The Properties of an HI-Selected Galaxy Sample
Realtek USB Ethernet适配器用户手册说明书

Under Windows OS, you can read “Realtek USB FE Family Controller” under Network adapter’s catalog of hardware device manager.Note: If you are running Microsoft Windows 7 and XP OS, system will detect a removable storage that includes Ethernet adapter’s driver. Click icon to start driver installation step.Hardware SettingsWindows OSUSB Type-CFast Ethernet AdapterUser Manual• Adapts USB C-Type equipped laptops to enable 10/100Mbps network connection.• Compliant USB Type-C Standard Rev1.0.• Compliant with IEEE 802.3 (10Base-T) and 802.3u (100Base-TX) standards.• Ethernet supports full-duplex and half-duplex operations and Auto MDIX feature.• Supports suspend mode and remote wakeup via link-up and magic packet • Built-in LED to indicate Ethernet operating status.• Easy plug & play and USB bus powered design.• Driver support for Apple MAC, Google Chromebook and Microsoft Windows operation systems.• Certified by Electromagnetic Compatibility (CE, FCC, VCCI, C-Tick, BSMI) and RoHS approval.• CTL1200 - USB Type-C to Fast Ethernet Adapter • User ManualFeaturesPackageSUNIX CTL1200, USB-C to Fast Ethernet Adapter offers a reliable USB Ethernet connection, adding a single RJ45 Ethernet port to a USB Type-C enabled computer system, with support for connecting to 10/100Mbps networks. The compact and portable USB-C to Fast Ethernet Adapter works with Apple MacBook, Google Chromebook, or Windows laptop and offers an ideal laptop accessory that needs network access in an environment lacking wireless capability. With support for features such as Jumbo Frames, VLAN tagging and Wake on LAN (WOL), the adapter is suitable for home and business users alike.IntroductionTroubleshootingQ 1. This Ethernet adapter is none-functional?Ans: It may cause by following issues:1). Make sure all cables are firmly and properly connected to the correct port.2). Check LED on the RJ45 connector status. Does “Activity/Link” white LED is active? If not, please check Ethernet wire cable connection is correct.3). Check Ethernet adapter get correct IP from your connected DHCP server. If not, please contact with your technical support to get allowed IP address.Q 2. I am unable to connect to the internet over this Ethernet adapter?Ans: It may cause by following issues:1). Check “Activity/Link” white LED is active on the RJ45 connector. If not, please check Ethernet wire cable connection is correct.2). Check Ethernet adapter get correct network IP address.3). Check network DNS (Domain Name Server) setting is correct. For example, you could use free Google DNS server IP 8.8.8.8.Q 3. May I want be aware of USB-C cable plug direction?Ans: With Type-C, a USB plug's both sides will be the same, allowing for reversible plug orientation. You don't need to worry about plugging it in upside down.Q 4. Does USB to Ethernet adapter support Android OS?Ans: Native Android OS does not include USB-Ethernet controller driver. You may have to contact with your tablet or mobile hardware vendor (e.g. Google, Samsung, or SONY) to get technical support for “Realtek USB Ethernet” solution. We do not support additional Android driver package, because driver has to compile with Android OS kernel in advanced.Scan for detailSUNIX USB Type-C to Fast Ethernet Adapter is driver free under Windows 8 (or above), MAC 10.6 (or above), and Google Chrome operation systems. DHCP (Dynamic Host Configuration Protocol) is the default setting of this Ethernet Adapter; you can set fixed IP address, DNS, Gateway, and other detail setting in the network adapter page.Under Apple MAC X OS, you can read “USB 10/100 LAN” information in the Network setting page.MAC OSCopyrightCopyright© 2014 SUNIX Co., Ltd. All Rights Reserved.No part of this publication may be reproduced, transcribed, stored in a retrieval system, translated into any language, or transmitted in any form or by any means, photocopying, manual, or otherwise, without prior written permission from SUNIX Co., Ltd.DisclaimerSUNIX Co., Ltd. Shall not be liable for any incidental or consequential damages resulting from the performance or use of this equipment.SUNIX Co., Ltd. makes no representations or warranties regarding the contents of this manual. Information in this manual has been carefully checked for reliability; however, no guarantee is given as to the correctness of this content. In the interest of continued product improvement, this company reserves the right to revise the manual or include change in the specifications of the product described within it at any time without notice and without obligation to notify any person of such revision or changes. The information contained in this manual is provided for general use by the customers.TrademarksSUNIX is a registered trademark of SUNIX Co., Ltd.Other registered marks used herein are for identification purposes only and may be trademarks of their respective owners.E-mailfortechnicalsupport:**************Website for product information: Tel: +886-2-8913-1987Fax: +886-2-8913-1986SpecificationsLED DisplayMade in China 771-CTL120000-S04說明書USB Type-C轉 標準乙太網 轉換器• 透過USB-C介面轉換為標準乙太網介面,透過RJ45接頭連接實體網路。
74HC595 74HCT595 8位串行输入、串行或并行输出的移位寄存器说明书

74HC595; 74HCT5958-bit serial-in, serial or parallel-out shift register with outputlatches; 3-stateRev. 9 — 28 February 2017Product data sheet 1General descriptionThe 74HC595; 74HCT595 is an 8-bit serial-in/serial or parallel-out shift register with astorage register and 3-state outputs. Both the shift and storage register have separateclocks. The device features a serial input (DS) and a serial output (Q7S) to enablecascading and an asynchronous reset MR input. A LOW on MR will reset the shiftregister. Data is shifted on the LOW-to-HIGH transitions of the SHCP input. The data inthe shift register is transferred to the storage register on a LOW-to-HIGH transition ofthe STCP input. If both clocks are connected together, the shift register will always beone clock pulse ahead of the storage register. Data in the storage register appears atthe output whenever the output enable input (OE) is LOW. A HIGH on OE causes theoutputs to assume a high-impedance OFF-state. Operation of the OE input does notaffect the state of the registers. Inputs include clamp diodes. This enables the use ofcurrent limiting resistors to interface inputs to voltages in excess of V CC.2Features and benefits•8-bit serial input•8-bit serial or parallel output•Storage register with 3-state outputs•Shift register with direct clear•100 MHz (typical) shift out frequency•Complies with JEDEC standard no. 7A•Input levels:–For 74HC595: CMOS level–For 74HCT595: TTL level•ESD protection:–HBM JESD22-A114F exceeds 2000 V–MM JESD22-A115-A exceeds 200 V•Multiple package options•Specified from -40 °C to +85 °C and from -40 °C to +125 °C3Applications•Serial-to-parallel data conversion•Remote control holding register8-bit serial-in, serial or parallel-out shift register with output latches; 3-state 4Ordering information5Functional diagram8-bit serial-in, serial or parallel-out shift register with output latches; 3-state8-bit serial-in, serial or parallel-out shift register with output latches; 3-state6Pinning information6.1Pinning74HC59574HCT595Q1V CC Q2Q0Q3DS Q4OE Q5STCP Q6SHCP Q7MR GNDQ7S001aao24212345678109121114131615Figure 5. Pin configuration for SO16, SSOP16 and TSSOP16001aao24374HC59574HCT595Q7MRQ6SHCP Q5STCP Q4OE Q3DS Q2Q0G N DQ 7S Q 1V C CTransparent top view71061151241331421589116terminal 1index areaGND (1)(1) This is not a supply pin. The substrate is attached to this pad using conductive die attach material. There is no electrical or mechanical requirement to solder this pad.However, if it is soldered, the solder land should remain floating or be connected to GND.Figure 6. Pin configuration for DHVQFN166.2Pin description8-bit serial-in, serial or parallel-out shift register with output latches; 3-state7Functional description[1][1]H = HIGH voltage state;L = LOW voltage state;↑ = LOW-to-HIGH transition;X = don’t care;NC = no change;Z = high-impedance OFF-state.8-bit serial-in, serial or parallel-out shift register with output latches; 3-state 8Limiting valuesTable 4. Limiting valuesIn accordance with the Absolute Maximum Rating System (IEC 60134). Voltages are referenced to GND (ground = 0 V).[1]For SO16 package: P tot derates linearly with 8 mW/K above 70 °C.[2]For SSOP16 and TSSOP16 packages: P tot derates linearly with 5.5 mW/K above 60 °C.[3]For DHVQFN16 package: P tot derates linearly with 4.5 mW/K above 60 °C.9Recommended operating conditions8-bit serial-in, serial or parallel-out shift register with output latches; 3-state 10Static characteristicsTable 6. Static characteristicsAt recommended operating conditions; voltages are referenced to GND (ground = 0 V).8-bit serial-in, serial or parallel-out shift register with output latches; 3-state8-bit serial-in, serial or parallel-out shift register with output latches; 3-state 11Dynamic characteristicsTable 7. Dynamic characteristicsVoltages are referenced to GND (ground = 0 V); for test circuit see Figure 13.8-bit serial-in, serial or parallel-out shift register with output latches; 3-state8-bit serial-in, serial or parallel-out shift register with output latches; 3-state[1]Typical values are measured at nominal supply voltage.[2]t pd is the same as t PHL and t PLH.[3]t en is the same as t PZL and t PZH.[4]t dis is the same as t PLZ and t PHZ.[5]C PD is used to determine the dynamic power dissipation (P D in μW).P D = C PD × V CC2 × f i + Σ(C L × V CC2 × f o) where:f i = input frequency in MHz;f o = output frequency in MHz;Σ(C L × V CC2 × f o) = sum of outputs;C L = output load capacitance in pF;V CC = supply voltage in V.[6]All 9 outputs switching.11.1Waveforms and test circuit8-bit serial-in, serial or parallel-out shift register with output latches; 3-state8-bit serial-in, serial or parallel-out shift register with output latches; 3-state8-bit serial-in, serial or parallel-out shift register with output latches; 3-state8-bit serial-in, serial or parallel-out shift register with output latches; 3-state 12Package outline8-bit serial-in, serial or parallel-out shift register with output latches; 3-state8-bit serial-in, serial or parallel-out shift register with output latches; 3-state8-bit serial-in, serial or parallel-out shift register with output latches; 3-state8-bit serial-in, serial or parallel-out shift register with output latches; 3-state 13Abbreviations14Revision history8-bit serial-in, serial or parallel-out shift register with output latches; 3-state 15Legal information15.1 Data sheet status[1]Please consult the most recently issued document before initiating or completing a design.[2]The term 'short data sheet' is explained in section "Definitions".[3]The product status of device(s) described in this document may have changed since this document was published and may differ in case of multipledevices. The latest product status information is available on the Internet at URL .15.2 DefinitionsDraft — The document is a draft version only. The content is still under internal review and subject to formal approval, which may result in modifications or additions. Nexperia does not give any representations or warranties as to the accuracy or completeness of information included herein and shall have no liability for the consequences of use of such information.Short data sheet — A short data sheet is an extract from a full data sheet with the same product type number(s) and title. A short data sheet is intended for quick reference only and should not be relied upon to contain detailed and full information. For detailed and full information see the relevant full data sheet, which is available on request via the local Nexperia sales office. In case of any inconsistency or conflict with the short data sheet, the full data sheet shall prevail.Product specification — The information and data provided in a Product data sheet shall define the specification of the product as agreed between Nexperia and its customer, unless Nexperia and customer have explicitly agreed otherwise in writing. In no event however, shall an agreement be valid in which the Nexperia product is deemed to offer functions and qualities beyond those described in the Product data sheet.15.3 DisclaimersLimited warranty and liability — Information in this document is believed to be accurate and reliable. However, Nexperia does not give any representations or warranties, expressed or implied, as to the accuracyor completeness of such information and shall have no liability for the consequences of use of such information. Nexperia takes no responsibility for the content in this document if provided by an information source outside of Nexperia. In no event shall Nexperia be liable for any indirect, incidental, punitive, special or consequential damages (including - without limitation -lost profits, lost savings, business interruption, costs related to the removal or replacement of any products or rework charges) whether or not such damages are based on tort (including negligence), warranty, breach of contract or any other legal theory. Notwithstanding any damages that customer might incur for any reason whatsoever, Nexperia's aggregate and cumulative liability towards customer for the products described herein shall be limited in accordance with the Terms and conditions of commercial sale of Nexperia.Right to make changes — Nexperia reserves the right to make changesto information published in this document, including without limitation specifications and product descriptions, at any time and without notice. This document supersedes and replaces all information supplied prior to the publication hereof.Suitability for use — Nexperia products are not designed, authorized or warranted to be suitable for use in life support, life-critical or safety-critical systems or equipment, nor in applications where failure or malfunctionof an Nexperia product can reasonably be expected to result in personal injury, death or severe property or environmental damage. Nexperia and its suppliers accept no liability for inclusion and/or use of Nexperia products in such equipment or applications and therefore such inclusion and/or use is at the customer’s own risk.Applications — Applications that are described herein for any of these products are for illustrative purposes only. Nexperia makes no representation or warranty that such applications will be suitable for the specified use without further testing or modification. Customers are responsible for the design and operation of their applications and products using Nexperia products, and Nexperia accepts no liability for any assistance with applications or customer product design. It is customer’s sole responsibility to determine whether the Nexperia product is suitable and fit for the customer’s applications and products planned, as well as for the planned application and use of customer’s third party customer(s). Customers should provide appropriate design and operating safeguards to minimize the risks associated with their applications and products. Nexperia does not accept any liability related to any default, damage, costs or problem which is based on any weakness or default in the customer’s applications or products, or the application or use by customer’s third party customer(s). Customer is responsible for doing all necessary testing for the customer’s applications and products using Nexperia products in order to avoid a default of the applications and the products or of the application or use by customer’s third party customer(s). Nexperia does not accept any liability in this respect.Limiting values — Stress above one or more limiting values (as defined in the Absolute Maximum Ratings System of IEC 60134) will cause permanent damage to the device. Limiting values are stress ratings only and (proper) operation of the device at these or any other conditions above thosegiven in the Recommended operating conditions section (if present) or the Characteristics sections of this document is not warranted. Constant or repeated exposure to limiting values will permanently and irreversibly affect the quality and reliability of the device.Terms and conditions of commercial sale — Nexperia products aresold subject to the general terms and conditions of commercial sale, as published at /profile/terms, unless otherwise agreed in a valid written individual agreement. In case an individual agreement is concluded only the terms and conditions of the respective agreement shall apply. Nexperia hereby expressly objects to applying the customer’s general terms and conditions with regard to the purchase of Nexperia products by customer.No offer to sell or license — Nothing in this document may be interpreted or construed as an offer to sell products that is open for acceptance orthe grant, conveyance or implication of any license under any copyrights, patents or other industrial or intellectual property rights.Export control — This document as well as the item(s) described herein may be subject to export control regulations. Export might require a prior authorization from competent authorities.8-bit serial-in, serial or parallel-out shift register with output latches; 3-state74HC_HCT595All information provided in this document is subject to legal disclaimers.© Nexperia B.V. 2017. All rights reserved.Product data sheet Rev. 9 — 28 February 201721 / 22Non-automotive qualified products — Unless this data sheet expressly states that this specific Nexperia product is automotive qualified, the product is not suitable for automotive use. It is neither qualified nor tested in accordance with automotive testing or application requirements. Nexperia accepts no liability for inclusion and/or use of non-automotive qualified products in automotive equipment or applications. In the event that customeruses the product for design-in and use in automotive applications toautomotive specifications and standards, customer (a) shall use the productwithout Nexperia's warranty of the product for such automotive applications,use and specifications, and (b) whenever customer uses the product forautomotive applications beyond Nexperia's specifications such use shall besolely at customer’s own risk, and (c) customer fully indemnifies Nexperiafor any liability, damages or failed product claims resulting from customer design and use of the product for automotive applications beyond Nexperia'sstandard warranty and Nexperia's product specifications.Translations — A non-English (translated) version of a document is for reference only. The English version shall prevail in case of any discrepancybetween the translated and English versions.15.4 Trademarks Notice: All referenced brands, product names, service names and trademarks are the property of their respective owners.8-bit serial-in, serial or parallel-out shift register with output latches; 3-statePlease be aware that important notices concerning this document and the product(s)described herein, have been included in section 'Legal information'.© Nexperia B.V. 2017.All rights reserved.For more information, please visit: Forsalesofficeaddresses,pleasesendanemailto:***************************Date of release: 28 February 2017Document identifier: 74HC_HCT595Contents1General description ............................................12Features and benefits .........................................13Applications .........................................................14Ordering information ..........................................25Functional diagram .............................................26Pinning information ............................................46.1Pinning ...............................................................46.2Pin description ...................................................47Functional description ........................................58Limiting values ....................................................69Recommended operating conditions ................610Static characteristics ..........................................711Dynamic characteristics .....................................911.1Waveforms and test circuit ..............................1112Package outline .................................................1513Abbreviations ....................................................1914Revision history ................................................1915Legal information . (20)Mouser ElectronicsAuthorized DistributorClick to View Pricing, Inventory, Delivery & Lifecycle Information:N experia:74HC595BQ,11574HC595D,11274HC595DB,11274HC595DB,11874HC595D,11874HC595N,11274HC595PW,11274HC595PW,11874HCT595BQ,11574HCT595D,11274HCT595DB,11274HCT595DB,118 74HCT595D,11874HCT595N,11274HCT595PW,11274HCT595PW,11874HC595PW/AUJ。
CCNA认证基础课程-课后作业.习题答案
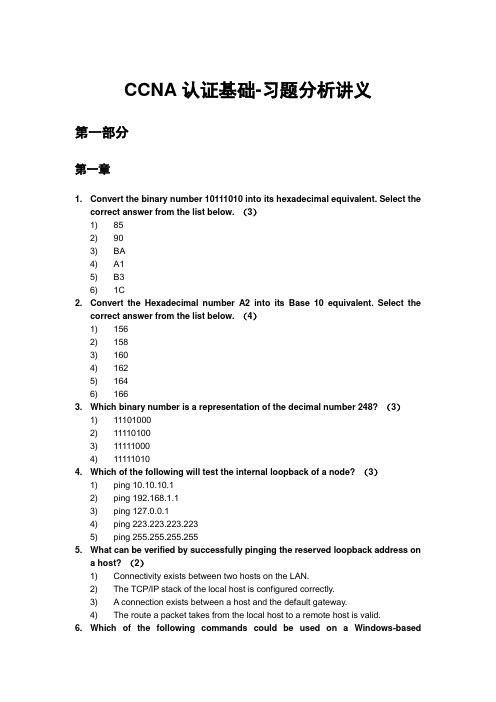
CCNA认证基础-习题分析讲义第一部分第一章1. Convert the binary number 10111010 into its hexadecimal equivalent. Select thecorrect answer from the list below. (3)1) 852) 903) BA4) A15) B36) 1C2. Convert the Hexadecimal number A2 into its Base 10 equivalent. Select thecorrect answer from the list below. (4)1) 1562) 1583) 1604) 1625) 1646) 1663. Which binary number is a representation of the decimal number 248? (3)1) 111010002) 111101003) 111110004) 111110104. Which of the following will test the internal loopback of a node? (3)1) ping 10.10.10.12) ping 192.168.1.13) ping 127.0.0.14) ping 223.223.223.2235) ping 255.255.255.2555. What can be verified by successfully pinging the reserved loopback address ona host? (2)1) Connectivity exists between two hosts on the LAN.2) The TCP/IP stack of the local host is configured correctly.3) A connection exists between a host and the default gateway.4) The route a packet takes from the local host to a remote host is valid.6. Which of the following commands could be used on a Windows-basedcomputer to view the current IP configuration of the system? (Choose two.) (3,4)1) configip2) ifconfig3) ipconfig4) winipcfg5) Winipconfig7.Refer to the exhibit. What must be configured on Host B to allow it to communicate withthe Host C? (Choose three.) (2,4,6)1)the MAC address of RTA router interface connected to Switch 12) a unique host IP address3)the IP address of Switch 14)the default gateway address5)the MAC address of Host C6)the subnet mask for the LAN8. What are important characteristics to consider when purchasing a networkinterface card? (Choose two.) (2,3)1) security used on the network2) media used on the network3) system bus used on the computer4) software installed on the network5) diagnostic tools installed on the network第二章1. Select the necessary information that is required to compute the estimated timeit would take to transfer data from one location to another. (Choose two.) (1,5)1) file size2) data format3) network in use4) type of medium5) bandwidth of the link2. Using the data transfer calculation T=S/BW, how long would it take a 4MB file tobe sent over a 1.5Mbps connection? (2)1) 52.2 seconds2) 21.3 seconds3) 6.4 seconds4) 2 seconds5) 0.075 seconds6) 0.0375 seconds3. What are features of the TCP/IP Transport layer? (Choose two.) (3,5)1) path determination2) handles representation, encoding and dialog control3) uses TCP and UDP protocols4) packet switching5) reliability, flow control and error correction4. Which of the following is the Layer 4 PDU? (4)1) bit2) frame3) packet4) Segment5. What is important to remember about the data link layer of the OSI model whenconsidering Peer to Peer communication? (Choose three.) (3,4,5)1) It links data to the transport layer.2) It encapsulates frames into packets.3) It provides a service to the network layer.4) It encapsulates the network layer information into a frame.5) Its header contains a physical address which is required to complete the datalink functions.6) It encodes the data link frame into a pattern of 1s and 0s (bits) for transmissionon the medium.6. Which statement describes a star topology? (2)1) Each host in the network is connected to a backbone cable that is terminated atboth ends.2) Each host is connected to a hub or switch, either of which acts as a central pointfor all network connections.3) Each host is directly connected to two other hosts to form a long chain of hosts.4) Each host has a connection to all other hosts in the network.7. Which statements describe the logical token-passing topology? (Choose two.)(2)1) Network usage is on a first come, first serve basis.2) Computers are allowed to transmit data only when they possess a token.3) Data from a host is received by all other hosts. Electronic tokens are passedsequentially to each other.4) Token passing networks have problems with high collision rates.8. Which technologies are considered to be LAN technologies? (Choose two.) (2,5)1) DSL2) Token Ring3) Frame Relay4) ISDN5) Ethernet9.Refer to the exhibit. Host A wants to send a message to host B. Place the following stepsin the correct order so that the message can be sent. (4)A - add network layer addressesB - transmit bitsC - create application dataD - add data link layer addresses1) B, A, D, C2) D, A, C, B3) A, D, A, B4) C, A, D, B5) C, D, A, B6) C, B, A, D10.After an uns u ccessful ping to the local router, the technician decides to investigate therouter. The technician observes that the lights and fan on the router are not operational.In which layer of the OSI model is the problem most likely occurring? (4)1) transport2) network3) data link4) physical11. Refer t o the exhibit. What is the order of the TCP/IP Protocol Data Units as datais moved as indicated through the OSI model? (3)1) data, segments, frames, packets, bits2) data, packets, segments, frames, bits3) data, segments, packets, frames, bits4) data, packets, frames, segments, bits第三章1. Which combinations of charges will be repelled by electric force? (Choose two.)