8D templates from Pilkington Automotive
8D报告模板(中英文)
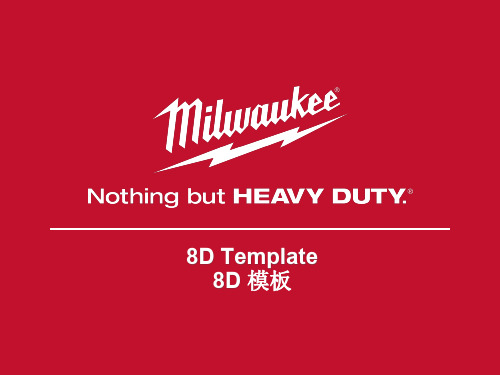
Where the problem was
found? 在哪发现问题?
When the defect was detected? 何时探测到次品?
Why this is a problem?
为什么是问题?
How the defect was detected? 次品是如何被探测
8D Template 8D 模板
Team Formation (成立专案小组)
Customer/Area Name 客户/区间名 Model Description 型号描述 Model Part No. 型号零件编号
D1 - TEAM FORMATION D1 – 成立专案小组
Customer/Internal Reference Case No 客户/内部参考个案编号
D2 – PROBLEM STATEMENT D2 – 问题描述
Describe Problem - Cont’d (描述问题 - 续前页)
D2.4) Problem Description by 5W2H + Is/Is Not Means (用5W2H + Is/Is Not 描述)
Is 是
What is the problem? 问题是什么?
联系方式
Start Date 开始日期
Contact Information (联系方式)
Contact Information (联系方式)
© Milwaukee Electric Tool Corp., 2010. Confidential Material. We reserve all rights in the event of intellectual property rights. We reserve all rights of disposal such as copying or passing on to third parties.
8D手法应用
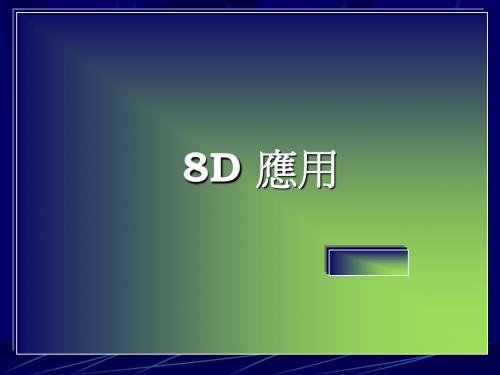
三﹑適用范圍
1. 當產品在製程中發生問題,且問題原因不明,必須 當產品在製程中發生問題,且問題原因不明, 製程中發生問題 以團隊的力量加以探討解決並提出對策時,適用之。 以團隊的力量加以探討解決並提出對策時,適用之。 2. 當外部客戶反應問題,影響產品及公司形象,必須 外部客戶反應問題 影響產品及公司形象, 反應問題, 以團隊的力量迅速解決問題時,適用之。 以團隊的力量迅速解決問題時,適用之。 3. 當供應商交貨產品發生品質問題﹐影響公司生產出貨 供應商交貨產品發生品質問題 交貨產品發生品質問題﹐ 或者引致使客戶抱怨時﹐應要求供應商應用『 或者引致使客戶抱怨時﹐應要求供應商應用『 8D 』 方法進行處理并提出書面報告時。 方法進行處理并提出書面報告時。
D4. 界定及确认真正肇因 指出所有均能解释造成该问题的可能肇因,然后与 之 指出所有均能解释造成该问题的可能肇因 然后与D2之 然后与 问题叙述及试验资料比对测试,划分及确认出真正的肇 问题叙述及试验资料比对测试 划分及确认出真正的肇 因. 界定所有的可能肇因,透过为什么 界定所有的可能肇因 透过为什么(WHY)?反覆地多次 透过为什么 反覆地多次 演练,一直到真正肇因找到及确认有效为止 演练 一直到真正肇因找到及确认有效为止 运用脑力激荡法. 运用脑力激荡法 运用要因分析图(鱼骨图) 运用要因分析图(鱼骨图) 广纳所有成员的意见 如果是一椿新发生的问题, 如果是一椿新发生的问题,要订定一个进度表
D4. 界定及确认真正肇因 續)﹕ 界定及确认真正肇因(續 ﹕ 探讨可能肇因的十二道查检法﹕ 探讨可能肇因的十二道查检法﹕ 有无绘制制程流程图来界定所有的变异肇因? 有无绘制制程流程图来界定所有的变异肇因? 是否所有的情报来源都已经用来探讨肇因? 是否所有的情报来源都已经用来探讨肇因? 有没有『物性』的证据? 有没有『物性』的证据? 制程与问题之间有无因果关系? 制程与问题之间有无因果关系? 有没有反覆地透过『为什么』 因为』 有没有反覆地透过『为什么』(WHY); 『因为』 (BECAUSE)来追查『可能的真正肇因』用以建立过 来追查『 来追查 可能的真正肇因』 渡的替代方案? 渡的替代方案 它是不是唯一的情况?这次问题或许类似过去发生过 它是不是唯一的情况 这次问题或许类似过去发生过 的?
8D简介
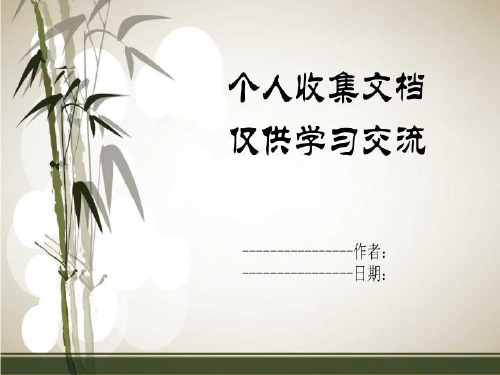
表單
樣板
試試看?!
