ADM6825YART-RL7中文资料
MEMORY存储芯片ADM3202ARUZ-REEL7中文规格书

READ OperationREAD bursts are initiated with a READ command. The starting column and bank ad-dresses are provided with the READ command and auto precharge is either enabled or disabled for that burst access. If auto precharge is enabled, the row being accessed is automatically precharged at the completion of the burst. If auto precharge is disabled,the row will be left open after the completion of the burst.During READ bursts, the valid data-out element from the starting column address is available READ latency (RL) clocks later. RL is defined as the sum of posted CAS additive latency (AL) and CAS latency (CL) (RL = AL + CL). The value of AL and CL is programma-ble in the mode register via the MRS command. Each subsequent data-out element is valid nominally at the next positive or negative clock edge (that is, at the next crossing of CK and CK#). Figure 69 shows an example of RL based on a CL setting of 8 and an AL setting of 0.Figure 69: READ LatencyCKCK#CommandAddressDQDQS, DQS#Don’t CareTransitioning Data Indicates break in time scaleNotes:1.DO n = data-out from column n .2.Subsequent elements of data-out appear in the programmed order following DO n .DQS, DQS# is driven by the DRAM along with the output data. The initial LOW state on DQS and HIGH state on DQS# is known as the READ preamble (t RPRE). The LOW state on DQS and the HIGH state on DQS#, coincident with the last data-out element, isknown as the READ postamble (t RPST). Upon completion of a burst, assuming no other commands have been initiated, the DQ goes High-Z. A detailed explanation of t DQSQ (valid data-out skew), t QH (data-out window hold), and the valid data window are de-picted in Figure 80 (page 171). A detailed explanation of t DQSCK (DQS transition skew to CK) is also depicted in Figure 80 (page 171).Data from any READ burst may be concatenated with data from a subsequent READ command to provide a continuous flow of data. The first data element from the new burst follows the last element of a completed burst. The new READ command should be issued t CCD cycles after the first READ command. This is shown for BL8 in Figure 70(page 165). If BC4 is enabled, t CCD must still be met, which will cause a gap in the data output, as shown in Figure 71 (page 165). Nonconsecutive READ data is reflected in Figure 72 (page 166). DDR3 SDRAM does not allow interrupting or truncating any READ burst.Figure 100: Precharge Power-Down (Slow-Exit Mode) Entry and ExitCKCK#CommandCKEEnter power-downmode Exit power-downmodeDon’t CareIndicates break in time scaleNotes:1.Any valid command not requiring a locked DLL.2.Any valid command requiring a locked DLL.Figure 101: Power-Down Entry After READ or READ with Auto Precharge (RDAP)Don’t CareTransitioning Data CKCK#Command DQ BL8DQ BC4DQS, DQS#Address CKEPower-down or self refresh entryIndicates break in time scaleFigure 102: Power-Down Entry After WRITECKCK#Command DQ BL8DQ BC4DQS, DQS#AddressCKEself refresh entry1Don’t CareTransitioning Data Indicates break in time scaleNote:1.CKE can go LOW 2t CK earlier if BC4MRS.Figure 103: Power-Down Entry After WRITE with Auto Precharge (WRAP)Don’t CareTransitioning Data CKCK#CommandDQ BL8DQ BC4DQS, DQS#Address A10CKEPower-down or self refresh entry 2Start internal precharge Indicates break in time scaleNotes:1.t WR is programmed through MR0[11:9] and represents t WRmin (ns)/t CK rounded up tothe next integer t CK.2.CKE can go LOW 2t CK earlier if BC4MRS.Figure 104: REFRESH to Power-Down EntryCKCK#CommandCKET0T1T2T3Ta0Ta1Ta2Tb0Don’t CareIndicates break in time scaleNote:1.After CKE goes HIGH during t RFC, CKE must remain HIGH until t RFC is satisfied.Figure 105: ACTIVATE to Power-Down EntryCKCK#Command Address CKET0T1T2T3T4T5T6T7Figure 108: Power-Down Exit to Refresh to Power-Down EntryCKCK#CKET0T1T2T3T4Ta0Ta1Tb0Command。
尼克萨里鸟控制产品说明书

Effective Installations Don't Just Happen...They Are Planned.Thorough planning,proper instal-lation,follow-up maintenance in the first weeks and periodic inspection of the mounting sys-tem,are the keys to a successful plan for Nixalite Bird Control.Always study the building carefully .Nixalite must be installed on all areas where birds alight,roost or build nests.All areas above,from which birds can drop nesting materials,as well as areas where birds can fly above the installation to drop materi-als,must be protected with Nixalite.Even though stainless steel has a very low rate of corrosion or reaction with other metals,it is still recommended to apply a protective coating or sealer on dissimilar metal surfaces before installing Nixalite to prevent any gal-vanic action.When installing Nixalite in small pieces or on a complicated surface,cut and fit each piece carefully .Be patient and thorough when applying Nixalite,being sure to cover all con-tours and angles closely .Do not jam the Nixalite together .Before deciding on the proper amount of Nixalite to be used,there are some specific figures to consider .Take time to establish the proper position and amount of the Nixalite by referring to the Surface Depth and charts on .Too much Nixalite can be as ineffective as too little."Space-i-fication"page 4All exposed edges,as well as the inte-rior of flat surfaces,must be covered.On inside corners,particularly cornice returns and similarly protected areas,it may be necessary to make a screen or special device with Nixalite to close off the protected area.In some areas,the Nixalite should be installed both on the surface and upside down on the surface directly above.Nixalite can be used on pipes,sup-ports and similar areas.It is also used as a deterrent for climbing ani-mals,rodents and humans.Clean the surface thoroughly with a disinfectant.The scent of bird drop-pings can encourage the birds to come back.Birds will fight hard to retain their old roosts.Before installing Nixalite remove all overhanging branches and similar foliage where birds can land to drop nesting materials.A free consultation service is pro-vided by our planning depart-ment.Submit drawings with exact measurements for recommendations.On site consultation is available by request.However ,there is a charge for this service.In cases where the accumulation ofQuestions About Y our Installation?Ph:800-624-1189or 309-755-8771Fax:800-624-1196or 309-755-0077E-mail:*********************Website:www For your protection ,wear goggles,gloves and a protective mask to help protect you against the health haz-ards associated with the bird debris.bird dung is heavy ,it may be neces-sary to use a bactericide to kill the dis-ease carrying bacteria.1.Carefully measure the depth and length of the surface,then refer to the Surface Depth Specification Charts page 4on for the number of rows needed.It is sometimes necessary to measure for height clearance when installing Nixalite in tight spaces.Proper placement and quantity of Nixalite starts with accurate mea-surements of the surface.Installing Nixalite StripsNOTE:Make sure the dimensionsyou record are accurate .Do not guess or estimate dimensions from a distance.Accurate dimensions are essential for an effective Nixalite installation.The Guide To Success121819gaw - new mhdBefore installing the Nixalite strips into the mounting hard-ware,there are some important guidelines that must be followed.2.Do not leave gaps in the Nixalite coverage.Cover all possible land-ing areas above,behind or next to the installation areas.1.Be sure the Nixalite strips will fit the area properly .The Nixalite base strip must follow the installa-tion surface closely .3.At the exposed ends of a surface ,run the strips over the ends.Make sure the of the strip is the or wire at all exposed surface ends.Make sure the strip wires extend at least over the outside edges.1/2"tallest wire first last 1/4"2.Mark where the Nixalite base strip will be positioned.To help you space the Nixalite on the surface correctly ,refer to the "Space-i-fications "chart on page 4.Steel or IronMounting Hardware InstructionsAll Nixalite mounting hardware is made of high grade stainless steel or weather resistant materials. If you have any questions or need more information, contact Nixalite or go to .4.Slip Nixalite base strip into mount-ing clips.3.Drive flush with hammer .MasonryWood &Sheet Metal4.Slip Nixalite base strip into mount-ing clips.1.Drill 11/64"diameter holes,at least 1/2"deep or through the steel.2.Blow out debris,insert anchors.3.Insert sheet metal screws through the mounting clips and drive flush into anchors with a screw driver .1.If necessary ,make small guide holes with a drill,punch,etc.2.Insert stainless steel sheet metal screw through the mounting clip and washer (in that order ,top to bottom).1.Drill 3/16”diameter holes,1"deep.4.Slip Nixalite base strip into mount-ing clips.Optional:Fill drilled holes with silicone sealer before installing hardware.This provides protection against water damage2.Insert stainless steel drive screws with mounting clips and washers (in that order ,top to bottom)into drilled holes.Fill drilled holes with silicone sealer before inserting anchors.This provides protection against water damage.Optional:Use the Mounting HardwareSpacing Chart on page 4to find the proper mounting hardware spacing.e a screw driver to drive screws,clips and washers flush to surface.The "hook"end of the mounting clip should point to the closest out-side edge of the surface.e the Mounting HardwareSpacing Chart on ,to deter-mine the proper mounting hard-ware spacing.Make a mark for each mounting hardware unit,or use an installation template.Call Nixalite for installation template details.page 43.Mounting hardware is installed 7/8"from Nixalite base strip.Mark the surface where the mounting hardware units are to be placed.MasonryWood/Sheet MetalNixalite Mounting Hardware UnitsQuestions About Y our Installation?Ph:800-624-1189 or 309-755-8771 Fax:800-624-1196 or 309-755-0077Wire Tie and Adhesive2.Apply adhesive to the bottom of the Nixalite base strip and to the installation surface.Recommended for fastening the Nixalite strips to suspended struc-tures,such as pipe,cables,etc.Follow the adhesive manufacturers direc-tions printed on the container .1.Clean the surface thoroughly ."Non-removable"Method1.Clean the surface thoroughly .2.By following manufacturers direc-tions printed on the adhesive con-tainer ,apply adhesive to surface where clips are to be attached.Put clips into the adhesive,making sure not to get any adhesive into the hook end of the clip.The clip hook should point to the closest out-side edge of the surface.3.Cover the eyelet end of the clip with adhesive.Make sure not to get adhesive into the hook end of the mounting clip.5.It is absolutely necessary to allow the adhesive holding the mounting clips to cure for at least 24hours before inserting the Nixalite strips.Removable MethodKeeping TabsWhen the use of supplied mounting hardware is not possible,a removable adhesive installation can be done.However ,it is recommended to use one mounting hardware unit at each end of the Nixalite strip to ensure solid mounting.1.Clean the surface thoroughly .2.By following manufacturers direc-tions printed on the adhesive con-tainer ,apply adhesive to surface where clips are to be attached.Put clips into this adhesive,making sure not to get any adhesive into the hook end of the clip.The hook end of clip should point toward the closest outside edge of the surface (see sketch #2at left).3.Cover the eyelet of the mounting clip with adhesive making sure not to get adhesive in the hook end of the clip (see sketch #3at left).4.It is absolutely necessary to allow the adhesive holding the mounting clips to cure for at least 24hours before inserting the Nixalite strips.By setting up a bi-annual visualinspection of the installation,you can keep an eye out for any debris that may get caught in the needles of the strips.Also inspect the mounting hard-ware system at this time.This allows re-securing the strips in the unlikely event that the strips have come loose from the hardware.Bear in mind that the birds may fight to retain their nesting and roosting places.Credit the birds for being cun-ning,persistent and tenacious.Sufficient Nixalite must be installed to do the job effectively .Careful observa-tion before the installation is neces-sary to locate all the problem areas.Remember that birds will try to drop sticks and other nesting materials into the Nixalite in an attempt to.....continued next pageIn Closing...3.Press the Nixalite strip into the sur-face adhesive.4.Wrap the wire tie around the strip and the suspended surface.Twist the loop ends with wire tying tool until tight.Space the wire ties in accordance with the Mounting Hardware Spacing Chart on page 4of this guideline.Adhesive Installation InstructionsWhen the use of supplied mounting hardware is not possible,an adhesive installation can be done.It is recom-mended to use one mounting hard-ware unit at each end of the Nixalite strip to ensure solid mounting.Always follow instructions printed on the adhesive container .4.After the adhesive holding the clips has cured,apply adhesive to the bottom of the Nixalite base strip and the installation surface.Slip the Nixalite strip into the mounting clips.For More Information or Planning AssistanceE-mail:*********************Careful thought and planning are required to make the installation suc-cessful.We can furnish the material,render it useless.That is why the areas above the installation must be pro-tected with Nixalite strips.but it must be installed with skill and ingenuity .Naturally ,since there are so many dif-ferent factors to be considered,we make no warranties,guarantees or representations,expressed or implied.Surface Depth Specification ChartsDetails to Remember:Nixalite "Space-i-fication" ChartsMounting Hardware Spacing Chart*½row indicates the use of Model H Nixalite.Whole number indicate the use of full row models S Nixalite.charts apply to .If using Model W ,review the Installing Model W Nixalite pages from Nixalite.Download this brochure from www or contact Nixalite for a free copy .NOTE:Model W Nixalite DO NOT A Always measure from the of the Nixalite base strip.center C1¾”(4.4cm)max.from the outsiderow .B5”(12.7cm)max.and 3½”(8.9cm)min.between two rows of Nixalite.2½”(6.4cm)max.and 2”(5.1cm)min.between models H and S Nixalite.E Extend Nixalite base strip at least ½”(1.3cm)over ends of surface.D 2¼”(5.7cm)max.from inside wall to the center of the inside row of Nixalite.FNixalite needles must extend over the outside edge at least ¼”(0.6cm).48"6units -one at each end,four spaced evenly between 16"2units -one at each end.Strip length Mounting Hardware Spacing12"2units -one at each end.24"3units -one at each end,one inmiddle Outside Corners &Exposed Edges:At outside corners,space the strips as shown below .At exposed ends,the tallest wire of the strip is always the first and/or last wire.Make sure there are no gaps where Nixalite strips meet walls or other objects,or where two Nixalite strips butt together end-to-end.Gaps:When two Nixalite strips are butted together in a row ,make sure the Nixalite wire pattern continues from one strip to the next strip.No gaps.Butting Strips:Single ExposedSurface DepthInchesCentimetersRows Required 8.5 - 13.50 - 3.53.5 - 5.55.5 - 8.513.5 - 18.518.5 - 23.523.5 - 28.528.5 - 33.533.5 - 38.538.5 - 43.534.3 - 47.00 - 8.98.9 - 14.014.0 - 21.621.6 - 34.372.4 - 81.597.8 - 110.547.0 - 59.759.7 - 72.481.5 - 97.8 3 rows 1 row 6 rows 7 rows 9 rows4 rows 8 rows 2 rows5 rows 1½ row*½ row*1 row 4 rows 2 rows 8 rows1½ rows 3 rows 6 rows 7 rows 5 rows 73.7 - 86.45.2 - 10.20 - 5.161.0 - 73.710.3 - 15.322.9 - 35.635.6 - 48.348.3 - 61.086.4 - 99.115.3 - 22.90 - 22 - 44 - 66 - 99 - 1414 - 1919 - 2429 - 3424 - 2934 - 39Double ExposedSurface DepthInchesCentimetersRows Required Need Help?U.S.\Canada - Ph:800-624-1189 Fax:800-624-1196E-mail Web :******************: Nixalite is open 8:00 a.m. to 4:30 p.m. Central Time,Monday through Friday . Fax or E-mail anytime.International - Ph:309-755-8771 Fax:309-755-0077Never use less than 2hardware units per strip,no matter how short the strip may be.Copyright© 2008 - 2019 by Nixalite® of America Inc. All rights reserved.Nixalite® is a registered trademark of Nixalite® of America Inc. Printed with pride in the .USA 1025 16th Avenue East Moline,. 61244IL Nixalite of America Inc®Experts In Architectural Bird Control Since 1950P_GuideToSuccess100219gaw .cdr - mhd new。
ADM6821TART-RL7资料

