FMEA评分标准
fmea打分规则
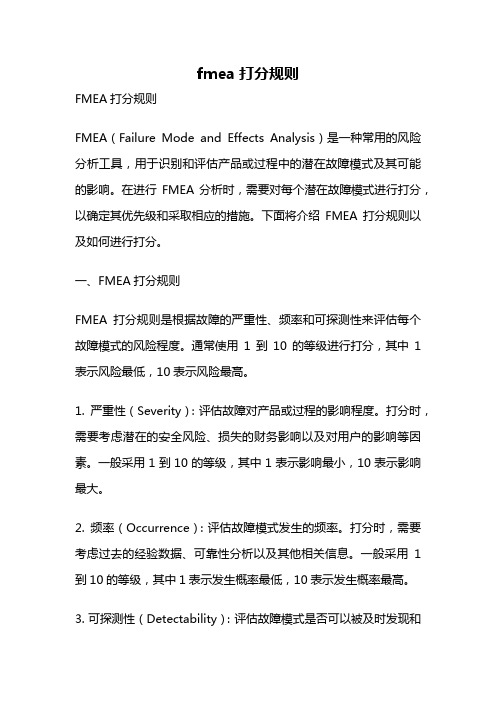
fmea打分规则FMEA打分规则FMEA(Failure Mode and Effects Analysis)是一种常用的风险分析工具,用于识别和评估产品或过程中的潜在故障模式及其可能的影响。
在进行FMEA分析时,需要对每个潜在故障模式进行打分,以确定其优先级和采取相应的措施。
下面将介绍FMEA打分规则以及如何进行打分。
一、FMEA打分规则FMEA打分规则是根据故障的严重性、频率和可探测性来评估每个故障模式的风险程度。
通常使用1到10的等级进行打分,其中1表示风险最低,10表示风险最高。
1. 严重性(Severity):评估故障对产品或过程的影响程度。
打分时,需要考虑潜在的安全风险、损失的财务影响以及对用户的影响等因素。
一般采用1到10的等级,其中1表示影响最小,10表示影响最大。
2. 频率(Occurrence):评估故障模式发生的频率。
打分时,需要考虑过去的经验数据、可靠性分析以及其他相关信息。
一般采用1到10的等级,其中1表示发生概率最低,10表示发生概率最高。
3. 可探测性(Detectability):评估故障模式是否可以被及时发现和探测。
打分时,需要考虑现有的检测手段、监测系统以及人工检查等因素。
一般采用1到10的等级,其中1表示可以容易地被探测到,10表示很难被探测到。
二、FMEA打分方法1. 计算风险优先数(Risk Priority Number,RPN):RPN是FMEA中用于确定优先级的指标,是通过将严重性、频率和可探测性的打分相乘得到的。
RPN=Severity × Occurrence × Detectability。
根据RPN的大小,可以确定优先处理的故障模式。
2. 制定打分规则:根据实际情况和需求,制定FMEA打分规则。
例如,可以定义RPN大于100的故障模式为高风险,需要立即采取措施;RPN在50到100之间的故障模式为中风险,需要进行改进;RPN小于50的故障模式为低风险,可以接受。
fmea探测度评级方法
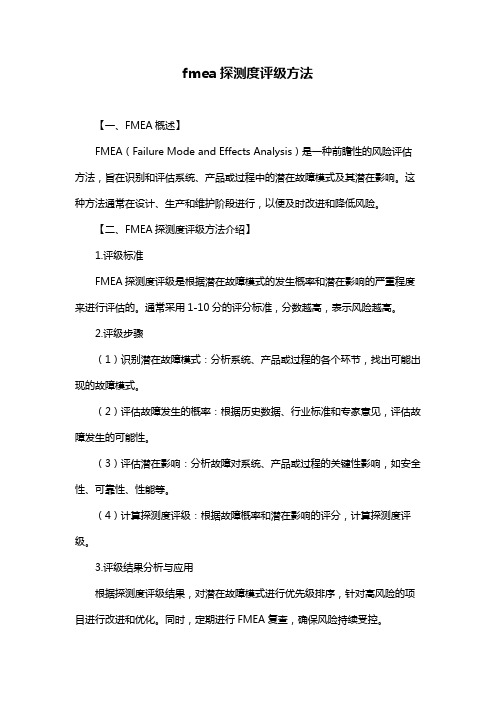
fmea探测度评级方法
【一、FMEA概述】
FMEA(Failure Mode and Effects Analysis)是一种前瞻性的风险评估方法,旨在识别和评估系统、产品或过程中的潜在故障模式及其潜在影响。
这种方法通常在设计、生产和维护阶段进行,以便及时改进和降低风险。
【二、FMEA探测度评级方法介绍】
1.评级标准
FMEA探测度评级是根据潜在故障模式的发生概率和潜在影响的严重程度来进行评估的。
通常采用1-10分的评分标准,分数越高,表示风险越高。
2.评级步骤
(1)识别潜在故障模式:分析系统、产品或过程的各个环节,找出可能出现的故障模式。
(2)评估故障发生的概率:根据历史数据、行业标准和专家意见,评估故障发生的可能性。
(3)评估潜在影响:分析故障对系统、产品或过程的关键性影响,如安全性、可靠性、性能等。
(4)计算探测度评级:根据故障概率和潜在影响的评分,计算探测度评级。
3.评级结果分析与应用
根据探测度评级结果,对潜在故障模式进行优先级排序,针对高风险的项目进行改进和优化。
同时,定期进行FMEA复查,确保风险持续受控。
【三、FMEA探测度评级方法在实际案例中的应用】
在某汽车制造商的生产线中,通过FMEA探测度评级方法,发现了潜在的装配错误导致的车辆安全隐患。
针对这一高风险项目,企业进行了改进,提高了装配过程中的质量控制,有效降低了故障率。
【四、总结与展望】
FMEA探测度评级方法是一种有效的风险评估工具,可以帮助企业及时发现和解决潜在问题,提高产品质量和安全性。
FMEA评价标准(RPN)
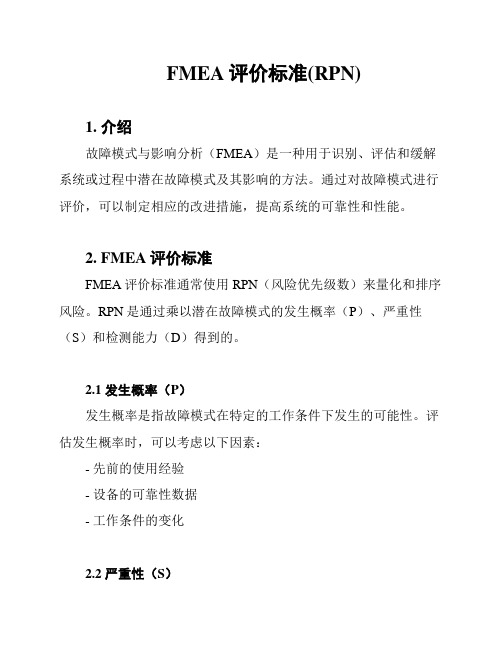
FMEA评价标准(RPN)1. 介绍故障模式与影响分析(FMEA)是一种用于识别、评估和缓解系统或过程中潜在故障模式及其影响的方法。
通过对故障模式进行评价,可以制定相应的改进措施,提高系统的可靠性和性能。
2. FMEA评价标准FMEA评价标准通常使用RPN(风险优先级数)来量化和排序风险。
RPN是通过乘以潜在故障模式的发生概率(P)、严重性(S)和检测能力(D)得到的。
2.1 发生概率(P)发生概率是指故障模式在特定的工作条件下发生的可能性。
评估发生概率时,可以考虑以下因素:- 先前的使用经验- 设备的可靠性数据- 工作条件的变化2.2 严重性(S)严重性是指故障模式对系统性能、工作过程或安全性产生的影响程度。
评估严重性时,可以考虑以下因素:- 潜在的损害或危险- 对生产能力或成本的影响- 用户的感知和体验2.3 检测能力(D)检测能力是指在故障模式发生后,能够及时检测和识别故障的能力。
评估检测能力时,可以考虑以下因素:- 监控设备和技术的有效性- 人员培训和专业知识- 检测系统的灵敏度3. 使用FMEA评价标准的步骤使用FMEA评价标准进行分析和评估时,可以按照以下步骤进行:1. 选择要评估的系统、过程或设备。
2. 识别故障模式和潜在影响。
3. 为每个故障模式分配发生概率(P)、严重性(S)和检测能力(D)等级。
4. 计算每个故障模式的RPN。
5. 根据RPN的大小排序,确定优先处理的故障模式。
6. 提出相应的改进措施,降低高RPN值的故障模式的风险。
4. 总结FMEA评价标准使用RPN来量化和排序潜在故障模式的风险。
通过评估发生概率、严重性和检测能力等因素,可以识别潜在的高风险故障模式,并采取适当的措施进行缓解。
通过使用FMEA评价标准,可以提高系统的可靠性和性能,减少潜在的系统故障和质量问题的发生。
请注意:以上内容仅为参考,具体的FMEA评价标准应根据实际情况进行调整和应用。
FMEA评分准则
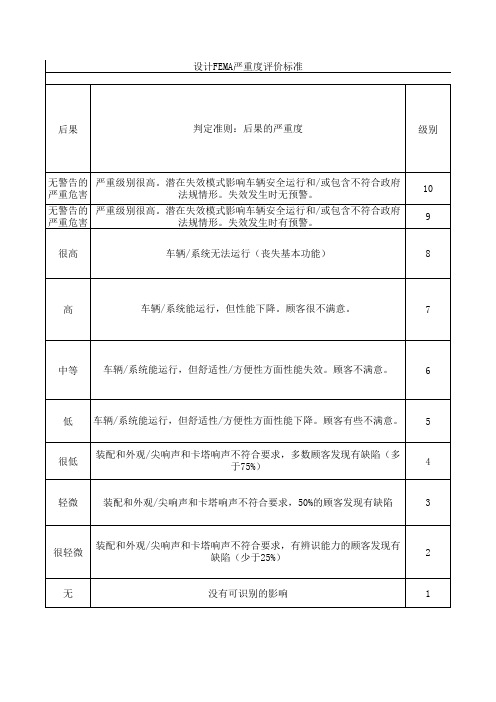
10 9 8 7 6 5
中上
设计控制有中上多的机会能找出潜在的起因/机理及后续的失效模式
4
多