注意點
A.不能只靠臆測、想像及經驗就直接驟下結論。 尤其是真正肇因不清楚時。
B.經驗固然重要,但若有完整計劃,實施時按部 就班、循序漸進,才能獲得最大成效。
C.一種負責任的承諾,問題的解決與否,不能靠 一句話,而是需要有事實來證明。
有關於品質方面的幾個觀念
品質是設計出來的 品質是製造出來的 品質是習慣出來的 一次性ok原則
准備使用8D程序
D1 - Establish a Team
成立團隊
D2 - Describe the Problem
問題描述
D3 - Develop Interim Containment Action (ICA)
緊急防止對策
D4 - Define & Verify Root Cause and Escape Point
預防
問題點?
home
放映結束
•1)賺錢?? •2)危機??
8D與顧客滿意
1. 顾客抱怨是一种满意程度低的最常见的表达 方式
2. 没有抱怨并不一定表明顾客很满意。
ISO精神??
預防與矯正
品質管理的核心 雀巢公司的故事
有更好的 工具嗎?
矯正與預防
–矯正措施 再發防止 –預防措施 防患於未然
持續 改善
8D=??
D0 - Prepare for Global-8D Process
Choose & Verify Permanent Corrective Actions (PCAs) for Root Cause & Escape Point
永久改善對策 5.確認矯正行動→
–透過暫時性的預先生產方式的測試計劃, –確定所選定的矯正措施確實能為顧客解決問題, –同時不會演伸不良影響。
8D报告模板
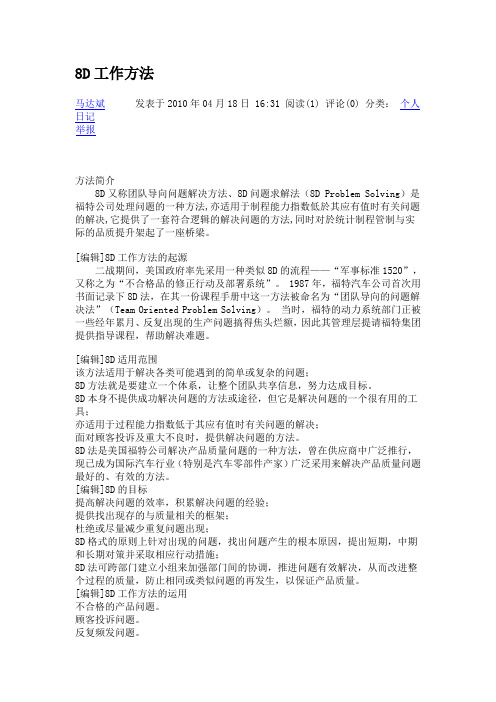
8D工作方法马达斌发表于2010年04月18日 16:31 阅读(1) 评论(0) 分类:个人日记举报方法简介8D又称团队导向问题解决方法、8D问题求解法(8D Problem Solving)是福特公司处理问题的一种方法,亦适用于制程能力指数低於其应有值时有关问题的解决,它提供了一套符合逻辑的解决问题的方法,同时对於统计制程管制与实际的品质提升架起了一座桥梁。
[编辑]8D工作方法的起源二战期间,美国政府率先采用一种类似8D的流程——“军事标准1520”,又称之为“不合格品的修正行动及部署系统”。
1987年,福特汽车公司首次用书面记录下8D法,在其一份课程手册中这一方法被命名为“团队导向的问题解决法”(Team Oriented Problem Solving)。
当时,福特的动力系统部门正被一些经年累月、反复出现的生产问题搞得焦头烂额,因此其管理层提请福特集团提供指导课程,帮助解决难题。
[编辑]8D适用范围该方法适用于解决各类可能遇到的简单或复杂的问题;8D方法就是要建立一个体系,让整个团队共享信息,努力达成目标。
8D本身不提供成功解决问题的方法或途径,但它是解决问题的一个很有用的工具;亦适用于过程能力指数低于其应有值时有关问题的解决;面对顾客投诉及重大不良时,提供解决问题的方法。
8D法是美国福特公司解决产品质量问题的一种方法,曾在供应商中广泛推行,现已成为国际汽车行业(特别是汽车零部件产家)广泛采用来解决产品质量问题最好的、有效的方法。
[编辑]8D的目标提高解决问题的效率,积累解决问题的经验;提供找出现存的与质量相关的框架;杜绝或尽量减少重复问题出现;8D格式的原则上针对出现的问题,找出问题产生的根本原因,提出短期,中期和长期对策并采取相应行动措施;8D法可跨部门建立小组来加强部门间的协调,推进问题有效解决,从而改进整个过程的质量,防止相同或类似问题的再发生,以保证产品质量。
[编辑]8D工作方法的运用不合格的产品问题。
最全中英文版8D模板
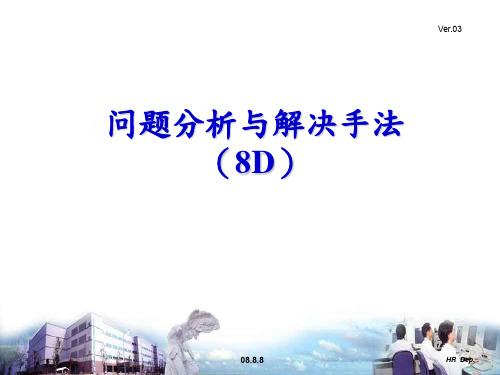
Action
Hold Sorting Sorting Sorting Sorting Sorting
NG Q’ty 0 ? 15 3 3 2 2
F/Y
Owner Due day
CS:张三 6/12
?
