第二章 冲模设计基础
冲压模具设计与制造

第一章 冲压模具设计与制造基础
内容简介:
本章讲述冲压模具设计与制造的基础知识。 涉及冲压和冲模概念、冲压工序和冲模分类;常见冲压设备及工作原理、选用原则;冲压成形基本原理和规律;冲压成形性能及常见冲压材料;模具材料种类、性能、选用原则及热处理方法;模具制造特点、模具零件加工方法及应用等 。
第一章 冲压模具设计与制造基础
一、冲压与冲模概念
1.基本概念(续)
冲压模具:
在冲压加工中,将材料加工成零件(或半成品)的一种特殊工艺装备,称为冲压模具(俗称冲模)。
第一章 冲压模具设计与制造基础
第一节 冲压成形与模具技术概述 冲压与冲模概念 基本概念(续) 合理的冲压工艺 先进的模具 高效的冲压设备 冲压生产的三要素
第一章 冲压模具设计与制造基础
多工位精密级进模
第一章 冲压模具设计与制造基础
冲压成形产品示例一——日常用品
第一章 冲压模具设计与制造基础
冲压成形产品示例二—— 高科技产品 汽车覆盖件 飞机蒙皮
第一章 冲压模具设计与制造基础
数控高速铣削加工
高效 、高精度 、高的表面质量 、可加工高硬材料
第一章 冲压模具设计与制造基础
五、冲压技术现状与发展方向(续)
第一节 冲压成形与模具技术概述
多品种、少批量,更新换代速度快
计算机技术、制造新技术
第一章 冲压模具设计与制造基础
(1)冲压成形理论及冲压工艺
加强理论研究,开展CAE技术应用。 开发和应用冲压新工艺。
2.冲压技术发展方向
满足产品开发在T(Time)、Q(Quality)、 C(Cost)、S(Service)、E(Environment)的要求。
1.我国冲压技术现状 技术落后、经济效益低。 主要原因:①冲压基础理论与成形工艺落后; ②模具标准化程度低; ③模具设计方法和手段、模具制造工艺及设备落后; ④模具专业化水平低。 所以,结果导致我国模具在寿命、效率、加工精度、生产周期等方面与先进工业发达国家的模具相比差距相当大。
冲压模具设计与制造基础

电子通讯业
手机、电脑等产品的金属板 材零部件需要进行冲压加工
,需要相应的冲压模具。
其他行业
建筑、包装、家具等众 多行业都需要用到冲压
模具进行板材加工。
冲压模具的设计与制造流程
01
02
03
设计阶段
根据产品要求和工艺条件, 进行模具结构设计、零件 设计、工艺计算等。
制造阶段
根据设计图纸进行备料、 加工、装配、调试等,完 成模具的制造。
分类
按照不同的分类标准,冲压模具可以分为多种类型。例如, 按照工艺用途可以分为冲孔模、落料模、弯曲模、拉深模等 ;按照模具结构可以分为单工序模、复合模和级进模等。
冲压模具的应用领域
汽车制造业
汽车车身覆盖件、零部 件的冲压加工需要大量
冲压模具。
家用电器业
各种金属和非金属板材 零件的冲压加工需要冲
压模具。
润滑保养
定期对模具进行润滑保养,保证各运 动部件的顺畅,防止磨损和卡滞。
清洁保养
定期对模具进行清洁保养,去除污垢 和杂物,保持模具的清洁和良好的外 观。
防锈保养
对于易生锈的部位,应采取防锈措施, 如涂抹防锈油等,以防止模具生锈。
冲压模具常见故障及排除方法
凸模断裂
可能是由于凸模强度不足或冲压材料太硬, 应检查凸模设计是否合理,选用更合适的 材料或对凸模进行热处理。
智能化自动化的冲压生产线
智能化技术应用
随着人工智能和物联网技术的发展,智能化技术在冲压行业的应用越来越广泛。 通过引入智能化技术,实现冲压生产线的自动化控制和智能化管理,提高生产线 的效率和灵活性。
自动化生产系统
自动化生产系统是实现高效生产的必要手段。通过自动化系统,实现冲压过程的 自动化控制、自动化检测和自动化调整,减少人工干预和操作误差,提高生产效 率和产品质量。
1-2冲压模具设计与制造基础
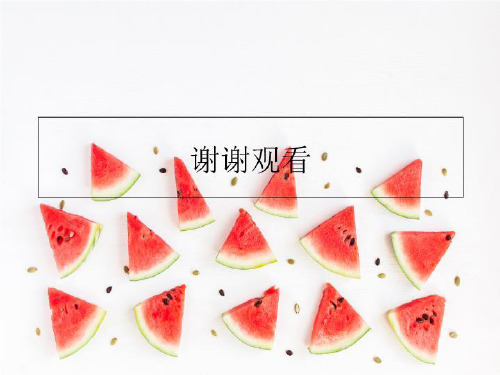
模具制造主要有三项工作: (1)模具工作零件的制造 (2)配购通用、标准件及 进行补充加工 (3)进行模具装配和试模
其中,模具工作零件的制 造和模具装配是重点。
二类工具:模具加工、装 配中需要的专用工具,如 非标准铰刀、量规,靠模, 检验样板。。。
MD&M 第一章 冲压工艺及模具设计与制造基础
MD&M 第一章 冲压工艺及模具设计与制造基础
MD&M 第一章 冲压工艺及模具设计与制造基础
MD&M 第一章 冲压工艺及模具设计与制造基础
MD&M 第一章 冲压工艺及模具设计与制造基础
