ES249V3.0.1.130503_CN
舟山电信EVDO掉话率优化指导书

浙江电信舟山分公司EVDO网络掉话率优化指导书浙江电信舟山分公司EVDO网络掉话率优化指导书华为技术有限公司二〇一三年八月十一日舟山电信EVDO络掉话率优化指导书 (5)1概述 (5)1.1掉话的定义 (5)1.2关于掉话的几点说明 (6)1.3掉话的分类 (6)1.3.1空口丢失 (6)1.3.2其它原因 (8)2掉话机制 (8)2.1前向掉话机制 (8)2.2反向掉话机制 (9)3与掉话相关的话统 (10)3.1掉话率、掉话比率、用户早释率、无线掉线率 (10)3.2掉话率[%] (10)3.3连接成功次数 (10)3.4连接正常释放次数[次] (10)3.5连接释放次数(空口丢失)[次] (11)3.6连接释放次数(其它原因)[次] (12)3.7连接释放次数(硬切换失败)[次] (12)3.8连接释放次数(休眠态定时器超时)[次] (13)3.9连接释放次数(休眠态定时器超时AT无响应)[次] (13)3.10分支释放次数(专线用户接入)[次] (14)3.11连接正常释放总次数(含DORMANT 释放)[次] (15)3.12连接异常释放次数 (15)3.13连接正常释放率[%] (16)3.14连接释放(前向负荷高强制释放)[次] (16)3.15连接释放(反向负荷高强制释放)[次] (16)3.16连接释放(由1X和DO互操作引起)[次] (16)3.17连接释放(连接态收到C ONNECTION R EQUEST)[次] (16)3.18呼叫释放总次数-EVDO (17)3.19掉话比率-EVDO[%] (17)3.20用户早释次数[次] (17)3.21PDSN原因要求释放次数[次] (17)3.22无线掉线次数(其他原因)[次] (17)3.23无线掉线次数(空口丢失)[次] (18)3.24无线连接释放次数(含PDSN要求释放次数)[次] (18)3.25用户早释率[%] (18)3.26无线连接释放次数(不含PDSN要求释放次数)[次] (18)3.27无线掉线率[%] (18)3.28无线网络掉线率(含PDSN原因释放)[%] (19)4掉话率分析优化思路 (19)4.1整网问题分析思路 (19)4.2TOP小区优化思路 (22)4.3掉话率分析优化流程图 (24)5掉话常见原因及处理方法 (24)5.1异常用户 (25)5.2用户直接拔卡 (27)5.31X/DO互操作 (27)5.4告警 (28)5.5RSSI异常 (29)5.6邻区配置不合理 (30)5.7PN复用不合理 (31)5.8参数设置不合理 (31)5.9AN间切换失败 (32)5.10异频硬切换 (33)5.11覆盖差 (33)6舟山现网掉话率话统分析 (36)6.1BSC2AN级掉话分析 (36)6.2载频级掉话分析 (38)6.3CDR辅助掉话分析 (39)6.3.1呼叫资源释放时激活集分支分析(移动性分析) (39)6.3.2呼叫释放的原因值分析 (39)6.3.3掉话次数TOP用户分析 (40)6.3.4DO互操作分析(全天) (41)6.3.5拔卡行为分析(全天) (42)6.3.6孖机分析(全天) (43)6.3.7弱覆盖分析(全天) (44)6.3.8邻区漏配分析(全天) (45)6.3.9越区覆盖分析(全天) (45)6.3.10导频污染分析(全天) (46)7优化措施及成果汇编 (47)7.1AN间软切换开通 (47)7.2多载波边界优化 (50)7.2.1某局配置OFS硬切换优化某多载频边界掉话率案例 (50)7.2.2某局点通过调整多载频边界基站叠加载频功率优化掉话率案例 (53)7.3RF优化 (55)7.3.1某局调整室外基站射频增益降低室内用户高掉话案例 (55)7.3.2某局调整射频增益优化用户高掉话案例 (57)7.3.3某局控制高站越区覆盖优化高掉话案例 (58)7.4RSSI整治 (63)7.4.1东山隧道RSSI高导致终端掉话案例 (63)7.4.2某小区因外部强干扰的EVDO高掉话优化案例 (66)7.5数据配置问题 (69)7.5.1A18链路配置不一致引起BSC间软切换失败进而掉话问题 (69)7.5.2新增小区登记区错配导致周边区域EVDO掉话率超高 (71)7.5.3某本地网PDSN重协商失败导致频繁EVDO上网卡频繁掉线 (72)7.5.4某局合理调整无数据态PCT参数降低掉话率案例................................... 错误!未定义书签。
霍尔传感器ES249中文手册
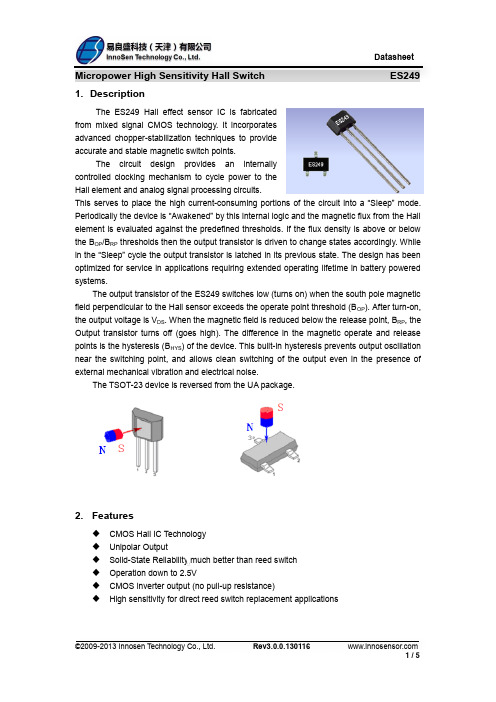
6. Absolute Maximum Ratings
Parameter
Supply Voltage(operating) Supply Current
©2009-2013 Innosen Technology Co., Ltd.
Symbol
VDD IDD
Value
5.5 70
Units
V μA
2/5
Symbol
VDD IDD IOUT VSAT TAW TSL
Test Conditions
Operating Average
Min
2.5
Typ
3 45 1.0
Max
5.5
Units
V μA mA
IOUT=1mA Operating Operating 20
0.4
V μS μS
600
8.
Magnetic Characteristics
24921
3 - 0.44 3.90 0.05 0.05 3.90 3 - 0.39 3.90
Active Area Depth:
3 1
0.84(Nom) 6 1
2.3. 0.1
1 2
2 1
3 4
3 1
6 1
0.5 14
Notes: 1). Controlling dimension: mm; 2). Leads must be free of flash and plating voids; 3). Do not bend leads within 1 mm of lead to package interface; 4). PINOUT: Pin 1 Pin 2 Pin 3 VDD GND Output
ES4600_用户手册_V1.1.3

用户手册
版本:ES4600_UM_CN_V1.Байду номын сангаас.3
i
目录
注意事项 ...................................................................................................................................................................iv 1 参数 ........................................................................................................................................................................ 1
1-1 技术参数........................................................................................................................................................ 1 1-2 条码预设参数................................................................................................................................................ 2 2 开始使用 ...................................................
网赢视讯VOPEX-USBH-2 4 DVI HDMI USB KVM 分频器使用说明书

Front and Rear View of VOPEX-USBH-2TRADEMARKVOPEX and the NTI logo are registered trademarks of Network Technologies Inc in the U.S. and other countries. All other brand names and trademarks or registered trademarks are the property of their respective owners.COPYRIGHTCopyright © 2004-2023 by Network Technologies Inc. All rights reserved. No part of this publication may be reproduced, stored in a retrieval system, or transmitted, in any form or by any means, electronic, mechanical, photocopying, recording, or otherwise, without the prior written consent of Network Technologies Inc, 1275 Danner Drive, Aurora, Ohio 44202.CHANGESThe material in this guide is for information only and is subject to change without notice. Network Technologies Inc reserves the right to make changes in the product design without reservation and without notification to its users.TABLE OF CONTENTS INTRODUCTION (1)LIMITATIONS (2)MATERIALS (2)CONNECTORS AND LEDS (2)INSTALLATION (3)Monitor Connection (3)Mouse Connection (3)Keyboard Connection (3)CPU Connection (4)Hub Ports (5)Power-Up (6)OPERATION (7)Keyboard Command Mode (7)Mice and Trackballs with MACs (8)International SUN Keyboards (8)Hub Ports (9)SPECIFICATIONS (9)TROUBLESHOOTING (9)WARRANTY INFORMATION (9)TABLE OF FIGURESFigure 1- Connect User 1 Keyboard, Mouse, and Monitor (3)Figure 2- Connect the VOPEX to the CPU (4)Figure 3- Example of configuration with HDMI extenders on input and output (5)Figure 4- Connect other devices to Hub Ports (5)Figure 5- Connect the AC adapter to the VOPEX (6)INTRODUCTIONThe VOPEX-USBH-2 (VOPEX) is a DVI/HDMI and USB KVM Splitter and 3-Port Hub. It enables the control of one USB enabled CPU through two separate USB keyboards, USB mice, and DVI or HDMI monitors and it enables the connection of 3 additional USB devices (other than keyboards or mice). Each user is able to have complete control of a CPU (although it is not recommended to access the CPU more than one at a time as unpredictable results may occur). While the user access is controlled by three (3) separate modes of operation, both user monitors will show the same image at all times. The 3 hub ports (for printer, scanner, camera, etc.) will be connected to the CPU at all times.Options:∙ A 4-port model (VOPEX-USBH-4) is available supporting up to 4 users.Types of User Input Devices Supported:∙USB keyboard with Windows layout∙USB keyboard with SUN layout∙USB keyboard with MAC layout∙USB Mouse - (up to 3 buttons)∙USB IntelliMouse (scroll wheel)∙Mouse-Trak trackball∙Logitech, Kensington and Microsoft Wheelmouse or Trackball on Mac CPUs with special drivers∙Logitech Cordless Elite Duo keyboard and mouse∙Crystal Vision keyboard with touchpad∙Gyration keyboard/mouse∙NTI USB-PS/2 Adapter∙NTI USB-SUN Adapter∙Logitech Comport MK345Types of Shared Devices Supported:∙Both low-speed and full speed USB devices are supported.∙USB 1.1 (low/full speed) standards.Video Support:∙Compliant with HDMI 1.2, HDCP 1.1 and DVI 1.0 standards. Plug-n-Play specification supported∙Supports HDMI CEC∙Supports HDTV resolutions up to 1080i and computer resolutions up to 1920x1200.Types of CPUs Supported:Any USB CPU supporting USB version 1.0 or above including:∙USB WINxx∙USB MAC∙USB SUNNTI Extenders Supported:∙ST-C6USBH-300 300 Foot HDMI USB KVM Extender∙ST-C6USBH-HDBT 328 Foot HDMI USB KVM Extender over HDBase-TLIMITATIONS∙The USB ports on the VOPEX are USB 1.1 compatible. Any USB 2.0 device connected to the VOPEX will be regulated to USB 1.1 speeds.MATERIALSMaterials included with this kit:∙VOPEX-USBH-2/4 2/4-Port DVI/HDMI USB KVM Splitter∙USB2-AB-1M-5T 1 Meter Transparent USB A-B Device Cable∙DVI-HD-3-MM 3' M-M DVI-to-HDMI Video Cable∙120 or 240VAC @ 50 or 60Hz-5VDC/3.0A AC Adapter (2-Port Model)or∙120 or 240VAC @ 50 or 60Hz-5VDC/6.0A AC Adapter (4-Port Model)∙URL Slip with path to this manualCONNECTORS AND LEDSLABEL CONNECTOR/LED DESCRIPTIONO Power Switch To power up or power down the VOPEX1 I/2 Power Green LED Illuminates to indicate proper power to the unitx Green LED For visual indication of the splitter’s operating mode3 UserSelect Push Button Press to manually switch between operating modes4 ModeIN HDMI Type A female for connecting the video cable from the CPU5 VIDEOx HDMI Type A female for connection of the user video monitors6 MONITOR3.0A 2.1x5.5mm Power Jack for connection of power supply7 5VDCPORTS USB type A female for connection of the cables from USB devices8 HUB9 USER x DEVICES USB type A female for connection of user USB device(s) (keyboard and mouse)10 CPU USB type B female for connection of the devices cable from the CPUINSTALLATIONFYI: It is not necessary to disconnect power to the CPU and monitor(s) before installation.Monitor Connection1.Disconnect the monitor cable at the CPU and reconnect it to the "MONITOR 1" port on the VOPEX. (See Fig. 1)(A second DVI-HDMI-x-MM cable may be required (sold separately)- one has been supplied for connection to the CPU.)2.Plug a second monitor into the "MONITOR 2" port on the VOPEX.Mouse Connection1. Disconnect the mouse at the CPU and reconnect it to one of the female USB type A 'USER 1 DEVICES" ports on theVOPEX.2. Connect a second mouse (or optional USB extension cable NTI USB-A+A-5M) to the female USB type A "USER 2 DEVICES"ports on the VOPEX.Keyboard Connection1. Disconnect the keyboard at the CPU and reconnect the keyboard to the remaining female USB type A "USER 1 DEVICES"port on the VOPEX.2.Connect a second keyboard (or optional USB extension cable NTI USB-A+A-5M) to the remaining female USB type A "USER2 DEVICES" ports on the VOPEX.Figure 1- Connect User 1 Keyboard, Mouse, and MonitorCPU Connection1. Connect the male USB type A connector end of the USB2-AB-1M-5T cable into the device port on the CPU.2. Connect the male USB type B connector of the same cable to the "CPU" port on the VOPEX.3.Connect the male DVI-D connector end of the DVI-HD-3-MM into the CPU’s video port. (See Fig. 2)4.Connect the male HDMI connector end of the DVI-HD-3-MM into the "VIDEO" port on the VOPEX.Figure 2- Connect the VOPEX to the CPUNote: If your CPU has an HDMI video port instead of DVI, an HD-xx-MM cable can be purchased separately from NTI. Contact your NTI salesperson or visit our web site at for details.Figure 3- Example of configuration with HDMI extenders on input and outputHub PortsIf desired, connect additional USB devices toeach of the three "Hub Ports". These portswill be powered and operational anytime the VOPEXand CPU are powered ON. See Fig. 3.Figure 4- Connect other devices to Hub PortsPower-UpConnect the AC adapter to the VOPEX and power ON the VOPEX. If not already ON, power ON the CPU and monitors.Figure 5- Connect the AC adapter to the VOPEXOPERATIONMode SelectionThe VOPEX comes equipped with three (3) modes of operation- INSTANT AUTO, DELAYED AUTO, and USERx. To manually toggle between modes, depress the MODE button once each time a mode change is desired. Select the mode according to the chart below.INSTANTANEOUSAll users have control of the CPU simultaneously.DELAYThe first user with an activedevice gets control of CPU. The second user is locked out until after 5 seconds of inactivity from the first user.USER 1"USER 1" has sole access. Other users are locked out.USER 2 "USER 2" has sole access. Other users are locked out.USER 3 "USER 3" has sole access. Other users are locked out. ------USER 4"USER 4" has sole access. Other users are locked out.------Note: In Instantaneous Mode all users have control of the CPU simultaneously, but it is recommended that only one user take control at a time. Movements from multiple mice at the same time will cause unpredictable movements on the monitor.Keyboard Command ModeIn order to control the other features of the VOPEX with the keyboard, Command Mode must be enabled. To enter Command Mode from the keyboard:PressWhen the Command Mode is enabled, all 3 status lights on the keyboard will illuminate and both LED’s on the VOPEX will blink continuously to indicate Command Mode is enabled. See the table below for functions that are available while in Command Mode.NOTE: The user must exit Command Mode in order for the CPU to switch to the selected mode. To exit Command Mode, press ESC on the keyboard. The mouse will not operate while in Command Mode.NOTE: While in Command Mode, when a proper programming command is entered and is recognized by the switch, the hiLED’s on the keyboard will flash once to indicate acceptance. The user must exit Command Mode (by pressing ESC) to see a change take effect in the switch operation .NOTE: The VOPEX will automatically exit Command Mode after 5 seconds of inactivity by the user if the user does not manually exit Command Mode.+Ctrl ~(ACCENT KEY)`U1U2U3U4U1U2U1U2U3U4U1U2U1U2U1U2U3U4U1U2U3U4U1U2U1U2U3U4U1U2U3U4The following functions exist while in Command Mode:<X>-<key>-<Y> Select a new key sequence to use to enter Command Mode – Replace <key> with the desired keyto follow <Ctrl> with. Note: <Ctrl> + <'> will still function as a method to enter Command Mode<L> - <x> - <x> Select the country code of the keyboard being used with a USB SUN CPU (see Country Codeschart below)<V> - <Enter> This will print the version of the code in the VOPEX to a text editor window (i.e. Windows Notepad)for use when troubleshooting the VOPEX. Note: The text editor should be open and active prior toentering Command Mode.<M> Configure the CPU port to connect to a MAC CPU (see "Mice and Trackballs with MACs" below.)<W> Configure the CPU port to connect to a Windows or SUN CPU<D> - <x> Select the operating mode, x=1 for Instantaneous Mode, x=2 for Delay Mode, x=3 User 1Mode, x=4for User 2 mode. x= 5 for User 3 Mode, x=6 for User 4 Mode. (Modes are described in the table onpage 6.)<P> - <x> Select the default mode to have the VOPEX enter upon power-up.<Esc> Exit Command ModeMice and Trackballs with MACsThe VOPEX can be configured to enable full functionality between mice and trackballs having two or more buttons and a USB MAC CPU. By default, the CPU port on the VOPEX is configured for use with a WINDOWS or SUN CPU and has no special translation for using multi-function mice and trackballs when a MAC CPU is connected. Using the commands in Command Mode above, either enable or disable this feature as needed.NOTE: Be sure to re-configure the port for connection to a WINDOWS or SUN CPU if a MAC CPU is removed and a WINDOWS or SUN CPU is then connected.International SUN KeyboardsThe VOPEX can recognize international layouts for Sun keyboards. To use an international Sun keyboard, follow this procedure:1. Disconnect the CPU from the VOPEX2. Connect the international keyboard to be used to the VOPEX3. Power down the VOPEX for at least 3 seconds4. Power up the VOPEX5. Reconnect the CPU to the VOPEXIt is also possible to configure the VOPEX to emulate a specific international Sun keyboard regardless of what actual keyboard is connected. This is recommended when the CPU needs the layout code (i.e. a SUN CPU) and the keyboard doesn't have an explicit layout code (i.e. some Windows keyboards). To do this, manually set the VOPEX to indicate the international keyboard identification number to the CPU using the following procedure:1. Connect the keyboard to be used to the VOPEX2. Power down the VOPEX for at least 3 seconds3. Power up the VOPEX4. Enter Command Mode (<Ctrl> + <`>)5. Type Lxx, where xx is the number from the list below that corresponds to the desired country code6. Exit Command Mode7. Power down the VOPEX for at least 3 seconds8. Power up the VOPEX9. Reboot the CPU connected to the VOPEXCountry CodesNetherlands/Dutch 27 Swiss/French Supported 09 German 1800 NotNorwegian 28 Swiss/German 01 Arabic 10 Greek 19(Farsi) 29 Switzerland02 Belgian 11 Hebrew 20PersianPoland 30 Taiwan03 Canadian-Bilingual 12 Hungary 2104 Canadian-French 13 International (ISO) 22 Portuguese 31 TurkishRussia 32 UK Republic 14 Italian 2305 CzechSlovakia 33 US06 Danish 15 Japan(Katakana) 24Spanish 34 Yugoslavia07 Finnish 16 Korean 25Swedish 35-99 Reserved08 French 17 LatinAmerican 26Hub PortsThe three connections labeled "Hub Ports" can be used to connect any USB device, such as a printer, scanner, camera, etc. for continuous operation at USB 1.1 compliant speeds. These ports are not controlled by the VOPEX.SPECIFICATIONSSize: Each unit is 8.5”W x 6”D x 2.6”HPower: VOPEX-USBH-2- Powered by 120 or 240VAC @ 50 or 60Hz-5VDC/3.0A AC AdapterVOPEX-USBH-4- Powered by 120 or 240VAC @ 50 or 60Hz-5VDC/6.0A AC AdapterConnections: HDMI Type A- supports HDTV resolutions to 1080i and computer resolutions to 1920x1200. VGA & SGAcompatibleUSB Type A female device connectorsUSB Type B female CPU connectorTROUBLESHOOTINGPROBLEM SOLUTION∙Keyboard error ∙Check cable connections on CPU and VOPEX∙Mouse not working ∙Check cable connections on CPU and VOPEXWARRANTY INFORMATIONThe warranty period on this product (parts and labor) is two (2) years from the date of purchase. Please contact Network Technologies Inc at (800) 742-8324 (800-RGB-TECH) or (330) 562-7070 or visit our website at for information regarding repairs and/or returns. A return authorization number is required for all repairs/returns.Man123 Rev 1/17/23。
国家信息安全产品认证获证名单
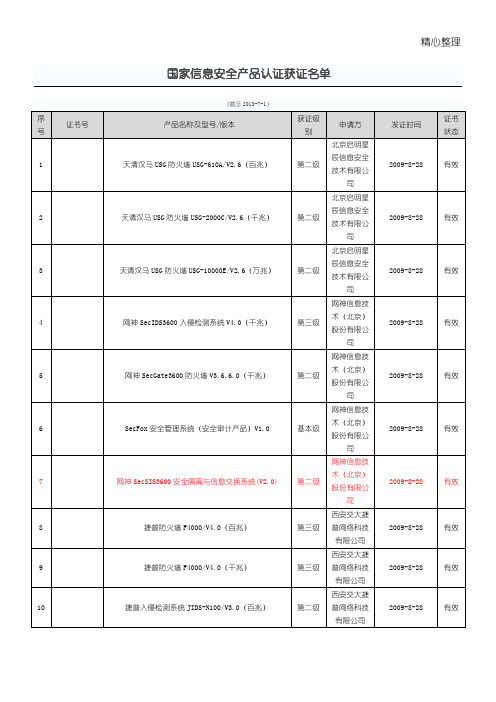
第一级
网御 SIS-3000 安全隔离与信息交换系统 V1.0(千兆) 第二级
网康互联网控制网关 NS-ICG/V5.5.1(安全审计产品) 基本级
数字电视条件接收系统智能卡软件(V5.1)
EAL4 增 强级
绿盟安全审计系统 V5.6
增强级
绿盟网络入侵检测系统 V5.6?(百兆)
第三级
绿盟安全网关 V5.6(百兆)(防火墙产品)
证书 状态 有效 有效 有效 有效 有效 有效 有效 有效 有效 有效
精心整理
序 证书号
号
11
12
13
200
14 15 16 17 18 19
20
21 22 23 24
25
26
27
20
产品名称及型号/版本 捷普入侵检测系统 JIDS-N1000/V3.0(千兆)
捷普信息审计系统 JBCA/V3.0
捷普主机监控与审计系统 JHAUDIT/V2.0 SecowayUSG2000?防火墙 V3.3(百兆) SecowayUSG5000?防火墙 V3.3(千兆) QuidwayEudemon200E 防火墙 V3.3(百兆) QuidwayEudemon1000E 防火墙 V3.3(千兆) 华堂千兆网络安全防御系统 V4.3(防火墙产品) 华堂网络安全防御系统 V4.0(防火墙产品)(百兆)
