度可根据两物品之间的距离自动变换防止传送物品之间发生碰撞;(2)能够实现故障报警、状态指示、传送带带负载软启动等;(3)能够实现手动与自动状态切换,方便维护。
该系统主要运用了PLC、传感器、继电器、变频器等器件,利用PLC良好的自动控制性能,实现流水线传送带传送过程的无人控制。
本文将主要对PLC、变频器以及PLC 对变频器的控制部分进行介绍。
关键词:PLC传送带;变频器;无人控制摘要.................................................................. ■■- I1设计目的及意义 (1)2设计内容 (1)2.1传送机的简介 (1)2.2可编程逻辑控制器(PLC) (1)2.3变频器 (1)3功能需求分析 (2)3.1系统功能 (2)3.2方案设计 (2)4具体设计 (3)4.1 PLC 选型 (3)4.2电动机的选择 (4)4.3变频器的选择 (4)4.4传感器 (4)4.5系统梯形图程序 (4)结论 (9)参考文献 (10)1设计目的及意义传统的传送带系统往往只能工作在某一固定的速度上,这种设计有着其他系统无法比拟的优点。
三层传送带PLC系统控制设计
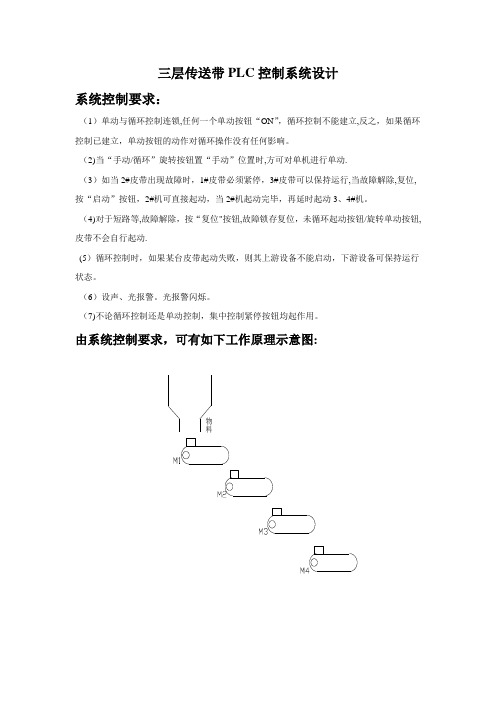
三层传送带PLC控制系统设计
系统控制要求:
(1)单动与循环控制连锁,任何一个单动按钮“ON”,循环控制不能建立,反之,如果循环控制已建立,单动按钮的动作对循环操作没有任何影响。
(2)当“手动/循环”旋转按钮置“手动”位置时,方可对单机进行单动.
(3)如当2#皮带出现故障时,1#皮带必须紧停,3#皮带可以保持运行,当故障解除,复位,按“启动”按钮,2#机可直接起动,当2#机起动完毕,再延时起动3、4#机。
(4)对于短路等,故障解除,按“复位"按钮,故障锁存复位,未循环起动按钮/旋转单动按钮,皮带不会自行起动.
(5)循环控制时,如果某台皮带起动失败,则其上游设备不能启动,下游设备可保持运行状态。
(6)设声、光报警。
光报警闪烁。
(7)不论循环控制还是单动控制,集中控制紧停按钮均起作用。
由系统控制要求,可有如下工作原理示意图:
物
料
PLC控制系统程序设计:(1)根据控制要求,有输入和输出表::
(2)由控制要求,可有PLC接线图:
(3)由控制设计的要求,可有外部电机接线图:
有上设计,可有传送带的PLC控制系统接线图:。
基于PLC的传送带控制系统设计

基于PLC的传送带控制系统设计第一章:引言1.1 研究背景随着工业自动化的发展,传送带在各个行业中被广泛应用。
传送带控制系统是其中重要的组成部分,它通过精确的控制实现物品的运输和分拣,提高生产效率和质量。
PLC(可编程逻辑控制器)作为一种可编程电子系统,具备高性能和可靠性,逐渐成为控制传送带系统的首选。
1.2 研究目的和意义本文旨在设计一种基于PLC的传送带控制系统,通过对传送带的运行状态进行监测和控制,实现物品的准确分拣和运输。
这对于提高传送带系统的工作效率和减少人力成本具有重要意义。
同时,本文的研究成果可以为其他控制系统的设计和优化提供参考。
第二章:传送带的工作原理和要求2.1 传送带的工作原理传送带由电动机、驱动轮、输送带和支撑构架等部分组成。
电动机通过驱动轮带动输送带运行,物品通过传送带在不同工位之间进行传送。
传送带控制系统需要根据实际需求,对传送带的运行速度、方向和起停等进行准确控制。
2.2 传送带控制系统的要求传送带控制系统首先需要具备良好的稳定性和可靠性,能够长时间稳定运行。
其次,系统需要具备高度的灵活性和扩展性,能够适应不同工况和物品的运输需求。
还需要实现对传送带的自动监测和报警功能,及时发现和修复故障。
第三章:基于PLC的传送带控制系统设计3.1 系统结构设计基于PLC的传送带控制系统由PLC主控单元、输入输出模块、传感器和执行器组成。
PLC主控单元负责控制传送带的运行状态,输入输出模块用于与外界进行信号交互,传感器用于监测传送带的运行情况,执行器用于控制传送带的运行。
3.2 PLC程序设计PLC程序设计是传送带控制系统设计的核心。
根据控制需求,设计PLC程序实现传送带的控制逻辑。
程序需要根据传感器的信号进行判断,控制执行器的动作,精确控制传送带的运行速度、方向和起停等功能。
3.3 传感器选择和布置传感器是实现对传送带运行状态监测的重要组成部分。
本文选择xx型传感器,该传感器具有良好的稳定性和高度的灵敏度。
基于PLC的传送带控制系统设计

基于PLC的传送带控制系统设计第一章:引言1.1 研究背景传送带是工业生产中常用的一种输送装置,广泛应用于物流、制造业、矿山和港口等各个领域。
为了提高生产效率和操作安全性,设计一个高效可靠的传送带控制系统至关重要。
本章将介绍基于PLC的传送带控制系统设计的背景和意义。
1.2 研究目的本研究的目的是设计一个基于PLC的传送带控制系统,通过自动化控制实现传送带的启动、停止、速度调节、倾斜角度控制等功能。
同时,通过传感器和监控设备实时监测传送带的工作状态,并及时报警和记录异常情况,提高生产效率和安全性。
第二章:传送带控制系统的总体架构2.1 传送带控制系统概述传送带控制系统由传送带本体、传感器、PLC控制器、人机界面和监控设备等组成。
其中,PLC控制器作为核心部件负责接收传感器信号并根据设定的逻辑和算法实现对传送带的控制。
2.2 传送带控制系统的工作流程本节将详细介绍传送带控制系统的工作流程,包括传感器信号采集、PLC控制算法实现、控制指令发送和监控设备数据处理等环节,以及各环节之间的数据流动和逻辑关系。
第三章:传送带控制系统的详细设计3.1 传感器信号采集为了实现对传送带的状态监测和控制,需要采集传感器的信号,包括传送带的速度、倾斜角度、工作温度等信息。
本节将介绍常用的传感器类型和其工作原理,并设计合适的信号采集电路进行数据获取。
3.2 PLC控制算法实现PLC控制器负责接收传感器信号并进行逻辑判断和控制指令生成。
本节将详细阐述传送带控制的算法设计,包括启动和停止控制、速度调节、倾斜角度控制和异常情况处理等。