MD&M 第一章 冲压工艺及模具设计与制造基础
MD&M 第一章 冲压工艺及模具设计与制造基础
MD&M 第一章 冲压工艺及模具设计与制造基础
MD&M 第一章 冲压工艺及模具设计与制造基础
曲轴压力机传动系统 1-电机 2-皮带轮 3、4-齿轮 5-离合器 6-连杆 7-滑块
MD&M 第一章 冲压工艺及模具设计与制造基础
油 压 机
MD&M 第一章 冲压工艺及模具设计与制造基础
工作原理与特点
类 设备名
型
称
机
摩擦压
械
力机
压
力
机
曲柄压 力机
冲模制造
MD&M 第一章 冲压工艺及模具设计与制造基础
2.冲压模具设计与制造的内容
冲压工艺设计、模具设计与模具制造。
冲压工艺设计——冲模设计的基础和依据。 冲模设计——实现冲压工艺。 冲模制造则是模具设计过程的延续,目的是使设计图样,通 过原材料的加工和装配,转变为具有使用功能和使用价值的 模具实体。
冲压模具设计基础知识

3.5.5.1 UI SHIELDING產品
3.5.5.2 UI SHIELDING產品
3.5.6.1 SIM LID產品
3.5.6.2 SIM LID產品
3.6 沖壓模具設計技術要因圖
沖模設計技術
產品展開 產品工藝分析
材料塑性成型
工程排配 沖裁技術 復合模結構設計
模具設計標準化
沖裁模結構設計
及余
工序分析
模具結構
3.3.9 彎曲工序(壓彎)
一將 定平 形的 狀坯 的件 零壓 件成
壓彎
工序分析
模具結構
3.3.10 彎曲工序(卷圓)
壓將 彎坯 成件 一的 定邊 形根 狀據 的一 圓定 弧半 形徑
卷圓
工序分析
模具結構
3.3.11 彎曲工序(扭彎)
相將 對平 轉坯 一件 個的 角一 度部 變份 成與 曲另 線一 零部 件份
反拉深
模具結構
3.3.15 拉深工序(變薄拉深)
而 改 變 空 心 坯 件 尺 寸
將 坯 件 減 小 直 徑 和 壁 厚
變薄拉深
工序分析
模具結構
3.4 沖模設計手順
3.4.1 客戶成品圖確認 A.成品用途,機能 B.重點要求 C.使用方法,組合零件之關系 D.加工方式,前後處理情形 E.檢驗方式,尺寸公差確認,基準點面判定 F.有無Sample G.材料使用確認,購買情況,壓延方向分析 H.沖壓設備之可行性
1.5 沖壓模具在集團的作用與發展
★ 沖壓模具是在工業中實現大量生產的工具; ★ 沖壓模具是集團創業之源,生存之本; ★ 沖壓模具是集團核心技術之一。
二 沖壓模具開發流程簡介
2.1 沖壓模具開發流程簡介
冲压模具设计知识点
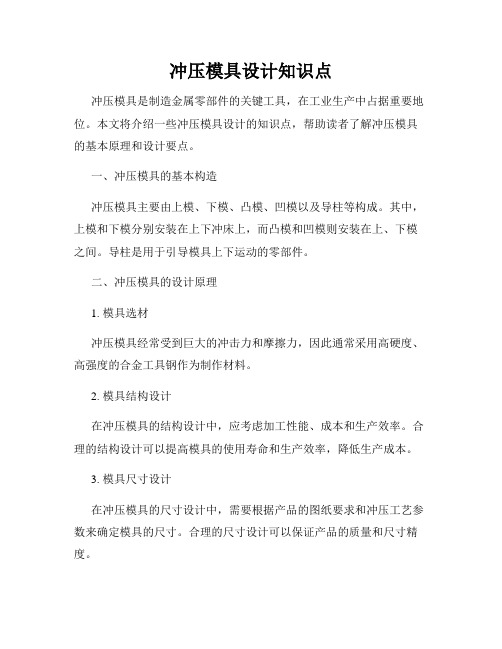
冲压模具设计知识点冲压模具是制造金属零部件的关键工具,在工业生产中占据重要地位。
本文将介绍一些冲压模具设计的知识点,帮助读者了解冲压模具的基本原理和设计要点。
一、冲压模具的基本构造冲压模具主要由上模、下模、凸模、凹模以及导柱等构成。
其中,上模和下模分别安装在上下冲床上,而凸模和凹模则安装在上、下模之间。
导柱是用于引导模具上下运动的零部件。
二、冲压模具的设计原理1. 模具选材冲压模具经常受到巨大的冲击力和摩擦力,因此通常采用高硬度、高强度的合金工具钢作为制作材料。
2. 模具结构设计在冲压模具的结构设计中,应考虑加工性能、成本和生产效率。
合理的结构设计可以提高模具的使用寿命和生产效率,降低生产成本。
3. 模具尺寸设计在冲压模具的尺寸设计中,需要根据产品的图纸要求和冲压工艺参数来确定模具的尺寸。
合理的尺寸设计可以保证产品的质量和尺寸精度。
4. 冲压工艺参数设计冲压模具设计中的重要一环是冲压工艺参数的设计。
包括冲程、压力、冲头直径、冲孔深度等参数的选取,这些参数决定了冲压过程中的力的大小和应变情况。
5. 模具热处理为了提高模具的硬度和耐磨性,冲压模具在制造完成后需进行热处理。
常用的热处理方法有淬火、回火和表面渗碳等,以达到模具的优化性能。
三、冲压模具设计要点1. 合理设计模具结构和尺寸,根据产品要求和冲压工艺参数来确定模具的尺寸和形状。
2. 注意模具的材料选用,选择合适的合金工具钢以提高模具的硬度和耐磨性。
3. 加工模具时,应保证模具的精度和表面质量,避免因加工不当而影响到冲压成型。
4. 冲压过程中,要注意模具的使用和维护,定期检查模具的磨损情况,及时修复或更换。
5. 做好冲压工艺参数的选取和控制,确保冲压过程的稳定和产品质量的一致性。