CS:李四 6/13
0.70% 0.58% 0.58%
CS:王二 OQC:李四 OQC:李四
6/14 6/15 6/15
8 Steps
Step 1:Team Formation(组成团队) Step 2:Problem description(问题描述)
Step 3: Containment Actions(防堵行动) Step 4:Root Cause Analysis(发生原因分析)
Step 5:Corrective Actions(矫正措施) Step 6: Verification of Action Effectiveness(效 果确认) Step 7: Recurrence Prevention(预防再发) Step 8:Congratulation the Team(恭喜团队完成 任务)
4. How to contain ?
In-Line
5. Who/When ?
4. How to contain ? 5. Who/When ?
IQC
3. Where to contain ?
On the way
5. Who/When ? 4. How to contain ?
Warehouse
OQC
0.77% MFG:李四 6/16
0.77% SQE:李四 6/17
Who and when?
13
原因分析
怎樣讓客戶信服你的rootcause分析?
8D培训课件(PPT 42页)

第十八页,共40页。
‹#›
‹‹1##7›
何謂5W2H
何人 :识別哪一个客戶在埋怨
何事 :适当、准确地识別效果
何時 :从什么时分红绩末尾发作(fāzuò)
何地 :什么中央发作(fāzuò)效果
为何 :识別的解释
如何 :在什么方式或外形下发作(fāzuò) 这问題
又要再换了,所以不但要换,而且要换好的橡胶密封。 Deming在上课时不时追问为什么、为什么、为什么,不时到无
法拆解下去,那么才干算为基本缘由。
第六页,共40页。
‹#›
‹#6›
解決基本( jīběn)性問題
丰田员工提出〝5个为什么〞。要找出效果的基本 缘由,必需至少依次(yīcì)提出5个〝为什么?〞这 就象一层层剥洋葱一样。例如,焊接到膜盒上的一 根毛细管发作了泄漏:
为什么样会泄漏?
焊接密封不好。
为什么焊接的密封不好?
在毛细管内有堆积物。
为什么在毛细管内有堆积物?
清洗管子时没有清洗掉。 第七页,共40页。
‹#›
‹#7›
处置(chǔzhì)基本性效果
为什么清洗不掉? 运用的洗濯剂效果不好。 为什么洗濯剂效果不好? 洗濯剂的配方对毛细管内的这种堆积物有效。 必需记住的是当你可以〝发作又消弭〞时,也就是说可
以随意地重现一个效果,然后又能使其处置时,你就能 确定曾经(céngjīng)找到了这个效果的基本缘由。
第八页,共40页。
‹#›
‹#8›
何谓(héwèi)8D
此方式(fāngshì)是团队运作导向以理想 为基础,防止集团主意的介入,使效果的处 置能更具条理。
8D报告模板中英文
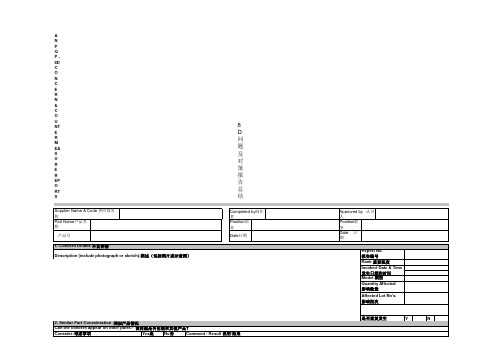
5. Final Analysis 最终分析 5 WHY Analysis to identify root cause:5Why 分析根本原因
Consider: Man, Material, Machine, Method, Who, Where When Why, How, Process settings, Rework, Maintenance etc. Attach extra detail sheets where necessary 法、谁、在哪里、何时、为什么、怎样解决、工艺流程设计、返工、维护等。 如有需要可以增加表格。
Why?为什么 Why?为什 Why?为什么 么
Why?为什么 Why?为什 Why?为什么 么
Why?为什么 Why?为什 Why?为什么 么
Why?为什么 Why?为什 Why?为什么 么
Why?为什么 Why?为什么 Why?为什么 Why?为什么 Why?为什么 Why?为什么 Why?为什么 Why?为什么 Why?为什么 Why?为什么
A N P Q P8D C O N C E R N & C O U NT E R M EA S U R E R EP O RT S
Supplier Name & Code 供应商名 称 Part Name产品名 称
产品号
1. Concern Details 不良详情
Description (include photograph or sketch):描述(包括图片或示意图)
Qty. NG
Qty. OK 未通过数 % Effective 临时
通过数量 量
8D method(8D报告)教材中英文讲解
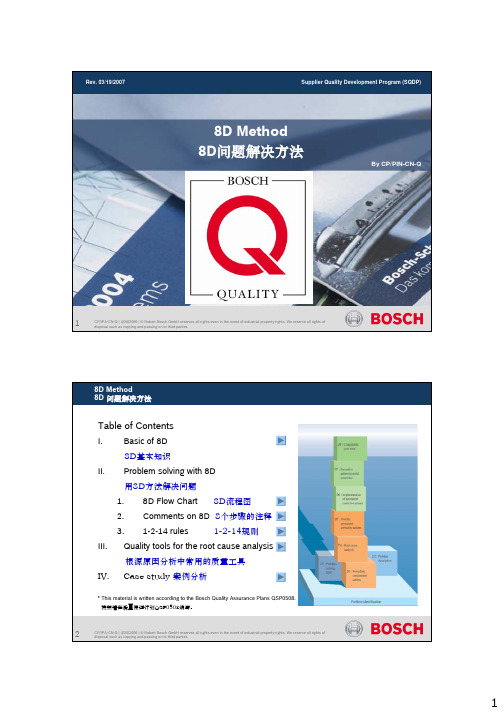
8D Method 8D 问题解决方法
1. 8D Flow Chart 8D流程图
Comments/注释
-Solve complex problems with (but not only) the: 用以下方法(但不 限于)解决复杂问题:
-5x why questioning technique/5"why"法
2
8D Method 8D 问题解决方法
I. Basic of 8D 8D基本知识
¾ Complaint 抱怨8D问题解决方法
„Complaint” is understood here as a deviation (e.g. of products, processed, organizational procedures) that is reported by an internal or external customer. “抱怨”在这里理解为由内部或者外部客户反馈的某种特性的偏差( 比如产品,过程,有组织的程序)。
4
CP/IPA-CN-Q | 4/20/2006 | © Robert Bosch GmbH reserves all rights even in the event of industrial property rights. We reserve all rights of disposal such as copying and passing on to third parties.