有限公司 北京天融信 科技有限公
司 北京天融信 科技有限公
司 北京网御星 云信息技术
有限公司 杭州迪普科 技有限公司 北京网御星 云信息技术
有限公司 北京网御星 云信息技术
有限公司
发证时间 2009-12-10 2009-12-22 2009-12-24 2009-12-24 2009-12-24
研控科技MS-Mini3E总线型混合伺服驱动器用户手册说明书

目录前言 (4)1概述 (5)1.1产品介绍 (5)1.2特性 (5)1.3应用领域 (5)1.4产品命名规则 (5)2性能指标 (6)2.1 EtherCAT特性 (6)2.2电气特性 (6)2.3使用环境 (6)3安装 (7)3.1安装尺寸 (7)3.2安装方法 (7)4 驱动器端口与接线 (8)4.1接线示意图 (8)4.2端口定义 (8)4.2.1状态指示界面 (8)4.2.2旋钮拨码 (9)4.2.3状态指示灯 (9)4.2.4 EtherCAT通讯端口 (9)4.2.5控制信号输入/输出端口 (10)4.2.6编码器输入端口 (10)4.2.7电机输出端口 (10)4.2.8电源输入端口 (10)4.3输入/输出端口操作 (11)5适配电机 (14)5.1电机尺寸 (14)5.2电机规格 (17)5.3技术参数 (17)5.4电机线规格(仅适用闭环电机) (18)5.5编码器线规格(仅适用闭环电机) (18)5.6电机接线图 (19)6 EtherCAT总线 (22)6.1 EtherCAT技术原理 (22)6.2 EtherCAT数据结构 (22)6.3 EtherCAT报文寻址 (23)6.3.1 设备寻址 (24)6.3.2 逻辑寻址 (25)6.4 EtherCAT分布时钟 (25)6.5 EtherCAT通信模式 (25)6.5.1 Free Run模式 (25)6.5.2 SM2/3模式 (26)6.5.3 DC模式 (26)6.6 EtherCAT状态机 (27)6.7 应用层协议COE (27)6.7.1 COE对象字典 (28)6.7.2 服务数据对象(SDO) (28)6.7.3 过程数据对象(PDO) (28)7驱动器控制协议CiA 402 (29)7.1 CIA402状态机 (29)7.2 工作模式 (30)7.3循环同步位置模式(CSP) (31)7.4 循环同步速度模式(CSV)........................................................ 错误!未定义书签。
乐舜信息科技LS-智盒LS-D4000产品手册说明书
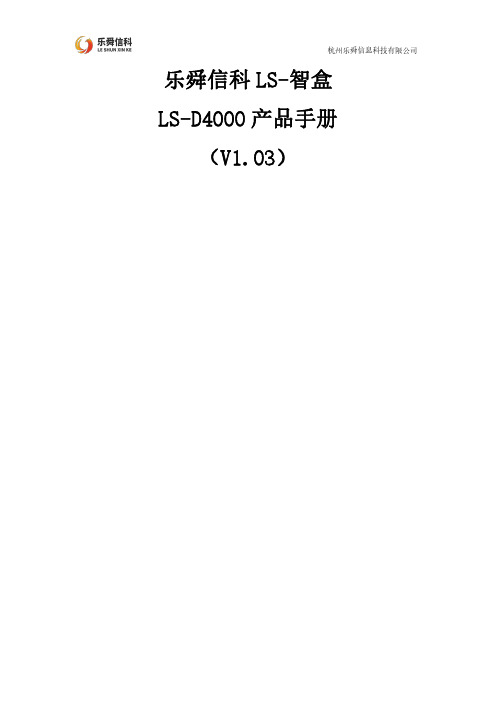
乐舜信科LS-智盒LS-D4000产品手册(V1.03)修改日期版本修改描述作者备注2019-7-25V1.01初稿Fzy2019-10-25V1.02ESD参数修正Fzy2019-11-17V1.031.增加尺寸图描述2.增加指示灯说明描述3.名称统一Fzy目录1.产品简介 (2)2.功能特点 (2)3.产品外观 (3)3.1实物图 (3)3.2尺寸图 (4)4.接口说明 (4)4.1电源接口 (4)4.2天线接口 (4)4.3SIM卡接口 (5)4.4外部接口 (5)5.工作原理 (5)6.参数规格 (6)6.1技术参数 (6)6.2指示灯说明 (7)7.产品应用 (7)8.产品优势 (8)1.产品简介LS智盒(LS-D4000)是一安全稳定的工业级边缘计算网关,是集数据采集、数据存储、边缘计算、云服务于一体的智能设备。
产品特点:⏹工业级ARM Cortex-A7处理器,主频528MHz⏹256MB DDR3RAM;256MB NAND;8KB E2PROM⏹外置RTC独立时钟,时钟掉电保持⏹系统外置独立看门狗设计,稳定可靠⏹支持多种通讯链路,RS485*2,RS232*1,CAN*1,USB HOST接口⏹支持模拟量输入4~20mA,1~5V输入⏹支持数字量输入干接点*1,湿节点*2⏹支持1路IO继电器输出;⏹多指示灯,通讯指示灯和2路可编程指示灯⏹双网口隔离设计⏹支持4G全网通、WiFi(选配);2.功能特点⏹工业级设计:-40℃~85℃⏹电源接口:DC12~28V⏹接口隔离:对外接口均采用隔离保护设计,安全可靠⏹安全等级:三级EMC⏹数据存储:本地存储支持1个月⏹支持协议:支持标准Modbus RTU/TCP协议、DLT645-2007规约;⏹支持PLC接入:支持西门子,三菱、台达、欧姆龙等PLC;⏹支持本地Web:配置参数如配置路由器一样简便;⏹网络平台:阿里云物联网平台、网易工业物联网平台、乐舜物联网平台;⏹定制开发:可协议定制开发;⏹远程维护:可通过集中式控制台来进行设备远程管理(平台免费);多途径故障告警:可通过短信、邮件、微信等多途径对故障进行告警;3.产品外观3.1实物图3.2尺寸图尺寸:30*133*166(不含挂耳)4.接口说明4.1电源接口电源接线端子DC12~28V输入,防反接4.2天线接口SMA标准天线接口,默认吸盘天线4.3SIM卡接口标准插拔SIM卡(大卡),支持贴片卡。
NanoVNA-F V3 便携式矢量网络分析仪用户手册说明书
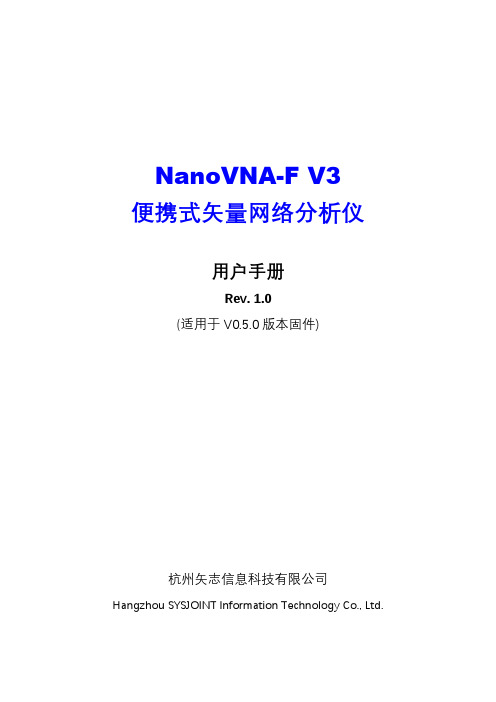
NanoVNA-F V3便携式矢量网络分析仪用户手册Rev.1.0(适用于V0.5.0版本固件)杭州矢志信息科技有限公司Hangzhou SYSJOINT Information Technology Co.,Ltd.目录1.产品简介 (1)1.1.关于NanoVNA-F V3 (1)1.2.产品特点 (1)1.3.技术指标 (2)1.4.VNA基础知识 (3)2.产品外观 (4)3.用户界面 (5)3.1.主界面 (5)3.2.菜单 (8)3.3.键盘 (8)4.菜单功能 (9)4.1.显示 (9)4.2.标记 (12)4.3.频率设置 (14)4.4.校准 (16)4.5.回调/保存 (20)4.6.时域变换TDR (20)4.7.设置 (22)4.8.存储功能 (25)5.用户自定义信息 (25)6.夜间模式 (25)7.上位机 (26)8.串口命令 (28)8.1.连接串口 (28)8.2.命令详解 (30)9.固件升级 (39)1.产品简介1.1.关于NanoVNA-F V3NanoVNA-F V3是一款便携式矢量网络分析仪(Vector Network Analyzer,VNA),测量频率范围1MHz~6GHz,可测量S11和S21参数,其中,S11动态范围50dB,S21动态范围65dB。
NanoVNA-F V3可用于测试MF/HF/VHF/UHF/SHF频段的各类天线,如短波天线、ISM频段天线、WiFi天线、蓝牙天线、GPS天线等,也可用于测量滤波器、放大器、衰减器、电缆、功分器、耦合器、双工器等射频组件,并支持幅频曲线、相频曲线、驻波比、史密斯圆图、极坐标、群时延等多种显示格式。
此外,NanoVNA-F V3还具有TDR功能,可用于测量电缆长度。
NanoVNA-F V3采用全金属机壳设计,坚固耐用,并可有效屏蔽电磁干扰。
机身尺寸125mmx75mmx20mm,小巧便携。
机身采用SMA型射频接头,并配备了高品质SMA延长缆,方便连接各类被测件。
ESET Mobile Antivirus 安装手册和用户指南说明书
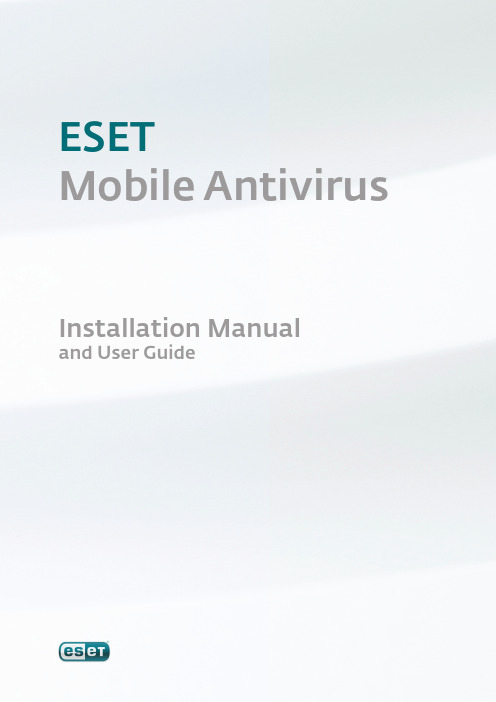
ESETMobile AntivirusInstallation Manualand User GuideESET Mobile Antivirusr. o.ESET Smart Security was developed by ESET, spol. s r.o.For more information visit .sgAll rights reserved. No part of this documentation may be reproduced, stored in a retrieval system or transmitted in any form or by any means, electronic, mechanical, photocopying, recording, scanning, or otherwise without permission in writing from the author.ESET, spol. s r.o. reserves the right to change any of the described application software without prior notice. Customer Care Singapore: www.eset.sg/supportcontents 1. Installation of ESET Mobile Antivirus (4)1.1 Minimum system requirements (4)1.2 Installation (4)1.2.1 Installation on your Device (4)1.2.2 Installation using your computer (4)1.3 Product activation (6)1.3.1 Username and password (6)1.3.2 Registration key (6)1.4 Uninstalling (6)2. On-access scanner (7)2.1 Settings (7)2.2 Testing On-access Scanning (8)3. On-demand scanner (8)3.1 Running a Whole device scan (8)3.2 Scanning a folder (9)3.3 Settings (9)3.4 Scan objects setup (10)4. Virus found (10)4.1 Quarantine (11)5. Spam filter (11)5.1 Settings (11)5.2 Whitelist / Blacklist (12)5.3 Locating blocked (Spam) messages (12)5.4 Deleting Spam Messages (13)6. Update (13)6.1 Updating using your computer (13)6.2 Settings (13)7. Viewing Logs and statistics (14)8. Troubleshooting (15)8.1 Connection to update server failed (15)8.2 Unsuccessful Installation (15)9. Technical support (16)1. Installation of ESET Mobile Antivirus1.1 Minimum system requirementsTo install ESET Mobile Antivirus, your mobile devicemust meet the following minimum requirements:Most PDA and Smartphone mobile devices fulfill these requirements.1.2 InstallationSave all open documents and exit all running applications before installing.You can install ESET Mobile Antivirus directly on your device or use your computer.1.2.1 Installation on your DeviceTo install ESET Mobile Antivirus directly on your device, download the .cab installation file by WiFi, Bluetooth file transfer or email attachment (it is similar to an .msi file on your PC).After downloading the .cab file, tap Start > File Explorer to locate the file and tap it to launch theinstaller.Figure 1-1:Installation package Figure 1-2: Installation progressWhen you see the message that the program was installed successfully, tap okto complete installation.Figure 1-3: Successful installationAfter installation, you can modify the program settings. However, the default configuration provides the maximum level of protection against malicious programs.1.2.2 Installation using your computerTo install ESET Mobile Antivirus using your computer (Active Sync in Windows XP or Windows Mobile Device Center in Windows Vista), download and run the installation package (.exe file) on the computer to which your mobile device is connected and then follow the instructions in the installation wizard.Verify that your system meets the minimum requirements for ESET Mobile Antivirus (see section 1.1, “Minimum system requirements”) and click Next.45Figure 1-4: Launching the installer on your computerIn the next window, accept the End User License Agreement (EULA) and then click Finish to begininstallation on your mobile device.Figure 1-5: Installation on the computer is completeAfter the installation package has been copied to your mobile device, click OK to exit the installer on your computer. To finish installation, follow the stepsdescribed in section 1.2.1, “Installation on your device”.Figure 1-6: Installing the .cab file on your deviceWhen installation is complete, the installer displays a message indicating that the program was successfully installed (Figure 1‑3). Tap ok to exit installation. Then, activate ESET Mobile Antivirus by following the steps insection 1.3, “Product activation”.Figure 1-7: Installation is complete1.3 Product activationAfter installation, ESET Mobile Antivirus must be activated. If you are not prompted to activate your product, tap Menu > Activate from the main program window. There are two activation methods depending on how you acquired your product.1.3.1 Username and passwordIf you purchased your product from a distributor, you received a username and password with your purchase. Select the Login/Password option, enter a current contact address in the e-mail field and then enterthe information you received in the Username and Password fields. Tap Activate to complete activation.1.3.2 Registration keyIf you acquired ESET Mobile Antivirus with a new device (or as a boxed product), you received a Registrationkey with your purchase. Select the Registration key option, enter a current contact address in the e-mail field and then enter the information you received in the Key field. Tap Activate to complete activation. Your new authentication data (Username and Password) will automatically replace the Registration key and be sent to the email address you specified.Figure.1-8: Program activationWarning: When activating and updating ESET Mobile Antivirus, a small amount of data must be downloaded from the Internet. These transfers are charged according to your mobile provider.1.4 UninstallingTo uninstall ESET Mobile Antivirus from your mobile device, tap Start > Settings, tap the System taband then tap the Remove Programsicon.Figure 1-9: The Remove Programs icon in the Settings menuIn the Remove Programs list, select ESET Mobile Antivirus and tap Remove. Tap Yes when prompted toconfirm uninstallation.Figure 1-10: Select a program to be uninstalled672. On-access scannerThe main ESET Mobile Antivirus window (tap Start > ESET Mobile Antivirus ) is the starting point for all instructions in this manual.The On‑access scanner checks files that you interact with in real time. Files that are run, opened or saved are checked for viruses automatically. Scanning takes place before any action is performed on a file, ensuring maximum protection. The On‑access scanner launches automatically at system startup.2.1 SettingsTap Menu > Settings > On Access to enable or disable the following options:Enable On Access scan – If selected, the On‑access scanner runs in the background.Heuristics – Select this option to apply heuristic scanning techniques.Heuristics identifies new malware not yet detected by the virus signature database by analyzing code and recognizing typical virus behavior.Run after restart – If selected, the On‑access scanner will automatically initiate after restart.Display scan in action status – Select this option to show scan status in the bottom right corner while scanning is in progress.Show Shell Icon – Displays the ESET Mobile Antivirusicon on the main mobile device window.Figure 2-1: On-access scanner settingsFigure 1-11: Confirm uninstallationAfter the program has been removed, tap ok to close the Remove Programs window.82.2Testing On-access ScanningTo verify that real‑time protection is working properly, select the Display scan in action status check box in the On‑access settings window (see section 2.1, “Settings”).Then, open a file or initiate an activity (i.e., play a music file or take a picture). A Scanning… message should appear briefly in the bottom right corner (Figure 2‑2).NOTE : The Display scan in action status option uses additional battery power. We recommend deselecting this option (default setting) after testing real‑timeprotection.Figure 2-2: On-access scanning3. On-demand scannerYou can use the On‑demand scanner to check your mobile device for the presence of infiltrations.By default, specific, predefined file types are scanned.To run the On‑demand scanner, tap Scan in the lowerleft corner of the main ESET Mobile Antivirus window.Figure 3-1: An On-demand scan in progress3.1 Running a Whole device scanA Whole device scan checks memory, running processes, their dependent dynamic link libraries (DLLs) and files that are part of internal and removable storage.NOTE: The memory scan is not performed by default. To activate it, tap Menu > Settings > General and select the Memory Scan check box.From the main ESET Mobile Antivirus window, tap Scan > Whole device . System memory is scanned first (including processes found running in it and their dependent DLLs), and then files and folders are scanned. The full path and file name of each file scanned will be displayed briefly.93.2 Scanning a folderTo scan a single folder on your device, tap Start > ESET Mobile Antivirus . From the lower left corner, tap Scan > Folder , tap the folder you wish to scan and tap Select to begin scanning the selected folder. If Memory Scan is enabled (Menu > Settings > General > Memory Scan), it is performed as well.NOTE: To abort a scan in progress, tap Menu > Stop Scanfrom the bottom right.Figure 3-3: Scanning a folderFigure 3-4: Select a folder to scan3.3 SettingsTo modify parameters related to scanning, tap Menu > Settings > General.Figure 3-5: The Settings menuThe General settings window allows you to specify what action to take if a virus is found. Select the Show alert dialog option to display virus alert notifications.The drop‑down menu allows you to select an action to be performed automatically for infected files. You can select from the following options: Delete infected file (file will be removed), Do nothing (not recommended) and Move to quarantine .The Stored logs drop‑down menu allows you to define the maximum number of logs to be stored.If the Memory scan option is selected (default setting), the device memory will automatically be scanned for active malicious programs prior to the actual file scan.If the Heuristics option is selected, ESET Mobile Antivirus uses heuristic scanning techniques. Heuristics is an algorithm‑based detection method that analyzes the code and searches for typical virus behavior. Its main advantage is the ability to identify malicious software not yet known by the current virus signature database. Archive nesting allows you to specify the depth of nested archives to be scanned.Select Archive deletion to automaticallydelete archive files containing infected objects.Figure 3-6: General settings3.4 Scan objects setupTo specify the file types to be scanned on your mobile device, tap Menu > Settings > Extensions.The Extension settings window will display (Figure3‑7), showing the most common file types exposed to infiltration. Select the file types you wish to be scanned. To exclude an extension from scanning, deselect its check box.To scan all files, deselect the Extension sensitive check box.Figure 3-7: Advanced scan parameter setup 4. Virus foundIf a virus is found, ESET Mobile Antivirus will prompt you to take an action. We recommend you select Delete infected file. If you select Do nothing (not recommended), no action will be performed and the infected file will remain on your mobile device. If you select Move to quarantine, the file will be moved toquarantine and deleted.Figure 4-1: Action if a virus is foundWhen a virus is detected, ESET Mobile Antivirus displays the Show alert dialog check box. Deselect this option to prevent alert windows from displaying in the future. All future actions will be performed automatically. NOTE: If an infiltration is detected in an archive, the Delete archive option is available in the alert window. Select this option along with the Delete infected fileoption to delete all infected archive files.Figure 4-2: Virus found104.1 QuarantineThe main task of quarantine is to safely store infected files. Files should be quarantined if they cannot be cleaned, if it is not safe or advisable to delete them or if they are being falsely detected by ESET Mobile Antivirus. Files stored in the quarantine folder can be viewed in a table that displays the date and time of quarantine and the path to the original location of the infected files. You can restore quarantined files by tapping Menu > View > Quarantine > Options > Restore (each file will be restored to its original location). You can also choose to permanently remove the files by tapping Options> Delete. If you want your choice to apply to multiple files, tap Options > Select all before performing thedesired action.Figure 4-3: Quarantine 5. Spam filterThe Spam filter blocks unsolicited SMS messages that are sent to your mobile device.Unsolicited messages usually include advertisements from mobile phone service providers or messages from unknown or unspecified users.5.1 SettingsTap Menu > View > Statistics to see statistical information about the number of received and blocked messages.In the Spam filter settings (Menu > Settings > Spam Filter), the following filter modes are available:Block SMS from contact list – Enable this option to allow SMS messages only from senders that are not in your address book. The Whitelist and Blacklist entries override this option.Block SMS from unknown senders – Enable this option to accept messages only from contacts inyour address book. The Whitelist and Blacklist entries override this option.Select both Block SMS from contact list and Block SMS from unknown senders to automatically block all incoming SMS messages. The Whitelist and Blacklist entries override this option (see section 5.2, “Whitelist/ Blacklist“).To not block any messages, deselect both Block SMS from contact list and Block SMS from unknown senders to disable the Spam filter. All incoming messages will be accepted. The Whitelist and Blacklist entries override this option (see section 5.2, “Whitelist/Blacklist“).Figure 5-1: Spam filter11125.2 Whitelist / BlacklistThe Whitelist is a list of telephone numbers from which all SMS messages are accepted. Entries listed here override all options in the general spam filter setup (Settingstab).Figure 5-2: The WhitelistThe Blacklist is a list of telephone numbers from which all SMS messages are blocked. Entries listed here override all options in the general Spam filter setup (Settings tab).Warning: Adding a number/contact to the Blacklist will automatically move messages from that sender to the Spam folder.To add a number or a contact to the Whitelist/Blacklist, select