电容失效切片分析流程
失效分析的程序和步骤

失效分析的程序和步骤失效分析是一种用于识别和解决系统或设备失效问题的方法。
它通过仔细的观察和分析失效现象,找出失效原因,并采取相应的措施来修复或防止失效的再次发生。
下面将介绍失效分析的基本步骤和常用程序。
1.收集相关信息:在进行失效分析之前,首先需要收集相关的信息和数据。
这包括失效现象的描述、相关历史记录、设备的技术参数、使用条件等。
2.确定失效的范围和目标:在进行失效分析时,需要明确分析的范围和目标。
这可以帮助专家集中精力分析关键部分,更好地解决问题。
3.制定研究方案:根据收集到的信息和目标,制定研究方案。
这包括确定所需的实验、测试、分析方法和工具。
4.实施实验和测试:根据制定的方案,进行必要的实验和测试。
这包括对失效现象进行再现性测试,测量相关的物理量和参数等。
5.分析测试数据:根据实验和测试的结果,对数据进行仔细的分析。
这包括对数据的统计处理、趋势分析、相关性分析等。
6.确定失效原因:根据数据分析的结果,确定失效的原因。
这可能涉及到不同层面的分析,包括物理层面、材料层面、设计层面、制造层面等。
7.提出解决方案:根据确定的失效原因,提出相应的解决方案。
这可能需要进行工艺改进、设计修改、部件更换等。
8.实施解决方案:根据提出的解决方案,进行相应的实施。
这包括对设备进行修复、改进、更新等操作。
9.验证解决方案:在实施解决方案后,进行必要的验证。
这包括对修复后的设备进行功能测试、性能测试等,以确保解决方案的有效性。
10.记录和总结:对整个失效分析过程进行记录和总结。
这有助于积累经验,提高问题解决能力,并为今后的类似问题提供参考。
失效分析的程序和步骤并没有固定的模式,具体的程序和步骤可能因问题的性质、复杂度和资源的限制而有所不同。
在实际应用中,可能需要结合专业技术和经验来灵活地进行失效分析,并不断地进行迭代和改进。
同时,要充分利用各种技术手段和工具,如扫描电镜、红外热像仪、故障模式与失效分析(FMEA)等,以提高分析的准确性和效率。
失效分析的流程

失效分析的流程
失效分析的流程主要包括以下步骤:
1. 故障现象记录:详细记录失效产品的故障表现、使用环境和条件,初步判断失效模式。
2. 样品收集与预处理:获取失效产品或部件样本,进行必要的保护和清洗,确保后续分析不受干扰。
3. 外观检查与非破坏性测试:通过肉眼观察、光学显微镜检查、X射线透视等手段,寻找外部可见的缺陷及内部结构异常。
4. 破坏性分析:采用金相分析、化学成分分析、断口分析等方法,深入探究失效机理。
5. 功能测试与模拟实验:对样品进行电气性能测试、力学性能测试,并根据需要设计加速老化、应力测试等模拟实验,重现失效过程。
6. 数据分析与结论得出:综合所有测试结果,分析失效原因,确定责任方,并提出改进措施或预防对策。
7. 报告编写与反馈:整理失效分析报告,将结论反馈给相关部门,指导产品质量改进和工艺优化。
失效分析处理流程失效分析处理流程

Take the market need as the guidance,Take the technical innovation as the motive.内容:✓失效分析处理流程✓生产伙伴的失效分析设备✓昊宏失效分析设备情况✓仓库条件生产控制分析(24小时)芯片设计失效分析(24小时)QA 部门成立问题分析小组(12小时)接收客户投诉信息(24小时)要求流片、封装、测试公司做失效分析试验(由供应商控制)客户市场部补货发出(12小时)初步失效分析(48小时)FAE 提供解决方案(72小时)输出失效分析报告(12小时)方案一方案二方案三记录失效分析过程,给出明确的失效分析结论和改进措施SOP5SOP2SOP3SOP4SOP1SOP6解决芯片设计失效(根据设计周期确定)SOP7}SOP8接收客户投诉信息SOP11.QA部收到客户正式的产品投诉后,应填写《产品失效信息表》1.1投诉反馈内容必须完整,至少应包括以下内容1.1.1填写投诉表序号、顾客名称/代号、产品的编号;1.1.2投诉何种缺陷或问题;1.1.3对应的出货日期及出货数量;1.1.4不良率有多少(或提供批量及不良数);1.1.5顾客方在什么环节发现该问题。