Low Voltage Supervisory Circuits withWatchdog & Manual Reset in 5-Lead SOT-23 Preliminary Technical Data ADM6821–ADM6825Rev.PrAInformation furnished by Analog Devices is believed to be accurate and reliable.However, no responsibility is assumed by Analog Devices for its use, nor for anyinfringements of patents or other rights of third parties that may result from its use. Specifications subject to change without notice. No license is granted by implication or otherwise under any patent or patent rights of Analog Devices. Trademarks and registered trademarks are the property of their respective companies.One Technology Way, P.O. Box 9106, Norwood, MA 02062-9106, U.S.A. Tel: Fax: 781.326.8703© 2004 Analog Devices, Inc. All rights reserved.FEATURESPrecision Low Voltage Monitoring down to 1.8V9 Reset Threshold Options:1.58V to 4.63V140ms (Min) Reset TimeoutWatchdog Timer with 1.6s TimeoutManual Reset InputReset Output StagesPush-Pull Active-LowOpen-Drain Active-LowPush-Pull Active-HighLow Power Consumption (3µA)Guaranteed Reset Output valid to V CC=1VPower Supply Glitch ImmunitySpecified from -40°C to +125°C5-Lead SOT-23 PackageAPPLICATIONSMicroprocessor SystemsComputersControllersIntelligent InstrumentsPortable EquipmentGENERAL DESCRIPTIONThe ADM6821-ADM6825 are supervisory circuits which monitor power supply voltage levels and code execution integrity in microprocessor-based systems. As well as providing power-on-reset signals, an on-chip watchdog timer can reset the microprocessor if it fails to strobe within a preset timeout period. A reset signal can also be asserted by means of an external push-button, through a manual reset input. The three parts feature different combinations of watchdog input, manual reset input and output stage configuration, as shown in table 1.FUNCTIONAL BLOCK DIAGRAMMRRESET VEach part is available in a choice of 9 reset threshold options ranging from 1.58V to 4.63V. The reset and watchdog timeout periods are fixed at 140ms (min) and 1.6s (typ), respectively. The ADM6821-ADM6825 are available in 5-lead SOT-23 packages and typically consume only 3µA, making them suitable for use in low power portable applications.Table 1. Selection TableADM6821–ADM6825 Preliminary Technical DataADM6821–ADM6825—SPECIFICATIONSTable 2. V CC=4. 5V to 5.5V for ADM682_L/M, V CC=2.7V to 3.6V for ADM682_T/S/R, V CC=2.1V to 2.75V for ADM682_Z/Y,V CC=1.53V to 2.0V for ADM682_W/V, T A=-40°C to +125°C, unless otherwise noted.Rev.PrA | Page 2 of 7Preliminary Technical DataADM6821–ADM6825Rev.PrA | Page 3 of 7ABSOLUTE MAXIMUM RATINGSTable 3. T A = 25°C unless otherwise noted.Stresses above those listed under Absolute Maximum Ratings may cause permanent damage to the device. This is a stress rating only and functional operation of the device at these or any other conditions above those indicated in the operational section of this specification is not implied. Exposure to absolute maximum rating conditions for extended periods may affect device reliability.ADM6821–ADM6825Preliminary Technical DataRev.PrA | Page 4 of 7PIN CONFIGURATIONS AND FUNCTIONAL DESCRIPTIONSV CCRESET GNDMRWDIV CC GND MRWDI V CC RESET GND RESETWDI V CCRESET GNDRESET MRTable 4. Pin Functional DescriptionsESD CAUTION`ESD (electrostatic discharge) sensitive device. Electrostatic charges as high as 4000 V readily accumulate on the human body and test equipment and can discharge without detection. Although this product features proprietary ESD protection circuitry, permanent damage may occur on devices subjected to high energy electrostatic discharges. Therefore, proper ESD precautions are recommended to avoid performance degradation or loss of functionality.Preliminary Technical DataADM6821–ADM6825Rev. PrA | Page 5 of 7ORDERING GUIDEModel Reset Threshold (V) Temperature Range Quantity Package Type Branding ADM6821LART-RL 4.63 -40°C to +125°C 10k SOT-23-5 N0A ADM6821LART-RL7 4.63 -40°C to +125°C 3k SOT-23-5 N0A ADM6821MART-RL 4.38 -40°C to +125°C 10k SOT-23-5 N0A ADM6821MART-RL7 4.38 -40°C to +125°C 3k SOT-23-5 N0A ADM6821TART-RL 3.08 -40°C to +125°C 10k SOT-23-5 N0A ADM6821TART-RL7 3.08 -40°C to +125°C 3k SOT-23-5 N0A ADM6821SART-RL 2.93 -40°C to +125°C 10k SOT-23-5 N0A ADM6821SART-RL7 2.93 -40°C to +125°C 3k SOT-23-5 N0A ADM6821RART-RL 2.63 -40°C to +125°C 10k SOT-23-5 N0A ADM6821RART-RL7 2.63 -40°C to +125°C 3k SOT-23-5 N0A ADM6821ZART-RL 2.32 -40°C to +125°C 10k SOT-23-5 N0A ADM6821ZART-RL7 2.32 -40°C to +125°C 3k SOT-23-5 N0A ADM6821YART-R L 2.19 -40°C to +125°C 10k SOT-23-5 N0A ADM6821YART-R L 7 2.19 -40°C to +125°C 3k SOT-23-5 N0A ADM6821WART-RL 1.67 -40°C to +125°C 10k SOT-23-5 N0A ADM6821WART-RL7 1.67 -40°C to +125°C 3k SOT-23-5 N0A ADM6821VART-RL 1.58 -40°C to +125°C 10k SOT-23-5 N0A ADM6821VART-RL7 1.58 -40°C to +125°C 3k SOT-23-5 N0A ADM6822LART-RL 4.63 -40°C to +125°C 10k SOT-23-5 N0B ADM6822LART-RL7 4.63 -40°C to +125°C 3k SOT-23-5 N0B ADM6822MART-RL 4.38 -40°C to +125°C 10k SOT-23-5 N0B ADM6822MART-RL7 4.38 -40°C to +125°C 3k SOT-23-5 N0B ADM6822TART-RL 3.08 -40°C to +125°C 10k SOT-23-5 N0B ADM6822TART-RL7 3.08 -40°C to +125°C 3k SOT-23-5 N0B ADM6822SART-RL 2.93 -40°C to +125°C 10k SOT-23-5 N0B ADM6822SART-RL7 2.93 -40°C to +125°C 3k SOT-23-5 N0B ADM6822RART-RL 2.63 -40°C to +125°C 10k SOT-23-5 N0B ADM6822RART-RL7 2.63 -40°C to +125°C 3k SOT-23-5 N0B ADM6822ZART-RL 2.32 -40°C to +125°C 10k SOT-23-5 N0B ADM6822ZART-RL7 2.32 -40°C to +125°C 3k SOT-23-5 N0B ADM6822YART-RL 2.19 -40°C to +125°C 10k SOT-23-5 N0B ADM6822YART-RL7 2.19 -40°C to +125°C 3k SOT-23-5 N0B ADM6822WART-RL 1.67 -40°C to +125°C 10k SOT-23-5 N0B ADM6822WART-RL7 1.67 -40°C to +125°C 3k SOT-23-5 N0B ADM6822VART-RL 1.58 -40°C to +125°C 10k SOT-23-5 N0B ADM6822VART-RL7 1.58 -40°C to +125°C 3k SOT-23-5 N0B ADM6823LART-RL 4.63 -40°C to +125°C 10k SOT-23-5 N0C ADM6823LART-RL7 4.63 -40°C to +125°C 3k SOT-23-5 N0C ADM6823MART-RL 4.38 -40°C to +125°C 10k SOT-23-5 N0C ADM6823MART-RL7 4.38 -40°C to +125°C 3k SOT-23-5 N0C ADM6823TART-RL 3.08 -40°C to +125°C 10k SOT-23-5 N0C ADM6823TART-RL7 3.08 -40°C to +125°C 3k SOT-23-5 N0C ADM6823SART-RL 2.93 -40°C to +125°C 10k SOT-23-5 N0C ADM6823SART-RL7 2.93 -40°C to +125°C 3k SOT-23-5 N0C ADM6823RART-RL 2.63 -40°C to +125°C 10k SOT-23-5 N0C ADM6823RART-RL7 2.63 -40°C to +125°C 3k SOT-23-5 N0C ADM6823ZART-RL 2.32 -40°C to +125°C 10k SOT-23-5 N0C ADM6823ZART-RL7 2.32 -40°C to +125°C 3k SOT-23-5 N0C ADM6823YART-R L2.19 -40°C to +125°C 10k SOT-23-5 N0C ADM6823YART-R L 7 2.19 -40°C to +125°C 3kSOT-23-5N0CADM6821–ADM6825Preliminary Technical DataRev.PrA | Page 6 of 7ORDERING GUIDE (CONTD.)Model Reset Threshold (V) Temperature Range Quantity Package Type Branding ADM6823WART-RL 1.67 -40°C to +125°C 10k SOT-23-5 N0C ADM6823WART-RL7 1.67 -40°C to +125°C 3k SOT-23-5 N0C ADM6823VART-RL 1.58 -40°C to +125°C 10k SOT-23-5 N0C ADM6823VART-RL7 1.58 -40°C to +125°C 3k SOT-23-5 N0C ADM6824LART-RL 4.63 -40°C to +125°C 10k SOT-23-5 N0D ADM6824LART-RL7 4.63 -40°C to +125°C 3k SOT-23-5 N0D ADM6824MART-RL 4.38 -40°C to +125°C 10k SOT-23-5 N0D ADM6824MART-RL7 4.38 -40°C to +125°C 3k SOT-23-5 N0D ADM6824TART-RL 3.08 -40°C to +125°C 10k SOT-23-5 N0D ADM6824TART-RL7 3.08 -40°C to +125°C 3k SOT-23-5 N0D ADM6824SART-RL 2.93 -40°C to +125°C 10k SOT-23-5 N0D ADM6824SART-RL7 2.93 -40°C to +125°C 3k SOT-23-5 N0D ADM6824RART-RL 2.63 -40°C to +125°C 10k SOT-23-5 N0D ADM6824RART-RL7 2.63 -40°C to +125°C 3k SOT-23-5 N0D ADM6824ZART-RL 2.32 -40°C to +125°C 10k SOT-23-5 N0D ADM6824ZART-RL7 2.32 -40°C to +125°C 3k SOT-23-5 N0D ADM6824YART-R L 2.19 -40°C to +125°C 10k SOT-23-5 N0D ADM6824YART-R L 7 2.19 -40°C to +125°C 3k SOT-23-5 N0D ADM6824WART-RL 1.67 -40°C to +125°C 10k SOT-23-5 N0D ADM6824WART-RL7 1.67 -40°C to +125°C 3k SOT-23-5 N0D ADM6824VART-RL 1.58 -40°C to +125°C 10k SOT-23-5 N0D ADM6824VART-RL7 1.58 -40°C to +125°C 3k SOT-23-5 N0D ADM6825LART-RL 4.63 -40°C to +125°C 10k SOT-23-5 N0E ADM6825LART-RL7 4.63 -40°C to +125°C 3k SOT-23-5 N0E ADM6825MART-RL 4.38 -40°C to +125°C 10k SOT-23-5 N0E ADM6825MART-RL7 4.38 -40°C to +125°C 3k SOT-23-5 N0E ADM6825TART-RL 3.08 -40°C to +125°C 10k SOT-23-5 N0E ADM6825TART-RL7 3.08 -40°C to +125°C 3k SOT-23-5 N0E ADM6825SART-RL 2.93 -40°C to +125°C 10k SOT-23-5 N0E ADM6825SART-RL7 2.93 -40°C to +125°C 3k SOT-23-5 N0E ADM6825RART-RL 2.63 -40°C to +125°C 10k SOT-23-5 N0E ADM6825RART-RL7 2.63 -40°C to +125°C 3k SOT-23-5 N0E ADM6825ZART-RL 2.32 -40°C to +125°C 10k SOT-23-5 N0E ADM6825ZART-RL7 2.32 -40°C to +125°C 3k SOT-23-5 N0E ADM6825YART-R L 2.19 -40°C to +125°C 10k SOT-23-5 N0E ADM6825YART-R L 7 2.19 -40°C to +125°C 3k SOT-23-5 N0E ADM6825WART-RL 1.67 -40°C to +125°C 10k SOT-23-5 N0E ADM6825WART-RL7 1.67 -40°C to +125°C 3k SOT-23-5 N0E ADM6825VART-RL 1.58 -40°C to +125°C 10k SOT-23-5 N0E ADM6825VART-RL7 1.58 -40°C to +125°C 3kSOT-23-5N0EPreliminary Technical DataADM6821–ADM6825Rev. PrA | Page 7 of 7OUTLINE DIMENSIONS0.3PLANECOMPLIANT TO JEDEC STANDARDS MO-178AAFigure 1. 5-Lead Small Outline Transistor Package [SOT-23](RT-5)Dimensions shown in millimeters© 2004 Analog Devices, Inc. All rights reserved. Trademarks and registered trademarks are the property of their respective companies. Printed in the U.S.A.。
[机械仪表]API682中文
![[机械仪表]API682中文](https://img.taocdn.com/s3/m/34488bf75ff7ba0d4a7302768e9951e79b8969a2.png)
(3) C 型密封 内装、平衡、集装式金属波纹管机械密封。标准密封的弹性元件为静止 式,辅助密封元件为柔性石墨。
1
API 标准 682
A 型、B 型密封的最高工作温度为 176℃(350℉),通过数据表可以选择静止式密封;C 型密封的最高工作温度为 400℃(750℉),通过数据表可以选择旋转式密封。
(2) 背对背: 双密封 两组弹性元件位于两组摩擦副之间; (3) 面对面: 双密封 两组摩擦副位于两组弹性元件之间。
1.3 密封性能要求
符合本标准的密封应达到下列性能要求:
(1) 所有密封连续运行寿命不低于 25000 小时; (2) 抑制密封在抑制密封腔的压力不高于压力开关设定的泄漏压力值【表压≤0.7bar
3.4 布置方式 3 密封
集装式双密封,阻塞流体由外部供给。
3.5 背对背结构
双密封,两组弹性元件位于两组摩擦副之间
11
API 标准 682
3.6 平衡型密封
载荷系数小于 1 的机械密封
3.7 阻塞流体
外部提供的流体,其压力大于泵的密封腔压力,用于布置方式 3 密封,使泵送液与环境 完全隔离
3.8 波纹管密封
注:图 1 所示为密封结构方框图,图中列出了所有密封型式,由图可以对各种密封型式 进行全面了解。
1.2 密封的类别、型式和布置方式
密封可以分为以下三大类别:
(1) 第 1 类密封 用于 ISO 13709 以外的密封腔,主要适用于 ANSI/ASME B73.1、 ANSI/ASME B73.2 和 ISO 3069 C 型密封腔。其工作条件为:密封腔内温度在–40 ℃(–40℉)和 260℃(500℉)之间,绝对压力可达到 22 巴(315psi【磅/英尺 2】)。
亚特兰蒂克MWR系列电动锥头驱动系统说明书