the tab for the list you want to modify and tap Options.Figure 5-3: The Blacklist5.3 Locating blocked (Spam) messagesThe Spam folder is used to store blocked messages that are routed to it and is automatically created when the first spam message is deleted. To locate the Spam folder and review blocked messages, follow the steps below:1. Open the program your device uses for textmessaging. For example, from the Start menu tap Messaging.Figure 5-4: Tap Messaging2. Tap Messagesto open the list of received items.Figure 5-5: Tap MessagesNOTE: Your device will likely point to the folder most recently visited. To switch to another folder, such as the Spam folder, tap Show in the upper left (for Smartphones tap Menu > Folders ).133. Select the Spamfolder.Figure 5-6: Spam folder5.4 Deleting Spam MessagesTo delete spam messages from your mobile device, follow the steps below:1. Tap Menu >Settings > Spam Filter .2. Tap Clear spam .3. Tap Yesto confirm the deletion of all spam messages.Figure 5-7: Deleting Spam Messages6. UpdateBy default, ESET Mobile Antivirus is installed with an update task to ensure that the program is regularly updated. You can also perform updates manually. After installation, we recommend you run the first update manually. To do so, tap Menu > Update .6.1 Updating using your computerIf your mobile device is not connected to the Internet, you can also update the virus signature database using your computer by following the steps below:1. Disable Internet updates under Miscellaneous settings (tap Menu > Settings > Update and deselect the Internet update option).2. Download the file containing the most recent virus signature database to your PC.3. Connect your device to your PC (Windows XP and earlier require that ActiveSync be installed. Windows Vista uses Windows Mobile Device Center).4. Copy the virus signature database update file (EsetAV_WM.upd) to the ESET Mobile Antivirus installation directory (Program Files\ESET\ESET Mobile Antivirus).5. Tap Menu > Update . ESET Mobile Antivirus will check the update file and, if the update file is not damaged, the latest virus signature database will be installed.6.2 SettingsTo configure the update settings, tap Menu > Settings > Update .The Internet update check box enables or disables automatic updates. To set the time interval for the automatic update, use the Auto update drop‑down menu. You can also specify the Internet server fromwhich updates are downloaded (we recommend leaving the default setting of ). In the Login and Password fields, enter the username and password you received after purchasing ESET Mobile Antivirus.14Figure 6-1: Update settingsFigure 6-2: Downloading updatesNOTE: To prevent unnecessary bandwidth usage, virus signature database updates are issued as needed, when a new threat occurs. While virus signaturedatabase updates are free with your active license, you may be charged by your mobile service provider for data transfers. Please check with your mobile service provider. You can also update the virus signaturedatabase using your computer (see section 6, “Update“)7. Viewing Logs and statisticsThe Choose log section (Menu > View > Logs ) stores all file scan results and scan status reports, along with information about locked and infected files. Logs are created when a scan is initiated or when an infiltration is detected. All infected files are highlighted in red. At the end of each log entry is the reason why the file is included in the log.System logs contain the following information:• Time – Date and time of the event• Log name – Log file name (usually in the form EsetAV_log_number.log)• Scanned files• Actions performed or errors encountered during thescanFigure 7-1:Opening scan logFigure 7-2: Choose log15Figure 7-3: Log detailsThe statistics screen (Menu > View > Statistics )displays a summary of files scanned by the On‑Access scanner and a summary of SMS Messages received. In addition, the totals of files quarantined by the On‑Access scanner display here next to the sum of files in the Quarantine (this figure includes the results of theOn‑demand scan).Figure 7-4: Statistics8. TroubleshootingThis section provides solutions to common questions about ESET Mobile Antivirus.8.1 Connection to update server failedThis error message is displayed after an unsuccessful update attempt if the program is not able to contact the update servers.Try the following solutions:1. Check your Internet connectionOpen your Internet browser to to verify that you are connected to the Internet 2. Check if the program is using the correct update server. To check the server address, tap Menu > Settings > Update and you should see in the Internet server field.8.2 Unsuccessful InstallationIf an error message displays when you begininstallation, the most common cause is installing the wrong version of ESET Mobile Antivirus for your device (installing ESET Mobile Antivirus for Pocket PC on a Smartphone or vice versa). When downloading the installation file from the ESET homepage, please make sure you are downloading the correct product version for your device.Technical supportFor administrative assistance or technical support related to ESET Mobile Antivirus or any other ESET security product, our Customer Care specialists are available to help. To find a solution to your technical support issue, you can choose from the following options:To find answers to the most frequently asked questions, access the ESET Knowledgebase, here:.sg/support/faqThe Knowledgebase contains an abundance of useful information on resolving the most common and current issues, with easy to use drill down categories and an advanced keyword search.To contact ESET Customer Care, use the support request form available here:.sg/company/enquiry。
DrayTek VigorAP 960C 802.11ax Ceiling-mount Access
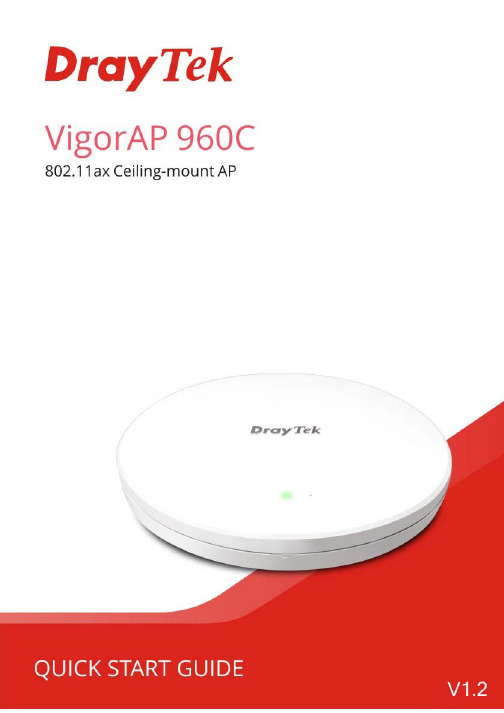
VigorAP 960C802.11ax Ceiling-mount AccessPointQuick Start GuideVersion: 1.2Firmware Version: V1.4.5(For future update, please visit DrayTek web site)Date: Dec. 21, 2022Intellectual Property Rights (IPR) InformationCopyrights © All rights reserved. This publication contains information that is protected by copyright. No part may be reproduced, transmitted, transcribed, stored ina retrieval system, or translated into any language without written permissionfrom the copyright holders.Trademarks The following trademarks are used in this document:●Microsoft is a registered trademark of Microsoft Corp.●Windows, Windows 8, 10, 11 and Explorer are trademarks of MicrosoftCorp.●Apple and Mac OS are registered trademarks of Apple Inc.●Other products may be trademarks or registered trademarks of theirrespective manufacturers.Safety Instructions and ApprovalSafety Instructions ●Read the installation guide thoroughly before you set up the device.●The device is a complicated electronic unit that may be repaired only beauthorized and qualified personnel. Do not try to open or repair thedevice yourself.●Do not place the device in a damp or humid place, e.g. a bathroom.●Do not stack the devices.●The device should be used in a sheltered area, within a temperaturerange of 0 to +40 Celsius.●Do not expose the device to direct sunlight or other heat sources. Thehousing and electronic components may be damaged by direct sunlight or heat sources.●Do not deploy the cable for LAN connection outdoor to preventelectronic shock hazards.●Keep the package out of reach of children.●When you want to dispose of the device, please follow local regulationson conservation of the environment.Warranty We warrant to the original end user (purchaser) that the device will be free from any defects in workmanship or materials for a period of two (2) yearsfrom the date of purchase from the dealer. Please keep your purchase receiptin a safe place as it serves as proof of date of purchase. During the warrantyperiod, and upon proof of purchase, should the product have indications offailure due to faulty workmanship and/or materials, we will, at our discretion,repair or replace the defective products or components, without charge foreither parts or labor, to whatever extent we deem necessary tore-store theproduct to proper operating condition. Any replacement will consist of a newor re-manufactured functionally equivalent product of equal value, and willbe offered solely at our discretion. This warranty will not apply if the productis modified, misused, tampered with, damaged by an act of God, or subjectedto abnormal working conditions. The warranty does not cover the bundled orlicensed software of other vendors. Defects which do not significantly affectthe usability of the product will not be covered by the warranty. We reservethe right to revise the manual and online documentation and to make changesfrom time to time in the contents hereof without obligation to notify anyperson of such revision or changes.Declaration of ConformityHereby, DrayTek Corporation declares that the radio equipment type VigorAP 960C is in compliance with Directive 2014/53/EU.The full text of the EU declaration of conformity is available at the following internet address: https:///VigorAP 960C/Document/CE/Manufacturer: DrayTek Corp.Address: No.26, Fushing Rd., Hukou, Hsinchu Industrial Park, Hsinchu 303, Taiwan Product: VigorAP 960CFrequency Information for Europe area:2.4GHz WLAN 2400MHz - 2483MHz, max. TX power: 19.95dBm5GHz WLAN 5150MHz - 5350MHz, max. TX power: 22.84dBm5470MHz - 5725MHz, max. TX power: 28.14dBmRequirements in AT/BE/BG/CZ/DZ/DK/EE/FR/DE/IS/IE/IT/EL/ES/CY/LV/LI/LT/ LU/HU/MT/NL/NO/PL/PT/RO/SI/SK/TR/FI/SE/CH/HR.5150MHz~5350MHz is for indoor use only.This product is designed for 2.4GHz and 5GHz WLAN network throughout the EC region.Declaration of ConformityHereby, DrayTek Corporation declares that the radio equipment type VigorAP 960C is in compliance with Regulation SI 2017 No. 1206.Manufacturer: DrayTek Corp.Address: No.26, Fushing Rd., Hukou, Hsinchu Industrial Park, Hsinchu 303, Taiwan Product: VigorAP 960CImporter: CMS Distribution Ltd: Bohola Road, Kiltimagh, Co Mayo, IrelandFrequency Information for UK area:2.4GHz WLAN 2400MHz - 2483MHz, max. TX power: 19.95dBm5GHz WLAN 5150MHz - 5350MHz, max. TX power: 22.84dBm5470MHz - 5725MHz, max. TX power: 28.14dBmRequirements in UK. 5150MHz~5350MHz is for indoor use only.This product is designed 2.4GHz and 5GHz WLAN network use in the UK & Ireland.Regulatory InformationFederal Communication Commission Interference StatementThis equipment has been tested and found to comply with the limits for a Class B digital device, pursuant to Part 15 of the FCC Rules. These limits are designed to provide reasonable protection against harmful interference in a residential installation. This equipment generates, uses and can radiate radio frequency energy and, if not installed and used in accordance with the instructions, may cause harmful interference to radio communications. However, there is no guarantee that interference will not occur in a particular installation. If this equipment does cause harmfulinterference to radio or television reception, which can be determined by turning the equipment off and on, the user is encouraged to try to correct the interference by one of the following measures:● Reorient or relocate the receiving antenna.● Increase the separation between the equipment and receiver.● Connect the equipment into an outlet on a circuit different from that to which the receiver is connected.●Consult the dealer or an experienced radio/TV technician for help.This device complies with Part 15 of the FCC Rules. Operation is subject to the following two conditions:(1) This device may not cause harmful interference, and(2) This device may accept any interference received, including interference that may cause undesired operation.Company nameABP International Inc.Address 13988 Diplomat Drive Suite 180 Dallas TX 75234 ZIP Code 75234E-mail*******************USA Local Representative Contact PersonMr. Robert MesserTel. 19728311600Caution ● Any changes or modifications not expressly approved by the grantee of this device could void the user's authority to operate the equipment.● Any changes or modifications not expressly approved by the party responsible for compliance could void the user's authority to operate this equipment.● This transmitter must not be co-located or operating in conjunction with any other antenna or transmitter.●Radiation Exposure Statement: This equipment complies with FCC radiation exposure limits set forth for an uncontrolled environment. This equipment should be installed and operated with minimum distance 20cm between the radiator & your body.External Power Supply ErP Information1 2A Manufacturer DVE DVEB Address No.5, Baogao Rd, XindianDist, New Taipei City(23144), TaiwanNo.5, Baogao Rd, XindianDist, New Taipei City(23144), Taiwan DSA-12PF09-12 FUK DSA-18PFR-12 FUKC Model identifierDSA-12PF09-12 FEU DSA-18PFR-12 FEU D Input voltage 100~240V 100~240VInput AC frequency 50/60Hz 50/60HzEOutput voltage DC 12.0V 12.0VF Output current 1.0A 1.5AG Output power 12.0W 18.0WH Average active efficiency 83.3% 85.5%I Efficiency at low load 10% 80.8% 83.7%J No-load power consumption 0.06W 0.07W*The external power supply used for each product will be model dependent.For more update, please visit .T a b l e o f C o n t e n t s1. Package Content (1)2. Panel Explanation (2)3. Installation (3)3.1 Ceiling-mount Installation (Wooden Ceiling) (3)3.2 Ceiling-mount Installation (Plasterboard Ceiling) (4)3.3 Suspended Ceiling (Lightweight Steel Frame) Installation (5)3.4 Wall-Mounted Installation (7)4. Connection and Configuration (8)4.1 Notifications for Hardware Connection (8)4.2 Connect to a Vigor Router using AP Management (9)4.3 Web Configurations (10)5. Customer Service (14)Be a Registered Owner (14)Firmware & Tools Updates (14)1.P a c k a g e C o n t e n tTake a look at the package content. If there is anything missed or damaged, please contact DrayTek or dealer immediately.VigorAP 960C Main Unit Ceiling mount bracket & Quick StartGuideT-Rail Mounting Kits(Used for suspended ceiling)Fixings and Screws(for ceiling mounting) RJ-45 Cable (Ethernet)Screw set (for wall mounting) The type of the power adapter depends on the country that the AP will be installed:UK-type Power Adapter EU-type Power AdapterUSA/Taiwan-type Power Adapter AU/NZ-type Power AdapterThe maximum power consumption is 11 Watt.2. P a n e l E x p l a n a t i o nLED Status ExplanationOn The system is in boot-loader mode. OffThe system is not ready or fails.Blue LEDBlinking The system is in AP mode and work normally.Green LED BlinkingThe system is in Mesh mode or Range Extender modeand works normally.Orange LED Blinking The system is in TFTP mode. Off Off VigorAP is turned off or not functioning. Interface Explanation Ethernet Port Connects to LAN or router.Supports PoE power & Gigabit (1000BaseT).Power Jack (DC IN) Connecter for a power adapter. Hole Explanation Factory Reset Restores the unit back to factory default settings.To use, insert a small item such as an unbent paperclip into the hole. You will feel the button inside depress gently. Hold it for 5 seconds. The VigorAP will restart with the factory default configuration and the LED will blink blue.Note● For the sake of security, make the accessory kit away fromchildren.● Remove the protective film from the access point before useto ensure ventilation.LEDFactory ResetEthernet PortPower Jack (DC IN)3. I n s t a l l a t i o nVigorAP can be installed under certain locations: wooden ceiling, plasterboard ceilings, light-weighted steel frame and wall.3.1 C e i l i n g -m o u n t I n s t a l l a t i o n (W o o d e n C e i l i n g )1. Place the bracket under the wooden ceiling and fasten two screws firmly (asshown in Figure below, Step 1). 2. When the bracket is in place, fasten two screws firmly (as shown in Figurebelow, Step 2) on the bottom of VigorAP. 3. Make the device just below the bracket. Put the screws installed in Step 2 onthe holes of the bracket (as shown in Figure below, Step 3). 