1.2必要时,须包括以下内容1.2.1顾客是否对产品进行了试验或特殊处理;1.2.2如果顾客有进行试验或特殊处理,须了解客户的试验条件及处理过程;1.2.3顾客的组装工艺。
1.3如有附件/样品,须在反馈表上注明1.3.1“有附件/样品”字样;1.3.2在附件/样品上标识相应的投诉序号;1.3.3如分析后需要把样品返还顾客,请注明“需返还顾客”字样,并注明返还流程。
SOP1接收客户投诉信息2.QA负责组织客户投诉的处理收到《产品失效信息表》后,QA须对投诉的问题进行确认24小时之内用标准email格式正式回复客户。
格式如下:XX,您好,很感谢您的来信。
我们会尽快审核您发来的《产品失效信息表》,并反馈给有关部门进行分析,并及时给您通告分析结果。
失效分析的流程

失效分析的流程Failure Analysis ProcessThe failure analysis process involves a series of steps to identify the root cause of a product or system malfunction. Here is a typical flow for conducting a comprehensive failure analysis:Problem Identification: The initial step is to clearly define the problem, including symptoms observed and the conditions under which the failure occurred.Data Collection: Gather relevant data such as operating logs, maintenance records, user feedback, and any available test results.Inspection and Testing: Conduct a thorough inspection of the failed component or system, using visual, mechanical, and electrical testing methods.Isolation of Failure Mode: Determine the specific mode of failure, such as a mechanical breakdown, electrical malfunction, or material degradation.Cause Analysis: Analyze the collected data and test results to identify potential causes of the failure. This may involve reviewing design specifications, manufacturing processes, and environmental factors.Verification and Confirmation: Conduct further tests or experiments to verify the identified causes and confirm their validity.Recommendation and Prevention: Based on the analysis, develop recommendations for corrective actions and preventative measures to prevent future failures.Documentation: Document the entire failure analysis process, including the findings, conclusions, and recommendations.Follow-up and Closure: Monitor the implementation of the corrective actions and ensure the problem is resolved. Close the failure analysis process once satisfaction is achieved.