四、冲压模具设计的应用领域冲压模具广泛应用于汽车、家电、电子、航空航天等领域,是这些行业中零部件制造的主要工具。
同时,随着科技的发展,冲压模具的应用也在不断扩大,已涉及到了医疗、能源等更多领域。
模具第二章冲裁模

为了防止冲裁时凸模折断或压弯,冲孔的尺寸不能太小, 有关要求见下表 (一)
一般冲孔模可冲压的最小孔径值
(mm)
材料
钢г>700MPa 钢г=400~700MPa 钢г<400MPa 黄铜、铜 铝、锌 纸胶板、布胶板 硬纸、纸
d≥1.5t d≥1.3t
d≥t d≥0.9t d≥0.8t d≥0.7t d≥0.6t
凹
0
d x Z min
凹 0
式中:d凸、d凹——冲孔凸、凹模基本尺寸(mm); △——工件制造公差(mm); X——因数,见表2-13
冲孔时各部分尺寸公差的分配 位置如右图a)
(2)落料 设工件尺寸为D-△。
根据刃口尺寸计算原则,落料 时应首先确定凹模刃口尺寸。 由于基准件凹模的刃口尺寸在 磨损后会增大,因此应使凹模 的基本尺寸接近工件轮廓的最 小极限尺寸,再减小凸模尺寸 以保证最小合理间隙值Zmin。仍 然是凸模取负偏差,凹模取正偏 差。落料时各部分尺寸公差的 分配位置如右图b)
表2-3 冲裁件内外形所能达到的经济精度
基本尺寸/mm
材料厚度t/mm
≤3 1~2 2~3 3~5
≤3
3~6
6~10 10~18 18~500
IT12~IT13
IT14
IT12~IT13
IT14
--
IT14
IT11 IT11
IT12~IT13 IT12~IT13
表2-4 两孔中心距离公差
一般精度(模具)
1、尺寸计算原则(在决定模具刃口尺寸及制造公差时): 1)落料件的尺寸取决于凹件尺寸,冲孔件的尺寸取决于凸模
尺寸。因此,设计落料模时,以凹模为基准,间隙取在凸模上。 设计冲孔模时,以凸模为基准,间隙取在凹模上。
冲压模具设计教程

冲压模具设计教程引言冲压模具是工业生产中常用的工具,用于将金属材料加工成所需形状的零件。
冲压模具的设计是冲压工艺中至关重要的一步,本文将介绍冲压模具设计的基本原理和步骤。
1. 冲压模具的分类冲压模具根据其用途和结构可以分为以下几类:•单工位冲模:适用于简单的冲压工艺,一次只能完成一道工序。
•进给式冲模:通过进给机构实现连续成形的模具,适用于大批量生产。
•复合式冲模:结合多个单工位冲模的模具,能够完成复杂形状的零件成形。
•特殊冲模:适用于特殊需求的冲压工艺,如切断、翻弯、拉伸等。
2. 冲压模具的设计过程冲压模具设计包括以下几个主要步骤:2.1. 零件分析在进行冲压模具设计之前,首先要对待加工的零件进行分析。
了解零件的形状、尺寸、材料以及工艺要求,确定零件的加工工艺和模具设计方案。
2.2. 模具结构设计根据零件的形状和工艺要求,设计模具的整体结构。
包括上模、下模、导向机构、顶出机构等组成部分,保证模具在使用过程中的稳定性和精度。
2.3. 零件分解根据零件的形状和复杂程度,将其分解成若干较简单的形状,确定每个分解零件的加工工艺和尺寸。
2.4. 模具零件设计对模具的每个零件进行详细设计,包括上模、下模、导向机构、顶出机构等。
要考虑零件的加工工艺、材料选择、尺寸精度要求等因素。
2.5. 模具装配根据模具的设计图纸,将各个零件进行装配,保证模具的完整性和稳定性。
2.6. 模具加工和调试根据模具的设计图纸,进行模具的加工制造。
在完成后,进行模具的调试,保证模具在使用时的稳定性和加工精度。
3. 冲压模具设计的注意事项在进行冲压模具设计时,需要注意以下几个方面:•合理选择模具材料,根据零件的材料和加工工艺要求,选择适合的模具材料,保证模具的寿命和加工质量。
•保证模具的刚性和稳定性,避免因振动或变形导致加工质量下降。
•合理设置模具的导向和顶出机构,确保零件的形状和尺寸精度。
•在设计模具时,考虑模具的拆卸和维修便捷性,方便模具的维护和保养。
模具设计与制造基础
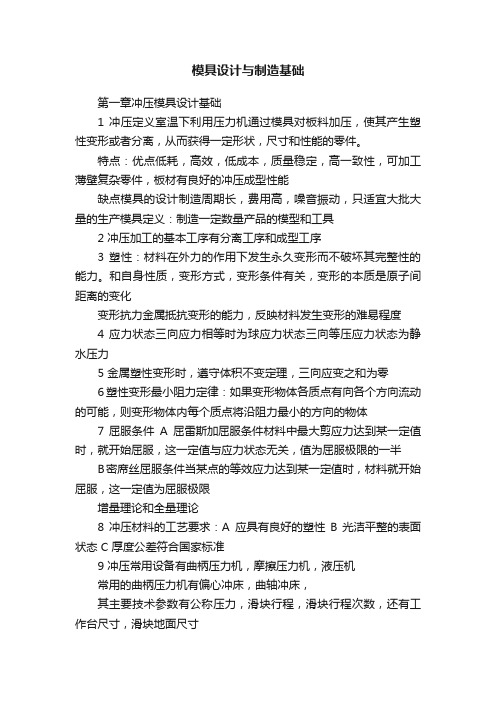
模具设计与制造基础第一章冲压模具设计基础1 冲压定义室温下利用压力机通过模具对板料加压,使其产生塑性变形或者分离,从而获得一定形状,尺寸和性能的零件。
特点:优点低耗,高效,低成本,质量稳定,高一致性,可加工薄壁复杂零件,板材有良好的冲压成型性能缺点模具的设计制造周期长,费用高,噪音振动,只适宜大批大量的生产模具定义:制造一定数量产品的模型和工具2 冲压加工的基本工序有分离工序和成型工序3 塑性:材料在外力的作用下发生永久变形而不破坏其完整性的能力。