8D Method 8D 问题解决方法
I. Basic of 8D 8D基本知识
¾ Why 8D 8D的目8D的问题解决方法
1. Rapid, lasting and systematic processing of internal and external complaints, locating and eliminating the root defect cause. 快速、持续并且系统的处理内部以及外部的抱怨,定位并消除根 源缺陷原因。
8D报告英文版格式
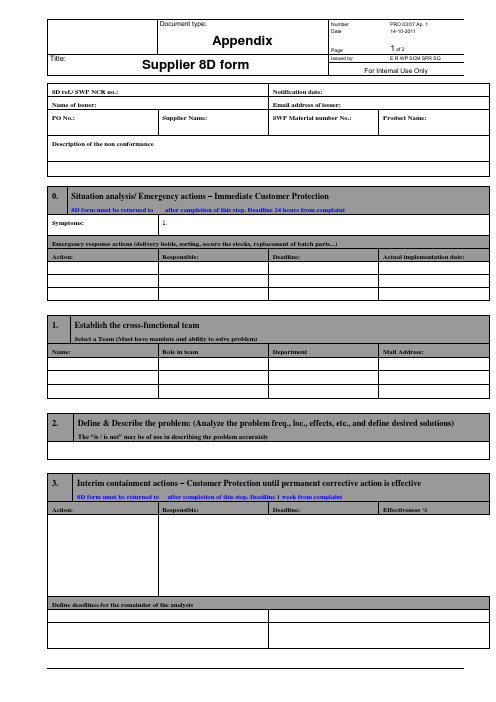
Action:
Responsible:
Deadline:
Effectiveness %
Define deadlines for the remainder of the analysis
1.
Establish the cross-functional team
Select a Team (Must have mandate and ability to solve problem)
Name:
Role in team
Department
Mail Address:
2.
Define & Describe the problem: (Analyze the problem freq., loc., effects, etc., and define desired solutions)
8D form must be returned toafter completion of this step.
8D form must be returned toafter completion of this step.
Action:
Responsible:
Implementation date:
Effectiveness %
6.
Implement Permanent corrective actions and confirm the Effects
4.
Identify the root causes for both occurrence and escape of detection for den non conformance
8D template for suppliers
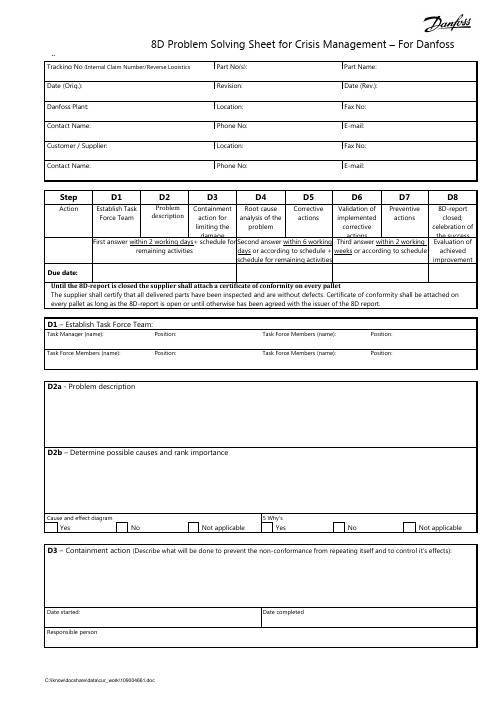
D2a - Problem description
D2b – Determine possible causes and rank importance
Cause and effect diagram
5 Why’s
Yes
No
Not applicable
Yes
No
Not applicable
D3 – Containment action (Describe what will be done to prevent the non-conformance from repeating itself and to control it’s effects):
Not applicable Not applicable Not applicable Not applicable
Check Sheet Yes Graphs and charts Yes Control chart Yes Scatter diagram Yes
Actual Date Completed
D4 – Root Cause Analysis of the Problem
Concentration diagram Yes No Cause and effect diagram Yes No Pareto diagram Yes No Histogram Yes No
Target Completion Date
Tracking No (Internal Claim Number/Reverse Logistics
Number):Emne
iire
8D Problem Solving Sheet for Crisis Management – For Danfoss Suppliers
8D format
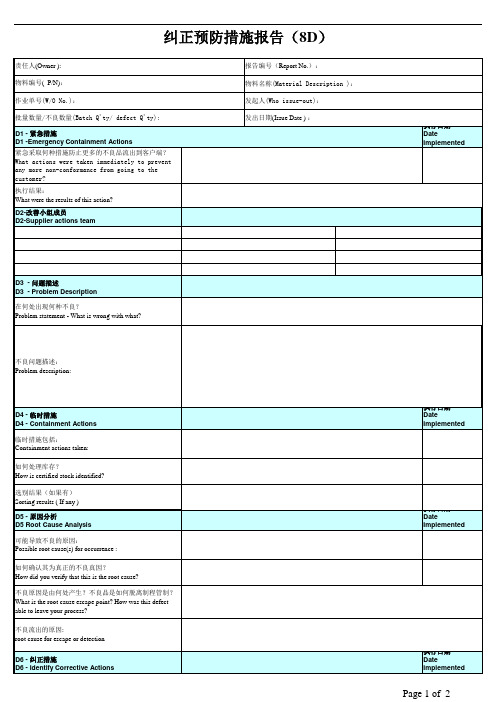
执行日期 Date Implemented
执行日期 Date Implemented