失效分析流程失效分析流程涉及一系列步骤,用于确定产品或系统故障的根本原因。
失效分析流程图

2.1 研磨机采用快速固化剂将材料固化与此内,再用180、320、600目砂纸进行研磨,然后再用抛 光纸进行抛光使之更清晰,再用显微镜观察(15倍)数显微镜测试纵、横截面积及测量结深之
2.2 X-RAY了解到烧结件或焊接件之异常点,若详细观察内部结构还要采用 化学方式解剖分析。
2.3.1 采用H2SO4每次倒200ml左右在烧杯中,再将烧杯放到功率400W的电炉上进行加热,加热到30
2.3.2 进一步用HF去除烧结玻璃,观察焊接件并拍照留证。 2.3.3 再用HNO3将引线、晶粒、焊片分开,观察晶粒状况(30倍显微镜)并拍照留证。
流程图及能力说明
流程说明
1.0 对不良品外观进行检查,采用20,30倍显微镜观察,电子数显卡尺对外观检测,并对材料进行
2.0 电性参数的不良,分别进行常规电性测试及试验测试,进一步确定不良状态,与相同类型的材 料做电性对比(留样及库存材料),收集各相关的实验资料,TK-168测试仪(VR/VF/DVR/IR/TRR) 4810示波器测试VR/VF;576示波器测试VR/VF/IR; 正向电压测试仪测试VF;反向电压测试仪测
电性测试(2.0) 解剖分析
2.0 电性参数的不良,分别进行常规电性测试及试验测试,进一步确定不良状态,与相同类型的材 料做电性对比(留样及库存材料),收集各相关的实验资料,TK-168测试仪(VR/VF/DVR/IR/TRR) 4810示波器测试VR/VF;576示波器测试VR/VF/IR; 正向电压测试仪测试VF;反向电压测试仪测
1研磨机采用快速固化剂将材料固化与此内再用180320600目砂纸进行研磨然后再用抛焊接偏位焊接气孔晶粒位置光纸进行抛光使之更清晰再用显微镜观察15倍数显微镜测试纵横截面积及测量结深之结深深度
失效分析流程
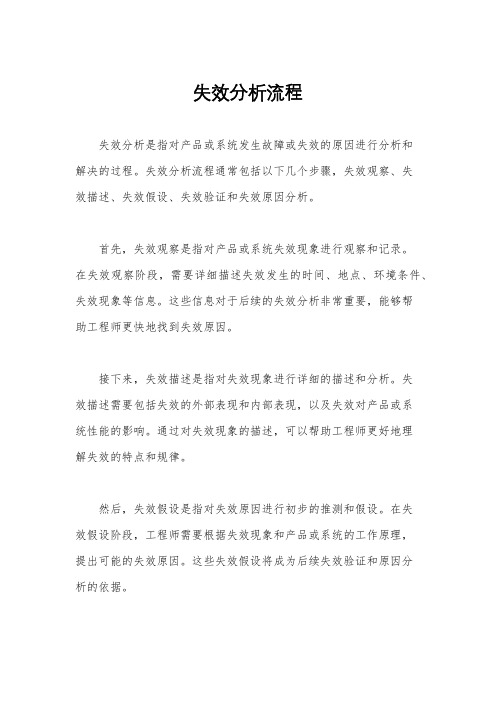
失效分析流程失效分析是指对产品或系统发生故障或失效的原因进行分析和解决的过程。
失效分析流程通常包括以下几个步骤,失效观察、失效描述、失效假设、失效验证和失效原因分析。
首先,失效观察是指对产品或系统失效现象进行观察和记录。
在失效观察阶段,需要详细描述失效发生的时间、地点、环境条件、失效现象等信息。
这些信息对于后续的失效分析非常重要,能够帮助工程师更快地找到失效原因。
接下来,失效描述是指对失效现象进行详细的描述和分析。
失效描述需要包括失效的外部表现和内部表现,以及失效对产品或系统性能的影响。
通过对失效现象的描述,可以帮助工程师更好地理解失效的特点和规律。
然后,失效假设是指对失效原因进行初步的推测和假设。
在失效假设阶段,工程师需要根据失效现象和产品或系统的工作原理,提出可能的失效原因。
这些失效假设将成为后续失效验证和原因分析的依据。
随后,失效验证是指对失效假设进行验证和排除。
在失效验证阶段,工程师需要通过实验、测试或仿真等手段,验证每一个失效假设的可行性和可靠性。
通过失效验证,可以确定哪些失效假设成立,哪些失效假设需要进一步分析。
最后,失效原因分析是指对经过验证的失效假设进行深入分析,找出真正的失效原因。
在失效原因分析阶段,工程师需要综合考虑失效现象、失效描述、失效假设和失效验证的结果,找出导致产品或系统失效的根本原因。
通过失效原因分析,可以采取相应的措施,防止类似的失效再次发生。