和自身性质,变形方式,变形条件有关,变形的本质是原子间距离的变化变形抗力金属抵抗变形的能力,反映材料发生变形的难易程度4 应力状态三向应力相等时为球应力状态三向等压应力状态为静水压力5 金属塑性变形时,遵守体积不变定理,三向应变之和为零6塑性变形最小阻力定律:如果变形物体各质点有向各个方向流动的可能,则变形物体内每个质点将沿阻力最小的方向的物体7 屈服条件A屈雷斯加屈服条件材料中最大剪应力达到某一定值时,就开始屈服,这一定值与应力状态无关,值为屈服极限的一半B密席丝屈服条件当某点的等效应力达到某一定值时,材料就开始屈服,这一定值为屈服极限增量理论和全量理论8 冲压材料的工艺要求:A应具有良好的塑性B 光洁平整的表面状态 C 厚度公差符合国家标准9 冲压常用设备有曲柄压力机,摩擦压力机,液压机常用的曲柄压力机有偏心冲床,曲轴冲床,其主要技术参数有公称压力,滑块行程,滑块行程次数,还有工作台尺寸,滑块地面尺寸10冲模材料的选用原则A根据模具种类及工作条件B根据冲压材料和冲压件的生产批量C满足加工要求D满足经济性要求11模具制造特点形状复杂,精度要求高;加工难度大12冲压三要素:合理的冲压工艺;先进的模具;高效的冲压设备第二章冲裁工艺及冲裁模的设计1冲裁是利用冲裁模是板料产生分离的冲压工艺,包括落料,冲孔,切口,切边,剖切等工序落料从板料上冲下所需形状的零件冲孔在工件上冲出所需形状的孔2 冲裁变形的过程,可分为三个阶段弹性变形阶段塑性变形阶段断裂分离阶段3 冲裁件的断面特征在断面上可分为圆角带,光亮带,断裂带,毛刺四个部分A断裂带是由刃口处的微裂纹在拉应力的作用下不断扩展而形成的撕裂面,是冲裁件断面粗糙,有斜度B毛刺是因为微裂纹产生的位置不是正对刃口,而是在刃口附近的侧面上,加上凸凹模之间的间隙以及刃口不锋利等原因,是金属拉断形成毛刺儿残留在冲裁件上。
冲压模具及冲模设计

冲压模具及冲模设计引言冲压模具是冲压工艺中不可缺少的工具,通过将金属板材置于模具之间施加压力从而将其裁剪成所需形状。
冲模设计则是为了确保冲压过程能够顺利进行而进行的重要步骤。
本文将深入介绍冲压模具及冲模设计的相关内容。
一、冲压模具的分类根据冲压工艺的不同需求,冲压模具可分为以下几类:1.单工位模具:每工位完成一道工序,适用于简单形状的冲压件。
2.进料式模具:通过进料装置将金属板材连续送入模具进行冲压,适用于大批量生产。
3.连续式模具:在连续进行冲压的同时,实现多道工序的一体化,提高生产效率。
4.多工位模具:在一个模具上设置多个工位,适用于复杂形状的冲压件。
二、冲压模具的设计原则在进行冲模设计时,需要遵循以下几个原则:1.合理布局:模具的各个部分要合理分布,便于材料的进料、定位和排渣。
2.简化结构:尽量减少模具的零件数量和工艺复杂度,提高制作和维修的便利性。
3.提高刚度:通过加强模具的结构,提高其刚度和稳定性,以提高冲压精度和延长使用寿命。
4.正确选择材料:根据冲压件的材质和数量,选择合适的模具材料,以确保其耐磨性和抗拉强度。
三、冲模设计的步骤进行冲模设计时,需要按照以下步骤进行:1.冲压件分析:对冲压件进行分析,包括形状、尺寸、材质等方面的特点。
2.模具结构设计:根据冲压件的特点,设计模具的整体结构,包括上模、下模、导向机构等部分。
3.模具零部件设计:对模具的各个零部件进行设计,包括定位销、排渣孔、导向柱等。
4.模具加工制造:根据设计图纸,进行模具的加工制造,包括车削、铣削、磨削等工序。
5.模具调试和试模:对制造好的模具进行调试和试模,确保其能够正常运行。
6.模具维护和维修:及时进行模具的维护和维修,以延长其使用寿命和保证冲压质量。
四、冲压模具的常见问题及解决方法在冲压模具的使用过程中,可能会遇到以下常见问题:1.模具磨损:由于长时间使用和摩擦,模具表面可能会磨损,影响冲压质量。
解决方法包括定期维护和更换磨损部件。
冲压模具设计与制造基础
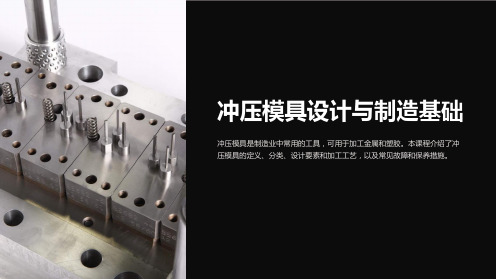
手动模具、机械模具、液动模具、液压模具
冲压模具的工作原理和流程
冲压模具通过压力使原材料变形,实现成形、剪切、冲切、弯曲等工艺。工作流程包括送料、定位、定 位销、冲裁、出料和排废。
冲压模具设计的基本要素
1 产品设计
产品尺寸、几何形状和表面特征
2 工艺需求
成形工艺、材料特性和加工要求