执行日期 Date Implemented来自Page 1 of 2
针对不良产生原因的纠正措施: corrective actions for occurrence root cause: 针对不良流出原因的纠正措施: corrective actions for detection root cause: D7 - 执行与确认纠正措施 D7 - Implement And Validate Chosen Corrective Actions 执行的纠正措施包括: List corrective actions implemented: 执行日期 Date Implemented
D8 - 预防措施 D8 - Preventive Actions 如何消除不良原因,防止此类不良再次发生: What has been put in place in order to prevent this root cause from occurring again? 是否有系统文件管制?纠正措施有否展开至生产所涉及 的所有部门?如果有,请列出: Are there any systemic applications? Can this action be taken across all product lines? If so, list them here. 执行成效 following up & review
纠正预防措施报告(8D)
责任人(Owner ): 物料编号( P/N): 作业单号(W/O No.): 批量数量/不良数量(Batch Q'ty/ defect Q'ty): D1 - 紧急措施 D1 -Emergency Containment Actions 紧急采取何种措施防止更多的不良品流出到客户端? What actions were taken immediately to prevent any more non-conformance from going to the customer? 执行结果: What were the results of this action? D2-改善小组成员 D2-Supplier actions team 报告编号(Report No.): 物料名称(Material Description ): 发起人(Who issue-out): 发出日期(Issue Date ) : 执行日期 Date Implemented
TS16949报告英文模板 8D
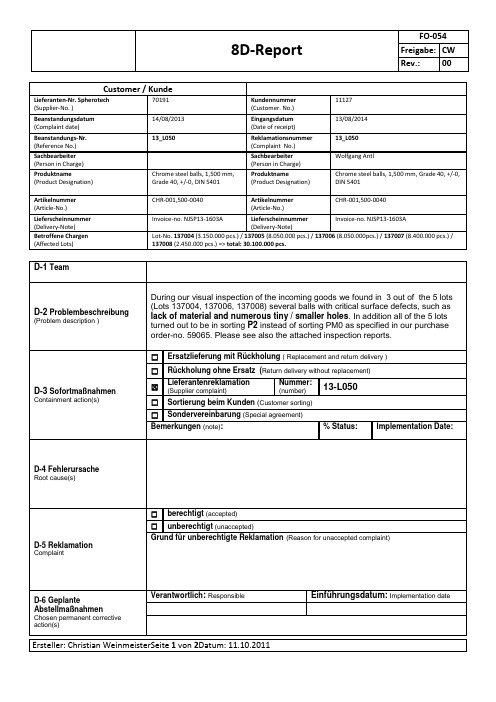
Chosen permanent corrective action(s)
Verantwortlich:Responsபைடு நூலகம்ble
Einführungsdatum:Implementation date
D-7 Eingeführte Abstellmaßnahme(n)Implemented permanent corrective action(s)
Artikelnummer
(Article-No.)
CHR-001,500-0040
Artikelnummer
(Article-No.)
CHR-001,500-0040
Lieferscheinnummer
(Delivery-Note)
Invoice-no. NJSP13-1603A
Lieferscheinnummer
%Status:
Implementation Date:
D-4 Fehlerursache
Root cause(s)
D-5 Reklamation
Complaint
☐
berechtigt(accepted)
☐
unberechtigt(unaccepted)
Grund für unberechtigte Reklamation(Reason for unaccepted complaint)
(Delivery-Note)
Invoice-no. NJSP13-1603A
Betroffene Chargen
(Affected Lots)
Lot-No.137004(3.150.000 pcs.) /137005(8.050.000 pcs.) /137006(8.050.000pcs.) /137007(8.400.000 pcs.) /137008(2.450.000 pcs.) =>total: 30.100.000 pcs.