综上所述,失效分析流程是一个系统的、有条不紊的过程,需要工程师对失效现象进行认真观察和描述,提出合理的失效假设,进行有效的失效验证,最终找出真正的失效原因。
只有在每一个步骤都认真对待,才能确保失效分析的准确性和可靠性,为产品或系统的改进和优化提供有力支持。
失效分析的操作步骤

失效分析的操作步骤失效分析简介失效分析是一门发展中的新兴学科,近年开始从军工向普通企业普及,它一般根据失效模式和现象,通过分析和验证,模拟重现失效的现象,找出失效的原因,挖掘出失效的机理的活动。
在提高产品质量,技术开发、改进,产品修复及仲裁失效事故等方面具有很强的实际意义。
失效分析流程图1 失效分析流程各种材料失效分析操作步骤1 PCB/PCBA失效分析图2 PCB/PCBA失效模式爆板、分层、短路、起泡,焊接不良,腐蚀迁移等。
常用手段无损检测:外观检查,X射线透视检测,三维CT检测,C-SAM检测,红外热成像表面元素分析:扫描电镜及能谱分析(SEM/EDS)显微红外分析(FTIR)俄歇电子能谱分析(AES)X射线光电子能谱分析(XPS)二次离子质谱分析(TOF-SIMS)热分析:差示扫描量热法(DSC)热机械分析(TMA)热重分析(TGA)动态热机械分析(DMA)导热系数(稳态热流法、激光散射法)电性能测试:击穿电压、耐电压、介电常数、电迁移破坏性能测试:染色及渗透检测2 电子元器件失效分析电子元器件技术的快速发展和可靠性的提高奠定了现代电子装备的基础,元器件可靠性工作的根本任务是提高元器件的可靠性。
图3 电子元器件失效模式开路,短路,漏电,功能失效,电参数漂移,非稳定失效等常用手段电测:连接性测试电参数测试功能测试无损检测:开封技术(机械开封、化学开封、激光开封)去钝化层技术(化学腐蚀去钝化层、等离子腐蚀去钝化层、机械研磨去钝化层)微区分析技术(FIB、CP)制样技术:开封技术(机械开封、化学开封、激光开封)去钝化层技术(化学腐蚀去钝化层、等离子腐蚀去钝化层、机械研磨去钝化层)微区分析技术(FIB、CP)显微形貌分析:光学显微分析技术扫描电子显微镜二次电子像技术表面元素分析:扫描电镜及能谱分析(SEM/EDS)俄歇电子能谱分析(AES)X射线光电子能谱分析(XPS)二次离子质谱分析(SIMS)无损分析技术:X射线透视技术三维透视技术反射式扫描声学显微技术(C-SAM)3 金属材料失效分析随着社会的进步和科技的发展,金属制品在工业、农业、科技以及人们的生活各个领域的运用越来越广泛,因此金属材料的质量应更加值得关注。
失效分析步骤及手法
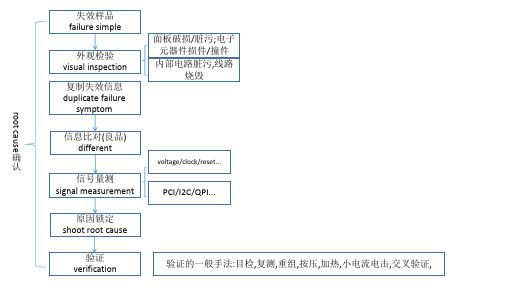
组装 assemble
针对不良原因,立 即改善不良状况
针对不良原因,做出长 期有效的改善对策
根据不良产品的占比,列出TOP分布,描绘不良曲线图,以便后续生产观察
不上电 不开机 不显示 不联网
DVT1/2 2.6 2.5 3.5 2.3
PVT1/2 1.2 1.5 1.8 1.3
MP1/2 0.2 0.5 0.5 0.2
来料 仓储
供应商
存储温湿度,包装
空焊,连锡
SMT
复测,程式
reflow profile(reflow时间,温 度,N2速度) 物料上料(错料,漏件)
测试 test
重组,外观
测试人员误判
improvement
测试程式存在 bug
组装人员过失 组装SOP存在缺 陷
短期对策 improve action off hand 长期对策 improve action for further
信号量测 signal measurement 原因锁定 shoot root cause 验证 verification
PCI/I2C/QPI...
验证的一般手法:目检,复测,重组,按压,加热,小电流电击,交叉验证,
失效数量占比 failure rate 责任归属 owner
不良分布
物料不良
物料 material
4 3.5 3 2.5 2 1.5 1 0.5 0 不上电
failure tip top
DVT1/2
PVT1/2
MP1/2
不开机
不显示
不联网