4. Gently rotate the device to make screws slide into the notches of thebracket and move forward till it is firmly fixed.Step 1Step 2BracketStep 33.2 C e i l i n g -m o u n t I n s t a l l a t i o n (P l a s t e r b o a r d C e i l i n g )1. Place the bracket under the plasterboard ceiling and fasten two turnbuckles firmly (as shown in Figure below, Step 1).2. Make the screws pass through the bracket and insert into the turnbuckles (asshown in Figure below, Step 2). Fasten them to offer more powerful supporting force.3. When the bracket is in place, fasten two screws firmly (as shown in Figurebelow, Step 3) on the bottom of VigorAP.4. Make the device just below the bracket. Put the screws installed in Step 3 onthe screw holes of the bracket (as shown in Figure below, Step 4).5. Gently rotate the device to make screws slide into the notches of thebracket and move forward till it is firmly fixed.BracketStep 1Step 2Step 3Step 43.3 S u s p e n d e d C e i l i n g (L i g h t w e i g h t S t e e l F r a m e )I n s t a l l a t i o nYou cannot screw into ceiling tiles as they are weak and not suitable for bearing loads. Your VigorAP is supplied with mounts (T-Rail brackets) which attach directly to the metal grid (‘T-Rail’) of your suspended ceiling.1. Choose one set of T-Rail mounting kits from the bundled package.2. Put the T-Rail brackets on the holes of the bottom side of the device. Fastenthem with suitable screws.3. If a larger gap is required between the ceiling and the VigorAP, use theextension pieces to extend the height of the brackets.T-Rail BracketExtension PieceT-Rail BracketExtension Piece4.Attach the T-Rail brackets to the ceiling frame.NoteWarning: The screw set shown below is for wall mounting only. Do not use such set for ceiling mounting due to the danger offalling.3.4 W a l l -M o u n t e d I n s t a l l a t i o nFor wall-mounting, the VigorAP has keyhole type mounting slots on the underside. You can fit the AP at any axis (i.e. 12, 3, 6 or 9 O’Clock) to allow for cable entry from the most convenient location if you are using side entry – note the position of the side entry cable cutout.1. A template is provided on the VigorAP’s packaging box to enable you tospace the screws correctly on the wall.2. Place the template on the wall and drill the holes according to therecommended instruction.3. Fit screws into the wall using the appropriate type of wall plug (as shown inthe ceiling section) but do not use the ceiling bracket – the VigorAP hangs directly onto the screws.Wall (wooden, concrete, plasterboard or others)4.C o n n e c t i o n a n d C o n f i g u r a t i o n4.1N o t i f i c a t i o n s f o r H a r d w a r e C o n n e c t i o n●If required, remove the protective cap of VigorAP to create extra spacefor the cables to pass through.●Connect VigorAP to Vigor router (via LAN port) with Ethernet cable.●Connect VigorAP to PoE switch (via LAN port) with Ethernet cable. Forconnecting with PoE switch, do not connect the power adapter. VigorAPwill get the power from the switch directly.4.2C o n n e c t t o a V i g o r R o u t e r u s i n g A P M a n a g e m e n tYour VigorAP can be used with Vigor routers which support AP management (such as the Vigor2865 or Vigor2927 series). AP Management enables you to monitor and manage multiple DrayTek APs from a single interface.1.Connect one end of the power adapter to power port of VigorAP, and theother side into a wall outlet.2.Access into the web user interface of Vigor router. Here we take Vigor2865as an example. Open Central Management>>AP>>Status.3.Locate VigorAP 960C. Click the IP address assigned by Vigor router to accessinto web user interface of VigorAP 960C.4.After typing username and password (admin/admin), the main screen will bedisplayed.4.3W e b C o n f i g u r a t i o n sThis section will guide you to install the AP and make configuration for VigorAP.C o n n e c t e d A s a M e s h N o d e(i n M e s h N e t w o r k)❶Install VigorAP on to the ceiling.❷As a mesh node, settings related to VigorAP 960C must be configured by a remote Mesh Root (e.g., VigorAP 903) within the mesh network.The user must detect VigorAP 960C via a Mesh Root to add it as a meshnode.C o n n e c t e d A s a n A c c e s s P o i n tAs an access point, VigorAP 960C must be connected to a router and configured in AP (Access Point) / Range Extender mode.❶Install VigorAP on to the ceiling.❷Use a twisted-pair cable with RJ-45 plugs at both ends, and plug into Ethernet device (e.g., Vigor router) and Ethernet port of VigorAP.❸ There are two methods to configure VigorAP.Method 1:(a) First, open a web browser on your PC and type https://192.168.1.2. Apop-up window will open to ask for username and password.Note You may either simply set up your computer to get IPdynamically from the router or set up the IP address of thecomputer to be in the same subnet as the IP address ofVigorAP 960C.● If there is no DHCP server on the network, then VigorAP960C will have an IP address of 192.168.1.2.● If there is DHCP available on the network, then VigorAP960C will receive its IP address via the DHCP server.● If you connect to VigorAP by wireless LAN, you could tryto access the web user interface through .(b) After clicking Login, Quick Start Wizard for configuring wirelesssettings will appear as follows.(c)Follow the on-screen steps to finish the network connection.Method 2:(a)Use a mobile phone to scan the QR code named with DrayTek WirelessApp to download DrayTek Wireless APP.(b)After downloading, run the APP.(c)From the home page, click the Connect icon to access the Connectpage. Next, press the QR code icon next to Scan QR Code on yourphone screen to open the camera.Scan the QR code named with Connect SSID to access the web user interface (configuration wizard) of VigorAP 960C. (For iOS users, the SSID and the password will be shown first. Simply click the Connect button to access the web user interface of VigorAP.)5.C u s t o m e r S e r v i c eIf the device cannot work correctly after trying many efforts, please contact your dealer/DrayTek for further help right away. For any questions, please feel freetosende-mailto“*******************”.B e a R e g i s t e r e d O w n e rWeb registration is preferred. You can register your Vigor router viahttps://..F i r m w a r e&T o o l s U p d a t e sDue to the continuous evolution of DrayTek technology, all routers will beregularly upgraded. Please consult the DrayTek web site for more information on newest firmware, tools and documents.https://GPL Notice This DrayTek product uses software partially or completely licensedunder the terms of the GNU GENERAL PUBLIC LICENSE. The author ofthe software does not provide any warranty. A Limited Warranty isoffered on DrayTek products. This Limited Warranty does not coverany software applications or programs.To download source codes please visit:GNU GENERAL PUBLIC LICENSE:https:///licenses/gpl-2.0Version 2, June 1991For any question, please feel free to contact DrayTek technical*************************************************.14。
ELMO VP Receiver VPR-2 用户手册说明书
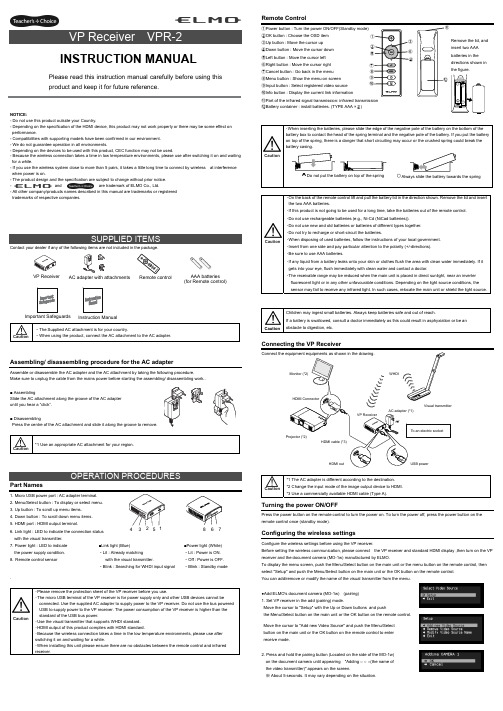
NOTICE:- Do not use this product outside your Country.- Depending on the specification of the HDMI device, this product may not work properly or there may be some effect on performance.- Compatibilities with supporting models have been confirmed in our environment. - We do not guarantee operation in all environments.- Depending on the devices to be used with this product, CEC function may not be used.- Because the wireless connection takes a time in low temperature environments, please use after switching it on and waiting for a while.- If you use the wireless system close to more than 5 pairs, it takes a little long time to connect by wireless at interference when power is on.- The product design and the specification are subject to change without prior notice. -and are trademark of ELMO Co., Ltd.- All other company/products names described in this manual are trademarks or registered trademarks of respective companies.Contact your dealer if any of the following items are not included in the package. Caution・The Supplied AC attachment is for your country.・When using the product, connect the AC attachment to the AC adapter.Assembling/ disassembling procedure for the AC adapterAssemble or disassemble the AC adapter and the AC attachment by taking the following procedure.Make sure to unplug the cable from the mains power before starting the assembling/ disassembling work..■ AssemblingSlide the AC attachment along the groove of the AC adapter until you hear a “click”.■ DisassemblingPress the centre of the AC attachment and slide it along the groove to remove. Caution *1 Use an appropriate AC attachment for your region.Part Names1. Micro USB power port : AC adapter terminal.2. Menu/Select button : To display or select menu.3. Up button : To scroll up menu items.4. Down button : To scroll down menu items.5. HDMI port : HDMI output terminal.6. Link light : LED to indicate the connection status with the visual transmitter.7. Power light : LED to indicate the power supply condition.8. Remote control sensor . Caution・Please remove the protection sheet of the VP receiver before you use.・The micro USB terminal of the VP receiver is for power supply only and other USB devices cannot beconnected. Use the supplied AC adapter to supply power to the VP receiver. Do not use the bus powered USB to supply power to the VP receiver. The power consumption of the VP receiver is higher than the standard of the USB bus power.・Use the visual transmitter that supports WHDI standard. ・HDMI output of this product complies with HDMI standard.・Because the wireless connection takes a time in the low temperature environments, please use after switching it on and waiting for a while.・When installing this unit please ensure there are no obstacles between the remote control and infrared receiver .Remote Control①Power button : Turn the power ON/OFF(Standby mode) ②OK button : Choose the OSD item ③Up button : Move the cursor up ④Down button : Move the cursor down ⑤Left button : Move the cursor left ⑥Right button : Move the cursor right ⑦Cancel button : Go back in the menu ⑧Menu button : Show the menu on screen ⑨Input button : Select registered video source ⑩Info button : Display the current link information⑪Part of the infrared signal transmission: infrared transmission⑫Battery container : install batteries. (TYPE AAA ×2)Caution・On the back of the remote control lift and pull the battery lid in the direction shown. Remove the lid and insert the two AAA batteries.・If this product is not going to be used for a long time, take the batteries out of the remote control. ・Do not use rechargeable batteries (e.g., Ni-Cd (NiCad batteries)). ・Do not use new and old batteries or batteries of different types together. ・Do not try to recharge or short-circuit the batteries.・When disposing of used batteries, follow the instructions of your local government. ・Insert from one side and pay particular attention to the polarity (+/-directions). ・Be sure to use AAA batteries.・If any liquid from a battery leaks onto your skin or clothes flush the area with clean water immediately. If it gets into your eye, flush immediately with clean water and contact a doctor.・The receivable range may be reduced when the main unit is placed in direct sunlight, near an inverter fluorescent light or in any other unfavourable conditions. Depending on the light source conditions, the sensor may fail to receive any infrared light. In such cases, relocate the main unit or shield the light source.CautionChildren may ingest small batteries. Always keep batteries safe and out of reach.If a battery is swallowed, consult a doctor immediately as this could result in asphyxiation or be an obstacle to digestion, etc.Connecting the VP ReceiverCaution *1 The AC adapter is different according to the destination. *2 Change the input mode of the image output device to HDMI. *3 Use a commercially available HDMI cable (Type A).Turning the power ON/OFFPress the power button on the remote control to turn the power on. To turn the power off, press the power button on the remote control once (standby mode).Configuring the wireless settingsConfigure the wireless settings before using the VP receiver.Before setting the wireless communication, please connect the VP receiver and standard HDMI display ,then turn on the VP receiver and the document camera (MO-1w) manufactured by ELMO.To display the menu screen, push the Menu/Select button on the main unit or the menu button on the remote control, then select "Setup" and push the Menu/Select button on the main unit or the OK button on the remote control. You can add/remove or modify the name of the visual transmitter from the menu.●Add ELMO's document camera (MO-1w) (pairing) 1. Set VP receiver in the add (pairing) mode.Move the cursor to "Setup" with the Up or Down buttons and push the Menu/Select button on the main unit or the OK button on the remote control.Move the cursor to "Add new Video Source" and push the Menu/Selectbutton on the main unit or the OK button on the remote control to enter receive mode.2. Press and hold the pairing button (Located on the side of the MO-1w) on the document camera until appearing "Adding ○ ○ ○(the name of the video transmitter)" appears on the screen.※ About 5 seconds. It may vary depending on the situation.CautionPlease read this instruction manual carefully before using this product and keep it for future reference.INSTRUCTION MANUALInstruction ManualVP Receiver3 4 5 6 7■Link light (Blue) ・Lit : Already matchingwith the visual transmitter.・Blink : Searching for WHDI input signal■Power light (White) ・Lit : Power is ON. ・Off : Power is OFF. ・Blink : Standby modeAC adapter with attachments AAA batteries (for Remote control)Important Safeguards ⑪Remove the lid, and insert two AAA batteries in the directions shown in the figure. 83. Move the cursor to "OK" on the screen and push the Menu/Select button on the main unit or the OK button on the remote control.Pairing will start. The image of the documemt camera displays automatically when pairing finishes.If the pairing stops please turn the power of VP receiver power off and the document camera, and restart pairing.4. If you wish to register more than 1 document camera, repeat form step 1. (Up to eight document cameras can be paired). Caution ・For details about the operation of the Visual transmitter, refer to the instruction manual of the respective Visual transmitter.■Remove the visual transmitter1. Select “Setup”. Then press the Menu/Select button on the main unit or the OK button on the remote control.2. Select “Remove Video Source” from the menu. Then press the Menu/Select button of the main unit or the OK button of the remote control.3. Select the name of Visual transmitter to remove. Then press the Menu/Select button of the main unit or the OK button of the remote control.4. Select “OK” and press the Menu/Select button or the OK button of the remote control.5. The confirmation of "Removing ○ ○ ○(Name of the transmitter) " appears, then select OK and press the Menu/Select button on the main unit or the OK button on remote control.■Modify the name of the visual transmitter1. Select “Setup”. Then press the Menu/Select button.2. Select “Modify Video Source Name” from the menu. Then press the Menu/Select button on the main unit or the OK button on the remote control.3. Select the registered visual transmitter. Then press the Menu/Select button on the main unit or the OK button on the remote control.4. (Using the main unit) Use the Up or Down buttons to move the cursor left and right to the character you want to change. Press the Menu/Select button and cursor will change colour to confirm selection. Now usethe up and down buttons to move to the new character you want to replace the old one with and press the Menu/Select button to confirm.(Using the remote control) This is the same procedure as the main unit, but use the remote control left or right button to move the cursor, the up or down buttons to change the character and press the OK button to confirm.5. Once completed press and hold the Menu/Select button on the main unit or press the OK button on the remote control. Then select “Save” and press the Menu/Select button on the main unit or the OK button on the remote control.Selecting the Video SourceDisplay the menu by pressing the Menu/Select button.A list of registered visual transmitters appears in the menu. Select the desired visual transmitter. Press the Menu/Select button to output the image of the selected visual Transmitter.In addition, by pressing the Input button on the remote control you can output video by selecting the video transmitter registration.When the message of “Please remove and register this ○○○ again” is shown while linking with the transmitter, please remove and add the transmitter again.Info MenuPush the Info button on the remote control, to display the current link status. The registered name of the video transmitter and signal strength of the video is displayed on the transmitter.How to wall mount this unitIf you install on a wall as shown below, please install with standard screws (not supplied).If trouble occurs or you have any queries, first check this section.If the problem persists, check your warranty and contact the dealer where you purchased the product.The AC adapter is disconnected. Check the connection between the AC adapter and the wall outlet.Is the visual transmitter registered? Add the visual transmitter.Equipment which uses the same frequency may cause radio interference. Check the surrounding radio frequency environment.The VP Receiver does not work.The AC adapter is disconnected from the VP Receiver.Check the connection between the AC adapter and the VP Receiver. HDMI cable is not connected properly.Firmly insert HDMI cable into the connector. The cable is damaged.Do not use a damaged cable. (Replace the cable)The input signal is out of the display range of the visual transmitter. Check the resolution.No image is displayed. orThe image is distorted.Equipment which uses the same frequency may cause radio interference.Check the surrounding radio frequency environment.HDMI cable is not connected properly.Firmly insert HDMI cable into the connector. The cable is damaged.Do not use a damaged cable.No audio from the visual transmitter is input. No sound is output when there is no audio input.No sound is output.The volume of the visual transmitter or the image output device is set to minimum. Turn up the volume.Caution・When error messages appear, follow the instructions to fix the error. ・If the problem persists, the product may be defective. Contact the dealer where you purchased the product for repair.PRODUCT SPECIFICATIONSOperating Temperature 0℃ - 40℃ (32°F – 104°F) Wireless Band Used 5190MHz - 5670MHz Communication DistanceApprox. 10m (32.8feet)(differs depending on the usage conditions) Power Supply AC adapterInput: 100V-240V, 50/60Hz(0.3A)Output: 5V, 2AStandards HDMI / WHDI standard compliance, including HDCP Transmitter registration 8 setsImage output:VGA (640x480)60Hz/75Hz, SVGA (800x600)60Hz/75Hz, XGA (1024x768) 60Hz/75Hz, WXGA (1280x768) 60Hz, WXGA (1280x800) 60Hz, SXGA (1280x1024) 60Hz/75Hz1152x864 (60Hz), 1280x960(60Hz) 480p, 576p, 720p, 1080i, 1080p HDMI OUT (Type A)Audio output: 192 kHz x 24 bitPower Consumption (Current) 7W( 5V / 1.4A) without AC adapterExternal DimensionsL83 x W80 x H31 (mm)L3 1/4” x W3 1/8” x H1 1/4”Weight 110g (0.24lb)6-14, Meizen-cho, Mizuho-ku, Nagoya, 467-8567, JapanELMO Europe SASHeadquartersImmeuble Elysées La Défense, 7C Place du Dôme, 92056 Paris La Défense, FRANCETel: +33 (0) 1 73 02 67 06 Fax: +33 (0) 1 73 02 67 10E-mail: *********************: /German BranchHansaallee 201, Haus 140549 Düsseldorf, GermanyTel: +49 (0)211 544756 40 Fax: +49 (0)211 544756 60E-mail: ******************** Web: http://www.elmo-germany.de/VPR-2(E2)_M R0-XexCAMERA 1CAMERA 2Pairing ButtonThe side panel of the MO-1wSelection order of the transmitterVP ReceiverPushSignal strengthName of the video transmitter Wall Mount screws are not included. Please use the screws as shown below. The screw head should be about 5mm from wall.When mounted to wall, the remote control operation range is 30 ° left and right , 30 ° to the front wall as shown in the figure.Please attach the screws to the wall. When attached to the wall of the hollow wall material such as gypsum board, please use the plug anchor corresponding to each of the wall material.The distance between screw and screw is 50mm.Then hook the screw hole on the unit.。