3.3 控制指令发送PLC控制器通过各类输出模块将控制指令发送给传送带的电机、液压装置等执行机构。
本节将设计合适的接口电路和通信协议实现可靠的指令传输。
3.4 监控设备数据处理监控设备负责实时监测传送带的工作状态,并及时报警和记录异常情况。
本节将介绍监控设备的选型和接口设计,以及数据处理算法的实现。
plc传送带控制系统
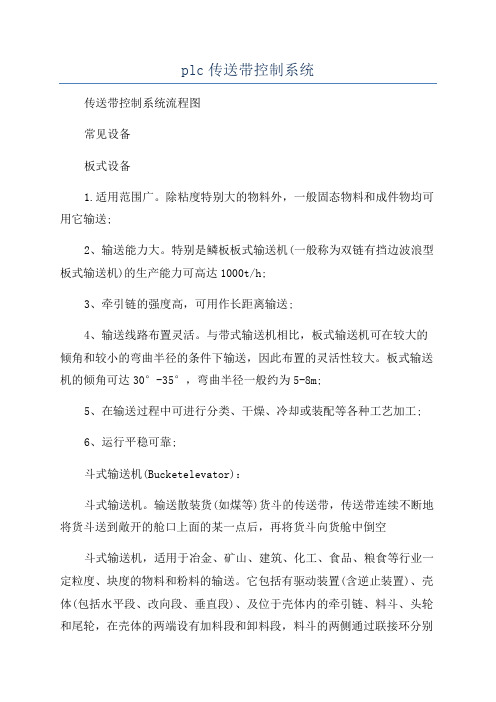
plc传送带控制系统传送带控制系统流程图常见设备板式设备1.适用范围广。
除粘度特别大的物料外,一般固态物料和成件物均可用它输送;2、输送能力大。
特别是鳞板板式输送机(一般称为双链有挡边波浪型板式输送机)的生产能力可高达1000t/h;3、牵引链的强度高,可用作长距离输送;4、输送线路布置灵活。
与带式输送机相比,板式输送机可在较大的倾角和较小的弯曲半径的条件下输送,因此布置的灵活性较大。
板式输送机的倾角可达30°-35°,弯曲半径一般约为5-8m;5、在输送过程中可进行分类、干燥、冷却或装配等各种工艺加工;6、运行平稳可靠;斗式输送机(Bucketelevator):斗式输送机。
输送散装货(如煤等)货斗的传送带,传送带连续不断地将货斗送到敞开的舱口上面的某一点后,再将货斗向货舱中倒空斗式输送机,适用于冶金、矿山、建筑、化工、食品、粮食等行业一定粒度、块度的物料和粉料的输送。
它包括有驱动装置(含逆止装置)、壳体(包括水平段、改向段、垂直段)、及位于壳体内的牵引链、料斗、头轮和尾轮,在壳体的两端设有加料段和卸料段,料斗的两侧通过联接环分别与两根平行的牵引链相联接。
头轮上设有与牵引链相吻合的齿。
其输送形式为一字形、L形、Z形三种。
本实用新型的优点是具有体积小、功耗低、输送形式灵活、密封输送等特点。
跑偏原因及处理方法传送带运行时输送带跑偏是最常见的故障之一。
跑偏的原因有多种,其主要原因是安装精度低和日常的维护保养差。
安装过程中,头尾滚筒、中间托辊之间尽量在同一中心线上,并且相互平行,以确保输送带不偏或少偏。
另外,带子接头要正确,两侧周长应相同。
在使用过程中,如果出现跑偏,则要作以下检查以确定原因,进行进行调整。
输送带跑偏时常检查的部位和处理方法有:(1)检查托辊横向中心线与带式输送机纵向中心线的不重合度。
如果不重合度值超过3mm,则应利用托辊组两侧的长形安装孔对其进行调整。
具体方法是输送带偏向哪一侧,托辊组的哪一侧向输送带前进的方向前移,或另外一侧后移。
传送带PLC控制系统设计

传送带PLC控制系统设计一、本文概述Overview of this article随着工业自动化水平的不断提升,传送带作为物流和生产流程中的关键环节,其控制系统设计变得愈发重要。
本文将深入探讨《传送带PLC控制系统设计》的相关内容,旨在为读者提供一套全面、高效的传送带控制系统设计方案。
文章将首先介绍传送带PLC控制系统的基本概念、发展历程以及其在工业自动化领域的应用价值。
随后,文章将详细阐述PLC控制系统的硬件组成、软件编程以及系统调试等关键环节,并结合实际案例进行分析。
文章还将探讨传送带PLC控制系统设计中的常见问题及解决方案,为读者在实际应用中提供有益参考。
通过本文的阅读,读者将能够深入了解传送带PLC控制系统的设计原理和实践方法,为工业自动化领域的发展贡献力量。
With the continuous improvement of industrial automation level, the control system design of conveyor belts, as a key link in logistics and production processes, has become increasingly important. This article will delve into the relevant content of "Design of PLC Control System for ConveyorBelt", aiming to provide readers with a comprehensive and efficient design scheme for conveyor belt control system. The article will first introduce the basic concept, development history, and application value of PLC control system for conveyor belts in the field of industrial automation. Subsequently, the article will elaborate in detail on the hardware composition, software programming, and system debugging of the PLC control system, and analyze them in conjunction with practical cases. The article will also explore common problems and solutions in the design of PLC control systems for conveyor belts, providing useful references for readers in practical applications. Through reading this article, readers will be able to gain a deeper understanding of the design principles and practical methods of PLC control systems for conveyor belts, contributing to the development of industrial automation.二、传送带基础知识Fundamentals of conveyor belts传送带作为工业生产和物流运输中的关键设备,广泛应用于各个行业。