3 模具结构
模板、凹模、顶模、导向机构和固定装置
冲压模具设计流程及预算
1
需求分析
了解产品需求和技术要求
方案设计
2
制定模具结构、加工路线和设备选择
3
详细设计
绘制各部件图纸和制定工艺文件
制造加工
4
按图纸和工艺文件进行制造与加工
5
试模调试
测试模具性能和模具与设备配合情况
冲压模具材料的选择与应用
金属模具
常用材料有工具钢、硬质合金和粉末冶金材料。
塑胶模具
常用材料有热流道模具、冷流道模具和热流道冷 却模具。
冲压模具加工工艺及步骤
1
材料准备
选材、切割和热处理
加工制造
2
车削、铣削、割线、装配等
3
表面处理
研磨、抛光、电镀等
检验和保养
4
检测模具尺寸和性能,定期保养模具
冲压模具检验方法和装配要求
尺寸检验
卡尺、千分尺、高度规等工具检查模具尺寸
性能检验
冲压模具设计与制造基础
冲压模具是制造业中常用的工具,可用于加工金属和塑胶。本课程介绍了冲 压模具的定义、分类、设计要素和加工艺,以及常见故障和保养措施。
冲压模具的分类及常见形式
按结构分类
单工位模具、连续工位模具、复合工位模具
冲模DFM范本
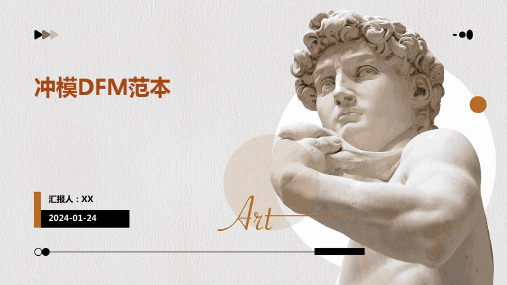
01
02
03
THANKS
感谢您的观看。
避免过深的拉深深度;采用压边圈防止起皱;考虑拉深过程中的摩擦和润滑。
拉深件的结构工艺性
根据材料的力学性能、拉深件的形状和尺寸等因素,确定合理的拉深系数和拉深次数。
拉深系数与拉深次数
考虑拉深过程中的变形抗力、摩擦力和压边力等因素,计算拉深所需的力。
拉深力的计算
根据拉深件的形状和精度要求,选择合适的拉深模结构形式,并进行必要的强度校核。
装配与调试
检查装配和调试的便利性,包括零件的配合精度、定位方式等。
CAD软件
利用CAD软件进行冲模的三维建模和模拟分析,优化设计方案。
CAM软件
应用CAM软件生成加工代码,指导数控机床进行精确加工。
CAE软件
采用CAE软件进行有限元分析,预测冲模的应力分布和变形情况。
DFM分软件
利用DFM分析软件对冲模设计方案进行可制造性分析,提出改进建议。
拉深模设计
成形件的结构工艺性
01
避免复杂的形状;采用合理的圆角过渡;考虑成形过程中的回弹和收缩。
成形力的计算
02
根据成形件的形状、尺寸和材料力学性能等因素,计算成形所需的力。
成形模设计
03
根据成形件的形状和精度要求,选择合适的成形模结构形式,并进行必要的强度校核。同时,还需考虑成形过程中的摩擦、润滑和冷却等因素对模具的影响。
模具调试
试冲前的准备
准备好试冲材料、润滑油和测量工具等,检查冲床和模具的安装情况,确保试冲条件符合要求。
试冲结果分析
根据试冲结果,分析模具的间隙、刃口磨损和定位精度等因素对冲裁件质量的影响,提出改进措施。
试冲过程
将试冲材料放入模具中,启动冲床进行试冲,观察冲裁件的断面质量、毛刺大小和尺寸精度等指标,记录试冲结果。
冲压模具基础习题与解答

第2章冲压变形基础(答案)一、填空1.在室温下,利用安装在压力机上的模具对被冲材料施加一定的压力,使之产生分离和塑性变形,从而获得所需要形状和尺寸的零件(也称制件)的一种加工方法。
2.用于实现冷冲压工艺的一种工艺装备称为冲压模具。
3.冲压工艺分为两大类,一类叫分离工序,一类是变形工序。
4.物体在外力作用下会产生变形,若外力去除以后,物体并不能完全恢复自己的原有形状和尺寸,称为塑性变形.5.变形温度对金属的塑性有重大影响。
就大多数金属而言,其总的趋势是:随着温度的升高,塑性增加,变形抗力降低。
6.以主应力表示点的应力状态称为主应力状态,表示主应力个数及其符号的简图称为主应力图。
可能出现的主应力图共有九种。
7.塑性变形时的体积不变定律用公式来表示为:ε1+ε2+ε3=0。
8.加工硬化是指一般常用的金属材料,随着塑性变形程度的增加,其强度、硬度和变形抗力逐渐增加,而塑性和韧性逐渐降低。
9.在实际冲压时,分离或成形后的冲压件的形状和尺寸与模具工作部分形状和尺寸不尽相同,就是因卸载规律引起的弹性回复(简称回弹)造成的。
10. 材料对各种冲压成形方法的适应能力称为材料的冲压成形性能。
冲压成形性能是一个综合性的概念,它涉及的因素很多,但就其主要内容来看,有两个方面:一是成形极限,二是成形质量。
二、判断(正确的在括号内打√,错误的打×)1.(× )主应变状态一共有9种可能的形式。
2.(×)材料的成形质量好,其成形性能一定好。