失效样品 failure simple 外观检验 visual inspection 复制失效信息 duplicate failure symptom 面板破损/脏污;电子 元器件损件/撞件 内部电路脏污,线路 烧毁
电子元器件失效模式总结

元器件的失效模式总结Beverly Chen2016-2-4一、失效分析的意义失效分析(Failure Analysis)的意义在于通过对已失效器件进行事后检查,确定失效模式,找出失效机理,确定失效的原因或相互关系,在产品设计或生产工艺等方面进行纠正以消除失效的再次发生。
一般的失效原因如下:二、失效分析的步骤失效分析的步骤要遵循先无损,后有损的方法来一步步验证。
比如先进行外观检查,再进行相关仪器的内部探查,然后再进行电气测试,最后才可以进行破坏性拆解分析。
这样可以避免破坏性的拆解破坏证据。
拿到失效样品,首先从外观检查开始。
1. 外观检查:收到失效样品后,首先拍照,记录器件表面Marking信息,观察器件颜色外观等有何异常。
2.根据器件类型开始分析:2.1贴片电阻,电流采样电阻A: 外观检查,顶面覆盖保护层有针状圆形鼓起或黑色击穿孔->内部电阻层烧坏可能->万用表测量阻值:测得开路或者阻抗偏大->内部电阻层烧毁可能->可能原因:过电压或过电流烧毁—>检查改电阻的稳态功率/电压或者瞬时功率/电压是否已超出spec要求。
Coating 鼓起并开裂黑色击穿点●可失效样品寄给供应商做开盖分析,查看供应商失效报告:如发现烧毁位置位于激光切割线下端,可确定是过电压导致失效。
需要考虑调整应用电路,降低电压应力,或者换成能承受更大应力的电阻。
激光切割线去除coating保护层后,可以看到烧毁位置位于激光切割线旁边,该位置电应力最集中。
B: 外观检查,顶面底面均无异常->万用表测量阻值:测得开路或者阻抗偏大->内部电阻层烧毁或者电极因硫化断开或阻抗增大->检查改电阻的稳态功率或者瞬时功率是否已超出spec要求,如有可能是过电压或过功率烧毁;应力分析在范围内,考虑硫化->失效样品寄给供应商分析。
查看供应商失效报告:●如发现烧毁位置位于激光切割线下端,可确定是过电压导致失效。
失效分析流程规范文件

失效分析流程规范文件一、失效分析的重要性。
1. 失效分析就像医生给病人看病一样重要。
当一个产品或者设备出现问题,不能正常工作了,这就好比人生病了。
我们得搞清楚到底是哪里出了毛病,不然就像蒙着眼睛走路,啥也干不成。
这时候,失效分析就是那盏照亮黑暗的灯。
1.2 从企业的角度看,失效分析直接关系到成本和声誉。
如果不做失效分析,可能会一直生产有问题的产品,那可就是“赔了夫人又折兵”,既浪费钱又让客户失望。
二、失效分析的流程。
2.1 收集信息。
首先得像个侦探一样,收集各种各样的信息。
这包括产品的使用环境,是在高温、潮湿还是其他特殊环境下出的问题。
就像了解一个人犯罪时的现场环境一样重要。
还有产品的使用历史,之前有没有过类似的小毛病之类的。
这些信息就像拼图的碎片,一块都不能少。
2.2 外观检查。
外观检查是失效分析的第一步,这个环节可不能走马观花。
要仔仔细细地查看产品的表面,有没有裂痕、变形或者磨损之类的。
这就好比相亲的时候,第一眼看对方的外貌,虽然不能完全了解一个人,但能发现一些明显的问题。
有时候,从外观上就能发现很关键的线索,可能直接就指向问题的根源了。
2.3 无损检测。
无损检测可是个技术活。
就像给产品做个全身的X光检查,不用破坏产品就能看到内部的结构有没有问题。
比如说用超声波检测,看看内部有没有裂缝之类的隐藏问题。
这就像孙悟空的火眼金睛,能看穿表象看到本质。
2.4 破坏性检测。
如果无损检测还不能找到问题,那就只能进行破坏性检测了。
这就有点像破釜沉舟了,虽然会破坏产品,但是为了找到问题根源也不得不这么做。
比如说对产品进行切片,看看内部的微观结构,像金相组织是不是正常之类的。
三、结果分析与报告。
3.1 结果分析。
在做完各种检测之后,就得像个学者一样,静下心来分析结果。
把所有的检测数据、观察到的现象都放在一起,仔细琢磨。
有时候一个小细节可能就是解决问题的关键。