TMS320x28xx, 28xxx Enhanced Capture (ECAP) Module Reference Guide (Rev. A)

TMS320x28xx,28xxx Enhanced Capture(eCAP)ModuleReference GuideLiterature Number:SPRU807ANovember2004–Revised October20062SPRU807A–November2004–Revised October2006Submit Documentation FeedbackPreface (6)1Introduction (9)2Description (9)3Capture and APWM Operating Mode (10)4Capture Mode Description (12)4.1Event Prescaler (12)4.2Edge Polarity Select and Qualifier (13)4.3Continuous/One-Shot Control (13)4.432-Bit Counter and Phase Control (14)4.5CAP1-CAP4Registers (15)4.6Interrupt Control (15)4.7Shadow Load and Lockout Control (16)4.8APWM Mode Operation (17)5Capture Module-Control and Status Registers (18)6Register Mapping (26)7Application of the ECAP Module (27)7.1Example1-Absolute Time-Stamp Operation Rising Edge Trigger (28)7.2Example2-Absolute Time-Stamp Operation Rising and Falling Edge Trigger (30)7.3Example3-Time Difference(Delta)Operation Rising Edge Trigger (32)7.4Example4-Time Difference(Delta)Operation Rising and Falling Edge Trigger (34)8Application of the APWM Mode (36)8.1Example1-Simple PWM Generation(Independent Channel/s) (36)8.2Example2-Multi-channel PWM Generation With Synchronization (37)8.3Example3-Multi-channel PWM Generation With Phase Control (39)Appendix A Revision History (42)SPRU807A–November2004–Revised October2006Table of Contents3 Submit Documentation Feedback1Multiple eCAP Modules In A28x System (10)2Capture and APWM Modes of Operation (11)3Capture Function Diagram (12)4Event Prescale Control (13)5Prescale Function Waveforms (13)6Details of the Continuous/One-shot Block (14)7Details of the Counter and Synchronization Block (15)8Interrupts in eCAP Module (16)9PWM Waveform Details Of APWM Mode Operation (17)10Time-Stamp Counter Register(TSCTR) (18)11Counter Phase Control Register(CTRPHS) (18)12Capture-1Register(CAP1) (18)13Capture-2Register(CAP2) (18)14Capture-3Register(CAP3) (19)15Capture-4Register(CAP4) (19)16ECAP Control Register1(ECCTL1) (19)17ECAP Control Register2(ECCTL2) (21)18ECAP Interrupt Enable Register(ECEINT) (23)19ECAP Interrupt Flag Register(ECFLG) (24)20ECAP Interrupt Clear Register(ECCLR) (24)21ECAP Interrupt Forcing Register(ECFRC) (25)22Capture Sequence for Absolute Time-stamp and Rising Edge Detect (28)23Capture Sequence for Absolute Time-stamp With Rising and Falling Edge Detect (30)24Capture Sequence for Delta Mode Time-stamp and Rising Edge Detect (32)25Capture Sequence for Delta Mode Time-stamp With Rising and Falling Edge Detect (34)26PWM Waveform Details of APWM Mode Operation (36)27Multichannel PWM Example Using4eCAP Modules (38)28Multi-phase(channel)Interleaved PWM Example Using3eCAP Modules (40)4List of Figures SPRU807A–November2004–Revised October2006Submit Documentation Feedback1Time-Stamp Counter Register(TSCTR)Field Descriptions (18)2Counter Phase Control Register(CTRPHS)Field Descriptions (18)3Capture-1Register(CAP1)Field Descriptions (18)4Capture-2Register(CAP2)Field Descriptions (19)5Capture-3Register(CAP3)Field Descriptions (19)6Capture-4Register(CAP4)Field Descriptions (19)7ECAP Control Register1(ECCTL1)Field Descriptions (19)8ECAP Control Register2(ECCTL2)Field Descriptions (21)9ECAP Interrupt Enable Register(ECEINT)Field Descriptions (23)10ECAP Interrupt Flag Register(ECFLG)Field Descriptions (24)11ECAP Interrupt Clear Register(ECCLR)Field Descriptions (25)12ECAP Interrupt Forcing Register(ECFRC)Field Descriptions (25)13Control and Status Register Set (26)A-1Changes Made in This Revision (42)SPRU807A–November2004–Revised October2006List of Tables5 Submit Documentation FeedbackPrefaceSPRU807A–November2004–Revised October2006The enhanced capture(eCAP)module is used in systems where accurate timing ofexternal events is important.This guide describes the module and how to use it.Related Documentation From Texas InstrumentsThe following documents describe the TMS320C28x and related support tools and can be downloaded from the TI website():Data Manuals—SPRS357:contains the pinout,signalF28044device.User's Guides—SPRU051:describes theSCI,modulessupport digital communications between the CPU and other asynchronous peripherals that use thestandard non-return-to-zero(NRZ)format.SPRU059:describes the SPI-a ofprogrammed length(one to sixteen bits)to be shifted into and out of the device at a programmedbit-transfer rate.SPRU074:in electrically noisy environments.SPRU430:describes the centralfixed-point digital signal processors(DSPs).It also describes emulation features available on these DSPs.SPRU513:—describes the assembly languagetools code),assembler directives,macros,common object file format,and symbolic debugging directives for the TMS320C28x device.SPRU514:describes the TMS320C28x™C/C++code and produces TMS320DSP assembly language source code for the TMS320C28x device.SPRU566:describes the peripheral referenceguidesSPRU608:—describes the simulator,the instruction set of the C28x™core.6Preface SPRU807A–November2004–Revised October2006Submit Documentation FeedbackRelated Documentation From Texas Instruments SPRU625:SPRU712:describes the(DSPs).SPRU716:SPRU721:—describes the featuresand TMS320x280xdigital signal processor(DSP).SPRU722:describes the purpose andIt also describes other contents of the device on-chip boot ROM and identifies where all of the information is located withinthat memory.SPRU790:encoder to get position,direction,and speed information from a rotating machine in highperformance motion and position control systems.It includes the module description and registers SPRU791:switch mode power supply control,UPS(uninterruptible power supplies),and other forms of powerconversionSPRU807:describes theSPRU924:describes theApplication Reports—SPRAA58:—describes differences between theTexas assist in application migration fromthe281x to the280x.While the main focus of this document is migration from281x to280x,usersconsidering migrating in the reverse direction(280x to281x)will also find this document useful.SPRA550:describes a scenario of a3.3-V-only motor controllerissue of interfacing between3.3V and5V exists.On-chip3.3-V analog-to-digital converter(ADC)versus5-V ADC is also discussed.Guidelines for component layout and printed circuit board(PCB)design that can reduce systemnoise and EMI effects are summarized.SPRA820:presents the methodology foronline code is provided thatcontains functions for implementing the overflow detection on both DSP/BIOS™andnon-DSP/BIOS applications.SPRA861:provides an easy way to use thean arbitrary device.This application report presents a sample implementation of a user-defined device driver.SPRA873:signal processor(DSP)and DRV592power amplifier.The DSP implements a digitalproportional-integral-derivative feedback controller using an integrated12-bit analog-to-digitalconverter to read the thermistor,and direct output of pulse-width-modulated waveforms to theH-bridge DRV592power amplifier.A complete description of the experimental system,along withsoftware and software operating instructions,is provided.SPRU807A–November2004–Revised October2006Read This First7 Submit Documentation Feedback Related Documentation From Texas InstrumentsSPRA876:contains several programmingmodes of operation to help you come up to speed quickly in programming the eCAN.All projects and CANalyzer configuration filesare included in the attached SPRA876.zip file.SPRA953:describes the traditional and new thermal metrics and will puttheir to system level junction temperature estimation.SPRA958:coverson-chip flash memory.Requirements for both DSP/BIOS™and non-DSP/BIOS projects arepresented.Example code projects are included.SPRA963:describes reliability data forSPRA989:describes a method for improving the absolutefound on the F2810/F2811/F2812devices.This application note is accompanied by an example program(ADCcalibration.zip)that executesfrom RAM on the F2812eZdsp.SPRA991:them to evaluate system alternatives more effectively.TrademarksTMS320C28x,C28x are trademarks of Texas Instruments.8Read This First SPRU807A–November2004–Revised October2006Submit Documentation Feedback1Introduction2DescriptionReference GuideSPRU807A–November 2004–Revised October 2006The enhanced Capture (eCAP)module is essential in systems where accurate timingof external events is important.This reference guide is applicable for the eCAP found on the TMS320x28xx andTMS320x28xxx family of processors.This includes all Flash-based,ROM-based,andRAM-based devices within the 280xx and 28xxx family.Uses for eCAP include:•Speed measurements of rotating machinery (e.g.,toothed sprockets sensed via Hall sensors)•Elapsed time measurements between position sensor pulses•Period and duty cycle measurements of pulse train signals•Decoding current or voltage amplitude derived from duty cycle encoded current/voltage sensors The eCAP module described in this guide includes the following features:•32-bit time base with 10-nS time resolution with a 100-MHz system clock•4-event time-stamp registers (each 32bits)•Edge polarity selection for up to four sequenced time-stamp capture events•Interrupt on either of the four events•Single shot capture of up to four event time-stamps•Continuous mode capture of time-stamps in a four-deep circular buffer•Absolute time-stamp capture•Difference (Delta)mode time-stamp capture•All above resources dedicated to a single input pin•When not used in capture mode,the ECAP module can be configured as a single channel PWM output The eCAP module represents one complete capture channel that can be instantiated multiple times depending on the target device.In the context of this guide,one eCAP channel has the followingindependent key resources:•Dedicated input capture pin•32-bit time base (counter)•4x 32-bit time-stamp capture registers (CAP1-CAP4)•4-stage sequencer (Modulo4counter)that is synchronized to external events,ECAP pin rising/falling edges.•Independent edge polarity (rising/falling edge)selection for all 4events•Input capture signal prescaling (from 2-62)•One-shot compare register (2bits)to freeze captures after 1to 4time-stamp events•Control for continuous time-stamp captures using a 4-deep circular buffer (CAP1-CAP4)scheme •Interrupt capabilities on any of the 4capture eventsSPRU807A–November 2004–Revised October 2006Enhanced Capture (eCAP)Module 9Submit Documentation Feedback Capture and APWM Operating ModeMultiple identical eCAP modules can be contained in a280x system as shown in Figure1.The number of modules is device-dependent and is based on target application needs.Figure1.Multiple eCAP Modules In A28x System3Capture and APWM Operating ModeYou can use the eCAP module resources to implement a single-channel PWM generator(with32bitcapabilities)when it is not being used for input captures.The counter operates in count-up mode,providing a time-base for asymmetrical pulse width modulation(PWM)waveforms.The CAP1and CAP2 registers become the active period and compare registers,respectively,while CAP3and CAP4registers become the period and capture shadow registers,respectively.Figure2is a high-level view of both the capture and auxiliary pulse-width modulator(APWM)modes of10Enhanced Capture(eCAP)Module SPRU807A–November2004–Revised October2006Submit Documentation FeedbackCapture and APWM Operating Mode Figure2.Capture and APWM Modes of OperationA A single pin is shared between CAP and APWM functions.In capture mode,it is an input;in APWM mode,it is anoutput.B In APWM mode,writing any value to CAP1/CAP2active registers also writes the same value to the correspondingshadow registers CAP3/CAP4.This emulates immediate mode.Writing to the shadow registers CAP3/CAP4invokesthe shadow mode.4Capture Mode Description4.1Event PrescalerCapture Mode DescriptionFigure 3shows the various components that implement the capture function.Figure 3.Capture Function Diagram•An input capture signal (pulse train)can be prescaled by N =2-62(in multiples of 2)or can bypass the prescaler.This is useful when very high frequency signals are used as inputs.Figure 4shows a functional diagram and Figure 5shows the operation of the prescale function.12Enhanced Capture (eCAP)ModuleSPRU807A–November 2004–Revised October 2006ECAPx pin (from GPIO)PSoutECAPxPSout div 2PSout div 4PSout div 6PSout div 8PSout div 104.2Edge Polarity Select and Qualifier4.3Continuous/One-Shot ControlCapture Mode DescriptionFigure 4.Event Prescale ControlAWhen a prescale value of 1is chosen (i.e.ECCTL1[13:9]=0,0,0,0,0)the input capture signal by-passes the prescale logic completely.Figure 5.Prescale Function Waveforms•Four independent edge polarity (rising edge/falling edge)selection MUXes are used,one for each capture event.•Each edge (up to 4)is event qualified by the Modulo4sequencer.•The edge event is gated to its respective CAPx register by the Mod4counter.The CAPx register is loaded on the falling edge.•The Mod4(2bit)counter is incremented via edge qualified events (CEVT1-CEVT4).•The Mod4counter continues counting (0->1->2->3->0)and wraps around unless stopped.