3.(√)热处理退火可以消除加工硬化(冷作硬化)。
4.(√)屈强比越小,则金属的成形性能越好。
5.(×)拉深属于分离工序。
三、选择1.主应力状态中, A ,则金属的塑性越好。
A.压应力的成份越多,数值越大 B. 拉应力的成份越多,数值越大。
2.当坯料三向受拉,且σ1>σ2>σ3>0时,在最大拉应力σ1方向上的变形一定是 A ,在最小拉应力σ3方向上的变形一定是 BA.伸长变形 B。
第二章冲裁工艺与冲裁模
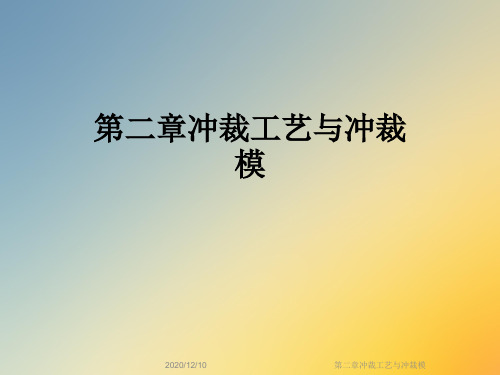
凸模:
凹模:
式中: d—冲孔工件孔的基本尺寸,mm dp、dd—冲孔凸、凹模刃口尺寸,mm Δ—工件公差,mm —凸、凹模制造偏差(查表),mm X—磨损系数(查表)
第二章冲裁工艺与冲裁模
第二章冲裁工艺与冲裁模
②落料 设冲裁件的落料尺寸为
计算原则,计算公式为:
凹模:
,根据刃口尺寸
如不满足,则应提高模具制造精度,即减小 、 ⑤优点
凸、凹模具有互换性,制造周期短,便于批量生产。 ⑥缺点:模具制造公差小,模具制造困难,成本高。
第二章冲裁工艺与冲裁模
刃口尺寸计算注意点:
1.分清是冲孔还是落料 2.冲裁间隙Z的确定:与材料和料厚有关 3.冲裁件的尺寸标注是否标准
孔的标注: 落料的标注: 中心距标注:L
基准件刃口尺寸计算式:
A类尺寸:
B类尺寸:
C类尺寸:
C = C ±D ' 4 = C ±D 8
第二章冲裁工艺与冲裁模
A类尺寸:
B类尺寸:
C类尺寸: C = C ±D ' 4 = C ±D 8
式中: A、B、C—基准件基本尺寸, mm Amax—冲裁件A类尺寸最大极限值, mm B min—冲裁件B类尺寸最小极限值, mm δ—模具制造公差, mm
毛剌区:是由于冲裁间隙的存在 而产生,该区域一般不可避免。Байду номын сангаас
第二章冲裁工艺与冲裁模
注意事项
a、粗大毛刺的产生部位:
当凸模刃口磨钝时,落料件的上端会出现 粗大的毛刺; 当凹模刃口磨钝时,冲孔件的下端会出现 粗大的毛刺; 当凸、凹模刃口同时磨钝时,则冲裁件上、下端都会产生毛刺。
第二章冲裁工艺与冲裁模
冲压模具设基础

冲压现状与发展方向
目前,我国冲压技术与先进工业发达国家相比还相当 落后,主要原因是我国在冲压基础理论及成形工艺、模 具标准化、模具设计、模具制造工艺及设备等方面与工 业发达国家尚有相当大的差距,导致我国模具在寿命、 效率、加工精度、生产周期等方面与先进工业发达国家 的模具相比差距相当大。 随着工业产品质量的不断提高,冲压产品生产正呈现 多品种、少批量,复杂、大型、精密,更新换代速度快 的变化特点,冲压模具正向高效、精密、长寿命、大型 化方向发展。为适应市场变化,随着计算机技术和制造 技术的迅速发展,冲压模具设计与制造技术正由手工设 计、依靠人工经验和常规机械加工技术向以计算机辅助 设计(CAD)、数控切削加工、数控电加工为核心的计 算机辅助设计与制造(CAD/CAM)技术转变
在冲压零件的生产中,合理的冲压成形工艺、先进的模 具、高效的冲压设备是必不可少的三要素。
冲压加工因制件的形状、尺寸和精度的不同,所采用的 工序也不同。根据材料的变形特点可将冷冲压工序分为 分离工序和成形工序两类:
分离工序——是指坯料在冲压力作用下,变形 部分的应力达到强度极限σb以后,使坯料发生 断裂而产生分离。分离工序主要有剪裁和冲裁 等。 成形工序——是指坯料在冲压力作用下,变形 部分的应力达到屈服极限σs,但未达到强度极 限σb,使坯料产生塑性变形,成为具有一定形 状、尺寸与精度制件的加工工序。成形工序主 要有弯曲、拉深、翻边、旋压等。
2.根据工序组合程度分类 (1)单工序模 在压力机的一次行程中,只完成一道 冲压工序的模具。 (2)复合模 只有一个工位,在压力机的一次行程中, 在同一工位上同时完成两道或两道以上冲压工序的模具。 (3)级进模(也称连续模) 在毛坯的送进方向上, 具有两个或更多的工位,在压力机的一次行程中,在不同 的工位上逐次完成两道或两道以上冲压工序的模具。
冲模基础知识.ppt(薛来生)

九、沖 裁 間 隙
沖裁間隙是直接關系到沖件斷面質量、尺寸精度、 模具壽命和力能消耗的重要工藝參數. 沖裁間隙數值,主要與材料牌號、供應狀態、厚度有 關. 對於厚度在1MM左右的薄材,單邊間隙值取0.5t%. 在沖孔時,間隙放在下凹模上;在落料時,間隙放在下 凸模上.