CA D BThe mechatronic systemAA Thanks to a standard drive (9x12 and14x18) , the operator can always find theperfect end fitting for his application.B Operator can always know if a wrench isready to work, and if the tightening wascorrect, by looking at the onboard LEDs.C Thanks to the wireless connection theoperator is free to move around and toaccess bolt location.D The charging cradle is a stable holderand a battery charger, making sure thatthe tools are always ready to perform theirtasks. Shift after shift.E Detailed tightening information isimmediately available on the Focus 60and 61 display.F Tightening data from MWR wrenchesare easily transferred to productiondata collection systems like T oolsNet.Communicating either with the simpleprotocol or with the Atlas Copco OpenProtocol.G With a barcode reader connected to theFocus controller, operator scans an IDnumber and the right job is selected. Alltightening data will automatically includethe scanned ID number.H Intuitive “just a few clicks away” interface.I Production stations can easily implement areal-time feedback in a Live monitor usingTT BLM software.IFEGHMorethan a click!Increase the quality of your joints considerably with the error proofing functionalities of the MWR mechatronic system. Combining the productivity of a click wrench with the traceability of an electronic one, this smart manual fastening system for tightening processes is a good investment. Using the smallest version of this high productive wrench you are able to get access to joints inaccessible for a standard tool. T he online results provide a complete traceability of the tightening process.A b l u e L E D s i g n a l o n t h e w r e n ch g u i d e s t h e o p e r a t o re a s i l y t h r o u g h t h e t i g h t e nin g p r o c e s s .MWR -50MWR wrenchBased on the mechanical “click” wrench, the MWR mechatronic wrench is highly productive. T he clear physical feedback of the “click” makes it easy to handle even for untrained workers, giving you a very short training period.Feedback of the tightening process is clearwith the distinctive “click” of the MWRmechanism in combination with the colored LEDs. If needed the MWR mechatronic system can be completed with the stack lights connected to the Focus controller.Size and performancemakes the MWR wrenches optimal for limited space applications. With all functionalities in a compact size.ProductivityFeedbackSizeM W R -25 (1:1s c a le )MWR-85Feature Focus 60Focus 61 Number of workstations12 Number of wrenches110 Communication Simple Open Protocol Barcode••ToolsNet••Atlas Copco I/O Bus••The MWR-TA measures torque and angle values, reporting problems immediately. Wrong screws or damaged threads are history! Any re-hit is detected making you 100% sure that all the screws in a sequence are properly tightened.T orque and angleThe MWR-S supports batch counting systemsin the production line by transmitting an OK signal. The MWR-S increases ergonomy aspects during tightening processes compared to a Clickwrench with a Microswitch because the signal is transmitted wireless.SwitchThe MWR-T is measuring torque during the entire tightening process. Depending on the limits, the peak value gives the OK/NOK status. Giving you the real torque applied on the joint.T orqueSmart clickThroughout a tightening, the MWR wrench will monitor three important processparameters,, depending on the choosen model. It measures if the right torque is applied, the correct angle is archievedand if the operator releases the tightening at the correct time .The standard software for programming the mechatronic system – T TBLM – enables the planning engineer to set up all the joint, batch and job settings for Focus 60 and 61. You can get a list of all the available Focus 60/61controllers via LAN/Ethernet and get connected to anyone of them to administrate your application from the office.TTBLM offers you a complete overview about the status of each MWR wrench in your plant like battery level, calibration and availability. T he live monitor can display online results from the wrench highlighting status by colors.T ools talk BLMEnd fittingsOpen endOrdering No. 4027 5012 30 4027 5012 31BBHMaß der SchlüsselweiteOpen End with Ratchet function 14x18Connectors for dovetail insertsT ype T orque range Drive Weight kg Length mm Nm ft lb MWR-25 S 5-25 3.7-18.49x120.4461778439 0044 00MWR-50 S 10-507.4-36.99x120.5652348439 0044 01MWR-85 S 17-8512.5-62.79x120.6303078439 0044 02MWR-200 S 40-20029.5-147.514x180.8514198439 0044 03MWR-300 S 60-30044.2-221.214x18 2.58988439 0044 04MWR-25 T 5-25 3.7-18.49x120.4461778439 0044 10MWR-50 T 10-507.4-36.99x120.5652348439 0044 11MWR-85 T 17-8512.5-62.79x120.6303078439 0044 12MWR-200 T 40-20029.5-147.514x180.8514198439 0044 13MWR-300 T 60-30044.2-221.214x18 2.58988439 0044 14MWR-25 T A 5-25 3.7-18.49x120.4461778439 0044 20MWR-50 T A 10-507.4-36.99x120.5652348439 0044 21MWR-85 T A 17-8512.5-62.79x120.6303078439 0044 22MWR-200 T A 40-20029.5-147.514x180.8514198439 0044 23MWR-300 T A60-30044.2-221.214x182.58988439 0044 24Controller Ordering No.Focus 608439 0044 30Focus 618439 0044 31Number of workstations 12Number of administrable MWR 110Wireless wrench communication ••Communication Standard••Communication Open Protocol •Toolsnet communication••TTBLM communication ••Possibility to add protocols •LAN/Ethernet communication ••LAN/Ethernet programming ••Job programming •Batch programming ••Results storage 25.00025.000Languages: English - German ••Multi-unit ••Display ••BNC Antenna••LAN/Ethernet Interface 12Barcode interface ••Accessory-BUS ••Weight (kg)2.52.5Dimensions (mm)147x219x121147x219x121Mechatronic W renchMWR - S MW R - T MW R - TA 4 colored status LED on 3 sides of the wrench•••Tightening time•••Torque measuring••Angle measuring•Doubleclick detection (same screw)••Rehit detection•Observing tightening direction ••Displaying online status •••End fitting length adjustable ••Standard drive (9x12 / 14x18) for different end fittings •••Wireless 868/910 MHz range •••Low power management •••Battery status signalization •••Software Ordering No.TTBLM 1 User License 8059 0981 105 User License 8059 0981 1110 User License 8059 0981 12Plant License8050 0981 13Wrench protection capsOrdering No.MWR protection cap 5PCS (blue) 4027 5022 20MWR protection cap 5PCS (green) 4027 5022 21MWR protection cap 5PCS (red) 4027 5022 22MWR protection cap 5PCS (Colormix) 4027 5022 23MWR protection cap 5PCS (gold) 4027 5022 24MWR protection cap 5PCS (black)4027 5022 25AccessoriesOrdering No.Charging Cradle MWR4027 5022 10Charging Cradle MWR Clips (HD)4027 5026 14MWR Protection Cover 4027 5026 28Setting key MWR/CWR4027 5013 96Recharg. battery NIMH AAA MWR 1.2 V, 1000 mAh4027 5021 01Stacklight ESL -04 Standard 8433 0570 13IO Expander (sealed)8433 0564 45Focus 60/61 Dig. Out Connector 4027 5022 04Antennas Antenna 868 MHz 4027 5022 13Antenna915 MHz 4027 5022 14Cable-Antenna, 2,5 m 868/915 MHz 4027 5022 15Extended Cable-Antenna, 5 m 868/915 MHz 4027 5020 95Cables I/O bus cable 0.5 m 4222 0917 00I/O bus cable 1 m 4222 0917 01I/O bus cable 3 m 4222 0917 03I/O bus cable 5 m 4222 0917 05I/O bus cable 10 m 4222 0917 10I/O bus cable 15 m 4222 0917 15I/O T ermination plug 4222 0443 00Ethernet straight 0.5 m 4222 0754 00Ethernet straight 1 m 4222 0754 01Ethernet straight 3 m 4222 0754 03Ethernet straight 5 m 4222 0754 05Ethernet straight 10 m 4222 0754 10Ethernet straight 15 m 4222 0754 15Ethernet straight 25 m 4222 0754 25Ethernet straight50 m 4222 0754 509833 2017 01 – E N © A t l a s C o p c o B L M , M i l 2019Atlas Copco BLM Milan, Italy 。
ADUM1201ARZ-RL7中文资料

3 ns maximum channel-to-channel matching High common-mode transient immunity: > 25 kV/µs Safety and regulatory approvals
UL recognition 2500 V rms for 1 minute per UL 1577
APPLICATIONS
The ADuM120x isolators provide two independent isolation channels in a variety of channel configurations and data rates (see the Ordering Guide). Both parts operate with the supply voltage on either side ranging from 2.7 V to 5.5 V, providing compatibility with lower voltage systems as well as enabling a voltage translation functionality across the isolation barrier. In addition, the ADuM120x provide low pulse-width distortion (< 3 ns for CR grade) and tight channel-to-channel matching (< 3 ns for CR grade). Unlike other optocoupler alternatives, the ADuM120x isolators have a patented refresh feature that ensures dc correctness in the absence of input logic transitions
艾茨顿电动机驱动器产品介绍说明书

/drives 1-877-386-2273, option2, option
Drive selector switch Start stop pushbuttons HOA selector switch Drive run and fault lights External fault light Keypad for each drive
Optional
Lead / lag alternating switch Multi-motor protection
Class 3C2 Mechanical particles: IEC 60721-3-3, unit in
operation, Class 3S2
Altitude
100% load capacity (no derating) up to 3280 ft
(1000m); 1% derating for each 328 ft (100m) above
Enclosure Dimensions
ENCLOSURE CX
CX
NEMA 1 / 12 NEMA 3R
H1
56.08
56.08
H2
54.77
54.77
H3
48.35
48.35
H4
56.96
56.96
H5
35.85
35.85
W1
30.92
30.92
W2
30.88
30.88
W3
29.30
29.30
W4
Storage
40° to +158°F (40° to +70°C)
temperature
Relative
Moxa DA-682A-DPP 系列2U rackmount计算机产品介绍说明书