•A 2-bit stop register is used to compare the Mod4counter output,and when equal stops the Mod4counter and inhibits further loads of the CAP1-CAP4registers.This occurs during one-shot operation.CEVT1CEVT2CEVT3CEVT4ECCTL2[CONT/ONESHT]4.432-Bit Counter and Phase ControlCapture Mode DescriptionThe continuous/one-shot block controls the start/stop and reset (zero)functions of the Mod4counter via a mono-shot type of action that can be triggered by the stop-value comparator and re-armed via software control.Once armed,the eCAP module waits for 1-4(defined by stop-value)capture events before freezing both the Mod4counter and contents of CAP1-4registers (i.e.,time-stamps).Re-arming prepares the eCAP module for another capture sequence.Also re-arming clears (to zero)the Mod4counter and permits loading of CAP1-4registers again,providing the CAPLDEN bit is set.In continuous mode,the Mod4counter continues to run (0->1->2->3->0,the one-shot action is ignored,and capture values continue to be written to CAP1-4in a circular buffer sequence.Figure 6.Details of the Continuous/One-shot BlockThis counter provides the time-base for event captures,and is clocked via the system clock.A phase register is provided to achieve synchronization with other counters,via a hardware and software forced sync.This is useful in APWM mode when a phase offset between modules is needed.On any of the four event loads,an option to reset the 32-bit counter is given.This is useful for time difference capture.The 32-bit counter value is captured first,then it is reset to 0by any of the LD1-LD4signals.14Enhanced Capture (eCAP)ModuleSPRU807A–November 2004–Revised October 2006SYNCOSYNCECCTL2[SYNCI_EN]Delta−modeCTR−OVFCTR[31−0]4.5CAP1-CAP4Registers4.6Interrupt ControlCapture Mode DescriptionFigure 7.Details of the Counter and Synchronization BlockThese 32-bit registers are fed by the 32-bit counter timer bus,CTR[0-31]and are loaded (i.e.,capture a time-stamp)when their respective LD inputs are strobed.Loading of the capture registers can be inhibited via control bit CAPLDEN.During one-shot operation,this bit is cleared (loading is inhibited)automatically when a stop condition occurs,i.e.StopValue =Mod4.CAP1and CAP2registers become the active period and compare registers,respectively,in APWM mode.CAP3and CAP4registers become the respective shadow registers (APRD and ACMP)for CAP1and CAP2during APWM operation.An Interrupt can be generated on capture events (CEVT1-CEVT4,CTROVF)or APWM events (CTR =PRD,CTR =CMP).A counter overflow event (FFFFFFFF->00000000)is also provided as an interrupt source (CTROVF).The capture events are edge and sequencer qualified (i.e.,ordered in time)by the polarity select and Mod4gating,respectively.One of these events can be selected as the interrupt source (from the eCAPx module)going to the PIE.Seven interrupt events (CEVT1,CEVT2,CEVT3,CEVT4,CNTOVF,CTR=PRD,CTR=CMP)can be generated.The interrupt enable register (ECEINT)is used to enable/disable individual interrupt eventsources.The interrupt flag register (ECFLG)indicates if any interrupt event has been latched and contains the global interrupt flag bit (INT).An interrupt pulse is generated to the PIE only if any of the interrupt events are enabled,the flag bit is 1,and the INT flag bit is 0.The interrupt service routine must clear the global interrupt flag bit and the serviced event via the interrupt clear register (ECCLR)before any other interrupt pulses are generated.You can force an interrupt event via the interrupt force register (ECFRC).This is useful for test purposes.4.7Shadow Load and Lockout ControlCapture Mode DescriptionNote:The CEVT1,CEVT2,CEVT3,CEVT4flags are only active in capture mode (ECCTL2[CAP/APWM ==0]).The CTR=PRD,CTR=CMP flags are only valid in APWM mode (ECCTL2[CAP/APWM ==1]).CNTOVF flag is valid in both modes.Figure 8.Interrupts in eCAP ModuleIn capture mode,this logic inhibits (locks out)any shadow loading of CAP1or CAP2from APRD and ACMP registers,respectively.In APWM mode,shadow loading is active and two choices are permitted:•Immediate -APRD or ACMP are transferred to CAP1or CAP2immediately upon writing a new value.•On period equal,i.e.,CTR[31:0]=PRD[31:0]Enhanced Capture (eCAP)Module16SPRU807A–November 2004–Revised October 20064.8APWM Mode OperationAPRDACMPtimeCapture Mode DescriptionMain operating highlights of the APWM section:•The time-stamp counter bus is made available for comparison via 2digital (32-bit)comparators.•When CAP1/2registers are not used in capture mode,their contents can be used as Period and Compare values in APWM mode.•Double buffering is achieved via shadow registers APRD and ACMP (CAP3/4).The shadow register contents are transferred over to CAP1/2registers either immediately upon a write,or on a CTR =PRD trigger.•In APWM mode,writing to CAP1/CAP2active registers will also write the same value to thecorresponding shadow registers CAP3/CAP4.This emulates immediate mode.Writing to the shadow registers CAP3/CAP4will invoke the shadow mode.•During initialization,you must write to the active registers for both period and compare.Thisautomatically copies the initial values into the shadow values.For subsequent compare updates,i.e.,during run-time,you only need to use the shadow registers.Figure 9.PWM Waveform Details Of APWM Mode OperationThe behavior of APWM active high mode (APWMPOL ==0)is as follows:CMP =0x00000000,output low for duration of period (0%duty)CMP =0x00000001,output high 1cycle CMP =0x00000002,output high 2cycles CMP =PERIOD,output high except for 1cycle (<100%duty)CMP =PERIOD+1,output high for complete period (100%duty)CMP >PERIOD+1,output high for complete periodThe behavior of APWM active low mode (APWMPOL ==1)is as follows:CMP =0x00000000,output high for duration of period (0%duty)CMP =0x00000001,output low 1cycle CMP =0x00000002,output low 2cycles CMP =PERIOD,output low except for 1cycle (<100%duty)CMP =PERIOD+1,output low for complete period (100%duty)CMP >PERIOD+1,output low for complete period Capture Module-Control and Status Registers5Capture Module-Control and Status RegistersFigure10.Time-Stamp Counter Register(TSCTR)R/W-0LEGEND:R/W=Read/Write;R=Read only;-n=value after resetTable1.Time-Stamp Counter Register(TSCTR)Field Descriptions Bit(s)Field Description31:0TSCTR Active32-bit counter register that is used as the capture time-baseFigure11.Counter Phase Control Register(CTRPHS)R/W-0LEGEND:R/W=Read/Write;R=Read only;-n=value after resetTable2.Counter Phase Control Register(CTRPHS)Field Descriptions Bit(s)Field Description31:0CTRPHS Counter phase value register that can be programmed for phase lag/lead.This register shadowsTSCTR and is loaded into TSCTR upon either a SYNCI event or S/W force via a control edto achieve phase control synchronization with respect to other eCAP and EPWM time-bases.Figure12.Capture-1Register(CAP1)R/W-0LEGEND:R/W=Read/Write;R=Read only;-n=value after resetTable3.Capture-1Register(CAP1)Field DescriptionsBit(s)Field Description31:0CAP1This register can be loaded(written)by:)Time-Stamp(i.e.,counter value TSCTR)during a captureevent)Software-may be useful for test purposes/initialization)APRD shadow register(i.e.,CAP3)when used in APWM modeFigure13.Capture-2Register(CAP2)R/W-0LEGEND:R/W=Read/Write;R=Read only;-n=value after reset18Enhanced Capture(eCAP)Module SPRU807A–November2004–Revised October2006Capture Module-Control and Status RegistersTable4.Capture-2Register(CAP2)Field DescriptionsBit(s)Field Description31:0CAP2This register can be loaded(written)by:•Time-Stamp(i.e.,counter value)during a capture event•Software-may be useful for test purposes•APRD shadow register(i.e.,CAP4)when used in APWM modeNote:In APWM mode,writing to CAP1/CAP2active registers also writes the same value to thecorresponding shadow registers CAP3/CAP4.This emulates immediate mode.Writing tothe shadow registers CAP3/CAP4invokes the shadow mode.Figure14.Capture-3Register(CAP3)R/W-0LEGEND:R/W=Read/Write;R=Read only;-n=value after resetTable5.Capture-3Register(CAP3)Field DescriptionsBit(s)Field Description31:0CAP3In CMP mode,this is a time-stamp capture register.In APWM mode,this is the period shadow(APER)register.You update the PWM period value through this register.In this mode,CAP3(APRD)shadows CAP1.Figure15.Capture-4Register(CAP4)R/W-0LEGEND:R/W=Read/Write;R=Read only;-n=value after resetTable6.Capture-4Register(CAP4)Field DescriptionsBit(s)Field Description31:0CAP4In CMP mode,this is a time-stamp capture register.In APWM mode,this is the compare shadow(ACMP)register.You update the PWM compare value via this register.In this mode,CAP4(ACMP)shadows CAP2.Figure16.ECAP Control Register1(ECCTL1)R/W-0R/W-0R/W-0R/W-0R/W-0R/W-0R/W-0R/W-0R/W-0R/W-0R/W-0 LEGEND:R/W=Read/Write;R=Read only;-n=value after resetTable7.ECAP Control Register1(ECCTL1)Field Descriptions Bit(s)Field Value Description15:14FREE/SOFT Emulation Control00TSCTR counter stops immediately on emulation suspend Capture Module-Control and Status RegistersTable7.ECAP Control Register1(ECCTL1)Field Descriptions(continued) Bit(s)Field Value Description01TSCTR counter runs until=01x TSCTR counter is unaffected by emulation suspend(Run Free)13:9PRESCALE Event Filter prescale select00000Divide by1(i.e,.no prescale,by-pass the prescaler)00001Divide by200010Divide by400011Divide by600100Divide by800101Divide by10...11110Divide by6011111Divide by628CAPLDEN Enable Loading of CAP1-4registers on a capture event0Disable CAP1-4register loads at capture event time.1Enable CAP1-4register loads at capture event time.7CTRRST4Counter Reset on Capture Event40Do not reset counter on Capture Event4(absolute time stamp operation)1Reset counter after Capture Event4time-stamp has been captured(used in difference mode operation)6CAP4POL Capture Event4Polarity select0Capture Event4triggered on a rising edge(RE)1Capture Event4triggered on a falling edge(FE)5CTRRST3Counter Reset on Capture Event30Do not reset counter on Capture Event3(absolute time stamp)1Reset counter after Event3time-stamp has been captured(used in difference mode operation)4CAP3POL Capture Event3Polarity select0Capture Event3triggered on a rising edge(RE)1Capture Event3triggered on a falling edge(FE)3CTRRST2Counter Reset on Capture Event20Do not reset counter on Capture Event2(absolute time stamp)1Reset counter after Event2time-stamp has been captured(used in difference mode operation)2CAP2POL Capture Event2Polarity select0Capture Event2triggered on a rising edge(RE)1Capture Event2triggered on a falling edge(FE)1CTRRST1Counter Reset on Capture Event10Do not reset counter on Capture Event1(absolute time stamp)1Reset counter after Event1time-stamp has been captured(used in difference modeoperation)0CAP1POL Capture Event1Polarity select0Capture Event1triggered on a rising edge(RE)1Capture Event1triggered on a falling edge(FE)20SPRU807A–November2004–Revised October2006 Enhanced Capture(eCAP)ModuleCapture Module-Control and Status RegistersFigure17.ECAP Control Register2(ECCTL2)R-0R/W-0R/W-0R/W-0R/W-0R/W-0R/W-0R/W-0R/W-1R/W-1R/W-0 LEGEND:R/W=Read/Write;R=Read only;-n=value after resetTable8.ECAP Control Register2(ECCTL2)Field DescriptionsBit(s)Field Description15:11Reserved Reserved10APWMPOL APWM output polarity select.This is applicable only in APWM operating mode0Output is active high(i.e.,Compare value defines high time)1Output is active low(i.e.,Compare value defines low time)9CAP/APWM CAP/APWM operating mode select0ECAP module operates in capture mode.This mode forces the followingconfiguration:•Inhibits TSCTR resets via CTR=PRD event•Inhibits shadow loads on CAP1and2registers•Permits user to enable CAP1-4register load•CAPx/APWMx pin operates as a capture input1ECAP module operates in APWM mode.This mode forces the followingconfiguration:•Resets TSCTR on CTR=PRD event(period boundary•Permits shadow loading on CAP1and2registers•Disables loading of time-stamps into CAP1-4registers•CAPx/APWMx pin operates as a APWM output8SWSYNC Software-forced Counter(TSCTR)Synchronizing.This provides a convenientsoftware method to synchronize some or all ECAP time bases.In APWM mode,the synchronizing can also be done via the CTR=PRD event.0Writing a zero has no effect.Reading always returns a zero1Writing a one forces a TSCTR shadow load of current ECAP module and anyECAP modules down-stream providing the SYNCO_SEL bits are0,0.After writinga1,this bit returns to a zero.Note:Selection CTR=PRD is meaningful only in APWM mode;however,you canchoose it in CAP mode if you find doing so useful.7:6SYNCO_SEL Sync-Out Select00Select sync-in event to be the sync-out signal(pass through)01Select CTR=PRD event to be the sync-out signal10Disable sync out signal11Disable sync out signal5SYNCI_EN Counter(TSCTR)Sync-In select mode0Disable sync-in option1Enable counter(TSCTR)to be loaded from TSCTR register upon either a SYNCIsignal or a S/W force event.4TSCTRSTOP Time Stamp(TSCTR)Counter Stop(freeze)Control0TSCTR stopped1TSCTR free-running3RE-ARM One-Shot Re-Arming Control,i.e.wait for stop trigger.Note:The re-arm function isvalid in one shot or continuous mode.0Has no effect(reading always returns a0)SPRU807A–November2004–Revised October2006Enhanced Capture(eCAP)Module21 Submit Documentation Feedback。
技术手册 PD4-E (EtherCAT)说明书

技术手册 PD4-E现场总线: EtherCAT适用于以下设备:PD4-E591L42-E-65-1, PD4-E601L42-E-65-1, PD4-EB59CD-E-65-1适用于固件版本 FIR-v1748技术手册版本: 1.0.1内容1 简介 (7)1.1 版本信息 (7)1.2 版权、名称和联系信息 (7)1.3 预期用途 (7)1.4 保修和免责声明 (7)1.5 专业人员 (8)1.6 其他适用规则 (8)1.7 欧盟产品安全指令 (8)1.8 使用的图标 (8)1.9 文本中的强调 (8)1.10 数值 (9)1.11 位 (9)1.12 计数方向#箭头# (9)2 安全和警告通知 (10)3 技术细节和引脚分配 (11)3.1 环境条件 (11)3.2 尺寸图 (11)3.3 电性能和技术数据 (12)3.4 过热保护 (13)3.5 LED 信号 (15)3.6 引脚分配 (17)4 调试 (22)4.1 正在建立通信 (22)4.2 自动设置 (23)4.3 试运行 (26)4.4 特殊驱动模式#脉冲方向和模拟转速# (27)5 一般概念 (30)5.1 控制模式 (30)5.2 CiA 402 电源状态机 (33)5.3 用户定义单位 (38)5.4 运动范围限制 (42)5.5 循环时间 (42)6 工作模式 (44)6.1 标准定位 (44)6.2 速度 (52)6.3 标准速度 (53)6.6 插补位置模式 (65)6.7 循环同步位置 (66)6.8 循环同步速度 (68)6.9 循环同步转矩 (69)6.10 脉冲方向模式 (70)6.11 自动设置 (72)7 特殊功能 (73)7.1 数字输入和输出 (73)7.2 I2t 电机过载保护 (81)7.3 保存对象 (82)8 EtherCAT (87)9 使用NanoJ编程 (88)9.1 NanoJ 程序 (88)9.2 NanoJ 程序中的映射 (91)9.3 NanoJ 程序中的系统调用 (93)10 对象目录说明 (95)10.1 概述 (95)10.2 对象说明的结构 (95)10.3 对象说明 (95)10.4 数值说明 (96)10.5 说明 (97)1000h Device Type (98)1001h Error Register (98)1003h Pre-defined Error Field (99)1008h Manufacturer Device Name (103)1009h Manufacturer Hardware Version (104)100Ah Manufacturer Software Version (104)1010h Store Parameters (105)1011h Restore Default Parameters (108)1018h Identity Object (111)1020h Verify Configuration (113)1600h Receive PDO 1 Mapping Parameter (114)1601h Receive PDO 2 Mapping Parameter (117)1602h Receive PDO 3 Mapping Parameter (119)1603h Receive PDO 4 Mapping Parameter (121)1A00h Transmit PDO 1 Mapping Parameter (123)1A01h Transmit PDO 2 Mapping Parameter (126)1A02h Transmit PDO 3 Mapping Parameter (128)1A03h Transmit PDO 4 Mapping Parameter (131)1C00h Sync Manager Communication Type (133)1C12h Sync Manager PDO Assignment (135)1C13h Sync Manager PDO Assignment (136)1C32h Output Sync Manager Synchronization (138)1C33h Input Sync Manager Synchronization (139)1F50h Program Data (140)1F51h Program Control (142)1F57h Program Status (143)2034h Upper Voltage Warning Level (145)2035h Lower Voltage Warning Level (146)2036h Open Loop Current Reduction Idle Time (146)2037h Open Loop Current Reduction Value/factor (147)2038h Brake Controller Timing (147)2039h Motor Currents (149)203Ah Homing On Block Configuration (151)203Bh I2t Parameters (152)203Dh Torque Window (155)203Eh Torque Window Time Out (155)203Fh Max Slippage Time Out (156)2056h Limit Switch Tolerance Band (156)2057h Clock Direction Multiplier (157)2058h Clock Direction Divider (157)2059h Encoder Configuration (157)205Ah Absolute Sensor Boot Value (in User Units) (158)205Bh Clock Direction Or Clockwise/Counter Clockwise Mode (158)2084h Bootup Delay (159)2101h Fieldbus Module Availability (159)2102h Fieldbus Module Control (160)2103h Fieldbus Module Status (162)2110h EtherCAT Slave Status (164)2300h NanoJ Control (164)2301h NanoJ Status (165)2302h NanoJ Error Code (166)230Fh Uptime Seconds (167)2310h NanoJ Input Data Selection (168)2320h NanoJ Output Data Selection (169)2330h NanoJ In/output Data Selection (171)2400h NanoJ Inputs (172)2410h NanoJ Init Parameters (173)2500h NanoJ Outputs (174)2600h NanoJ Debug Output (175)2701h Customer Storage Area (176)2800h Bootloader And Reboot Settings (176)3202h Motor Drive Submode Select (178)3203h Feedback Selection (179)3204h Feedback Mapping (180)3210h Motor Drive Parameter Set (182)3212h Motor Drive Flags (186)3220h Analog Inputs (188)3221h Analogue Inputs Control (189)3240h Digital Inputs Control (189)3241h Digital Input Capture (192)3242h Digital Input Routing (194)3243h Digital Input Homing Capture (196)3250h Digital Outputs Control (197)3252h Digital Output Routing (200)3320h Read Analogue Input (201)3321h Analogue Input Offset (203)3322h Analogue Input Pre-scaling (204)33A0h Feedback Incremental A/B/I 1 (205)3700h Deviation Error Option Code (206)4012h HW Information (207)4013h HW Configuration (207)4014h Operating Conditions (208)4015h Special Drive Modes (210)4016h Factory Settings (212)6040h Controlword (214)6041h Statusword (215)6042h Vl Target Velocity (216)6043h Vl Velocity Demand (217)6044h Vl Velocity Actual Value (217)6046h Vl Velocity Min Max Amount (218)6048h Vl Velocity Acceleration (219)6049h Vl Velocity Deceleration (220)604Ah Vl Velocity Quick Stop (221)604Ch Vl Dimension Factor (222)605Ah Quick Stop Option Code (223)605Bh Shutdown Option Code (224)605Ch Disable Option Code (224)605Dh Halt Option Code (225)605Eh Fault Option Code (226)6060h Modes Of Operation (226)6061h Modes Of Operation Display (227)6062h Position Demand Value (227)6063h Position Actual Internal Value (228)6064h Position Actual Value (228)6065h Following Error Window (229)6066h Following Error Time Out (229)6067h Position Window (230)6068h Position Window Time (231)606Bh Velocity Demand Value (231)606Ch Velocity Actual Value (232)606Dh Velocity Window (232)606Eh Velocity Window Time (233)6071h Target Torque (233)6072h Max Torque (234)6074h Torque Demand (234)6075h Motor Rated Current (235)6077h Torque Actual Value (235)607Ah Target Position (236)607Bh Position Range Limit (236)607Ch Home Offset (237)607Dh Software Position Limit (238)607Eh Polarity (239)607Fh Max Profile Velocity (240)6080h Max Motor Speed (240)6081h Profile Velocity (241)6082h End Velocity (241)6083h Profile Acceleration (242)6084h Profile Deceleration (242)6085h Quick Stop Deceleration (243)6086h Motion Profile Type (243)6087h Torque Slope (244)608Fh Position Encoder Resolution (244)6090h Velocity Encoder Resolution (245)6091h Gear Ratio (246)6092h Feed Constant (247)6096h Velocity Factor (248)6097h Acceleration Factor (250)6098h Homing Method (251)6099h Homing Speed (251)609Ah Homing Acceleration (252)60A9h SI Unit Velocity (256)60B0h Position Offset (257)60B1h Velocity Offset (257)60B2h Torque Offset (258)60C1h Interpolation Data Record (258)60C2h Interpolation Time Period (259)60C4h Interpolation Data Configuration (260)60C5h Max Acceleration (262)60C6h Max Deceleration (263)60E4h Additional Position Actual Value (263)60E5h Additional Velocity Actual Value (264)60E6h Additional Position Encoder Resolution - Encoder Increments (265)60E8h Additional Gear Ratio - Motor Shaft Revolutions (266)60E9h Additional Feed Constant - Feed (268)60EBh Additional Position Encoder Resolution - Motor Revolutions (269)60EDh Additional Gear Ratio - Driving Shaft Revolutions (270)60EEh Additional Feed Constant - Driving Shaft Revolutions (271)60F2h Positioning Option Code (272)60F4h Following Error Actual Value (273)60F8h Max Slippage (274)60FAh Control Effort (274)60FCh Position Demand Internal Value (275)60FDh Digital Inputs (275)60FEh Digital Outputs (276)60FFh Target Velocity (277)6502h Supported Drive Modes (278)6503h Drive Catalogue Number (279)6505h Http Drive Catalogue Address (279)11 版权 (280)11.1 简介 (280)11.2 AES (280)11.3 MD5 (280)11.4 uIP (281)11.5 DHCP (281)11.6 CMSIS DSP Software Library (282)11.7 FatFs (282)11.8 Protothreads (282)11.9 lwIP (282)1 简介PD4-E 是一款带有集成控制器的无刷电机,防护等级为 IP65。