设计控制有较多的机会能找出潜在的起因/机理及后续的失效模式
3
很多
设计控制有很多机会能找出潜在的起因/机理及后续的失效模式
2
几乎肯定
设计控制几乎肯定能找出潜在的起因/机理及后续的失效模式
1
后果
判定准则:后果的严重度 这级 别导致当一个潜在失效模式造成 了在最终顾客和/或制造/组装工 厂的缺陷。应该随时首先考虑到 最终顾客。如果放在两者都发生 缺陷,则采用较高一级的严重度 (顾客后果)
中上
现行控制方法有好 的机会去探测
× ×
高
现行控制方法有好 的机会去探测 现行控制方法几乎 确定可以探测
× ×
很高
× ×
几乎肯定
现行控制方法肯定 可以探测
×
该项目有过程/产品设计了防 错法,不会生产出缺陷零件
级别
10 9
8
7
6
5
4
3
2
1
级别
10 9 8 7 6 5
4
3
2
1
设计FEMA严重度评价标准
后果
判定准则:后果的严重度
级别
无警告的 严重级别很高。潜在失效模式影响车辆安全运行和/或包含不符合政府 法规情形。失效发生时无预警。 严重危害 无警告的 严重级别很高。潜在失效模式影响车辆安全运行和/或包含不符合政府 严重危害 法规情形。失效发生时有预警。 很高 车辆/系统无法运行(丧失基本功能)
判定准则:后果的严重度 这级别导致当一个潜在失效模 式造成了在最终顾客和/或制 造/组装工厂的缺陷。应该随 时首先考虑到最终顾客。如果 放在两者都发生缺陷,则采用 较高一级的严重度 (制造/组装后果) 或,可能危及作业员(机器或 组装)而无警告。 或,可能危及作业员(机器或 组装)但有警告。 或,产品可能必须要100%丢 弃,或车辆/系统要在修理部 门花上多于一小时来加以修理 或,产品可能必须要经过筛 选,且一部分(少于100%)被 丢弃,或车辆/系统要在修理 部门花上半小时到一小时来加 以修理 或,可能有一部分(少于 100%)的产品不经筛选地被丢 弃,或车辆/系统要在修理部 门花上少于半小时来加以修理 或,100%的产品需要重新加 工,或车辆/系统要下生产线 修理,但不用到修理部门。 或,产品可能必须要筛选,没 有被丢弃,但一部分(少于 100%)需要重新加工。 或车辆/系统要在修理部门花 上半小时到一小时来加以修 理,而没有别丢弃。 或车辆/系统要在修理部门花 上半小时到一小时来加以修 理,而没有别丢弃。 或,轻微的对作业或作业员不 方便,或没有影响。
fmea的评分标准
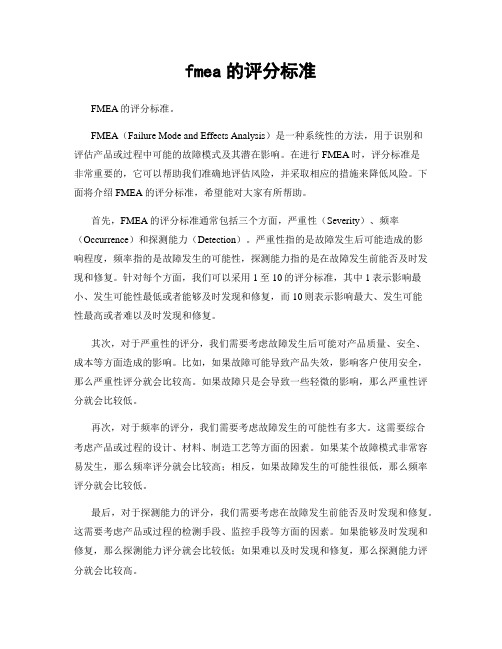
fmea的评分标准FMEA的评分标准。
FMEA(Failure Mode and Effects Analysis)是一种系统性的方法,用于识别和评估产品或过程中可能的故障模式及其潜在影响。
在进行FMEA时,评分标准是非常重要的,它可以帮助我们准确地评估风险,并采取相应的措施来降低风险。
下面将介绍FMEA的评分标准,希望能对大家有所帮助。
首先,FMEA的评分标准通常包括三个方面,严重性(Severity)、频率(Occurrence)和探测能力(Detection)。
严重性指的是故障发生后可能造成的影响程度,频率指的是故障发生的可能性,探测能力指的是在故障发生前能否及时发现和修复。
针对每个方面,我们可以采用1至10的评分标准,其中1表示影响最小、发生可能性最低或者能够及时发现和修复,而10则表示影响最大、发生可能性最高或者难以及时发现和修复。
其次,对于严重性的评分,我们需要考虑故障发生后可能对产品质量、安全、成本等方面造成的影响。
比如,如果故障可能导致产品失效,影响客户使用安全,那么严重性评分就会比较高。
如果故障只是会导致一些轻微的影响,那么严重性评分就会比较低。
再次,对于频率的评分,我们需要考虑故障发生的可能性有多大。
这需要综合考虑产品或过程的设计、材料、制造工艺等方面的因素。
如果某个故障模式非常容易发生,那么频率评分就会比较高;相反,如果故障发生的可能性很低,那么频率评分就会比较低。
最后,对于探测能力的评分,我们需要考虑在故障发生前能否及时发现和修复。
这需要考虑产品或过程的检测手段、监控手段等方面的因素。
如果能够及时发现和修复,那么探测能力评分就会比较低;如果难以及时发现和修复,那么探测能力评分就会比较高。
综上所述,FMEA的评分标准是非常重要的,它可以帮助我们全面地评估产品或过程中的风险,并采取相应的措施来降低风险。
在进行FMEA时,我们应该充分考虑严重性、频率和探测能力这三个方面,合理地评分,以便更好地指导我们的改进工作。
fmea评级标准及示例
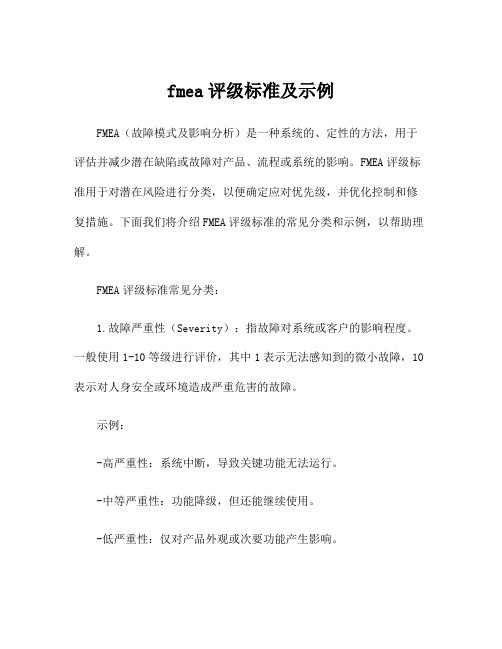
fmea评级标准及示例FMEA(故障模式及影响分析)是一种系统的、定性的方法,用于评估并减少潜在缺陷或故障对产品、流程或系统的影响。
FMEA评级标准用于对潜在风险进行分类,以便确定应对优先级,并优化控制和修复措施。
下面我们将介绍FMEA评级标准的常见分类和示例,以帮助理解。
FMEA评级标准常见分类:1.故障严重性(Severity):指故障对系统或客户的影响程度。
一般使用1-10等级进行评价,其中1表示无法感知到的微小故障,10表示对人身安全或环境造成严重危害的故障。
示例:-高严重性:系统中断,导致关键功能无法运行。
-中等严重性:功能降级,但还能继续使用。
-低严重性:仅对产品外观或次要功能产生影响。
2.故障发生频率(Occurrence):指故障发生的概率或频率。
一般使用1-10等级进行评价,其中1表示极不可能发生,10表示几乎可预见故障会发生。
示例:-高发生频率:故障很容易发生,几乎每次使用都会出现。
-中等发生频率:偶尔会发生故障,有一定概率。
-低发生频率:发生概率很低,极少出现故障。
3.故障探测能力(Detection):指故障被探测到的概率或能力。
一般使用1-10等级进行评价,其中1表示能够100%探测到,10表示几乎无法探测到。
示例:-高探测能力:故障很容易被发现或检测到。
-中等探测能力:故障有一定的概率被发现或检测到。
-低探测能力:故障很难被发现或检测到。
4.设计性评估(Design Control):指设计是否合理和完善,是否存在潜在的可改进点。