DA-682A-DPP SeriesIntel®3rd Gen Core™CPU,IEC-61850,2U rackmount computers with 2expansion slotsFeatures and Benefits•IEC 61850-3,IEEE 1613,and IEC 60255compliant for power substationautomation systems•EN 50121-4compliant for railway wayside applications•3rd Gen Intel®Core™processor (Ivy Bridge)•6Gigabit Ethernet ports for network redundancy•2PCI expansion slots for expansion modules•4high-speed,system-bootable USB 2.0ports•Supports dual power inputs:100to 240VAC and 100to 240VDC•Optional IRIG-B expansion module available CertificationsIntroductionThe DA-682A-DPP computers have an x86platform with VGA,6Gigabit Ethernet ports,USB,and two PCI ports for DA Series expansion modules.The DA-682A-DPP comes with three different CPU options,and basic models that allow system designers to install the DOM,RAM,and operating system according to their specific requirements.IEC-61850-3and IEEE 1613compliance helps ensure that the DA-682A-DPP can deliver stable and reliable system operations in power applications.Additional value and convenience are provided through a modular design with two independent slots for flexible system integration and ers have the option to add a variety of different communications modules,including an 8-port RS-232/422/485module,8-port RS-422/485module,8-port 10/100Mbps switch module,IRIG-B time synchronization card and a universal PCI expansion module.The DA-682A-DPP also complies with the IEC 60255standards to enable the protection of electrical relays in a smart substation.IEC 60255is one of the most widely used standards for testing relays and protection equipment,and compliance ensures that the DA-682A-DPP will work reliably and seamlessly with IEDs (intelligent electronic devices)as a part of the robust substation automation system.EN 50121-4compliance confirms that the DA-682A-DPP can deliver stable and reliable system operations in rail applications.In station ISCS (Integrated Supervisory Control System)and wayside control and monitoring systems,a powerful front-end processor is needed for controlling the local SCADA and traction power relay house.The expandable serial interfaces and Gigabit Ethernet ports enable the integration of station subsystems,including AFC,PAS,PSD,and FAS,on a single platform.For wayside applications,you can also integrate disaster prevention,traction power,and signaling and safety systems to provide an integrated view of your smart rail setup.Smart Recovery FunctionThe DA-682A-DPP’s Smart Recovery function minimizes downtime by making it easy to recover from operating system crashes.Engineers who are experts in a particular vertical market may not have enough computer domain knowledge to know how to fix operating system problems.Moxa Smart Recovery™is an automated BIOS-level software recovery system that allows engineers to automatically trigger OS recovery to minimize downtime.Proactive Monitoring FunctionMoxa Proactive Monitoring is a small-footprint,resource-friendly,easy-to-use utility that allows users to track a number of system ers can view the current parameter values for these key parts by simply clicking on the icons corresponding to the parameters in the user er-defined key part indicators (KPIs)are used to monitor the computer’s key parts.Visible and/or audio alerts are triggered automatically via relay and SNMP traps when these KPIs exceed their preset threshold values,making it extremely convenient for operators to avoid system downtime by setting up predictive maintenance tasks well in advance.AppearanceFront ViewRear ViewSpecificationsComputerCPU DA-682A-C1-DPP Series:Intel®Celeron®Processor1047UE(2M Cache,1.40GHz)DA-682A-C3-DPP Series:Intel®Core™i3-3217UE Processor(3M Cache,1.6GHz)DA-682A-C7-DPP Series:Intel®Core™i7-3517UE Processor(4M Cache,up to2.80GHz)System Chipset Mobile Intel®HM65Express ChipsetGraphics Controller Intel®HD GraphicsSystem Memory Pre-installed DA-682A-DPP LX Series:1GB DDR3System Memory Slot SODIMM DDR3/DDR3L slot x1Supported OS Linux Debian7Windows Embedded Standard7(WS7P)32-bitWindows Embedded Standard7(WS7E)32-bitStorage Slot 2.5-inch HDD/SSD slots x2Computer InterfaceEthernet Ports Auto-sensing10/100/1000Mbps ports(RJ45connector)x6USB2.0USB2.0hosts x4,type-A connectorsExpansion Slots PCI slots x2Video Input VGA x1,15-pin D-sub connector(female)LED IndicatorsSystem Power x1Storage x1Programmable x8LAN2per port(10/100/1000Mbps)Power ParametersOperating Voltage100to240VDC,100to240VACPower Button Reset button(front panel)ON/OFF(rear panel)Power Consumption30W(max.)Physical CharacteristicsHousing MetalDimensions(without ears)440x315x90mm(17.32x12.40x3.54in) Weight6,500g(14.33lb)Installation19-inch rack mountingEnvironmental LimitsOperating Temperature-25to60°C(-13to140°F)Storage Temperature(package included)-40to80°C(-40to176°F)Ambient Relative Humidity5to95%(non-condensing)Standards and CertificationsEMC EN61000-6-2/-6-4EMI CISPR32,FCC Part15B Class AEMS IEC61000-4-2ESD:Contact:8kV;Air:15kVIEC61000-4-3RS:80MHz to1GHz:10V/mIEC61000-4-4EFT:Power:4kV;Signal:4kVIEC61000-4-5Surge:Power:4kV;Signal:4kVIEC61000-4-6CS:10VIEC61000-4-8PFMFIEC61000-4-11Power Substation IEC61850-3,IEEE1613Railway EN50121-4Protection Relay IEC60255Safety EN60950-1,IEC60950-1,UL60950-1Shock IEC60870-2-2,IEC61850-3Edition1.0 Vibration IEC61850-3,IEC60870-2-2DeclarationGreen Product RoHS,CRoHS,WEEEMTBFTime360,807hrsStandards Telcordia SR332WarrantyWarranty Period3yearsDetails See /warrantyPackage ContentsDevice1x DA-682A-DPP Series computerInstallation Kit1x rack-mounting earDocumentation1x quick installation guide1x warranty cardNote This product requires additional modules(sold separately)to function. DimensionsOrdering InformationModel Name CPU DDR3RAM Linux Debian732-bitPower Input100-240VAC/VDCOperating Temp.DA-682A-C1-DPP Intel®Celeron®1047UE––✓-25to60°CDA-682A-C1-DPP-LX Intel®Celeron®1047UE1GB✓✓-25to60°CDA-682A-C3-DPP Intel®Core™i3-3217UE––✓-25to60°CDA-682A-C3-DPP-LX Intel®Core™i3-3217UE1GB✓✓-25to60°CDA-682A-C7-DPP Intel®Core™i7-3517UE––✓-25to60°CDA-682A-C7-DPP-LX Intel®Core™i7-3517UE1GB✓✓-25to60°CAccessories(sold separately)Expansion ModulesDA-SP08-I-EMC4-DB8-port RS-232/422/485serial module with DB9connector and isolation;suitable for EMC Level4environmentsDA-SP08-I-EMC4-TB8-port RS-232/422/485serial module with terminal block connector and isolation;suitable for EMCLevel4environmentsDA-SP08-I-DB8-port RS-232/422/485serial module with a digitally isolated DB9connectorDA-SP08-DB8-port RS-232/422/485serial module with DB9connectorDA-SP08-I-TB8-port RS-422/485serial module with digitally isolated terminal blockDA-SP38-I-TB8-port RS-422/485serial module with digitally isolated terminal blockDA-SW08-RJ8-port10/100Mbps unmanaged switch moduleDA-LN04-RJ4-port10/100Mbps LAN moduleDA-UPCI-DK Universal PCI development kitDA-FX04-MM-ST-T4-port(100BaseFX)fiber LAN module with multi-mode,ST connector,supports IP Teaming Storage KitsDA-682A HDD Kit DA-682A HDD kitUSB Dongle KitsUSB Dongle Kit Internal USB dongle kit installation package©Moxa Inc.All rights reserved.Updated Jun30,2020.This document and any portion thereof may not be reproduced or used in any manner whatsoever without the express written permission of Moxa Inc.Product specifications subject to change without notice.Visit our website for the most up-to-date product information.。
API682密封系统-中英文对照版

API Piping Plans API 冲洗方案Leabharlann Throat Bushing
Points to Note for API Plan 32: 对于API plan 32 须注意:
- Chose a proper source of seal
flush to eliminate the potential for
Other applications其他应用
* high temperature liquid close to bubble point. * 接近沸点的高温液体.
API Piping Plans API 冲洗方案
Clean overflow
Inlet Underflow
Recirculation from pump discharge through a cyclone separator delivering clean fluid to the seal and fluid with solids back to pump suction line冲洗液从泵出口流出,通过一旋液分离器,使干净流体进入
Recirculation from seal chamber through a flow control orifice and back to pump suction从密封
腔里出,通过一个孔板返回到泵的入口
API Piping Plans API 冲洗方案
+=
Points to Note for API Plan 14: API 冲洗方案 14 应注意的事项:
API Piping Plans API 冲洗方案
Cooling Water Inlet
扫特龙和曼维尔产品数据表705、706、710和726个人攻击发射器说明书

705, 706, 710 & 726 Personal attack transmittersWhy settle for less when your staffneed help most?Hopefully, your staff will never need to find out whyour personal attack transmitters are so highly regarded.But should they ever be attacked, they’ll quickly realisewhy over 750,000 people worldwide trust them withtheir lives. The 705, 706, 710 and 726 models all comewith 10mW transmitting power compared to the usual0.25mW. And, to ensure your transmitter is alwaysworking, the long-life lithium battery sends a signalwhen less than one month’s operation remains.All models are designed to prevent accidental activationand a variety of wearing options – hand-held, neckpendant or clip-on – means there’s a style to suiteveryone.With many other state-of-the-art features (see overleaf),no other range of personal attack transmitters is betterequipped to draw attention to a member of staff whenthey are under attack.• Reliable, secure Scantronic 868 MHz narrow-bandradio operation• Dual button operation• 2-channel version for alert (pre-warning) + alarmsignals• Extended and standard range options• Lithium battery-powered (supplied)At a glance...Tel: +44 (0)1594 545 400Fax: +44 (0)1594 545 401Email:***********************Web: EatonElectrical Sector EMEA Route de la Longeraie 71110 Morges, Switzerland EatonSecurity House,Vantage Point Business Village, Mitcheldean, Gloucestershire GL17 0SXScantronic and Menvier product datasheetCompatible productsProduct specification705rEUR-00706rEUR-00710rEUR-00726rEUR-50726rEUR-60Part number 710rEUR-00705rEUR-00706rEUR-00726rEUR-50726rEUR-60Description2 channel personal attack transmitter2 channel personal attack transmitter Double push lock, beltmounted, secondary tilit sensor “man down” channel Extended range, dualoperation personal attack transmitter Standard, dual operationpersonal attack transmitter Channels12 (alert + alarm)211Operating frequency868.6625MHz @ 20KHz bandwidth.CE tested to I-ETS 300 220868.6625MHz @ 20KHz bandwidth.CE tested to I-ETS 300 220868.6625MHz at 20kHz bandwidth. I-ETS 300 220868.6625MHz @ 20KHz bandwidth.CE tested to I-ETS 300 220868.6625MHz @ 20KHz bandwidth.CE tested to I-ETS 300 220T ransmission power 10mW 10mW 10mW 10mW 10mW Free space radio range >1000m >600m>900m> 1000m>600mPower supply (battery)3v CR2 Li 3.6v Li 1/2 AA Not user replaceble 3.6v Li 1/2 AA Not user replaceable 3.6v Li 1/2 AA Not user replaceble 3.6v Li 1/2 AA Not user replaceble T ypical battery life 3-5 years 3-5 years 3-5 years 3-5 years 3-5 years T emperature range -10 to +55 ˚C -10 to +55 ˚C -10 to +55 ˚C -10 to +55 ˚C -10 to +55 ˚C Dimensions 58 x 40 x 16mm 104 x 46 x 30mm 170 x 45 x 30mm (including aerial)163 x 46 x 30mm 104 x 46 x 30mm Weight 34gm 60gm 68gm 65gm 65gm Colour Dark GreyDark GreyDark GreyDark GreyDark GreyComplianceEN50131-2 Grade 2, EN61000-6-3:2001, environmental class ll PD6662:2004EN50131-2 Grade 2, EN61000-6-3:2001, environmental class ll PD6662:2004EN50131-2 Grade 2EN61000-6-3:2001environmental class II PD6662:2004EN50131-2 Grade 2, EN61000-6-3:2001, environmental class ll PD6662:2004EN50131-2 Grade 2, EN61000-6-3:2001, environmental class ll PD6662:2004Scantronic 9960rEUR-08 & 16 RFX receiver interfaces (not 705rEUR-00)i-on4040 zone control panel Scantronic Homelink 55 24zone radio alarm panel (not 705rEUR-00)i-on50EX 50 zone control panel Scantronic Homelink 75 32zone radio alarm system (not 705rEUR-00)i-on160EX 160 zone control panel Scantronic 762rEUR-00 2 channel receiver Menvier3030 zone control panel Scantronic 768rEUR-008 - 32 channel receiver Menvier4040 zone control panel Scantronic EXP-R1010 zone radio expander Menvier100100 zone control panel Scantronic EXP-R3030 zone radio expander Menvier300300 zone control paneli-on1616 zone control panel Menvier MRNODE receiver interface (not 705rEUR-00)i-on30EX16 zone control panelMultibus1000 zone control panel。
ADUM1251ARZ-RL7,ADUM1250ARZ-RL7,ADUM1250WSRZ-RL7,ADUM1250SRZ-RL7,ADUM1250WSRZ, 规格书,Datasheet 资料

Figure 2. ADuM1251
GENERAL DESCRIPTION
The ADuM1250/ADuM12511 are hot swappable digital isolators with nonlatching, bidirectional communication channels compatible with I2C® interfaces. This eliminates the need for splitting I2C signals into separate transmit and receive signals for use with standalone optocouplers. The ADuM1250 provides two bidirectional channels, supporting a complete isolated I2C interface. The ADuM1251 provides one bidirectional channel and one unidirectional channel for those applications where a bidirectional clock is not required. Both the ADuM1250 and ADuM1251 contain hot swap circuitry to prevent glitching data when an unpowered card is inserted onto an active bus. These isolators are based on iCoupler® chip scale transformer technology from Analog Devices, Inc. iCoupler is a magnetic isolation technology with functional, performance, size, and power consumption advantages as compared to optocouplers. With the ADuM1250/ADuM1251, iCoupler channels can be integrated with semiconductor circuitry, which enables a complete isolated I2C interface to be implemented in a small form factor.
MEMORY存储芯片ADM3078EARZ-REEL7中文规格书