传送带PLC控制系统设计

2 系统分析
根 据控制 要求可知 四级传送带 控制有6 个 输
1 控 制要求
本 文 以四 级 传 送 带 为 例 进 行 系 统 分析 和方 案
设计 ,四级 、停 止 及 M l 故 障 ̄ M4 故 障 )和 4 个
输 出信 号 ( 电动机 M 1 ~ 电动 机M4 )。如 果 采用 传 统 的 定 时 器 控 制 方 案 则 逆 序 启 动 时 需 要3 个 定 时
备 Ⅲ。传送 带 常 见的 控制 方案 是 采用若 干 个定 时器
实现 其 逆 序 启动 、顺 序 停 止 及 故 障 处理 功 能 ,程
序 复杂 且 不 易扩 展 ,触 发器 指 令 功能 类 似 于置/ 复 位 指令 , 合理 利 用 触 发 器 指 令 和 比 较 指令 简化 传
送带 顺序 控制程 序 。
程序控制器 ( 简称P L C )具有控制简单方便 ,适应能力强等特点 ,是工业控制领域的主流设 备。采用西门子¥ 7 - 2 0 0 P L O 的触发器 及比较 指令进行 四级传送制 I I 页 序控制 ,实现了四级传 送 带的逆序 启动 、顺序 停止及故 障处理等功 能 ,与传统 的定时器指令 控制方案相 比 ,设计思路 清晰新颖,设计程序简单,且易于扩展至多级传动带的J 0 页 序控制。 关键词 :传送带 ;可编程序 控制器 ; 顺序 控制 ;比较指令 ; 触发器指令
( 1 . 石家庄职 业技术学院 电气与 电子工程系 ,石家庄 0 5 0 0 8 1 ;2 . 石家庄职业技术学院 财务处 ,石家庄 0 5 0 0 8 1 ; 3 . 天津电气传动设计研 究所 ,天 津 3 0 0 3 8 0 ) 摘 要 :传送带广泛应用于运输 、电力、冶金 、建材等行业 ,是工业生产中常见的控制设备之一。可编
皮带传输机PLC控制系统

皮带传输机PLC控制系统皮带传输机是一种用于物流和工业领域的常见设备,它可以将物品从起点一直传输到终点,许多工厂和仓库都使用这种设备。
为了实现高效的自动控制,PLC控制系统已经被广泛应用于皮带传输机中。
什么是PLC控制系统PLC全称为可编程逻辑控制器(Programmable Logic Controller),它是一种能够接收和处理数字和模拟信号,并根据预定程序执行控制指令的设备。
PLC控制系统通常用于自动化生产线和机械设备中,以实现可编程的自动化控制。
PLC控制系统由以下几部分组成:•中央处理器(CPU):负责计算和执行控制程序;•输入模块:负责接收来自传感器或开关的信号,并将这些信号转换为数字信号;•输出模块:负责将PLC所执行的控制指令转换为模拟或数字信号,并将这些信号传递给执行器或其他设备;•编程器:负责编写和上传控制程序到PLC中。
皮带传输机PLC控制系统的工作原理皮带传输机的PLC控制系统通常由以下部分组成:•传感器:用于检测物品在皮带上的位置、速度和方向等信息;•PLC:控制所有的电机和执行器,实现对皮带的控制;•电机:驱动皮带运动;•执行器:用于控制物品在皮带上的流动方向和区域;•人机界面:提供可视化的控制界面,方便工作人员进行参数设置和监控。
整个PLC控制系统的流程如下:1.传感器检测物品在皮带上的位置、速度和方向等信息,并将这些信息传递给PLC控制器。
2.PLC根据预设的程序和传感器检测到的信息,计算出要执行的控制指令。
3.PLC将控制指令转换为模拟或数字信号,并将这些信号传递给电机和执行器。
4.电机开始工作,驱动皮带运动。
5.执行器控制物品在皮带上流动的方向和区域,实现物品的分流。
6.工作人员可以通过人机界面进行参数设置和监控,实现对PLC控制系统进行远程控制和监控。
皮带传输机PLC控制系统的优点与传统的控制方式相比,皮带传输机PLC控制系统具有以下优点:1.稳定性高:PLC具有较高的稳定性和可靠性,能够适应各种恶劣环境。
变频器和PLC在传送带多种速度控制中的应用

变频器和PLC在传送带多种速度控制中的应用一、本文概述随着工业自动化程度的不断提升,传送带作为物料运输的核心设备,其运行效率与稳定性对于生产线的顺畅运作至关重要。
在传送带的运行过程中,速度控制是关键因素之一,它直接影响到生产线的生产效率和产品质量。
近年来,随着变频器与PLC(可编程逻辑控制器)技术的快速发展和应用,它们在传送带速度控制中发挥着越来越重要的作用。
本文旨在探讨变频器和PLC在传送带多种速度控制中的应用,分析它们的工作原理、优势以及在实际生产中的应用案例,以期为相关领域的工程技术人员提供有益的参考和启示。
二、变频器的基本原理与功能变频器是一种能够调整电机运行频率的设备,它通过改变电源的频率和电压,实现对电机转速的精确控制。
变频器主要由整流器、滤波器和逆变器三部分组成。
整流器将输入的交流电转换为直流电,滤波器则用于平滑直流电压,消除谐波干扰,而逆变器则将直流电转换回交流电,其频率和电压可以根据需要进行调整。
变频器的基本工作原理是通过改变逆变器的开关模式,从而改变输出交流电的频率和电压。
当变频器接收到来自PLC或其他控制器的指令时,它会根据指令调整输出电压和频率,进而改变电机的转速。
通过这种方式,变频器能够实现电机的平滑调速,提高设备的运行效率和稳定性。
除了基本的调速功能外,变频器还具有多种保护功能,如过流保护、过压保护、欠压保护、过热保护等。
这些保护功能可以确保电机在出现异常情况时能够及时停机,避免设备损坏或事故发生。
变频器还可以通过与PLC等设备的通讯,实现远程监控和控制,提高设备的自动化程度和运行效率。
在传送带速度控制中,变频器发挥着至关重要的作用。
通过精确控制电机的转速,变频器可以实现传送带的平稳运行和多种速度切换。
变频器还可以与PLC等设备配合,实现对传送带速度的自动调整和监控,提高生产线的自动化程度和运行效率。