Moxa INJ-24 Series PoE 一体化插件指南说明书

P/N: 1802000240013 *1802000240013*INJ-24 SeriesQuick Installation GuideMoxa PoE InjectorEdition 4.0, February 2017Technical Support Contact Information/supportMoxa Americas:Toll-free: 1-888-669-2872 Tel: 1-714-528-6777 Fax: 1-714-528-6778 Moxa China (Shanghai office): Toll-free: 800-820-5036 Tel: +86-21-5258-9955 Fax: +86-21-5258-5505 Moxa Europe:Tel: +49-89-3 70 03 99-0 Fax: +49-89-3 70 03 99-99 Moxa Asia-Pacific:Tel: +886-2-8919-1230 Fax: +886-2-8919-1231 Moxa India:Tel: +91-80-4172-9088 Fax: +91-80-4132-10452017 Moxa Inc. All rights reserved.OverviewThe Moxa PoE Injector INJ-24 Series is a 1-port PoE injector that delivers both data and electrical power to Ethernet-enabled devices using a single Ethernet cable. The INJ-24 can supply up to 30 watts of power through the Ethernet port, and can power IEEE 802.3af/at compliant powered devices (PD), such as wireless access points or IP cameras, eliminating the need for additional wiring. The INJ-24 supports Gigabit communication, which is vital for high-speed and low-latency applications. The INJ-24 also offers a wide operating temperature range of -40 to 75°C, and is designed to withstand a high degree of vibration and shock. A rugged hardware design makes the INJ-24 perfect for ensuring that your Ethernet equipment can operate in critical industrial environments, such as in hazardous locations, and complies with FCC and CE standards. Wiring RequirementsYou should also pay attention to the following items:•Use separate paths to route wiring for power and devices. If power wiring and device wiring paths must cross, make sure the wires are perpendicular at the intersection point.NOTE: Do not run signal or communications wiring and power wiring in the same wire conduit. To avoid interference, wires with different signal characteristics should be routed separately.•You can use the type of signal transmitted through a wire to determine which wires should be kept separate. The rule of thumb is that wiring that shares similar electrical characteristics can bebundled together.•Keep input wiring and output wiring separated.•It is strongly advised that you label wiring to all devices in the system when necessary.Package ChecklistThe Moxa INJ-24 Series is shipped with the following items. If any of these items is missing or damaged, contact a Moxa customer service representative for assistance.•Moxa PoE Injector INJ-24•Quick installation guide (printed)•Warranty cardFeaturesHigh Performance Network Switching Technology•10/100/1000BaseT(X)•Provides up to 30 watts per PoE port•Active circuit protection•Auto disconnection for over voltage or under voltage•Power consumption detection and classification•Industrial-grade reliabilityRugged Design•Operating temperature range from 0 to 60°C, or extended operating temperature from -40 to 75°C for “T” models•IP30, rugged high-strength case•DIN-Rail or panel mounting abilityPanel Layout1.Heat dissipation orifices2.Terminal block for power input and grounding3.Moxa Logo4.Power LED5.Data input port6.PoE LED7.PoE output port8.DIN-RailMounting Dimensions (unit = mm)DIN-Rail MountingThe plastic DIN-Rail attachment plate should already be fixed to the back panel of INJ-24 when you take it out of the box. If you need to reattach the DIN-Rail attachment plate, make sure the stiff metal spring is situated towards the top, as shown in the figures below.STEP 1: Insert the top of the DIN-Rail into the slot. STEP 2:The DIN-Rail attachment unit will snap into place as shown below.To remove the INJ-24 from the DIN-Rail, insert a flat-blade screw driver horizontally into the DIN-Rail kit under the INJ-24, and then pull it upwards and release INJ-24 towards you away from the DIN-Rail.You may also take the following steps to remove the INJ-24 from the DIN-Rail.Step 1: Press the middle of the flat side of the mounting kit as indicated. Pull the INJ-24 downwards.Step 2:Release it towards you and away from the DIN-Rail.Grounding the INJ-24Grounding and wire routing help limit the effects of noise due to electromagneticinterference (EMI). Run the right most contact of the 3-contact terminal block to the grounding surface prior to connecting devices.Wiring the INJ-24’s Power OutputsThe two left-most contacts of the 3-contact terminal block connector on the INJ-24’s top panel are used for 24 VDC output. Top and front views of one of the terminal block connectors are shown here.STEP 1: Array Insert the negative/positive DC wires into the V-/V+terminals.STEP 2:To keep the DC wires from pulling loose, use a smallflat-blade screwdriver to tighten the wire-clampscrews on the front of the terminal block connector.STEP 3:Insert the plastic terminal block connector prongsinto the terminal block receptor, which is located onINJ-24’s top panel.LED IndicatorsSeveral LED indicators are located on the ING-24’s front panel. Thefunction of each LED is described in the table below.SpecificationsPatent /doc/operations/Moxa_Patent_Marking.pdf。
Furious True-D Diversity Receiver Rev.3 用户手册说明书

Furious True-D Diversity Receiver Rev.3 - User Manual Specified for the wildly popular FatsharkDominator V2 & V3 & SE and Fatshark HD V1, V2 &V3 goggles, Furious FPV debuts an all new take on built in receiver functionality, bringing forth new layers of race ready performance that will change the way you FPV.-1. Features:-True Diversity System Functionality-Smooth Switch Video Switching Technology-Raceband Channel Ready-Multiple Channel Modes - Auto, Manual & Working Modes-Ultra Compact Design-Designed for the FatShark Dominator V2/V3, Dominator HD V1/V2/V3, and Dominator SE goggles-Audible Buzzer Warnings/Alarms-Supports audio output-New user friendly layout and design-Increased resolution read signal for better antenna selection-Algorithm diversity upgrade for smooth and fast video switching speed-Easily update Firmware and custom logos with built-in FTDI with a convenient USB port - 3 selection buttons replace wheel button-Supports navigation with native Fatshark channel button-Configurable warning Buzzer: Time up, low signal …-Supports new user defined channels from 5300 to 5945 Ghz-Optimized hardware design for efficient cooling-Includes an SMA 45 and 90 degree adapter2. Specifications:-SMA Style: SMA Jack Connector / Female-Working Frequency: 5.8GHz-Application: FatShark Dominator V2/V3, Dominator HD V1/V2/V3, and Dominator SE goggles-Number of Channels: (40) Channels-USB port for firmware flashing-Supports utilizationof native Fatshark buttons to change channels-Save favorite channel, and set home channel-Built In Easy View LCD Screen for the ultimate in setup ease3. Installations:We have designed the modulesto not require any modificationofthe Fatshark goggles whichwould void the factory warrantywhen mounting the moduleexternally.Main module installation is thesame as any othermodule.Gently seat the 9-pinheader into the module bayreceptacleheaders.For those wanting the cleaninternal install we haveoptimallydesignedthe product torequire only minimalmodifications to yourgoggles. 4. Supported Fatshark Goggles:-Dominators-Dominator V2-Dominator V3-Dominator HD-Dominator HD V2-Dominator HD V3-Dominator SE-Attitude V3 - Some modification required.5. Product Layout:∙Red LEDSignal A is activatedwhen the True D module is usingantenna A.∙Blue LEDSignal A is activatedwhen the True D module is usingantenna B.∙Green LEDStatus is activatedwhen making selections with theTrue D module.∙USB Port is built-in for firmwareand logo updates with theintegrated FTDI.∙Up and Down Button utilized tomove the selection cursorindesired direction for menunavigation.∙Select Button confirms the highlighted selection.∙SMA Antenna Female compatiblewith many of the most popular antennas6. Usage: Diagram True-D rev.3Boot Logo: When powering on the Fatshark goggles, the OLED screen will display the Logo and the current firmware revision installed. You can proudly display your personalized call sign/pilot handle, logo, or team’s logo. You can request a custom logo ********************************.Active Channel: Show current band, channel number and frequency with your configured call sign. You may also use the native Fatshark channel navigation buttons to change channels.WORKING MODE: Utilize to show signals and strength on all detected channels.Allows you to select from “Favorite” channels that were saved in MANUAL MODE . Highly suggested to configure IMD5 or IMD6channels and access them here. Long press on center button provides you a selection menu that allows for saving or deleting the current configured channel. If you select save this will be the channel in which goggles and module power up upon start.MANUAL MODE: Use the Up or Downbuttons to manually select a channel. Single press to change your Channel selection - Buzzer will single beep to confirm.Long press the Up or Down buttons holding them for 2 seconds to change the Band selection -Buzzer will dual beep to confirm. This allows you to manually step through channels and receive visual indication of RSSI signal strength.SMART SEARCH: The True-D module will automatically find and show all the detected channels with corresponding signal strength.BAND SCANNER: Utilize to determine current broadcast band, channels, andfrequencies with a powered video transmitter. Identify a potential channel, band, and frequency with low noise for optimal use. Quickly find a pilot/VTX for spectating,troubleshooting, and even locating your lost drone by observing signal strength.SETTING: The setting menu is utilized to configure the True-D module functions.ALARM: Buzzer will warn you at configured low signal level. The options are as follows: None, 25%, 35% and 50%. If a low signal is detected on antenna A the buzzer will single beep and if a low signal is detected on antenna B the buzzer will dual beep.TIME UP: An audible warning can beconfigured to alert you when the goggles are left on. The options are as follows: None, 15 minutes, 30 minutes, 45 minutes.NEW F:Create user defined custom channels in the entire available range from 5300 to 5945 GHz. You may set the custom name with two characters: Alpha + Numeric (i.e. F1).SIGN:Configure your call sign/pilot name or text to be displayed on your goggles when flying. You may utilize up to 9 alphanumeric characters and symbols.FILTER: Configure sensitivity and switching speed for the diversity algorithm. Three choices are available for use: Low: Slow switching speed, which is optimal for long range. Normal: Is a Balanced mode, and the default recommend stock setting. High:Fast switching speed, which is optimal for short range.CALIBRATE: Utilize this menu to calibrate the True D modules for first time usage. It is highly recommend you re-calibrate when using a different video transmitter.EXIT: Utilize the Exit function to return to theChannel working space.7. Calibration:Why we need calibrate TrueD?A Diversity receiver system is two receivers built into a single package, allowing the pilot to choose two different antenna systems for maximum levels of video range & clarity. With two receivers used by algorithm diversity, you need to get constant numbers between the two individual modules for calculation of the best video signal in the goggles.How to do I calibrate the True-D diversity module?Step 1: Remove all antennas on True-D.Step 2: Turn on your VTX and set power working at 25mW if possible – This is the best power setting for calibrating True-D modules.Step 3: Put your True-D within a 2 meter or less radius.Step 4: Calibrate True D with the following steps:1. Plugin and turn on the True-D module.2. Press the middle Select button to open the navigation menu.3. Use Down button and scroll to the Setting menu.a.4. At the setting menu use the Down button to move cursor to select the Calibratefunctionand pressthe Select button.a.i. During the calibration you will briefly see a scanning process occur similarto the picture below.1.ii. After the automated process of calibration has completed a pop-up message will appear indicating the calibration is completeas is visible in the picture below.1.iii. If you would like to try once again you may select RE-CALIBRATE.1.iv. Select SAVE & EXIT to save process calibrate.1.v. Select EXIT to cancel this process.1.。
EN 300328 差

歐洲電信標準協會(European Telecommunications Standards Institute,簡稱ETSI)在2012年6月4日發布了ETSI EN 300 328 V1.8.1正式版本, 由於上一版本是在2006年發布的, 因此最新版本和前一版本有許多差異, 強制實施日期為2014年12月31日由於一般使用者在使用2.4GHz產品時, 容易被其他同頻段的產品干擾, 因此在最新版本中, 特別提出adaptive equipment, 而adaptive mode在1.8.1版法規中的定義如下:adaptive mode: mechanism by which equipment can adapt to its environment by identifying other transmissions present in the band在1.8.1版本中新增了一些測試項目, 分別針對adaptive equipment和non-adaptive equipment新增的測試項目, 其中有Medium Utilisation (MU) factor, Adaptivity, Receiver Blocking, 這些都是前一版本沒有的測項;此外, 舊版中Frequency range的測試項目1.8.1版本中被替換成99% Occupied Channel Bandwidth, 並且EN 300 328 V1.7.1EN 300 328 V1.8.1Technical requirements for Frequency Hopping equipment Description Clause RF output power 4.3.1.1 Duty Cycle, Tx-sequence, Tx-gap.. 4.3.1.2 Dwell time, Minimum Frequency Occupation and Hopping Seque4.3.1.3 Hopping Frequency Separation 4.3.1.4 Medium Utilisation (MU) factor 4.3.1.5 Adapitive 4.3.1.6 Occupied Channel Bandwidth.. 4.3.1.7 Transmitter unwanted emissions in the out-of-band domain 4.3.1.8 Transmitter unwanted emissions in the spurious domain. 4.3.1.9 Receiver spurious emissions 4.3.1.10 Receiver Blocking 4.3.1.11 Technical requirements for other types of Wide Band modulation . Description Clause RF output power. 4.3.2.1Power Spectral Density 4.3.2.2Duty Cycle, Tx-sequence, Tx-gap 4.3.2.3Medium Utilisation (MU) factor 4.3.2.4 Adapitive 4.3.2.5 Occupied Channel Bandwidth... 4.3.2.6 Transmitter unwanted emissions in the out-of-band domain . 4.3.2.7 Transmitter unwanted emissions in the spurious domain.. 4.3.2.8 Receiver spurious emissions 4.3.2.9 Receiver Blocking .. 4.3.2.10Figure 1: Transmit maskLimit≦ 20 dBmmaximum Tx-sequence time shall be 5 ms while the minimum Tx-gap time shall be 5 msmaximum dwell time is 400 msminimum separation of 100 kHzshall be 10 %Reference 4.3.1.6shall not be greater than 5 MHzFigure 1Table 1Table 2Table 3Limit≦ 20 dBm Table 1Frequency range10 dBm per MHz30 MHz to 47 MHzMaximum Tx-Sequence Time = Minimum Tx-gap Time = M,where M is inthe range of 3,5 ms to 10 msshall be 10 %.47 MHz to 74 MHzReference 4.3.2.5shall be less than 20 MHz74 MHz to 87,5 MHzFigure 387,5 MHz to 118 MHzTable 4118 MHz to 174 MHzTable 5174 MHz to 230 MHzTable 6230 MHz to 470 MHz470 MHz to 862 MHz862 MHz to 1 GHz1 GHz to 12,75 GHzTable 2Frequency range30 MHz to 1 GHz1 GHz to 12,75 GHzTable 3Equipment Type(LBT / non- LBT)LBTNon-LBTNOTE 1: The highest blockingfrequency, while the lowest blocking frequency s NOTE 2: A typical value which can beFigure 3: Transmit maskTable 4: TrFrequency range30 MHz to 47 MHz47 MHz to 74 MHz74 MHz to 87,5 MHz87,5 MHz to 118 MHz118 MHz to 174 MHz174 MHz to 230 MHz230 MHz to 470 MHz470 MHz to 862 MHz862 MHz to 1 GHz1 GHz to 12,75 GHzTable 5:Frequency range30 MHz to 1 GHz1 GHz to 12,75 GHzTable 6Equipment Type(LBT / non- LBT)LBTNon-LBTNOTE 1: The highest blockingwhile the lowest blocking frequency shall be use NOTE 2: A typical value which can beMaximum power,e.r.p.(≤1GHz)e.i.r.p. (> 1 GHz)Bandwidth-36 dBm100 kHz -54 dBm 100 kHz-36 dBm100 kHz -54 dBm100 kHz -36 dBm100 kHz -54 dBm100 kHz -36 dBm100 kHz -54 dBm100 kHz -36 dBm100 kHz -30 dBm 1 MHzMaximum powere.r.p.(≤1GHz)e.i.r.p. (> 1 GHz)Measurement bandwidth -57 dBm100 kHz -47 dBm 1 MHzable 3: Receiver Blocking parametersWanted signalmean powerfrom companionBlocking signal frequency Blocking signal power Type of interfering device [MHz][dBm]signal2 395 or 2 488,5-30CW-30 dBm (see note 1)4: Transmitter limits for spurious emissionsMaximum power,e.r.p.(≤1GHz)e.i.r.p. (> 1 GHz)Bandwidth -36 dBm100 kHz -54 dBm100 kHz -36 dBm100 kHz -54 dBm100 kHz -36 dBm100 kHz -54 dBm100 kHz -36 dBm100 kHz -54 dBm100 kHz -36 dBm100 kHz -30 dBm 1 MHzle 5: Spurious emission limits for receiversMaximum power,e.r.p.Measurement bandwidth -57 dBm100 kHz -47 dBm 1 MHzable 6: Receiver Blocking parameterssufficient tomaintain thelink (see noteking frequency shall be used for testing the lowest operating hoppinge the lowest blocking frequency shall be used for testing the highest hoppingn be used in most cases is -50 dBm/MHz.Wanted signal mean powerfrom companionBlocking signal frequency Blocking signal power Type of interfering device[MHz][dBm]signal 2 395 or 2 488,5-30CW-30 dBm (see note 1)sufficient tomaintain thelink (see noteking frequency shall be used for testing the lowest operating channel,blocking frequency shall be used for testing the highest operating channel.n be used in most cases is -50 dBm/MHz.。