(4,6)1) neutral and neutral2) neutral and positive3) neutral and negative4) positive and positive5) positive and negative6) negative and negative2. Which of the following are considered the best media for use in data networkcommunications? (Choose three.) (2,3,6)1) glass2) fibers3) copper4) gold5) plastic6) silicon7) Silver3. Which of the following wireless standards increased transmission capabilitiesto 11 Mbps? (2)1) 802.11a2) 802.11b3) 802.11c4) 802.11d4. What is attenuation? (3)1) opposition to the flow of current2) measurement of electrical signals relative to time3) degradation of a signal as it travels along the medium4) amount or volume of traffic that is flowing on the medium5. Which cable specifications are indicated by 10BASE-T? (3)1) 10 Mbps transmission speed, baseband signal, 500 meter cable length, coaxialcable2) 10 Mbps transmission speed, broadband signal, 100 meter cable length, coaxialcable3) 10 Mbps transmission speed, baseband signal, 100 meter cable length,twisted-pair cable4) 10 Gbps transmission speed, broadband signal, 500 meter cable length,twisted-pair cable6. For which Ethernet installations would fiber optic rather than Cat5 UTP be abetter media choice? (Choose two.) (2,4)1) a 3 meter connection between two 10BASE-T hubs2) an environment with many potential sources of EMI and RFI3) a peer to peer connection between two NICs with RJ45 connectors4) an installation between two buildings that are located 500 meters apart5) a single building installation where installation costs are the major concern7. Refer to the exhibit. Which type of UTP cable should be used to connect Host Ato Switch1? (4)1) rollover2) console3) crossover4) straight-through8. Refer to the exhibit. Which type of Category 5 cable is used to make an Ethernetconnection between Host A and Host B? (3)1) coax cable2) rollover cable3) crossover cable4) straight-through cable第四章1. During cable testing, which of the following are used to calculate theinformation carrying capacity of a data cable? (Choose two.) (2,5)1) bit speed2) attenuation3) wire map4) saturation limit5) analog bandwidth2. What type of wiring problem is depicted in this sample of a cable tester? (3)1) a fault2) a short3) an open4) a split a good map3. In a new network installation, the network administrator has decided to use amedium that is not affected by electrical noise. Which cable type will best meet this standard? (5)1) coaxial2) screened twisted pair3) shielded twisted pair4) unshielded twisted pair5) fiber optic4. How does network cable length affect attenuation? (3)1) Category 5 cable that is run in metal conduit has the highest attenuation in theshortest distance.2) Shorter cable lengths have greater signal attenuation.3) Longer cable lengths have greater signal attenuation.4) The length of the cable has no effect on signal attenuation.第五章1. The highest capacity Ethernet technologies should be implemented in whichareas of a network? (Choose three.) (3,4,5)1) between workstation and backbone switch2) between individual workstations3) between backbone switches4) between enterprise server and switch5) on aggregate access links2. What device must be used between an AUI port of a networking device and themedia to which it is being connected? (3)1) a transducer2) a transmitter3) a transceiver4) a transponder5) a port replicator3. An ISDN Basic Rate Interface (BRI) is composed of how many signalingchannels? (1)1) 12) 23) 34) 44. Which layer of the OSI model covers physical media? (1)1) Layer 12) Layer 23) Layer 34) Layer 45) Layer 56) Layer 65. What type of network cable is used between a terminal and a console port? (3)1) cross-over2) straight-through3) rollover4) patch cable6. What is the recommended maximum number of workstations configured on apeer-to-peer network? (3)1) 252) 153) 104) 55) 27. Which of the following increases the potential for a collision to occur? (4)1) the use of an active hub instead of an intelligent hub2) the use of an intelligent hub instead of an active hub3) a reduction in the number of devices attached to the hub4) an increase in the number of devices attached to the hub8. What is the maximum length of a media segment used for 100BASE-TX? (1)1) 100 meters2) 185 meters3) 400 meters4) 500 meters9. Which cable diagram displays the end to end pinout for a crossover cable usedwith Cisco devices? (3)1) Cable A2) Cable B3) Cable C4) Cable D第六章1. What does the "10" in 10Base2 indicate about this version of Ethernet? (2)1) The version uses Base10 numbering within the frames.2) The version operates at a transmission rate of 10 Mbps.3) Frames can travel 10 meters unrepeated.4) The maximum frame length is 10 octets.2. How is a MAC address represented? (4)1) four groups of eight binary digits separated by a decimal point2) four Base10 digits separated by a decimal point3) six hexadecimal digits4) twelve hexadecimal digits5) twenty-four Base10 digits3. Which of the following statements are correct about CSMA/CD? (Choose three.)(1,3,6)1) It is a media access method used in LANs.2) It is a media access method used in FDDI WANs.3) When a device needs to transmit, it checks to see if the media is available.4) A device sends data without checking media availability because all deviceshave equal access.5) Multiple devices can successfully transmit simultaneously.6) Only one device can successfully transmit at a time.4. Which devices shown in the graphic must have a MAC address? (5)1) only PC2) only router3) PC and router4) PC, hub, and router5) PC, printer, and router第七章1. Which of the following items are common to all 100BASE technologies?(Choose three.) (1,4,5)1) frame format2) media3) connectors4) timing5) multi-part encoding2. Which of the following does 1000BASE-T use to accomplish gigabit speeds onCat 5e cable? (4)1) the use of four conductors in full-duplex mode2) the use of two multiplexed pairs of wires, simultaneously3) the use of three pairs of wires for data and the fourth for stabilization andforward error correction4) the use of all four pairs of wires in full-duplex mode, simultaneously3. For which of the following is Ethernet considered the standard? (Choose three.)(1,4,5)1) inter-building connection2) mid-length voice3) video conferencing4) vertical wiring5) horizontal wiring6) diagonal wiring4. To make sure timing limitations are not violated when implementing a 10 MbpsEthernet network involving hubs or repeaters, a technician should adhere to which rule? (4)1) the 4-5-3 rule2) the 6-4-2 rule3) the 3-4-5 rule4) the 5-4-3 rule5. What is the maximum distance that 10BASE-T will transmit data before signalattenuation affects the data delivery? (1)1) 100 meters2) 185 meters3) 300 meters4) 500 meters6. When using Category 5 UTP cable, which RJ-45 pin pairs are used to exchangedata between hosts on an Ethernet network? (2)1) 1 and 2; 4 and 52) 1 and 2; 3 and 63) 3 and 6; 7 and 84) 4 and 5; 7 and 8第八章1. John has been hired as the network administrator of a local company and hasdecided to add more hubs to the company's existing network. Which of the following has been caused by John's inexperience? (1)1) collision domain extended2) an increased number of collision domains3) increased network performance4) increased bandwidth5) extended bandwidth2. "CompA" is trying to locate a new computer named "CompB" on the network.Which of the following does "CompA" broadcast to find the MAC address of "CompB"? (2)1) MAC request2) ARP request3) ping4) Telnet5) proxy ARP3. Which of the following is a term associated with replacing hubs with switchesto increase the number of collision domains? (3)1) encapsulation2) latency3) segmentation4) layered model5) broadcast domain6) Extended4. The accumulation of traffic from which of the following can cause a networkcondition called broadcast radiation? (Choose three.) (3,5,6)1) anonymous FTP servers2) telnet sessions3) video over IP applications4) NAS services5) ARP requests6) RIP updates5. Which of the following describes the use of Spanning Tree Protocol (STP)? (4)1) resolve routing loops2) eliminate Split Horizon errors3) limit collisions4) resolve switching loops6. Which term describes the delay in time that occurs when a frame leaves itssource device and reaches its destination? (4)1) collision2) backoff3) attenuation4) latency5) broadcast7. Based on the graphic above, which of the following occurs as each host systemcomes on line in the topology? (2)1) The switch sends its MAC address to each host.2) The switch adds MAC address to the bridge table as each host sends a frame.3) Each host exchanges MAC addresses with each other.4) The switch listens for data traffic to block since the switch lacks an IP address. 8. Which devices segment collision domains? (Choose two.) (2,3)1) transceiver2) router3) switch4) hub5) media9. Which protocol is used to eliminate switching loops? (3)1) Transmission Control Protocol2) Routing Information Protocol3) Spanning Tree Protocol4) Interior Gateway Routing Protocol5) Internetworking Protocol10. Refer to the exhibit. A network associate needs to establish an Ethernetconnection between Host A and Host B. However, the distance between the two hosts is further than the cabling standards allow. Which two devices that operate at the physical layer of the OSI can be used to allow Host A and Host B to communicate? (2,5)1) switch2) hub3) bridge4) router5) repeater第九章1. Which term describes an ARP response by a router on behalf of a requestinghost? (3)1) ARP2) RARP3) Proxy ARP4) Proxy RARP2. Which protocol functions at the internet layer of the TCP/IP protocol suite? (4)1) File Transfer Protocol (FTP)2) Trivial File Transfer Protocol (TFTP)3) Transmission Control Protocol (TCP)4) Internet Protocol (IP)5) User Datagram Protocol (UDP)6) Simple Mail Transport Protocol (SMTP)3. Which of these workstation installation and setup tasks are concerned withnetwork access layer functions? (Choose two.) (2,4)1) configuring the e-mail client2) installing NIC drivers3) configuring IP network settings4) connecting the network cable5) using FTP to download application software updates4. Which part of an IP address identifies a specific device on a network? (4)1) first two octets2) third and fourth octets3) network portion4) host portion5) only the fourth octet5. Which of the following are features of the Internet Protocol (IP)? (Choose two.)(1,3)1) It is the most widely implemented global addressing scheme.2) It allows two hosts to share a single address on a local area network.3) It is a hierarchical addressing scheme allowing addresses to be grouped.4) It is only locally significant, used primarily on local area networks.6. Which of the following are useable Class A IP addresses with a default subnetmask? (Choose three.) (2,3,5)1) 127.0.39.12) 111.9.28.303) 123.1.2.1324) 128.50.38.25) 105.1.34.16) 0.23.92.37. Which application layer protocols use UDP at the transport layer? (Choose two.)(2,4)1) FTP2) SNMP3) Telnet4) DHCP5) SMTP第十章1. Which OSI layer encapsulates data into packets? (3)1) session2) transport3) network4) data link2. Which OSI layer defines the functions of a router? (3)1) physical2) data link3) network4) transport5) session3. Which of the following are Cisco proprietary routing protocols? (Choose two.)(2,6)1) RIPv22) IGRP3) OSPF4) BGP5) RIPv16) EIGRP4. A company with a Class B license needs to have a minimum of 1,000 subnetswith each subnet capable of accommodating 50 hosts. Which mask below is the appropriate one? (4)1) 255.255.0.02) 255.255.240.03) 255.255.255.04) 255.255.255.1925) 255.255.255.2245. A small company has a class C network license and needs to create five usablesubnets, each subnet capable of accommodating at least 20 hosts. Which of the following is the appropriate subnet mask? (3)1) 255.255.255.02) 255.255.255.1923) 255.255.255.2244) 255.255.255.2406. When a network administrator applies the subnet mask 255.255.255.248 to aClass A address, for any given subnet, how many IP addresses are available to be assigned to devices? (6)1) 10222) 5103) 2544) 1265) 306) 67. Host A is assigned the IP address 10.18.97.55 /21. How many more networkdevices can be assigned to this subnetwork if Host A is the only one that has an IP address assigned so far? (4)1) 2542) 5093) 10214) 20455) 40946) 81908.Refe r to the exhibit. The network administrator wants to create a subnet for thepoint-to-point connection between the two routers. Which subnetwork mask would provide enough addresses for the point-to-point link with the least number of wasted addresses?1) 255.255.255.1922) 255.255.255.2243) 255.255.255.2404) 255.255.255.2485) 255.255.255.2529. What is the correct number of usable subnetworks and hosts for the IP networkaddress 192.168.35.0 subnetted with a /28 mask?1) 6 networks / 64 hosts2) 14 networks / 32 hosts3) 14 networks / 14 hosts4) 30 networks / 64 hosts10. Which subnet masks would be valid for a subnetted Class B address? (Choosetwo.) (5,6)1) 255.0.0.02) 255.254.0.03) 255.224.0.04) 255.255.0.05) 255.255.252.06) 255.255.255.19211. Refer to the exhibit. How will the Fohi router dynamically learn routes to the192.168.16.16/28, 192.168.16.32/28, and 192.168.16.48/28 subnetworks? (3)1) with a static route2) with a routed protocol3) with a routing protocol4) with a directly connected route12. How many broadcast domains are shown in the diagram? (1)1) three2) four3) five4) six5) seven6) eight13. How many collision domains are shown in the diagram? (5)1) three2) four3) five4) six5) seven6) eight14. A router interface has been assigned an IP address of 172.16.192.166 with amask of 255.255.255.248. To which subnet does the IP address belong?1) 172.16.0.02) 172.16.192.03) 172.16.192.1284) 172.16.192.1605) 172.16.192.1686) 172.16.192.17615. Refer to the exhibit. Host A is sending data to Host B. Once R2 determines thatdata from Host A must be forwarded to R1 to reach Host B, which layer of the OSI model will R2 use to address and build the frames destined for R1?1) physical2) data link3) network4) transport5) session6) presentation16. Which type of address is 192.168.170.112/28?1) host address2) subnetwork address3) broadcast address4) multicast address17. Which type of address is 223.168.17.167/29?1) host address2) multicast address3) broadcast address4) subnetwork address18. Which combination of network id and subnet mask correctly identifies all IPaddresses from 172.16.128.0 through 172.16.159.255?1) 172.16.128.0 255.255.255.2242) 172.16.128.0 255.255.0.03) 172.16.128.0 255.255.192.04) 172.16.128.0 255.255.224.05) 172.16.128.0 255.255.255.19219. Refer to the exhibit. The internetwork in the exhibit has been assigned the IPaddress 172.20.0.0. What would be the appropriate subnet mask to maximize the number of networks available for future growth?1) 255.255.224.02) 255.255.240.03) 255.255.248.04) 255.255.252.05) 255.255.254.06) 255.255.255.0第十一章1. If a network administrator needed to download files from a remote server, whichprotocols could the administrator use to remotely access those files? (Choose two.) (3,5)1) NFS2) ASCII3) TFTP4) IMAP5) FTP6) UDP2. What is established during a connection-oriented file transfer betweencomputers? (Choose two.) (2,5)1) a temporary connection to establish authentication of hosts2) a connection used for ASCII or binary mode data transfer3) a connection used to provide the tunnel through which file headers aretransported4) a command connection which allows the transfer of multiple commands directlyto the remote server system5) a control connection between the client and server3. Which of the following protocols are used for e-mail transfer between clientsand servers? (Choose three.) (3,4,5)1) TFTP2) SNMP3) POP34) SMTP5) IMAP46) postoffice4. Which type of institution does the domain suffix .org represent? (4)1) government2) education3) network4) non-profit5. Which of the following services is used to translate a web address into an IPaddress? (1)1) DNS2) WINS3) DHCP4) Telnet6. Which part of the URL http://www.awsb.ca/teacher gives the name of thedomain? (4)1) www2) http://3) /teacher4) awsb.ca7. Which protocols are TCP/IP application layer protocols? (Choose two.) (2,4)1) UDP2) FTP3) IP4) SMTP5) TCP8. What are three characteristics of the TCP protocol? (Choose three.) (3,4,6)1) has less overhead than UDP2) is used for IP error messages3) forces the retransmission undelivered packets4) creates a virtual session between end-user applications5) carries the IP address of destination host in the TCP header6) is responsible for breaking messages into segments and reassembling9. Two peer hosts are exchanging data using TFTP. During the current session, adatagram fails to arrive at the destination. Which statement is true regarding the retransmission of the datagram? (2)1) Datagram retransmission requires user authentication.2) Datagram retransmission is controlled by the application.3) Datagram retransmission relies on the acknowledgements at transport layer.4) Datagram retransmission occurs when the retransmission timer expires in thesource host.案例学习1. 子网计算练习:Answer2. 子网号及广播地址计算练习Answer3. 子网规划练习:已知:给定一个C类地址201.16.5.0/24。
TP-Link Smart Switch 安装指南说明书

Follow these instructions to set up your smart switch. Prepare to Install Your Smart Switch•Prepare a PC with an Ethernet adapter and a CD ROM drive.•Before proceeding with the smart switch installation, familiarize yourself with the contents of the Resource CD, especially the manuals.First, Install the Smartwizard Discovery Utility on a PC 1.Power on your PC, let the operating system boot up completely, and log in asneeded.2.Insert the Resource CD for the Smart Switch Series into your CD-ROM drive.The CD main page shown below will load.3.Click Install. Follow the links on the CD and the setup utility prompts tocomplete the installation of the Smartwizard Discovery utility.4.Click OK when done. Next, Connect Your Smart Switch in the Correct OrderNote: These instructions assume you are using DHCP in your network. If you areusing static IP addressing in your network, configure the switch IP address beforeconnecting it to your network. In the absence of a DHCP server, the switch willdefault to 192.168.0.239 for its IP address. To configure the switch beforeconnecting it to your network, set up the PC with an IP address in the 192.168.0.xsubnet, and connect the PC to the switch. Then, use the Smartwizard Discoveryutility as illustrated below to configure the switch.1.2.Power on the switch. The switch will get its TCP/IP configuration from theDHCP server on your network.3.Assure that the PC with the Smartwizard Discovery utility can assess the switch.Now, Configure the Switch with the SmartwizardDiscovery Utility1.Click the SmartDiscovery icon on your desktop or in Windows Startmenu Programs to view this screen.2.Click Discover to find your switch in the network.The Smartwizard Discovery utility finds the switch and displays its MACAddress, IP Address, and model number. If you cannot configure your switch,verify that the cable connections are secure, that the IP address configuration ofthe PC is in the same subnet as the switch, and click the Discover button.3.Click to select the line displaying the details of your switch. If there are multiplesmart switches in your network, be sure to select the one you want to configure.3& ZLWK 6PDUWZL]DUG 'LVFRYHU\ 8WLOLW\4.Click Web Access to view the switch log in screen.5.Enter the default password of password in lower case letters and click Login.The switch will display the switch settings main page. Configure the switch for your network. Consult the manual on the CD or the online help in the switch for assistance with configuration procedures.After you log in to the switch, the main Web Access menu displays.Use the configuration menu options to configure your switch.Troubleshooting TipsHere are some tips for correcting simple problems you may have.Be sure to power on your PC and smart switch in the correct sequence.Follow this sequence. Turn off the smart switch and computer. First, turn on thesmart switch and wait two minutes. Next turn on the computer.Make sure the Ethernet cables are securely plugged in.For each powered on computer connected to the smart switch with a securelyplugged in Ethernet cable, the corresponding smart switch LAN port status lightwill be lit.Make sure the network settings of the computer are correct.In most cases, computers should be configured to obtain an IP addressautomatically via DHCP.If your network uses static IP addresses, be sure the switch and computer areconfigured with valid IP addresses.Check the smart switch status lights to verify correct operation.If the Power light does not turn on or the port status lights do not light, verifythat the power cord is properly plugged in and then reset the smart switchaccording to the instructions in the Hardware Manual on the CD.Technical SupportThank you for selecting NETGEAR products.Register Your ProductTo register, go to: /registerGo to /support for support information.©2004 by NETGEAR, Inc. All rights reserved.NETGEAR is a registered trademark of NETGEAR, Inc. in the United States and/orother countries.Other brand and product names are trademarks or registered trademarks of theirrespective holders. Information is subject to change without notice. February 2004。
西格玛泰克说明书

C-DIAS PROCESSOR MODULECCP 521C-DIAS Processor ModuleThe CCP 521 processor module runs the control program and thereby represents an essential component of an automation system. The internal DC/DC converter powers all modules on a C-DIAS module carrier. The VARAN bus, the CAN bus, an Ethernet interface or the USB device (Mini USB) can be used as the online interface connection. A 7-segment display and 2 status LEDs provide information on the actual status of the CPU. For program updates, the integrated USB Host interface can be used (USB stick, keyboard). With help from the exchangeable SD card, the entire control program can be easily exchanged. The CCP 521 processor module is designed to be mounted in the control cabinet.CCP 521Compatibility Completely PC-compatible. The CCP 521 works with standard PC BIOS and therefore no SIGMATEK-specific BIOS is needed; the LASAL operating system in provided.26.05.2010Page 1CCP 521C-DIAS PROCESSOR MODULETechnical DataPerformance dataProcessor Addressable I/O/P modules EDGE-Technology X86 compatible VARAN bus: 65,280 CAN bus: 32 C-DIAS bus: 8 No 32-kbyte L1 Cache 256-kbyte L2 Cache AMI 64 Mbytes 512 Kbytes 1-Gbyte micro SD card 1 x USB Host 2.0 (full speed 12 Mbit/s) 1 x USB Device 1.1 1 x Ethernet 1 x CAN 1 x VARAN 1 x C-DIAS Yes Yes Yes Yes (buffering approximately 10 days)Internal I/O Internal cache BIOS Internal program and data memory (DDR2 RAM) Internal remnant data memory Internal storage device (IDE) Interface connectionsData buffer Status display Status LEDs Real-time clockPage 2 a26.05.2010C-DIAS PROCESSOR MODULE Electrical requirementsSupply voltage Current consumption of (+24 V) power supply Starting current Power supply on the C-DIAS bus Current load on C-DIAS bus (power supply for I/O/P modules). Typically 150 mA +18 –30 V DCCCP 521Maximum 500 mAFor a very short time (~20 ms) : 30 A Supplied by the CCP 521 Maximum 1.2 AStandard configurationEthernet 1 CAN bus IP: 10.10.150.1 Station: 00 Subnet-Mask:255.0.0.0 Baud rate: 01 = 500 kBaudProblems can arise if a control is connected to an IP network, which contains modules that do not contain a SIGMATEK operating system. With such devices, Ethernet packets could be sent to the control with such a high frequency (i.e. broadcasts), that the high interrupt load could cause a real-time runtime error. By configuring the packet filter (Firewall or Router) accordingly however, it is possible to connect a network with SIGMATEK hardware to a third party network without triggering the error mentioned above.26.05.2010Page 3CCP 521 MiscellaneousArticle number Hardware version Project back-up StandardC-DIAS PROCESSOR MODULE12-104-521 1.x Internally on the micro SD card UL in preparationEnvironmental conditionsStorage temperature Operating temperature Humidity EMV stabilityShock resistance Protection Type -10 –+85 °C 0 –+50 °C 10 - 90 %, uncondensed According to EN 61000-6-2 (industrial area) EN 60068-2-27 EN 60529 150 m/s? IP 20Page 426.05.2010C-DIAS PROCESSOR MODULECCP 521Mechanical Dimensions104.10 (dimensioning incl. covers)109.212924.9026.05.2010Page 5CCP 521C-DIAS PROCESSOR MODULEConnector LayoutPC通讯底层通讯电源Page 626.05.2010C-DIAS PROCESSOR MODULE X1: USB Device 1.1CCP 521Pin 1 2 3 4 5Assignment +5 V DD+ GNDX2: USB Host 2.0Pin 1 2 3 4 Assignment +5 V DD+ GNDIt should be noted that many USB devices on the market do not comply with the relevant EMC standards for industrial environments. Connecting such a device can lead to malfunctions.X3: EthernetPin 1 2 3 4-5 6 7-8 Assignment TX+ TXRX+ RX-X4: VARANPin 1 2 3 4-5 6 7-8 Assignment TX+ / RX+ TX- / RXRX+ / TX+ RX- / TX-26.05.2010Page 7CCP 521 X5: CAN-BusC-DIAS PROCESSOR MODULE12Pin 1 2 3 4 5 6Assignment CAN A (CAN LOW) CAN B (High) CAN A (CAN LOW) CAN B (High) GND -56X6: Power plug1Pin 1 2Assignment +24 V supply GNDX7: micro SD card Sandisk SDSDQ-1024-KPage 826.05.2010C-DIAS PROCESSOR MODULE Exchanging the micro SD cardCCP 521The micro SD card is located under the LED cover.To exchange the micro SD card, carefully lift the LED cover.The micro SD card is located on the left side and can be disengaged by lightly pressing on the card itself.Remove the micro SD card.26.05.2010Page 9CCP 521C-DIAS PROCESSOR MODULEApplicable connectors USB Device: USB Host: Ethernet: VARAN: CAN-Bus: Supply: 5-pin, type mini B 4-pin, type A 8-pin, RJ45 8-pin, RJ45 6-pin Weidmüller plug, B2L3, 5/6 2-pin Phoenix plug with screw terminal technology MC1, 5/2-ST-3,5 2-pin Phoenix plug with spring terminal FK-MCP1, 5/2-ST-3Page 10 a26.05.2010C-DIAS PROCESSOR MODULECCP 521Status DisplaysEthernet LED Active Link Color Yellow Green Description Lights when data is exchanged over Ethernet Lights when the connection betweenthe two PHYs is established VARAN LED Active Link Color Yellow Green Description Lights when data is exchanged over the VARAN bus Lights when the connection between the two PHYs is established Control LED ERROR DCOK Color Red Green Description Lights when an error occurs (defective USV) Lights when the power supply is OK26.05.2010Page 11CCP 521C-DIAS PROCESSOR MODULEDisplayThe CCP 521 processor module has a 2-digit decimal display (7 segment display) for the following functions:- When configuring the processor module, the parameters are shown in the display. - If an error occurs while running the program or no valid user program is found, the displayshows an error message. Thereby, "Er" (error) and the error code aredisplayed alternatingly. The same error code is also shown in the LASAL status line.