8D分析报告中英文模板

报告编号(Report No. ):.主题(Subject ): 发货日期产品名称问题分析小组成员姓名(Name )组长(Team Leader )组员(Team Member ) :(Issue(s)Description) :应急对策(Containment Action(s))1).对策(Action(s)) :2).有效性(Effect): 3.)生效日期(Implemcntation Date) :(Root Cause(s))1)原因分析过程(Analysis) :2)根本原因(Root Cause(s)) :3)有效性(Effect) (%):长期纠正措施(Chosep Permanent Corrective Action(s)1).纠正措施选择(Corrective Action(s)) :2).有效性(Effect) (%):纠正措施实施(Implemcnted Permanent Corrective Action(s)) :1)实施方法(Implemented Corrective Action(s): 客户名称数量 联系电话/e-mail(Telephone/e-mail)所在部门(Department ) 投诉/退货日期 产品型号2).开始实施日期(Implementation Date) : 2012-4-6防止问题再次发生的措施(Action(s)to Prevent Recurrence) :1).防止方法(Action(s)) :2).开始实施的日期(Implementation Date):通知相关部门(Congratulate your Team) :需要通知的部门(Team to Congratulate) : 问题解决日期(Close Date)。
汽车部件8D报告及8D项目模板解释

D4、寻找出根本原因----案例 对可能原因进行验证----主动验证 为了再验证脚板变形对脚板晃动故障的直接影响,到仓库抽取在库脚板进行组装验证,发现脚板与胶垫接触点高度对脚板晃动故障会产生重要影响
D4、寻找出根本原因(附)
丰田汽车公司前副社长大野耐一曾举了一个例子来找出停机的真正原因 有一次,大野耐一在生产线上的机器总是停转,虽然修过多次但仍不见 好转。于是,大野耐一与工人进行了以下的问答: 问“为什么机器停了?”答“因为超过了负荷,保险丝就断了。” 问“为什么超负荷呢?”答“因为轴承的润滑不够。” 问“为什么润滑不够?” 答“因为润滑泵吸不上油来。” 问“为什么吸不上油来?”答“因为油泵轴磨损、松动了。” 问“为什么磨损了呢?”再答“因为没有安装过滤器,混进了铁屑等杂质。” 经过连续五次不停地问“为什么”,才找到问题的真正原因和解决的方法, 在油泵轴上安装过滤器。 如果我们没有这种追根究底的精神来发掘问题,我们很可能只是换根保险 丝草草了事,真正的问题还是没有解决。
概述:
1
措施实施断点确认 断点后质量信息收集 目标未达成,返回D4 目标达成,ICA解除
任务:
2
D6、验证措施有效性
D6、验证措施有效性----案例
市场目标跟踪
现场目标跟踪
现场目标未达成,增补措施: 1、故障件再收集分析—李志军 2、预装配工艺纪律检查—张艳龙 3、预装完成品抽查—李志军
D7提供修改需要的系统,包括标准、规范、程序等来对措施进行巩固,防止问题再次发生的机会。
E N D 谢 谢 !
单击添加文本具体内容简明扼要地阐述你的观点
单击此处添加副标题
概述:
整理小组改进档案 确定需要修改的文件(如图纸、技术规范、控制计划、作业文件、检查标准等) 更新文件并发布
8D报告模板(英文 5WHY)
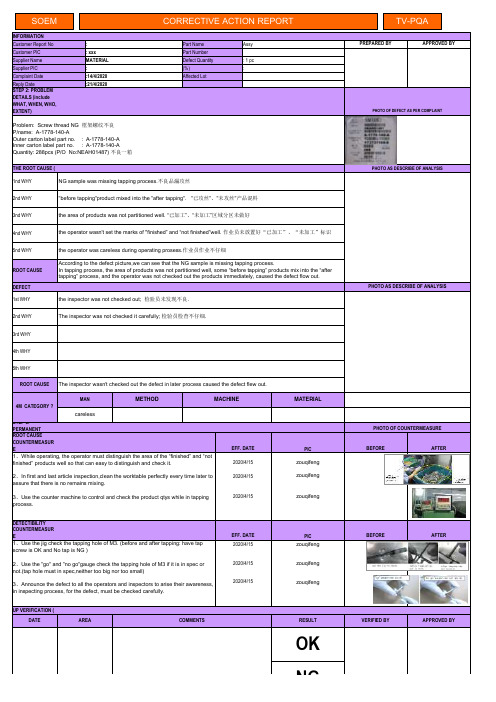
STEP 1: GENERAL INFORMATION Customer Report No :Part Name : Pre Case Assy Customer PIC : xxx Part Number Supplier Name : NEW MATERIAL Defect Quantity : 1 pc Supplier PIC :Defect Ratio (%):Complaint Date :14/4/2020Affected LotReply Date:21/4/2020STEP 2: PROBLEM DETAILS (include WHAT, WHEN, WHO,EXTENT)STEP 3: DESCRIBE THE ROOT CAUSE (1nd WHY 2nd WHY 3nd WHY 4nd WHY 5nd WHYROOT CAUSE STEP 4: WHY DEFECT 1st WHY 2nd WHY 3rd WHY 4th WHY 5th WHY ROOT CAUSEMETHODMATERIALSTEP 6:PERMANENT ROOT CAUSECOUNTERMEASUR EPIC zouqifeng zouqifengzouqifengDETECTIBILITY COUNTERMEASUR EPIC zouqifeng zouqifeng zouqifengSTEP 7: FOLLOW UP VERIFICATION (DATERESULTAPPROVED BY4M CATEGORY ?OK NGProblem: Screw thread NG 框架螺纹不良P/name: A-1778-140-AOuter carton label part no. : A-1778-140-A Inner carton label part no. : A-1778-140-AQuantity: 288pcs (P/O No:NEAH01487) 不良一箱1、While operating, the operator must distinguish the area of the “finished” and “not finished” products well so that can easy to distinguish and check it.2、In first and last