一般使用1-10等级进行评价,其中1表示设计已经非常完善,10表示设计存在严重问题。
示例:-高设计性评估:设计很完善,不存在明显的缺陷或改进点。
-中等设计性评估:设计存在些许缺陷或改进点,但不会对整体功能产生重大影响。
-低设计性评估:设计存在严重缺陷或改进点,会对整体功能产生重大影响。
FMEA评级标准还可以根据实际情况进行扩展,对特定领域或项目进行评估。
fmea探测度评分标准
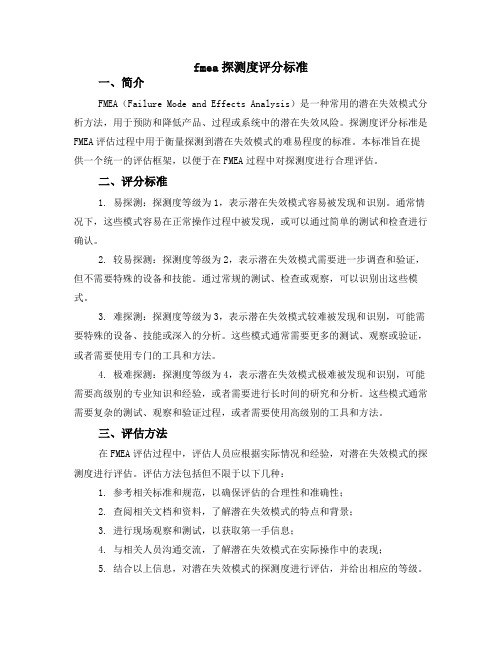
fmea探测度评分标准一、简介FMEA(Failure Mode and Effects Analysis)是一种常用的潜在失效模式分析方法,用于预防和降低产品、过程或系统中的潜在失效风险。
探测度评分标准是FMEA评估过程中用于衡量探测到潜在失效模式的难易程度的标准。
本标准旨在提供一个统一的评估框架,以便于在FMEA过程中对探测度进行合理评估。
二、评分标准1. 易探测:探测度等级为1,表示潜在失效模式容易被发现和识别。
通常情况下,这些模式容易在正常操作过程中被发现,或可以通过简单的测试和检查进行确认。
2. 较易探测:探测度等级为2,表示潜在失效模式需要进一步调查和验证,但不需要特殊的设备和技能。
通过常规的测试、检查或观察,可以识别出这些模式。
3. 难探测:探测度等级为3,表示潜在失效模式较难被发现和识别,可能需要特殊的设备、技能或深入的分析。
这些模式通常需要更多的测试、观察或验证,或者需要使用专门的工具和方法。
4. 极难探测:探测度等级为4,表示潜在失效模式极难被发现和识别,可能需要高级别的专业知识和经验,或者需要进行长时间的研究和分析。
这些模式通常需要复杂的测试、观察和验证过程,或者需要使用高级别的工具和方法。
三、评估方法在FMEA评估过程中,评估人员应根据实际情况和经验,对潜在失效模式的探测度进行评估。
评估方法包括但不限于以下几种:1. 参考相关标准和规范,以确保评估的合理性和准确性;2. 查阅相关文档和资料,了解潜在失效模式的特点和背景;3. 进行现场观察和测试,以获取第一手信息;4. 与相关人员沟通交流,了解潜在失效模式在实际操作中的表现;5. 结合以上信息,对潜在失效模式的探测度进行评估,并给出相应的等级。
四、应用范围本标准适用于各种产品、过程或系统的潜在失效模式评估,尤其适用于高风险领域(如航空、航天、医疗设备等)。
在评估过程中,应根据实际情况和具体要求,选择合适的探测度评分标准。
五、总结本标准提供了FMEA探测度评分标准的概述和评估方法,旨在提供一个统一的评估框架,以便于在FMEA过程中对探测度进行合理评估。
fmea评级标准及示例
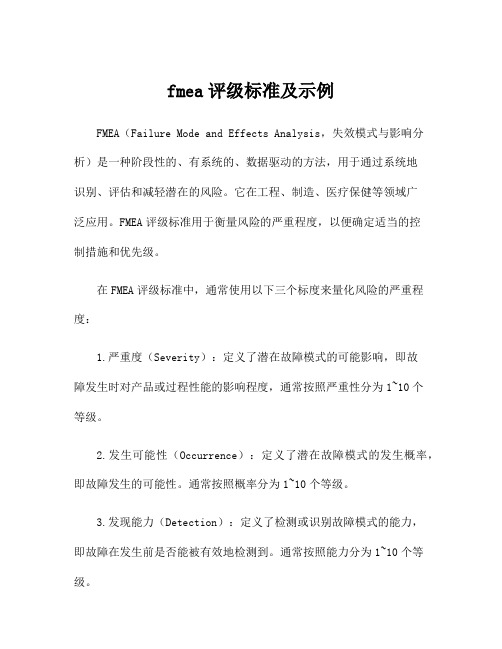
fmea评级标准及示例FMEA(Failure Mode and Effects Analysis,失效模式与影响分析)是一种阶段性的、有系统的、数据驱动的方法,用于通过系统地识别、评估和减轻潜在的风险。
它在工程、制造、医疗保健等领域广泛应用。
FMEA评级标准用于衡量风险的严重程度,以便确定适当的控制措施和优先级。
在FMEA评级标准中,通常使用以下三个标度来量化风险的严重程度:1.严重度(Severity):定义了潜在故障模式的可能影响,即故障发生时对产品或过程性能的影响程度,通常按照严重性分为1~10个等级。
2.发生可能性(Occurrence):定义了潜在故障模式的发生概率,即故障发生的可能性。
通常按照概率分为1~10个等级。
3.发现能力(Detection):定义了检测或识别故障模式的能力,即故障在发生前是否能被有效地检测到。
通常按照能力分为1~10个等级。
以上三个标度的乘积(Severity × Occurrence × Detection)被称为风险优先级数(Risk Priority Number,简称RPN)。
使用RPN可以对潜在故障模式进行优先级排序,从而确定需要采取的控制措施。
以下是一个关于汽车制造业的FMEA评级标准和示例:1.制动系统故障严重度:8发生可能性:5发现能力:7RPN:2802.气囊系统故障严重度:6发生可能性:4发现能力:8RPN:1923.发动机故障严重度:9发生可能性:6发现能力:6RPN:3244.转向系统故障严重度:7发生可能性:5发现能力:8RPN:280根据以上示例,可以看出不同故障模式的风险优先级,从而决定需要采取的控制措施。
比如,发动机故障的风险优先级最高,需要采取更严格的检测和控制措施。
而制动系统故障和转向系统故障的风险优先级较高,也需要采取相应的控制措施来降低风险。
FMEA评级标准可以根据不同行业和应用进行调整,以更好地适应特定的需求。
fmea评分标准
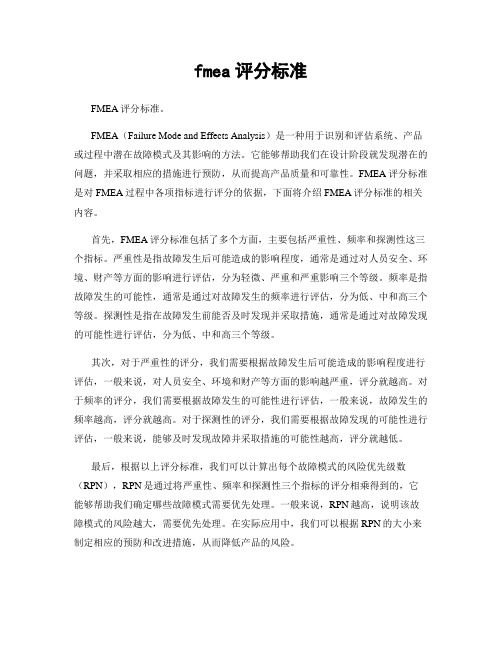
fmea评分标准FMEA评分标准。
FMEA(Failure Mode and Effects Analysis)是一种用于识别和评估系统、产品或过程中潜在故障模式及其影响的方法。
它能够帮助我们在设计阶段就发现潜在的问题,并采取相应的措施进行预防,从而提高产品质量和可靠性。
FMEA评分标准是对FMEA过程中各项指标进行评分的依据,下面将介绍FMEA评分标准的相关内容。
首先,FMEA评分标准包括了多个方面,主要包括严重性、频率和探测性这三个指标。
严重性是指故障发生后可能造成的影响程度,通常是通过对人员安全、环境、财产等方面的影响进行评估,分为轻微、严重和严重影响三个等级。
频率是指故障发生的可能性,通常是通过对故障发生的频率进行评估,分为低、中和高三个等级。
探测性是指在故障发生前能否及时发现并采取措施,通常是通过对故障发现的可能性进行评估,分为低、中和高三个等级。
其次,对于严重性的评分,我们需要根据故障发生后可能造成的影响程度进行评估,一般来说,对人员安全、环境和财产等方面的影响越严重,评分就越高。
对于频率的评分,我们需要根据故障发生的可能性进行评估,一般来说,故障发生的频率越高,评分就越高。