- While running the program, the display can be used to show digits using the system vari-able _cpuDisplay. Valid values are 0 to 255; values over 99, however, are not shown and the display remains dark.Page 1226.05.2010C-DIAS PROCESSOR MODULECCP 521CAN Bus SetupThis section explains how to configure a CAN bus correctly. The following parameters must first be set: Station number and data transfer rate. CAN bus station number Each CAN bus station is assigned its own station number. With this station number, data can be exchanged with other stations connected to the bus. Up to 31 stations can be installed in a CANbus system. However, each station number can only be assigned once. CAN bus data transfer rate The data transfer rate (baud rate) for the CAN bus can be set. However, the longer the length of the bus, the smaller the transfer rate that must be selected.Value 00 01 02 03 04 05 06 07Baud rate 615 kBit/s 500 kbit/s 250 kBit/s 125 kBit/s 100 kBit/s 50 kBit/s 20 kBit/s 1 Mbit / sMaximum length 60 m 80 m 160 m 320 m 400 m 800 m 1200 m 30 mThese values are valid for the following cable: 120 ?, Twisted Pair. NOTE: the following is valid for the CAN bus protocol: 1 kBit/s = 1 kBaud.26.05.2010Page 13CCP 521C-DIAS PROCESSOR MODULEConfiguration of the Process ModulePage 1426.05.2010C-DIAS PROCESSOR MODULECCP 521To enter the mode for setting changes, press and hold the SETbutton while the C-IPC is booting. When the following appears in the display:the SET button can be released. After releasing the SET button, the first menu appears in the display.With several short presses of the SET button, it is possible to switch through the various menu points. By pressing the SET button for approximately 1.5 s, the menu is accessed and the setting can be changed with short presses. Once the desired changes are made, press the SET button for about 5 seconds to end the process. If the changes areto be discarded, press the RESET button to restart the C-IPC. The settings for the IP address, subnet mask and gateway are hexadecimal, whereas in the left and right digits, 0 - F must be entered separately. The switch occurs when the SET button is pressed for about 1.5 s. The values from AUTOEXEC.LSL are used as the standard settings; changes are written back to this file. Before this, the original content of the file is written to AUTOEXEC.BAK.26.05.2010Page 15 aCCP 521C-DIAS PROCESSOR MODULEC1 ... CAN PLC station 00 –30 ... Station numberC2 ... CAN PLC baud rate 00 ... 615.000 01 …500.000 02 …250.000 03 …125.000 04 …100.000 05 …50.000 06 …20.000 07 …1.000.000 I1, I2, I3, I4 IP address I1.I2.I3.I4, Hexadecimal 00 –FF respectivelyS1,S2,S3,S4 Subnet Mask S1.S2.S3.S4, hexadecimal 00 –FFrespectivelyG1,G2,G3,G4 Gateway G1,G2.G3.G4, hexadecimal 00 –FF respectivelyPage 16 a26.05.2010C-DIAS PROCESSOR MODULECCP 521CAN Bus TerminationIn a CAN bus system, both end modules must be terminated. This is necessary to avoid transmission errors caused by reflections in the line.Device 1e.g. CPU DCP 080 CAN-Bustermination on terminal moduleDevice 2e.g. Terminal ET 081Device 3Device ne.g. Terminal ET 805 D-SUB-plug with terminating resistorsCAN-Bus-ConnectionsIf the CCP 521 processor module is an end module, it can be terminated by placing a 150Ohm resistor between CAN-A (Low) and CAN-B (High).1 x 150-Ohm resistor26.05.2010Page 17CCP 521C-DIAS PROCESSOR MODULEWiring and Mounting InstructionsEarth ConnectionThe CCP 521 must be connected to earth over the mounting on the back wall of the control cabinet or over the earth terminal provided (C-DIAS module carrier). It is important to create a low-ohm earth connection, only then can error-free operation be guaranteed. The earth connection should have the maximum cross section and the largest electrical surface possible. Any noise signals that reach the CCP 521 over external cables must be filtered out over the earth connection. With a large (electrical) surface, high frequency noise can also be well dissipated.Page 1826.05.2010C-DIAS PROCESSOR MODULECCP 521ShieldingThe wiring for the CAN bus, Ethernet and VARAN bus must be shielded. The low-ohm shielding is either connected at the entry to the control cabinet or directly before the CCP 521 processor module over a large surface (cable grommets, grounding clamps)! Noise signals can thereforebe prohibited from reaching the electronics and affecting the function.ESD ProtectionBefore any device is connected to or disconnected from the CCP 521, the potential with ground should be equalized (by touching the control cabinet or earth terminal). Static electricity (from clothing, footwear) can therefore be reduced.26.05.2010Page 19CCP 521C-DIAS PROCESSOR MODULEProcess DiagramMain voltage onOnline with Lasal Software?noyes Output of a reset of the peripheral modules Output of a reset of the peripheral modulesDeletion of specific data areasDeletion of specific data areasStatus RESETProgram in external memory module functional?noyes Copy program into application program memory Program in internal memory module functional? noyes Status RUN ROM Copy program into application program memory Status CHKSUM or POINTERCall of application programStatus RUN ROMCall of application programPage 2026.05.2010C-DIAS PROCESSOR MODULECCP 521Status and Error MessagesStatus and error messages are shown in the status test of the Lasal Class software. If the CPU has a status display, the status or error number is also show here as well. POINTER or CHKSUM messages can also be shown on the terminal screen.Number 00 Message RUN RAM Definition The user program is currently running in RAM. The display is not affected. 01 RUN ROM The user program in the program memory module was loaded into the RAM and is currently being run. The display is not affected. 02 RUNTIME The total duration of all cyclic objects exceeds the maximum time; the time can beconfigured using 2 system variables: -Runtime: time remaining -SWRuntime: pre-selected value for the runtime counter 03 POINTER Incorrect program pointers were detected before running the user program Possible Causes: Cause/solution- The program memory module ismissing, not programmed or defect.- The program in the user programmemory (RAM) is not executable.- The user program is overwriting asoftware error Solution:- Reprogram the memory module, if theerror reoccurs exchange the module.- Correct programming error04 CHKSUM An invalid checksum was detected before running the user program. Cause/solution: s. POINTER26.05.2010Page 21CCP 52105C-DIAS PROCESSOR MODULEWatchdog The program was interrupted through the watchdog logic. Possible Causes:- User program interrupts blockedover a longer period of time (STI command forgotten)- Programming error in a hardwareinterrupt.- INB, OUTB, INW, OUTW instructions used incorrectly.- The processor is defect.Solution:- Correct programming error.- Exchange CPU. 06 07 GENERAL ERROR PROM DEFECT General error An error has occurred while programming the memory module. Cause:- The program memory module isdefect.- The user program is too large. - The program memory module is missing. Solution:- Exchange the program memorymodule 08 Reset The CPU has received the reset signal and is waiting for further instructions. The user program is not processed. 09 WD DEFEKT The hardware monitoring circuit (watchdog logic) is defect. After power-up, the CPU checks the watchdog logic function. If an error occurs during this test, the CPU deliberately enters an infinite loop from which no further instructions are accepted. 10 11 12 13 14 STOP PROG BUSYS PROGRAM LENGTH PROG END PROG MEMO The memory module was successfully completed. The CPU is currently programming the memory module. Solution: Exchange CPU.Page 2226.05.2010C-DIAS PROCESSOR MODULE15 16 17 STOP BRKPT CPU STOP INT ERROR The CPU was stopped by a breakpoint in the program. The CPU was stopped by the PG software (F6 HALT in status test). The CPU has triggered a false interrupt and stopped the user program or has encountered an unknown instruction while running the program. Cause:CCP 521- A nonexistent operating system wasused.- Stack error (uneven number of PUSHand POP instructions).- The user program was interrupted bya software error. Solution: - Correct programming error. 18 19 2021 22 SINGLE STEP Ready LOAD UNZUL. Modul MEMORY FULL The CPU is insingle step mode and is waiting for further instructions. A module or project has been sent to the CPU and it is ready to run the program. Theprogram has stopped and is receiving a module or project. The CPU has received a module, which does not belong to the project. The operating system memory /Heap) is too small. No more memory could be reserved, when an internal or interface function was called from theapplication. When starting the CPU, a missing module or a module that does not belong to the project was detected. A division error has occurred. Possible Causes:23NOT LINKED24DIV BY 0- Division by 0. - The result of a division does not fit inthe result register. Solution: - Correct programming error.26.05.2010Page 23CCP 52125C-DIAS PROCESSOR MODULEDIAS ERROR An error has occurred accessing a DIAS module. while Possible Causes:- An attempt is made to accessa nonexistent DIAS module.- DIAS bus error.Solution:- Check the DIAS bus - Check the termination resistors. 26 27 28 29 30 WAIT OP PROG OP INSTALLED OS TOO LONG NO OPERATING SYSTEM The CPU is busy. The operating system is currently being reprogrammed. The operating system has been reinstalled. The operating system cannot be loaded; too little memory. Boot loader message. No operating system found in RAM. 31 32 33 34 SEARCH FOR OS NO DEVICE UNUSED CODE MEM ERROR The operating system loaded does not match the hardware configuration. The boot loader is searching for the operating system inRAM.35 36 37MAX IO MODULE LOAD ERROR GENERELLER BS-FEHLER The LASAL Module or project cannot be loaded. A general error has occurred while loading the operating system. An error has occurred in the application memory (user heap).38 39 40 41APPLMEM ERROR OFFLINE APPL LOAD APPL SAVEPage 2426.05.2010C-DIAS PROCESSOR MODULE46 47 50 APPL-LOAD-ERROR APPL-SAVE-ERROR ACCESS-EXCEPTIONERROR BOUND EXCEEDED PRIVILEDGED INSTRUCTION An error has occurred loading the application. whileCCP 521An error has occurred while attempting to save the application. Read or write access of a restricted memory area. (I.e. writing to the NULL pointer). An exception error caused by exceeding the memory limits An unauthorized instruction for the current CPU level was given. For example, setting the segment register. An error has occurred during a floating-point operation. Error from ASMaster. the Intelligent DIRestart; report error to Sigmatek.51 5253 60 64 65 66 67FLOATING POINT ERROR DIAS-RISC-ERROR INTERNAL ERROR FILE ERROR DEBUG ASSERTION FAILED REALTIME RUNTIMEAn internal error has occurred, all applications are stopped. An error has occurred during a file operation. Internal error. The total duration of all real-time objects exceeds the maximum time; the time cannot be configured. 2 ms for 386 CPUs 1 ms for all other CPUsRestart; report error to Sigmatek. Starting from Version 1.1.768BACKGROUND RUNTIMEThe total time for all background objects exceed the maximum time; the time can be configured using two system variables: -BTRuntime: time remaining -SWBTRuntime: pre-selected value for the runtime counter95 96 97 98USER DEFINED 0 USER DEFINED 1 USER DEFINED 2 USER DEFINED 3User-definable code. User-definable code. User-definable code.User-definable code.26.05.2010Page 25CCP 52199 100 101 102 103 104 105 106C-DIAS PROCESSOR MODULEUSER DEFINED 4 C_INIT C_RUNRAM C_RUNROM C_RUNTIME C_READY C_OKC_UNKNOWN_CID The CPU is ready for operation. The CPU is ready for operation. An unknown class from a standalong or embedded object: unknown base class. The operating system class cannot be created; the operating system is probably wrong. Reference to an unknown object in an interpreter program, creation of more than one DCC080 object. The hardware module number is greater than 60. No connection to the required channels. Wrong server attribute. No specific error, recompile all and reload project components. An attempt was made to open an unknown table.Memory allocation error Memory allocation error User-definable code. Initialization start; the configuration is run. The LASAL project was successfully started from RAM. The LASAL project was successfullystarted from ROM.107C_UNKNOWN_CONSTR108C_UNKNOWN_OBJECT109 110 111 112 113 114 115C_UNKNOWN_CHNL C_WRONG_CONNECT C_WRONG_ATTR C_SYNTAX_ERRORC_NO_FILE_OPEN C_OUTOF_NEAR C_OUT OF_FARPage 2626.05.2010C-DIAS PROCESSOR MODULE116 117 224 225 C_INCOMAPTIBLE C_COMPATIBLE LINKING LINKING ERROR An object with the same name exists but has another class. An object with the same name and class exists but must be updated. The application is currently linking. An error has occurred while linking. An error messaged is generated in the LASAL status window. Linking is complete. The operating system is currently being burned into the Flash memory. An error has occurred while burning the operating system. The operatingsystem is currently being installed. The power supply was disconnected; the UPS is active. The operating system is restarted.CCP 521226 230 231 232 240 241 242 243 252 253 254 255LINKING DONE OP BURN OP BURN FAIL OP INSTALL USV-WAIT Reboot LSL SAVE LSL LOAD CONTINUE PRERUN PRERESET CONNECTION BREAKThe application is started. The application is ended.26.05.2010Page 27CCP 521C-DIAS PROCESSOR MODULEApplication exceptionsSRAM and IRQ routines Writing remnant data during interruptroutines is not allowed and leads to a system crash. SRAM and consistency of changed data If more than 32 different sectors are changed (512 byteseach) shortly before shutting down the voltage supply while the user program is writing to the micro SD card, this can sometimes lead to partial loss of remnant data. The file system does not support safe writing through SRAM If files are stored, modified or written on the micro SD card from the user program, these files must always be storedwith a fixed maximum size. Since changes in size and the simultaneous shutdown of the voltage supply can corrupt the file system, a later change in the file size is not allowed. Data Breakpoint This CPU does not support the data breakpoint is a feature.Page 2826.05.2010C-DIAS PROCESSOR MODULECCP 521Recommended Shielding for VARANThe real-time VARAN Ethernet bus system exhibits very robust characteristics in industrial environments. Through the use of IEEE 802.3 standard Ethernet physics, the potentials between an Ethernet line andsending/receiving components are separated. Messages to a bus participant are immediately repeated by the VARAN Manager in the event of an error. The shielding described below is principally recommended. For applications in which the bus is run outside the control cabinet, the correct shielding is required. Especially when for structural reasons, the bus line must be placed next to strong electromagnetic interference. It is recommended to avoid placing Varan bus linesparallel to power cables whenever possible. SIGMATEK recommends the use of CAT5e industrial Ethernet bus cables. For the shielding, an S-FTP cable should be used. An S-FTP bus is a symmetric, multi-wire cable withunshielded pairs. For the total shielding, a combination of foil and braiding is used. A non-laminated variant is recommended.The VARAN cable must be secured at a distance of 20 cm from the connector for protection against vibration!26.05.2010Page 29CCP 521C-DIAS PROCESSOR MODULE1. Wiring from the Control Cabinet to an External VARAN ComponentIf the Ethernet lines are connected from a VARAN component to a VARAN node located outside the control cabinet, the shielding should be placed at the entry point to the control cabinet housing. All noise can then be dissipated before reaching the electronic components.Page 3026.05.2010C-DIAS PROCESSOR MODULECCP 5212. Wiring Outside of the Control CabinetIf a VARAN bus cable must be placed outside of the control cabinet, additional shielding is not required. Outside of the control cabinet,IP67 modules and connectors are used exclusively. These components are very robust and noise resistant. The shielding for all sockets in IP67modules is electrically connected internally or over the housing, whereby voltage spikes are not deflected through the electronics.26.05.2010Page 31CCP 521C-DIAS PROCESSOR MODULE3. Shielding for Wiring Within the Control CabinetSources of strong electromagnetic noise located within the control cabinet (drives, Transformers, etc.) can induce interference in a VARAN bus line. Voltage spikes are dissipated over the metallic housing of aRJ45 connector. Noise is conducted over the control cabinet without additional measures needed on the circuit board of electronic components. To avoid error sources with data exchange, it is recommended that shielding be placed before any electronic components in the control cabinet.Page 3226.05.2010C-DIAS PROCESSOR MODULECCP 5214. Connecting Noise-Generating Components.When connecting power lines to the bus that generate strong electromagnetic noise, the correct shielding is also important. The shielding should be placed before a power element (or group of power elements).26.05.2010Page 33CCP 521C-DIAS PROCESSOR MODULE5. Shielding Between Two Control CabinetsIf two control cabinets must be connected over a VARAN bus, it is recommended that the shielding be located at the entry points of each cabinet. Noise is therefore prevented from reaching the electronic components in both cabinets.Page 3426.05.2010。
NI 5783 Four Channel Transceiver Adapter Module 的说
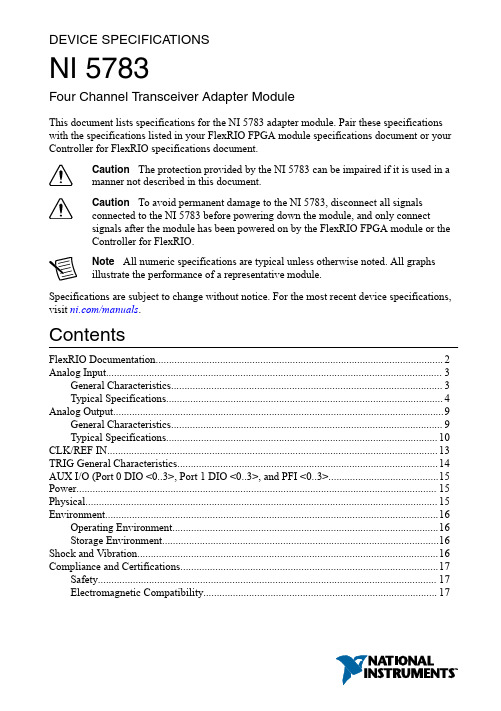
DEVICE SPECIFICATIONSNI 5783Four Channel Transceiver Adapter ModuleThis document lists specifications for the NI 5783 adapter module. Pair these specifications with the specifications listed in your FlexRIO FPGA module specifications document or your Controller for FlexRIO specifications document.Caution The protection provided by the NI 5783 can be impaired if it is used in amanner not described in this document.Caution To avoid permanent damage to the NI 5783, disconnect all signalsconnected to the NI 5783 before powering down the module, and only connectsignals after the module has been powered on by the FlexRIO FPGA module or theController for FlexRIO.Note All numeric specifications are typical unless otherwise noted. All graphsillustrate the performance of a representative module.Specifications are subject to change without notice. For the most recent device specifications, visit /manuals.ContentsFlexRIO Documentation (2)Analog Input (3)General Characteristics (3)Typical Specifications (4)Analog Output (9)General Characteristics (9)Typical Specifications (10)CLK/REF IN (13)TRIG General Characteristics (14)AUX I/O (Port 0 DIO <0..3>, Port 1 DIO <0..3>, and PFI <0..3> (15)Power (15)Physical (15)Environment (16)Operating Environment (16)Storage Environment (16)Shock and Vibration (16)Compliance and Certifications (17)Safety (17)Electromagnetic Compatibility (17)CE Compliance (17)Online Product Certification (18)Environmental Management (18)FlexRIO Documentation2| | NI 5783 SpecificationsTable 1. FlexRIO Documentation Locations and Descriptions (Continued)Analog InputGeneral CharacteristicsNumber of channels Four, single-ended, simultaneously sampled Connector Type HDBNC (high-density BNC)Input type50 ΩInput coupling DCNI 5783 Specifications| © National Instruments| 3Sample rateInternal Sample Clock100 MHzExternal Sample Clock60 MHz to 100 MHzAnalog-to-digital converter (ADC)Type Quad, 16-bitPart number AD9653Related InformationFor more information about the ADC, refer to the AD9653 datasheet at . Typical SpecificationsFull-scale input range (normal operating conditions)Elliptic 2.030 V pk-pkButterworth 2.037 V pk-pkDC accuracyElliptic±[(0.80% × reading) + 3.5 mV]Butterworth±[(1.00% × reading) + 3.75 mV]Input impedanceElliptic50 Ω ± 0.5%Butterworth50 Ω ± 0.8%Bandwidth (-3 dB)Elliptic39.4 MHzButterworth39.5 MHzNote All AI spectral performance values apply to both the Elliptic and Butterworthvariants.1Measured at 10.1 MHz with a -1 dBFS signal adjusted to full-scale.2Calculated from SINAD corrected to fullscale.3Measured at 10.1 MHz with a -1 dBFS signal.4| | NI 5783 SpecificationsTable 3. AI Noise Spectral DensityNote All AI channel crosstalk values apply to both the Elliptic and Butterworth variants.Figure 1. AI CrosstalkAmplitude(dBc)Frequency (Hz)NI 5783 Specifications| © National Instruments| 5Figure 2. AI Frequency Response (Zoomed Out)N o r m a l i z e d A m p l i t u d e t o 100 k H z (d B )Frequency (Hz)Figure 3. AI Frequency Response (Zoomed In)N o r m a l i z e d A m p l i t u d e t o100 k H z (d B )Frequency (Hz)6 | | NI 5783 SpecificationsFigure 4. AI Step Response (Butterworth)A m p l i t u d e (V )1–50 m050 m100 m 150 m 200 m 250 m 300 m 350 m 400 m 450 m 500 m 550 m 600 m 650 m 700 m 750 m 800 m 850 m 900 m 950 m Time (ns)20020–10406080100120140160180Figure 5. AI Step Response (Elliptic)A m p l i t u d e (V )–50 m050 m100 m 150 m 200 m 250 m 300 m 350 m 400 m 450 m 500 m 550 m 600 m 650 m 700 m 750 m 800 m 850 m 900 m 950 m 1Time (ns)20020–10406080100120140160180NI 5783 Specifications | © National Instruments | 7Figure 6. AI Spectral (10.1 MHz at -1 dBFS input signal, 6.1 kHz RBW, 10 Averages)A m p l i t u d e (dB F S )0–120–115–110–105–100–95–90–85–80–75–70–65–60–55–50–45–40–35–30–25–20–15–10–5Frequency (Hz)50 M0 2 M6 M10 M14 M18 M22 M26 M30 M34 M38 M42 M46 MNote AI Spectral figure applies to both the Elliptic and Butterworth variants.Figure 7.AI Return LossA m p l i t u d e (dB )Frequency (Hz)8 | | NI 5783 SpecificationsAnalog OutputGeneral CharacteristicsNumber of channels Four, single-ended, simultaneously updated Connector type HDBNC (high-density BNC)Output type50 ΩOutput coupling DCDigital-to-analog converter (DAC)Type Quad, 16-bitPart number DAC3484Minimum analog input to analog output response time4100 MS/s1130 ns200 MS/s720 ns400 MS/s550 nsRelated InformationFor more information about the DAC, refer to the DAC3484 datasheet at .4Minimum time to digitize a signal (AI) and output a response (AO). Time measured from signal entering the AI connector, passing into and out of the LabVIEW FPGA diagram, and observed at the AO connector.5400 MS/s with 2x interpolation is available only when operating in 2 channel analog output mode.NI 5783 Specifications| © National Instruments| 9Typical SpecificationsFull-scale output range (normal operation conditions)50 Ω 1.001 V pk-pk High-Z2.002 V pk-pkDC accuracy (into High-Z)±[(2.0% × desired voltage) + 4.4 mV]Output impedance 50 Ω ± 0.7%SFDR 6-81 dBcTable 6. AO Noise Spectral Density (into 50 Ω)Table 7. AO Channel Crosstalk (10 MHz)Figure 8. AO Crosstalk (into 50 Ω Load)A m p l i t u d e (dB c )Frequency (Hz)610.1 MHz tone at -1 dBFS.10 | | NI 5783 SpecificationsFigure 9. AO Frequency Response Across Data RateN o r m a l i z e d A m p l i t u d e t o 100 k H z (d B )0–10–9.5–9.0–8.5–8.0–7.5–7.0–6.5–6.0–5.5–5.0–4.5–4.0–3.5–3.0–2.5–2.0–1.5–1.0–0.5Frequency (Hz)Figure 10. AO Phase Noise (Signal at 12.1 MHz)A m p l i t u d e (dB c /H z )–95–155–150–145–140–135–130–125–120–115–110–105–100Offset from Carrier (Hz)1 M101001 k10 k100 k–160NI 5783 Specifications | © National Instruments | 11Figure 11. AO Return LossA m p l i t u d e (dB )0–32–30–28–26–24–22–20–18–16–14–12–10–8–6–4–2Frequency (Hz)300 M10 M40 M60 M80 M 100 M 120 M 140 M 160 M 180 M 200 M 220 M 240 M 260 M 280 M Figure 12. AO Two Tone, Each T one at -7 dBFS, 69.95 MHz, and 70.05 MHz, 500 HzRBW0–95–90–85–80–75–70–65–60–55–50–45–40–35–30–25–20–15–10–5Frequency (Hz)70.5 M69.5 M69.6 M 69.7 M 69.8 M 69.9 M 70.0 M 70.1 M 70.2 M 70.3 M70.4 M A m p l i t u d e (d B m )Note The noise floor in the above figure is limited by the noise floor of themeasurement device. Refer to the AO Noise Spectral Density table for more information.12 | | NI 5783 SpecificationsCLK/REF INConnector type HDBNC (high-density BNC)Input impedance50 ΩInput coupling ACReference input voltage range0.75 V pk-pk to 5.2 V pk-pkSample Clock input voltage range0.4 V pk-pk to 5.2 V pk-pkAbsolute maximum voltage±8.0 VDC, 8.0 V pk-pk ACDuty cycle45% - 55%Internal VCXO phase noise10 Hz-80 dBc/Hz100 Hz-110 dBc/Hz1 kHz-140 dBc/Hz10 kHz-150 dBc/Hz100 kHz-155 dBc/Hz1 MHz-160 dBc/Hz10 MHz-162 dBc/Hz7Default clocking configuration.NI 5783 Specifications| © National Instruments| 13Figure 