article inspection,clean the worktable perfectly every time later to assure that there is no remains mixing.3、Use the counter machine to control and check the product qtys while in tapping process.1、Use the jig check the tapping hole of M3. (before and after tapping: have tap screw is OK and No tap is NG )2、Use the "go" and "no go"gauge check the tapping hole of M3 if it is in spec or not.(tap hole must in spec,neither too big nor too small)3、Announce the defect to all the operators and inspectors to arise their awareness,in inspecting process, for the defect, must be checked carefully.2020/4/152020/4/152020/4/15AREACOMMENTSVERIFIED BY2020/4/152020/4/152020/4/15EFF. DATE BEFORE AFTERMANMACHINEcarelessPHOTO OF COUNTERMEASUREEFF. DATE BEFORE AFTERthe inspector was not checked out; 检验员未发现不良.The inspector was not checked it carefully; 检验员检查不仔细.The inspector wasn't checked out the defect in later process caused the defect flew out."before tapping"product mixed into the "after tapping". "已攻丝"、"未攻丝"产品混料the area of products was not partitioned well. “已加工”、“未加工”区域分区未做好the operator wasn't set the marks of "finished” and “not finished”well. 作业员未放置好“已加工”、“未加工”标识the operator was careless during operating prosess.作业员作业不仔细According to the defect picture,we can see that the NG sample is missing tapping process.In tapping process, the area of products was not partitioned well, some “before tapping” products mix into the “after tapping” process, and the operator was not checked out the products immediately, caused the defect flow out.PHOTO AS DESCRIBE OF ANALYSISPREPARED BYAPPROVED BYPHOTO OF DEFECT AS PER COMPLAINTPHOTO AS DESCRIBE OF ANALYSISNG sample was missing tapping process.不良品漏攻丝TV-PQASOEMCORRECTIVE ACTION REPORT。
8D 范本英文版
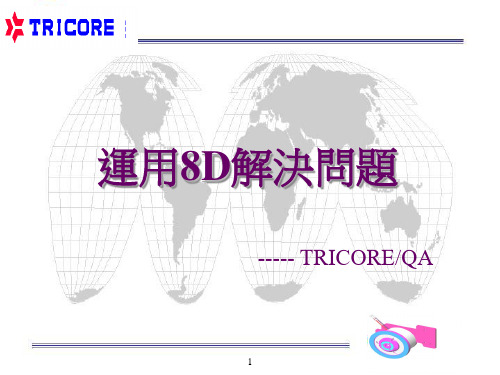
原則3- 描述根因(3)
原因的確認
1. 當一個短期對策執行後,是否能確保不會衍生其它問題? 2.當評估改善措施的有效性時,是否有考慮最終的使用者? 3.所有受影響的程序/操作是否被監控以確定和排除後續衍
生的問題? 4.相關的DFMEA/PFMEA資料是否被更新?
11
五個為什麼 (1)
因為沒有釘子,所以馬蹄鐵丟失了; 因為沒有馬蹄鐵,所以戰馬丟失了; 因為沒有戰馬,所以騎士丟失了; 因為沒有騎士,所以戰爭失敗了; 因為戰爭失敗了,所以王國消失了。
WHERE - 問題點發生在產品的何處? - 當發現問題時,問題出在哪裡? ( 發生地點 )
WHY - 為什麼它是個問題? ( 抱怨的內容)
HOW - 問題怎樣被發現的? ( 目視檢查、客訴等)
HOW - 有多少產品或組件有此問題? MANY - 問題是變好或是變壞,還是保持原狀?
7
原則2 - 描述問題(2)
真因。 7.參與者將明白在定義可能的真因時原因和影響分析圖的重要性。 8.參與者將知道在他們的工作環境中成功運用8D程序需從管理階層所
得到的支持。 9.參與者將明白體會到在找出問題的真因中,團隊行動的需要性與重
要性。
2
運用8D解決問題
發現區 8D分析
運用8D解決問題
根本原因
預防區 優先考慮的原因
DFMEA PFMEA
* 選擇和證實改善措施
1. 是否有把預期的改善措施通知所有相關被影響的人員? 2. 監控所有後續影響的程序/操作的結果以確定是否有後續的問題? 3. 相關的DFMEA/PFMEA資料是否有更新? 4. 所有臨時性的對策是否有移至合適的位置? 5. 是否能確保所有短期對策的實施不會產生其它問題? 6. 所有短期對策行動是否會持續到一長串的系列措施的實施? 7. 是否有與客戶協調你的行動計劃? 8. 是否有作測試來評估短期對策行動的有效性? 9. 是否有小規模的試驗短期對策行動以測試其有效性? 10.是否有收集資料已確保行動的有效性?