不能“眉毛胡子一把抓”,要分清主次,找到真正的原因。
电容失效分析(详解干货)

电容失效分析(详解干货)【导读】电子元器件的主要失效模式包括但不限于开路、短路、烧毁、爆炸、漏电、功能失效、电参数漂移、非稳定失效等。
对于硬件工程师来讲电子元器件失效是个非常麻烦的事情,比如某个半导体器件外表完好但实际上已经半失效或者全失效会在硬件电路调试上花费大把的时间,有时甚至炸机。
陶瓷电容失效分析:多层片状陶介电容器由陶瓷介质、端电极、金属电极三种材料构成,失效形式为金属电极和陶介之间层错,电气表现为受外力(如轻轻弯曲板子或用烙铁头碰一下)和温度冲击(如烙铁焊接)时电容时好时坏。
多层片状陶介电容器具体不良可分为:1、热击失效2、扭曲破裂失效3、原材失效三个大类(1)热击失效模式:热击失效的原理是:在制造多层陶瓷电容时,使用各种兼容材料会导致内部出现张力的不同热膨胀系数及导热率。
当温度转变率过大时就容易出现因热击而破裂的现象,这种破裂往往从结构最弱及机械结构最集中时发生,一般是在接近外露端接和中央陶瓷端接的界面处、产生最大机械张力的地方(一般在晶体最坚硬的四角),而热击则可能造成多种现象:第一种是显而易见的形如指甲狀或U-形的裂縫第二种是隐藏在内的微小裂缝第二种裂缝也会由裸露在外的中央部份,或陶瓷/端接界面的下部开始,并随温度的转变,或于组装进行时,顺着扭曲而蔓延开来(见图4)。
第一种形如指甲狀或U-形的裂縫和第二种隐藏在内的微小裂缝,两者的区别只是后者所受的张力较小,而引致的裂缝也较轻微。
第一种引起的破裂明显,一般可以在金相中测出,第二种只有在发展到一定程度后金相才可测。
(2)扭曲破裂失效此种不良的可能性很多:按大类及表现可以分为两种:第一种情况、SMT阶段导致的破裂失效当进行零件的取放尤其是SMT阶段零件取放时,取放的定中爪因为磨损、对位不准确,倾斜等造成的。
由定中爪集中起来的压力,会造成很大的压力或切断率,继而形成破裂点。
这些破裂现象一般为可见的表面裂缝,或2至3个电极间的内部破裂;表面破裂一般会沿着最强的压力线及陶瓷位移的方向。
失效分析步骤

失效分析步骤
研发和生产过程当中,会出现不可避免的一些错误,当错误出现时,需要及时找到问题的原因去解决。
随着产品质量和可靠性的要求不断提高,失效分析的工作显得尤为重要,发现并解决问题是必要的,防止频繁地出现同一个问题。
失效分析的步骤原则上是先进行非破坏性分析,后进行破坏性分析;先外部分析,后内部(解剖)分析;先调查和了解与失效相关的情况(线路、应力条件、失效现象等),然后分析失效元器件。
而失效分析的流程也可以根据工作开展的顺序分为以下几个步骤:样品信息调查、失效样品保护、失效分析方案设计、外观检查、电测试、应力试验分析、故障模拟分析、失效定位分析(非破坏性分析、半破坏性分析、破坏性分析)、综合分析、失效分析结论和改进建议,结果验证。
鉴于失效分析的重要作用,应将该项工作贯穿于整个电子元器件设计、研发、生产、试验和使用的全过程当中,这些技术的过程需要进行失效分析才能得以完善。
华南检测失效分析,专业的团队人员,主要分析对象:半导体分立器件,各种规模、各种封装形式的集成电路,射频、微波器件,电源模块、光电模块等各种元器件和模块。
失效分析通常通过哪几个程序

失效分析通常通过哪几个程序失效分析是一个非常重要的过程,特别是在制造、维护和运行过程中。
它通常涉及对失效原因进行分析,以确定如何纠正或预防类似事件的再次发生。
为帮助大家深入了解,以下内容由创芯检测网整理,提供给您参考。
收集数据在进行失效分析之前,必须收集与失效相关的所有数据。
这些数据可能包括使用情况、环境条件、产品规格和设计文档等。
通过对这些数据进行分析,可以确定可能的失效原因。
分析失效原因在收集数据后,必须对数据进行分析,以确定失效的根本原因。
这可能涉及到对材料、工艺、设备、人员等各个方面进行调查和分析。
只有通过深入的分析,才能找到失效的根本原因。
制定解决方案一旦确定了失效的根本原因,就必须制定解决方案。
这可能包括修改设计、改变工艺、改进材料或更换零部件等。