13. Internal Sample Clock Phase NoiseA m p l i t u d e (dB c /H z )–85–175–170–165–160–155–150–145–140–135–130–125–120–115–110–105–100–95–90Offset Frequency (from carrier)10 M101001 k10 k100 k1 MTRIG General CharacteristicsNumber of channels 1, single-ended Connector type HDBNC Coupling DCImpedanceInput 10 kΩOutput 50 ΩLogic level 3.3 V LVCMOS V oltageV IH_MIN 2 V V IL_MAX0.8 V V OH_MIN (unloaded) 3.1 V V OL_MAX (unloaded)0.2 VAbsolute maximum voltage±20 VDC, +21 dBm (7.1 V pk-pk )14 | | NI 5783 SpecificationsAUX I/O (Port 0 DIO <0..3>, Port 1 DIO <0..3>, and PFI <0..3>Number of channels12 bidirectional (8 DIO and 4 PFI) Connector type HDMIInterface standard 3.3 V LVCMOSInterface logicMaximum V IL0.8 VMinimum V IH 2.0 VMaximum V OL0.4 VMinimum V OH 2.7 VMaximum V OH 3.6 VZ out50 Ω ± 20%I out (DC)±2 mAPull-down resistor150 kΩRecommended operating voltage-0.3 V to 3.6 VOvervoltage protection±10 VMaximum toggle frequency100 MHz+5 V maximum current10 mA+5 V voltage tolerance 4.2 V to 5 VPowerTotal power, typical operation 4.6 WPhysicalDimensions12.9 x 2.0 x 12.1 cm (5.1 x 0.8 x 4.7 in.) Weight420 g (14.8 oz)Front panel connectors Ten HDBNC and one HDMINI 5783 Specifications| © National Instruments| 15EnvironmentMaximum altitude2,000 m (800 mbar) (at 25 °C ambienttemperature)Pollution Degree2Indoor use only.Operating EnvironmentAmbient temperature range0 °C to 55 °C (Tested in accordance withIEC 60068-2-1 and IEC 60068-2-2. MeetsMIL-PRF-28800F Class 3 low temperaturelimit and MIL-PRF-28800F Class 2 hightemperature limit.)Relative humidity range10% to 90%, noncondensing (Tested inaccordance with IEC 60068-2-56.) Storage EnvironmentAmbient temperature range-20 °C to 70 °C (Tested in accordancewith IEC 60068-2-1 and IEC 60068-2-2. MeetsMIL-PRF-28800F Class 3 limits.)Relative humidity range5% to 95%, noncondensing (Tested inaccordance with IEC 60068-2-56.)Shock and VibrationOperating shock30 g peak, half-sine, 11 ms pulse (Tested inaccordance with IEC 60068-2-27. MeetsMIL-PRF-28800F Class 2 limits.)Random vibrationOperating 5 Hz to 500 Hz, 0.3 g rmsNonoperating 5 Hz to 500 Hz, 2.4 g rms (Tested in accordancewith IEC 60068-2-64. Nonoperating testprofile exceeds the requirements ofMIL-PRF-28800F, Class 3.)16| | NI 5783 SpecificationsCompliance and CertificationsSafetyThis product is designed to meet the requirements of the following electrical equipment safety standards for measurement, control, and laboratory use:•IEC 61010-1, EN 61010-1•UL 61010-1, CSA 61010-1Note For UL and other safety certifications, refer to the product label or the OnlineProduct Certification section.Electromagnetic CompatibilityThis product meets the requirements of the following EMC standards for electrical equipment for measurement, control, and laboratory use:•EN 61326-1 (IEC 61326-1): Class A emissions; Basic immunity•EN 55011 (CISPR 11): Group 1, Class A emissions•EN 55022 (CISPR 22): Class A emissions•EN 55024 (CISPR 24): Immunity•AS/NZS CISPR 11: Group 1, Class A emissions•AS/NZS CISPR 22: Class A emissions•FCC 47 CFR Part 15B: Class A emissions•ICES-001: Class A emissionsNote In the United States (per FCC 47 CFR), Class A equipment is intended foruse in commercial, light-industrial, and heavy-industrial locations. In Europe,Canada, Australia, and New Zealand (per CISPR 11), Class A equipment is intendedfor use only in heavy-industrial locations.Note Group 1 equipment (per CISPR 11) is any industrial, scientific, or medicalequipment that does not intentionally generate radio frequency energy for thetreatment of material or inspection/analysis purposes.Note For EMC declarations, certifications, and additional information, refer to theOnline Product Certification section.CE ComplianceThis product meets the essential requirements of applicable European Directives, as follows:•2014/35/EU; Low-V oltage Directive (safety)•2014/30/EU; Electromagnetic Compatibility Directive (EMC)NI 5783 Specifications| © National Instruments| 17Online Product CertificationRefer to the product Declaration of Conformity (DoC) for additional regulatory compliance information. To obtain product certifications and the DoC for this product, visit / certification, search by model number or product line, and click the appropriate link in the Certification column.Environmental ManagementNI is committed to designing and manufacturing products in an environmentally responsible manner. NI recognizes that eliminating certain hazardous substances from our products is beneficial to the environment and to NI customers.For additional environmental information, refer to the Minimize Our Environmental Impact web page at /environment. This page contains the environmental regulations and directives with which NI complies, as well as other environmental information not included in this document.Waste Electrical and Electronic Equipment (WEEE)EU Customers At the end of the product life cycle, all NI products must bedisposed of according to local laws and regulations. For more information abouthow to recycle NI products in your region, visit /environment/weee.电子信息产品污染控制管理办法(中国RoHS)中国客户National Instruments符合中国电子信息产品中限制使用某些有害物质指令(RoHS)。
西门子电力传输与分布设备 Input Output Expander (IOEX) 卡说明书
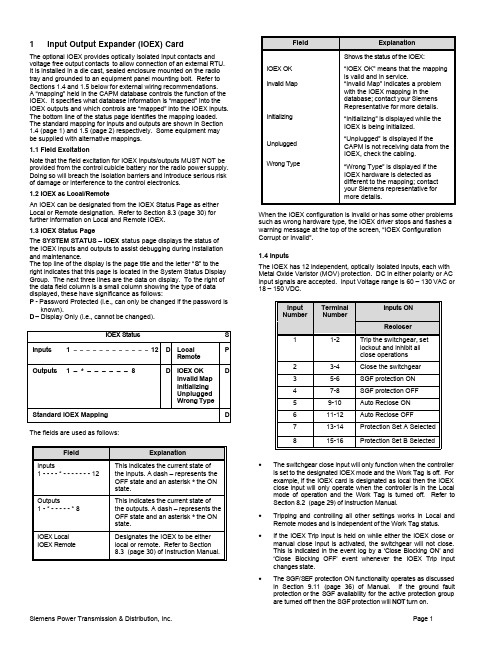
1 Input Output Expander (IOEX) CardThe optional IOEX provides optically isolated input contacts and voltage free output contacts to allow connection of an external RTU. It is installed in a die cast, sealed enclosure mounted on the radio tray and grounded to an equipment panel mounting bolt. Refer to Sections 1.4 and 1.5 below for external wiring recommendations.A “mapping” held in the CAPM database controls the function of the IOEX. It specifies what database information is “mapped” into the IOEX outputs and which controls are “mapped” into the IOEX inputs. The bottom line of the status page identifies the mapping loaded. The standard mapping for inputs and outputs are shown in Section 1.4 (page 1) and 1.5 (page 2) respectively. Some equipment may be supplied with alternative mappings.1.1 Field ExcitationNote that the field excitation for IOEX inputs/outputs MUST NOT be provided from the control cubicle battery nor the radio power supply. Doing so will breach the isolation barriers and introduce serious risk of damage or interference to the control electronics.1.2 IOEX as Local/RemoteAn IOEX can be designated from the IOEX Status Page as either Local or Remote designation. Refer to Section 8.3 (page 30) for further information on Local and Remote IOEX.1.3 IOEX Status PageThe SYSTEM STATUS – IOEX status page displays the status of the IOEX inputs and outputs to assist debugging during installation and maintenance.The top line of the display is the page title and the letter “S” to the right indicates that this page is located in the System Status Display Group. The next three lines are the data on display. To the right of the data field column is a small column showing the type of data displayed, these have significance as follows:P - Password Protected (i.e., can only be changed if the password is known).D – Display Only (i.e., cannot be changed).IOEX Status S Inputs 1 – – – – – – – – – – – – 12D LocalRemotePOutputs 1 – * – – – – – – 8D IOEX OKInvalid MapInitializingUnpluggedWrong TypeDStandard IOEX Mapping D The fields are used as follows:Field ExplanationInputs1 - - - - * - - - - - - - 12This indicates the current state of the inputs. A dash – represents the OFF state and an asterisk * the ON state.Outputs1 - * - - - - - * 8This indicates the current state of the outputs. A dash – represents the OFF state and an asterisk * the ON state.IOEX Local IOEX Remote Designates the IOEX to be eitherlocal or remote. Refer to Section8.3 (page 30) of Instruction Manual.Field ExplanationIOEX OKInvalid MapInitializingUnpluggedWrong TypeShows the status of the IOEX:“IOEX OK” means that the mappingis valid and in service.“Invalid Map” indicates a problemwith the IOEX mapping in thedatabase; contact your SiemensRepresentative for more details.“Initializing” is displayed while theIOEX is being initialized.“Unplugged” is displayed if theCAPM is not receiving data from theIOEX, check the cabling.“Wrong Type” is displayed if theIOEX hardware is detected asdifferent to the mapping; contactyour Siemens representative formore details.When the IOEX configuration is invalid or has some other problemssuch as wrong hardware type, the IOEX driver stops and flashes awarning message at the top of the screen, “IOEX ConfigurationCorrupt or Invalid”.1.4 InputsThe IOEX has 12 independent, optically isolated inputs, each withMetal Oxide Varistor (MOV) protection. DC in either polarity or ACinput signals are accepted. Input Voltage range is 60 – 130 VAC or18 – 150 VDC.InputNumberInputs ONTerminalNumberRecloser11-2Trip the switchgear, setlockout and inhibit allclose operations23-4Close the switchgear35-6SGF protection ON47-8SGF protection OFF59-10Auto Reclose ON611-12Auto Reclose OFF713-14Protection Set A Selected815-16Protection Set B Selected•The switchgear close input will only function when the controlleris set to the designated IOEX mode and the Work Tag is off. Forexample, if the IOEX card is designated as local then the IOEXclose input will only operate when the controller is in the Localmode of operation and the Work Tag is turned off. Refer toSection 8.2 (page 29) of Instruction Manual.•Tripping and controlling all other settings works in Local andRemote modes and is independent of the Work Tag status.•If the IOEX Trip input is held on while either the IOEX close ormanual close input is activated, the switchgear will not close.This is indicated in the event log by a ‘Close Blocking ON’ and‘Close Blocking OFF’ event whenever the IOEX Trip inputchanges state.•The SGF/SEF protection ON functionality operates as discussedin Section 9.11 (page 36) of Manual. If the ground faultprotection or the SGF availability for the active protection groupare turned off then the SGF protection will NOT turn on.•If both SGF protection ON and OFF inputs are on, the default is SGF protection ON •If both Auto Reclose ON and OFF inputs are on, the default is Auto Reclose ON.1.5 OutputsThe IOEX has 8 independent voltage free relay contact outputs, each with MOV protection. The contacts are rated for 150 VAC, 2A or 150 VDC, 1A non-inductive.Output Number TerminalNumberOutput On(relay closed)Output Off(relay open)125-26Tripped Closed227-28Closed Tripped329-30Flag A,OvercurrentProtection Tripindication. Seetable below.431-32Lockout Not in lockout533-34SGF protectionON SGF protection OFF635-36Auto RecloseON Auto Reclose OFF737-38Flag B,OvercurrentProtection Tripindication. Seetable below.839-40SystemHealthy (referto Section13.2.3, page50)Other conditionsTrip Source Flag A,TripIndication Flag B, Trip IndicationReset, Set to this stateon Recloser Close.Off OffPhase Trip On OnGround Trip Off OnSGF Trip On OffNote: The Trip Indicator outputs do not show other causes of a trip such as Loss of Phase.The IOEX contacts are not guaranteed to change duringfast Auto Reclose sequences but will indicate the finalsteady state condition within 300ms.1.6 System Healthy IndicatorThe IOEX System Healthy indicator is present when all of the following are true:•Aux Supply OK;•Battery Supply OK;•SCEM Data Valid;•CAPM Electronics OK;•Contact Life greater than 20% on all phases;•IOEX to CAPM communications OK; and•Mechanism OK.Failure of any of these will cause the System Healthy flag to be extinguished.1.7 Power ConsumptionIf an IOEX card is fitted to the control cubicle, the battery holdup time can be affected. This is due to the current drawn by the IOEX card and its relay coils. An IOEX card draws 10mA without any relays turned on. The relays draw approximately 20mA each for an IOEX Rev 1 and 10mA each for an IOEX Rev 2. There can be up to four relays energized at once with at least one relay energized at all times.Therefore an IOEX Rev 1 draws a minimum of 30mA and a maximum of 90mA while an IOEX Rev 2 will draw a minimum of20mA and maximum of 50mA. Battery holdup time rating is based on a recloser installation without the IOEX card installed.。
华硕(Harman Kardon)L1 模型 1S 系统与 ToneMatch 端口的使用者指南说明

L1® model 1S system with ToneMatch® portOwner’s GuideGuía de usuarioNotice d’utilisation2S AFETY I NFORMATIONPlease read this owner’s guidePlease take the time to follow the instructions in this owner’s guide carefully. It will help you set up and operate yoursystem properly and enjoy its advanced features. Please save this owner’s guide for future reference.WARNING: To reduce the risk of fire or electrical shock, do not expose the system to rain or moisture.WARNING: To reduce the risk of electric shock, do not disassemble this system unless you are qualified. Refer servicing to qualified service personnel.The lightning flash with arrowhead symbol within an equilateral triangle alerts the user to the presence of uninsulated, dangerous voltage within the system enclosure that may be of sufficient magnitude to constitute a risk of electrical shock.The exclamation point within an equilateral triangle, as marked on the system, is intended to alert the user to the presence of important operating and maintenance instructions in this owner’s guide.CAUTION: This product shall be connected to a mains socket outlet with a protective earthing connection.CAUTION: Make no modifications to the system or accessories. Unauthorized alterations may compromise safety, regulatory compliance, and system performance.CAUTION: Do not place any naked flame sources, such as lighted candles, on or near the apparatus.CAUTION: Where the mains plug or appliance coupler is used as the disconnect device, such disconnect device shall remain readily operable.Note: The product must be used indoors. It is neither designed nor tested for use outdoors, in recreation vehicles, or on boats.This product conforms to all applicable EU requirements.The complete Declaration of Conformity can be found at: /compliance.Please complete for your recordsNow is a good time to record the serial numbers of your system here and on your product registration card. You can register your product online at /register or call (800) 905-1044. Failure to do so will not affect your warranty rights.L1® model 1S power stand: _____________________________________________________________________Top array and bottom extension:_________________________________________________________________B1 or B2 bass module: _________________________________________________________________________©2012 Bose Corporation. No part of this work may be reproduced, modified, distributed, or otherwise used without prior written permission.3I MPORTANT S AFETY I NSTRUCTIONS1.Read these instructions.2.Keep these instructions.3.Heed all warnings.4.Follow all instructions.5.Do not use this apparatus near water.6.Clean only with a dry cloth.7.Do not block any ventilation openings. Install inaccordance with the manufacturer’s instruc-tions.8.Do not install near any heat sources, such asradiators, heat registers, stoves, or other appa-ratus (including amplifiers) that produce heat. 9.Do not defeat the safety purpose of the polar-ized or grounding-type plug. A polarized plug has two blades with one wider than the other. A grounding-type plug has two blades and a third grounding prong. The wider blade or third prong is provided for your safety. If the provided plug does not fit into your outlet, consult an electri-cian for replacement of the obsolete outlet.10.Protect the power cord from being walked on orpinched, particularly at plugs, conveniencereceptacles, and the point where they exit from the apparatus. 11.Only use attachments/accessories specified bythe e only with the cart, stand, tripod,bracket, or table specified by the man-ufacturer or sold with the apparatus. When a cart is used, use caution whenmoving the cart/apparatus combination to avoid injury from tip-over.13.Unplug this apparatus during lightning stormsor when unused for long periods of time.14.Refer all servicing to qualified service personnel.Servicing is required when the apparatus has been damaged in any way, such as power-supply cord or plug is damaged, liquid has been spilled or objects have fallen into the apparatus, the apparatus has been exposed to rain or moisture, does not operate normally, or has been dropped.15.To prevent risk of fire or electric shock, avoidoverloading wall outlets, extension cords, or integral convenience receptacles.16.Do not let objects or liquids enter the product –as they may touch dangerous voltage points or short-circuit parts that could result in a fire or electric shock.17.See product enclosure bottom for safety-relatedmarkings. e proper power sources – Plug the product intoa proper power source, as described in the operating instructions or as marked on the product.19.Apparatus shall not be exposed to dripping orsplashing, and no objects filled with liquids, such as vases, shall be placed on the apparatus.Information about products that generate electrical noiseNOTE: This equipment has been tested and found to comply with the limits for a Class A digital device, pursuant to part 15 of the FCC Rules.These limits are designed to provide reasonable protection against harmful interference when the equipment is operated in a commercial environment. This equipment generates, uses, and can radiate radio frequency energy and, if not installed and used in accordance with theinstruction manual, may cause harmful interference to radio communications. Operation of this equipment in a residential area is likely to cause harmful interference in which case the user will be required to correct the interference at their own expense.Changes or modifications not expressly approved by Bose Corporation could void the user's authority to operate this equipment.This Class A digital apparatus complies with Canadian ICES-003.Initial turn on inrush current: 32 AmpsInrush current after AC mains interruption of 5 seconds: 32 AmpsThis product meets all EN55103-2 immunityrequirements for E2 electromagnetic environment.I NTRODUCTION5Welcome . . . . . . . . . . . . . . . . . . . . . . . . . . . . . . . . . . . . . . . . . . . . . . . . . . . . . . . . . . . . . . . . . . . . . . . . . . . . . . . . . . . 5 Features and benefits . . . . . . . . . . . . . . . . . . . . . . . . . . . . . . . . . . . . . . . . . . . . . . . . . . . . . . . . . . . . . . . . . . . . . . . . . 5 Product overview . . . . . . . . . . . . . . . . . . . . . . . . . . . . . . . . . . . . . . . . . . . . . . . . . . . . . . . . . . . . . . . . . . . . . . . . . . . . . 6 Connections and controls . . . . . . . . . . . . . . . . . . . . . . . . . . . . . . . . . . . . . . . . . . . . . . . . . . . . . . . . . . . . . . . . . . . . . . 7S YSTEM S ETUP8 Parts list . . . . . . . . . . . . . . . . . . . . . . . . . . . . . . . . . . . . . . . . . . . . . . . . . . . . . . . . . . . . . . . . . . . . . . . . . . . . . . . . . . . . 8 Positioning your system . . . . . . . . . . . . . . . . . . . . . . . . . . . . . . . . . . . . . . . . . . . . . . . . . . . . . . . . . . . . . . . . . . . . . . . . 9 Setting up the power stand . . . . . . . . . . . . . . . . . . . . . . . . . . . . . . . . . . . . . . . . . . . . . . . . . . . . . . . . . . . . . . . . . . . . . 10 Assembling the L1® model 1S system . . . . . . . . . . . . . . . . . . . . . . . . . . . . . . . . . . . . . . . . . . . . . . . . . . . . . . . . . . . . . 10 Connecting to AC power . . . . . . . . . . . . . . . . . . . . . . . . . . . . . . . . . . . . . . . . . . . . . . . . . . . . . . . . . . . . . . . . . . . . . . . 11 Connecting the B1 or B2 bass module . . . . . . . . . . . . . . . . . . . . . . . . . . . . . . . . . . . . . . . . . . . . . . . . . . . . . . . . . . . . 12 Adding a T1 ToneMatch® audio engine (optional) . . . . . . . . . . . . . . . . . . . . . . . . . . . . . . . . . . . . . . . . . . . . . . . . . . . . 13 Adding a second B1 bass module (optional) . . . . . . . . . . . . . . . . . . . . . . . . . . . . . . . . . . . . . . . . . . . . . . . . . . . . . . . . 14O PERATING I NFORMATION 15 Setting the analog input level . . . . . . . . . . . . . . . . . . . . . . . . . . . . . . . . . . . . . . . . . . . . . . . . . . . . . . . . . . . . . . . . . . . . 15 Using a T1 ToneMatch® audio engine and an analog input source . . . . . . . . . . . . . . . . . . . . . . . . . . . . . . . . . . . . . . . 15 User scenarios . . . . . . . . . . . . . . . . . . . . . . . . . . . . . . . . . . . . . . . . . . . . . . . . . . . . . . . . . . . . . . . . . . . . . . . . . . . . . . . 15 Single musician . . . . . . . . . . . . . . . . . . . . . . . . . . . . . . . . . . . . . . . . . . . . . . . . . . . . . . . . . . . . . . . . . . . . . . . . . 15 Multiple musicians . . . . . . . . . . . . . . . . . . . . . . . . . . . . . . . . . . . . . . . . . . . . . . . . . . . . . . . . . . . . . . . . . . . . . . . 16 Full band . . . . . . . . . . . . . . . . . . . . . . . . . . . . . . . . . . . . . . . . . . . . . . . . . . . . . . . . . . . . . . . . . . . . . . . . . . . . . . . 17 DJ events . . . . . . . . . . . . . . . . . . . . . . . . . . . . . . . . . . . . . . . . . . . . . . . . . . . . . . . . . . . . . . . . . . . . . . . . . . . . . . 18C ARE AND M AINTENANCE 19 Caring for your product . . . . . . . . . . . . . . . . . . . . . . . . . . . . . . . . . . . . . . . . . . . . . . . . . . . . . . . . . . . . . . . . . . . . . . . . 19 Cleaning . . . . . . . . . . . . . . . . . . . . . . . . . . . . . . . . . . . . . . . . . . . . . . . . . . . . . . . . . . . . . . . . . . . . . . . . . . . . . . . 19 Getting service . . . . . . . . . . . . . . . . . . . . . . . . . . . . . . . . . . . . . . . . . . . . . . . . . . . . . . . . . . . . . . . . . . . . . . . . . . 19 Troubleshooting . . . . . . . . . . . . . . . . . . . . . . . . . . . . . . . . . . . . . . . . . . . . . . . . . . . . . . . . . . . . . . . . . . . . . . . . . . . . . . 19 Limited Warranty and Registration . . . . . . . . . . . . . . . . . . . . . . . . . . . . . . . . . . . . . . . . . . . . . . . . . . . . . . . . . . . . . . . . 21 Accessories . . . . . . . . . . . . . . . . . . . . . . . . . . . . . . . . . . . . . . . . . . . . . . . . . . . . . . . . . . . . . . . . . . . . . . . . . . . . . . . . . 21 Technical Information . . . . . . . . . . . . . . . . . . . . . . . . . . . . . . . . . . . . . . . . . . . . . . . . . . . . . . . . . . . . . . . . . . . . . . . . . . 21 Mechanical . . . . . . . . . . . . . . . . . . . . . . . . . . . . . . . . . . . . . . . . . . . . . . . . . . . . . . . . . . . . . . . . . . . . . . . . . . . . . 21 Electrical . . . . . . . . . . . . . . . . . . . . . . . . . . . . . . . . . . . . . . . . . . . . . . . . . . . . . . . . . . . . . . . . . . . . . . . . . . . . . . . 21 Audio Input/Output . . . . . . . . . . . . . . . . . . . . . . . . . . . . . . . . . . . . . . . . . . . . . . . . . . . . . . . . . . . . . . . . . . . . . . . 214I NTRODUCTIONWelcomeThank you for purchasing the Bose® L1® model 1S system with ToneMatch® port. Based on arevolutionary new technology, this system brings the benefits of an intimate acoustic concertto amplified performance.This owner’s guide provides detailed setup and operating instructions for your L1 system andexplains how to connect equipment to it.For additional information on using this system, including tips, techniques, and frequentlyasked questions, please visit /livesound on the Internet.Features and benefits•You control the sound – Just as in an unamplified performance, you control the sound.You will no longer wonder how you sound to your fellow musicians or to your audiencebecause you will hear what they hear.•Quick and easy setup – The L1 system is easy to carry and can be set up in minutes, nothours. This frees you from the time-consuming and often frustrating effort required to prop-erly set up conventional sound equipment.•Dramatically improved performance – Compared to using conventional equipment,performance and enjoyment dramatically improve because the struggle to hear yourselfand the other musicians is diminished.•Creates excitement and emotion – Enhanced performance of the musicians creates thekind of excitement and emotion that is valued by music lovers.•You hear what the audience hears – For the first time, musicians hear what theiraudiences hear and thus, are less likely to play at uncomfortable sound levels.•The music is naturally dynamic – The softest to the most intense passages can beheard and enjoyed.•Improves your appearance – There is less equipment on the stage and more room.•Sound reproduction unlike before – Audience members report that the clarity andexcitement that come from hearing the accurate reproduction of sound from eachinstrument, and from hearing the sound of each instrument in its position on stage(as opposed to mono or even stereo mix of all instruments), is unlike anything they haveheard before in an amplified performance.56I NTRODUCTIONProduct overviewThe L1® model 1S system – with ToneMatch ® port consists of: the power stand, bottomextension, top array, and a B1 or B2 bass module. The system also comes with a padded carrying bag for each of its parts.To expand your system and enhance performance, you can add:•A second B1 bass module for bass guitar, kick drum, or organ. Each power stand can power up to two B1 bass modules.