eset 激活码

密 码: c6jr4pnhp4
适用版本:EAV
有效期至:2012-01-18
用户名: EAV-49341311
密 码: v75hfurdae
适用版本:EAV
有效期至:2012-01-18
用户名: EAV-49323091
密 码: abn2ufj5ku
用户名: EAV-49051632
密 码: 7j8s4aja6b
适用版本:EAV
有效期至:2012-01-08
用户名: EAV-49050917
密 码: adfur6hesp
适用版本:EAV
有效期至:2012-01-08
适用版本:EAV
有效期至:2012-01-22
用户名: EAV-49067574
密 码: b6f65ujtac
适用版本:EAV
有效期至:2012-01-20
用户名: EAV-49428730
密 码: jnat22vdaj
适用版本:EAV
有效期至:2012-01-20
用户名: EAV-49443465
密 码: 6df3tc45nt
适用版本:EAV
有效期至:2012-01-22
用户名: EAV-49442171
密 码: u55vb87tu8
适用版本:EAV
有效期至:2012-01-22
用户名: EAV-49442139
密 码: ae5pf4fmxa
用户名: EAV-49545857
密 码: amx85asmvs
适用版本:EAV
有效期至:2012-01-27
欧尼臣 ESM-BT4.. 系列安全继电器 使用说明书
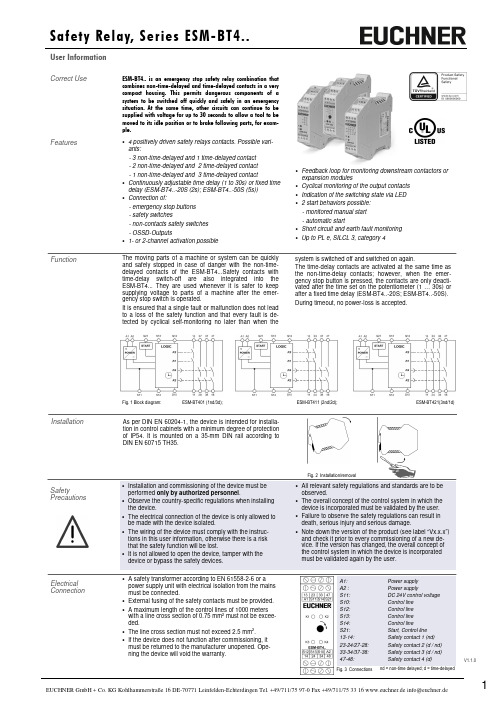
V1.1.0• Feedback loop for monitoring downstream contactors orexpansion modules• Cyclical monitoring of the output contacts • Indication of the switching state via LED • 2 start behaviors possible: - monitored manual start - automatic start• Short circuit and earth fault monitoring • Up to PL e, SILCL 3, category 4Correct UseESM-BT4.. is an emergency stop safety relay combination that combines non-time-delayed and time-delayed contacts in a very compact housing. This permits dangerous components of a system to be switched off quickly and safely in an emergency situation. At the same time, other circuits can continue to be supplied with voltage for up to 30 seconds to allow a tool to be moved to its idle position or to brake following parts, for exam-ple.Features• 4 positively driven safety relays contacts. Possible vari-ants:- 3 non-time-delayed and 1 time-delayed contact - 2 non-time-delayed and 2 time-delayed contact - 1 non-time-delayed and 3 time-delayed contact• Continuously adjustable time delay (1 to 30s) or fixed time delay (ESM-BT4..-20S (2s); ESM-BT4..-50S (5s)) • Connection of:- emergency stop buttons - safety switches- non-contacts safety switches - OSSD-Outputs• 1- or 2-channel activation possibleFunctionThe moving parts of a machine or system can be quickly and safely stopped in case of danger with the non-time-delayed contacts of the ESM-BT4...Safety contacts with time-delay switch-off are also integrated into the ESM-BT4... They are used whenever it is safer to keep supplying voltage to parts of a machine after the emer-gency stop switch is operated.It is ensured that a single fault or malfunction does not lead to a loss of the safety function and that every fault is de-tected by cyclical self-monitoring no later than when theInstallationAs per DIN EN 60204-1, the device is intended for installa-tion in control cabinets with a minimum degree of protection of IP54. It is mounted on a 35-mm DIN rail according to DIN EN 60715 TH35.system is switched off and switched on again. The time-delay contacts are activated at the same time asthe non-time-delay contacts; however, when the emer-gency stop button is pressed, the contacts are only deacti-vated after the time set on the potentiometer (1 … 30s) or after a fixed time delay (ESM-BT4..-20S; ESM-BT4..-50S).During timeout, no power-loss is accepted.Electrical ConnectionFig. 1 Block diagram: ESM-BT401 (1nd/3d); ESM-BT411 (2nd/2d); ESM-BT421(3nd/1d)V1.1.0Depending on the application or the result of the risk assessment according to EN ISO 13849-1, the device must be wired as shown in Fig. 1 to Fig. 11. Non-time delayed contacts can be used up to category 4, PL e, time-delayed safety contacts up to category 3, PL e.ApplicationsFig. 3:Single-channel emer-gency stop circuit with earth fault monitoring. (category 1, up to PL c)Fig. 2:Two-channel emergen-cy stop circuit with earth fault monitoring.(category 3, up to PL d)Fig. 1:Two-channel emergen-cy stop circuit with short circuit and earth fault monitoring.(category 4, up to PL e)Fig. 4:Two-channel sliding guard monitoring with short circuit and earth fault monitoring.(category 4, up to PL e)Emergency StopCircuitFig. 7:Automatic start (e.g. for application with a safety door).Max perm. delay during closing of the safety switches on S12 and S13: S12 before S13: 300ms; S13 before S12: anyWarning:Safety contacts switch when the power supply is connected.Fig. 8:Feedback loop for monitored manual start:The feedback loop monitors contactors or the expansion modules .Starting Behavior Feedback LoopNote: The items listed under “Electrical connection” must be observed during commissioning . Commissioning Procedure1. Wiring emergency stop circuit:Wirethe emergency stop circuit according to the requiredPerformance Level determined (see Fig. 1 to Fig 5). 2. Wiring start circuit:Wire the start circuit according to Fig. 6 or Fig. 7 to set the starting behavior. Warning:If “Automatic start” is set, bear in mind that the safety con-tacts will switch immediately after the power supply is connected.If“Monitored manual start” is set, the start button must be opened after wiring. 3. Wiring feedback loop:If your application provides for external contactors or ex-pansion modules, connect them to the device according to Fig. 8 or Fig. 9.4. Wiring power supply:Connect the power supply to terminals A1 and A2 (Fig. 10). Warning: Wiring only in de-energized state. 5. Set time delay:Set the desired time delay on the rotary knob (not for fixed delay time)Warning:Scale divisions should be regarding only as a setting aid. Always make shure to measure the delay time. 6. Starting the device:Switch on the operating voltage. Warning:If the “Automatic start” starting behavior is set, the safety contacts will close immediately.If the “Monitored manual start” starting behavior is set, close the start button to close the safety contacts. LEDs K1, K2, K3 and K4 are lit. 7. Triggering safety function:Open the emergency stop circuit by actuating the connec-ted safety switch. The safety contacts open immediately. Warning: Measure the delay-time. 8. Reactivation:Close the emergency stop circuit. If “Automatic start” is selected, the safety contacts will close immediately.If the “Monitored manual start” starting behavior is set, close the start button to close the safety contacts.Warning:In order to activate earth fault monitoring, the PE must be connected only to the power supply unit in accordance with EN60204-1.Corresponded to the application, the starting circuit have to be wired according to Fig. 6 or Fig. 7.Fig. 5:Two-channel emergency stop with pnp-outputs/OSSD-outputs with short circuit monitoring. (category 4, up to PL e)Fig. 9:Feedback loop for automatic start: The feedback loop monitors contac-tors or the expansion modules .Power supply andSafety contactsFig. 10:Power supply A1 and A2.(Power supply according to techn. data )Fig. 11:Connecting load to safety contacts.(Figure shows example.Voltage …+V“ according to techn. data)Fig. 6:Manual start.User InformationV1.1.0MaintenanceDevice cannot be switched on again after an emergency stop:• Check whether the emergency stop circuit was closed again.• Was the start button opened before closing of the emer-gency stop circuit (with manual start)? • Is the feedback loop closed?If the fault still exists, perform the steps listed under “Commissioning Procedure”.If these steps do not remedy the fault either, return the device to the manufacturer for examination.Opening the device is impermissible and will void the warranty.What to Do in Case of a Fault?The device must be checked once per month for proper function and for signs of tampering and bypassing of the safety function (to do this, check the wiring of the device and activate the emergency stop function. Check the delay time).The device is otherwise maintenance free, provided that it was installed properly.Note:Additional data can be requested from the manufacturer for applications that deviate from these conditions.SafetyCharacteristics According to EN ISO 13849-1The device is certified according to EN ISO 13849-1 up to a Performance Level of PL e.Device does not switch on:• Check the wiring by comparing it to the wiring diagrams. • Check the safety switch used for correct function and adjustment.• Check whether the emergency stop circuit is closed. • Check whether the start button (with manual start) is closed.• Check the operating voltage at A1 and A2. • Is the feedback loop closed?*) If several ESM-BT4.. devices are closely spaced under load, the max. total current at the ambient temperature of T=20 °C: 9 A; at T=30 °C: 3 A; at T=40 °C =1 A. If these currents are exceeded, a spacing of 5 mm between the devices must be observed.Safety characteristics according to EN ISO 13849-1 for all variants of ESM-BT4 Load (DC-13; 24 V) <= 0.1 A <= 1 A <= 2 A T10d [years] 20 20 20 Category: Time-delay Non-time-delay 3 4 3 4 3 4 PLe e e PFHd [1/h]: Time-delay Non-time-delay8,84E-08 4,22E-088,84E-08 4,22E-088,84E-08 4,22E-08 nop [cycle / year]<= 500,000<= 350,000<= 100,000User InformationV1.1.0Dimension DrawingS u b j e c t t o t e c h n i c a l m o d i f i c a t i o n s , n o r e s p o n s i b i l i t y i s a c c e p t e d f o r t h e a c c u r a c y o f t h i s i n f o r m a t i o n . © E U C H N E R G m b H + C o . K G 109074-09-02/18 (T r a n s l a t i o n o f t h e O r i g i n a l O p e r a t i n g I n s t r u c t i o n s ) Fixed TerminalsPlug-InTerminals。
ES102用户手册说明书
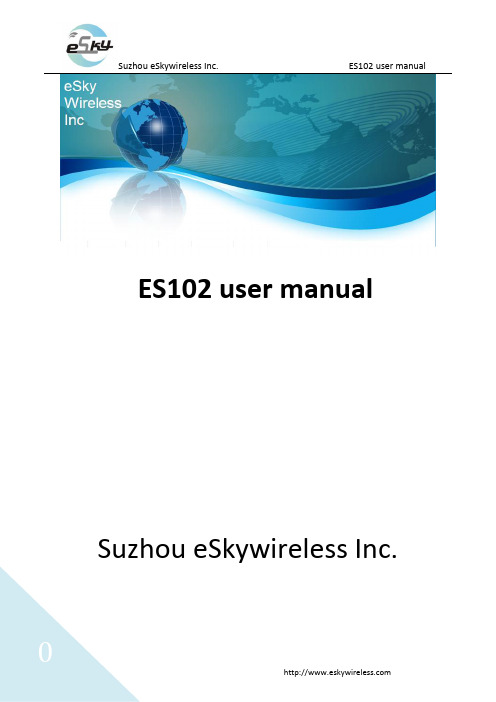
ES102 user manual Suzhou eSkywireless Inc.Information to UserThis device complies with part 15 of the FCC Rules. Operation is subject to the following two conditions: (1) This device may not cause harmful interference, and (2) this device must accept any interference received, including interference that may cause undesired operation.NOTE:This equipment has been tested and found to comply with the limits for a Class B digital device, pursuant to part 15 of the FCC Rules. These limits are designed to provide reasonable protection against harmful interference in a residential installation. This equipment generates uses and can radiate radio frequency energy and, if not installed and used in accordance with the instructions, may cause harmful interference to radio communications. However, there is no guarantee that interference will not occur in a particular installation. If this equipment does cause harmful interference to radio or television reception, which can be determined by turning the equipment off and on, the user is encouraged to try to correct the interference by relocating the receiving antenna or consulting the dealer or an experienced radio/TV technician for help.Mobile RF WarningThis equipment complies with FCC radiation exposure limits set forth for an uncontrolled environment. This equipment should be installed and operated with minimum distance 20cm between the radiator & your body.Changes and Modification Warning StatementAny Changes or modifications not expressly approved by the party responsible for compliance could void the user's authority to operate the equipment.1 PREPARE before INSATLLATION1.1 Product Display(image of ES102)(wire harness of ES102)1.2Packaging InspectionOpen the box, check the terminal model is correct and the accessories are complete. Otherwise, please contact your dealer.1.3Install SIM Card1.3.1Selection of SIM CardThe ES102 is a GPS/GPRS terminal, and it needs a GSM/GPRS SIM card. please reference dealer’s opinion to select carrier.1.3.2Installation SIM cardOpen the terminal cover, and put the metal side of SIM card face down and then fasten the card slot cover.1.4Power OnThe terminal standard power supply is 6V-34V. the red line is the positive power supply and the black line is the negative power supply.Note:Please select the negative power line grounding alone.2 Steps of AT Setting before testsStart hyper-terminal connection as follows.1)select the comm port of PC through which ES102 is connected with PC, as the follows2) In Port Settings, change communication speed (bits per second) to 115200bps,3)Final step is the certain AT settings necessary after 1st running of downloaded program.3.1) Start connection first3.2) Restart ES1023.3) After you see the "IIII"as the following picture, start setting.3 INSTALL and OPERATION3.1 Installation MethodThe terminal is GPS positioning products, it is recommended that you follow the instructions to install.Note:1) The following installation order, please do not inverted.2) During the installation process, please do not supply the terminal.The terminal installation is divided into hidden installation and open installation.When the terminal is using special vehicles, hidden installation is recommended. Otherwise, open installation is chosen. (To avoid thieves’ damage, the installation location should be hidden)(cigarette lighter)(OBD)①Battery connector②Power connector, connecting terminal with the power connector of wire harness, as picture above.③I/O connector, connecting terminal with the I/O connector of wire harness, as picture above.④I/O lines⑤Power lines, it can connect with cigarette lighter or OBD, as picture above.3.1.1 Open InstallationThe power connecting line we selected is provided by original cigarette lighter cord.3.1.2 Hidden installationThe power connecting line we selected is provided by original the main power core. And the red line has a fuse box (3A fuse) which can play a short circuit overcurrent protection role.3.2Installation SiteThe places that we suggest to install:①The bottom of the front windshield decorative plates②Around of front dashboard (epidermis as nonmetallic material)③Below the decorative panels of rear windshield④Inside the front bumper (should pay attention of water)⑤Below the wipers plate (should pay attention of water)3.3 Installation Notes① Avoid put together with the emission source, for example, reversing radar, anti-theft devices and other on-board communications equipment.② As for fixing the terminal, you can bound with ties or stick with wide sponge strength double-faced adhesive.③ The terminal has GSM antenna and GPS antenna,so the installation should ensure that the ES102face up (that is GPS toward the sky). Besides, there is no on-metallic object that obscures above the terminal.④If your car’s windshield pasted with metal insul ation layer or the heating layer, GPS receiving signal will be weakened, and it may cause GPS work abnormal. So please change the location you installed the terminal.。
- 1、下载文档前请自行甄别文档内容的完整性,平台不提供额外的编辑、内容补充、找答案等附加服务。
- 2、"仅部分预览"的文档,不可在线预览部分如存在完整性等问题,可反馈申请退款(可完整预览的文档不适用该条件!)。
- 3、如文档侵犯您的权益,请联系客服反馈,我们会尽快为您处理(人工客服工作时间:9:00-18:30)。
ES249
机制,芯片被周期性地“唤醒”并且根据预定好的磁场强度阈值检测外界穿过霍尔器件磁场强度 的大小。如果磁通密度高于“工作点”阈值或者低于“释放点”阈值,则输出晶体管被驱动并转 变成与之相对应的状态。而在“休眠”周期中,输出晶体管被锁定在其先前的状态下。在电池供 电应用中,这种设计对于延长工作寿命提供了最好支持。 当垂直于霍尔传感器的南极磁场超过工作点时,ES249 输出晶体管转变为低电平(输出导 通) , 导通后输出电压是 VDS。 当磁场减弱到低于释放点 BRP 时, 输出晶体管截止 (输出高电平) 。 磁场工作点与释放点之间的差距为器件的磁滞(BHYS) 。内置磁滞防止了在转换点附近的输出振 荡,而且即使在外部机械振动和电器噪声的情况下也能得到清晰的输出转换。
6. 极限参数
参数
电源电压(工作时) 电源电流 输出电压 输出电流 工作温度范围 储存温度范围 静电击穿电压
符号
VDD IDD VOUT IOUT TA TS -
参数值
5.5 70 5.5 5 -40 to 85 -50 to 150 4000
单位
V μA V mA ℃ ℃ V
注意:应用不要超过最大额定值,以防止损坏。长时间工作在最大额定值的情况下可能影响器件 的可靠性。
©2009-2013 易良盛科技(天津)有限公司
Rev3.0.1.130503
5/5Biblioteka 3249mm1
1.70 2.10
1.60 2.65 1.70 2.95
2
Side View
2.82 3.02 0.70 0.90 3.00 0.35 0.50 3.00 0.00 0.10 3.00
End View
0.70 0.80 3.00
0.08 0.20 3.00 0.20 MIN 3.00
SOT-23 封装 Hall 器件位置
Bottom View of TSOT-23 Package Chip
3
0.95 0.80 3.00 2 3 1 2 1.50 1.40
0.36 0.46
©2009-2013 易良盛科技(天津)有限公司
Rev3.0.1.130503
3/5
数据手册
微功耗高灵敏度霍尔开关
0.4
V μS μS
600
8.
磁场特性
测试条件:TA = 25℃,VDD=3VDC
©2009-2013 易良盛科技(天津)有限公司 Rev3.0.1.130503 2/5
数据手册
微功耗高灵敏度霍尔开关
参数
工作点 释放点 磁滞
ES249
最小值 典型值
150 50 90 60 -
Active Area Depth:
3 1
0.84(Nom) 6 1
2.3. 0.1
1 2
2 1
3 4
3 1
6 1
14
0.5
Notes: 1). 测量单位:mm; 2). 引脚必须避开 Flash 和电镀针孔; 3). 不要弯曲距离封装接口 1mm 以内的引脚线; 4). PINOUT: Pin 1 VDD Pin 2 GND
数据手册
微功耗高灵敏度霍尔开关 1. 概述
ES249 是一款基于混合信号 CMOS 技术的霍尔效 应传感器,这款 IC 采用了先进的斩波稳定技术,因而能 够提供准确而稳定的磁开关点。 在电路设计上,ES249 提供了一个内嵌的受控时钟 机制来为霍尔器件和模拟信号处理电路提供时钟源,同 时这个受控时钟机制可以发出控制信号使得消耗电流较 大的电路周期性的进入“休眠”模式;同样通过这个
符号
BOP BRP BHYS
最大值
200
单位
Gs Gs Gs
9.
封装
9.1 SOT-23 封装物理特性 Top View
注意: 1). 引脚: Pin 1 VDD Pin 2 Output Pin 3 GND 2). 所有尺寸都以毫米为单位; 标记: 249 —器件型号 ( ES249 );; y – 年份最后一位; mm – 生产批号;
7. 电学特性
直流工作参数:TA = 25℃,VDD =3V 参数
工作电压 电源电流 输出电流 饱和压降 唤醒模式时间 休眠模式时间
符号
VDD IDD IOUT VSAT TAW TSL
测试条件
工作时 平均值
最小值
2.5
典型值
3 45 1.0
最大值
5.5
单位
V μA mA
IOUT=1mA 工作时 工作时 20
1.27
Pin 3 Output
©2009-2013 易良盛科技(天津)有限公司
Rev3.0.1.130503
4/5
数据手册
微功耗高灵敏度霍尔开关 10. 订购信息
产品型号
ES249
ES249
封装类型
UA (TO-92S) SO (SOT-23)
联系方式:
易良盛科技(天津)有限公司 地址:天津市泰达开发区第六大街 110 号天润科技园 4 楼 电话:022-65830511 ext. 8002 网址: 邮编:300457 传真:022-65830611
2. 特点
CMOS 霍尔集成电路工艺 单极输出 固态开关,可靠性比簧片开关高 工作电压低至 2.5V CMOS 逆向输出(无上拉电阻) 高灵敏度直接簧片开关的替代应用
3. 应用
固态开关 磁电转换开关 低占空比替代簧片管的磁接近传感
4. 功能框图
©2009-2013 易良盛科技(天津)有限公司
Rev3.0.1.130503
1/5
数据手册
微功耗高灵敏度霍尔开关 5. 内部时钟电路
Current Period Iaw
ES249
Sample & Output Latched Iav Isp Awake TAW: 20μs 0 Sleep Tsl: 600μs Time
9.2 TO-92S 封装物理特性
0.76 0.05 1.58 0.1
ES249
3 1 45 1
2.13 1.87 3.90 1.1 0.1 3.90
4.1 0.1 3.90
1 2
2 1
3 4
Sensor Location
3.18 0.1
24921
3 - 0.44 3.90 0.05 0.05 3.90 3 - 0.38 3.90