Error ManagementEach NAND Flash die (LUN) is specified to have a minimum number of valid blocks(NVB) of the total available blocks. This means the die (LUNs) could have blocks thatare invalid when shipped from the factory. An invalid block is one that contains at leastone page that has more bad bits than can be corrected by the minimum required ECC.Additional blocks can develop with use. However, the total number of available blocksper die (LUN) will not fall below NVB during the endurance life of the product.Although NAND Flash memory devices could contain bad blocks, they can be usedquite reliably in systems that provide bad block management and error-correction algo-rithms. This type of software environment ensures data integrity.Internal circuitry isolates each block from other blocks, so the presence of a bad blockdoes not affect the operation of the rest of the NAND Flash array.NAND Flash devices are shipped from the factory erased. The factory identifies invalidblocks before shipping by attempting to program the bad block mark into every loca-tion in the first page of each invalid block. It may not be possible to program every loca-tion with the bad block mark. However, the first spare area location in each bad block isguaranteed to contain the bad block mark. This method is compliant with ONFI FactoryDefect Mapping requirements. See the following table for the first spare area locationand the bad block mark.System software should check the first spare area location on the first page of eachblock prior to performing any PROGRAM or ERASE operations on the NAND Flash de-vice. A bad block table can then be created, enabling system software to map aroundthese areas. Factory testing is performed under worst-case conditions. Because invalidblocks could be marginal, it may not be possible to recover this information if the blockis erased.Over time, some memory locations may fail to program or erase properly. In order toensure that data is stored properly over the life of the NAND Flash device, the followingprecautions are required:•Always check status after a PROGRAM or ERASE operation•Under typical conditions, use the minimum required ECC (see table below)•Use bad block management and wear-leveling algorithmsThe first block (physical block address 00h) for each CE# is guaranteed to be validwith ECC when shipped from the factory.Table 21: Error Management DetailsElectrical Specifications4Gb, 8Gb, 16Gb: x8, x16 NAND Flash MemoryElectrical SpecificationsElectrical Specifications – AC Characteristics and Operating Conditions Table 29: AC Characteristics: Command, Data, and Address Input (3.3V)Notes: 1.Operating mode timings meet ONFI timing mode 5 parameters.2.Timing for t ADL begins in the address cycle, on the final rising edge of WE#, and endswith the first rising edge of WE# for data input.Table 30: AC Characteristics: Command, Data, and Address Input (1.8V)Notes: 1.Operating mode timings meet ONFI timing mode 4 parameters.2.Timing for t ADL begins in the address cycle on the final rising edge of WE#, and endswith the first rising edge of WE# for data input.Table 31: AC Characteristics: Normal Operation (3.3V)Notes: 1.AC characteristics may need to be relaxed if I/O drive strength is not set to full.2.Transition is measured ±200mV from steady-state voltage with load. This parameter issampled and not 100% tested.3.The first time the RESET (FFh) command is issued while the device is idle, the device willgo busy for a maximum of 1ms. Thereafter, the device goes busy for a maximum of 5µs. Table 32: AC Characteristics: Normal Operation (1.8V)Asynchronous Interface Timing DiagramsFigure 82: RESET OperationCLECE#WE#R/B#I/O[7:0]RESET commandFigure 83: READ STATUS CycleRE#CE#WE#CLEI/O[7:0]4Gb, 8Gb, 16Gb: x8, x16 NAND Flash MemoryAsynchronous Interface Timing Diagrams。
MAX6825中文资料

General DescriptionThe MAX6821–MAX6825 are low-voltage microprocessor (µP) supervisory circuits that combine voltage monitor-ing, watchdog timer, and manual reset input functions in a 5-pin SOT23 package. Microprocessor supervisory cir-cuits significantly improve system reliability and accura-cy compared to separate I Cs or discrete components.These devices assert a reset signal whenever the moni-tored voltage drops below its preset threshold, keeping it asserted for a minimum timeout period after V CC rises above the threshold. In addition, a watchdog timer moni-tors against code execution errors. A debounced manual reset is also available. The MAX6821–MAX6825 monitor voltages from +1.8V to +5.0V. These outputs are guaran-teed to be in the correct state for V CC down to +1.0V.Nine preprogrammed reset threshold voltages are available (see T hreshold Suffix Guide ). The MAX6821,MAX6822, and MAX6823 all have a manual reset input and a watchdog timer. The MAX6821 has push-pull RESET, the MAX6822 has open-drain RESET , and the MAX6823 has push-pull RESET . The MAX6824 has a watchdog timer and both push-pull RESET and push-pull RESET. The MAX6825 has a manual reset input and both push-pull RESET and push-pull RESET. The Selector Guide explains the functions offered in this series of parts.________________________ApplicationsFeatureso Monitors +1.8V, +2.5V, +3.0V, +3.3V, +5.0V Supplieso 140ms (min) Reset Timeout Delay o 1.6s Watchdog Timeout Period(MAX6821/MAX6822/MAX6823/MAX6824)o Manual Reset Input(MAX6821/MAX6822/MAX6823/MAX6825)o Three Reset Output OptionsPush-Pull RESET Push-Pull RESET Open-Drain RESETo Guaranteed Reset Valid to V CC = +1.0V o Immune to Short Negative V CC Transients o No External Components o Small 5-Pin SOT23 PackagesMAX6821–MAX6825Low-Voltage SOT23 µP Supervisors withManual Reset and Watchdog Timer________________________________________________________________Maxim Integrated Products1Pin Configurations19-1868; Rev 1; 1/01Ordering InformationThreshold Suffix Guideto complete the part number.minimum order increment. Contact factory for availability.Typical Operating Circuit appears at end of data sheet.Selector Guide appears at end of data sheet.Set-Top BoxesComputers and ControllersEmbedded Controllers Intelligent InstrumentsAutomotive Systems Critical µP Monitoring Portable/Battery-Powered EquipmentFor price, delivery, and to place orders,please contact Maxim Distribution at 1-888-629-4642,or visit Maxim’s website at .M A X 6821–M A X 6825Low-Voltage SOT23 µP Supervisors with Manual Reset and Watchdog TimerABSOLUTE MAXIMUM RATINGSELECTRICAL CHARACTERISTICS(V CC = +4.5V to +5.5V for MAX682_L/M, V CC = +2.7V to +3.6V for MAX682_T/S/R, V CC = +2.1V to +2.75V for MAX682_Z/Y, V CC =+1.53V to +2.0V for MAX682_W/V, T A = -40°C to +125°C, unless otherwise specified. Typical values are at T A = +25°C.) (Note 1)Stresses beyond those listed under “Absolute Maximum Ratings” may cause permanent damage to the device. These are stress ratings only, and functional operation of the device at these or any other conditions beyond those indicated in the operational sections of the specifications is not implied. Exposure to absolute maximum rating conditions for extended periods may affect device reliability.V CC to GND...........................................................-0.3V to +6.0V Open-Drain RESET ................................................-0.3V to +6.0V Push-Pull RESET , RESET, MR , WDI...........-0.3V to (V CC + 0.3V)Input Current (V CC ).............................................................20mA Output Current (RESET , RESET).........................................20mA Continuous Power Dissipation (T A = +70°C)5-Pin SOT23 (derate 7.1mW/°C above +70°C)............571mWOperating Temperature Range .........................-40°C to +125°C Junction Temperature......................................................+150°C Storage Temperature Range.............................-65°C to +150°C Lead Temperature (soldering, 10s).................................+300°CMAX6821–MAX6825Low-Voltage SOT23 µP Supervisors withManual Reset and Watchdog Timer_______________________________________________________________________________________3ELECTRICAL CHARACTERISTICS (continued)(V CC = +4.5V to +5.5V for MAX682_L/M, V CC = +2.7V to +3.6V for MAX682_T/S/R, V CC = +2.1V to +2.75V for MAX682_Z/Y, V CC =Note 2:Guaranteed by design and not production tested.M A X 6821–M A X 6825Low-Voltage SOT23 µP Supervisors with Manual Reset and Watchdog Timer 4_______________________________________________________________________________________Typical Operating Characteristics(T A = +25°C, unless otherwise noted.)354769*********-4002040-206080100120SUPPLY CURRENT vs.TEMPERATURETEMPERATURE (°C)S U P P L Y C U R R E N T (µA )150170160190180210200220240230250-4002040-206080100120RESET TIMEOUT PERIOD vs.TEMPERATUREM A X 6821 t o c 02TEMPERATURE (°C)R E S E T T I M E O U T P E R I O D (m s )1052015302535-40020-20406080100120V CC TO RESET OUTPUT DELAY vs.TEMPERATURETEMPERATURE (°C)P R O P A G A T I O N D E L A Y (µs )1.01.21.11.41.31.61.51.71.91.82.0-4002040-206080100120WATCHDOG TIMEOUT PERIOD vs.TEMPERATUREM A X 6821 t o c 04TEMPERATURE (°C)W A T C H D O G T I M E O U T P E R I O D (s )0.940.961.000.981.041.021.06-40020-20406080100120NORMALIZED RESET THRESHOLD DELAY vs. TEMPERATUREM A X 6821 t o c 05TEMPERATURE (°C)R E S E T T H R E S H O L D (V )060402080100120080602040100120140160180200MAXIMUM V CC TRANSIENT DURATION vs. RESET THRESHOLD OVERDRIVERESET THRESHOLD OVERDRIVE (mV), V TH - V CCT R A N S I E N T D U R A T I O N (µs)00.100.050.200.150.300.250.3502314567VOLTAGE OUTPUT LOW vs. I SINKI SINK (mA)V O U T (V )2.742.782.762.822.802.842.862.902.882.9200.10.20.30.40.50.60.70.80.9 1.0VOLTAGE OUTPUT HIGH vs. I SOURCEI SOURCE (mA)V O U T (V )MAX6821–MAX6825Low-Voltage SOT23 µP Supervisors withManual Reset and Watchdog Timer_______________________________________________________________________________________5RESET /RESET OutputA µP ’s reset input starts the µP in a known state. TheMAX6821–MAX6825 µP supervisory circuits assert a reset to prevent code-execution errors during power-up, power-down, and brownout conditions. Whenever V CC falls below the reset threshold, the reset output asserts low for RESET and high for RESET. Once V CC exceeds the reset threshold, an internal timer keeps the reset output asserted for the specified reset timeout period (t RP ); after this interval, reset output returns to its original state (see Figure 2).Manual Reset InputMany µP-based products require manual reset capabil-ity, allowing the operator, a test technician, or external logic circuitry to initiate a reset. On the MAX6821/MAX6822/MAX6823/MAX6825, a logic low on MR asserts a reset. Reset remains asserted while MR is low, and for the timeout period (140ms min) after itven with CMOS logic levels or with open-drain/collector outputs. Connect a normally open momentary switch from MR to GND to create a manual reset function;external debounce circuitry is not required. If MR is dri-ven from long cables or the device is used in a noisy environment, connect a 0.1µF capacitor from MR to GND to provide additional noise immunity.Watchdog InputIn the MAX6821–MAX6824, the watchdog circuit moni-tors the µP ’s activity. I f the µP does not toggle (low to high or high to low) the watchdog input (WDI) within the watchdog timeout period (1.6s nominal), reset asserts for the reset timoeout period. The internal 1.6s timer can be cleared by either a reset pulse or by toggling WDI. The WDI can detect pulses as short as 50ns.While reset is asserted, the timer remains cleared and does not count. As soon as reset is released, the timer starts counting (see Figure 3).Disable the watchdog function by leaving WDI uncon-nected or by three-stating the driver connected to WDI.The watchdog input is internally driven low during the first 7/8 of the watchdog timeout period and high for the last 1/8 of the watchdog timeout period. When WDI is left unconnected, this internal driver clears the 1.6s timer every 1.4s. When WDI is three-stated or unconnected,the maximum allowable leakage current is 10µA and the maximum allowable load capacitance is 200pF.Applications InformationWatchdog Input CurrentThe MAX6821/MAX6822/MAX6823/MAX6824 WDI inputs are internally driven through a buffer and series resistor from the watchdog timer (Figure 1). When WDI is left unconnected, the watchdog timer is serviced within the watchdog timeout period by a low-high-low pulse from the counter chain. For minimum watchdog input current (minimum overall power consumption), leave WDI low for the majority of the watchdog timeout period, pulsing it low-high-low once within the first 7/8 of the watchdog timeout period to reset the watchdog timer. I f WDI is externally driven high for the majority of the timeout peri-od, up to 160µA can flow into WDI.Interfacing to µPs with Bidirectional Reset PinsSince the RESET output on the MAX6822 is open drain,it interfaces easily with µPs that have bidirectional reset pins, such as the Motorola 68HC11. Connecting the µP supervisor ’s RESET output directly to the microcon-troller ’s RESET pin with a single pullup resistor allows either device to assert reset (see Figure 4).Negative-Going V CC TransientsThese supervisors are relatively immune to short-dura-tion, negative-going V CC transients (glitches), which usually do not require the entire system to shut down.M A X 6821–M A X 6825Low-Voltage SOT23 µP Supervisors with Manual Reset and Watchdog Timer 6_______________________________________________________________________________________Figure 1. Functional DiagramResets are issued to the µP during power-up, power-down, and brownout conditions. The Typical Operating Characteristics show a graph of the MAX6821–MAX6825’s Maximum V CC Transient Duration vs. Reset Threshold Overdrive, for which reset pulses are not generated. The graph was produced using negative-going V CC pulses, starting at the standard monitored voltage and ending below the reset threshold by the magnitude indicated (reset threshold overdrive). The graph shows the maximum pulse width that a negative-going V CC transient can typically have without trigger-ing a reset pulse. As the amplitude of the transient increases (i.e., goes farther below the reset threshold),the maximum allowable pulse width decreases.Typically, a V CC transient that goes 100mV below the reset threshold and lasts for 20µs or less will not trigger a reset pulse.Watchdog Software ConsiderationsOne way to help the watchdog timer monitor software execution more closely is to set and reset the watch-dog input at different points in the program, rather than pulsing the watchdog input high-low-high or low-high-low. This technique avoids a stuck loop, in which the watchdog timer would continue to be reset inside the loop, keeping the watchdog from timing out.Figure 5shows an example of a flow diagram where the I /O driving the watchdog input is set high at the beginning of the program, set low at the beginning of every subroutine or loop, then set high again when the program returns to the beginning. I f the program should hang in any subroutine, the problem would quickly be corrected, since the I /O is continually set low and the watchdog timer is allowed to time out,causing a reset or interrupt to be issued. As described in the Watchdog Input Current section, this scheme results in higher time average WDI input current than does leaving WDI low for the majority of the timeout period and periodically pulsing it low-high-low.MAX6821–MAX6825Low-Voltage SOT23 µP Supervisors withManual Reset and Watchdog Timer_______________________________________________________________________________________7Figure 4. Interfacing Open-Drain RESET to µPs with Bidirectional Reset I/OFigure 5. Watchdog Flow DiagramTypical Operating CircuitChip InformationTRANSISTOR COUNT: 750PROCESS: BiCMOSSelector GuidePin Configurations (continued)M A X 6821–M A X 6825Low-Voltage SOT23 µP Supervisors with Manual Reset and Watchdog Timer 8_______________________________________________________________________________________Low-Voltage SOT23 µP Supervisors withManual Reset and Watchdog TimerMaxim cannot assume responsibility for use of any circuitry other than circuitry entirely embodied in a Maxim product. No circuit patent licenses are implied. Maxim reserves the right to change the circuitry and specifications without notice at any time.Maxim Integrated Products, 120 San Gabriel Drive, Sunnyvale, CA 94086 408-737-7600 _____________________9©2001 Maxim Integrated Products Printed USAis a registered trademark of Maxim Integrated Products.MAX6821–MAX6825Package Information。
MEMORY存储芯片ADM3075EARZ-REEL中文规格书