•A T1 ToneMatch audio engine for digital signal processing, additional inputs and user-inter-face control.For a complete list of optional equipment and accessories, please visit: /livesound.Figure 1optional equipmentL1 model 1S system with ToneMatch port and B1 bass moduleOptional equipment B1 bass moduleB2 bass moduleI NTRODUCTION® port78S YSTEM S ETUPParts listThe L1® system is shipped in three cartons. Carefully unpack the cartons and check that youhave all the items listed on this page.WARNING: To avoid danger of suffocation, keep the plastic bags out of the reach of children.S YSTEM S ETUPPositioning your systemPlacing the power stand in the right location is an important part of setting up this product.Determining the best location for your performance depends on several things.•Size of staging area•Number of performers•Shared system (adding a T1 ToneMatch® audio engine and multiple instruments)The following guidelines should get you started in setting up for a concert or show.•Set up your system in the rear area of the performance stage.•If possible, position your system behind the performer(s).•If you are part of a group, avoid crowding together on stage. Allow some distance,ideally 7-8 feet (2.1-2.4 m), between you and the L1® system and anotherperformer. This allows the sound to wrap around performers and reflect off adjacentsurfaces of the room, creating a more pleasing room-filling sound.Figure 1recommendationsBest910S YSTEM S ETUPSetting up the power stand1.The legs must be 2.Figure 2Putting the power stand on the floorchosen location before assembling the system.Figure 3Setting up the systemCAUTION: Bose recommends using a quality surge suppressor on all electronic equipment. Voltage variations and spikes can damage electronic components in any system. A quality suppressor, which can eliminate the vast majority of failures attributed to surges, may bepurchased at electronics stores.S YSTEM S ETUPFigure 5B1 and B2 bass modulesCAUTIONS:•DO NOT connect any bass module other than the B1 or B2 to the power stand.•DO NOT substitute the supplied cable with a 2-wire speaker cable. Use only the supplied B1 bass module 4-wire cable to connect the B1 bass module to the power stand. The power stand uses the signals on two of the wires to automatically sense how many B1 or B2 bass modules are connected.•DO NOT connect a B1 or B2 bass module to two power stands at the same time.S YSTEM S ETUPAdding a T1 ToneMatch ® audio engine (optional)The T1 ToneMatch ® audio engine provides additional input/output capabilities to yoursystem, plus digital signal processing to customize the way you sound. The audio engine comes with hardware for mounting it on the left or right side of the bottom extension.Note: The audio engine mounts on the bottom section of the loudspeaker and requires removal of the top section before starting this procedure.1.Slide the carriage into the channel on the rear of the bottom extension and turn the knob clockwise to lock it in place (Figure 6).2.Insert the mounting bar into the slot in the carriage and push it downward.3.Place the T1 on the mounting bar as shown.4.Plug one end of the ToneMatch cable (supplied with the audio engine) into the ToneMatch output port () on the T1.ing the hook and loop strap, secure the cable to the carriage.6.Plug the other end of the cable into the ToneMatch port on the power stand.Figure 6Mounting the T1S YSTEM S ETUPAdding a second B1 bass module (optional)The bass module output of the power stand can adequately drive one or two B1 bass1.2.Figure 7Installation of two B1 bassmodulescableO PERATING I NFORMATIONO PERATING I NFORMATIONSetting the analog input levelWhen connecting an audio source to the Analog Input, follow these steps to adjust the inputTrim control.1.Set the Trim control on the power stand to the 0 (zero) position.2.Connect the audio source to the Analog Input.3.Adjust the volume of the audio source to the desired level.4.While playing the source, increase the Trim level until the Signal/Clip indicator glowsgreen or yellow.5.If the Signal/Clip indicator glows red, decrease the Trim level so that it glows only greenor yellow.®C ARE AND M AINTENANCEC ARE AND M AINTENANCE Caring for your productCleaning•Clean the product enclosures using only a soft, dry cloth.•Do not use any solvents, chemicals, or cleaning solutions containing alcohol, ammonia,or abrasives.•Do not use any sprays near the product or allow liquids to spill into any openings.•If necessary, you may carefully vacuum the grille of the L1® loudspeaker.Getting serviceFor additional help in solving problems, contact Bose® Live Music Customer Service Productand Technical Support Team at (877) 335-2673 or visit our support area online at/livesound.TroubleshootingIf you experience problems while using this product, try the following solutions. If you stillcan’t solve the problem, please call the Bose Live Music Product and Technical SupportTeam direct at (877) 335-2673 to arrange for service.Recommended troubleshooting tools•Portable voltmeter •XLR and ¼" phone plug cables•Cable tester•B1 bass module 4-wire cable•AC outlet tester•Spare AC power cordProblem What to doSystem is plugged in, power switch is on, but power LED is off •Make sure you have power at the AC outlet. Try operating a lamp or other equipment from the same AC outlet or test the outlet using an AC outlet tester.•Make sure the power stand’s power cord plug is fully inserted into the AC outlet.Power LED is on (green), but no sound •Make sure volume control is turned up on your instrument.•Make sure the Trim level control is turned up on the power stand.•Make sure your instrument is plugged into the Analog Input jack.•Connect your instrument to the power stand using a different cable.•Plug your instrument into a different amplifier to make sure the instrument is working.Power LED is red while thepower stand is on•Please call Bose Live Music Customer Support at (877) 335-2673 for assistance.House circuit breaker keeps tripping •If more than one power stand is plugged into the same AC circuit, stagger the turn-on times. Each power stand has an inrush current of about 32 amps when turned on.•If you have more than three power stands plugged into a single 15 amp circuit, move some systems to another AC circuit. Each power stand can draw 5 amps or more when playing at high volumes for long periods of time.C ARE AND M AINTENANCEWith nothing plugged into the power stand, a slight hum or buzz is heard •Using an AC outlet tester, test the AC outlet that the power stand is plugged into for reversed or open (hot, neutral, and/or ground) contacts.•If using an extension cord, make sure that the cord is also tested as above.B1 or B2 bass module is plugged in, but no bass audio is heard •Make sure you are using the included 4-wire B1/B2 bass module cable.•Make sure the B1 or B2 bass module cable is plugged into the Bass Module Out connector and the cable plug is fully engaged in the connector.•Try a different 4-wire cable.•If available, try a different B1/B2 bass module.B1 bass module sounds out of balance with the system •Make sure you are using the B1/B2 bass module 4-wire cable included with the B1 bass module package.•Make sure that the B1 or B2 bass module grille is facing forward toward the musicians and audience.No mid/high sounds heard from the L1® top array •Make sure the L1 top array and bottom extension are firmly seated in their connectors.•Make sure connections are not bent or broken.•Try cleaning the contacts on the loudspeaker top and bottom with electronic contact spray cleaner.Instrument or audio source sounds distorted •Make sure the Signal/Clip LED is not constantly red. If it is, lower the trim level.•Try a different source or instrument.•Try your source or instrument on another power stand.Microphone is encountering feedback •Orient the microphone so that it is not pointing directly at its respective L1 system.•Try a different microphone.•Try a different position for the loudspeaker and/or vocalist on stage.•Increase the distance from the loudspeaker to the microphone.•If using a vocal effects processor, make sure it is not contributing to the feedback problem.Problem What to do21C ARE AND M AINTENANCELimited Warranty and RegistrationYour product is covered by a limited warranty. Details of the warranty are provided with your product. Register your products online at /register or call (800) 905-1044. Failure to do so will not affect your warranty rights.AccessoriesVisit /livesound, or call (800) 905-0886 for accessory information.Technical InformationMechanicalComponent Dimensions Weight Power stand:5''H x 10''W x 27''D (12.8 cm x 26.2 cm x 69.2 cm)23.7 lb(10.7 kg)Top array:43½''H x 3½''W x 4''D (111.0 cm x 9.0 cm x 10.5 cm)16.3 lb(7.4 kg)Bottom extension:39.63''H x 4.15''W x 4.13''D (100.6 cm x 10.6 cm x 10.5 cm)8.5 lb(3.8 kg)B1 bass module:15''H x 10¼''W x 17¾''D (38.0 cm x 26.0 cm x 45.0 cm)25.1 lb(11.4 kg)B2 bass module:23.4''H x 13.31''W x 18.9''D (59.4 cm x 33.8 cm x 48 cm)45 lb(20.41 kg)Electrical•AC power rating:50/60Hz 500W (Europe)•Peak inrush current:50Hz (Europe)Component ImpedanceL1® model 1S loudspeaker:ΩB1 bass module:8ΩB2 bass module:4ΩAudio Input/Output•T1 ToneMatch ® port:DC output/data input Ethercon/RJ45 connector for aT1 ToneMatch audio engine•Analog Input:Line-level input channel for ¼" TRS phone plug•Bass Module Out:Neutrik ® NL4 output for one or two B1 bass modulesL1 and ToneMatch are registered trademarks of Bose Corporation in the U.S. and other countries. All trademarks are the property of their respective owners.8©2012 Bose Corporation, The Mountain, Framingham, MA 01701-9168 USAAM356144 Rev.00/livesound。
Indradrive 系列 故障代码
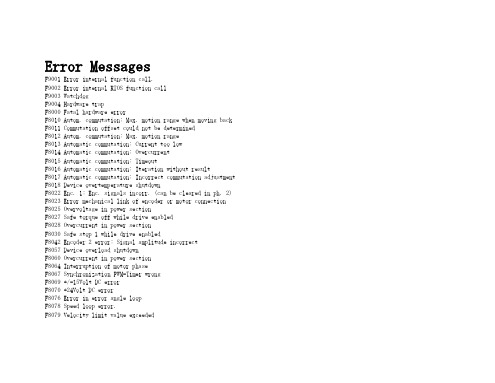
Error MessagesF9001 Error internal function call.F9002 Error internal RTOS function callF9003 WatchdogF9004 Hardware trapF8000 Fatal hardware errorF8010 Autom. commutation: Max. motion range when moving back F8011 Commutation offset could not be determinedF8012 Autom. commutation: Max. motion rangeF8013 Automatic commutation: Current too lowF8014 Automatic commutation: OvercurrentF8015 Automatic commutation: TimeoutF8016 Automatic commutation: Iteration without resultF8017 Automatic commutation: Incorrect commutation adjustment F8018 Device overtemperature shutdownF8022 Enc. 1: Enc. signals incorr. (can be cleared in ph. 2) F8023 Error mechanical link of encoder or motor connectionF8025 Overvoltage in power sectionF8027 Safe torque off while drive enabledF8028 Overcurrent in power sectionF8030 Safe stop 1 while drive enabledF8042 Encoder 2 error: Signal amplitude incorrectF8057 Device overload shutdownF8060 Overcurrent in power sectionF8064 Interruption of motor phaseF8067 Synchronization PWM-Timer wrongF8069 +/-15Volt DC errorF8070 +24Volt DC errorF8076 Error in error angle loopF8078 Speed loop error.F8079 Velocity limit value exceededF8091 Power section defectiveF8100 Error when initializing the parameter handlingF8102 Error when initializing power sectionF8118 Invalid power section/firmware combinationF8120 Invalid control section/firmware combinationF8122 Control section defectiveF8129 Incorrect optional module firmwareF8130 Firmware of option 2 of safety technology defectiveF8133 Error when checking interrupting circuitsF8134 SBS: Fatal errorF8135 SMD: Velocity exceededF8140 Fatal CCD error.F8201 Safety command for basic initialization incorrectF8203 Safety technology configuration parameter invalidF8813 Connection error mains chokeF8830 Power section errorF8838 Overcurrent external braking resistorF7010 Safely-limited increment exceededF7011 Safely-monitored position, exceeded in pos. DirectionF7012 Safely-monitored position, exceeded in neg. DirectionF7013 Safely-limited speed exceededF7020 Safe maximum speed exceededF7021 Safely-limited position exceededF7030 Position window Safe stop 2 exceededF7031 Incorrect direction of motionF7040 Validation error parameterized - effective thresholdF7041 Actual position value validation errorF7042 Validation error of safe operation modeF7043 Error of output stage interlockF7050 Time for stopping process exceeded8.3.15 F7051 Safely-monitored deceleration exceeded (159)8.4 Travel Range Errors (F6xxx) (161)8.4.1 Behavior in the Case of Travel Range Errors (161)8.4.2 F6010 PLC Runtime Error (162)8.4.3 F6024 Maximum braking time exceeded (163)8.4.4 F6028 Position limit value exceeded (overflow) (164)8.4.5 F6029 Positive position limit exceeded (164)8.4.6 F6030 Negative position limit exceeded (165)8.4.7 F6034 Emergency-Stop (166)8.4.8 F6042 Both travel range limit switches activated (167)8.4.9 F6043 Positive travel range limit switch activated (167)8.4.10 F6044 Negative travel range limit switch activated (168)8.4.11 F6140 CCD slave error (emergency halt) (169)8.5 Interface Errors (F4xxx) (169)8.5.1 Behavior in the Case of Interface Errors (169)8.5.2 F4001 Sync telegram failure (170)8.5.3 F4002 RTD telegram failure (171)8.5.4 F4003 Invalid communication phase shutdown (172)8.5.5 F4004 Error during phase progression (172)8.5.6 F4005 Error during phase regression (173)8.5.7 F4006 Phase switching without ready signal (173)8.5.8 F4009 Bus failure (173)8.5.9 F4012 Incorrect I/O length (175)8.5.10 F4016 PLC double real-time channel failure (176)8.5.11 F4017 S-III: Incorrect sequence during phase switch (176)8.5.12 F4034 Emergency-Stop (177)8.5.13 F4140 CCD communication error (178)8.6 Non-Fatal Safety Technology Errors (F3xxx) (178)8.6.1 Behavior in the Case of Non-Fatal Safety Technology Errors (178)8.6.2 F3111 Refer. missing when selecting safety related end pos (179)8.6.3 F3112 Safe reference missing (179)8.6.4 F3115 Brake check time interval exceeded (181)Troubleshooting Guide | Rexroth IndraDrive Electric Drivesand ControlsI Bosch Rexroth AG VII/XXIITable of ContentsPage8.6.5 F3116 Nominal load torque of holding system exceeded (182)8.6.6 F3117 Actual position values validation error (182)8.6.7 F3122 SBS: System error (183)8.6.8 F3123 SBS: Brake check missing (184)8.6.9 F3130 Error when checking input signals (185)8.6.10 F3131 Error when checking acknowledgment signal (185)8.6.11 F3132 Error when checking diagnostic output signal (186)8.6.12 F3133 Error when checking interrupting circuits (187)8.6.13 F3134 Dynamization time interval incorrect (188)8.6.14 F3135 Dynamization pulse width incorrect (189)8.6.15 F3140 Safety parameters validation error (192)8.6.16 F3141 Selection validation error (192)8.6.17 F3142 Activation time of enabling control exceeded (193)8.6.18 F3143 Safety command for clearing errors incorrect (194)8.6.19 F3144 Incorrect safety configuration (195)8.6.20 F3145 Error when unlocking the safety door (196)8.6.21 F3146 System error channel 2 (197)8.6.22 F3147 System error channel 1 (198)8.6.23 F3150 Safety command for system start incorrect (199)8.6.24 F3151 Safety command for system halt incorrect (200)8.6.25 F3152 Incorrect backup of safety technology data (201)8.6.26 F3160 Communication error of safe communication (202)8.7 Non-Fatal Errors (F2xxx) (202)8.7.1 Behavior in the Case of Non-Fatal Errors (202)8.7.2 F2002 Encoder assignment not allowed for synchronization (203)8.7.3 F2003 Motion step skipped (203)8.7.4 F2004 Error in MotionProfile (204)8.7.5 F2005 Cam table invalid (205)8.7.6 F2006 MMC was removed (206)8.7.7 F2007 Switching to non-initialized operation mode (206)8.7.8 F2008 RL The motor type has changed (207)8.7.9 F2009 PL Load parameter default values (208)8.7.10 F2010 Error when initializing digital I/O (-> S-0-0423) (209)8.7.11 F2011 PLC - Error no. 1 (210)8.7.12 F2012 PLC - Error no. 2 (210)8.7.13 F2013 PLC - Error no. 3 (211)8.7.14 F2014 PLC - Error no. 4 (211)8.7.15 F2018 Device overtemperature shutdown (211)8.7.16 F2019 Motor overtemperature shutdown (212)8.7.17 F2021 Motor temperature monitor defective (213)8.7.18 F2022 Device temperature monitor defective (214)8.7.19 F2025 Drive not ready for control (214)8.7.20 F2026 Undervoltage in power section (215)8.7.21 F2027 Excessive oscillation in DC bus (216)8.7.22 F2028 Excessive deviation (216)8.7.23 F2031 Encoder 1 error: Signal amplitude incorrect (217)VIII/XXII Bosch Rexroth AG | Electric Drivesand ControlsRexroth IndraDrive | Troubleshooting GuideTable of ContentsPage8.7.24 F2032 Validation error during commutation fine adjustment (217)8.7.25 F2033 External power supply X10 error (218)8.7.26 F2036 Excessive position feedback difference (219)8.7.27 F2037 Excessive position command difference (220)8.7.28 F2039 Maximum acceleration exceeded (220)8.7.29 F2040 Device overtemperature 2 shutdown (221)8.7.30 F2042 Encoder 2: Encoder signals incorrect (222)8.7.31 F2043 Measuring encoder: Encoder signals incorrect (222)8.7.32 F2044 External power supply X15 error (223)8.7.33 F2048 Low battery voltage (224)8.7.34 F2050 Overflow of target position preset memory (225)8.7.35 F2051 No sequential block in target position preset memory (225)8.7.36 F2053 Incr. encoder emulator: Pulse frequency too high (226)8.7.37 F2054 Incr. encoder emulator: Hardware error (226)8.7.38 F2055 External power supply dig. I/O error (227)8.7.39 F2057 Target position out of travel range (227)8.7.40 F2058 Internal overflow by positioning input (228)8.7.41 F2059 Incorrect command value direction when positioning (229)8.7.42 F2063 Internal overflow master axis generator (230)8.7.43 F2064 Incorrect cmd value direction master axis generator (230)8.7.44 F2067 Synchronization to master communication incorrect (231)8.7.45 F2068 Brake error (231)8.7.46 F2069 Error when releasing the motor holding brake (232)8.7.47 F2074 Actual pos. value 1 outside absolute encoder window (232)8.7.48 F2075 Actual pos. value 2 outside absolute encoder window (233)8.7.49 F2076 Actual pos. value 3 outside absolute encoder window (234)8.7.50 F2077 Current measurement trim wrong (235)8.7.51 F2086 Error supply module (236)8.7.52 F2087 Module group communication error (236)8.7.53 F2100 Incorrect access to command value memory (237)8.7.54 F2101 It was impossible to address MMC (237)8.7.55 F2102 It was impossible to address I2C memory (238)8.7.56 F2103 It was impossible to address EnDat memory (238)8.7.57 F2104 Commutation offset invalid (239)8.7.58 F2105 It was impossible to address Hiperface memory (239)8.7.59 F2110 Error in non-cyclical data communic. of power section (240)8.7.60 F2120 MMC: Defective or missing, replace (240)8.7.61 F2121 MMC: Incorrect data or file, create correctly (241)8.7.62 F2122 MMC: Incorrect IBF file, correct it (241)8.7.63 F2123 Retain data backup impossible (242)8.7.64 F2124 MMC: Saving too slowly, replace (243)8.7.65 F2130 Error comfort control panel (243)8.7.66 F2140 CCD slave error (243)8.7.67 F2150 MLD motion function block error (244)8.7.68 F2174 Loss of motor encoder reference (244)8.7.69 F2175 Loss of optional encoder reference (245)Troubleshooting Guide | Rexroth IndraDrive Electric Drivesand Controls| Bosch Rexroth AG IX/XXIITable of ContentsPage8.7.70 F2176 Loss of measuring encoder reference (246)8.7.71 F2177 Modulo limitation error of motor encoder (246)8.7.72 F2178 Modulo limitation error of optional encoder (247)8.7.73 F2179 Modulo limitation error of measuring encoder (247)8.7.74 F2190 Incorrect Ethernet configuration (248)8.7.75 F2260 Command current limit shutoff (249)8.7.76 F2270 Analog input 1 or 2, wire break (249)8.7.77 F2802 PLL is not synchronized (250)8.7.78 F2814 Undervoltage in mains (250)8.7.79 F2815 Overvoltage in mains (251)8.7.80 F2816 Softstart fault power supply unit (251)8.7.81 F2817 Overvoltage in power section (251)8.7.82 F2818 Phase failure (252)8.7.83 F2819 Mains failure (253)8.7.84 F2820 Braking resistor overload (253)8.7.85 F2821 Error in control of braking resistor (254)8.7.86 F2825 Switch-on threshold braking resistor too low (255)8.7.87 F2833 Ground fault in motor line (255)8.7.88 F2834 Contactor control error (256)8.7.89 F2835 Mains contactor wiring error (256)8.7.90 F2836 DC bus balancing monitor error (257)8.7.91 F2837 Contactor monitoring error (257)8.7.92 F2840 Error supply shutdown (257)8.7.93 F2860 Overcurrent in mains-side power section (258)8.7.94 F2890 Invalid device code (259)8.7.95 F2891 Incorrect interrupt timing (259)8.7.96 F2892 Hardware variant not supported (259)8.8 SERCOS Error Codes / Error Messages of Serial Communication (259)9 Warnings (Exxxx) (263)9.1 Fatal Warnings (E8xxx) (263)9.1.1 Behavior in the Case of Fatal Warnings (263)9.1.2 E8025 Overvoltage in power section (263)9.1.3 E8026 Undervoltage in power section (264)9.1.4 E8027 Safe torque off while drive enabled (265)9.1.5 E8028 Overcurrent in power section (265)9.1.6 E8029 Positive position limit exceeded (266)9.1.7 E8030 Negative position limit exceeded (267)9.1.8 E8034 Emergency-Stop (268)9.1.9 E8040 Torque/force actual value limit active (268)9.1.10 E8041 Current limit active (269)9.1.11 E8042 Both travel range limit switches activated (269)9.1.12 E8043 Positive travel range limit switch activated (270)9.1.13 E8044 Negative travel range limit switch activated (271)9.1.14 E8055 Motor overload, current limit active (271)9.1.15 E8057 Device overload, current limit active (272)X/XXII Bosch Rexroth AG | Electric Drivesand ControlsRexroth IndraDrive | Troubleshooting GuideTable of ContentsPage9.1.16 E8058 Drive system not ready for operation (273)9.1.17 E8260 Torque/force command value limit active (273)9.1.18 E8802 PLL is not synchronized (274)9.1.19 E8814 Undervoltage in mains (275)9.1.20 E8815 Overvoltage in mains (275)9.1.21 E8818 Phase failure (276)9.1.22 E8819 Mains failure (276)9.2 Warnings of Category E4xxx (277)9.2.1 E4001 Double MST failure shutdown (277)9.2.2 E4002 Double MDT failure shutdown (278)9.2.3 E4005 No command value input via master communication (279)9.2.4 E4007 SERCOS III: Consumer connection failed (280)9.2.5 E4008 Invalid addressing command value data container A (280)9.2.6 E4009 Invalid addressing actual value data container A (281)9.2.7 E4010 Slave not scanned or address 0 (281)9.2.8 E4012 Maximum number of CCD slaves exceeded (282)9.2.9 E4013 Incorrect CCD addressing (282)9.2.10 E4014 Incorrect phase switch of CCD slaves (283)9.3 Possible Warnings When Operating Safety Technology (E3xxx) (283)9.3.1 Behavior in Case a Safety Technology Warning Occurs (283)9.3.2 E3100 Error when checking input signals (284)9.3.3 E3101 Error when checking acknowledgment signal (284)9.3.4 E3102 Actual position values validation error (285)9.3.5 E3103 Dynamization failed (285)9.3.6 E3104 Safety parameters validation error (286)9.3.7 E3105 Validation error of safe operation mode (286)9.3.8 E3106 System error safety technology (287)9.3.9 E3107 Safe reference missing (287)9.3.10 E3108 Safely-monitored deceleration exceeded (288)9.3.11 E3110 Time interval of forced dynamization exceeded (289)9.3.12 E3115 Prewarning, end of brake check time interval (289)9.3.13 E3116 Nominal load torque of holding system reached (290)9.4 Non-Fatal Warnings (E2xxx) (290)9.4.1 Behavior in Case a Non-Fatal Warning Occurs (290)9.4.2 E2010 Position control with encoder 2 not possible (291)9.4.3 E2011 PLC - Warning no. 1 (291)9.4.4 E2012 PLC - Warning no. 2 (291)9.4.5 E2013 PLC - Warning no. 3 (292)9.4.6 E2014 PLC - Warning no. 4 (292)9.4.7 E2021 Motor temperature outside of measuring range (292)9.4.8 E2026 Undervoltage in power section (293)9.4.9 E2040 Device overtemperature 2 prewarning (294)9.4.10 E2047 Interpolation velocity = 0 (294)9.4.11 E2048 Interpolation acceleration = 0 (295)9.4.12 E2049 Positioning velocity >= limit value (296)9.4.13 E2050 Device overtemp. Prewarning (297)Troubleshooting Guide | Rexroth IndraDrive Electric Drivesand Controls| Bosch Rexroth AG XI/XXIITable of ContentsPage9.4.14 E2051 Motor overtemp. prewarning (298)9.4.15 E2053 Target position out of travel range (298)9.4.16 E2054 Not homed (300)9.4.17 E2055 Feedrate override S-0-0108 = 0 (300)9.4.18 E2056 Torque limit = 0 (301)9.4.19 E2058 Selected positioning block has not been programmed (302)9.4.20 E2059 Velocity command value limit active (302)9.4.21 E2061 Device overload prewarning (303)9.4.22 E2063 Velocity command value > limit value (304)9.4.23 E2064 Target position out of num. range (304)9.4.24 E2069 Holding brake torque too low (305)9.4.25 E2070 Acceleration limit active (306)9.4.26 E2074 Encoder 1: Encoder signals disturbed (306)9.4.27 E2075 Encoder 2: Encoder signals disturbed (307)9.4.28 E2076 Measuring encoder: Encoder signals disturbed (308)9.4.29 E2077 Absolute encoder monitoring, motor encoder (encoder alarm) (308)9.4.30 E2078 Absolute encoder monitoring, opt. encoder (encoder alarm) (309)9.4.31 E2079 Absolute enc. monitoring, measuring encoder (encoder alarm) (309)9.4.32 E2086 Prewarning supply module overload (310)9.4.33 E2092 Internal synchronization defective (310)9.4.34 E2100 Positioning velocity of master axis generator too high (311)9.4.35 E2101 Acceleration of master axis generator is zero (312)9.4.36 E2140 CCD error at node (312)9.4.37 E2270 Analog input 1 or 2, wire break (312)9.4.38 E2802 HW control of braking resistor (313)9.4.39 E2810 Drive system not ready for operation (314)9.4.40 E2814 Undervoltage in mains (314)9.4.41 E2816 Undervoltage in power section (314)9.4.42 E2818 Phase failure (315)9.4.43 E2819 Mains failure (315)9.4.44 E2820 Braking resistor overload prewarning (316)9.4.45 E2829 Not ready for power on (316)。
ALC221_DataSheet_0.65_Punch_Type AUDIO CODECO

4. BLOCK DIAGRAM ...........................................................................................................................................................5
2.1. HARDWARE FEATURES .................................................................................................................................................2 2.2. SOFTWARE FEATURES ..................................................................................................................................................4
USING THIS DOCUMENT
This document is intended for the hardware and software engineer’s general information on the Realtek ALC221 HD Audio Codec IC.