三、(可编程逻辑控制器)的基本原理与功能可编程逻辑控制器(PLC)是一种数字运算操作的电子系统,专为在工业环境下应用而设计。
基于PLC的传送带控制系统设计

基于PLC的传送带控制系统设计第一章:引言随着工业自动化程度的不断提高,传送带控制系统在现代工业中得到广泛应用。
传送带控制系统作为一个关键的部分,用于有效地管理和控制物体在生产过程中的运输和分拣。
本章将简要介绍传送带控制系统的作用和意义,并对文章的结构进行概述。
第二章:传送带控制系统的基本原理本章将介绍传送带控制系统的基本原理。
首先,将介绍传送带控制系统的组成部分,包括传送带、传动装置、传感器和PLC。
然后,将详细阐述传送带控制系统的工作原理,包括传送带的启停控制、速度控制和方向控制。
第三章:PLC在传送带控制系统中的应用本章将详细讨论PLC在传送带控制系统中的应用。
首先,将介绍PLC的基本原理和特点,包括可编程性、可扩展性和可靠性。
然后,将重点介绍PLC在传送带控制系统中的功能和应用,包括信号输入输出的处理、逻辑控制的实现和故障检测与处理。
第四章:传送带控制系统的设计与实现本章将详细介绍传送带控制系统的设计与实现过程。
首先,将介绍传送带控制系统的硬件设计,包括传送带的选择与布置、传动装置的选型和PLC的选取与配置。
然后,将重点讨论传送带控制系统的软件设计,包括PLC程序的编写、逻辑流程的设计和参数设置。
第五章:传送带控制系统的性能评估与优化本章将对传送带控制系统的性能进行评估与优化。
首先,将介绍性能评估的基本指标,包括传送效率、运行稳定性和故障率。
然后,将讨论性能优化的方法与策略,包括优化控制算法和改进硬件配置。
第六章:实验与结果分析本章将设计实验并分析实验结果,以验证传送带控制系统的性能与可靠性。
首先,将介绍实验的设计与搭建,包括实验样本的准备和实验环境的设置。
然后,将详细分析实验结果,并与设计要求进行对比和评价。
第七章:总结与展望本章将对文章进行总结,并展望传送带控制系统未来的发展趋势。
首先,将回顾本文的研究内容和成果。
然后,将对传送带控制系统在智能化、网络化和大数据时代的应用进行展望,并提出进一步的研究方向。
基于PLC的四级传送带控制系统的设计

基于PLC的四级传送带控制系统的设计PLC(可编程逻辑控制器)是一种用于控制工厂和机械设备的自动化技术。
传送带控制系统是PLC的一个重要应用领域。
本文将设计一个基于PLC的四级传送带控制系统,旨在提高生产效率和生产质量。
首先,需要明确传送带控制系统的工作流程。
在这个四级传送带控制系统中,原材料从一级传送带进入系统,经过分级加工后,最终成品从四级传送带输出。
每个传送带都有自己的控制要求,需要控制传送带的启动、停止、速度调节以及报警功能。
接下来,需要选择合适的PLC进行控制系统的设计。
需考虑系统的复杂性、性能要求和成本预算。
通常采用可编程逻辑控制器(PLC)作为控制系统的核心,因为它具有可靠性高、易于程序设计和调试的特点。
然后,设计PLC的输入输出模块。
根据传送带控制系统的要求,需要将传感器、按钮等硬件设备连接到PLC的输入模块上,以获取现场数据。
同时,还需要将伺服驱动器和报警设备连接到PLC的输出模块上,以实现对传送带的控制。
在PLC的程序设计方面,需要按照控制系统的工作流程编写相应的控制程序。
具体而言,在PLC的程序中,需要设置传送带的启动和停止条件,并通过调整传送带的速度来控制物料的流动。
此外,还需要编写报警功能,以便及时发现和处理异常情况。
在系统的运行调试过程中,需要使用PLC的编程软件对程序进行调试,模拟各种工况下的运行情况,并逐步优化程序的性能。
最后,进行系统的测试和验收。
将系统连接到实际的传送带设备上,并通过对系统的稳定性、可靠性以及性能的测试,验证系统是否满足设计要求。
在设计过程中,需要充分考虑安全性和可靠性。
对于传送带控制系统而言,应注意防止传送带的堵塞和异常物料的流进。
可以通过添加额外的传感器和采用冗余控制方式来提高系统的安全性。
总之,本文基于PLC的四级传送带控制系统设计是一个复杂而关键的工程,需要综合考虑硬件和软件的要求,以实现高效、稳定和可靠的传送带控制。
通过合理的设计和严格的测试验证,可以提高生产效率和生产质量,满足生产线的需求。
四节传送带PLC模拟控制系统

电机
驱动传送带运转的动力来源, 通常采用三相异步电机。
传送带
承载物料,通过连续运动将物 料从一个位置输送到另一个位 置。
控制系统
由PLC、继电器、接触器等组 成,用于控制电机启停、调节 传送带速度等。
工作原理
当物料放置在传送带上时,传感 器检测到物料的数量和位置信息。
PLC控制系统根据传感器反馈的 信息,控制电机的启停和转速,
进入20世纪后,随着自动化技术的不断发展,PLC等控制系 统的出现,传送带的发展也进入了新的阶段。四节传送带 PLC模拟控制系统就是其中的代表之一,它能够实现对传送 带的精确控制,提高了生产效率和产品质量。
02
四节传送带系统
系统构成
减速器
降低电机转速,增大扭矩,使 传送带能够平稳运行。
传感器
检测传送带上物料的数量、位 置等信息,为PLC控制系统提 供反馈。
特点
高可靠性、灵活性、易于编程和易于扩展等。
PLC的工作原理
输入采样
PLC读取输入端子的状态,并将 其存储在输入映像寄存器中。
程序执行
PLC按照从上到下的顺序扫描用户 程序,并根据输入映像寄存器中的 数据执行相应的逻辑运算或指令。
输出更新
在程序执行完成后,PLC将输出映 像寄存器中的数据写入到输出模块, 从而控制外部设备。
模拟控制系统的搭建
确定系统规模和要求
选择合适的PLC
根据实际需求,确定控制系统的规模和功 能要求,如控制节数、传送带速度、物料 检测等。
根据系统规模和要求,选择合适的PLC型号 和规格,确保其具有足够的输入输出点数 、处理速度和通讯能力。
配置输入输出模块
编写控制程序
根据实际控制需求,配置适当的输入输出 模块,如限位开关、传感器、电磁阀等。
基于PLC的传送带控制系统设计
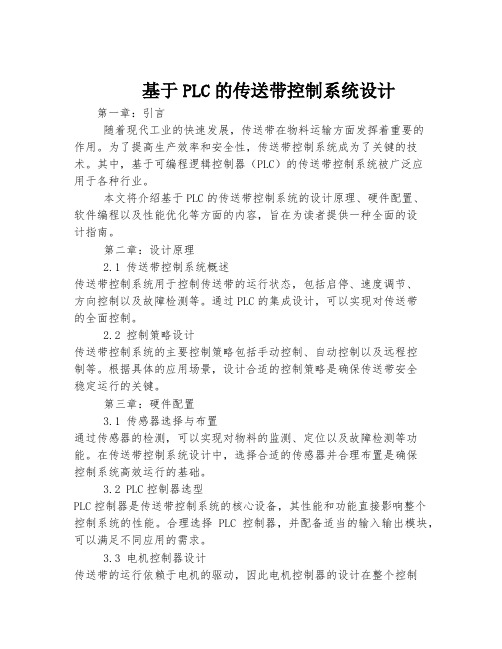