对于探测性的评分,我们需要根据故障发现的可能性进行评估,一般来说,能够及时发现故障并采取措施的可能性越高,评分就越低。
最后,根据以上评分标准,我们可以计算出每个故障模式的风险优先级数(RPN),RPN是通过将严重性、频率和探测性三个指标的评分相乘得到的,它能够帮助我们确定哪些故障模式需要优先处理。
一般来说,RPN越高,说明该故障模式的风险越大,需要优先处理。
在实际应用中,我们可以根据RPN的大小来制定相应的预防和改进措施,从而降低产品的风险。
总之,FMEA评分标准是FMEA过程中非常重要的一部分,它能够帮助我们对潜在的故障模式进行评估和优先处理,从而提高产品的质量和可靠性。
在实际应用中,我们需要根据实际情况对严重性、频率和探测性进行合理评分,并根据RPN的大小来制定相应的预防和改进措施,以确保产品的质量和可靠性达到预期的要求。
fmea评级标准及示例
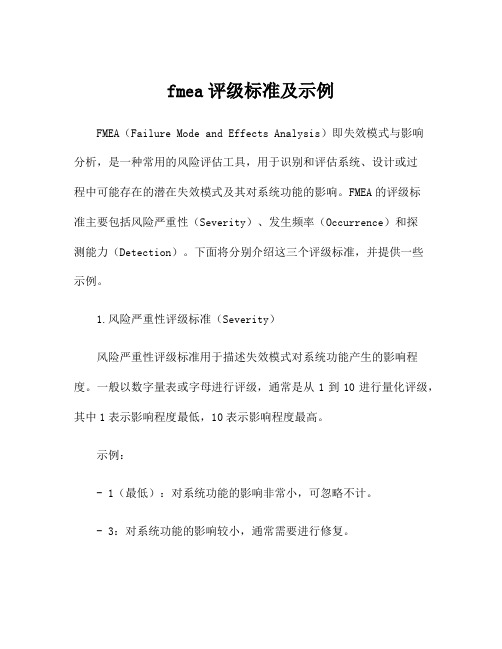
fmea评级标准及示例FMEA(Failure Mode and Effects Analysis)即失效模式与影响分析,是一种常用的风险评估工具,用于识别和评估系统、设计或过程中可能存在的潜在失效模式及其对系统功能的影响。
FMEA的评级标准主要包括风险严重性(Severity)、发生频率(Occurrence)和探测能力(Detection)。
下面将分别介绍这三个评级标准,并提供一些示例。
1.风险严重性评级标准(Severity)风险严重性评级标准用于描述失效模式对系统功能产生的影响程度。
一般以数字量表或字母进行评级,通常是从1到10进行量化评级,其中1表示影响程度最低,10表示影响程度最高。
示例:- 1(最低):对系统功能的影响非常小,可忽略不计。
- 3:对系统功能的影响较小,通常需要进行修复。
- 5:对系统功能的影响中等,可能导致系统的一部分功能无法正常工作。
- 8:对系统功能的影响较大,可能导致系统整体性能下降。
- 10(最高):对系统功能的影响非常严重,可能导致系统完全失效。
2.发生频率评级标准(Occurrence)发生频率评级标准用于描述失效模式的发生频率,即出现该失效模式的概率。
评级一般也采用1到10的量化评级,其中1表示非常低的发生频率,10表示非常高的发生频率。
示例:- 1(最低):失效模式的发生频率极低,非常罕见。
- 3:失效模式的发生频率较低,可能偶尔会发生。
- 5:失效模式的发生频率中等,有一定的风险。
- 8:失效模式的发生频率较高,可能会频繁发生。
- 10(最高):失效模式的发生频率非常高,几乎肯定会发生。
3.探测能力评级标准(Detection)探测能力评级标准用于描述系统中是否存在针对失效模式的有效探测手段以及探测的可靠程度。
评级同样采用1到10的量化评级,其中1表示探测能力非常强,10表示完全没有探测能力。
示例:- 1(最低):对失效模式有非常强的探测能力,几乎不会出现漏检。
FMEA评定标准
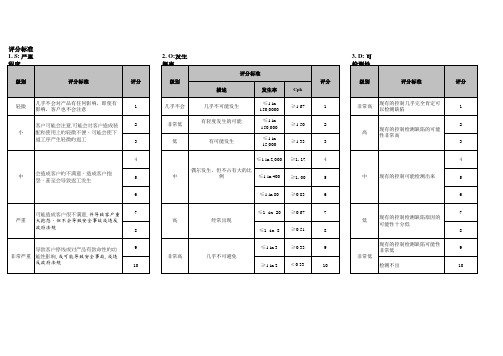
评分标准 1. S: 严重 程度
级别
评分标准
评分
轻微
几乎不会对产品有任何影响,即使有 影响,客户也不会注意
1
客户可能会注意,可能会对客户造成装
2
小 配和使用上的轻微不便。可能会使下
道工序产生轻微的返工
3
4
中
会造成客户的不满意,造成客户抱 怨,甚至会导致返工发生
5
6
可能造成客户很不满意,并导致客户重
7
评分
1 2 3 4 5 6 7 8 9 10
3. D: 可 检测性
级别
评分标准
评分
非常高
现有的控制几乎完全肯定可 以检测缺陷
1
2
高
现有的控制检测缺陷的可能 性非常高
3
4
中 现有的测缺陷原因的 可能性十分低
8
现有的控制检测缺陷可能性 非常低
9
非常低
检测不出
10
备注: 风 险指数 (RPN) = 严重程度 S*发生概 率O*可 检测性D
严重 大抱怨,但不会导致安全事故或违反
政府法规
8
导致客户停线或对产品有致命性的功
9
非常严重 能性影响,或可能导致安全事故,或违
反政府法规
10
2. O:发生 概率
级别
评分标准
描述
发生率
Cpk
几乎不会 非常低 低
几乎不可能发生 有轻度发生的可能
有可能发生
≤1 in 150,0000
≤1 in 150,000
≤1 in 15,000
≥1.67 ≥1.50 ≥1.33
潜在失效模式(FMEA)评分表[1]
![潜在失效模式(FMEA)评分表[1]](https://img.taocdn.com/s3/m/8a90e1669b6648d7c1c74647.png)
高
控制有较多机会
可探测出
X
X
在工位上的误差探测,或利用多层验收在后续工序上进行误差探测:供应、选择、安装、确认。不能接受有差异的零件。
3
很高
控制几乎肯定能
探动停机)。不能通过有差异的零件。
2
很高
肯定能探测出
X
由于有关项目已通过过程/产品设计采用了防错措施,有差异的零件不可能产出。
4
轻微
配合和外观/尖响和卡嗒项目不舒服。50%的顾客能发觉缺陷。
或部分(小于100%)产品可能需要返工,无需报废,在生产线上其它工位返工。
3
很轻微
配合和外观/尖响和卡嗒项目不舒服。有辨识力顾客(25%以下)能发觉缺陷。
或部分(小于100%)产品可能需要返工,无报废,在生产线上其它工位返工。
2
无
无可辨别的影响
或一部分(小于100%)产品可能需要报废,不需分检或者车辆/项目需在返修部门返修少于0.5小时
6
低
车辆/项目可运行但舒适性/便利性项目性能水平有所下降。
或100%的产品可能需要返工或者车辆/项目在线下返修,不需送往返修部门处理
5
很低
配合和外观/尖响和卡嗒项目不舒服。多数(75%以上)顾客能发觉缺陷
或产品可能需要分检,无需报废,但部分产品(小不100%)需返工。
会能探测出
X
只通过目测检查来实现控制
8
很小
控制有很少的机
会能探测出
X
只通过双重目测检查来实现控制
7
小
控制可能能探测
出
X
X
用制图的方法,如SPC(统计过程控制)来实现控制。
6
中等
控制可能能探测
fmea评级标准及示例