Though every effort has been made to ensure that this document is current and accurate, more information may have become available subsequent to the production of this guide. In that event, please contact your Realtek representative for additional information that may help in the development process.
Silicon Labs 芯片评估板 套件说明书
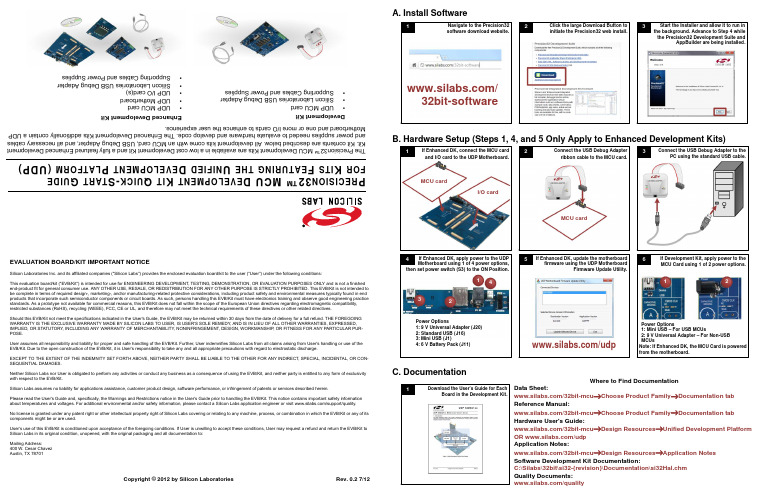
EVALUATION BOARD/KIT IMPORTANT NOTICESilicon Laboratories Inc. and its affiliated companies ("Silicon Labs") provides the enclosed evaluation board/kit to the user ("User") under the following conditions:This evaluation board/kit ("EVB/Kit") is intended for use for ENGINEERING DEVELOPMENT, TESTING, DEMONSTRATION, OR EVALUATION PURPOSES ONLY and is not a finished end-product fit for general consumer use. ANY OTHER USE, RESALE, OR REDISTRIBUTION FOR ANY OTHER PURPOSE IS STRICTLY PROHIBITED. This EVB/Kit is not intended to be complete in terms of required design-, marketing-, and/or manufacturing-related protective considerations, including product safety and environmental measures typically found in end products that incorporate such semiconductor components or circuit boards. As such, persons handling this EVB/Kit must have electronics training and observe good engineering practice standards. As a prototype not available for commercial reasons, this EVB/Kit does not fall within the scope of the European Union directives regarding electromagnetic compatibility, restricted substances (RoHS), recycling (WEEE), FCC, CE or UL, and therefore may not meet the technical requirements of these directives or other related directives.Should this EVB/Kit not meet the specifications indicated in the User's Guide, the EVB/Kit may be returned within 30 days from the date of delivery for a full refund. THE FOREGOING WARRANTY IS THE EXCLUSIVE WARRANTY MADE BY SILICON LABS TO USER, IS USER'S SOLE REMEDY , AND IS IN LIEU OF ALL OTHER WARRANTIES, EXPRESSED, IMPLIED, OR STATUTORY , INCLUDING ANY WARRANTY OF MERCHANTABILITY , NONINFRINGEMENT, DESIGN, WORKMANSHIP , OR FITNESS FOR ANY PARTICULAR PUR-POSE.User assumes all responsibility and liability for proper and safe handling of the EVB/Kit. Further, User indemnifies Silicon Labs from all claims arising from User's handling or use of the EVB/Kit. Due to the open construction of the EVB/Kit, it is User's responsibility to take any and all appropriate precautions with regard to electrostatic discharge.EXCEPT TO THE EXTENT OF THE INDEMNITY SET FORTH ABOVE, NEITHER PARTY SHALL BE LIABLE TO THE OTHER FOR ANY INDIRECT, SPECIAL, INCIDENTAL, OR CON-SEQUENTIAL DAMAGES.Neither Silicon Labs nor User is obligated to perform any activities or conduct any business as a consequence of using the EVB/Kit, and neither party is entitled to any form of exclusivity with respect to the EVB/Kit.Silicon Labs assumes no liability for applications assistance, customer product design, software performance, or infringement of patents or services described herein.Please read the User's Guide and, specifically, the Warnings and Restrictions notice in the User's Guide prior to handling the EVB/Kit. This notice contains important safety information about temperatures and voltages. For additional environmental and/or safety information, please contact a Silicon Labs application engineer or visit /support/quality.No license is granted under any patent right or other intellectual property right of Silicon Labs covering or relating to any machine, process, or combination in which the EVB/Kit or any of its components might be or are used.User's use of this EVB/Kit is conditioned upon acceptance of the foregoing conditions. If User is unwilling to accept these conditions, User may request a refund and return the EVB/Kit to Silicon Labs in its original condition, unopened, with the original packaging and all documentation to:Mailing Address:400 W. Cesar Chavez Austin, TX 78701Copyright © 2012 by Silicon Laboratories Rev. 0.2 7/12P R E C I S I O N 32™ M C U D E V E L O P M E N T K I T Q U I C K -S T A R T G U I D E F O R K I T S F E A T U R I N G T H E U N I F I E D D E V E L O P M E N T P L A T F O R M (U D P )T h e P r e c i s i o n 32™ M C U D e v e l o p m e n t K i t s a r e a v a i l a b l e i n a l o w c o s t D e v e l o p m e n t K i t a n d a f u l l y f e a t u r e d E n h a n c e d D e v e l o p m e n t K i t . K i t c o n t e n t s a r e d e s c r i b e d b e l o w . A l l d e v e l o p m e n t k i t s c o m e w i t h a n M C U c a r d , U S B D e b u g A d a p t e r , a n d a l l n e c e s s a r y c a b l e s a n d p o w e r s u p p l i e s n e e d e d t o e v a l u a t e h a r d w a r e a n d d e v e l o p c o d e . T h e E n h a n c e d D e v e l o p m e n t K i t s a d d i t i o n a l l y c o n t a i n a U D PM o t h e r b o a r d a n d o n e o r m o r e I /O c a r d s t o e n h a n c e t h e u s e r e x p e r i e n c e .D e v e l o p m e n t K i t•U D P M C U c a r d•S i l i c o n L a b o r a t o r i e s U S B D e b u g A d a p t e r •S u p p o r t i n g C a b l e s a n d P o w e r S u p p l i esE n h a n c e d D e v e l o p m e n t K i t•U D P M C U c a r d•U D P M o t h e r b o a r d •U D P I /O c a r d (s )•S i l i c o n L a b o r a t o r i e s U S B D e b u g A d a p t e r •S u p p o r t i n g C a b l e s a n d P o w e r S u p p l i e sA. Install SoftwareB. Hardware Setup (Steps 1, 4, and 5 Only Apply to Enhanced Development Kits)C. Documentation12Click the large Download Button to initiate the Precision32 web install.Navigate to the Precision32 software download website.3Start the Installer and allow it to run in the background. Advance to Step 4 while the Precision32 Development Suite andAppBuilder are being installed./32bit-software1Connect the USB Debug Adapter ribbon cable to the MCU card.2Connect the USB Debug Adapter to thePC using the standard USB cable.I/O cardMCU card45If Enhanced DK, apply power to the UDP Motherboard using 1 of 4 power options,Power Options1: 9 V Universal Adapter (J20)2: Standard USB (J16) 3: Mini USB (J1)4: 6 V Battery Pack (J11)then set power switch (S3) to the ON Position.If Development Kit, apply power to the MCU Card using 1 of 2 power options.Power Options1: Mini USB – For USB MCUs2: 9 V Universal Adapter – For Non-USB MCUsIf Enhanced DK, update the motherboardfirmware using the UDP MotherboardFirmware Update Utility./udpMCU card321412Note: If Enhanced DK, the MCU Card is powered from the motherboard.36If Enhanced DK, connect the MCU card and I/O card to the UDP Motherboard.1Download the User’s Guide for EachBoard in the Development Kit.Where to Find DocumentationData Sheet:/32bit-mcu →Choose Product Family →Documentation tab Reference Manual:/32bit-mcu →Choose Product Family →Documentation tab Hardware User's Guide:/32bit-mcu →Design Resources →Unified Development Platform OR /udp Application Notes:/32bit-mcu →Design Resources →Application Notes Software Development Kit Documentation:C:\Silabs\32bit\si32-{revision}\Documentation\si32Hal.chm Quality Documents:/qualityE . U s i n g t h e P r e c i s i o n 32 D e v e l o p m e n t S u i t eT h e P r e c i s i o n 32 D e v e l o p m e n t S u i t e i s a c o m p l e t e d e v e l o p m e n t s y s t e m f o r S i l i c o n L a b s 32-b i t M C U s . T h e D e v e l o p m e n t S u i t e c o n s i s t s o f t h r e e p a r t s : t h e U n i f i e d D e v e l o p m e n t P l a t f o r m (U D P ) h a r d w a r e , t h e S o f t w a r e D e v e l o p m e n t K i t (S D K ), a n d t h e P C d e v e l o p m e n t t o o l s i n c l u d i n g A p p B u i l d e r a n d t h e I n t e g r a t e d D e v e l o p m e n t E n v i r o n m e n t (I D E ). S e e t h e a p p l i c a t i o n n o t e s l i s t e d b e l o wf o r c o m p l e t e d e t a i l s .t h e p r o g r a m . T h e L E D b l i n k . P a u s e p r o g r a R u nl i n e s o f c o d e a n d s e l e c t T o g B r e a k p o i n t t o a d d a b r e a k p o T h e n p r e s s R u n t o r u n t o b r e a k p o i c o d e .S t e p I n t o o r S t e p O v e r V i e w o r m o d i f y P e r i p h e r a R e g i s t e r s , o r M e m o i a b l e , r i g h t -c l i a n d s e l e c t A d d W a t c h E x p r e t o a d d i t t o t h e E x p r e s s i o n s w A p p B u i l d e r I D E•A N 675: P r e c i s i o n 32 D e v e l o p m e n t S u i t e O v e r v i e w•A N 667: G e t t i n g S t a r t e d w i t h t h e S i l i c o n L a b s P r e c i s i o n 32 I D E•A N 670: G e t t i n g S t a r t e d w i t h t h e S i l i c o n L a b s P r e c i s i o n 32 A p p B u i l d e r•A N 678: P r e c i s i o n 32 s i 32F l a s h U t i l i t y C o m m a n d -L i n e P r o g r a m m e r U s e r 's G u i d e•A N 719: P r e c i s i o n 32 I D E a n d A p p B u i l d e r D e t a i l e d T u t o r i a l a n d W a l k t h r o u g hW h e r e t o F i n d S u p p o r tM C U K n o w l e d g e B a s e :w w w .s i l a b s .c o m →S u p p o r t →K n o w l e d g e B a s eV i d e o T r a i n i n g M o d u l e s :w w w .s i l a b s .c o m →S u p p o r t →T r a i n i n g a n d R e s o u r c e sC o n t a c t a n A p p l i c a t i o n s E n g i n e e r :w w w .s i l a b s .c o m →S u p p o r t →C o n t a c t T e c h n i c a l S u p p o r tD . U s i n g t h e P r e c i s i o n 32 I DE f o r t h eF i r s t T i m e2R e g i s t e r t h e I D E u s i n g t h e s t e p s l i s t e d o n t h e W e l c o m e p a g e .1O p e n t h e P r e c i s i o n 32 I D E a n d s e l e c t t h e p r o j e c t w o r k s p a c e .313456S e l e c t j u s t t h e s i m x x x x x _B l i n k y c h e c k b o x ,e n s u r e C o p y p r o j e c t s i n t o w o r k s p a c e i s s e l e c t e d , a n d p r e s s F i n i s h .S e l e c t t h e I m p o r t S I 32 S D Ke x a m p l e (s ) l i n k i n t h e Q u i c k s t a r t w i n d o w .S e l e c t t h e s i m x x x x x _B l i n k yp r o j e c t i n t h e P r o j e c t E x p l o r e r a n d p r e s s B u i l d ‘B l i n k y ’ [D e b u g ] i n t h e Q u i c k s t a r t w i n d o w .S t a r t a D e b u g s e s s i o n b yc l i c k i n g D e b u g ‘B l i n k y ’ [D e b u g ] i n t h e Q u i c k s t a r t w i nd o w .。
1PPC控制器故障代码查询重要

Rexroth IndraControl VCP 20Industrial Hydraulics Electric Drivesand ControlsLinear Motion andAssembly Technologies PneumaticsServiceAutomationMobileHydraulicsRexroth VisualMotion 10 Multi-Axis Machine Control R911306327 Edition 01Troubleshooting GuideAbout this Documentation Rexroth VisualMotion 10 Troubleshooting Guide DOK-VISMOT-VM*-10VRS**-WA01-EN-PRexroth VisualMotion 10Multi-Axis Machine ControlTroubleshooting Guide DOK-VISMOT-VM*-10VRS**-WA01-EN-P Document Number, 120-2300-B323-01/ENPart of Box Set, 20-10V-EN (MN R911306370)This documentation describes …•the use of VisualMotion Toolkit for assitance in diagnostics •the proper steps for indentifing diagnostic faults • and the suggested remedies for clearing faults Description ReleaseDateNotes DOK-VISMOT-VM*-10VRS**-WA01-EN-P 08/2004Initial release© 2004 Bosch Rexroth AGCopying this document, giving it to others and the use or communicationof the contents thereof without express authority, are forbidden. Offendersare liable for the payment of damages. All rights are reserved in the eventof the grant of a patent or the registration of a utility model or design(DIN 34-1).The specified data is for product description purposes only and may notbe deemed to be guaranteed unless expressly confirmed in the contract.All rights are reserved with respect to the content of this documentationand the availability of the product.Bosch Rexroth AGBgm.-Dr.-Nebel-Str. 2 • D-97816 Lohr a. MainTel.: +49 (0)93 52/40-0 • Fax: +49 (0)93 52/40-48 85 • Telex: 68 94 21Bosch Rexroth Corporation • Electric Drives and Controls5150 Prairie Stone Parkway • Hoffman Estates, IL 60192 • USATel.: 847-645-3600 • Fax: 847-645-6201/Dept. ESG4 (DPJ)This document has been printed on chlorine-free bleached paper.Title Type of DocumentationDocument TypecodeInternal File Reference Purpose of Documentation Record of Revisions Copyright Validity Published byNoteRexroth VisualMotion 10 Troubleshooting Guide Table of Contents I Table of Contents1VisualMotion Tools for Diagnosing1-1 The Diagnostics Menu.............................................................................................................1-1System Diagnostics.................................................................................................................1-1Tasks Diagnostics...................................................................................................................1-3Drive Overview….....................................................................................................................1-42Monitoring and Diagnostics2-12.1System Diagnostics - Codes and Message...................................................................................2-1Parameters..............................................................................................................................2-2DriveTop..................................................................................................................................2-32.2Control Startup Messages.............................................................................................................2-4PPC Boot-Up Sequence..........................................................................................................2-4Control Firmware Sequence....................................................................................................2-42.3Status Messages (001-199)...........................................................................................................2-5001 Initializing System.............................................................................................................2-5002 Parameter Mode...............................................................................................................2-5003 Initializing Drives...............................................................................................................2-5004 System is Ready...............................................................................................................2-5005 Manual Mode....................................................................................................................2-5006 Automatic Mode: ABCD....................................................................................................2-5007 Program Running: ABCD.................................................................................................2-6008 Single-Stepping: ABCD....................................................................................................2-6009 Select Parameter Mode to Continue................................................................................2-6010 Breakpoint Reached: ABCD.............................................................................................2-6018 Please cycle power to continue........................................................................................2-6019 Executing User Initialization Task....................................................................................2-62.4Warning Messages (201-399).......................................................................................................2-7201 Invalid jog type or axis selected........................................................................................2-7202 Drive %d is not ready.......................................................................................................2-7203 Power Fail detected..........................................................................................................2-7204 Sercos ring was disconnected..........................................................................................2-8205 Parameter transfer warning in Task %c...........................................................................2-8207 Axis %d position limit reached..........................................................................................2-8208 Lost Fieldbus Connection.................................................................................................2-9209 Fieldbus Mapping Timeout...............................................................................................2-9210 File System Defrag: %d completed................................................................................2-10211 Program- & Data memory cleared..................................................................................2-10212 Option Card PLS Warning, see ext. diag.......................................................................2-10213 Sercos cycle time changed.............................................................................................2-11214 PCI Bus Cyclic Mapping Timeout...................................................................................2-11 DOK-VISMOT-VM*-10VRS**-WA01-EN-PII Table of Contents Rexroth VisualMotion 10 Troubleshooting Guide215 RECO I/O Failure, see ext. diag.....................................................................................2-11216 Control PLS %d warning, see ext. diag..........................................................................2-12217 PCI Bus Communication, see ext. diag..........................................................................2-12218 PCI Bus Register Mapping Timeout...............................................................................2-13219 PCI Bus Lifecounter Timeout.........................................................................................2-13220 Excessive deviation in PMG%d, see ext. diag...............................................................2-13221 Excessive Master Position Slip Deviation......................................................................2-13222 ELS Config. Warning, see ext. diag...............................................................................2-14223 PCI Bus reset occurred, cyclic data are invalid..............................................................2-14225 System booted................................................................................................................2-14226 RS485 Serial Communication Error (port X1%d)...........................................................2-15227 Control Over-temperature Warning................................................................................2-15228 Control - SYSTEM WARNING.......................................................................................2-152.5Shutdown Messages (400 - 599).................................................................................................2-16400 EMERGENCY STOP......................................................................................................2-16401 Sercos Controller Error: %02d........................................................................................2-16402 Sercos Config. Error: see ext. diag................................................................................2-16403 System Error see ext. diag.............................................................................................2-17405 Phase %d: Drive did not respond...................................................................................2-17407 Drive %d Phase 3 Switch Error......................................................................................2-17409 Sercos Disconnect Error.................................................................................................2-18411 Drive %d Phase 4 Switch Error......................................................................................2-18412 No drives were found on ring..........................................................................................2-18414 Parameters were lost......................................................................................................2-19415 Drive %d was not found..................................................................................................2-19416 Invalid Instruction at %04x..............................................................................................2-19417 SYSTEM ERROR: pSOS #%04x...................................................................................2-19418 No program is active.......................................................................................................2-20419 Invalid Program File: code = %d....................................................................................2-20420 Drive %d Shutdown Error...............................................................................................2-20421 User Program Stack Overflow........................................................................................2-20422 Parameter transfer error in Task %c..............................................................................2-21423 Unimplemented Instruction.............................................................................................2-21425 Instruction error: see Task %c diag................................................................................2-21426 Drive %d is not ready.....................................................................................................2-22427 Calc: invalid table index %d............................................................................................2-22428 Calc: division by zero......................................................................................................2-22429 Calc: too many operands................................................................................................2-22430 Calc: invalid operator......................................................................................................2-23431 Calc error: see Task %c diag.........................................................................................2-23432 Calc: too many nested expressions...............................................................................2-23433 Setup instruction outside of a task.................................................................................2-23434 Axis %d configured more than once...............................................................................2-23435 Axis %d is not assigned to a task...................................................................................2-24436 General Compiler Error: %04x.......................................................................................2-24438 Invalid Axis Selected: %d...............................................................................................2-24DOK-VISMOT-VM*-10VRS**-WA01-EN-PRexroth VisualMotion 10 Troubleshooting Guide Table of Contents III439 Axis %d: Invalid Motion Type.........................................................................................2-24440 I/O Transfer Error: see task diag....................................................................................2-25450 Event %d: invalid event type..........................................................................................2-25451 Invalid event number ‘%d’..............................................................................................2-25452 More than %d event timers armed.................................................................................2-25453 Homing param. transfer error: %d..................................................................................2-25454 Axis %d homing not complete........................................................................................2-26459 Axis %d target position out of bounds............................................................................2-26460 Invalid program %d from binary inputs...........................................................................2-26463 Ratio command: invalid ratio..........................................................................................2-26464 Can't activate while program running.............................................................................2-27465 Drive %d config. error, see ext. diag..............................................................................2-27467 Invalid ELS Master Option..............................................................................................2-27468 ELS adjustment out of bounds.......................................................................................2-27470 Axis %d velocity > maximum..........................................................................................2-28474 Drive %d cyclic data size too large.................................................................................2-28477 Axis D: probe edge not configured.................................................................................2-28478 Calc: operand out of range.............................................................................................2-28483 Parameter Init. Error: see Task %c diag........................................................................2-29484 Control SYSTEM ERROR..............................................................................................2-29486 Sercos Device %d is not a drive.....................................................................................2-29487 CAM %d is invalid or not stored.....................................................................................2-29488 CAM Error: See Task %c diag........................................................................................2-30489 More than %d CAM axes selected.................................................................................2-30490 System Memory Allocation Error....................................................................................2-30492 Programs were lost, see ext. diag..................................................................................2-30496 Can't execute this instruction from an event..................................................................2-31497 Limit switch config. error, see ext. diag.........................................................................2-31498 Drive %d Shutdown Warning..........................................................................................2-32499 Axis number %d not supported in this version...............................................................2-32500 Axis %d is not referenced...............................................................................................2-32501 Drive %d comm. error, see ext. diag..............................................................................2-33502 ELS and cams not supported in this version..................................................................2-33504 Communication Timeout.................................................................................................2-33505 Axis %d is not configured...............................................................................................2-33508 User Watchdog Timeout.................................................................................................2-33509 Control System Timing Error (%d).................................................................................2-34515 PLC Communications Error............................................................................................2-34516 More than %d registration functions enabled.................................................................2-34519 Lost Fieldbus/PLC Connection.......................................................................................2-35520 Fieldbus Mapping Timeout.............................................................................................2-35521 Invalid Virtual Master ID: %d..........................................................................................2-36522 Invalid ELS Master ID: %d..............................................................................................2-36523 IFS status, facility = 0x%x..............................................................................................2-36524 Hardware Watchdog timeout..........................................................................................2-36525 I/O Configuration error, see ext. diag.............................................................................2-36 DOK-VISMOT-VM*-10VRS**-WA01-EN-PIV Table of Contents Rexroth VisualMotion 10 Troubleshooting Guide526 Sercos Multiplex Channel Config, see ext. diag.............................................................2-37527 Control Initialization Error, see ext. diag.........................................................................2-38528 System Event %d Occurred...........................................................................................2-38529 Invalid ELS Group ID: %d...............................................................................................2-38530 CAM %d is active, can't overwrite..................................................................................2-39531 Invalid variable for Fieldbus/PCI Bus Mapping...............................................................2-39532 Power fail brown out condition detected.........................................................................2-39533 Multiple instances of index CAM: %d found...................................................................2-39534 Hardware Version Not Supported..................................................................................2-40539 Invalid Parameter Number..............................................................................................2-40540 Option Card PLS error....................................................................................................2-40541 Link Ring Error, see ext. diag.........................................................................................2-41542 PLC Cyclic Mapping Timeout.........................................................................................2-42543 