在制定解决方案时,必须考虑成本和时间因素,以确保方案的可行性和有效性。
验证解决方案一旦制定了解决方案,必须对其进行验证,以确保其能够有效地预防类似事件的再次发生。
验证可能包括实验、测试或模拟等。
只有通过验证,才能确保解决方案的有效性和可靠性。
培训和维护失效分析的结果不仅可能影响产品的设计和制造,也可能对维护和运行过程产生影响。
因此,在进行失效分析后,必须对相关人员进行培训,以确保他们能够正确使用和维护产品,并及时发现和纠正潜在的问题。
失效分析是一个复杂而关键的过程。
只有通过全面的调查和分析,才能找到失效的根本原因,并制定有效的解决方案。
此外,培训和维护也是失效分析的重要组成部分,以确保产品和过程的安全和可靠性。
我公司拥有专业工程师及行业精英团队,建有标准化实验室3个,实验室面积1800平米以上,可承接电子元器件测试验证、IC真假鉴别,产品设计选料、失效分析,功能检测、工厂来料检验以及编带等多种测试项目。
失效分析流程

失效分析流程失效分析(Failure Analysis)是指对产品、系统或工艺失效的原因进行分析和诊断,从而找出根本原因并提出改进措施的过程。
失效分析通常包括以下几个步骤:问题定义、收集数据、实验分析、原因诊断、提出改进措施和验证。
首先,问题定义是失效分析的第一步。
在这一步中,需要明确失效的具体表现、发生的时间以及对系统或工艺造成的影响。
这可以帮助确定失效的范围,并缩小分析的方向。
接下来,收集数据是为了进一步分析失效的原因。
通过收集相关的数据,如失效前的工艺参数、产品性能等,可以帮助确定失效的可能原因。
这些数据可以来自于产品测试、生产线记录等。
然后,进行实验分析。
在这一步中,可以通过实验来模拟失效现象,并进一步观察失效的特点和规律。
实验分析可以分为定性实验和定量实验。
定性实验可以通过观察和对比来确定失效的可能原因,而定量实验可以通过实验数据的统计分析来确定失效的具体原因。
在实验分析的基础上,进行原因诊断。
这一步是失效分析的关键步骤,通过对实验数据的分析和比对,可以确定失效的根本原因。
原因诊断通常需要结合领域知识和经验,以及分析工具和方法,如光学显微镜、电子显微镜、能谱分析等。
根据原因诊断的结果,提出改进措施。
改进措施可以包括工艺参数的调整、材料的更换、设备的升级等。
根据失效分析的结果,制定合理、切实可行的改进措施,以避免类似的失效事件再次发生。
最后,验证改进措施的有效性。
通过对改进措施的应用和实施,观察和测试失效是否得到解决,以验证改进措施的有效性。
如果失效得到解决,则说明改进措施的效果良好,如果仍然存在失效问题,则需要重新进行分析和改进。
综上所述,失效分析流程包括问题定义、收集数据、实验分析、原因诊断、提出改进措施和验证几个关键步骤。
通过这一流程,可以找出失效的根本原因,提出合理的改进措施,从而提高产品、系统或工艺的可靠性和稳定性。
失效分析是一项重要的工作,对于企业的质量管理和技术创新具有重要的意义。
失效分析流程

失效分析流程失效分析是指对产品或系统在使用过程中出现的故障进行分析,找出故障的原因和根源,以便及时修复和改进产品或系统的设计。
失效分析流程是一个系统的、有条理的过程,它可以帮助我们更快速、更准确地找出故障的原因,并采取相应的措施来解决问题。
下面将介绍失效分析流程的具体步骤。
1. 收集信息。
失效分析的第一步是收集相关信息。
这包括对故障现象的描述、故障发生的时间和地点、故障对系统性能和安全性的影响等。
同时,还需要收集产品或系统的设计文件、生产记录、使用说明书等相关资料,以便后续的分析工作。
2. 故障确认。
在收集到足够的信息后,需要对故障进行确认。
这包括对故障现象进行验证,确定故障是否真实存在,以及对故障的范围和影响进行评估。
只有确认了故障的存在,才能进行后续的分析工作。
3. 制定分析计划。
在确认了故障后,需要制定分析计划。
这包括确定分析的范围和目标,制定分析的方法和工具,确定分析的时间和人员等。
分析计划的制定有助于提高分析的效率和准确性。
4. 故障分析。