十、沖 件 質 量
沖件質量是指沖裁件的尺寸精度、斷面粗糙度、 表面平面度. 尺寸精度取決於凸凹的尺寸精度. 斷面粗糙度取決於凸凹之間的間隙. 表面平面度取決於很多因素,主要有壓料力,沖 件結構,模板的平面度等.
Guiding parts:outer guiding post 、outer bush 、inner guiding post 、inner bush
4.卸料部分:脫料板、浮升塊、頂料銷.
Stripping parts:stripping plate 、floating block 、ejection pin
1.壓力機的閉合高度h:是指滑塊在下死點時,工作台 面至滑塊下平面的距離. 2.沖模閉合高度h模:是指模具在最低的工作位置時, 下模座的底面至上模座的頂面的距離,它與壓力機的 閉合高度協調. 3.二者關系: h模>=hmin+M/3
hmin:連杆調到最長時,壓力機的閉合高度最小,稱最小閉合高度. M :連杆調節量.
機殼典型零件
沖模結構及認識
The structure and knowledge of stamping die about typical parts of computer enclosure
主講人: 薛來生
一、沖壓模具典型結構
Typical structure of stamping dies
1.單工序模(Single operation dies)
冲模设计(第2章)冲压加工基

2.2.3 影响金属塑性和变形抗力的主要因素
1、化学成份与组织对塑性和变 形抗力的影响。
2、变形温度对塑性和变形抗力 的影响。
3、变形速度塑性和变形抗力的 影响。
2. 3 金属塑性变形理论
为了简化塑性变形力研究过程,塑性理论通常采用 以下假设:
1)变形体是连续的,即整个变形体内不存在任何空隙。 这样,应力、应变、位移等物理量也都是连续的,并 可用坐标的连续函数来表示。
2)晶体的缺陷
晶体缺陷是指实际晶体结构中和理想的晶体点阵 结构发生偏差的区域。根据晶体缺陷的几何形态特征, 一般将之分成三大类:
a)点缺陷 如空位、 间隙原子、溶质原子。
b)线缺陷 如位错。 c)面缺陷 如晶界、相界、孪晶界、堆垛层错。
刃型位错示意图 a) 晶格立体模型 b) 平面图
3、塑性变形的基本形式
ln b b0
,
3
t dt ln t
t t0
t0
实际应变与相对应变之间的关系: ln(l )
1 2 3 0 ε1 ≥ ε2 ≥ ε3
(1)塑性变形时,物体只有形状和尺寸发生变化,而体积保 持不变。 (2)不论应变状态如何,其中必有一个主应变的符号与其他 两个主应变的符号相反,这个主应变的绝对值最大,称为最大 主应变。 (3)当已知两个主应变数值时,便可算出第三个主应变。 (4)任何一种物体的塑性变形方式只有三种,与此相应的主 应变的状态图也只有三种。
若作用于物体的外力卸载后,物体并不能完 全恢复自己的原始形状和尺寸,这样的变形称为 塑性变形(也称为残余变形)。
金属材料在外力作用下,既能产生弹性变形, 又能从弹性变形发展到塑性变形,是一种具有弹 塑性的工程材料。
冲压模具设计基础.40页PPT

•
30、风俗可以造就法律,也可以废除 法律。 ——塞·约翰逊
冲压模具设计基础.