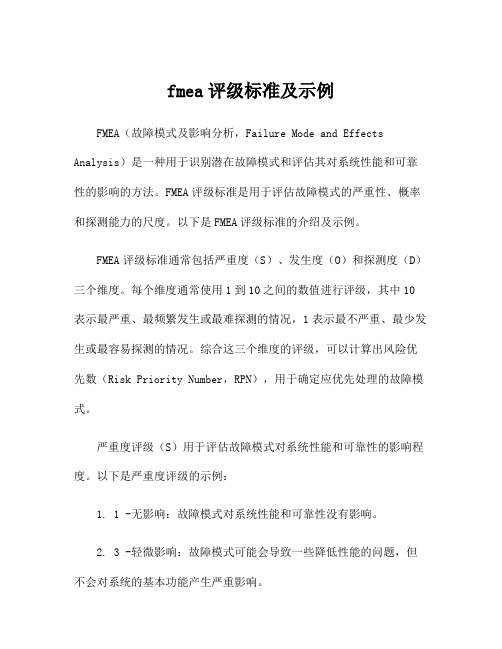
fmea评级标准及示例FMEA(故障模式及影响分析,Failure Mode and Effects Analysis)是一种用于识别潜在故障模式和评估其对系统性能和可靠性的影响的方法。
FMEA评级标准是用于评估故障模式的严重性、概率和探测能力的尺度。
以下是FMEA评级标准的介绍及示例。
FMEA评级标准通常包括严重度(S)、发生度(O)和探测度(D)三个维度。
每个维度通常使用1到10之间的数值进行评级,其中10表示最严重、最频繁发生或最难探测的情况,1表示最不严重、最少发生或最容易探测的情况。
综合这三个维度的评级,可以计算出风险优先数(Risk Priority Number,RPN),用于确定应优先处理的故障模式。
严重度评级(S)用于评估故障模式对系统性能和可靠性的影响程度。
以下是严重度评级的示例:1. 1 -无影响:故障模式对系统性能和可靠性没有影响。
2. 3 -轻微影响:故障模式可能会导致一些降低性能的问题,但不会对系统的基本功能产生严重影响。
3. 5 -一般影响:故障模式可能会导致系统的基本功能部分失效,但不会对整个系统产生破坏性影响。
4. 8 -严重影响:故障模式可能会导致系统完全失效或对系统性能和可靠性产生严重负面影响。
5. 10 -灾难性影响:故障模式可能会导致系统完全失效,对人身安全或环境产生严重威胁。
发生度评级(O)用于评估故障模式发生的频率或概率。
以下是发生度评级的示例:1. 1 -极低发生:故障模式非常罕见,发生的概率几乎可以忽略不计。
2. 3 -很低发生:故障模式发生的概率很低,但偶尔可能会发生。
3. 5 -一般发生:故障模式发生的概率在正常运行条件下可能会偶尔发生。
4. 8 -高发生:故障模式发生的概率相对较高,可能会在正常运行的条件下经常发生。
5. 10 -极高发生:故障模式发生的概率非常高,几乎可以肯定会在正常运行的条件下发生。
探测度评级(D)用于评估故障模式在发生后能够被及时探测和防止的能力。
fmea评级标准及示例
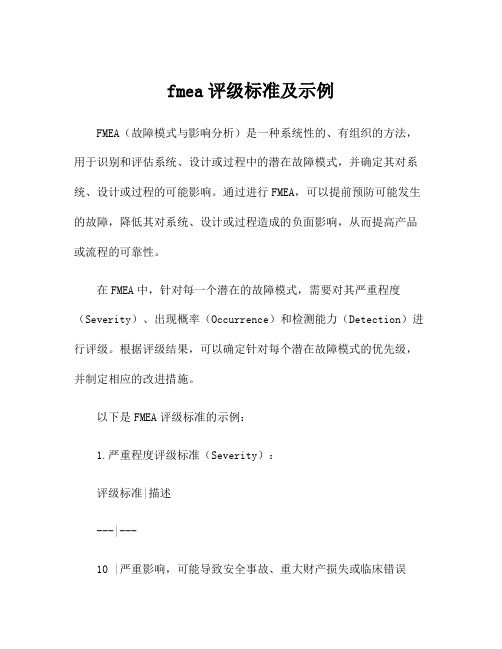
fmea评级标准及示例FMEA(故障模式与影响分析)是一种系统性的、有组织的方法,用于识别和评估系统、设计或过程中的潜在故障模式,并确定其对系统、设计或过程的可能影响。
通过进行FMEA,可以提前预防可能发生的故障,降低其对系统、设计或过程造成的负面影响,从而提高产品或流程的可靠性。
在FMEA中,针对每一个潜在的故障模式,需要对其严重程度(Severity)、出现概率(Occurrence)和检测能力(Detection)进行评级。
根据评级结果,可以确定针对每个潜在故障模式的优先级,并制定相应的改进措施。
以下是FMEA评级标准的示例:1.严重程度评级标准(Severity):评级标准|描述---|---10 |严重影响,可能导致安全事故、重大财产损失或临床错误8 |非常严重影响,可能导致可逆损坏、较大财产损失或潜在临床错误6 |严重影响,可能导致功能失效、财产损失或潜在临床错误4 |中等影响,可能导致功能降低、财产损失或潜在临床错误2 |轻微影响,可能导致不重要的财产损失或潜在临床错误2.出现概率评级标准(Occurrence):评级标准|描述---|---10 |概率极高,每次使用均会出现问题8 |概率较高,几乎每次使用都会出现问题6 |概率中等,偶尔会出现问题4 |概率较低,但还是有可能发生问题2 |概率极低,很少会出现问题3.检测能力评级标准(Detection):评级标准|描述---|---10 |可以完全检测到潜在故障模式8 |几乎可以全面检测到潜在故障模式6 |可以部分检测到潜在故障模式4 |检测能力有限,可能无法发现潜在故障模式2 |几乎无法检测到潜在故障模式通过将严重程度、出现概率和检测能力的评级综合计算,可以得到一个风险优先级数值(Risk Priority Number, RPN),用于确定改善措施的优先级顺序。
计算方式为RPN = Severity × Occurrence × Detection。
fmea 评分标准
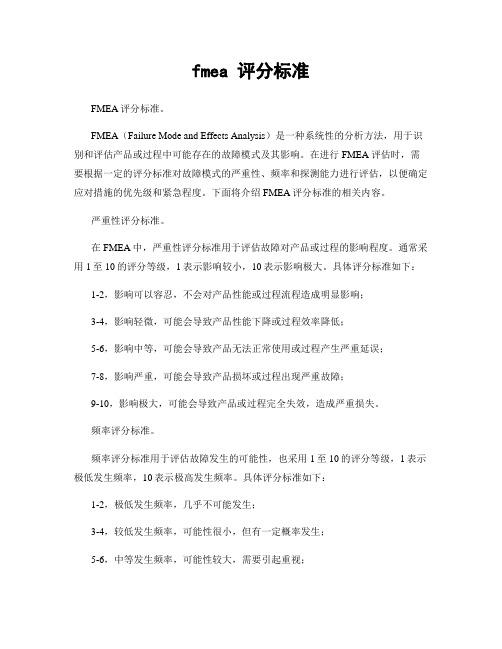
fmea 评分标准FMEA评分标准。
FMEA(Failure Mode and Effects Analysis)是一种系统性的分析方法,用于识别和评估产品或过程中可能存在的故障模式及其影响。
在进行FMEA评估时,需要根据一定的评分标准对故障模式的严重性、频率和探测能力进行评估,以便确定应对措施的优先级和紧急程度。
下面将介绍FMEA评分标准的相关内容。
严重性评分标准。
在FMEA中,严重性评分标准用于评估故障对产品或过程的影响程度。
通常采用1至10的评分等级,1表示影响较小,10表示影响极大。
具体评分标准如下:1-2,影响可以容忍,不会对产品性能或过程流程造成明显影响;3-4,影响轻微,可能会导致产品性能下降或过程效率降低;5-6,影响中等,可能会导致产品无法正常使用或过程产生严重延误;7-8,影响严重,可能会导致产品损坏或过程出现严重故障;9-10,影响极大,可能会导致产品或过程完全失效,造成严重损失。
频率评分标准。
频率评分标准用于评估故障发生的可能性,也采用1至10的评分等级,1表示极低发生频率,10表示极高发生频率。
具体评分标准如下:1-2,极低发生频率,几乎不可能发生;3-4,较低发生频率,可能性很小,但有一定概率发生;5-6,中等发生频率,可能性较大,需要引起重视;7-8,较高发生频率,经常会发生,需要立即采取措施;9-10,极高发生频率,几乎肯定会发生,需要立即采取紧急措施。
探测能力评分标准。
探测能力评分标准用于评估故障是否容易被检测到,也采用1至10的评分等级,1表示容易被检测到,10表示难以被检测到。
具体评分标准如下:1-2,容易被检测到,几乎可以立即发现;3-4,较容易被检测到,需要一定的检测手段才能发现;5-6,中等被检测到,需要较为复杂的检测手段才能发现;7-8,较难被检测到,需要专业的检测设备才能发现;9-10,难以被检测到,几乎不可能在事前发现,需要采取其他预防措施。