基于PLC的传送带控制系统设计第一章:引言随着现代工业的快速发展,传送带在物料运输方面发挥着重要的作用。
为了提高生产效率和安全性,传送带控制系统成为了关键的技术。
其中,基于可编程逻辑控制器(PLC)的传送带控制系统被广泛应用于各种行业。
本文将介绍基于PLC的传送带控制系统的设计原理、硬件配置、软件编程以及性能优化等方面的内容,旨在为读者提供一种全面的设计指南。
第二章:设计原理2.1 传送带控制系统概述传送带控制系统用于控制传送带的运行状态,包括启停、速度调节、方向控制以及故障检测等。
通过PLC的集成设计,可以实现对传送带的全面控制。
2.2 控制策略设计传送带控制系统的主要控制策略包括手动控制、自动控制以及远程控制等。
根据具体的应用场景,设计合适的控制策略是确保传送带安全稳定运行的关键。
第三章:硬件配置3.1 传感器选择与布置通过传感器的检测,可以实现对物料的监测、定位以及故障检测等功能。
在传送带控制系统设计中,选择合适的传感器并合理布置是确保控制系统高效运行的基础。
3.2 PLC控制器选型PLC控制器是传送带控制系统的核心设备,其性能和功能直接影响整个控制系统的性能。
合理选择PLC控制器,并配备适当的输入输出模块,可以满足不同应用的需求。
3.3 电机控制器设计传送带的运行依赖于电机的驱动,因此电机控制器的设计在整个控制系统中占据着重要的地位。
选择合适的电机控制器,并进行恰当的配置和编程,可以实现传送带的平稳运行。
第四章:软件编程4.1 PLC编程设计PLC编程是设计控制系统的关键环节,需要根据具体的控制策略,利用PLC编程软件进行程序设计。
本章将介绍PLC编程的基本原理和常用的编程语言,以及在传送带控制系统中的应用。
4.2 状态监测与故障检测传送带控制系统需要实现对传送带的状态监测和故障检测。
通过合理设置检测程序,并编写相应的故障处理程序,可以提高控制系统对异常情况的响应能力。
第五章:性能优化5.1 传送带速度控制传送带的速度控制是提高生产效率的关键,通过PLC编程和配置合适的速度传感器,可以实现对传送带速度的精确控制。
基于PLC的四级传送带控制系统的设计
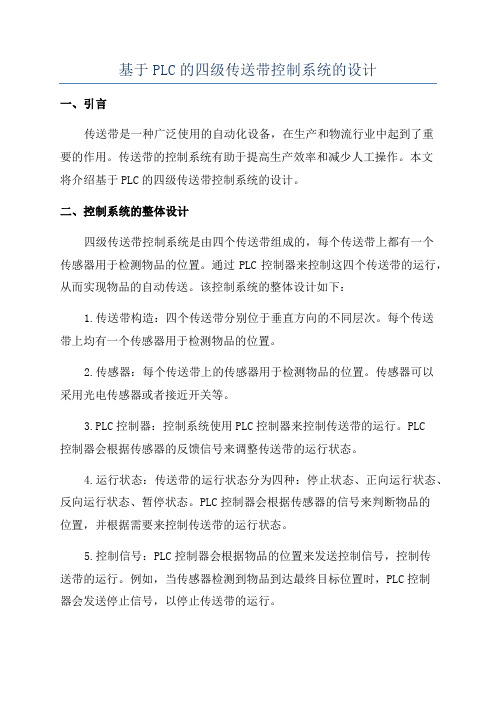
基于PLC的四级传送带控制系统的设计一、引言传送带是一种广泛使用的自动化设备,在生产和物流行业中起到了重要的作用。
传送带的控制系统有助于提高生产效率和减少人工操作。
本文将介绍基于PLC的四级传送带控制系统的设计。
二、控制系统的整体设计四级传送带控制系统是由四个传送带组成的,每个传送带上都有一个传感器用于检测物品的位置。
通过PLC控制器来控制这四个传送带的运行,从而实现物品的自动传送。
该控制系统的整体设计如下:1.传送带构造:四个传送带分别位于垂直方向的不同层次。
每个传送带上均有一个传感器用于检测物品的位置。
2.传感器:每个传送带上的传感器用于检测物品的位置。
传感器可以采用光电传感器或者接近开关等。
3.PLC控制器:控制系统使用PLC控制器来控制传送带的运行。
PLC控制器会根据传感器的反馈信号来调整传送带的运行状态。
4.运行状态:传送带的运行状态分为四种:停止状态、正向运行状态、反向运行状态、暂停状态。
PLC控制器会根据传感器的信号来判断物品的位置,并根据需要来控制传送带的运行状态。
5.控制信号:PLC控制器会根据物品的位置来发送控制信号,控制传送带的运行。
例如,当传感器检测到物品到达最终目标位置时,PLC控制器会发送停止信号,以停止传送带的运行。
6.人机界面:控制系统还可以加入一个人机界面,用于操作员监控和控制传送带的运行。
人机界面可以显示传送带的运行状态、物品位置等信息,并且允许操作员通过按键来控制传送带的运行。
三、PLC控制器的程序设计PLC控制器的程序设计是整个传送带控制系统的关键。
以下是PLC控制器的程序设计流程:1.初始化:在程序开始时,PLC控制器会对传送带、传感器和控制信号进行初始化设置。
2.检测信号:PLC控制器会不断地检测传感器的信号,判断物品的位置。
3.运行控制:根据传感器的信号,PLC控制器会判断当前物品的位置并发送相应的控制信号,控制传送带的运行状态。
4.反馈信号:当传感器检测到物品到达最终目标位置时,会发送反馈信号给PLC控制器,PLC控制器接收到反馈信号后,会停止传送带的运行。
PLC传送带电控系统

PLC传送带电控系统PLC因具有工作可靠性高、抗干扰能力强、使用维护方便等优点使它在目前的流水线自动控制系统中得到了广泛的应用,下面介绍一下包装车间电控系统中的PLC的应用。
控制流程:把生产的产品放在纸箱中,纸箱经过1#传送带送到自动封箱机处,将纸箱上、下箱口用胶带封好,有自动打包机打包后在电子秤上称量(自动打包机上有自带的光电传感器,用来检测是否有纸箱送来),再由人工贴上标签,送到2#传送带上,最后进入仓库。
仓库中有三条传送带分别将纸箱送到不同的区域。
在电子秤上需要人工计数及贴标签,有可能使纸箱在封箱机和打包机上积压,造成机器不能正常工作,为避免这种情况的发生,分别在1#传送带末端、封箱机和电子称上分别安装了传感器,以检测纸箱的位置,通过程序来控制1#传送带电机的启停以保证机器正常工作。
I/O地址分配清单:输入地址:X0 1#电机开关X1 1#传感器X2 2#传感器X3 3#传感器X4 4#传感器X5 5#传感器X6 6#传感器输出地址:Y1 1号电机Y2 2号电机Y3 3号电机Y4 4号电机M0、M1为内部继电器X11、X12、X13为计数器,计时5s自动断开梯形图:包装区的控制过程:将1#传送带的电机转换开关开启,即X0接通,PLC输出Y1,1号电机启动。
1.当1#传送带末端的传感器处没有纸箱时,X1是断开的,1号电机一直运转2. 当纸箱传送到自动封装机时,X2接通,PLC内部继电器M0吸合并自锁,这时当下一个纸箱送到X1处时,1号电机停止,等前一个纸箱从电子秤移到X2处时,1号电机才启动,(X3先接通,然后又断开),把纸箱送到自动封装机的位置。
3.电子秤上有纸箱时(X3接通),当下一个纸箱传送到X1,1号电机就会停止,等电子秤上的纸箱移走后,1号电机就会重新启动仓库中纸箱的传送过程:当纸箱到达包装区的电子秤时,X3接通,PLC输出Y1,2号电机启动。