1
Disable
1 0 Mode register set 2 (MR2)
1 Disabled 1 Enabled
M5 M1 Output Drive St rength
1 1 Mode register set 3 (MR3)
M9 M6 M2
RTT,nom (ODT) 2 Non- Writes
0 0 0 RTT,nom disabled 0 0 1 RZQ/4 (60ȍ [NOM])
satisfied, the updated features are to be assumed unavailable.
09005aef85af8fa8 4Gb_DDR3L.pdf - Rev. R 09/18 EN
Figure 53: MRS to nonMRS Command Timing (tMOD)
The MR1 register must be loaded when all banks are idle and no bursts are in progress. The controller must satisfy the specified timing parameters tMRD and tMOD before initiating a subsequent operation.
RTT,nom (ODT) 3 Writes
RTT,nom disabled RZQ/4 (60ȍ [NOM])
M7 Write Levelization
0 Disable (normal)
1
Enable
00 01 10 11
RZQ/6 (40ȍ [NOM]) RZQ/7 (34ȍ [NOM])
思科 DECT 6823 和 6825 用户指南说明书

CISCO DECT 6823 & 6825USER GUIDELast Updated: October 2021SMARTVOICEOverview (1)Install The Battery in the Handset (1)Buttons and Hardware (3)Navigation (6)Supported Characters (6)Screen Features (7)Header Icons (7)Make Calls (9)Create an N-Way Conference Call (12)Transfer A Call (13)Ring Volume Settings (13)Directories (14)OverviewLearn about the features of your C isco DEC T 6823 and 6825 Handset so you can initiate calls, transfer calls and much more.Install The Battery in the HandsetThe handset battery is shipped inside the handset but there’s a plastic tab overthe battery contacts. You need to remove the plastic tab.Step 1On the back of the handset,turn the latch counterclockwise to unlock the back, lift the clip, and lift the cover to remove the battery cover.Step 2Remove the battery from the handset.Step 3Removethe plastic over the contacts.Step 4Place the battery under the clip and drop it into the compartment.The battery contacts are on the top left edge of the battery and the top left edge of the battery compartment.Ensure that the contacts meet and that the battery is seated in the compartment.Note: The battery fits only one way in the compartment. Don’t force the battery in the wrong way in the battery compartment.Step 5Replace the battery cover, make sure that the cover is closed, and turn the latch clockwise to the locked position.Don't force the cover closed. If it doesn't close easily, take it off and check that the battery is completely seated in the battery compartment.Buttons and HardwareYour handset has many buttons and hardware features that you’ll useregularly. Use the following figure and table to identify the important button and hardware features. The figure above the 6823 Handset and 6825 Handset. The 6825 Ruggedized Handset is similar to 6825 Handset in appearance.6825 & 6823 Handset Buttons and Hardware6825 & 6825 Ruggedized521 4 351 22 3 4435ItemName orGroupingDescription1 Indicator Light (LED)Indicator light to identify states. You can configure the event that triggers the red, yellow or green LED.2Headset PortHeadset port with cover Remove the protective cover and plug in headset or ear buds (3.5 mm audio jack).3Softkeys, handset control buttons (Speaker, Menu), Navigation cluster, call control buttons (Answer/Send, Power/End).Softkeys Activate the option displayed on the screen SpeakerToggle the speaker mode on or off for the handset.Menu Access directories, settings, status, and other information.Navigation cluster Navigation ring and Select button:• Navigation ring (outer ring): Move up, down, left or right• Select button(centre of the cluster): select a menuitem.Answer/Send Answer a ringing call, or after dialing a number, press to place the call.Power/End Turn the handset on or off, or end a connected call. In menus, this button returns you to the previous screen.ItemName orDescriptionGrouping4 Keypad Dial numbers and enter letter. Use the keys 2 through 9 to enterletters and numbers.One•Enter “1” when you dial a number•Access voicemail by pressing and holding to automaticallydial the voicemail system.•Enter these special text characters: . ! ? , “ @ + ; :Asterisk•Press and hold to add the plus (+) symbol at the beginningof a phone number.Zero•Enter “0” when you dial a number.•Press and hold to lock or unlock the keypad.•Enter a space.Pound•Press and hold to silence the handset ringer. If configured,the handset vibrates instead.•Enter this special text character: #5 Volume and MutebuttonsVolume•When the handset is idle, change the ring volume or turn off theringer.•During a call, control the speaker volume for the active handset,headset, or speaker.Mute Toggle the mute feature on or off.NavigationUse the outer ring of the Navigation cluster to scroll through menus and to move between fields. Use the inner Select button of the Navigation cluster to select menu items.Supported C haractersWhen you input information, the handsets support the following characters:Tip: You can press the centre softkey in the 6823 Handset to access the special characters.Screen FeaturesThe screen shows information about your handset such as directory number, date and time, and softkeys. The screen is made up of three sections: the header row, the middle section, and the footer row. Menu items on the screen may vary based on service provider configuration.Header IconsThe header icons tell you about the handset state. This section displays the header icons and gives their meaning. The header row icons can be different when do not disturb (DND) is enabled.Audio Path IconsIconDND Mode IconDescriptionSpeaker is off.Headset in use.Handset is muted.1At the top of the screen is the header row. The header rowdisplays the radio signal strength and battery charge, as well several icons. The icons display when features are active. 2The middle of the screen displays the information associated with the handset: date and time, configured handset owner, and handset phone number.3The bottom row of the screen contains the softkey labels. Each label indicates the action for the softkey button below the screen. Sometimes, icons are displayed above the softkey labels.Bluetooth IconsOnly the 6825 Handset supports Bluetooth. The feature may not be supported with certain wireless headsets.IconDND Mode IconDescriptionBluetooth® is connected.Bluetooth® is disconnected.Network IconsIconDND Mode IconDescriptionNo network connection.Weak network connection. Good network connection. Better network connection.Best network connection.Battery IconsIconDND Mode IconDescriptionBattery is depleted. Recharge the battery to use the handset.Battery is 1% to 24% charged. Recharge the battery as soon as possible.Battery is 25% to 49% charged.Battery is 50% to 74% charged.Battery is 75% to 100% charged.Battery is charging.C all Related IconsIconDND Mode IconDescription N/A Answered call. N/A Dialed call.N/ADo not disturb is enabled. N/A Phone is forwarded. N/A Voicemail message waiting.N/AMissed call.Make CallsYour handset works just like a regular phone, but the features make it easier for you to make calls.Make a CallStep 1When your handset is idle, enter the phone number with thekeypad. To start the number with plus (+), press and hold Asteriskuntil the + displays on the screenStep 2Press Answer/Send.Make a C all with the SpeakerphoneMake a Call with a HeadsetAnswer a CallEnd a C allStep 1When your handset is idle, enter the phone number with thekeypad. To start the number with plus (+), press and hold Asteriskuntil the + displays on the screen.Step 2 Press Speakerphone Step 3Press Answer/Send.Step 1 When your handset is idle, remove the cover from the headset port and plug in your headset.Step 2Enter the phone number with the keypad. To start the number with plus(+), press and hold Asterisk until the + displays on thescreen.Step 3Press Answer/Send.Step 1Press Answer/Send.Step 1Press Power/End.Hold and Resume a C allYou can put a call on hold and then resume it.Swap Between Active and Held C allsWhen you have an active call and a held call, you can easily swap the calls. The current active call goes on hold and the previously held call becomes the active call. Perform one of these actions:Step 1 From an active call, press Hold. Step 2Press Resume to pick the call back up.6823 Handset Press up or down on the navigation ring.6825 HandsetPress up or down on the navigation ring, or Press Swap.Create an N-Way Conference CallYou can add another person into an active call to create a three-way conference call.Step 1Froman active call,• 6825Handset: PressConf. then the Hold softkey.• 6823 Handset: Press More > C onference > Hold.Step 2User A now calls User B and the call connects. User A then presses Conf again to let User B join the conference call.Step 3To add another participant, User A presses the Hold softkey, dials the number then presses Conf. Everyone should hear each other now and be able to have conversation. User A does this procedure again to add more participants to the call.Transfer A CallYou can transfer a call to a coworker. You can transfer the call without waiting for the coworker to answer, or talk with the coworker before you transfer the call.Blind C all TransferConsultative Call TransferRing Volume SettingsSet The Ring Volume Settings from the Settings MenuYou can change the volume of the ringer. The ring volume does not impact the volume level when you are on a call.6823 Handset Press More > Select Transfer, dial the number > Press Transfer again.6825 HandsetPress Transfer, dial the number > Press Transfer again.6823 Handset Press More > Select Transfer, dial the number > Press C all button> stay on the line to introduce caller then Transfer. 6825 HandsetPress Transfer, dial the number > Press Call button > stay on the line to introduce caller then Transfer.Step 1 Press MenuStep 2 Select Settings> Audio settings > Ring volume.Step 3 Press right or left on the ring of the navigation cluster.Step 4Press Ok to save the level.Set The Ringtone for Different C all TypesYou can set different ring tones for these types of calls:• Normal call • Normal message • Urgent message• Emergency High, Medium, and Low • AlertDirectoriesStep 1 Press MenuStep 2Select Settings > Audio settingsStep 36823 Handset: Ring melody6825 Handset:• Ring melody • Ring normal msg• Ring urgent msg • Ring emergency • Ring emerg. high • Ring emerg. med • Ring emerg. lowStep 1 On your phone, go to Directory > Select Enterprise or Group or GroupC ommon or Personal.Step 2 Enter First Name or Last Name and click Search.Step 3 The searched Enterprise or Group or Group C ommon or Personal contact will appear.Step 4 Select the contact from the result. Step 5Press the middle "Navigating ring" to call.。
远驱控制器驱动芯片中文资料

远驱控制器驱动芯片中文资料远程驱动控制器是一种用于实现远程控制的芯片。
它采用一种特殊的电路设计和专门的算法,能够将来自远程设备的控制信号转换为对目标设备的驱动信号,实现对目标设备的远程控制。
远程驱动控制器芯片通常由微控制器和通信接口模块组成。
微控制器是芯片的核心部件,负责接收和解析来自远程设备的控制信号,并根据解析结果生成相应的驱动信号。
通信接口模块则负责与远程设备进行通信,接收和发送控制信号和数据。
在远程驱动控制器芯片的设计中,需要考虑多种因素。
首先,芯片需要具备稳定可靠的性能,能够在不同环境条件下正常工作。
其次,芯片需要具备快速响应的能力,能够及时准确地解析和处理控制信号。
此外,芯片还需要具备低功耗的特性,以延长电池使用寿命或减少能源消耗。
远程驱动控制器芯片广泛应用于各个领域。
在智能家居领域,远程驱动控制器可以实现对家庭电器的远程控制,如通过手机APP控制灯光、空调、电视等设备。
在工业自动化领域,远程驱动控制器可以实现对生产设备的远程控制,如通过计算机或SCADA系统远程监控和控制工厂的各种设备。
在农业领域,远程驱动控制器可以实现对温室灌溉系统、禽畜养殖设备等的远程控制,提高农作物的生长效率和动物的养殖效益。
在使用远程驱动控制器芯片时,需要注意一些要点。
首先,应选择具有良好品质和稳定性能的芯片,以保证远程控制的可靠性和安全性。
其次,应根据实际应用需求,选择适合的通信接口和控制协议。
最后,应遵循芯片厂商提供的使用说明和设计指南,合理布局电路和连接方式,以确保芯片能够正常工作。
总而言之,远程驱动控制器芯片是一种实现远程控制的重要组成部件。
它通过将远程设备的控制信号转换为驱动信号,实现对目标设备的远程控制。
远程驱动控制器芯片在智能家居、工业自动化、农业等领域都有广泛的应用前景。
在使用时,需要注意选择合适的芯片和控制协议,并遵循设计指南进行合理布局。
MEMORY存储芯片ADM3485EARZ-REEL7中文规格书
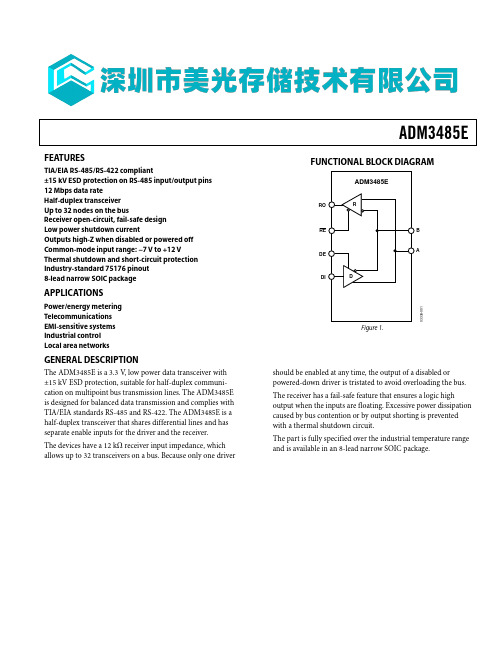
Logic Inputs Input Low Voltage Input High Voltage Logic Input Current
ADM3485E
RO
R
RE
B
A DE
DI
D
03338-001
Figure 1.
should be enabled at any time, the output of a disabled or powered-down driver is tristated to avoid overloading the bus. The receiver has a fail-safe feature that ensures a logic high output when the inputs are floating. Excessive power dissipation caused by bus contention or by output shorting is prevented with a thermal shutdown circuit. The part is fully specified over the industrial temperature range and is available in an 8-lead narrow SOIC package.
ADM3485E
SPECIFICATIONS
艾伦达尔单车部件说明书