PCI Bus Runtime Error...................................................................................................2-42544 RECO I/O Failure, see ext. diag.....................................................................................2-42545 Invalid Coordinated Articulation Function ID: %d...........................................................2-43546 Multiple Instance of Coordinated Articulation Function with ID: %d...............................2-43547 Task %c Coordinated Articulation Error, see ext. diag...................................................2-43548 Invalid Kinematic Number: %d.......................................................................................2-43549 Fieldbus Initialization Error.............................................................................................2-43550 User Initialization Task Timeout.....................................................................................2-44551 Master Slip Config. Error, see ext. diag..........................................................................2-44552 Excessive Master Position Slip Deviation......................................................................2-44553 Invalid Parameter Detected, see C-0-2002....................................................................2-44554 Excessive Deviation in PMG%d, see ext. diag...............................................................2-45555 PCI Bus Register Mapping Timeout...............................................................................2-45556 PCI Bus Lifecounter Timeout.........................................................................................2-45557 PMG%d Maximum allowed deviation window is Zero....................................................2-45558 PMG%d Only 1 axis parameterized...............................................................................2-46559 PMG%d Number of offsets does not match number of Axis..........................................2-46560 PMG%d Max. allowed dev. window is larger than 25% of Modulo................................2-46561 PMG%d Offset is larger than Modulo.............................................................................2-46562 PMG%d Parameterized Axis is not in system................................................................2-46563 Invalid Task Specified, Must be A-D..............................................................................2-46564 PMG%d Invalid configuration, see ext. diag...................................................................2-46565 Axis %d: Configuration error, see ext. diag....................................................................2-47566 Filter sample rate and cutoff frequency mismatch.........................................................2-47567 ELS Config. Error, see ext. diag.....................................................................................2-47568 Axis %d: Assigned Task is Not Defined.........................................................................2-48570 ELS Max. Vel. Exceeded, see ext. diag.........................................................................2-48571 No Program Found.........................................................................................................2-49572 PCI Bus reset occurred, cyclic data is invalid.................................................................2-49573 CAM %d is being built....................................................................................................2-49575 ELS Master for ELS Group %d is invalid........................................................................2-49576 Event for input I%d is already armed, cannot arm again...............................................2-50577 Restored non volatile memory from compact flash........................................................2-50DOK-VISMOT-VM*-10VRS**-WA01-EN-PRexroth VisualMotion 10 Troubleshooting Guide Table of Contents V578 Virtual Master %d Exceeded Its Max. Vel., see ext. diag...............................................2-50579 Group %d Exceeded Its Jog Velocity, see ext. diag......................................................2-51580 pROBE Error Occurred in Task:0x%04X.......................................................................2-51581 Probe Function for Axis # is locked by the PLC.............................................................2-51582 Integrated PLC: PLC Stopped in Operation Mode.........................................................2-51583 Integrated PLC: Internal System Error...........................................................................2-51584 ELS System Master %d is invalid, see ext. diag............................................................2-51585 Drive %d separate deceleration not supported..............................................................2-52586 Master Encoder Card Error, see ext diag.......................................................................2-522.6Integrated PLC Status Messages................................................................................................2-536001 Integrated PLC: Running..............................................................................................2-536002 Integrated PLC: Stopped..............................................................................................2-536002 Integrated PLC: Stopped at Breakpoint........................................................................2-532.7Integrated PLC Error Codes........................................................................................................2-530016 Integrated PLC: Software Watchdog Error...................................................................2-530019 Integrated PLC: Program Checksum Error..................................................................2-530020 Integrated PLC: Fieldbus Master Error.........................................................................2-540021 Integrated PLC: I/O Update Error.................................................................................2-542000 Integrated PLC: Internal SIS System Error..................................................................2-542001 Integrated PLC: Internal Acyclic Access Error.............................................................2-542002 Integrated PLC: Internal Acyclic Memory Error............................................................2-542003 Integrated PLC: PLC Configuration Error.....................................................................2-552004 Integrated PLC: File Access Error................................................................................2-552005 Integrated PLC: Internal Fatal Task Error....................................................................2-556011 Integrated PLC: PLC Program Stopped in Operation Mode........................................2-556012 Integrated PLC: General Error.....................................................................................2-552.8Communication Error Codes and Messages...............................................................................2-56!01 Sercos Error Code # xxxx...............................................................................................2-56!02 Invalid Parameter Number..............................................................................................2-57!03 Data is Read Only...........................................................................................................2-57!04 Write Protected in this mode/phase...............................................................................2-57!05 Greater than maximum value.........................................................................................2-57!06 Less than minimum value...............................................................................................2-57!07 Data is Invalid.................................................................................................................2-57!08 Drive was not found........................................................................................................2-57!09 Drive not ready for communication.................................................................................2-57!10 Drive is not responding...................................................................................................2-57!11 Service channel is not open...........................................................................................2-57!12 Invalid Command Class..................................................................................................2-57!13 Checksum Error: xx (xx= checksum that control calculated).........................................2-58!14 Invalid Command Subclass............................................................................................2-58!15 Invalid Parameter Set.....................................................................................................2-58!16 List already in progress..................................................................................................2-58!17 Invalid Sequence Number..............................................................................................2-58!18 List has not started.........................................................................................................2-58!19 List is finished.................................................................................................................2-58 DOK-VISMOT-VM*-10VRS**-WA01-EN-P。
VANMASS 2 in 1 Wireless Charger CDRZ35说明书
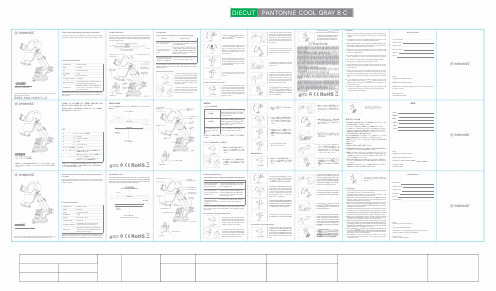
@VANMASS™ Thank you for purchasing and using this product!In order to bring you a better exper ence, 『ead th1S manual and alsoplease refer to you『mobile phone or沪ur electronic product manual.WIRELESS CHARGERPlease read th s operation instruction carefully and keep it proper!Y扫lorn us ng this product.@VANMASS™2in1'J,(七匕又充雷器芒使用前1工`乙O取1!l:锐明霍宅去苍切动上、正1.-(安全1匕在使c,<茫i!'C、。
衷九、布骁为仁左-,t,梭灶、L、勹家飞旯6n石.I:?书手元仁大切保芒L<<忔古小。
上纪11)/污又一夕比VANMASS"奶研究室(f)屯(f)飞才夫暇切芍又夕比裂品七于(f)他(f)要因l.:J:?飞兵坛苍渴合纾;\jl}jji东写哀灶爹考保尺9([)飞、英院O裂品苍基準1.:1,去才.@VANMASS-Product SpecificationsPmduct Name Wire比ss c归rgerMod� CDRZ35Size 巧(1OOx 93 x 55)mmNet We ght •92gInput 5V=2A. 9V=1.8ACharging Distance •(4·6)mmAppl尥t,on Model Compatible with Qi standard cellphon@:iPhone, Samsung, LG, Mato etc.W咱坴car扣rger•1,US氏如cable x1,Pa欢age L叹Air vent dip x1,Sudion cup holder x1,Instruction book x 1The pa『ameters abo心a"'derived from the laboratory of V闷MASS巴The actual parameter would be different Because of p『oducts andother f釭tor<Bitte lesen S e d ese Bedienungsanleitung aufmerksam durch undbewahren Sie sie vor de『Verwendung dieses Produkts aul.乙0度比、7千乍匕又充霓台(以下『本毅品J匕表兄L衷Tl宅巧贯L、上I九卞任宅、械仁il;'),Jf,七夕己名L、玄L九本蚁品宅它使用韵IC1:0)取贷祝明吝宅.I:(扫怯办<茫古C、。
FLAC3D中出错警告

B ERROR MESSAGESB.1FLAC3D-Specific Errors***A zone has undefined material modelOne or more zones in the model has not had a material model defined.This must bedone before cycling.***All zones have NULL fluid modelNo zones with activefluid material models are present.Either activate some zonesforfluid calculations or disablefluid calculations.***Attempted to create a degenerate triangleThe generation a surface item caused the creation of a degenerate triangle(i.e.onewith co-linear points).***Bad commandFLAC3D failed to recognize the command entered.***Bad format parameter i(string)The i th parameter on the command line was not in the format required by the com-mand syntax.***Bad I/O on filefileFLAC3D was unable to either read or write tofilefile.If writing,there may be noavailable disk space.If reading,thefile may be corrupt.***Bad keyword parameter i(string)Parameter i on the command line was not processed by FLAC3D.Check the commandsyntax.***Bad overlay codeAn illegal overlay code was specified in the MODEL command.Legal values areintegers between-1and2.***Bad RANGE keywordA range was specified with an illegal or unrecognized keyword.Check for spellingerrors and see the manual for the correct syntax.***Biot modulus fluid mode is offMay not access Biot modulus when Biot modulus mode is off.***Biot modulus fluid mode is onMay not accessfluid modulus fmodulus when Biot modulus mode is on.***Cable element not foundA reference was made to a cable element that does not match any element currentlyin memory.***Cable has zero lengthA cable was specified/found with a zero element length.***Cable stiffness parameters have not been setSome cable material properties were not specified prior to cycling.***Cannot allocate memoryFLAC3D could not allocate its reserved memory.Specify less reserved memory atthe command line***Cannot apply stress in global and local axes on same faceApply stresses using one axis system.***Cannot combine NULL and PLANE keywords on a contour plot itemIt is impossible to contour the interior regions of null zones.This combination ofkeywords is not allowed.***Cannot deactivate an external volumeAn external volume is always active and may not be deactivated.***Cannot destroy base viewThe view“Base/0”cannot be destroyed.***Cannot destroy current viewThe current view can not be destroyed.Make another view current and try again.***Cannot find ID numberAn ID number was specified that does not match any existing object of that type.***Cannot FIX and APPLY velocity in the same directionA FIX condition is implied on gridpoints under an APPLY velocity condition.***Cannot fix or apply velocities to a node that is slaved to an active zoneA cable node that is internal to an active zone may not have its motion restricted inany way.Only a“free”cable node can have its velocity constrained.***Cannot have applied velocities in global and local axes at same gridpoint Apply velocities using one axis system.***Cannot open filefileFLAC3D was unable to open thefile.If reading,thefile probably does not exist.Ifwriting,thefile may already exist in a protected state.***Cannot rename base viewThe view‘Base/0’cannot be renamed.***Cannot set group of an active volumeAn active volume has already chosen its internal zones.This choice can only bemodified if the volume is made inactive.***Command line overflowA fully-expanded command line has exceeded the maximum length of1024char-acters.***Configuration file errorThe configurationfile is a mirror image of the information stored in the hardwarekey.Thisfile is created thefirst time FLAC3D is executed.Thereafter,thisfile allowsthe user to create models and generate plots without the hardware key attached.Thehardware key will still be required to be attached to cycle.The configurationfiledetected has invalid information,attach your hardware key to regenerate it or replacethe configurationfile specified.***Creep mode not availableCreep extentions are not available in this version of the code.***Density needed for thermal runThe thermal option requires that density be specified in all active zones.***Density not definedThe dynamic option requires that density be specified in all active zones.***Device mode mode not compatible with current hardwareThe specified device mode was not detected as being available on the hardware ofthe current system.***Device mode mode not foundThe specified device mode is not one currently recognized by the screen device.***Display information not availableThe screen display information was not available.This error should never happen;if it does,contact Itasca.***DOS critical error:stringA critical error(disk access,etc)has occurred on the system.You will be promptedfor possible corrective actions.***Dynamic extension absent from gpDynamic extention information was not present in a gridpoint.There is probablyinsufficient memory available.***Dynamic mode not availableDynamic extentions are not available in this version of the code.***Error creating PCX fileAn error occurred while attempting to output a PCX-file image of the screen device.***Error initializing deviceAn error occurred while initializing a screen device.Check the mode setting.***Error initializing graphics systemAn error occurred while trying to initialize an output device.Check that the properdevice has been selected.***Error in syntax while specifying output historiesFLAC3D encountered an incorrect syntax while specifying histories to output.Checkthe correct syntax.***Error in system/temp memoryThis is an internal FLAC3D memory management error.If it occurs,contact Itasca.***Error opening history temp fileFLAC3D was unable to open a temporaryfile to store history traces.There is probablya problem with the disk drive.***Error reading history temp fileFLAC3D was unable to read the temporaryfile it stores history traces in.There isprobably a problem with the disk drive.***Error writing history temp fileFLAC3D was unable to write to the temporaryfile it stores history traces in.The diskdrive may be full.***Extra array index out of boundsAn attempt was made to index a gridpont or zone extra array past the number thathad been specified with the CONFIG command.***Face a,b already has interface elementsCannot double place interface elements from the same interface on the same zoneface.***Face with less than3nodesA face was specified with less than the minimum of three nodes while building awater table.***Failure to assign gridpointAn error occurred while generating internal gridpoints in a zone primitive.There isprobably no more memory available.***Failure to initialize interface logicThe interface logic is unavailable in this session.There is probably insufficientmemory available.***Failure to insert valueThe Table logic was unable to insert a value into a table.This error should neverappear.If it does,contact Itasca.***Fatal key error--contact ItascaAn error has occurred in the hardware logic detection system that makes it impossibleto continue executing the program.***Filefile not save fileAn attempt was made to restore afile that was not a FLAC3D savefile.***Font file name not foundA fontfile needed by the screen device was not found.Check for their existence inthe current directory.***Free surface already exists at that locationAn attempt was made to create a surface triangle in a location where a free(notbound to a volume)surface already exists.***GEN iterator error:stringThis is an internal error to the grid iterator.These errors should never happen.If itdoes,note the contents of string and notify Itasca.***General interface error-stringAn internal interface processing error.This error should never occur.If it does,contact Itasca.***Generic dynamic array processing errorThis error should never occur.Contact Itasca.***Generic linked list processing errorThis error should never occur.Contact Itasca.***Gravity not definedThe gravity vector must be defined prior to the definition of the water table.***Gridpoint already has applied velocities in another local axes system Use one axis system.***Gridpoint i does not existA reference was made to a gridpoint ID that does not match any currently in memory.***Group’string’does not existA reference was made to a group whose name does not match any currently inmemory.***History i does not existAn attempt was made to access a history ID that does not exist.***Illegal block plot typeThis error should never occur.If it does,contact Itasca.***Illegal contour typeThis error should never occur.If it does,contact Itasca.***Illegal error code iThis error should never occur.If it does,contact Itasca.***Illegal geometry in zone iZone i contains one or more internal tetrahedrons with zero or negative volume.Check zone geometry.***Implicit scheme failed to converge***Insufficient memory to restore stateThe savefile used more memory than is available to this session of FLAC3D.RestartFLAC3D and reserve more memory.***Insufficient number of vertices definedMore vertices need to be specified to fully describe the surface desired.***Intended device not availableThe device specified for output is not available on this version of FLAC3D.***Interface element already exists with those vertices.Cannot create two identical interface elements in the same interface.***Interface i not foundA reference was made to an interface that does not yet exist.***Interface node i already exists at that location.Cannot create two nodes on the same interface at the same location.***Interface node not foundNo interface nodes are present in that interface.***Invalid history ID numberAn illegal integer was specified as a history ID number.***Invalid input type(i)This error should never appear.If it does,contact Itasca.***Key for different code IDThe hardware lock detected is for a different program.***Key for newer version of codeThe hardware lock detected is for an older version of the program.Contact Itascato update the version.***Library error stringThis is an internal C runtime library error.In general,this will pertain to afloatingpoint error.***May only have one contour plotitem per viewThere may only be a single PlotItem of type Contour in a view’s PlotItem list.***May only ouput one history to a single tableWhen writing a history to a table,only one history trace and one table may bespecified.***May only specify i output historiesA maximum of i histories may be output simultaneously.***Memory overflowFLAC3D has run out of its reserved memory.Save the run,and restart with morememory if available.***MetaWindow Query Error Code i/iAn internal error from the graphics library driving the screen device.***Missing parameter iFLAC3D required another parameter at position i on the command line.***Mouse driver not foundA mouse driver was not found on the system.Check your computers initializationfiles.***Multiple volume constraint failureA gridpoint which was constrained to two or more volumes was unable to meet all ofits constraints.A probable cause is a surface geometry much smaller that the zonesizes near it.***Must specify a non-zero extrusion vectorAn extrusion vector must be specified for an extruded type of surface generation.***Must specify position to create new nodeIn order to create a new cable node,a position in space must be specified.***Must specify all three nodes of an interface element.The locations of all vertices of an interface element must be specified to create it.***Must specify an interface ID number.An interface ID number must be specified for most interface commands.***Must specify position to create new nodeIn order to create a new cable node,a position in space must be specified.***No convergence in30SVDCMP iterationsThis error should never occur.If it does,contact Itasca.***Node not foundA reference was made to a cable or surface node that does not match any currentlyin memory.***Non-convex faceWhile entering a water table,a polygon was entered that was not convex.***Non-planar faceWhile entering a water table,a polygon was entered that was not planar.***Not configured for creep calculationThe code must be configured(using the CONFIG command)for creep calculationbefore creep extentions can be used.***Not configured for dynamic calculationThe code must be configured(using the CONFIG command)for dynamic calculationbefore dynamic extentions can be used.***Not configured for fluid flow calculationThe code must be configured(using the CONFIG command)forfluid calculationbefore thermalfluid can be used.***Not configured for thermal calculationThe code must be configured(using the CONFIG command)for thermal calculationbefore thermal extentions can be used.***Not enough memory available for command processorThere must be enough memory left in the system(outside of the memory reserved forFLAC3D)to load command processor.If possible,reserve less memory at start-up.***Open surface at zone a face b edge cThe grid iterator was unable to build a closed list of faces and gridpoints for a newlyactivated volume.***PlotItem ID i not foundA reference was made to a plot-item ID number that does not exist in the currentview list.***Property bad,or does not correspond to modelAn attempt was made to specify a non-existent property,or one that does not corre-spond to a given model.***Recursive use of named rangesA name was given to a range that matches a name used by one of its elements.Thisrecursive relationship is not allowed,and the new range is not saved under that name.***Referenced non-existent auxiliary input(i)This error should never occur;if it does,contact Itasca.***Save file incompatible with present versionThe savefile is no longer compatible with the present version of the e theold version or re-run the problem.***hardware copy protection not detected...Press ESC to exit program or any other key to try again and continue.If unsuccessful,contact your local code agentThe hardware copy protection(i.e.,hardware lock,hostid)was not detected.Replaceit and try again.If FLAC3D is still unable to detect it,contact your local code agent.***SOLVE Error:No master processes activeAt least on process(mechanical,fluid,or thermal)must not be a slave to use theSOLVE command.***Table i does not existA reference was made to a table number that does not yet exist.***Table i not foundA reference was made to a table ID that does not match any currently in memory.***Thermal mode not availableThermal extentions are not available in this version of the code.***This model name does not existPlease refer to the manual to determine the available models and their names.***Time step too large for given propertiesCheck the properties.***Timestep rejected by moduleThis error should never occur.Contact Itasca.***Token length overflowA single token has exceeded the maximum length of80characters.***Unable to fix degenerate zone iWhile grid iterating,a zone has degenerated in a way that the iterator was unable tomodify.Increasing the number of zones in the region might help,as might adjustingthe sizefield tofit the surface geometry better.***Unable to find Gp i in surface listThe grid iterator was unable to build a closed list of faces and gridpoints for a newlyactivated volume.***Unable to initialize device stringUnable to initialize screen device string.***Unable to load fontfileUnable to load fontfilefile,which is needed by the graphics system.***ViewID name already existsAn attempt was made to create a new View with an ID that matches one alreadypresent.***ViewID i not foundA reference was made to a ViewID number that does not exist.***ViewID name not foundA reference was made to a ViewID name that does not exist.***Viscous damping too highReduce the damping value specified.***Volume i not foundA reference was made to a V olume ID number that does not currently exist.***Water density not definedThe water density must be defined prior to the definition of the water table.***Water table orthogonal to gravityA water table element was added that was parallel with the direction of the gravityvector.This is not allowed.***Zero gridpoint massAn active gridpoint shows zero inertial mass.Check the material properties beingused.***Zero gridpoint stiffnessAn active gridpoint shows zero accumulated stiffness.Check the material propertiesbeing used.B.2FISH Error Messages***Array index is not an integer***Array name is already used by an array***Bad syntaxCheck your spelling(including case),punctuation and assignments.***Bad type conversionThis usually means that a string or a pointer is being used in an arithmetic expressionwith a number.***Call number is invalidThe given FISHCALL number is not between0and50.***Cannot execute(string)...not a functionThe named symbol is not a defined function.***Cannot give value to left-hand sideThe intrinsic variable is“read only”—i.e.,it cannot be given a value.***Cannot interpret function or array argumentThe argument of an intrinsic or FLAC3D-specific function has a bad format—seemanual.***Cannot interpret(string)as a numberA built-in function expects a number as argument,but something else is present.***Cannot process...not a DEFined functionCheck your spelling(including case),punctuation and assignments.***Cannot raise negative number to real powerThe manipulation of complex numbers is not within the scope of the code.***CASE must be followed by integer between0and256Only constant integer values are allowed.***CASE or END CASE,but no preceding CASE OFStructure is CASEOF...CASE...<CASE>...ENDCASE with multipleCASE clauses.***CASE OF must be followed by somethingA valid expression with an integer result is expected.***Dimension should be positive integerArray dimensions should either be integers or FISH variables names that have integervalues at compile time.***Duplicate CASE numberCASE numbers must appear once only in a CASE section.***ELSE or END IF,but no preceding IFStructure is IF...THEN...<ELSE>...ENDIF with a single ELSE clause optional.Indenting your code will help you track this error.***Empty line after’=’***END COMMAND,but no preceding COMMANDStructure is COMMAND...ENDCOMMAND.Indenting your code will help you trackthis error.***END LOOP,but no preceding LOOPStructure is LOOP...ENDLOOP.Indenting your code will help you track this error. ***Expected=<>#<=or>=but missing***Extraneous materialThere are extraneous characters on the same line after a FISH statement.***FISH compilation errorFISH was unable to compile the function as entered,probably due to an erroneouscommand or a spelling error.***FISH execution errorFISH was unable to execute the function as entered.This could be caused bycommand errors,division by zero,or other such programming faux pas.***Fish-function name expected but not found***Function name has been defined before***Function name is already an array***Function name is inappropriate or conflicts with reserved word***Function string is being called recursivelyThe named function is trying to execute itself(e.g.,the function name is on theleft-hand side of an assignment).***Inappropriate equals signAn equals sign is in an inappropriate place.***Inappropriate keywordA FISH keyword is being used in an inappropriate place.***Inappropriate right parenthesisCheck your punctuation.***Incomplete string(missing quotation mark)Check your punctuation.***Integer between0&255must follow CASE***Internal FISH error..send data file to Itasca***Missing argument(s)Refer to Chapter4,FISH User’s Guide,for the arguments required.***Missing comma in loop rangeCheck format of LOOP statement—see definition in manual.***Missing END CASE statementThe function has ended,but with an incomplete CASE section.***Missing END IF statement(s)A function definition has been ended,but with an incomplete IF section.***Missing END LOOP statementThe function has ended,but with an incomplete LOOP.***Missing left-hand side to assignment***Missing loop range(s)***Missing material***Missing name***Missing right-hand side to assignment***Missing test symbol:=<>#<=or>=One,and only one,of the noted test symbols may be used in the expression. ***More than one equals sign***Name conflicts with existing symbol name***Name conflicts with keyword or intrinsic name***Name corresponds to an existing function***Name is already an array;cannot re-define***Nested SECTIONs not allowed***No corresponding IF statementAn ENDIF has been given without a preceding IF.***No END SECTION statementThe function has ended,but with an incomplete SECTION.***No function name***No preceding CASE OFCASE or ENDCASE has been encountered with no proceeding CASEOF.***No preceding LOOP statement***No SECTION has been definedAn ENDSECTION or EXIT SECTION has been encountered,but there is no precedingSECTION.***Non-existent table***Not a user-defined symbol***Not currently within a SECTIONInappropriate EXIT SECTION in datafile.***Number has bad format***Number of arguments conflicts with previous usage***Parentheses do not balanceCheck your punctuation.***Pointers can only be compared with=or#The general test symbols(<,>,etc.)are not available for pointers.***Premature end of line***Reached END,but with missing END CASEFISH has reached the END of your function and has detected a bad CASE construct.***Reached END,but with missing END IFFISH has reached the END of your function and has detected a bad IF construct.***Reached END but with missing END SECTIONFISH has reached the END of your function and has detected a bad SECTION construct.***Reached END,but with unclosed LOOPFISH has reached the END of your function and has detected a bad LOOP construct. ***Requested table or item does not exist***Square root of negative number***This is a Fish variable,not a functionThe given FISH symbol cannot be executed because it is not the name of a function.***Too many ELSE statementsOnly one ELSE may come between IF and ENDIF.***Trying to divide by zero***Unbalanced parentheses***Unbalanced quote marks***WHILE STEPPING&COMMAND cannot co-exist in a function***Wrong number of argumentsRefer to Chapter4,FISH User’s Guide,for the arguments required.。