综合评分和优先级。
fmea评分标准
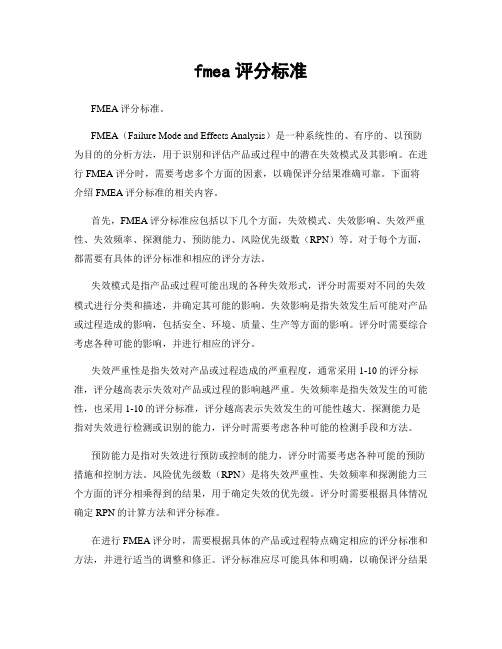
fmea评分标准FMEA评分标准。
FMEA(Failure Mode and Effects Analysis)是一种系统性的、有序的、以预防为目的的分析方法,用于识别和评估产品或过程中的潜在失效模式及其影响。
在进行FMEA评分时,需要考虑多个方面的因素,以确保评分结果准确可靠。
下面将介绍FMEA评分标准的相关内容。
首先,FMEA评分标准应包括以下几个方面,失效模式、失效影响、失效严重性、失效频率、探测能力、预防能力、风险优先级数(RPN)等。
对于每个方面,都需要有具体的评分标准和相应的评分方法。
失效模式是指产品或过程可能出现的各种失效形式,评分时需要对不同的失效模式进行分类和描述,并确定其可能的影响。
失效影响是指失效发生后可能对产品或过程造成的影响,包括安全、环境、质量、生产等方面的影响。
评分时需要综合考虑各种可能的影响,并进行相应的评分。
失效严重性是指失效对产品或过程造成的严重程度,通常采用1-10的评分标准,评分越高表示失效对产品或过程的影响越严重。
失效频率是指失效发生的可能性,也采用1-10的评分标准,评分越高表示失效发生的可能性越大。
探测能力是指对失效进行检测或识别的能力,评分时需要考虑各种可能的检测手段和方法。
预防能力是指对失效进行预防或控制的能力,评分时需要考虑各种可能的预防措施和控制方法。
风险优先级数(RPN)是将失效严重性、失效频率和探测能力三个方面的评分相乘得到的结果,用于确定失效的优先级。
评分时需要根据具体情况确定RPN的计算方法和评分标准。
在进行FMEA评分时,需要根据具体的产品或过程特点确定相应的评分标准和方法,并进行适当的调整和修正。
评分标准应尽可能具体和明确,以确保评分结果的准确性和可靠性。
同时,评分时需要充分考虑各种可能的情况和因素,以避免评分结果的主观性和片面性。
总之,FMEA评分标准是确保FMEA评分结果准确可靠的重要保障,需要综合考虑失效模式、失效影响、失效严重性、失效频率、探测能力、预防能力、风险优先级数等多个方面的因素,制定具体的评分标准和方法,并进行科学、客观、全面的评分分析,以确保评分结果的准确性和可靠性。
fmea打分标准对照表
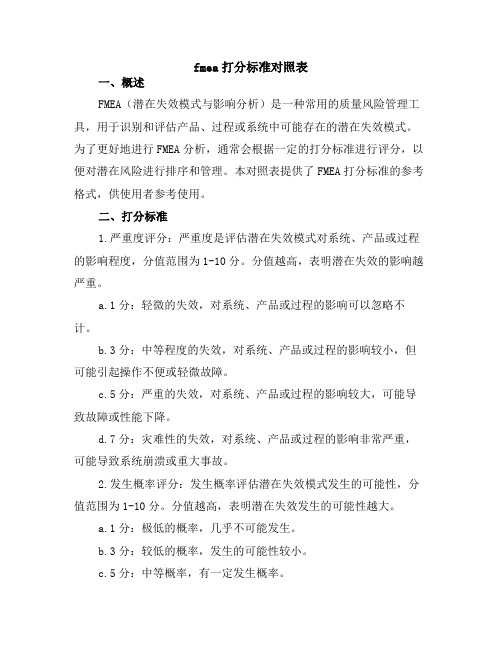
fmea打分标准对照表一、概述FMEA(潜在失效模式与影响分析)是一种常用的质量风险管理工具,用于识别和评估产品、过程或系统中可能存在的潜在失效模式。
为了更好地进行FMEA分析,通常会根据一定的打分标准进行评分,以便对潜在风险进行排序和管理。
本对照表提供了FMEA打分标准的参考格式,供使用者参考使用。
二、打分标准1.严重度评分:严重度是评估潜在失效模式对系统、产品或过程的影响程度,分值范围为1-10分。
分值越高,表明潜在失效的影响越严重。
a.1分:轻微的失效,对系统、产品或过程的影响可以忽略不计。
b.3分:中等程度的失效,对系统、产品或过程的影响较小,但可能引起操作不便或轻微故障。
c.5分:严重的失效,对系统、产品或过程的影响较大,可能导致故障或性能下降。
d.7分:灾难性的失效,对系统、产品或过程的影响非常严重,可能导致系统崩溃或重大事故。
2.发生概率评分:发生概率评估潜在失效模式发生的可能性,分值范围为1-10分。
分值越高,表明潜在失效发生的可能性越大。
a.1分:极低的概率,几乎不可能发生。
b.3分:较低的概率,发生的可能性较小。
c.5分:中等概率,有一定发生概率。
d.7分:较高的概率,发生概率较高。
e.9分:极高的概率,几乎一定会发生。
3.现有控制措施:现有控制措施是为了减少潜在失效发生概率或严重度而采取的措施,分值范围为0-5分。
分值越高,表明现有控制措施的效果越好。
a.0分:没有采取任何控制措施。
b.1-2分:部分控制措施,可能有一定的效果。
c.3-4分:多数控制措施,效果较好。
d.5分:全部控制措施,效果显著。
三、对照表使用方法1.根据潜在失效模式的具体情况,在相应的严重度、发生概率和现有控制措施的评分栏中填入对应分值。
2.将三个维度的分数相加,得到总分值。
总分值越高,表明潜在风险越大。
3.根据总分值对风险进行排序,优先处理高分值的潜在失效模式。
4.根据排序结果,采取相应的改进措施或加强现有控制措施,以降低潜在风险。
FMEA评分标准

可能的失效 ≥100个 每1000辆车/项目 50个 20个 每1000辆车/项目 每1000辆车/项目
7 高,经常 ≤1% Cpk≥0.86 6 中等偶然 ≤0.5% Cpk≥0.94 5 中等偶然 ≤0.2% Cpk≥1.0 4 中等偶然 ≤0.1% Cpk≥1.10 3 低,很少 ≤0.05% Cpk≥1.20 2 低,很少 ≤0.01% Cpk≥1.30
10个 5个 2个 1个 0.5个 0.1个
每1000辆车/项目
7 6 5 4 3 2 1 级低:失 效不太可 能发生 低:相对 很少发生 中等:偶 然性失效
10个 5个 2个 1个 0.5个 0.1个 ≤0.01个
每1000件 每1000件 每1000件 每1000件 每1000件 每1000件 每1000件
每1000辆车/项目 每1000辆车/项目 每1000辆车/项目 每1000辆车/项目 每1000辆车/项目 每1000辆车/项目
≤0.010个
1 极低,不太可能≤0.001%Cpk≥1.67
.推荐的DFMEA探测度评价准则 可探测度 D
10 几乎不可能 9 很微小 8 微小 7 很小 6 小 5 中等 4 中上
检查类别 B X X X X X X X C
几乎不可能 绝对肯定不可能探测 很微小 微小 很小 小 中等 控制方法可能探测不出来 控制有很少的机会能探测出 控制有很少的机会能探测出 控制可能能探测出 控制可能能探测出