GENERAL SAFETY INFORMATION .........2About This Supplement .......................2Special Manual Messages ...................2ALLOY CRANKARMS (ROAD & MTN) .....3Removal ...................................................3Installation ..............................................4SI CARBON .............................................5Removal ...................................................5Installation ..............................................5BB SHELL BEARINGS .............................6Inspection ..............................................6Removal ...................................................7Installation ..............................................7BB SHELL CIRCLIPS ................................9Removal ..................................................9Installation .............................................9BB SPINDLE ...........................................10Removal .................................................10Installation .. (10)SI COMPACT CARBON EXPLD VIEW .....12SI ALLOY MTN EXPLD VIEW ..................14SI ALLOY ROAD EXPLD VIEW ................14SI MTN 3X9 CHAINRINGS .....................18SI MTN 2X9 CHAINRINGS (19)SI CARBON CRNK/CHAINRINGS .........20SI BB ADAPTER ......................................21REPLACEMENT PARTS (KITS) .. (22)SI SPECIAL TOOLS (24)CONTENTSsi cranksets Owner’s Manual Supplement118609.PDFPlease note that the specifications and information in this manual are subject to change for product improvement without notice. For the latest product information, go to /bikes/tech/.general safety informationAbout This Supplement Cannondale Owner’s Manual Supplements provide important model specific safety, maintenance, and technical information. They are not replacements.This supplement may be one of several for your bike. Be sure to obtain and read all of them.If you need a manual or supplement, or have a question about your bike, please contact your Cannondale Dealer immediately, or call us at one of the telephone numbers listed on the back cover of this manual. You can download Adobe Acrobat PDF versions of any Cannondale Owner’s Manuals or Supplements from our website. Go to: /bikes/ tech• This manual is not a comprehensive safety or service manual for your bike.• This manual does not include assembly instructions for your bike.• All Cannondale bikes must be completely assembled and inspected for proper operation by a Cannondale Dealer before delivery to the owner.* * IMPORTANT * *This manual may include procedures beyond the scope of general mechanical aptitude. Special tools, skills, and knowledge may be required.If you have any doubt about your ability to properly inspect, adjust, or service your bicycle, do not attempt to perform the work described; please take the fork to a Cannondale Dealer.Special Manual MessagesI n this manual, information which affects your safety is emphasized in the followingways:NOTE:A NOTE provides helpful information or tips intended to make the information presented clearer.118609.PDFalloy crankarm remov al & installationRemovalTOOLS & SUPPLIES ● Cannondale tool KT013/●8 mm Allen Key ●15 mm open end wrench ●Clean shop towel ●Bicycle bearing greaseBefore starting, consult the exploded view parts drawing so that you can identified parts and features not shown in the following photographs. 1.Insert an 8 mm Allen key into the fixing bolt completely, hold crankarm with your hand and turn the fixing boltcounter-clockwise to remove it.Figure12.When the bolt is removed, be sure to collect and retain the thin steel washer under the bolt head. It is black in color; check the bolt or use a pencil tip toremove it from the crankarm seat.Figure 23.With the fixing bolt out, apply some bicycle bearing grease to the threads of the tool stud (1) and thread it into the bottom bracket spindle until the top of the stud is flush with the top of the spindle.KT013/15mm 8mm 12Cannondale ToolTOOLFlush with thisFigure 43. Next, apply grease to thethreads of the tool body (2) and exposed face of the tool stud.Install the tool body into the crankarm completely and tighten it snug with a 15mm open end wrench. 4. Insert a 8mm Allen key through thetool body and intothe stud. Hold the crankarm and turn the Allen key counter-clockwise until the crankarm can be removed from the spindle end.Figure 55. Repeat the previous steps for the othercrankarm.InstallationTOOLS & SUPPLIES●8 mm Allen Key●Clean shop towel●Bicycle bearing grease Crankarms are pressed onto the spindle ends using the fixing bolt. It is important that the fixing bolt, crankarm socket/ threads, and spindle splines are clean and greased before tightening to the specified torque. Consult the exploded view.118609.PDFcarbon crankarm remov al & installation RemovalTOOLS & SUPPLIES●10 mm Allen Key1. Insert a 10 mm Allen key through theretaining ring (1) into the fixing bolt.2. Hold the crankarm, and turn thefixing bolt counter-clockwise until the crankarm can be removed.It is not necessary to remove the retaining ring when removing or installing the crankarms.Insufficient grease behind the retaining ring can cause it to be removed while turning the fixing bolt.If the ring begins to unscrew while turning the fixing bolt, remove it witha red pin spanner (Park SPA-2) and applygrease to the top of the fixing bolt.Apply Loctite 603 to the ring threads and reinstall the ring so it it flush with the top of the crankarm.InstallationTOOLS & SUPPLIES●10 mm Allen Key1. Consult the exploded view forarrangement order of drive and non-drive side parts.2. Prior to installation, always be sure tothoroughly clean and grease the spindle splines and fixing bolt threads and the crankarm sockets with a high-quality bicycle bearing grease. Insufficient grease coverage can result in “creaking”of the crankarm assembly when riding.Be generous with the grease and cover all the contact surfaces.See SI Carkbon Crankset Exploded View for areas where it is important to ensure adequate grease coverage of mating surfaces.3. Tighten the fixing bolt to 34-41 N•m(25-30Ft•Lbs). using an accurately calibrated torque wrench.10 mmAllen KeyInsert thruRETAININGRING Figure 8bb shell bearings InformationThe two bearings in the SI bottom bracket shell are a maintenace free sealed cartridge type and do not require lubrication. The bearings can be worn out overtime or damaged due to corrosion.RACEFigure 7In general, the condition of the bearings should be inspected annually or anytime the crankset assembly is disassembled or serviced using the a simple inspection procedure.Frequent renewal is not recommended. because r epeated r emoval a nd r einstallation can damage the inside BB shell surfaces resulting in poor bearing fit. NOTE: Loose bearings can be acause of “creaking.”Replacement bearings are available through a Cannondale dealer. See “Replacement Parts (Kits)” at the end of this manual.InspectionFigure81. Remove the crankarms and spindle.2. Clean the bearings with a dry shoptowel to remove grease and grime.3. Rotate the inner bearing race of bothbearings with your fingers; they should rotate smoothly and quietly with only the force of your finger. It should not move side-to-side, stick or feel gritty.There should not be any play detected in the inner race and the bearing should not be free to slide in the bottom bracket shell.The bearings are a press fit and if they move in the shell, this is an indication of damage to either the bearings or bottom bracket shell.1. Always thoroughly clean the insidesurface of the BB shell with a dry shoptowel.2. Lightly grease entire inside surface ofthe bottom bracket shell.3. Install the drive side bearing first. Usethe tool arrangements for each bearingside. See next Figure.Press the bearing until it bottomsagainst the circlip.4. Apply a coating of grease to both sidesof each bearing seal to repel help repelmoisture.Figure 11118609.PDFbb shell circlipsRemovalTOOLS & SUPPLIES ●Small thin blade screw driverThe two circlips in the bottom bracket shell can be left in place unless they are damaged.Should they need to be removed, use a flatthe machined bearing seats (b) on both sides of the bottom bracket. And, carefully inspect the BB (outer and inner surfaces) and frame welds for evidence of fatigue cracking or damage. 3.Apply a thin film of bearing grease to the BB circlip groove. Install the square end (a) of the circlip into the groove first, then moving clockwise, push the clip into the groove until it is fully seated in the groove. Install the other circlip the same way.Figure 12spindleRemovalTOOLS & SUPPLIES● A small non-marring rubber mallet Before starting, consult the exploded view parts drawing so that you can identified parts and features not shown in the following photographs.1. Remove the crankarms.2. Remove the small parts from the driveside spindle end (wave washer, shims, spacer (mountain only) bearing shield and seal (mountain only).3. Use a plastic mallet to lightly tap thespindle on the drive side and pull it outon the non-drive side with your hand.Figure 13InstallationTOOLS & SUPPLIES● A small non-marring rubber mallet ●Clean shop towel●Bicycle bearing greaseBefore starting, consult the exploded view parts drawing so that you can identify parts and features not shown in the following photographs.1. Install the circlips.2. Install the bearings.3. Consult the appropriate explodedview for your crankset and assemble the non-drive (left) side parts onto the spindle.Make sure the flat side of the bearing shield faces outward and the bearing seal face is coated with bicycle bearing grease.118609.PDF118609.PDF118609.PDF118609.PDFFigure 21118609.PDF si bottom bracket adapterThe SI bottom bracket adapter enables the use of standard English/68mm bottom bracket cranksets in Cannondale System Integration (SI) road or mountain bicycle frames. Its is sold as an Cannondale Kit. The adapter is removable on alloy BB frames, however, repeated removal and reinstallation could result in damage to the SI BB shell and is not recommended. The adapter IS NOT a repair part and will only work in undamaged frames in good condition. Improper installation or removal can result in damage and void applicable frame warranty. If the adapter is installed in a Synapse carbon frame , the installation is permanent and can not be removed.Figure 22replacement parts (kits)118609.PDFFor an up to date list of kits available for your bike, please visit our Tech Center at : /bikes/tech/si special tools。
OFDM电力载波芯片BSC6825手册(电力线载波)