8D报告模板-汽车行业
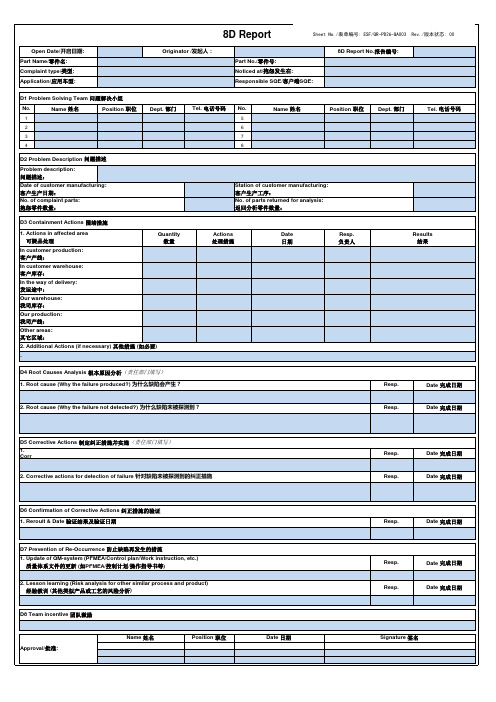
N o.Name 姓名Position 职位Dept. 部门No.Name 姓名Position 职位Dept. 部门Tel. 电话号码15263748Date 日期Resp.负责人Resp.Date 完成日期Resp.Date 完成日期1. Corrective actions for production of failure 针对缺陷产生的纠正措施Resp.Date 完成日期Resp.Date 完成日期Resp.Date 完成日期Resp.Date 完成日期Resp.Date 完成日期D1 Problem Solving Team 问题解决小组D2 Problem Description 问题描述D3 Containment Actions 围堵措施2. Lesson learning (Risk analysis for other similar process and product) 经验教训 (其他类似产品或工艺的风险分析)D8 Team incentive 团队激励Name 姓名Position 职位Date 日期Signature 签名Approval/批准:D6 Confirmation of Corrective Actions 纠正措施的验证1. Reroult & Date 验证结果及验证日期D7 Prevention of Re-Occurrence 防止缺陷再发生的措施1. Update of QM-system (PFMEA/Control plan/Work instruction, etc.) 质量体系文件的更新 (如PFMEA/控制计划/操作指导书等)D4 Root Causes Analysis 根本原因分析(责任部门填写)1. Root cause (Why the failure produced?) 为什么缺陷会产生?2. Root cause (Why the failure not detected?) 为什么缺陷未被探测到?D5 Corrective Actions 制定纠正措施并实施(责任部门填写)2. Corrective actions for detection of failure 针对缺陷未被探测到的纠正措施Other areas:其它区域:2. Additional Actions (if necessary) 其他措施 (如必要)-Our warehouse:我司库存:Our production:我司产线:In customer warehouse:客户库存:In the way of delivery:发运途中:1. Actions in affected area 可疑品处理Quantity 数量Actions 处理措施Results 结果In customer production:客户产线:Date of customer manufacturing:客户生产日期:Station of customer manufacturing:客户生产工序:No. of complaint parts:抱怨零件数量:No. of parts returned for analysis:返回分析零件数量:Tel. 电话号码Problem description:问题描述:Complaint type/类型:Noticed at/抱怨发生在:Application/应用车型:Responsible SQE/客户端SQE:8D ReportOpen Date/开启日期:Originator /发起人:8D Report No.报告编号:Part Name/零件名:Part No./零件号:Sheet No./表单编号: ESF/QR-PD26-QA003 Rev./版本状态: 00。
- 1、下载文档前请自行甄别文档内容的完整性,平台不提供额外的编辑、内容补充、找答案等附加服务。
- 2、"仅部分预览"的文档,不可在线预览部分如存在完整性等问题,可反馈申请退款(可完整预览的文档不适用该条件!)。
- 3、如文档侵犯您的权益,请联系客服反馈,我们会尽快为您处理(人工客服工作时间:9:00-18:30)。
Responsible
Date
Assessment
Responsible
Date
Assessment
Responsible Plant Manager
Name ……………………Signature …………………….Date …………. Responsible Plant Quality Manager
Name ……………………
Signature …………………….
Date ………….
Concern Action Plan (8D) Report
Concern Reference:
Date:
Full or Interim Report:
when the concern occurred what is the defect
how many products were rejected in Pilkington / customer and bonded in stock / warehouse [what impact to Pilkington/customer by the concern]what reaction came from Pilkington/customer [was any penalty applied by Pilkington/customer]was rejected sample returned to plant was it repeated concern or new concern detailed data to be attached
Send to:
Concerned Party:
what containment actions have been taken
what stocks were reinspected ( stock in Pilkington, customer, outside warehouse, inhouse stock, WIP )was our operation improved and back to normal condition is it still continued
details of action to be attached
list of team members outline of analysis
root-cause(s) identified
details of failure mechanism(s)
detailed analysis process and data to be attached
did inspection operator mistake or not outline of analysis
detailed analysis process and data to be attached
3. Root-cause Analysis:
3.1. Reason why the defect was generated: 3.2. Reason why the defect product was shipped to customer:Internal plant or Supplier's name and plant responsible
for concern Responsible Plant:Affected product/material and defect:
1. Outline of concern:
Plant Manager Name & Quality
Manager Name at Responsible Plant:
Specified contacts in Pilkington
Automotive
Part or material concerned and major defect
Customer's and/or Plant's name affected by concern (reference
SQIN)
5. Cross-site dissemination action ( action to prevent similar problem ):
6. Future Improvement Action Plans (if applicable):
7. Signatures
how this experience is utilised for prevention of similar problems in the future details of action to be attached
what are future medium to long term plans for improving the processes linked to this concern study item, name of responsible person, time schedules
2. Containment Action:
outline of action taken to eliminate root cause(s)
outline of action taken to verify the root cause(s) have been effectively eliminated have SOPs, Process Control Plans, Set-up Sheets been revised details of action to be attached
4.Corrective Action:
PU0101 A2. The controlled version is the electronic version.。