称重完成后,将纸箱移到2#传送带上,当纸箱到达4#传感器时,X4接通,PLC输出Y3,相应的3号电机启动。
PLC传送带控制系统
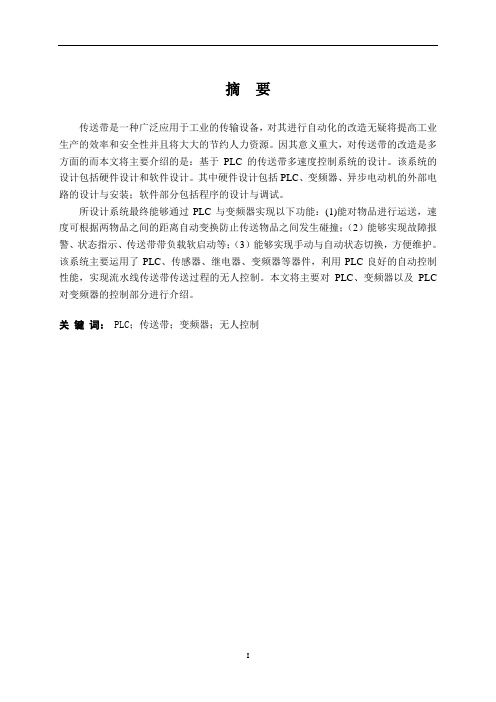
摘要传送带是一种广泛应用于工业的传输设备,对其进行自动化的改造无疑将提高工业生产的效率和安全性并且将大大的节约人力资源。
因其意义重大,对传送带的改造是多方面的而本文将主要介绍的是:基于PLC的传送带多速度控制系统的设计。
该系统的设计包括硬件设计和软件设计。
其中硬件设计包括PLC、变频器、异步电动机的外部电路的设计与安装;软件部分包括程序的设计与调试。
所设计系统最终能够通过PLC与变频器实现以下功能:(1)能对物品进行运送,速度可根据两物品之间的距离自动变换防止传送物品之间发生碰撞;(2)能够实现故障报警、状态指示、传送带带负载软启动等;(3)能够实现手动与自动状态切换,方便维护。
该系统主要运用了PLC、传感器、继电器、变频器等器件,利用PLC良好的自动控制性能,实现流水线传送带传送过程的无人控制。
本文将主要对PLC、变频器以及PLC 对变频器的控制部分进行介绍。
关键词:PLC;传送带;变频器;无人控制目录摘要 (I)1 设计目的及意义 (1)2 设计内容 (1)2.1 传送机的简介 (1)2.2 可编程逻辑控制器(PLC) (1)2.3 变频器 (1)3功能需求分析 (2)3.1系统功能 (2)3.2方案设计 (2)4具体设计 (3)4.1 PLC选型 (3)4.2电动机的选择 (4)4.3变频器的选择 (4)4.4 传感器 (4)4.5 系统梯形图程序 (4)结论 (9)参考文献 (10)1 设计目的及意义传统的传送带系统往往只能工作在某一固定的速度上,这种设计有着其他系统无法比拟的优点。
那就是系统及其简单,操作简便易于掌握使用且用途广泛。
其缺点也同样明显,当传送带上传送物品为易碎品或某些危险品时,若出口处有传送物品积压如果操作不当必然会造成损失甚至发生危险。
传统传送带虽然可以加入自动停止功能,但反复的启停势必对电动机产生不良影响并且会影响物品传输时的稳定性。
基于对单一速度传送带存在以上问题,一种多速度控制系统的概念被提出。
PLC的运输带控制系统[整理]
![PLC的运输带控制系统[整理]](https://img.taocdn.com/s3/m/cbc941b41eb91a37f0115c66.png)
体系常识汇编Compilation of system knowledge 20XX标题运送带操控体系名字:刘保坤班级:P14电气5班学号:2014031400042016 10.20目录摘要2Abstract3第一章导言41.1运送带在出产中的运用41.2 PLC操控及开展41.3操控体系人机界面效果及开展5第二章体系规划82.1体系的硬件规划82.1.1规划方案82.1.2操控电路规划92.1.3主电路规划92.2 体系软件规划102.2.1操控要求102.2.2操控功用的完结112.2.3手动/主动程序梯形图11第三章触摸屏画面组态12第四章体系调试与作业操作144.1调试进程144.2作业操作14结束语15参考文献16致谢17附录18摘要工业主动化是机器设设备或出产进程在不需求人工直接干涉的情况下,按预期的方针完结丈量、操作等信息处理和进程操控的总称。
主动化技能便是探究和研讨完结主动化进程的办法和技能。
它是触及机械、微电子、计算机等技能范畴的一门归纳性技能。
工业革命是主动化技能的助产士。
正是因为工业革命的需求,主动化技能才冲破了卵壳,得到了蓬勃开展。
一起主动化技能也促进了工业的前进,现在主动化技能现已被广泛的运用于机械制造、电力、修建、交通运送、信息技能等范畴,成为进步劳动出产率的首要手法。
结合当今社会办法,我规划了一种根据西门子PLC的触摸屏运送带操控体系。
本规划能满意简略的传送带操控,操作简洁,简略易懂,界面友爱。
能够完结手动启停,主动启停,并有报警体系。
要害词:主动操控、传送带、PLCAbstractIndustrial automation is a machine equipment or manufacturing process do not need artificial direct intervention in the case, according to the expected goals measurement, control, information processing and process control collectively. Automation technology is to explore and research process automation of the methods and technology. It is related to the mechanical, microelectronics and computer technology in the field of a comprehensive technology. The industrial revolution is the automation technology of the midwife. It is because of the needs of the industrial revolution, automation technology just broke through the egg shell, obtained the vigorous development. At the same time automation technology also promoted the progress of industry, now automation technology has been widely used in mechanical