设计控制有中等到的机会能找出潜在的起因 /机理及后续的失效模式 设计控制有中上多的机会能找出潜在的起因 /机理及后续的失效模式 设计控制有较多的机会能找出潜在的起因/ 机理及后续的失效模式 设计控制有很多的机会能找出潜在的起因/ 机理及后续的失效模式 设计控制几乎肯定能找出潜在的起因/机理 及后续的失效模式
fmea评分标准
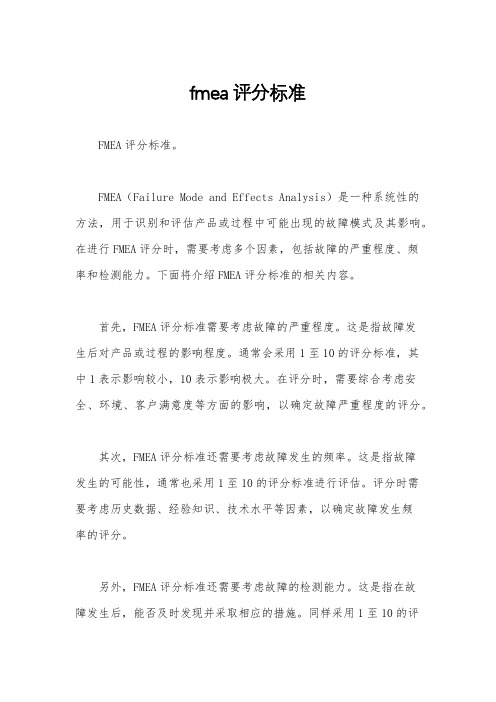
fmea评分标准FMEA评分标准。
FMEA(Failure Mode and Effects Analysis)是一种系统性的方法,用于识别和评估产品或过程中可能出现的故障模式及其影响。
在进行FMEA评分时,需要考虑多个因素,包括故障的严重程度、频率和检测能力。
下面将介绍FMEA评分标准的相关内容。
首先,FMEA评分标准需要考虑故障的严重程度。
这是指故障发生后对产品或过程的影响程度。
通常会采用1至10的评分标准,其中1表示影响较小,10表示影响极大。
在评分时,需要综合考虑安全、环境、客户满意度等方面的影响,以确定故障严重程度的评分。
其次,FMEA评分标准还需要考虑故障发生的频率。
这是指故障发生的可能性,通常也采用1至10的评分标准进行评估。
评分时需要考虑历史数据、经验知识、技术水平等因素,以确定故障发生频率的评分。
另外,FMEA评分标准还需要考虑故障的检测能力。
这是指在故障发生后,能否及时发现并采取相应的措施。
同样采用1至10的评分标准进行评估,评分时需要考虑检测手段的可靠性、有效性、及时性等因素,以确定故障检测能力的评分。
综合考虑上述三个方面的评分标准,可以得到FMEA综合评分。
通常采用以下公式进行计算,综合评分 = 严重程度评分× 频率评分× 检测能力评分。
根据综合评分的结果,可以确定故障的优先级,进而制定相应的改进措施和风险管理策略。
在进行FMEA评分时,需要注意以下几点,首先,评分标准需要根据具体的产品或过程进行调整,不能一概而论;其次,评分过程需要有明确的标准和流程,以确保评分结果的准确性和可靠性;最后,评分需要进行多轮讨论和确认,以充分考虑不同专业领域的意见和建议。
总之,FMEA评分标准是一个重要的工具,可以帮助企业识别和管理潜在的风险,提高产品质量和生产效率。
通过合理的评分标准和方法,可以有效地指导改进和优化工作,确保产品和过程的稳定性和可靠性。
因此,对FMEA评分标准的理解和应用具有重要意义,需要在实践中不断总结和完善,以适应不断变化的市场和技术需求。
- 1、下载文档前请自行甄别文档内容的完整性,平台不提供额外的编辑、内容补充、找答案等附加服务。
- 2、"仅部分预览"的文档,不可在线预览部分如存在完整性等问题,可反馈申请退款(可完整预览的文档不适用该条件!)。
- 3、如文档侵犯您的权益,请联系客服反馈,我们会尽快为您处理(人工客服工作时间:9:00-18:30)。
Product may have to be sorted, with no scrap and a portion (less than 100%) reworked 产品经过分检,无报废、部分须返工 (不到 100%)
Vehicle / item operable but at a reduced level of performance. Customer very dissatisfied 产品性能下降、客户非常不满
Vehicle / item operable but comfort / convenience items inoperable. Customer
final customer should always be considered first. If both occur, use the higher of the two
severities. 此评分因潜在缺陷模式导致最终客户和/或一种制 作/安装缺陷而产生。通常会首先考虑最终客户。
如果两者均有,采用其中较严重者。 (Customer Effect) (客户的后果)
or involves noncompliance with government regulation with warning
缺陷模式在有警告的情况下影响产品的安全操 作、在最终用户处引起功能上的问题 / 不符合政府条文 Vehicle / item inoperable (loss of primary function) 产品不可用(失去基本功能)
out-of-station 部分产品(不到 100%)需要返工,无报废
在生产线上原工序返工 Slight inconvenience to operation, no effect
轻微操作不便,无影响
Ranking 评分
10
9 8 7 6 5 4 3 2 1
FMEA Occurrence Evaluation Criteria FMEA 机率性评估参考标准
Suggested FMEA Detection Evaluation Criteria FMEA 检测性评估参考标准
Detection 检测性
Almost impossible 几乎不可能 Very remote
很微小
Remote 微小
Very low 很小
Low 小
Moderate 普通
Moderately high 较高
100% of product have to be scrapped, or repair time exceeds one hour
100%的产品可能需要报废或修理时间超过一小时 Product have to be sorted and a portion (less
than 100%) scrapped, or repaired time between one and half an hour
A portion (less than 100%) of the product may have to be reworked, with no scrap, on-line but
out-of-station 部分产品(不到 100%)需要返工,无报废
在生产线上其它工序返工