1、最灵繁的人也看不见自己的背脊。——非洲 2、最困难的事情就是认识自己。——希腊 3、有勇气承担命运这才是英雄好汉。——黑塞 4、与肝胆人共事,无字句处读书。——周恩来 5、阅读使人充实,会谈使人敏捷,写作使人精确。——培根
•
26、我们像鹰一样,生来就是自由的 ,但是 为了生 存,我 们不得 不为自 己编织 一个笼 子,然 后把自 己关在 里面。 ——博 有 制约力 的。— —爱·科 克
•
28、好法律是由坏风俗创造出来的。 ——马 克罗维 乌斯
•
29、在一切能够接受法律支配的人类 的状态 中,哪 里没有 法律, 那里就 没有自 由。— —洛克
2 冲压模具设计基础

00 900 450 2
大
各向异性严重,拉伸时会出 现凸耳现象
00、900、 450
与板料轧制纤维方向成0o、 90o 45o试样的厚向异性指数
2.3
冲压常用的材料
1.金属材料 • 伸长率大、屈强比小、弹性模量大、硬化指数高和厚向异 性指数大有利于各种冲压成形工序。 (1)板料应有良好的表面质量。 板料表面不能有划伤、缩孔、麻点或断面分层,否则在冲 压过程中会造成应力集中而产生破裂。 (2)板料的规格应符合有关标准。 板料厚度及公差确定拉深工艺,凸模和凹模的间隙主要 是板料厚度公差确定的。
n 硬化指数
与材料的种类和性能 有关,通过实验获得
材料在变形时硬化性能的重要指标,n越大,表示变形过程中,材 料的变形抗力随着变形程度的增加而迅速增长,同时不易出现局部 的集中变形和破坏,有利于增大伸长类零件成形时的变形极限,对 板料的成形性能有着重要的影响。
变形抗力的大小取决于 材料在一定变形温度、变形速度和变形程度下的真实应力; 塑性加工时的应力状态、接触摩擦及相对尺寸因素等。 (1)化学成分及组织对变形抗力的影响 各种纯金属的变形抗力也不同,纯度越高,变形抗力 越小。不同牌号的合金,因组织状态不同,变形抗力也 不同。 一般合金元素、杂质元素含量越高,变形抗力越大, 尤其是弥散分布对变形抗力的增大影响较大。 (2)变形温度对变形抗力的影响 温度升高,金属原子间结合力降低,变形抗力降低。在 某些温度区间出现脆性区的金属则例外。
分离工序
切断 落料 冲孔 切舌 切边 剖切 弯曲
冲压工序
成形工序
拉深
成形
起伏 翻边 胀形 缩口
见P3-4 表1.1
2.2 板料的冲压成形性能
- 1、下载文档前请自行甄别文档内容的完整性,平台不提供额外的编辑、内容补充、找答案等附加服务。
- 2、"仅部分预览"的文档,不可在线预览部分如存在完整性等问题,可反馈申请退款(可完整预览的文档不适用该条件!)。
- 3、如文档侵犯您的权益,请联系客服反馈,我们会尽快为您处理(人工客服工作时间:9:00-18:30)。
第二章冲模设计基础
第一节冲压工艺类型及变形特点
1.冲压加工工艺概念
2.冲压加工工艺三要素
3.冲压加工基本工序分类
4.分离工序概念
5.变形工序概念
6.冲裁工序内容及模具简图绘制
7.弯曲与拉深工序内容及模具简图绘制
8.冲裁变形过程中的四个带区
9.冲裁变形过程的三个阶段
10.弯曲变形过程的三个阶段
11.冲压件的冲压工艺性①材料②形状③尖角倒圆角④悬臂和窄槽⑤孔径⑥孔间距孔边距
12.弯曲工艺性①②最小弯曲半径③最小弯曲高度④孔与弯曲处的最小距离
13.拉深工艺性
第二节冲模分类及其典型结构
1.单工序模及其结构简图
2.复合模及其结构简图
3.连续模(或级进模)及其结构简图特点比较单工序模、复合模及连续模
4.单工序模、复合模、连续模工作原理
5.冲模零部件组成及其作用
6.模具闭合高度、压力机闭合高度(最小闭合高度、最大闭合高度)、校核公式
7.冲模类型选择
第三章冲压工艺过程设
第一节毛坯展开与毛坯排样
1.弯曲展开计算
2.拉深展开计算:Δh,毛坯尺寸的确定(注意t的大小)
3.毛坯排样:排样方式,有少无废料排样的特点
4.搭边及其作用
5.步距、材料利用率
第二节冲压工艺方案设计
1.冲压工艺设计、拉深工艺设计
2.拉深工序的设计计算:拉深系数、总拉深系数、最小拉深系数、极限拉深系数,作用
3.工序顺序安排遵循的原则
4.冲压力及压力中心,计算冲压力及压力中心的目的
第四章冲模结构及零部件设计
第二节冲模总体结构设计
1.条料定位方式:X方向、Y方向
2.卸料方式:刚性卸料、弹性卸料(部件组成)及简图
3.模具的正倒装关系
4.标准模架的组成
第三节工作件设计
1.冲裁间隙、合理间隙、单面间隙
2.冲裁凸、凹模刃口尺寸计算时基准件的选取
3.弯曲、拉深工序凸、凹模尺寸计算
4.凸凹模结构及固定方式
第六章塑料注射模设计概述
1.塑料的分类及其特点(按成型性能分)
2. 塑料的成形收缩及公式注射过程的5阶段(冲模、压实、保压、倒流和冷却)
3. 注射工艺的三要素
4. 注射模具的基本结构及注射原理(过程)
5. 注射模的零部件组成
6. 普通流道浇注系统组成
7. 分流道及其作用、设计的场合
8. 冷料穴的作用
9. 浇口、点浇口及其适用塑件类型
10. 点浇口的优缺点
11. 浇口设计注意事项
12. 成型零件工作尺寸计算
13. 排气方式
14. 导向机构的两种形式
15. 推出机构及推出过程
16. 注射模温度调节对制品质量影响表现的四个方面:变形、精度、力学性能、表面质量
17. 重视型芯的冷却
第十一章压铸工艺及其模具设计概述
1.压铸工艺概念
2.压铸成型工艺三要素
3.压铸工艺的主要特征
4.压铸工艺的特点
5.热室压铸机与冷室压铸机的特征及特点
6.压射工艺参数:压铸压力、压射速度、充型速度、充型时间、持压时间、浇注温度、压铸模温度
7.压铸模预热与保持热平衡的原因
8.压铸模结构组成
9.分型面
10.分型面选择原则
11.例题及各种例图
12.溢流槽及其作用、设计部位
13.排气槽开设原因、排气方式
1. 2. 3. 4.。