bestrong-techBSC6825 DatasheetDigital And Analog Mixed Signal Chip SolutionBSC6825 is compatible to 6688 (internal code)Version 6.0i1 芯片特点及功能概述1.1 芯片概述BSC6825是一颗面向直流应用而优化设计的基于正交多载波技术的电力载波芯片(也支持交流应用)。
具有抗干扰、长距离传输特性。
通信频段为10kHz~500kHz,线上用户有效数据传输率最高可达230kbps。
1.2 芯片特点1.面向直流电力载波应用而优化(也可用于交流应用)2. 抗强噪声干扰的数字信号处理算法3. 支持1024节点4. 完整的硬件设计和软件设计(易用)5. 无中继传输距离可大于5Km,线上有效数据率最高230Kbps6.128K flash片内储存器7.芯片包含模拟前端,单芯片数模混合将所有功能集成在一个芯片里9. 内置两个可灵活配置的全双工多功能UART10. 内置三个8/16位定时/计数器,一个看门狗定时器11.内置程序存储器编程接口,支持在线系统编程(UART)12.具有10个GPIO端口,其中两路GPIO具有15mA的驱动能力13.具有可独立配置的外部IO中断功能14.片内2个LDO,采用3.3V单电源供电15.温度适用范围 -40℃ ~ 85℃1.3 芯片参数与指标表1-1 芯片参数参数参数值参数参数值系统时钟/MHz 19.2 频率范围/kHz 3~500采样率/MHz 1.2 调制方式 DB/Q/8PSKFFT点数 1024 鲁棒模式 RoboRep2/4/8 可用子载波数 419 ADC/DAC位宽10 bit子载波间隔/kHz 1.17 AGC增益/dB -20~102表1-2 芯片指标参数指标灵敏度 <0.1uV 高低温 -40℃ ~ 85℃供电 3.3~3.6V 耐压 HBM-2KV,MM-200V2 芯片设计说明2.1 管脚分布图2-1引脚图2.2 管脚分配表2-2管脚分配Bank No Pin FunctionGND1 1 DGNDDigital(Left) 2 DVDDIN1_8 Digital power 1.8 V input3 P_0GPIO0.04 P_1GPIO0.15 P_2GPIO0.26 DGNDDigitalGND7 P_3GPIO0.38 P_4GPIO0.49 P_5GPIO0.510 P_6GPIO0.611 DGNDDigitalGND12 P_7GPIO0.713 P_8GPIO1.014 P_9GPIO1.115 DGNDDigitalGND16 DGNDDigitalGND2 (Bottom) 17 DGNDDigitalGND18 DVDD3_3 Digital power 3.3 V input19 DVDDIN1_8 Digital power 1.8 V input20 TXD2Flashtransmit 21 RXD2Flashreceive 22 DGNDDigitalground 23 LEDLED24 SDAI2C data line25 SCLI2C clock line26 TXD0 UART 0 transmit27 DGNDDigitalGND28 RXD0 UART 0 receive29 TXD1 UART 1 transmit30 RXD1 UART 1 receive31 CLK19_2 Clock 19.2 MHz32 DGNDDigitalGND3 (Right) 33 DGNDDigitalGND34 XTAL_I Crystal oscillator input35 XTAL_O Crystal oscillator output36 TXENTXenableoutput(active low) 37 AGNDAnalogground38 NCNoconnection39 PREADCN Analog test interface negative40 PREADCP Analog test interface positive41 REF RX ADC reference CAP42 AVDD3_3 Analog Power 3.3 Input43 NCNoconnection44 RXINN AC powerline negative input45 RXINP AC powerline positive input46 TXOUTP AC powerline positive output47 TXOUTN AC powerline negative output48 NCNoconnection4 (Top) 49 NCNoconnection 50 AGNDAnalogground51 AVDDOUT1_8Analog power 1.8 V output52 AVDD3_3 Analog power 3.3 V input53 DVDDOUT1_8Digital power 1.8 V output54 NCNoconnection55 DVDD3_3 Digital power 3.3 V input56 RSTN Power on reset57 CHIPMODE_0Chipmode[0]58 CHIPMODE_1Chipmode[1]59 DGNDDigitalground 60 CHIPMODE_2Chipmode[2]61 TESTMODE_0Testmode[0]62 TESTMODE_1Testmode[1]63 TESTMODE_2Testmode[2]64 DGNDDigitalground2.3 芯片系统架构图2-1系统架构图芯片的基带部分主要分为发射端、接收端和与模拟前端的接口三部分组成。
- 1、下载文档前请自行甄别文档内容的完整性,平台不提供额外的编辑、内容补充、找答案等附加服务。
- 2、"仅部分预览"的文档,不可在线预览部分如存在完整性等问题,可反馈申请退款(可完整预览的文档不适用该条件!)。
- 3、如文档侵犯您的权益,请联系客服反馈,我们会尽快为您处理(人工客服工作时间:9:00-18:30)。
Low Voltage Supervisory Circuits withWatchdog & Manual Reset in 5-Lead SOT-23 Preliminary Technical Data ADM6821–ADM6825Rev.PrAInformation furnished by Analog Devices is believed to be accurate and reliable.However, no responsibility is assumed by Analog Devices for its use, nor for anyinfringements of patents or other rights of third parties that may result from its use. Specifications subject to change without notice. No license is granted by implication or otherwise under any patent or patent rights of Analog Devices. Trademarks and registered trademarks are the property of their respective companies.One Technology Way, P.O. Box 9106, Norwood, MA 02062-9106, U.S.A. Tel: Fax: 781.326.8703© 2004 Analog Devices, Inc. All rights reserved.FEATURESPrecision Low Voltage Monitoring down to 1.8V9 Reset Threshold Options:1.58V to 4.63V140ms (Min) Reset TimeoutWatchdog Timer with 1.6s TimeoutManual Reset InputReset Output StagesPush-Pull Active-LowOpen-Drain Active-LowPush-Pull Active-HighLow Power Consumption (3µA)Guaranteed Reset Output valid to V CC=1VPower Supply Glitch ImmunitySpecified from -40°C to +125°C5-Lead SOT-23 PackageAPPLICATIONSMicroprocessor SystemsComputersControllersIntelligent InstrumentsPortable EquipmentGENERAL DESCRIPTIONThe ADM6821-ADM6825 are supervisory circuits which monitor power supply voltage levels and code execution integrity in microprocessor-based systems. As well as providing power-on-reset signals, an on-chip watchdog timer can reset the microprocessor if it fails to strobe within a preset timeout period. A reset signal can also be asserted by means of an external push-button, through a manual reset input. The three parts feature different combinations of watchdog input, manual reset input and output stage configuration, as shown in table 1.FUNCTIONAL BLOCK DIAGRAMMRRESET VEach part is available in a choice of 9 reset threshold options ranging from 1.58V to 4.63V. The reset and watchdog timeout periods are fixed at 140ms (min) and 1.6s (typ), respectively. The ADM6821-ADM6825 are available in 5-lead SOT-23 packages and typically consume only 3µA, making them suitable for use in low power portable applications.Table 1. Selection TableADM6821–ADM6825 Preliminary Technical DataADM6821–ADM6825—SPECIFICATIONSTable 2. V CC=4. 5V to 5.5V for ADM682_L/M, V CC=2.7V to 3.6V for ADM682_T/S/R, V CC=2.1V to 2.75V for ADM682_Z/Y,V CC=1.53V to 2.0V for ADM682_W/V, T A=-40°C to +125°C, unless otherwise noted.Rev.PrA | Page 2 of 7Preliminary Technical DataADM6821–ADM6825Rev.PrA | Page 3 of 7ABSOLUTE MAXIMUM RATINGSTable 3. T A = 25°C unless otherwise noted.Stresses above those listed under Absolute Maximum Ratings may cause permanent damage to the device. This is a stress rating only and functional operation of the device at these or any other conditions above those indicated in the operational section of this specification is not implied. Exposure to absolute maximum rating conditions for extended periods may affect device reliability.ADM6821–ADM6825Preliminary Technical DataRev.PrA | Page 4 of 7PIN CONFIGURATIONS AND FUNCTIONAL DESCRIPTIONSV CCRESET GNDMRWDIV CC GND MRWDI V CC RESET GND RESETWDI V CCRESET GNDRESET MRTable 4. Pin Functional DescriptionsESD CAUTION`ESD (electrostatic discharge) sensitive device. Electrostatic charges as high as 4000 V readily accumulate on the human body and test equipment and can discharge without detection. Although this product features proprietary ESD protection circuitry, permanent damage may occur on devices subjected to high energy electrostatic discharges. Therefore, proper ESD precautions are recommended to avoid performance degradation or loss of functionality.Preliminary Technical DataADM6821–ADM6825Rev. PrA | Page 5 of 7ORDERING GUIDEModel Reset Threshold (V) Temperature Range Quantity Package Type Branding ADM6821LART-RL 4.63 -40°C to +125°C 10k SOT-23-5 N0A ADM6821LART-RL7 4.63 -40°C to +125°C 3k SOT-23-5 N0A ADM6821MART-RL 4.38 -40°C to +125°C 10k SOT-23-5 N0A ADM6821MART-RL7 4.38 -40°C to +125°C 3k SOT-23-5 N0A ADM6821TART-RL 3.08 -40°C to +125°C 10k SOT-23-5 N0A ADM6821TART-RL7 3.08 -40°C to +125°C 3k SOT-23-5 N0A ADM6821SART-RL 2.93 -40°C to +125°C 10k SOT-23-5 N0A ADM6821SART-RL7 2.93 -40°C to +125°C 3k SOT-23-5 N0A ADM6821RART-RL 2.63 -40°C to +125°C 10k SOT-23-5 N0A ADM6821RART-RL7 2.63 -40°C to +125°C 3k SOT-23-5 N0A ADM6821ZART-RL 2.32 -40°C to +125°C 10k SOT-23-5 N0A ADM6821ZART-RL7 2.32 -40°C to +125°C 3k SOT-23-5 N0A ADM6821YART-R L 2.19 -40°C to +125°C 10k SOT-23-5 N0A ADM6821YART-R L 7 2.19 -40°C to +125°C 3k SOT-23-5 N0A ADM6821WART-RL 1.67 -40°C to +125°C 10k SOT-23-5 N0A ADM6821WART-RL7 1.67 -40°C to +125°C 3k SOT-23-5 N0A ADM6821VART-RL 1.58 -40°C to +125°C 10k SOT-23-5 N0A ADM6821VART-RL7 1.58 -40°C to +125°C 3k SOT-23-5 N0A ADM6822LART-RL 4.63 -40°C to +125°C 10k SOT-23-5 N0B ADM6822LART-RL7 4.63 -40°C to +125°C 3k SOT-23-5 N0B ADM6822MART-RL 4.38 -40°C to +125°C 10k SOT-23-5 N0B ADM6822MART-RL7 4.38 -40°C to +125°C 3k SOT-23-5 N0B ADM6822TART-RL 3.08 -40°C to +125°C 10k SOT-23-5 N0B ADM6822TART-RL7 3.08 -40°C to +125°C 3k SOT-23-5 N0B ADM6822SART-RL 2.93 -40°C to +125°C 10k SOT-23-5 N0B ADM6822SART-RL7 2.93 -40°C to +125°C 3k SOT-23-5 N0B ADM6822RART-RL 2.63 -40°C to +125°C 10k SOT-23-5 N0B ADM6822RART-RL7 2.63 -40°C to +125°C 3k SOT-23-5 N0B ADM6822ZART-RL 2.32 -40°C to +125°C 10k SOT-23-5 N0B ADM6822ZART-RL7 2.32 -40°C to +125°C 3k SOT-23-5 N0B ADM6822YART-RL 2.19 -40°C to +125°C 10k SOT-23-5 N0B ADM6822YART-RL7 2.19 -40°C to +125°C 3k SOT-23-5 N0B ADM6822WART-RL 1.67 -40°C to +125°C 10k SOT-23-5 N0B ADM6822WART-RL7 1.67 -40°C to +125°C 3k SOT-23-5 N0B ADM6822VART-RL 1.58 -40°C to +125°C 10k SOT-23-5 N0B ADM6822VART-RL7 1.58 -40°C to +125°C 3k SOT-23-5 N0B ADM6823LART-RL 4.63 -40°C to +125°C 10k SOT-23-5 N0C ADM6823LART-RL7 4.63 -40°C to +125°C 3k SOT-23-5 N0C ADM6823MART-RL 4.38 -40°C to +125°C 10k SOT-23-5 N0C ADM6823MART-RL7 4.38 -40°C to +125°C 3k SOT-23-5 N0C ADM6823TART-RL 3.08 -40°C to +125°C 10k SOT-23-5 N0C ADM6823TART-RL7 3.08 -40°C to +125°C 3k SOT-23-5 N0C ADM6823SART-RL 2.93 -40°C to +125°C 10k SOT-23-5 N0C ADM6823SART-RL7 2.93 -40°C to +125°C 3k SOT-23-5 N0C ADM6823RART-RL 2.63 -40°C to +125°C 10k SOT-23-5 N0C ADM6823RART-RL7 2.63 -40°C to +125°C 3k SOT-23-5 N0C ADM6823ZART-RL 2.32 -40°C to +125°C 10k SOT-23-5 N0C ADM6823ZART-RL7 2.32 -40°C to +125°C 3k SOT-23-5 N0C ADM6823YART-R L2.19 -40°C to +125°C 10k SOT-23-5 N0C ADM6823YART-R L 7 2.19 -40°C to +125°C 3kSOT-23-5N0CADM6821–ADM6825Preliminary Technical DataRev.PrA | Page 6 of 7ORDERING GUIDE (CONTD.)Model Reset Threshold (V) Temperature Range Quantity Package Type Branding ADM6823WART-RL 1.67 -40°C to +125°C 10k SOT-23-5 N0C ADM6823WART-RL7 1.67 -40°C to +125°C 3k SOT-23-5 N0C ADM6823VART-RL 1.58 -40°C to +125°C 10k SOT-23-5 N0C ADM6823VART-RL7 1.58 -40°C to +125°C 3k SOT-23-5 N0C ADM6824LART-RL 4.63 -40°C to +125°C 10k SOT-23-5 N0D ADM6824LART-RL7 4.63 -40°C to +125°C 3k SOT-23-5 N0D ADM6824MART-RL 4.38 -40°C to +125°C 10k SOT-23-5 N0D ADM6824MART-RL7 4.38 -40°C to +125°C 3k SOT-23-5 N0D ADM6824TART-RL 3.08 -40°C to +125°C 10k SOT-23-5 N0D ADM6824TART-RL7 3.08 -40°C to +125°C 3k SOT-23-5 N0D ADM6824SART-RL 2.93 -40°C to +125°C 10k SOT-23-5 N0D ADM6824SART-RL7 2.93 -40°C to +125°C 3k SOT-23-5 N0D ADM6824RART-RL 2.63 -40°C to +125°C 10k SOT-23-5 N0D ADM6824RART-RL7 2.63 -40°C to +125°C 3k SOT-23-5 N0D ADM6824ZART-RL 2.32 -40°C to +125°C 10k SOT-23-5 N0D ADM6824ZART-RL7 2.32 -40°C to +125°C 3k SOT-23-5 N0D ADM6824YART-R L 2.19 -40°C to +125°C 10k SOT-23-5 N0D ADM6824YART-R L 7 2.19 -40°C to +125°C 3k SOT-23-5 N0D ADM6824WART-RL 1.67 -40°C to +125°C 10k SOT-23-5 N0D ADM6824WART-RL7 1.67 -40°C to +125°C 3k SOT-23-5 N0D ADM6824VART-RL 1.58 -40°C to +125°C 10k SOT-23-5 N0D ADM6824VART-RL7 1.58 -40°C to +125°C 3k SOT-23-5 N0D ADM6825LART-RL 4.63 -40°C to +125°C 10k SOT-23-5 N0E ADM6825LART-RL7 4.63 -40°C to +125°C 3k SOT-23-5 N0E ADM6825MART-RL 4.38 -40°C to +125°C 10k SOT-23-5 N0E ADM6825MART-RL7 4.38 -40°C to +125°C 3k SOT-23-5 N0E ADM6825TART-RL 3.08 -40°C to +125°C 10k SOT-23-5 N0E ADM6825TART-RL7 3.08 -40°C to +125°C 3k SOT-23-5 N0E ADM6825SART-RL 2.93 -40°C to +125°C 10k SOT-23-5 N0E ADM6825SART-RL7 2.93 -40°C to +125°C 3k SOT-23-5 N0E ADM6825RART-RL 2.63 -40°C to +125°C 10k SOT-23-5 N0E ADM6825RART-RL7 2.63 -40°C to +125°C 3k SOT-23-5 N0E ADM6825ZART-RL 2.32 -40°C to +125°C 10k SOT-23-5 N0E ADM6825ZART-RL7 2.32 -40°C to +125°C 3k SOT-23-5 N0E ADM6825YART-R L 2.19 -40°C to +125°C 10k SOT-23-5 N0E ADM6825YART-R L 7 2.19 -40°C to +125°C 3k SOT-23-5 N0E ADM6825WART-RL 1.67 -40°C to +125°C 10k SOT-23-5 N0E ADM6825WART-RL7 1.67 -40°C to +125°C 3k SOT-23-5 N0E ADM6825VART-RL 1.58 -40°C to +125°C 10k SOT-23-5 N0E ADM6825VART-RL7 1.58 -40°C to +125°C 3kSOT-23-5N0EPreliminary Technical DataADM6821–ADM6825Rev. PrA | Page 7 of 7OUTLINE DIMENSIONS0.3PLANECOMPLIANT TO JEDEC STANDARDS MO-178AAFigure 1. 5-Lead Small Outline Transistor Package [SOT-23](RT-5)Dimensions shown in millimeters© 2004 Analog Devices, Inc. All rights reserved. Trademarks and registered trademarks are the property of their respective companies. Printed in the U.S.A.。