manufacturing, power, construction, transportation,information technology and other fields, and become the main means to improve labor productivity.On the social form, I design based on Siemens PLC touch screen with transportation control system. This design can satisfy simple conveyor belt control, simple operation, easy to understand and friendly interface. Can achieve manually rev. Stop, stop, and automatic and alarm system.Keywords: automatic control, the conveyor belt, PLC第一章导言1.1运送带在出产中的运用运送带运送是根据PLC的主动操控体系,它在水泥、煤炭、冶金、化工、饲料、食物等职业有很广泛的运用。
- 1、下载文档前请自行甄别文档内容的完整性,平台不提供额外的编辑、内容补充、找答案等附加服务。
- 2、"仅部分预览"的文档,不可在线预览部分如存在完整性等问题,可反馈申请退款(可完整预览的文档不适用该条件!)。
- 3、如文档侵犯您的权益,请联系客服反馈,我们会尽快为您处理(人工客服工作时间:9:00-18:30)。
计控学院College of computer and control engineeringQiqihar university电气工程课程设计报告题目:PLC传送带控制系统系别电气工程系专业班级学生学号指导教师提交日期成绩摘要传送带是一种广泛应用于工业的传输设备,对其进行自动化的改造无疑将提高工业生产的效率和安全性并且将大大的节约人力资源。
因其意义重大,对传送带的改造是多方面的而本文将主要介绍的是:基于PLC的传送带多速度控制系统的设计。
该系统的设计包括硬件设计和软件设计。
其中硬件设计包括PLC、变频器、异步电动机的外部电路的设计与安装;软件部分包括程序的设计与调试。
所设计系统最终能够通过PLC与变频器实现以下功能:(1)能对物品进行运送,速度可根据两物品之间的距离自动变换防止传送物品之间发生碰撞;(2)能够实现故障报警、状态指示、传送带带负载软启动等;(3)能够实现手动与自动状态切换,方便维护。
该系统主要运用了PLC、传感器、继电器、变频器等器件,利用PLC良好的自动控制性能,实现流水线传送带传送过程的无人控制。
本文将主要对PLC、变频器以及PLC对变频器的控制部分进行介绍。
关键词:PLC;传送带;变频器;无人控制目录摘要 (I)1 设计目的及意义 (1)2 设计容 (1)2.1 传送机的简介 (1)2.2 可编程逻辑控制器(PLC) (1)2.3 变频器 (2)3功能需求分析 (2)3.1系统功能 (2)3.2方案设计 (3)4具体设计 (4)4.1 PLC选型 (4)4.2电动机的选择 (4)4.3变频器的选择 (4)4.4 传感器 (5)4.5 系统梯形图程序 (5)结论 (11)参考文献 (12)1 设计目的及意义传统的传送带系统往往只能工作在某一固定的速度上,这种设计有着其他系统无法比拟的优点。
那就是系统及其简单,操作简便易于掌握使用且用途广泛。
其缺点也同样明显,当传送带上传送物品为易碎品或某些危险品时,若出口处有传送物品积压如果操作不当必然会造成损失甚至发生危险。
传统传送带虽然可以加入自动停止功能,但反复的启停势必对电动机产生不良影响并且会影响物品传输时的稳定性。
基于对单一速度传送带存在以上问题,一种多速度控制系统的概念被提出。
本文即阐述了基于PLC的传送带多速度控制系统的一种设计方案。
2 设计容2.1 传送机的简介17世纪中叶,美国人开始应用一种架空的索道来传送散状的物料,所谓的传送带自此诞生;进入19世纪中后期,经过了近两个世纪的发展,各种现代结构的传送带输送机相继出现。
1868年,在英国出现了皮带式传送带的输送机;1887年,在美国出现了螺旋式的输送机;20世纪后,1905年,在瑞士出现了钢带式输送机;1906年,在英国和德国出现了惯性输送机。
至此现代意义的传送带基本成型并且在此后传送带输送机受到机械制造、化工、电机、电子和冶金工业技术进步的影响,不断完善,逐步由完成车间部的传送,发展到完成在企业部、企业之间甚至城市之间的物料搬运。
时至今日传送带已然成为物料搬运系统机械化和自动化不可缺少的重要组成部分。
现代工业生产过程中,因传送带应用之广泛、工作之可靠相信在未来相当一段时间其地位无可动摇。
2.2 可编程逻辑控制器(PLC)PLC即可编程控制器,它是微机技术与继电接触器常规控制概念相结合的产物,即采用了微型计算机的基本结构和工作原理,融合了继电接触器控制的概念构成一种新型电控器,它专为在工业环境下应用而设计,它采用可编程的存储器,用来存储执行逻辑运算、顺序控制、定时、计数和算术运算等操作的指令,并采用数字式和模拟式的输入和输出,控制各种类型的机械和生产过程。
PLC具有各种优良的特点:通用性强;接线简单;编程容易;抗干扰能力强、可靠性高;容量大、体积小、重量轻、功耗少、成本低、维修方便。
2.3 变频器变频器可理解为能改变施加于交流电动机出线端上的电源频率值和电压值的调速设备。
它由电力电子器件、电子器件、微处理器(CPU)等组成。
它可分为交-交和交-直-交两种。
交-交变频器可将工频交流电直接变换成电压、频率可调的交流电。
所以交-交变频器又被叫做直接式变频器。
交-直-交变频器则是先把工频交流电通过整流器变成直流电,然后再把直流电变换成频率和电压均可控的交流电,又可称之为间接变频器。
在变频调速时,往往需要同时对逆变器的输出电压和频率进行调节,用以保障电动机主磁通维持恒定。
3功能需求分析3.1系统功能首先本系统必需能够进行正常的传送工作,如正运行、反向运行、启动与停止。