京东发23.8寸液晶屏MV238FHM-N10规格书-杭州旭虹科技

R2013-9024-O(3/3)
A4(210 X 297)
友达群创奇美京东方液晶屏代理商
PRODUCT GROUP
TFT- LCD PRODUCT SPEC. NUMBER
SPEC. TITLE MV238FHM-N10 Product Specification_Rev.0
R2013-9024-O(1/3)
A4(210 X 297)
友达群创奇美京东方液晶屏代理商
PRODUCT GROUP
TFT- LCD PRODUCT
SPEC. NUMBER SPEC. TITLE MV238FHM-N10 Product Specification Rev.0
REV Rev.0
ISSUE DATE Aug. 19. 14’ PAGE 3 OF30
Contents
No. 1.0 2.0 3.0 4.0 5.0 60 6.0 7.0 8.0 9.0 10.0 11 0 11.0 12.0 13.0 14.0 15.0 General Description Absolute Maximum Ratings Electrical Specifications Optical Specifications Interface Connection Signal Timing Specifications Signal Timing Waveforms of Interface Signal Input Signals, Display Colors & Gray Scale of Colors Power Sequence Mechanical Characteristics Reliabili li bili Handling& Cautions Product Serial Number Packing Appendix Item Page 4 6 7 8 10 13 15 17 18 19 20 21 22 23 25
Sun Flash Accelerator F20 PCIe 安装指南说明书

The Sun Flash Accelerator F20PCIe card can be used as a storage device and SAS/SATA controller in systems that support it.This guide outlines the preinstallation considerations and tasks involved in installing a Sun Flash Accelerator F20PCIe in a system.Preparing for Installation■Before you begin,gather all of the information required for the installation,including the following:■Sun Flash Accelerator F20PCIe Card Product Notes (820-7267)■Sun Flash Accelerator F20PCIe Card User’s Guide (820-7265)Located at:/pls/topic/lookup?ctx=SFA_F20_PCIe■Get the service manual and product notes for the system into which you will install the card.Thosedocuments will provide the platform-specific information you need to install the card into your specific model of system (for example,slot restrictions).Located at:/technetwork/documentation/index.html#servers_work_hw ■Follow all safety precautions as described in the Sun Flash Accelerator F20PCIe Card User’s Guide and yoursystem documentation to ensure that the system,the card,and the installer are protected during installation.■Verify the ship kit contents:Sun Flash Accelerator F20PCIe card,full-height PCIe bracket,and anti-static wrist strap.Sun Flash Accelerator F20 PCIe CardGetting Started GuideNote–A No.1Phillips screwdriver is required for installation.■Verify that you have a supported system with an appropriate PCIe slot for the card.Check your systemdocumentation to verify card support and to identify any restrictions that apply to your system.verifying that such configurations are supported by your system.Ensure the system and the Sun Flash Accelerator F20PCIe card are properly cooled.Refer to the site planning and installation requirements in your system documentation for more information.In addition,read the Sun Flash Accelerator F20PCIe Card User’s Guide for complete card specifications.■Update your system firmware,including patches as needed,before you install the card.Visit /us/support/index.html to determine whether updates exist for the SATA, host bus adapter(HBA),drive backplane,service processor,system BIOS,or OpenBoot™PROM/system firmware that is installed on your system.▼Installing the Sun Flash Accelerator F20PCIe1.Power off and prepare the system for service,according to your system documentation.2.If applicable,install the card into the full-height bracket.See the Sun Flash Accelerator F20PCIe Card User’s Guide for more information.3.Install the card into the PCIe slot,according to your system documentation.4.If applicable,connect SAS/SATA cables from your system's disk backplane to the two SAS/SATA ports atthe edge of the card.See the Sun Flash Accelerator F20PCIe Card User’s Guide for more information.5.Return your system to service and power on,according to your system documentation.6.If applicable,perform a command like cfgadm or reboot-r for your system to recognize the new card.Use the appropriate command for your OS.7.Verify successful installation of the card through your system’s OS.With Solaris,use the formatcommand.Upon completed installation,the4DOMs on the card will appear to your system as4discrete SSDs.8.Verify that the latest version of the card firmware is installed.See the Sun Flash Accelerator F20PCIe Card Product Notes for information about card firmware updates.9.Configure your system to maximize flash technology performance.Solid state flash devices have block alignments typically aligned on4KByte boundaries,not the512Byte boundaries of conventional disks.In order to maximize performance,partitions need to be aligned on4KByte boundaries.For more information about tuning your system,see the Sun Flash Accelerator F20PCIe Card Product Notes.Accessing DocumentationYou can view,print,or purchase a broad selection of documentation,including localized versions,at: /cd/E19682-01Copyright©2010,2012,Oracle and/or its affiliates.All rights reserved.Copyright©2010,2012,Oracle et/ou ses affiliés.Tous droits réservés.Part No.: E29800-01Mfg No.: 7050401April 2012。
BIOSUpdateProcedure

BIOSUpdateProcedureBIOS Update ProcedureAll latest Motherboards today, 486/ Pentium / Pentium Pro etc.,ensure that upgrades are easily obtained by incorporating the system BIOS in a FLASH Memory component. With FLASH BIOS, there is no need to replace an EPROM component. Once downloaded, the upgrade utility fits on a floppy disc allowing the user to save, verify and update the system BIOS. A hard drive or a network drive can also be used to run the newer upgrade utilities. However, memory managers can not be installed while upgrading.Most pre-Pentium motherboards do not have a Flash BIOS. The following instructions therefore do not apply to these boards. If your motherboard does not have a Flash BIOS (EEPROM) you will need to use an EPROM programmer to re-program the BIOS chip. See your dealer for more information about this.Please read the following instructions in full before starting a Flash BIOS upgrade:A. Create a Bootable Floppy (in DOS)昗ith a non-formatted disk, type the following:format a:/s旾f using a formatted disk, type:sys a:This procedure will ensure a clean boot when you are flashing the new BIOS.B. Download the BIOS file旸ownload the correct BIOS file by clicking on the file name of the BIOS file you wish to download.昐ave the BIOS file and the Flash Utility file in the boot disk you have created. Unzip the BIOS file and the flash utility file. If you don't have an "unzip" utility, download the WinZip for Windows 95 shareware/ evaluation copy for that one time use from _/doc/188210584.html, or _/doc/188210584.html,. Most CD ROMs found in computer magazines, have a shareware version of WinZip on them.昚ou should have extracted two files:Flash BIOS utility eg: flash7265.exe (for example)BIOS eg: 6152J900.bin (example)Use the latest flash utility available unless otherwise specified (either on the BIOS update page or in the archive file). This information is usually provided.C. Upgrade the System BIOSDuring boot up, write down the old BIOS version because you will need to use it for the BIOS backup file name.Place the bootable floppy disk containing the BIOS file and the Flash Utility in drive a, and reboot the system in MS-DOS, preferably Version 6.22旳t the A:> prompt, type the corresponding Flash BIOS utility and the BIOS file with its extension.For example:flash625 615j900.bin旻rom the Flash Memory Writer menu, select "Y" to "Do you want to save BIOS?" if you want to save (back up) your current BIOS (strongly recommended), then type the name of your current BIOS and its extension after FILE NAME TO SAVE: eg: a:\613J900.binAlternatively select "N" if you don't want to save your current BIOS. Beware, though, that you won't be able to recover from a possible failure.昐elect "Y" to "Are you sure to program?"昗ait until it displays "Message: Power Off or Reset the system"Once the BIOS has been successfully loaded, remove the floppy disk and reboot the system. If you write to BIOS but cannot complete the procedure, do not switch off, because the computer will not be able to boo, and you will not be given another chance to flash. In this case leave your system on until you resolve the problem (flashing BIOS with old file is a possible solution, provided you've made a backup before)Make sure the new BIOS version has been loaded properly by taking note of the BIOS identifier as the system is rebooting.For AMI BIOSOnce the BIOS has been successfully loaded, remove the floppy disk and reboot the system holding the "END" key prior to power on until you enter CMOS setup. If you do not do this the first time booting up after upgrading the BIOS, the system will hang.BIOS Update Tipsnote:1.Make sure never to turn off or reset your computer during the flash process. This will corrupt the BIOS data. We also recommend that you make a copy of your current BIOS on the bootable floppy so you can reflash it if you need to. (This option is not available when flashing an AMI BIOS).2. If you have problems installing your new BIOS please check the following:Have you done a clean boot?In other words, did you follow the above procedure for making a bootable floppy? This ensures that when booting from "A" there are no device drivers on the diskette. Failing to do a clean boot is the most common cause for getting a "Memory Insufficient" error message when attempting to flash a BIOS.If you have not used a bootable floppy, insure a clean boot either bya) pressing F5 during bootupb) by removing all device drivers on the CONFIG.SYS including the HIMEM.SYS. Do this by using the EDIT command.Have you booted up under DOS?Booting in Windows is another common cause for getting a "Memory Insufficient" error message when attempting to flash a BIOS. Make sure to boot up to DOS with a minimum set of drivers. Important: Booting in DOS does not mean selecting "Restart computer in MS-DOS Mode" from Windows98/95 shutdown menu or going to Prompt mode in WindowsNT, but rather following the above procedure (format a: /s and rebooting from a:\).Have you entered the full file name of the flash utility and the BIOS plus its extension?Do not forget that often you will need to add a drive letter (a:\) before flashing the BIOS. Example: when asked for file name of new BIOS file which is on your floppy disk, in case you'reworking from c:\ your will need to type a:\615j900.bin, rather than 615j900.bin only.。
15英寸电容触摸屏显示器用户手册说明书

TCM006Table of ContentsChapter I: Overview21.1 Safety Information21.2 Electromagnetic Compatibility Statement3 Chapter II: Installation Guide32.1 Appearance of TCM006 Touch Screen Monitor:42.2 The Rear Panel I/O Signs and Description:4Key Function:5 Chapter III: Instructions for Installation63.1 Touch Screen Driver Installation:6 Chapter IV: Common Problems and Solutions15 No display on the screen15 Characters look too dark or too light15 The monitor display needs to be adjusted15 The text on the screen is unclear or blurred15 Touch panel doesn’t respond15Chapter I: OverviewDear Valued Customer,Thank you for purchasing 3nStar products. We are committed to continuously maintaining the product quality and providing better after-sales service. In order to take full advantage of our devices, we recommend reading through this manual before the driver installation.1.1 Safety Information●TCM006 is fully compliant with the relevant requirements of the national standardGB/4943-2001 IT equipment security.●Make sure the electricity meets the power requirements (such as voltage, frequency)before installation and power outlet are properly grounded.●Lightning may damage the product. Unplug the network cable, power cable or anyother conductors during lightning storms.●Do not unplug the components and connections (except for the USB device) when thepower is on.●Do not open the cabinet of the product by a non-professional technician.●Do not leave any item or liquid inside the product. Do not place any objects into theventilation holes, it may cause short-circuit of the internal components and may causefire or electric shock.●In accordance with the national standards GB/T9813-2000 microcomputers generalspecification, after the computer is below the temperature of 10 ° C, place the machinein room temperature (10-35 ° C) conditions for more than two hours to avoid damagefrom low temperature. In the meantime, please do not remove the casing but allow thecomputer to restore the natural temperature. Avoid heating the unit up too fast becausethe computer may generate frost and condensation that might damage the electricalcomponents.●This unit is in strict compliance with the electrical appliance standards.●Safe use voltage range: 100V ~ 240V & 50Hz/60Hz.●Verify that the power outlet is available to connect to a reliable ground circuit.●Keep the device clean, dry, away from dust, moisture and direct sunlight.●Do not share the same power outlet with high-power consumption electrical devices.Keep distance from high level magnetic interference.●Turn off the power to the monitor after use to extend useful life.●Do not use sharp points with, draw on or cut the touch screen to ensure a normal lifecycle.●Switch off the power supply before plugging in or unplugging the communication cableor connecting to an external device.●Unauthorized and unqualified technicians should not open the machine, or they assumeall risks and may damage the unit.When any of the following occurs:●Liquid penetrates into the body of the monitor●Monitor is accidentally damaged●Monitor produces a burning smell●Monitor display is suddenly abnormal or distortedDisconnect the power supply immediately, unplug the power cord and contact a qualified service technician to service the unit.1.2 Electromagnetic Compatibility Statement●TCM006 is fully compliant with the relevant requirements of the national standards(GB/9254-1998) “The limits and measurement methods of radio disturbancecharacteristics of information technology equipment” for Class B products.●TCM006 is fully compliant with the relevant requirements of the People's Republic ofChina’s national standards of (GB/17625.1-2003) “Electromagnetic CompatibilityLimits for harmonic current emission limits” for Class B products.Chapter II: Installation Guide2.1 Appearance of TCM006 Touch Screen Monitor:2.2 The Rear Panel I/O Signs and Description:A row of the external device connection interface is located at the rear bottom panel of the monitor, such as: power outlet, Line in, VGA and USB interface, detailed as follows:●TOUCH USB: this is connected to PC’s USB Ports, used for touch function●DC In: 12V DC in, power supply for the touch monitor.●VGA In: This is connected to PC’s VGA output port.Key Function:●Menu: Press this button to get a pop-up OSD menu, and enter the menu item (function)highlighted while the OSD menu is activated.●ON/OFF: Turn the LCD power on and off. When the power is on, the light is showinggreen, stand by will be red●UP: Press this button to increase the value of the function selected or move to theprevious function●Down: Press this button to decrease the value of the function selected or move to theprevious function●AUTO/EXIT: Press this button to apply the monitor setting automatically and Exit theOSD menuTCM006 touch screen monitor uses a manual handle design which is able to be adjusted within the range of 0 degrees to 90 degrees to make operation and viewing more comfortable.Chapter III: Instructions for Installation3.1 Touch Screen Driver Installation:Step 1: Open the installer directory on the CD, double-click “Setup.exe”Step 2: Installation begins as the following figure shows. Click Next to proceed to the next step.Step 3: Installation in progressStep 4: Click “Install PS/2 interface driver” and click “Next” to proceed with the installation.Step 5: For the touch interface RS232, click “Install RS232 interface driver” and click “Next” to proceed with the installation.Step 6: When choosing the calibrations, select NONE and click “Next” to proceed with the installation.Step 7: When installing USB touch, please connect the USB controller and USB cable.Step 8: When using two or more touch screens, please select “Support multi- monitor system”.Step 9: Select the destination location to store the driver. The default path isC: \ Program Files \ eGalaxtouch. Use the default path here and click “Next” toproceed with the installation.Click “Next” to proceed with the installation.Step 10: Select the option to create a desktop shortcut icon.After installing the driver successfully, identify the USB controller card and RS232 control card as the following two figures show:Related touch function settingTouch device line testTouch screen settingTouch device edge correction setting Touch device hardware information displayChapter IV: Common Problems and SolutionsNo display on the screen●Power saving mode is on, press any key on the keyboard or move the mouseto activate.●The pins of the VGA cable connector are bent or lost contact to the VGAinterface. Change the VGA cable. If the problem still persists, bring the unit to an authorized service provider.Characters look too dark or too lightUse the OSD Menu to adjust the brightness.The monitor display needs to be adjustedThe resolution frequency should be changed.The text on the screen is unclear or blurredMake sure the resolution or refresh rate are compatible with the Display Mode. Touch panel doesn’t respondMake sure the touch screen driver is installed properly into your PC system and calibration is done.Thank you very much for using this 3nStar product.。
F2培养基的配制
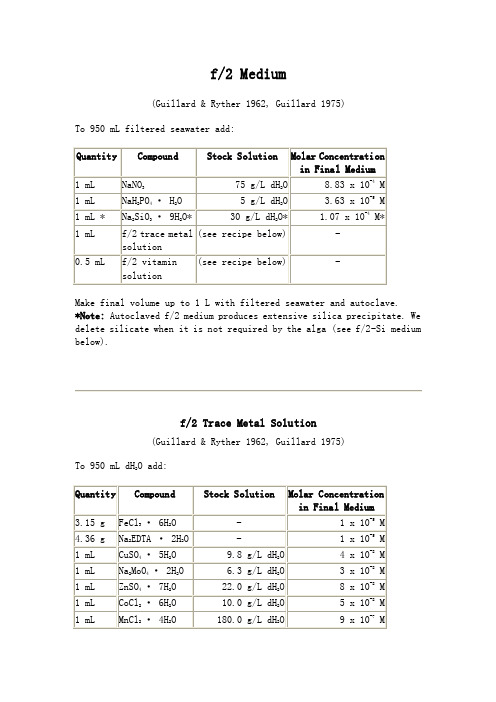
f/2 Medium(Guillard & Ryther 1962, Guillard 1975)To 950 mL filtered seawater add:Make final volume up to 1 L with filtered seawater and autoclave.*Note: Autoclaved f/2 medium produces extensive silica precipitate. We delete silicate when it is not required by the alga (see f/2-Si medium below).f/2 Trace Metal Solution(Guillard & Ryther 1962, Guillard 1975)To 950 mL dH2O add:Make final volume up to 1 L with dH2O. Autoclave.f/2 Vitamin Solution(Guillard & Ryther 1962, Guillard 1975)To 950 mL dH2O add:Make final volume up to 1 L with dH2O. Autoclave and store in refrigerator. Note: Vitamin B12 and biotin are obtained in a crystalline form. When preparing the vitamin B12stock solution, allow for approximately 11% water of crystallization (for each 1 mg of Vitamin B12, add 0.89 mL dH2O). When preparing the biotin stock solution, allow for approximately 4% water of crystallization (for each 1 mg of biotin, add 9.6 mL dH2O).f/2 DerivativesBlack Sea Medium: For brackish water organisms (16 psu, half-strength nutrients). Combine 500 mL f/2 medium and 500 mL dH2O. Autoclave.f/2 agar: Prepare 1 liter of f/2 medium and dissolve 9g Bacto-agar (heat and mix). For test tubes, dispense dissolved agar medium into tubes, autoclave, and then cool with tubes slanted at an angle. For Petri plates, autoclave in a flask, cool almost to the gelling point, and then aseptically dispense into sterile Petri plates. Note: Agar can be added to other media (e.g., f/50 agar), and agar concentration can be varied to produce softer or firmer substrates.f/2-Si: Prepare as for f/2 medium but omit Na2SiO3 · 9H2O. This is preferred over f/2 medium for organisms with no silica requirement because less precipitation forms.f/2 + Se: Extra silicon and selenium are beneficial to several diatom strains. Prepare 1 L of f/2 medium but use 2 mL of silicate stock, then add 1.0 mL of selenium stock solution (1.29 mg H2SeO 3 /L distilled H2O). Autoclave.f/2 (11 psu): For brackish water organisms. Mix 650 mL distilled H2O and 350 mL filtered seawater. Add f/2 medium nutrients and autoclave.f/2-Si (24 psu): Mix 750 mL distilled H2O and 250 mL filtered seawater. Prepare as for f/2 medium but omit Na2SiO 3 · 9H2O.f/4: Add 500 mL f/2 medium to 500 mL filtered seawater, then autoclave.f/4-Si: Autoclave 1 L of filtered seawater. When cool, aseptically add f/2-Si nutrients at half concentration (i.e., 0.5 mL).f/20-Si: Autoclave 1 L of filtered seawater. When cool, aseptically add f/2-Si nutrients at one tenth concentration (i.e., 100 μL).f/50-Si: This is more than a 1/25 dilution of f/2-Si medium. We autoclave 1 L of seawater in a Teflon-lined bottle. Wait for the autoclaved se awater to cool to room temperature (important). Aseptically add 40 μL of sterile f/2 nutrients (20 μL of vitamins).f/50-Si + CCMP1320 as food:Prepare f/50 and aseptically add 50 μL of healthy, moderately dense culture of CCMP1320.f/2m: To 1L f/2 medium add 1 g methylamine · HCl, mix until dissolved and autoclave. This medium is used to test for contamination by methylaminotrophic bacteria.f/2p: To 1 L f/2 medium, add 1 g Bacto-peptone, mix until dissolves and autoclave. This medium is used to test for contamination by non- methylaminotrophic bacteria and fungi.f/2pm: To 1L f/2 medium add 1 g Bacto-peptone and 1 g methylamine · HCl, mix until dissolved and autoclave. This general medium is used to test for contamination by bacteria and fungi.f/2 + NPM: Add f/2 nutrients to 900 mL of seawater and autoclave. After cooling, aseptically add 100 mL of the following organic stock solution. Dispense aseptically into test tubes.Organics Stock Solution(modified from Guillard 1960)To 900 mL dH2O add:Bring up to 1 L with dH2O. Dispense in small aliquots and autoclave.ReferencesGuillard, R.R.L. 1960. A mutant of Chlamydomonas moewusii lacking contractile vacuoles. J. Protozool. 7: 262-268.Guillard, R.R.L. 1975. Culture of phytoplankton for feeding marine invertebrates. pp 26-60. In Smith, W.L. and Chanle,y M.H. (eds.) Culture of Marine Invertebrate Animals. Plenum Press, New York, USA.Guillard, R.R.L. and Ryther, J.H. 1962. Studies of marine planktonic diatoms. I. Cyclotella nana Hustedt and Detonula confervacea Cleve. Can. J. Microbiol.8: 229-239.。
- 1、下载文档前请自行甄别文档内容的完整性,平台不提供额外的编辑、内容补充、找答案等附加服务。
- 2、"仅部分预览"的文档,不可在线预览部分如存在完整性等问题,可反馈申请退款(可完整预览的文档不适用该条件!)。
- 3、如文档侵犯您的权益,请联系客服反馈,我们会尽快为您处理(人工客服工作时间:9:00-18:30)。
Most investigations of the properties or the spatial distribution of galaxies begin with a sample selected in the optical, or sometimes in the infrared (based on IRAS Neugebauer 1
et al. 1984] 100 m detections). Even 21-cm or radio continuum studies usually target a sample of galaxies taken from optical catalogs, like the Uppsala Galaxy Catalog (UGC; Nilson 1973) or the Catalog of Galaxies and Clusters of Galaxies (Zwicky et al. 1961{ 1968). Thus, any population of galaxies or gas clouds with very low optical luminosity or surface brightness could have largely escaped detection and study. To circumvent this problem, we have conducted a direct search in the 21-cm line of neutral hydrogen, using the D-con guration of the Very Large Array (VLA1; Napier et al. 1983), covering elds in the Perseus-Pisces supercluster and in its foreground void (see Haynes & Giovanelli 1989, hereafter HG). In an earlier paper (Weinberg et al. 1991, hereafter Paper I), we summarized the Hi properties of our detected objects, and we discussed the implications of our results for the shape of the Hi mass function and for the spatial distribution of dwarf galaxies. In this paper, we describe the 21-cm observations and results in greater detail, and we also present the results of follow-up optical observations, both broad-band and H imaging. These data allow us to compare directly the properties of our Hi-selected objects to those of optically selected galaxies. For the VLA survey, we observed twelve elds in the Perseus-Pisces supercluster and thirty elds in the foreground void. The e ective survey volume varies with Hi mass, since more massive objects can be detected farther from the center of the primary beam and at greater distances from the earth. Paper I discussed the resulting \selection function" of the survey and compared it to that of previous 21-cm searches, particularly that of Fisher & Tully (1981), which at the time was the largest directly comparable survey. We will not repeat the details here|the salient points are that our survey covered nearly equal volumes in the void and the supercluster, and that its total e ective volume, roughly 100 Mpc3 for MHI > 3 108 M and 200 Mpc3 for MHI > 109 M , was much larger than that of previous surveys for Hi masses in the 108{109 M range typical of gas-rich dwarf galaxies.2 Henning (1992) has recently published results of a much larger 21-cm survey, which covers regions that are obscured by the Galactic plane at optical wavelengths. The sensitivity of these observations varied from one line-of-sight to another because of solar and man-made interference, dependence on declination and frequency resolution (Henning 1992); we are therefore unable to make a quantitative comparison of survey volumes. The survey detected 37 extragalactic objects, 19 of them previously cataloged. Follow-up optical analysis of the sample is still in progress. For a review of other 21-cm surveys, see Briggs (1990). Our survey detected nine previously uncataloged galaxies, along with seven brighter galaxies that are listed in the UGC or the Zwicky catalog. Our de nition of supercluster and void elds is based on HG's redshift surveys of optically selected galaxies. This strategy allows us to address some questions of large-scale structure even with a small survey volume, but it complicates the interpretation of our results to some extent. In particular, it is unclear whether the optically cataloged galaxies should be considered part of our Hi-selected \sample", since they played a role in the choice of survey elds. Our approach in this paper is to present results for our full sample but to focus on
astro-ph/9404058 22 Apr 94
Abstract
We analyze the properties of a sample of galaxies identi ed in a 21-cm, Hi-line survey of selected areas in the Perseus-Pisces supercluster and its foreground void. Twelve elds were observed in the supercluster, ve of them (target elds) centered on optically bright galaxies, and the other seven (blank elds) selected to contain no bright galaxies within 450 of their centers. We detected nine previously uncataloged, gas-rich galaxies, six of them in the target elds. We also detected Hi from seven previously cataloged galaxies in these elds. Observations in the void covered the same volume as the twelve supercluster elds at the same Hi-mass sensitivity, but no objects were detected. Combining our Hi data with optical broad-band and H imaging, we conclude that the properties of Hi-selected galaxies do not di er substantially from those of late-type galaxies found in optical surveys. In particular, the galaxies in our sample do not appear to be unusually faint for their Hi mass, or for their circular velocity. We nd tentative evidence for a connection between optical surface brightness and degree of isolation, in the sense that low surface brightness galaxies tend to be more isolated. The previously cataloged, optically bright galaxies in our survey volume dominate the total Hi mass density and cross-section; the uncataloged galaxies contribute only 19% of the mass and 12% of the cross-section. Thus, existing estimates of the density and cross-section of neutral hydrogen, most of which are based on optically-selected galaxy samples, are probably accurate. Such estimates can be used to compare the nearby universe to the high-redshift universe probed by quasar absorption lines.