在制定了分析计划后,可以开始对故障进行分析。
这包括对故障的可能原因进行推测和假设,利用各种分析方法和工具对故障进行深入分析,找出故障的根本原因。
在故障分析过程中,需要注重数据的准确性和完整性,确保分析结果的可靠性。
5. 制定改进措施。
在找出了故障的根本原因后,需要制定相应的改进措施。
这包括对产品或系统的设计、制造、使用等方面进行改进,以防止类似的故障再次发生。
改进措施的制定需要考虑到成本、效果、可行性等因素,确保能够有效地解决问题。
6. 实施改进措施。
在制定了改进措施后,需要及时地进行实施。
这包括对产品或系统进行相应的改进和调整,确保改进措施能够有效地落实到位。
同时,还需要对改进措施的实施效果进行监控和评估,及时调整和改进。
7. 总结经验。
在实施了改进措施后,需要对整个失效分析过程进行总结和经验归纳。
这包括对分析过程中的不足和问题进行反思和总结,提出改进建议,为今后的失效分析工作提供参考和借鉴。
(整理)陶瓷电容失效分析
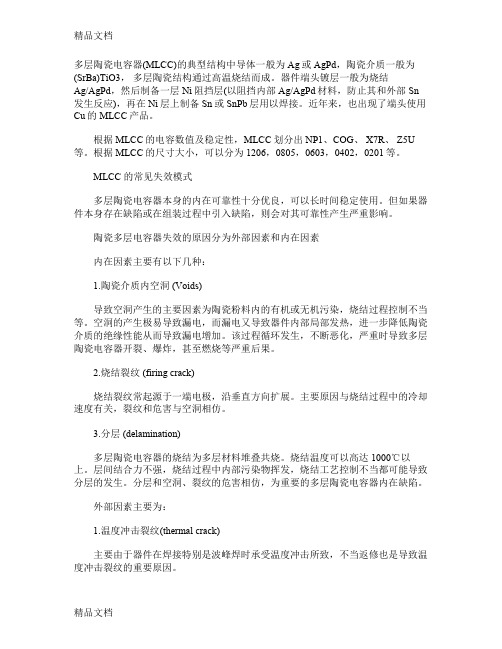
多层陶瓷电容器(MLCC)的典型结构中导体一般为Ag或AgPd,陶瓷介质一般为(SrBa)TiO3,多层陶瓷结构通过高温烧结而成。
器件端头镀层一般为烧结Ag/AgPd,然后制备一层Ni阻挡层(以阻挡内部Ag/AgPd材料,防止其和外部Sn 发生反应),再在Ni层上制备Sn或SnPb层用以焊接。
近年来,也出现了端头使用Cu的MLCC产品。
根据MLCC的电容数值及稳定性,MLCC划分出NP1、COG、 X7R、 Z5U 等。
根据MLCC的尺寸大小,可以分为1206,0805,0603,0402,0201等。
MLCC 的常见失效模式多层陶瓷电容器本身的内在可靠性十分优良,可以长时间稳定使用。
但如果器件本身存在缺陷或在组装过程中引入缺陷,则会对其可靠性产生严重影响。
陶瓷多层电容器失效的原因分为外部因素和内在因素内在因素主要有以下几种:1.陶瓷介质内空洞 (Voids)导致空洞产生的主要因素为陶瓷粉料内的有机或无机污染,烧结过程控制不当等。
空洞的产生极易导致漏电,而漏电又导致器件内部局部发热,进一步降低陶瓷介质的绝缘性能从而导致漏电增加。
该过程循环发生,不断恶化,严重时导致多层陶瓷电容器开裂、爆炸,甚至燃烧等严重后果。
2.烧结裂纹 (firing crack)烧结裂纹常起源于一端电极,沿垂直方向扩展。
主要原因与烧结过程中的冷却速度有关,裂纹和危害与空洞相仿。
3.分层 (delamination)多层陶瓷电容器的烧结为多层材料堆叠共烧。
烧结温度可以高达1000℃以上。
层间结合力不强,烧结过程中内部污染物挥发,烧结工艺控制不当都可能导致分层的发生。
分层和空洞、裂纹的危害相仿,为重要的多层陶瓷电容器内在缺陷。
外部因素主要为:1.温度冲击裂纹(thermal crack)主要由于器件在焊接特别是波峰焊时承受温度冲击所致,不当返修也是导致温度冲击裂纹的重要原因。
2.机械应力裂纹(flex crack)多层陶瓷电容器的特点是能够承受较大的压应力,但抵抗弯曲能力比较差。
- 1、下载文档前请自行甄别文档内容的完整性,平台不提供额外的编辑、内容补充、找答案等附加服务。
- 2、"仅部分预览"的文档,不可在线预览部分如存在完整性等问题,可反馈申请退款(可完整预览的文档不适用该条件!)。
- 3、如文档侵犯您的权益,请联系客服反馈,我们会尽快为您处理(人工客服工作时间:9:00-18:30)。
电容失效切片分析流程
电容失效切片分析通用流程
万用表测量是否短路
金相观察
外观是否完好
否
裂纹
否
优先选择破损侧面切片
平行于电极层
否
是
继续切
转90°切
是
贯穿裂纹从侧面切
优先选裂纹面切
否
是
是否存在板级裂纹
否
是
板级应力导致
寻找烧毁点,必要时转90°
是否存在板级裂纹
否
是
板级应力导致
寻找烧毁点,必要时转90°
是
从侧面切
是
是否存在板级裂纹
板级原因导致失效
是
平行于电极层
否
否
是
继续切找烧毁点
转90°切找烧毁点
失效背景收集
收样
创见未来。