与此同时为改进传统传送带的不足系统要具有多速度切换功能。
即系统运行中检测前方出口处是否有物品积压情况,如果没有则系统保持正常速度运行。
如果前方出现积压情况,则系统开始测量距离出口最近的物品与出口的距离。
系统为防止物品间的碰撞会根据距离出口最近的物品与出口的距离进行减速或停止直到物品积压情况解除。
为保护电动机,传送带一般禁止带负载启动,所以设计时要加入软启动功能。
为防止系统工作中发生危险,整个系统要对工作状态进行指示同时对变频器的故障进行报警并紧急停止工作。
为保证系统在检修维护是仍能够维持工作,所以系统须具备手动工作与自动工作状态相互切换的功能。
3.2方案设计为完成上述功能,本设计将使用PLC为整个系统的核心控制部分。
以上几乎所有功能都由PLC进行控制。
利用PLC的开关量输入对系统开关、工作状态选择、传送带是否有积压进行控制、选择或反馈。
另外通过PLC的数字输出量对系统工作状态进行指示,最主要的是对变频器进行控制。
变频器通过对电动机的频率的调节来控制电动机的正反转和转速。
因为需要手动,所以需要两个变频器一个主变频器负责平时的自动调速,该变频器全部功能都由数字控制。
另一个变频器变速部分为模拟量控制,另正反转部分为开关量控制,负则检修时的手动控制, 整个系统的运作流程如图2-1所示。
图2-1 功能框图4具体设计本系统接工频电源主要分为PLC、变频器和电动机三大部分。
系统最终能够通过PLC 与变频器实现以下功能:(1)能对物品进行运送,速度可根据两物品之间的距离自动变换防止传送物品之间发生碰撞;(2)能够实现故障报警、状态指示、传送带带负载软启动等;(3)能够实现手动与自动状态切换,方便维护。
该系统主要运用了西门子PLC、传感器、继电器、变频器等器件,利用PLC良好的自动控制性能,实现流水线传送带传送过程的无人控制。
4.1 PLC选型系统PLC总共有开关量输入7个、开关量输出10个;模拟量输入1个。
参照实际应用的输入输出端口数量和PLC产品目录,选用主机为8入/6继电器输出的CPU222一台,加上一台扩展模块EM222(8点继电器输出),在扩展一个模拟量模块EM235(4AI/1AO)。
4.2电动机的选择考虑到系统的通用性问题,本系统并不注重电动机的选择。
具体的应用不同,电动机可根据需要进行选择。
为方便下文的论述,本系统采用西门子1LG0106-2AA20 电动机。
该电动机的容量为3KW、额定电压220/380V,电源频率50H,允许电压偏差±5%。
4.3变频器的选择在变频器的选择时,应该充分考虑到所使用的场合的使用工况条件的最恶劣情况,留有充足的设计裕度和必要的保护措施。
在选型时应对经济指标和技术指标进行综合的考虑,以选择相应的变频器规格。
若选型不当造成容量偏小,对变频器的效率和正常运行影响极大。
4.4 传感器限位开关又可成为称行程开关,它可以安装在相对静止的物体(如固定架、门框等,简称静物)上或者运动的物体(如行车、门等,简称动物)上。
当动物接近或接触静物时,开关的连杆驱动开关闭合的触点分断或者断开的触闭合。
由开关触点开、合状态的改变去反馈信息。
4.5 系统梯形图程序为明确PLC各个接口的功能同时方便编程下文中给出PLC的I/O分配。
输入接口输出接口I0.0 自动控制Q0.0 KM0I0.1 手动控制Q0.1 运行灯I0.2 故障监控Q0.2 故障灯I0.3 反转Q0.3 KM1I0.4 启动Q0.4待机速度I0.5 压力传感器Q0.5 减一档I0.6 正转Q1.0减二档I0.7 暂停Q1.1 正速Q1.2停车Q1.3反转明确了PLC输入输出分配后便可以据此编辑程序。
如图4-1所示,I0.2为常闭触点平时为闭合状态,开关SA选择手动控制状态时I0.1闭合,与此同时自动控制状态断开线圈Q0.3、Q0.1得电,运行灯亮起并且线圈KM1得电,开关Q0.3闭合,此时手动控制状态同路自锁直到开关SA选择自动控制状态。
当开关SA选择自动控制状态时,触点I0.0闭合,此时手动控制通路由于有I0.0常闭触点而断开。
此时Q0.0实现自锁同时开始调用子程序SBR-0。
当变频器传送回故障信号时,即I0.2闭合,此时PLC控制Q0.2输出,故障提示灯亮。
图4-1 梯形图主程序图图4-2 梯形图子程序1AIW0是模拟量输入输出模块EM235将采集的模拟量变换成数字量后的值。
其围在0~32000之间。
因为测距传感的反馈信号为4~20mA所以本程序中AIW0的值在6400~3200之间。
本文不对传送带上距离进行细致论述,因此设当AIW0的值大于等于25000时即相当于传送带上无负载。
另设AIW0值为19200、12800、6500分别为第一安全距离、第二安全距离、第三安全距离。
如图4-2所示,此时按下启动键I0.4。
当AIW0的值大于32000时开关闭合,部继电器M0.0得电,断开常闭触点M0.0。
系统进入待机低速运行状态。
当按下停止按钮I1.1接通,系统暂停。
图4-3 梯形图子程序2如图4-3所示,当AWI0值不再大于等于32000时说明传送带上有负载。
此时,继电器M0.0失电系统软启动。
T33路接通后,定时器T33开始计时。
在计时结束之前电动机以待机速度运行。
T33计时结束同时T34开始计时此时变频器输出频率为10Hz。
T34计时结束同时T35开始计时,此时变频器输出频率为25Hz。
图4-4 梯形图子程序3如图4-4所示,T35计时结束同时T36开始计时此后变频器输出为50Hz。
当压力开关闭合时系统会开始计算物位,常闭触点Q0.5、Q1.2、Q1.0实际是与下图中的各种状态互锁。
即Q0.5、Q1.2、Q1.0中有任意一中输出Q1.1都不可能输出。
图4-5 梯形图子程序4如图4-5,I0.5为一压力开关,即有物品在前方积压时I0.5闭合。
前文已经介绍AIW0值为19200、12800、6500分别为第一安全距离、第二安全距离、第三安全距离。
当I0.5闭合且AIW0值小于等于19200时,说明物品已进入第一安全距离,此时Q0.5输出。
同样当AIW0值小于等于12800时Q1.0输出。