A portion (less than 100%) of the product may have to be reworked, with no scrap, on-line but
Failure is unlikely 缺陷基本不可能出现
Likely Failure Rates 可能出现的缺陷机率
(DPPM) ≥100 per thousand pieces
50 per thousand pieces 20 per thousand pieces 10 per thousand pieces 5 per thousand pieces 2 per thousand pieces 1 per thousand pieces 0.5 per thousand pieces 0.1 per thousand pieces
Suggested FMEA Severity Evaluation Criteria FMEA 严重性评估参考标准
Effect 后果
Hazardous without warning 无预兆性 危险
Hazardous with
warning 有预兆性
危险
Very high 非常严重
High 严重
Moderate 中等
≥1.67
Ranking 评分
10 9 8 7 6 5 4 3 2
1
缺陷机率简算:
1、假设抽检板数量共 58000 块,发现缺陷板数量 116 块; 2、计算缺陷板数量在总抽检板数量里所占比例: = 116÷58000 = 0.002,即 0.2%; 3、缺陷机率即缺陷的百万分率(DPPM)= 0.2%×100,0000 = 200; 4、核对机率性评估参考标准:缺陷机率 200 介于 100~500 之间,故机率性评分为 3 分;
×
×
×
×
×
×
×
×
×
×
×
Suggested range of detection methods
检测方法的建议范围
Cannot detect or is not checked 不能检测或没有检测
Control is achieved with indirect or random checks only
Controls almost certain to detect 控制几乎肯定能检
测出
Controls certain to detect
肯定能检测出
Inspection types 检测种类
Errorproofed
防错
Gauging 量具
Manual Inspection
人工(手动) 检测
×
×
×
Low 低
Very low 很低
Minor 轻微
Very minor 细微
None 无
Criteria: Severity of Effect 标准:后果严重性
This ranking results when a potential failure mode results in a final customer and/or a manufacturing/assembly plant defect. The
High 高
Very high 很高
Very high 极高
Criteria 标准
Absolute certainty of non-detection 绝对不能检测 Controls will
probably not detect 控制方法可能检测
不出 Controls have poor chance of detection 控制检测机会少 Controls have poor chance of detection 检测缺陷及防止漏
Level 级别
Probability 可能性
Very high 非常高
High 高
Persistent failures 缺陷持续不断
Frequent failures 缺陷频繁出现
Moderate 中等
Occasional failures 缺陷偶尔出现
Low 低
Remote 几乎不会
Relatively few failures 缺陷相对较少
(制作 / 装配后果)
May endanger operator (machine or assembly) without warning
无警告的情况下危害操作者 (机器或装配)
May endanger operator (machine or assembly) with warning
有警告的情况下危害操作者 (机器或装配)
(不到 25%)发现缺陷
No discernible effect 无辩别的影响
Criteria: Severity of Effect 标准:后果严重性
This ranking results when a potential failure mode results in a final customer and/or a manufacturing/assembly plant defect. The
≤0.01 per thousand pieces
以一百万块板 里的缺陷数计
(DPPM) 50000~100000 20000~50000 10000~20000
5000~10000 2000~5000 1000~2000 500~1000
100~500 10~100
1~10
Ppk
<0.55 ≥0.55 ≥0.78 ≥0.86 ≥0.94 ≥1.00 ≥1.10 ≥1.20 ≥1.30
Failure mode affects safe vehicle operation, cause some functional and reliable problems of
operation / or involves noncompliance with government regulation without warning
产品须分检且部分(非全部)需报废、 修理时间在半小时至一小时间
A portion (less than 100%) of the product have to scrapped with no sorting, repair time less than one hour 部分产品需报废,不需分检, 修理时间小于一小时